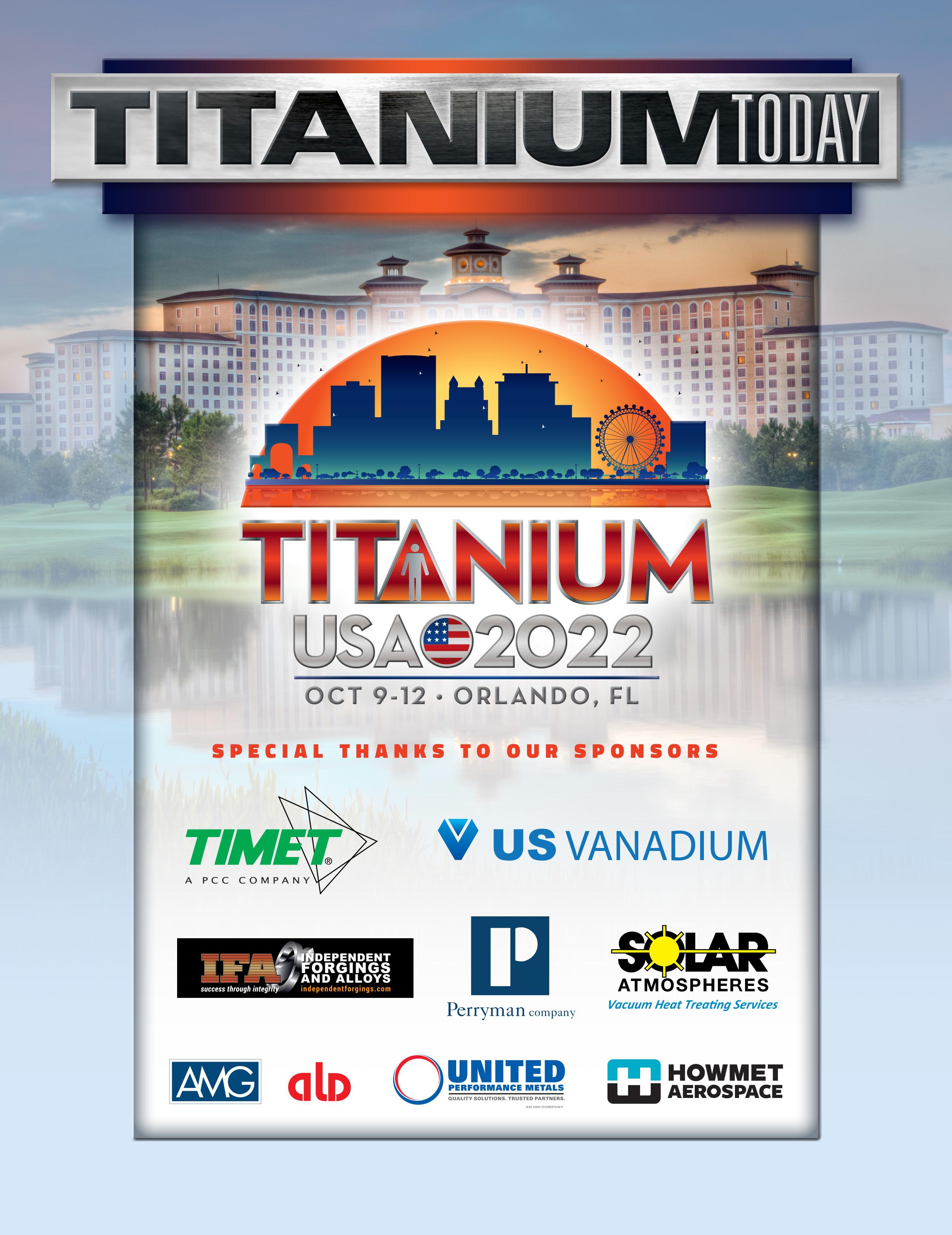
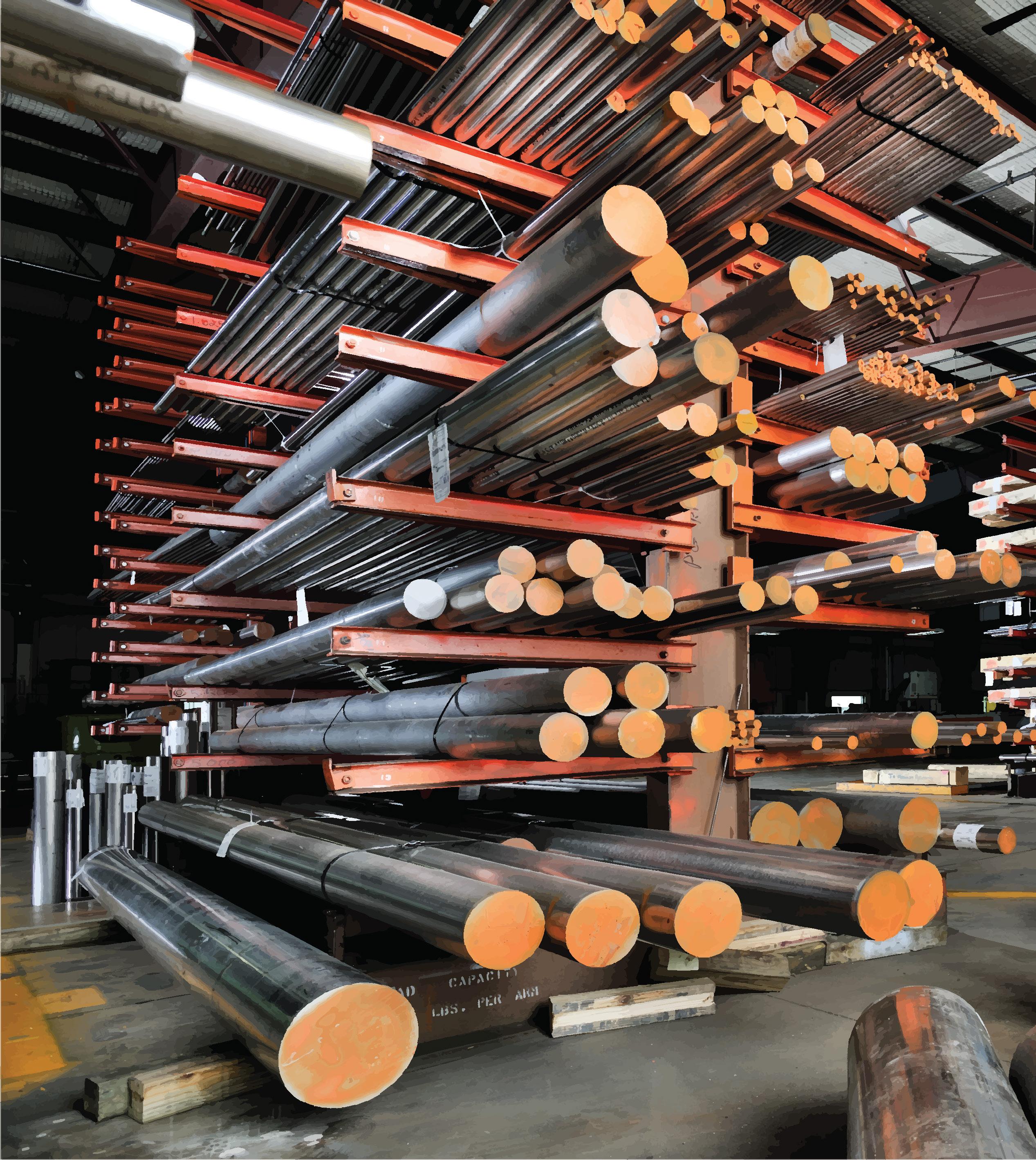
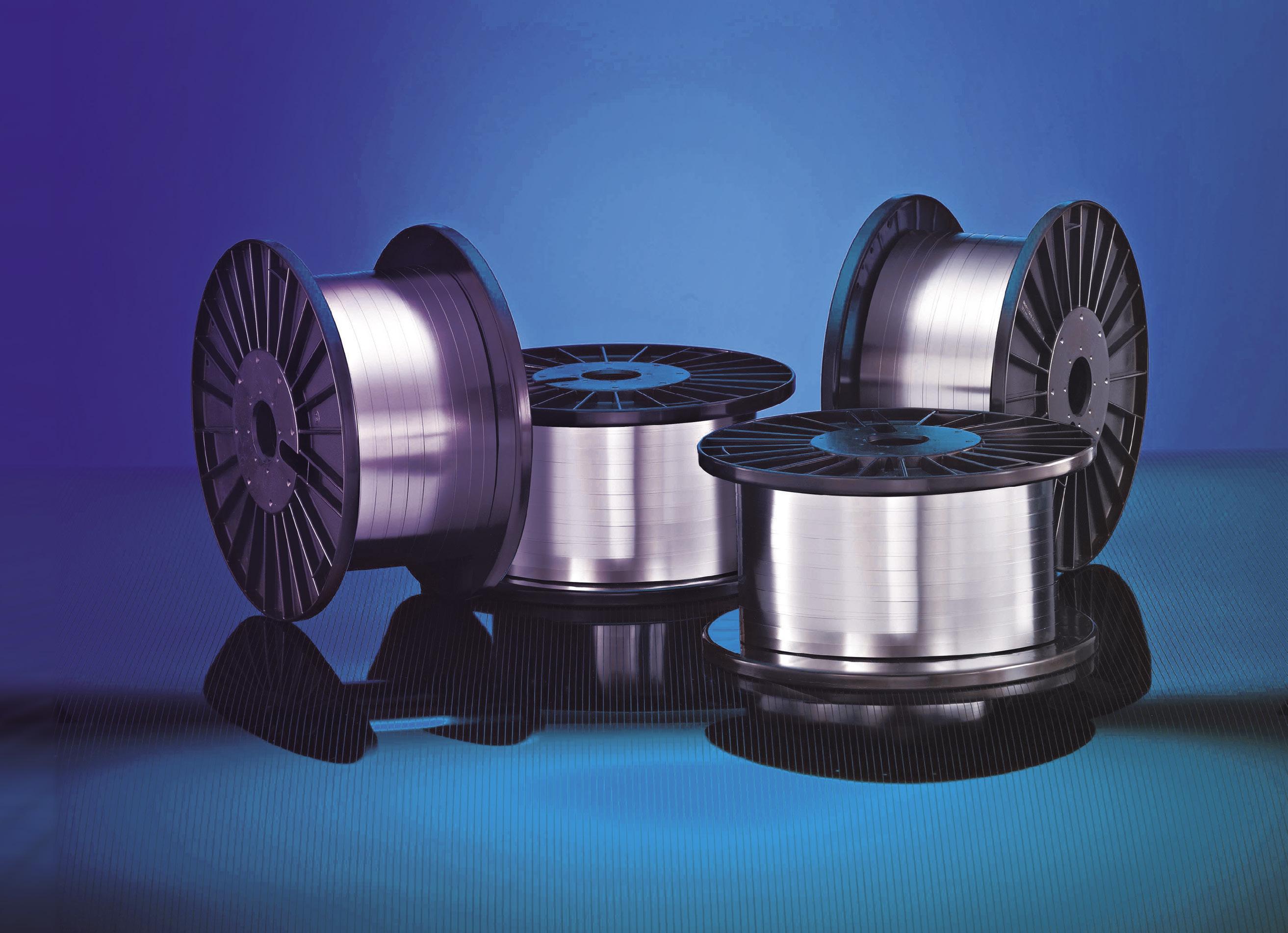
Editor
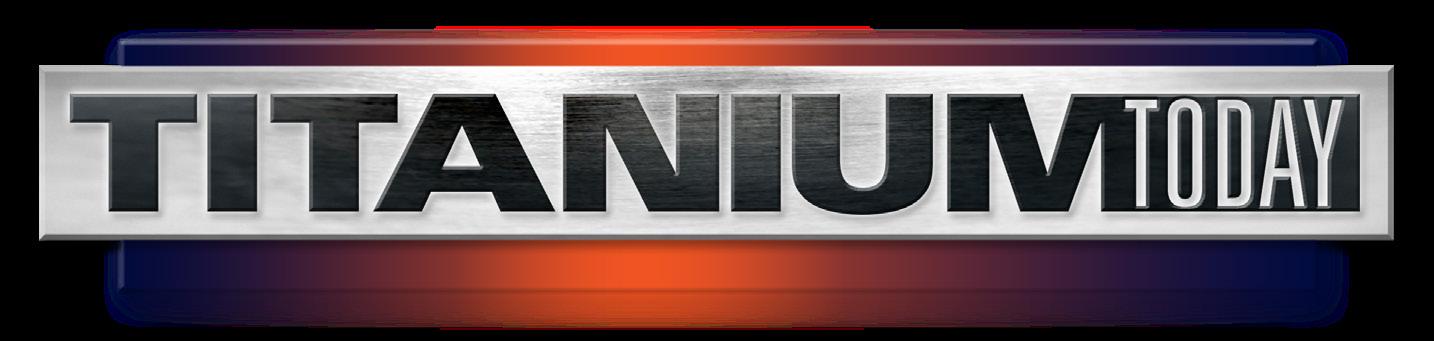
Director:
Box
80614-1300
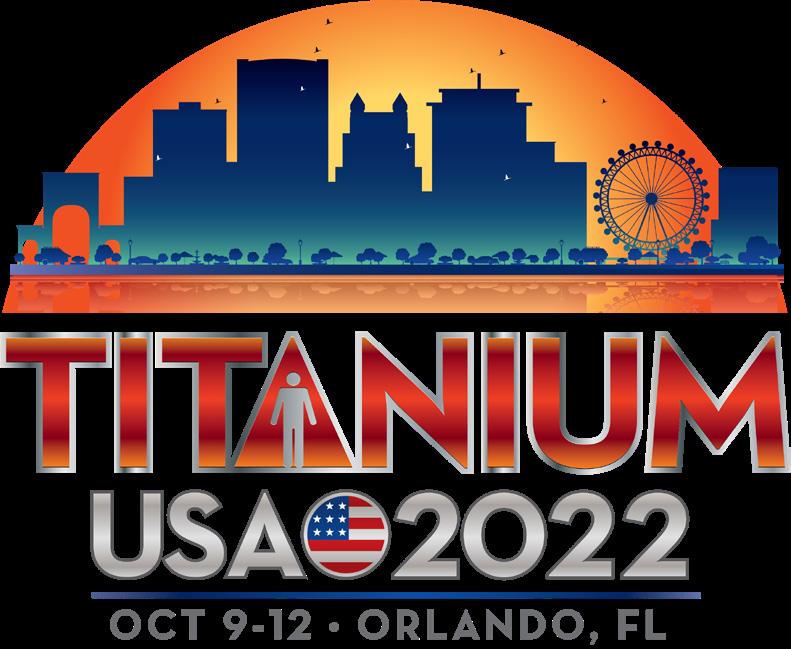

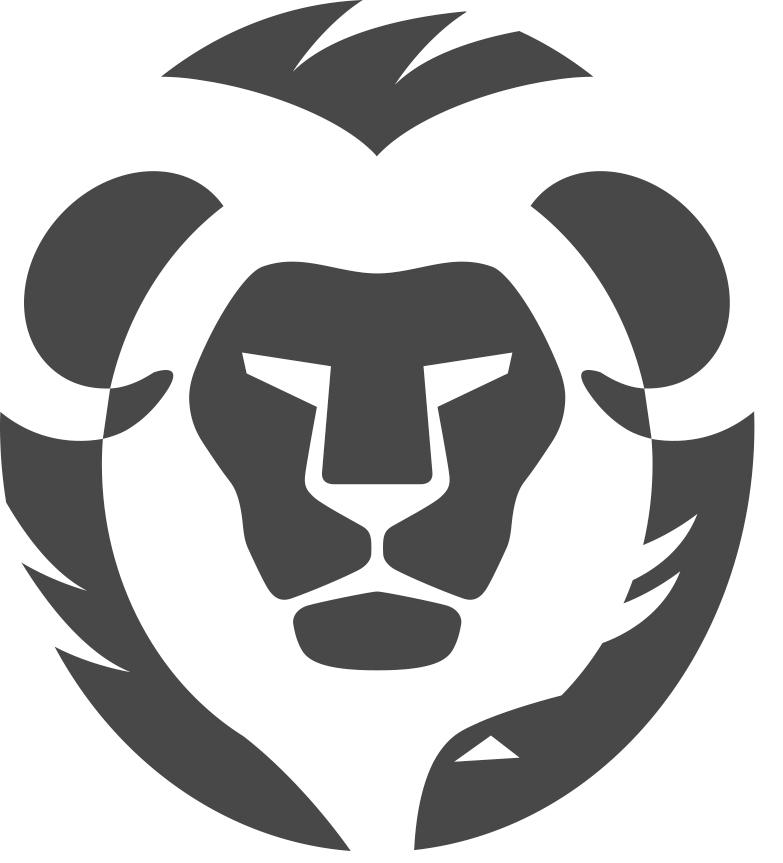
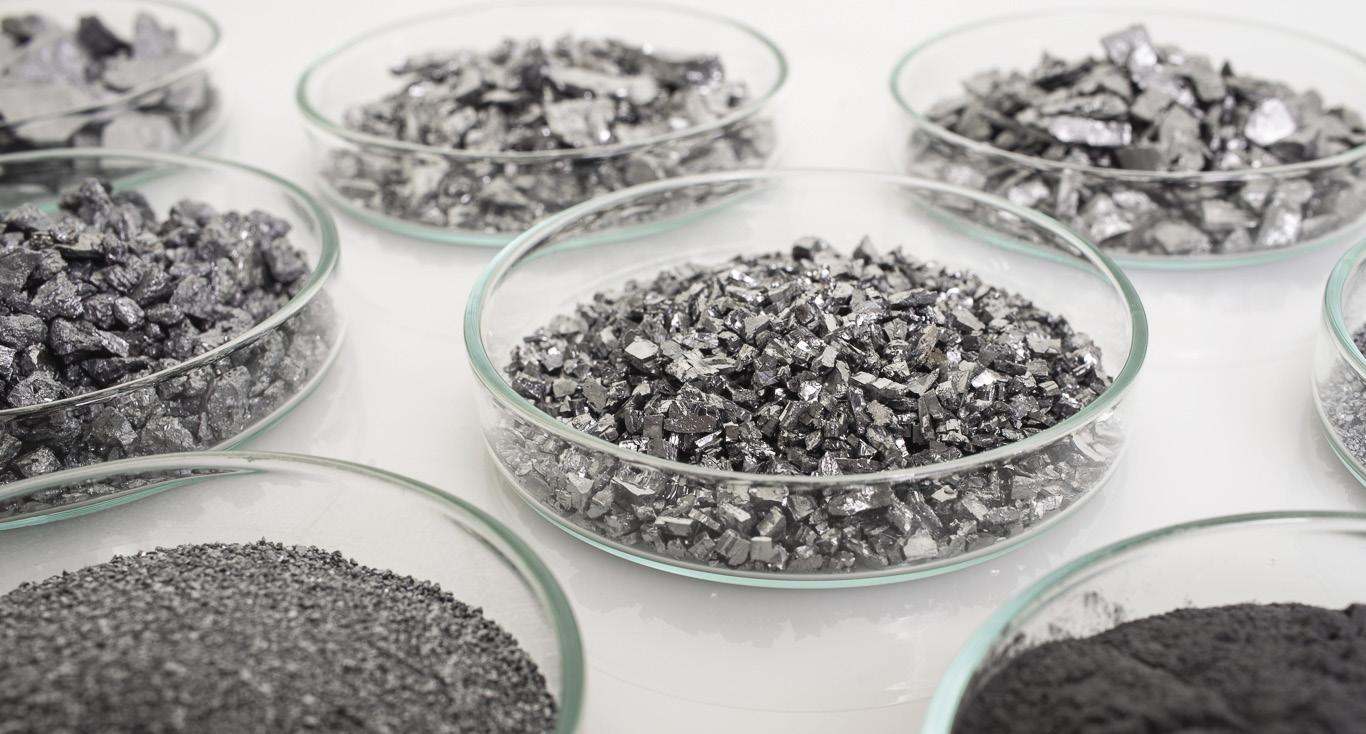

Editor
Director:
Box
80614-1300
Mr. Perryman graduated from Millikin University in 1986 with a Bachelor of Science in Industrial Engineering. In 1988 he co-founded Perryman Company with his father and brother. Since December of 2008 he has held the position of President and CEO of Perryman Company. Perryman Company is a fully integrated supplier of specialty titanium products. From melting through finishing, founded in 1988, Perryman Company is headquartered in Houston, Pennsylvania, with office locations in Philadelphia, Los Angeles, London, Zurich, Tokyo and Xi’an. Perryman is an integrated titanium producer from melting of ingot to finished products. The company’s product portfolio includes ingot, bar, coil, fine wire, net shapes, and hot rolled products. The Forge and Fabrication group offers medical device contract manufacturing in a range of materials including plastics and titanium. A titanium global leader, Perryman supplies and services customers in the aerospace, medical, consumer, industrial, recreation, additive/3D printing and infrastructure markets worldwide.
ITA Vice President 2020-2022
Dr. Markus Holz is presently an industry consultant. Formerly President of AMG’s Engineering Systems Division and CEO of Vacuum Technologies GmbH from 2012 to 2019. He joined the ALD Management Board in October 2011. Dr. Holz graduated in Aerospace Engineering in 1986 and earned his PhD in 1992. Following his 10 years of service in the German Airforce, Dr. Holz began his career with ThyssenKrupp in 1992, where he assumed several executive positions mainly in the stainless steel and special metals branch. In 1999, Dr. Holz became Managing Director of ThyssenKrupp Titanium GmbH (formerly Deutsche Titan GmbH) and in 2002 he was appointed Managing Director of ThyssenKrupp Titanium S.p.A. (formerly Titania S.p.A.). Furthermore, he was responsible for Tubifi cio di Terni, Italien, from 2004 through 2007. From 2007 to 2009 he was CEO of the ThyssenKrupp Titanium Group (Germany and Italy). In January 2010 he joined the Managing Board of Hempel Special Metals, Oberhausen, Germany. He is Honorary Professor at University of Applied Sciences Anhalt Teaching Operations Management.
Vice President - Commercial ATI Specialty Materials
ITA Secretary/Treasurer 2020-2022
Martin Pike is the Vice President - Commercial for ATI Specialty Materials with responsibilities which include international product management, sales, and long-term agreements with customers. Martin joined ATI in August 2001 and held several positions with increasing responsibility including Titanium Rolled Products, Product Manager and Director of Sales. Prior to joining ATI, Martin worked in manufacturing where he held various commercial positions including Regional Vice-President of Sales. His educational background includes a Bachelor’s Degree from the University of North Carolina at Charlotte.
Donald E. Larsen
President, KineTic Engineering
ITA Past President 2020-2022
Donald E. Larsen is currently President of KineTic Engineering a consulting firm that provides expertise across the Titanium industry. Prior to this he spent over 30 years at Howmet Aerospace/Arconic retiring in 2018 as Vice President, R&D, General Manager Advanced Manufacturing for Arconic. In this role, he was responsible for leading R&D and production teams working on priority titanium technology projects, including 3D printing and advanced manufacturing activities. He also served as a liaison to the Arconic Technical Center (ATC) and Arconic’s Whitehall Technology Center. Don retired in Q3 of 2018 and temporarily took on the role of Interim Plant Manager Ti-Ingot Operation and Director of Special Projects.
Don joined the Howmet Aerospace in 1988 and served in a number of roles focused on the research, development and production of titanium products. He has also held operational and sales and marketing roles with the company. Don has a master’s degree in metallurgical engineering from The Ohio State University, and is the holder of 11 U.S. patents. He has published more than 30 technical articles in the field of titanium.
Professor, ITA Academic Member Education Committee Co-Chair
Titanium Europe Conference Chair
Chief Technology Officer Kymera International
Edward Sobota Jr. President TSI Titanium
Vice President, the Americas PCC Metals Group Global Sales
Sam Stiller
Vice President – Commercial Howmet Structure Systems
Brett Paddock
President and Chief Executive Officer T .I . (Titanium Industries, Inc .)
Michael Stitzlein President Tricor Metals
John J. Scherzer
Vice President – Medical Markets Carpenter Technology Corporation
Jennifer Simpson Executive Director, Ex-Officio Board Member
Robert G. Lee President Accushape Inc . Industrial Applications
Robert Henson
Manager, Business Development VSMPO-Tirus, US
Women in Titanium Holly Both Vice President of Marketing Plymouth Tube / Plymouth Engineered Shapes
(This is the fourth in a series of annual guest articles by Tom Captain, offering his insight and observations on the commercial aerospace industry.)
Just when it looked like the aerospace industry was overcoming the setbacks from the Covid-19 pandemic, along comes the labor shortages, supply chain crunch, high fuel costs, war in Ukraine, and high inflation. Will the predicted recession dash any hopes of a recovery in the industry? Let’s look at what has happened since we wrote in August 2021 about the industry’s prospects for recovery, and offer some new predictions.
In August 2021, in Part Three of this series, we forecasted aircraft sales and production to return to its prepandemic levels by early 2023, which is now roughly six to nine months away. That would mean that industry
original equipment manufacturers (OEMs) would sell about 1,800 large commercial aircraft annually and production would return to about 1,600 aircraft per year. Is that prediction still on course or will we see another nosedive or something less severe?
The pandemic and its impact
As of this writing, the global official death toll from the pandemic is estimated by the World Health Organization (WHO) to be 6.5 million, on a base of 550 million infection cases, but others indicate the impact is much larger. However, with
increased levels of vaccinations, the death toll has significantly been reduced. It’s estimated that 5.2 billion people have been administered at least one vaccination dose, almost three-quarters of all humanity, and recent reports indicated that vaccinations have been responsible for averting another 20 million deaths. This is a remarkable achievement of science and technology.
The following WHO chart illustrates the remarkable rate of vaccination globally, a key to recovery of the airline industry and their suppliers:
Since our writings of last August, the airline industry has staged quite a rebound from a pandemic low of 10 percent of normal flight operations, being 2019. Average load factors are
increasing dramatically, especially in the domestic markets approaching pre-pandemic levels in Europe and the US, but less so in the Asia Pacific region. In 2021 according to IATA,
global domestic traveler numbers were 61 percent of 2019 levels. International travel was 27 percent of 2019 levels.
*Note: green are highly vaccinated countries; red are low vaccinated countriesTom Captain
The impact of the pandemic has been existential, not only due to the freefall in demand for air travel, cancellation of aircraft orders, but also due to the Boeing 737 MAX crashes and its aftermath, and production challenges on the 787 program. Never in the history of commercial jet powered commercial aircraft has the industry experienced the magnitude of its circumstances. The following chart illustrates the dramatic fall in production in 2020 and 2021, especially when compared to 2016 thru 2018. Also note that the industry order activity also experienced a steep nosedive 2019 thru 2021, with a nascent recovery starting in 2021.
Aircraft
2,036 2,858 2,888 1,848 1,078 2,021 1,640 681 -203 1,042
1,189 1,274 1,352 1,397 1,436 1,481 1,606 1,243 723 951
Production Change 17.6% 7.1% 6.1% 3.3% 2.8% 3.1% 8.4% -22.6% -41.8% 31.5%
green numbers are peak order and production years; red are pandemic low years
Recovery, albeit halting, of commercial aircraft production in 2021 and the first half of 2022 is due to recovery of air travel demand. This has been largely due to the progressive removal of restrictions by governments, as more people are vaccinated, infection rates decrease and the realization of the economic and social hardship damage that is caused by travel restrictions. Although masks are still required in many markets, additional testing requirements have been removed for international travel by many countries. Air travel is on the rebound.
Load factors may be up, but passenger counts aren’t as high as would be expected in a rebound. This is partly due to cancelled flights and reduced operating capacity of airlines. Much of this is due to the shortage of available pilots and operations personnel. During the pandemic, many pilots, and flight crew were furloughed due to the significantly reduced demand for travel during the pandemic. Some simply retired by taking advantage of buy-out packages. Also, many aspects of the labor market changed, such as working from home, “quitting,” sitting out and people moving to
remote areas due to their ability to work from anywhere – the online “Zoom” effect.
This has had a large impact on personnel available to fly those commercial aircraft, resulting in many routes being temporarily curtailed or worse yet, flights being cancelled. Coming back from furloughs is tough. Pilots are required to maintain currency in competence to fly those aircraft, and required recurrent training after returning from furlough, which takes time to become recertified.
Who would have thought within the span of 2 years, the industry could go from a mass furlough scenario to one where airlines are paying hiring bonuses due to the shortage of staff. As of mid-year 2022, cancellations and delays have become the norm for major US based airlines, with a sampling of data below:
situation may not improve in the short term, as witnessed in some recent headlines:
• “American Airlines CEO says it will hike pay for 14,000 pilots even higher than originally proposed, as the industry faces a crippling labor shortage”
• “Summer travel might not take off as expected due to ‘challenging’ labor shortages, pilot warns”
• “Pilot shortages add to U.S. travel chaos as airlines struggle to meet demand”
In general, aerospace supply chain companies also had labor shortage problems, due to similar causes cited above. This has led to operating capacity constraints on aerospace suppliers, which caused a significant and unprecedented impact on the global aerospace supply chain. The gradual return to service of aircraft over the last two years has resulted in an uneven return of the aerospace supply chain, due to shortages, labor adjustments, training issues and loss of “corporate memory.”
For the maintenance, repair and overhaul (MRO) industry, the pandemic-induced fall in flight hours reduced demand for parts during the last two years. With so many aircraft grounded, airlines swapped
out aircraft and green-time engines to avoid maintenance. Purchase of new parts was stopped or delayed by aircraft operators and MRO organizations to reduce costs, which severely impacted the aftermarket supply chain of sales revenue. The starvation, albeit temporary, of the commercial aerospace supply chain industry serving the OEM and aftermarket business, created a void, and it created a delay to reenergize the industry in order to restore its functionality.
However, the more insidious and potentially existential threat to the industry is the Ukraine war and its impact on titanium supplies. The escalating conflict between Russia and Ukraine is fueling concerns in the aerospace supply chain, with key producers of raw materials, metal and alloy located on both sides of the border serving global customers. Sanctions and embargoes could threaten a substantial portion of the titanium sponge market. VSMPOAvisma based in Russia, is the largest titanium producer in the world, with an operating capacity of 34,000 tons per year, with a 20-percent global market-share. They supply a large portion of titanium used by aircraft OEMs in their products.
However, engine makers for Boeing Co. and Airbus SE jets are working to diversify sources of titanium away from major suppliers in Russia, as the conflict in Ukraine threatens access to the metal needed to make critical plane equipment. Suppliers and OEMs are increasing their backstock of materials, investigating alternative sources and utilizing advanced technologies.
Russia’s invasion of Ukraine is
a major reason that aircraft fuel prices have increased. Russia is one of the largest oil exporters globally. In December it produced an estimated eight million barrels of oil and other petroleum products for global markets, five million of them as crude oil, however, very little of that went to the United States. An estimated 60 percent of Russian oil in 2021 went to Europe and 20 percent went to China. However, a key reason for high oil prices is that oil is a global commodity and is priced accordingly. Thus, the loss of Russian oil impacts prices globally, no matter its location of use.
Other reasons for the crude oil price spike include the ferocious rebound of demand. Oil prices plunged when stay-at-home
restrictions crushed demand in the second quarter of 2020, when crude was trading very low. As a response, OPEC members and Russia, drastically cut crude oil production to support prices. Demand returned sooner than expected, but they kept crude oil production low creating an imbalance.
During the pandemic, a factor keeping oil prices low was the surge of Covid cases, and the especially strict lockdown rules in China. Given its significant global thirst for oil, China’s significant drop in demand for oil contributed to low global prices. As Covid started to retreat, lockdowns are being lifted in major cities such as Shanghai. A rebound in oil demand in China, without the aforementioned
Is it Time for an Aerospace Ascent, or Another Nosedive? (continued) Supply chain shortages of titanium will continue to be an issue, as regulations regarding the use of restricted materials from foreign suppliers may become a problem, with potential further restrictions from Russia. OEMs and engine manufacturers will have implemented adequate risk-mitigation measures such as alternate titanium sources to meet increased demand for aircraft production. The aerospace industry is resilient and will not only survive but eventually thrive on the demand for air travel. That is reason for hope.
increased supply, has contributed to the oil price increases.
However, to put this in perspective, the price of oil has significantly increased of late, but on an inflation adjusted basis, we are returning to the levels experienced from 2014 thru the early 2020, before the pandemic started. Despite this, increased fuel costs are certainly impacting the costs for flying and airlines globally are increasing passenger fares to recover this increase in costs. On April 24, 2020, the price of a barrel of West Texas Intermediate Crude Oil (WTI) was $20.89. On June 24, 2022, the price of a barrel of WTI is $107.62 for a whopping 515-percent increase.
services in the general economy, there is concern that we will experience a recession in the near term. As the U.S. Federal Reserve and various central banks globally come to terms with how high and how soon to increase interest rates, there will be a careful balancing act without going too far and tipping the global economy into recession. Time will tell if demand and supply can reach equilibrium in a non-destructive manner.
A recent cause for optimism is the nascent trend in reduced oil prices in the mid and late summer, caused by lowered demand, which in turn are caused by high prices at the pump, recession worries and increased interest rates.
Notwithstanding the above discussion regarding increases in labor pay and oil prices, there is a general imbalance of supply and demand throughout the UK, United States and global economies. This in turn is causing generalized economic inflation in many countries. In the United Kingdom, the inflation rate as of June 2022 was a whopping 9.4 percent. In the United States, during the same period, the annual inflation rate was 9.1 percent, the highest monthly rate since 1981. To put this in perspective, the average CPI index inflation rate from 2015-2021 was 3.01 percent annually. The following chart illustrates the dramatic increase in inflation rates in just the last two years:
Pilot shortages should be largely addressed by early to mid-2023, with completion of recurrent training for furloughed pilots and entry to the workforce by student pilots undergoing flight school training. Increased pilot pay should draw others such as from the military, general aviation and private pilots to the industry. This in turn should reduce cancelled and delayed flights, as well as open up routes that have been cancelled. Recent headlines underscore the efforts underway:
• “United opens flight school, airlines find creative solutions as industry faces looming pilot shortage - United projects the academy to recruit 5000 pilots by 2030”
• “Delta tries to fix the national pilot shortage and accelerate training using private charter company in new partnership”
• “Airlines Are Rushing to Train New Pilots After PandemicCaused Shortage”
Inflation is not a theoretical concept, but a real one for the aerospace industry. The prices of labor rates for pilots, mechanics, and suppliers are rising. The prices of new and used aircraft, MRO services, supply chain parts and systems are rising. The price of jet fuel is rising. This in turn translates into higher prices for airline tickets. This is turn is likely to moderate demand for travel. As demand is reduced not only for airline travel but for goods and
• The Montreal-based International Air Transport Association (IATA) predicts air travel to rebound almost fully by the end of 2023 and grow beyond pre-pandemic levels by 2024, as illustrated in the following chart:
chain shortages of titanium
continue to be an issue, as regulations
the use of restricted materials from foreign suppliers may become a problem, with potential further restrictions from Russia. Shortages of machined parts, subassemblies and systems will start to be alleviated as the industry works out its own labor shortages. Orders for materials should improve as the supply chain network works toward supply/demand equilibrium. OEMs and engine manufacturers will have implemented adequate risk mitigation measures such as alternate titanium sources, and increased back stock in place to meet increased demand for aircraft production. Thus we expect that many of the key supply bottlenecks that impact aircraft OEM production progress will get back to a “new normal” in the late 2023 and early 2024 timeframe.
predict domestic commercial airline travel to improve to 90 percent of 2019 levels by yearend 2022 and international commercial airline travel to improve to 70 percent by year-end 2022. We predict globally that over four billion passengers will be flying annually by late 2024 and early 2025, over nine trillion revenue passenger kilometers (RPKs) will be flown, with over 100,000 flights taking to the skies globally per day. All this again would return the industry to 2019 levels or better - back to the “new normal.” We expect by 2025 to see global aircraft OEMs to produce over 1,600 aircraft annually. Thus, it will have taken 5 years for the industry to recover to the 2019 levels of economic activity.
With the “interruptions” as described above to the recovery from the pandemic, the aerospace industry is facing a delay, not a backward step. We do not foresee a “nosedive”, but rather a halting and delayed recovery, moving in a positive direction. After all, there is an insatiable appetite for family, business and leisure passenger travel, and for air cargo due to the internet shopping and “Amazon” effect. The pandemic itself was an interruption, as was the subsequent fuel price increases and labor shortages, not to mention the Ukraine war, and production delays on the 737 MAX and the 787 programs, plus the possibility of a recession in late 2022 and early 2023. The industry is resilient and will not only survive, but eventually thrive on the demand for air travel—it always has. That is reason for hope. n
(Editor’s note: Tom Captain is the managing director of Captain Global Advisory, LLC, headquartered in Mercer Island, WA, and is a 40-year industry veteran and expert in the aerospace, defense and space sector. He is the retired vice chairman of a Big Four consultancy where he led their global industry practice. Captain currently serves on the boards of several industry-related organizations.)
The North American forging industry, including companies operating in the titanium sector, have quietly been investing in an automation renaissance during the last four years—an effort that’s expected to continue through the foreseeable future to modernize the industry’s manufacturing technology.
Jim Warren, the president and chief executive officer of the Cleveland-based Forging Industry Association (https://www.forging. org), said this automation renaissance is fulfilling the organization’s outlook filed in a report titled “Vision of the Future—Technology Initiative,” which was published two years ago. That report laid out a technology roadmap for the forging industry to keep pace with competitors in Asia and Europe.
“New knowledge must be developed and applied industrywide through specific research and development that focuses on bulk deformation sciences and engineering technologies so that more cost efficient and higher performing products and processes are developed,” the report stated. “Partnerships between the forging industry, federal laboratories, universities, and vendor companies must be formed to share information on integrated computational tools, advanced modeling, and automation techniques. Advancements in computer modeling, sensors
and controls, and technology for intelligent manufacturing are other areas in which developments could be applied to benefit the forging industry as well as several other vision industries.”
Warren underlined three key areas of automation being adopted by the forging industry. The most forward-thinking of these is the use of a “digital twin,” a technology that runs parallel with a factory floor forging operation. He said this digital twin can track the manufacturing operation in real time and anticipate potential system disruptions before they occur.
A Jan. 28 online article posted by Forbes.com (“How To Reinvent Continuous Improvement With Intelligent Digital Twins In Manufacturing”) explained that the unfolding “fourth wave” of a global industrial revolution is being realized “through the use of various technologies, including intelligent digital twins that
allow for real-time monitoring of a machine’s condition, artificial intelligence that can analyze large amounts of data to produce actionable insights, and connected devices that provide live status updates.”
“Intelligent digital twins are software models that closely resemble the real-life counterpart they are based on,” Forbes reported. “The twin is fed information from various sources, including sensors, monitoring equipment, and software programs. This digital twin constantly learns to provide the latest updates on the physical machine’s health based on observed conditions. As intelligent factories become a reality, they will enable
continued investment and expansion has us in the right place to meet your needs.
capacities and resources are aligned. We are prepared and well positioned to supply a full range of products including ingot, centerless ground bar, precision coil, additive wire, premium fine wire and shapes – all at competitive lead-times.
are expertly equipped to address the growing demands of the aerospace, medical, recreation, infrastructure, and industrial markets worldwide. We understand the ever-changing factors of the industries we serve and are committed to supporting the growth of your business.
the manufacturing industry to shorten delivery cycles, reduce the cost of production and improve product quality through real-time insights.”
A second area of automation involves improvements in nextgeneration digital forging simulation systems, used off-line at the front end of the manufacturing process. Simulation systems can predict how a titanium billet is likely to flow inside a forging die, based on factors such as the die design, time, temperature and pressure. Warren said simulation systems can help streamline the forging process, as well as offer a guide to extend the life of a die. These systems also can simulate the heat treating process, which is especially significant to maximize the quality and integrity of forged titanium parts.
Warren said a third area of forging automation can be found in the incremental upgrades to factory floor material handling systems, enhancing the accuracy, safety and repeatability of robotic and conveyor equipment in transporting a heated titanium billet to the forging press. In addition, the forging industry is migrating to induction electrical heating systems, gaining the benefits of more precise heating control of billets, compared with more traditional gas-fired furnaces.
While commercial aerospace remains a dominant market for titanium forgings for the production of landing gear, advanced engines and aero structures, opportunities continue to emerge in military applications. Aside from military aircraft, the Defense Logistics Agency of the Department of Defense is
focused on light-weighting weapons and military equipment. For example, The New York Times, in a pageone, May 23 story, reported that American-made M777 howitzers are being shipped to support Ukraine.
The lethal American howitzers “are chunky machines of steel and titanium swathed in hydraulic hoses and perched on four braces that fold up and down.” The lightweight weapons are appreciated on the battlefield for their maneuverability, but also from the perspective of strategic military logistics—the ability to transport and deliver the equipment via long-distance cargo planes.
Warren acknowledged that the U.S. forging industry, compared with global competitors, has “legacy” issues, given its heavy level of investment in older equipment. “China has a fully automated forging industry. Europe changes out its forging equipment more often than the United States.” The Forging Industry Association’s “Vision of the Future” document outlined these challenges and charted a road
Jim Warren, the president and chief executive officer of the Forging Industry Association, underlined key areas of automation being adopted by the forging industry. The most forwardthinking of these is the use of a “digital twin,” a technology that runs parallel with a factory floor forging operation. He said this digital twin can track the manufacturing operation in real time and anticipate potential system disruptions before they occur.
map for this industrial group. “The forging industry is a key link between critical manufacturing segments— metal suppliers (both ferrous and nonferrous) and end user industries. Forgings, which appear in 20 percent of the products representing the gross domestic product of the United States, are essential to the U.S. industrial economy, its society, and its national security. In recent years the U.S. forging industry has undergone significant shrinkage associated with intense global competition, technological changes, and environmental and economic
factors. Those companies that survived the industry downsizing emerged stronger and better equipped to face the competitive challenges of manufacturing today.”
The document identified major U.S. industries that depend on forgings, a list that included automotive and truck; agricultural machinery and equipment; valves, fittings, and petrochemical applications; hand tools and hardware; off-highway and railroad equipment; general industrial equipment; ordnance and marine; and aerospace.
“Impediments to collaborative, pre-competitive research must be eliminated, advocating programs that reward performance rather than specific methods of regulatory compliance. Cost, benefits, and relative risk of cooperative ventures must be given greater consideration. Forging companies must work with U.S. and international governments and standards organizations to harmonize standards for nomenclature, documentation, quality, and testing. The industry needs to improve the efficiency of logistics by developing new methods for working more effectively with suppliers, sponsoring efforts to shape information technology and standards to meet the manufacturing needs of the forging industry.” n
(Editor’s note: All photos courtesy of the Forging Industry Association.)
The Forging Industry Association provides basic information on the forging of titanium on its website (https:// www.forging.org/forging/ design/46-titanium-alloys.html).
Titanium alloys are selected for applications requiring high strength, low weight, high operating temperature or high corrosion resistance. Specific strength is high compared with steel. Densities are approximately 55 percent those of steel and 60 percent greater than aluminum alloys. The properties and cost of titanium alloys make them the choice in applications where a premium can be justified for high performance, such as aerospace, chemical processing and prosthetic devices. The
designation system indicates the type and amount of the major alloying constituents. For example Ti-6Al-4V contains 6 percent aluminum and 4 percent vanadium.
As with other forging alloys, the mechanical properties of titanium alloys are affected by forging and thermal processes as well as alloy content. However, when die filling is optimized, there is only a moderate change in tensile properties with grain direction, and comparable strengths and ductility are obtainable in both thick and thin sections. The processing of titanium alloys through the forging and subsequent thermal processes is a highly developed technology.
Titanium alloys are more difficult to forge than most steels. The metallurgical behavior of the alloys imposes some limitations and controls on forging operations, and influences all of the steps in the manufacturing operation. Special care is exercised throughout all processing steps to minimize surface contamination by oxygen, carbon or nitrogen. These contaminants can severely impair ductility, impact toughness, and the overall quality of a titanium forging if left on the surfaces.
Hydrogen can also be absorbed by titanium alloys and can cause
problems if levels exceed specified amounts. Hydrogen absorption, unlike that of oxygen, is not always confined to the surface.
Titanium alloys can be forged to precision tolerances. However, excessive die wear, the need for expensive tooling, and problems with microstructure control and contamination may make the cost of close tolerance (not machined) forging prohibitive except for simple shapes like compressor fan blades for turbo-fan engines.
Close tolerance forgings in moderately large sizes are currently being developed using hot die and isothermal forging techniques. Hot die and conventional forging of the Ti-10V-2Fe-3Al alloy, which has a relatively low forging temperature, has been demonstrated to be very successful with dies made from heat resistant alloys and heat treated to over 650°C (1200°F).
Glass coatings are commonly used to protect the titanium forgings from excessive oxidation and to provide some lubrication as well as serving as a release compound to prevent die galling (pressure welding).
There are three basic types of titanium forging alloys: alpha alloys, alpha-beta alloys, and beta alloys. The alpha alloys are designed
for resistance to creep at elevated temperatures, exceeding 535°C (1000°F) in some cases. They are not heat treatable in the conventional sense but they are annealed after forging to relieve stresses. The microstructure of alpha is essentially all alpha phase.
The alpha-beta alloys are those that include a mixture of alpha and transformed beta microstructures at room temperatures. They are heat treatable to very high strengths with a solution treatment and an age cycle. The widely used Ti-6Al-4V alloy is also the most common forging alloy.
The beta alloys are those containing sufficient alloy content to retain the beta phase to room temperature. Alloys include the more common Ti-10V2Fe3Al as well as some more highly alloyed grades such as Ti-13V-11Cr-3Al. These alloys are treatable to high strengths exceeding those achievable with Ti6Al-4V. The alloy Ti-13V-11Cr-3Al has been largely superseded by the 10-2-3 grade for forgings. In all three groups, the forging practices have a profound influence on the resulting properties. Forging suppliers should be contacted for their experiences in forging and heat treating these families of titanium alloys. n
The titanium industry has been waiting two years for Boeing’s 787 Dreamliner to be approved for takeoff. Based on reports from the July 2022 Farnborough Air Show, along with articles by two major national newspapers, the titaniumintensive commercial jet may soon be gaining altitude, albeit slowly and cautiously.
The Wall Street Journal, on Aug. 9, reported American Airlines would take its first delivery of a 787 Dreamliner “after a long pause in deliveries of the jet. Earlier, in a July 19 online article, the Journal reported that Boeing sold five widebody 787s to AerCap Holdings NV, at Farnborough, describing the deal as a “boost for Boeing’s 787 Dreamliner program. Delivery of the jets have been on hold for much of the last two years as the plane maker resolved production issues with U.S. air safety regulators.
AerCap, based in Dublin Ireland, which touts itself as the largest aircraft leasing company and the world’s biggest 787 customer, confirmed the Farnborough transaction on its website (www.aercap.com), while noting that the deal brings AerCap’s total bookings of the 787 to 125 jets, owned or on order.
In the wake of the Farnborough deal, The New York Times reported, on July 30, that the Federal Aviation Administration (FAA) “cleared the way” for Boeing to resume deliveries of the 787 Dreamliner, which were put on hold in 2020 due to quality concerns. The quality issues “included finding and filling paper-think gaps
in the plane’s body, replacing certain titanium parts that were made with the wrong material, and other fixes.”
From the perspective of the titanium industry, the 787—a compositeintensive commercial jet—is a major platform for the use of titanium. Boeing, on its website, stated that the 787 “makes greater use of composite material in its airframe and primary structure than any previous Boeing commercial airframe,” all of which is designed to reduce weight and fuel consumption for long-distance, international service. A key advantage for titanium, aside from its light weight, strength and corrosion resistance, is the metal’s compatibility with composite structures.
Boeing, as detailed on its website, indicated titanium use has been increased on the 787 to roughly 14 percent of the total airframe.
“The expanded use of composites, especially in the highly tensionloaded environment of the fuselage, greatly reduces maintenance due to fatigue when compared with an aluminum structure. This type of analysis has resulted in an increased use of titanium as well. Where loading indicates metal is a preferred material system but environmental
considerations indicate aluminum is a poor choice, titanium is an excellent low-maintenance design solution. Titanium can withstand comparable loads better than aluminum, has minimal fatigue concerns, and is highly resistant to corrosion.”
Richard Aboulafia, who joined the Ann Arbor, MI-based consulting firm AeroDynamic Advisory as a managing director in January (he previously served as the vice president of analysis at Teal Group, Fairfax, VA), took note of the developments regarding the 787. He described the FAA’s approval for Boeing to resume deliveries of the Dreamliner as “significant,” but quickly added that the current global market for widebody aircraft—despite the booking by AerCap—remains “rather dead.”
Aboulafia, a widely quoted analyst in the titanium industry regarding aerospace industry trends and business conditions, pointed to larger trends affecting the recent and future production of wide-body aircraft for both Boeing and Airbus. He’s long
observed the “secular shift” away from twin-aisle commercial jets in favor of the production of single-aisle aircraft in the fleet planning of Boeing and Airbus. He reiterated and further underlined this trend in an online April guest article for AviationWeek. The shift to single-aisles has been apparent for years, he wrote. “Backlog and delivery numbers both show this. By the first quarter of this year (2022), twin-aisle deliveries and backlogs by value had declined to just 30 percent of the market. This percentage is an all-time low since twin-aisles first entered the market.” Aboulafia, in the AviationWeek article, cited route fragmentation as the long-term trend “driving single-aisles upward and twin-aisles downward. Then the Covid-19 pandemic hit international traffic first, most and longest. This created a terrible twin-aisle overcapacity situation.”
consists of four A350-1000s and two A350-900s.”
Separately, the website simpleflying.com, in an online article published on July 11, reported Airbus next year is expecting to increase monthly production of its A350 family of jets to six from five aircraft—perhaps an early sign of increased interest in wide-body jets and international travel, in the wake of the global pandemic. For example, Australia’s Quantas Airways, in the first half of this year, ordered 12 A350-1000 jets, which are slated to provide direct service to London and New York from Australia. The simpleflying online report also mentioned that Airbus had delivered 29 A350-900 jets in the first half of 2022. In addition, Reuters, which filed a report from Farnborough on July 20, reported that Air India is mulling a possible booking of $50 billion that might include up to 70 wide-body jets (Airbus A350s and Beoing 787s) and as many as 300 single-aisle aircraft.
Ethiopian Airlines will “upsize” four Airbus A350 wide-body, twinaisle Airbus jets, according to a July 28 press release. The A350 competes with Boeing’s 787 and is another major platform for titanium. The press release reported that “Ethiopian Airlines has already ordered 22 A350-900s, of which 16 aircraft have been delivered. With the A350-1000 upsizing, Ethiopian Airlines’ backlog
In contrast to these developments, The Wall Street Journal on Aug. 4 reported that Airbus cancelled a deal to deliver 19 A350 jets to Qatar Airways, a transaction estimated at $7 billion. The article stated that Qatar already has taken delivery of 53 A350s and was set to receive an additional 19 jets in the coming years.
Separately, aside from trends on commercial aerospace twin-aisle
jets, Aboulafia raised a red flag on near-term, global titanium supplychain vulnerabilities stemming from Russia’s ongoing invasion of Ukraine, which would affect singleand twin-aisle commercial aircraft. The worry is that economic sanctions imposed on Russia by the United States and Europe will disrupt the ability to acquire titanium castings and forgings. However, because of the uncertainty, he said titanium companies in the aerospace supply chain remain reluctant to make major capital investments as the bitter conflict drags on—in other words, forgo doing business with Russia and focus on domestic production.
The 787—a compositeintensive commercial jet—is a major platform for the use of titanium. A key advantage for titanium is its compatibility with composite structures. Boeing indicated titanium use has been increased on the 787 to roughly 14 percent of the total airframe. “Titanium can withstand comparable loads better than aluminum, has minimal fatigue concerns, and is highly resistant to corrosion.”
Aboulafia said the titanium supply chain is waiting to see whether Russia might once again become a major player in producing aerospace structures and parts. “Everyone is waiting to see if the problems with Russia can be resolved. U.S. suppliers don’t want to be left holding the bag.”
Concerns regarding the war in Ukraine have gripped the titanium/ aerospace supply chain this year. As outlined in the first-quarter edition of TITANIUM TODAY, Boeing halted titanium purchases from Russia. The Wall Street Journal, on March 7, reported that Boeing stopped purchasing Russian titanium since the invasion of Ukraine. Boeing also closed its engineering offices in Moscow and Kyiv and stopped sending spare plane parts to Russian airlines. A Boeing spokeswoman stated that the aerospace giant said it will focus on sourcing its titanium from suppliers the United States, Japan, China and Kazakhstan. “Our inventory and diversity of titanium sources provide sufficient supply for airplane production, and we will continue to take the right steps to ensure long-term continuity,” she said.
Pittsburgh-based Allegheny Technologies Inc., on March 9, announced the termination of Uniti LLC, its joint venture with Russianbased VSMPO-AVISMA, to market and sell a range of commercially pure titanium products. The joint venture primarily focused on selling to industrial markets such as power generation, chemical and petroleum processing, automotive, and transportation. ATI formed the Uniti joint venture with VSMPO in April 2003.
An Aug. 9 story in The Wall Street Journal reinforced Aboulafia’s worries on Russia’s dominance in the global
supply chain. “VSMPO sells finished titanium goods at artificially low prices, which is probably why it serves about half of Airbus’ titanium needs,” the article stated. However, due to the ongoing conflict in Ukraine, “U.S. aerospace giants like Boeing, Ratheon and General Electric have either walked away from Russian titanium or minimized its use.” But the story reiterated concerns heard in recent months that the U.S. Department of Commerce has “repeatedly warned” that the status quo regarding reliance on Russian titanium is a threat to national security; in essence, identifying titanium as a strategic metal. “Airbus and other Western (aerospace) manufacturers have gained time to shift supply chains elsewhere. The aerospace industry will find it hard to shed its dependence on autocratic regimes.”
Andrew Bayne, Jr., the director of global materials planning for the Titanium Metals Corp. (Timet), in a guest article published in the secondquarter edition of TITANIUM TODAY, wrote that the titanium supply chain has been strained of due to Russia’s invasion of Ukraine.
“Producers need to be flexible in how they source raw materials and schedule production,” Bayne declared. “Every link in the chain needs to be asking itself: Will my hiring of manpower to increase rates synchronize properly with my incoming raw materials? Will my suppliers be able to ramp up to support my increased requirements?
Do I have a plan B or inventory if my supplies do not arrive on time? If you can answer yes, make sure the tier ahead of you and behind you agrees. And if you cannot, communicate early and often. If not, titanium runs the risk of impeding the overall air traffic recovery.”
Aside from the war in Ukraine and in the wake of the global pandemic, volatility in energy supplies and the tensions between China and the United States have had an impact on supply-chain vulnerabilities. Willy C. Shih, the Robert & Jane Cizik Professor of Management Practice at Harvard Business School in Boston, interviewed earlier this year, said it’s time for companies in the U.S. titanium industry to begin thinking 10 years ahead to change their investment strategies with an eye on long-term resiliency. Russia has been a dominant player in titanium and titanium forgings, especially in the aerospace sector, he pointed out. “Many people are waking up to the potential consequences of a longerterm stoppage in the flow of these critical materials.”
Shih said many business leaders are grappling with the strategic questions regarding strains in an over-extended global supply chain. According to Shih, the lessons from the turmoil caused by the global pandemic and the war in Eastern Europe are that “unpriced risks” and supply chain disruptions are no longer a vague concern in the distant future; rather, they’re highly likely, near-term threats that are becoming part of the annual business cycle. As a result, titanium supplychain executives need to invest in resiliency. Investments in resiliency might mean keeping idle production capacity at the ready in order to guard against potential supply chain problems, or establishing cooperative manufacturing consortia, which are narrowly focused to capitalize on process technology innovations. n
The long-awaited inflection point for full-fledged commercial additive manufacturing (AM) in the titanium industry finally has arrived. This declaration comes as a result of cumulative advances in AM in recent months, as profiled in the pages of TITANIUM TODAY, with the final piece of the inflection-point puzzle arriving via recent developments at Norsk Titanium’s operations in Plattsburgh, NY.
AM has been a hot-button issue for the titanium industry for more than seven years. Even though the pieces of the puzzle are rapidly falling in place, two questions remain: how fast will production ramp up to achieve commercial volumes?; and will AM fulfill its highly touted promise as a manufacturing technology to compete with traditional machining, casting and forging, especially in the aerospace industry and beyond?
Norsk Titanium received the International Titanium Association’s (ITA) 2018 Titanium Application Development Award for its AM work. Nicholas Mayer, vice president, commercial, said Norsk has verified that the AM technology will accelerate as an industry process for commercial aerospace in the first quarter of 2023 and will continue to advance throughout next year, as the company now has specifications in place as well as a full stable of wire-fed AM machines. According to Mayer, Norsk has widely accepted Society of Automotive Engineers (SAE) production specifications that are applicable across multiple industries as well as manufacturer
Close-up shot of Norsk’s Merke G4 AM machine producing parts at the company’s Plattsburgh, NY, facility.
specific specifications from Boeing and Airbus to design and build parts that “specify” AM titanium.
Specifications have also been developed by U.S. defense contractors for manned and unmanned military applications. The company also recently announced an expansion to the rapidly growing semiconductor manufacturing equipment market with their partner, Hittech Group BV (website: https://hittech.com/). “This 150-pound titanium print allows Hittech to increase their capacity to meet end customer needs without costly capital investment and will be in full scale production late this year.”
In addition, the company has qualified a supply chain for the specs, and there is a confluence of technologies that will provide complete material and part inspections needed for aerospace and defense applications. Mayer said
Norsk works with tier-one suppliers such as Spirit Aerosystems, Wichita, KA (website: https://www.spiritaero. com) and Premium AEROTEC GmbH (website: https://www. premium-aerotec.com/) to integrate into the existing OEM supply chain.
The Plattsburgh facility has a fleet of 31 Merke IV® AM, CNC controlled machines, and is expecting one more unit in the near future. Thanks to a $125-million partnership with the State of New York, Norsk is “building out production capacity to meet customer needs in the aerospace industry.” Along with its AM machines in Plattsburgh, Norsk has three Merke IV® units in Hønefoss, Norway.
Mayer said Plattsburgh’s Merke IV® fleet includes G4B model machines, with a 900 millimeters (3 feet) by 600 millimeters (2 feet) by 300 millimeters (1 foot) workspace, along
with G4L machines, which provide a work envelope of up to 1.9 meters (6.5 feet) in length. All of the equipment is “sized to meet aerospace demand for structural parts.” He declined to identify specific parts currently in the production pipeline.
Norsk’s AM will focus on the longstanding, workhorse alloy Ti-6Al-4V wire, but new, advanced titanium and other metal alloys also are under consideration. Mayer said their titanium wire additive process is used for large, primary structure parts that require high material deposition rates, with powder metal AM being best suited for smaller, more detailed components. “Our market
its facilities in Norway and the United States, which supports our business plan through 2026 and beyond. With no need for further investments in machinery, we have directed our resources towards qualifications and testing to ensure our customers can utilize our 3D printed material commercially as a direct replacement for parts currently manufactured using traditional technologies. Through highly optimized and repeatable digital programming, RPD® technology melts titanium wire into near-net-shape parts while maintaining material integrity equivalent to the highest specifications, like aerospace-grade forgings.”
The company’s annual report indicated that Norsk’s “successful
execution of Boeing’s Material Allowables Program in 2017 enabled the first additively manufactured titanium component qualified for structural application on a commercial airliner. Norsk Titanium currently provides seven AM parts on every Boeing 787 aircraft put into operation.” Last year Norsk began expanding its commercial aerospace applications through Airbus’ machine qualification and part development efforts and anticipates introduction of serial production parts in 2023 on the A350.
for aerospace parts doesn’t intersect with the laser powder market,” Mayer pointed out.
As stated in its most recent annual company report, Norsk, with its proprietary Rapid Plasma Deposition® (RPD®) technology, “is enabling a paradigm shift to a clean and sustainable manufacturing process. Thanks, in part, to our partnership with the State of New York, Norsk Titanium has 700 metric tons of annual production capacity between
Nicholas Mayer, Norsk Titanium’s vice president, commercial, said the company has verified that the AM technology will accelerate as an industry process for commercial aerospace in the first quarter of 2023 and will continue to advance throughout next year, as the company now has specifications in place as well as a full stable of wirefed AM machines. Norsk’s Plattsburgh, NY, facility has a fleet of 31 Merke IV® AM, CNC controlled machines. Norsk currently provides seven AM parts on every Boeing 787 aircraft put into operation.Norsk’s fleet of Merke AM equipment Norsk’s Plattsburgh, NY, factory floor Progress at Norsk and Other Organizations Combine to Achieve AM ‘Inflection Point’ (continued)
Each Merke IV® fourth-generation production machine can produce up to 20 metric tons annually of AM parts, depending on part size and geometry. “Each machine follows a routine calibration sequence which maintains machine-tomachine equivalency and maintains performance over time.” The annual report stated that Norsk’s Plattsburgh Production Center (PPC) covers an area of 80,000 square feet. “Our machines at PPC were approved for Boeing production in 2021 and we expect additional customer qualifications to be complete by mid-2022, with mass production for contracted parts to begin during the fourth quarter of 2022.”
During the last four-plus years TITANIUM TODAY has dedicated significant coverage to the milestones for an AM “inflection point,” a termed used by Art Kracke, the president of AAK Consulting L.L.C., who’s been associated with the global titanium industry for four decades. During his presentation at the TITANIUM USA 2018 conference and exhibition, he compared the commercial and technical progress of titanium AM with the inflection point of aluminum in the early 1950s—the period when aluminum evolved from a high-cost metal to an industrial commodity. Kracke focused his remarks on powder metal AM, but he did recognize Norsk’s success on producing AM parts for Boeing’s 787 with its wire-fed RPD® technology to produce near-net-shape titanium parts.
Earlier this year, TITANIUM TODAY reported on Amaero International Limited (website: https://www.amaero.com.au), an Australian-based public company specializing in the provision of end-to-end metal additive manufacturing solutions in terms of materials, services, equipment and
technology to its key clients in the aviation, defense, space, and medical sectors, as well as in the specialized tool and die industry. Amaero International evolved out of one of the Technology Research Platforms of Monash University, Australia’s largest university (website: https:// www.monash.edu). Amaero works with many of the world’s leading manufacturers of aerospace and defense products in research and development as well as in scaling up additive manufacturing capability. Amaero established its facility in the greater Los Angeles area of El Segundo in 2020 to service and be strategically located nearby the leading global defense contractors. Having set up its manufacturing bases in Australia and the United States, Amaero is tackling the issue of strategic supply of titanium alloy powders, on which its business relies. With the bulk of the global supply of titanium metal feedstock coming from Russia, China and Kazakhstan, it’s challenging to source titanium powder that has been manufactured from feedstock produced only in allied nations.
The National Center for Additive Manufacturing Excellence (NCAME) (website: https://www.eng.auburn.
edu/research/centers/additive/index. html) at the Samuel Ginn College of Engineering at Auburn University, Auburn, AL, is contributing to the trek towards arriving at a much-anticipated inflection point. The center operates as additive manufacturing center of excellence, a collaborative effort among Auburn University, NASA, National Institute of Standards and Technology (NIST), and ASTM International. NCAME’s mission is to facilitate effective collaborations among industry, government, academia, non-profit organizations, and ASTM committees, ensuring a coordinated, global effort toward rapidly closing standards and workforce development gaps in additive manufacturing. NCAME has benefitted from strategic capital investments in recent years, which, collectively, have helped to transform the group into a hub for leading-edge technology. The list of investments and grants include a $18-million renovation of Auburn’s Gavin Engineering Research Laboratory; support from Auburn’s Presidential Awards for Interdisciplinary Research grant to explore additive manufacturing for medical implants; $7-million in grants from the NIST; a $4.5-million
www.ald-vt.com www.ald-usa.com
grant for the FAA; a $10-million award from NASA; and a $250,000 Concept Laser MLAB 100R metal printer from GE Aviation.
The ASTM Global Additive Manufacturing Program (website: https://amcoe.org) has created a “Center of Excellence” to accelerate the standardization and industrialization of AM technology. The program is focused on identifying gaps in the AM standards. Established in 2018, the center is an alliance between ASTM and its founding partners (NASA, Auburn University, the Manufacturing Technology Center of England, and Edison Welding Institute [EWI]). The program’s mission is to provide education and workforce development offerings to support the adoption of AM technology. The partnership roster also included the National Institute for Aviation Research at Wichita State University, Kansas, and the National Additive Manufacturing
Innovation Cluster in Singapore.
In August 2021, General Electric Aviation (website: https://www. geaviation.com) issued a press release trumpeting that its facility in Auburn, AL, shipped its 100,000th fuel nozzle tip produced via AM. According to GE, the AM nozzles are used on CFM International LEAP engines for various commercial aerospace platforms. Each engine has 18 or 19 fuel nozzles, depending on the specific model. CFM International is a joint venture between GE Aviation and Safran Aircraft Engines of France.
Bill Bihlman, founder of Aerolytics (website: www.aerolyticsllc. com), a strategic consultancy dedicated to aerospace materials, manufacturing, and the supply chain, penned a guest article earlier this year on incremental milestones for AM technology. “Clearly, the industry needs to walk before it runs, particularly for aerospace” regarding
advances in AM, Bihlman wrote. “AM shows promise for aerospace. A large proportion of additive manufactured parts involve titanium. For AM to be cost effective for newer designs, the entire artifact needs to be considered. Targeting single parts is rarely prudent for serialized production. Parts usually need to be designed with additive in mind, from the beginning. This mentality will take time. Meanwhile, the titanium industry can expect to see novel use cases for both aerostructure and turbine applications. There will be no step change. The industry will indeed continue to incrementally evolve, for the benefit and safety of the flying public. But someday, AM will be just another tool in the toolbox.” n
TiFast S.r.L., like all companies, lives and operates in the framework of a human society; hence the activities dedicated to relationship with stakeholders, the agents having a direct or indirect interest in TiFast life, are of paramount importance. First and foremost, the local community is one of the stakeholders. The development of a good relationship with such stakeholder can be an important added value for both the company and the surrounding area.
Fig. 1: Drawing of a 18th cen. French bell used as an inspiration for the project
Among the projects already completed, one can recount the collaboration with the local Church Authorities, for the Parrish Church of San Liberato in Terni – Narni – Amelia Arch - dioceses, for the donation of a Titanium cross for the façade of the above – mentione d church. TiFast came to know that both the two bells of the same church are in grave disrepair, hence it proposed to have one of them substituted with a Titanium one.
The fabrication of said Titanium bell has been carried out by TiFast as a whole, no TiFast Dept excluded. It included the finding of the raw material, preparation of the constructive drawings, mechanical works and assembling.
The bell was fabricated from Ti-6Al-4V Titanium alloy, also known as Grade 5, one of the Titanium
alloys more common in aerospace. The present bell is probably the first one in the world to be made from Titanium, instead of the traditional bronze. The clapper was fabricated from Commercially Pure Titanium alloy, or Grade 2, that is softer than the rest of the bell, in order to avoid denting the inner surface of the bell while ringing.
Fig. 2: The bell in its finished form
The profile of the bell was inspired by the drawing of a 18th cen. French bell (Fig. 1).
The main body of the bell was fabricated from a single piece of Titanium alloy by machining. Then the surface was sandblasted. The clapper and its attachment point were machined and connected to the bell main body by
threaded connections and welds. On the brim of the bell a laser – engraved inscription quotes:
nobis, sed ad maiorem Dei gloriam - A.D. MMXXI” (= Not for us, but for the highest Glory of God. In the Year of the Lord 2021) [Fig. 2]
Blueprints of the bell are given in the drawings from Fig. 3 to Fig. 5.
The bell is completed made from Titanium, therefore it is insensible to weathering. The same holds for the caption.
The specific weight of Titanium is much lower than bronze, therefore the Titanium bell is much lighter than the old bronze one, hence a reduction of the weight impinging on the ancient bell gable of the church (Tab. 1).
and size of the
Placing the bell on its natural location involved also the removal of the ancient bronze bell, discovered with surprise as bringing the datum of year 1427, and the total restoring of the sail bell - tower of the San Liberato church (probably dating back to the 17th century), and the fixing of the supports of the new bell, also in Ti-6Al-4V, embedded in the masonry of the bell – tower.
The cross beam of the bell was made in part from oakwood, purely for the aesthetics, and in part from Ti6Al4V (see Fig. 6).
Finally in September 2022 the bell got its new home on the top of the San Liberato church bell – tower, and everybody could appreciate its tolling in B flat 5 (Fig. 7). n
Fig.
Frank Caputo, a 50year veteran of the titanium industry and a former president and chief executive officer of Oremet (the Oregon Metallurgical Corp.), is the recipient of the International Titanium Association’s (ITA) 2022 Lifetime Achievement Award. Jennifer Simpson, the executive director of the ITA, made the announcement on Oct. 3.
Caputo, who resides in Albany, OR, was a key member of the U.S. Bureau of Mines team in the early 1950s. Steve Shelton, the Bureau of Mines regional director, enlisted 11 of his colleagues, including Caputo, to establish the pioneering titanium company Oremet. Oremet was incorporated on Dec. 1, 1955, and began operations in 1956. Kathleen L. Housley, in her book Black Sand, the History of Titanium, wrote that “the level of expertise at Oremet was high from the start as evidenced by the fact that, in 1957, less than two years after its founding, Oremet built the world’s first titanium casting facility under Caputo’s direction.”
He developed and led the titanium industry in the technical advancement of recycling bulk weldables and titanium chips. Caputo pioneered the world of recycling titanium scrap into the ingot melting process, which offered a solution to the growing industry scrap volume
and allowed for a lower-cost input material.
Serving as one of the early presidents of the Titanium Development Association (TDA), the precursor organization to the ITA, he worked with Boeing and major aerospace jet engine manufacturers in the promotion and acceptance of titanium as a material of choice for their applications.
Caputo admitted he was surprised when informed that he had received the ITA’s Lifetime Achievement Award. “I respect the honor, but I never expected it,” Caputo said, interviewed in early October. “I had a job to do (in the titanium industry) and I loved it.”
Born on March 2, 1928, in Portland, OR, Caputo served in the Marines during the final months of World War II. He attended the University of Portland and Lewis and Clark College, with the intention of becoming a dentist. Instead, he took a job in the metallurgy department of the Albany Research Center in Oregon—at the time part of the Bureau of Mines—working with titanium and zirconium. He praised
his mentors at the Bureau of Mines, especially Steve Shelton and Earl Hayes, for guiding him to a career in the metals industry. It was during that period he also met Dr. William J. Kroll at the Bureau of Mines, lauded as the father of the titanium industry for his development of the Kroll Process, which led to the production of titanium as an industrial metal.
Greg Caputo, a sales executive with Elmet Technologies, Lewiston, ME, a producer of tungsten and molybdenum and the son of Frank Caputo, said his father, in the 1970s and early 1980s, was known throughout the industry as “Mr. Titanium.” Greg said that Frank’s background and experience in the development of the commercial titanium manufacturing process, from his days at the Bureau of Mines, provided the insight for Frank’s leadership at Oremet and the TDA.
“As one of the TDA’s original presidents, (my father) helped take titanium from its infancy to the product we see today. From golf clubs to eye glass frames to medical implants, Frank Caputo had an integral part in this growth.” He also worked with NASA to incorporate titanium as the material of choice for the moon rover tires and wheels assembly, and helped to get titanium approved for downhole applications in the oil and gas industry. n
Stevensville, Michigan, August 23, 2022 – Alpha Resources LLC, the leading aftermarket supplier of consumables and reference materials, has recently expanded their product line to include supplies for Optical Emission Spectroscopy (OES) analysis. In-stock OES supplies include: electrodes, syringes, o-rings, filters, vacuum pumps, and more.
Alpha’s new OES products are compatible with OES analysis equipment from several leading OEMs, Thermo Fisher Scientific® and Bruker®. As with all Alpha products, the high-quality lab supplies are compatible for aftermarket use in the specified analyzers.
“Many current Alpha customers are in the metalcasting and cement sectors where use of gas combustible analysis machines for quality checks is accompanied by use of an OES analyzer. Adding OES aftermarket product lines will allow our customers the convenience of ordering lab supplies from a trusted vendor,” notes Ken Mantei, Director of Operations, at Alpha Resources. “Customers know that Alpha’s quality is second to none and that they will pay less from an aftermarket supplier like Alpha than they would to an OEM.”
Additional information about the new line of OES supplies may be found on the website, https://www. alpharesources.com/oes-consumables.php .
Founded in 1978, Alpha Resources, LLC is a global leader in the manufacture and distribution of aftermarket consumables and certified reference materials for use in atomic spectroscopy analysis. Alpha Resources is ISO17034, ISO17025, ISO9001:2015 certified.
Kevin Kramer, Chief Commercial and Marketing Officer, is retiring from ATI. He will become Special Advisor to the CEO effective January 1, 2023, until his retirement on January 31, 2024. Since joining ATI in 2014, Kevin has been instrumental in developing a customercentric leadership culture within ATI and expanding our commercial aptitude. He has helped solidify ATI’s position as a true customer partner.
Marty Pike has been named VP of Global Commercial Strategies for ATI. In this new role, Marty will be the primary point of contact across ATI for strategic customers seeking to grow and expand their partnerships with ATI. With extraordinary expertise in materials science and incredible capabilities and process technologies, ATI is uniquely positioned to solve our customer’ most difficult challenges. Marty will be instrumental to expanding relationships to unlock that growth. Marty will build on his expertise as VP of Commercial for ATI Specialty Materials and his 20 years’ experience in sales and commercial roles at ATI, as well as the experience he gained as interim president of ATI’s Specialty Materials business unit last year.
Banner Industries (Banner) is pleased to announce the opening of its latest distribution and manufacturing facility in Windsor, Connecticut.
All 6 divisions of Banner - Banner Commercial; Banner Medical; Banner P & M Supply; Edge International; NKS/National Kwikmetal Service; Supra Alloys - will be utilizing this 52,000 SF warehouse, strategically located just minutes from Hartford-Bradley International Airport.
Banner serves a diverse range of aerospace, industrial, and medical customers and this new Northeast location will allow Banner to meet local customer needs in the region with lower freight costs and reduced lead times.
Initial operations will focus on a full suite of high-value metal bar and sheet products, including stainless steel, specialty nickel and cobalt alloys, and titanium, available off-the-shelf.
Banner will populate the newly acquired facility with a wide range of state-of-the-art machinery and equipment: small diameter (0.020” dia. to 1.250” dia.) Centerless Bar Grinding, Straightening and Cutting; Coil Shearing; Plate Cutting; and a Water Jet Cutting unit to supply near netshape pieces. Additional equipment will be installed as the facility ramps up.
“Banner has established itself as a one-stop-shop for all customers’ bar and sheet product needs and employs a solutions-oriented business model,” stated Banner CEO, Dan Stoettner. “We are excited to expand into the Northeast region of the country with its high concentration of aerospace and medical customers.”
Established in 1961, Banner is a value-added metals processor and distributor serving OEMs, contract manufacturers, and precision machine customers. Banner is headquartered in Carol Stream, Illinois, with additional facilities in California, Illinois, Indiana, Ohio, Tennessee, Texas, and Queretaro, Mexico.
For further information, please call (800) 950-3652 or visit www.banner-industries.com
We are happy to share with you an addition to the Tricor Metals team. Larry Haubner joins us as the Engineered Product Sales Director with over 25 years of fabrication experience in the CPI, Pharmaceutical, Petrochemical, Steel, Oil & Gas and Mining markets globally with experience in corrosion resistant equipment that Tricor manufactures. His experience should be a valuable addition to our experienced Business Development and Project Management team.
Feel free to Welcome Larry with us. His email is lhaubner@tricormetals.com.
Sep 23, 2022, 08:38 ET With this approach, the developed photocathodes exhibit a remarkable stability and demonstrate sunlight-driven clean hydrogen production by water splitting GWANGJU, South Korea, Sept. 23, 2022 /PRNewswire/ -- Hydrogen is emerging as a popular eco-friendly alternative to fossil fuel resources owing to its carbon-neutral combustion products (water, electricity, and heat) and is considered to be the nextgeneration fuel for a zero-emission society. However, the major source of hydrogen is, ironically, fossil fuels.
One way to produce hydrogen in a clean and sustainable manner is through water splitting driven by sunlight. The process, known as “photo electrochemical (PEC) water splitting” is the basis of operation of organic photo voltaic cells. What makes this method attractive is that it enables 1) mass hydrogen production in limited space without a grid system and 2) high efficiency conversion of solar energy to hydrogen. Despite such advantages, however, the photo active materials used in conventional PECs do not have the properties required for a commercial setting. In this regard, organic semiconductors (OSs) have emerged as a potential photo electrode material for commercial PEC hydrogen production due to their high performance and low-cost printing. But, on the downside, OSs suffer from poor chemical stability and low photo current density.
Now, a team of researchers led by Prof. Sanghan Lee from Gwangju Institute of Science and Technology, Korea, may have finally solved this problem. In their recent breakthrough that appeared on the front cover page of the Journal of Materials Chemistry A, the team adopted an approach based on encapsulating the OS photo cathode in platinum-decorated titanium foil, a technique known as “metal foil encapsulation,” to prevent its exposure to the electrolyte solution.
“The metal foil encapsulation is a powerful approach for realizing long-term stable OS-based photo cathodes since it helps impede the penetration of electrolytes into the OS, improving their long-term stability as has been demonstrated in our previous studies and other reports
on OS-based photo electrodes,” explains Prof. Lee. The study was made available online on 14 May 2022 and was published in Issue 25 of the journal on 07 July 2022.
The team fabricated an organic photo voltaic cell, in which the OS photo cathode was covered with titanium foil and well-dispersed platinum nano particles. Upon testing, the OS photo cathode showed an onset potential of 1 V versus the reversible hydrogen electrode (RHE) and a photo current density of -12.3 mA cm at 0 V RHE . Most remarkably, the cell demonstrated a record operation stability, retaining 95.4% of the maximum photo current for over 30 hours without any noticeable deterioration in the OS. Further, the team tested the module under actual sunlight and was able to produce hydrogen.
The highly stable and efficient PEC module developed in this study can enable large-scale production of hydrogen and inspire innovative routes for building future hydrogen gas stations. “With the growing threat of global warming, it is imperative to develop eco-friendly energy sources. The PEC module explored in our study could be installed in hydrogen gas stations, where hydrogen can be both mass-produced and sold at the same time,” speculates an optimistic Prof. Lee.
We sure hope his vision is realized soon!
Reference DOI: https://doi.org/10.1039/d2ta02322a
Title of original paper: A long-term stable organic semiconductor photo cathode-based photo electrochemical module system for hydrogen production Journal: Journal of Materials Chemistry A About the Gwangju Institute of Science and Technology (GIST)
Website: http://www.gist.ac.kr/ Contact: ChangSung Kang 82 62 715 6253 345129@email4pr.com
HOT SPRINGS, Ark., Sept. 20, 2022 /PRNewswire/ -US Vanadium (“USV” or the “Company”) is pleased to announce that it has completed a $5.8 million upgrade of its vanadium processing operations in Hot Springs, including the installation of an industrial Belt Filter plant that will further improve the facility’s vanadium recovery rates, cut operating costs, increase recycling operations, and reduce the plant’s overall environmental footprint.
The USV facility produces ultra-high-purity electrolyte and other high-purity vanadium-based products by recovering contained vanadium from a variety of postindustrial waste streams.
USV’s recycling of waste streams also allows it to produce vanadium products with a much smaller carbon footprint than primary vanadium mining operations.
The plant’s new Belt Filter system allows for increased vanadium recovery and boosts production of high-value vanadium products. The belt filter generates a relatively dry cake, with only 5-6% moisture content, that can be recycled for use in other industrial applications such as the cement industry. In doing so, it is expected to eliminate the need to store leached solids in the facility’s tailings pond, significantly reducing the overall environmental footprint of the Hot Springs plant.
“The Board of Directors is pleased to see the team complete this plant and we look forward to seeing the
many benefits this upgrade is expected to deliver,” said Mark A. Smith, USV’s CEO and Chairman. “In addition to strengthening our production operations and streamlining costs, the belt filter also underscores USV’s commitment to maximizing sustainable practices in our operations. This is a win for the company, our employees, and the environment.”
US Vanadium produces the world’s highest-purity vanadium oxides (V2O5 and V2O3) at its Hot Springs facility. The availability of extremely pure vanadium oxides is the critical component of the VRFB electrolyte supply chain. The new electrolyte production facility is adjacent to the vanadium oxide production facilities and puts US Vanadium in the unique position of controlling the entire supply chain for ultra-high-purity vanadium electrolyte. In addition to the production of electrolyte, high-purity vanadium oxides from the Hot Springs facility support production of titanium alloys in the U.S. that are critical for defense, commercial aerospace, and industrial applications. US Vanadium also supplies highpurity vanadium oxides and downstream vanadium chemicals to various chemical and catalyst production applications.
Media Contact: Jim Sims 303-503-6203 344989@email4pr.com
Warren, MI, August 29, 2022 – Solar Atmospheres, Inc. is pleased to announce the acquisition of Vac-Met, Inc. With locations in Warren and Fraser, Michigan, Vac-Met has built a strong heat treating presence in the Midwest over the last 41 years. The addition of Vac-Met within the Solar Family of Companies will increase the total commercial vacuum heat treating and brazing facilities to a total of five (5) plants across the USA. Their goals of providing state-of-the-art commercial heat treating, primarily in a vacuum environment, aligns perfectly with Solar’s mission. Joseph White will continue to head the day-to-day operations of Vac-Met’s nine (9) vacuum furnaces, while leading an impressive team that he has built over the years. Joseph will report to Robert Hill, President of Solar Atmospheres of Western PA. Robert Hill states “We look forward to continuing to provide
unparalleled vacuum thermal processing services to Vac-Met’s valued customers while expanding Solar’s footprint. Solar is excited to support a dedicated and loyal employee base and welcome them to the Solar Team. Together, we will grow the business with unwavering commitment to honesty as our core value.”
For additional information about Solar Atmospheres, contact Bob Hill at 1-855-934-3284 x2224, email at bob@ solaratm.com, and visit us at solaratm.com.
U.S. VANADIUM’S NEW $5.8 MILLION UPGRADE IMPROVES VANADIUM RECOVERY, INCREASES RECYCLING, AND SUPPORTS CONTINUED PRODUCTION RATES FOR ULTRA-HIGH-PURITY ELECTROLYTE FOR VANADIUM REDOX FLOW BATTERIES
ST. AUGUSTINE, Florida (October 4, 2022) – Vested Metals International is pleased to announce the addition of Thomas Zuccarini as Chief Commercial Officer. Tom will begin his journey with Vested Metals on October 8th as part of the executive leadership team and will report directly to Founder and President, Viv Helwig. Tom brings more than 30 years of sales, marketing, supply, and commercial leadership experience in the specialty metals industry to this new role. Tom most recently retired from Carpenter Technology Corporation where he excelled in business development across multiple markets globally.
He brings a vast level of knowledge from multiple markets, especially the Orthopedic Medical Device Market where he has worked with organizations across the globe at all levels of the supply chain.
“I am very excited to be joining the Vested Metals team,” said Zuccarini. “Vested is a young, dynamic, and growing company that has made a significant impact in eight short years. I look forward to contributing to future growth through the investment in the best people, satisfied customers, and industry relationships.”
“We are excited to have Tom join our team at this critical and exciting time in your company’s history and story,” said Helwig. “I have known and worked with Tom for
over a decade and have always admired his business acumen and talent. He has always operated with the highest level of integrity, fairness, and transparency. He has a great desire to make sure customer’s needs are fully cared for while also being a great mentor and leader to his colleagues. Above all, I have admired his character, humility, and drive. I couldn’t be more excited not just to welcome his business prowess, but above all, his personhood. I would like to congratulate him on his retirement from a storied 37-year career in our industry and welcome him to the Vested family.”
ABOUT VESTED METALS INTERNATIONAL –Vested Metals was founded in 2014 by Viv Helwig, a Jamaican native who grew up in Palm Bay, Florida and graduated from Flagler College. The fast-growing distribution company is headquartered in St. Augustine, Florida and has been on the Inc. 5000 fastest growing companies in America and Jacksonville Business Journal fastest growing companies in the region for the past four years in a row. Vested Metals sources hard-to-find alloys, grades, and sizes for niche applications and markets such as aerospace, medical, automotive, industrial, and power generation. For more information, visit vestedmetals.net.
Rockaway, New Jersey, September 2022 – Titanium Industries (T.I.) continues to meet market demand head on. As a worldwide leader in specialty metals for the Aerospace, Defense, Industrial, Medical, Oil & Gas, and many other markets, T.I. is well positioned to serve customers across their expansive global service center network. Addressing material shortage concerns and long mill lead times, T.I. remains committed to expand inventory and stocking capacity, as well as processing capabilities.
Distribution facility and sales office expansions in Europe and Asia, increased storage capacity in Jacksonville and Detroit, additional processing capacity and capabilities in Rockaway, N.J., Birmingham, U.K. and Los Angeles, CA. are examples of continued investment to expand and provide additional services to T.I.’s global customer base.
Brett Paddock, T.I.’s President and CEO added, “T.I.’s focus during the COVID driven market issues and into the current supply constrained situation has been
resiliency. Our investment in the expansion and depth of our inventory, our growing service center footprint, and continuous development of processing capabilities have put us in a position to outperform, for even our most demanding customers and markets.”
Maintaining numerous distribution and sales operations across North America, Asia, Europe, and Latin America; T.I. is poised to handle economic volatility, supply chain disruptions, and the increasing demands of our loyal customers. For over 50 years, Titanium Industries has provided dependable, quality driven service.
T.I. is the global leader in specialty metals supply for the aerospace, medical, industrial, and oil & gas markets. Holding the world’s most complete inventory of specialty metals across a global service center network, T.I. delivers supply solutions to every level of the supply chain. With a globally experienced and technically driven team, T.I. has provided dependable, quality driven service to customers since 1972.
6K Additive’s nickel alloy 625 powder surpasses every quality measure in tests performed by Incodema3D
North Andover, MA, September 8th 2022 – 6K Additive, a division of 6K, a leader in the sustainable production of engineered materials for additive manufacturing and lithium-ion batteries produced from its UniMelt® plasma technology, announces a strategic AM powder supply agreement and recycling partnership with Freeville, NYbased Incodema3D.
Following increased demand and larger volume orders, predominantly from aerospace and defense customers, Incodema3D sought to secure a domestic AM metals powder supply that met strict quality standards and a solution for recycling their used powder and parts. 6K Additive, through its UniMelt plasma microwave powder production system, is able to provide high volumes of domestically manufactured powder and a route to sustainably recycle Incodema3D’s used metals through its Powder Buy Back program.
Incodema3D director of additive manufacturing and metrology operations, Kevin Engel explains: “We are talking to clients now about projects for 2023 that will require ten tons of metal powder per month. When you’re going through that volume of powder, recycling becomes imperative, and sustainability is key to our business. By recycling our used powder with 6K Additive we have been able to drive down our contribution costs for material by 15% already. Add to it the quality standards both Incodema3D and our customers demand sets a high bar for any one supplier. 6K Additive overachieved on this front.”
6K Additive’s mission is to provide a solution for global decarbonization in producing performance additive manufacturing materials that are critical to production in markets such as aerospace, medical and industrial applications. The company recently released results from an LCA study conducted by Foresight
Management comparing the environmental impact of 6K’s UniMelt microwave plasma technology to current atomization technologies to produce metal powders. The results showed a 91% reduction in energy use and a 91.5% reduction in carbon emissions when using the 6K UniMelt process. The independent studies can be download here.
Incodema3D undertook its own pre-qualification of 6K Additive’s nickel alloy 625 (Ni625), a high-strength and corrosion-resistant alloy, popular with many of their customer’s applications. Internal qualification samples measured tensile strength, microstructure, density, and chemical composition and benchmarked the results against existing suppliers and their strategic customer’s requirements.
6K Additive’s Ni625 surpassed every measure used in the assessment, including tensile strength (greater than 125 ksi), yield strength (greater than 85 ksi), and elongation at break (greater than 30%).
“We tested five samples and each one returned density results of 99.9%, which far exceeds the minimum requirement. Anything over 99.5% density in additive manufacturing is a good part,” continued Engel.
Securing a scalable domestic materials supplier was also important to Incodema3D. As 6K Additive upcycles used and waste material from domestic sources, they are not at risk of supply chain disruptions. For defense customers a shorter domestic supply chain is also preferable from a security and traceability standpoint.
In addition to Ni625, 6K Additive produces a full suite of AM powders including Ni718, low oxygen (500-700ppm) Ti64, stainless steel 316/17-4, copper 18150 and GRCOP, refractory powders including tungsten, tantalum, and rhenium.
In 1980, Ed began working for Dynamet, Inc., retiring as vice president and general manager in 1997. He was the executive director of the International Titanium Association from 1996-1997. After that he and his son, David purchased the Pittsburgh Batteries Plus franchise and worked together for 10 years before selling the business.
His career began at Precision Castparts in 1957 when it was a small start-up. Between 1957 and 1966 he held positions in inspection and development engineering. He left PCC in 1967 and helped start REM Metals, a titanium investment casting company.
In 1949, Wing received his BS in Chemistry and Minor in Metallurgy from the University of Illinois. He headed the Titanium Development Plant at the Bureau of Mines, Boulder City, Nevada from 1954-56. Hired by Wah Chang in 1956 as its 2nd employee, he designed the new Zirconium plant, equipment and directed operations. He soon led the development and production of high purity Titanium and Hafnium.
Originally from Newport, South Wales, UK Derek moved to the US in the early 2000s and first settled in Newport Beach, CA. After spending several years in California, he relocated for a new job opportunity, to Pittsburgh, where he remained for the rest of his life. He loved his work in the world of titanium and enjoyed his many interactions with colleagues, customers, and suppliers.
6K Additive
A. M. Castle
Abkomet
Accushape Inc.
ACNIS ® International
Advanced Metal Industries CO (AMIC)
ALD Vacuum Technologies, Inc
All-Met Recycling
Alpha Resources
Alta Alloys
American Titanium Works LLC
Andersen Horie & Co.
Aries Manufacturing
ATI
ATX Co.,Ltd.
Bahco Banner Industries
Baoji Sino-Swiss Titanium Co.,Ltd
Baoji Titanium Industry Co., Ltd
Bodycote
Butech Bliss
Carpenter Technology Corporation
CBMM North America, Inc
Consarc Corporation
Coogee Titanium PTY LTD
CSM Tech Co., Ltd.
Dr. Markus Holz, Academic Member
Duferco SA
ELG Utica Alloys, Inc.
Epoch Wire
Fort Wayne Metals
FRIGGI N.A. Inc.
GfE Metalle und Materialien GmbH
Grandis Titanium
Greystone Alloys, LLC
Hempel Special Metals AG
HETRAN-B
Howmet Aerospace
ICD Alloys & Metals, LLC
Independent Forgings & Alloys Ltd
Industrial Metals International Ltd. IperionX Limited
KASTO Inc.
Keywell Metals LLC KineTic Engineering
Kings Mountain International (KMI) Kymera International
Laboratory Testing Inc. Lomon Billions
M3 Metals
Medart Processing Technologies Mega Metals LLC Metals & Alloys UK MetCon Technologies, LLC
Metraco, FE Mottram and Eesti Titaan oü Michelle Pharand, Individual Member Monico Alloys, Inc. Mott corporation
MPS Technology Sp. Z o.o. Neotiss
North American Alloys NSL Analytical
Nu-Tech Precision Metals Oerlikon Metco (Canada) Inc.
Osaka Titanium technologies CO., Ltd. Paris Saint-Denis Aero Perryman Company
Plaxys Inc.
Plymouth Engineered Shapes
Precision Abrasives
President Titanium Co., Inc. Product Evaluations Systems, Inc (PES)
Prolog Titanium Corporation Co., Ltd. Quantum Design Inc. Retech Systems LLC Rex Heat Treat
Rolled Alloys Inc
Ross Precision Manufacturing
S+D Metals / Bibus Metals
Sandvik Materials Technology Product Unit
Service Steel Aerospace SES, LLC
Shasta Services LLC
Simonds Saw LLC
Solar Atmospheres
Specialty Metals Company
Specialty Metals Processing Company
Sumitomo Corporation of Americas (SCOA)
Timesavers International B.V.
TIMET, Titanium Metals Corporation
TITAN Metal Fabricators, Inc.
Titanium Engineering
Titanium Fabrication Corporation
Titanium Finishing Company
Titanium Industries, Incorporated
Titanium International Group SRL Titanium Processing Center
Toho Titanium America Co., Ltd.
Tricor Metals
TSI Titanium
Ulbrich Stainless Steels & Special Metals
United Alloys & Metals Inc
United Performance Metals (UPMET)
United Titanium Uniti Titanium US Vanadium
Vested Metals International, LLC
VSMPO Tirus, US Weber Metals Inc.
Weldaloy Specialty Forgings
Westbrook Light Alloys Ltd
Xi’an Metals & Minerals Import & Export
Titanium Industries, Incorporated https://titanium com/
Ulbrich Stainless Steels & Special Metals https://www ulbrich com/
Kymera International https://www kymerainternational com/?locale=en
United Performance Metals (UPMET) https://www upmet com/
North American Alloys https://north-american-alloys webflow io/
Weldaloy Specialty Forgings https://weldaloy com/
TIMET, Titanium Metals Corporation https://www timet com/
17
Perryman Company https://www perrymanco com/ 19
Solar Atmospheres https://solaratm com/ 21
Rolled Alloys Inc https://www rolledalloys com/ 23
Tricor Metals https://tricormetals com/ 25
Titanium Finishing Company https://www titaniumfinishing com/ 27
Quantum Design Inc. https://www centrometalcut com/ 29 Retech Systems LLC https://www retechsystemsllc com/ 31
Product Evaluations Systems, Inc (PES) https://www pes-testing com/
Laboratory Testing Inc. https://labtesting com/ 35
ALD Vacuum Technologies, Inc https://www ald-vt com/
37
Alpha Resources https://www alpharesources com/ 39
Aries Manufacturing https://www aries-manufacturing com/
41
Banner Industries http://www supraalloys com/ 43 Butech Bliss https://www butechbliss com/ 45