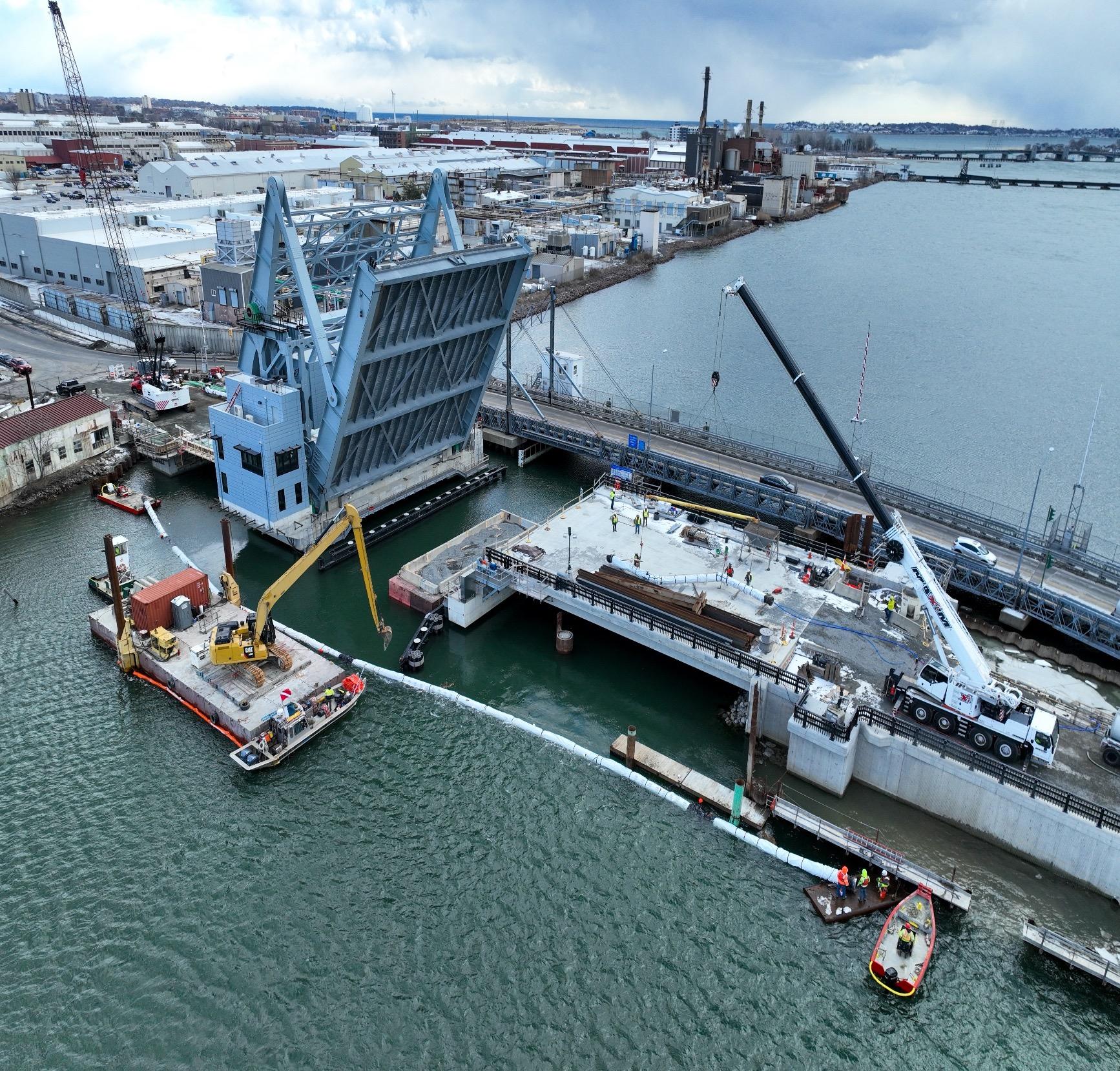
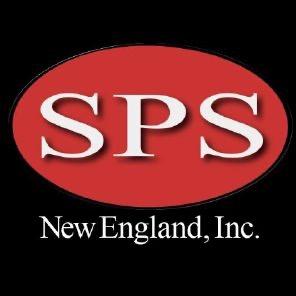
MassDOT Bridge Project over the Saugus River Includes Tricky MWRA Water Main Replacement
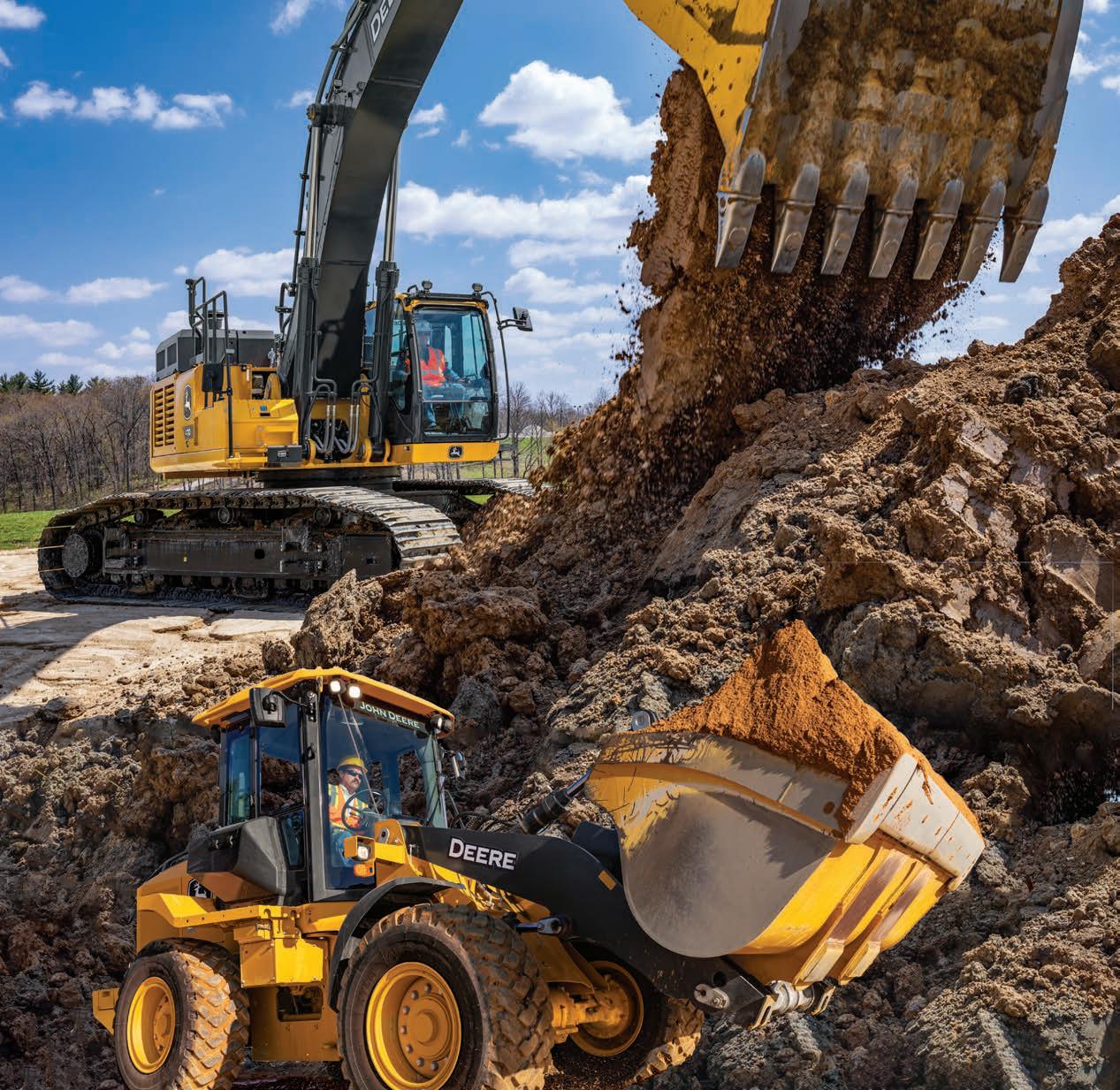
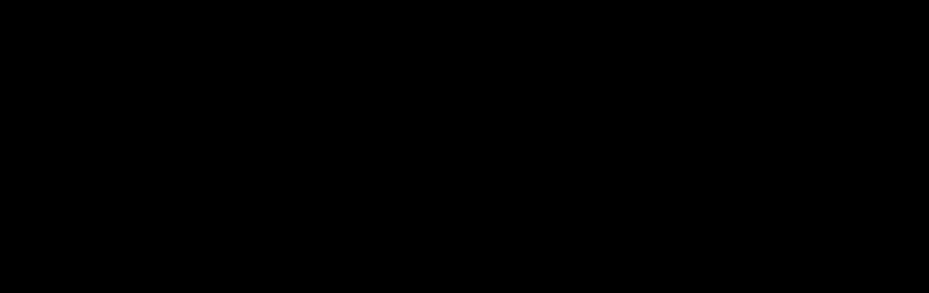
MassDOT Bridge Project over the Saugus River Includes Tricky MWRA Water Main Replacement
Construction:
• Heavy Industrial
• Commercial
• Multi-Unit Residential
• Design Build
• Ground Up
• Renovation
• Pumping Stations Transportation:
• Traffic Signal Systems
• Highway & Street Lighting Systems
• Intelligent Transportation Systems
• Parking & Snow Melt Systems
• Rail Transit Installation
Alternative Energy:
• Wind Turbine
• Photo Voltaic
• Green Technology
Other Services:
• Tel/Data
• Fiber Optic
• Fire Alarm
• Stand By Power Systems
• Sports Lighting
• Marine Power Installations
• Special Event Lighting & Power
Years of Excellence 1954-2025
OFFICERS
President BRIAN COONEY
C. C. Construction, Inc.
President Elect
CHRIS
GVC Construction, Inc.
Treasurer
QUERINO PACELLA RJV Construction Corp.
Secretary
LISA FRENCH KELLEY
W. L. French Excavating Corp. BOARD OF DIRECTORS
MARCELLA ALBANESE
Albanese Brothers, Inc.
CALVIN BRANDFORD
CHB Excavating
GERRY CARNEY, JR.
C. N. Wood Company, Inc.
JULIA D’ALLESSANDRO D’Allessandro Corp.
JERRY GAGLIARDUCCI
Gagliarducci Construction, Inc.
MARCO GIOIOSO
P. Gioioso & Sons, Inc.
JUSTIN GOODHEART
J. F. White Contracting Co.
DAN HORGAN
R. H. White Const. Co., Inc.
MARK LANGEVIN Phoenix Communications, Inc.
WILLIAM LEONARD
Aqua Line Utility, Inc.
KARIN MARSHALL
Boston Concrete Corp.
MIKE McCARTHY
J. Derenzo Co.
RYAN McCOURT
McCourt Construction Company
JOHN McGRATH
Methuen Construction Co.
MICHELE NORTON
HUB International New England
ROBBIE OUR
Robert B. Our Co., Inc.
RICHARD PACELLA, JR.
R. M. Pacella, Inc.
MARK SZELA
Insituform Technologies LLC
JOSEPH NOLAN Executive
APRIL, 2025
5 President’s Message: UCANE Hosts Annual Trade Show and Forecast Dinner Meeting, Prepares for Water Week in Washington, D.C.
7 Legislative Update:
• City of Boston’s Streets Cabinet Unveils Procurement Preview Tool
• Healey-Driscoll Administration Awards $825,000 in Grants to Improve Water Quality
• EPA Names Regional Administrator for New England; CLF Raises Concerns
• Public Input Sought for Federal MS4 Permits
• Governor Healey Signs Executive Order to Promote Project Labor Agreements
• News in Brief
23 UCANE Interview: Senator John Velis (D-Hampden and Hampshire District)
29 Legal Corner: Cybersecurity Fraud Settlement in Whistleblower Action
32 UCANE’s 2025 Forecast Dinner Meeting: MassDEP, MWRA, and BWSC Leaders Discuss Their Upcoming Capital Improvement Projects
41 MWRA FY25-FY26 Upcoming Construction Awards
43 BWSC 2025 CIP Upcoming Projects
45 David Coppes, Chief Operating Officer to Retire After 32 Years with MWRA
47 Under the Hard Hat:
A n Interview with UCANE Board Member Marco Gioioso, P. Gioioso & Sons, Inc. 53 UCANE’s Updated Employee Safety Manuals Now Available 54 UCANE Contractor Member of the Month: SPS New England, Inc.
61 Insurance Perspective: The Advantages of a Group Captive Insurance Program for UCANE Contractors
64 UCANE’s Associate Members Featured at 13th Annual Trade Show
71 A Close Call Emphasizes the Need for Infrastructure Resilience
73 Construction Safety & Compliance:
A n Interview with Ed Sarin, Health, Safety, and Training Director, Feeney Brothers Environmental Services
77 UCANE’s Safety Corner: In the Zone: The Importance of Setting Up a Proper Work Zone 80 UCANE Member Testimonials 81 Technology in Construction: Hardware and Software Subscriptions Deliver Cost and Performance Advantages
Editors: Joseph F. Nolan & Anne Klayman, Associate Editor: Suzanne Hatch
Magazine Designer/Associate Editor: Sherri Klayman, Head Writer/Assistant Editor: Mike Lenihan
Construction Outlook Chair: Brian Cooney
Editorial Board: Brian Cooney, Chris Valenti, Querino Pacella, & Lisa French Kelley
The Jack Farrelly Company, Putnam Pipe and HR Prescott have united, as part of the Core & Main family.
• W. Boylston, MA 508-835-4431
• Bloomfield, CT 860-769-6760
• East Lyme, CT 860-739-5457
• New Britain, CT 860-826-0517
• Hopkinton, MA 508-435-3090
• North Haven, CT 203-777-5548
• Westbrook, ME 207-464-0585
• N. Billerica, MA 978-459-6701
• Norwood, MA 781-407-9133
• Taunton, MA 508-880-8736
• Worcester, MA 508-752-7473
• Loudon, NH 603-263-7350
• New Milford, CT 860-210-6262
• Springfield, MA 413-732-8400
• Johnston, RI 401-725-0140
We’re still the dependable experts you’ve always known, but now as one team, continuing to handle all your water, wastewater, fusible, and storm drainage material
As President of UCANE, I am proud to reflect on the tremendous success of our recent Annual Forecast Dinner Meeting and Trade Show, held on March 25 at the Four Points by Sheraton Hotel in Norwood. This flagship event once again demonstrated the strength and dedication of our membership, with over 310 attendees filling the ballroom.
The Forecast Dinner featured an impressive lineup of keynote speakers who shared valuable insight into the future of our industry. We were honored to welcome Gary Moran, Deputy Commissioner of MassDEP; Fred Laskey, Executive Director of the MWRA; and John Sullivan, Chief Engineer at Boston Water and Sewer Commission. Each speaker delivered engaging presentations outlining their agencies’ 2025 capital investment priorities, offering transparency, and opening the floor to thoughtful questions from our members. Their participation reflects UCANE’s respected role as a trusted partner in shaping infrastructure development across the Commonwealth.
Earlier in the day, UCANE’s Board of Directors and Government Relations Committee convened to conduct important association business. Key topics included the impact of Massachusetts’ adoption of Heavy-Duty Omnibus (HDO) and Advanced Clean Truck (ACT) regulations, which will affect our members’ ability to purchase medium and heavy-duty trucks in 2025 and beyond. The board also discussed the upcoming sideguard regulation requirements that take effect at the end of 2025. These internal meetings are crucial in guiding our advocacy efforts and addressing ongoing challenges related to funding, workforce development, and evolving regulatory frameworks.
The Trade Show portion of the evening was equally successful. Many of our advertising members, those who regularly support Construction Outlook magazine, were given complimentary booth space to showcase their latest products, services, and technologies. The energy on the show floor was palpable, with vendors and contractors engaging face-to-face and building partnerships that continue to strengthen our industry.
Looking ahead, April marks another key milestone as our Executive Director and members of the Executive Board traveled to Washington, D.C. for Water Week 2025. This national event provides a platform for engaging with federal policymakers and highlighting the critical need for ongoing investment in water and wastewater infrastructure. Our delegation attended a national policy conference, met with our federal lobbyists at Banner Public Affairs, and coordinated efforts with the Clean Water Construction Coalition, of which UCANE is a proud member.
In addition, UCANE leaders met with members of the Massachusetts Congressional delegation to advocate for increased funding and support for utility, water, and wastewater infrastructure investments across our region. n
ATS EQUIPMENT HAS FOUR CONVENIENT LOCATIONS
BOSTON, MA, 33 Locust St.
Tel: (617) 825-3600
AUBURN, MA, 487 Washington St.
Tel: (508) 832-8500
REHOBOTH, MA, 51 Fall River Ave.
Tel: (508) 379-6200
CANDIA , NH, 133 Raymond Rd.
Tel: (603) 483-2100
www.atsequipment.com
Our range of Epiroc premium hydraulic breakers give you everything you want from a hydraulic breaker: efficient and highly adaptable products, that combine superior efficiency and performance with high durability and low impact on the environment. SBU breakers are used for road work, trenching and demolition as well as in primary and secondary rock breaking. It has an air injection porting for under water breaking. A solid body breaker is manufactured from a single block of cast metal.
The Connolly family and all the professional staff ATS Equipment look forward to serving you – our friends!
The City of Boston’s Streets Cabinet has unveiled a clear and easy way to track upcoming opportunities before the City of Boston, under the Streets Cabinet, comprised of the Boston Transportation and Boston Public Works Departments. “Procurement Preview” provides an early look at upcoming contracting opportunities. The City of Boston’s Streets Cabinet, headed by Chief Jascha Franklin-Hodge, now posts procurement previews up to a year in advance, giving potential bidders time to prepare before official bid solicitations are released.
If interested in an upcoming opportunity, contractors can contact the City of Boston’s Streets Cabinet for more details before the official bidding process begins. The team member in charge of the procurement will be able to answer questions regarding publicly available information. The goal of the “Procurement Preview” is to enhance transparency, increase vendor participation, and ensure the best possible outcomes for Boston’s streets and infrastructure projects.
By way of reminder, the Boston Public Works Department directs the general construction, maintenance, and cleaning of approximately 802 miles of roadways throughout the City. It also operates two major drawbridges, maintains 68,055 City-owned street lights, and supervises contracts for the removal and disposal of approximately 260,000 tons of solid waste. The Public Works Department also operates Boston’s recycling program with an annual diversion of approximately 44,000 tons. The City of Boston’s Transportation Department plans, builds, maintains, and operates the City’s streets in a manner that increases access to opportunities, promotes safety and resilience, and fosters the highest quality of life for everyone living, working, and visiting the City.
As with all procurement processes on the state or local level, a blackout period begins once a bid is officially posted. During this time, the City of Boston’s Streets Cabinet can only answer questions through their official
bid procurement process. All relevant information will be publicly available through the official bid posting in our online supplier portal, which ensures a fair and transparent bidding process for all potential vendors.
To learn more about the City of Boston’s Streets Cabinet Procurement Preview, please visit: https:// www.boston.gov/government/cabinets/streets-cabinet/streets-cabinet-procurement-look-ahead.
continued on page 9
IF YOU LIVE FOR IT, WE’LL HELP YOU PLAN FOR IT.
Patrick Di Cerbo CFP®, MSFS Wealth Management Advisor 518-281-8200 pat.dicerbo@nm.com www.patdicerbo.com
As reported by a press release from the Massachusetts Department of Environmental Protection (MassDEP), the Healey-Driscoll Administration announced $825,000 in grants to the Towns of Barnstable, Brewster, Chatham, Dennis, Falmouth, Mashpee, Wellfleet and Yarmouth. These grants will support projects aimed at reducing nitrogen pollution, which mostly comes from wastewater. Nitrogen can cause serious problems in the water, such as harmful algae blooms that can affect both the environment and public health. The MassDEP selected these projects to help the towns meet compliance with the state’s updated Title 5 and Watershed Permitting regulations, which took effect on July 7, 2023.
Massachusetts Title 5 regulates the design, installation, inspection and maintenance of septic systems and other onsite wastewater disposal systems to protect public health and the environ -
ment, particularly groundwater and surface water quality. MassDEP’s Natural Resource Nitrogen Sensitive Areas (NRNSA) Grant Program enables municipalities on Cape Cod to develop solutions to combat cultural eutrophication, a process driven by excessive nitrogen pollution that leads to harmful algae blooms and degraded water quality. There are currently 31 watersheds across the Cape that have been designated as NRNSAs under Title 5.
The eight recipients of the MassDEP’s NRNSA grants are:
• Town of Barnstable – $37,615
• Town of Brewster – $133,605
• Town of Chatham – $133,500
• Town of Dennis – $175,000
• Town of Falmouth – $94,000
A trusted partner in construction...
For over a decade, RogersGray has been a proud UCANE member, and that commitment continues as we transition to The Baldwin Group. While our name is evolving, our dedication to protecting what matters most remains unwavering—now with even greater resources and expertise.
We’re here to support owners, developers, general contractors, designers, and subcontractors, helping them navigate risk, strengthen their businesses, and achieve their next level of growth. At The Baldwin Group, we’re not just protecting your projects—we’re Protecting the Possible.
Strategic differentiators:
Dedicated Construction Practice Group
Captive and standard market relationships
Our people Service strategy
Trust & transparency
• Town of Mashpee – $65,000
• Town of Wellfleet – $36,280
• Town of Yarmouth – $150,000
The grants were a result of the MassDEP’s efforts seeking proposals from Massachusetts municipalities, or other government entities, that meet the definition of “Local Government Unit,” as defined in 314 CMR 21.02, and have a watershed that has been designated as a Natural Resource Nitrogen Sensitive Area under 310 CMR 15.000, Title 5. The purpose of the grant program is to assist municipalities in a variety of activities which facilitate completion of a Watershed Management Plan (WMP) for the purpose of completing a Watershed Permit application or De Minimis Load application, each of which address solutions to cultural eutrophication caused by nitrogen pollution from wastewater and other sources.
For more information about this grant program, please visit: https://www.mass.gov/info-details/ grants-financial-assistance-watersheds-waterquality#natural-resource-nitrogen-sensitive-areagrant-program.
continued on page 13
Ferguson offers a complete line of products to cover all your water, sewer and storm water management needs, and our relationships with the waterworks industry’s top vendors give our customers peace of mind through unmatched customer service, on-time delivery, and industry leading fill rates.
Canton (781) 828-1350 North Harwich (508) 430-1696 Worcester (508) 754- 2027 ©2014 Ferguson Enterprises, Inc.
The United States Environmental Protection Agency (EPA) Administrator Lee Zeldin, announced that President Donald J. Trump has appointed Mr. Mark Sanborn as the Regional Administrator for EPA Region 1. As Regional Administrator, Mr. Sanborn will lead efforts to advance the Administration's environmental agenda across the six New England states—Connecticut, Maine, Massachusetts, New Hampshire, Rhode Island, and Vermont— and 10 federally recognized Tribal Nations.
According to the press announcement, Regional Administrator Sanborn is a native of New Hampshire, and brings a unique combination of federal and state experience, coupled with experience in the private sector. Mr. Sanford has extensive background in domestic policy, government relations, and project management, spanning both the public and
p rivate sectors. Prior to his appointment, he held key roles in New Hampshire state government, including the Assistant Commissioner of New Hampshire’s Department of Environmental Services and Energy Advisor at the New Hampshire Department of Energy. At the federal level, Mr. Sanford has served in several leadership positions, including Senior Advisor at the U.S. Department of Housing and Urban Development, Chief of Staff at the U.S. Department of Agriculture-Rural Development, and as Director of Governmental and Public Affairs at the U.S. Department of Transportation. He began his career on Capitol Hill working for U.S. Senator Bob Smith of New Hampshire. Mr. Sanford holds a degree in political science from the University of New Hampsh ire.
continued on page 15
NJ: 908-753-8080
Introducing the most powerful Ditch Witch truck vac to ever hit the open road — the Warlock Series W12. With a 2,800 PSI water system, 12 cubic yard debris tank capacity, and a 5,000 CFM, 27″ Hg vac system, this beast-of-a-machine easily devours jobs of all shapes and sizes.
MA: 508-719-0200 Lumberton, NJ: 609-534-7477
NY: 845-831-1800
Park, NY: 631-392-2605 Middletown, DE: 302-376-0784
MD 410-687-1700
Shortly after the appointment of Mr. Sanford was announced, the Conservation Law Foundation (CLF) released a statement expressing concern about EPA resources given potential federal financial cuts. According to the CLF’s press release on the same, “[a]t a time when New Hampshire was being inundated with out-of-state trash, Mark Sanborn worked with waste industry lobbyists to let even more waste in,” said CLF President Brad Campbell, “making him an apt choice for an EPA Administrator and President systematically dismantling EPA’s capacity to protect public health and the environment. Trump’s prior appointees to EPA New England had similar backgrounds but worked constructively with CLF on issues of shared concern; however, it is not clear that Regional Administrator Sanborn will have either the staff or the authority to protect the communities and resources Congress has entrusted to his care.”
continued on page 17
In additional EPA news, the agency announced a newly scheduled public hearing for an updated draft of the general permit for all small and regulated “Municipal Separate Storm Sewer Systems” (MS4s) located in Massachusetts. The draft permit was initially placed on public notice last November. The proposed permit affects more than 260 municipalities in the Commonwealth, all of which were already covered under the previous Massachusetts Small MS4 General Permit that the EPA issued in 2016.
The updated draft of this existing general permit continues to require MS4s to develop, implement, and enforce a “Stormwater Management Program” designed to control the discharge of pollutants from stormwater to water bodies, to the maximum extent practicable, protect water quality, and satisfy appropriate requirements of the federal Clean Water Act.
The EPA will hold a virtual hearing for the Draft
We improve the lives of our partners, and our family by going beneath the surface to build America’s essential infrastructure.
While we’re capable of taking on any trenchless construction project across the U.S., we’re bestsuited for the hard jobs no one else wants to touch.
We are proud to offer an array of trenchless construction methods to choose from to perfectly fit every job. Partner with us on your next project.
Jack and Bore
Hand Mining
Micro-tunneling
Conventional Tunneling
Horizontal Directional Drilling
Rehabilitation
Permit on May 7, 2025 at 7pm. Registration for the virtual public hearing can be completed at https:// www.epa.gov/npdes-permits/massachusetts-smallms4-general-permit#2024draftmams4gp. As detailed by the EPA, rainwater that falls on hard surfaces, such as parking lots, roadways, and roofs can pick up pollutants that are then carried into local waterways via the storm drains, pipes, and ditches that make up municipal storm sewer systems. Stormwater runoff flows over these hard surfaces directly into storm drains so there is no opportunity for soil and plants to absorb the rainwater and filter out pollutants. Pollutants lead to water quality issues (such as growth of harmful algae and bacteria and accumulation of trash, oil and grease, and metals) that can make waters unsafe for swimming and boating and can harm aquatic life.
The requirements in the Draft Permit largely follow or build on the requirements of the currently ef-
continued on page 19
Update continued from page 17
fective 2016 MA MS4 Permit. It also includes new requirements to expand public engagement, develop street design standards that feature nature-based solutions, develop an integrated system to track MS4 assets and maintenance, begin implementing plans developed under the 2016 Permit to install controls to treat stormwater runoff on permittee-owned property, and begin upgrading catch basins to better control solids in stormwater runoff.
The Draft Permit requires municipal permittees that discharge to nutrient-impaired waterbodies to begin installing stormwater treatment based on the Source Identification Reports developed under the 2016 Permit. Finally, the Draft Permit proposes a new requirement for permittees discharging to waterbodies in the Mystic River watershed to reduce the phosphorus load in stormwater discharges from hard surfaces by twenty-percent (20%) within six years.
EPA encourages and will accept written comments from the public on the Draft Permit during the notice period which ends May 21, 2025. The Draft Permit and associated documents are available at https://www.epa.gov/npdes-permits/massachusettssmall-ms4-general-permit.
continued on page 21
Custom Structures
With a track record of excellence and positive outcomes, our nationally recognized Construction & Public Contracts practice is committed to delivering results for you and your business. We understand construction and our clients’ needs and businesses. Our experienced attorneys thrive on addressing complex challenges by leveraging their extensive industry knowledge, partnering with industry leaders, and participating in a vast network of professional affiliations.
Our comprehensive suite of services includes contract analysis, drafting, negotiation, procurement and bid protest issues, strategic project advice, crisis management, claims preparation, prosecution and defense, and all forms of dispute resolution, such as mediation, arbitration, litigation, and appeals. We also assist with compliance and investigations, OSHA investigations, insurance recovery, and risk management.
We can help you navigate any phase of your project and protect your interests through practical advice and effective legal strategies.
On March 11, 2025, during the Massachusetts Building Trades 106th Annual Convention in Springfield, Governor Maura Healey signed an executive order promoting the use of Project Labor Agreements (PLAs) for large public works (i.e. exceeding $35 million) projects managed by state agencies. This initiative aims to ensure that construction projects are completed on time and within budget.
A PLA is a collective bargaining agreement between contractors and labor organizations that establishes the terms and conditions of employment for all contractors, subcontractors, and craft labor employees working on a specific construction project. Such agreements are designed to ensure a diverse workforce while maintaining competitive costs and project timelines. While some studies have found that PLAs do not add costs to construction projects, others have found that they, in fact, increase costs.
The executive order requires executive department agencies to review public works construction projects with estimated costs exceeding $35 million to determine if a PLA is in the best interest of the project, the workers, and the community. This
analysis will consider factors such as scope, complexity, proposed schedule, site conditions, and the size and nature of the required construction workforce. In her announcement, Governor Healey emphasized the importance of setting up these critical construction projects for success by ensuring that contractors have a trained and ready workforce, a plan for meeting deadlines, staying within budget, and maintaining safety standards.
While the executive order has received support from labor leaders and community organizations, a variety of organizations highlighted that PLAs can constrain competition and drive-up costs by requiring union labor, thereby shrinking the field of potential bidders. The executive order, which shares the same process, and in many ways mimics language within last session’s economic development bill, is not a mandate to enter into a PLA, but a requirement for state awarding authorities to conduct the analysis for those projects exceeding $35 million.
To review the executive order, please visit: https:// www.mass.gov/executive-orders/no-641-using-project-labor-agreements-to-promote-successful-delivery-of-major-projects.
• Extension Passed for Hybrid and Remote Public Meetings. In late March, Governor Healey signed Chapter 2 of the Acts of 2025, An Act Extending Certain COVID-19 Measures Adopted During the State of Emergency. This legislation will permit state and local public bodies to conduct public meetings in a hybrid or remote format while also allowing participants at town meetings to participate remotely. Earlier this year, Governor Healey and Lieutenant Governor Kim Driscoll proposed the Municipal Empowerment Act, which would make hybrid and remote access to public meetings permanent. To view the updated law, please visit: https://malegislature.gov/Laws/SessionLaws/ Acts/2025/Chapter2.
• Beverly To Spend $7.5 Million On New Water Meters. The Beverly City Council approved the borrowing of funds to get ahead of potential cost
increases as a result of threatened federal government tariffs. City officials stated that Beverly residents and business owners should expect to pay an additional ten percent (10%) for water and sewer service in 2026, in part, because of $7.5 million in new water meter purchases and installation designed to more accurately measure water use and to replace aging meters that no longer report accurately. Costs directly related to the new meters will likely result in a 3.37 percent increase in 2026 and a 2.87 percent increase in 2027, and combined with other projects and expenses, could raise rates about ten (10%) percent. The new meters are expected to have a useful lifespan of 15 to 20 years. As reported by the Beverly Patch, even with the increases, the City of Beverly would remain on the lower end of water and sewer rates compared to neighboring communities. n
At C.N. Wood, we’ve been empowering contractors with top-tier CemenTech volumetric concrete equipment for over 60 years. Whether you're constructing a sidewalk in front of an office park or working on other commercial projects, CemenTech’s flexibility and precision ensure the job gets done right, on time, and with minimal waste.
CemenTech's volumetric mixers provide on-demand, custom concrete, making it easy to adjust mix designs and quantities as the job progresses. From busy office parks to urban environments, you can deliver the exact amount of concrete needed without delays or excess, keeping your project on track and your clients satisfied.
Following his graduation from Suffolk Law School, where he earned his Juris Doctorate, Senator John Velis returned home to Western Massachusetts where he began working in public service at the Hampden County Superior Court and State Treasurer’s office. However, one of his first experiences in government was as a member of the City of Westfield’s Commission for Citizens with Disabilities. During this time, he got to see first-hand how government can truly make a meaningful difference in the lives of community members, and it helped motivate him to see what other ways he could further serve his community.
In 2014, he was elected to the Massachusetts House of Representative, where he had the honor of representing his hometown of Westfield in the Massachusetts legislature for the first time. Over the next six years he served as a member of the 160 member chamber where he authored his first piece of legislation that was later signed into law, the “Stolen Valor Act.” During his time in the House, he began to meet folks from all over the state because of his strong advocacy on veteran and service member issues.
However, while it was an absolute privilege serving in the House, he knew he could be a more effective lawmaker as a member of the Senate. That is why in 2019 he jumped at the opportunity to run for the open State Senate seat that represented not only Westfield but 10 other local communities in Western Massachusetts.
As costs continue to rise and federal aid decreases, please give your thoughts on how the state will continue to support local aid to cities and towns to help support basic municipal services, specifically water, wastewater, and underground utility infrastructure.
A:
Every day I hear from constituents about how increasingly difficult it is becoming for them to afford even some of their basic necessities. My guiding north stars this session are two things that I feel are incredibly intertwined, affordability and competitiveness. If we do not remain a place where people would like to move to or stay, we are going to have some very real problems beyond what we are anticipating now.
Tied to all of this is our responsibility to our partners in municipal government and to our constituents to find ways to continue to support the basic services that we all rely on, like clean water and reliable utilities. While there will undoubtedly be tough decisions ahead, investing in these services is paramount to ensuring our Commonwealth remains competitive and that costs are kept down for constituents.
Representing the Hampden and Hampshire District which is comprised of the cities of
Holyoke, Agawam and Chicopee as well as the towns of Montgomery, Russell, Easthampton, and West Springfield, among others, what are the biggest challenges for your district and the accompanying region with regards to continued economic growth?
One of the incredible aspects of my district is just how diverse it is, with some very urban communities like Holyoke or Chicopee, and small rural Hilltowns like Montgomery or Russell. This provides me with what I feel to be a unique perspective when it comes to the challenges that our region and state faces, whether that be access to transportation, housing, education, or more generally with cost of living.
I truly believe Western Massachusetts has been under-valued for too long. Put simply we have so much to offer our Commonwealth. With access to affordable properties and land, some of the best universities in the nation, and an eager workforce, the opportunities are endless. I am proud of the initiatives that I have played a part in over the last several years that are going to be economic drivers for our region for years to come, including a provision incentivizing data centers in the last session’s Economic Development Bill and the recent assignment of the
continued on page 25
For over 75 years, Shea Concrete Products has proudly served the New England construction market by providing industry leading product quality and service to our customers and industry partners. Our robust product line of precast concrete products provides solutions for all project types and our truck fleet ensures on-time delivery.
F-35s to the 104th Fighter Wing in Westfield.
The #InvestInWaterMA campaign, sponsored by UCANE, highlights the importance of water infrastructure to a wide variety of industries. Can you share a sampling of some of the specific industries in your district that benefit from our investments in water infrastructure?
Everyone deserves access to clean and reliable water, that is something we feel strongly about back in my hometown of Westfield. For nearly a decade Westfield has been seriously investing in its water infrastructure ever since we learned of the dangerous levels of PFAS contamination impacting our drinking water. More and more I have heard from colleagues around the state that have communities just learning about PFAS levels, the impact it has locally, and the serious investment it requires to remediate to prevent further health consequences.
Beyond this investment in our water infrastructure as it relates to PFAS mitigation, investing in water infrastructure also plays a major role in how our Commonwealth addresses the housing crisis. Last session we passed an ambitious housing bond bill that is going to do a world of good. However, for many
communities this means expanding their infrastructure to accommodate the new demand that these new homes will put on these resources. I hear about this often, from my small communities to my more urban communities, about how their aging infrastructure was simply never made to meet such demand.
With your background in the military and strong record of support for veterans, will you share your thoughts on how the construction industry might be able to meet its growing workforce needs as older members of the industry retire?
We have an incredibly skilled Veteran workforce. All too often when service members return to civilian life their extensive resumes are not fully understood by employers, leading many to become “under employed.” I really think those in the construction industry, and truthfully all employers, should foster relationships with our various military installations around the Commonwealth and every municipality's Veteran Service Office to better be able to greet those returning to civilian life and to share the opportunities that are available to them if they were to pursue a career in the construction industry.
Please share some of your legislative or regulatory priorities for the 2025-2026 legislative session?
Whether you operate heavy equipment or use handheld tools, when you dig, you risk contacting natural gas pipelines. Use these tips to stay safe:
• Notify 811 well in advance of digging or moving earth in any way – even for small jobs
• Respect the locate marks and follow them when digging.
• Dig with care in the vicinity of underground natural gas pipelines.
• If you find an unmarked or mismarked line, stop digging and notify 811
• Report any suspicious activity near a natural gas pipeline marker.
• Don’t rely on your nose alone. Be alert for the many warning signs of a natural gas leak.
• Know what to do if your equipment contacts a natural gas pipeline.
To report a gas emergency, call 911 and National Grid immediately
Massachusetts 911 and 1-800-233-5325
Rhode Island 911 and 1-800-640-1595
New York
Long Island and the Rockaways: 911 and 1-800-490-0045
Metro NY: 911 and 1-718-643-4050
Upstate NY: 911 and 1-800-892-2345
For additional safety information and materials, visit ngridsafety.com and connect with us on
Affordability without a doubt sits at the very top of my priority list this session. Focusing on the issues that most directly impact constituents, the ones that folks are talking about each evening with their loved ones over the kitchen table, that’s what I am hearing and want to focus on. I think in some ways we need to do a better job at advocating for the middle class, especially during this specific time where there is so much uncertainty and costs are rising so drastically.
This session I was honored to be reappointed as the Senate Chair of the Joint Committee on Mental Health, Substance Use, and Recovery, as well as Senate Chair of the Joint Committee on Veterans and Federal Affairs. Last session we were able to send some tremendous bills to the Governor’s desk from each of these committees and I am looking forward to building upon that momentum. This session I really hope to tackle legislation to support our young people, many of whom are experiencing a true crisis as it relates to mental health. As it relates to our service members, I want to continue to expand support in the Commonwealth for military families, a key criteria considered by the Department of Defense when they are looking at further investments in our state’s military installations. n
BRAINTREE
150 Grossman Drive Suite 200
Braintree, MA 02184 (617) 773-9200
LEXINGTON
238 Bedford Street
Lexington, MA 02420 (781) 861-1800
PIPE RENEWAL OR REPLACEMENT, MANHOLE REHAB
• Geopolymer Lining
• Pipe Bursting
• Manhole Rehabilitation
PIPE RELINING
• CIPP Lining
• UV CIPP Lining
• Slip Lining
• Clean & CCTV
Serving the municipal and industrial markets, you can count on Vortex Services Northeast for end-to-end trenchless rehabilitation services!
INSPECTION, CLEANING & ASSESSMENT
• Multi-Sensor Inspection
• Specialty Cleaning
GROUTING
• Leak Stoppage
• Soil Stabilization
• I&I Prevention
Construction & Public Contracts Group, Hinckley Allen, LLP
The United States Department of Justice (“DOJ”) recently announced a $4.6 Million settlement with a federal defense contractor for alleged “cybersecurity fraud” in connection with Department of Defense (“DOD”) contracts. According to the DOJ, the contractor allegedly violated the False Claims Act by seeking payment on federal contracts despite knowing that it was not in compliance with contractual cybersecurity requirements.
The case arose out of a whistleblower action. According to the settlement, the Defense Federal Acquisition Regulation Supplement (“DFARS”) requires DOD “contractors and subcontractors to provide adequate security on all covered contractor information systems . . . .” In addition, the settlement agreement noted that DFARS provides that any DOD contractor or subcontractor that “‘intends to use an external cloud storage provider to store, process, or transmit any covered defense information’” in connection with the performance of a covered contract “‘shall require and ensure that the cloud service provider meets’” certain applicable security requirements. These include requirements relating to “cyber incident reporting, malicious software, media preservation and protection” and “cyber incident damage assessment.”
According to the settlement agreement, the contractor allegedly used a third-party company to provide “software-as-a-service” hosting of its emails “without requiring and ensuring” that the third party met applicable security requirements. In addition, the contractor allegedly did not implement applicable cybersecurity controls which could give rise to various security risks. The contractor allegedly knew that it was not in compliance with applicable cybersecurity requirements.
Nevertheless, according to the settlement, the contractor allegedly submitted claims for payment
to the federal government in connection with federal government contracts over a 5-year period. The settlement agreement stated that “[t]he United States contends that those claims for payment were false or fraudulent” allegedly because of the contractor’s knowledge of its cybersecurity shortcomings.
The contractor agreed to pay the United States $4,6 00,000.00 plus interest. Half of this settlement amount was designated as “restitution” in the settlement agreement. The settlement agreement further provided that the United States shall transfer 18.5% of the settlement payments to the whistleblower ($851,000.00). The settlement agreement further required the contractor to pay approximately $200,000.00 to the whistleblower’s legal counsel to cover expenses, attorneys’ fees, and costs.
continued on page 31
According to the DOJ, “[F]ederal contractors must fulfill their obligations to protect sensitive government information from cyber threats.” Another government official added that “[f]ailure to implement cybersecurity requirements can have devastating consequences, leaving sensitive DOD data vulnerable to cyber threats and malicious actors.”
With advancing technology comes increased cybersecurity risks and – depending on the contract – increased cybersecurity-related requirements. Contractors that use third-party technology – such as document management systems, email systems, cloud-based storage and hosting systems and the like – should be mindful of the cybersecurity risks associated with the use of such systems. Contractors performing work under government contracts should be sure to adhere to applicable cybersecurity requirements and take active steps to determine whether they are in compliance with those requirements. Beyond the various risks associated with unauthorized access to and disclosure of data and information, failure to implement appropriate cybersecurity controls can lead to other potentially adverse consequences, such as the risk of False Claims Act exposure, as in this case. n
Gary Moran MassDEP Deputy Commissioner
OFred Laskey MWRA Executive Director
n March 25, at the Sheraton Four Points Hotel in Norwood MA, UCANE held its 13th Annual Trade Show and Forecast Dinner Meeting, which was attended by over 310 members and guests. There was a familiar and welcoming “buzz” in the air from the moment the crowd began arriving at 4:30 p.m. to attend the Trade Show which was being held prior to dinner. (See related article on the Trade Show starting on page 64.)
Once-again we were able to get our partners at MassDEP, MWRA, and BWSC to volunteer their personal time to show UCANE members what their respective Capital Improvement Programs will look like in 2025 and beyond. The keynote speakers for the evening were Massachusetts DEP Deputy Commissioner, Gary Moran; Massachusetts Water Resources Authority (MWRA) Executive Director Fred Laskey; and Boston Water & Sewer Commission (BWSC) Chief Engineer John Sullivan. Each of these leaders would be providing a power point presentation showing the construction projects that our contractors can expect to be bidding on in 2025 and into 2026.
John
Sullivan,
P.E.
BWSC Chief Engineer
Following a delicious dinner served by the attentive and friendly Sheraton Staff, UCANE President Brian Cooney (C. C. Construction, Inc.) took to the podium and welcomed everyone to UCANE’s Annual Trade Show and Forecast meeting. He thanked longtime member C. N. Wood Co., Inc., Gerry Carney, Jr., and the Benard family for once again sponsoring this year’s event. Brian then welcomed our public agency guests and thanked them for their continued partnership of working together with UCANE contractors to design and build the critical water and sewer projects that improve the quality of life for all Massachusetts residents. Finally, Brian thanked UCANE members for attending tonight’s meeting and for their continued support of our Association and wished them all a safe and prosperous 2025 construction season.
UCANE Executive Director Joe Nolan then took to the podium and introduced several company representatives from our newest members who were recently voted into UCANE and who were in attendance:
Kyle Fonseca, Blue Collar Customs; Angela Sanchez, Merge-Tek; Isaiah Bean and Sophia Holmes, Vortex Companies; Jessica Drugan, Wendell Richardson, and David Capobianco, Rutter Networking Technologies; and John McGrath, Methuen Construction Company.
Joe also introduced several representatives from the Boston Public Works Department who were in attendance to see how the upcoming water and sewer projects might be impacting Boston’s Street Department: Julia Campbell, Deputy Chief of Streets; Norman Parks, Assistant Public Works Superintendent; and Bob Estrella, Public Works Civil Engineer
Joe then began the evening’s program by introducing our featured guest speakers.
The first was MassDEP Deputy Commissioner Gary Moran. Gary is a Mansfield native who graduated from Stonehill College and the Harvard Kennedy School. Gary has had ever increasingly responsible roles at MassDEP over his 30-year career and is currently the Deputy Commissioner handling Operations and Environmental Compliance. He oversees the Boston DEP Headquarters, as well as the four Regional DEP offices, and reports directly to MassDEP Commissioner Bonnie Heiple.
Mr. Moran told the audience that this year’s application list from Massachusetts cities and towns for State Revolving Loan Fund (SRF) Assistance was once again strong for both water and sewer projects. The Final IUP (Intended Use Plan) was delayed a bit due to the late passage in Washington of the six month CR (Continuing Resolution). The Final IUP list is due to be released next month, but projections for funding capacity indicate they may possibly be 2025% below the peak levels of loans seen in 2024. The reasons are two-fold:
1) Federal funds from the 2021 Federal Bi-Partisan Infrastructure Law (BIL) are beginning to wind down, and
2) MassDEP took a conservative approach to Federal funding availability beyond the six month
CR. The current administration is seeking to lower the federal budget and EPA is anticipating that their agency, like many others, will also see some reduction in funds
On the Drinking Water side, the SRF received 42 new project applications with a total financing request of $648 million. The SRF funding capacities for 2025 for Drinking water is estimated to be $346 million.
On the Clean Water side, the SRF received 75 new applications with needs of $1.3 billion. The SRF is estimating a funding capacity in 2025 of $845 million towards Clean Water projects.
A good portion of the available SRF funds will continue to be available at 0% interest, and others are eligible for loan forgiveness in varying rates up to 19%.
MWRA Executive Director Fred Laskey, accompanied by his key staff in the operations and construction divisions, then began his remarks and slide presentation. Mr. Laskey is in his 24th year of leading the Agency that provides drinking water to three million people in 61 Massachusetts Cities and Towns, as well as sewer treatment for two million residents living in 43 communities. It was noted that 2025 marks MWRA’s 40th Anniversary of the establishment of
the Agency that, along with DCR (Department of Conservation and Recreation) took over the operations of the old MDC (Metropolitan District Commission) in 1985.
Mr. Laskey began by highlighting multiple important sewer and water projects on the screen in various stages of construction being performed or recently completed by UCANE member contractors. He recognized UCANE contractors for their skilled performance and professionalism. He also thanked our Association for their constant efforts in support of Water Funding and a healthy environment which, according to Fred, has often helped to make his job a little easier. He also congratulated UCANE for putting on an impressive Trade Show prior to the dinner and expressed MWRA’s deep appreciation for the collaboration and “Open Door” policies that have marked the long relationship between MWRA and UCANE.
The breakdown of water and sewer projects currently being designed as part of the MWRA’s 5-year Capital Improvement Plan was quite extensive and of great interest to our attendees. The CIP for FY25 and FY26 is valued at $687 million incorporating 37 construction projects. Fred produced an impressive bar chart showing that over the next 5-year period, MWRA’s Capital Improvement Budget will average $505 Million per year. That compares with the prior five years (2019-2024), where capital expenditures averaged $165 million/year. Although not all expenditures represent UCANE contractor work, a majority of each year’s expenditures do. The numbers were
obviously well received by the UCANE audience and showed once again MWRA as the dominate force in the procurement of water and sewer infrastructure in the Commonwealth. (See the MWRA list of 2025 projects on page 41.)
Mr. Laskey reminded the audience that the Authority not only has award winning water quality, but they also have excess water capacity and they are actively exploring partnerships with new communities experiencing increased water demands. MWRA continues to do in-depth studies of expanding their water network toward the Ipswich River Basin, the South Shore area, and to MetroWest. Each preliminary plan involves miles of new pipelines and 10 to 14 new pump stations per area. Those expanded drinking water areas coupled with the Metropolitan Tunnel Redundancy Project, (nearing final design), assures local contractors of work for many years to come.
Fred ended his presentation by announcing that Chief Operating Officer Dave Coppes will be retiring from the MWRA this summer after a 32 year career with the Authority. Mr Coppes got a warm round of applause and appreciation from the UCANE audience. (See Dave Coppes profile on page 45.)
The final speaker of the evening was John Sullivan, BWSC’s Chief Engineer, certainly no stranger to most of the audience, or to anyone who relies on water or sewer service in the Boston and Greater Boston area. John’s agency is tasked with distributing MWRA’s award winning drinking water to about one continued on page 37
million people living and/or working in Boston on a daily basis. In exchange, John sends about 75 MGD (million gallons/day) of raw sewage to the MWRA for treatment and disposal. Although John’s agency builds and maintains both the water and sewer distribution systems, there was some (good-natured) disagreement between Fred and John over who is getting the better deal in the liquid exchange.
With over 50 years of experience working for, and leading BWSC, nobody knows the history of Boston infrastructure, or what pipes lie beneath Boston’s 950 miles of streets, better than John Sullivan. John is a nationally recognized voice for the Public Works Sector, and particularly for municipalities that own and manage water and sewer systems. His expertise has been called upon for advice by municipalities across the country including Flint, Michigan. He is a gifted speaker as any UCANE member who has attended prior Forecast Meetings can attest.
Despite being one of the oldest Cities in America and having one of the earliest sewer and water systems, BWSC is a model for other cities on how to maintain their water and sewer infrastructure. Through an aggressive 30-year construction program, BWSC has been able to not only keep up with
population growth and aging infrastructure, they have actually improved their overall systems. As a quasipublic commission, BWSC is one of the few agencies that is consistently able to fund a large percentage of their own upgrades, rehabilitations, and new installations every year. In 2024, BWSC boasted the fewest water breaks per mile of pipe for any city in the U.S.
As in past years, John presented a detailed list of projects ready to go for this season. As usual it was an impressive list. John pointed out that there are 13 various sized water and sewer projects on-going throughout the City at various stages of completion. Originally valued at a combined total of $168 million, the projects have about $70 million in work left to complete. Interestingly, 100% of the 13 projects are being performed by eight different UCANE Contractors.
The new projects coming out to bid in 2025 included 18 separate projects valued at $134 million. Project locations, descriptions, bid dates, and estimated contract values were presented to an “all-ears” audience. The projects will replace or rehabilitate about 13 miles of water and about 15 miles of sewers and drains. (See the BWSC upcoming projects listed on page 43.)
continued on page 39
Mr. Sullivan also talked about the planning that Boston has been doing over the past five years to predict and address future flooding in portions of the City predicted to be caused by severe storm events (Climate Ready Boston). Through historical measurements there is no doubt that the high tide levels in Boston are slowly increasing and that the frequency of severe storms is increasing. BWSC has recently been tasked with reviewing some Climate Ready Boston models, and Mr. Sullivan recommended that attendees go to the BWSC website and the Climate Ready Boston website to view some startling information relative to potential flooding impacts to the City by future severe storm events. The scope and costs of resiliency projects necessary to protect vulnerable portions of the City have not yet been finalized, but Chief Engineer Sullivan expects that resiliency projects will soon be arriving in the City and they are hopeful to be in line for Federal and State funding sources of all types to assist the Boston ratepayers.
The presentations by our three guest speakers were certainly eye opening and well received by all attendees. The volume of water and sewer work coming out to bid in both the short term and the long term was overall good news for UCANE contractors
and Associate members as well.
Executive Director Joe Nolan thanked the speakers for their informative presentations and thanked them again for their dedication and contributions to the water and sewer industry on behalf of UCANE and on behalf of all the citizens of Massachusetts. n
At UCANE’s Forecast Meeting, Executive Director Fred Laskey announced that MWRA would be losing Chief Operating Officer David Coppes to retirement at the end of June 2025. David, who has been a familiar face to many UCANE members over the years, attended our Forecast Meeting and received a warm congratulatory applause from the audience.
After graduating with a Civil Engineering degree from Cornell University, Mr. Coppes worked for the Peace Corps Service building rural water projects. He then worked at engineering firms E.J. Flynn and Fay, Spofford & Thorndike. In 1993 he accepted an engineering position with the MWRA and held various engineering positions within the agency. Mr. Coppes was promoted to Director of Western Operations in 2002 which included the operation and maintenance of MWRA's transmission and treatment systems. He also assumed the role of liaison to DCR's Department of Watershed Management, including operation of the Quabbin and Wachusett Reservoirs
From 2014 to 2018 Mr. Coppes served as MWRA’s Director of Waterworks, responsible for all aspects of water operations throughout the vast MWRA system. In 2018 David accepted the position as Chief Operating Officer. As COO he is responsible for all waterworks, plus sewerage operations and service delivery; planning, design, construction and start-up of capital construction projects; leadership within the operating areas to achieve cost effectiveness; and support for MWRA's objectives of financial and program accountability.
Mr. Coppes is a Registered Professional Engineer and holds a 4D Water Distribution license and a 2T Water Treatment license. He has served and continues to serve on several local, state, and national committees.
David and his wife Amante reside in Stoneham and are looking forward to their well-earned retirement, where they intend to increase their sailing hours and do some traveling.
UCANE thanks David for all of his dedication and contributions to the public works industry and to the Commonwealth. Our Association and its members also appreciate the open communication and objectivity that marked his tenure. We wish him the very best in his upcoming adventure! n
Wales Avenue-Rear Avon, MA 02322
Office: 508-583-2029
Plant: 508-587-6953
226 Nicks Rock Road Plymouth, MA 02360
Scale House: 508-732-9148
Asphalt Plant: 508-732-9140
Will you please give us some information on your background and tell us how you got started in the construction business?
My father and four of my uncles emigrated from Italy and started P. Gioioso & Sons in 1962. As the son of a construction company owner, I guess you might say that I was basically born into this business. I literally remember driving around with my dad as early as age five. He would take my brother Gino and I during school vacations and during the summer to spend time with him “on the job”- and that served as our vacations for many years. The most memorable part was that he would always take us to Friendly’s for lunch, which was great.
But from an early age there was no real question as to what I was going to do for a living. My brother and I have been basically living this family business every day since we were kids, so the construction business was a natural progression for the both of us. The early years were similar for my cousins, who are my partners in the company today.
Before I got fully immersed at the company, I attended Springfield College where I obtained a degree in Business/Finance. I came up through the ranks as a second generation Gioioso and at one time or another I have had just about every job title one could have in a family business. Today the second generation is running the business and all of us are hands-on owners that still wear lots of different hats.
Please tell our readers what types of construction your firm specializes in, and in what areas of New England do you pursue this work.
We are basically a Heavy Civil contractor specializing in Public Works. We do utility pipe work, road work, bridges, sheeting and pile work, concrete forming and pouring, marine work, pumping stations, duct bank installations, some track work, and anything else that we can be low bidder on. We do most of our work in Massachusetts, but have gone to other New England states if the project is right for us.
Operating a successful Heavy Construction business in New England has always been subject
continued on page 49
COMPONENT
to a variety of challenges. What aspects of the business do you see today that are challenging your company’s growth or bottom line?
New England is a very special place for a public low bid contractor. There has always been a lot of competition from many great companies and if you don’t work hard and pay attention, they will out-work you and it will be tough to stay competitive. I don’t feel like the rest of the country has the level of competition that we deal with in Massachusetts. The biggest challenge I feel for all contractors is our aging work force. If you drive by any construction crew pretty much anywhere in this state, you are sure to see a lot of grey hair. We need to get the young workforce into this industry and train them properly for future generations.
The last few years has seen a substantial increase in both Federal and state funding towards public infrastructure, in particular water and sewer projects and horizontal construction in general (roads and bridges). Looking ahead, how do you see the New England heavy construction market shaping up for 2025-2026?
It seems like there has been a good amount of work over the last four to five years for all of our members. I feel like the next couple of years should be as good, but with all this Federal spending that has been going on for this long, I am afraid that the well might start to dry up, especially with changes happening in Washington. The
need to maintain clean water, and maintain and upgrade other horizontal infrastructure, is certainly still a serious public concern for Massachusetts, as well as the entire country. I think it will be critical this year for our industry to get loud and promote the important work we do and the need to keep funding going to maintain a strong economy.
P. Gioioso & Sons has a long and commendable history with UCANE dating back to 1967. Multiple members of the Gioioso family have served on our Board of Directors, including yourself
Under the Hard Hat continued from page 49 even serving two terms as UCANE President in 2011 and 2012. Why did you offer to rejoin the UCANE Board of Directors?
There is no question that being part of UCANE has served our company well. Supporting an association that promotes and protects our type of work is for the greater good of the industry and it is something that the Gioioso family has long believed in. My family was basically involved in UCANE since its inception and I feel that we wouldn’t be the company we are today without being part of this great organization.
It’s a unique experience where competitors get together and put their competitiveness aside and everyone works for the common good of the industry and for our futures. It’s something that is great to see and something that myself and my family are proud to be part of. We have a third generation of Gioioso’s in the wings, and we look forward to many more years of success being part of UCANE. n
Your Company Must Have A Comprehensive Safety Program!
This year’s Safety Manual includes information on:
• Updated DOL Drug Testing information and Updated CDL information
• Massachusetts Safety Standards - COVID-19
• OSHA’s Final Rule on Silica Exposure Limits
• OSHA’s Final Rule on Improved Tracking of Workplace Injuries and Illnesses
• OSHA’s Final Rule on Confined Space in Construction
• OSHA’s New Requirements for Reporting Severe Injuries
It should be your company’s policy to provide a safe place to work, with the prevention of accidents being your ultimate goal.
Your Insurance/Bonding carrier requires a Safety Program. State and Federal Agencies require a Safety Program.
Inspectors Will Be Enforcing:
• Overall Construction Safety (29 CFR 1926)
• Excavating Standards
• Written Safety and Health Plans
• Hazard Communications Programs
• Drug Free Workplace
• OSHA 10-Hour Training Requirements
When ordering Company Safety Manuals, the Safety Manual section only, in the back of UCANE’s Pocket Directory, will be made up into an individual Employee Pocket Safety Manual with Your Company Name & Logo printed on the cover. Employee signature cards verifying compliance with safety manual procedures are included. When signed, these cards should be placed in each employee’s file.
Company Name:_________________________________ Authorized By:______________________
Pocket Manuals w/ Signature Cards: Qty.__________________ x $4.75 Ea. = $________________
Printing and Set Up Charge for Personalized Covers: $________________ Postage and Handling: $________________ Date:____________ Total: $________________ ❏ Company Logo Enclosed ❏ Company Logo to be mailed ❏ My check is enclosed 65.00 TBD
“UCANE Contractor SPS New England floats 350 feet of 20-inch ductile iron pipe across tidal river before sinking it into a trench below river bottom.”
Based in Salisbury, MA, SPS New England, Inc. recently celebrated their 40th Anniversary in 2024. From a small family business, the company has steadily grown into one of the most successful and dependable public works contractors in the Northeast when it comes to highway, transit, marine, and bridge work.
The Capolupo family - siblings Wayne, Phil, and Karen started SPS with a simple philosophy…offer the customer quality workmanship at competitive prices while completing projects both on-time and safely. Company integrity was also very important from the beginning, and SPS was a sought-after employer where construction professionals and craftsmen alike knew their work would be respected and recognized by the company ownership.
In the early years SPS bid mostly on small municipal road jobs running with about 20 employees. According to company CEO Wayne Capolupo, “Much of our early work was done as subcontract work, but it wasn’t long before our expertise in building formwork and pouring concrete walls and structures was making us stand out, and we wanted to perform as a GC.”
The company’s first prequalification from MassDOT was received in 1988, which allowed them to bid up to $1.0M on road and bridge work. Throughout the 1990s
the company grew at a manageable pace and could be seen doing roadwork and bridge deck rehab work throughout Massachusetts, New Hampshire, and Maine. By 2000 SPS had grown to 50 employees and was doing a volume of about $20M per year.
In the 2000s, Design-Build began gaining popularity with state agencies and the strength and reputation SPS had built allowed the company to joint venture with prominent design firms and added more and larger successful projects to the SPS resume. When MassDOT made the decision to add a third lane to Route 128 (95) in 2004, that began almost 10 years of steady work for SPS doing bridge deck rehabs, widenings, and new bridge construction, working alongside large GCs like McCourt Construction Co., Barletta Heavy Division, J. F. White Contracting Co., and Bond Brothers.
Since many bridges that SPS worked on were built over water, that necessitated the company to develop a marine division so that they could self-perform that element of bridgework. In 2010 the company expanded and bought their own 6-acre yard and high-quality marine terminal on the Island End River in Everett, MA, off the Mystic River, with a deep-water port linking directly to Boston Harbor. The terminal includes a newly-constructed modern bulkhead, 700 linear feet of wharf, and access to a rail spur, making it a truly unique facility with numerous
options for moving heavy cargo by water, rail, or highway in and around Boston and the New England region. SPS has the ability to load or unload cargo with hoisting capability up to 200 tons with its own Manitowoc 4100W lattice boom crane located on-site at the facility.
In recent years, SPS has put their signature on some of the most prominent transportation projects in the New England area including Logan Airport, I-495 Bridge Replacement over the Merrimac River in Haverhill, Massachusetts Avenue over Commonwealth Avenue in Boston, I-95 Bridge at Dedham Street in Canton, and the Lechmere Viaduct in Cambridge.
“We have come a long way since 1984,” says company Treasurer, Clerk, and HR Manager Karen Capolupo Douglas. “We are proud of our achievements that would not have been possible without our dedicated employees who we think are the best in the business.” The Capolupo family showed their deep appreciation to their employees by establishing SPS as an ESOP Company (Employee Stock Ownership Plan) in 2023.
According to company President, Phil Capolupo, SPS takes great pride in their Design-Build capabilities. They are comfortable bidding large projects solo or in joint venture as performed with fellow UCANE contractors like Walsh Construction Company, D. W. White Construction, Inc., and McCourt Construction Company on recent projects. “SPS completed its first $100M project in 2022,” says Phil, “and we have multiple large projects in
annual revenues exceeding $100M, SPS New England is poised for the future and bullish on the country’s transportation sector.
SPS New England was the low bidder on this complicated $87M project designed by STV Boston and put out to bid by MassDOT in October 2020. The project’s scope includes the total removal and replacement of a singleleaf Dutch-style bascule bridge, not commonly seen in the United States. The bridge is located along heavily traveled Route 107, spanning over the tidal Saugus River between Saugus and Lynn, MA. All systems necessary for the new movable bridge are included in the project such as: deep foundations, concrete piers, bridge fender construction, bridge abutments, retaining walls, electrical and mechanical systems for the new bridge, and two fixed approach spans.
A bascule bridge is a type of drawbridge that uses counterweights to raise its deck, allowing boats to pass underneath. The terms "bascule bridge" and "drawbridge" are often used interchangeably. Specifications called for the massive steel bridge and the two-million-pound counterweight system to be fabricated and shop tested at a single off-site facility to ensure fit and operation prior to delivery and installation in the field.
SPS New England continued from page 55
Work on the project began in January 2021. SPS assigned veteran supervisors Jack Pecora, P.E. (Project Executive), James Jones (Project Superintendent), and Bill Schurman (Project Manager) to manage the work. Each brings with them impressive resumes and over 30 years in heavy transportation projects throughout the New England area, including prior projects for MassDOT.
Some of the more challenging aspects of the project involved working over the 500-foot-wide Saugus River that was subject to 9-feet elevation swings twice a day due to tidal influence. Maintaining access for boats and commercial fishermen was critical with only minimal temporary blockage to the channel being allowed. For many phases of the demolition and reconstruction, heavy equipment, including cranes, worked off floating barges, or temporary steel platforms created by SPS.
Extensive coffer damming and dewatering was required to allow for foundation work. Sixteen five-foot diameter caissons were drilled 20 feet into bedrock to provide support for the Bascule pier. The pier itself contained approximately 1,000 cubic yards of concrete to support the entire bridge structure when it is in the open position.
At the time of this interview in March 2025, the steel Bascule bridge was in place, the MWRA water main had just been successfully installed across the river, and the project was at about 75% completion. Final completion is estimated to be Spring of 2026. Major elements remaining included building parts of the concrete approach slabs, full depth road reconstruction and drainage on Route 107, and removal of the formidable temporary two-lane Bypass Road and Bridge that has been carrying 6,000 vehicles per day across the river for the last four years.
An old 16-inch cast iron water main, built in the 1950s by the former Metropolitan District Commission (MDC), also crossed the Saugus River at this location. It had fallen into disrepair and was taken off-line by the MWRA in 2010. Both the removal of the old line and installation of the new 20-inch ductile iron pipe was part of the Belden Bly Bridge Project. Although installing the new pipe across the river represented only a small percentage of the overall $87M price tag, the planning and execution for the new pipeline was no less complicated or subject to less risk than other major elements of the project.
(L-R) James Waugh-Outside Sales - F.W. Webb; Jack Pecora P.E., Project Executive-SPS New England; Jeff Houser-Senior Sales Rep. McWane Ductile
MassDOT plans called for a submarine installation of the new pipeline below the bed of the Saugus River, between Lynn and Saugus, MA. The new line would include special bends and fittings, and all pipe and fittings joints were to be fully restrained from pullout. Permits from the Army Corps. of Engineers and the United States Coast Guard required that the new water line be installed four feet below the existing mudline. This required the top of 3.5 ton buoyancy blocks
the pipe to be lower than elevation -21.0 and bottom of trench at elevation -24.0. The Saugus River is tidal in this area, with water elevations rising and falling 9 feet twice a day. The mean high water is at elevation +4.3 and the mean low water elevation is -5.2.
SPS turned to fellow UCANE member, F. W. Webb Company, of Malden, MA to supply the necessary components to complete this crossing. F. W. Webb reached out to partner and fellow UCANE member McWane Ductile, headquartered in Phillipsburg New Jersey, for design and installation assistance, as well as manufacturer for the TR Flex Pipe specified for this project. McWane Ductile, is a family-owned company, established in 1921 and today has 25+ manufacturing facilities across the country, and employees over 6,900 associates. After extensive surveys of the river bottom was completed by SPS, there were multiple site meetings with engineers and designers from SPS, McWane, and F. W. Webb to review the contract documents, observe the site to assess field conditions, to get a better understanding of installation methods, and to determine the exact piping configuration.
According to McWane’s Regional Sales manager Jeff Houser, “I’ve certainly been involved in many complicated pipe installations over my 30-year career, but this project definitely had its share of obstacles and unique requirements. Partnership with local distributor F. W. Webb, SPS New England, and our technical support staff was on full
display in ensuring a successful crossing.”
The final layout utilized 34 feet of 20-inch TR-Flex boltless push-on restrained joint product within the riverbed, and about 576 feet of 16-inch TR-Flex on the land connections on both sides of the river. Nine bends were required to accommodate both grade and direction changes including three EBAA Flex 900 Ball Joints and one EBAA Flex-Tend Single Ball Expansion Joint. All pipe was Class 52 Cement Lined Interior, with Zinc and Seal Coat Exterior. The pipe was specified to be installed with V-Bio Enhanced Poly encasement for the entire crossing.
The first step in the pipeline installation was to excavate the trench below the river bottom. This was performed “in-the-wet” using an excavator working off a barge. With bottom of trench to barge deck distances approaching 30 feet in some locations, SPS utilized a Caterpillar 336F long boom excavator weighing 48 tons attached on top of a 30ft X 80ft sectional barge. To ensure that proper grades were maintained at the bottom of the trench, the excavator was equipped with a GPS guidance system provided by Trimble, Inc.
In December (2023) and January of 2024, the 400-foot-long trench was carefully excavated across the river while still maintaining boat traffic. In early January SPS crews, with oversight and assistance from McWane’s National Product Engineer Ken Rickvalsky, and F. W.
continued on page 59
Industry Expertise: We tackle the unique challenges of dispersed worksites, mobile workforce needs, and strict compliance. Why Construction Firms Choose Rutter Networking Technologies
Advanced Security: Multi-layered strategies protect your sensitive project data and corporate information.
Scalable Cloud Solutions: From Azure Virtual Desktops to cloud backups, our IT infrastructure grows with your business.
Proactive Support: Enjoy uninterrupted operations with our proactive monitoring, maintenance, and 24/7 support.
Construction firms trust Rutter for unmatched IT expertise and comprehensive solutions. READY TO ELEVATE YOUR
SPS New England continued from page 57
Webb’s James Waugh, preassembled and pressure tested three segments of the 20-inch pipeline above ground in preparation for the installation. One section was about 300 feet long and destined for the deepest part of the underwater trench. The other two sections were about 50 feet long each (called riser sections) and contained multiple bends to achieve elevation and alignment requirements in the design layout.
The 300-foot section, empty and capped at both ends, was floated across the river and positioned above the trench area. Each capped end of the floating segment was secured to a small floating platform where the caps at each end were removed. At that point two large cranes, a 150-ton American cable crane, and a 120-ton Liebherr Hydraulic crane, then hoisted the 50-foot pre-assembled segments using strong backs and lowered them down to the water where crews on skiffs connected the two 50-foot riser sections onto each end of the 300-foot floating segment.
When the three segments were assembled together, clean water from a 5,000-gallon standby tanker truck was pumped into the pipeline in order to make the pipe sink into the trench. While the cranes held onto the 50-foot end pieces, with guidance from surveyors and a team of divers from Black Dog Diving Co., and with assistance from the barge mounted excavator, the entire segment was submerged into the trench at the precise planned location. Caps were then placed on the tops of the two riser sections (located above the water) and the pipe was completely filled and pressure tested again.
Because this “float and sink” operation would temporarily block the river’s navigational channel, the Coast Guard only provided SPS with a very short window of time to complete it. “Our window happened to be one of the coldest weeks in the very cold winter of 2024-2025,” says Project Executive Jack Pecora. “Winds blowing 30-40 mph, and temperatures in the single digits made the operation extremely difficult.”
Project Superintendent James Jones credited his crew’s toughness for getting the job done. “It was really bitter conditions to be accomplishing a river crossing,” said James. “Our guys stood up to the elements, worked the long hours to get it done, and I’m extremely proud to work with these guys.” Jack Pecora agreed and added, “SPS has a dedicated group of key foremen, superintendents, and managers. These are the people that make the challenging work possible.”
In the days following the submarine pipe installation, nine 2½ ton concrete ballast blocks, guided by Black Dog Divers, were lowered into position over the ductile iron pipeline, and stone was placed around the pipe with a 110-foot Tele-Belt conveyor rented from UCANE contractor W. L. French Excavating Corp. Concrete manhole sections were positioned as thrust blocks at bend locations on the pipeline risers and then filled with tremie concrete delivered by a 41-meter pump truck. The remaining pipe was then backfilled with the original excavated trench soils.
Later this summer the SPS crews will install, via opencut excavation, the remaining 200 feet of new ductile iron pipe on either side of the bridge and make connections to the existing MWRA mains. This will restore the out-ofservice interconnection and provide much needed redundancy to the drinking water distribution system provided by the MWRA to customers in the Lynn and Saugus area.
UCANE is proud to count SPS
England and the Capolupo family as UCANE Members since 1997. We congratulate them on their many achievements, including the Belden Bly Bridge project and we wish them continued success long into the future! n
• Pre-mark the location of intended excavation using white stakes, paint or flags.
• In MA, ME, NH, RI and VT, notify Dig Safe® at least 72 hours in advance, not including weekends and holidays.
• Notify non-member facility owners.
• Maintain the marks placed by underground facility owners.
• Use caution and dig by hand when working within 18” of a marked facility.
• If a line is damaged, do not backfill. Notify the affected utility company immediately if the facility, its protective coating, or a tracer wire is damaged.
• Call 911 in the event of a gas leak, or if a damaged facility poses a risk to public safety.
• Know your state’s excavation requirements.
• Go to digsafe.com for educational material and current laws.
Michele L. Norton, AAI, CRIS Vice President, Account Executive-Construction HUB International New England, LLC
In recent years, the insurance landscape has experienced a notable transformation, marked in part by the surge in the establishment of insurance captives. No longer confined to captive advisors and consultants, even traditional insurance carriers are developing their own captive products to answer the demand for this alternative.
According to the Captive Insurance Companies Association (CICA), 2024 was a pivotal year for the growth of captives, with an astounding 8,000 around the world, writing a combined total of approximately $50 billion in premiums. This growth has been fueled not only by the challenges posed by a tough economic environment but, also by the ongoing hardened market for traditional insurance products, reductions in capacity and tighter restrictions on coverage. With fluctuating premiums and shifting market conditions, businesses in the construction sector are increasingly turning to captives as a strategic response to manage uncertainties.
The origins of captive insurance can be traced back several decades when businesses sought effective solutions to self-fund and more efficiently control their risks. Over the years, the concept has evolved into a viable means of obtaining insurance coverage at more favorable rates while also complementing existing policies.
In its most fundamental form, a captive is a selfinsurance entity where the insurer is wholly owned by the insured. Group captives operate under a collaborative framework, wherein multiple firms, either from diverse sectors (heterogeneous) or aligned within the same industry, such as construction (homogeneous), join forces to share ownership and operations. This
collective approach not only spreads risk but also fosters a culture of shared responsibility and rights among members and provides greater long-term cost stability.
The construction industry is characterized by its own unique risks, which have become increasingly complex over time. The appeal of captives extends beyond mere risk transfer to encompass several compelling advantages, including significant tax benefits, enhanced cost savings, predictable financial forecasting and the ability to reinvest underwriting profits back into the member company. Property & Casualty captives typically cover essential lines such as Gen -
continued on page 63
MATERIALS AVAILABLE FOR PURCHASE:
• 1” MINUS PROCESSED GRAVEL
• ¾” & 1½” CRUSHED STONE
• SCREENED LOAM
PLANT LOCATION: 200 LEGACY BLVD. DEDHAM, MA 02026 Plant: 617-590-0024
OFFICE: 1039 EAST STREET DEDHAM, MA 02026 Office: 781-329-4111 Fax: 781-329-1039
HOURS OF OPERATION: MONDAY-FRIDAY: 6:30 A.M. – 4:00 P.M. SATURDAY: 7:00 A.M. – 12:00 P.M.
• SCREENED SAND DELIVERIES AVAILABLE ON LARGE ORDERS. PLEASE CALL FOR PRICING.
MATERIALS ACCEPTED:
• BROKEN ASPHALT
• NON & REINFORCED CONCRETE
• CONCRETE WITH WIRE MESH
• ROCK
• BL ASTED LEDGE
eral Liability, Workers’ Compensation, and Commercial Auto insurance. As a member of the captive, owners have purchasing power or a vote in the limit structure, coverages, deductibles, claims handling, risk management and funding of the program, which is especially attractive for an industry where insurance is so closely tied to contractual obligations and the ability to win bids and continue to work.
While captives are an appealing risk financing option, not all construction companies are the right candidates. Contractors considering a captive program should evaluate the following key considerations:
Strong Financial Standing: At its core, adopting a captive strategy is a financial decision. Entities considering this route must possess robust financial capabilities and a solid understanding of self-insurance mechanics. This includes the ability to adequately fund and control losses through appropriate collateral, as well as proficiently manage and invest the premiums that would typically flow to a third-party insurer. A healthy balance sheet and stable cash flow, coupled with sufficient claims reserves, are critical components that bolster a firm's capacity for successful captive ownership.
A Proven Culture of Safety: Establishing an enterprise-wide focus on risk management is fundamental to fostering a safety-oriented culture. This is not only exemplified by implementing comprehensive safety programs that comply with, or even exceed, Occupational Safety and Health Administration (OSHA) standards, but also by maintaining a favorable loss history.
Commitment to Business Continuity: A demonstrated commitment to long-term business viability is essential for prospective captive participants. This includes showing a track record of growth and stability, as well as a forward-thinking strategy that prioritizes reinvestment in both tangible assets and human capital. Key components might include the establishment of an executive succession plan, particularly within family-owned businesses, ensuring operational continuity even as leadership transitions.
For construction firms that possess the requisite financial backing, a commitment to safety and a vision for sustainable growth, the adoption of property and casualty captives presents a strategic avenue worthy of exploration. The tangible value delivered through this model is evidenced by member retention rates soaring as high as 98%, illustrating the effectiveness of tailored insurance solutions in fostering a resilient and competitive industry. As the insurance landscape continues to evolve, group captives are likely to play an increasingly pivotal role in shaping the future of risk management for qualified UCANE contractors. Engaging your broker, at the onset of this process is the best way to ensure that you have the knowledge to make the most informed decision for your business. n
UCANE Contractors and guests descend on the Four Points by Sheraton Hotel in Norwood, MA to see the latest in equipment, technology, and business support offerings from 33 UCANE Associate Members.
On Monday March 25, 2025, UCANE hosted its Annual Trade Show prior to the Forecast Dinner Meeting at the Sheraton Four Points Hotel. Our Trade Show has become a much-anticipated flagship event for the Association and its membership since its debut in 2012. This year representatives from 33 member companies arrived early at the hotel to set up their booths and creative displays highlighting what products or services each company provides to the construction industry.
The UCANE Board of Directors held their March Board Meeting at the hotel earlier in the afternoon, and as they exited the meeting at 4:30 they were greeted to a colorful display of the latest construction products and services hitting the market in 2025. Tables were stretched throughout the wide first floor corridors and behind every table were smiling faces waiting to introduce themselves to new potential customers or, in many cases, to catch up with old friends and clients.
Our Trade Show has been traditionally held on the same day as UCANE’s Forecast Dinner Meeting where some of the most prominent public agencies present their lists of construction projects that will be coming out to bid in the upcoming season. (See related story on Forecast Meeting beginning on page XX). The combination Forecast Dinner Meeting/Trade Show is historically the most well attended of UCANE’s dinner meetings. This year’s event was true to course with over 300 UCANE members and friends in attendance.
Contractors and their guests also arrived early to attend the Trade Show and to enjoy some small talk before the Dinner Meeting. Being successful businessmen and women, UCANE members want to make sure they are up to date with the “latest and greatest” gadgets and equipment in the industry. The Trade Show gives them that opportunity. If they
continued on page 67
c an do it while enjoying a few hors d’oeuvres and a cold drink, all the better!
Complimentary booths at the Trade Show are made available to those members who advertise in our monthly publication, Construction Outlook magazine, as our way of thanking them for their ongoing support. Long recognized as the premier trade magazine in New England, not only for its content, but for its high quality presentation, Construction Outlook can be found on the desks of every UCANE member, every DPW Director in all 351 cities and towns across the state, as well as our State and Federal legislators. It can also be found on decision maker’s desks at dozens of State and Federal agencies that impact the horizontal construction industry.
Construction Outlook can also be viewed on UCANE’s website at www.ucane.com. In addition, our magazine advertiser’s logos are scrolled across the home page of our website, with direct links to our advertisers’ websites at no additional cost. There is no better, or more affordable way to promote your business and your products to the construction industry than through Construction Outlook magazine.
For further information on advertising opportunities and about participating in the 2026 Trade Show, please contact Suzanne at shatch@ucane.com or call the UCANE office at 617-471-9955.
continued on page 69
Advertisers: UCANE extends its sincere thanks to all our Associate members and advertisers who have helped to strengthen our organization by their ongoing support!
Contractors: Please support our Associate members throughout the year whenever possible. When making purchases for your next project, looking to renew a policy, or looking to lease, buy, or rent – please give our Associate Members a chance to earn your business.
UCANE is strengthened when members give other members an opportunity to bid! n
In late 2024, a water main break in MWRA’s Dorchester Tunnel was narrowly prevented from escalating into a full-blown crisis — a close call reminiscent of the 2010 main break that affected 2 million across Greater Boston. This recent incident underscored not only the critical nature of MWRA’s expertise and rapid response but also the urgent need for redundancy in our water infrastructure. As private and public construction activity continues to grow, this event highlights the vital role of MWRA as stewards of our regional water supply and their ongoing efforts to create system redundancy for critical segments of our system.
During geothermal drilling by a private contractor on private property, the Dorchester Tunnel, a crucial link in MWRA’s network, was compromised. Because of the tunnel’s depth, it wasn’t included on the standard DigSafe utility list. Geothermal energy is encouraged as part of the Commonwealth’s broader climate goals; however, this incident revealed how such efforts can present new challenges and potential impacts on deep, critical infrastructure. Thanks to the rapid actions of MWRA’s emergency team, what could have been catastrophic was narrowly averted. However, this incident illuminates the importance of projects like the Metropolitan Tunnel Redundancy initiative, designed to provide the additional security our aging systems now require.
Recognizing the gravity of the break, MWRA staff immediately reconfigured the water system, dispatching teams to operate 27 valves across the southern system and maintain flow to the Blue Hills Tank. The Chestnut Hill Emergency Pump Station was also activated, but balancing the entire network under unprecedented conditions required careful, round-theclock monitoring. Throughout the incident, MWRA had to continually coordinate and work with state and local officials to ensure a unified response. Teams faced confined spaces, manual valve operations, and fluctuating pressures, each step reinforcing MWRA’s
commitment to protecting our water supply against any interruption. Despite these well-coordinated efforts, minor breaks occurred as pressures fluctuated. However, by continually adapting in real time, MWRA crews were able to stabilize the system operations until a final repair could be made.
This incident further underscores the need for the Metropolitan Tunnel Redundancy project, now in progress. Designed to provide alternative pathways for water delivery, this initiative will make the entire region’s water supply more resilient against breaks continued on page 72
MWRA Advisory Board continued from page 71 or disruptions. In light of this near-crisis, the Redundancy project is essential — not just as a backup, but as a proactive measure against the challenges posed by deep construction projects and other unanticipated future challenges.
At the same time, it’s clear that current infrastructure policies must evolve. Geothermal projects and similar construction activities should be encouraged to help meet climate goals, but these should not come at the risk of vital infrastructure. To this end:
• Awareness for Deep Infrastructure: some of MWRA’s assets lie well below standard construction depths, yet they are foundational to water security. As new technologies expand, these deep assets need to be considered, requiring more robust oversight and coordination.
• Cross-Community Collaboration: While MWRA works with member communities to implement its existing permitting process, non-member regions hosting MWRA infrastructure may lack the awareness needed to protect these assets. Comprehensive, cross-community protocols are necessary to ensure all contractors recognize and respect MWRA’s infrastructure.
• Providing drinking water to Boston and 52 other communities
• Servicing 2.5 million Residents and 5,500 Businesses
• Distributing 200 million gallons of clean drinking water daily
Water Works Specialist Tel: 781-878-8098 Fax: 781-878-5298
John Hoadley and Sons Inc.
Water Works Specialist
Tel:781-878-8098 Fax:781-878-5298
“Our Products Are the Most Trusted Names in the Industry”
“Our Products Are the Most Trusted Names in the Industry”
� U.S. Pipe ● Cultec Chambers
• U.S. Pipe
� Mueller Fire Hydrants
• Mueller Fire Hydrants
• Cultec Chambers
● National Pipe & Plastics
• National Pipe & Plastics
� Smith Blair Clamps & Couplings
� Mueller Tapping Sleeves & Valves ● ADS Pipe & Chambers
• Mueller Tapping Sleeves & Valves
• Smith Blair Clamps & Couplings
Mechanical Services
Mechanical Services
• ADS Pipe & Chambers
� Smith Blair Clamps & Couplings ● General Foundry Castings
• General Foundry Castings
� Tapping Sleeves & Gates Installed / Cut
• Tapping Sleeves & Gates Installed / Cut
� Line Stop / EZ Valves
• Line Stop / EZ Valves
� Cutting of Chilled Water Lines & Steam Lines
• Cutting of Chilled Water Lines & Steam Lines
� Pressure Testing & Disinfection of New Mains
• Pressure Testing & Disinfection of New Mains
� Installation & Testing of Backflow Preventers
• Installation & Testing of Backflow Preventers
• Large Diameter Hydraulic Pipe Cutting
� Large Diameter Hydraulic Pipe Cutting
• Hydrant Installation & Repair
• Electronic Leak Detection
National Pipe & Plastics � Mueller Tapping Sleeves & Valves
● ADS Pipe & Chambers
● General Foundry Castings
Mechanical Services
� Tapping Sleeves & Gates Installed / Cut
� Line Stop / EZ Valves
� Cutting of Chilled Water Lines & Steam Lines
Pressure Testing & Disinfection of New Mains
Installation & Testing of Backflow Preventers
Large Diameter Hydraulic Pipe Cutting
Hydrant Installation & Repair
“Water-Sewer-Drain Supplies at a Competitive Price” www.hoadleyandsons.com 672 Union Street Rockland, MA 02370 24
“Water-Sewer-Drain Supplies at a Competitive Price” www.hoadleyandsons.com 672 Union Street Rockland, MA 02370
Electronic Leak Detection
The incident that threatened the Dorchester Tunnel reveals the vulnerabilities in our water infrastructure as construction activity and unanticipated future challenges due to new initiatives and technologies expand. Thankfully, MWRA’s rapid response prevented what could have been a devastating impact on the region, highlighting the critical need for continued investment in redundancy through projects like the Metropolitan Tunnel Redundancy. Moving forward, the MWRA Advisory Board stands ready to partner with MWRA to advocate for enhanced protocols, wider cross-community outreach, and rigorous protection of essential water systems. Together, MWRA and the Advisory Board can help lead the region in safeguarding our water resources, with resilience as the foundation for future growth. n
UCANE’s “Construction Outlook” magazine editors recently caught up with Ed Sarin at a busy construction site in Boston. Ed is Health, Safety, and Training Director with UCANE member firm Feeney Brothers Utility Services. We were able to get a few minutes of Ed’s’ time to talk about the importance of safety in today’s heavy construction industry.
Will you please tell us a bit about your back ground in the Construction Industry and how you decided to concentrate on the safety side of the business?
My initial interest in health and safety originated back while attending college at Central Michi gan University in the late 1980s, where I earned a bachelor’s degree in Industrial Supervision and Man agement. As part of that curriculum, I needed to take a course in safety which at the time consisted of the original Dupont STOP program. I was fortunate to have had an excellent professor who saw my enthu siasm and passion for health and safety and through his inspiration, I decided to pursue a minor in Safety Management.
Shortly after graduating from college, I started my ca reer in the Oil and Gas Industry, working for a turnkey operation consisting of drilling, well completions and service work, facility construction, trucking, and pipeline maintenance. That paved the way for the next 30+ years working in the energy sector in multiple diverse capacities both in health and safety, as well as operations. As a result, I was afforded the opportunity to work in nearly every major land basin throughout the continental United States, which not only allowed me to develop a strong and diverse safety background, but also to see all the different challenges and advantages each area had to offer.
What type of work does Feeney Brothers do and how far from Boston do they normally
Feeney Brothers is headquartered in Dorchester, MA and provides area utilities with comprehensive solutions for completing complex projects in urban, suburban, and rural settings. We equip our qualified workforce with comprehensive training and innovative tools to provide exemplary service to customers, with safety always being at the forefront of everything we do. We like to refer to the way we do business as “The Feeney Way.”
Ultimately, in 2023 I felt that I was ready to try something different and that is when I ended up accepting the role of Director of Health, Safety and Training for Feeney Brothers in Dorchester, MA.
Feeney Brothers’ capabilities include natural gas distribution, steam, electrical, and telecommunications work for the greater Northeast region. We are also part of a larger network of companies, which offers us opportunities to form partnerships and provide services that further expand our ability to serve our customers’ needs.
continued on page 74
Safety & Compliance continued from page 73
Feeney has been a long-time and active member of UCANE and is well known for their commitment to Safety. What was your impression of the Safety culture that exists at Feeney Brothers when you first arrived in Boston?
When I first met with the senior leadership team at Feeney, prior to starting, it was abundantly clear that safety and health and the culture of continuous safety improvement was held as the highest value within the organization. Shortly after I accepted my offer to work with Feeney, my wife and I moved from Fort Worth, Texas to the Boston area to begin a new chapter in my career. From day one, I immediately could see that holding safety as a key value was not just a talking point but rather a deep-seeded commitment to safety throughout the entire organization.
It was described to me as “The Feeney Way,” which is the belief that nothing is more important than the health and safety of every employee we have, as well as those we interface with daily. It shows in both the investment in our people, as well as the tools and equipment we use in the field. Furthermore, there is equal commitment to safety in terms of the train-
ing resources we have access to, such as our stateof-the-art training center, our mobile training classrooms, and hands-on equipment and simulator used for employee instruction. From the start, there was no doubt in my mind as to the commitment Feeney has to safety and health and the impressive culture that continues on a daily basis
In addition to training your crews for excavation and trench work and for working in high traffic urban areas, there is a lot of additional training required when installing pressure piping for natural gas. What type of additional training would a typical gas crew require?
To begin with, all our formal training is led by qualified trainers and subject matter experts, and focuses a great deal on trench safety and working in high traffic urban areas. In addition to this, however, we also provide both classroom and hands-on training on construction tasks relevant to our industry. Our curriculum is constantly being evaluated and adjusted to meet not only compliance and customer requirements, but even more importantly to make sure the health and safety of all our people is prioritized above all else.
continued on page 75
This goes beyond just the trench. This also includes new employee orientation and training, which focuses on key safety principals pertinent to our line of work, as well as additional classroom and hands-on training on topics such as awareness around heavy equipment, respiratory protection training and fit testing, the use of fall protection, first aid and CPR, and emergency action/fire safety training.
In conjunction with all the above, our training is not complete until our employees are fully accepted as OQ (Operator Qualified) through EWN and NGA for all covered tasks and/or prerequisites that our Gas Industry Clients might specify. As a result, we are fully confident that our employees have been empowered with the knowledge and skills to make informed decisions and create the safest set of circumstances for everyone they work with.
What are some of the most important goals you have and challenges you face being a Safety Director in the construction industry?
My primary goal as a safety director is to ensure the safety and well-being of employees, subcontractors, the public, and any others we may interface
with. This is accomplished by earning the respect of our field staff, the customers we work for and the communities we work within by focusing our efforts on continuous safety improvement. There will always be challenges which affect our business and must be faced head on, whether it is physical hazards, changes in economic conditions, new regulations, or even public perceptions of the construction industry.
However, if I and my safety team at Feeney Brothers stay focused on our goal of keeping our crews safe and maintaining our integrity in every decision we make, I believe we will continue to effect positive change while ensuring we stay steady in our pursuit of continuous safety improvement and a Zero Incident Workplace. n
The spring and summer months bring warmer temperatures, longer days and of course, roadside construction projects. These projects called Work Zones are crucial for maintaining and improving infrastructure, yet they pose significant risks to both drivers and workers. Recognizing this, National Work Zone Awareness Week (April 21-25) provides educational materials and activities to raise public awareness.
Every year, hundreds of workers and motorists lose their lives in work zones across the country. In Massachusetts alone, multiple tragic incidents in 2024 serve as stark reminders of the risks present in roadside construction sites.
• April 26, 2024 – Billerica: Sergeant Ian Taylor, a 49-year-old officer with the Billerica Police Department, tragically lost his life after being struck by an excavator while assisting a tractor-trailer at a road construction site on Boston Road (Route 3A).
• December 23, 2024 – Duxbury: A driver was fatally injured in a crash within an inactive construction zone on Route 3. The vehicle collided with a guardrail near the Franklin Street underpass, resulting in the driver's ejection and subsequent death at the scene.
• October 6, 2024 – Boston: Two roadway workers sustained serious injuries when a driver, allegedly under the influence, entered a work zone on I-90 near the Beacon Street Overpass and struck an elevated lift holding the workers. These incidents highlight the critical importance of safety measures in and around road construction zones to protect both workers and the public.
Federal Highway Administration (FHWA) –sets nationwide standards through the Manual on Uniform Traffic Control Devices (MUTCD), which provides guidelines for traffic control in work zones. A properly planned and executed Work Zone and traffic management system, helps to keep everyone
safe. Ultimately, ensuring safety in these areas is a shared responsibility. Both drivers and workers must remain alert and follow established guidelines to prevent further tragedies.
A well-designed work zone is set up to minimize risks and give drivers unambiguous instructions. The following are essential components of a successful work zone design:
1. Advance warning signs let drivers know when conditions on the road will change so they may reduce their pace and get ready for lane changes or detours.
continued on page 78
2. Traffic Control Devices: Flashing lights, barricades, and cones aid in safely guiding vehicles through or around the construction area.
3. Clear Lane Markings: By ensuring that cars stay on approved routes, temporary lane markers lower the chance of incidents.
4. Safe Work Areas for Employees: It is safer for employees to have enough room to work without being hampered by moving cars.
5. Speed Reduction Measures: In work zones, high-speed traffic accidents can be avoided with the deployment of speed limit signage and enforcement.
In Massachusetts, the initial line of protection, for both drivers and road workers, is provided by a police traffic detail but the MassDOT also allows for the use of Flaggers when a detail is unavailable. Among their duties are:
1. Traffic Flow Control: Flaggers safely direct cars through work zones using hand gestures and established signals.
2. Communicating with Workers: Construction workers can work safely if they are aware of approaching vehicles.
3. Responding to Emergencies: Skilled flaggers are able to act quickly in the event of an accident or dangerous circumstance, assisting in the prevention of additional accidents.
4. Improving Driver Awareness: When driving through work zones, drivers are reminded to stay vigilant and watchful by a visible and authoritative presence.
Effective traffic management plays a crucial role in maintaining safety within work zones, ensuring the smooth flow of traffic and protecting both workers and the public. Where officers on traffic detail have
continued on page 79
their recognized authority and experience in challenging roadway circumstances to help keep motorist in check, a flagger only has competence and skill. Recognizing the importance of standardized training for these essential personnel, both the Massachusetts Department of Transportation (MassDOT) and the National Safety Council (NSC) have established comprehensive flagger certification programs.
In Massachusetts, the use of road flaggers and police details on public works projects is governed by 700 CMR 6.00. This regulation aims to ensure the safety of pedestrians, motorists, bicyclists, and workers on or near public works projects by effectively utilizing traffic control devices, road flaggers, and police details.
To uphold these safety standards, MassDOT has the authority to approve certification programs that allow external entities to certify flaggers for work on Commonwealth roadways. The MassDOT Certification Program encompasses several key components, including training in construction zone safety, traffic control, and first aid. Flaggers must successfully complete a MassDOT-approved certification program and carry a valid certification card at all times while on duty.
The program also maintains a list of approved flagger certification programs, ensuring that training providers meet the necessary standards and guidelines.
The Federal Highway Administration (FHWA) reports that driver confusion, speeding, or disregard for instructions are frequently the causes of construction zone collisions. Everyone can travel on safer roads by reducing these dangers by putting best practices in work zone design into practice.
It is impossible to overestimate the significance of a well-designed work area and effective traffic control either with a police detail or trained flaggers. Investing in work zone safety improves overall road efficiency and dependability, in addition to saving lives. Setting these components as a top priority is a collective duty that benefits the community as a whole. By prioritizing safety, enforcing strict training standards, and fostering public awareness, we can drastically reduce injuries and fatalities in work zones. The responsibility falls on all of us—workers, motorists, and policymakers alike—to ensure these areas remain as safe as possible. n
“C.C. Construction, Inc. has been a member of UCANE for over 10 years now and we continue to see benefits each year. Whether it’s being introduced to new associate members, vendors, or subcontractors that can support our company goals, or keeping us deeply informed of legislative items that will affect our business operations. It’s a unique group of competitors who come together for the greater good of the Utility Industry and work together to make our industry thrive for generations to come. UCANE is an invaluable resource.”
~ BRIAN COONEY, C. C. Construction, Inc.
“Like the generations before me, I take great pride in supporting this Association, which has tirelessly championed our industry. UCANE’s dedication helps ensure a strong, thriving sector that provides a stable livelihood for my family, my employees, and countless others.”
~ QUERINO PACELLA, RJV Construction Corp.
“Building a strong network of trusted industry peers opens the door to fresh ideas, innovative solutions, and new perspectives. By exchanging insights and experiences, construction professionals can tackle challenges more effectively, stay ahead of industry trends, and drive success together.”
~ CHRIS VALENTI, GVC Construction, Inc.
“The information that UCANE provides to us about our industry is timely and invaluable. I find UCANE members to be committed and passionate about keeping the construction industry strong and well-respected, and our company is proud to be a part of that.”
~ LISA FRENCH KELLEY, W. L. French Excavating Corp.
“As a longtime member from Western MA, I can say that UCANE does a tremendous job keeping all members informed and being a strong advocate for our industry throughout the state and region.”
~ JERRY GAGLIARDUCCI, Gagliarducci Construction, Inc.
“Staying on top of proposed laws and regulations that impact our company could be a full-time job. That’s why I value UCANE’s expertise in identifying what truly matters. Their advocacy team is one of the most respected and effective in the industry, ensuring our voices are heard and our interests protected.”
~ DAN HORGAN, R. H. White Const. Co., Inc.
“Being part of a respected organization like UCANE creates valuable opportunities for networking, collaboration, and professional growth. It connects industry professionals, fosters strong partnerships, and helps drive success in the underground construction sector.”
~ KARIN MARSHALL, Boston Concrete Corp.
Toni Piwonka, Trimble
Contractors turn to subscription purchasing models to cut adoption costs and keep ahead of the technology curve.
Subscription-based models, alternatives to purchasing or licensing in perpetuity, are increasingly prevalent in our work and home lives. From machine control to office devices to software and more, buyers are embracing the power and convenience of subscriptions. For the construction industry, software and hardware subscriptions offer cost, predictability, scalability, and convenience advantages. They can also help contractors standardize processes across their organizations and stay at the forefront of technology adoption.
According to Global Market Insights, the global construction software-as-a-service market size was valued at USD $13.3 billion in 2023 and is projected to grow at a CAGR of over 10.8% between 2024 and 2032.
Staying current with construction technology assets makes contractors more competitive. For example, machine control is no longer a concept for the future – it’s here, and businesses run the risk of falling behind if they aren’t integrating solutions to bring their fleets into this new age. Likewise, spreadsheets and paper-based processes put contractors at a disadvantage against competitors leveraging the efficiency, accuracy, immediacy, and data sharing benefits of specialized software for estimating, operations, equipment maintenan ce, and financial management.
Subscriptions simplify the purchasing process for
customers by including everything they need – stateof-the-art hardware and software, maintenance, protection plans, field-to-office software, and cellular activity – into one simple monthly payment. They also lower the initial cost of adding new technology, often moving it from a larger one-time capital expense to smaller operational expenses paid monthly or annually. This option helps contractors to grow their businesses, manage costs, and remain competitive in a tight construction market.
Tiered subscription offerings are another option to fit varying contractor needs as well. With this option, a company can purchase their hardware outright, or even bring their own, and subscribe to the level of software, protection plans, and hardware services that fit their business.
continued on page
Technology in Const. continued from page 81
Consider these cost benefits for subscription services:
• Contractors purchase only what they need, spread payments out over time, and adjust the subscription as requirements evolve.
• The cost of technology becomes a monthly expense instead of an upfront capital expense. This lowers cost of entry, allowing contractors – including smaller contractors – to adopt state-of-the-art hardware and software that may otherwise be out of reach. Additionally, smaller companies can benefit from lower long-term debt ratios and improve their overall credit ratings.
• Subscriptions allow contractors to gain the economic benefits of the newest tools and functionalities as soon as they are released, at no additional cost.
• Cloud hosting of software minimizes the need for contractors to purchase and maintain hardware and IT infrastructure and personnel, leading to significant reductions in upfront and ongoing costs.
• Cloud solutions also offer sophisticated cybersecurity protections – with continuous, automatic updates – reducing costs and risk.
• Larger organizations may achieve faster internal approval cycles when the costs hit monthly operational budgets instead of capital expense budgets.
• If a technology assurance plan is purchased with the subscription, contractors can eliminate any unexpected repair or maintenance costs.
Colorado-based civil contractor Stutsman-Gerbaz leverages technology subscription services to run its business more efficiently and effectively.
“We know that technology subscription services provide real benefits on our projects and, ideally, we wanted to upgrade our entire fleet,” said Shay Stutsman, president of Stutsman-Gerbaz. “But the initial capital investment to outfit all of our machines with 3D grade control was daunting.”
With a subscription, Stutsman says, “We’re able to do more work in less time, with greater accuracy, while keeping our indirect expenses the same or even lower.”
Technology Assurance is Built In. Technology assurance is another advantage of the subscription model. Technology changes rapidly. Integrating the latest advancements, from machine learning and predictive analytics to user interface,
continued on page 83
LARGE RESOURCES. LOCAL RELATIONSHIPS.
Let us review your programs and recommend improvements to ensure you are fully protected should the unexpected happen.
COMMERCIAL INSURANCE & BONDS
• All forms of liability and property coverages
• Bonds including Express Bond Program
• Competitive terms
• Personalized service
• Highly experienced with Construction programs
CHRISTOPHER CLARK, PRINCIPAL, CLIENT ADVISOR
RISK MANAGEMENT SOLUTIONS
• Employee and executive benefits
• Retirement planning services
• Investment advisory services
• Private wealth management
• Personal and high-net-worth portfolios
World Insurance Associates LLC, 50 Prospect Street, Waltham, MA 02453
O 781-642-9000 | D 781-398-9318 | M 508-400-4010 | christopherclark@worldinsurance.com worldinsurance.com
Technology in Const. continued from page 82 data processing and reporting features into their daily workflows keeps contractors competitive and profitable.
Stutsman believes that his jobsites are more efficient and productive since moving to a technology subscription. “We’re able to do more with a smaller crew. Technology has really allowed our company to grow and continue to be successful. Five years ago, we were running maybe seven jobs on a daily basis. Today, we’re running 15.”
The “latest and greatest” is always available. Obtaining technology via subscription makes it easy for contractors to leverage the latest versions of software and hardware to tackle today’s toughest construction challenges. The latest technology, for example, provides considerable connectivity advantages for utilizing machine control systems in challenging conditions, such as under heavy tree canopies.
Consistency and standardization. For hardware, firmware and software, subscriptions also make it easier for contractors to get all of their employees and equipment operating on the same updated version of the technology. This paves the way for standardizing processes, training and technology
support across the organization. Purchasing various versions of technology over time, on the other hand, can leave contractors with disparity and compatibility challenges.
Stutsman says of his experience, “Every operator is running on the same platform. If one of our newer operators is not familiar with the system on his dozer, an excavator operator can share expertise. They have the same screen, even on a different machine.”
He added, “Also, we are always current with all the new sensors, harnesses, and cables along with software upgrades on desktops, rovers, and tablets—it’s all done automatically. Any time there’s an upgrade or we need a new piece of equipment, our distributor brings it out and installs it. It was a nobrainer for us to go with the subscription.”
The subscription model allows customers to gain access to true peace of mind on their terms, and also cultivates a collaborative working relationship between technology providers and contractors. Choosing a provider that you trust and want to work with long-term is imperative.
Toni Piwonka is Associate Vice President, Strategic Transformation, at Trimble, Inc. n
Corp.
P.O. Box 913 • Falmouth, MA 02541
396 Gifford Street • Falmouth, MA 02540
PH 508-548-1800 • FX 508-457-1825
Visit our website @ www.lawrencelynch.com White Bros. – Lynch Corp.
P.O. Box 155 • Oak Bluffs, MA 02557 20 Vineyard Ave. • Oak Bluffs, MA 02557
PH 508-693-0845 • FX 509-693-0312
Concrete Systems, Inc.: Manholes & Catch Basins, Box Culverts, Utility Structures, Special Box Structures, Containment Vaults, Fire Cisterns, CSI Arc-Span™ Bridges, Rigid Bridge ™ Systems, Bridge Deck Slabs, Permanent & Temporary Median Barrier, Uwall™ Retaining Wall Systems, Stablewall™ Retaining Wall, Headwalls & Wingwalls. Clampcrete Construction Systems: TL-4 Anchored Barrier for Roadway Structures. Tunnel Systems: Precision Segmental Tunnel Lining Rings. Cleco Manufacturing: Precision Fabricated Forms & Forming Systems, Complete Plant Design, Batch Plant Computer Automation, Countercurrent Mixers & Concrete Delivery Systems.