
3 minute read
Designs on BIM
For decades, building information modelling (BIM) has been touted as the future of the construction industry. Ironically, BIM continues to prove quite elusive in the residential and commercial segments. Instead, disintegrated functions are the norm with architects drawing one model, structural engineers using a different set of tools, and suppliers performing multiple material takeoffs in a variety of ways. There is one exception, however, from a surprising corner of the timber construction market. The promise of BIM is becoming a reality for post-frame with SmartBuild Systems.
Why BIM is MIA
Of all the programs released over the past 30 years, none have addressed the structure of the industry. BIM works when each segment is on a complete design system that seamlessly manages every stage of the project, saves money, reduces errors, and increases everyone’s bottom line.
The complete design system
In 2002, Keith Dietzen, founder and CEO of SmartBuild Systems, was commissioned to work on the Pulte Home Sciences project. The idea was to use the world’s best building technologies to produce home foundations, floors, and walls. When the factory opened in Detroit, it was Dietzen’s software that drove the operation.
“We went through the whole process of automating and made tremendous strides in terms of the design time,” he explained. When the recession hit, and the factory closed, Dietzen remained undeterred and continued his quest to improve construction through technology.
Dietzen travelled to Germany and returned with a Hans Hundegger computerised linear feed saw. Armed with his Whole House design software, Dietzen was able to model a complete structure and figure all the framing. The data downloaded to the saw to pre-cut and pre-mark everything for the project. All of it could then be packaged up and sent to a job site along with the entire set of plans.
“That’s why when I saw how the postframe industry worked, I was just enamoured of it and just said, yeah, I know we can do this. I know we can do it,” he said.
Knowing it might be a hard sell to the homebuilding industry, Dietzen focused on post-frame where one company typically builds the structure from start to finish.
SmartBuild Systems
SmartBuild is a state-of-the-art, web-based system that creates a 3D graphic model of a post-frame structure. Easy enough for almost anyone, the system guides the user through a series of prompts that automatically: • Frames custom structures • Builds cutlists for sheathing and trim • Compiles bid and order using a custom database • Generates construction drawings • Calculates the price of labour, materials, and sales tax • Populates sales documents • Creates building descriptions • Emails and prints copies for the customer Admittedly, says Dietzen: “The one thing we don’t do in our application that BIM really should, is automate the engineering.
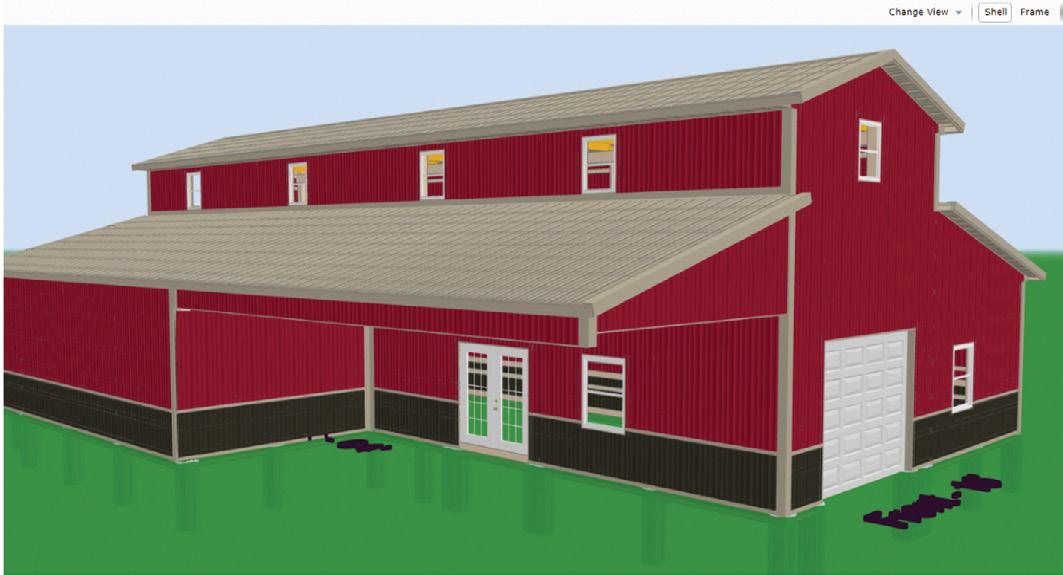
Although, that is something that we may include down the road.”
Custom database
SmartBuild works because it creates a relationship between the buyer, the contractor, and the distributor.
The team at SmartBuild works with the distributor setting up a custom database with all their inventory, part numbers, colour schemes, and sales documents. The distributor empowers the contractor, who is now able to sit face-to-face with the buyer and build a 3D model before their eyes. When the buyer is happy, the contractor pushes a button and the process is automatically completed and sent back to the distributor. Everyone wins. In just the last three months, using SmartBuild as a sales tool, Burrow’s Post Frame Supply has increased its sales by 15%. Burrow’s administrator, Brandon Hamilton, said: “With SmartBuild we get quotes turned around extremely fast, it’s blown my mind!”
And the contractors love it too. “We set up a guy yesterday. He said he’s used every kind of software and SmartBuild does things that nothing in the industry has ever been able to do,” he said.
What’s next
Post-frame has proven that BIM can work in construction, but is the rest of the industry onboard? When asked if he’d be willing to work on a program for the residential industry, Dietzen anwered: “Sure. That’s a distinct possibility. Right now, we are consumed with our post-frame effort, but you never know about tomorrow.”
making the transition to a ZERO CARBON WORLD
Join 27,000 industry influencers and shapers with the power to change the future of the built environment.
ACT NOW Get your FREE ticket using code MP35 and be part of the industry’s catalyst for change www.futurebuild.co.uk