
10 minute read
SIPs Made in Britain Supports Dutch Construction
Sips Supply BV in Holland works very closely with Hemsec, whose panels are all manufactured in Britain. Sips Supply has run 200 SIPs projects since 2015 and currently has a new, major programme in the pipeline, as company director Arthur Tromp explains.
Arthur Tromp is an engineer with 30 years’ experience working in the Dutch construction industry; his specialist knowledge and expertise is in using timber frames for housing. In 2011, he first came across SIPs, which was a real epiphany. .
Arthur was impressed by how much thinner, stronger and easier to use SIPs are, when compared to conventional timber frame. By using SIPs manufactured offsite, the construction of new homes on site is much quicker and more cost effective – as well as being more thermally efficient than houses constructed in a traditional way. This gave Arthur the idea to set up his own company: Sips Supply BV to serve the Dutch and European markets, which currently have an urgent need for new, energy-efficient homes.
Like many countries across Europe, including the UK, the Netherlands has a pressing need for new housing, and consequently it is an important social and political issue. House price rises are outpacing other countries within the EU and last year rose by 15%. Experts estimate that Holland has around 330,000 fewer houses than it requires and needs to build one million more over the next 10 years.
The Dutch housing market is conservative and traditional, with up to 70% using concrete or other materials. The market for timber frame is large, though, with around a 30% share. Within that, come SIPs and although their market is not currently large, demand is growing.
During the height of the Covid-19 crisis, many people used their extra time to research different and more sustainable solutions; higher quality buildings which are better insulated and highly thermally efficient. The recent surge in global energy prices will undoubtedly accelerate this trend. SIPs fit these needs perfectly.
Collaboration is an essential ingredient
Seeking the right partners was a key stage as Arthur established SIPs Supply BV. Growing the market is important; but it is equally important in Arthur’s view to build the SIPs market slowly, focusing attention on maintaining exacting standards to minimise the risk of poor delivery. Whilst researching the SIPs market, Arthur came across Hemsec, based in the north of England.
Impressed by the information provided by the Hemsec team during his initial conversations, Arthur travelled across to the UK from his
ADOPT AXIL 3000 P+
WOOD TREATMENT TO ENSURE YOUR CONSTRUCTIONAL TIMBER LONGEVITY
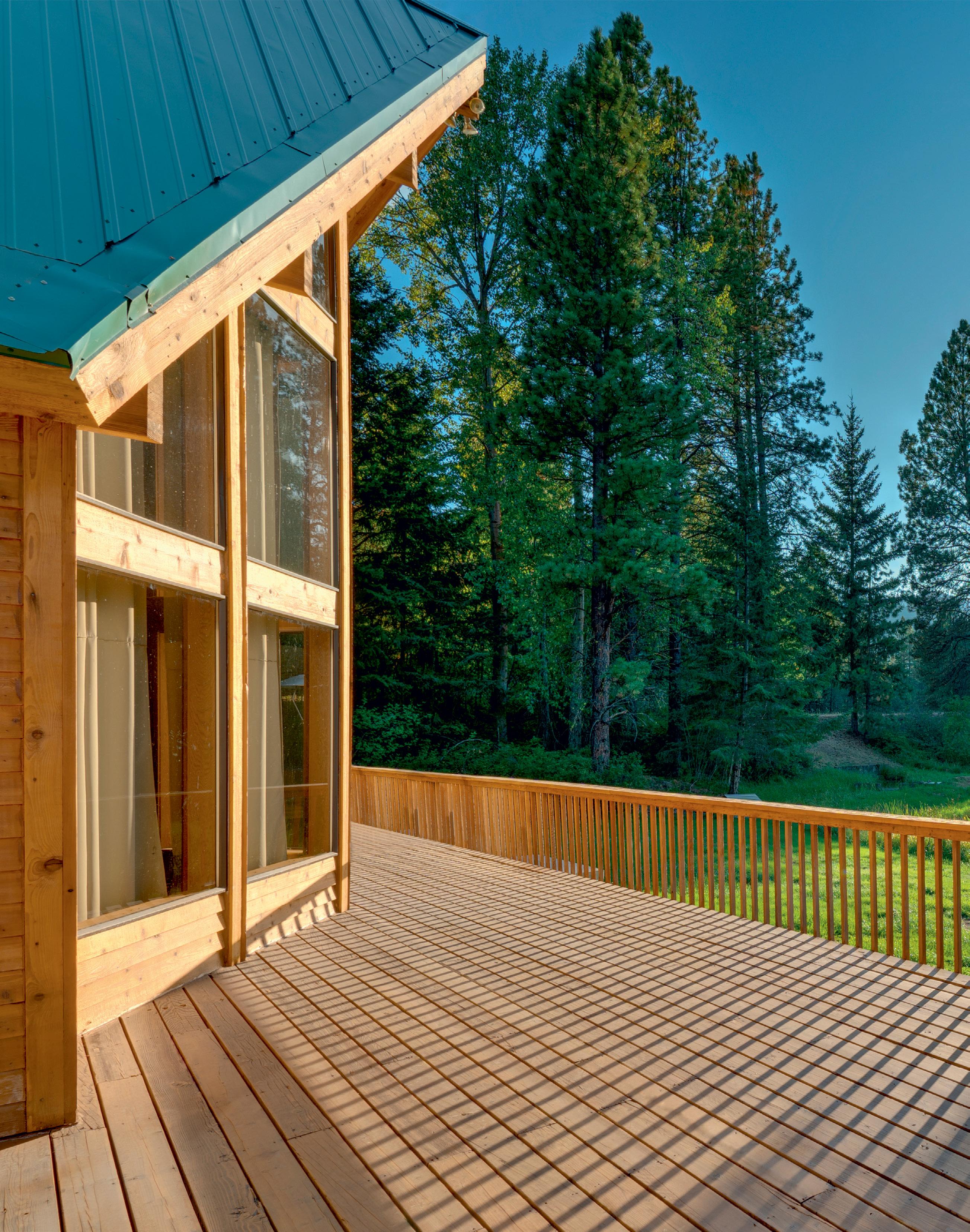
Preserve wood natural state Bio-Based wood preservative solution Up to class 3.2 autoclave treatment BPR Approval Wide range colours available
Use biocides safely. Always read the labels and product information before use.
home in Friesland to visit the Hemsec factory and learn more about the production facilities. It was important for him to assess for himself the quality of Hemsec’s SIPs.
Arthur was impressed. Importantly, Hemsec’s SIPs were of a better quality than panels fabricated closer to home in Europe. There were other critical factors too. Hemsec panels are CE and BBA Certified products, extensively evaluated for structural, acoustic and thermal properties, including fire resistance. In addition, the OSB/3 used in Hemsec SIPs is PEFC-certified, meaning that the timber is from sustainable forests – this is a requirement in the Dutch market.
The Dutch SIPs supply chain
Since 2016, Sips Supply has worked closely with Hemsec, importing the panels from across the North Sea. The company works with four processors in Holland – building companies who deliver to the end user - and is gradually expanding. The SIPs supply chain is a network of partners comprising architects, engineers, drafting technicians, processors and contractors. This comprehensive approach enables Sips Supply to undertake the whole project, from the foundations to completion and everything in between.
Ensuring that the build quality is the best it can be is fundamental to Arthur, with years of experience working on site, he aims to keep a careful eye on all the projects he is managing. By using this 360° approach he can help project managers to tackle issues as they arise and keep developments on track.
The benefits of using SIPs
Driven by market factors including construction materials shortages, demands for high insulation values and Covid-19 encouraging working from home and therefore requiring home extensions, more and more are considering SIPs. Professionals like the cost-effectiveness of SIPs, the speed of build, its safety record, durability, flexibility, energy-efficiency and the ability to improve the overall build quality. Arthur finds that many professionals such as carpenters – especially those working for smaller companies – love working with SIPs because it’s easier; everything is numbered precisely so that they ‘build it like a large Lego box’, and they are often impressed with what is achievable in one day.
Fitting a dormer window is another example. Dormers give extra roof space and the opportunity for extra rooms; they are particularly popular in today’s world, where people are increasingly working from home. In a timber frame house, it is quite complicated to fit a dormer window, however, with SIPs, the installation into the panel is easy. Arthur is a great exponent of the benefits of Posi-Joists: engineered joists that combine the lightness of timber with the strength of Posi-Strut steel web. This combination between Posi-Joists and SIPs is principally beneficial for providing extra space for utilities, such as thermal heat pump systems, electrics and water, which lay on top of the SIPs. This facilitates easy access for the installation and maintenance of the services in a floor zone, providing great space utilisation and structural qualities, as well as adding strength and stability.
Last year Arthur was approached by a Dutch development company within his network. The young leadership team discussed the potential for using SIPs on a 2200sq m apartment renovation project in Rotterdam. Inspired by the opportunity offered with SIPs, they agreed to proceed using the project as a pilot, with the potential for more and larger projects in the future.
The entire concrete structure is to be clad within a SIPs shell. The building design and materials ensure that the heat generated from the summer temperatures keeps the apartments suitably cool, whilst retaining the warmth for the colder winter months. The project is scheduled for completion in the spring of 2022.
More at www.hemsec.com
Stora Enso invests in automated CLT coating line
Stora Enso has invested EUR 9 million in an automated CLT coating line at the Ybbs sawmill in Austria. The investment will further strengthen Stora Enso’s position as a leading global provider of engineered wood products for low carbon, sustainable buildings.
In the construction industry, there is labor shortage and a pressure to shorten the construction time on-site. The investment enables industrially pre-applied CLT coatings on the CLT walls and floors produced at Stora Enso’s Ybbs site. The automated coating solution results in shorter construction times and higher wood protection.
“With this new automation line, we can apply high-quality water-based coating to approximately 500,000m² of CLT walls and floors per year – making us the world leader in this segment. Our customers will benefit from improved protection of CLT against moisture, sunlight, insects and fire, as well as nicely coloured visual surfaces,” says Lars Völkel, EVP Wood Products division.
Stora Enso aims to lead the development of the growing mass timber construction market. The company has a strong position in traditional wood products and develops growth through increased capacity, new building concepts, digital services, and value-added features like coatings. The automated CLT coating line will be built at the Ybbs sawmill and is expected to be finalised in the third quarter of 2023. The Ybbs sawmill is well located to serve all markets in Central Europe.
More at www.storaenso.com
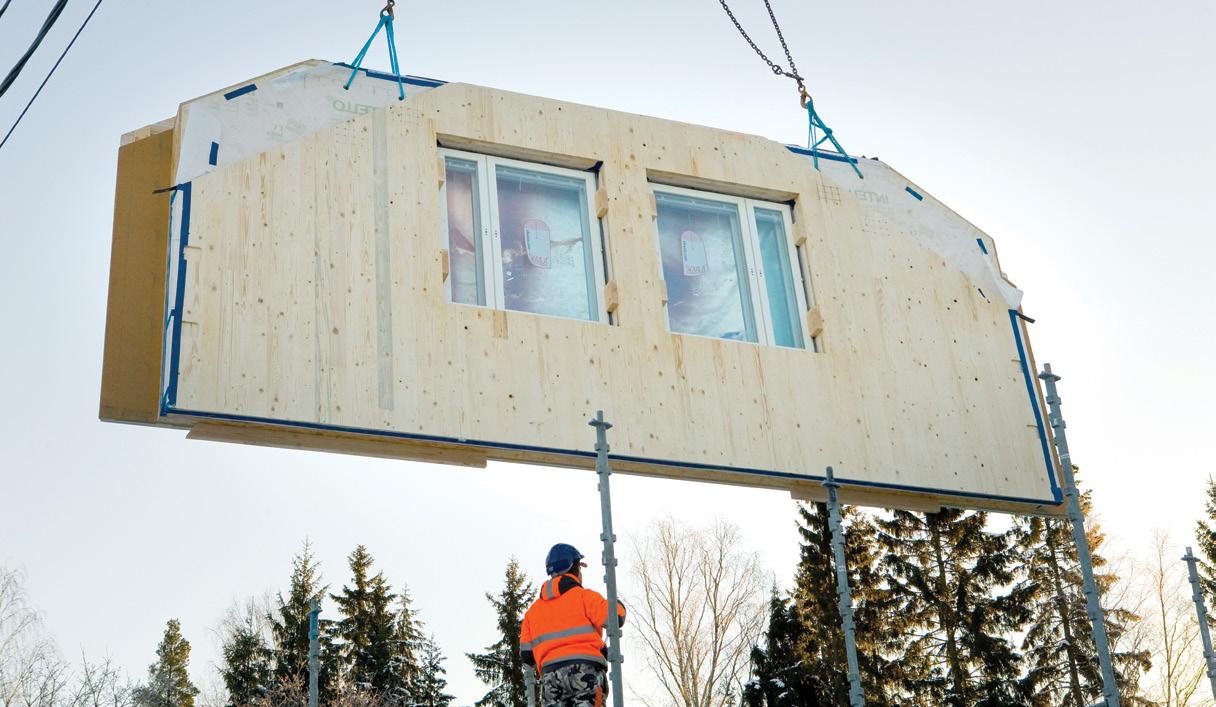
Organised by:

NEXT EDITION
FOLLOW US
@carrefourdubois #cib2022
With the support of:
INTERPROFESSION NATIONALE
Advertise with Timber Media’s Products & Services
For more information call Terry Hanlon on 01925 270093 or email terry.hanlon@timbermedia.co.uk

BIM Delivers a Grand Design
Inspired by large sculptures in the countryside and the rocky outcrops of the nearby Dartmoor moors, The Hux Shard – as seen on Channel 4’s Grand Designs – offers a striking, geometric appearance.

W
hile Tekla Structural Designer is perhaps predominantly renowned for its use with concrete and steel design, the software is also continuing to expand its capabilities for timber design. As the emphasis on sustainability and a building’s embodied carbon value continues, timber will inevitably become a more popular building material amongst clients, engineers and contractors. . Faced with a significant engineering challenge. TWP Consulting Engineers turned to Tekla Structural Designer software for help in bringing the client and architect’s dramatic vision to life. With the building’s geometric architecture inspired by Dartmoor’s wild granite tors, The Hux Shard’s exterior walls are formed of 34 shard-shaped sculptural panels, set in a jagged 70m line following the contours of the hill on which the property stands. It is the combination of these immensesized shards and the exposed rural landscape that was perhaps one of the key challenges behind the project, with TWP Consulting Engineers appointed as the structural engineers on the project.
The building design required a series of large concrete pad foundations and steel short columns, which in turn supported the gigantic timber frame’s floor structure and roof. The primary building frame consisted of 282 glulam timbers, which were bolted together with steel brackets to form a wooden skeleton reaching over seven metres into the air. The property’s exterior walls were then formed from 34 insulated timber shards, each around 600mm thick and clad in zinc, and interspersed with 46 equally complex glazed panels. As if that wasn’t enough of a challenge, the whole structure was also partially suspended, raised between 0.5 and 1.5 metres off the ground.
Speaking about the project, Nick Drew, Director at TWP said: “Perhaps the main challenge on this project was the shard-shaped panels that formed the building exterior, and which served to create the dramatic geometric impact of the overall building. Due to the intended architectural aesthetic, there was no uniformity to the panels, no parallel elements and no true-90 degrees. Each of the shards was wholly individual and unique, all at different angles to one another, and the whole property was also slightly curved on plan.
“As if those design complexities weren’t challenging enough, the shards were also incredibly large – some as tall as a two-storey house. Given the exposed and elevated hill-top location, the concern was that the shards would effectively act as wind sails, capturing a lot of wind and putting more stress into the primary structure itself. As engineers, we had to ensure that this wind loading was accounted for in the engineered design and that the shards wouldn’t place unnecessary strain and deflection on the primary structure and glazing.
“Fortunately for us, Tekla Structural Designer has an automated wind loading feature, meaning that we were able to quickly and automatically model and calculate full building wind loads. This, combined with the jagged layout of the shards and the uneven ground level, provided us with another challenge – mainly how to create clear layers in the software. It was imperative that we were able to create clear layers and gridlines, as well as ensuring that the gridlines were named correctly, as this information then referenced back to the gridline’s respective shard. Without the ability to clearly and concisely complete and model this in the software, it would have presented some serious difficulties and confusion that would have affected the whole project delivery.
“For us, we are seeing more and more timber being used on construction projects, such as this, as people become more focused on the importance of sustainability. With Tekla’s portfolio of software, we are able to analyse the timber building design in Tekla Structural Designer and understand all forces and potential stresses. Then, as a result of the software’s emphasis on integration and interoperability, we are then able to export the data and timber beams directly into Tekla Tedds, saving us considerable time.”
The Hux Shard was completed in 2021 and featured on Channel 4’s Grand Designs.

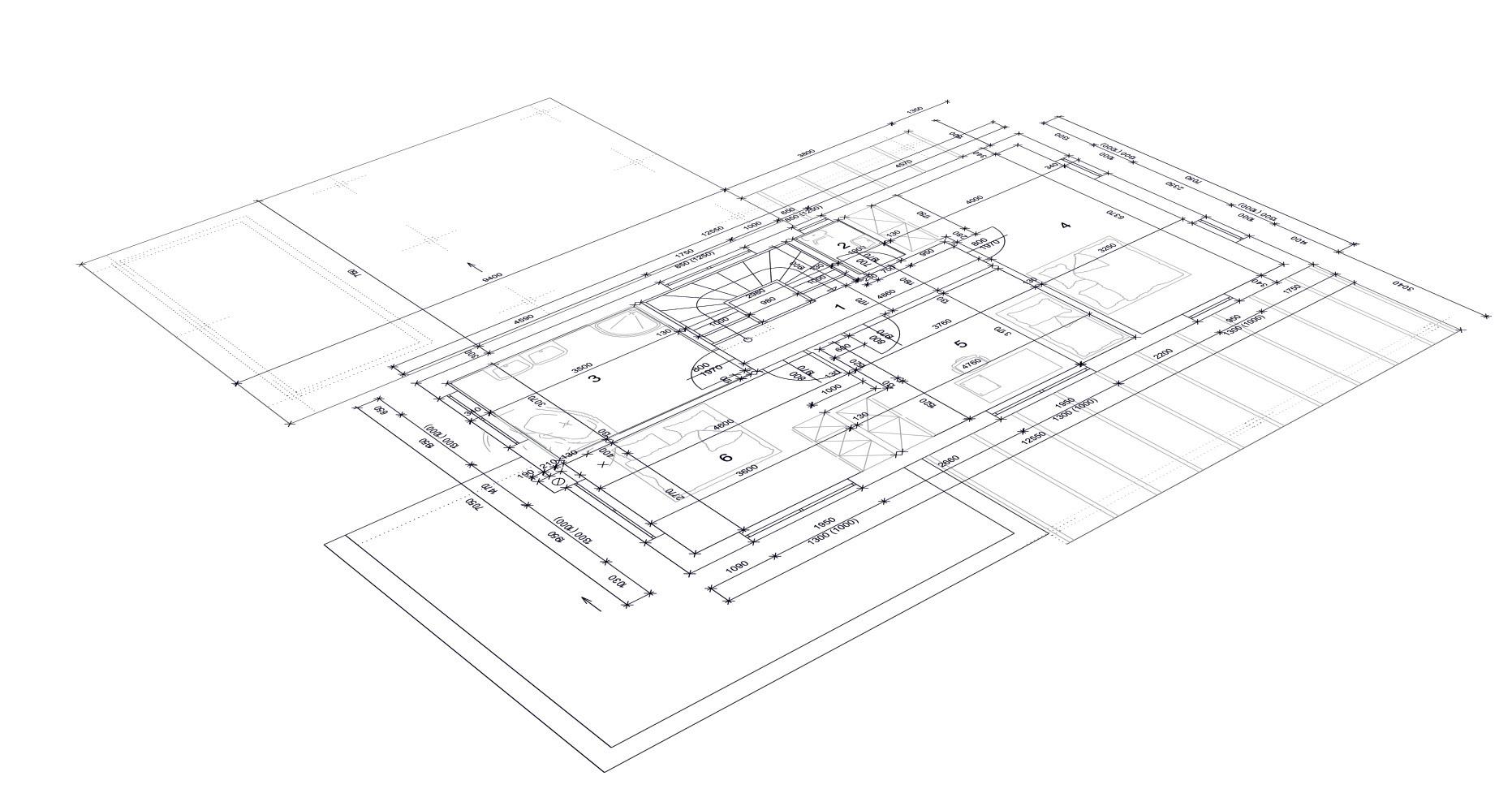
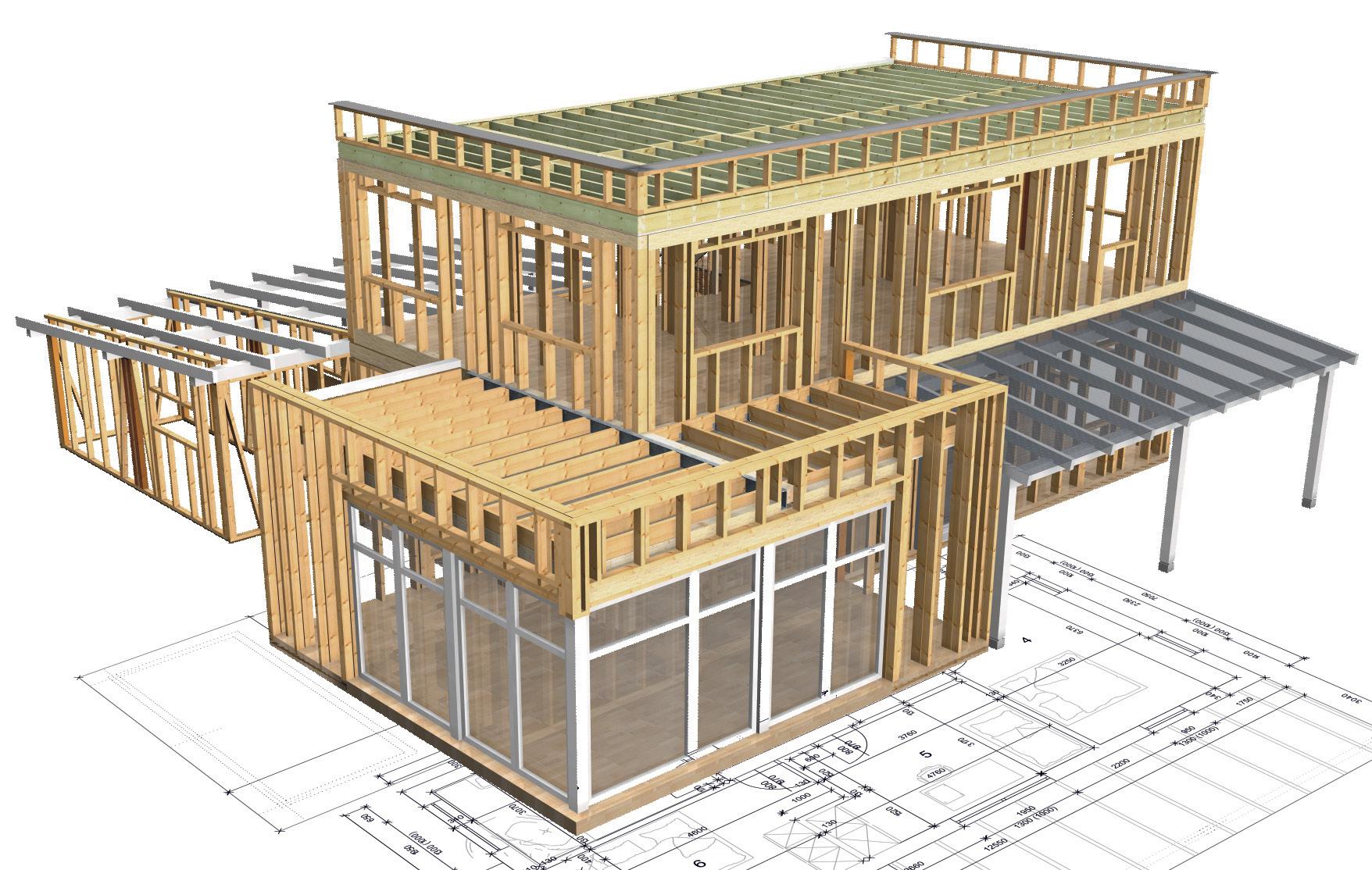

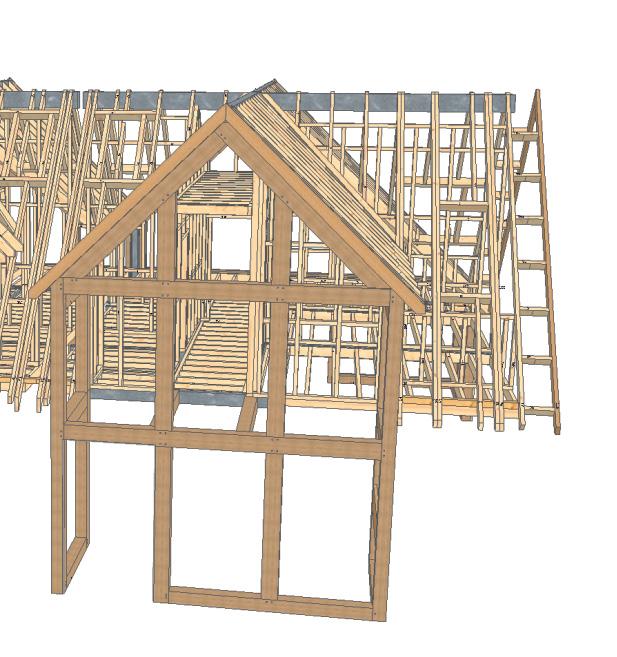