
13 minute read
Cladding creations
Timber cladding is proving to be an increasingly popular choice for both residential and commercial projects in the UK and beyond
Not only can timber cladding aesthetically enhance a building, it can also help to improve its energy performance, making it a popular choice for a wide range of projects. Over the following pages, we highlight a selection of buildings which showcase timber cladding’s beauty and versatility.
New lease of life
Kebony cladding has been used to give a modern twist to the extension of a once traditional 20th century home in Dorking, deep in the Surrey Hills.
Juxtaposed against the original building Lees Munday Architects selected Kebony to achieve the owner’s vision for a sustainable and family friendly home.
Improving the existing kitchen positioned on the east side of the house, with no garden access, was a key priority for the architects, who were able to rework the kitchen, dining and daytime seating area to provide an open plan functional living space which embraces the sunny western aspect of the house and takes advantage of the large rear garden and spectacular view. The adjacent lounge was significantly enlarged and continued the Kebony cladding along the rear elevation of the house.
For Lees Munday Architects, a relationship with the garden and the landscape was an essential focus throughout the design. As a result, two sides of the new extension, and the lounge, were completely glazed to incorporate the garden as part of the interior living space, whilst bespoke sliding doors opening onto a paved patio for alfresco dining and children’s play were also installed. A loft conversion has provided an extra en-suite bedroom, while the master bedroom has gained a full height window and roof terrace, both taking full advantage of the spectacular far-reaching views.
Natural materials and finishes, including stone and timber were selected inside and out for their authenticity and the way they wear in instead of wearing out. Improving the energy efficiency of the house was also paramount for the owner, this was achieved by draught


Kebony Cladding has been used to give a modern twist to the extension of a family home in Surrey. Photos © Jonathan Freeman

proofing, enhanced insulation, and the installation of 21 flat black photovoltaic panels on the new kitchen roof. Successfully integrated with the design, the panels were combined with Kebony wood as a rainscreen system positioned over a mechanically fixed UPVC roof membrane to supply all the hot water for the property. The form of the main extension took its cue from the many agricultural barns in the local area.
Lees Munday Architects discovered Kebony and selected the material for the roof and exterior cladding, which proved easy to work with without splintering.
“For this contemporary extension, we sought a single lightweight material that would be able to clad roofs as well as walls. After an extensive search for newly available modified woods, we were delighted to select Kebony with the knowledge that we could achieve our vision and leave the wood ‘authentically’ unfinished,” said David Lees of Lees Munday Architects. “We are extremely proud of this project and would thoroughly recommend Kebony as a cladding material, so much so that we have taken several clients to see this house and all have since chosen Kebony to clad their projects.” Adrian Pye, international sales director at Kebony added: “We are thrilled that Lees Munday Architects have realised the potential of Kebony to successfully introduce a new character to this building. The natural appearance of the wood perfectly complements the original building’s exterior; Kebony’s resistance to wear and weathering will also ensure the new extension stands the test of time.” Contemporary twist
James Latham supplied charred Accoya and Western Red Cedar which has been used as cladding in the part rebuilding, extension and conversion of a former agricultural building to create a barn-style home in Newmarket.
Cambridge-based NP Architects, an award-winning RIBA Chartered Practice, was commissioned to carry out the conversion and Arnold & Willis Construction was appointed as the main contractor.
The main steel-framed barn has been retained as a double height space and re-clad in corrugated steel, whilst the lower wings have been rebuilt in a courtyard arrangement and clad in charred Accoya. Large openings have been introduced to frame views and form a
strong connection with the wider landscape from within.
Charred timber cladding is a modern application of the ancient Japanese art of charring timber to provide a beautiful and long-lasting timber cladding and this is a technique that Shou Sugi Ban has perfected. Hidden from the exterior view is a centrally located courtyard, where a change of materials offers a softer palette giving a more homely feel. The raw unfinished Western Red Cedar creates a unique and distinctive fragrance.
Justin Hayward, James Latham’s technical timber sales development manager, added: “The reaction to Shou Sugi Ban from the market has been astonishing, Charred Accoya has been used to clad a barn-style home in Newmarket. Photo © James Latham
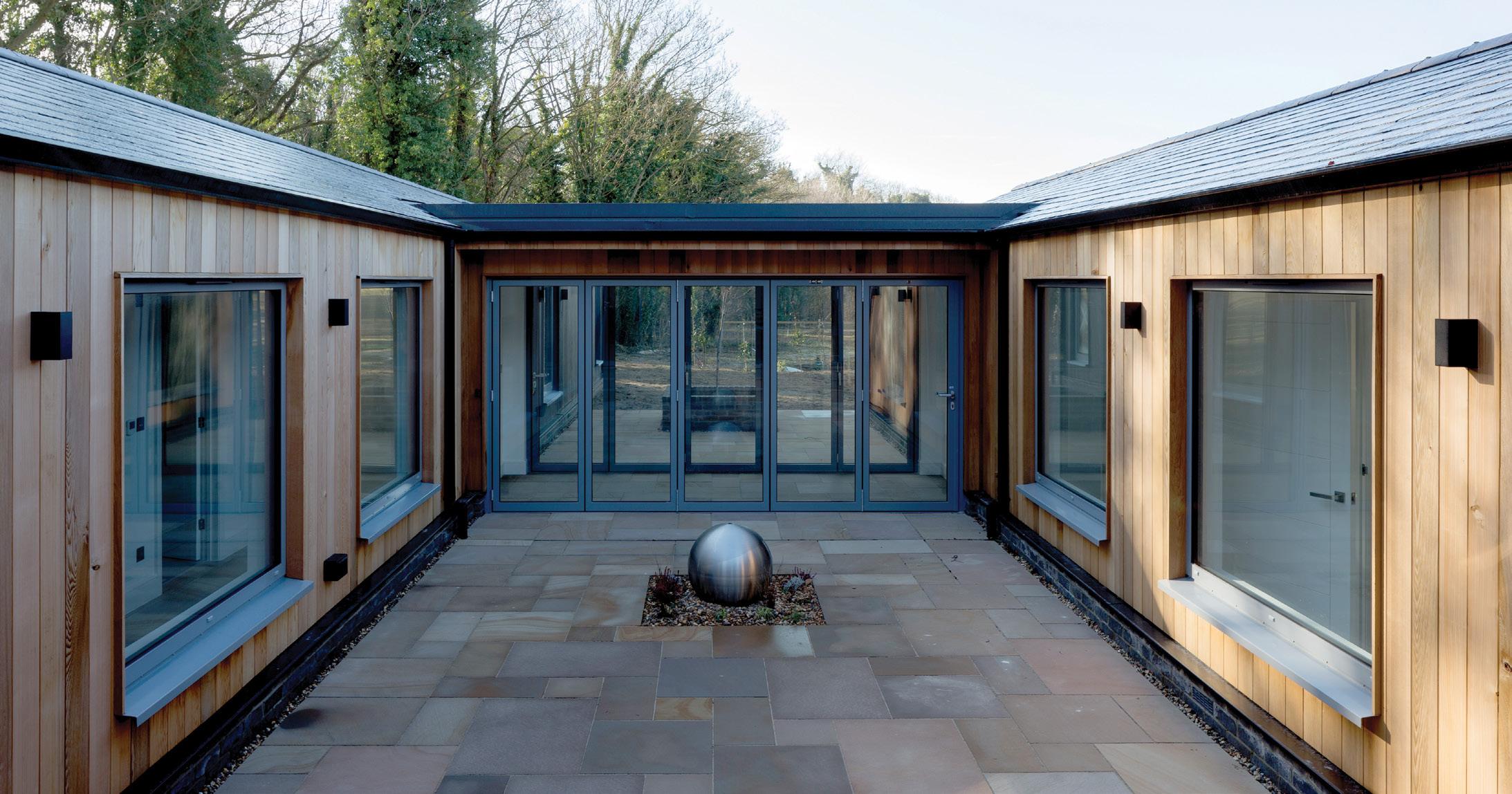
Order your free Trex® samples using code TiC2020
THE SECRET IS IN THE SHELL
The Trex ® shell is designed to resist fading and staining which is backed by the market leading 25-Year Limited Residential Fade and Stain Warranty

Trex ® decks will not rot, warp, crack or split and are covered by a 25-Year Limited Residential Warranty against material defects
GOOD
Trex® decks are made from 95% recycled material Quality capped product with a solid core delivers a durable and stable performance

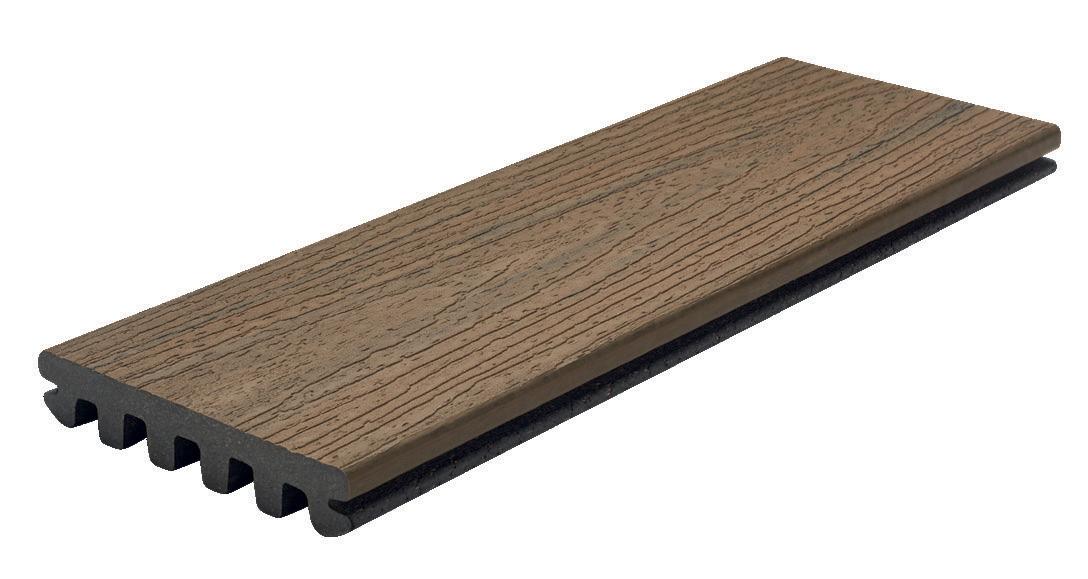

TREX ® FOR ANY DECK With fabulous colours and a realistic wood grain effect, the Trex® range has a solution for any project or budget.
BETTER
BEST
New higher specification for deck substructures

The specification requirements for pressure treated softwood deck substructures are set to change in BS8417, the British Standard for wood preservation, when it is next revised later this year with key trade bodies incorporating the changes now. This means that all softwood components used for the structural sub-frame of a deck will have to be treated to the same level as components in permanent contact with the ground, referred to as Use Class 4. Janet Sycamore from the Timber Decking and Cladding Association (TDCA) explains why and how it will mean better performance for timber decking. Pressure treated softwood is commonly used to build decking substructures to support timber and composite deck boards. Preservative treatment provides wood with added durability and BS 8417 requires that the loading and penetration of preservative, impregnated into the wood, is tailored to the desired end use. End uses are grouped into 5 categories; use class 3 relates to exterior above ground use whereas Use Class 4 relates to exterior ground contact use. Janet explains further ‘Ground contact use presents a higher biological risk to timber and therefore, in order to work well in this situation, a higher level of wood preservative needs to be impregnated into the timber’. The ‘Use Class’ system is important because it indicates the scale of the biological threat faced by a wood product in a specific end-use situation and determines the preservative loading and penetration required to deliver the service life required. Clear information about using wood correctly for decking and landscaping projects has been promoted widely in the UK for many years with organisations like the TDCA leading the way in providing supply chain and enduser good practice guidance. Despite this, mistakes and shortcuts are still being made in constructing timber deck substructures – which compromise both the performance of the finished deck and the reputation of wood. This is made worse because once a deck is completed the substructure is typically not visible with the consequences of bad practice not evident until it’s too late. For example, if vegetation and/ or debris is allowed to accumulate beneath a deck, this restricts air movement and traps water, increasing the exposure risk. Likewise, it is common for deck joists to be set directly on or very close to the ground.
The failure of the substructure is clearly safety critical. In Sweden, Finland, France and north America, the whole deck substructure system (posts, beams and joists) is categorised as Use Class 4.
Subsequently the decision has been taken to follow this best practice in order to ensure substructures are robust and perform better. In addition this should raise confidence in the market and help to maintain timber’s position as the most popular and cost effective solution when building decks. Going forward this means that in the UK the whole substructure will be categorised as Use Class 4, whereas previously, only the posts were categorised as Use Class 4.

Following a full review of the issues outlined, the Wood Protection Association Technical Committee, which includes representatives of the BRE (Building Research Establishment) and TRADA (Timber Research and Development Association), adopted these changes as WPA policy and were subsequently ratified by both the WPA and TDCA Boards. These changes have also been adopted by the BSI committee managing BS8417 (B/515) and so will be incorporated into the full standard review (probably later in 2020).
In due course the WPA, TDCA and Timber Trade Federation (TTF) will be working to adopt this change in policy across the membership of all three partner associations, so as to help them transition to the new requirements in time for the publication of the revised BS8417 towards the end of 2020. In fact TDCA members Hoppings Softwoods and BSW Timber have already introducecd products that meet the new guidance.
Further information about TDCA visit: www.tdca.org.uk
Check list when buying substructure components for timber decking
• Establish if the component has been impregnated with a wood preservative in an industrial treatment plant and that it is suitable for outdoor use. • Determine what service life is claimed – it should be similar or better than the deck boards you have chosen. • Ask your supplier to verify that the timber meets a Use Class 4 specification – on the delivery note or with a treatment certificate. • NEVER substitute wood that has been treated for an indoor application for use in an external application – early failure is inevitable. • When cross cutting, notching or boring treated timber products during installation, ALWAYS apply an end grain preservative treatment to freshly exposed areas – to maintain the integrity of the protection. NEVER put cut ends in the ground, even if end grain coated.
This expansive, modern residence on a former pecan farm outside of Houston in Texas comprises four “pods” clad in Kebony


it really does have the wow factor and enquiries, and indeed orders, are growing by the day.
“Charred timber cladding is becoming increasingly popular in the specification market. Traditional techniques are used to give uniqueness to each individual project and there are lots of finishes and textures available for both interior and exterior projects – from the traditional, highly charred, heavily textured looking cladding to the sleek and contemporary finish.”
Modern ranch
An expansive, modern residence, built on a former pecan farm a few miles outside of Houston in Texas, comprises four “pods” clad in Kebony. The nearly 6,000 square-foot property was designed by David Wersebe, who works in the mineral royalty business in Houston, and was constructed on his family’s 210-acre ranch.
It blends elements of its original pecan orchard site with materials complementary to the environment. Hand-cut Texas limestone and handhewn beams from a 200-year-old Amish barn frame the expansive entry, and large-scale custom metal windows open to the native landscape. Kebony was carefully selected to clad all four facades, reflecting the organic but modern feel of the house.
“The Kebony cladding worked extremely well for this project and as it weathers into its grey patina over time, it will blend beautifully into this environment,” said Wersebe.
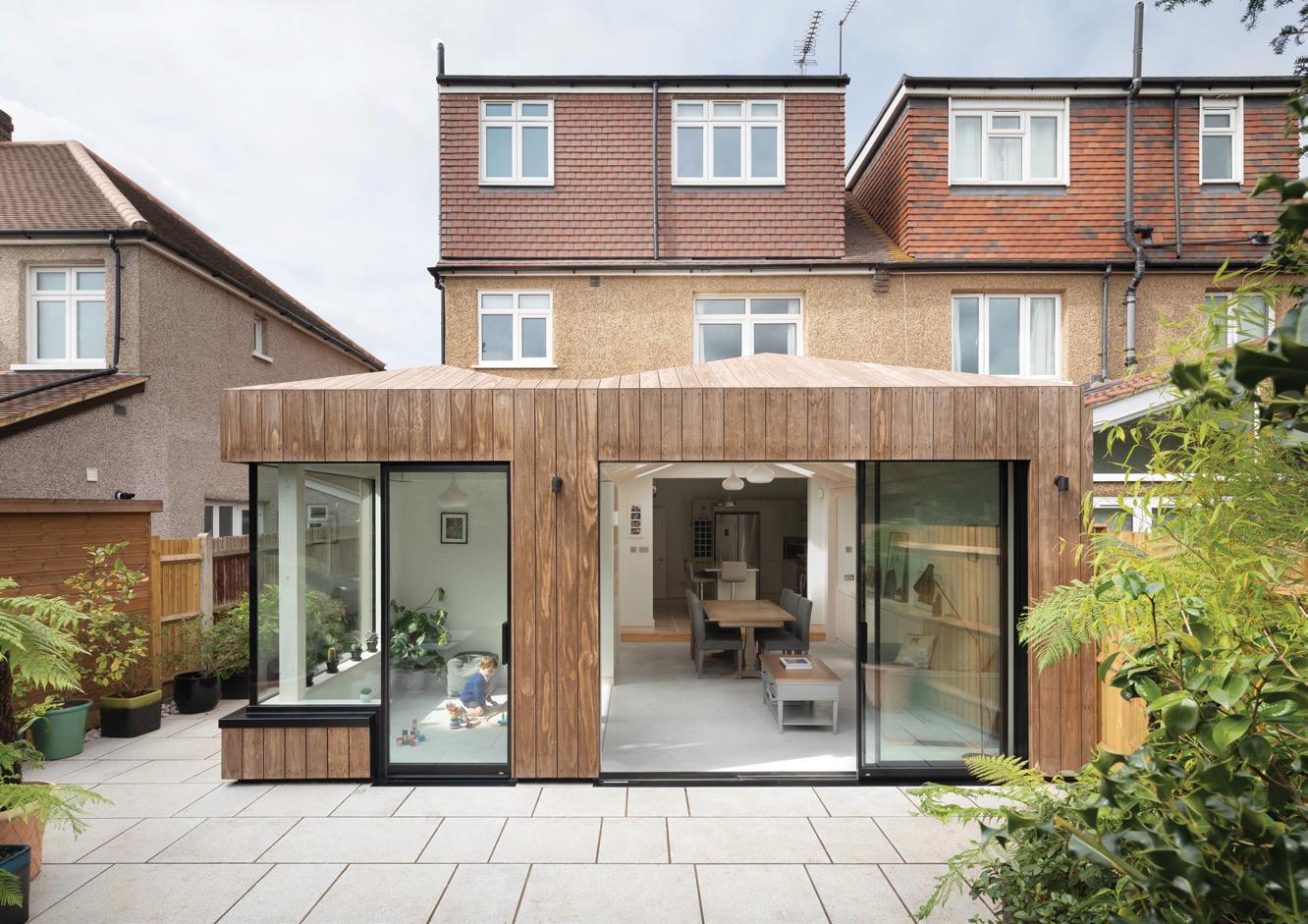
The home is arranged in four distinct pods. The centre pod houses the living room, kitchen and other common areas; the north and south pods comprise the guest rooms and master suite, respectively. A separate air-conditioned garage can accommodate four cars and features a hangar door that opens into an awning, as well as two elevated workspaces and a rooftop observation deck.
All four structures are roofed in metal with custom-designed awnings with irrigated trellises; the centre pod features a two-storey white oak living room cathedral ceiling; its back porch includes a cantilevered deck overlooking Lake Lucille with a covered patio and wood-burning fireplace. A glass-walled steel frame bridge with unobstructed views leads to the master suite.
Transforming a traditional suburban semi Up Architects selected Kebony for the exterior cladding of an extension to a traditional suburban semi-detached house in Wimbledon. It wanted to design an extension that stood out from the run-of-the-mill extensions in the area, and started with the idea of a single large space that could be adapted to suit the family’s needs over time, incorporating dining, living, a playroom, study area, TV room and guest room into the brief. A light filled open-plan living space was created with an enhanced connection to the garden. In keeping with the client’s brief, the design is simple, unassuming and honest with two simple roof forms sitting over the main space, formed from an exposed glulam timber structure with Kebony cladding used for the exterior walls and roof.
The simple geometry of the twin-hipped roofs breaks up the bulk seen from outside and defines the different spaces internally without a physical division. The timber Kebony cladding lines up across the walls and roof, with compound mitred joints, making the whole extension appear to be carved from one block of wood, with no visible gutters to compromise the sharp lines. “Following our appointment for this project, it was essential that the family felt they had made the right decision in opting for an extension rather than moving house,” said Marty McColl, director at Up Architects. “We were able to create substantially more space, whilst ensuring the extension reflected the brief to build something that was beautiful in design without being ostentatious; we are thrilled with the final product and loved working with Kebony to transform this traditional suburban semi-detached house into a contemporary and more practical family home.”
Industry news | Features | Design | Certification Construction | Interviews | Analysis | Sustainability Merchant news | Cladding | Decking | Offsite Timber protection | Markets | Health & safety Events | Case studies | & much more...

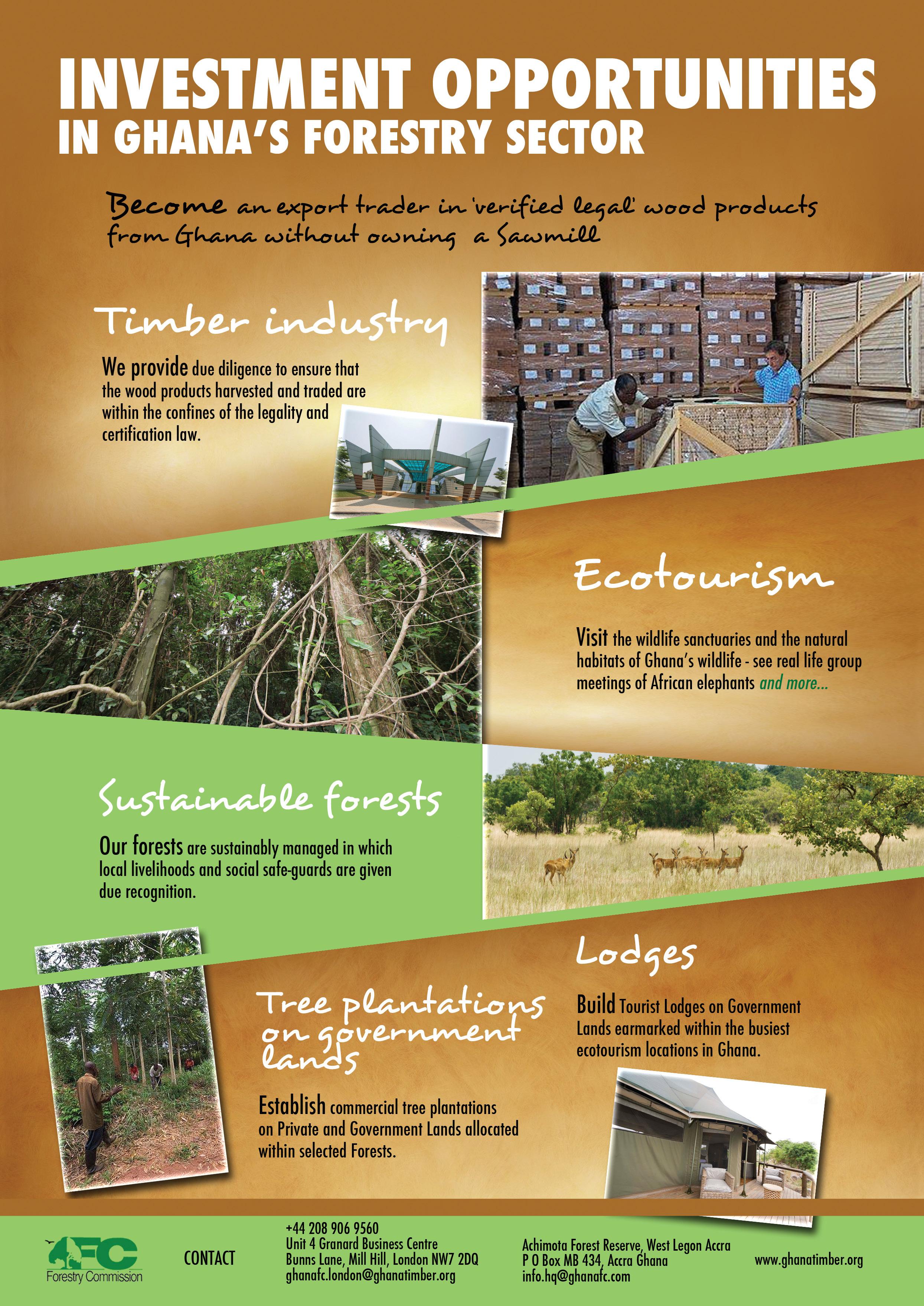


Setting the standards for timber fastening BeA your partner for timber frame and offsite construction manufacturing
Across Europe and worldwide, BeA’s fastening technology, tools and consumables are the trusted choice for some of the biggest and best known names in timber frame and offsite construction.

BeA manufacture an extensive range of market leading choice of fasteners, nails, staples and tools.
We offer customers:
An unrivalled range of manual, semi-automatic and fully automated fastening solutions.
Using industry leading quality controls, BeA meet or exceed standards such as Eurocode 5.

Reliable products, competitive prices and the kind of service and delivery you can depend on from BeA.
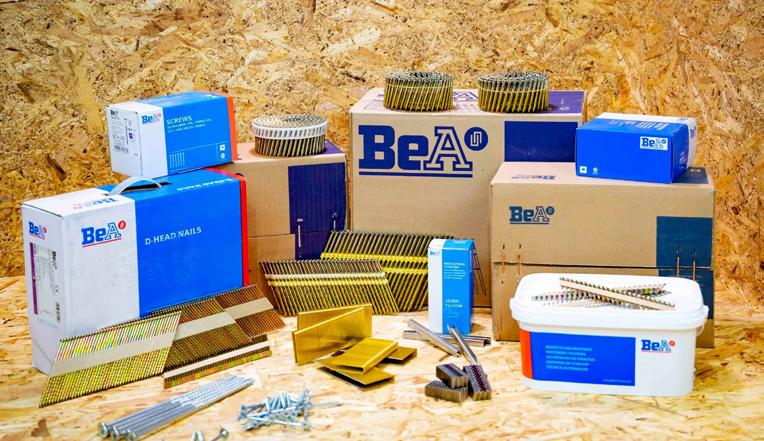