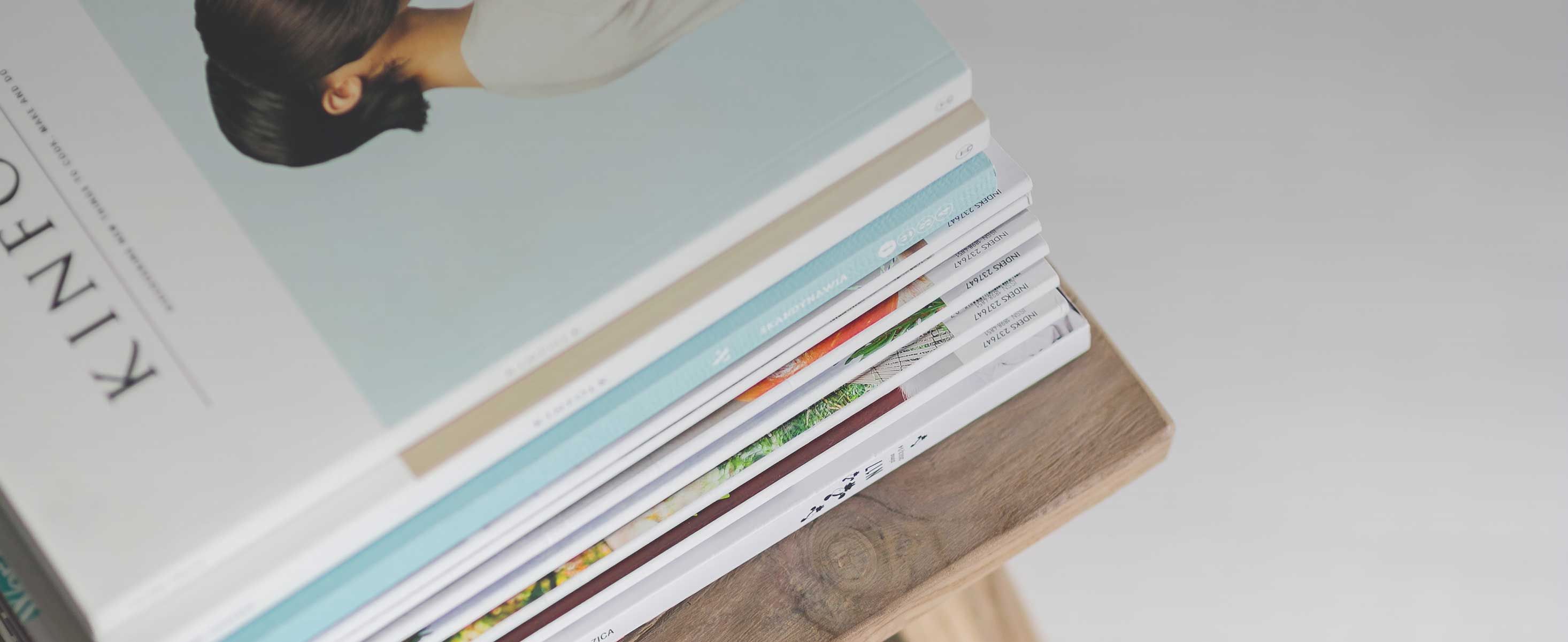
10 minute read
Occupational Health and Safety Policy
Company Name: Toronto Montessori School (TMS) Policy Title: Occupational Health and Safety Policy Policy Owner: Vince Haines, CAO Approver: Andrew Cross, Head of School Version: 1 Last Review: September 30th 2021
Policy Statement
TMS (TMS) is committed to the promotion of the health, safety and well-being of all members of the TMS community, to the provision of a safe and healthy work environment and to the prevention of occupational injuries and illnesses. In fulfilling this commitment, management will provide and maintain a safe and healthy work environment, in accordance with industry standards and in compliance with legislative requirements, and will strive to eliminate any foreseeable hazards which may result in property damage, accidents, or personal injury/illness.
Purpose
The TMS Health and Safety program is an amalgamation of existing policy, procedures, manuals and guidelines. It is intended to highlight all matters related to the health and safety of the TMS community and ensure the stated Health and Safety policy is being carried forward.
Application
We recognize that the responsibility for health and safety is shared. All employees will be equally responsible for minimizing accidents within our facilities. Safe work practices and job procedures will be clearly defined in the company’s Health and Safety Program for all employees to follow. Accidental loss can be controlled through good management in combination with active employee involvement. Safety is the direct responsibility of all managers, supervisors, employees, and contractors. All management activities will comply with company safety requirements as they relate to planning, operation and maintenance of facilities and equipment. All employees will perform their jobs properly in accordance with established procedures and safe work practices. *The safety information in this policy does not take precedence over Occupational Health and Safety legislation. All employees should be familiar with the Occupational Health and Safety Act and the Regulations for Construction Projects (current edition), to the extent required for their jobs.
Health and Safety Responsibilities
Senior Management
1) Prepare a health and safety policy. Post it in the workplace and review it annually. 2) Develop a program to implement the health and safety policy. Ensure it is known throughout the organization. Ensure training is in place to make the program work. 3) Appoint competent supervision. 4) Ensure that equipment, materials and protective devices are provided and maintained in good condition. 5) Provide resources so supervisors and workers can carry out safe and healthy work. 6) Ensure that adequate and suitable planning is done to provide safe and healthy workplaces.
7) Review accident reports and respond where necessary. 8) Review site inspection reports quarterly. 9) Delegate authority and responsibility. 10) Hold employees and subcontractors accountable for the authority and responsibility delegated to them. 11) Be visibly committed to making health and safety work. Inspire others to make it work.
Managers
1) Ensure that the TMS faculty and staff understand their health and safety responsibilities. 2) Ensure that equipment, materials and protective devices are provided and maintained in good condition. 3) Ensure the workforce is trained to safely complete the work and deal with hazards. Ensure that the training is current and regularly reviewed. 4) Be aware of applicable legislation and ensure compliance. 5) Take unresolved health and safety problems to senior management. 6) Respond appropriately to reports of problems and to Joint Health and Safety Committee/Health and Safety Rep recommendations. 7) Establish a system to review the health and safety program. Ensure it is up-to-date. 8) Review accident/incident reports. Ensure corrective actions are taken. 9) Ensure that workers comply with the Occupational Health and Safety Act, applicable regulations and the company’s policy and program. 10) Ensure that workers are aware of potential hazards and have dealt with, or are dealing with, the actual hazards in the workplace. 11) Provide orientation to new staff. 12) Encourage workers to report health and safety problems 13) Respond quickly and appropriately to worker concerns and cooperate in their correction. Accelerate the matter if it is beyond the supervisor's authority/ability. 14) Be aware of the applicable legislation and company procedures. 15) Set an example by being consistently safety conscious, and insisting on the safe performance of work. 16) Establish procedures and practices to ensure that workers can carry out safe and healthy work. 17) Ensure that workers comply with the Occupational Health and Safety Act, applicable regulations and the company’s policy and program. 18) Ensure that workers are aware of potential hazards and have dealt with, or are dealing with, the actual hazards in the workplace. 19) Provide orientation to new staff. 20) Encourage workers to report health and safety problems. 21) Set an example by being consistently safety conscious, and insisting on the safe performance of work.
Staff
1) Use or wear the equipment, protective devices or clothing that the School requires. 2) Work safely in accordance with TMS’s health and safety policy and program, and with the Occupational Health and Safety Act and applicable regulations. 3) Report unsafe conditions to the supervisor, after taking appropriate immediate action. 4) Report all accidents, injuries and near-misses immediately to the supervisor. 5) Work in a way that will not endanger yourself or others. 6) Advise other workers of unsafe conditions or work practices. 7) Participate in solving health and safety problems. 8) Provide recommendations to the supervisor to improve health and safety.
Crisis Management
In the event of a crisis situation proper procedures are to be followed. A list of all relevant crisis situations and what to do can be found in the Crisis Management Manual.
Joint Health & Safety Committee
Selection of the committee:
1) A Joint Health & Safety Committee of at least two persons is required at a workplace at which 20 or more workers are regularly employed. 2) At least half the committee members shall be workers who do not exercise managerial functions. 3) The worker member(s) shall be selected by the workers they are to represent. 4) The employer shall select the remaining members from among persons who exercise managerial functions. 5) The employer shall post the names and work locations of committee members on a bulletin board.
Responsibilities
The Joint Health & Safety Committee shall: 1. Meet at least once every three months. 2. Maintain written minutes of the meetings. 3. Conduct a monthly inspection of the work areas to identify hazards (worker member). 4. Report findings and make written recommendations to senior management. 5. Determine the time needed to conduct inspections. 6. Support the implementation and maintenance of the company safety program. 7. Assist senior management in the annual review of the company health and safety program. 8. Review inspection and accident reports. 9. Review committee membership to keep it representative of the workforce.
Safety Training
TMS will provide safety and related training that is necessary to minimize losses of human and physical resources of the company. Employees will participate in this training as appropriate.
This training will include, but not be limited to: ▪ Safety and Fire training ▪ New hire safety orientations ▪ Task and trade-specific training and certification ▪ Workplace Hazardous Materials Information System (WHMIS) orientation *The safety information in this policy does not take precedence over Occupational Health and Safety legislation. All employees should be familiar with the Occupational Health and Safety Act and the Regulations for Construction Projects (current edition), to the extent required for their jobs.
Employee Training/Instruction
All TMS employees will receive WHMIS training as required under current legislation. A record of this training must be maintained.
Material Safety Data Sheets (MSDS)
Responsibility for MSDS is as follows: Management: a) Review in conjunction with the supervisor all supplied material with the review of obtaining all MSDSs that are required. b) Obtain from the owner any MSDSs which are required for owner supplied material. c) Obtain from subcontractors any MSDSs which are required for material supplied by subcontractors. d) Cooperate with the owner/general contractor in setting up a general MSDS file for the schools. e) Ensure the facility manager has set up and has updated MSDS filing system on site. Facility Manager a) Ensure that there is an MSDS for controlled products used on the site and in the site file which is accessible to all workers. b) Review all TMS/Contractor supplied material and obtain all MSDS required. c) Make available “upon request” MSDS to all TMS employees. d) Ensure that proper personal protective equipment is available on site.
Hazard Reporting
Being aware of the surroundings helps to eliminate uncertainty. We encourage employees to take time to walk around the workplace and get a feel for their surroundings before starting any work. Employees are to report any problem areas immediately. If areas of concern pose a threat to the health and safety of an individual, that individual must report immediately to the supervisor on site. The supervisor will assess the situation and take necessary steps to correct the problem. If the situation requires a great deal of attention, then action must be taken.
Safe Work Practice
Industry standards have been developed for many safe work practices (e.g. use of ladders). In other instances manufacturers have developed specific safe work practices for their products. It is the responsibility of all employees to ensure they know how to use equipment safely, or to ask their supervisor for training if they do not know the safe work practices for use of equipment.
Maintenance Program
Introduction
This section has been included in our safety manual to highlight the importance of proper maintenance as a vital part of a safety program. It is vital that tools and equipment be properly inspected, maintained, and kept in good repair. Our maintenance program will reduce the risk of injury and damage.
Records
The maintenance program must contain a recording system. Part of this system should be made up of inventories and schedules. In addition, the recording system should document what maintenance work was done, when, and by whom.
Monitoring
The monitoring functions in a maintenance program fall into two areas. First, the people responsible for operating and/or maintaining equipment must monitor that equipment to ensure that appropriate checks and maintenance are done. Secondly, management should monitor the entire program to ensure that it is functioning in accordance with School policy.
Records Review and Statistical Analysis
Guidelines
In order to recognize hazards and monitor the success of the Health & Safety Program, reports, records and other performance measures must be reviewed. Analysis of these reports will provide information regarding which elements of the entire program need attention and improvement, and will assist in the prevention of accidents and injuries. In addition to Hazard Assessment Procedures already in place, it is TMS policy to perform annual reviews of the following performance measures: ▪ Hazard reports ▪ Accident investigations ▪ Lost time injury reports ▪ Joint Health & Safety Committee (JHSC) minutes To review data from these sources, it is necessary to establish a system to document, maintain and keep records on all injuries, accidents, and incidents that occur.
Roles and Responsibilities
Employee Report all accidents, incidents, first aid occurrences, lost time injuries and equipment damage to department head or manager
Department Heads/Managers
Senior Management ▪ Record all accidents, incidents, first aid occurrences, lost time injuries, equipment damage, and JHSC minutes ▪ Send all relevant health and safety information to HR department ▪ Coordinate first aid response, accident investigation or other follow up procedures subsequent to an occurrence. ▪ Maintain records of orientation, safety audits, and follow up actions. ▪ Monitor injury frequency rates. ▪ Compile an annual report on all health and safety activities and occurrences ▪ Ensure follow up performed for all action items.
Records Review and Statistical Analysis Procedures
1. All safety data is registered and recorded at the School, with appropriate responses initiated immediately (accident investigation, etc.). 2. All safety data are copied to management. 3. Room inspection checklists from routine safety inspections may be collected and statistically analyzed in a Health & Safety report.
Project Safety Data Room inspections Accident investigations
Lost Time injuries
Joint Health & Safety Committee, JHSC, minutes Statistical Focus Examples Number performed, issue involved, hazards identified Number performed, recommendations, by occupation Frequency, injury type, body part involved, by occupation
Issues identified, follow up, meeting frequency
4. Appropriate action is taken, beginning with management, to respond to trends, repeated contravention, repeated injuries or commonly identified hazards.
Applicable Legislation
Occupational Health and Safety Act, Sections 25-28.