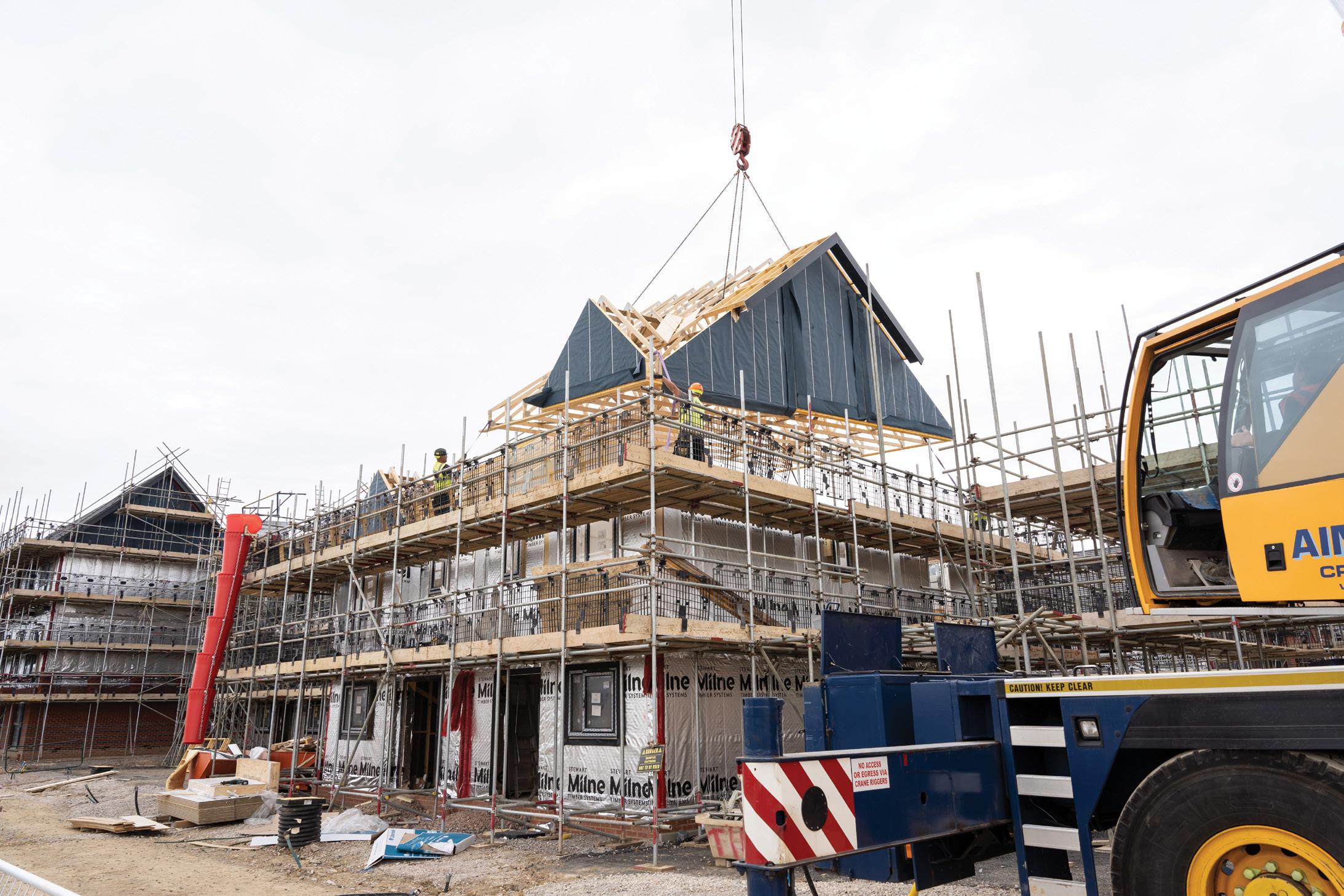
24 minute read
News
AIMCH Publishes Housebuilding Report
A new report, Whole Life Carbon Assessment of Homes, published by the Advanced Industrialised Methods for the Construction of Homes (AIMCH), concludes that using sustainably sourced timber panelised MMC methods to build new homes rather than masonry products can reduce the carbon impact of construction.
On a whole life carbon basis, the study predicts that up to 5t CO2e per four bed dwelling, equivalent to 16,500 road miles, could be saved, when using timber panelised MMC methods.
AIMCH is a £6.5 million collaborative R&D project which aims to promote and develop industrialised off-site modern construction methods to build homes quickly and viably. Participating partners are Stewart Milne Group, Barratt Developments PLC, L&Q, the Manufacturing Technology Centre (MTC), the Construction Scotland Innovation Centre (CSIC) and Forster Roofing Services Ltd.
Stewart Dalgarno, AIMCH Project Director and Director of Innovation and Sustainability at Stewart Milne Group said, “The comprehensiveness of this report provides valuable insights into where developers, house builders and the supply chain can make a positive contribution to reducing the whole and embodied carbon contributions of new build homes. “AIMCH commissioned the report to understand the differences in whole life carbon emissions over 60 years, to current building regulation standards, between open and closed panel timber MMC systems and aerated concrete blockwork used in masonry construction. All processes relevant to the construction cycle, in line with the RICS model have been considered — materials, manufacture, transport, usage through to the end-of life and disposal stages. The resulting comprehensive analysis provides invaluable data to inform house builders on the carbon intensity of the two construction methods.”
Using the RICS Standard for Whole Life Carbon Assessment, the report represents a rigorous cradle-to-grave assessment of the carbon impact of both types of construction materials and their respective methodologies. 82% of emissions are generated from the homes operational use over 60 years, which is the same for both methods. 14% of emissions are generated from the materials and construction process. A small proportion of emissions are generated at end of life.
The study, authored by green energy consultancy Verco, examined four types of home utilising either: masonry – aerated blockwork and offsite manufactured open and closed panel timber MMC, both with brick cladding. Carbon sequestration benefits of timber, in line with RICS protocols, were applied to all methods of construction, for example benefiting masonry homes bult with timber floors and roofs. End of life assumptions used identical 90% recycle/re-use and 10% to landfill ratio across both material types.
Cementitious products including roof tiles, concrete blocks, brick cladding, strip foundations and floor slabs, were found generally to have the highest lifecycle embodied emissions. Conversely, timber frame wall elements sent to landfill, were found to produce 0.5 tCO2e emissions at end of life, compared to aerated concrete blocks.
Panelised timber MMC construction methods outperformed masonry construction on a whole-life carbon basis, when comparing the direct substitution of various wall elements – external, load bearing and party wall elements. Embodied emissions of these wall elements being as much as 82% less than that of the masonry construction. In addition, timber MMC key properties contributing to reduced emissions.
BSW Group sees timber in new light
From Photo to 3D Point Cloud
BSW, the UK’s largest integrated forestry and sawmilling group, has unveiled its new brand, with an expanded vision of ‘seeing timber in new light’. The brand launch sees the group uniting its capabilities under a new, overarching, BSW Group brand, forging an integrated supply chain to create value and sustain long-term growth.
Tony Hackney, CEO, BSW Group, said: “As the sector’s biggest integrated business, with capabilities including tree nurseries, forestry management, harvesting, production and energy, we believe we have a responsibility to drive positive change. Following a period of intense acquisition activity, we commissioned a robust, independent review of our brand and market positioning to guide the actions needed to support a more sustainable future.
“The feedback we gained has been invaluable. It has inspired our vision to become the most innovative, technologically advanced and sustainable timber business in the UK. By growing markets, increasing efficiency and resilience, and elevating our craft, we can help secure the future of our industry and our planet. We have a shared will to create value and achieve sustainable growth,” added Tony.
As part of the launch, BSW Group is committing to ensuring a seamless, circular supply chain, to investing in innovation and education, and to giving people more stability and choice. The brand launch follows BSW Group’s acquisition by Binderholz, which completed on 5 January 2022, strengthening the brand’s positioning in the value-added timber market. The businesses – Maelor Forest Nurseries, Tilhill, Dick Brothers, BSW Timber, BSW Timber Solutions, Bayram Timber and BSW Energy – will continue to operate in their own specialist areas under the new overarching BSW Group brand, with a shared vision to create value and achieve sustainable growth.
More at www.thebswgroup.co.uk
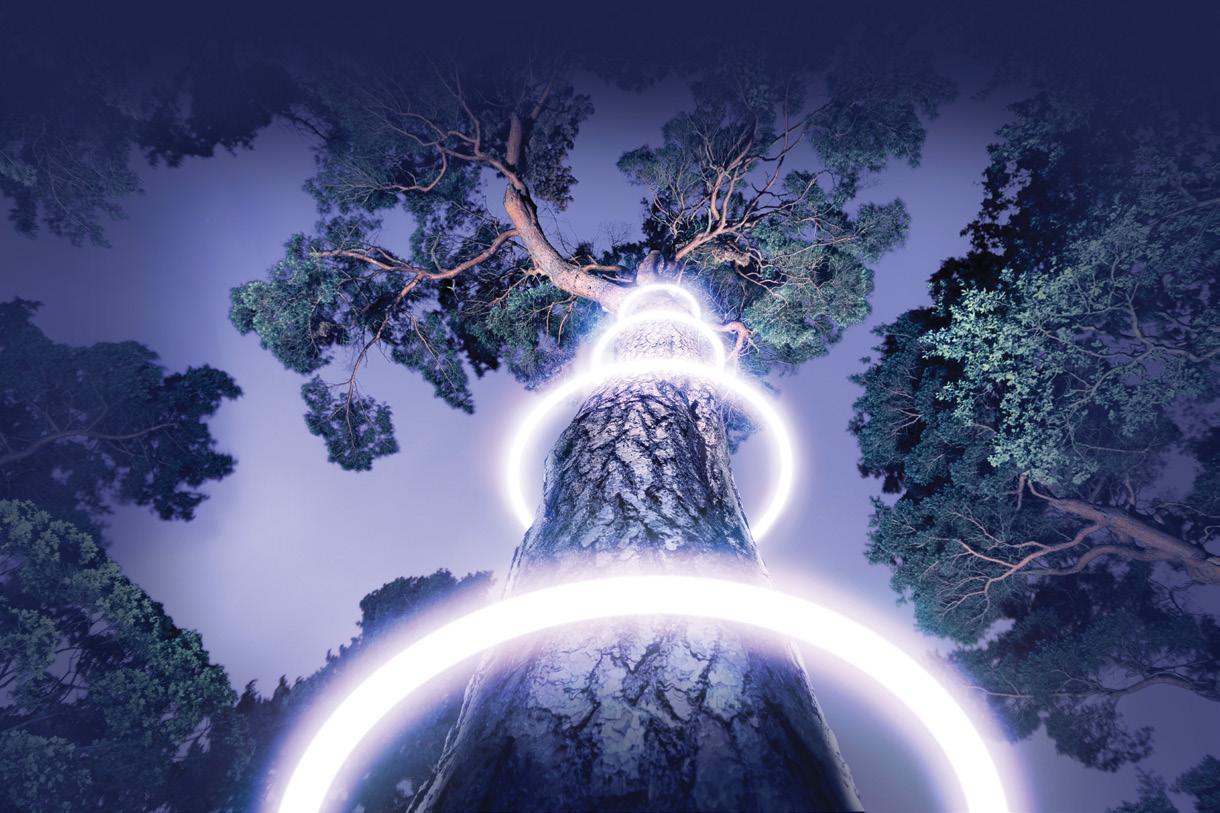
The ELCOVISION 10 software creates 3D point clouds from real photos using photgrammetry. The created 3D point cloud can be imported anytime to the SEMA 3D CAD/CAM timber construction software for further planning and construction.. 3D point clouds have conquered the digital world in the past two years. There are many ways to create a 3D view of an object. One new and not so expensive way is to generate 3D models and point clouds fully automatically from photos taken by a normal camera or with a drone. The high-precision and high-ly detailed 3D models have an almost laser scan quality.
The development of photogrammetry is advancing. An innovation of the ELCOVISION 10 is the fully automated generation of high-density point clouds taken from photos. The smallest differences in tex-ture on the object, even with areas that are barely distinguishable by colour, are sufficient to create almost ‘noise-free’ and detailed 3D point clouds.
But how do you create 3D point clouds from simple twodimensional images? Photos of different views of a building are read into the ELCOVISION program. The software now fully automatically calculates the viewpoints of the images when taken, calibrates the camera and finally, calculates a 3D point cloud of the building in high quality.
When a point cloud has been created from the object, it can be exported into the SEMA point cloud format (.spw) and read easily into the SEMA software. All the advantages of a point cloud generated with a 3D laser scanner are also valid for a point cloud generated with photogrammetry. The user gets the construction site virtually as a 3D model on their computer. Further processing, such as designing on the existing object or taking measurements, is carried out in SEMA as usual. Any sections of the scan are created in the program at the press of a button and all relevant quantity survey points are determined quickly and easily.
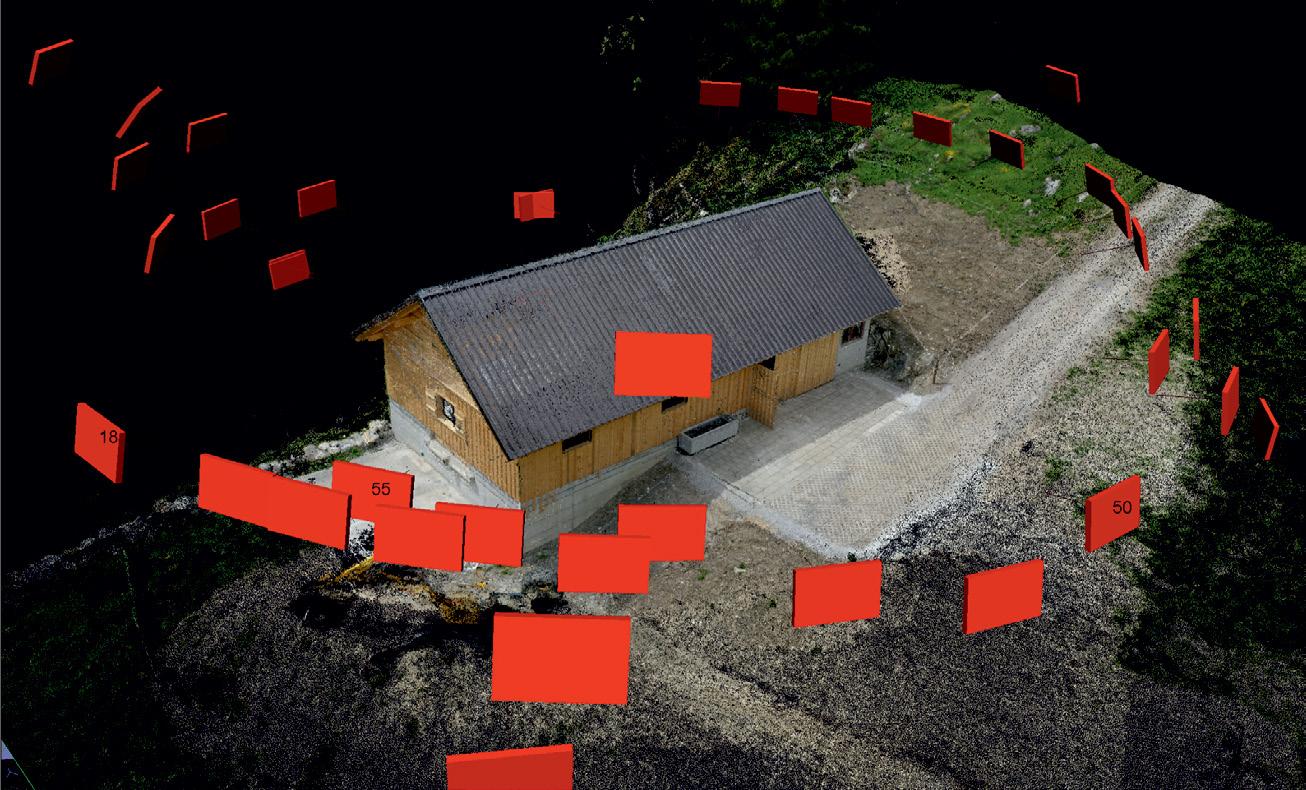
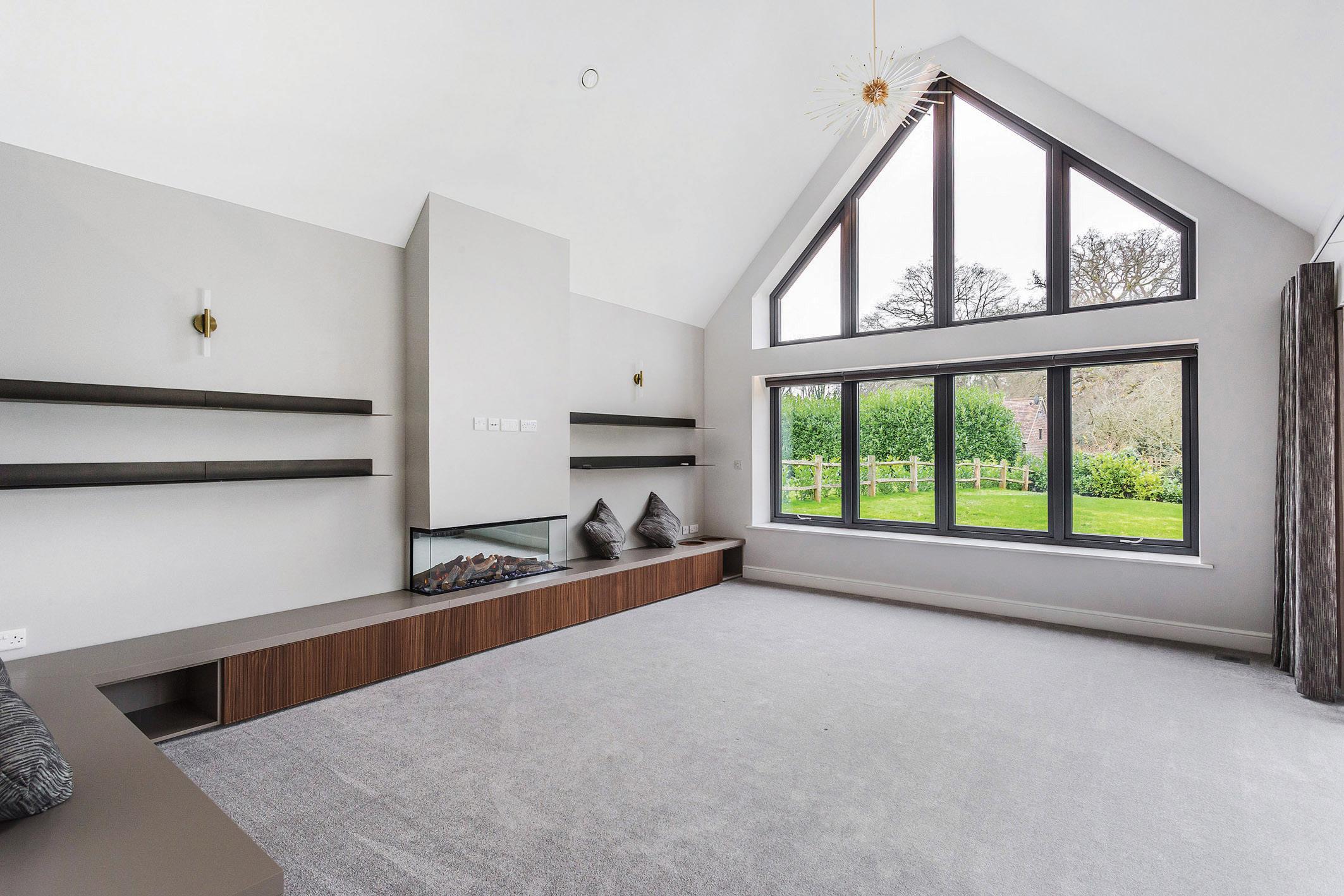
SAP reveals impressive energy efficiency at Scandia-Hus showhome
A third showhome created by timber frame specialist Scandia-Hus and insulated with Actis Hybrid products has achieved an impressive suite of energy efficiency and environmental performance parameters ahead of its unveiling to the public in the spring.
Its performance is captured in the as-built SAP calculation, which reveals an improvement of the Dwelling Emission Rate of 35% over the notional building specification and an improved Fabric Energy Efficiency rate of 24.5%. The 2,755sq ft three-bedroom chalet bungalow at Scandia-Hus’ Sussex premises also achieved an energy efficiency rating of B. And it has an impressively low level of air permeability, achieving an air leakage rate of 3.25 m3/hm2 at 50Pa, with this number of air changes per hour falling way within the building regulations’ limiting or notional values of 10 and 5m3/hm2 @50Pa respectively.
The UK’s largest designer and supplier of Swedish energy-saving timber framed homes was so impressed by the thermal efficiency achieved in the first two showhomes it built at its Sussex HQ that it replicated the precise specification it used on those buildings for its latest creation. The home offers the same U-values achieved in the initial two buildings - 0.14 in the roof and 0.16 in the walls thanks to the installation of vapour control layer HControl Hybrid and 155mm honeycomb design Hybris in the pitched roof and HControl Hybrid and 105mm Hybris in the walls.
The eco-friendly property runs on an air source heat pump, and the sustainably sourced timber used creates an airtight structure. The property is fully furnished and will be available for viewing from March.
Actis regional sales manager Liane Bayliss said: “Actis Hybrid products are particularly popular with timber frame manufacturers. Giving a hands-on demonstration of the various elements used in a build of this nature will be very educational, both for the potential buyers of Scandia-Hus properties and for specifiers keen to explore different insulation products and their benefits for other build projects.”
Scandia-Hus trialled the Actis Hybrid system a few years ago on its first, contemporary style, show home, carrying out a thermal imaging exercise after completion to help determine whether to switch to using the system for future projects. The results, which showed an impressive lack of thermal bridging, convinced them that this was the best insulation for most of the homes it builds every year.
Scandia-Hus MD Derek Dawson said: “Using Actis reduced installation time by up to 30%. Previously, insulation was installed in two phases – the first in the factory and the second on site after the first fix was complete. The panels are easy to cut to exactly the right size, so they simply slot into the stud wall. Due to the use of service voids and the ease of installation, the insulation will now generally be installed in one phase on site. This also ensures that the airtightness of the building is not compromised by follow-up trades.”
The first open day is on Saturday 19th March. More at www.scandia-hus.co.uk
Mumford and Wood, an Essex based Timber Window and Door manufacturer are excited to announce their carbon neutral organisation status, possibly the first to do so in the industry.
Mumford and Wood commissioned Carbon Footprint™ in 2021 to conduct a full annual audit of the firm, business practices and travel to reduce their carbon footprint and became 100% carbon neutral from January 2022.
Dion Panting, General Manager from Mumford & Wood explains: “As a manufacturer focused on using natural timber materials, it only seems right that we are environmentally responsible. We enlisted Carbon Footprint™ to advise us on how to make changes that will make a big difference. Our sales force use only hybrid cars and we continue to employ as many local people as possible, reducing emissions from staff that commute to our offices. We also continually review the green credentials of our manufacturing machinery, and this is a huge consideration for any new purchases we make. We had already transitioned to using only LED/low energy lighting throughout our office space and want to do even more to help.”
Mumford and Wood also pledge a UK native tree for every project completed and clients can even select where they are planted. Although UK based, Mumford and Wood source the majority of their wood from overseas and so to help offset any transportation emissions have also started work with the Rimba Raya Biodiversity Reserve Project to aid deforestation issues in Indonesia in addition to a verified carbon standard reduction project in the Amazon, Brazil, offsetting around 350 tonnes of CO2 in 2021 alone.

More at www.mumfordwood.com
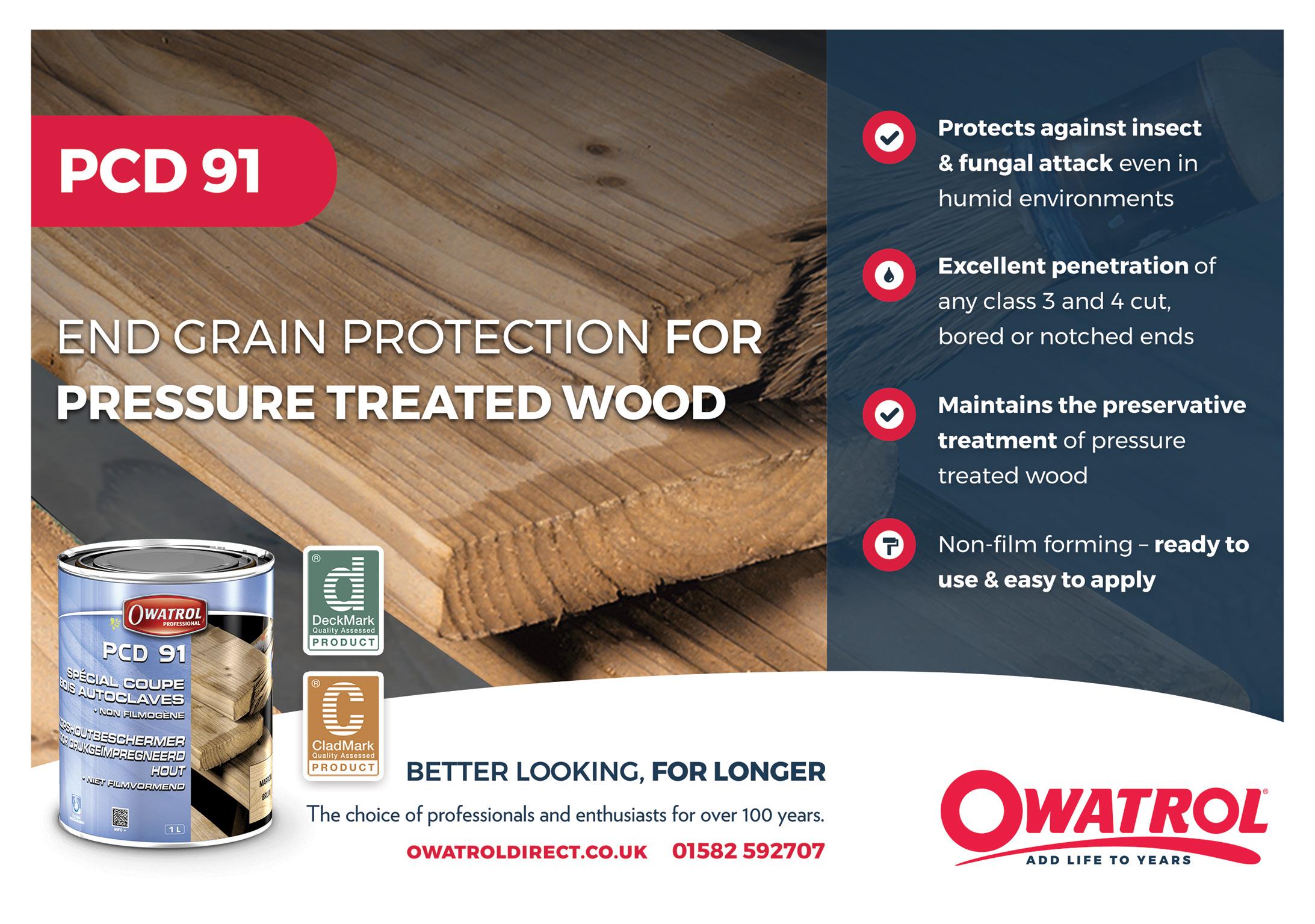
New OSB/3 Panel from MEDITE SMARTPLY
West Fraser launches new competition and ‘Architects’ web resource
MEDITE SMARTPLY has launched SMARTPLY SURE STEP – the brand new tongue and groove, structural OSB/3 panel with improved slip resistance.
This innovative, lightweight panel for flooring and roof decking, boasts improved performance during the construction phase of projects. Its unique, UV cured specialist coating, which is manufactured in-house at SMARTPLY, is designed to sustain the effects of the weather and construction foot traffic while reducing the slip risk even in wet conditions – this brings improved durability and slip resistance to the panel in all site conditions.
“We are delighted to introduce SMARTPLY SURE STEP to the marketplace as part of our specialist SMARTPLY range,” comments Rebecca Goldsmith, Product Marketing Executive. “We are constantly thinking of new ways our products can benefit the construction industry and our customers. One of the things our customers and end users have shown great interest in is a protected OSB panel that would provide some weather resistance. SMARTPLY SURE STEP is an innovative, high-performance panel that provides improved durability and has a low slip risk, which supports a safer future for timber buildings.”
SMARTPLY SURE STEP is manufactured in accordance with EN 300 and is a load bearing panel for use in humid conditions. It can withstand exposure to the weather for up to 42 days without degradation. It is ideal for applications such as flooring or roof decking, or where improved durability, temporary protection, reduced edge swelling and surface degradation is required on projects. This groundbreaking panel is available in large sizes and its distinctive tongue and groove edges allow the panels to easily slide into place. In addition, SMARTPLY SURE STEP can be used in numerous sectors such as modular, steel frame and timber construction, offsite manufacturing and temporary decking – making it the ideal panel for use in all construction projects. The panel has been tested by third party accredited labs where the panels achieved low slip potential in dry and wet conditions.
Like the rest of the SMARTPLY OSB range, SMARTPLY SURE STEP is manufactured using advanced resin technology that results in a high performance, no added formaldehyde panel. This allows specifying architects, fabricators and contractors to help create safer, healthier environments. In addition, it is FSC and CE-certified, maintaining MEDITE SMARTPLY’s stance on creating environmentally conscious products that add value throughout the supply chain.
More at www.mdfosb.com/products/smartply-sure-step
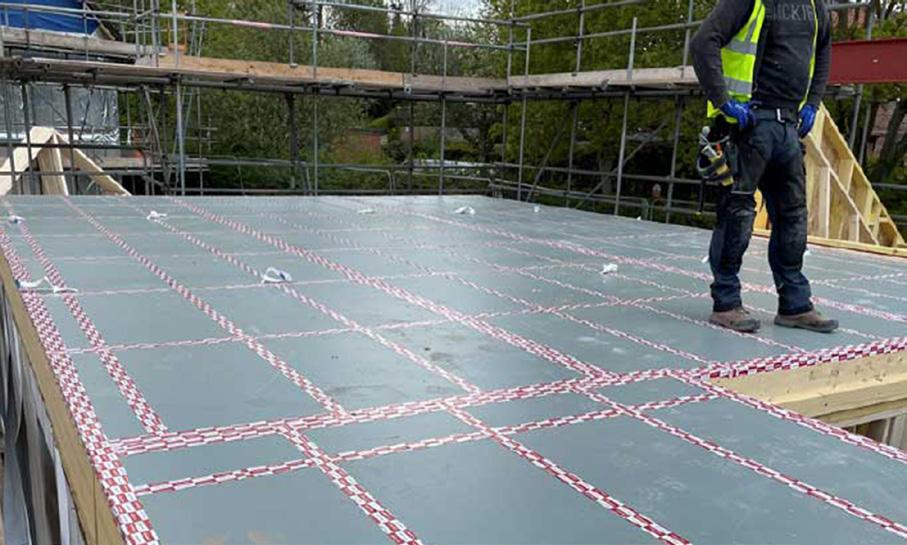
For the past six years, West Fraser (formerly Norbord), has partnered with RIBA Journal to hold an annual competition that challenges architects to use the industry’s most popular OSB brand, SterlingOSB Zero. With a different brief each year, the competition has been hotly contested by some of the industry’s most creative architectural practices, all vying to win the top prize of £2,500.
The interest from architects in West Fraser products, and the company’s environmental credentials, has led to the development of a specific architect hub. The new page details the competition as well as providing tailored information such as CPDs, downloadable product datasheets and BIM objects. The architect can also order product samples.
As one of the world’s leading manufacturers of engineered wood-based panel products, West Fraser’s OSB, particleboard and MDF products are used extensively by architects. Crucially, all West Fraser’s engineered wood panels have been certified as being net carbon negative which means that they lock up more carbon in the products than is emitted making them, helping the UK construction sector comply with net zero targets. The company is also committed to sourcing all timber from responsibly managed forests, and the European manufacturing facilities manufacture products that are certified to FSC standards. The 2021 challenge, named “Off Grid 2030”, saw RIBAJ asking entrants to design a family home of no more than 200m² GIA that adheres to the RIBA’s 2030 Climate Challenge principles. SterlingOSB Zero was to form the mainstay of the material’s palette, and designs had to look at the board’s capabilities, limitations and intrinsic properties. The home could accommodate either single or extended families in urban or rural contexts while attempting to meet the demands of the 2030 Climate Challenge, such as minimal operational energy use and water consumption, non-reliance on fossil fuels, limited waste, and offset residual carbon emissions. The 2021 winner was Kevin Sulca’s Ventanilla House – a modular solution to the unique challenges of living in Lima, Peru.
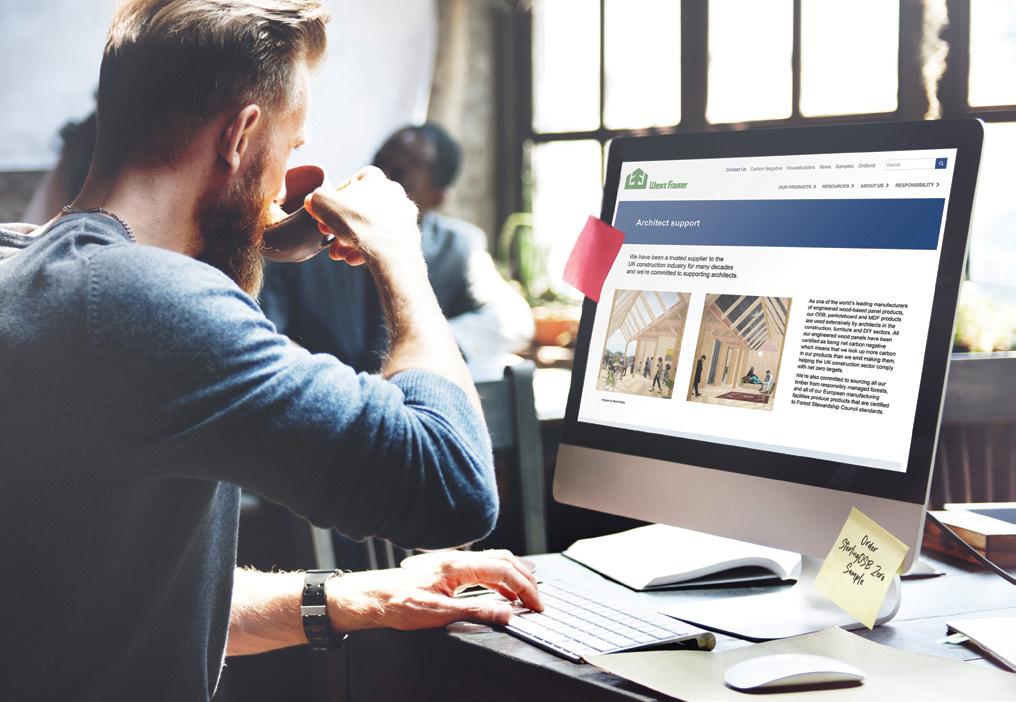
FOR TIMBER THAT KEEPS OUR FORESTS STRONG, CHOOSE FSC®

Our forests give us many things, including a huge variety of timber and timber products. FSC helps look after forests and the people and wildlife who call them home. So you can use timber, panels and other forest products while keeping our forests full of life.
https://uk.fsc.org
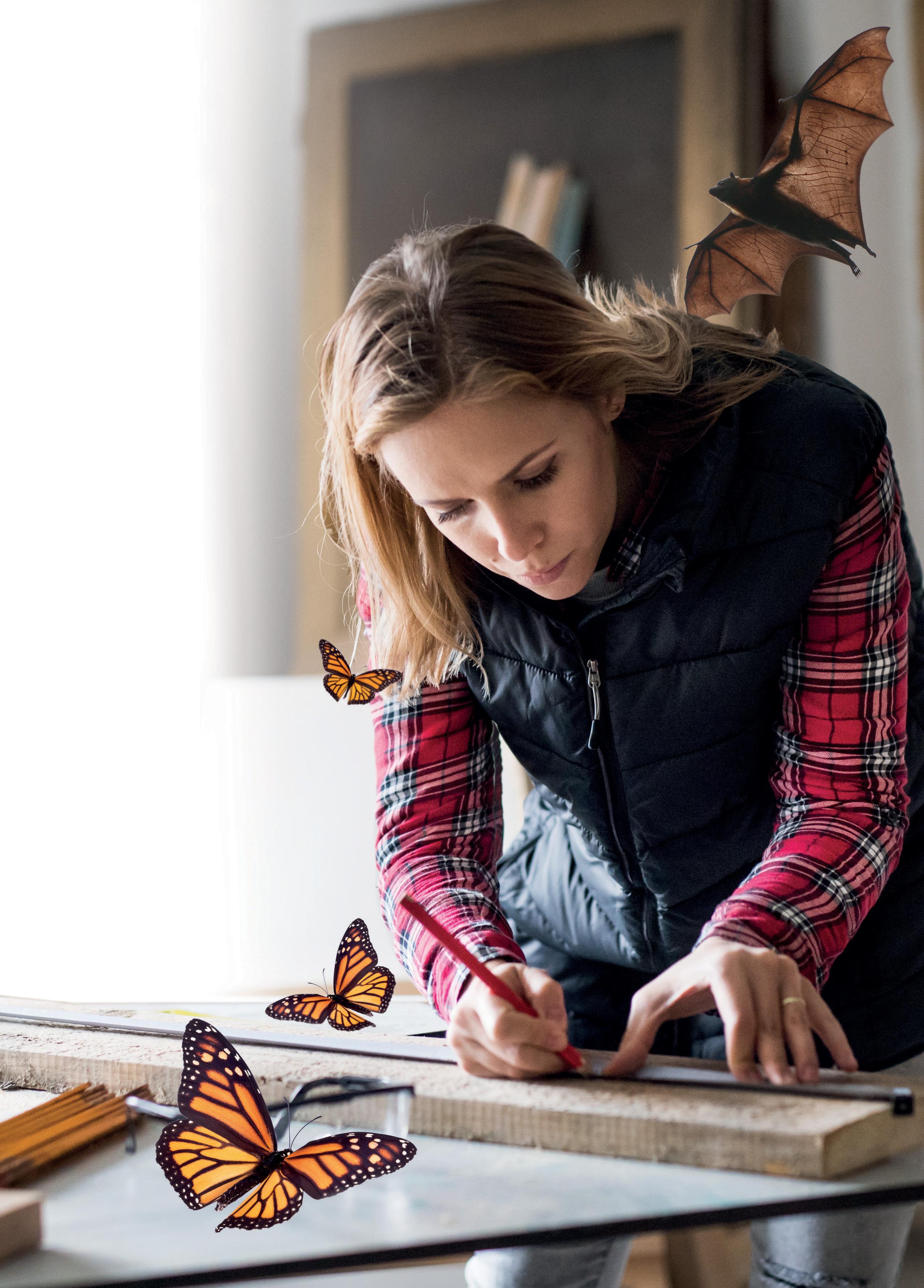
Premier Forest Group eyeing significant growth in 2022
Newport-based Premier Forest Group is predicting further significant rises in both turnover and profit as it continues to successfully navigate the global supply issues in the timber industry, caused by the pandemic. With the end of their financial year in April, Premier Forest Group is confidently forecasting that its annual turnover in the UK will have increased by 35% to circa £120 million, and that profits will have jumped from £8.8 million to over £20 million a growth of 130% since last year.
This is in part thanks to the sale of Premier’s Irish timber group in the summer of 2021. Brooks Timber, Premier’s biggest company in Ireland, was rescued from the verge of bankruptcy by the Premier Forest Group nine years ago, and was successfully reengineered into a highly profitable operation, rising to become the second largest builder’s merchant group in the Republic of Ireland. The sale freed up significant capital for Premier Forest Group, allowing the directors to further increase investment in its core UK business, Premier Forest Products.
Premier’s plans for 2022 are very much focused on further significant expansion. The board of directors is already considering several potential acquisitions that would be a good fit for the existing organisation. Terry Edgell (pictured), founder and CEO said: “The sale of our Irish group, which included Brooks Timber and Building Supplies, Dublin Plywood and Veneer and Premier Forest ROI ltd, was done as part of our wider strategic planning. If we hadn’t of sold our Irish assets our group turnover for the current year would have been approaching £220 million, our goal now is to replace this lost turnover as quickly as possible through a series of small, strategic acquisitions and with strong under lying organic growth.
“We are hoping to close an early acquisition at the start of the year, if we do it will result in a further £30 million growth in turnover for the next financial year, supplemented by the 15-20% forecasted organic growth. I’m optimistic for 2022 and, based on what we’ve seen in the last quarter, I believe the market is looking robust for the new year. The pipeline is stronger than we have ever seen, with stocks as high as they’ve been, which is no small feat given the supply chain challenges we have faced over the last 12 months.
“The past two years have demonstrated just how resilient our sector can be and with pent up demand, government funded infrastructural investment and a national housing shortage, all signs point to a serious demand for timber products in the short, medium and long term. Looking ahead to 2022/23 there is going to be continued focus on climate change and the need for businesses to move towards net zero. Reducing our carbon footprint has been on our agenda for many years now and I like to think that we’re ahead of the game in terms of our environmental impact, but there is always more that we can do, and we will be continuing to invest in green technology next year and beyond.”
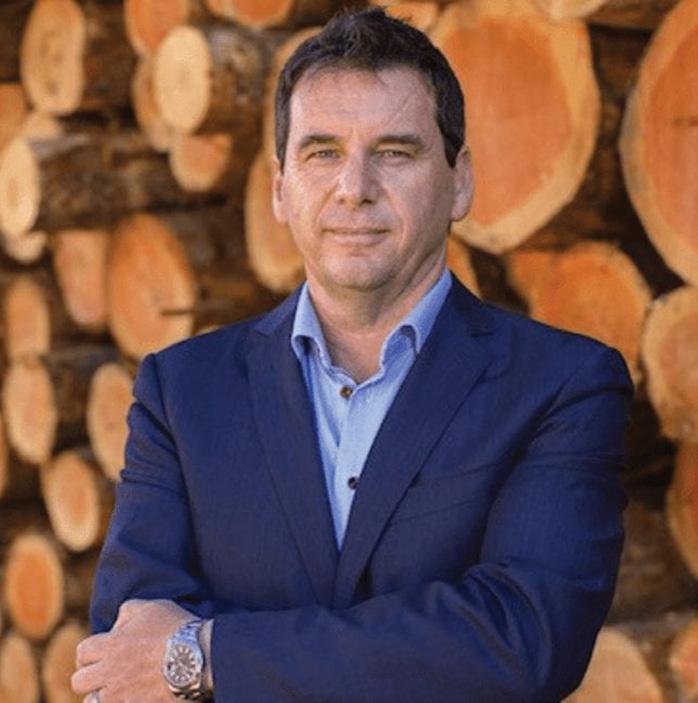
More at www.premierforest.co.uk
James Jones moves into Australian CLT
James Jones & Sons Ltd has announced that it has acquired just under 60% of the shares in Mayflower Enterprises Pty Ltd in Australia, the holding company of Hyne Timber and XLam. The transaction was approved by the Mayflower Enterprises shareholders and by the Australian Treasury’s Foreign Investment Review Board. Mayflower Enterprises Pty Ltd is a sixth generation, family-owned company with an annual turnover of AUD$380M in the year ending 30 June 2021.
Hyne Timber, dating back to 1882, operates two modern sawmills (Tuan, Queensland and Tumbarumba, NSW) producing circa 800,000m3 of sawn timber, employing 750 staff and enjoying a 21% market share in Australia. The mills source approximately 1.6 million tonnes of pine logs from plantations strategically located in Queensland, NSW and Victoria. Hyne Timber also operates a new glulam factory in Queensland, commissioned in 2020.
XLam (New Zealand) was the only CLT manufacturer in the southern hemisphere and was acquired in 2015. The company has since relocated to Wodonga, Victoria where Australia’s first ever CLT manufacturing plant was commissioned in 2018.
Tom Bruce-Jones, Chairman of James Jones & Sons, commented: “We first commenced discussions with the Hyne family members in late 2020, and it quickly became apparent that the two companies were very similar culturally and shared complementary values regarding service and quality and looking after their employees. The executive management team is very experienced, has been involved in the negotiations and is fully aligned with the new ownership strategy. We believe that this transaction will be an excellent addition to the James Jones & Sons Group and will provide a strong platform for further consolidation and growth in Australia and New Zealand.”
Jon Kleinschmidt, CEO of the Hyne Group, added: “This is an exciting day for Hyne Group with the partnership of two likeminded, multi-generational familyowned timber companies opening up significant growth opportunities that will deliver benefits to our customers, suppliers, our people and the communities in which we operate. Importantly, there is no overlap in the operations of the two companies because of our locations, with the Hyne Group focused on Australasia and JJSL on Europe. We can now concentrate on identifying and developing growth opportunities in our region and beyond, through organic growth and acquisition, and through a cross fertilisation of ideas.”
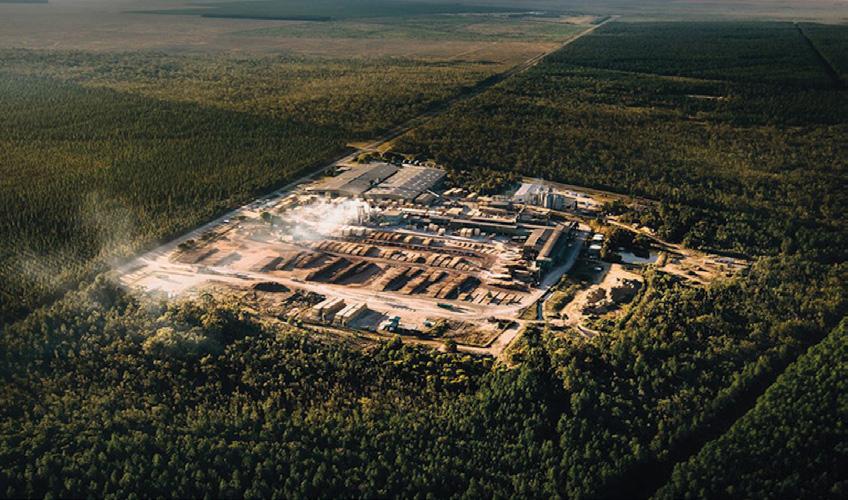
Big wins for Lathams Finish Line cladding collection
The Finish Line Collection, an exclusive cladding range launched by James Latham in 2020, has been recognised in two prominent industry awards for its development, design and performance. Judges of the British Woodworking Federation (BWF) Awards 2021 gave it the top spot in both the Process Efficiency category and Product Design in Wood category.
The former recognised the timber and materials supplier for “innovative and collaborative product development” with the Lathams team bringing Accoya Timber, timber engineering company Dresser Mouldings and Canadian coating specialist Sansin together to develop the range. The design category “recognises excellence in technical innovation, design and application in joinery product manufacture.” Judges said that they selected Finish Line thanks to its performance, quality factory finish and range of options available.
Richard Mosson, Group Cladding Technical Sales Manager at Lathams, said: “Our ambition was to bring together the best of modified wood, timber engineering and surface protection to create a best-in-class cladding product that would be long-lasting, easy to install and available in a range of contemporary options. To be recognised by our peers for our efforts is highly rewarding. It has also been fantastic to see the ways in which our customers have used it over the last twelve months. It is heavily resistant to peeling, fading and cracking, which reduces the need for maintenance and makes it appropriate for a broad range of climates and locations; we’ve seen some amazing projects throughout the UK and Europe showing it off to the best of its ability.” The Accoya provides a strong foundation for the Finish Line Collection. With a warranty of up to 50 years when used above the ground, it is a natural fit for cladding. It is well known for its durability due to the natural modification process (acetylation) and its performance rivals hardwoods. The manufacturing process sees the Accoya wood profiled, surface finished (either wire brushed or sanded, dependent upon specification) and coated by the team at Dresser Mouldings. This creates a key on the timber’s face, with tiny variations in texture allowing Sansin’s ultralow VOC coating to penetrate beneath the surface of the timber. The advantage is that this helps to bind it to the cells and prevents peeling and cracking. The cladding arrives on-site factory finished, front, back and ends, in a selection of 12 unique colours, effectively encapsulating the timber in a breathable envelope.
More at www.lathamtimber.co.uk
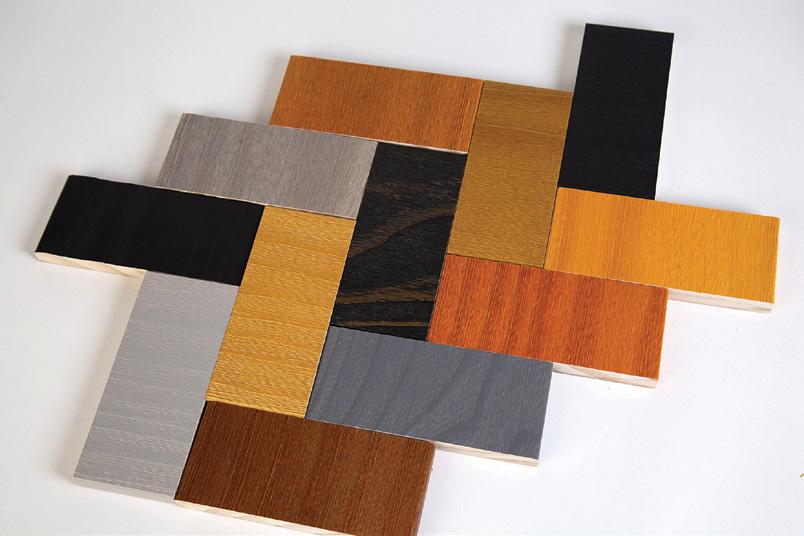
Built-in contemporary colours for pine cladding
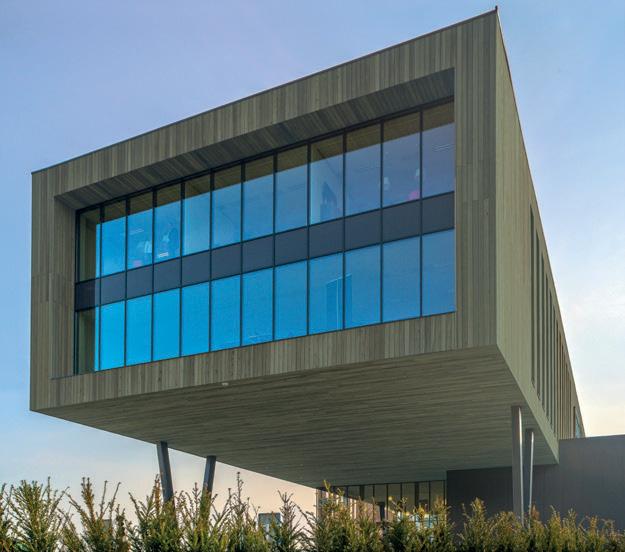


Tanalith™ Lifestyle high performance colourant blends have been developed for use with Tanalith™ wood preservative during the high-pressure vacuum process. www.trusttreatedtimber.com
The images for treated cladding shown above are illustrations only of the differences that the 3 Tanalith Lifestyle colours could bring to a cladding project. Use wood preservatives safely. Always read the label and product information before use.
More construction names sign Pallet LOOP charter
More companies have stepped up and signed The Pallet LOOP’s charter – committing to explore how a circular economy pallet scheme could benefit their business, the environment, and the UK construction industry as a whole. Marshalls, SISK, Countryside, Tobermore and the Wolseley Group are among the latest organisations to get in the LOOP and throw their support behind the team that is working to reduce the consumption of single-use pallets and switch the sector to a distribution model founded on the principles of recover, repair and reuse.
Aligned with the UK’s ambition of net zero by 2030, and due for operational roll out later this year, The Pallet LOOP’s aim is to eliminate avoidable pallet waste in the construction by incentivising pallet returns via a cost-effective, easy-to-use, deposit-based system. Estimates suggest that up to 10% of the construction waste stream is currently made up of pallets, which is costly from both a financial and an environmental perspective.
Commenting on Marshalls’ reasons for signing The Pallet LOOP charter, John Davies, sustainability improvement director at Marshalls PLC, said: “As well as focusing on achieving net zero by 2030, we’re always looking at ways to reduce our waste and recycle [and reuse] more, and a circular approach to our pallet use is something we’re very interested in exploring.”
Sarah-Jane Davies, sustainability manager for UK & Group Civils at John Sisk & Son Ltd, said: “The Pallet LOOP supports our strategic objective to successfully embed circular economy principles into our operations by 2023, as part of our 2030 Sustainability Roadmap. At Sisk we fully endorse this circular economy model to encourage the reuse of pallets in the construction sector, moving away from the single use discard routine which has previously been adopted.”
Nick Coad, head of ESG at Wolseley, said: “Wolseley is working on circular economy projects with some of our key suppliers. Pallet LOOP complements this by addressing the packaging element as we look to remove avoidable pallet waste.”
Phil Dent, CEO at The Pallet LOOP, said: “With sustainability now top of the agenda for most companies across the construction industry, the launch of The Pallet LOOP is incredibly timely – and we’ve been having some very productive conversations. The last year has seen a tangible shift in the way we all think about the environment. Businesses and consumers now recognise what needs to be done to get climate change under control – and realise that it can’t happen in isolation. That theme leaps out from the conversations we’ve been having.”
“As with safety, there is a common consensus that we can’t compete on sustainability and that the solution lies in working together to drive change. It’s an exciting time for the team at The Pallet LOOP and I’d like to thank everyone that’s stepped forward to embrace the idea of a circular economy pallet solution. As we move towards the roll out of our green pallets later this year, we look forward to continuing our work with all of our signatories, wider industry stakeholders and trade associations.”
Every year an estimated 18 million pallets are manufactured for the UK construction industry, with less than 10% currently reused. The Pallet LOOP is on a mission to change this. Delivering a more sustainable pallet distribution model, which is greener and leaner, the scheme is aligned with environmental targets set for the sector by UK Government, and the growing desire and need for businesses to adopt circular economy practices that are more environmentally friendly.
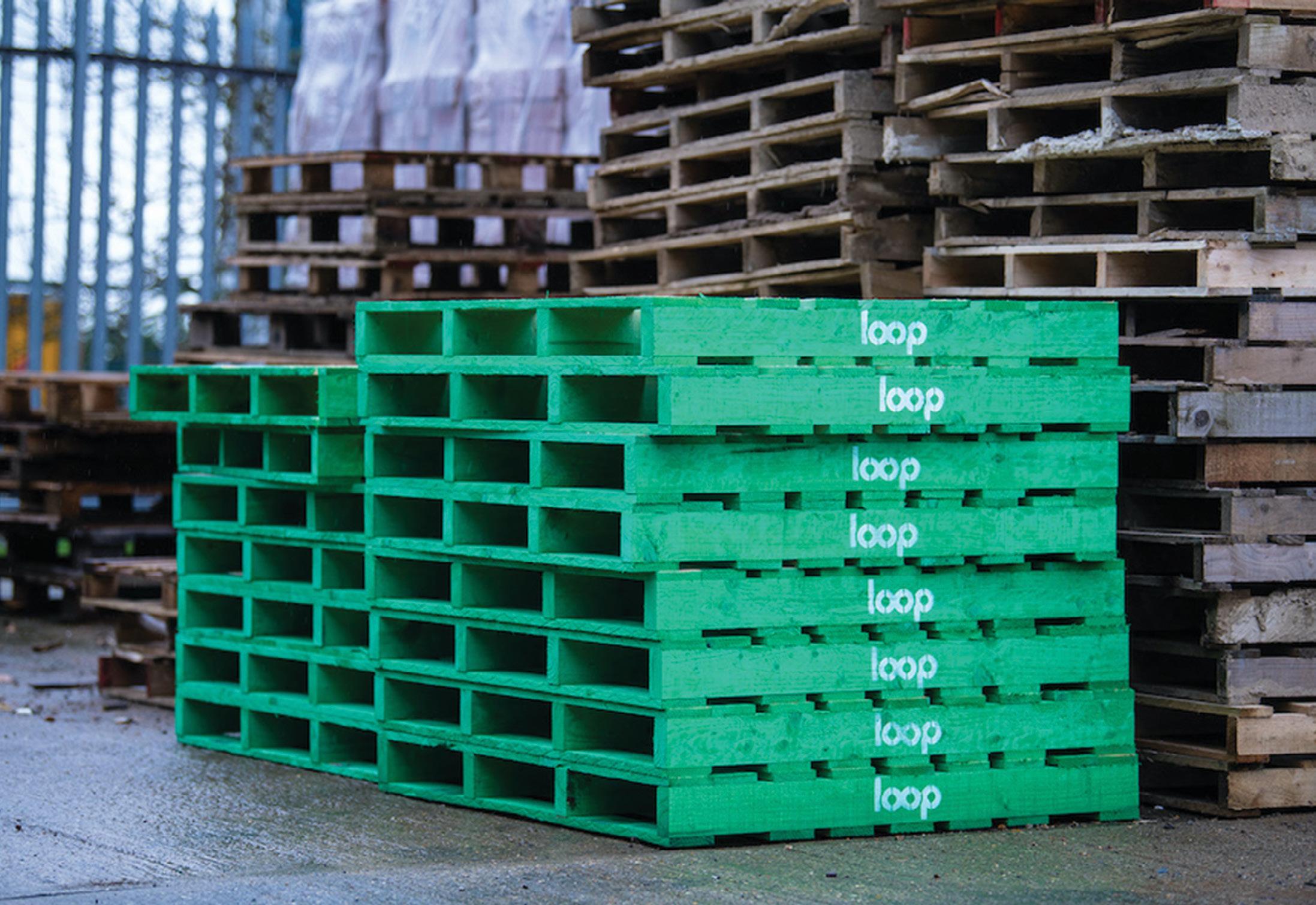
Creativity isn’t just in the mind. It’s in the connections.

Innovation is about forming new connections to inspire fresh thinking. So we’re uniting our industry, bringing together experts to share ideas and accelerate change. It’s how we develop cutting-edge products and services, like IRO Timber and CarbonStore. And it’s how we can create future growth that’s both profitable and sustainable.