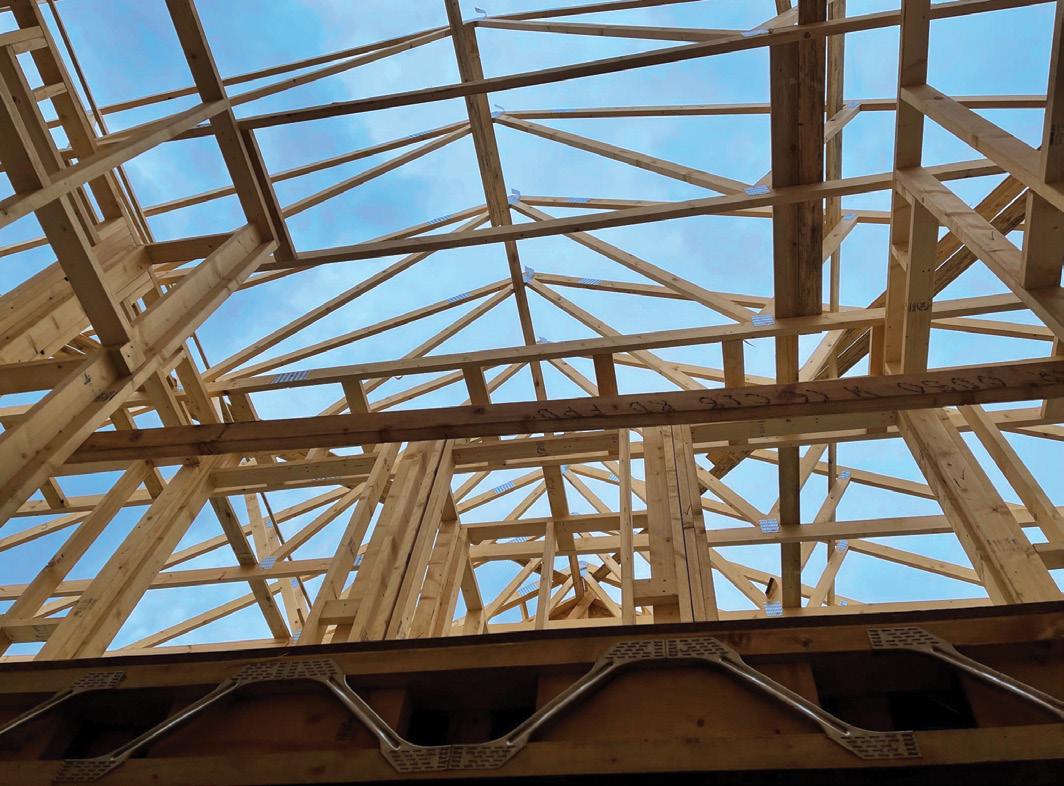
11 minute read
Lowering Carbon Levels with Timber
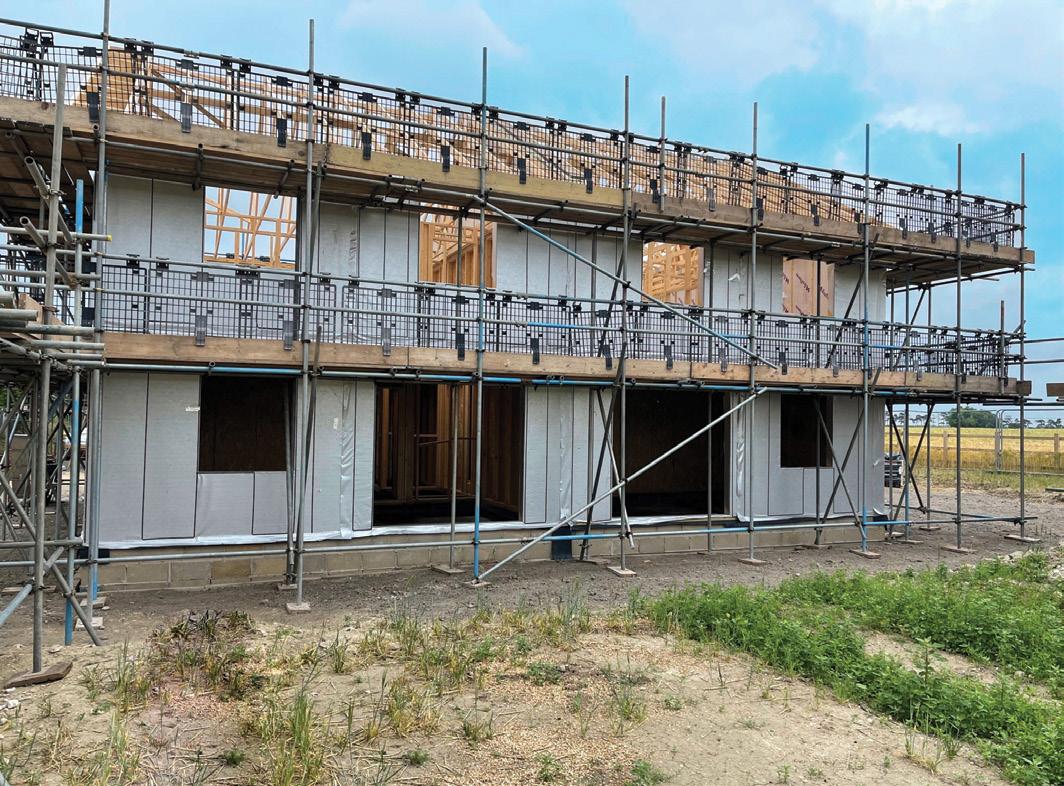
Most carbon emissions come from the building when energy is used to heat, cool and power them. But the embodied carbon emissions created during the manufacturing of building materials and the construction phases of a building is also central to sustainable construction.
The huge requirement for new dwellings in the UK alone is so significant that the government has a target of 300k homes per year to be built. (It is also being noted that having missed this number for the last few years the requirement is nearer 345k per annum now). This simply adds to the increasing pressure on the environment and the carbon production that is inevitable through this. It is therefore essential to reduce ‘upfront carbon’ emissions before a building is used. The embodied energy that is used in the production of building materials must be considered by builders and building designers if we are to hit the current and future targets of carbon reduction that are being set out.
Embodied carbon is unchangeable once a product is manufactured thus the designer needs to be specifying low carbon products and design solutions. With increased building performance around the corner in the form of tougher performance standards being introduced in the next change to building regulations there has never been a better time to swap to timber.
Unlike many modern methods of construction (MMC) timber frame is one of the oldest methods of construction known to mankind. It is stunningly simple in concept, widely used and accepted whilst rapidly increasing in popularity.
Environmentally, the advantages of building with timber are enormous. Timber is the stand-out performer, possessing the lowest embodied carbon for any building material. Managed forests that are properly maintained provide us with the only truly renewable building resource.
The primary goal of a sustainable building is to reduce the industry’s impact on the environment. Houses developed using structural timber solutions can be built up to 30% faster than traditional construction methods. In addition to this with the product being manufactured offsite, there is a 90% reduction in waste. A timber frame home can reach a weathertight stage of the build much sooner than with traditional methods of construction – a crucial driver for any self-build or housing solution.
Sustainable construction aims to use renewable and recyclable materials when building new structures and reducing energy consumption and waste. Offsite designs manufactured in a controlled factory environment assure precision engineering, minimal waste and dramatically reduce onsite movement. This in turn means reduced carbon emissions and a safer working site. The process also helps to eliminate many of the onsite checking procedures that traditional brick and block construction require.
One point of contact for the design manufacture and installation of a complete superstructure must be an advantage to the builder be it a one of or multi-unit project. Timber frame is the major solution within the offsite home building market. Other panelised systems such as cross laminated timber (CLT) and structural insulated panels (SIPs) will also help deliver carbon capture and help plug the skills gap that is facing traditional construction. Both premium systems with their own unique advantages add to the options available in help to embody carbon! Timber offers exceptional thermal performance, greatly reducing household emissions – a positive for both the environment and the pocket of the homeowner. Aside from its environmentally beneficial properties, prefabricated timber frame technology could prove to be a great assistance to meeting the demand for affordable housing. This trend has already started with many projects in this sector turning to the ‘fabric first’ approach that timber systems provide. There is no better way at this current moment in time to significantly help the environment whilst delivering the number of homes required.
SBUK GROUP modern construction methods are about better products and processes that aim to improve efficiency, quality, resident satisfaction, environmental performance, and sustainability. All timber products used within our business are sourced from sustainable sources and are either PEFC or FSC-certified.
More at www.framebuilduk.co.uk www.sipbuilduk.co.uk www.sbukgroup.co.uk
Stora Enso supplies renewable wood materials to Sweden’s National Museum of Science and Technology
The construction of Wisdome Stockholm, a scientific experience arena, is now underway. The building at Sweden’s National Museum of Science and Technology in Stockholm has a pioneering design and will be a landmark object for sustainable and climate-smart construction in wood. Stora Enso is the main partner and delivers wood construction materials to Wisdome Stockholm.
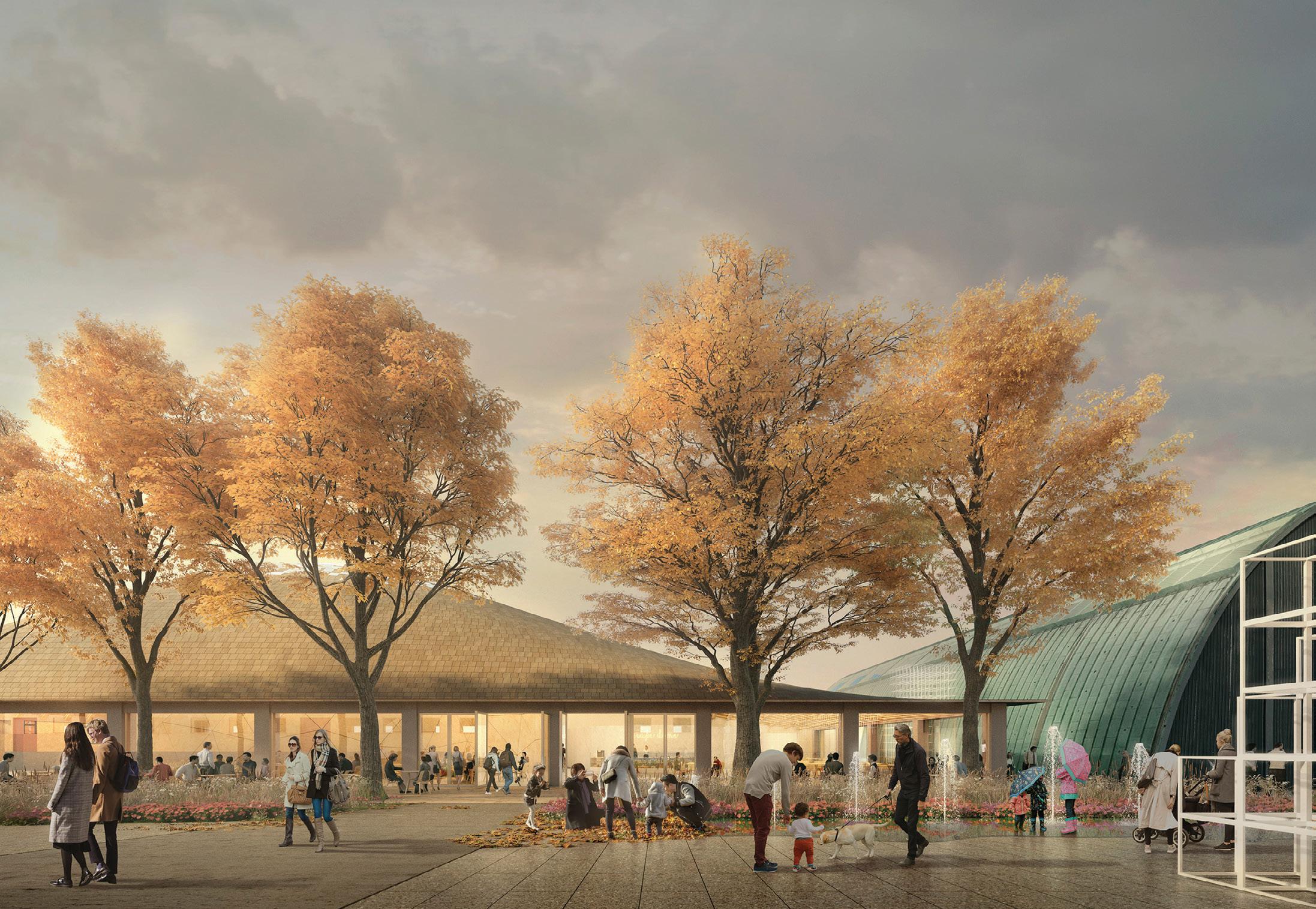
Wisdome Stockholm is a spectacular wooden building design of 1,325 square metres with a unique vaulted roof. Inside the building, there is a globe-shaped dome theatre of 21.6 metres in diameter hosting a 3D cinema with a spherical screen.
“We are a proud supplier to this ground-breaking project. Wisdome Stockholm pushes the boundaries and shows what is possible to create with wood as a climate-friendly construction material. Through unique projects like this we can strengthen our customer offering as well as our leading position within renewable construction materials,” says Per Lyrvall, Country Manager Sweden, Stora Enso.
Stora Enso supplies CLT (Cross Laminated Timber) and LVL (Laminated Veneer Lumber), which can replace traditional building materials such as steel and concrete. Several of Stora Enso’s digital solutions in wood
Key facts about Wisdome Stockholm
• Official start of construction: 2022 • Estimated opening: 2023 • Location: Sweden’s National Museum of Science and
Technology, Stockholm • Size of the building: 1,325 square metres • Dome size: 21.6 metres in diameter, 12.2 metres high • Number of seats in the dome theatre: 100
• Main partner and supplier of wood materials: Stora Enso • Architect: Elding Oscarson • Specialist Timber contractor: Blumer Lehmann • Construction contractor: Oljibe • Partners: Ericsson, Vectura, NIBE • Financiers: Wallenberg Foundations, Erling-Perssons
Foundation, Stora Foundation, Fritz Öst Foundation
construction will also be used in the project, such as the assembly app CLT 360+, the moisture sensors Wiiste and the calculation tool Calculatis.
Stora Enso is Europe’s largest supplier of wood products and has delivered wood materials to around 20,000 construction projects worldwide. In addition to being the only renewable building material, building in wood halves the construction time and reduces transport to the construction site by up to 80%. Stora Enso’s wood products come from sustainable managed forests.
The ground-breaking ceremony for Wisdome Stockholm took place on 21 February with Sweden’s Minister of Culture Jeanette Gustafsdotter together with partners in the project. The inauguration of Wisdome Stockholm is planned for 2023.
More at www.storaenso.com/en
Wisdome is a national initiative where Sweden’s five leading science centers collaborate; Malmö Museums, Universeum in Gothenburg, Curiosum in Umeå, Tekniska museet in Stockholm with Visualization Center C in Norrköping as the hub of the collaboration.
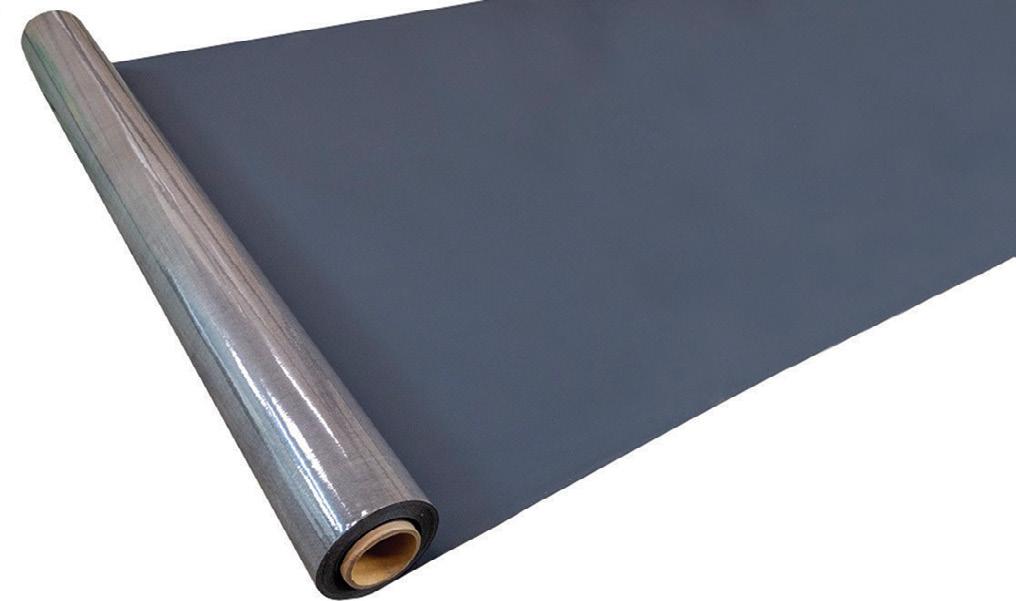
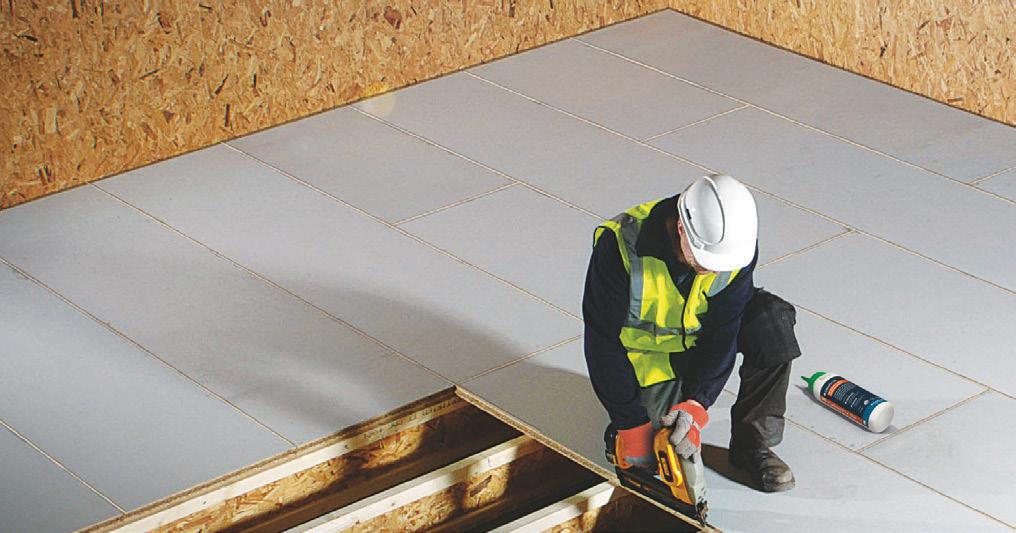
A Proctor Group launches Wraptite® UV airtightness membrane
Since its launch, the Wraptite® external airtightness membrane has been an incredible success and has been specified in a wide range of projects and applications. Now, Wraptite is being extended further with the introduction of Wraptite UV. Wraptite UV is a Class B fire rated membrane that combines the critical properties of vapour permeability and airtightness into one innovative, self-adhering product. Specifically designed for use behind open jointed cladding, Wraptite UV has exceptional water and UV resistance. In addition, the product provides a shadow gap detail behind open jointed façade systems in offsite construction, rainscreen and timber cladding systems. The inclusion of Wraptite UV prevents lateral air movement and enhances the building thermal performance. A rating of Sd 0.06m provides a high vapour permeability within a professional quality, selfadhered, airtight breathable membrane. In addition to its use behind open jointed cladding, the membrane is designed for applications that require protection against UV for extended periods. The membrane is ideal for use in the storage and transportation of volumetric modules, offsite panelised systems, and within high rise façade construction. During its application, the self-adhesive nature of Wraptite UV requires no mechanical attachment and bonds to multiple substrates for airtightness, offering ease of installation, negating the requirement for a primer, sealants, or tapes. Adhesive curing time is approximately 6hrs depending on environmental conditions.
Visit our website: www.proctorgroup.com
West Fraser’s CaberFloor provides a solution for all applications
When considering flooring products for new-build or refurbishment projects, the housebuilder and specifier can be sure that West Fraser’s CaberFloor range includes the perfect solution. Just as sound foundations are essential for any building, the right flooring system lays a good foundation for a quality flooring finish, saving problems and costs later. The West Fraser website contains a handy flowchart to help builders, specifiers and architects choose the right flooring system for every project, coupled with handy installation guides and videos https://uk.westfraser.com/resources/help-advice/installationinstructions/ for the individual CaberFloor products. Leading the field in the popularity stakes, CaberFloor P5 is the UK’s most specified moisture-resistant P5 flooring. The high-strength particleboard is ideal for domestic and most other floors and removes the need for intermediate noggins. The boards are moisture-resistant, stable, durable, easy to lay and, with a tongue and groove or square-edge profile, provide an excellent surface for subsequent floor laying operations. Some floors require more advanced solutions and, no matter the size or shape of the floor being laid, there are key questions to ask. Although not necessarily obvious, the first point to consider is whether the building’s roof will be in place. If the answer is no, the floor will need to withstand the elements. This is where CaberShieldPlus proves its worth as it is designed to allow building work to continue in all weathers. CaberShieldPlus is an advanced product that has all the inherent benefits of CaberFloor P5. In addition, it offers double-sided protection with a tough, permanent waterproof coating and is BBA approved for 60 days exposure, when laid according to manufacturer’s instructions. It is also a non-slip, safe working platform that withstands high site traffic. An alternative solution is CaberDek which is BBA approved for 42 days exposure, when installed with CaberFix according to manufacturer’s instructions. The P5 grade flooring has the advantage of a strong, waterproof and slip-resistant peelable film. It provides protection from the elements and construction mess and, when removed, leaves a clean, finished floor. The film is impact, puncture and tear-resistant to withstand high site traffic. CaberDek also provides 44dB sound reduction when used in conjunction with leading I-beam and insulation manufacturers.
For further information, call 01786 812 921 or visit Uk.westfraser.com
Combilift is a clever move for Smartroof
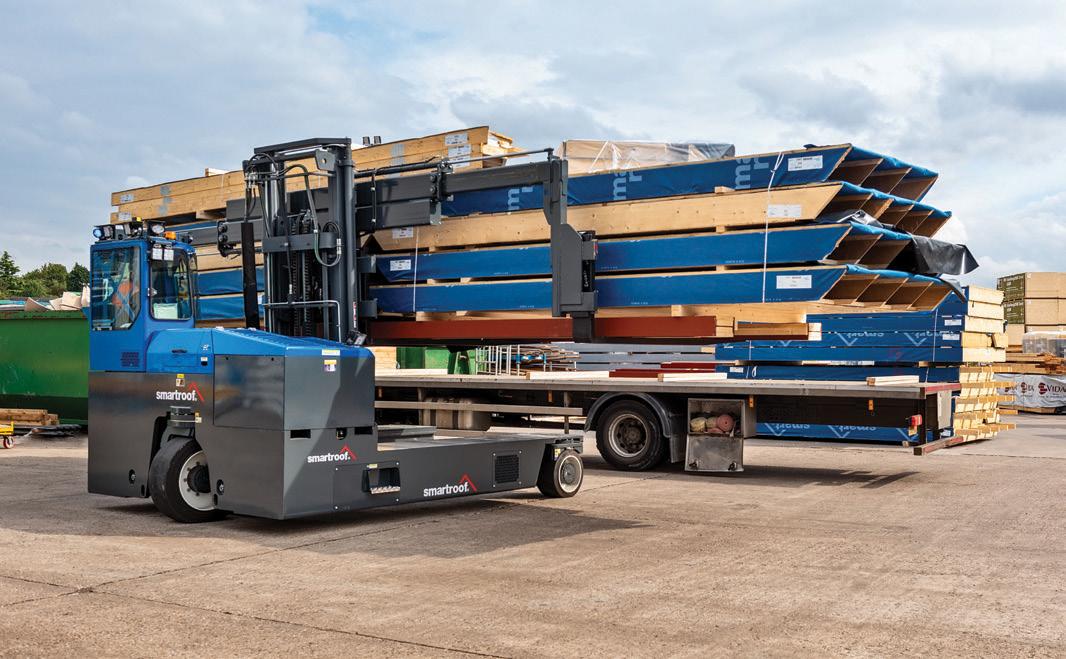

Smartroof is leading the way in developing innovative insulated room in roof panel systems that reduce overall build time, ensure consistent quality as a result of a factory controlled environment, and improve health and safety during the onsite installation process. In line with the company’s drive for sustainability it has switched from diesel to electric power for its fleet of material handling vehicles. These now include four Combilift multidirectional forklifts that have recently been delivered to the manufacturing facility in Swadlincote, Derbyshire. The company became part of The Keystone Group in 2012 and 2021 was its busiest year to date. As a consequence, there was a marked increase in the volume of materials that need to be handled inside and outside the factory. Due to the extreme size and bulk of the products, which can be up to 12m long and weigh 7t, Combilift was chosen as the preferred supplier. “We were aware of Combilift’s products, their capabilities and reliability,” said Production Director Lukasz Semen. As we are extending our production facility and yard, which will triple the size of our current footprint, we need to make sure we can handle our loads with utmost efficiency and safety.” Together with Glen May from materials handling consultants Forkway, specifications and attachments were drawn up for the two C8000E and the two CBE3000 models, which were supplied in Smartroof’s corporate livery. Although as Glen points out: “Lukasz and his team had really done their homework, and were clear on their requirements. For us at Forkway it was just a matter of firming up the various add-ons and attachments.” The C8000Es are the largest electric models that Forkway has supplied to date and are used for handling Smartroof’s most challenging loads of 10 to 12m long x 2.7m deep bundles of roof panels. With a 5.5m mast, 6m wide hydraulic spreader beam with 2.5m long forks, they can reach across the truck bed to lift a complete load in one single procedure. With the previous forklifts this necessitated multiple lifts, and what used to take 40 minutes is now complete in 10 minutes. The 3t counterbalance design CBEs offload lighter products and components and transport materials to the assembly lines. Thanks to their compact size and manoeuvrability they can move between machinery without hampering production. There are five cameras on each model, magnetically mounted so that they can easily be repositioned. Blue safety lights for each direction of travel, red zone pedestrian proximity warning lights and work lights for nightshift operation were also installed. A further safety feature is Forkway’s own SpeedZone system which reduces the trucks’ speed from 5km/h down to 3km/h when they transition from outdoor to indoor operation. “Space utilisation and speed were crucial factors and the Combilifts have been integral to keeping up with fast paced operations and gaining more work space inside,” said Lukasz. “Without their multidirectional ability we’d have at least 20% less capacity overall. They do exactly what we need and we’re very happy with the outcome.” For more information visit www.combilift.com and www. smartroof.co.uk