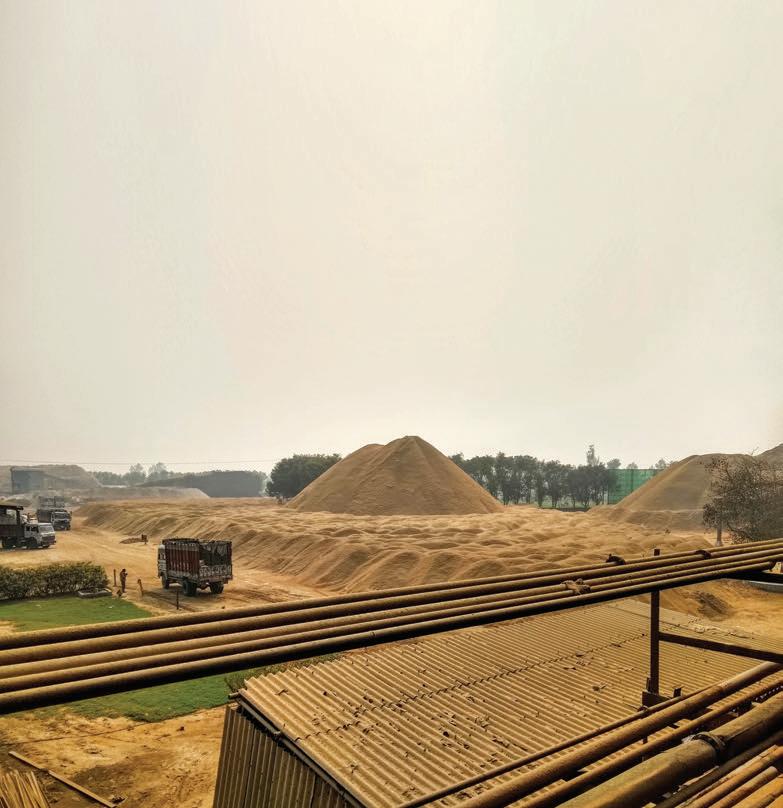
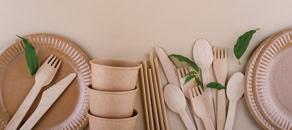
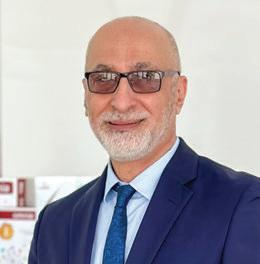
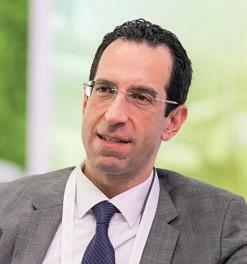
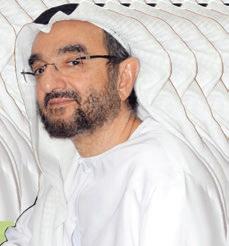
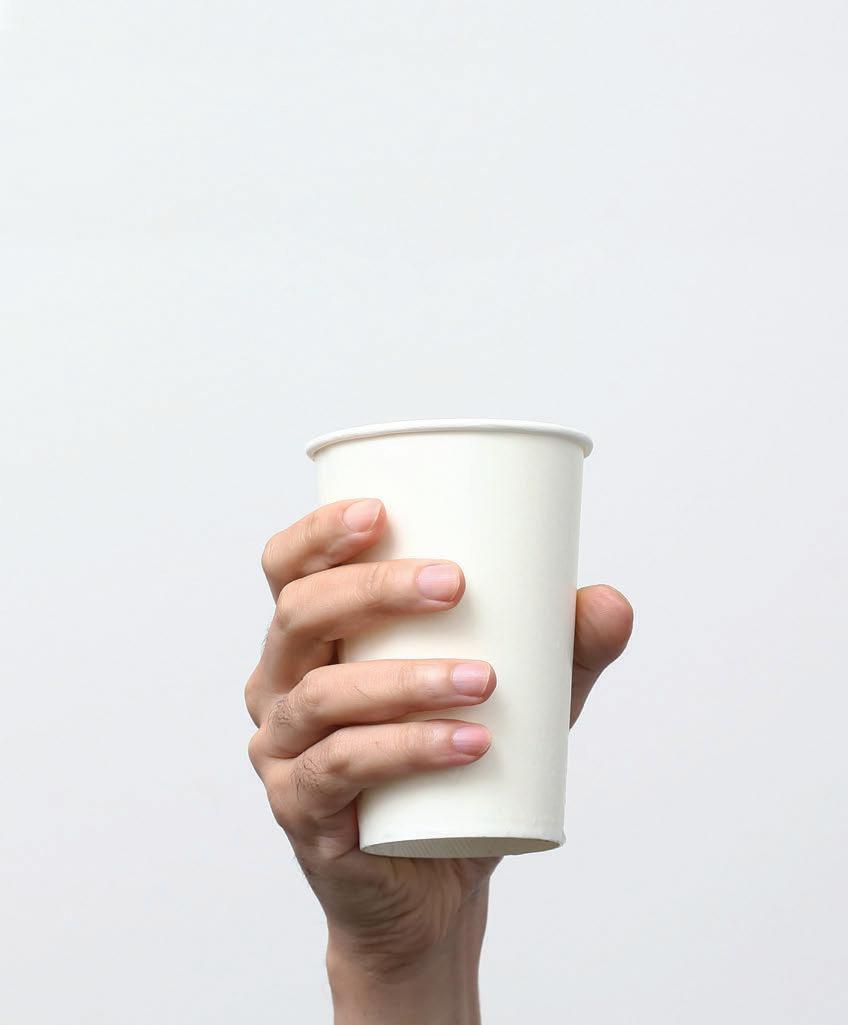


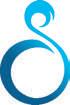



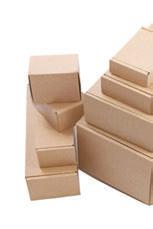


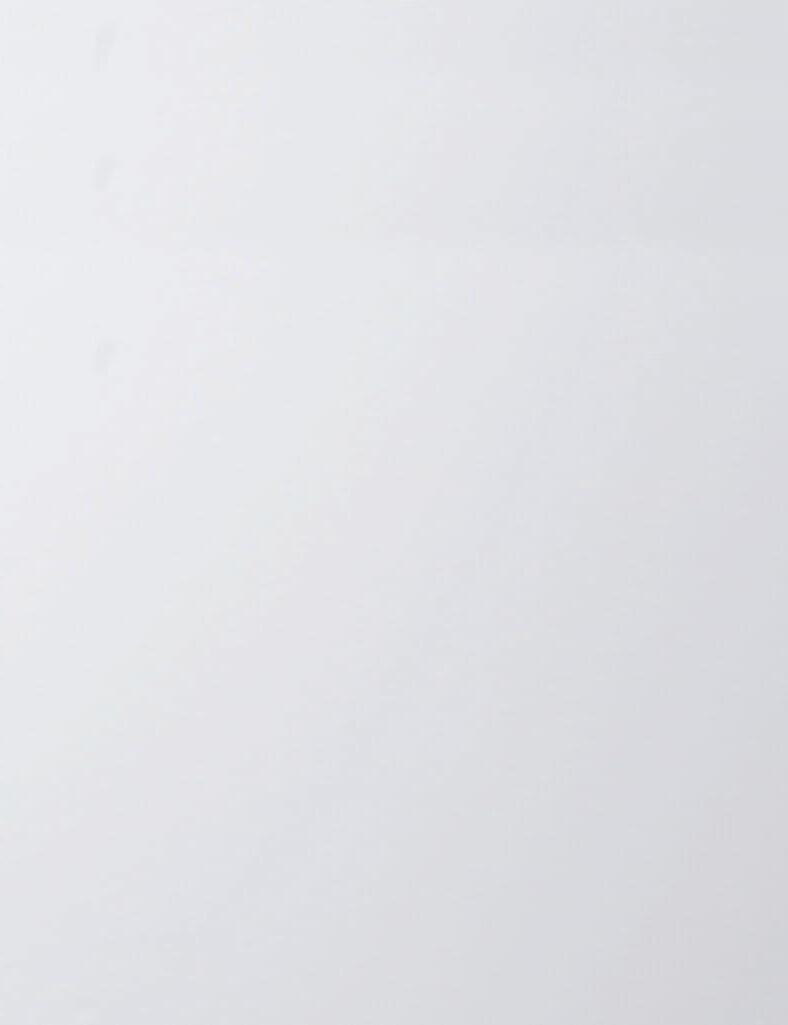
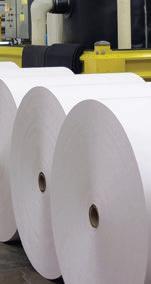
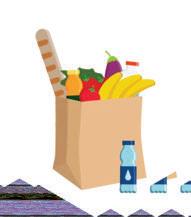
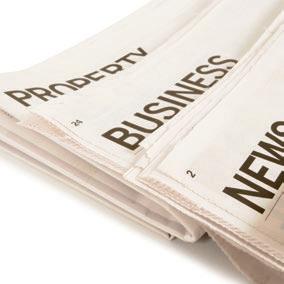
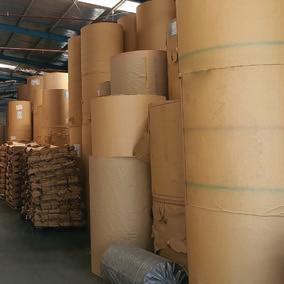
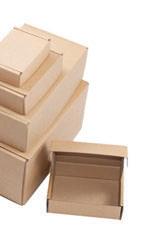
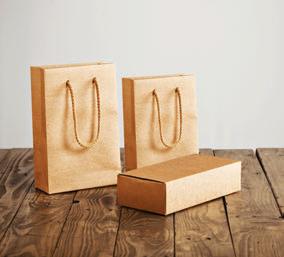
Sustainability isn‘t just about how many times a product can be used. It is also about reducing production waste, curbing energy consumption, and positively impacting both people and profits.
We offer products and services for the entire paper and board production process. From stock preparation to
the paper machine, our competencies incorporate world-class experience and expertise, automation support and technical services, as well as fabrics and rolls. Each solution is crafted to reduce environmental impact and improve the quality of the end product.
For further information, please contact us at paperboard@andritz.com
We at Shitla Papers Pvt. Ltd., markets and sells a broad variety of all sorts of Paper for Packaging since 1983, which includes Kraft Paper, Paperboard, Duplex Paper & Boards, Rigid Box Board, and Light GSM Papers, Absorbent Kraft, SBS/FBB, White Kraft Liner to cater to the rapidly growing paper industry worldwide.
PCF Maintenance BV
Industrial Zone Weerterveld 69
6231 NC Meerssen – Netherlands
+31 43 365 2077
ludofransen@pcfmaintenance.nl www.pcfmaintenance.nl
PCF Maintenance BV is a Dutch producer of cleaning and cutting equipment for the paper, board, tissue and non-woven industry.
We are working on an international level for various leading paper mills and are also specialized in preventive maintenance, repairs and overhauls of technical installations as well as turn-key projects.
Price, Quality (completely European make) and a Custom-Oriented Approach is what makes the difference between PCF and other companies.
Our custom made solutions:
Forming Fabric Cleaners, Press Felt Cleaners, Dryer Fabric Cleaners, Passivation Systems, Passivation Fluid, Tail Cutters for Wet and Dryer section (HP water needle jets, rotating and fixed knife), Moisture and Permeability measuring traverse beams, maintenance and repairs.
Our Exclusive Agent for India & Middle East Alliance International DWC-LLC
+91 9810 102608 / +97 1501 676740
aneja@allianceint.co / technical@allianceint.co
www.alliancepapermachinery.com
Decarbonization is the ecological megatrend of the century, but unlike common trends it has taken root and is here to make a profound impact. This megatrend comes as a boon to all industries, and since sustainability is the core idea for decarbonization and the paper industry alike, decarbonization benefits the industry by acting as a catalyst to bring about revolutionary changes which push the growth of the industry. This chain of benefits was best witnessed when the Government imposed a strict ban on single use plastic usage in order to reduce carbon footprint in accordance with the decarbonization trend. As a result of this decision, businesses turned towards the paper industry to replace polythene bags with paper bags, plastic tableware with biodegradable tableware and plastic packaging with biodegradable packaging, causing exponential growth in the sectors.
The vision for this note was clear; I wanted to talk oneon-one with the readers about all that Paper Mart has to offer. I wanted to share our efforts in bringing forward this edition, the concurrent events of the industry, and a small, profound piece of personal opinion. There are various ways to achieve our targets, and mine was to ensure a connection with my readers.
In order to contribute to decarbonization, the pulp and paper industry also works in various ways to contribute to decarbonization goals. The paper industry is inherently green and truly circular in nature. A prime example of this is agroforestry, a process used by the Indian paper industry, where trees are grown by farmers on their lands, which are usually considered unfit for other use, and their harvest is sold to paper mills. It is a common misconception among people that wood to create paper is sourced from forests. However, most Indian forests are either protected or inaccessible. Agroforestry has multiple benefits, as it turns unproductive land to plantations, while the trees, which take 4-5 years to grow, also contribute to the environment by producing oxygen in that duration. In addition to this, the paper industry utilizes waste paper and agricultural residue like sugarcane bagasse, wheat straw, rice husk etc to produce paper.
However, there is still a huge scope of growth for the Indian paper industry to reach its maximum decarbonization potential. It can take inspiration from the global pulp and paper industry as various companies are taking leaps towards their decarbonization goals like replacing natural gas with renewable hydrogen, setting up combined heat and power (CHP) plant, exploring carbon capture and storage technologies like Bio-CCS and many others. The industry's biggestchallenge isa financial and economic misperception, asenvironmental sustainability is perceived as an additional expense, while businesses tend to prioritize profit and economic growth. However, investment in environmentally friendly manufacturing practices must be seen as an asset rather than an expense by the industry, as it will generate value-based results over the years. An example to this is FSC certification, which was not prioritized by thepaper industryearlier, butgradually FSC-certified papers becamesoprevalent that they got more preference over non-FSC certified papers. This reflected the commitment of the consumers towards the environment. It is safe to presume that in the future, carbon footprint will become a similarly significant parameter of business for the paper industry.
The world celebrated Earth day on 22nd April. In light of an event which honors the environmental movement and its achievements in protecting our planet, I saw it befitting to bring forward the megatrend of decarbonization in this edition.
Paper Mart's Feb-Mar 2023 edition delves into one of the rapidly growing sectors in the paper industry contributing to decarbonization- biodegradable tableware. Through news coverages of major paper companies, their mills, new technologies and expansions, as well as interview articles with some of the major companies in the Indian biodegradable tableware market, this edition discusses the current condition of the biodegradable tableware market as well as its bright future and growth in the upcoming years.
CEOIttihad Paper Mill (IPM) is a flagship project owned by the UAE's leading private holding group, Ittihad
International Investments LLC. With a production capacity of 320,000 TPA, it is the first printing and writing paper production facility in the GCC and the largest in the Middle East. IPM also has a sister company, Crown Paper Mill, which is one of the largest tissue paper mills in the Middle East. Crown Paper Mill manufactures jumbo tissue rolls with a 100,000 TPA production capacity and is now gearing up to increase its capacity by 60,000 TPA. In a recent interview with Paper Mart, Mr. Abdullah Al Khateeb, Managing Director, Ittihad Paper Mill, talked about the mill's capacity, product portfolio, raw materials, and the future development plans at Crown Paper Mill.
Paper Mart: Please give us a brief walkthrough of your company, along with its major milestones.
Abdullah Al Khateeb: Ittihad Paper Mill is a printing and writing paper mill, established in the year 2019 with a production capacity of 320,000 TPA. We are proud to be the first printing and writing paper production facility in the GCC and the largest in the Middle East. We produce paper ranging from A3 and A4 to folio sheets as well as paper rolls. We export our paper to
approximately 66 countries worldwide, including regions like the Far East, Middle East, Europe, Africa, USA, and South America, with our focus on the Middle East and GCC region. Due to our superior quality, logistic network, technical knowhow and prices, we are able to compete on a global scale. We also have a sister mill called Crown Paper Mill, which manufactures jumbo tissue paper rolls. Crown Paper Mill is one of the largest tissue paper mills in the Middle East, with a
production capacity of 100,000 TPA. Due to the growing consumption of tissue paper in the region, we are continuously growing, and planning to expand in the Middle East.
PM: Kindly tell us about the raw materials used in your paper production.
AAK: With regards to the printing and writing paper, and the tissue paper industry, the main raw material is pulp sourced from eucalyptus. We buy around 400,000 tons of pulp
every year, making us the biggest buyer of pulp in the area. Major suppliers from whom we buy from are Brazil and other parts of South America, as well as the Far East. Softwood on the other hand, are mainly sourced from Europe and Chile. Having said that and interestingly because of us, the UAE has now become a landmark destination in the pulp industry.
PM: Could you share any recent or future developments from your end?
AAK: There is an upcoming development at Ittihad Paper Mill's sister company Crown Paper Mill. Initially, Crown Paper Mill had 2 machines. However, 3 years ago the mill got a new tissue machine from Valmet, having a capacity to produce 60,000 tonnes. Since we have a professional team coupled with years of experience in running paper machines, we decided to add another machine in Saudi Arabia. To execute this, we have
signed a contract with Valmet and are expecting to start the construction of the plant by 2024. This expansion will increase Crown Paper Mill's production capacity from 100,000 TPA to 160,000 TPA.
PM: What are your thoughts on sustainability in the paper industry?
AAK: Sustainability is a major component for both Ittihad Paper Mill and Crown Paper Mill. We always use FSC pulp in our production process. Sustainability to us means reducing emissions from the mill and protecting our environment including the communities that surround us. We are well aware that Environment and Sustainability plays a vital role in our industry, and we take it very seriously.
PM: Please share your insights on the paper industry in the Middle East market.
AAK: The tissue market is growing in
the Middle East. There are two reasons behind this - increase in population and change in the standard of living including a cultural shift in the Middle East. As a result, people are consuming more tissue and are hygiene conscious. Hence, if you review the last fifteen years of the tissue industry, you will see how tissue paper became a major component, how tissue consumption started increasing and why the number of tissue mills increased tremendously. However, in the printing and writing industry, the story is still unstable. Although the industry has witnessed growth in the Middle East, the global scenario is unstable. The industry has seen a decrease in demand in Europe, stability in the USA and growth in China. The difference in local and global markets is because of the industrial standards. If you compare per capita, the difference is huge between the Middle East and Europe as far as the paper consumption is concerned.
UAE-based Abu Dhabi
National Paper Mill was established in 2000, and is spread over an area of 60,000 sq m. The plant, with a production capacity of over 90,000 TPA, consists of three Crescent Former Machines each with a 30,000 TPA capacity. Promoting sustainable development, the FSC certified company also houses a de-inking facility to reutilize waste paper. In a recent interview with Paper Mart, Mr. Michael Shamma, General Manager, Abu Dhabi National Paper Mill (ADNPM) shared with us the company overview, manufacturing capabilities, sustainability policies and paper industry in the GCC and UAE markets.
Paper Mart: Could you please give us a brief walkthrough of your company?
Michael Shamma: Abu Dhabi National Paper Mill is a tissue manufacturing company. Being one of the leading manufacturer of hygienic tissue jumbo rolls in the UAE, we house 3 state-of-the-art machines at our facility, including the latest Advantage New Textured Tissue (NTT) machine that produces worldclass tissue paper from the highest grade virgin pulp. The machines have a capacity of around 30,000 tonnes each. Therefore, we have a total production capacity of over 90,000 TPA. Our company is 100 percent FSC certified and our raw materials are responsibly sourced from forests in North America, Latin America and Scandinavia. Our major product market is in the UAE and GCC region, and we also export products to Europe and North America.
PM: Kindly shed some light on the recent developments at the company.
MS: We have recently invested in a new water treatment facility, in order to reduce water consumption for the production of our jumbo tissue rolls. It is an essential effort that we are
making to contribute more towards preservation of the environment. We have invested a large amount on reducing water consumption and are continuing this effort on all paper machines.
PM: Please shed some light on how COVID-19 affected trade in the paper industry?
MS: During the past few years, when the global economy was affected by the post-Covid logistic bottleneck, all manufacturers moved from global geographic distribution to regional distribution. We were only able to sell locally and to the GCC because the container rates were simply too high to export. Last year, we sold approximately 50 percent to the UAE, 45 percent to the Saudi market and 5 percent to other markets. Our export business to Europe and North America was hindered due to the high container rates. However, the container rates have now come down and we are hoping to increase the share of our exports to foreign markets.
PM: Please tell us about the sustainability policy at ADNPM.
MS: Our company is very proud to be part of the circular economy. It is a model of production and consump-
tion which involves reusability and recyclability (among other factors) of materials and products for as long as possible. Our raw materials are sourced from responsibly managed forests, which are 100 percent FSC certified. These forests are limited in size. Our suppliers plant seeds, grow the trees, which are then harvested after many years. Seeds are then replanted within the same area. Thus we are only sourcing renewable material. We also have a de-inking facility within our factory, where all the utilized and consumed paper is reused. Therefore, we reproduce tissue paper which we call 'Super Commercial', which is recycled paper with a white or off white color. We also produce recycled brown paper made from recycled fibers which we purchase from the market. In this way, we are contributing to the sustainability movement.
PM: What are some major challenges faced by the paper industry and how can they be resolved?
MS: There is a common misconception in the community that the paper
industry harms the environment. On the contrary, since we are part of the circular economy, the raw material that we are sourcing is a sustainable resource and since all the products we produce can be recycled, we are contributing to protecting the environment. We believe that as paper manufacturers, we should focus more on creating awareness among the community that the paper we are consuming is not wasted and comes from renewable resources. We have to transfer that message to the community by advertising the beneficial outcome of that product vs the non beneficial outcome. Everything that is sourced by renewable resources is the solution that will contribute to a greener environment.
PM: Please share your insights on the paper industry in the UAE and GCC markets.
MS: The main grades in the tissue industry are facial, bath and kitchen. In the GCC, we see a large growth due
to increasing population in the region, especially in the facial and bath and kitchen grades, between today and 2030. At Abu Dhabi National Paper Mill, we are continu-
ously trying to provide solutions to our customers, and have no limitations whatsoever in terms of product development nor geographical distribution.
Ecosurepulpmolding offering sustainable solutions to produce inhouse pulp fiber from nonwood resources using chemical free patented technology & to produce molded fiber pulp products.
92, Udyog Kendra, Ecotech-III, Gautam Buddha Nagar, Greater Noida 201306, Uttar Pradesh, India. Mobile: + 91 - 9643762650 / 9873003226
Landline: +91-120- 2960000
Email: info@ecosurepulpmolding.in / sales@ecosurepulpmolding.in
of approximately 900,000 metric tons, making it the leading Kraft Paper producer in GCC. The proposed expansion will cost approximately one Billion Dirhams.
While announcing the expansion Mr. Salahuddin said“We are thankful to the Government of UAE for creating a platform for the industries working hard for sustainable development and adding value to the circular economy. As UAE is celebrating 2023 as the year of sustainability it becomes our prime responsibility to strategize our actions, our business initiatives to translate Sustainability in environmental protection, climate control and sustained Industrial growth.
Mr. Sharafi congratulated and thanked Mr. H.H Sheikh Mohamed bin Zayed Al Nahyan, the President of UAE, for laying down the new Industrial Strategy, and, for announcing 2023 as “year of sustainability”, and thanked Mr. H.H Shaikh Mohamed bin Rashid Al Maktoum, Vice President and Ruler of Dubai, for his continuous support to the Industrial sectors.
Feb 25, 2023
MAHY Khoory & Company, the pioneers in Paper
recycling, Water Pumps and other varied businesses, with an incredible success story has announced an expansion plan of setting up a new paper machine in their Al Dhafra Paper Mills at Abu Dhabi.
On the sidelines of Paper One show in UAE, Mr. Salahuddin Sharafi, Chairman of MAHY Khoory Group (which owns Al Dhafra Paper Manufacturing Company and Union Paper Mills), announced this exciting project of producing additional 500,000 tons of recycled kraft paper annually. Post expansion group's production will reach to annual capacity
Earlier, Mr. Shabbir Haideri, the Group General Manager, addressed the business delegates and saidrecycling business has multiple challenges like unpredictable market scenario, fluctuation in sea freights and scarcity of Raw material. Despite these challenges we gather courage for this great initiative with the blessings of UAE leadership.
Mr. Shabbir further added that our recycling endeavors translates our commitment of meeting the goals and objectives of environmental agencies, increasing exports, generating non-oil-based revenue for the nation, and, to be a leader on the path of circular economy.
Mr. Niraj Srivastava, General Manager Sales & Marketing, gave a brief presentation on Group's humble growth and its diverse business activities.
Keryas Paper Industry LLC, Oman, is only an infant if its 2021 establish-
ment is considered, however, its achievements and investments tell a whole other story. The mill not only exceeds its 100 percent production capacity within a year of becoming operational, but it is also already looking forward to solidifying its dominant position in the GCC paper industry. In a conversation with Paper Mart, Mr. Rajasekar Veerichetty, Vice President, who is having 32 years of experience in the paper industry and having 6+ yrs at C Level leadership, elaborated on various product diversification, market diversification, and technological upgrade plans of the company. One of these plans is a new paper mill in UAE for which the company has already announced an investment of USD 40 million, and which might become operational in 2024.
Paper Mart: Please introduce us to Keryas Paper and its major milestones.
RajasekarVeerichetty: Keryas Paper Industry is a part of the Keryas Group of Industries which is headed by the Al Hosni family. Mr. Al Hosni is our Chairman, his elder son, Mr. Mohammed Al Hosni, is our CEO, and his younger son, Mr. Abdullah Al Hosni, is our MD. The group in itself has a diversified presence, such as Keryas Steel, with an in-house fabrication team, a school, and a chain of supermarkets, Al Karama, in
Oman. Our paper mill is the first and the largest paper mill in Oman and is a 100 percent recycled fiber-based mill. It became operational in July 2021, and in 2022, that is within a year, we achieved over 100 percent efficiency by producing 100,000 tonnes of paper. At Keryas Paper, we are determined to plan and implement projects for continuous growth and upgrading, and as a result, we have already achieved FSE's ISO 9001: 2015 certification. Our efforts have resulted in varying achievements within a short period of being operational, for
instance, in 2021-22 we won Best Sustainable Award, in Dubai, and in October 2022 we won the Runner-up award in the Waste & Recycling Award category.
PM: Please elaborate on your product line and the markets served.
RV: We manufacture test liner paper, fluting medium paper, core board paper, and absorbent kraft paper. The machine can produce 110-200 gsm papers with a BF range of 22-26, our high-performance fluting medium paper, for the medium layer of carton boxes, ranges from 80-200 gsm, highperformance test liner paper, for covering layer of carton boxes, ranges 80-175 gsm, and core board for paper tubes ranges 200-450 gsm.
Our base market is Oman, as about 60 percent of our products sell here, however, we have a global presence as
Address:
Cell: Email: Website:
Plot No.19, SR.NO.2608, Shanta Gulab Industrial Park, Besides Damanganga Industrial Park, Karvad, Vapi-396193 +91 9898130415, +91 9227830415 ayaz@rs-engineers.com, sales@rs-engineers.com www.rs-engineers.com
“Our paper mill is the first and the largest paper mill in Oman and is a 100 percent recycled fiber-based mill. It became operational in July 2021, and in 2022, that is within a year, we achieved over 100 percent efficiency by producing 100,000 tonnes of paper.”
“Last October, we announced a USD 40 million investment for a new mill project in UAE, and we will be targeting to produce low gsm, 60-90, and high BF paper to cater to different types of markets. We plan to cater to carton boxes to paper bags and other markets, which GCC presently imports. The production capacity for the new mill is being aimed at 500-600 TPD”
we export to many countries, including UAE, Saudi Arabia, Bahrain, Kuwait, Bangladesh, South Africa, and Malta.
PM: Can you share your paper mill's manufacturing process and capacities?
RV: We have recently acquired a highperformance fluting test liner manufacturing line from China, and it takes care of the whole paper-making process, starting from pulp making. The machine is equipped with a 4.6width mesh wire, resulting in a 4.5width finished product. Its operational speed is 550 mpm and its production capacity is 450 metric TPD. The machine is one of a kind in the whole GCC region. Although our mill already is among the least consumers of water, at 2.5 cubic meters per ton of paper, among all GCC paper mills, we wish to bring it down more.
PM: How do you source raw materials for your mill?
RV: We source 60 percent of our papermaking raw material, waste paper, from Oman, and the rest 40 percent through imports, majorly from GCC member countries, and about 10 percent from Europe and the Middle East countries. We initially purchased waste, but recently our sister concern, Keryas Waste Management, is supplying us with our raw materials. The lack of proper segregation and collection habits was a major reason behind starting Keryas Waste Management. We employ over 150 people as our own collection
teams, and do the segregation and bailing in our own warehouse. We educate the general public on how to collect waste and segregate it properly through slogans, brochures, and various campaigns, and since we are turning waste into wealth, people are also supportive as now they get money for proper waste management. We have our own collection basket in all the malls of Oman and we are concerned with educating and collecting. People are supportive as well as they also benefit by making money.
PM: Please shed light on your approach towards sustainability.
RV: Mr. Abdullah Al Hosni, our MD, has put forward the idea of reusing waste paper that otherwise goes into landfill and our consequent efforts have resulted in better waste management, saving forest resources, and reducing our carbon footprint. We are also investing in the circular economy by reducing water usage.
Our entrepreneurs are young, within the 30-38 years age group, and all our projects are focused on taking care of the environment, sustainability, and aiming to become zero discharge plants.
We have over 200 people, from diverse backgrounds, such as India, Bangladesh, Pakistan, etc., employed, and plan to recruit more from Sri Lanka and Nepal in the future. Since in the first year only we achieved 100 percent of our production capacity, we are looking forward to expanding our wings and diversifying all across GCC.
PM:
RV: From 2022 onwards we have been on a constant lookout for better and latest technologies to improve product quality and expand our production capacity. Our detailed plans include the installation of new state-of-the-art technology for a dryer screen online cleaning system, supplied by ProJet the Netherlands, a new auto spool change system, supplied by Sander USA, which shall be implemented by 2023, incorporation of 1 MW TG, which is in final stages of commissioning and will be started by the end of February 2023. We want to increase our production capacity by 20 percent. In the upcoming period, we are going to upgrade our ETP plant with new DAF aeration, and install an anaerobic reactor to reduce effluent load and save water, a precious resource in the Gulf region. Additionally, we will install a new RO plant supplied by Thermax, a new auto-control dilution headbox. We also have other projects planned for environment and product diversification, for instance, a new coating plant and other diversification projects across Oman and GCC region.
Last October, we announced a USD 40 million investment for a new mill project in UAE, and we will be targeting to produce low gsm, 60-90, and high BF paper to cater to different types of markets. We plan to cater to carton boxes to paper bags and other markets, which GCC presently imports. The production capacity for the new mill is being aimed at 500600 TPD, and accordingly, the deckle shall be finalized. We are currently in the process of finalizing the location, once we finish land selection we could continue with further phases of the project and complete setting up the mill by 2024.
We are planning to expand in other areas as well, such as plastic recycling.
Orient Paper Mills is one of the oldest market players of tissue
paper industry, which is experiencing a growth phase. Mr. Saikat Basu, Head - Marketing & Sales, graced Paper Mart with an insightful conversation, discussing the events that drove the tissue industry in this phase and its future. About Orient Paper, he reveals that the company involves itself in robust strategy making, quality production, and concurrent feedback, earning every day its dominant market position. He further details the trends experienced by the industry, expected growth rate of different segments, and what the government can do to fuel hygiene awareness in India.
PM: The paper and tissue industry in India can benefit from hygiene awareness. What are your viewpoints on this statement?
SB: Hygiene parameters in India are still at nascent stage compared to Europe/US, but there is a gross change in outlook of the masses post Covid-19 pandemic. It's not only about personal hygiene priorities, but the basic social framework in India has also kept per capita consumption of tissue nominal till now. With increased hygiene awareness, demand for tissue products is bound to grow. Also it will fuel demand for food based paper usage like packaging boards for takeaway foods, cupstock, oil & grease resistance paper, etc.
Manufacturers and converters can diversify product range and introduce tissue products with anti-bacterial properties, carrier tissues, wet wipes, pocket size tissues, eco-friendly brown tissues, etc. Such value added products are still majorly imported in India, it has opened up an opportunity and
challenge for domestic manufacturers for product development. Various new product development efforts are happening with paper manufacturers and packaging converters in food packaging grades, water, oil and grease resistant categories, etc.
PM: What measures can the Government of India take to ensure better hygiene awareness? Could you also share the efforts made by OPIL in this respect?
SB: The Government of India can take several measures to ensure hygiene awareness among citizens. They can launch public awareness campaigns to educate the masses, through various media channels –print, TV and social media. School education programs are another area – hygiene education can be integrated into the curriculum. Government should also invest in infrastructure development to promote hygiene practices, for example – clean drinking water, sanitation facilities, waste management systems.
Encouragement for tissue dispensers in public places like colleges, hospitals, railway stations and airports should be a prime focus area for the government. The Government can provide incentives and awards to businesses and individuals to promote hygiene practices. Last but not the least, the government can enforce regulations and guidelines for hygiene practices in food, healthcare and tourism sectors and set standards for businesses to maintain certain levels of hygiene for public safety and product usage. This will fuel consumption for paper & packaging products for the food & HoReCa sector especially.
Orient Paper has been a forerunner in all such initiatives, being the oldest and one of the largest players in the writing-printing & tissue segment. We participate in various forums of hygiene awareness in schools, airports, offices and cooperative societies. We deeply study our products from raw material to ultimate disposal and constantly innovate.
PM: How does OPIL view its product line to cater to the standards of the hygiene sector?
SB: Orient Paper has a vast product line in virgin pulp based paper & tissue segments. The GSM range in tissues is exhaustive – 12.5 to 42 gsm, which can match the stretch of all renowned international players. We consistently produce, market and service customers for all varieties of tissue – napkin, facials, C fold, M/N fold, high wet strength tissue, HRT rolls, toilet rolls. We cater additional variants like maxi roll, bath tissue and serviettes for the international markets as well.
We have also developed paper categories for cup & plate disposables as well as oil & grease resistant paper. Our quality, consistency and new variant development capabilities match any international player. The ethos of the CK Birla group is percolated down to every aspect in Orient Paper – each individual within the organization understands the need to match the best of industry standards of quality and service.
PM: Could you share the past and current market trends in the Indian tissue industry? Where does Orient Paper stand among these trends?
SB: Trends are quite positive with the HoReCa sector at its peak consumption post Covid. Whether revenge tourism or cloud kitchens, each lifestyle change today is boosting tissue consumption. Covid curbed the growth rate of tissue in India in 20-21, and virgin tissue degrowth was a whopping 25% from 19-20 to 20-21. The HoReCa segment shrunk by 14% in 20-21, and institutional segment degrowth was as high as 43% in tissue.
The revival was partial in 21-22: 16% in HoReCa and 7% in institutions. In FY 23, while HoReCa revived sharply, the institutional segment was still in partial recovery mode, as trends of work from home still exist. Orient Paper & Industries Limited has been a forerunner in specialty products, particularly in tissue. Our last expansion was the installation of tissue machine no. 3 a few years back. In more recent times, we have augmented our virgin pulp capacities and commissioned a new recovery boiler.
PM: What are the major demand and supply changes that the tissue industry has experienced in the post-pandemic period?
SB: In FY 24, 25 and 26, we expect the Indian virgin tissue to grow by 15% YoY. Institutional growth will be faster than HoReCa now. The demand changes of the major end segments (HoReCa, institutions and retail/home buyer) have all been detailed in the previous queries – both during the pandemic as well as the post-pandemic period. On the supply side, the capex additions in virgin have not been so robust. That has caused increased usage of recycled tissue and MG, especially in the B and C towns.
PM: What is the strategy of Orient Paper to make the most and best out of the current and upcoming market trends in the tissue industry?
SB: As explained, Orient Paper & Industries Limited wishes to remain forerunner in the tissue business in India as well as in select export markets. We augmented our pulping as well as tissue paper production to ensure we grow in tandem with the industry or sectoral growth. Parallelly, we are putting extreme focus on quality improvement, as well as new product development.
We work in close tandem with converters and end users, both in India, as well as UAE, Qatar, Sri Lanka, Nepal and certain African markets as well. A robust feedback mechanism to our technical as well as marketing team is captured systematically in OPIL, and new variants designed accordingly. We study the pros and cons of hygiene alternatives and substitutes like handkerchiefs, hand dryers, etc as well.
PM: What role can globalization play in the growth of the Indian paper & tissue industry?
SB: Globalization can play a significant role in the growth of the Indian paper & tissue industry. With the rise of international trade, tissue & packaging paper manufacturers in India can tap into global markets to expand customer base and increase revenue. Market share of Indian producers can increase in the Middle East, Africa, Latin America and other growing economies. This will also help the domestic manufacturers to reduce reliance on Indian demand. Globalization also provides access to new technologies and manufacturing processes to improve quality produced in India. The best practices of international paper & tissue producers should be implemented in our production processes to enhance quality and meet international standards. Lastly, it will facilitate collaborations between Indian and international manufacturers. Sharing of knowledge and access to new markets will add to expertise.
Started in 1976, one of
Bangladesh's largest industrial conglomerates, Meghna Group houses more than 50,000 employees, 6,300 distributors and 15,000 suppliers under its umbrella, with an annual turnover of approximately USD 3 billion. The group boasts of a production capacity of 1200 TPD, with 100TPD tissue production, 800 TPD industrial grade production and 300 TPD writing and printing paper production. The group holds a broad array of industries including FMCG, building materials, pulp and paper, LPG, feeds, fiber, power plants, shipping, seeds crushing, chemicals, ship building, dockyard, securities, insurance, media, Foil packaging, ceramics and aviation. In a recent interview with Paper Mart, Md. Yearul Islam, General Manager (Sales and Marketing), shared about the company's paper mills, production capacities, expansion plans and current challenges for Bangladesh's paper industry.
Paper Mart: Please give us a brief overview of your company.
Md. Yearul Islam: Meghna Group is the leading conglomerate in Bangladesh, with more than 40 sister
concerns present under the group. Currently, our yearly turnover is approximately USD 3 billion. We are the leaders of industrial grade paper in Bangladesh, and the pioneer for the export market of the industrial grade. We already supply our papers to China, Sri Lanka, India and many other countries contact us for paper requirements because they like the quality of our products.
PM: Kindly shed some light on your paper mills, outlining the grades manufactured and their capacity.
MYI: We have 5 paper mills. Two mills are for tissue production, with a per day production capacity of 100 metric tonnes. In these mills, we produce all types of tissues, like napkins, scented tissues, toilet paper, facial tissues and others. Our company has a very good market for tissue paper. We already export to different regions like Africa, Middle East, Nepal and India. Other than this, we have mills for industrial grade paper, with 800 metric tonnes per day production. In these mills we produce fluting paper, liner paper, kraft liner paper, white liner paper, NCR paper and art paper. We also produce all types of writing and
printing paper from 40gsm to 170gsm with 300 metric tonnes per day production. We plan to expand our business to duplex boards, swedish boards and simplex boards.
PM: Please tell us about the raw material being used for tissue paper and industrial grade paper production. What are the challenges faced in obtaining raw material?
MYI: All the raw material we use for tissue paper and writing and printing paper is 100% imported. Writing and printing paper as well as tissues are produced using 100 percent virgin pulp. Industrial grade production uses 100 percent waste paper. Depending on the type of industrial paper we produce, we use various categories of raw materials like, NDLKC, OCC and NCC.
With regard to challenges, Bangladesh is currently suffering from a double crisis, with the value of the dollar being very high and the value of taka decreasing day by day. So it is difficult for the owner of the paper mills to import raw materials. If we collect raw materials locally, we will not face such problems. Every paper mill faces the same problem which
hampers their production. Since more than 100 paper mills perform their operations in Bangladesh, raw materials are priced very high in Bangladesh. Therefore, we are facing a crisis of raw materials.
PM: How do you feed power requirements for your paper mills?
MYI: In order to meet the power requirements of our mills, we have our own power plant supplying electricity. Our power plant generates almost 35 megawatts of electricity.
PM: Please give us your insights on the paper industry.
MYI: The tissue paper market is expanding every day and bringing more opportunities. Currently, we have approximately 25 percent share in our local market. For the writing and printing paper market, we have approximately 10 percent share and for industrial grade paper, we occupy 30 percent market share. For industrial grade, we have a big opportunity to grow since many packaging companies import paper from Bangladesh due to our good quality. In the next 2 to 3 years, the company will focus on creating high quality paper and increasing our market presence.
PM: What are your company's future plans for the paper business?
MYI: The group will expand 3 to 4 more concerns in industries like steel, glass and paper. The management will also try to invest more in the paper sector like duplex boards, writing and printing, and tissue machines. We will try to increase the volume of the paper manufactured in future depending on the market conditions at that time. Therefore, we aim to expand our presence in the paper market, not just in Bangladesh but also to export to South Asia, Middle East, and Africa and European countries.
Sri Lanka based Sakthi International Private Limited, one of the
major exporters of waste paper to the Indian-Subcontinent & the Middle East, and a manufacturer of fluting medium and packaging paper, has a goal to enter into production of test liner. Its group companies include Sakthi Papers Private Limited, Eco Papers Private Limited, G.K. Paper Mills Private Limited & G.K. Core Private Limited. In a recent interview with Paper Mart, Mr. G. Kamaleshan- Managing Director, Sakthi International Private Limited talked about the diverse group of companies, expansion and future plans.
Paper Mart: Could you please give us a brief overview of your company?
G Kamaleshan: Sakthi International was initially formed for the export of waste paper. Since 1995, we have been exporting waste paper to India. As we had the capacity to collect a huge amount of paper waste, we entered into paper manufacturing. We took over a paper mill in 2017, and since then we have been producing 60 to 80 metric tonnes of medium paper. We also produce 50 gsm, 30 metric tonne output of paper tablecloth. We have been exporting to Bangladesh, China as well as far east countries.
PM: Please shed some light on the diverse portfolio of companies under the Sakthi Group.
GK: Sakthi Group has 4 companies under it, all for paper related products. Under Sakthi International and Sakthi Papers, we do exports of waste paper. Eco Papers is our paper manufacturing mill and G.K. Paper Mills is where we do paper tablecloth manufacturing. In G.K. Core, we manufacture the core tubes for local markets and exports.
PM: Could you tell us about the manufacturing capabilities and
clientele of Sakthi International and Sakthi Paper.
GK: With Sakthi International and Sakthi Papercombined, weexport around 4,000 to 4,500 metric tonnesa month. Thegradeswhichwe handleare OCC, NCC, boxboard cutting, scanboard and tissuewasteaswell. Apart from thatwedo laminated box board cuttings, whitesorted officepack and sorted officepack. Our major buyers in Indiaare ITC, Seshasayee, Gaytrishakti, West Coast Paper, Subam Papers, Morbi millsand manyothers.
PM: Please give us a walkthrough of the manufacturing capacity and infrastructure at your Eco Papers mill.
GK: The machine we have at the facility was imported from Amit Paper and Consultants, India. We have recently started doing size press insulation, from the past 7 to 8 months. We have also set up a total ETP (Effluent Treatment Plant) to improve our effluent quality. We manufacture around 60-80 metric tonnes of medium paper per day and we are planning to soon start our manufacturing of test liner.
PM: Please tell us about the manufacturing capacity and infrastructure at G.K. Paper Mills.
GK: In G.K. Paper Mills, we manufacture paper tablecloths. It is equivalent to newsprint quality, which only targets the local market where we sell it for the wrapping of food parcels, fruits and other items. We have been supplying only for the local market at the moment. We target around 48 to 50 gsm, with an output of 30-40 metric tonnes per day.
PM: Please tell us about G.K. Core and the markets this company caters to.
GK: We are into core pipes for our own consumption at paper mills as well as for other export markets like thread, yarn companies as well as packaging units which need core pipes for wrapping. So we do production of around 10 to 15 metric tonnes at GK Core Pipes every day.
PM: Does the company have any plans for further expansion in the future?
GK: We are in the process of expanding our production and we want to increase our volume of production. Recently there has been increased demand in Bangladesh, one of the countries we export to. So for the future, we might be targeting 100-150 metric tonnes per day. We are aiming to start this production by the end of 2023, in November or December. That is the main target we hope to achieve very soon.
PM: Please share your insights about the Sri Lankan paper industry. What are the challenges and future of the industry?
GK: The Sri Lankan Paper industry is currently struggling a bit due to the economic downfall. Due to the dollar issue, the corrugators are finding it difficult to import finished paper. As a result, the demand has to be fulfilled by domestic mills only. However, we hope that with the IMF coming forward the situation will improve by the end of 2023. The main issue in the paper market in Sri Lanka is that we cannot import waste paper. There are
2 paper mills in Sri Lanka. So we have to only target the local collection, which means the production is limited. According to the government law, we cannot import waste paper to Sri Lanka unlike India. Due to this restriction and the financial crisis, the availability of raw materials is very less. This is the challenge the paper industry in Sri Lanka faces currently.
PM: What is the total paper and paperboard consumption in Sri Lanka annually and how much waste paper is exported from Sri Lanka?
GK: For kraft paper (both fluting medium and test liner) the consumption is nearly 10,000 metric tonnes per month. And duplex board consumption is around 15,000 metric tonnes monthly. Other types like MG paper and poster paper have lesser consumption. With regard to exports of waste paper from Sri Lanka, currently, brown grades have been restricted for exports. So only 3000-5000 tonnes per month is exported. And the other grades are around 7000 metric tonnes per month.
Aryan Paper Mills Private Limited
has announced the setup of a new paper mill in Gujarat. The company has signed an MoU with the Government of Gujarat to streamline the registration and permissions procedure for the new mill, whose civil work is in process. A pioneer of the Indian paper industry, the group has a history and profile of ongoing operations which allows the country to be proud of it. Mr. Mihir Shah, Director, Aryan Paper Mills shared with Paper Mart the finer details of the new mill project while recalling the humble starts of the group and attributing practices that allowed the current growth and platform.
Paper Mart: Please brief us about your company Aryan Paper, its history, business journey along with crucial milestones.
Mr. Mihir Shah: We have experience spanning over six decades in the paper industry. Aryan Packaging Industries was established in 1948 by Mr. Krishnalal Shah and Mr. Mansukhlal Seth in Dadar. At the time, the company and its operations were limited to being paper corrugators within one-room premises. In 1977, the company shifted manufacturing operations to Vapi, Gujarat, while retaining headquarters and marketing operations in Mumbai.
Our MD Shri Sunil Shah setup Aryan Paper Mills Private Limited in Vapi in 1989. Since then, we have upgraded our mill on various instances for both expansion and sustainable purposes. In 2004 we established a Captive Power Plant (CPP) and in 2006 we installed an integrated ESP. Our currently installed machine has a production capacity of 170 TPD. We run 2 corrugation lines in line with 8 converting lines which enable us to offer one of the largest corrugated capacities in western India.
We are focusing strongly on the environment under the leadership of our MD Shri Sunil Shah. Sustainable
growth with a focus on lowering the carbon footprint per ton of paper is our primary driver.
PM: What is your current product portfolio, infrastructural setup, and manufacturing capacities for the same with regard to paper and packaging solutions?
MS: We manufacture kraft paper ranging from 100-300 gsm and export over 50 percent of our total annual production owing to quality and consistency. Our key focus areas are test liners and fluting medium, along with other specialized products like special strength paper for multiwall applications, TTC (high ply bond) paper, and high-performing lining (HPL) and high-performing fluting Medium (HPF). We also manufacture custommade variants of recycled kraft paper.
Aryan Paper started as Aryan Packaging Industries, and it constitutes one of our most specialized services. It is our roots in this area which make us more than a corrugated vendor. Each step involved in the corrugated packaging process, from selecting a paper combination, adjusting moisture levels, choosing the right glue, and using the best technique to apply it, to printing, slotting, and punching, is undertaken with the utmost efficiency stemming from our knowledge and experience. We believe in giving our customers maximum satisfaction and weigh-in their technical needs first before drawing commercial engagements with them. We utilize our experience and extensive R&D to develop the optimal corrugated product which fulfills the technical requirements of our customers.
Our extensive and qualitative corrugated packaging product portfolio includes corrugated boards, RSC cartons, universal cartons, trays, wrap-around cartons, jumbo cartons and other customized cartons.
PM: Tell us about your upcoming paper mill for which you have recently signed an MoU with the Government of Gujarat. What kind of investments are associated with
this mill with regard to land acquisition and technology?
MS: Aryan Paper is keenly focused on exports besides the domestic market. This exposure to international markets drives us to diversify our product line, horizontally and vertically, and expand our existing production capacity. Our experience in export markets has also driven us to focus on the finer points of papermaking. The new paper mill has a width of 5.1 meters which is one of the largest in India. We have partnered with leading European suppliers to ensure we provide value to the constantly evolving corrugation market. Land acquisition has already been completed earlier.
Aryan Paper Mills Private Limited signed an MOU with the Government of Gujarat in the august presence of Shri Bhupendrabhai Patel, Chief Minister of the State, under which the government will facilitate obtaining of necessary permissions, registrations, approvals, or clearances, etc., from the concerned departments as per the existing policies, rules, and regulations.
PM: Explain the new mill's machinery or infrastructure setup, target production capacity, product
category to which it is going to cater, and other characteristics.
MS: We have sourced the machinery predominantly from established European suppliers like Bellmer, Valmet, and Kadant. It can be easily stated that PM 2 is going to be a stateof-the-art facility and shall contribute majorly to both domestic and international markets. The production capacity will depend on the product mix. We are looking to serve many upcoming segments besides corrugation and our product portfolio shall be based on market demand, both domestic and international, various diversifications, and technologically advanced applications. The market is already rich and the postpandemic global market prefers paper-based packaging solutions. This along with increasing demand has been our major motivator in planning and setting up the new mill.
PM: What are the timelines planned for this project in the context of land acquisition, civil work, order placement, and final start-up of the mill?
MS: We completed the land acquisition to set up the new mill three years ago. Subsequently, one can reliably
assume that our mill will be a result of extensive planning and organized execution. While the civil work is ongoing, we have already placed orders with all major equipment suppliers. We are hopeful to make our PM2 operational in Q1 2024.
PM: How are your company's activities in line with the nation's vision for a sustainable future?
MS: Sustainability is the basis of our organizational setup. Our new machine will have one of the lowest carbon footprints in paper manufacturing. Our installed ESP helps us keep our emissions below 50 gms, which is in adherence to European standards. We have a CPP which makes the mill self-reliant to fulfill our energy requirements, out of which 15 percent are covered by renewable energy sources. We ensure 100 percent water recycling in our paper-making process and have set benchmarks for the Indian recycled kraft paper
industry. We use a bio-mass briquette-based steam generation plant to meet the steam requirements of our packaging division.
We have planted more than 200,000 trees in the last three years and a Miyawaki forest in our paper mill is blooming with birds and squirrels. Additionally, we have invested in solar and wind power over the last two years.
PM: What are your company's USPs and how is it different from the rest of the players in the market?
MS: Our USP is plain and simple; quality and consistency. These are the basics that enable us to consistently export more than 50 percent of our products for many years. Price stability is another one of our key strengths in this service-oriented industry. All three attributes have been cultivated by us over the years and so we manage to maintain our set standards. A repetitive consumer base is an added profit of these practices.
Our supply chain partners constitute leading companies in E-commerce, FMCG, white goods, automotive industry and ancillaries, pharmaceutical, textiles, horticulture, industrial goods, flexible packaging, chemicals, and foods and beverages sectors.
PM: Please enlighten us about the current scenario and the future of the paper industry in India.
MS: There is a huge potential for good quality paper in India. We anticipate a shift in the corrugation industry from per kg basis to per sq meter basis in the coming times. This will enable modern paper mills as well as corrugators with good technology to provide value to customers. Moreover, the market overall has been in a continuous growth phase due to an increase in hygienic and environmental awareness among the endconsumers. Our hope for industrial growth is confirmed by our upcoming paper mill, which will result in capacity and product profile expansion.
JMC Paper Tech, an Indian machinery manufacturer for pulp & paper industry, has decided to further penetrate the pulp and paper market through its new subsidiary companyJMCPapers.JMCPaperswillventureintothemarketthroughanewrecycled fiberbasedkraftpapermillof150TPDcapacityintheNorthAmericanregion.
Mar 15, 2023
JMC Paper Tech
Private Limited has announced a new subsidiary, JMC Papers, to further penetrate the pulp and paper market in the North American region. The new subsidiary will deal with kraft paper production by setting up a new mill in North America with a production capacity of 150 TPD. The mill is expected to commence production by mid-2024.
“Our paper mill in North America will be a stepping-stone for JMC into the North American pulp and paper market. This
move will allow us to expand our global footprint, create new opportunities for growth, and provide a well-rounded portfolio to our customers. With JMC Papers we will be one step closer to achieving our vision of becoming a world-class leader in the pulp and paper industry”says Dr. Yesha Patel, CEO, JMC Papers.
JMC Paper Tech Private Limited undertakes designing, manufacturing, supply, erection and commissioning of new pulp mill and paper machines, and also the modernization of existing pulp mill and paper machines. It has its factories in Sanand, Gujarat. The company has effectively a customer base in Africa, Asian & US regions, including countries like Qatar, Saudi Arabia, UAE, South Africa, Kenya, Ethiopia, Ivory Coast, Indonesia, Canada, and Bangladesh, among many others.
Protecting the planet against plastic pollution is the need of the hour, with every industry and sector working towards sustainable goals. The biodegradable tableware industry, with sustainability at its very core, is undergoing enormous growth. Reports from Verified Market Research exhibit that the biodegradable tableware market size was valued at USD 2,754.9 million in 2018 and is projected to reach USD 4,355.1 million by 2026, growing at a CAGR of 6.01% from 2019 to 2026. Read further about the biodegradable tableware industry, its projected growth statistics and key growth drivers, and interviews with the major players in the Indian biodegradable tableware industry.
The responsibility to eradicate the looming crisis of plastic pollution from planet Earth falls inherently on all humans. In recent times, awareness towards this responsibility has increased, resulting in major manufacturing industries working towards the sustainability goal. The global paper industry is fulfilling this responsibility through the conception and adoption of biodegradable tableware. Biodegradable tableware is a range of eco-friendly, compostable tableware products manufactured primarily from agricultural waste like bagasse and renewable resources like bamboo. The biodegradable tableware industry is providing the world with an ecological solution to a crucial issue, utilizing the waste that previously harmed the planet and turning it into valuable packaging.
The product range is vast, ranging from bowls, plates, forks, spoons, container boxes, cups, straws, molded products and others. Biodegradable tableware has various attractive properties like being ovenable, microwaveable, freezable and recyclable. However, one of the most vital features of biodegradable tableware is that it is compostable, as the products naturally break down into organic materials by microorganisms like bacteria and fungi. Since they are made from agricultural residue or any plant-based renewable materials, they improve the quality of soil by reentering the ground, thus contributing in creating a circular economy. In addition to this, the safety of food is maintained as unlike plastic, this tableware is made out of natural, biodegradable materials, making it toxin-free. Due to its positive impact on the environment, the biodegradable tableware industry has witnessed large-scale growth in recent years. Governments across the world viewed the post covid time as an opportunity to restruc-
ture major sectors which could facilitate the transition to low-emission, climate-resilient, and resource-efficient economies. According to the Central Pollution Control Board (CPCB), a ban on single-use plastic products, along with its sale, stocking, distribution and export was imposed from 1st July, 2022. As a result of this significant decision, the demand for the biodegradable tableware industry skyrocketed. Reports from Verified Market Research exhibit that the biodegradable tableware market size was valued at USD 2,754.9 million in 2018 and is projected to reach USD 4,355.1 million by 2026, growing at a CAGR of 6.01% from 2019 to 2026.
There are multiple factors favoring this growth including the rise in awareness among eco-conscious consumers regarding the numerous benefits of eco-friendly tableware in comparison to the detrimental plastic tableware, the rigid regulations and laws imposed by governments in various countries in order to achieve the aim of minimizing carbon emissions as well as increasing adoption of nontoxic and petroleum free products. Moreover, the growing consumption of processed and ready-to-eat (RTE) food products and the increasing use of online food delivery applications have a positive influence on this market. This is because online food delivery applications collaborate with the HoReCa industry, which primarily focuses on food and beverage preparing, packaging and catering.
Following the expeditious growth in the industry, Paper Mart conducted interviews with the companies on the forefront of the Indian biodegradable tableware market, where they shared their contributions to the market through their manufacturing operations and product lines as well as their takes on the current and upcoming trends in the biodegradable tableware market.
Parason Machinery Private Limited is the most preferred supplier of machinery for the pulp and paper industry. With their constantly improving solutions and services, the company has been serving a wide number of pulp and paper mills in 73+ countries around the globe for the last four decades, along with consultation services with their offices based in India and abroad. In a recent interaction with Paper Mart, Mr. Madhure S. Desarda, Director, Parason Machinery Private Limited, shared about the company's clientele, market footprint, USP and its Molded Fiber Products line among other insightful information.
Paper Mart: Tell us about your 'Molded Fiber Products' business line – solutions offered, manufacturing infrastructure & capabilities, technology etc.
Madhure S. Desarda: Parason is providing complete package project for manufacturing compostable molded fiber products and single-use plastic alternative products from agri-residue, hardwood fiber, pre-consumer fiber, etc. Our state of the art manufacturing facility is house for end to end technology support to customer to cater the rising demand of environment sensitive and responsible packaging.
PM: What is your USP and how are your solutions better than your peers?
MSD: Our strength lies in the infrastructure, R&D, and in-house manufacturing facilities that we have along with manpower support. We are serving the industry with latest & advanced technology considering the cost
effectiveness and operation efficiency. Machines are robust and built quality is best in class and we are continuously working towards ease of operation. Our engineered solution is customized according to customers' specific demand like for layout, process, furnish, equipment, etc.
PM: Please share some information about your market footprint and clientele.
MSD: Our customer base is continuously growing with increasing repeat customers and new projects in India and abroad. So far, we have successfully commissioned 40+ projects in molded fiber and 12+ projects are in the pipeline. Market is now evolving with more critical and unique products in the packaging segment.
PM: Are there any new developments for this business segment or any future plans lined up at Parason?
MSD: We have introduced robotic technology in coordination with the main production line to fasten the operations and improve efficiency and economics. Apart from continual improvement in the existing product line, we are implementing and introducing more automated machines for critical geometry products. Our continuous former machine is in the development phase, it would be mainly focusing on the industrial packaging products.
PM: What kind of market trends do you foresee in the molded fiber products and more specifically biodegradable tableware market? What are the key demand drivers?
MSD: Nowadays, more and more products are coming under the compostable and eco-friendly products umbrella as the brands are becoming more conscious about the packaging and its life cycle. To a great extent, choice of customers is also affected due to sensitization
about the harmful effects of polystyrene and SUP. Globally various countries, agencies are running campaigns to make people aware about protection & restoration of the environment, health care, etc. These factors are driving the industry primarily. Compostable tableware is increasing its space in the market for serving and takeaway.
PM: In fact, there are some challenges along with opportunities. According to you, what are the main challenges for this sector and how best these can be addressed?
MSD: Main challenges in the molded fiber industry are fiber pulp, PFAS free chemicals and scalability. Concern with the PFAS free chemical substitute is that of cost. Being imported in India at present, keeping the economics under control is really a challenge. Molded fiber products constitute different product varieties in terms of size, design, usability, types, etc. and every SKU requires a dedicated machine to manufacture the products. Scalability becomes a challenge as the market is developing, supply of raw material is sometimes affected and the amount of investment required.
PM: Lastly, please share your vision for the molded fiber products business of Parason.
MSD: The molded fiber products industry has been growing in popularity due to its eco-friendly and sustainable nature. The industry produces products made from recycled materials that are biodegradable and compostable. Many consumers are now seeking out sustainable alternatives to plastic products, and molded fiber products fit the bill. Parason is also investing in research and development to create new and innovative products to meet consumer demand. Overall, the future looks promising for the molded fiber products industry as it continues to gain traction in the market.
EcosurePulpmolding Technologies Limited offers fiber-based pulp molding solutions to its customers. The whole product line has been designed to contribute deliberately to India's campaign of becoming free from single-use plastic-based products. The company is among the new-age contributors to the Indian pulp and paper industry and is committed to providing turnkey solutions for the industry through its pulp molding machinery. As the industry is experiencing a demand growth for varied packaging solutions, in the form of biodegradable agro-based products, EcosurePulpmolding contributes through customized customer-centric solutions and testedfor-application innovation. Paper Mart, assisted by Mr. Mohit Kumar, Chief Visionary Officer & Co-Founder of EPTL, explores how the company uses its various servicing arms and product portfolio to ensure a reliable customer base in the upcoming years.
“EcosurePulpmolding is the first Indian company offering indigenously designed -developed & manufactured in INDIA saving millions of dollars in imports,” Mr. Mohit Kumar introduces EcosurePulpmolding.
The Make in India campaign, or self-reliant India, is an important government-backed initiative for the Indian economy, industries, and manufacturing-based startups. EcosurePulpmolding Technologies Limited is among the various manufacturing companies that are not only using the opportunity to build a more profitable business for themselves, but also contributing to the Indian economy.
Although the company started its current operations in 2020, it boasts of an industrial experience in this domain of over 10 years in 2023.
The company's roots can be traced back to Taiwanese and Chinese partnerships and ventures in 2012 and 2016 respectively. After getting incorporated in 2019, the company established a state-of-the-art infrastructure to manufacture pulp molding machines and molds in 2020.
Mr. Kumar shared, “EcosurePulpmolding is an ISO 9001:2015 and IAF-certified Company and we have successfully completed more than 25 projects on an all-India basis, around 25 projects are under execution in the year 2023, and 2 international projects are under implementation in Thailand & Australia,” highlighting the success of the company.
Mr. Mohit Kumar descripts, “As a leading pulp molding machinery manufacturer, EcosurePulpmolding has various responsibilities to adhere to.” The responsibilities include understanding the customer's requirements and providing a customized solution. This includes pre-sales and processbased support to the customer.
EcosurePulpmolding offers turnkey solutions to produce eco-friendly molded fiber products and also offers indigenously built fully automatic, semi-automatic pulp molding machines, robotic pulp molding machines, edge trimming machines, and production molds. The semi-automatic pulp molding machines, namely ECOSA 7565 & ECOSA 10095. Out of these, ECOSA 10095 can be modified to adjust any existing mold of any other make of Indian or Chinese machine. The robotic pulp molding machines, ECOSAR 7565, ECOSAR 10095, and ECOSAR 12010, are integrated with the functioning of a ROBOTIC ARM and can be bought as oil-heated based or electric-heated based. The fully automatic pulp molding machines, having models as ECOFA 7565, ECOFA 9090 & ECOFA 12010, are all equipped with an oil-heated or electric heated- base.
EcosurePulpmolding's post-sales services scope is defined by Mr. Kumar, who says, “EcosurePulpmolding is not just a solution provider but a service provider as well. We offer a plethora of post-sales support, including training to machine operators for machine maintenance and operation, extended warranty, and annual maintenance contracts. The maintenance contracts allow our customers to get their installation services repaired timely and cost-effectively”.
In order to facilitate the pre and post-sales services
EcosurePulpmolding has undertaken various steps. “We have a designated R&D center for innovating existing technologies and working towards new ones. Our in-house drawing and designing facilities are used to develop customer-centric solutions along with the upgradation of existing products. We also have an in-house lab for pulp
and mold testing facilities, which we also rent out. We also train new machine operators and our demo-plant facility helps our customers to view and understand the working of the mechanized solutions. We offer 24x7 after-sales support to our customers,” shared Mr. Kumar.
EcosurePulpmolding's products undertake all the functions from pulp-molding or thermoforming, hot-pressing, trimming, and quality checking, to packaging the finished products. The products are designed to follow Zero Liquid Discharge Process (ZLD) and ensure 100 percent recycling of waste products.
Mr. Mohit Kumar elaborated on EcosurePulpmolding's market footprint, “In India, so far we have booked more than 56 projects, and 25 projects are successfully running. EcosurePulpmolding has entered into a technical joint venture with Fang Thai Factory Limited, aThailand Company. The joint venture, FTF Candia Fiber Mold Packaging (Thailand) Company Limited, will offer turnkey solutions by producing chemical-free enzymatic cellulosic fiber (GREEN fib technology) from various types of agro waste by using green fiber technology. We are setting up two international projects, one project in Thailand and another one in Australia.”
EcosurePulpmolding entered the market in a post-Covid era, but its preparations required a study of pre and postpandemic trends. The observation shows a preference for biodegradable products stemming from twin concerns. The first is a higher awareness of hygienic practices and the second is the realization of individual and societal carbon footprint. “The end consumer is more sensitized toward sustainable practices and prefers biodegradable products, like agro-fiber-based tableware, instead of plastic products, such as one-use plastic ware. Hence, EcosurePulpmolding is also making its presence and efforts known toward
manufacturing climate-conscious industrial products,” commented Mr. Kumar.
EcosurePulpmolding's products use agro-fiber or bagasse pulp to manufacture biodegradable products. The agro-fiber pulp is sourced from agro-waste of sugarcane, bamboo, rice straw, and wheat straw. Bagasse-based products are manufactured from sugarcane-based agro-waste pulp.
Mr. Kumar further highlighted the company's contribution towards the Indian economy, “EcosurePulpmolding is a contributor to various government campaigns, such as Make in India and Pradhan Mantri Kaushal Vikas Yojana. We also provide technical education support to our customers through an in-house design facility about how a production plant must be set up.” The motivation for all these facilities is stemmed from the market demand that the company forecasts for the industry's future.
Dinearth (Ashtavinayak Industries) was established by Abhinav Group of Industries to contribute towards sustainable practices in India. Today, the brand is known for its biodegradable high-quality tableware and packaging solutions. Mr. Harsh Mehta, Director, shared with Paper Mart how Dinearth uses bagassebased pulp to manufacture its product line. He also shared the company's history, vision, manufacturing capacity and process, and product line.
Dinearth, a brand of Abhinav Group of Industries, started its manufacturing process in 2018. The company started with a small production facility to test the market, and after a few months of production they realised the huge potential of the industry. Since then, the company's
Our equipment, technology, field service and knowledge is unmatched in the industry,creatingsignificantvalueovertheentirelifecycleofyoursootblower.
Having Boiler plugging or clinker formation issues? Want to avoid 3 days forced outages?
Here we come with our SMART Clean Intelligent Sootblowing System for Pulp and paper recovery boiler. Clyde industries customers realize an average yearly plant savings of $1.56 million and avoid 3 days of forced outages.
l Clyde have good record in reducing the Sootblower steam consumption to a level below 5% of the boiler steam generation while increasing the recovery boiler throughput.
l Increase Throughput and Reduce Operating Costs.
Gearbox Separate from Spindle Keeps Head Away
Seal Pack Packing Cartridge
Clyde Industries is the world's leading Boiler Cleaning operations expert.
production has grown to 8 times and today it is among India's largest bagasse tableware manufacturing companies. The monthly production of Dinearth is 500 tons, that is 6,000 TPA. The company has major market share in India alongwith exports. The company exports 60 percent of its existing products to 30+ countries. The major clientele of the company includes big QSR restaurants, like McDonalds, KFC, Burger King, Chaayos, etc.
Dinearth puts bagasse, that is sugarcane waste, through the hydra pulping process, which is followed by beating the pulp process in the pulp tank. Thermoforming of plates is followed by heating the formed product and then trimming is done on the products. After performing a thorough quality check the final products are packaged and eventually dispatched according to the orders. The company uses two factories to produce 6,000 TPA of finished products.
Mr. Mehta elaborated on the brand's product line, “We have the largest biodegradable tableware product line in India. We have a multiple category of products, such as bowls, plates, compartment plates, trays, containers, clamshell boxes, take away containers, lids, paper straws, etc.” The company offers round plates in 6-12 inches diameter, compartment plates ranging from minimum 3 to maximum 9 compartments, multipurpose trays with/without compartments (depending on their application), bowls ranging from 100-150 ml and 12 & 16 oz, 340 & 500 ml lid-containers, campshell containers in varying quantities and dimensions, and paper straws in different colours and patterns ranging from 5-12 mm sizes.
Market trends are favorable for the industry as the government is taking all the necessary steps for more public awareness to stop using plastic disposable tableware products, and switch to available eco-friendly disposable options. “As per our market study, the overall market size of this category product is 60,000 TPA, hence, there is a huge potential of growth in this industry and in the coming time it will grow in a sustainable way,” commented Mr. Mehta on the demand
of biodegradable tableware in the market. At some level bagasse tableware has taken over the market, but still, there are little difficulties in establishing good sales, because plastic tableware is still prominently available in the market.
Elaborating on Dinearth's plans to tap the mentioned market, he further shared, “We have a very aggressive growth plan in place for the coming years. At the end of last year, we opened our third manufacturing facility for bagasse tableware, which is now fully operational to cater to domestic as well as international demand of the market. We keep introducing new, innovative, and sustainable products in the marketplace. Our goal is to replace styrofoam products with our biodegradable tableware products and become Asia's largest manufacturing company for bagasse-based tableware.”
“As per our market study, the overall market size of this category product is 60,000 TPA, hence, there is a huge potential of growth in this industry and in the coming time it will grow in a sustainable way.”
“The company uses two factories to produce 6,000 TPA of finished products.”
CHUK, the flagship brand of Yash Pakka having a global market, has been manufacturing compostable and biodegradable tableware to tap into the demand from the food delivery sector much before the Covid-19 pandemic. Having a manufacturing capacity of 39,100 tonnes for paper and 42,900 tonnes for pulp, Yash Pakka is the solution provider to any organization that wants to package more sustainably. In an Interview with Paper Mart India, Mr. Satish Chamyvelumani, Business Head, shares interesting details about the company's history, its evolution, recent developments, and future plans.
“When the company was started, the annual production capacity was 1,940 tonnes. In less than 25 years, the capacity grew to 39,100 tonnes for paper as well as 42,900 tonnes for pulp and 8.5 MW of electricity generation.”
Yash Pakka Limited, founded in 1981 by Mr. K. K. Jhunjhunwala as Yash Papers Limited, is one of the pioneers in the Indian sustainable food packaging industry. The company was listed on the BSE in 1992 and has subsequently undergone expansion multiple times. When the company was started, the annual production capacity was 1,940 tonnes. In less than 25 years, the capacity has expanded to 39,100 tonnes for paper; 42,900 tonnes for pulp; and 8.5 MW of electricity generation.
While production was increasing manifold, consecutive plans were being made to expand the scope of offerings as well, which would further the resolve of the company to work towards a cleaner planet. After a successful journey of over 30 years, and having established a strong presence over the low grammage kraft market, Yash Pakka decided that it was time to expand its horizons. This is when the company stepped up to explore manufacturing compostable
tableware. The idea was born from the fact that most of the disposable products available in the market make their way to the landfills or the oceans and then take centuries to be wiped completely from the face of the Earth. After a few years of planning, research, and team building, Chuk was launched in 2017. The subsidiary allowed Yash Pakka to effectively transform its identity from a paper manufacturer to a sustainable and regenerative packaging solutions provider.
Bagasse is sourced locally from a radius of 200 km around the factory. It is depithed and then washed in the pulper. The pith which is separated is used as a fuel in the boiler, and the fibre is sent to the pulp mill, where it is converted into bleached and unbleached pulp. The pulp is then sent to the paper machines as well as tableware machines to make the varied line of products. All these products are bio-degradable and compost within 180 days.
There is a constant cycle of using and reusing the waste to ensure that waste output from the factory is minimized. Firstly, the wastewater from pulp mill is treated in ETP, 50 percent of this water is reused in pulp mill for gardening, bagasse washing, spraying, and irrigation. Likewise, the sludge that is removed in ETP is used to make egg trays. Secondly, black liquor generated in the process of making pulp is sent for chemical recovery. It then goes to the recovery boiler where it may be used for steam and power generation. A part of it is also sent to the recausticizer from the recovery boiler, where lime sludge is converted to mineral pellets, and subsequently to mineral bags. Theremaining chemical recovered from the recausticizer is again sent to the pulp mill.
Chuk manufactures following bio-degradable tableware in different ranges of types and dimensions:
l plates of 6, 7, 9, 10, 12 inch dimensions
l compartment plates in 3, 4, 5, 8 inch dimensions
l bowls of 120,180, 250 ml capacity
l 500 ml containers
l delivery containers of 350, 500, 750, 1000 ml capacities
All these products are in step with Chuk's USPs, which encompasses various points:
l leak proof, so that the food gets delivered without spilling out
l safe, it doesn't dissolve and mix with even hot food items. Usually, toxins get infused in hot food in case of plastic tableware
l sturdy, so the containers are rigid
l 100 percent compostable, so the earth remains clean
l common lids for multiple SKUs – making inventory management easier
l microwavable, freezable & ovenable
l natural & bleach free
l 100 percent food safe
l made in india
l made up of sugarcane pulp - bagasse
Mr. Chamyvelumani's opinion on the post-pandemic market shift provides a fresh perspective, “It is not entirely true that the landscape has only changed post Covid-19. I would like to state that we have seen an upward graph in the last 6 years, and the demand is only expected to increase exponentially in the years to come. The term 'taken over' is far-fetched as far as bagasse solidifying its presence in the packaging market is concerned. However, it must be said that there is growing acceptance of the material and not only businesses, but customers are also starting to use compostable tableware made of bagasse at their homes.”
The company expanded into cutlery and delivery segments. As stated above, the delivery containers are available in 4 different sizes: 350 ml, 500 ml, 750 ml, 1000 ml. Additionally, Chuk recently launched Party Caddy. It is a disposable combo party pack containing 10 pcs each of plates, spoons and tissues. It offers a value-addition for bakeries offering cake. It is also a stylish solution that can be placed on the table and is user-friendly, so anyone can pull out the elements as per requirement. In the near future, the company is exploring more manufacturing opportunities for varied products in the similar range such as tableware by experimenting with different substrates which are compostable in nature.
Belluga Papers Private Limited is a modern high tech enterprise dedicated to production and sales of environmentally friendly products. The company is a leading supplier for the national and international market segment and is ISO 9001: 2015 certified, hence providing full guarantee in product quality, safety and environment protection. The company is one of the foremost manufacturers in various industries having a good market share and have been deeply engaged for business in India, Sri Lanka, Bangladesh, Nepal, Bhutan, in European Nations like Turkey, Romania, Germany and more. In a recent conversation with Paper Mart, Mr. Aman Bajla, Director, Belluga Papers, gave an overview of his company, manufacturing operations and product line, along with the current trends in the biodegradable tableware market.
We at Belluga Papers believe 'Quality is not an Act, It's a Habit'. Having experience in railways and tea processing for 25 years gives us an edge to accelerate in the paper industry. We are an ISO 9001 : 2015 certified company and follow all the quality control practices. We take pride in having a great team of trained and helpful people who are easily available to attend your requirements. Using the latest machines and technology we thrive to improve the quality, reduce the wastage and hence benefit our customers. Our company has been trying to give the best to the tableware industry and make regular developments. We have been a foremost manufacturer in various industries having a good market share and have been deeply engaged for business in India, Sri Lanka, Bangladesh, Nepal, Bhutan, in European
Nations like Turkey, Romania, Germany and more. We constantly strive for improvements and innovations that enhance our performance, securing a healthy environment for future generations. Our outlook is for continued growth, and we plan on increasing our manufacturing capability, positioning ourselves to be one of the world's fastest growing manufacturers.
We procure the materials from the best mills across the country like ITC, Century, etc. which helps us to offer the best quality product. Every product has a different manufacturing process. We use coating machines, slitting, printing, cutting and shrink machines for most of our products. Currently, we have a capacity of 1200 MT/month which we are planning to increase by the end of this year. A major chunk of our revenue is through the tableware sector. We make the raw materials which are used by paper cup , paper straw, plate and box manufacturers and more. We make paper cup blanks of various sizes ranging from 30 ml to 300 ml. We also make paper plate circles of sizes 6 inch, 7 inch, 8 inch, 9 inch, 12 inch, 13 inch, 14 inch, etc. Our firm is engaged in offering poly coated cup stock paper, poly coated poster paper, poly coated maplitho paper, poly coated chrome paper, etc. We do promote recycled paper as well as it reduces the cost for the end users.
With regard to the biodegradable crockery, we assume that there would be a drastic increase in the market in upcoming years. Our company keeps working on the development round the clock. For instance, we have come up with more than 6 different grades of paper and boards for paper plate manufacturers. The biodegradable tableware industry has been increasing drastically but talking specifically about bagasse tableware, there is an acceptance in the country but most of the bagasse manufacturers are targeting exports . Being a premium product in the sector, it might take a bit more to be accepted by the masses.
Shri Veer Balaji Paper Mills has been acquired by Moar Value and is expected to restart operations by April 2023 end. The mill's production capacity has been increased,from100TPDto120TPD,alongwithotherupgrades.
Shri Veer Balaji Paper Mills, located in Muzaffarnagar, has
been acquired by Moar Value. Chaudhary Vikas Moar, the new owner of the mill shared the development with team Paper Mart, giving a background of the mill and its future plans. He informed,“The mill had the capacity to produce 30 TPD mono cartons and high BF kraft board in the range of 150 to 400 GSM, which has been expanded to 100/120 TPD now. We invested about INR 10-15 crore in expansion and the production will start by April 2023 end. To improve the power supply, the feeder line has been upgraded from 11 kVA to 33 kVA. With regard to raw material, we primarily use OCC select, sack kraft, and SMK waste papers which are imported through our group company Astonbury Impex Limited, Canada.”
He further informed that,“The machinery at the mill is majorly supplied by Samarth Paper Machines, Saloni, Parason, Voith, etc. In the future, we also plan to manufacture
duplex boards, file boards, and cup stock. I would like to mention that we received good support from the industry and especially from Mr. Abhishek Aggarwal of Agarwal Duplex Board Mills Limited.”
The Paper Village...
Authorised Dealer of Orient Paper and Industries Ltd. in North India
Vikas Moar
Mobile: +91 9068310683
Email: moarvalue@gmail.com
Address:
# 1109, Padma Tower-I
Rajendra Place, New Delhi-110008
MV Customer Care: 1800-532-9300
Factory: Village Tigri, Bhopa Road, Mazaffarnagar - 251001 (U.P.)
Delhi Office: # 1109, Padma Tower-I Rajendra Place, New Delhi-110008
WeAre RestartingTheMill ByAprilEndWith EnhancedCapacity
Greenvale Eco Products is one of the leaders in manufacturing products from renewable resources. The company is creating huge opportunities for industries looking to move away from plastic packaging, with their products having the capability to withstand moisture, oil & high and low temperatures. Greenvale holds a wide range of biodegradable and compostable food packaging products at their local headquarters in Ichalkaranji, Maharashtra. In a recent conversation with Paper Mart, Mr. Shyamsundar Malani and Mr. Anilkumar Malani, Managing Directors, Greenvale spoke about Greenvale's financial growth, extensive product line and manufacturing capabilities and trends in the biodegradable crockery market.
Greenvale Eco Products is at the forefront of manufacturing products from renewable resources. Our products have the capability to withstand moisture, oil and high and low temperatures, creating huge opportunities for industries looking to move away from plastic packaging. In terms of financial growth, Greenvale Eco Products has been growing at an annual growth of 1.5x to 2x on an average since 2016-2017. When it comes to product range, we started with 11 products at the beginning and at present we are very proud to have a range of 60+ ecofriendly and biodegradable products across various categories like plates, bowls, trays, containers and clamshells covering all the basic necessities for household and HO-RE-CA industry so that people can have many options to switch from traditional plastic products to
“We are producing around 250 tons per month and gradually we are planning and implementing things to raise it by 2.5x by August 2023”
Prioritising
SPRAYING SOLUTIONS
AN ISO 9001:2015 CERTIFIED COMPANY
Wire online cleaning (Actual Picture)
Dryer Screen Online Cleaning (Actual Picture)
OURPRODUCTS:•SHOWERS•OSCILLATORS•SPRAYNOZZLES•WEDGEFILTERS•ROBOCLEANERS
Compound33/16,Site-2,IndustrialArea,HindonAirForceLoniRoad,P.O.-MohanNagar,Sahibabad,Ghaziabad-201007UPIndia
Contact:09810636863,09899889855,09910320682,09999070778|E-mail:rahul_basra21@rediffmail.com,spraying.solutions@gmail.com, Info@sidhuindustries.com,sanjivbasra03@gmail.com|Website:www.sidhuindustries.com
biodegradable bagasse tableware. Overall, the characteristics of Greenvale Eco Products make it a popular choice for environmentally conscious individuals and businesses looking for a sustainable and cost-effective alternative to traditional disposable tableware.
The manufacturing process of Greenvale tableware typically involves a series of steps,which are the collection and cleaning of bagasse where the bagasse fibers are collected from sugarcane mills and cleaned to remove any impurities, followed by pulping where the bagasse fibers are pulped by adding water and chemicals to break down the fibers and create a pulp, after which the bagasse pulp is then molded into various shapes and sizes using molds and presses. The molded bagasse products are then dried in an oven to remove any moisture and increase their strength. The dried bagasse products are then trimmed to remove any excess material and finished to achieve a smooth surface and are then packaged and distributed to customers for use.
From a production perspective, Greenvale Eco Products is growing exponentially, as currently, we are producing around 250 tons per month and gradually we are planning and implementing things to raise it by 2.5x by August 2023 with the help of around 100 semi-automatic machines; currently we have 42 of these machines. As I mentioned earlier, Greenvale Eco Products offer 60+ biodegradable tableware products across categories like plates, bowls, containers, clamshells and food trays. All these products are derived from sugarcane bagasse and all these are compostable as well. Greenvale Eco Products' tableware has certain key characteristics. Bagasse tableware is eco friendly as it is made from sugarcane fibers as mentioned, which are a renewable and sustainable resource. Using bagasse tableware helps reduce the amount of waste sent to landfills and reduces the environmental impact of food service operations. Bagasse tableware is strong and durable, making it suitable for use with hot and cold foods and liquids. Bagasse tableware is microwave-safe, making it convenient for reheating food. Bagasse tableware can be stored in the freezer without losing its shape or durability. Bagasse tableware is fully compostable and will break down in a compost pile within a few months. Bagasse tableware is free from harmful chemicals and additives, making it safe for use with food. Bagasse tableware is an affordable alternative to traditional plastic and paper tableware, making it an excellent option for budget-conscious businesses and consumers.
According to a report by Grand View Research, the global biodegradable tableware market size was valued at USD 1.2 billion in 2020 and is expected to grow at a compound annual growth rate (CAGR) of 5.3% from 2021 to 2028. This growth is primarily driven by the increasing demand for eco-friendly, sustainable, and biodegradable products as consumers become more aware of the environmental impact of their consumption choices. Another report by MarketsandMarkets estimates that the global market for biodegradable plastics will grow from USD 3.02 billion in 2020 to USD 6.12 billion by 2025, at a CAGR of 15.1%. This growth is also driven by the increasing demand for ecofriendly products, as well as government initiatives and regulations promoting sustainable practices.
In addition to the quantitative market trends, there are also some qualitative trends that are driving the growth of the biodegradable tableware market. These include increased environmental awareness, that is, consumers are becoming more aware of the impact of their consumption choices on the environment, and are seeking out products that are more sustainable and eco-friendly, many governments around the world implementing regulations and initiatives to promote the use of biodegradable and sustainable products, which is driving demand for biodegradable crockery, companies investing in research and development to create new and innovative biodegradable crockery products that are more durable, affordable, and aesthetically pleasing as well as consumers increasingly prioritizing sustainability and eco-friendliness when making purchasing decisions, and willing to pay a premium for products that align with their values. Bagasse tableware is also a biodegradable and compostable alternative to traditional plastic or paper plates and bowls, and has good strength to give tough competition to plastic disposable tableware.
Overall, the market for biodegradable tableware is expected to continue growing in the coming years as more consumers and businesses prioritize sustainability and environmental responsibility.
By looking at such a big opportunity, we are expanding in every possible manner. We have our own mould making facility where we design and develop our own moulds and also provide moulds to other fellow tableware manufacturing companies. We have developed our own tuning workshop where we do R&D for our future machinery, we are becoming more independent with each passing day. Earlier we used to rely on the Chinese market for machinery and technologies but in recent times we developed a tendency and trained ourselves to stand independently in the industry.
HenanJingxinFabricTechnologyCo.,Ltd.,foundedin2011,isoneprofessionalmanufacturerandtechnicalservicerofpaper machineclothingandchemicalproductsforpulpandpapermills.
Initspapermachineclothingproductionbase,factoryhas33000squaremeters,annualproductioncapacitycanget 1000000sqm.JingxinfabricʼsformingfabricallusedtheGerman“Perlon”brandhighqualityimpomonofilament,andDryer screenwillusedPortugal“Filkemp”brandmono-filament.InJingxin,toproducehighqualityproducts,weintroducedthe mostadvanced5setsSwedenTEXOfullyautomaticrapierloom,14.5metershotsettingmachine,16metersGerman Jürgensweavingmachine,AustrianWISfullautomaticseamingmachine,etc.
ThecoreproductsforpapermachineclothinghasFormingFabric,DoubleWarpFlatWireDryerFabric,SingleWarpFlatWire DryerFabric,SpiralDryerFabric,PlainWeaveDryerFabric,SludgeDewateringFabric,etc.
Initspapermakingusedchemicalproducts productionbase,factoryhas44000squaremeters, annualproductioncapacitycanget400000tons.
ThecoreChemicalproductsare:SurfaceSizingAgent GS,SurfaceSizingAgentWS,WetStrengthAgent,Dry StrengthAgent,Defoamer,etc.
JingxinmanagementhaspassedISO9001qualitymanagementsystem,ISO14001environmentalmanagementsystem,ISO 18001occupationalsafetymanagementsystemcertification.
Duetothereliableproductquality,theproductssellwellalloverthecountry,andhavereachedlong-termcooperative relationswithmanylistedpapercompaniesinChinaandthepulpandpapermillsfromRussia,India,Vietnam,Pakistan,Iran, Indonesia......morethan15countries.
Tel.:+863945228866
Mobile:008618838386818
Fax:+863945106388
E-mail:info@jingxincorp.com
HENANJINGXINFABRICTECHNOLOGYCO.,LTD
Website:www.jingxincorp.com
SHENQIUNORTHINDUSTRYZONE, HENAN,CHINA
Bionova Packaging Solutions Private Limited is engaged in manufacturing 100% natural, 100% eco-friendly, 100% compostable & 100% biodegradable multi-purpose rigid packaging solutions made from agro waste pulp that breaks down really easily in natural environments and industrial facilities.
Bionova's technologies protect the products against oil, water and oxygen and eliminate the need of single-use plastics. In a recent interaction with Paper Mart, Mr. Nitin Mehta and Mr. Ankit Shroff, Founders, Bionova, shared about their company's journey, manufacturing process and capacity along
trends in the biode-
Bionova Packaging Solutions Private Limited was founded by Mr. Nitin C. Mehta, a Science graduate with Business Management certification and 40 years of experience in writing instrument & stationery industry; and Mr. Ankit P. Shroff, a Master of Science post graduate with 20 years of experience in manufacturing of chemical and plastics industry. These minds are on a mission to revolutionize the way we think about packaging with their innovative line of biodegradable and compostable products for single-use disposable categories. Their journey began in the midst of the pandemic in 2020, when they set out to create sustainable products made from bagasse. To ensure the reliability of their product and process, they invested in a small-capacity production machine that same year. Fast forward to today, Bionova Solutions Private Limited is proud to announce the launch of their state-of-the-art production plant, which has been started in phases. Production lines 1-3 were
launched in phase 1 at the beginning of 2022, with lines 47 following in phase 2 in mid-2022. And just recently, lines 8-10 were launched in phase three in early January 2023, marking a major milestone for the company.
Our manufacturing process begins with the pulping of bagasse & other raw materials, followed by moulding which involves forming and hot press, then the trimming procedure, sorting for quality check after which we do packing of finished product. We have 10 production lines having semiautomatic machines with robotics to place the finished product on the conveyor for final quality control sorting and/or packing. Our annual production capacity can vary from 1,000 MT to 1,500 MT based on the type of product.
Our company takes pride in introducing an extensive line of eco-friendly tableware products made from bagasse, a naturally occurring by-product of sugarcane. The range comprisesanarrayof products, including round and rectangle plates with compartments, meal trays, bowls, cups, cup lids, clamshell boxes, and spoon-fork-knife cutlery. Our products are unique because they are oil, water, and oxygen-resistant, eliminating the need for single-use plastics. We design our technologies with the intention of making them recyclable, compostable, and biodegradable. The products are also microwave and oven safe, catering to the demands of modern households and businesses alike. Our design ethos revolves around creating recyclable, compostable, and biodegradable products, aligning withourcommitment toreducing environmental waste. We are totally professional in this and we treat ourproducts & processwith scientific testing methodsand technologiesso, theproduct'squalityand itscompliance meet global standards & certifications such as: BPI, CIPET, TUVOk Compostable (Industrial), ISO, and USDA-Biopreferred.
Bagasse tableware products are gradually becoming the main consumption region in developing countries, particularly in Asia. The United States is currently the world's largest consumer of bagasse tableware products, followed by China. The growth rate of global bagasse tableware product
shipments is expected to be between 10 to 12 percent. Currently, the Asian countries are the largest consumers of bagasse tableware products, followed by Europe and North America. Owing to their cost-effectiveness and the economic development of developing countries, the bagasse tableware product industry is gradually shifting to these regions. This has resulted in a rise in the number of 40+ manufacturers from developed countries like India, establishing their plants in developing countries. The future outlook for the bagasse tableware products market in developing countries seems bright, with India already displaying a significant expansion.
At Bionova, we are proud to be the first in India to develop bagasse-based cutlery, comprising forks, spoons, and knives, rather than the conventional wood or PLA-based options. Wood-based cutlery poses smell and depth concerns, while PLA cutlery is relatively expensive. In the future, our expansion plans involve including more single-use category products in our product line, with custom printing options to cater to end customers. The bagasse tableware market has recently gained attention post-COVID-19 as a result of the rising trend towards sustainable living practices. With the increasing consumer demand for eco-friendly alternatives, eco-friendly bagasse tableware products are replacing nonbiodegradable plastic products. While plastic and Styrofoam remain the cheapest and most accessible packaging materials, they are not environmentally friendly. On the other hand, bagasse is one of the most sustainable options for producing various food packaging and serving products.
The market growth in this sector can be attributed to the escalating demand for sustainable and eco-friendly tableware, as well as the growing awareness among consumers regarding environmental issues. Furthermore, the Indian government's recent restrictions on the use of single-use plastic products have had a significant impact on the market's growth. Additionally, the high production of sugarcane in India has made it a readily available and viable source for the growth of the India sugarcane bagasse biodegradable disposable tableware market. It is expected that consumer awareness of the benefits associated with the use of biodegradable tableware will continue to drive the market growth. Consumers are increasingly choosing bagasse tableware products as a perfect packaging solution due to their safe, reliable, and hygienic characteristics, making them the ideal choice for food service providers.
Ecoware is a one-stop shop for eco-friendly products that are 100 percent natural, biodegradable, and easily affordable. Ecoware was established in 2010 by Ms. Rhea Mazumdar Singhal, Founder & CEO, who shared with Paper Mart how the company has remained focussed on adopting sourcing and manufacturing practices which are as sustainable as the company's product line.
Ecoware is led by its dynamic CEO and Founder, Ms. Rhea Mazumdar Singhal, who is a World Economic Forum Young Global Leader and a Nari Shakti Puraskar awardee. She is a trailblazer by being one of the few women leaders in the industry. Under her leadership, Ecoware has 12 sales partners globally, 21 distributors in India, and 1500+ point-of-sales shops across India. Ecoware takes immense pride in being over-certified. Ecoware is the only PFAS-free BPI (USA) and OK Compost (EN 13432, Europe) certified manufacturer in India and has been audited on Environmental, Social and Governance parameters and achieved USD 2.41 of impact for every USD 1 invested. Ecoware has been recognised for its efforts to promote the principles of a circular economy. The company was presented the Mahatma Award for Social Impact in 2021 and was first runner-up in the Amazon Sambhav Entrepreneurship Challenge in 2022. Furthermore, Ecoware was awarded equity-free grants by Dubai Expo 2020 and Barclays Unreasonable Impact Group.
Ms. Singhal's pride in her company is easily spottable, “Ecoware introduced bagasse tableware to India. We were
“Ecoware's production capacity will reach 1,800-2,000 TPA in this year.”
the first company to set up a manufacturing plant in 2010. Our efforts during those early days to introduce a revolutionary product in India, have since been validated with the explosion in demand for sustainable packaging, particularly bagasse tableware.” Bagasse is an important raw material for biodegradable tableware products, as no other truly sustainable product can offer a better alternative to singleuse plastic. Even paper has its limitations as it does not offer all the required shapes.
The manufacturing facility uses thermo-forming of wet pulp slurry to manufacture finished products, such as tableware and packaging. The pulp is sourced from local mills lying within a 250 km radius of the plant. Ecoware also actively works with low-income farmers to turn their waste biomass, which is usually burnt in the open and is financially and environmentally detrimental, into a source of positive outcomes. From rice straw to sugarcane bagasse, Ecoware takes what was once waste and turns it into a 100 percent ecofriendly product curbing the production of plastics and their dispersion into the natural environment.
Ecoware's production capacity will reach 1,800-2,000 TPA in this year.
Ecoware uses only bagasse pulp and does not adulterate with paper pulp or any other items. The company has a range of 50+ compostable products, including disposable tableware, cutlery, and takeaway packaging. All products are 100 percent natural, biodegradable in 90 days, and provide a permanent solution to single-use plastics. Ms. Mehta shared, “We use only local raw materials thereby keeping costs and our carbon footprint low.” Ecoware has 55 products across tableware, takeaway packaging, and food retail solutions. The company's products have a shelf life for food service from 1 hour up to 1 month. The company also offers a range of shelf-ready retail products with customized design and branding as per the customer's requirement.
The Ecoware range of products is water and oil proof, and provides varying degrees of repellence depending on the customer's need. These products can be microwaved safely O O up to +140 and frozen to -20C without changing the C structural integrity of the product. Most importantly, Ecoware is certified (ISO 17088) biodegradable and compostable, this means its products will disintegrate naturally in whichever waste stream they are disposed in.
Covid-19 has certainly accelerated demand for bagasse, with it being a natural, plant product that is considered healthier and more hygienic than plastic or aluminium. Furthermore, with many restaurants switching to delivery-only models the need for disposable packaging has increased manifold.
Covid-19 pandemic has taught people to lay lots of emphasis on health and follow safety measures. The disposable cutlery items are safer than the reusable cutlery items, as a result of which their sales spurred during the pandemic. The disposable cutlery items also reduce the risk of infection as these are disposed of after being used once. Thus, increased focus on hygiene measures is expected to surge the sales of disposable cutlery.
Ms. Mehta shared on behalf of Ecoware, “In our opinion, the milestone decision to ban single-use plastic in July 2022 has had a greater impact. End use customers are more aware of the harmful effects of plastic on human and animal health and are nudging retailers and food service operators to move away from plastic. This quantum of advocacy has never happened before and it is heartening to see a collective social push to rid our country of plastic once and for all.”
The global compostable foodservice packaging market is forecasted to attain a valuation of USD 18.9 billion in 2023. Total compostable foodservice packaging sales are projected to surge at a CAGR of 4.5 percent between 2023 and 2033, totalling a colossal valuation of USD 29.3 billion by 2033. The growing foodservice industry in India is a key factor augmenting sales of compostable foodservice packaging. Increasing non-chain restaurants across the global boost the demand for foodservice packaging including compostable foodservice packaging. As per Future Market Insights, India's compostable foodservice packaging market is projected to expand 1.9 times the current market value during the projection period of 2023 and 2033. Growing demand for compostable packaging solutions across restaurants, cafes, hotels, and other establishments due to their sustainable and eco-friendly nature is projected to boost the global market forward during the forecast period. The target segment is expected to remain the leading segment in the compostable foodservice packaging industry holding around 27 percent of the market value share by the end of 2023.
Ms. Mehta shared Ecoware's plans as well, “At Ecoware, we aim to support the ban on single-use plastic products along with government regulations towards sustainability. For this reason we plan to increase our capacity and product offering by 2x this calendar year by offering products for all demand of food services – catering, delivery kitchen, travel, food courts and retail.”
Varsya Eco Solutions Private Limited, an ISOcertified company, specializes in the manufacture and distribution of cost-effective eco-friendly products. The brand exclusively offers eco-friendly and biodegradable products like bagasse disposable plates and containers that are made from renewable resources such as bagasse, wheat, and bamboo fibers that help minimize harm to the environment. In a recent interaction with Paper Mart, Mr. Nitheesh Sundaresan, Founder, Varsya shared an overview of the company's work, vision and mission, their manufacturing capabilities and vast range of biodegradable products, as well as current qualitative and quantitative trends in the biodegradable crockery market.
Varsya Eco Solutions Private Limited is a company that recognizes the importance of sustainability and preserving the environment. Varsya Eco Solutions was established to address these challenges and promote eco-friendliness by launching the brand VARSYA. The brand exclusively offers eco-friendly and biodegradable products that help minimize harm to the environment.
Our bagasse disposable plates and containers are made from renewable resources such as bagasse, the dry fibrous residue left over once sugarcane has been pressed for juice, wheat, and bamboo fibers. These materials are not only eco-friendly, but also provide benefits such as being suitable for hot, wet, and oily foods, and are a great alternative to plastic/styrofoam disposable tableware. They are also ideal for take-away food items.
At Varsya Eco Solutions Private Limited, we only source the final products from trusted and high-quality manufacturers, ensuring that the products meet our strict standards for sustainability and quality. Our manufacturing partners use raw materials such as bagasse, recycled paper, natural clay, and other renewable resources to create our eco-friendly product lines. We work closely with our partners to ensure that the production process is sustainable and environmentally responsible. To ensure transparency in our manufacturing process, we maintain an open line of communication with our partners and conduct regular audits of their facilities. This allows us to verify that they are using sustainable production practices and maintaining the quality of the final product. Currently, we have partnered with several manufacturers across India to produce our eco-friendly product lines. Our partners have state-of-the-art machinery and equipment set up to produce high-quality products. One of our most popular product lines is the Varsya ecofriendly notebooks, which are made from 100% recycled waste papers and do not contain any wood pulp. Our pens and pencils are also made from recycled waste papers. This process produces lower carbon emissions and uses 77% less energy compared to virgin fiber paper. We also offer Varsya biodegradable carry bags, which are made of a bio-based polymer compound manufactured from renewable natural materials such as cassava starch and other vegetable oil derivatives. Varsya bagasse disposable plates and containers are another product line that we offer. Our clay tableware is made from natural clay extracted from deep soil layers. Its porous nature allows both moisture and heat to circulate through the food, which results in slow yet aromatic food. We also offer disposable kraft containers and paper cups, which are made from high-quality kraft papers and white paperboard with food-grade coating. These products are light-weight, durable, leak-proof in normal shake, greaseresistant, and suitable for hot curries and beverages.
The market trend for biodegradable crockery is definitely on the rise, and the demand for sustainable alternatives has increased significantly in recent years. According to a report by Grand View Research, the global market for biodegradable tableware is expected to reach USD 1.23 billion by 2027, with
a CAGR of 6.2 percent from 2020 to 2027. One of the main challenges faced by the industry is the use of plastic film coating on many sustainable alternatives, such as paper cups. This coating is used to maintain the integrity of the food and to ensure the longevity of the product. However, this creates a barrier to the biodegradability of the product and contributes to plastic pollution.
Varsya Eco has recognized this issue and has come up with an innovative solution by developing a bio-based alternative. Our company has revolutionized the packaging industry with its biolayer technology derived from vegetable seeds. This biolayer provides a sustainable and environmentally friendly alternative to plastic coating. Our biolayer is non-toxic and completely biodegradable, ensuring that it does not harm the environment in any way. It also serves as a food migration barrier, making it an excellent alternative for packaging products in various industries, including FMCG, pharma, printing, and courier industries.
India is the world's second-largest sugarcane producer, with an estimated 550 million metric tons of bagasse produced annually. This provides a vast resource for bagasse-based products, making it a sustainable and readily available option. Additionally, the Indian government has taken steps to promote the use of eco-friendly products, including bagasse tableware.
The Ministry of Environment, Forest, and Climate Change has even suggested a complete ban on single-use plastics by 2022. The advantages of using bagasse-based tableware are numerous. They are sturdy, microwave-safe, and can hold hot and wet foods without leaking or getting soggy. Additionally, they are compostable, and the discarded products can be used as natural fertilizers, making them a sustainable and eco-friendly option. Moreover, bagasse products are affordable and widely available, making them accessible to consumers and businesses alike.
In conclusion, we believe that bagasse tableware is an excellent alternative to unsustainable tableware products, especially post-Covid-19. The increased awareness of environmental issues and the need for sustainable solutions have made bagasse products more popular than ever before. We encourage everyone to switch to bagasse-based products and contribute to building a greener and more sustainable future.
SPS Kalyan Machine Designer assumes the responsibility of providing technologically advanced machines to agro-waste-based tableware manufacturers. These machines integrate the application of various types of agro-based waste for finished products. Mr. Kalyan Kumar, Director & Founder, SPS Kalyan, shares with Paper Mart the company's history, unique solutions, and market strategy.
In 2018, Mr. Kalyan Kumar started the company - SPS Kalyan Machine Designer with the help of his father's experience, who has been in the field of machine making for 14-15 years. Post-startup, the company continued on the areca plate machines project for a year, after which Mr. Kalyan self-conducted a small survey. He researched the agricultural materials that are thrown away by humans. Post-survey, he reimagined his machine-making formula and launched a machine design project, wherein the machine uses all types of agro-waste that the buyer can procure for their finished products.
“Now in my company's machines, I have successfully integrated application of 35+ types of agriculture raw materials,” comments Mr. Kalyan Kumar.
SPS Kalyan Machine Designer invests in designing and making machines that target the main problems of biodegradable tableware manufacturers, who use various
An upcoming media company, Tulip 3P Media brings out publications for different B2B verticals. Theactivitiesofthecompanynowembraceeventsandmarketresearchaswell.Tulipiscurrently on its way to further expanding its publication portfolio through publications for other business verticalsandarichofferingofothernichemediaservices.
types of agro-waste to make their finished products. The company's single machine can apply 30+ types of agrowaste into the manufacturing process, including rice bran, rice husk, rice straw, wheat bran, wheat grass, peanut shell, tamarind seed, bananas material, coir, non-poison wood powder, coffee shell, ginger spent, palm tree fiber, tender coconut, bamboo powder, onion peel, coffee waste, cotton waste, sugarcane waste, areca shell, etc.
The company also attends to the dual concerns of machinery maintenance and general technological awareness in the market.
The agro-based biodegradable tableware is in huge demand, especially during the post Covid-19 period. The manufacturers of these products are SPS Kalyan Machine Designer's customers, and it is the company's effort that the product manufacturers can satisfy all types of products bought. This area of service is important as the final product value differs for different raw materials.
The company's solutions have been designed after a careful market study, as Mr. Kalyan shares, “70 percent of biodegradable products manufacturing units suffer losses due to three reasons; only one raw material can be used by any one machine, the machine makers do not guide their customers on proper machine operation, and poor marketing of technological advancements and solutions. SPS Kalyan addresses all three resulting in 100 percent satisfaction and reduction in losses for our customers.” SPS Kalyan's technology is one-of-a-kind and the competition is negligible, hence marketing is easier as well. The company also trains the product manufacturers on managing machine operations.
All the machines are designed to process agro-based raw materials, instead of plastic or paper, for a final product that is biodegradable and edible, that is it can be used to feed cattle and poultry. Mr. Kalyan shares, “My company has successfully launched this project to design machines that make all types of biodegradable and edible tableware products.”
Thooshan, a unit of Vir Naturals Private Limited, has a clear goal; to provide a replacement for the current disposable single use plastic utensils in the market. The company believes that its initiative will help in increasing public awareness. The manufactured dishware have a longer shelf life, attractive designs, are completely biodegradable, and partially edible! Mr. Vinayakumar Balakrishnan, Chairman & MD of Vir Naturals Private Limited, shared with Paper Mart how Thooshan came into existence and why it is unique, the numerous accolades within a short span of time, and a glimpse into future plans.
Thooshan brand came into existence with a goal to provide a replacement for the current disposable plastic utensils in the market. Mr. Balakrishnan elaborates, “Millions of single-use cutleries end up in landfills every year after being used once. Through our initiative, we hope to put an end to this behaviour and increase public awareness. Our mission is to start a cutlery revolution.”
Thooshan was incubated at IIT-Kanpur, Kerala Agricultural University and Indigram Lab Foundation, New Delhi. On 17th August 2021, after a research and development of more than 3 years, the company soft launched commercial production in a fully automated robotic plant at Angamaly, Kochi. The project focused on creating fully biodegradable tableware, such as single-use plates, cups, take away boxes, cutleries and glasses. The company has already won many accolades on the way, including the prestigious United Nations' - UNDP Green Innovation Fund award. The company is institutionalized by Kerala Start-up Mission, and Haritha Kerala Mission, 2021, for its idea and start-up grant. The company is a national winner from Kerala for RAFFTAR ABI for innovation in Agricultural products, 2021, awarded by the Government of India.
NIIST-Council of Scientific and Industrial Research (CSIR), Govt Of India, Trivandrum, Kerala, is the technology partner of Thooshan. Thooshan's project is under technical collaboration with NIIST/CSIR (Govt of India).
Commenting on the uniqueness, Mr. Balakrishnan states, “We are 2nd in the world and 1st in India using this technology.”
Thooshan makes a range of plates, bowls made from natural wheat bran. The company uses dry process
technology with very less water and wastage at its fully automated robotic plant at Kochi, and can produce 1000 plates per day. “Our Thooshan plates are 100% biodegradable and mix with soil in less than 30 days. We are scaling up to make 5000 plates per day.” The whole product line consists of agriculture by-products (wheat bran or rice bran or rice husk) coated with other natural ingredients and natural binders.
Thooshan's dishware has a longer shelf life which is fungus and bacteria resistant. Dishware from Thooshan is completely biodegradable and partially edible. The whole product line is affordable to common man, especially once production reaches critical volumes, is safe for a bite, microwave friendly, and has water retention capacity. Thooshan offers packaging solutions which are fungus & bacteria resistant, biodegradable in 30 days, and have a long shelf life, that is of 1 year.
Thooshan's manufacturing process and products also help in additional income generation from waste for farmers and local mill owners. The company has plans to expand its current operations, as shared by Mr. Balakrishnan, “In June 2023, we are launching the full cutlery range including fork, knife, spoon, and takeaway containers, which has been certified by CSIR and CIPET.”
Thooshan's product line is biodegradable as well as partially edible! However, one doesn't always have to eat the plate; once thrown away, it decomposes into organic manure for the plants. After its use, these tableware can be used as cattle feed, fish feed, or poultry feed. The base idea is clarified by Mr. Balakrishnan, “The use of single-use plastic could be reduced to large extent by this novel concept. Join us to change the way we eat and think about waste.”
IPPTA organized its 58th AGM & Seminar 2023 in Hyderabad. The event was inaugurated in the presence of Mr. Jayesh Ranjan, Principal Secretary of Industries & Commerce (I&C) and Information Technology (IT), Telangana, and the keynote was delivered by Mr. D.P. Chandrana, CII Green Co Assessor & Founder of DC Careerplus. The two-day event brainstormed ideas from within the industry as well as from external participants about how green manufacturing could be integrated into industrial practices so that every process is as environmentally inclined as the industry's finished products are.
Indian Pulp and Paper Technical Association (IPPTA) conducted its 58th AGM and Seminar 2023 in Hyderabad. The two-day event was held on the 17th and 18th of March 2023, and its theme was Preparing Paper Industry Towards Green Manufacturing. The inaugural session of the IPPTA Seminar 2023 was guided by Mr. M.K. Goyal, Honorary Secretary General of IPPTA. The dais was enthroned with the seminar's Chief Guest Mr. Jayesh Ranjan, Guest of Honour Mr. K.N. Rao, Mr. Ganesh Bhadti, Mr. Anupam Sharma, Mr. Pavan Khaitan, and Mr. D.P. Chandrana.
The welcome address was given by Mr. Anupam Sharma, Chairman of the Programme Committee, and Vice President-Material at ITC Limited - PSPD, Secunderabad. He welcomed the guests and audience of the seminar, “The paper industry has gathered as a whole to discuss various challenges and find ways forward for inclusive growth. The industry has been facing challenges on various fronts, right from raw material
availability, energy, and fuel scarcity, spiraling cost, logistics constraints, and even HR-related issues; another front has been added to our list of challenges, which is how to make our manufacturing greener in the context of increasing pressure on natural resources and rising expectations from stakeholders, and we also need to stay ahead of any statutory needs which governments may impose in future. The biggest challenge is a financial and economic misperception, as sustainability is perceived as expensive, and businesses tend to prioritize profit and
economic growth. However, various studies, including at the World Economic Forum, suggest that both profit and caring for the environment can coexist and when we consume less, we recycle more, and overall costs can be reduced.”
The Keynote Address was delivered by Mr. D.P. Chandrana, CII Green Co Assessor & Founder of DC Careerplus. He covered various aspects of green manufacturing and how the pulp and paper industry can integrate it. His speech could be divided into parts, wherein in the
first part he bulleted various achievements and persisting challenges for the industry, “Earlier, our vision was confined to measuring BOD, COD, and TOC in effluents, and SPM in stacks. We have progressed a lot since then, for instance, our water consumption has been brought down to 30 kL per tonne from a high rate of 250 kL per tonne, and expansion of the bleaching sequence till the ozone level. However, we still have lingering issues, which have been heightened in the wake of a series of events- raw material availability, environmental regulations, Covid-19, the RussiaUkraine war, and lack of manpower. We have reduced our electricity and steam consumption by 13.5 percent and 16 percent, respectively, but our average remains higher in comparison to the global average. The global average for electricity consumption globally is 1,000-1,100 kWh per tonne, while the Indian paper industry's average is 1,400-1,500 kWh per tonne; the global steam consumption average is 7-9 kJ per tonne, and in India, it is 12-13 kJ per tonne.”
Mr. Chandrana's second part of the speech was identifiable with solutions to integrate green manufacturing in the Indian pulp and paper industry, “We need to change our thoughts and mindset. We need to think renewable to lower our carbon footprint and must inventorize our greenhouse gas emissions, for instance, Scope 1 and 2 is alright but Scope 3 must be addressed properly. Integration of green manufacturing will require a community effort to create a circular effect, such as setting up of a green supply chain. We also need to promote certification and honest and transparent annual green reporting. Paper plants need to visualize themselves working without coal boilers in upcoming times so that they can work on reducing their dependency on fossil fuels.” He also relayed that the Government of India has allocated INR 19,700 crore toward the exploration of green hydrogen exploration as an alternative fuel.
Mr. Jayesh Ranjan, Principal Secretaryof Industries & Commerce (I&C) and Information Technology (IT), Governmentof Telangana, urged the industry to change the outsiders' perception and take defined and deliberate steps to move towards green manufacturing. He addressed the event, “I want to bring to note that this industry is under public scrutiny due to obvious reasons. For instance, a cabinet of three ministers has been appointed to review mega-project investment proposals, that is with a capital investment of over INR 200 crore. Some time ago, we received a proposal of over INR 1,000 crore investment from a company based in the paper industry. While generally, such projects are discussed for the quantum of incentives that can be offered to them, this time around the discussion is, the kind and amount of damage and pollution that this project will inflict on the surrounding ecology. You need to turn around this perception by becoming remarkably efficient and gaining credit for green manufacturing. Your efforts need to be enhanced and venture into firm commitments and actions. Instead of mentioning cost concerns of integrating green manufacturing practices, you must initiate a Cost Benefit Analysis for short and long-term effects. You must engage with technological advancements and start-ups to optimize every step of your process. These steps will help you make a case to the general public and government as well, who can in turn help you in researching better options and support your investments.”
Mr. K.N. Rao, Corporate Head (EHS, AFR, Energy & Sustainability) of My Home Industries Private Limited, put forward a proposal to the pulp and paper industry, on behalf of the cement industry. He suggested a large-scale collaboration of the industries to exchange ideas and technologies for a united solution and movement towards green manufacturing, “Resource conservation is necessary and we need to mitigate our carbon footprint and emissions. The cement and paper industry share many concerns, such as raw material security, as there are only 90 billion tonnes of minable limestone reserves, which at the current rate of consumption will deplete severely in the next 30 years, and energy and fuel use, we need to replace fossil fuels with biomass and industrial waste as possible energy sources. However, both industries have managed to make advancements in different areas, for example, the cement industry is already water positive and follows ZLD policy, and the paper industry has managed to make its plants CO2 positive. I believe that the two industries must do a strategic collaboration and discover ways to help each other and bring forth a collective change. We can also brainstorm new advancements and ideas to convert our place of operations into biodiversity hubs, allowing nature to replenish itself.”
Mr. Ganesh Bhadti, President of IPPTA, and Director of Operations of Seshasayee Paper & Boards Limited, Erode, in his presidential address gave a general overview of Indian industry and the direction it should head towards, “India is growing and it is a good sign, but on the other hand, a grave concern demands our attention; degradation of environment and depletion of natural resources. We have to respect our suppliers and integrate green chemicals and technological support to increase the efficiency of our operations.”
At the end of the inaugural session, IPPTA awarded Lifetime Achievement Awards in four categories Professional, Entrepreneurship, Technology Provider, and R&D & Academics to Dr. A.R.K. Rao, Dr. Ajay Satia, Mr. C.S. Panigrahi, and Dr. A.K. Ray, respectively. The session was concluded by Mr. Pavan Khaitan, Vice President of IPPTA, and VC & MD of Kuantum Papers Limited, with a vote of thanks, “We are all here to deliberate upon an important theme; preparing the paper industry for green manufacturing. It is clearly the need of the hour, and if not now, then when? We need to take proactive action to save our planet. A lot has already been done by the industry, but a lot more needs to be done. As the Indian economy is progressing at a fast pace, so is our paper industry, but there is a risk to the environment. We need to take
action now and inculcate sustainable practices in our processes, as all of us are leaders in our own rights. A vote of thanks to Mr. Jayesh Ranjan, for his clarity of thoughts on sustainable development, Mr. D.P. Chandrana for enlightening us with the industrywide trends and motivating steps, and the event programming committee.”
The panel discussion was held on the second day of the event and consisted of nine panelists, Mr. Akshat Agarwal, Vice-President (Purchases) of Vijay Anand Kraft Papers Private Limited, Mr. Akshay Rathi, Director of Kaygaon Paper Mills Limited, Mr. Aseem Bordia, President of Federation of Paper Traders Association of India (FPTA), Mr. Hardik Patel, Director of Om Shree Papertek Private Limited, Mr. Madhure Desarda, Director of Operations of Parason Machinery (India) Private Limited, Mr. Mike Grundy, CEO of Amazon Papyrus Chemicals Private Limited, Ms. Priya Venkat, Co-Founder & COO of Haber Water Technologies LLP, Mr. Ramit Bhatnagar, COO of M.J. Global, Mr. Siddhart Mohanty, Vice President & Bhadrachalam Unit Head of ITC Limited - PSPD.
Mr. K.S. Venkatgiri, Executive Director of CII - GBC, Hyderabad, moderated the panel discussion, urging the members to discuss ways to double the growth percentage, overcome the industry-wide challenges, and penetrate the new markets in the domestic and global scenario. The panelists put forward their views individually and while each of them had unique ideas to put forward, major ideas overlapped. The conclusion that can be drawn from their ideas is that the industry needs to undertake major re-engineering of its structure and processes. The industry needs to reimagine all of its
current processes and operating models so that it can create a secure future for itself, which is in step with green manufacturing.
Raw material availability is a huge challenge for the pulp and paper industry. There are three types of raw materials used by the industry, agriculture waste, waste paper, and wood. While many mills have started opting for waste paper and agricultural waste in their green manufacturing integration drive, the lack of organization in the waste collection is a huge problem, especially for smalllevel mills, which often suffer at the hands of the local-procurement system. The panel proposed that the industry must collectively take initiative to organize the waste paper collection so that the raw material is easily available and unpredictable cost fluctuations could be avoided.
Technology must be integrated into the mill operations for maximum efficiency, resource optimization, lesser breakdowns, and expedited processes. The Indian industry can learn from European and North American industries, wherein many plants have streamlined their whole mill operations onto a single interface. This gives centralized control of mill operations. The technology integration will broaden the human resource pool as well, as gender bias which still grapples the industry could be eliminated. The centralized operation will shift the manual labor focus to mind labor allowing increased participation of women in the industry's factory-based work as well.
Human Resources for the pulp and paper industry is labor-oriented presently, and professionals have to be fished from other industrial pools. This hampers the mills from integrating technology into their operations. It is proposed that the industry takes initiative to train their blue-collar workers within updated operations. Additionally, the industry needs to collaborate with national universities to introduce paper-engineering-based
courses into their curriculum. Mr. Desarda proposed elective courses and OPT programmes, so that the industry can recruit fresh talent and initiatives.
Investment in green manufacturing practices must be seen as an asset rather than a cost by the industry, that is it will generate value-based results over the years. The industry can benefit by investing in processes that reduce CO2 emissions, water consumption, odor emissions, energy, fuel consumption, etc. These practices will improve the general perception of the industry attracting government support and international interest as well.
Green Manufacturing practices must be visioned at every level of operation of the industry. These
practices rather than being initiated as ethical procedures on a small level must be undertaken as accountable drives. Green Accounting will help the industry to accept responsibility and establish accountability for their actions. This will help them see the said practices as consequential. The industry will then have to integrate growth and profitability with green practices, ultimately driving innovation and long-term solutions. The aim of reducing dependency on nonenvironment-friendly practices could be achieved faster, ahead of statutory regulations that the international market and Indian government are moving towards.
Brand Image is a major determinant behind success, especially in times of omnipresent connection. The industry needs to reverse the
mindset of the general public and government or it could not grow. The times are favorable as single-use plastic could be replaced by paperbased solutions, which are biodegradable and environment-friendly. When the processes undertaken to produce eco-friendly products gain a good reputation, our current capacity could be built upon. The Indian pulp and paper industry has a lot of opportunities in this area, as the country can integrate service and manufacturing aspects domestically, which the US and China have achieved individually, respectively. Hence, India has dual opportunities to grow its per capita consumption and exports of paper-based solutions. The industry can identify several markets wherein plastic solutions need to be replaced.
Archroma is a global,
diversified provider of specialty chemicals serving the branded and performance textiles, packaging and paper, and coatings, adhesives and sealants markets. Headquartered in Pratteln, Switzerland, the company operates a highly integrated, customer-focused platform that delivers specialized performance and color solutions in over 100 countries. They do that by applying the principles of “The Archroma Way to a Sustainable World: Safe, Efficient, Enhanced. It's our nature.” They help brands and manufacturers to create more sustainable products and processes, with their color, effect and performance chemical innovations and solution systems. In their recently organized event “BLISS: Transforming Together”, the company's CEO, Ms. Heike Van De Kherkof, shared Archroma's vision of zero discharge, stepping away from landfills and no carbon footprint as “big investments we have to make” for a sustainable future. The company's India Cluster Head, Mr. Anjani Prasad shared that 71 percent of India's paper production comes from recycled fiber.
Global specialty chemicals company
Archroma organized the event “BLISS: Transforming Together” in Delhi on 9th January, 2023. The event showcased Archroma's best-in-class, sustainable solutions for textiles, paper and packaging industries and was joined by over 150 participants from the textile, paper and packaging industry.
Archroma's CEO, HeikeVan De Kherkof shared a keynote presentation and Archroma's India Cluster Head, Mr. Anjani Prasad also addressed the event. Through her presentation, Ms. Kherkof outlined the history of Archroma, sharing the company's journey of leading through mergers and acquisitions to solidify their position as leaders in the industry. The event focused on the need of the industry to become more environmentally aware and emphasized on
the importance of sustainability. “We would like to transform the paper packaging industry towards a more sustainable industry,” she said. She added that though it is an ambitious goal, it can be achieved through the industry coming together.
Ms. Kherkof spoke about the various technologies developed by Archroma, dedicated to the sustainability cause and reducing carbon footprint. A major technology that has recently been introduced to the paper industry is the Archroma ONE WAY Impact Calculator. This is a calculation tool used by Archroma's experts to provide the customers and partners with an accurate estimate of the process costs, resource utilization, effluent discharge quality, and CO emissions of 2 the existing production process and of the newly evaluated system. The
Archroma ONE WAY Impact
Calculator can be used to extract data at each step of the textile manufacturing chain: sizing, pretreatment, dyeing, printing and finishing, thus helping to validate the applicable Archroma system or solution.
Head of India Cluster, Mr. Anjani Prasad shared some figures and insights based on the Indian market. He shares that out of the total paper production, 21 percent is coming from wood and 71 percent is coming from recycled fiber, which is a good figure. Mr. Prasad also stated that among the human population of approximately 8 billion people, 6 billion of the population is between Asia and Africa. Therefore he states that the manufacturing and whole industry value chain has to be linked here, to eradicate the problem of carbon footprint.
Indian Packaging industry’s CAGR for 2022-2026 is projected at 9-11 percent. Andhra Paper Limited has ambitions to reap relevant benefits. The Board has approved an investment of INR 2,000 crore to acquire paper board machinery of 1,75,000 TPA production capacity.The production capacity of pulp and paper board shall increase by 2,21,000 TPA and 1,56,000 TPA respectively. The proposed project is expected to finishby2025ifallauthorizedclearancesfollow.
On January 31, 2023, Andhra Paper Limited’s Board of
Directors approved the Green Field Project for expanding the production capacity of their pulping and paperboard manufacturing at their Kadiyam unit.
The proposal presented suggested acquiring additional paper board machinery (KA#4) of 1,75,000 TPA to increase the production capacity of the company. The company intends to increase its production capacity by 2,21,000 TPA pulp and 1,56,000 TPA paper board production. Currently, the company has 87,000 TPA production capacity (at 95% utilization). The new investment is expected to cost the company approximately INR 2,000 crore.
According to Mordor Intelligence’s report, the Indian packaging industry is slated to grow at a CAGR of 12.60 percent for the 2022-2027 period. Andhra Paper Limited seeks to make the most of the ongoing industrial growth trend. Along with the clearances and further project execution, the company could start the proposed production by 2025.
In line with Section 30(4) of SEBI regulations, the company released a press statement immediately after the proposal
was accepted by the Board in the meeting. The project can only be heralded with the final approval of the company’s Board, which is subject to various government clearances, such as the environmental clearance of the Ministry of Environment & Forest for Climate Change.
Andhra Pradesh’s SIPB meeting was held on February 7, 2023, under the supervision of Mr. Y.S. Jagan Mohan Reddy, State Chief Minister. The committee approved proposals amounting to over INR 1,44,000 crore for establishing heavy industries in the state. Andhra Paper’s proposal is also among them. As per the reports, SIPM has granted the company to make an investment of up to INR 3,400 crore to execute the proposal.
UPM has adopted a new streamwater programme, as a
part of its biodiversity projects, to release or restore 500 kilometers of streamwater by 2030, integrated along with the organization's migratory fish programme, launched in 2016. The programme will remove migratory barriers, such as defunct dams, and replace old culverts with new ones to restore rapids and streams to their natural state. This includes 5,000 structures that have been identified as dams along the river routes, approximately 220 hydropower plants and connected dams, and around 30 percent of approximately 90,000 road culverts.
Already, two projects, namely the Sapsokoski and Arvajankoski rapids of the programme were completed, in the Autumn of 2022. The old dams were dismantled, and the
rapids were restored, freeing up the stream water routes and offering new spawning areas for migratory fish.
The primary restoration sites have been identified in areas owned by UPM or close to UPM's hydropower plants. The programme will help boost Finland's inland waters biodiversity which includes 5 percent of threatened species.
Mar17, 2023
rient Paper and Industries announced that its board has approved a capital expenditure of INR 475 crore. The capex will be used in modernisation of its manufacturing facility at Amlai in Madhya Pradesh. The company in a regulatory filing at exchanges has said, "The Board of Directors of the Company at its meeting held
Otoday, inter alia, approved the capital expenditure of INR 475 crores for modernisation of its manufacturing facility at Amlai, Madha Pradesh. The project will improve operating capacity of the paper mill to 400 tonnes per day and is likely to be completed in 24 months.”
Earlier during an interview given to Paper Mart in 2022, Mr. Ashwin J. Laddha, Managing Director & CEO of Orient Paper & Industries Limited informed that,“we are looking at debottlenecking our capacity and our second step would be to gain more depth and expand the capacities in that space.”
The 172,000 TPA PM5 at JK Paper Limited's Fort Songadh Mill had a fast and smooth start-up in August 2021. JK Paper and Valmet are Partnering for creating a global benchmarkonthismachine.
Mar 15, 2023
The Valmet delivered PM5 at JK Paper Limited's Fort
Songadh Mill in India started up in August 2021. The start-up was successful, fast and smooth, and good operation close to the guaranteed production levels was achieved right in the beginning.
“This machine has been designed for a capacity of 172,000 TPA. Valmet has been supporting us well since the start-up. JK Paper is now looking forward to further optimizing the process conditions and auxiliary systems in terms of energy and capacity which were not part of Valmet delivery scope, to make the machine as one of the global benchmarks. Given the fact that it is a multi-supplier set-up, Valmet has been relentlessly supporting us in all the aspects irrespective of the scope of supplied items,”says Mr. PK Suri, JK Paper Limited. In order to further enhance the production to maximum potential, JK Paper has signed a Performance Agreement with Valmet for the PM5 machine. The agreement period is 6 months and will commence on March 1, 2023.
The target of the agreement is to utilize in cooperation Valmet's know-how and expertise to achieve trouble free operations and further improve machine efficiency. The defined KPIs are aimed to be achieved through necessary modifications / upgrades of the auxiliary systems and optimizing process parameters.
We are pleased with the cooperation with Valmet and support so far and would like to take the relationship to the next level to become a global benchmark,”says Mr. Piyush Kumar Mittal, Chief General Manager, JK Paper Limited.
“This is a good example of moving our customers
performance forward with improved operation efficiency and less resources which is in line with Valmet's Climate Program. This partnering approach is the best solution in terms of achieving desired results consistently and right Capex planning,”says Mr. Varun Jain, Director, India Region, Asia Pacific, Valmet.
A project team has been nominated to guide and monitor development, take development actions and give recommendations at the machine line.
Scope of Valmet's delivery in 2021: Valmet's delivery included the coated board machine from the headboxes to reel with air dryers, chemical systems, heat recovery and other board making systems. The coating is applied in multiple coating stations including a technologically advanced Opti Coat Layer coating station, which applies two coating layers simultaneously. The delivery also included a mill wide Valmet DNA Distributed Control System with all the controls in one platform for ease access of data as well as Valmet Performance Center services.
The investment will increase Orient's operating capacity to 400 TPD, which is expectedtobecompletedin24months
Kuantum Papers Limited has contracted BTG Group, a unit of Voith, for the integration of DataPARC, a data visualization and management software, to streamlinethevariousoperationalunitsacrossthemill'ssite.
Mar 9, 2023
Kuantum Papers Limited, India, and BTG have partnered
for a new project, namely Neev, to integrate the latter's data visualization and management software, namely DataPARC, to streamline the mill's various unit operations across the site for advanced control, better quality, and optimized costs. The user-friendly software will enable historizing and retrieval of data from multiple data sources as well as visualizing critical information in real-time. Software features and functionalities include dashboards, center lining, statistical tools, downtime analysis, consumption reporting, and smart alarms among many others.
”We are very excited to embark on our digitalization journey with BTG who are the industry leaders in this domain. In this dynamic business environment, as we scale up our operations, it is imperative that we leverage the data that is being generated and use it to make decisions that will enhance our quality, boost efficiency and drive sustainable business growth. Our objective behind“Project Neev”is to empower operators with a data driven decision support system backed by detailed analytics. I truly believe that we are stepping into an era of digital transformation and this collaboration with BTG will help Kuantum achieve greater heights.”Mr. Pavan Khaitan, Managing Director of Kuantum Papers Limited.
“Kuantum is a front runner in embracing new technology and
a thought leader in the Indian Pulp & Paper industry. BTG is honored to partner with Kuantum Papers to provide a cutting-edge digital solution to improve their operations and bottom-line performance. The investments they are making in this space combined with our broad capabilities will provide the opportunity for continuous improvement and mutual profitable growth for both organizations for many years to come”, says Mr. Akhlesh Mathur, Head of Business South Asia & Southeast Asia for BTG group.
ABB robots will help Parason to increase equipment effectiveness by 30%. Parason is working for the new sustainable packaging made from agro-waste to help reduce relianceonsingle-useplastics.
Mar 23, 2023
arason, one of the largest manufacturers & suppliers of Ppulp and paper machinery has collaborated with ABB in India to automate and up-scale production of sustainable and compostable packaging solutions. The collaboration has been established to help Parason's customers reduce their reliance on single-use plastics and Styrofoam packaging. These molded fiber tableware products are widely used across multiple industries across restaurants and cafes, food catering, transport, travel and industry canteens.
ABB robots, integrated with Parason's machinery, will help to facilitate the effective manufacturing of agro-waste products - creating 100 percent eco-friendly compostable packaging solutions. ABB initially deployed 10 robots at Parason's five forming machine cell and added another 20 robots at the end of last year.
“The 3.5 million tons of plastic waste generated in India per annum creates various hazards, which is why India has initiated a nationwide ban on single-use plastic,”said Mr. Subrata Karmakar, Country President for Robotics & Discrete
Automation Business at ABB India. “ABB's innovative robotic solutions, combined with Parason's revolutionary turn-key manufacturing process using agro-waste, will be a key contributor to addressing climate change by adopting a 100% compostable alternative to plastics.”
Compared to manual pick-and-place applications, ABB robots
will help increase OEE (Overall Equipment Effectiveness) performance by 30 percent, while eliminating ergonomic risks for the workforce, and improving overall health and safety. The shift to ABB's robotic solutions has also enabled the business to divert the workforce to more meaningful, interesting and rewarding tasks.
“Every year India generates about 500 million tonnes of farm waste which can now be used to create sustainable packaging solutions. ABB's automated solutions have helped us create a viable, cost-effective value chain and maintain a low carbon environment,”said Mr. Madhure Desarda, Director of Operations, Parason Group. “This year, Parason intends to deploy 250 forming machine cells, which have the capacity to replace 150 tonnes of single-use plastic per day.”
Developing the latest innovative, digital and AI learning technologies for smarter robotics, ABB is helping businesses like Parason operate more sustainably and become more flexible, efficient and resilient all around the world.
Compostable packaging industry pioneer Yash Pakka Limited (YPL) has kickstarted the development of its first overseas plant in the Central American country Guatemala. The company has signed a MoU with the country's major sugar companies to procure bagasse, which is the primary raw material used by the company for its products. Expected to be operational by mid-2025 with a production capacity of 400 tonnes per day, the new plant will produce flexible packaging and mouldedfibreproductsasitsprimaryofferings.
Apr 11, 2023
Yash Pakka Limited (YPL) has kickstarted the development
of its first overseas plant in the Central American country Guatemala. As the first big step in this direction, Pakka has signed a MoU with the country's major sugar companies to procure sugarcane residue, also known as bagasse, which is the primary raw material used by the company for its products. The new plant at Guatemala will produce flexible packaging and moulded fibre products as its primary offerings and is expected to be the world's largest compostable flexible packaging and moulded fibre facility. The primary market that the company is willing to cater to is North America. The company chose Guatemala due to the widespread availability of sugarcane in the country, as well as the positive response they received from Guatemala authorities and sugar companies. The upcoming plant is expected to be operational by mid-2025 with a production capacity of 400 tonnes per day.
Ved Krishna, Strategy Lead,Yash Pakka Ltd., said,“We are delighted to partner with the Guatemalan sugar industry to start the process of setting up the world's largest compostable packaging and moulded fibre facility. The idea is to work towards developing better bio-materials for food packaging and service "
Billerud has successfully got the nod of Michigan's state legislation for investment support of a maximum of USD 200 million against USD 1 billion investment. The companyisplanningtoexpanditsEscanabaMillintoapaperboardproductionfacility.
Feb 24, 2023
illerud's expansion plans have been approved for investment support of USD 200 million, in an assumption of USD 1 billion investments, as signed by Mr. Gretchen Whitmer, Governor of Michigan, under the Michigan Economic Development Corporation's (MEDC) appropriation of the funds. This funding follows additional incentives recently approved by the State of Michigan Administrative Board, including approval of the Forest Products Processing Renaissance Zone, which exempts the company from paying almost all state and local property taxes at the Escanaba Mill. The company is planning to transform Escanaba Mill, as a part of its North American, which is one of the largest and growing markets in primary fiber premium carton board,
Bexpansion plans, into a world-class paperboard production facility. Currently, a pre-feasibility study about the mill's conversion into a paperboard production unit is in process and is expected to be completed in the first half of 2023, after which the company's Board of Directors can make an investment decision.
The final government support amount shall be proportionate to the company's actual investment, subject to the execution of the necessary agreements between the Michigan Strategic Fund (MSF) and Billerud U.S. Production Holdings LLC.
Billerud provides paper and packaging materials that challenge conventional packaging for a sustainable future. The company has nine production units in Sweden, the USA, and Finland, offices in over 13 countries, and a wide customer base in over 100 countries. It is also listed on Nasdaq Stockholm.
Norske Skog Skogn, Norway, will invest USD 17.5 million, in addition to USD 3.8-4.8 million from NOx fund, to acquire a new Thermomechanical Production (TMP) line, which will increase the mill's thermomechanical wood pulp production capacity by 100,000TPA,replacingexpensiverecycledpaperwithfreshfibre.
Feb 24, 2023
Norske Skog Skogn will invest about USD 17.5 million
above USD 3.8-4.8 million sourced from NOx funding to acquire a new thermomechanical production line (TMP) to replace expensive recycled paper with fresh fibre. The replacement will increase the production capacity by 100,000 TPA.
Håvard Busklein, Managing Director of Norske Skog Skogn, shared the company's plan to secure its position in the newsprint market and seek opportunities to explore new markets. To reduce investment costs and CO₂ emissions during purchase, the new machinery will be bought from a closed Sweden paper mill.
The line is expected to become operational in the first half of 2024. The new TMP line is expected to reduce variable costs by significantly reducing NOx and fossil CO₂ emissions, and landfilled waste. The investment will significantly reduce the company's fossil CO₂, by 80 percent, NOx, by 40 percent, and
ash, by 60% emissions. Ash from fresh fiber has smaller amounts of residual materials and several application opportunities, which shall be investigated.
The Norske Skog Group, Norway, a world-leading producer of publication papers, operates four mills in Europe, two of which will produce recycled packaging paper following ongoing conversion projects, and one paper mill in Australia. The group aims to further diversify its operations and continue its transformation into a growing and high-margin business through a range of promising energy and bioproduct development projects and is listed on Oslo Stock Exchange under the ticker NSKOG.
Arauco Paper Mill, Chile, with a pulp production capacity of 2,100,000 TPA has becomeoperationalasitproduceditsfirstbaleofpulponJanuary20,2023.
Feb 24, 2023
rauco Paper Mill, Biobío region, Chile, produced its first bale of pulp on January 20, 2023, after the process of feeding and loading wood chips into the digester of Line 3 began on December 29, 2023. The operational line has elevated Arauco mill's pulp production capacity to 2,100,000 TPA.
The construction of the paper mill's new production line, which started in December 2019, was undertaken under the Arauco MAPA project, which included improvements in Line 2 and the acquisition of new Line 3.
AValmet, a developer, and supplier of technologies, automation systems, and services for the pulp, paper, and energy industries, played a key role in the development of the MAPA project by supplying the pulp drying line, characterized by its low energy consumption, the recovery boiler, whose high power output allows for maximum energy efficiency, and the power boiler, which provides renewable energy to the entire plant, which has subsequently become operational as well.
The company is also providing a comprehensive Industrial Internet services agreement comprising the use of plantwide optimization applications, advanced prediction, and monitoring applications, as well as expert services.
DS Smith, an Italian paper and packaging solutions provider, has contractedValmet to deliver a new 450,000 TPA containerboard machine for its Porcari (Lucca), Italy site. The BM 3 liner will produce recycled liner grades ranging from 70-135 gsm at a productionspeedof1,500m/min.
Mar 27, 2023
DS Smith Paper Italia S.r.l has contracted Valmet to supply a new containerboard machine of 450,000 TPA production capacity, with extensive packages of automation, services, and industrial internet applications, for its Porcari (Lucca) site in Italy. The deal is among Valmet's Q4FY22 orders and its start-up is scheduled for the middle of 2025.
The delivery will include a recycled liner board-making line, inclusive of broke collection, reel and winder, and board machine process ventilation systems. The 8,600 mm wide (wire) BM 3 will produce recycled liner grades with a basis weight range of 70–135 gsm at a production speed of 1,500 m/min and a mechanical design speed of 1,700m/min.
The wide automation package includes a Valmet DNA automation system for process and machine controls, runnability and condition monitoring, and a Valmet IQ quality management system. A comprehensive Valmet Industrial Internet package including Valmet Performance Center services, advanced monitoring, and predictive applications as well as training simulators will also be delivered, along with Valmet Paper Machine Clothing, spare parts, and consumables packages.
Mr. Niels Flierman, Head of Paper & Recycling at DS Smith,
commented on the purchase,“We are pleased to be working with Valmet to install a new machine at our Porcari plant. Not only will the machine help us meet the demand for sustainable packaging innovation in Italy, but it will also help us to increase the plant's environmental performance by reducing CO₂ emissions and specific water use per ton of paper produced.”
Mr. Kari Räisänen, Sales Director, Board and Paper Mills, Paper business line, Valmet, further revealed about the deal, "Driven by increased demand for sustainable packaging solutions, the containerboard market is growing fast. Valmet as a market leader in innovative board-making technologies has developed a number of sustainable solutions to meet the market needs. Our unique offering together with the production potential of the containerboard machine were the decisive factors for DS Smith.”
Stora Enso contracts Valmet as a part of its EUR 1 billion investment for its Oulu, Finland, paper mill's upgrade, to deliver bleached Chemi-ThermoMechanical pulp (BCTMP), evaporation plant, non-condensable gas (NCG) technology, and automatedsolutions.
Feb 24, 2023
tora Enso has contracted Valmet to deliver bleached ChemiThermoMechanical pulp (BCTMP), evaporation, and noncondensable gas (NCG) technology as well as an extensive automation solutions package, under its approximately EUR 1 billion investment for conversion of an idle paper machine into high-volume consumer board production line, to its Oulu, Finland, paper mill.
Valmet's technology delivery includes a BCTMP line, featuring low operating costs, high process flexibility, and reliability with excellent pulp quality, and high bulk for board production, an evaporation plant, tailored for BCTMP filtrate recovery,
Sincluding a Valmet Mechanical Vapor Recompression (MVR) Evaporator and the mechanically reliable Tube Evaporation technology, with high energy efficiency, and low electricity and steam consumption, and an NCG boiler designed for very low NOx emissions and odorous gas handling. The delivery is supported by Valmet Industrial Internet solutions including connectivity and process support with analytics tools, including mill-wide Valmet DNA distributed control system with the new web-based user interface as well as an integrated Valmet IQ Machine Vision system.
Valmet will also deliver a rebuilt recovery boiler, including an electrostatic precipitator upgrade, for the site.
The order, with an estimated delivery value of EUR 75-100 million, is among Valmet's orders for the fourth quarter of 2022 and shall be delivered in phases leading to the mill becoming operational in early 2025.
GraphicPackagingInternationalwillinvestUSD1billiontobuildapapermillinWaco, Texas.Themillwillhousemanufacturingunits,housingaCoatedRecycledPaperboard machine,alongwithwarehousingunitsspreadingovera6,40,000squarefeetarea.
Feb 23, 2023
Graphic Packaging International shall build a new 119-
acre facility in Texas Central Park, Waco’s largest industrial park, at an investment of USD 1 billion to house its new state-of-the-art Coated Recycled Paperboard (CRB) machine. The campus’s manufacturing and warehousing units shall spread over 6,40,000 square feet.
The mill shall help the company to increase the production capacity for recycled fiber-based packaging products and opportune the increasing global demand, commercial and consumer.
The mill shall be built on a strategic collaboration between Graphic Packaging, the City of Waco, McLennan County, the Waco Industrial Foundation, and the Greater Waco Chamber.
Mr. Michael Doss, CEO of Graphic Packaging, defined Waco and McLennan County as regions of strategic, economic, and communal importance.
Mr. Dillon Meek, Mayor of Waco, expressed his gratitude
towards the company for providing support and inclusion to the local community through workforce development, the mill shall add 230 jobs, and long-range infrastructure plans.
Graphic Packaging, based in Atlanta, manufactures fiberbased consumer packaging solutions for end consumers as well as businesses.
UPM's Paso de los Toros, Uruguay, pulp mill has reached technical readiness to start operations. The new pulp mill is a part of the company's USD 3.47 billion investment projectinUruguay,andhasaproductioncapacityof2.1millionTPA.
Mar 31, 2023
UPM's new Uruguay pulp mill, which is a part of USD 3.47
billion investment project, has received the environmental authorities' acceptance of all the procedures, systems and technologies and has reached the technical readiness to start operations.
The new Paso de los Toros mill will produce 2.1 million TPA of eucalyptus pulp, and is expected to have a cash cost level of approximately USD 280 per delivered tonne of pulp. puts us among the leading pulp suppliers in the world. The environmental approval precedes the final operating authorization, which is expected to be received in a few weeks and the mill will start its first customer deliveries within the first month following the start-up.
The overall investment of USD 3.47 billion includes a deep sea-port terminal in Montevideo, a new eucalyptus tree nursery, and local investments in infrastructure and facilities. All of these are already completed and in operation.
Mr. Jussi Pesonen, CEO and President, commented on the start-up, “The finalization of UPM Paso de los Toros completes our transformative growth investment in Uruguay. Over the years, UPM has created a highly competitive industrial platform with sustainable, secure wood-supply and efficient
logistics in Uruguay. This offers a competitive and secure pulp supply to new and existing customers and helps meet the growing need for renewable materials. With an over 50 percent increase in UPM's current pulp capacity, this investment creates a step change in the scale of our pulp business and UPM's future earnings. It also has a significant impact on Uruguay's economy and creates significant opportunities for the people and communities.”
Post the set-up, UPM will have two pulp mills in Uruguay and three pulp mills in Finland, which helps the company offer sustainable hardwood and softwood pulp to its customers, globally. The mill will also contribute to socio-economic upgrade of Uruguay, inducing an approximate 2 percent increase in national GDP.
Stora Enso has contracted with Voith, a leading line producer, to transform its Oulu, Finland, site's paper machine. Post-transformation the line will have the highest production capacity in Europe for high-quality folding boxboard and CKB at 750,000TPA.
Feb 24, 2023
Stora Enso has contracted Voith to transform its Oulu, Finland, site's paper machine, used to produce coated graphic papers, into Europe's largest manufacturing unit
for high-quality folding boxboard and coated kraft back (CKB) at a production capacity of 750,000 TPA. Post-transformation the line shall be the highest production capacity unit in Europe for high-quality packaging made of folding boxboard and CKB. The transformed machine shall become operational in early 2025.
To achieve the transformation goals, Voith and Stora Enso have developed a tailor-made concept to maximize
efficiency and sustainability along the entire line. The supply scope shall include a new, three-layer wire section with the DuoFormer D II and a high-performance Triple NipcoFlex shoe press concept will be added for maximum production output at the highest quality level. The machine will also feature a SpeedSizer system and four DynaCoat AT coating units, which are partly made of carbon fiber to ensure stable cross sections at all grades and speeds, with JetFlow F applicators for maximum flexibility. In addition, Voith's bulk-saving EcoCal HiBulk calender will provide excellent stiffness, outstanding smoothness, and printability.
Stora Enso has specially requested Voith's leading digitalization and automation expertise, hence the OnControl, Machine MCS for the automation of the board machine, the OnQuality quality control system, and the
OnCare.Health condition monitoring solution shall be integrated into the line controls. The dataPARC cloud will serve as the IIoT platform.
Stora Enso's transformation requirements included optimal production efficiency along with the achievement of the highest environmental standards, especially excellent heat recovery.
For ideal energy efficiency, the existing dryer section shall be rebuilt and the high operating dew point of up to 65°C in the EcoHood 65 dryer hood will help lower the supply and exhaust air volumes, thus reducing power and steam consumption. The CombiDuoRun drying concept will efficiently dry the web on both sides, preventing curl even at high operating speeds. Finally, two VariFlex Performance winders will be installed.
SCA has invested about USD 139 million to set up a new CTMP pulp manufacturing unit in Sweden. The new plant will triple the production capacity of the company to 300,000 TPA and will replace the operations of Ostrand pulp mill. The Ostrand mill will focus on manufacturing of sulphate pulp, for which its current production capacityis900,000TPA.
Apr 4, 2023
CA has invested close to USD 139 million to set up a new manufacturing plant of CTMP pulp (chemical thermomechanical paper pulp) to triple its capacity from 100,000 TPA to 300,000 TPA. The plant was commissioned at the end of 2022. CTMP is a tailored, bulky pulp that can be used for everything from cardboard to kitchen roll, wherein cardboard is its largest application, with end-products including electronics packaging and juice cartons.
Ms. Kristina Enander, Director, SCA Pulp, described, “We see demand for CTMP increasing globally and there are several reasons for that. Firstly, CTMP is a cost-effective alternative; it also offers quality advantages. In addition, sustainability is becoming increasingly important to consumers, so interest in climate-smart products is growing. Now our customers can manufacture more climate-smart products, which replace products made from fossil-based materials.”
The company will wind down its existing Östrand pulp factory in Timrå once the operations at the Ortviken
Sindustrial site in Sundsvall come fully online. Ms. Enander explained, “We plan to focus entirely on the production of sulphate pulp at Östrand. Just like CTMP, sulphate pulp is an important plastic substitute, especially for packaging. Moving production of CTMP to Ortviken opens up opportunities for the further expansion of sulphate pulp production at Östrand.”Currently, the facility has a capacity of 900,000 TPA for sulphate pulp.
As the production of sustainable materials at Östrand has grown, the plant has been able to increase its deliveries of other climate-smart products, such as green electricity and district heating. Excess heat from pulp production at Östrand also becomes district heating, which supplies the entire local municipality's district heating network. A large proportion of the heat also goes to the Sundsvall grid, for which Ortviken also provides a large share of bio-based district heating.
SCA also sells a growing number of green products that are extracted as by-products from pulp production at Östrand, mainly tall oil and turpentine. Tall oil is a renewable raw material for biodiesel, while turpentine is used in the manufacture of cosmetics and as an additive in paint, for example.
MetsaTissue's Mariestad paper mill gets an investment of EUR 370 million to expand its production capacity and recruit state-of-the-art technology. This includes acquiringamoderntissuepapermachinewitha70,000TPAproductioncapacity.The overall production capacity is expected to double to 145,000 TPA. Meanwhile, fresh fibershareshallincreaseto80%.
Feb 10, 2023
Metsa Tissue has approved an investment of
approximately EUR 370 million to expand the production capacity and upgrade the current technology of Mariestad's tissue paper mill. The expansion shall improve the dependency of the Scandinavian market on imports. The renovated mill shall house a new tissue paper machine powered with modern technology and a production capacity of 70,000 TPA. The overall production capacity shall increase to 145,000 TPA. Three new converting lines shall be added for rolled and folded tissues. It will have an automated warehouse for handling both raw materials and finished goods. A new office facility shall also be developed. The expansion process shall start in spring 2023 and conclude by mid-2025. The operations shall begin in the second half of 2025.
The addition of modern technology shall result in various positive environmental changes and the mill will be able to increase its fresh fiber share to 80%. According to the expansion design, the mill's fossil CO₂ emissions will drop to zero by 2030. The upgraded water circulation and purification
processes shall reduce the mill's water consumption by 50% to 10 tonnes per cubic meter and foul odor emissions. New embankments between the residential area and mill and 26 silencers will bring the noise levels down by 3-5 dBA.
Metsa Tissue is a subsidiary of Metsa Group. The company operates eight paper mills in the Scandinavian region. Mariestad's paper mill, built in 1765, was acquired by the company in 1989. It produces Lambi, Serla, and Katrin tissue products, leading brands in the Nordic region, for professional and consumer use.
Essity has successfully achieved a CO2 emission-free tissue production process at its German mill by replacing natural gas with renewable hydrogen for the paper drying process.The152,000TPAcapacitymillisthefirstintheindustrytoachievethisfeat.
Mar 10, 2023
ssity uses renewable hydrogen at its Mainz-Kostheim, Germany, tissue production mill, becoming the first mill in the industry to engage in the CO₂ emission-free production process.
The German mill used natural gas in the paper drying process to achieve the required high temperature of 600 degrees Celsius to produce 152,000 TPA of high-quality tissue. In 2021, a pilot project was initiated encompassing efficiency programs and electrification through renewable energy. To
achieve the said goals, renewable hydrogen was used to replace natural gas in the hood dryer as a final building block.
EThe mill uses sustainable and cyclical processes to transform recycled paper into high-quality tissue, marketed under the company's Tork brand and aims to achieve net-zero emissions by 2050.
Essity, headquartered in Stockholm, Sweden, is a leading global hygiene and health company with a consumer base in approximately 150 countries under the leading global brands TENA and Tork, and other strong brands, such as Actimove, JOBST, Knix, Leukoplast, Libero, Libresse, Lotus, Modibodi, Nosotras, Saba, Tempo, TOM Organic, Vinda, and Zewa.
International Paper, celebrating its 125th anniversary, rolled out the company's rebranding project in March 2023, along with a new corporate website which is supposed as a one-stop shop for the stakeholders to keep a tab on the company's variousproductsandinitiatives.
Mar 9, 2023
International Paper, which is celebrating its 125th
anniversary this year, has announced a new corporate website along with the company's rebranding. The new branding was rolled out globally at the beginning of March 2023, including the updated website and logo.
The website, launched last week, has been developed as a one-stop shop for stakeholders to see the company's commitment to being among the most successful, sustainable, and responsible companies in the world. Meanwhile, the rebranding highlights the resilience of IP, the sustainability of its mission, and its commitment to creating what's next, and is rooted in the company's legacy of safety, ethics, and stewardship. It embodies a renewed sense of purpose, energy, and optimism, and marks another major milestone in the evolution of International Paper.
Mark Sutton, Chairman and CEO, shared that rebranding will help the company to direct its efforts toward current needs for renewable, fiber-based packaging and pulp while
sharpening our focus on the future.
IP, headquartered in Memphis, Tennessee, is a global producer of planet-friendly packaging, pulp, and other fiberbased products, and one of North America's largest recyclers. The company has a global customer base with manufacturing operations in North America, Latin America, North Africa, and Europe. It is listed on NYSE under the ticker of IP and recorded net sales of USD 21.2 billion in FY22.
Line O Matic celebrated its silver jubilee by launching an online shopping portal for its export division and made the day a major milestone in the company's history.The company has a global presence in over 80 countries, with over 3000 machines deliveredforpaperindustrysolutions.
Feb 27, 2023
r. Nirav Parikh, General Manager of Line O Matic, a well-known brand in paper stationery machinery, paper converting machinery, packaging machinery, etc., launched an online shopping portal for the company's export division on the occasion of its Silver Jubliee celebration, marking its 25th year in the industry, in Ahmedabad.
Mr. Swapnil Patel, Executive Management, highlighted the statistics of company's successful journey in carving a place in the paper industry by delivering over 3000 machines, functionally installed, worldwide. He shared the company's
Mfootprint in India, in 25 states and 5 union territories, and in more than 80 countries across the globe. He also expresses gratitude to the contributors of company for their 100 percent efforts.
Mr. Bhupendra Patel, Chief Minister of Gujarat, applauded Line O Matic for its crucial contribution, through machinery and services, to the paper industry, Indian economy, and education sector. Mr. Uday Patel, Founder Owner, reminisced the company's journey in the paper and packaging industry, and initiated efforts and impact in the Indian economy and education sector, and end-lined his speech with a promise of expansion through consistent and quality efforts. The event was attended by over 1000 invitees, including clients, associates, vendors, employees, and family members.
EssityandVoithhavecometogethertodevelopasustainableCO2-neutralizedtissueproduction process. The process will reduce the freshwater consumption requirementby95percentandenergyconsumptionby40percent.
Mar 23, 2023
Essity has contracted Voith to co-develop a new
sustainable tissue-making process. The new disruptive concept will revolutionize and rethink tissue manufacturing, in comparison to conventional paper-making processes, by enabling CO₂- neutral tissue production and reducing freshwater consumption by 95 percent, and energy consumption by up to 40 percent.
The initiative incorporates Essity's extensive expertise in the tissue industry and Voith's know-how as the leading technology supplier. Successful test runs have already taken place on a laboratory scale, and the concept is now being transferred to a dynamic process. A pilot phase will be launched later this year before being implemented industrially.
“Sustainability is integrated into Essity's strategy for longterm profitable growth. We are committed to reducing our environmental footprint and achieving net zero emissions by 2050. The partnership with Voith is yet another concrete example of this,”says Mr. Magnus Groth, President and CEO of Essity. A few weeks ago, Essity became the first company in the industry to produce tissue in a CO₂ -free production
process using renewable hydrogen, and one and a half years earlier, it managed to produce high-quality tissue from agricultural waste.
Mr. Andreas Endters, President & CEO of Voith Paper, further commented, “The fact that we have developed this new process is an important milestone in the industry and demonstrates our high level of innovation. We are very pleased to have found a suitable partner in Essity, who shares our objective of climate-neutral paper production.
IPhasagreedtosell50percentofitsownershipinterestsinILIMSA,Russia,theholding companyofitsIlimjointventure,toitsjointventurepartnersforUSD484million.
includes USD 2.45 billion of net debt.
Feb 24, 2023
International Paper (IP) has entered into an agreement to
sell its 50 percent interest in Ilim SA, Russia, the holding company for its Ilim joint venture (JV), to its JV partners for USD 484 million equity value, subject to regulatory approvals in Russia. This transaction indicates USD 3.5 billion in total enterprise value (TEV) for Ilim based on a 3.1x EBITDA multiple on 2022 full-year results, that is USD 1.11 billion EBITDA (unaudited). The FY22 year-end unaudited TEV of Ilim
The company received an indication of interest from its JV partners to purchase all of the company's shares, that is a stake of 2.39% stake, in JSC Ilim Group for USD 24 million, subject to certain terms and conditions. The company intends to pursue an agreement to sell the JSC Ilim Group shares and divest other non-material residual interests associated with Ilim, to its JV partners.
IP, Memphis, Tennessee, is a leading global supplier of renewable fiber-based products, such as corrugated packaging products, and pulp for diapers, tissue, and other personal care products, with manufacturing operations in North America, Latin America, North Africa, and Europe. It is listed on NYSE under the ticker of IP.
Ilim Group has planned a three-fold supply increase, from 5 percent to 16 percent, for the southwest China region. The group's new 600,000 TPA capacity KLB mill in UstIlimsk will help the group to achieve its target. In extension of these plans, the group recently held a press-conference in Yunnan in collaboration with Chengdu Peibaobo PaperCo.
Mar 16, 2023
Ilim Group plans to increase its southwest China supply
three-fold from 5 percent to 16 percent by 2025, which is another 100 thousand tons of the finished products, which will make the company a key player in the regional pulp and paper market. The group's new pulp and paper mill (the KLB Mill) in Ust-Ilimsk will help in boosting the regional supply as its production capacity will amount to 600,000 TPA. Presently, Ilim will focus on implementing go-to-market strategy to introduce the mill products to the market.
Ilim Group recently held a conference in collaboration with Chengdu Peibaobo Paper Co. for existing and potential partners in Kunming, Yunnan province in collaboration with Chengdu Peibaobo Paper Co., including Yunnan Packaging Association and logistics companies. Chengdu Peibaobo Paper Co., one of the group's Chinese partners, is a large manufacturer of packaging and a service operator in China. In liaison with the company, Ilim plans to enter the market of Laos and supply packaging materials to the FMCG market.
Mr. Alexander Lykhin, Vice President and Head of the Representative Office of JSC Ilim Group in Asia, said, “We will deepen our cooperation with Chengdu Peibaobo Paper Co., seeking to render customized services to the consumers in the southwest of China, improve logistical itineraries and
enhance efficiency under the Belt and Road initiative. Apart from this, we are now working on deliveries to Southeast Asia through the China-Laos railway route.”
Mr. Wang Xiaoju, President of Chengdu Peibaobo Paper Co., further added “Potential area of cooperation between Chengdu Peibaobo Paper Co. and Ilim Group is to perform centralized purchasing, gain a competitive price and cut down logistics expenses through joined supply volumes.”
Toscotec will supply INDEVCO Group's UNIPAKHELLAS Pelasgia Greece Paper Mill with a complete packaging paper machine from Toscotec. The mill shall use the machinetoproducecontainerboardgradesfortheGreekandexportsmarket.
Feb 15, 2023
oscotec has been approached by UNIPAKHELLAS, a Tmember of INDEVCO Group to buy a complete paper production line, under a comprehensive service package contract including engineering, erection supervision, commissioning, training, and start-up assistance, for its UNIPAKHELLAS Central (UHC) mill in Pelasgia, Greece.
The new machine, with a wire width of 3,000 mm and a maximum operating speed of 800 m/min, will produce corrugated paper in the range of 90 to 200 gsm while processing 100% waste paper. It also features a two-layer Fourdrinier configuration with a hydraulic TT Headbox-SL along with Toscotec's shoe press, TT Xpress, TT SteelDryers, steam and condensate system, and stabilization boxes in the
dryer section. Other features include a hard nip calender, a hydraulic pope reel, and the tail threading system, complete with mechanical drives, an enclosed hood, and air and ventilation systems.
UNIPAKHELLAS S.A. is a part of INDEVCO Group and operates as an international company through its various facilities in Greece, including locations in Athens, Pelasgia, Thiva, Thessaloniki, and Crete. The company shall use the machine to produce high-quality containerboard grades for Greek and export markets, including European, and the Mediterranean.
The machine is slated to become operational soon, while Phoenix, INDEVCO's engineering company, will realize all the auxiliary plants.
Enrico Fazio, Sales Director of Toscotec P&B division, expressed elation at the opportunity to collaborate with INDEVCO Group and hope for future relations. The company has a proven history of engineering capabilities and successful complex installations.
ABB officially opened a global research and development (R&D) unit to drive technological advancements in the pulp and paper industry in Dundalk, Ireland.
ABB's investment in quality management solutions will continue to boost papermakers' quality and efficiency goals. The new R&D facility will provide innovation to help papermakers in areas such as waste reduction, reducing emissions,findingnewwaysofreachingsustainabilitygoals.
February 28, 2023
ABB officially opened a global research and development
(R&D) centre for the pulp and paper industry in Dundalk, Ireland. The new multi-million-dollar ABB Dundalk R&D Centre is at the heart of ABB's automation and digital offering for the sector and will be home to the ongoing evolution of the ABB Quality Control System (QCS). New ideas and products will be piloted and managed into the suite of applications for improved quality in the complex world of papermaking, where manufacturers often struggle to balance ever-changing variables to produce paper to customers' particular specifications. This will include solutions for measuring, adjusting, optimizing and controlling quality as the paper web makes its way through the paper machine to form the endproducts, including paper and board.
This project is supported by the Irish Government through IDA Ireland. The new R&D facility will provide an exciting space for innovation to help papermakers in areas such as waste reduction, reducing emissions including finding new ways of reaching sustainability goals. ABB's vision for the centre is to develop solutions that respond to global trends and can meet the sustainability goals of the rapidly evolving industry. A new QCS, for example, has the potential to reduce annual waste (production losses) by two percent or more per paper machine. This can impact a mill's sustainability goals by also reducing annual emissions for each machine by the same two percent, or 1.1 kt CO2, using the assumption of 57
kt CO2 emissions for a typical paper/board/tissue machine. The centre will take advantage of modern technologies such as additive manufacturing (3D printing), collaborative robots and Augmented/Virtual Reality for training and field service delivery to better meet the needs of ABB's pulp and paper development team. The site will also include a new training hub that will provide skills development support for ABB and customers alike, enabling more cross-industry partnerships and collaboration.
Dundalk is one of ABB's four main Pulp and Paper R&D centres globally, along with Bangalore, Singapore, and Stockholm. It will also serve as a sales and service office for ABB Robotics & Discrete Automation, who have had a presence in Ireland for 25 years. The facility will provide an excellent base from which to foster new ways of collaborating across business areas to better serve customers.
Domtar Corporation has announced its agreement to sell its Dryden pulp mill to First Quality Enterprises, who will retain all business operations of the mill in consistencywithDomtar'spractices.Thesaleisthedirectresultofadealbetweenthe Canadian Competition Bureau and Domtar, wherein bureau's consent for Domtar's acquisitionofResoluteForestProductsInc.wasconditionedonmill'ssale.
Feb 28, 2023
Domtar Corporation has signed an agreement to sell its
Dryden pulp mill to First Quality Enterprises. First Quality will continue the business operations of the mill in consistency with past practices, including retention and maintenance of employees and the surrounding community.
The agreement is an extension of Domtar and the Canadian Competition Bureau's agreement, wherein Domtar needs to sell its Dryden mill to acquire Resolute Forest Products Inc. Hence, the Dryden mill sale is subject to various regulatory conditions, such as approval of the Commissioner of Competition, and clearance under the Hart-Scott-Rodino Act.
The Resolute's acquisition will close in first-half of 2023, followed by Dryden mill's sale closing in early third quarter of 2023.
Domtar Corporation is a part of the Paper Excellence Group, and has contracted BMO Capital Markets to act as its
financial advisor. The transaction is backed by legal advisory as well, wherein Domtar, and McCarthy Tétrault LLP, and McMillan LLP are Domtar's advisors, and Wachtell, Lipton, Rosen & Katz, and Osler, Hoskin & Harcourt LLP are First Quality's.
Suzano Paper mill, Ribas do Rio Pardo, Brazil, is being supplied a SulfoLoop concentratedsulfuricacidplant,witha153TPDcapacity, byANDRITZ.
Feb 24, 2023
uzano Mill, Brazil, has contracted ANDRITZ to deliver a SulfoLoop concentrated sulfuric acid plant for its new pulp mill, which is under construction in Ribas do Rio Pardo, state of Mato Grosso do Sul, scheduled to become operational in the second half of 2024. The mill, on completion, shall be the world's largest plant with a single eucalyptus pulp production line.
Currently, ANDRITZ is in the process of supplying all pulp mill technology and process equipment for the new plant. SulfoLoop sulfuric acid plants are part of the company's CircleToZero initiative, which includes new technologies aimed at optimizing pulp mill side streams.
The sulfuric acid plant will have the capacity to produce 153
STPD, that is more that 97 percent, commercial grade sulfuric acid per day from the pulp mill's concentrated odorous gases and elemental sulfur, and shall make the mill completely selfsufficient in sulfuric acid and recycling sulfur from the waste streams. The ANDRITZ SulfoLoop solution is based on the Wet-gas Sulfuric Acid (WSA) technology for converting wet, sulfur-rich gases and elemental sulfur into sulfuric acid.
The sulfuric acid plant will help the mill to control the sodium and sulfur (Na/S) balance, the sulfide concentration, mill's resource efficiency, as less sulfate needs to be discharged, and reduce the truck transportation volume, as need for hazardous sulfuric acid transport will be eliminated. The sulfuric acid plant will meet the strict air emission limits and will bring a significant improvement to the overall footprint of the new Suzano paper mill.
International Paper will invest USD 103 million for the construction of two natural gas-based boilers in its Containerboard Mill in Cedar Rapids, Iowa. The boilers will replace the existing steam-based boiler of the company and will become operational in2025.
Feb 23, 2023
International Paper (IP) will invest approximately USD 103
million in its Containerboard Mill, Cedar Rapids, Iowa, to build and operate two natural gas power boilers for steam generation. The boilers will replace the mill's current coalbased steam generator resulting in the reduction of greenhouse gas emissions by 25 percent approximately. The construction shall start by the end of 2023 and boilers are expected to become operational by 2025.
Mr. Jay Royalty, Senior Vice President, Containerboard, IP, shared the company's Vision 2030 targets of reducing greenhouse gas emissions by 35 percent, as verified by the Science Based Target Initiative. 100 construction and seven additional mill jobs will be initiated by the project.
International Paper, Memphis, listed in NYSE as IP, is a leading global supplier of renewable fiber-based products, including corrugated packaging products that protect and promote goods, and enable worldwide commerce, and pulp for diapers, tissue, and other personal care products that promote health and wellness. The company has active manufacturing operations in North America, Latin America, North Africa, and Europe and its net sales in 2021 accounted for USD 19.4 billion.
Voith bought stakes inYangi, a Swedish sustainablestart-up, to invest in the dry pulp molding process, which is a sustainable alternative built by the latter to the wet pulp moldingprocess,andfurtherdecarbonizationinthepaperandpackagingindustry.
Feb 27, 2023
Voith, a leading full-line supplier, has acquired shares in
Yangi AB, Varberg, Sweden, as a result of an agreement signed in December 2022, to invest in sustainable technology of dry pulp molding process, which is a result of 10 years of R&D conducted by Yangi's sister company, The Loop Factory, to further drive decarbonization in the paper industry.
Yangi has developed a manufacturing process and is pioneering a new technology to produce 3D-formed, cellulosebased packaging The process is based on dry forming principles in one machine line and enables a cost- and resource-efficient solution, as it uses 75 percent less energy and emits similarly less CO₂ than wet pulp molding process, that has the potential to replace rigid plastic at scale. Yangi has also developed next-generation fiber-based solutions for the packaging industry, whose applications range from cosmetics and beauty products to fresh food, take-away, and consumer goods, which saves 75 percent of CO₂ emissions in comparison to petroleum-based packaging.
Recently, Chanel also acquired stakes in Yangi and is actively investing in the latter's business development.
The Loop Factory offers an open-source, turn-key machine platform and customized packages of value-added services such as material on subscription and ready-made design concepts, meeting the needs of manufacturers and brands for more sustainable packaging alternatives.
Resolute Forest Products has developed an innovative biomaterial, cellulose filaments (CF). The company has further partnered with FP Innovations, Performance BioFilaments, and Innofibre to develop a see-through CF-based film thatcanserveasareplacementforplasticpackaging.Thepartneredgroupislooking tocommercializetheCF-basedfilmandotherapplicationsofthebiomaterial.
package, that can be easily disposed of through a single-stream recycling collection system or a typical municipal composting infrastructure.
Mar 29, 2023
Resolute Forest Products Inc. is
focusing on bringing commercial volumes of its new cellulose filaments,
an innovative biomaterial, to the market through its almost complete Kénogami (Saguenay, Quebec) plant. The company is working closely with key partners Performance BioFilaments and FPInnovations, and the ministère des Ressources naturelles et des Forêts du Québec Wood Innovation Program, to commercialize a translucent film made of cellulose filaments (CF), a product that could potentially replace clear plastic films for various everyday applications, notably in store packaging of fresh foods.
The new CF-based film can be applied as a 100 percent biosourced package that can be easily disposed of through a single-stream recycling collection system or a typical municipal composting infrastructure.
Resolute, along with Innofibre and FPInnovations, has successfully produced pilot quantities of CF film, which have been successfully used in converting on commercial bag lines with potential customers. Resolute and Performance BioFilaments are now working with manufacturers of these novel films.
Mr. Alain Bourdages, Vice President of Innovation and Energy, commented, “Bio-based translucent film is another example of what our cellulose filament product platform can lead to. Improving the sustainability profile of packaging products is an exciting challenge, and we believe that we can be part of the solution. This development shows that wood-based products have a clear future.”
Valmet has introduced Mill-Wide Optimization in order to enhance overall pulp and paper mill profitability by making well-informed decisions across different process areas towards shared goals. The optimization observes the entire mill balance in real-time and considers both the current and future states of the mill. It also helps to uncover development opportunities required for moving towards fully optimized operations.
Mar 28, 2023
Industrial equipment supplier Valmet recently introduced Mill-Wide Optimization (MWO) to enhance overall pulp and paper mill profitability. With Valmet MWO, production teams can boost the mill's performance by making well-informed decisions across different process areas towards shared goals.
Valmet Mill-Wide Optimization will be introduced at Valmet
Customer Days in Copenhagen, Denmark, on March 29 to 31, 2023. The optimization observes the entire mill balance in real-time and considers both the current and future states of the mill. As a result, suboptimization of individual processes that do not align with mill goals can be avoided.MWO also provides the ability to balance environmental sustainability with production, quality, and cost. Valmet MWO reflects the mill's current state and maximizes production subject to
existing and projected bottlenecks, while stabilizing the process and balancing pulp and liquor inventories. It adjusts the quality targets at each step from chip to finished product.
The company also introduced the Valmet Mill-Wide Optimization Audit that helps to reveal the true production potential and the corresponding return on investment. Based on historical data, the audit helps to evaluate production, increase potential, identify limitations, and highlight use cases of mill-wide optimization. It also helps to uncover development opportunities required for moving towards fully optimized operations.
Greg Fralic, Product Manager, Mill-Wide Optimization, Automation Systems business line at Valmet says,“The pulp and paper industry is transitioning towards self-governing autonomous operations and towards a younger workforce with new roles and responsibilities. Valmet MWO helps to capitalize on these changes and unlock the mill's full potential.”
UPM Communication Papers has planned capacity reductions for its Germany and Austria based paper plants by Q2 2023. The decision is in wake of decade-long characterization of industry for demand decline. The reduction will help the companytosaveannualfixedcostsofapproximatelyEUR13million.
UPM Communication Papers, a part of UPM Group, is planning capacity reductions in its Germany and Austria based plants. The planned actions are estimated to result in annual fixed cost savings of EUR 13 million.
In Germany, the company plans to permanently close PM 6 at UPM Schongau, reducing the annual capacity of uncoated publication papers by 165,000 tonnes by the end of Q2 2023. The machine will be closed post-finalization of the employee consultation process, which is planned to start immediately in line with local legislation. The cost-competitive PM 7 and PM 9 will remain operational along with four other uncoated publication paper machines in Germany and Finland, totalling the production capacity at 1,800,000 TPA.
In Austria, the company has decided to stop the newsprint production at its Steyrermühl newsprint mill by the end of Q2 2023, and plans to accelerate the plans to ensure competitive production at remaining newsprint paper machines in Europe. The exit of a total annual capacity of 320,000 tonnes of newsprint will take place already by the end of Q2 2023.
Mr. Massimo Reynaudo, Executive Vice President, UPM Communication Papers, commented on the decision, “The continued long-term decline in graphic paper demand forces us to continue our efforts to ensure cost competitive production and that our assets are in efficient use in all circumstances. In a declining market, competitiveness in company operations is key to substantiating our long-term
commitment to the publication paper market and to remain as a reliable partner to our customers. UPM aims to handle the restructuring measures in a socially responsible manner and will engage now in a fair dialogue with employee representatives.” The Covid-19 years led to demand disruptions in the graphic paper markets, followed by a period of high inflation and unprecedented volatility last year. As the volatility is subsiding, the graphic paper market is returning to its long-term trend of declining demand, industry characterization for over a decade. UPM will recognize charges of EUR 10 million for its Austrian site, and EUR 26 million restructuring charges for its German site, as items affecting comparability in its Q1 2023 results.
Feb 24, 2023
rown Van Gelder, Netherland-based specialty paper producer, has been marked bankrupt by the District Court of Noord-Holland. Although the company generated positive operating profits in 2021 and 2022, a combination of factors, including continually rising energy and raw materials costs, have resulted in its inability to meet the payment obligations in 2023.
Crown Van Gelder's paper mill, established in 1896 in VelsenNoord, the Dutch province of North Holland, has two paper machines for the production of specialty papers, for food
Cpackaging and luxury shopping bags, and various grades of inkjet paper, including globally acclaimed Crown Letsgo and sugar beet paper Crown Native, over 90 percent of which are exported outside The Netherlands.
The energy and raw materials cost increase along with a sudden drop in orders has resulted in an unusually long standstill of production and liquidity shortfall. Moreover, future market developments for the company are also uncertain.
Mr. R. Mulder LLM, Pot Jonker Advocaten, and Mr. A.H.J. Dunselman LLM, Schenkeveld Advocaten, managing board, and bankruptcy trustees, are trying to deliberate conversations with varying interested parties to work out a future for the company.
ABB'sMES,alongwithlayeringsystems,willbeusedtostreamlinetheproductionprocess at Stora Enso's two Sweden mills. The system will be applied to a production capacity of 900,000TPAconsumerpackagingboardsforhigherefficiency,productivity,cybersecurity.
Feb 14, 2023
Stora Enso has signed a deal with ABB for the upgradation
of their two Sweden mills, for pulp and paper, through the latter's Manufacturing Execution System (MES). Skoghall Mill and Forshoga, the barrier coating site, have been shortlisted for MES application and the system has been customized to suit the respective site requirements.
MES shall help Stora Enso to streamline its entire production process, for higher mill efficiency and productivity and less wastage, for a consumer packaging board capacity of 900,000 TPA. The system application shall include layering of Production Planning, Production Management, Quality Data Management, Overall Equipment Effectiveness (OEE), Diary, and Operative Reporting modules, with interfaces to ABB and third-party systems.
The layering has been designed to ensure mills' safety from any cyber security threats.
After the system application, the mills' ERP, DCS, QCS, WIS, laboratory devices, and all the other systems shall get integrated over a centralized digital interface, helping the operators, supervisors, production engineers, and plant
managers to optimize their functions and overall processes. The contract dictating the terms and conditions shall go live in 2023, post-startup.
Skoghall Mill is the manufacturing unit of Stora Enso for the renewable and recyclable premium board, and production of bleached and unbleached kraft pulp. It uses a single fiber line with continuous cooking and Chemi-ThermoMechanical Pulp (CTMP) for kraft pulp production. Stora Enso uses the Forshaga barrier coating site to manufacture and develop a wide range of barrier solutions and laminations for food and beverages.
CrownVanGelder,TheNetherlands,hadfiledforbankruptcyduetoincreasedenergy andrawmaterialcosts, sudden dropindemand,andlongproductionstandstill,with theDistrictCourtofNoord-Holland,whichhasbeenaccepted.
Europe's leading corrugated packaging company, Smurfit Kappa released its 16th annualSustainableDevelopmentReport,reporting severallandmarkachievements to deliver on its long-term goal to have at least net zero emissions by 2050. The companyachievedmanyfeatshighlightingitscontinuedleadershipinsustainability and the report also shows the measurable progress that Smurfit Kappa has delivered during2022againstallitsBetterPlanet2050sustainabilitytargets.
Mar 29, 2023
Smurfit Kappa has reported several landmark
achievements to deliver on its long-term goal to have at least net zero emissions by 2050, in its 16th annual Sustainable Development Report, covering January to December 2022. The comprehensive report highlighted the company's progress through continued capital investment, ongoing operational improvement and collaboration with customers and other key stakeholders.
The company achieved many feats highlighting its continued leadership in sustainability including becoming a world first in successfully trialing hydrogen in its Saillat paper mill in France, completion of a multi-fuel boiler in the Zülpich paper mill in Germany which reduced emissions at the mill by 25%, announcement of the Group's largest decarbonisation project in Cali, Colombia involving an investment of almost EUR 100 million and commencement of a district heating project in Austria to benefit 20,000 homes across 3 communities.
The report also shows the measurable progress that Smurfit Kappa has delivered during 2022 against all its Better Planet 2050 sustainability targets, which includes 43.9% reduction in CO2 emissions since 2005 and 4% in 2022 alone, reduction in water consumption by 2.1% in 2022, waste to landfill
intensity decreased by 24% since 2013, packaging solutions sold as Chain of Custody, certified at 94.3%, management positions held by women stood at 23.5% at the end of 2022, up from 22% in 2021.
The company has also witnessed additional recognition in its sustainability credentials in the past six months. Smurfit Kappa received two 'Top Rated' badges from Morningstar Sustainalytics, for both 'regional' and 'industry' outperformance. These improved ratings build on the improved CDP (a global disclosure system for investors) climate rating of A- achieved in 2022 and the category-leading MSCI AA rating.
Fedrigoni Group has signed two deals with Arjowiggins Group to acquire its two majorrealities, aspecialtypapermillof7,000TPAcapacityinChina,andadedicated R&D center in France for building RFID, Printed electronics, and paper substrates research.
Feb 23, 2023
The Fedrigoni Group has contracted two major strategic
agreements, separately, for acquiring two major realities, namely a manufacturing partnership with a Chinese specialty paper mill and the acquisition of a French dedicated research
and development (R&D) center, of the Arjowiggins Group. The latter group filed for liquidation in September 2022.
The Quzhou, Zhejiang-China specialty paper mill is a worldleading producer of translucent papers, sold under the brand names of Gateway, Idem, and Sylvicta, with a production
capacity of 7,000 TPA. The manufactured product's applications range from industrial design and graphics to packaging for food, consumer electronics, and luxury products. The mill's capacity, along with its workforce of 130 employees, shall help the group to strengthen its presence in the Asian market.
The Grenoble, France, R&D center will help the group to boost its product innovation roadmap through testing and prototyping RFID, printed electronics, and advanced research on paper substrates.
The acquisition shall be helmed by two former Arjowiggins senior executives in consideration for a loan, for the
liquidation process, and a call option, giving Fedrigoni the option to take over the company in the longer term. The deal will help the group to boost its innovation capability in the field of alternative pulp-based materials along with its existing relationships in the Grenoble area, such as the International Paper Engineering School Grenoble INPPAGORA and the Pulp and Paper Research & Technical Centre (CTP). The group aims to strengthen its Asian geographical footprint and expand its product portfolio in the translucent papers segment, which has the potential to replace plastic packaging as a fully recyclable mono-material. The latter is one of the ESG strategy and roadmap goals of the group towards 2030.
The Fedrigoni Group is the world's leading producer of highend specialty papers, with applications in luxury packaging and other creative verticals, premium labels, and selfadhesive materials. The group already has a wide distribution network in China, Hong Kong, the Philippines, Indonesia, and Bangladesh, 11 warehouses, and a self-adhesive materials production plant in Hefei. The group recently acquired Guarro Casas, Spain (formerly part of Arjowiggins Group), Papeterie Zuber Rieder, France, as well, and entered an industrial partnership with Mohawk Fine Papers, USA.
French paper manufacturer Gascogne Papier recently placed an order for the supply of a PrimeLine MG (Machine Glazed) paper production line to Gascogne's mill located in Mimizan, France with International technology group ANDRITZ. The ANDRITZ MG line will replace three of the mill's four paper machines. The main target of the investment is to establish a multi-grade production line, capable of producingmorethan80differentgradesofribbedandunribbedpaper.
Mar 31, 2023
France-based Gascogne Papier has placed an order with
International technology group ANDRITZ for the supply of a PrimeLine MG (Machine Glazed) paper production line to Gascogne's mill located in Mimizan, France. The ANDRITZ MG line will replace three of the mill's four paper machines. With a web width of 6.8 m and a design speed of 1,300 m/min, this is the widest MG paper machine worldwide producing basis weights from 120 down to 25 gsm, based on 100% softwood unbleached kraft pulp. With a capacity of 125,000 t/a it will set a new industry benchmark with the highest capacity for uncoated MG papers. The ANDRITZ transfer-belt application closes the draw between press section and dryer section for highest efficiency at lowest basis weights and high-speed. The main target of the investment is to establish a multi-grade production line, capable of producing more than 80 different grades of ribbed
and unribbed paper. The start up is scheduled for 2025. Dominique Coutière, CEO of Gascogne Papier explains: “Investments of that scale are a big milestone for companies in our business. The selection of the right partner is a decisive success criterion. The experience and references in the MG sector as well as the customer-orientated approach of ANDRITZ convinced us. We are really looking forward to a great partnership.”
Toscotec has recently reconstructed the PM1 paper machine, which has now been startedbyOmniaAdvancedMaterials attheBeaverFallsfacilityinNewYork,USA.
Mar 29, 2023
Italy-based company Toscotec has successfully rebuilt the
PM1 paper machine, which has been started up by Omnia Advanced Materials at the Beaver Falls facility in New York, USA. The paper machine, PM1 produces highly customized specialty paper including gaskets, absorbency, and filtration media for numerous industrial and consumer applications and was modified to resume operations with the installation of a completely new dryer section.
The entire dryer section was supplied by Toscotec, including 20 TT SteelDryers featuring a diameter of 1,250 mm (49.2 inches), a useful drying width of 2,175 mm (86.6 inches), and an operating pressure of 10 barg (145 psig). It also applied a non-stick coating on many of the steel dryers to ensure effective cleaning during the papermaking process. Toscotec developed a customized solution designed to deliver a significant increase in PM1's paper width compared to the pre-existing width. The rebuild achieved its target of increasing the machine's production capacity.
Enrico Fazio, Sales Director of Toscotec's Paper & Board division, says, “It is always a pleasure to receive a repeated order. Toscotec has developed a customized rebuilding solution designed to bring an idle machine back to life. This project has a strategic impact on the specialty papers market, and it contributes to Omnia Advanced Materials continuous growth. We are happy to support them in this strategic expansion.”
Mar 1, 2023
Leading paper packaging provider, Smurfit Kappa has
recently invested 27 million euros for setting up a new waste management and recovery facility in its Nervión paper mill in Luretta, Spain. This initiative is a collaboration between Smurfit Kappa Nervión and several technology firms. The investment will see the expansion and optimisation of the plant, as well as the construction of a state-of-the-art lime kiln and gas treatment system. The mill will be adopting a fully circular production procedure, consisting of the biggest landfill reduction project the company has undertaken in order to deliver on its 2025 sustainability commitments. With a production capacity of 120 tonnes of lime per day, The lime kiln and gas treatment system will provide significant environmental benefits. The new circular system will allow the calcium carbonate waste that is currently generated in the mill's manufacturing process to be transformed into lime and subsequently reintroduced into the production process as a raw material. Mr. Javier Rivas, Smurfit Kappa COO of Paper & Board Europe,
said: “We are delighted about the installation of this industryleading system which will help our mill to become more sustainable and environmentally friendly. With this new lime kiln and gas treatment system, we will be able to recover and reuse more of our materials. We look forward to seeing the new system up and running later this year.”
Papelera Internacional of GrandBay Group has made its Toscotec-supplied doublewidth AHEAD 2.2L, PM7 line, operational at its Guatemala site. The tissue machine will add 60,000 TPA to the site's overall production. The group has contracted ToscotecforanotherPM5lineAHEAD2.2LtissuemachineforitsColumbiasite.
Feb 23, 2023
GrandBay Papelera Internacional recently made their
Toscotec-supplied double-width AHEAD 2.2 L (PM7) tissue machine operational, which shall expand the production by 60,000 TPA, at its Rio Hondo Zacapa, Guatemala, site. The GrandBay Group has contracted Toscotec for a second AHEAD 2.2 tissue line (PM5) at Papeles Nacionales' Pereira, Colombia, facility, which shall be supplied as a turnkey operation, scheduled to come online in 2024.
The AHEAD 2.2L machine (PM7) has a sheet trim width of 5,500 millimeters and a design speed of 2,200 m/min to deliver the maximum possible drying efficiency with the lowest energy consumption. It is equipped with a shoe press, an upgraded TT NextPress design, a third-generation TT SYD Steel Yankee Dryer, and a high-efficiency TT Hood. It also has Toscotec's patented TT SAF® DD (Short Approach Flow system with Double Dilution), which ensures efficient stock dilution in two steps for a significant reduction of electrical energy consumption.
Alberto Matos, GrandBay Project Engineering Manager, shared that the start-up was smooth and the machine is already producing high-quality tissue, powering the mill's belief of quickly achieving good running ability and high energy efficiency. Pier Paolo Brunazzi, Toscotec Project
Manager, labeled the partnership as strategic. He also highlighted a cooperative relationship between the two companies by quoting the worldwide shipment issues and associated delays. Mr. Brunazzi has earlier managed three new tissue line projects for Toscotec in the Latin American market.
Papelera Internacional, a unit of GrandBay Group, a leading Latin-American company established in 1953, is involved in the manufacturing, conversion, and sales of premium quality personal care, and home products. Its active market in over 25 countries includes the regions of Central America, the Andean, and the Caribbean.
Smurfit Kappa has concluded all the administrative process to transfer its Russian operations, including 1 corrugated plant in Moscow, and 2 corrugated plants and 1 bag-in-boxfacilityinStPetersburg,toalocalmanagement.
Mar 20, 2023
Smurfit Kappa, an Italian corrugated packaging specialist,
has sold its operations in Russia to a local management. The company owned 1 bag-in-box facility and 2 corrugated plants in St Petersburg, and 1 corrugated plant in Moscow.
The Russian exit of the company can be traced back to April 2022, when it announced to suspend support for its Russiabased operations following the country's invasion of Ukraine. The overall business from Russia accounted for less than 1 percent of Smurfit Kappa's forecasted sales.
ABi-monthly Magazine for Pulp, Paper & Converting Industries in INDIA
Please choose the following subscription plans: India Rest of World
o 1year(6issues) Rs.1000 USD200
o 3year(18issues) Rs.2000 USD350
o 5year(30issues) Rs.3000 USD500
*Including Mailing Cost & GST
Company Details (PleasecompleteinEnglishusingBlockletters&attachyour Business Card)
Pay Online
First Name_______________________________________________ Last Name___________________________________ Company Name___________________________________________ Designation_________________________________ Delivery Address______________________________________________________________________________________
City__________________ State___________________ Zip code___________ Country______________________________ Tel._________________________________Mobile_______________________________Fax________________________ Email______________________________________________Website__________________________________________ Business Activity______________________________________________________________________________________ Cheque/DDNo.__________________Dated________________ForRs______________Drawnon_________________________ GSTNo._________________________BillingAddress___________________________________________________________
Favouring “TULIP 3P MEDIA PVT. LTD.”
Transfer from Abroad
(Please mail the duly filled subscription form along with Bank Remittance copy to info@papermart.in)
Bank Details for Payment Transfer:HDFC BANK (Swift Code: HDFCINBB)
IFSC Code: HDFC0000287
Credit: TULIP 3P MEDIA PVT. LTD., A/C No.: 02872560002186
Branch: Ashok Vihar, Ph.-II, New Delhi-110052 (INDIA)
Please fill & return to : TULIP 3P MEDIA PVT.LTD., 501-502, ABW Tower, MG Road, IFFCO Chowk, Sector-25, Gurugram-122002, Haryana, INDIA Ph: +91-0124-4250148, Mobile : +91 99999 35011 / 22 / 44, Email: info@papermart.in, info@tulip3pmedia.in
Signature / Stamp
* Due to COVID-19 event status could change. Please check with the organizers before visiting.
TAPPICon
22-26 April 2023
Atlanta, Georgia (USA)
www.tappicon.org
International Pulp Week
4 - 6 June, 2023
Vancouver, Canada
www.internationalpulpweek.com
Latam Paper
14 - 16 June, 2023
Sao Paulo, Brazil
www.latampaper.com
Zellcheming Expo
20 - 22 June, 2023
Wiesbaden, Germany
www.zellcheming.de
Paper-ME
2-4 September 2023
Cairo, Egypt
www.papermideast.com
MIAC 2023
11 - 13 October 2023
Lucca, Italy
www.miac.info/en
Paperex 2023
6 - 9, December 2023
Greater Noida, India
https://india.paperex-expo.com
Paperex South India
5 - 7 December 2024
Chennai, India
https://southindia.paperex.in
A Bi-monthly Magazine for PULP, PAPER & CONVERTING INDUSTRIES in INDIA
Editor & Publisher
Parveen Kumar Jain – pkj@tulip3pmedia.in
Deputy Editor Geetika Jain – gjain@papermart.in
Sristy Sharma
Sub Editor – desk3@tulip3pmedia.in
Anushka Chauhan – desk2@tulip3pmedia.in
Graphic Designer
Ravi Thakur – ravithakur@tulip3pmedia.in
Advertising & Marketing
Puneet Dua – mktg@papermart.in
Akansha Tiwari – mktg3@tulip3pmedia.in
Priya Thapar – mktg2@tulip3pmedia.in
Support Team
Kushagra Mehrotra
Sandeep Kumar Deepak Kumar admin@tulip3pmedia.in
Chief Executive Officer
Priyank Jain pj@tulip3pmedia.in
Editorial & Publisher's Office : Paper Mart, Tulip 3P Media Pvt. Ltd.
218, Sanjay Nagar, Gulabi Bagh, New Delhi-110007, INDIA
Correspondence Address: Tulip 3P Media Pvt. Ltd.
501-502, ABW Tower, MG Road, IFFCO Chowk, Gurugram, Haryana-122003, INDIA, Tel.:0124 447 0798 / 99
Mob.: +91 99999 350 11 / 44, E-mail : info@papermart.in / info@tulip3pmedia.in
International Sales : RNP
Nicolas Pelletier
16, rue Bannier 45000 Orleans, France
Tel.: +33 682 25 12 06, Fax: +33 238 422910
Chinese Representative: China Pulp & Paper Industry Publishing House No. 101, Gongyenan Road, Jinan Shandong, China Tel.: +86 531 88522949
Owned, Published & Printed By : Parveen Kumar Jain, Published at 218, Sanjay Nagar, Gulabi Bagh, Delhi-110007, INDIA. Printed at: Pankaj Paper Mart, 218, Sanjay Nagar, Gulabi Bagh, Delhi-110007, INDIA.
All disputes regarding this magazine will be settled in Delhi (India) Jurisdiction Only.
The views expressed in the columns of Paper Mart are not necessarily those of the editor or the publisher & they accept no responsibility for them.
CAUTION: No part of this magazine including advertisements designs, prepared by us or through us should be copied, reproduced or transmitted by any one without prior written permission of the publisher.
Paper Mart Partner
magazine: