technical resolution
Beattie Passive Units
Technical Details
On Site Construction Strategy
Modular Unit Placement
Material Selection
Technical Building Plans
Project Conclusion
beattie passive| passivhaus modular construction
Beattie Passive is a company located in Norwich, UK, that specialises in passivhaus design and construction. They have completed many projects across the UK to a highquality standard whilst also remaining sustainable.
They were the first company in the UK to achieve certification by the Passivhaus institute for a complete build system that is patented in 42 countries. The build system provides a continuous insulation layer around the core of a timber-framed structure.
Traditional methods of construction creates numerous joints between floors, walls, and roofs, of which [at each joint] the building will lose heat. The Beattie passive system overcomes this problem whilst also meeting the rigorous demands of passivhaus.
The build system uses a treated timber frame structure [available in modular volumes] to deliver a complete solution. High performance insulation is injected into the floor, wall, roof and ceiling cavities and creates one continuous insulated layer with no leaks.
The build system can also differ depending on the method of delivery chosen. With modular being the most common and has many advantages.
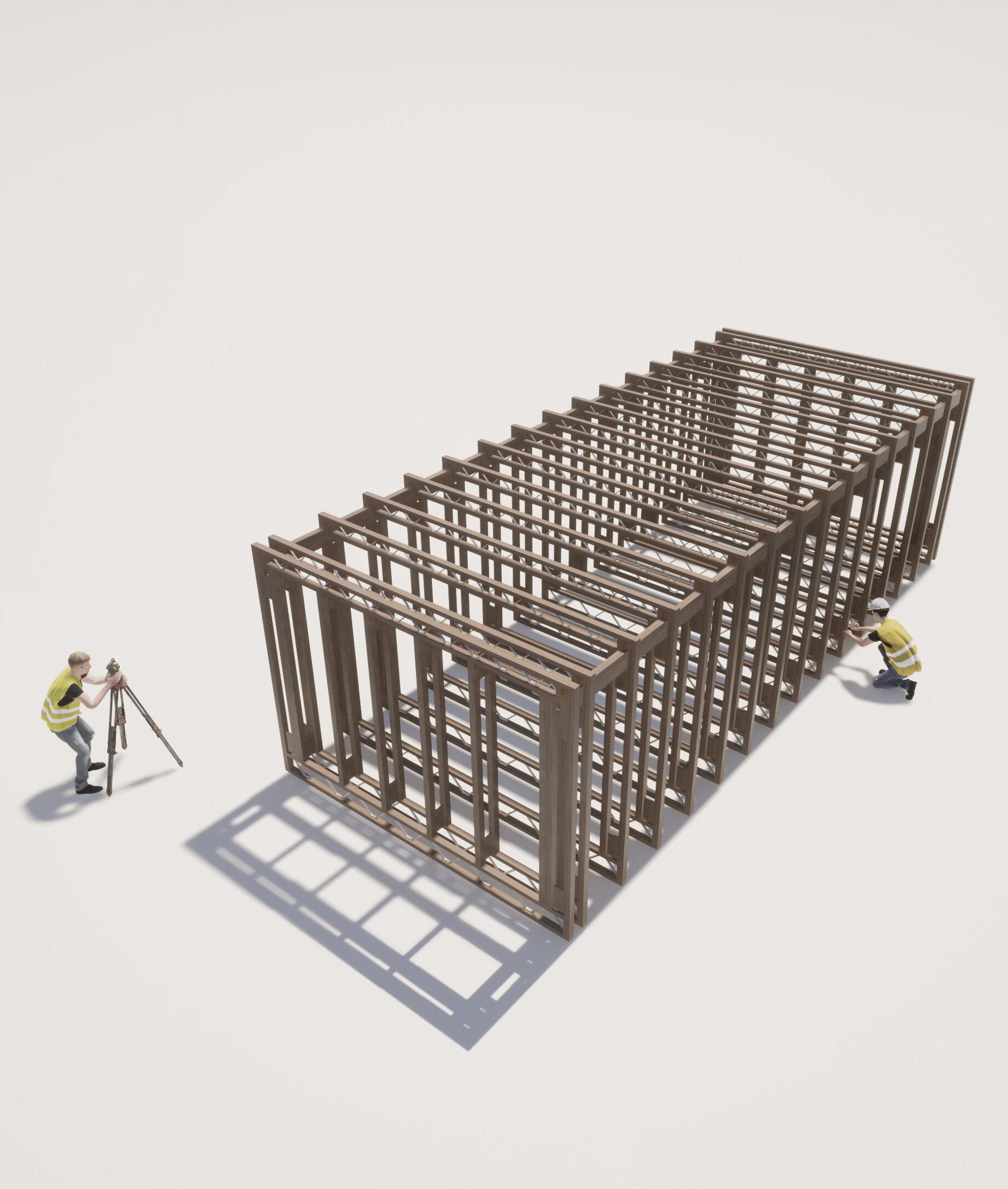
wall detail | 1:10 | U-Value = 0.11 W/m2K
wall structure| beattie passive unit
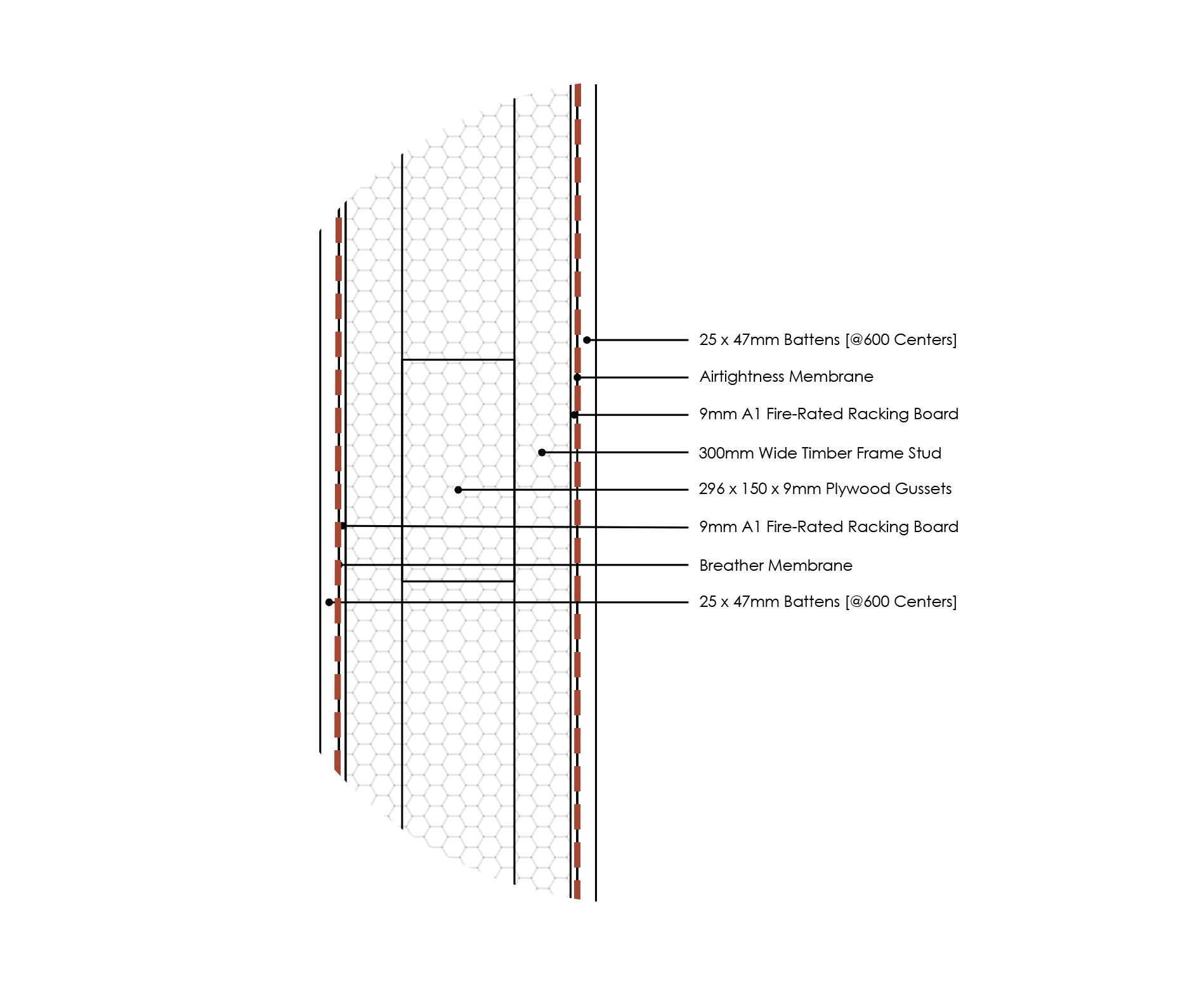
The wall of a Beattie Passive modular unit is constructed with 300mm deep twin stud work. The frame is then filled with EPS beads to provide a continuous insulation layer.
Internal Walls | An airtightness layer is applied to the inner face of the structural frame [protected by a 9mm fire racking board] Service voids are created with 25x47mm battens.
External Walls | Another 9mm fire board is fixed to the main frame system. A breather membrane is then applied to the out face with battens then attached to allow for any external cladding.
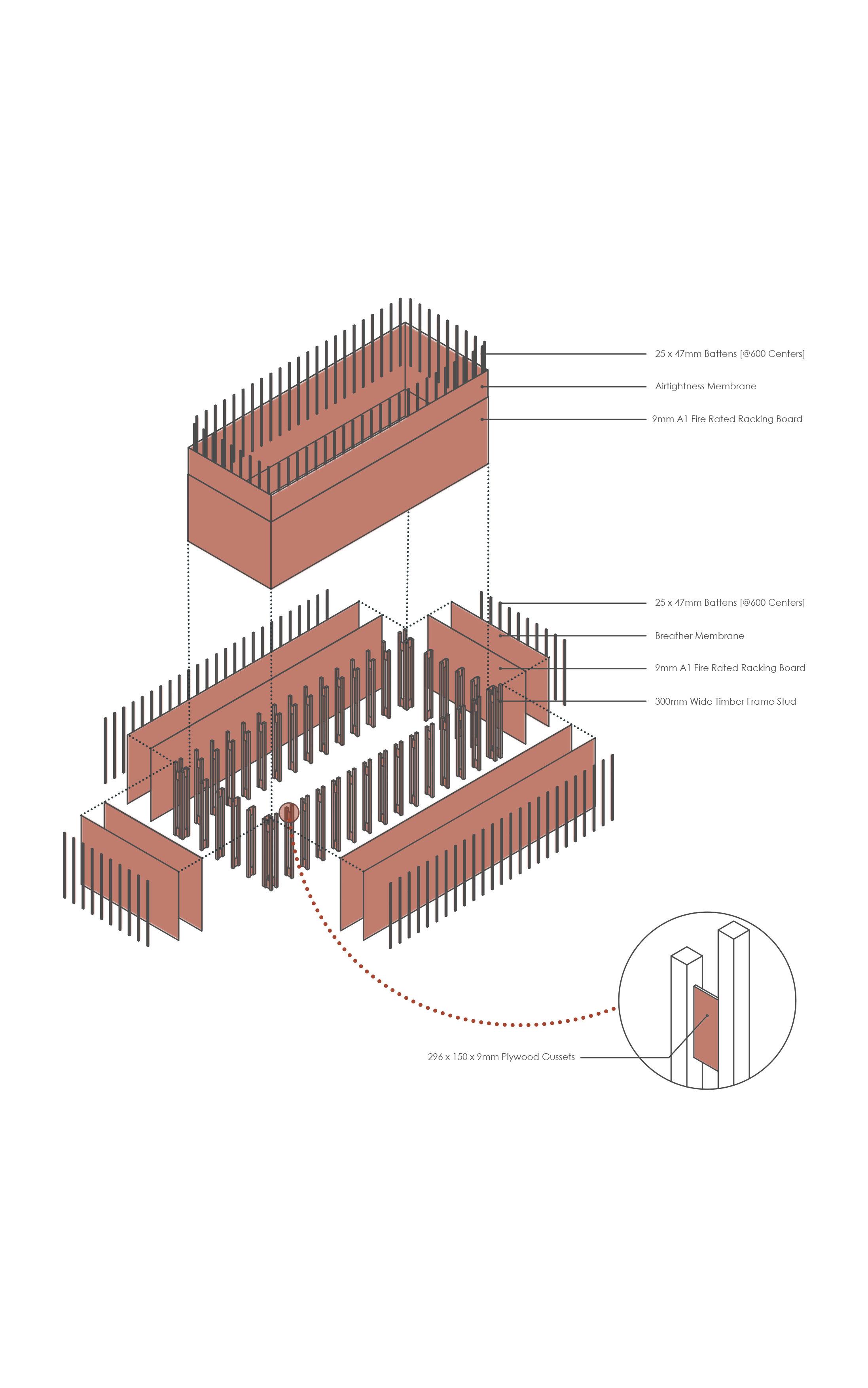
ground floor detail | 1:10 | U-Value = 0.11 W/m2K
ground bearing| beattie passive unit
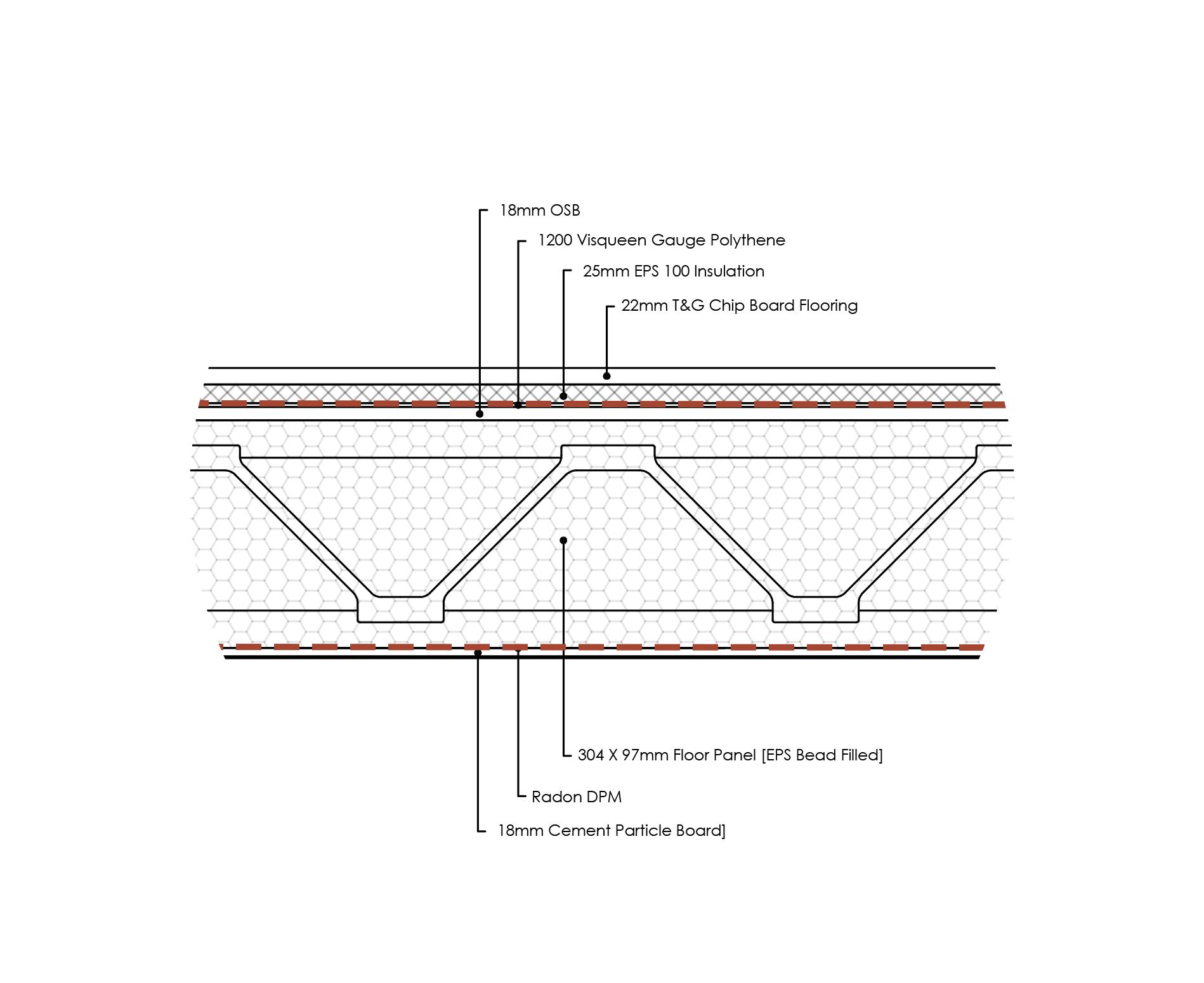
The Beattie Passive ground floor system can be constructed on site or come with the modular unit itself.
The method I have chosen is for the ground bearing floor to be part of the ground floor modular unit, so that each unit can be brought onto site and lifted directly into place.
Like walls, floors and roof, the ground bearing system uses the same method of timber stud work, to ensure the constant insulated envelope.
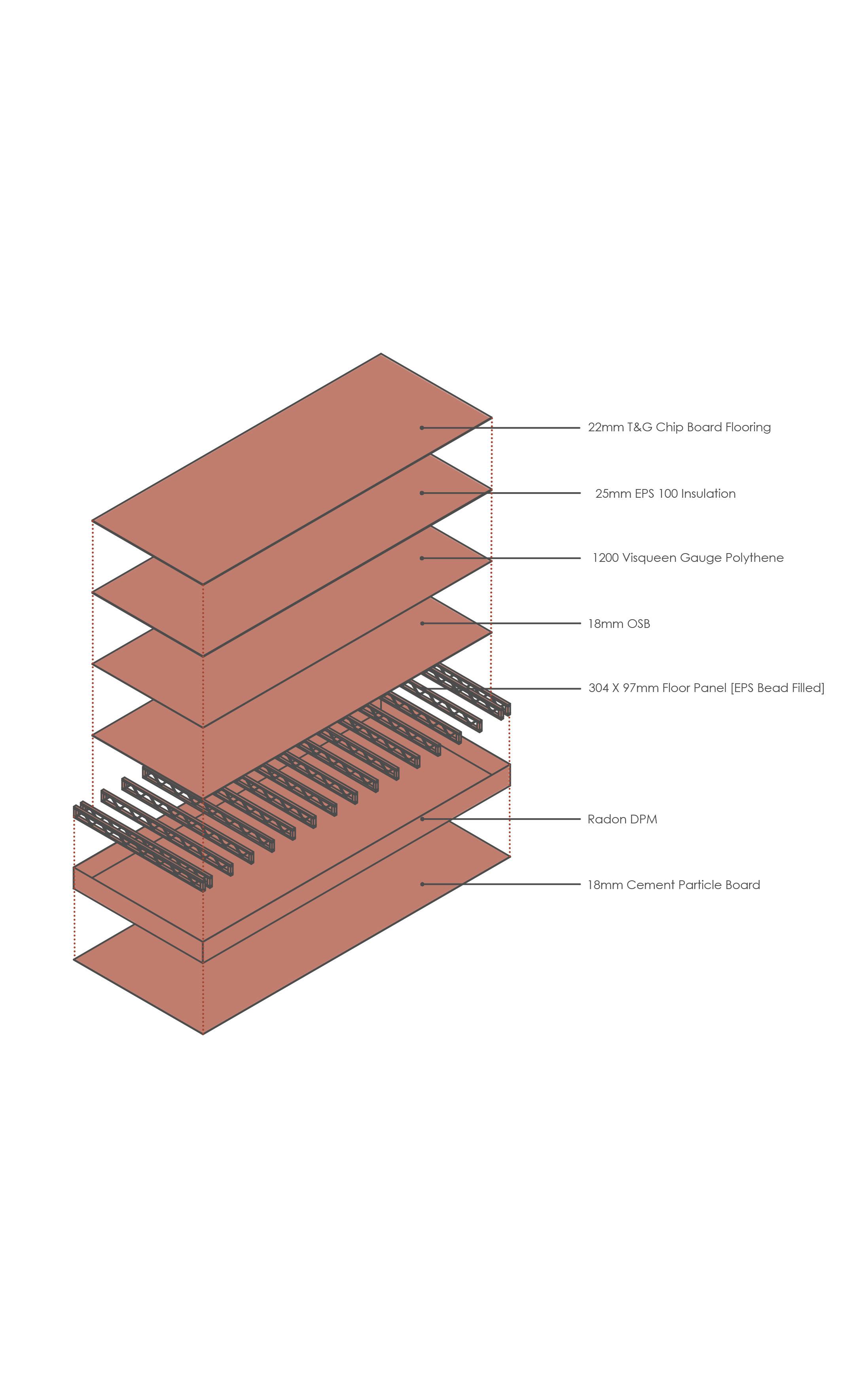
intermediate
floor detail | 1:10
intermediate floor| on-site install
To construct the intermediate floors of the beattie passive modular unit, installation must take place on site. The main joist structure of the floor uses top hung easy joists. A ring beam [wall plate in detail] is attached to the outer stud of the timber frame.
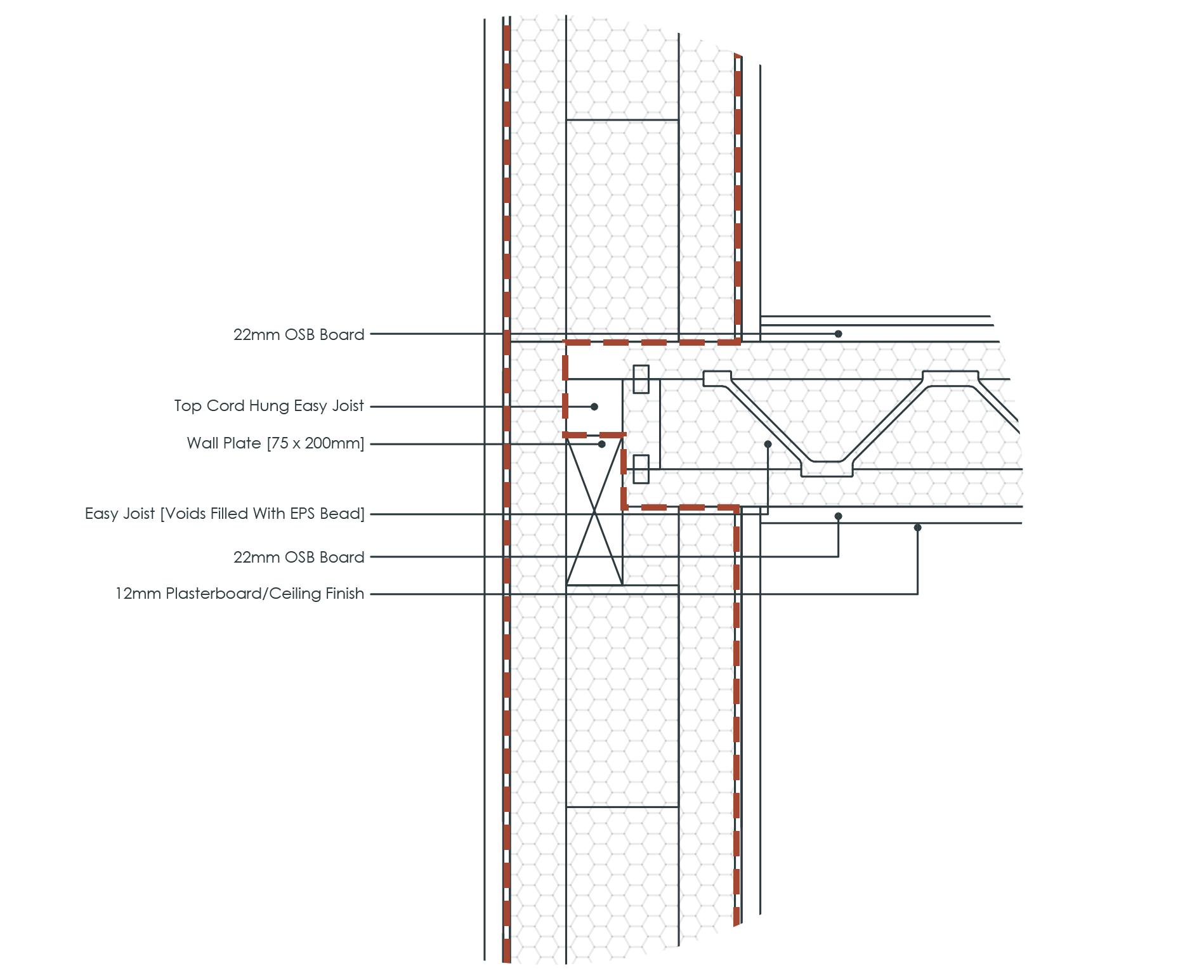
By attaching the ring beam to the outer stud, it allows for more stability and strength as it bears some weight onto the ‘inner stud’ and also prevents a thermal bridge forming at the floor junction as insulation can easily flow between joists and walls.
Easy joists are lightweight and easy to work with. By the nature of design, joists already have voids between them where services can easy by routed without any disruption to the structural integrity. The spans of these ‘metal web’ joists are also larger than standard timber joists.
‘inner stud’ can bear extra weight and take a small load off the ring beam
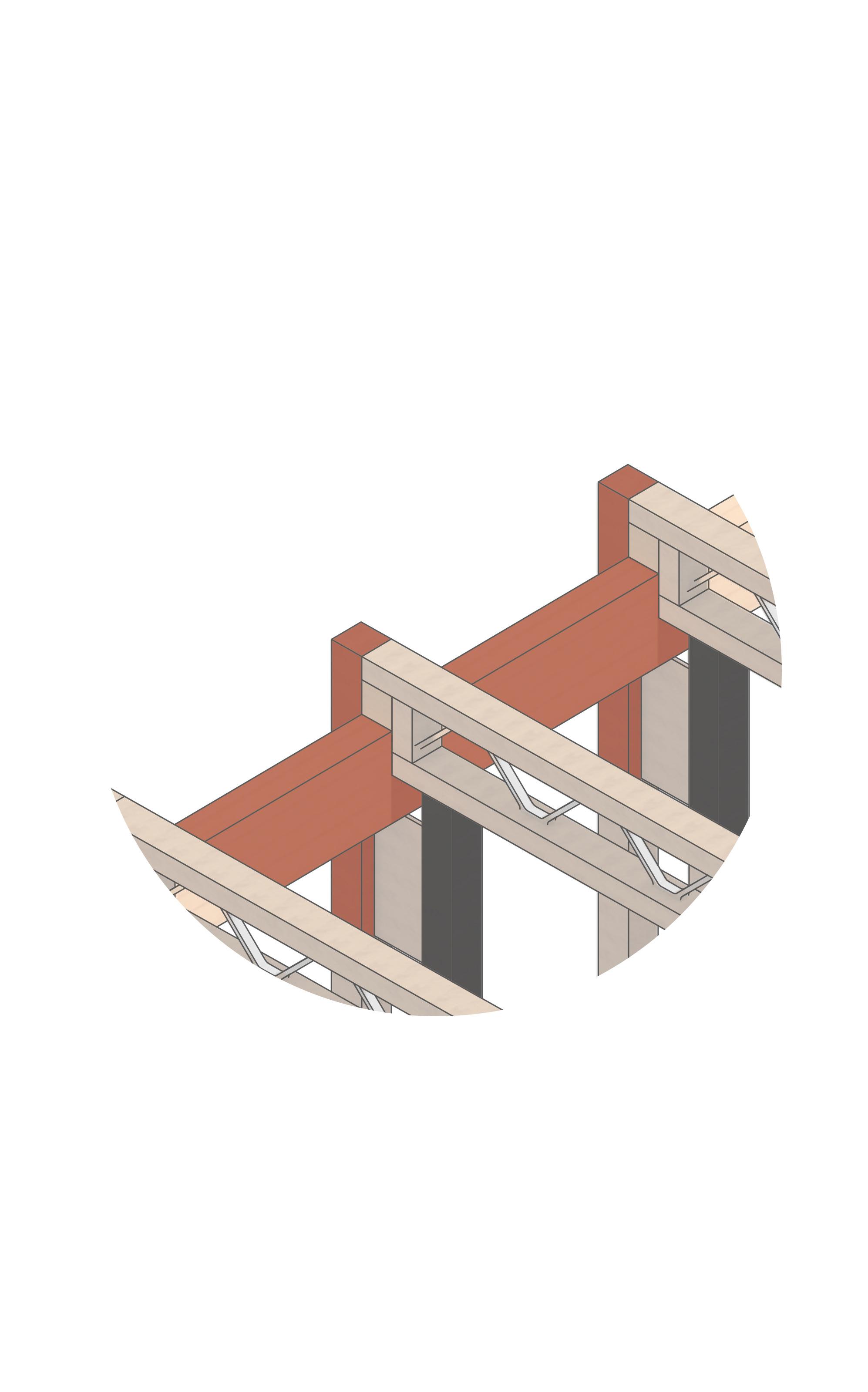
roof detail | 1:10 | U-Value = 0.11 W/m2K
roof| on-site install
The roof system can be constructed as a cold or warm roof. There are two options that Beattie Passive provide, which are and on site build system and a modular roof build system.
The modular build system only supports flat roofs, and for this reason I have chosen on site installation of the roof.
The roof system is the same method used for the walls and floors which again allows there to be a complete continuous layer of insulation from, ground floor, intermediate floor and roof, with no thermal bridges.
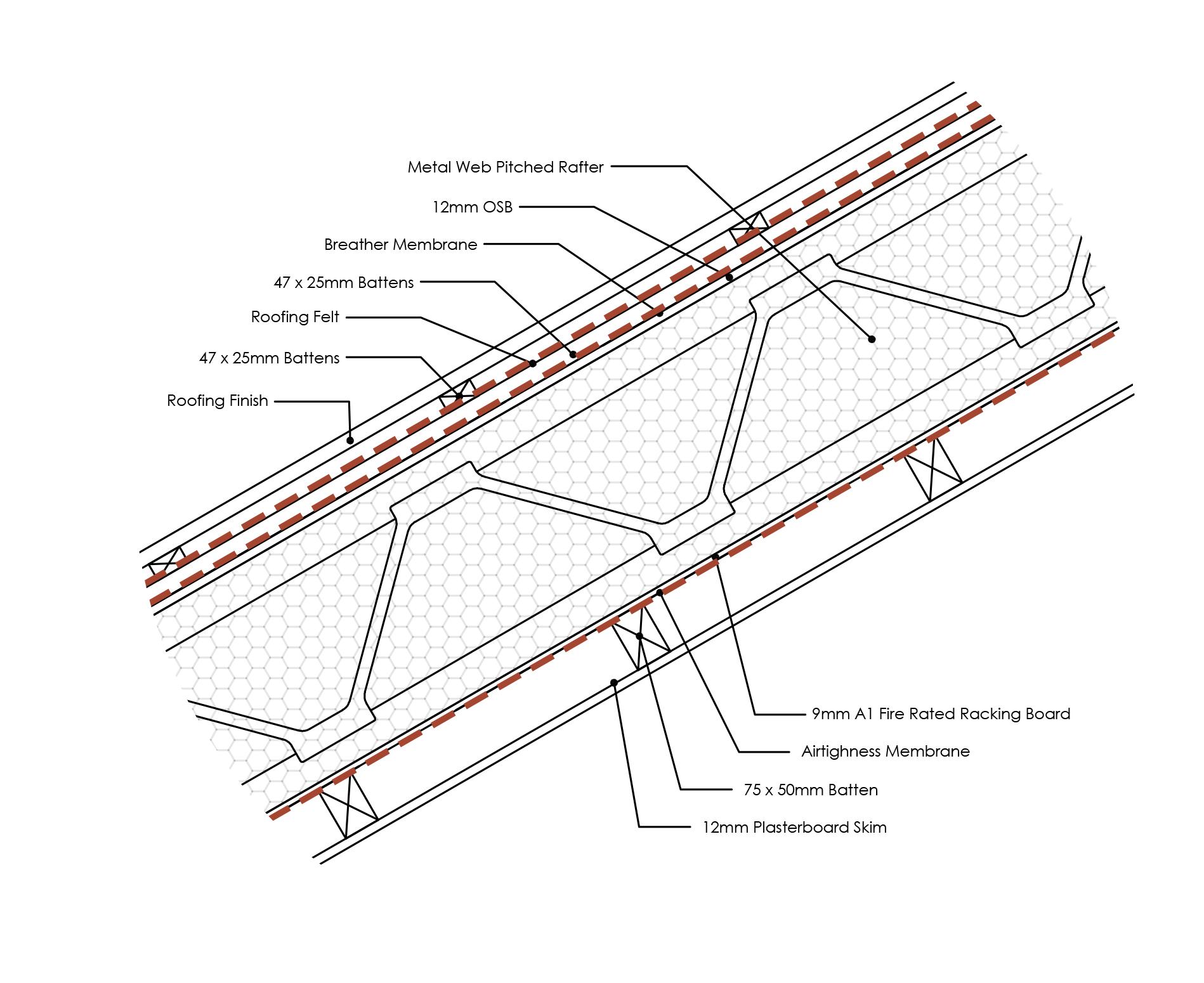

Upper
Individual units are delivered to site on individual trucks.
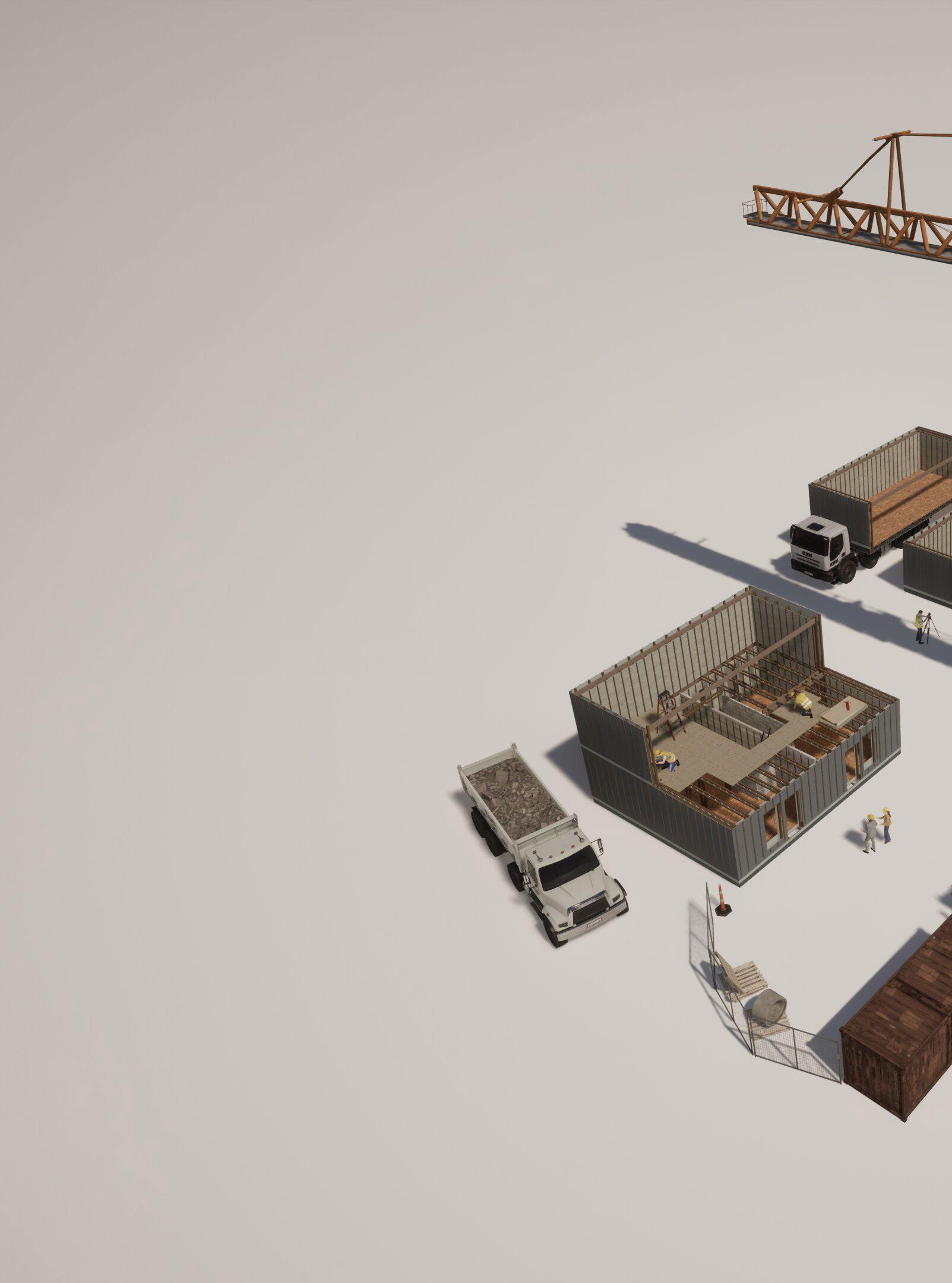
When units are delivered, they can be stored easily and can undergo quality checks before being installed. Storage of on site construction materials such as block work bricks, drywall, floor boards. There is also spaces for mixing mortar and a waste disposal skip for any waste generated [which isn’t much]
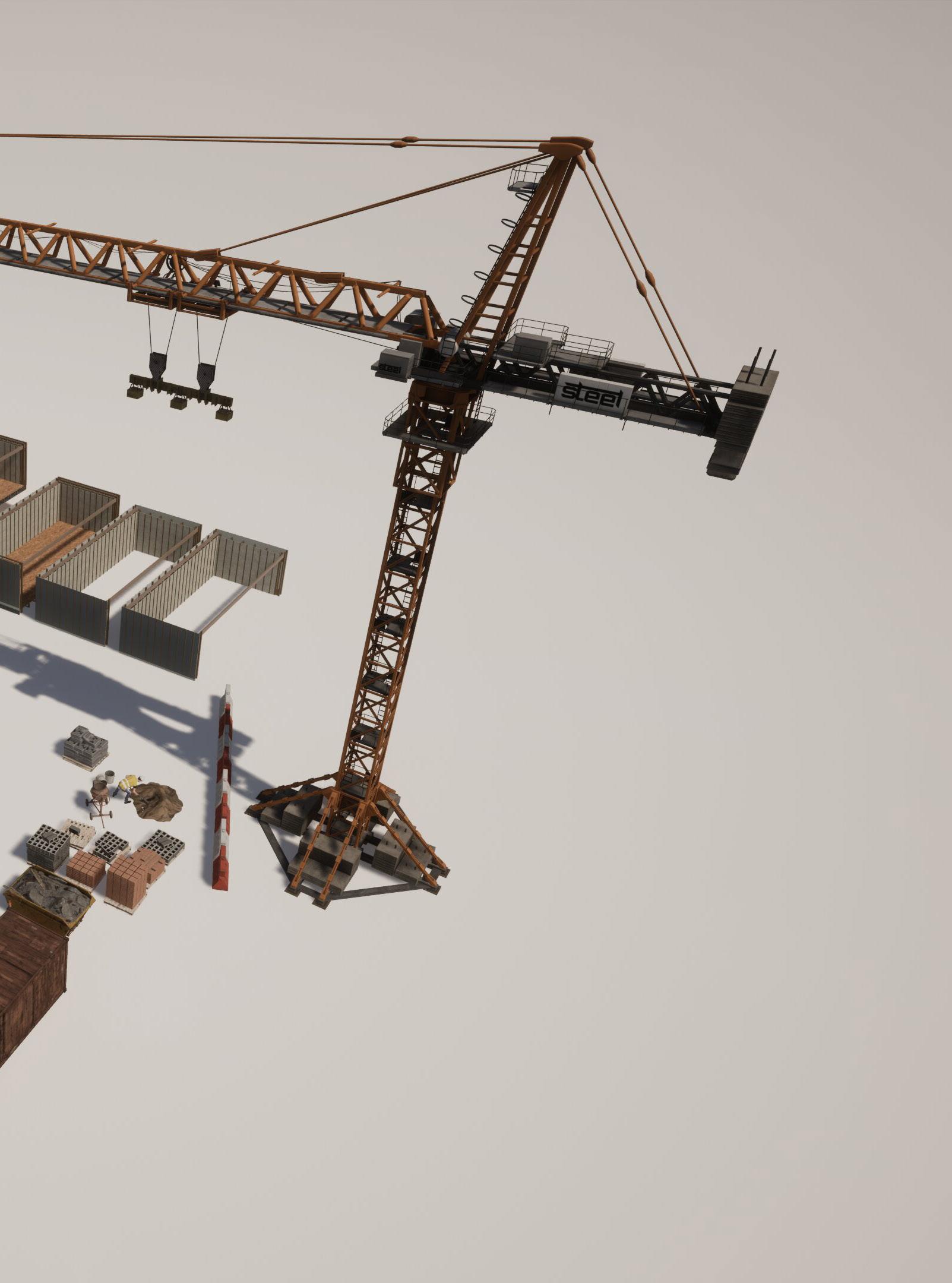
modular units placement & sizes | beattie passive

material selection| whole life carbon
reclaimed timber| pallet wood
The main cladding material for my design proposal will be reclaimed timber & aluminium cladding.
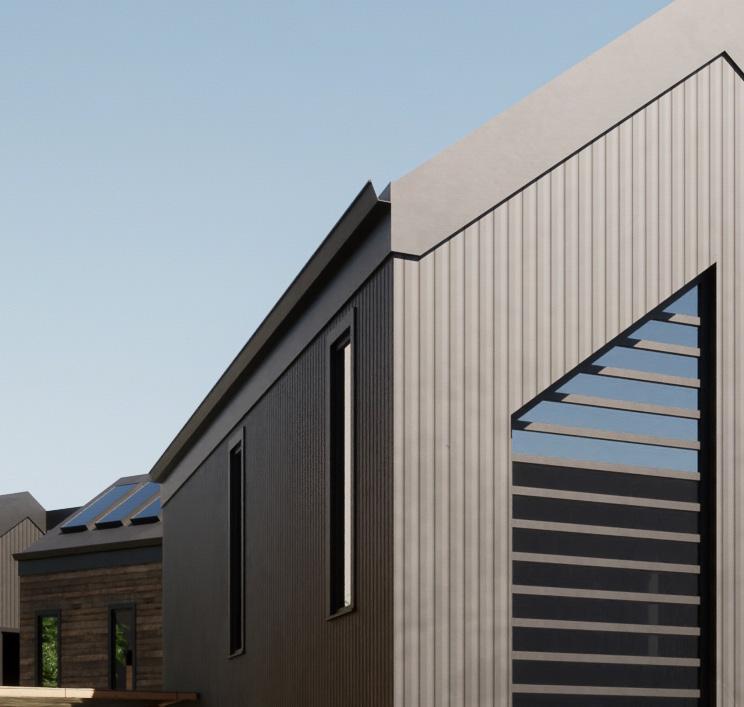

Reclaimed timber is special in many different ways, as it provides a ‘rugged’ appearance to the design and is highly unique in itself as no two pieces of reclaimed timber are the same. It also helps the design to have a feeling of ‘aging’ and adds a sense of history. When used in partnership with a ‘newer’ material [such as aluminium] it gives a contrast between the old and new.
Some of the main environmental benefits of using reclaimed timber are that it has a high level of stability and durability, and it has already performed all the expanding it will ever do which reduces the risk of splitting or warping in the future.
Timber can then also be reclaimed and broken down and recycled into wood chips that can be used for many different things.
aluminium| high carbon?
Whilst aluminium does in-fact have a relativity high upfront carbon cost, we also have to consider the ‘whole life carbon of aluminium, and is it really that bad?
Aluminium is one of the world most recyclable/reused materials . this is because it can be recycled in a very high-value manner, and doing so requires significantly less energy. It is frequently reported that recycling Aluminium uses ‘5% of the energy required to manufacture aluminium from ore’.
Assuming a lifespan of 25-40 years it would take (roughly) 750 years (that’s up to 30 use cycles) for you to be ‘embodied energy neutral’ when using recycled Aluminium products vs. using new timber products every time. Furthermore, after 30 use cycles, more than 181kg of C02 per kg of Aluminium used will have been produced, versus up to 250kg of sequestered carbon by using new timber products each time.