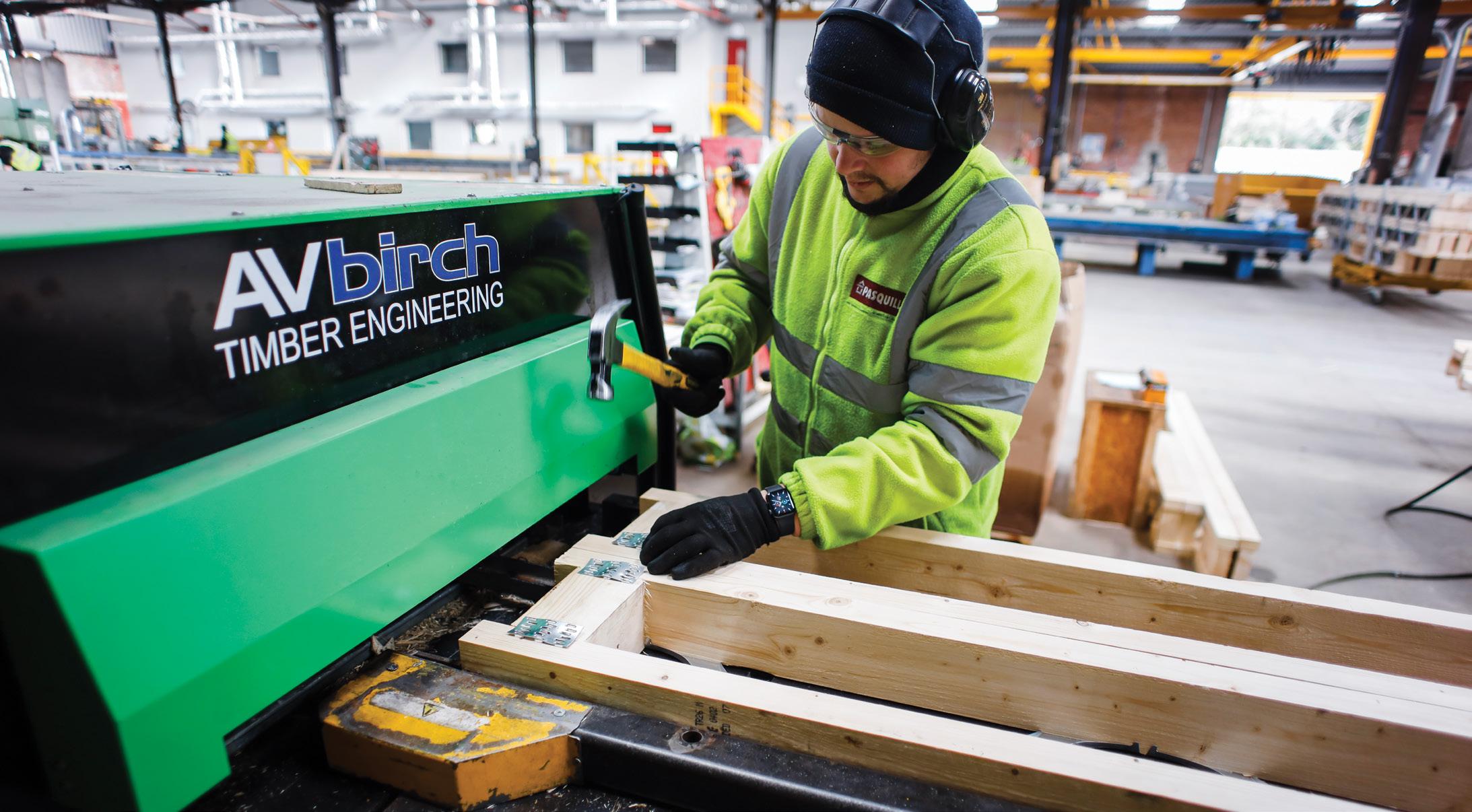
2 minute read
Pasquill reveals huge investment programme
Pasquill, one of the UK’s leading supplier of trussed rafters, has revealed further details of a multi-million-pound strategic investment programme across its UK sites. The investment includes £4.5 million spent in 2022, £3.6 million planned across 2023 and an additional £6 million to be spent in 2024. The outlay aims to upgrade facilities, improve operations, reduce waste and enhance the customer experience.
A £0.5 million machinery upgrade at Stoney Stanton forms a part of the investment and is part of the next phase at the site following the installation of the Hundegger TurboDrive in 2022. Already in place at Pasquill’s Bodmin and Redhill sites, the Hundegger will increase capacity, reliability and quality while reducing waste by 8%, contributing to a better all-around service for customers.
Meanwhile, a fifth £185k new AV Birch Uni-Roll will be installed at the Inverness site. The Uni-Roll has been designed to work in tandem with a planned glulam cutting line and cutting table, ensuring seamless integration within the facility. As a result of the Uni-Roll installation, customers can expect faster order processing, enhanced precision in material handling, and a higher standard of service. In addition to the UniRoll, Pasquill has forecast a circa £600k investment this year for a dedicated JJI Joist line at the Stoney Stanton site. This investment will follow the Uni-roll installation and help Pasquill enhance its production capabilities and meet the increasing demand for joists.
Pasquill has also invested £450k in four electric Combilift forklift trucks at its Redhill site. These versatile, multi-directional forklifts are designed to improve material handling, particularly in tight spaces, and contribute to the company’s commitment to sustainability by reducing carbon emissions.
Gabriel Prior, operations and continuous improvement director at Saint-Gobain Off-Site Solutions, said: “These strategic investments demonstrate Pasquill’s commitment to continuous improvement, enhancing efficiency and creating a more sustainable future for our business as we work to make the world a better home. As we invest in cutting-edge technology and better facilities, we ultimately aim to provide an even higher level of service for our customers, while prioritising the welfare of our colleagues and reducing our environmental impact.”
As a result of previous investment and subsequent growth, there was also a need for office expansions at Pasquill’s Chorley and Bodmin, costing £1.4 million and £160k respectively. Both projects place colleague welfare at the heart of the investments, with enhanced workspaces and better welfare facilities. A new meeting and training room in Bodmin has also been combined with a private area to show customers a 3D walkthrough of project designs.
Several additional enhancements have been implemented at Pasquill as part of their ongoing commitment to a safety culture ethos. These upgrades include new entryway safety goalposts, designed to protect personnel and reduce damage from forklift trucks and timber products. Machinery updates also feature improved guarding on saws, enhancing colleague safety when operating or working near these saws. Furthermore, the introduction of a vacuum lifter at the Leeds site’s Spandrel area eliminates the need for a two-person team to move boards, effectively reducing potential manual handling issues and trip hazards while achieving a 50% timesaving.
Looking to the future, the team is currently laying the groundwork for the completion of a £6 million project in 2024, this will see the business install a Randek AutoEye line at Pasquill’s Redhill site – which will be the UK’s first automated truss production line. The system streamlines the manufacturing process by visually identifying roof trusses and automatically picking, placing, positioning, and pressing nail plates. The pressing force is precisely adapted to the nail plate and timber thickness. This improves safety and productivity while at the same time ensuring a high-quality truss is produced every time.
“As we continue to innovate and enhance our facilities, we’re excited about our plans to implement the technology for automated truss machinery,” added Gabriel Prior. “This investment underscores our dedication to staying at the forefront of industry advancements and demonstrates our commitment to providing exceptional services to our customers. By embracing the future, we’re confident that Pasquill will remain the go-to supplier of trussed rafters in the UK market.”
More at www.pasquill.co.uk