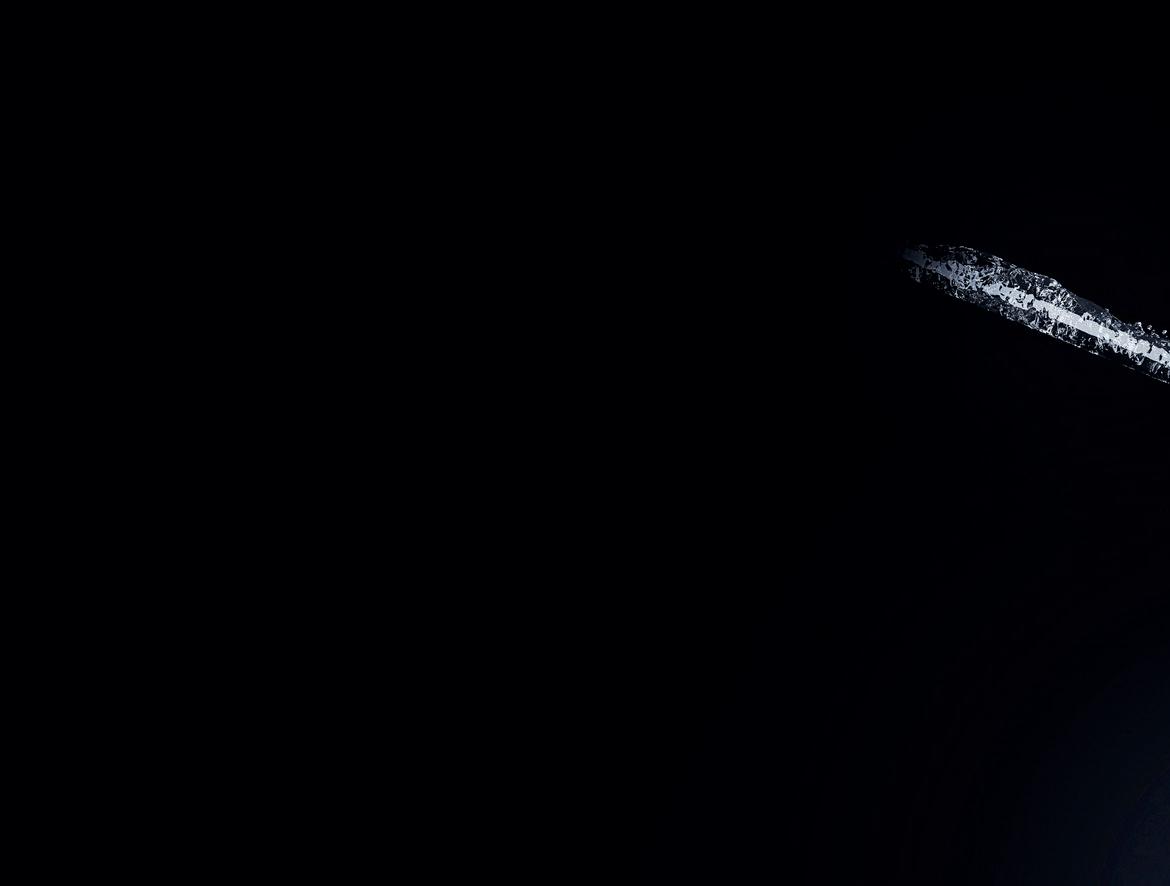
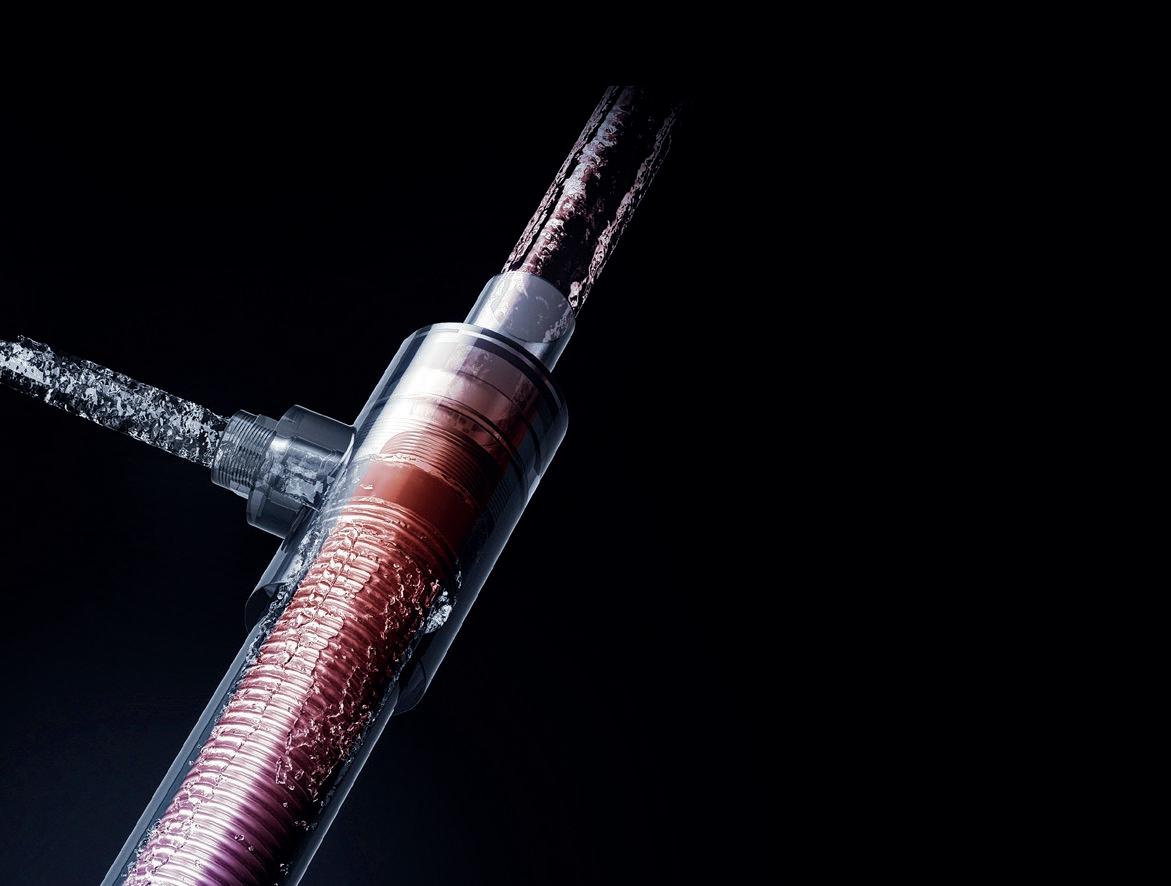
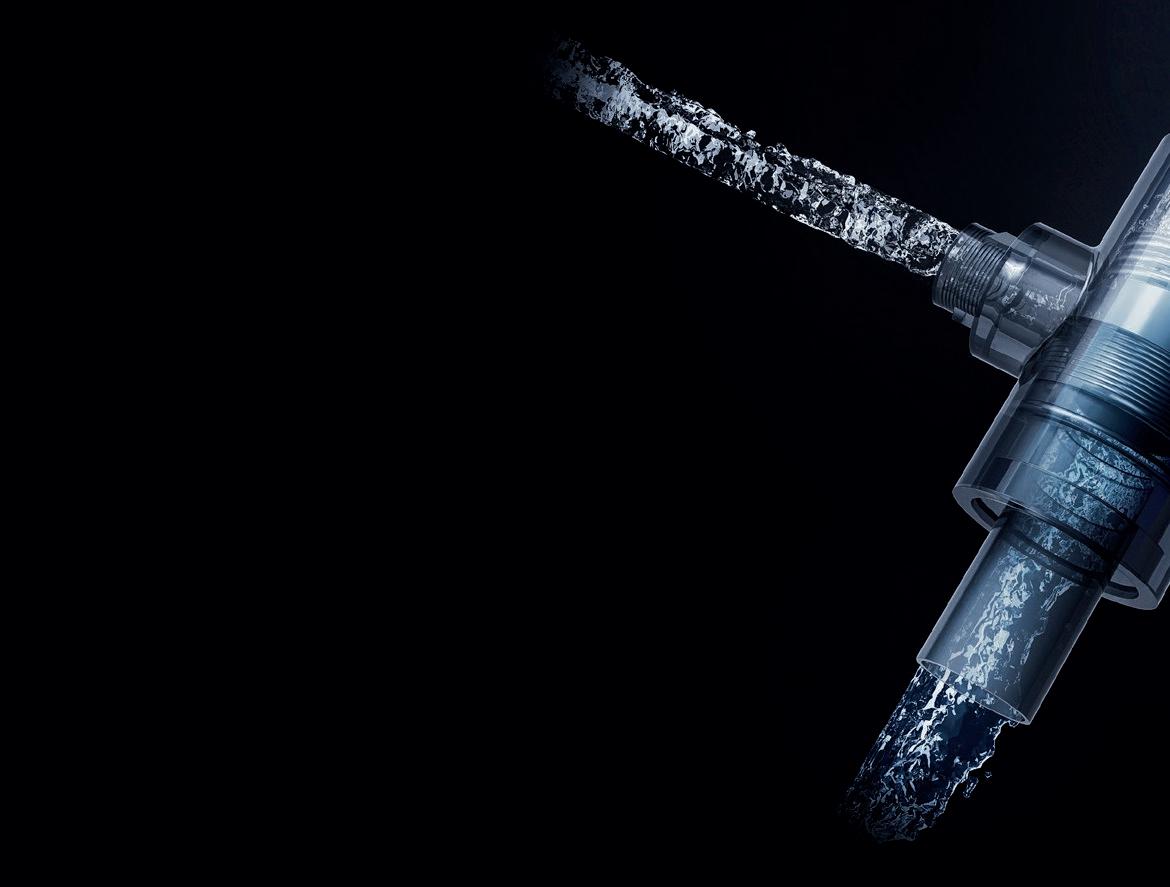
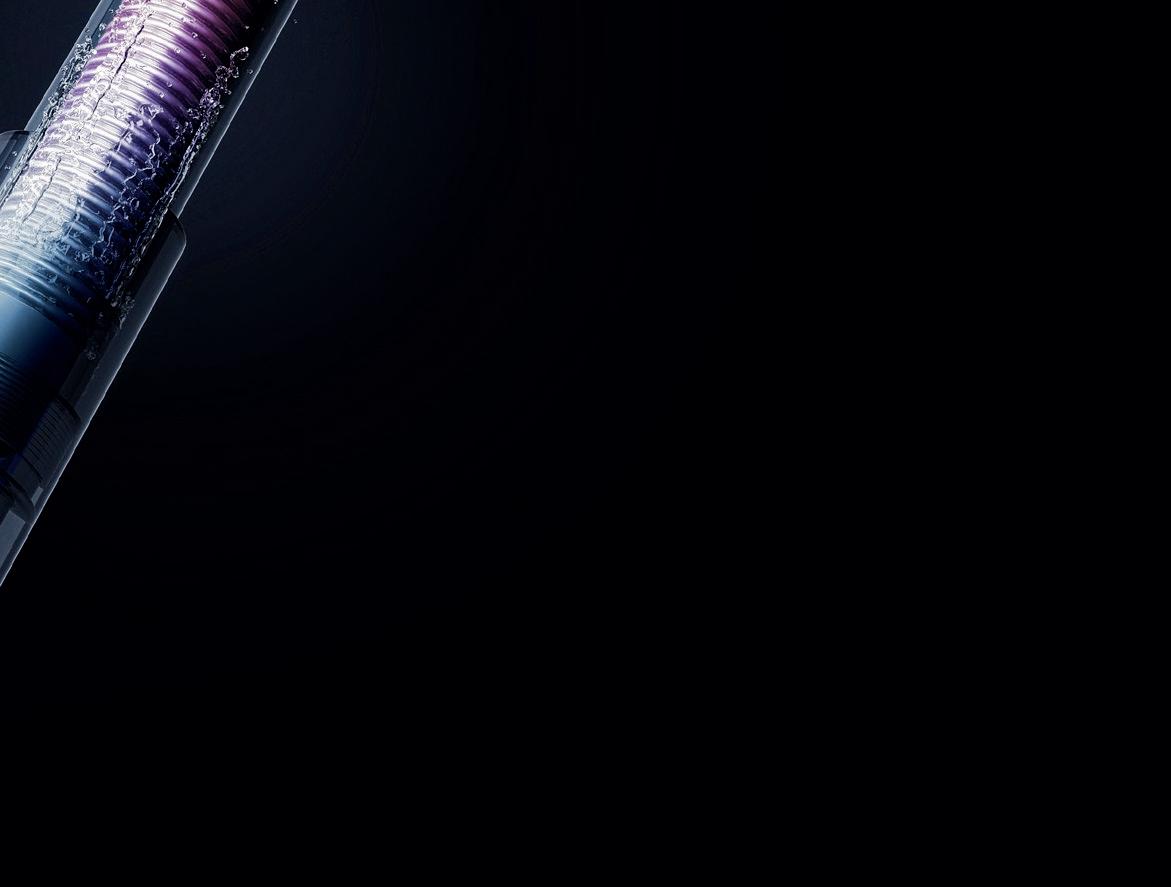

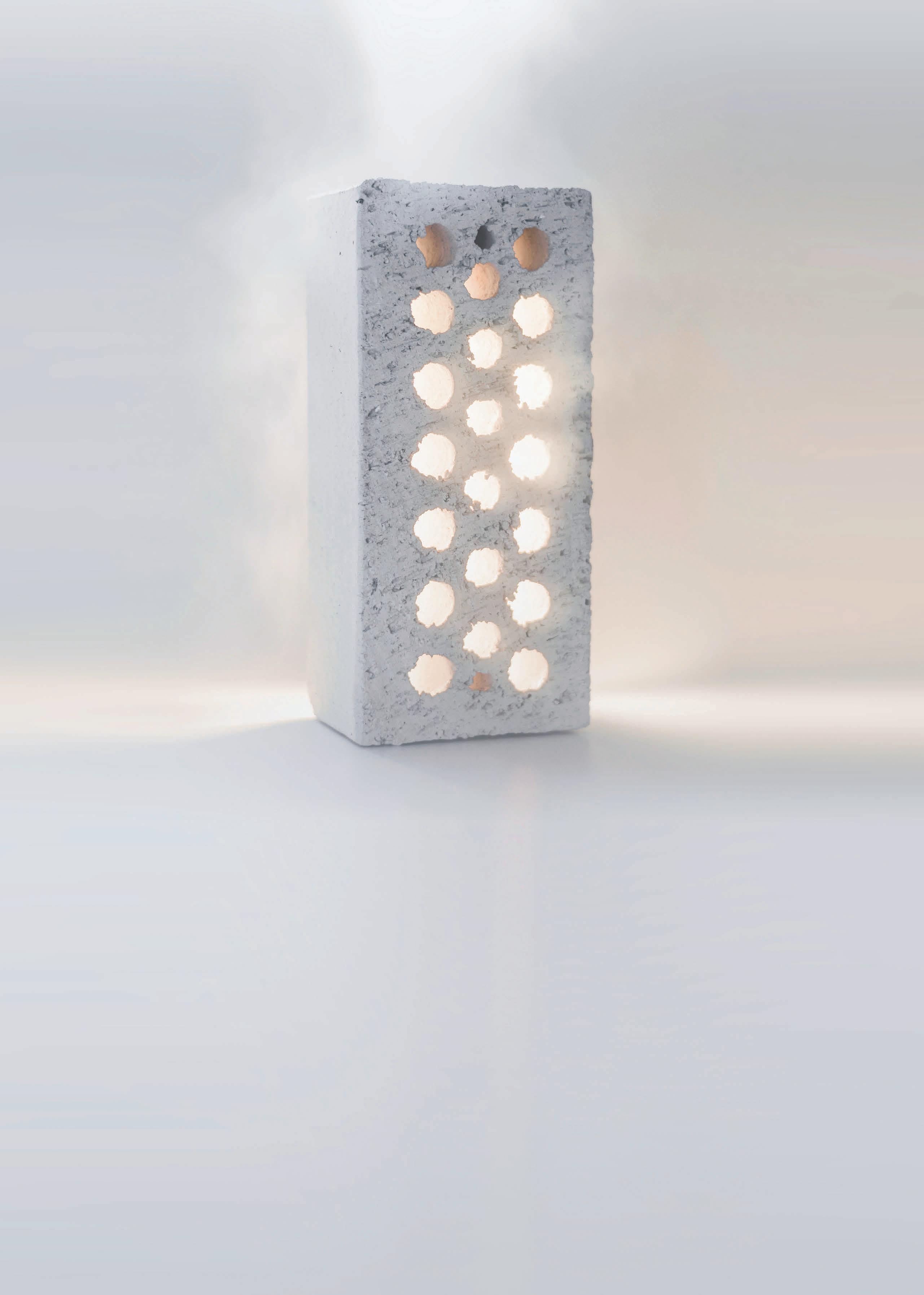
Manufactured in the UK, OSMO ® F1 is a new innovative concealed category 5 cistern designed to be stylish, versatile and easy to fit and service with minimal disruption to WC furniture or panelling.
Fitted with Turbo Edge® & Hydroflo® , the world’s most compact syphon & guaranteed to be leak-free & quiet fill type AG Inlet Valve
Unique Flush Handle, patented front access system, ergonomically tested design for optimum light touch operation.
The Government’s positive response to the Bacon Review is the third key element of its recent announcements, which includes the launch of the Help to Build equity loan and long term funding for the Right to Build Task Force.
The response includes the creation of a new delivery unit in Homes England for custom and self build, with community led homes also included in its remit as examples of owner commissioned homes. NaCSBA welcomes the response, especially the enthusiastic foreword by Stuart Andrew Minister of State for Housing, who wrote:
“The government strongly believes that self and custom build housing can play a crucial role-as part of a wider package of measures-in securing greater diversity in the housing market, increasing overall supply and helping to deliver the homes people want.”
Andrew Baddeley-Chappell, CEO National Custom and Self Build Association, commented: “Following the request of the Prime Minister, in August 2021 Richard Bacon presented his excellent report setting out his plan for a major scaling up of self-commissioned new homes.
“That plan included a limited number of necessary and achievable proposals that together would deliver the step change needed to increase diversity and quality within our new homes market. The response to the Review, together with the launch of Help to Build, delivers an important platform for growth of the sector.
“The Ministerial Forward is extremely positive and most welcome. The more detailed response contains important commitments with regards Homes England, Help to Build and the Right to Build legislation.
“It is however relatively high level, and in some areas, notably tax, there is less definitive commitment that we would have liked to see. In these areas we will continue to support Richard Bacon MP in ensuring the changes are required to deliver the major scaling up that is at the heart of this work. We are starting from a strong base but there is more to do.”
paul.groves@tspmedia.co.uk
Sustainable
Grass
Grass Concrete Limited info@grasscrete.com Tel: +44(0)1924 379443
For over 100 years, Mira has created innovative, solution led products to meet the needs of specification.
like the Mira HeatCaptureTM, that recovers heat from waste water to save energy and boost efficiency. Alongside product development, Mira has also invested in supply chain capability. The new distribution centre has been designed to respond to changes in demand quickly and efficiently, as the demand for
Newly-appointed Levelling Up Secretary Greg Clark has announced that contracts to turn the building safety pledge into legally binding requirements have been sent to major housebuilders to be signed within a month.
The Building Safety Act came into force last month and leaseholders are now protected in law from unfair bills to make their homes safe, and a rigorous regulatory regime will bring order to decades of lax practice. Former minister Michael Gove spearheaded the Government’s drive to ensure that companies should fix the buildings they played a part in constructing.
Some of the UK’s major housebuilders have pledged an estimated £2 billion to this end. But there remains concerns from key industry bodies, such as the HBF and the CPA, regarding what they regard as a lack of clear information and data on the scale of the cladding crisis and the role
developers and manufacturers should play in terms of financial contributions. Now, writing in The i newspaper, the new minister maintains that it is time these commitments are put into force.
He has published the contract that will turn that pledge into legally binding undertakings. “I will make it available for comment for 4 weeks, after which the contract will be finalised,” he explained.
“The faithful translation of these pledges into action is essential to the reputation for dependability that such an important sector of our economy must maintain. Nor will there be backsliding on the £3 billion building safety levy.
“The taxpayer is contributing £5 billion towards fixing those buildings which have been left orphaned by absent ee developers: the industry must pay its share too. The levy will be raised against all qualifying projects in England, and companies and firms who headquarter
themselves overseas will pay it, as well as home - grown developers. Ensuring that this funding is available to all affected buildings is essential to re-building confidence in the sector. The approach to industry contributions and leaseholder protection has the strong and unambiguous support of all parties in parliament. The Building Safety Act has given strong powers to disrupt the business of those developers that do not deliver on their pledge. Parliament rightly expects that the powers it has legislated be used unflinchingly, and they will be.
“The new Act also gives us new tools to pursue those who have contributed to this problem, not just housebuilders. I have instructed my department’s new Recovery Strategy Unit to target any individuals or companies – not just developers, but freeholders, product manufacturers, and contractors, wherever they register themselves–that do not step up to do what is required of them.”
RIBA announces House of the Year 2022 longlist Hill Group gifts six SoloHaus to council
The Royal Institute of British Architects (RIBA) has announced the longlist for the 2022. RIBA House of the Year.The 20 longlisted homes are:
• Derwent Valley Villa (Derbyshire) by Blee Halligan
• House at Lough Beg (Northern Ireland) by McGonigle McGrath
• Leyton House (London) by McMahon Architecture Ltd
• Mere House (Cambridgeshire) by Mole Architects
• Mews House Deep Retrofit (London) by Prewett Bizley Architects
• Mountain View (London) by CAN
• Norfolk Barn (Norfolk) by 31/44 Architects and Taylor Made Space
• Ostro Passivhaus (Scotland) by Paper Igloo
• Peeking house (London) by Fletcher Crane Architects
• Ravine House (Derbyshire) by Chiles Evans + Care Architects Ltd
• Seabreeze (East Sussex) by RX Architects
• Suffolk Cottage (Suffolk) by Haysom Ward Miller Architects
• Surbiton Springs (London) by Surman Weston
• The Cowshed (Dorset) by Crawshaw Architects LLP
• The Den (Scotland) by Technique Architecture and Design in collaboration with Stallan-Brand
• The Dutch Barn (West Sussex) by Sandy Rendel Architects Ltd
• The Garden Studio (Norfolk) by Brisco Loran and James Alder Architect
• The Library House (London) by Macdonald Wright Architects
• The Parchment Works (Suffolk) by Will Gamble Architects
• The Red House (Dorset) by David Kohn Architects (pictured)
The shortlist and winner of the RIBA House of the Year 2022 will be revealed in the seventh series of Channel 4’s Grand Designs: House of the Year, produced by Naked West (a Fremantle label), airing later this year.
Hill Group gifts six SoloHaus to council
The Hill Group has officially handed over the keys for six SoloHaus to Southend-on -Sea City Council, the first council in Essex to make use of these purpose-built modular homes as follow-on accommodation for people experiencing homelessness in the local area.
Regional Director Eastern Partnerships, Robert Jack at The Hill Group, and Captain Tracey Bale of The Salvation Army joined Southend -on-Sea City Council for the official handover of these purpose-built homes, providing much -needed safe and secure housing for people to rebuild their lives after a period of rough sleeping.The turnkey homes have been gifted by Hill, including all associated external works and installation. The Salvation Army-the church and charity that own and manage the project-will provide ongoing support to residents on their journey to independence.
Don’t think heating. Think sustainable business partner. Before your next project even begins, The Vaillant Standard has your back. With end-to-end expert support on everything from market-leading sustainability and flexible warranties to full heating system design… once you unbox The Vaillant Standard, you’re ready to take on anything.
Unbox our expertise, visit www.vaillant.co.uk/unbox
Derelict and underused brownfield sites across England will be transformed into thousands of new homes, creating thriving communities and levelling up the countrythe Department for Levelling Up, Housing and Communities has announced.
Councils will now be able to apply for a share of the new £180 million Brownfield Land Release Fund 2, which will help to transform disused urban areas into 17,600 new homes and create around 54,000 jobs over the next 4 years. An initial £40 million is available to support local regeneration projects, releasing council land for around 4,000 new homes (and creating 12,400 jobs).
The move will boost local economies and help thousands of young people and families into homeownership. The
remaining £140 million of the Brownfield Land Release Fund 2 will be made available to councils over the next 2 years. The scheme forms part of the government’s plan to level up communities across the country and turn unloved areas into new places for people to live and work Minister for Government Efficiency Jacob Rees-Mogg said: “Opening up this land is a fantastic opportunity for regeneration, improving government efficiency and playing a vital role in tackling the housing shortage while increasing home ownership. I am pleased to see this work is being delivered, after many attempts over the decades.
“This will provide a boost to the economy, foster the creation of thousands of jobs, and it is also the opportunity to convert derelict and unloved land into beautiful new hamlets or villages, which will give
many young families their first step on the housing ladder.” The fund aims to support the transformation of small council-owned sites that have been previously developed, by funding small scale infrastructure and remediation work to enable the release of the land for new homes.
This builds on the success of the first Brownfield Land Release Fund which saw £77 million go to councils across the country to release brownfield sites for around 7,750 new homes.
Councils will be able to draw on their understanding of local needs in determining the type, tenure and delivery approach for the new homes.
They have until 19 August 2022 to submit applications via the designated accountable body of their local OPE Partnership.
As part of two major regeneration projects, leading housebuilder Harron Homes has commenced construction of nearly 300 new homes on recently acquired land in Doncaster and Harworth. Both sites are the product of extensive investment schemes led by Harworth Group PLC, one of the UK’s leading land and property regeneration companies.
DLA Architecture has completed works on the redesign of the historic Shot Tower in Chester and handed over the completed scheme.
The site of the prominent landmark building has been transformed into a 72 unit residential-led development by Manchester based developer Whitecroft Group. The significant redevelopment incorporates the restoration of Grade II listed industrial heritage buildings
together with new-build elements. DLA has delivered a high specification scheme of one, two and three-bedroom apartments and duplex apartments alongside three, four-bedroom family orientated townhouses.
The homes are situated across the newbuild and listed elements with new public realm connecting the north and south side of the Shropshire Union Canal with the new business quarter and the rail station. www.housingspecification.co.uk
Harron Homes previously worked with Harworth Group at its Thoresby Vale site in Edwinstowe, where Harron has built 143 homes surrounded by beautiful views of Sherwood Forest.As two of the largest sites in Harworth Group’s portfolio, both Simpson Park and Riverdale Park look set to provide valuable opportunities for retail, residential, commercial, employment, leisure and green infrastructure developments.
Nearly a third (30%) of those responsible for fire door safety say they do not fully understand their responsibilities under the Building Safety Act, one of the UK’s leading authorities on fire door safety and third-party certification has revealed.
The British Woodworking Federation (BWF) Fire Door Alliance’s survey of 1,000 people with responsibility for fire door specification, installation, and maintenance across the UK identified a lack of understanding of fire safetyrelated responsibilities under the new legislation. Almost one in ten (8%) were unaware how new laws will affect how fire doors are specified. However, in signs of an early positive effect of new legislation, more than half of respondents said they would now ask for more information on product traceability and seek more proof of performance.
Helen Hewitt, Chief Executive of the BWF Fire Door Alliance, said: “Our findings clearly show that while the new legislation appears to have had a positive
initial impact, there is still some work to be done in disseminating the detail, and building an understanding of how compliance with the law can be met. This must be made an urgent priority for all those responsible for fire safety.”
The research, published in a new report as part of the BWF Fire Door Alliance’s Be Certain, Be Certified campaign explored understanding and attitudes towards third-party certification of fire doors, which can assist those responsible for a building’s fire safety to fulfil their legal obligations and offer robust proof of a fire door’s performance.
While, encouragingly, more than half (55%) of fire doors that respondents had responsibility for are third-party certified, 80% said that end clients, such as building owners and managers, do not require third-party certification.
Helen Hewitt said: “Third-party certification provides robust proof of performance and traceability of a fire door’s components, its manufacture
The first steel-framed modular homes manufactured at the CoreHaus factory were recently delivered, assembled and completed on a new homes site in the North East.
The County Durham-based company has handed over four three-bedroom semi-detached homes to regional housebuilder Homes by Carlton at its almost complete Thorpe Paddocks site at Thorpe Thewles, Tees Valley.
This is the latest milestone for CoreHaus, a social enterprise company, which operates from a 20,000 sq ft manufacturing unit on Jade Business Park, Murton, near Seaham. CoreHaus managing director Scott Bibby explained: “This project has allowed us to demonstrate the flexibility of our product by matching traditional aesthetics and finishes on these four homes while still offering a high level of pre manufactured value.
“It has been a genuine learning exercise where have been able to refine the
product, improve skills and knowledge while also bringing efficiencies to the manufacturing process.
“We will be able to speed up the entire process on future projects from design, manufacture, delivery, assembly, and final build.”
and journey through the supply chain. Despite this, there is still no mandatory requirement under Building Regulations for the use of third-party certified fire doors, despite the essential role fire doors play in protecting building occupants from the spread of smoke and fire.
“Our latest report, which we’re proud to launch as part of our Be Certain, Be Certified campaign, calls for those ultimately responsible for building fire safety to specify third-party certified fire doors as a requirement throughout all UK buildings. Not only will this raise the standard of fire door safety but crucially, it will help protect lives.”
Among those who do specify or use third-party certified fire doors, the primary reason for doing so is to meet and comply with fire safety legislation (47%). 40% said that the reason was to provide traceability of fire door components, manufacture and journey through the supply chain–highlighting a strong awareness of the benefits of third-party certification.
Located on the former site of an 18thcentury military barracks, St Arthur Homes has acquired a new collection of one and two-bedroom homes for Shared Ownership at TopHat’s Kitchener Barracks development in Chatham, Kent. TopHat is a leading 3D modular housebuilder which has recently announced it is building Europe’s largest homebuilding factory.The Kitchener Barracks apartments are being manufactured in TopHat’s existing factory at Foston in Derby where robotics and lean manufacturing techniques are used to increase housing supply, improve quality, reduce costs and protect the environment.
As AIMCH, the UKs flagship collaborative R&D project, whose aim has been to develop, trial and scale up industrialised housing techniques ends, Stewart Dalgarno, its Project Director reflects on its achievements and predicts what’s next for the house building sector.
MMC systems, suitable for volume, viable and scalable residential construction.
Net zero carbon homes are absolutely, possible. We know that from the Z-House Concept Home developed by Barratt, as part of AIMCH.
Moving forward, the focus needs to be on assembling a wider collaborative network — house builders, vehicle manufacturers, utilities providers, network operators, energy companies, and the community—to arrive at the most efficient way of scaling what we have learned and plugging AIMCH into an all-electric world.
Over the last 3 years AIMCH partners have sought to prove the efficacy of adopting near to market, scalable and viable industrialised approaches to housing delivery, such as panelised off - site modern methods of construction (MMC), design standardisation, housing pattern books and advanced manufacturing to build new homes.
This flagship housing innovation programme has been a truly collaborative enterprise involving forward thinking house builders, stakeholders, suppliers, sub-contractors and academia.
Because of our work, scaling up volume production of net zero carbon ready homes in a factory setting, is no longer an abstract concept. Panelised MMC methods and housing industrialisation are here to stay. AIMCH has built the framework, created the rule sets and blueprints for factory investments to scale up production, using automotive expertise and processes to accelerate panelised MMC capacity, as a viable system of choice.
As a result, we are going to see very rapid change over the next few years, with huge leaps in housing productivity, output and quality of the homes we build.
The AIMCH has lived up to its mantra ‘Structural shell built in a day’, ready for cladding and fit out, with the ground being laid for future prefabricated components beyond walls, windows, floor cassettes and roofs to be used, especially in high value areas like bathrooms.
These areas are very labour intensive, often accounting for 54% of the work on a new build home. Ripe for the MMC model, as prefabricated bathroom pods, providing a pod and panel building solution of the future, with increased pre-manufactured value (PMV).
However, AIMCH research into standardisation, utilising the L&Q methodology, identified the lack of repetition in bathroom designs, making volume production unattractive and not viable for low rise housing. AIMCH pattern book of homes, are designed to optimise standardised bathroom designs, using a kit of parts, that can provide the platform for future pod and panel hybrid MMC building systems of the future.
The next challenge for the sector is to engage with future MMC pod suppliers to find pathways to greater standardisation and making hybrid MMC systems commercially attractive, using standardised pods and panelised
AIMCH has demonstrated the path for scaling up industrialised house building using panelised MMC, focused on energy efficient fabric designs, standardisation, digital working, and advanced manufacturing. The next challenge– the electrification and integration of homes, communities, cars, and energy systems, is far greater.
Encasement’s range of pipe boxing and casings has been used across the UK for more than 15 years to conceal interior and exterior pipework in a range of social housing projects from fire sprinkler installations and heating system upgrades to low carbon district heating schemes.
Versa pre-formed pipe boxing is already installed in countless retrofit fire sprinkler projects to cover pipework in flats, lobbies and corridors, while for applications requiring a flame retardant solution, Versa FR pipe boxing provides an ideal solution.
For heating system refurbishment, Riva pre-formed pipe boxing is a quick, easy and cost-effective solution for concealing skirting level pipework, while boiler pipework, valves and flues can be hidden simply with Encasement’s ex-stock or bespoke boiler pipe casings.
All of Encasement’s plywood boxings and casings are manufactured, as standard, from EUTR/UKTR compliant sustainably sourced timbers, although an FSC® certified option is also available within the range. Also, as they are pre-finished in white melamine, they don’t require painting, which saves time and money on site.
Where external gas supply and distributed heating system pipework needs protecting from accidental damage, tampering or vandalism, Arma metal boxing provides a tough and durable solution. It is also increasingly being used to conceal air source and ground source heat pump installations, as well as interior sprinkler pipework in communal areas where no sprinkler heads are present, as Arma is non-combustible.
Bespoke manufactured from strong, lightweight and corrosion resistant aluminium, Arma profiles are usually specified with a PPC finish and can be readily secured to external walls using heavy-duty aluminium angle brackets and suitable fixings.
www.housingspecification.co.uk | To make an enquiry - Go online: www.enquire2.com or post our free Reader Enquiry Card
Michelmersh has announced its successful bid to the Department for Business, Energy & Industrial Strategy (BEIS) UK Government, Industrial Fuel Switching competition to conduct a feasibility study to replace natural gas with hydrogen in the brick making process.
The programme is part of the £1 billion Net Zero Innovation Portfolio (NZIP) which aims to provide funding for low-carbon technologies to decreasing the costs of decarbonisation.The project represents a global flagship physical study to replace natural gas with hydrogen in brick manufacturing. Phase 1 of the project will demonstrate the viability of fuel switching and will see hydrogen used in the clay brick production process at Michelmersh’s Freshfield Lane site.
The project aims to inspire radical change across the sector and present opportunities and evidence-based research to support manufacturers on their journey to heavily decarbonise the production processes.
As the organisation leading the BEIS ‘Deep Decarbonisation of Brick Manufacturing’ project, Michelmersh has gone a step further to promote and disseminate the progression and learning of the project through a dedicated brand; HyBrick.
Working alongside a panel of expert partners, and after an introduction
by Hydrogen Sussex, the consortium includes Limpsfield Combustion, Net Zero Associates, the University of Brighton, Greater South East Net Zero Hub, FT Pipelines, Geopura, and Safety Monitors.Green electrolytic hydrogen will be used for this innovative study, helping to demonstrate how this technology can transform the brick manufacturing industry.
All the consortium partners are thrilled to facilitate and promote the production of the world’s first 100% hydrogen-fired clay bricks, enabling a movement towards hydrogen and providing a pathway to the net-zero future that our country is aspiring towards.
This first HyBrick study will explore testing of specific infrastructure components to prove hydrogen firing capability and determine any impact on overall quality, brick integrity or aesthetics.
Data will be collected and analysed to ascertain any effect to process temperatures or stability. The bricks will then be compared against control bricks (produced using 100% natural gas) to
ensure they meet all technical, aesthetic and characteristic requirements, with independent laboratory testing to determine their durability and structural performance.
Of paramount importance and conducted throughout the project are dedicated health and safety risk analyses, assessments and training, alongside air quality performance testing.
Feasibility studies began in spring, and we will see the production of the world’s most sustainable clay bricks, and the first to be produced with 100% hydrogen.
To celebrate Michelmersh’s achievement and to encourage its customers to stand in unity with it on this journey to positive change, the Group will be presenting a select quantity of the HyBrick products to its most engaged customers and stakeholders.
D U-values ensure thermal performance Located on the former BBC site, Circle Square in Manchester aims to create a vibrant neighbourhood comprising city living apartments, prime office, retail and leisure space.
Phase two of the development saw the construction of No’s 5 to 8, four buildings totalling 677 luxury flats with private dining, resident lounge, gym and cinema, as well as commercial space. FK Group were appointed to design and install a bespoke façade solution which meant they were responsible for specifying the insulation.
There were three main performance factors that needed to be considered.Firstly, the insulation had to be non-combustible to ensure compliance with building regulations in England and Wales, which ban the use of combustible materials on the external walls of certain buildings over 18m tall.
The second consideration was thermal performance. “When you’re designing a bespoke façade solution, accurate thermal modelling is essential because there are so many variables that can affect its energy efficiency,” explained Ben Hufton, Associate Design Director of FK Group.
“One of the reasons we work with Knauf Insulation so much is because of their technical support. They always conduct 3DU- value calculations for rainscreen façade projects, so we know the insulation will deliver the performance we need to achieve.” This enhanced level of accuracy is one of the main benefits of 3D U -value calculations over other calculation methods, because it ensures a building’s real world thermal performance matches its initial design.
To achieve the required U-value of 0.28 W/m2K, the Knauf Insulation Technical Support Team recommended 200mm Rocksilk RainScreen Slab for the external cavity.
This has a thermal conductivity of just 0.034W/mK. Rocksilk RainScreen Slab is manufactured from Rock Mineral Wool and is BBA certified for use in high rise buildings for the broadest range of build-ups of any rainscreen solution on the market.
It is also non-combustible with the best possible Euroclass A1 reaction to fire classification. This means it will not contribute to the development or spread of fire should it occur.
The final specification factor was acoustic performance due to the site’s busy city centre location. FK Group conducted offsite acoustic tests to ensure that the build-up met the requirements of Approved Document E.
The Mineral Wool insulation contributes significantly to the acoustic performance of the build-up thanks to its open structure.
Sound waves are trapped between the individual strands of Mineral Wool and turned into heat energy. This will help to reduce noise from surrounding roads, ensuring residents can enjoy peaceful homes.
Rocksilk RainScreen Slab is also manufactured with ECOSE Technology, Knauf Insulation’s unique bio-based binder that contains no added formaldehyde or phenol.
It is made from natural raw materials that are rapidly renewable, and is 70% less energy-intensive to manufacture than traditional binder, so it is more environmentally-friendly.
For Fresh’s Pavilion Point student accommodation scheme, TECHNAL’s high performance glazing systems manufactured from low carbon recycled aluminium provided the solution to meet the project’s thermal, acoustic and sustainability goals.
The five storey development, designed by Corstorphine & Wright, targeted BREEAM Excellent standards as well as high levels of acoustic performance.
TECHNAL’s Elegance 52 ST curtain walling, Dualframe 75 Si Tilt Before Turn casement windows, Stormframe STII doors and C160S lift and slide doors were all specified for the Pavilion Point building. The systems are designed to integrate together seamlessly, making it easy to build multiple systems into a single project.
In addition to the TECHNAL products, the external façade features a clay brick slip system for the ground to third floors with a grey rainscreen cladding on the set- back fourth floor.
The use of TECHNAL’s aluminium systems contributed to creating an A1 rated noncombustible façade, a client requirement given the increased focus on fire safety.
The UK’s race to net zero by 2050 continues and with the built environment accounting for 40% of the nation’s carbon footprint, the housing sector faces a significant design and innovation challenge.
Supporting the housing sectors journey to net zero, shower manufacturer Mira Showers is proudly working with the University of Salford and Bellway Homes on the unique Future House @ Energy House 2.0 (EH 2.0) project. EH 2.0 is the largest test and research facility of its kind and is focussed on developing low carbon technologies to accelerate the progress towards net zero housing in the UK.
The environmental chambers within EH 2.0 contain houses under controlled conditions. The academic and technical teams can recreate a wide variety of weather conditions, with temperatures ranging between -20°C and +40°C and simulations of wind, rain, snow and solar radiation put in place to test the energy performance of numerous technologies under a variety of climatic conditions.
Mira Showers has spent the last 100 years creating innovative, solutionled products to meet the demands of specifiers, proudly demonstrating the brand’s commitment to sustainability.
Committed to supporting specifiers and new property developers in their bid to reduce their carbon footprint, Mira Showers has provided both existing technologies and yet-to-be-released innovations to the EH 2.0 project, including Mira HeatCapture™
Mira HeatCapture™ is an energy-saving system that utilises the heat from bathroom wastewater to increase the efficiency of a domestic heating system, so that the boiler applies less energy to heat water as the required heat rise has been reduced.
With hot water demand being added to the Standard Assessment Procedure (SAP) regulations for 2025, Mira HeatCapture™ helps specifiers and new property developers ensure building projects are in-line with regulations from the onset. In fact, the product will increase the overall hot water efficiency of a new home by up to 10%! Designed with a unique double wall stainless
steel exchanger, Mira HeatCapture™ has a ridged stainless-steel core that ensures water exiting the shower waste or bath clings to the side of the tube to transfer its heat to the cool incoming mains. Conforming to EN1717, the steel heat exchanger is perfect for new build applications. The technology not only provides incredible value to its SAP points ratio but offers KIWA-approved efficiencies of up to 64%, too.
Plus, once installed, it requires no further maintenance by the homeowner –meaning they can fit and forget whilst gaining all the benefits of the efficient system.
Improving the efficiency of new homes, Mira HeatCapture™ has been designed to provide specifiers and developers the opportunity to offer an effective and sustainable wastewater heat recovery system. Tested and certified by WRAS,
KIWA, BRE as well as being SAP registered, it has undergone rigorous testing and validation to ensure its performance, quality and longevity meet the high standards the brand has built its reputation upon.
Mira HeatCapture™ along with other Mira product innovations are currently being installed into the EH 2.0 facility ahead of testing and research programmes taking place, which are expected to continue until Spring 2023.
These programmes will spearhead future technologies for the housing sector and help to inform the development of Mira’s new product pipeline.
For further information, please visit the Mira Showers website: www.mirashowers.co.uk/heatcapture
Mira Showers - Enquiry 10
post our free Reader Enquiry
The world is facing a climate crisis, yet it remains hesitant about what to do. Another year of dramatic climate events and record-breaking temperatures helped yield an unprecedented societal will to act. There has never before been a greater consensus that humanity is at risk from a changing climate.
There remain, however, discrepancies in the sense of urgency that needs to be shared by everyone, if we are to protect the planet we have. This includes the consumer and individual households as much as it does multinational businesses and governments, but crucially also builders, engineers and developers – all of whom have the capacity to design and implement solutions at speed.
The residential sector holds the key to unlocking dramatic change; it is perhaps the area where individuals can make their greatest contribution, and where the total benefit is far greater than the sum of its parts.
By delivering a clear and simple path that people can easily, credibly follow to overhaul the environmental credentials of their homes, and by leading the charge against an established acceptance of energy wastefulness in our national housing, we can be the drivers of progress.
By spotlighting a path of innovation and improvement – evident in the buildings we design, build and operate – we can spur the supply of the right products, services, and developments that transform our chances of tackling climate change.
The opportunity is there. It is one we must seize.
The majority of the world’s decision-makers recognise that we are in a decisive decade. The outcomes of COP26 in Glasgow may have fallen short of the expectations of many, but the event demonstrated progress: the Glasgow Climate Pact was the first agreement of its kind to plan to reduce unabated coal usage. At Expo 2020 Dubai in January 2022, the United Nations relaunched its Sustainable Development Goals, calling on the Twenties to be a “decade of action”. Both the Irish and UK governments have committed to reaching Net Zero by 2050.
But there is only so much that high-level intervention can achieve. There needs to be bottom-up and mid-level engagement to support national and international strategies to limit carbon emissions, reach Net Zero commitments and craft a sustainable existence for centuries to come.
Nico Van Der Merwe is VP Home & Distribution UK&I at Schneider Electric, the global specialist in energy management and automation.
With our homes becoming increasingly connected and the spotlight on the inefficiencies of the UK&I housing stock becoming a great focus in the battle to halt climate change, Nico believes that smart and sustainable technologies such will have a large role to play in creating truly connected and efficient homes.
With electrical demand in the residential space growing, Nico believes that Schneider Electric already has the technology and relevant channels in place to bring these solutions from grid to plug.
As the UK’s first manufacturer to bi-directionally fire test its riser doors, Profab Access understands the importance of ensuring the highest standards of compliance and certification.
That’s why it has developed a comprehensive suite of fire rated riser doors that provide architects and specifiers with affordable yet compliant solutions that are ideal for specification throughout student accommodation and social housing applications.
This includes the VEGA 1500 Series, INTEGRA 4000 Series and VISION 8000 Series. As the riser door sets are fire tested from both sides for 60 or 120 minutes, depending on the riser doors specified, and are supplied with
comprehensive certification, architects and specifiers can be sure the doors will maintain their frame and integrity for this period, preventing the spread of fire throughout the building.
The VEGA 1500 Series Fire Rated Riser Door is supplied as standard with Profab Access’ revolutionary PRECISION adjustable frame, which completely transforms the installation process and reduces fitting times by up to 30%. The product’s unique construction enables the frame to be fully adjusted
to meet the specific dimensions of each structural opening. Featuring a continual adjustable steel packer system, the PRECISION adjustable frame ensures the installation is fit for purpose by providing the highest standards in accuracy, whilst also removing the requirement for traditionally used packers during installation.
The engineered frame also features built in factory applied intumescent fire rated mastic strips to the outer frame, which provides fire stopping between the wall and the frame.
This eliminates the reliance of the correct thickness of intumescent mastic bead being applied, removing any potential margin for error and ensuring compliance and adequacy of the entire installation.
Extensively bi-directionally tested by Efectis in France and Ireland, the riser door is suitable for use in shaft walls, standard flexible wall constructions and with all board manufacturers.
The lightweight, easy to install solutions provide professionals with permanent and safe access to mechanical and electrical services housed within a riser core.
Situated in the heart of Dublin just a short walk or cycle from Trinity College, Royal College of Surgeons Ireland and University College Dublin, Scape Aungier Street is a new state-of-the-art student accommodation complex.
Offering a diverse range of high quality accommodation options, from en suite rooms in shared apartments, through to large and premium studios, the latest Scape development features communal study spaces, large open plan kitchens and gym areas to offer students all of the amenities they require.
As part of the construction process, which was managed by John Paul Construction, 226 Profab Access Riser Doors were specified for installation by AE Doors throughout every part of the building, including the communal areas and individual bedrooms. The Riser Doors offer the highest standards of fire safety, supplied with third party accredited comprehensive bi-directional fire testing certification.
This means the Riser doors are fire tested from both sides providing the specifiers, contractors and ultimately the students residing within the building with confidence the critical fire integrity products offer the highest standard and most up to date evidence for fire safety performance.
The steel Riser Doors feature a slimline construction that doesn’t compromise on quality or functionality, offering aesthetics without compromise. Providing clean and concealed access to the riser shafts, the unobtrusive doors were specified with a central key cylinder lock.
This significantly streamlined the installation process for the team at AE Doors and reduced the risk of damage to the doors upon installation, particularly in the student bedrooms and bathrooms where access was restricted.
Pat Woods, Technical Sales at AE Doors, said: “Given the nature of this development we knew the quality and durability of the Riser Doors was paramount to ensure their longevity and continued efficiency.
“We have supplied and installed Profab Access’ Riser Doors for over two years and continue to be extremely impressed with the quality of construction, so we knew they would be the ideal choice for this project. The products are extremely easy to install and as they are manufactured in the UK, they are available with impressive lead times. This meant we could ensure the development of the project was kept on track, ready for its opening.”
The Riser Doors are acoustic rated, smoke sealed and airtight to Part L, whilst also featuring intumescent smoke seals that enable occupants to safely exit the building.
By specifying the bi-directionally fire tested Riser Doors, the development is actively future proofed as the comprehensive testing certification provides a complete and transparent audit trail of due diligence that evidences the products are not only fit for purpose, but meet the duty of care required to ensure legal compliance. Marcus Parnham, Commercial Director at Profab Access, said: “Scape provides students across Ireland, the UK and Australia with contemporary accommodation that offers
the highest standards in quality, safety and functionality.
“The specification of our bi-directionally fire tested Riser doors throughout all areas of the new Aungier Street development is a further reflection of this commitment, ensuring the building features the highest levels of riser shaft fire protection currently available on the Irish and UK markets.”
The Riser Doors were supplied with a high quality powder-coated matt surface, which were finished on-site in a range of bold colours to reflect the contemporary interior design scheme.
Profab Access’ diverse portfolio of Riser Doors and access panels are supported by a wide range of BIM Level 2 and CAD files to aid the specification process and streamline the initial design stages.
Manufactured at Profab Access’ UK headquarters in accordance with ISO 9001, the Riser Doors can be specified and installed in a range of configurations to meet each project’s specific measurements and requirements.
For further information on Profab Access and its range of access panels, riser doors and steel doors, call +44(0)1827 718222 or visit www.profabaccess.com.
Profab Access - Enquiry 12
An experienced builder and roofing contractor has made use of some 300 standard and tapered Marmox Multiboards to complete a complex refurbishment of a large, top floor balcony on an apartment building in North London.
Lightwood Construction carries out work for mainly residential clients right across the capital and has used Marmox Multiboards on many occasions in the past for both interior and exterior applications.
In this instance, long term exposure to the weather and ponding had caused the original waterproofing system to deteriorate, and leaks to occur.
Having stripped off all of the rotten felt and boarding, Lightwood Construction’s operatives installed 90 sheets of 20mm thick 1250mm x 600mm standard Multiboards, along with 200 of the 1200mm x 1200mm cut-to-falls variant which taper from 33mm down to 10mm: enabling subtle gradients to be created in draining the balcony to multiple outlets.
IDS had it covered at Housing 2022
Equally suitable for wet room applications, Marmox’s Sloping Boards are made from the same waterproofing products as Multiboard - thermally insulating
Decorative surface materials distributor IDS showcased its strength as a specialist supplier of flooring and wall panelling at Housing 2022 where it displayed a host of innovative new and existing products from its expansive portfolio.
As the UK’s largest distributor of decorative surfaces, IDS offers housebuilders and developers access to hundreds of wall panelling and flooring products from a range of quality and design-led brands, at a wide variety of price points and with the benefit of ex-stock delivery nationwide.
IDS has 18 branches nationwide, unrivalled stockholding and logistics expertise enabling products to be delivered anywhere in the UK in 48 hours.
IDS - Enquiry 14
Titon’s MVHR provides a breath of fresh air
Titon’s powerful but compact HRV1.6 Q Plus MVHR unit has recently been installed in Moda Living’s Lexington Tower on the Liverpool waterfront.
The ultra-compact HRV 1.6 Q Plus is a high-performance MVHR unit measuring just 600mm wide, enabling it to fit into tight spaces for easy installation and access. It has extremely low specific fan power (SFP) of 0.49 W/l/s and a heat exchanger offering efficiencies up to 89%, which enhances SAP performance via Appendix Q.
The lightweight HRV 1.6 Q Plus can achieve excellent flow rates of up to 100 l/s (359 m3/h) as independently tested by the BRE.
Titon - Enquiry 15
XPS sandwiched between two layers of Marmox’s patented polymer-concrete.
Marmox - Enquiry 13
Senior makes the most of its time in Greenwich
Senior Architectural Systems, the UK’s largest privately owned aluminium fenestration solutions provider, has supplied an attractive combination of aluminium curtain wall and commercial doors for a new mixed-use project in Greenwich, southeast London. Senior’s SF52 aluminium curtain wall system and PURe® Commercial Doors have been installed as part of the new Village Centre scheme at the heart of the existing Kidbrooke Village housing development, which has been designed by Lifschutz Davidson Sandilands and developed by Berkeley Homes.
Senior Architectural Systems - Enquiry 16
www.housingspecification.co.uk | To make an enquiry - Go online: www.enquire2.com or post our free Reader
A new case study from Interpave explores recent urban realm regeneration projects in Tottenham, London exemplifying the synergy of concrete block permeable paving and street trees to address climate change while delivering SuDS. It demonstrates important new techniques applicable to all urban areas.
The regeneration of White Hart Lane in north Tottenham, by muf architecture/ art, was a pilot designed using ‘Healthy Streets’ principles. But it also applies innovative sustainable drainage (SuDS) techniques introduced by design collaborators Robert Bray Associates. This approach reduces flooding and pollution through the integration of bioretention raingardens to collect and treat polluted road runoff.
In addition, extensive concrete block permeable paving surfaces not only act as SuDS elements – attenuating and treating rainwater runoff – but also enable essential air/CO2 exchange and optimised water supply for tree roots, using a range of techniques.
A new, concrete block permeable paved, adopted highway accepts runoff from
White Hart Lane and other impermeable surfaces. At two points, structural tree pits span the full width below the road surface, connecting road-narrowing tree planters on each side, based on the ‘Stockholm Solution’ for urban tree planting.
At the nearby renovation of Broad Lane Square, the same designers take forward these principles with further innovations. In particular, ‘inverted raingardens’ protect existing trees and new green infrastructure, supplied with a gradual supply of clean water from extensive concrete block permeable paving catchments.
Concrete block permeable paving –whether full-construction with storage sub-base or applied as an overlay to an existing impermeable road base – works in synergy with trees. It collects available
rainfall, including away from the canopy, and conveys it to trees and can be used over standard tree pits, proprietary tree planters, Stockholm System or other structural soil installations.
It enables irrigation and simple air/ CO2 exchange essential to trees –without additional reservoirs or pipes – and also avoids tree root disruption common with other paved surfaces. Concrete block permeable paving technology will prove invaluable in delivering the street trees now demanded by planning policies for developments, as well as regeneration.
For project case studies and guidance on all aspects of permeable paving, street trees and SuDS visit: www.paving.org.uk
Interpave - Enquiry 17
Fire doorset legislation has changed significantly in the recent years, with changes made at every stage in the lifecycle of a fire doorset, from design & testing to inspection & maintenance. For social housing fire doorset specifications, this means that all the stages in the lifecycle of a fire doorset, need to not just be included in the specification, but reviewed to ensure compliance with the new legislation.
One of the most important changes to legislation is The Golden Thread, created to link all stages in the lifecycle of a fire doorset. It is required for all high-risk residential buildings (HRRBs) to ensure that the original design intent of the fire doorset is preserved, that any changes must be made through a formal review process and the data for lifecycle is visible to responsible person(s) and tenants.
There are five steps in the lifecycle of compliance for a fire doorset, with the first step (Design & Test) being the key reference point for all other steps to ensure the original design intent is preserved.
As an example, if a fire doorset has a damaged or broken piece of glazing, the maintenance team will need to have been trained and have the knowledge of how the doorset was constructed. They must be able to replace components like for like and know what components should be replaced as part of this repair. This will ensure the fire doorset remains compliant and its performance is maintained as per original design intent. For example, how will a non-trained maintenance team be able to know the type of glass required to carry out a repair?
risk to you as the responsible person(s). Under the new legislation the responsible person(s) is both legally and financially at risk if The Golden Thread is not adhered to at every stage of the lifecycle.
Who are Winkhaus?
Over the past decade the Winkhaus UK technical team have been involved in the creation and implementation of the latest standards and guidance. All our fire doorset solutions are compliant with the latest MHCLG guidance and are triple Q Mark independent 3rd Party audited.
It is of paramount importance that maintenance teams are fully trained and have knowledge of the individual aspects of a fire doorset. This should include, tested performance knowledge and product composition to ensure what was tested is the same as what is surveyed, manufactured, installed and maintained.
We are seeing an increasing number of report cases where components are being replaced during maintenance with components that are not part of the original test data and even where non-fire rated components have been used.
When specifications are changed and aren’t reviewed to ensure compliance with legislation, this brings significant personal
Winkhaus UK Composite Fire Doorset solutions are the first to attain the new Q Mark 3rd party audited certification for Smoke and become the first company to attain Q Mark certification for all three critical performance requirements Fire, Smoke & Security. Winkhaus UK Timber Fire Doorset solutions are also currently completing accreditation.
What can Winkhaus do for you?
If you’re unsure whether your specification is complaint or unsure about what compliance is, we can do a specification health check or even write your fire doorset specification.
We have expanded our free training to aid the understanding of the new requirements for a compliant fire doorset specification. We offer three different levels of training which can be tailored to the audience to ensure it meets your requirements.
To further aid in adoption and understanding of the new legislation we have created The Golden Thread for Fire Doors Checklist which provides you with a definitive list of key things that you are required to include in your specification at every stage of The Golden Thread.
To register for our free training, to receive a specification health check or a copy of our specification checklist, please visit www.firetraining.winkhaus.com
Winkhaus - Enquiry 18
www.housingspecification.co.uk | To make an enquiry - Go online: www.enquire2.com or post our free Reader
Hybrid working is here to stay, and the housing industry is no exception. According to the latest figures from ONS, 33% of housing firms will adopt the new working model in the long-term, marking a big shift from traditional office life.
For housing professionals, switching to Intratone’s wireless access control technology can help put this into practice – allowing them to manage multi-resident properties more effectively by moving most administration tasks online and minimising the need for site visits.
All Intratone’s door entry devices – from intercoms to coded keypads – connect to an online, secure remote management system, so it’s never been easier to work away from the office.
Housing managers have a real-time overview of building access and can update tenant information from a central, digital platform – wherever they are. Simple tasks like deleting key fobs and
granting entry to external contractors can be done in just a few clicks. This helps to significantly streamline time-intensive processes that would normally need to be done in-person – reducing site visits and centralising operations.
The latest wireless access control devices do more than just simplify door entry for tenants. Choose the right model and it can make a real difference to housing providers’ working lives – for the better!
Interested in hearing how Intratone’s range of wireless door entry systems can help your hybrid working life? Visit www.intratone.uk.com.
Intratone - Enquiry 19
Nittan Europe has had its Evolution analogue addressable fire detection system installed throughout Ashburton Triangle, situated on the Emirates Stadium site in North London. The system was supply and commissioned by Nittan Elite Partner Coomber Fire and Security Systems. Nittan’s advanced, premium Evolution analogue addressable fire detection system was specified for this iconic development due to its exceptional reliability together with a very high degree of protection against unwanted false alarms. Furthermore, its flexible protocol allows for substantial amounts of information to be transmitted at high speed supporting high-performing cause and effect programming - a key factor in the decision-making process.
Sierra Windows is launch partner for Yale SensCheck
Yale has announced Sierra Windows as the first official launch partner for SensCheck™, the company’s new range of integrated smart window and door lock sensors.
The partnership will see Sierra Windows –part of the Epwin Group – supply all its PVC casement window, flush window, and door products with SensCheck™ compatibility as standard. This will enable homeowners to check the status of their doors and windows using their smartphones and devices while providing an outstanding smart advantage for installers. The range is also compatible with leading voice partners Amazon Alexa and Google Assistant.
Sierra Windows - Enquiry 20
Nittan Europe - Enquiry 21
Pyroguard’s fire safety glass was the product of choice on the Quantock House development, one of the first UK projects to feature a compliant A2-s1 glass balustrade system on its apartment balconies. Quantock House is also one of the first UK projects to have an NHBC accepted A2-s1 glass balustrade system installed on its apartment balconies - the result of a close working partnership between fire safety glass manufacturer Pyroguard and Architectural Metalwork Installations Limited (AMI), the architectural metalwork specialist. This collaboration resulted in the development of AMI’s Fire-Tek Balustrade system, featuring Pyroguard Balustrade fire safety glass.
Pyroguard - Enquiry 22
www.enquire2.com or post our free
The SC-03 isn’t just a point of access. It’s a wireless solution that promises an advanced user experience, with scrollable functionality and a vandal resistant, durable and full colour screen. Better visibility with its light sensor and excellent functionality with its online remote management system.
The quality you are used to with new features you won’t want to miss.
Discover Intratone’s SC-03 wireless intercom. www.intratone.uk.com
Renowned for its ability to assure a clean, unhindered appearance to doors and interiors, Samuel Heath’s Powermatic controlled, concealed door closer is used extensively in flats, apartments and HMOs throughout the social housing sector thanks to the safety, reliability and low maintenance benefits that the door closer delivers.
Unlike surface-mounted door closers, Powermatic is completely concealed when the door is closed, and not easily visible when open. This can significantly reduce the opportunity for the door closer to be vandalised, tampered with or removed.
Together with the fact that the door closer is maintenance-free and facilitates adjustment of closing speed and latching action without removal from the door, this attribute can result in a reduced maintenance burden for social landlords. Reduced risk of vandalism also provides significant safety benefits; a damaged door closer can prevent the door from closing correctly. Any door, especially a fire door, that fails to function is, at best, an inconvenience and, at worst, potentially fatal.
Samuel Heath - Enquiry 24www.housingspecification.co.uk | To make an enquiry - Go online: www.enquire2.com or post our free Reader Enquiry Card
As Building Regulations continue to come under rising scrutiny, contractors are increasingly turning to the reliability of tried and tested high-performing British roofing underlays such as Roofshield.
The A. Proctor Group developed Roofshield 26 years ago in response to problems caused by the requirements of the UK’s demand for cold-pitched roof construction and the drive towards ever-increasing thermal performance requirements. Roofshield is designed to ensure contractors are guaranteed the highest quality, providing a pitched roof underlay, which is both air and vapour permeable.
Under guidelines issued by the NHBC, independently certified air and vapour permeable underlays can be used without additional ridge ventilation in cold roofs. The use of Roofshield will lead to savings in labour and material costs due to the fact that no vapour control is required, and its high-performance air permeability means that the roof space has similar air changes to that of a roof using traditional eaves/ridge ventilation.
Since 1996, the A. Proctor Group have played a crucial role in pitched roof design, helping develop practical air and moisture movement strategies to ensure roofs are energy efficient and condensation-free.
The primary sources of moisture that roofs must control are 1) moisture from internal sources, water vapour and condensation, and 2) moisture from external sources, rain, and snow.
Protection from external moisture is assumed to be handled by the external weatherproofing, but roofing underlay membranes can provide temporary weather protection until the outer covering is completed. In addition, underlays continue to support roof systems throughout the building’s life, providing wind uplift resistance and protection against wind-driven moisture penetrating the structure.
BS5250 gives detailed guidance on different combinations of roofs and underlay types (HR vs LR) to ensure each roof system can respond to moisture challenges within acceptable limits. A roof that cannot adequately deal with moisture is susceptible to adverse effects, including mould growth and long-term structural damage.
A critical first factor is the air permeability of the external roof covering. If it is considered air-impermeable, such as in the case of metal sheeting, some degree of ventilation will be required. On the other hand, natural slates and tiles are usually considered sufficiently air permeable.
The traditional pitched Cold Roof (ventilated) is used as the historic standard against which modern alternatives are evaluated
in condensation risk and timber moisture contents. However, given the various categories and differing guidance for ventilation and the lack of precise specification advice for more complex roof types and shapes, a more straightforward option is to omit the ventilation and rely on the vapour permeability of the underlay to remove moisture.
Cold Roof (Non-Ventilated) - Where airtight LR underlays are specified, BS5250 does not address situations where ventilation is reduced below the levels given in L5.5. However, it may be permissible if the underlay is covered by appropriate third-party certification. Using an air-permeable low resistance (APLR) underlay such as Roofshield in this roof type requires no additional ventilation. APLR underlays allow vapour to escape by diffusion and provide a degree of airflow to boost moisture vapour transfer. APLR membranes can generally be used in all circumstances without ventilation, regardless of the size and shape of the roof. In addition, they don’t require a well-sealed ceiling and may not require a VCL, making this type of underlay a good choice for refurbishments where the precise ceiling specification may be unknown.
The lack of a sizeable cold void in warms roofs makes controlling moisture simpler, provided the correct specifications are followed. Warm roofs with impermeable HR underlays will always require ventilation below the underlay and a VCL at ceiling level. Using an LR underlay can simplify moisture control and may allow the ventilation to be removed, provided the internal layers are convection tight. If this can’t be guaranteed or the outer covering is not air permeable, ventilation will be needed.
Where insulation follows the roof’s pitch from the eaves to the ridge, the lack of roof voids means less benefit to using an air-permeable underlay. A pure warm roof design lends itself to maximising energy efficiency and prioritising low air leakage rates. If we extend this principle to the rest of the building, the airtight warm roof construction could be integrated into the wall assembly with an external air barrier membrane such as Wraptite.
Whatever the roofing type, in meeting the increasing demands of Building Regulations, contractors can rest assured of the reliable performance of a great British roofing underlay in Roofshield. The high performance of Roofshield, backed by two BBA Certificates, means it is a critical element in preserving and protecting the fabric of residential and commercial buildings.
But is the industry prepared?
Changes to Part L of the Building Regulations - which sets the standards for the energy performance and carbon emissions of new and existing buildings –came into force on the 15th June this year.
And, according to an exclusive survey* of housebuilders, architects, and specifiers conducted by Marley, almost two thirds of respondents are ‘unaware’ of the changes outlined in Part L.
The survey found that for those that expressed knowledge of the new Part L regulations, ‘cost pressures,’ ‘a lack of skills to implement the changes’, and low levels of ‘client understanding around sustainability’ were viewed to be the biggest challenges.
Questioned about confidence levels associated with the changes and their resulting responsibilities, 79% admitted they ‘did not feel confident’ about their understanding of the new responsibilities ahead of the impending revisions.
With solar PV roofing systems widely acknowledged to be an important product solution to help produce the low carbon and energy efficient housing required in the future, the positive news is that two fifths of those polled said
they were already aware of the role solar PV can play as a sustainable technology within the overall building fabric.
When asked about the main challenges to the implementation of the Part L changes, the primary concerns focus on the cost pressures it will bring. In addition, the issue of the current lack of skills needed to implement the updates, and the level of client understanding around the issue of sustainability, were also cited as challenges.
Probed about product specification considerations around sustainable construction and reducing carbon emissions, the issue of having an extended warranty when selecting solutions was deemed to be ‘very important’ by nearly half of those questioned.
The ability to demonstrate strong sustainability credentials was also considered to be a ‘very important/ slightly important’ factor for nearly three quarters (73%) when it came to selecting a product manufacturer or supplier.
Stuart Nicholson, Roof Systems Director for Marley, comments: “The findings from our latest research makes for interesting reading. With the introduction of changes
to Part L as part of the roadmap towards 2025’s Future Homes Standard, and it appears that awareness and subsequent confidence around the impact of this important milestone among housebuilders, architects, and specifiers is currently low.
“With solar PV identified as one of the key technologies to help create low carbon housing, alongside other sustainable heating solutions such as heat pumps, it was encouraging to see good levels of awareness about the role solar PV can play in helping meet the Part L-related 31% carbon reduction target for all new homes.”
For more information from Marley, or the ways Marley SolarTile® can help housebuilders meet Part L changes, visit: www.marley.co.uk/partlspec
Marley - Enquiry 26
Following on from the announcement that EOS Framing has reached the finals of the Construction News Specialists Awards and has an unprecedented seven entries shortlisted in the Offsite Awards, the leading steel framing innovators have reported that the company has been awarded Buildoffsite Property Assurance Scheme (BOPAS) Accreditation.
BOPAS Accreditation is recognised by principal mortgage lenders as providing the necessary assurance underpinned by a warranty provision that the property will be readily mortgageable for at least 60 years.
For funders and lenders BOPAS provides assurances that EOS Framing’s light steel systems are fit for purpose and eliminates the uncertainty surrounding the construction for valuation purposes.
It also removes the risk for developers of mortgages being declined on construction grounds and improves business opportunities for EOS as a manufacturer of offsite systems.
BOPAS demonstrates to funders, lenders, valuers and purchasers that homes built from non-traditional methods will be durable, delivered to high quality
standards and stand the test of time. Managing Director of EOS, Steve Thompson stressed the importance of certification and accreditation: “We take our responsibilities as a manufacturer extremely seriously. Our light steel frame systems are rigorously tested, manufactured under ISO 9001:2015 quality management standards and are now backed by BOPAS Accreditation.
“Our aim is to deliver confidence and certainty in the construction process and empower specifiers to be technical forerunners in the offsite sector. This achievement has only been made possible by our dedicated team who share our vision and values. My thanks and appreciation goes out to all those involved.”
Against a backdrop of government targets to build 300,000 homes a year combined with increasing construction costs and poor quality conventionally constructed houses as well as a huge shortfall in
traditional skills – the demand for innovative offsite construction methods has never been greater.
Complete and Compliant Systems
Specialising in advanced light steel framing technologies, EOS is taking the construction industry forward by pioneering a new certified systems approach, helping specifiers to comply and compete in challenging markets.
EOS are committed to technical competence and as part of Etex, have some of the best building performance experts in the UK on their team. They work closely with certification bodies to jointly develop and design advanced technical solutions.
To discover how EOS systems are delivering certified, predictable and warrantied performance, go to: www.eosframing.co.uk
EOS - Enquiry 27
Onduline, the light weight roofing systems and water-proofing specialist, is delighted to announce the launch of its new and unique under roof system, ISOLINE® low line-the only system in the UK to be BRE tested and BBA accredited to as low as 10O.
Easy to carry, handle and fix, the non-slippery sheets are simple to cut with vertical overlaps embossed into the sheet.
This makes installation even quicker and easier as it takes away the need to measure and it also removes confusion when it comes to knowing how much to overlap.
Due to the corrugations, ISOLINE® LOW LINE allows increased ventilation and airflow both above and below the sheet and tile battens positioned above the corrugations allow moisture to drain to the eaves which, with the enhanced ventilation, maintains excellent moisture control within the cavity.
The material is also in line with the growing awareness of ‘green’ issues and the need to offer sustainable solutions as ISOLINE® LOW LINE sheets are made of a minimum 50% recycled cellulose fibres, contain no asbestos and do not release any hazardous substances.
Onduline - Enquiry 28
Designed specifically for use on low pitch roofs, this lightweight bituminous underlay sheeting has been rigorously tested and is proven to be at least three times less likely to leak compared to a traditional tile system.
With a corrugation height of just 24mm, ISOLINE® LOW LINE is fixed below the primary tile or slate roof covering, acting as the primary waterproofing layer of a roof. Thus, making roof tiles a secondary line of defence enabling the pitch of the roof to be much lower than the minimum as recommended by the tile manufacturer.
Not only does this help to meet the demand for maximising living space, as the low pitch means the roof void can be minimised, it also enables traditional tiles to be used in situations where they
wouldn’t have been able to be utilised previously, such as extensions or large roofing projects, greatly enhancing the aesthetic quality of a property.
Ardit Strica, Technical Manager for Onduline Building Products, said: “We’re delighted to be launching ISOLINE® LOW LINE, it’s exciting as it is the only under roofing system in the UK that can be used on a pitch as low as 10o, which is huge for the construction industry.
“Maximising ease of use for the installer was also a key priority for us with the design of this system, with the smaller corrugations of the sheet not only adding rigidity and strength, they also allow for easier fixing and greater compatibility with mechanical fixings for solar panels, which will be key over the coming years.”
Amid concerns over rapidly escalating energy prices - and with more rises to come- homeowners are naturally concerned over how they can conserve energy and keep costs down.
Installing Granada Glazing’s secondary glazing has helped the owners of a singleglazed apartment to save around 40% on their monthly electricity bills, as well as exclude external noise.
Lindsey Gordon’s monthly electricity bill dropped from around £450 per month to £230 in the following month after 11 secondary glazed panels were fitted in her three-bedroomed home at Murrays’ Mills, Ancoats in central Manchester.
Formerly the world’s oldest steam powered cotton mill dating back to 1797, the Grade II & II listed buildings have been sensitively restored for residential use. The 107 apartments retain many historic features, such as exposed brickwork walls and multi-pane, sash and bay heritage windows.
“Secondary glazing is the best investment we’ve made, I think, on this property to date. It’s made a huge difference, saved us money and the flat is now silent and warm,” comments Lindsey, who moved into the all-electric duplex flat in November 2019.
“We had a whole year where we couldn’t understand why the bills were so big. It was a combination of not having secondary glazing and leaving the heaters on most of the time. I reckon it’s a 40% saving overall.”
Reducing outside noise intrusion was Lindsey’s main reason for getting secondary glazing and the 6.4mm acoustic laminate glass offers enhanced sound insulation that can reduce noise levels by as much as 80% (54 decibels).
Granada Glazing - Enquiry 29CUPACLAD 101 Logic was recently installed as part of a striking new-build project, located in Aberystwyth, Wales. The natural slate cladding was chosen because it could complement the coastal surroundings as well as provide outstanding resistance to the harsh weather conditions.
High quality natural slate is a very resistant material – its deterioration is unnoticeable to the human eye, meaning its colour does not change across its 100 year lifespan, even in the coldest environments. Natural slate also has a permanent sheen, unlike other roofing materials which can decrease up to eight times superior. CUPACLAD is constructed using specially selected slates, which are dark in colour, creating a bold and dramatic look, particularly when utilised alongside lighter materials such as glass, timber and render.
CUPACLAD 101 Logic is made up of 40x20cm slates installed horizontally using fixing systems that are completely invisible once installed to avoid impacting the design. As with the rest of the CUPACLAD 101 series, it is BBA certified, verifying that it has an incredibly low level of water absorption, test results show a value between 0.16 and 0.17%. Furthermore, the BBA certificate demonstrates the slate is very resistant to high winds, fire and impacts.
Add timeless elegance to your property with Garador’s Georgian style garage doors. These stand out garage doors have been beautifully designed with deep, crisp panel pressings to add exceptional quality and style to the overall look. The more formal, traditional design will instantly enhance both modern and traditional properties in a variety of surroundings from suburban cul-de-sacs to period country homes. Each of Garador’s Georgian styles have been precision engineered with rivet free panelling to ensure the smooth, clean outlines of this special door. Available in a range of smart durable colour finishes, these doors stand head and shoulders above other panelled garage doors currently on the market. They are available in an array of standard and made-to-measure sizes for both single and double doors.
Garador - Enquiry 31
www.housingspecification.co.uk | To make an enquiry - Go online: www.enquire2.com or post our free Reader Enquiry Card
www.housingspecification.co.uk
provides the natural solution for new coastal home
To support housing specifiers successfully navigate industry regulations, legislation and the green agenda, Vaillant has brought together its end-to-end expertise and support teams under the umbrella, The Vaillant Standard.
Already offering a robust portfolio of heating products, from energy-efficient heat pumps and boilers to effective controls, The Vaillant Standard showcases the business’ complete support offering for housing specification customers. Including pre-planning, system design, consultancy services and aftersales support including flexible warranties.
The Vaillant Standard means housing specifiers can make the most of this wider support to help plan projects, meet the challenge of designing sustainable heating systems, maximising the potential of each build and allowing customers to provide the best service for future homeowners.
Drawing on the knowledge of its expert teams, each step of a building project or development is covered. For example, Vaillant’s pre-planning and design service team can offer fully indemnified heating system designs and support on
designing for new build developments, helping to mitigate possible issues before they occur.
Vaillant’s dedicated national specification team is also available to advise throughout a project too, arranging training as needed, and ensuring the project is feasible and designed to meet the correct standards. Commissioning, servicing, and maintenance is offered for all products where required and designed to suit individual project needs. A 300-strong aftersales and customer support team can continue to provide support even when the build is complete.
Adam Tilford, Sustainability Manager from Top Hat Construction, commented; “We included aroTHERM plus heat pumps within one of our more recent modular builds. As well as providing onsite support to ensure the products were correctly installed and commissioned throughout the build,
Vaillant provided our contractors, Sub Modular, with inhouse training in Belper, covering both of these elements plus how to set up the sensoCOMORT controls to get the very best out of this technology. The result is a quality finish all involved are proud of.”
Commercial Director, Steve Cipriano at Vaillant, comments, “We are all aware that one size does not fit all, and each development brings its own challenges and questions. The Vaillant Standard ensures that our customers across the country have access to the expert advice they need, when they need it most. Giving peace of mind from the beginning to the end of each project.
“It is never too early to speak to our teams either. Tapping into the support available can help tailor the solution to suit a particular build or development, creating a result that delivers now and into the future.”
Built around Vaillant’s strong specification proposition, The Vaillant Standard is backed by the assurance of quality. All Vaillant products are designed with housing specifiers in mind, built to last and are lifetime tested for up to 15 years. Using the highest quality materials, each product is built using the one-piece flow method, meaning every product can be traced back to its manufacture.
To find out more about the Vaillant Standard visit www.vaillant.co.uk/unbox.
Michelmersh is excited to announce a global flagship physical study to replace natural gas with hydrogen in brick manufacturing. Sponsored by the Department for Business, Energy & Industrial Strategy (BEIS) UK Government, phase 1 of the project will demonstrate the viability of fuel switching and will see hydrogen used in the clay brick production process at Michelmersh’s Freshfield Lane site. The project aims to inspire radical change across the sector and present opportunities and evidence-based research to support manufacturers on their journey to heavily decarbonise the production processes.
To follow the project, or to sign up for your chance to receive one of the first hydrogen-fired clay bricks we produce, head over to:
www.mbhplc.co.uk/hybrick