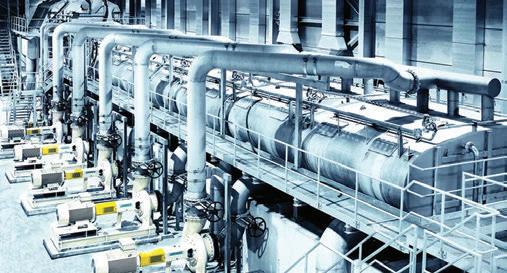
1 minute read
Progroup Starts Up PW14,
New Corrugated Sheetfeeder Plant in Strykow, Poland
For the new corrugated sheetfeeder plant spanning 28,000 sq m, Progroup has invested around EUR 72 million.
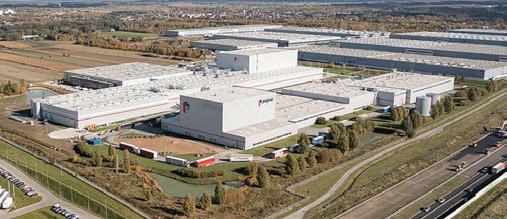
January13,2023
Progroup has commenced operations at PW14, which is its new28,000sqmcorrugatedsheetfeederplantinStrykow, Poland. The new plant will produce up to 200,000 tonnes of corrugated sheetboard annually. Along with the PW07 plant situated nearby, the new unit will have an annual production capacity of 825 million sq m. This makes Stryków as one of the world's largest sites for corrugated board production. Progroup has invested around EUR 72 million in the project at the site, which covers around 28,000 sq m, and created 50 new jobs.
Almost all standard grades of the corrugated board can be produced at the PW14 plant, with a working width of 3.35 metres and a production speed of 400 metres per minute. At the heart of the corrugator machine is the Modul Facer MF-A concept which was developed by BHS Corrugated Maschinenund Anlagenbau GmbH. It has been used for the first time anywherewithaworkingwidthof3.35metresatProgroup.
Due to the modern combined cooling, heat and power plant, carbon emissions are now as lowest as possible. The state-ofthe-art plant utilises waste heat from its own power generation either in an absorption chiller to“produce”cold, or feeding the heat into the heating circuit, as and when required. This will enableinthesavingofasignificantquantityoffossilfuels.
The plant also has a 32-metre-high, fully automatic high-bay warehouse with more than 14,000 storage spaces and four automatic storage and retrieval machines. It will be able to store up to two days of corrugated sheetboard production, enabling perfect just-in-time deliveries by decoupling the time between the manufacture of the corrugated board and the productionofpackagingbythecustomer.
Based in Landau, Germany, Progroup AG is one of the leading European manufacturers of containerboard and corrugated boards.n
Lipy Paper Mills Places Order with ANDRITZ for Energy-Efficient Wastepaper Processing Systems
ANDRITZ will supply key equipment for two RCF lines, featuring a total capacity of 150 t/d and processing LOCC (Local OCC) and MOW (Mixed Office Waste) as raw material for production of testliner, writing and printing paper.
December24,2022
Bangladesh-based Lipy Paper Mills Ltd. has placed an order with ANDRITZ for wastepaper processing systems. ANDRITZwillsupplykeyequipmentfortwoRCFlines,featuring a total capacity of 150 TPD and processing LOCC (Local OCC) and MOW (Mixed Office Waste) as raw material for production of testliner, writing and printing paper. This would be first ANDRITZRCFlinesforBangladesh.
Talking about the project, Mr. Shahiar Hasan Khan, Deputy Managing Director, Lipy Paper Mills says, “ANDRITZ convinced us because of its energy-saving technology for screening and flotation and its focus on minimum fiber loss. In addition, with the Ultra High Dispersion we'll be able to keep steam demand atalowlevel.Allthesetopicsarestrategicdevelopmenttargets foranaspiringcompanylikeLipyPaperMills.”
The processing systems would be delivered to the mill in Changine, Modonpur, Kanchpur, Sonargaon. Start-up is scheduledforthethirdquarterin2023.n