Issue 11; 2024 All Markets

In this issue:
TITANIUM EUROPE 2024 Executive Summary
Observations on Near-Term Titanium Scrap Trends
Titanium Connection to DB Cooper
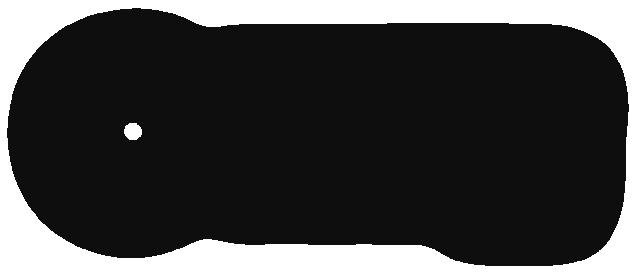
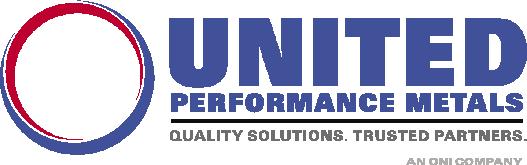

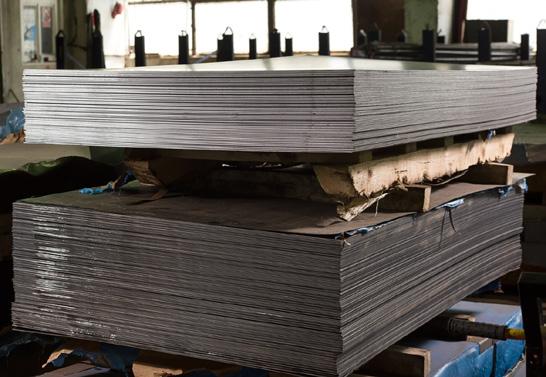
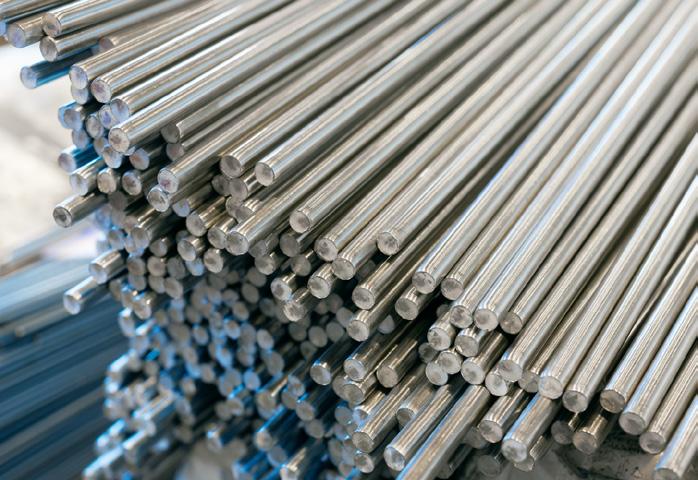
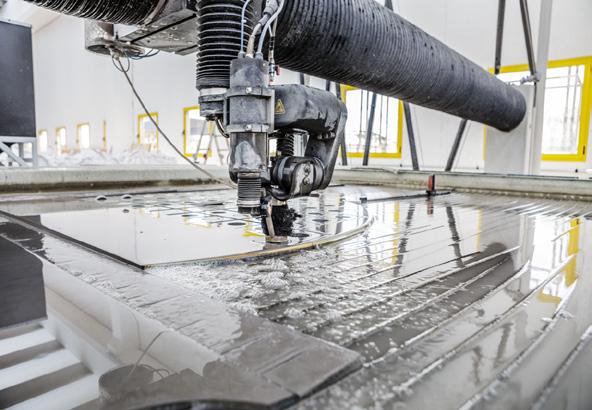

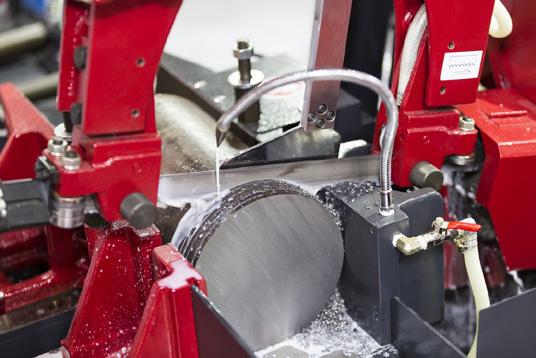


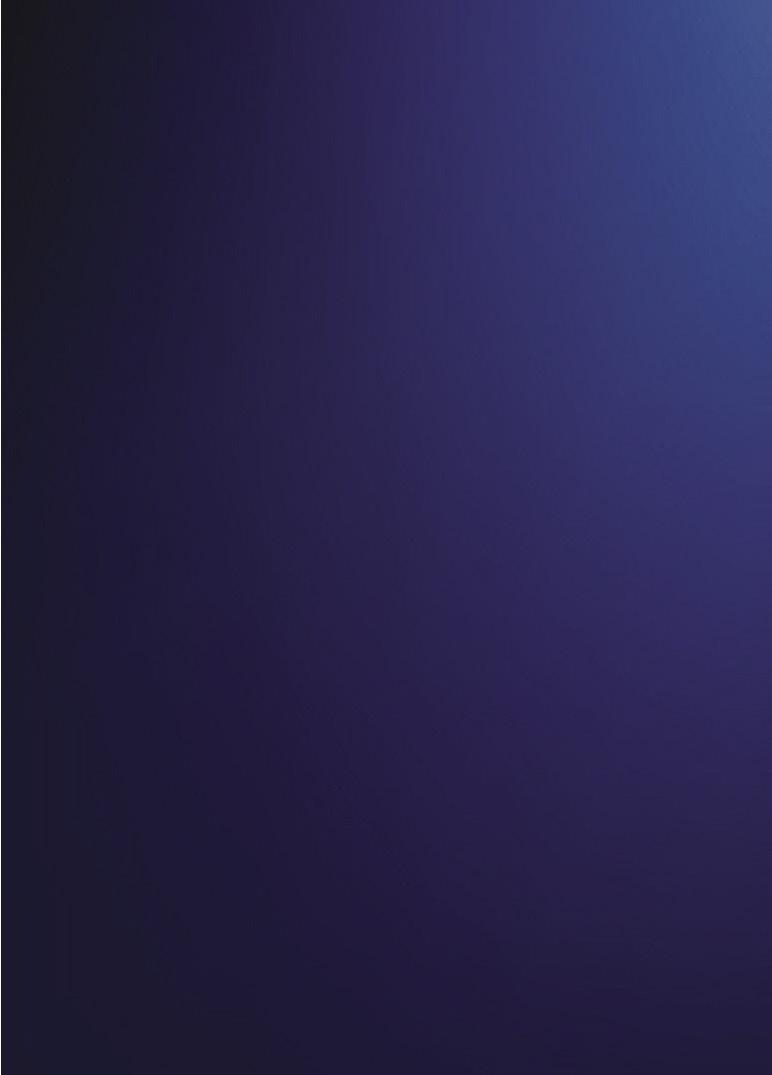
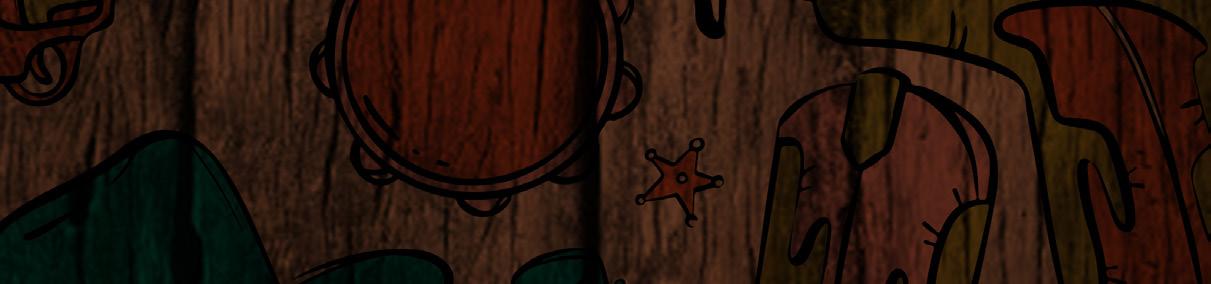
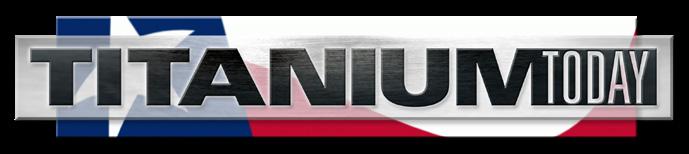
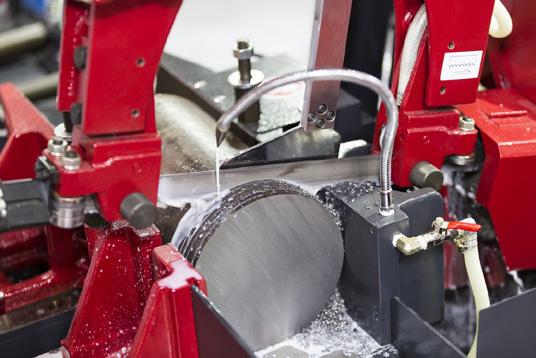

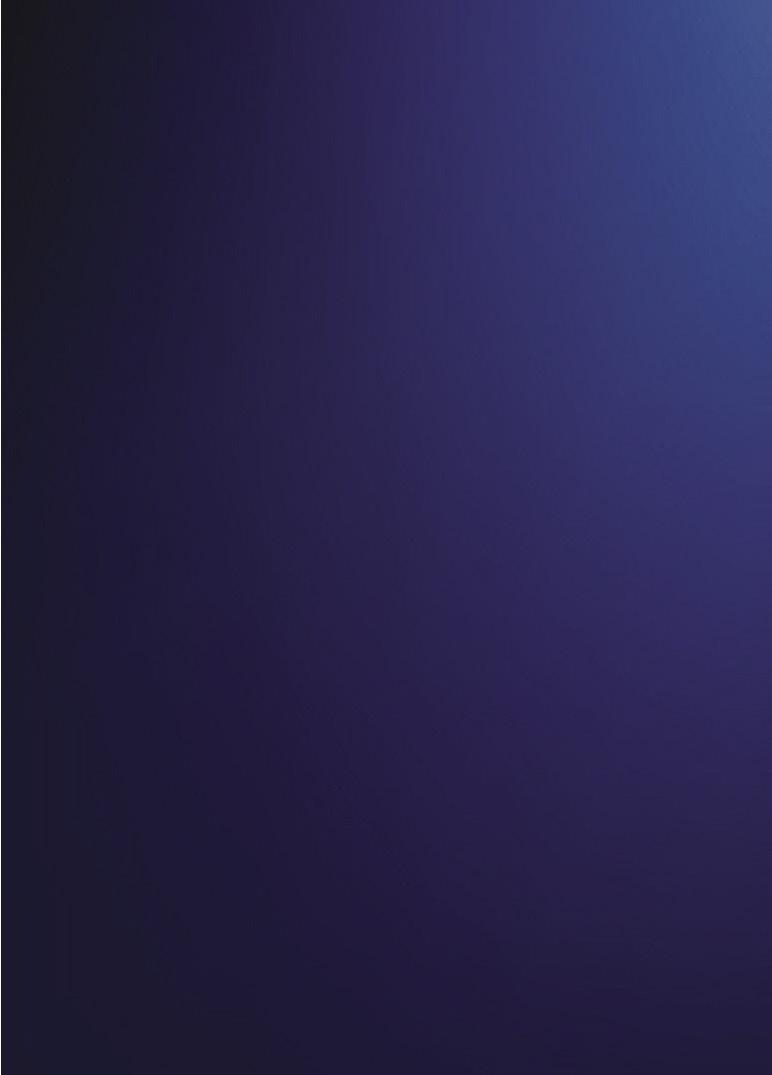
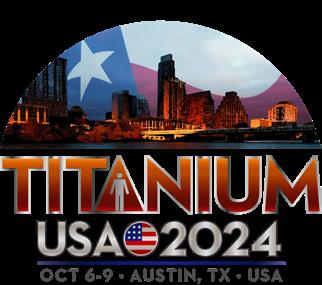

Issue 11; 2024 All Markets
In this issue:
TITANIUM EUROPE 2024 Executive Summary
Observations on Near-Term Titanium Scrap Trends
Titanium Connection to DB Cooper
Dr. Markus Holz
Professor, ITA Academic Member
Education Committee Co-Chair
Titanium Europe Conference Chair
ITA President 2022-2024
Dr. Markus Holz is currently Professor at University of Applied Sciences
Anhalt starting from 2020. There he is the program director of Logistics Management, teaching Operations Management and is currently involved in several national and international research programs in the field of sustainability and digitization in the industry.
Dr. Holz graduated in Aerospace Engineering in 1986 and earned his PhD in 1992. Following his 10 years of service in the German Airforce, Dr. Holz began his career with ThyssenKrupp in 1992, where he assumed several executive positions mainly in the stainless steel and special metals branch. In 1999, Dr. Holz became Managing Director of ThyssenKrupp Titanium GmbH (formerly Deutsche Titan GmbH) and in 2002 he was appointed Managing Director of ThyssenKrupp Titanium S.p.A. (formerly Titania S.p.A.). Furthermore, he was responsible for Tubificio di Terni, Italien, from 2004 through 2007. From 2007 to 2009 he was CEO of the ThyssenKrupp Titanium Group (Germany and Italy). In January 2010 he joined the Managing Board of Hempel Special Metals, Oberhausen, Germany. After joining as MD the ALD Management Board in October 2011, Dr. Markus Holz was the President of AMG’s Engineering Systems Division and CEO of Vacuum Technologies GmbH from 2012 to 2019.
Martin Pike President – Specialty Materials
ATI
ITA Vice President 2022-2024
Martin (Marty) Pike is President, ATI Specialty Materials, reporting to CEO and President Kim Fields. Marty brings more than two decades of ATI experience to this role, leading the Specialty Materials team to successful execution in meeting the demands of the aerospace ramp today and in the future.
In addition, Marty currently serves as Vice President, Global Commercial Strategies. Marty is the primary point of contact across ATI with strategic customers seeking to grow and expand their partnerships with ATI. Along with his responsbility for strategic customers, Marty leads our International Sales organization, the Defense Market Sector and Hypersonics teams. He also serves on the boards of Shanghai STAL Precision Stainless Steel Co., Ltd, a joint venture between ATI and Baowu Special Metallurgy and as Vice President on the Board of Directors for the International Titanium Association.
Marty has 25+ years of experience in commercial strategy, marketing and sales in Aerospace, Engergy, and Defense end-markets. He previously held the role of Vice President –Commercial for ATI Specialty Materials business where he led the product marketing, business development, international sales and managing long-term agreements with customers. In addition to the commercial role, Marty served as interim president of ATI’s Specialty Materials business unit in 2021, before being named to the Vice President, Global Commercial Strategies role in 2023.
Prior to joining ATI, Marty worked in footwear manufacturing and for an internet startup where he held various commercial positions including Regional Vice President of Sales. Marty has a BA in Political Science from the University of North Carolina at Charlotte.
Sam Stiller
Vice President – Commercial
Howmet Structure Systems
ITA Secretary/Treasurer 2022-2024
Sam Stiller is Vice President, Commercial for Howmet Aerospace. All Sales, Marketing, and Customer Service, globally, is led by Sam’s commercial team.
Frank L. Perryman
President and Chief Executive Officer
Perryman Company
ITA Past President 2022-2024
Mr. Perryman graduated from Millikin University in 1986 with a Bachelor of Science in Industrial Engineering. In 1988 he co-founded Perryman Company with his father and brother. Since December of 2008 he has held the position of President and CEO of Perryman Company. Perryman Company is a fully integrated supplier of specialty titanium products. From melting through finishing, founded in 1988, Perryman Company is headquartered in Houston, Pennsylvania, with office locations in Philadelphia, Los Angeles, London, Zurich, Tokyo and Xi’an. Perryman is an integrated titanium producer from melting of ingot to finished products. The company’s product portfolio includes ingot, bar, coil, fine wire, net shapes, and hot rolled products. The Forge and Fabrication group offers medical device contract manufacturing in a range of materials including plastics and titanium. A titanium global leader, Perryman supplies and services customers in the aerospace, medical, consumer, industrial, recreation, additive/3D printing and infrastructure markets worldwide.
Phil MacVane
Vice President, the Americas PCC Metals Group Global Sales
Michael Marucci Chief Technology Officer Kymera International
Safety Education
Robert G. Lee President Accushape Inc
Industrial Applications
Christopher Wilson Director of Research and Development NobelClad
John J. Scherzer Vice President – Medical Markets Carpenter Technology Corporation
Edward Sobota Jr. VP, New Product Development STS Metals
Jennifer Simpson Executive Director Ex-Officio Member of the Board International Titanium Association
Women in Titanium
Holly Both
Vice President of Marketing Plymouth Tube / Plymouth Engineered Shapes Medical Technology
Eric Baum Senior Business Development Manger Laboratory Testing Inc
By Michael C. Gabriele
The International Titanium Association (ITA), Denver, organized and hosted the TITANIUM EUROPE 2024 conference and expo at the Clayton Hotel Burlington Road, May 7-9 in Dublin, Ireland. The show had over 40 exhibitors and featured speakers who focused on economic trends and manufacturing technology innovations for the global titanium industry. Nearly 400 attendees came to the event from 31 countries.
Several presentations weighed in on titanium applications in the medical field, while others focused on metal-recovery techniques, powder metal production and additive manufacturing (AM) trends. In addition, Takeshi Nakashima, the deputy general manager of the titanium division of Toho Titanium Co. Ltd., provided in-depth analysis on the global titanium sponge market.
industry is driven by solid economic fundamentals. “Industry recovery (from the Covid-19 downturn) is progressing broadly as anticipated.”
Of particular importance to the titanium industry, Carpenter forecasted that airlines will need 42,600 new airplanes during the next 20 years, with single-aisle jets
trillion in 2022. Revenue Passenger Kilometers (RPKs) would grow to 20 trillion by 2024 from 6 trillion in 2022. Cargo traffic, measured in revenue ton kilometers (RTK) will reach 630 billion by 2042, up from 260 billion in 2022.
Boeing, to be sure, has faced its share of challenges during the last
accounting for 32,420 units and widebody jets 7,440 units.
Jeff Carpenter, Boeing’s senior director for contracts, sourcing and category management, and the special guest speaker for the conference, offered an upbeat assessment of global aerospace industry trends, saying that steady long-term forecast for the
Carpenter provided a similar outlook during his presentation at the TITANIUM USA 2023 conference held in Denver. He said the world economy’s gross domestic product (GDP) would reach $155 trillion by the year 2042, compared with $92
12 months regarding issues with its 737 fleet. The New York Times, in its March 28 edition, wrote that recent reports “paint a worrying picture about a company long considered to be at the pinnacle of American engineering.” As a result, two top executives announced they were stepping down from their positions.
Last October at the titanium conference in Denver, Carpenter thanked all the players in the titanium supply chain that do work with Boeing. “In 2022 we (Boeing) made some tough choices on where to get supply,” presumably a reference to the disruptions caused by Russia’s invasion of Ukraine. Boeing suspended purchasing of titanium from Russia in 2022. “It caused
longer vertically integrated back to (titanium) sponge, nor the cost-based” sponge price stability that came with it.” He displayed a chart that estimated 2023 titanium sponge global capacity at 825 million pounds, according to the January 2024 U.S. Geological Survey of Mineral Commodity Summaries, which excludes Russian supply due to assumed, continued sanctions.
everyone a lot of work—melters, forgers, process houses. A lot of forgers are under strain.”
Robert S. Wetherbee, ATI board chair and CEO, focused on “Commercial Aero-Engine Trends and Demands” in his presentation. He began by pointing out that there would be a 7.7 percent compound annual growth rate (CAGR) for aero engine titanium demand through the year 2028.
Supply chain stress points include stability and availability, cost pressures and geopolitical risks. “Customers are committing to eliminating single points of failure in their supply chains,” Wetherbee said, adding that there’s a tight supply for premiumquality titanium bar and billet. “Continued inflation creates pressure. The U.S. titanium industry is no
chief executive officer and director of Airbus SE, who said “the geopolitical tensions and supply chain challenges are upon us (a presumed reference to the ongoing invasion of Ukraine by Russia). In this context, the supply chain remains the pacing factor for the ramp up of the aerospace industry.”
Sam Stiller, vice president, commercial for Howmet Engineered Structures (a division of Howmet Aerospace Inc.) addressed “Titanium Demand Trends in Defense Aerostructures.” Stiller said that global defense market trends “play to the strength of titanium aerostructures and drive innovations.” He cited defense market trends such as air superiority, off-the-shelf technologies, speed to market and hypersonics. Titanium’s strengths include resistance to high operating temperatures, compatibility with composite structures, environmental resistance and reduced weight and near-net shapes. He listed innovations of
Wetherbee stated that the “titanium industry needs to be proactive to avoid being the ‘rate limiter.’” To underline points in his presentation, he quoted an April 2024 statement by Guillaume Faury, the
monolithic forgings, proprietary hightemperatures, titanium fine-grain sheet production, titanium extrusion in hot-stretch forming, and digital manufacturing and automation.
Takeshi Nakashima, the deputy general manager of the titanium division of Toho Titanium Co. Ltd., Japan, a producer of titanium sponge, provided a global titanium sponge outlook. Nakashima said that sponge demand for the aerospace market continues to grow steadily while demand for Industrial market grows slower than before. “In February 2024, the airline industry achieved full recovery in total passenger traffic, surpassing the 2019 level by 5.7 percent. In 2023, Airbus achieved a high A320 build rate while Boeing’s 737 build rate remains constrained. However, both OEMs are confident about higher build rates in the future. Both Boeing and Airbus still have very aggressive building plans. The 2026 delivery results should exceed the previous historical record set in 2018.”
As for the titanium sponge market situation in 2023 and 2024, Nakashima indicated that Japanese suppliers run their factories at more than 90 percent of capacity. “UKTMP (Kazakhstan) has hardly ramped up their sponge production due to a delay in importing equipment from Russia. VSMPOAVISMA seems to produce sponge at full capacity for Airbus and Russian
military demand. While there has not been an announcement of sponge capacity expansion from any aerospace-grade sponge supplier,
it is believed that Japanese sponge suppliers are studying the possibility of expansion.”
Nakashima, who also addressed the 2023 TITANIUM USA conference, pointed out that Airbus is still purchasing titanium products from Russia, which balances current sponge demand and supply in aerospace market. “If Airbus tried to reduce or suspend titanium products procurement from Russia, the sponge shortage would be serious. Even if Airbus continues procurement from Russia, there will be a sponge shortage. Only if aerospace-grade sponge production capacity expands, will it be avoided. Chinese surplus sponge supply will have only a limited influence on the
Premium Quality, Stability and Reliability.
One-Stop titanium alloy production and service.
A dozen years of titanium alloy production and research experience, with more than 100 patents and achievements to its credit, mastering a number of core technologies; Accredited with Nadcap non-destructive testing certificate and AS9100D, ISO14001, ISO 45001 and other certifications;
Titanium bar/billet
Size range: Φ15-500mm
Grade: Ti6Al4V, Ti-6242, Ti-6246, Ti-38644, Ti-15333, etc.
Titanium wire rod coil
Size range: Φ1.0-20.0mm
Grade: Ti6Al4V, Ti6Al4V ELI, Ti-38644, Ti-6242, Ti-6246, Ti-15333, Ti-422, etc.
Titanium forging
Size range: customized, disc, bar, ring, etc.
L(max):14m, W(max):4m, H(max):4m.
Grade: Ti6Al4V, Ti6246, Ti6242, Ti662, Ti38644, Ti15333, Ti1023, Ti422, etc.
For more information, please visit www.tcae.com/en/
aerospace industry.”
Quality concerns and geopolitical risks still exist for the global sponge market, according to Nakashima. “Considering the huge demand and supply gap, the Chinese sponge price decline is expected to continue. It looks as if many Chinese sponge suppliers are trying to assure their running rate at the cost of their profitability. It is uncertain if Chinese sponge suppliers will start reducing their production to improve their sponge price.”
Fundamentals leaning towards sponge production capacity expansion are improving for aerospace-grade sponge suppliers, Nakashima observed. “The U.S. import sponge price continues to increase. The Japanese government is trying to improve aerospace industry supply chain resilience, including Titanium sponge, which may provide financial support policies for Japanese sponge suppliers. However, current sponge suppliers still hesitate to expand capacity. Construction of a new sponge factory will cost hundreds of millions of dollars in (capital expenditures). Sponge suppliers have suffered from low profitability due to unstable demand and unfavorable prices to them despite their cost reduction. Only capacity expansion of aerospacegrade sponge suppliers can solve the looming sponge shortage in aerospace industry.
Nakashima cautioned that there will be a supply and demand gap in the future due to the growing requirements of the industry. “The aerospace supply chain including OEMs should consider how to convince sponge suppliers to approve new investments. Sponge suppliers want assurances of their profitability before deciding on capacity expansions. The aerospace supply chain would secure sponge supply if
they could assure sponge suppliers
Security; Critical to Manufacturing
Category
Quality
Economics
ESG
Geopolitical
Considerations
Consistency, TiO2 content, impurities, process yields, track record, qualification
Capital and operating costs, brown field versus green field, infrastructure, ore grade, mine‐life, investment
Company credentials, governance, licenceto operate, community, reputation (local and global)
Regional stability, permitting and fiscal arrangements, conflict zones
Supply Chain Seasonality, force majeure type events
Inputs, staffing, export routes, final delivery (port)
Climate
Declining reserves at existing operations
Lack of investment in new projects
Future rutile demand is production constrained
Rutile’s green credentials support demand growth
Over 20% of future supply are currently in project stage
of stable sponge demand as well as a reasonable sponge price.”
Derek Folmer, general manager, marketing for Sierra Rutile, shared his thoughts on “Rutile Supply
Titanium Sponge.” Sierra Rutile is the world’s largest producer of natural rutile, an Australian mining company with assets in Sierra Leone, West Africa. Folmer said TiO2
pigment drives feedstock demand, with the vast majority going to pigment compared with a small segment for titanium metal.
He identified the titanium feedstock value chain and listed the risks facing rutile supply.
“The world needs rutile and risks must be weighed and considered by source. Sierra Rutile committed to responsibly supplying the world’s rutile requirements with approval pending on $300 million Sembehun
Area 5 project (a town in the southern province of Sierra Leone in Africa),” Folmer said.
Aamir Abid, Ph.D., an executive with Retech (a Seco/Warwick company) discussed the “Recycling of Titanium Scrap to Produce High-Quality Ingot and Additive Manufacturing Powder,” and touted the plasma gas atomizer (PGA) process. Abid said PGA “provides an economically viable method to produce reactive and refractory alloy
powders. PGA is inherently scalable due to use of hearth melting via DC plasma and ability to continuously feed, melt and atomize powder. Significant reduction in powder cost-PGA allows for improved yield, use of lower cost raw materials and recycling of revert.” Successfully produced complex refractory (titanium and nickel) alloys on PGA yields “best in class” powder performance, according to Abid.
Michael Wilkes, global product manager for Kymera International, presented an overview on the business dynamics of titanium master alloys. Common master alloy metals include vanadium, the most common master alloy for titanium, along with aluminum, used in the production of the workhorse aerospace alloy Ti6A4V; and molybdenum and niobium. He pointed out that titanium scrap plays a major role in master alloys. Wilkes defined master alloys for titanium melting as a combination of two or more metals in a metallurgically alloyed form. “Shortterm demand dynamics for master alloying elements will be mainly influenced by the availability of titanium scrap used during the melting practice, and inventory levels of scrap,” Wilkes said. “Longerterm trends suggest continued unpredictability for key master alloy elements. Continued supply surges and dips in the global steel industry, led by China, will drive (business) dynamics. New technologies for green energy storage will compete for the same materials used by the titanium industry. Continuous risk management is recommended.”
He provided charts that illustrated forecasts for vanadium, molybdenum and niobium. The iron and steel industries accounted for 94
percent of total vanadium demand in 2021 and remains a major source of demand, according to Wilkes. The steel market expected to grow at a CAGR of about 3.1 percent until 2030. “Vanadium demand is being revolutionized before our eyes.” For molybdenum, the majority of growth during the next 10 years is expected to occur in the chemical and petrochemical industry, including the hydrogen sector and power generation driven by the demand for sustainable construction and energy, specifically wind and geothermal. “The niobium market is estimated to be at 97,208 metric tons, while growth over the next five years is projecting over 10 percent CAGR, reaching nearly 190,000 metric tons.” Niobium production in 2022 registered 79,000 metric tons.
There were several presentations regarding the use of titanium in medical markets, with a focus on AM technology. Nicolas Bouduban of the Swiss m4m Center AG, said his group enables innovations and support in medical and dental applications via AM and related engineering expertise. He evaluated the use of Ti6A4V as a material choice for long-term medical implants. Matthias Scharvogel, the founder and CEO of Element 22 Gmbh, makes use of metal injection molding (MIM), fused filament fabrication, and cold metal fusion as complements to additive manufacturing.
The presentation by Chris Norris of APS Materials Inc. discussed “Titanium Technology in Medical Applications; Thermal Plasma Spraying Biomedical Implants,” and listed the capabilities of plasma spray equipment used by his company.
Ali Madani, the managing partner for Avicenne Medical presented an “Outlook for the Orthopedic Market.” Madani estimated that the worldwide market
for orthopedic implants (knee, spine, trauma and hips) in 2023 at $51 billion.
Madani then offered a forecast for orthopedic market drivers and market limiters through the year 2030. For orthopedics market drivers, extremities and shoulder applications, currently estimated at around $5.9 billion, “will almost double in 2030 to $10 billion.” There will be “historical constant growth” for knee and trauma application, and high volume growth in emerging markets.
By contrast, market limiters include “continuous regulatory cost increases, while price pressure on the end markets will remain moderate.” He observed that the end-user orthopedics market “has long market visibility and very high barriers to entry. The profitability of established companies is very high. Challengers can gain market share through new product launches. This market is suffering from sales prices that are almost frozen.”
The key success factors for an orthopedic company, according to Madani, include having a proven products with a long trackrecord; continuously introduce incremental innovations in implants and instruments; regulatory and certification expertise; control over distribution networks; and
maintaining the efficiency and continuity of their supply chains.
Wei Chen and Carl Boehlert, of the Department of Chemical Engineering and Materials Science at Michigan State University, provided information on the “Characterization of the Microstructure, Tensile, Fatigue, and Creep Behavior of Powder Metallurgy Processed Rolled and Extruded Ti-6Al-4V-1B (wt. percent) Alloys.” They identified their objectives as being able to evaluate processing effects on the elevated-temperature fatigue and creep behavior of Ti-64-1B alloy Ti6Al-4V (wt. percent), Ti-64, and to evaluate the effect of B content on the elevated-temperature fatigue and creep behavior of powder metallurgy (PM) rolled plate and PM extrusions. They evaluated tensile behavior, fatigue behavior, fracture analysis, the creep behavior of Ti-64-xB alloys and creep fatigue interaction. They concluded that “processing significantly influences the fatigue behavior of Ti-64-xB alloys. Powder metal (PM) processing induces an equiaxed grain size, (which) results in enhanced fatigue lives compared to cast metallurgy. The finest equiaxed microstructure (PM extruded) resulted in the
greatest fatigue lives. Texture, induced through the extrusions, enhanced the tensile and fatigue strengths through aligning both the a-phase and the Ti-B phase into ‘hard’ orientations. The extruded alloys exhibited tensile anisotropy where the extrusion directions were stronger than the transverse directions. However, the anisotropic
have placed orders for more than 1,000 aircraft within the last two years. He said the Asian giant will develop and operationalize 220 airports within the next five years, making it the third largest global civil aviation market. India, he said, is “quickly becoming the goto source for aero assemblies and subassemblies, with more than $2
behavior was not a ‘show stopper’ as the transverse orientations for the B-containing alloys remained quite strong.”
“Overall, Ti-B alloys have shown promise for fatigue-driven and creep-driven applications of Ti-64 and PM processed Ti-64-xB have the potential to replace Ti-64 for both RT and elevated-temperature structural applications.”
Jim Collins, chief technology officer, PTC Industries and Aerolloy Technologies, evaluated “Green Titanium – Enhancing the Aerospace Titanium Market from India.” He began by identifying aerospace business opportunities in India, saying that Indian airlines
billion of annual exports to major air framers.”
PTC/Aerolloy was established in 1963 as India’s first investment casting foundry, operating plasma arc melting technologies, and now operating two advanced manufacturing campuses in India. Collins reviewed the technologies and timelines of Aerolloy’s electron beam cold hearth refining; plasma arc cold hearth refining; the cold hearth refining process; vacuum arc remelting; and open die forging and hot rolling. Many of these manufacturing technologies are slated to come online this year and in 2025. He also noted that PTC Industries and Aerolloy are committed to “comply with carbon footprint reduction and greenhouse gas (GHG) protocols in accordance with international standards, meeting the Paris Agreement targets.”
TITANIUM TODAY, the quarterly online magazine published by the ITA, provided a news analysis feature in the third quarter of 2023 on how the Republic of India is
positioning itself to become a major force in the global aerospace and titanium industries. As noted by Collins, the giant Asian subcontinent is building an industrial infrastructure to compete in the aerospace and titanium sectors.
“With the leverage made from the additional in-house generated renewable energy at 50 percent of the plants operating power and additional high efficiency process equipment/technologies, a further three tons of CO2 saving per kg of Titanium produced at via Aerolloy’s Green Titanium process line. Finally, with the total supply cycle advanced Campus, a significant carbon footprint reduction is to be achieved via the reduction in process logistics.”
Kurt Faller, the founder and chairman of MetCon, talked about “Free, No-Cost Saleable Metal Hiding in Traditional Titanium Conversion.” He said MetCon Introduced Electrochemistry to Titanium Processing, with more than 25 million pounds processed. Faller defined “free” as finding available metal typically removed due to conditioning yield losses. “Yield, yield, yield: the mantra of management.”
He said that free metal can be found as “every hot working step generates certain yield losses: end crops (removing bulged ends), and side trims (removing as-rolled ragged edge). “Hidden” yield losses generally are less understood: alpha case layer removal and conditioning of cooling cracks (cracks covered in alpha case). “Most producers use post-conditioning pickle to reveal hidden defects.”
Faller explained that the MetCon alternative involves “green chemistry:” 96 percent H2O plus citric acid plus ABF; less acidic
Established in France (Lyon), the stockist Acnis Group is one of the world leaders in the distribution of metal alloys especially in TITANIUM, in all forms : sheets, bars, tubes and powder for 3D printing.
ISO 13485 certified since 15 years, the family business has specialized in the medical field since its creation in 1991, to meet the demand of orthopedic manufacturers and dental implants, as well as surgical instruments.
ACNIS Group acts as a buffer between producers and users, thanks to its 600 to 700 tons rotating stock and 1,300 references of different origins. Our unique cut-to-size service center (15 machines: waterjet, high-definition waterjet, plate sawing, bar sawing, shearing, machining, chamfering) allows us to reduce your costs by optimizing scrap rates.
As a result, the company is able to deliver very quickly its customers, in barely a week, no matter the ordered quantity. Major implant manufacturers among the main American and European OEMs themselves call on ACNIS Group to source their metal alloys.
The last creation of ACNIS USA stock in 2023 in Chicago has changed the game. Acnis Group is now the only distributor that can stock and deliver any quantity in North America (ACNIS TITANIUM & ALLOYS USA-Chicago), South America (ACNIS DO BRAZIL-Sao Paulo), Europe (ACNIS FRANCE-Lyon), South Asia (ACNIS CHINAShanghai) for global worldwide contracts.
Acnis is your one-stop shop for all TITANIUM grades, stainless steel (316L, 420B, cobalt chrome, 17/4 PH, high nitrogen alloy, Custom 455, Custom 465…) and polymers
Our dental subsidiary BCS, a European leading distributor of CAD CAM products for additive manufacturing, is registered with the FDA for titanium powder & discs, and cobalt chromium powder.
than soft drinks. MetCon electrochemical technology is a rectifier for controlled surface reactions: precision in process; no adiabatic heating; and 100 percent reproducible, with no hazardous waste disposal, no air permits and no scrubbers.
He summarized by saying that free material involves “condition all over” (CAO) and delivers the greatest value (replacing grinding). “MetCon Defect Reveal pickling reveals and eliminates cracks below conditioned layer.” MetCon CAO and MetCon Defect Reveal involve no crack propagation, little post-rolling conditioning, predictable and repeatable process control, and significantly simplifies environmental compliance.”
Dave Ochar, vice president, aerospace sales, Bodycote Metal Additive Manufacturing Services, reviewed the benefits of metal additive production technologies, while pointing out that all AM parts need post processing. These processes include stress relief, hot isostatic pressing, annealing. In particular, he focused on hot isostatic pressing (HIP) at Bodycote, which combines high temperatures
(up to 2,000°C) with isostatically applied gas pressures (up to 45,000 psi).
“HIP is used to eliminate porosity in castings and consolidate powder metallurgy materials into fully dense components. Dissimilar materials can be bonded together to manufacture unique, cost-effective parts. Bodycote operates a global HIP network with over 50 HIP vessels of varying sizes in multiple locations. We provide two major HIP routes for customers: HIP product fabrication, for the manufacture of components through powder metallurgy and diffusion bonding; and HIP services, providing porosity removal through HIP densification.” Each week a typical Bodycote HIP plant will process many tons of materials such as titanium, aluminum, steel, cobalt, and nickel-based superalloy castings, removing porosity and uprating the performance of parts such as turbine blades and turbochargers, according to Ochar.
Beate Orberger, director of EuroTitan, outlined “Decarbonized Titanium Recovery from Aluminum and Titanium Production Residues.” EuroTitan is a consortium
of European counties (Germany, France, Greece, the Netherlands and others), with experience from previous and ongoing projects for metals extraction from industrial wastes. Orberger said EuroTitan contributes to solving three challenges: Europe’s dependency of titanium metal and its related supply chain; highly polluting titanium metal production via the Kroll process; and Europe’s high metallurgical residue volumes in industrial waste streams.
EuroTitan’s objectives involve unlocking titanium from European waste streams. “EuroTitan will produce Ti-metal nanopowders through efficient and low-carbon footprint extraction technologies
and in-line process optimization,” Orberger said, which results in over 90 percent of CO2 reduction compared to the Kroll process. There will be full integration of H2
technologies and renewable energy sources, with onsite H2 production (electrolysis and electricity from wind power).
The estimated reduction of energy and water consumption: minimum 20 percent on-site, while minimizing production interruption. The remaining residues are converted into innovative (30 percent lower CO2 emissions compared to cement based) construction materials. Orberge said water will be recycled, and excess heat energy will serve local households. Rest waste (slags) will be converted into construction materials.
EuroTitan’s vision is to diversify and secure the supply chain for the aeronautic sectors (master alloy and 3D printing) and decrease Europe’s dependency from Russia, according to Orberger.
L.P. Lefebvre of the National Research Council of Canada, and Olivier Bergeron, AP&C-Une Société de GE Additive, discussed “Near Net Shape Precursors for the Production of Titanium Plates, Sheets, Forging and Hipping.” The objective involves developing powder metal (PM) precursors for the production of net shape titanium products to take advantage of the availability of high quality rapidly solidified titanium powders, reducing cost by reducing
the number of steps and waste during manufacturing, and developing new materials, such as high-tech composites.
Production capacity of high-quality titanium powders has increased with the development of AM, which only uses a fraction of the particle size distribution. A significant fraction of high-quality fine and coarse powders are now available in significant quantities. This directly impacts the cost and sustainability of AM processes and provides opportunities in processes that could not, until recently, afford procuring such powders.
Piet Kooman, grinding specialist, Time Savers LLC service centers, addressed “Unlocking Precision: WideBelt Grinders for Titanium Grinding in Aerospace; Grinding Titanium with Finesse and Efficiency.” Kooman underlined the importance of precision titanium grinding, saying it’s essential in aerospace, medical, and other high-performance industries. “Challenges like removing alpha case and passing the bending test can be effectively addressed with wide belt grinders, specialized tools designed for titanium grinding,” he stated.
He asked the audience to consider the benefits of wide-belt grinders, saying they offer effective solutions for precision grinding in titanium processing. “By adopting this technology, engineers and technicians in the aerospace industry can significantly improve efficiency and quality in their titanium applications.” Wide-belt grinders used as specialized tools provide consistent
material removal, versatility in abrasives and settings, effective heat management, minimized tool wear, surface finish precision and specialized tooling for titanium.
“Operator training is crucial for maintaining precision and safety in titanium grinding,” Kooman said. “Adhering to industry standards and regulations ensures the integrity of the grinding process and guarantees the safety of both the operators and the final product. Additionally, implementing safety guidelines and quality control measures helps to prevent accidents and ensure consistent quality in titanium precision grinding.”
Martin Jackson, a professor of advanced metals processing at the University of Sheffield, presented information on “Digital Microstructural Fingerprints of Closed-Loop Recycling of Titanium Alloys.” He showed a
slide on the availability of titanium waste and said there’s a need to start to refer to waste or scrap as a valuable feedstock.
The use of high value alloyed titanium swarf as a feedstock is used for the FAST and FAST-forge process, with the generation of near-net shape components in high strength and good fatigue-life applications, he said. “There’s an indication of production volume capability and cost level for automotive industry.”
Thomas Klein of the Austrian Institute of Technology reviewed the “Processing of Ti-6Al-4V by Cold Metal Transfer: Microstructure Evolution and Mechanical Properties.” Klein acknowledged that Ti-6Al4V is the “workhorse alloy of the titanium industry and more industries are trying to implement the waDED (wire and arc-based directed energy deposition) process.
“Cold metal transfer (CMT) was shown to break up epitaxially grown β grains and reduce their size with increasing build height, Klein said. “Multiscale automated image analysis and compositional mapping of the microstructure revealed α-lath size variations as a function of build height and formation of fusion boundaries depleted in V and Fe. Hardness maps reveal local variations in hardness dependent on grain orientations; Acceptable strength values were reached while further improvement of ductility remained; Good fatigue strength obtained, whereby scatter was observed.”
“CMT is shown to be capable of producing Ti-6Al-4V alloy builds with very high deposition rates. The ability to remove
the mechanical anisotropy and achieving enhanced properties in Ti-6Al-4V alloy makes this process as one of the most suitable AM
processes for adaptation in aerospace and other industries.”
Dr. Alexander Klassen of ALD Vacuum Technologies GmbH,
a subsidiary of AMG Advanced Metallurgical Group N.V., presented information on “Advanced Vacuum Furnaces for Metal Powder Production and Additive Manufacturing—Bridging Raw Materials to Products.” Klassen provided an overview of ALD’s Electrode Induction Melting Inert Gas Atomization (EIGA) systems.
Benefits of the EIGA, according to Klassen, include ceramic-free powder production process, with no contamination of raw material with non-metallic elements, direct conversion of electrode into powder, a robust and simple process, and high productivity due to short cycle times. Materials processed by the EIGA system include titanium metal alloy powders, reactive and refractory metal powders, precious metal alloy powders, and materials with up to 3000 °C melting temperature, such as niobium, molybdenum and tantalum.
Klassen identified ALK EBUILD® 850 as “the world’s largest industrial electron beam powder bed fusion system, and gave examples of parts the system is able to produce.
In his summary remarks, Klassen said AM at ALD features a powder bed fusion electron beam (PBF-EB) build volume of 850 x 850 x 1000 mm³. The system has a beam power of 45 kW @ 150 kV acceleration voltage, with high productivity rates of up to 1000 cm³/h. Powder Recycling at ALD provides a “circular economy” solution for metal powders, with a wide range of powder particle sizes, fast AMbuild using up to 400 µm layers, electrode production under vacuum conditions, and closed capsules for easy storage.
ITA will host TITANIUM USA 2024 at the JW Marriott Hotel in Austin, TX, Oct. 6-9. Visit www. TitaniumUSA.org for registration information. Many managers from prime contractors as well as sub-tier suppliers are coming as they recognize the efficiency of attending a meeting such as TITANIUM.
Because there are producers, distributors and fabricators from all parts of the world across several consuming market segments at the conference, it’s a very cost effective means for the delegates to meet
with a wide variety of customers and vendors in a single trip. At the same time, TITANIUM USA, much like TITANIUM EUROPE, offers opportunities to hear from leading industry executives and attend panel discussions on market topics that affect each industry segment.
The ITA is a membership-based international trade association dedicated to the titanium metal industry. Established in 1984, the ITA’s main mission is to connect the public interested in using titanium with specialists from across the globe who may offer sales and technical assistance. Working through extensive membership resources, the ITA seeks to expand the knowledge base for the metal, providing technical literature and sponsoring seminars and conferences. Current ITA membership is comprised of more than 120 organizations and over 1,500 individual members worldwide.
Advantages
•
• Furnace capacities
•
• Titanium and high nickel alloys
By Michael C. Gabriele
As the titanium industry navigates evolving business trends for the near term, some executives have focused on the availability of titanium scrap to support their assorted manufacturing operations. In addition to supply and demand concerns, the pendulum continues to swing regarding the balance between utilizing scrap and sponge, considering the advantages of each.
Several titanium scrap executives weighed in on these issues, providing insight and forecasts, and the industry continues to distance itself from the painful years of the downturn caused by Covid-19.
Steve Chavez, the president of All-Met Recycling, Anaheim CA, observed that titanium scrap supply and demand will increase over the next five years mainly due to commercial aviation projected build rates. He shared his estimates, saying that supply this year will be 250,000 metric tons, while demand will reach 210,000 metric tons. The supply/ demand balance is expected to tighten in 2025, with supply at 250,000 metric tons and demand growing to 240,000 metric tons.
A potential shortfall is projected in 2026 with demand outpacing supply: 290,000 metric tons of demand versus 270,000 metric tons of supply. The situation will shift in the following two years. Demand will rise to 300,000 metric tons versus 320,000 metric tons of supply in 2027, with 310,000 metric tons of demand versus 330,000 metric tons of supply in 2028.
“We see the market in three
‘Scrap and sponge compete as raw material sources for the melters. Whichever offers the greatest cost benefit, ultimately will have higher demand. While this is certainly not a one for one, it serves as a good general rule. Other factors are that master
alloy prices impact the value of scrap as well (vanadium, molybdenum, etc.), and newer melt technologies actually need a certain amount of scrap to produce consistent chemistry in the heats.’
—Nick Corby ELG Utica Alloys
major categories: aerospace/medical; industrial; and ferrotitanium,” Chavez stated. “Supply and demand levels vary for each segment. We have seen additional availability of scrap from U.S. generators, thus a positive impact. We do not see a potential scrap shortfall until 2026. We see a direct correlation between scrap and sponge both in utilization and pricing. As sponge production meets, exceeds, or falls short of demand, scrap fills the gap. It also works the opposite way. There is a balance that fluctuates between sponge, scrap, and master alloys.”
All-Met Recycling is a family owned and operated recycling company, founded in 1957 by Chavez’s father, Manuel A. Chavez. In 1977 the Chavez family took its small business and incorporated and opened its first recycling facility in Los Angeles. For the last 40 years AllMet has processed aluminum, ferrous and steel alloys for smelters and foundries throughout the world. In
2016 All-Met expanded its processing capabilities to include titanium alloys and has supplier of titanium feedstock to many U.S. melters.
Much like Chavez, Matt Schmink, the president of EJ Metals LLC, Detroit, sees the demand for titanium scrap increasing during the next five years. “Some of this is due to increased utilization of scrap by some melters who are installing EB (electron beam) melt capacity to give them greater flexibility in how they melt and allowing them to take advantage of market conditions when scrap is cheaper than sponge and alloy.”
However, Schmink also sees the ongoing war in Ukraine
“turbocharging” titanium scrap demand. “The reason for this is that the U.S. melters (which have long been larger users of scrap than any other part of the world) are expanding capacity and taking on contracts that are moving away from Russian sources. This not only increases the demand for scrap overall but also is redefining the shipping lanes and relationships for how scrap flows. Generation sources are not always located close to a user of the scrap so that is having some impact as well.”
The expanded use of electron beam (EB) melt systems, international turmoil, and other market conditions have altered Schmink’s assessment of the titanium scrap market. “In 2022, I estimated that total scrap utilized in titanium melting was roughly 115,000 metric tons, and that number would grow to 232,000 metric by 2030. Now, my estimate is that it will basically double. That’s not a U.S. number; it’s a global number. On top of that, in 2022, you had utilization of scrap in
sacrificial markets of roughly 88,000 metric tons with growth in that segment to 120,000 metric tons by 2030.”
Schmink offered insights into the “segregation” of the titanium scrap market. “The scrap market is both segregated and not segregated. Certainly, from a usage perspective, there is clear delineation of what types of scrap are usable for the different markets. The aerospace market is much more stringent in the type of scrap it can use. Ferrotitanium is basically everything else.
Industrial applications are essentially commercially pure scrap so that one is pretty well segregated though there are some stainless applications that require commercially pure scrap so there is some competition there.
“The markets historically have been fairly close together though there has been a divergence recently,” Schmink continued. “Aerospace grade scrap has become much more valuable than ferrotitanium grade scrap, and that is reflected in
the price. However, this is difficult because there is a relationship. Turnings scrap is where we see this the most. Turnings that qualify for aerospace essentially qualify based on chemistry. If there is too much contamination it is downgraded for use in ferrotitanium. However, as there is such a disparity in value between these two applications, it muddies the water a bit and makes managing those scrap flows very difficult.”
Schmink also provided an update on the scrap operations of Aeropro Industries, a joint venture between EJ Metals and AllTi, based in Redford, MI. He said Aeropro is operating and involved in qualification trials, “working with some potential customers to identify their needs and see if we are a good fit.”
The business dynamics in the relationship between titanium scrap and titanium sponge production can be puzzling, even for seasoned industry observers. There are questions about what material stream is best suited for a given production application, and which material stream is the most cost effective. Today, global supply chain issues have become a major factor when it comes to price comparisons and market demand, especially when many in the titanium industry have raised concerns over potential metal shortages.
According to various online news outlets (Reuters, Financial Times, Washington Tariff and Trade Letter and others), Japan is the largest supplier of titanium sponge for the United States, especially aerospacegrade sponge. Since the closing of facilities by Timet and ATI, it’s believed that there is virtually
no industrial titanium sponge production in the United States.
Takeshi Nakashima, the deputy general manager of the titanium division of Toho Titanium Co. Ltd., Japan, a producer of titanium sponge, offered a cautious outlook on the production and availability of titanium sponge for the global aerospace market during his presentation at TITANIUM USA 2023 held in Denver. “Aerospace supply chain will face a sponge shortage as well as its own production ability,” he warned. “The sponge demand and supply gap will keep increasing, even if OEMs ramp up production gradually. A shift of sponge allocation from the industrial market to the aerospace market might occur to catch up with increasing demand.”
The aerospace supply chain and OEMs need to understand that a large-scale investment in titanium sponge production normally requires up to four years construction, he pointed out. “Sponge suppliers are trying to expand capacity by 10 to 20 percent, which will increase sponge supply for aerospace market. Many sponge suppliers still haven’t reached full capacity and are trying to ramp up their production.”
Nakashima estimated that sponge demand for commercial and military aerospace (excluding China) registered about 75,000 metric tons in 2023, and would continue to grow, reaching about 115,000 metric tons by the year 2031. “Sponge suppliers expect a shortage of sponge supply will increase sponge prices continuously even though production costs fall. Sponge suppliers need to gain enough profit for new investments. The aerospace supply chain will secure enough sponge that they need if they can accept a reasonable sponge price.”
(Editor’s note: Nakashima also was a speaker at the TITANIUM EUROPE 2024 conference held May 7-9 in Dublin, Ireland, and his remarks are included in a story appears in this issue.)
Another speaker at TITANIUM USA 2023, Yasuji Yamao, the chairman of the Japan Titanium Society and the president and representative director of Toho Titanium Co. Ltd., said titanium sponge demand surged in 2021 with the recovery from the Covid pandemic downturn. Japan sponge shipments, domestic and export, are expected to surpass 60,000 metric tons in 2023, which would be a record high and above 2019 levels of sponge shipments. Titanium sponge production in Japan registered 47,000 metric tons in 2022.
Schmink weighed in on the topic and provided his own observations. “Sure, there are definitely complexities in the scrap/sponge formulation,” Schmink said. “In other words, making sure you are making the right blend of material to reach a desired chemistry. That can certainly muddy the waters a bit as scrap demand may go up or down depending on the pedigree of the scrap. However, in simple terms, the titanium melter has a basic choice when choosing to melt titanium ingot. Do I melt sponge mixed with master alloy or do I melt scrap? (There is always a little bit of sponge in there. No melter consistently melts only scrap and some specifications do not allow for all scrap. But it comes down to a market decision: which is most cost-effective and does the melter have the right equipment to take advantage of variation in the markets. I think that is why you are seeing more melters installing EB Hearth Melting capacity. They want the flexibility to change things up
when market conditions dictate a different mix.”
Nick Corby, vice president, titanium products and services at ELG Utica Alloys, Downingtown, PA, gave his assessment. “Scrap and sponge compete as raw material sources for the melters,” Corby said. “Whichever offers the greatest cost benefit, ultimately will have higher demand. While this is certainly not a one for one, it serves as a good general rule. Other factors are that master alloy prices impact the value of scrap as well (vanadium, molybdenum, etc.), and newer melt technologies actually need a certain amount of scrap to produce consistent chemistry in the heats. This prevents melters from going to 100 percent sponge and alloy, while chemistry will impede 100 percent scrap heats due to higher oxygen levels or trace elements in scrap.”
Corby said he believes the demand on titanium scrap will remain strong in the near term. “The demand on scrap will continue at its current levels for the next five year. This is driven not only by the aerospace industry growth, but also the installation of new melting capacities in the United States that have scrap as a raw material component at their core.”
Given the ongoing global business disruptions caused by the Russia/ Ukraine war, which began in February 2022, concerns remain regarding titanium scrap and metal supply chains, according to Corby. The immediate impact was uncertainty of supply of mill products and understanding these disruptions. Long term, both Airbus and Boeing have announced their intention to decouple from Russian supplied titanium mill products. While initially started to meet increasing demands in Aerospace (and other markets), it looks like U.S. melt
A microscopic metal fragment found on the tie of infamous plane hijacker D.B. Cooper has been determined to be part stainless steel, part titanium. Host of the podcast “The Cooper Vortex”, Darren Schaefer, interviews ITA’s own Stan Seagle regarding this important discovery.
Listen Now To The Cooper Vortex Podcast
expansion will be needed to cover Russia’s market share to the OEM’s.”
Regarding worries of metal and scrap shortages in the near term, Corby said he believes that U.S. melters have “caught up” with demand, while noting that there are still some concerns. “The rising issue is with new melt capacity coming online in 2024 and beyond, will supply/demand remain in balance?
Based upon United States Geological Survey (USGS) statistics, 2023 scrap Imports have reached the same levels they were in 2017 and 2018, but are still about 12-percent short of 2019 where the supply/demand curve was essentially in balance. So technically, we are still short on scrap. Sponge at the moment is available to cover the
aforementioned gap, but once the new melting capacity comes online, it appears that there will be an imbalance.” (The USGS is based in Reston, VA.)
“The disruption for scrap is a matter of getting the scrap where it needs to go,” Schmink observed. “Since the United States is the largest consumer of scrap for new titanium, that creates some difficulty since there are so many generation points. However, the industry I think is doing a pretty good job of adjusting to that and moving the scrap where it needs to go,
but this will continue to be an issue. Nearly all of the major U.S. melters have announced capacity expansions. As they are the predominate melters of scrap, this will require additional scrap handling and processing capacity in the industry. Some companies, such as our company Aeropro, are looking to try and fill that potential gap.” n
By Paul E. King, Ph.D.
This article addresses the product quality improvements demanded from the increasingly severe service conditions that we are expecting from the metal alloys we use on a daily basis. For instance, turbine blades, typically made of titanium (Ti-6Al-4V), are being asked to maintain their physical integrity regardless of the fact that we are also asking the components made from it to be lighter (e.g. thinner sections) and to operate under more extreme conditions in order to meet carbon emissions standards.
For these materials to continue to meet these stringent requirements, tighter controls over chemistry and structure must be maintained. Yet, Delzant et al1 have recently shown that there is as high as a 12.5-percent segregation of vanadium across the cross section of a Ti-6Al-4V ingot. It is indicated that this variation is due to the processing conditions itself while this high of a variation could lead to catastrophic failures in the components made from them.
Titanium and other alloys of high value such as nickel based super alloys, highly alloyed steels and other reactive metals such as zirconium, are typically melted by vacuum arc remelting (VAR), a metallurgical process used to produce high homogeneity in the alloys such. Although VAR-melted material
Figure 1-Uncontained engine failure on a British Airways 777 occurred upon take off from Las Vegas in 2018.
Figure 2 - “Contained” engine failure on SW Flight 1380 resulting in one loss of life due to structural damage from engine debris.
Source - NTSB
represents only a small fraction of the overall metals industry, the products made from these metals are often of the highest criticality. Failure of the parts means catastrophic results, including loss of life.2 One would expect that failures would be rare, and they are in terms of probabilities. But,
Titanium and other alloys of high value such as nickel based super alloys, highly alloyed steels and other reactive metals such as zirconium, are typically melted by vacuum arc remelting (VAR), a metallurgical process used to produce high homogeneity in the alloys such. Although VAR-melted material represents only a small fraction of the overall metals industry, the products made from these metals are often of the highest criticality. Failure of the parts means catastrophic results, including loss of life.
—Paul E King
1 Delzant, Chapelle, Jardy, Matveichev and Millet -Impact of a Transient and Asymmetrical Distribution of the Electric Arc on the Solidification Conditions of the Ingot in the VAR Process. Metals 2022, 12, 500.
2 https://abc13.com/philadelphia-southwest-airlines-emergency-landing-international-airport/4691167/
3 A contained engine failure is one in which all internal rotating components remain within or embedded in the engine’s case (including any containment wrapping that is part of the engine), or exit the engine through the tail pipe or air inlet.
4 An uncontained engine event occurs when an engine failure results in fragments of rotating engine parts penetrating and escaping through the engine case.
Epoch Wires is pleased to announce their involvement in an Innovate UK research project as part of the “NATEP helping SMEs innovate in aerospace - Autumn 2021” competition. The project entitled “NanoTi - Grain refinement of Ti-6Al-4V wire to enable Aerospace DED AM” is led by Epoch Wires and supported by TWI.
The project aims to design novel-alloy wire chemistry to minimise the grain growth in Ti6Al4V alloys deposited by Additive Manufacturing. In this work, Epoch Wires will produce new wires with a nanoparticle injection, forming equiaxed grains to enhance the mechanical properties of Ti6Al4V alloys. TWI will be depositing the wires using laser, plasma, and electron-beam additive manufacturing techniques. Epoch Wires will be utilising it’s proprietary technology of producing metal-cored wires using continuous laser-seam welding technology, designed for titanium alloys.
The NanoTi project has received funding from Innovate UK under grant agreement No. 10030392.
Innovative and cost-effective titanium wires for the aerospace industry
Laser-seam welded Ti6Al4V wire
Ti6Al4V material deposited using Nano Ti wires, with laser additive manufacturing technology (image courtesy of TWI)
Contact
Serdar Atamert (CEO) serdar.atamert@epochwires.com +44 (0) 7414 866801
Epochwires.com info@epochwires.com Unit 8, Burlington Park, Cambridge, CB22 6SA, UK
in terms of the number events on an annual basis, they are more common than we would like, with “contained”3 and “uncontained”4 engine failures on commercial jet liners happening more than once per year on average in the United States alone.
The VAR process itself is more than 70 years old and has remained relatively unchanged for decades. Although incremental changes in operations have increased product quality over the years, there has been no substantial update to these highly used melting processes since the introduction of video cameras and the development of “drip short control.” Both of these advancements occurred in the last century (1980’s). In 1989, the United Flight 232 airplane crash at Sioux City, IA, caused by an uncontained engine failure, provided a call to arms for the industry. At the suggestion of the FAA, the industry was challenged to improve product quality through better process control. To this day, industry safety committees exist with their roots to that call to arms, specifically the Jet Engine Titanium Quality Control Committee (JETQC). More recently, the American Airlines 383 incident at Chicago’s O’Hare airport in October of 2016 renewed the call to action and the renewal of the Jet Engine Nickel Quality Control Committee (JENQC).
With renewed concerns regarding the quality of the metals going into such critical components as exhibited here, and with the increases in performance that we are asking of our metals as a result of decarbonization and/or supersonic flight, for example, a renewed effort in ensuring higher metal quality is certainly warranted. Ampere Scientific, based in Albany, OR, and founded in 2014,
has been working on this problem for more than two decades. With its early work within the U.S. Department of Energy, the founders were able to successfully develop and demonstrate a new measurement system capable of identifying the types of events within the VAR process that lead to defects in the base metal. Much like a medical magnetic resonance imaging system, this new technology utilizes the varying magnetic fields produced by the VAR to image within the VAR. The (then) scientists at the National Lab realized the power and potential of the technology as a diagnostic tool to increase product quality.
Since 2014, this laboratory experiment has become a robust, industrial process. Coined “VARmetric,” this measurement system is gaining ground as the measurement system for metal quality in titanium (and nickel super alloy) melting via VAR. The system itself mounts to the exterior of the VAR
Figure 3 - Render of an industrial VAR with VARmetric sensors (orange stripes on the bottom portion of the VAR) installed.
water jacket with a static mounting system, and passively monitors the process, sending signals to the control room at a rate of 500 samples per second. This data is then analyzed by a combination of mathematical routines and machine learning algorithms in order to detail the dynamics of the melting system and to categorize these states. It is well documented that the changing states of operation are the root cause of many of the defects categorized by the industry. Yet, the industry state of the art measurements cannot identify these changes in state.
One such state change of major concern to the titanium melting community is the so-called “side arc.” In this case, the plasma arc utilized as the heating source during melting, transitions from between
Titanium Mill Products:
Sheet, Plate, Bar,Pipe,Tube,Fittings, Fasteners, Expanded Sheet & Ti Clad Copper or Steel.
Titanium Forgings and Billet:
Staged intermediate ingot & billet to deliver swift supply of high quality forgings in all forms and sizes including: rounds, shafts, bars, sleeves, rings, discs, custom shapes, and rectangular blocks.
Titanium, Zirconium, Tantalum & High-Alloy Fabrication & Field Repair Services: Vessels, Columns, Heat Exchangers, Piping, Anodes, Custom Fabrications, Field & In-House Reactive-Metal Welding & Equipment Repair Services Available 24/7.
Plate Heat Exchangers:
Plate Heat Exchangers to ASME VIII Div 1 Design, Ports from 1” through 20” with Stainless Steel, Titanium and Special Metals, Plate Heat Exchanger Refurbishing Services & Spare Parts.
Two Service Centers & Fabrication Facilities in Ohio & Texas with Capabilities in: Waterjet, Welding, Machining, Sawing, Plasma Cutting & Forming.
Serving a Wide Variety of Industries: Chemical Processing, Mining, Pulp & Paper, Plating, Aerospace, Power and others.
4-VARmetric data indicating variations in the state of operations during a single melt. State 1 is recognized as an off-center constricted arc; State 2 is an off-center diffuse arc that is oscillating; State 3 is a slightly off-centered diffuse arc that is rotating; State 4 is an off center constricted arc that is also rotating; and state 5 is a centered constricted arc.
the electrode and the ingot to being between the electrode and the crucible wall. This type of event can cause catastrophic failure of the crucible causing a series of staged explosions powerful enough to ruin buildings and leading to loss of life, equipment, production schedules and opportunity.
VARmetric was first introduced as a developmental product in 2015 and as an industrial process measurement system in 2018. Overall, VARmetric provides a passive means of measuring the VAR process, providing critical information and warnings to the control room operators. Action on these warnings can either be integrated to the control systems through the existing PLC gateways, or can be implemented by the operators based upon an analysis of the severity of the warning. For example, centering of the electrode within the VAR is critical to maintaining uniform melt pool
geometry.
VARmetric can measure whether the electrode is centered or not and can either provide the operator a suggested amount to move the electrode in the x-y direction or can be integrated into the control system to automatically maintain a centered electrode. A second example is the case of an onset of a side arc. VARmetric can measure the onset of a side arc and provide a measure of severity of the condition within 10-100 ms. Once the severity threshold is reached, VARmetric can either provide audible alarms or shut the system down to avoid any further catastrophes.
As a measurement system, VARmetric provides superior process information over what exists today. At the end of each melt campaign, a report of product quality is provided and the data archived. Engineers can then recall the data to perform additional analyses as required, investigating such events as arc states, arc locations, transition from state to state, shelf fall-in, etc. As a passive measurement system, VARmetric is recognized as providing valuable information regarding the postprocessed ingot quality. ARControl, on the other hand, is an active control capable of tailoring the heat flux subject to precise quality requirements.
The basic idea behind the
ARControl is to utilize magnetic fields to influence the current conduction within the VAR. This is not a new idea and, in fact, magnetic fields are used every day to manipulate the plasmas in VAR processing of titanium every day. The industry standard use of magnetic fields has been to outfit the VAR water jacket with a solenoid type coil. In this case, the magnetic fields produced are parallel to the current conduction pathway in the electrode and across the arc gap within the crucible; however they are perpendicular to the current conduction pathway within the molten metal pool. Maxwell’s Law clearly defines the force interaction here, where parallel current and magnetic fields do not interact but perpendicular ones do. Because of this, the applied fields have little or no effect on the current pathway except when it is transversing the molten pool. The force applied then instigates a stirring action within the metal pool and hence this configuration is called a stirring coil.
ARControl, on the other hand, does not influence the molten pool as
the magnetic fields are parallel to the current in the molten metal pool. It does, however, influence the current in the electrode and across the arc gap. Because of this, the magnetic field can be manipulated in order to reposition the current carrying arcs, especially across the arc gap. In this manner, ARControl takes a random process (the arc dynamics) and turns it into a process control variable! We can now control the arc dynamics, hence heat flux and solidification. This is all capable now because the motion of the arcs is measurable with the VARmetric. That is, the two systems work in concert with one another.
The figure at right shows overhead images of the arc distribution as measured by VARmetric. In the left image, no control is applied to the system and the arcs move as a stochastic process. Meanwhile, on the right, ARControl was implemented to provide a nine-point star pattern. This heat flux pattern is just one of any number of heat flux patterns and was chosen for several reasons: a) we
desired to maintain a flat electrode tip bottom; b) we desired to have an as close to a uniform heat flux distribution as possible; c) we desired to have the shelf to be washed every revolution so that there was not any shelf buildup; and d) we desired to maintain this through the final, hot topping phase of the melting to reduce the shrinkage and hence reduce the amount of material being cropped.
Overall, in this case, we provided an avenue for the customer to achieve as high as a 13-percent increase in yield through a combination of improved skin quality and decreased cropping. Additionally, in this case, the metal quality proved to be more uniform over their existing operations.
In 2005, Maurer et al[1] indicated the nine key elements of the vacuum arc remelting process that needs improvement in order to achieve
and avoid operating conditions that lead to defects is the VARmetric and ARControl suite.
Today, we demand a tremendous amount of our specialty alloys such as Ti-6Al-4V. For such applications as commercial air transportation, failure of the components is catastrophic and can cause loss of life. To combat this, the industry has adopted a statistical approach to quality driven by regulations and the vast historical data available. Yet, catastrophic events such as uncontained engine failures continue to occur due to the introduction of crack initiation sites during the processing of the base alloys. Ampere Scientific has introduced and validated new measurement and control systems capable of ensuring a defectless metal from the VAR process.
As Ampere Scientific looks to the future, and as we continue to develop the evidence
Product Quality Improvement Through the Application Of Vacuum Arc Remelting Transverse Magnetic Fields (continued)
on how we combat the lingering issues outlined by Maurer et al and deBarbadillo, we are also integrating our measurement and controls system into existing VAR installations. The future promises that we will also provide tighter coupling to new VAR systems, leading the industry to defect-free alloys. n
[1] Maurer, G., Patel, A., Melt Processing of Superalloys: Past, Present and Future Needs, Proc. Liq. Metals Proc. and Casting Conf., 2005.
[2] deBarbadillo, J., The Road to Zero Defects in Nickle Superalloys, Proc. Liq. Metals Proc. and Casting Conf., 2022.
[Editor’s note: Paul E. King is the CEO and president of Ampere Scientific (website: www.amperescientific.com/). His responsibilities include leading the strategic, financial, operational and technical aspects of all Ampere Scientific product lines. King was a speaker at TITANIUM USA 2023 in Denver, presenting a paper on “Control of VAR processing utilizing Transverse Magnetic Fields.” Ampere Scientific is dedicated to the continuous improvement of specialty alloy production and processing. With its collection of sensor and control systems, combined with innovative software suite, Ampere Scientific offers advanced Vacuum Arc Remelting process monitoring and control systems.]
Product Evaluation Systems, Inc. (PES) is a fully accredited, independent leader in titanium materials testing for aerospace and other applications.
With a dedicated, experienced staff and state-of-the-art testing facilities, we offer full-service capabilities for all of your titanium testing needs, including:
• Mechanical Testing
• Metallurgical Analysis
• Chemical Analysis
PES responds to your needs promptly with personal service, customized solutions and expedient turnaround. We work with clients throughout the United States and Europe on projects of all types and sizes.
To request a free quote for your titanium testing needs and to see a full list of capabilities, please visit our website at www.PES-Testing.com or call 724-834-8848.
MACCLESFIELD (U.K.) —
Bodycote, the world’s largest thermal processing services provider, has begun production for its previously reported expansion of Hot Isostatic Pressing (HIP) services in Greenville, South Carolina, USA.
Date: August 2024
Length: 217 Words
capacity now in full production, Bodycote addresses the rising customer demand for highly reliable additive manufacturing post-processing. The capacity is well situated near key customers and other Bodycote locations to simplify the supply chain and reduce transportation. This continued investment is part of Bodycote’s commitment to align resources to serve the North American market.
In recognition of the growing market for additive manufacturing and the associated need for high-quality HIP processing, Bodycote commissioned additional HIP capacity to service the development and processing of advanced materials. Bodycote’s Greenville, SC plant is a Nadcapaccredited site and holds several core OEM approvals. The site consists of numerous vacuum furnaces, aluminum heat treatment, EDM, and other capabilities well suited to support additive manufacturing customers. The Greenville site serves the aerospace, defense, power generation, medical and general industrial customers throughout the Southeastern region.
MACCLESFIELD (U.K.)
Bodycote operates the world’s largest network of HIP equipment. Having established industry expertise over decades, Bodycote has more than 50 HIP vessels of varying sizes in multiple locations. Processing capability can accommodate components nominally up to 6.5ft in diameter by 12ft high, and weighing over 30,000kg.
of thermal processing services. Through Specialist Technologies and classical heat treatment, Bodycote improves the properties of metals and alloys, extending the life of vital components for a wide range of industries, including aerospace, defence, automotive, power generation, medical, oil & gas, construction, and transportation. Customers in all of these industries have entrusted their products to Bodycote’s care for more than 50 years. For more information visit www.bodycote.com.
Bodycote, the world’s largest thermal processing services begun production for its previously reported expansion of Hot Isostatic Pressing (HIP) Greenville, South Carolina, USA.
For more information, please contact: Jamie Kuriger, Regional Sales Manager Email: jamie.kuriger@bodycote.com
Sellersville, PA, June 18 – Solar Manufacturing, Inc. recently announced the hiring of Nicholas Max, BSME Drexel University, as its Chief Mechanical Engineer to head up its vacuum furnace mechanical design group. Nick is also pursuing an MBA at Lehigh University in Bethlehem PA.
Nick will be tasked to lead the further development of Solar Manufacturing’s energy efficient hot zones, vacuum vessels, high pressure gas quenching systems, and vacuum pumping systems. Nick was a Program Manager in his last position and led a team of design
In recognition of the growing market for additive manufacturing and the associated need HIP processing, Bodycote commissioned additional HIP capacity to service the development processing of advanced materials. Bodycote’s Greenville, SC plant is a Nadcap-accredited holds several core OEM approvals. The site consists of numerous vacuum furnaces, treatment, EDM, and other capabilities well suited to support additive manufacturing Greenville site serves the aerospace, defense, power generation, medical and general customers throughout the Southeastern region.
engineers who were focused on the development of specialty battery technologies for space and defense applications.
its excellent reputation as an industry leader of robust vacuum furnace designs.”
With Greenville’s additional HIP capacity now in full production, addresses the demand additive manufacturing post-processing The capacity is well key customers and other Bodycote locations to simplify the supply chain and reduce This continued investment is part of Bodycote’s commitment to align resources to American market
Bob Wilson, VP of Engineering stated, “Nick will be an excellent addition to our design team from his rich, multi-disciplinary industrial experience of the past 10 years. He will work alongside me for the next couple of years as I prepare for eventual retirement. The company will be well-positioned to continue
Bodycote operates the world’s largest network of HIP equipment. Having established industry over decades, Bodycote has more than 50 HIP vessels of varying sizes in multiple locations. capability can accommodate components nominally up to 6.5ft in diameter by 12ft high over 30,000kg – Ends –
Solar Manufacturing designs and manufactures a wide variety of vacuum heat treating, sintering, and brazing furnaces. They also offer replacement hot zones, spare parts, and professional service. To learn more about Solar Manufacturing visit us at solarmfg. com or call 267-384-5040.
With more than 165 accredited facilities in 22 countries, Bodycote is the world's
El Cajon, CA, June 13, 2024 – Solar Atmospheres’ newest acquisition, Solar Atmospheres of San Diego, is pleased to announce the addition of Chris Constable as their new Vice President of Operations. Chris brings with him nearly 25 years of Heat Treating experience that includes quality, operations, management, plant safety, business development, and sales. Chris is well suited to understanding the customers’ needs and providing effective solutions to their most difficult challenges. Coupled with the Solar Atmospheres knowledgeable and dedicated team, Solar
Atmospheres of San Diego stands ready to provide high-quality heattreating services with a focus on honesty and integrity and a reliable customer service experience.
Derek Dennis, President of Solar Atmospheres of California, states, “We are very fortunate to introduce Chris into the Solar Family of companies. As a highly disciplined business leader, Chris has the experience and knowledge to lead the Solar San Diego team through the new acquisition and establish a solid foot hold in the Southern California heat treat and brazing market. I enthusiastically welcome
Chesterfield, MI, July 17, 2024 – After successfully relocating and commissioning ten vacuum furnaces into their current facility, Solar Atmospheres of Michigan Inc. is poised for further expansion. Bulldozers have commenced work on a new 20,000-square-foot building, which will more than double the current footprint at their Chesterfield, Michigan location.
Bob Hill, President of Solar Atmospheres of Michigan, commented, “This expansion will create a larger shipping and receiving area to better serve our customers’ needs and position us for future growth. Come watch us grow!”
For more information about the Solar Atmospheres Michigan facility contact Chris Molencupp at (586) 264-8100 ext. 1620, or chrism@solaratm.com, and visit us at www.solaratm.com.
Chris to the Solar team and look forward to working with him in the growth of the Solar San Diego operation. Truly exciting times for Solar Atmospheres!”
For more information about the Solar Atmospheres of San Diego facility, visit solaratm.com, or contact Chris directly at 619-5933636 ext. 1933, or Chrisc@solaratm. com.
ARIES Manufacturing is dedicated to the supply of complex airframe structure components, in both titanium and aluminum alloys, to leading manufacturers in the aerospace industry.
ARIES Manufacturing is part of the ARIES Alliance, a group of companies focused on developing innovative technology that creates value for the aerospace industry.
Panel mechanical pocket milling, drilling and trimming
Superplastic Forming and Hot Forming for titanium airplane structural and engine components
HSF® process technology for titanium airframe components
We are saddened to announce the passing of Charles “Chuck” Young on June 12, 2024. Chuck was 76 years old and worked at Tricor since 2009. He was born in Pennsylvania and graduated from Carnegie Mellon with a degree in Metallurgy. He also had an MBA from Ashland University. Chuck was a longtime promotor of Titanium. He had worked at several companies where Titanium was their main product. Chuck also served on the board of directors for the Materials Technology Institute. He has written many papers and done many presentations promoting Titanium and other corrosion resistant materials. Chuck will be deeply missed by his many friends and colleagues.
�
�
�
�
�
� EIGA: Ceramicfree Metal Powder Production � VIGA: Inert Gas Atomization Equipment NEAR NET SHAPE TECHNOLOGY COATING SYSTEMS
� EB-PVD SYSTEMS
Electron Beam Physical Vapour Deposition (EB-PVD) of Thermal Barrier Coatings (TBC)
The premier publication delivering key industry insights, technological breakthroughs, and expert analyses to the titanium industry. With a focus on actionable intelligence, each issue provides critical information to navigate the complexities of the market. From in-depth features to exclusive interviews, TITANIUM TODAY fosters collaboration and innovation, empowering stakeholders to stay informed and ahead of the curve in this dynamic field.
7 mins 33 seconds
Average read time in 2023
16,764
Online Reads in 2023
TITANIUM TODAY delivers key industry insights, technological breakthroughs, market trends, and expert analyses to an engaged readership across our online format.
field.
The premier publication delivering key industry insights, technological breakthroughs, and expert analyses to the titanium industry. With a focus on actionable intelligence, each issue provides critical information to navigate the complexities of the market. From in-depth features to exclusive interviews, TITANIUM TODAY fosters collaboration and innovation, empowering
We regularly publish specialized editions of TITANIUM TODAY tailored to the aerospace and medical industries, as well as emerging markets, powder applications, industrial themes, and specialized editions coinciding with titanium conferences.
That’s why when it comes to the design and manufacture or the repair and reconditioning of crucibles, molds, and hearths for your ESR, VAR, EBM, or PAM installations, we draw on our more than 130 years of design, engineering and manufacturing excellence to ensure that your copper-based melting equipment is operating at peak efficiency.
A reputation for quality work and on-time delivery.
Our staff of expert millwrights, welders and machinists can tear down, assess, repair and test your valuable melting equipment. Additionally, our manufacturing capabilities are fully supported by our staff of over 50+ engineers. Our services include:
• Machining, welding, straightening, and sizing of stainless steel, copper, nickel, aluminum, bronze, and carbon steel
• Preventative maintenance, including cleaning, re-sizing, straightening and seal replacement
• Crucible diameter and size modifications
• New crucibles, molds, base assemblies, water jackets, etc.
To learn more about our rebuilding and manufacturing services,call (330) 337-0000, visit www.ButechBliss.com or email cu@butech.com.
A. W. Bell
Accushape Inc.
ACNIS® International
Advanced Metal Industries CO (AMIC)
Aerolloy Technologies Limited – A PTC Industries Company
Aeropro Industries
Airbus
ALD Vacuum Technologies, Inc
Alleima Tube AB
All-Met Recycling
Alta Alloys
AMC LLC
Aries Manufacturing
ASIIC UK LTD
ATI
ATX Co.,Ltd.
Bahco
Banner Industries (Merged with Castle)
Baoji Hongsen Titanium Metal Manufactory Co.,Ltd
Baoji Sino-Swiss Titanium Co.,Ltd
Baoji Titanium Industry Co., Ltd
Bodycote
Boeing Company
Butech Bliss
Carpenter Technology Corporation
Chengde Tianda Vanadium
CKOE
Consarc Corporation
Consolidated Engineering Company
Coogee Titanium PTY LTD
CSM Tech Co., Ltd.
Dr. Markus Holz, Academic Member
Duferco SA
ELG Utica Alloys, Inc.
Fort Wayne Metals
FRIGGI N.A. Inc.
GfE Metalle und Materialien GmbH
Goldman Titanium
Grandis Titanium
Greystone Alloys, LLC
Hempel Special Metals AG
Horie Corporation
Howmet Aerospace
Hunan Xiangtou Goldsky Titanium Metal Co., Ltd.
ICD Alloys & Metals, LLC
Independent Forgings & Alloys Ltd
Industrial Metals International Ltd.
Inteco Melting & Casting Technologies
IperionX Limited
Jezhiang Shenji
Jiangsu Hongbao High-Precise Pipe & Tube Co., Ltd.
Kamet
KASTO Inc.
Keywell Metals LLC
KineTic Engineering
Kings Mountain International (KMI)
Kittyhawk
Kymera International
Laboratory Testing Inc.
Leybold USA Inc
Lockheed Martin Corporation
M3 Metals
Medart Processing Technologies
Mega Metals LLC
Metals & Alloys UK
MetCon Technologies, LLC
Metraco, FE Mottram and Eesti Titaan oü
Mistras Group, Inc.
Monico Alloys, Inc.
Mott Corporation
MPS Technology Sp. Z o.o.
NobelClad
NSL Analytical
Nu-Tech Precision Metals
Oerlikon Metco (Canada) Inc.
Osaka Titanium technologies CO., Ltd.
Paris Saint-Denis Aero
Perryman Company
Plaxys Inc.
Plymouth Engineered Shapes
Precision Abrasives
President Titanium Co., Inc.
Product Evaluations Systems, Inc (PES)
Quantum Design Inc. / Centro Metalcut
Retech Systems LLC
Rex Heat Treat
Rolled Alloys Inc
Ross Precision Manufacturing
S+D Metals / Bibus Metals
Service Steel Aerospace
SES, LLC
Shaanxi Lasting Titanium Industry Co. Ltd
Shaanxi Tian Cheng Aerospace Co., Ltd. (TCAE)
Shasta Services LLC
Solar Atmospheres
Specialty Metals Company
Specialty Metals Processing Company
Star Group, India
State Nuclear Baoti
STRUCTURAL DIAGNOSTICS, INC.
STS Metals
Sumitomo Corporation of Americas (SCOA)
TiFast Srl
Timesavers International B.V.
TIMET, Titanium Metals Corporation
TITAN Metal Fabricators, Inc.
Titanium Consulting & Trading S.r.l.
Titanium Engineering
Titanium Fabrication Corporation
Titanium Industries, Incorporated
Titanium International Group SRL
Titanium Processing Center
Toho Titanium America Co., Ltd.
Tricor Metals
Uhr Corp.
Ulbrich Stainless Steels & Special Metals
United Alloys & Metals Inc
United Performance Metals (UPMET)
United Titanium
US Vanadium
Vested Metals International, LLC
VSMPO Tirus US
Weber Metals
Weiler Abrasives Group
Wellmet International Inc.
Xi’an Metals & Minerals Import & Export
XI’AN XRUN NEW MATERIAL
Yunnan National Titanium Metal
INTECO is your rst choice for cutting edge plant technology and process know-how for melting, rening, casting, atomization and solidi cation of high performance steels, super-alloys and titanium.
Are you aiming to increase the recycling rates in your titanium production shop?
INTECO´s new innovative vacuum arc cold hearth skull melting and casting furnace ...
› can achieve recycling rates of up to 100% by feeding virgin and scrap material (e.g. compacted chips) between melting & casting cycles
› can achieve an improved energy ef ciency compared to other cold hearth technologies
› allows static casting of ingots and slabs as well as dynamic casting of complex investment cast parts
› can achieve pouring weights from 250kg up to 2.500kg in one cast
› More than 15 years of experience as a premium supplier in the titanium industry
› Supply of melting and casting equipment for titanium including auxiliaries
› Engineering studies, project- and technology consulting for entire titanium production lines
› Know-how transfer, from selections of raw material up to aerospace certi cation
› Customized process and production management systems (IMAS) for titanium production lines
https://www
https://www
Our continued investment and expansion has us in the right place to meet your needs.
Our capacities and resources are aligned. We are prepared and well positioned to supply a full range of products including ingot, centerless ground bar, precision coil, additive wire, premium fine wire and shapes – all at competitive lead-times.
We are expertly equipped to address the growing demands of the aerospace, medical, recreation, infrastructure, and industrial markets worldwide. We understand the ever-changing factors of the industries we serve and are committed to supporting the growth of your business.