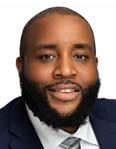

UCANE CoNtr ACtors
LEAd

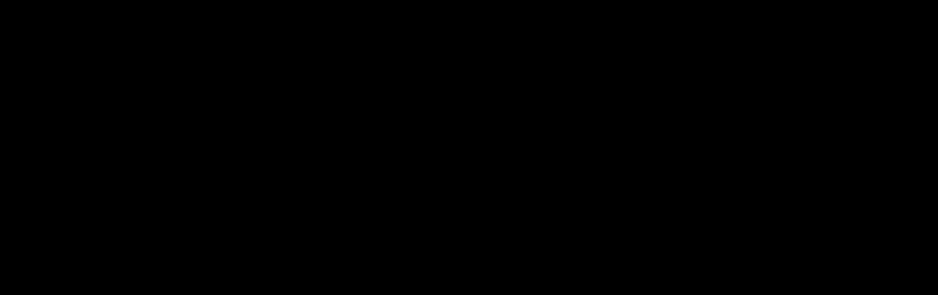
LEAd
OFFICERS
President
BRIAN COONEY
C. C. Construction Inc.
President Elect
CHRIS VALENTI
GVC Construction, Inc.
Treasurer
QUERINO PACELLA
RJV Construction Corp.
Secretary
DAN HORGAN
R. H. White Const. Co., Inc.
BOARD OF DIRECTORS
VINCENT BARLETTA
Barletta Heavy Division
MIKE BISZKO, III
Biszko Contracting Corp.
CALVIN BRANDFORD
CHB Excavating
CHRISTOPHER CLARK World Insurance Associates, LLC
JULIA D’ALLESSANDRO D’Allessandro Corp.
JERRY GAGLIARDUCCI
Gagliarducci Construction, Inc.
JOE GIOIOSO
P. Gioioso & Sons, Inc.
JUSTIN GOODHEART
J. F. White Contracting Co.
DAVID HAMILTON
E. J. Prescott, Inc.
LISA FRENCH KELLEY
W. L. French Excavating Corp.
WILLIAM LEONARD
Aqua Line Utility, Inc.
RYAN McCOURT
McCourt Construction Company
CHIP McDONALD
ATS Equipment, Inc.
MIKE OTTAVIANO
Jolin Paving & Excavating, Inc.
ROBBIE OUR
Robert B. Our Co., Inc.
RICHARD PACELLA, JR.
R. M. Pacella, Inc.
JOSEPH F. NOLAN
Executive Director
5 President’s Message: Leveraging Advertising to Improve Your Company’s Branding and Increase Profits
7 Legislative Update:
• MassDEP Delays Heavy Duty Omnibus Rule for One Year
• Conference Committee Report on Energy Emerges for Final Approval
• Administration Awards More Than $17 Million in Skills Capital Lab Modernization Grants
• Town of Dennis Approves First Phase of Needed Wastewater Plan
• Grants to Fund Programs for Coastal Resilience Awarded
• News in Brief
25 UCANE Interviews: Representative Christopher Worrell (5th Suffolk District)
29 Legal Corner: Update: Current Status of Davis-Bacon Final Rule
35 Construction Safety & Compliance: A n Interview with Mark Brown, Northeast Area Safety Director, Sunbelt Rentals, Inc.
41 How to Solidify Your Hiring & Retention Strategies
45 5 Risk Myths Demolished
49 Insurance Perspective: Importance of Flood Insurance for Construction Companies
53 Biden-Harris Administration Issues Final Rule Requiring Replacement of All Lead Pipes Within 10 Years
57 Safety & Health Corner: Personal Fall Arrest System (PFAS)
61 UCANE Joins W. L. French Excavating Corp. for Workforce Development Trades Day
62 MBTA gets $472M Federal Grant: Largest in Agency’s History
65 Spotlight on Cape Cod:
• Yarmouth and Dennis – Latest Towns on Cape Cod to Move Forward with Section 208 Sewer Programs
• Buzzards Bay Coalition Wants Federal Aid to Fix New Bedford’s Sewer Problems
Editors: Joseph F. Nolan & Anne Klayman, Associate Editor: Suzanne Hatch
Magazine Designer/Associate Editor: Sherri Klayman, Head Writer/Assistant Editor: Mike Lenihan
Construction Outlook Chair: Brian Cooney
Editorial Board: Brian Cooney, Chris Valenti, Querino Pacella, & Dan Horgan
CONSTRUCTION OUTLOOK published monthly by the Utility Contractors’ Association of New England, Inc., 300 Congress Street, Suite 101, Quincy, MA 02169; Tel: 617.471.9955; Fax: 617.471.8939; Email: jnolan@ucane.com; Website: www.ucane.com. Statements of fact and opinion are those of the authors alone and not necessarily those of UCANE and the Construction Outlook editorial board and staff. Subscriptions are included in dues payments for UCANE members. Presorted Standard postage paid at Brockton, MA. POSTMASTER, please send form #3579 to Construction Outlook, Crown Colony Office Park, 300 Congress Street, Suite 101, Quincy, MA 02169.
The Jack Farrelly Company, Putnam Pipe and HR Prescott have united, as part of the Core & Main family.
• W. Boylston, MA 508-835-4431
• Bloomfield, CT 860-769-6760
• East Lyme, CT 860-739-5457
• New Britain, CT 860-826-0517
• Hopkinton, MA 508-435-3090
• North Haven, CT 203-777-5548
• Westbrook, ME 207-464-0585
• N. Billerica, MA 978-459-6701
• Norwood, MA 781-407-9133
• Taunton, MA 508-880-8736
• Worcester, MA 508-752-7473
• Loudon, NH 603-263-7350
• New Milford, CT 860-210-6262
• Springfield, MA 413-732-8400
• Johnston, RI 401-725-0140
We’re still the dependable experts you’ve always known, but now as one team, continuing to handle all your water, wastewater, fusible, and storm drainage material
As we move forward in an industry filled with both challenges and opportunities, now is a great time to consider how we can enhance our visibility and impact. With our contractor and associate members supporting one another, UCANE represents a robust network of expertise and opportunity. To fully leverage this network, we must ensure we stay visible—not just to clients, but to each other. Advertising is a powerful tool that allows us to do just that, strengthening both individual businesses and UCANE’s collective presence.
The most successful companies understand that advertising is essential—not just for visibility but for building and maintaining a strong, reputable brand. For each of us, it’s a way to promote our work, highlight our services, and reinforce our industry’s values. As we increase our own visibility, we are also enhancing UCANE’s profile through our branding efforts, which include, UCANE’s magazine, social media, and our website—each working together to showcase members’ achievements.
A major advantage of belonging to UCANE is access to reliable partners and trusted suppliers. Our branding efforts amplify our members’ work and elevates the quality that UCANE represents. Advertising within UCANE enables each member to showcase their specialties, whether in deep trench excavation, advanced construction techniques, safety, or a myriad of other critical trades needed to complete our projects. When members know who to turn to for specific services or supplies, collaboration becomes more seamless and effective fostering a network built on trust.
Each platform—whether it’s a social media post, a feature on our website, or an ad in construction outlook magazine—works in concert to ensure that when a need arises, UCANE members look to each other first.
For contractors and associates alike, advertising is a powerful way to grow your reach and connect with a larger audience. It lets you highlight your unique offerings and reach new potential clients both inside and outside UCANE’s network. Through UCANE’s branding
efforts across these platforms, your advertising goes even further, showcasing the talent and solutions our members bring to the field.
Our members are experts across a range of services, from construction to specialized materials, equipment, and services. Advertising allows you to communicate your capabilities, helping other members understand what you and your firms bring to the t able. Through ads in UCANE’s magazine, posts on our social media, and features on our website, you can highlight recent successes or new services, positioning yourself as a valuable resource and strengthening your credibility.
Advertising, in combination with our ongoing branding efforts, is a long-term investment in both your business and UCANE’s future. Every member who invests in advertising strengthens not only their own visibility but also enhances UCANE’s profile as New England’s leading utility construction resource. This exposure benefits everyone, c reating a well-connected network that elevates the reputation of our entire association.
I encourage each of you to consider how advertising with UCANE can elevate your company’s presence and success. Together, we’re building a stronger, more visible, and trusted UCANE network—one that represents the best of what we have to offer for generations to come across the construction industry. UCANE – 70 Years and Growing. n
Mid-October saw the Massachusetts Department of Environmental Protection (MassDEP) announce that it was delaying the implementation of the Heavy-Duty Omnibus (HDO) rule for one year while also creating a very limited exception for government purchases of snowplows and street sweepers from the Advanced Clean Truck (ACT) rule. The move follows similar actions by the States of Oregon and New York as the realization that the well-intentioned rules impacting medium and heavy-duty truck sales are ahead of technological and infrastructure advances.
Before the MassDEP’s announcement, UCANE joined with 35 other industry associations to raise concerns about the actions of Oregon and New York. In a letter to Governor Maura Healey and MassDEP Commissioner Bonnie Heiple, UCANE, along with large business employer organizations, Associated Industries of Massachusetts, the Retailers Association of Massachusetts, and the Greater Boston Chamber of Commerce, industry specific groups like the School Bus Transportation Association of Massachusetts, the Green Alliance, and Massachusetts Retail Lumber Dealers Association, stated:
“While delaying the HDO rule as Oregon did makes sense for the Commonwealth, the lack of a delay for the ACT rule will still leave the Commonwealth’s end-users in a poor position. The ACT rule’s requirement that manufacturers sell a certain percentage of electric MHD trucks has been interpreted as a requirement that truck dealers must sell – and thereby end-users who
cannot afford the price and risk of an electric MHD must purchase – t hese vehicles fi rst. Regardless of whether the regulatory agency or a manufacturer is “right” in their interpretation as to how the ACT rule should be implemented, MHD truck dealers and end-users, public and private, are caught in the middle. The fact remains that technology and infrastructure are simply not to the point where they will sustain the ACT rule at this time.
As highlighted by many industries’ correspondence to your office, Massachusetts has not made enough progress on building out a network of public or private charging stations for commercial vehicles. Further, even if many of the companies could afford an electric MHD truck option, the most important fact remains that an electric option does not yet exist for many of the MHD trucks that are needed by almost every industry – whether in construction, forestry, landscaping, grocery, concrete mixing, towing, or any other industry. As a result, we continue to urge you to delay both the ACT and HDO rules.”
The MassDEP’s decision means that, for now, the Advanced Clean Truck rule will be implemented as of January 1, 2025. The broad coalition of stakeholders will continue to press the Administration to delay the ACT now and in the future until both technology and infrastructure catch-up to the regulation’s stringent requirements. For more information about the variety of stakeholder outreach to the Administration, please visit: https:// smartenergyformass.org.
continued on page 9
While not yet finally approved as of this writing, the Massachusetts legislature unveiled a Conference Committee report on clean energy that is expected to get to the Governor’s desk shortly. The compromise bill includes language that is expected to speed up the siting and permitting of energy infrastructure projects by giving an existing state board more power and setting a fi xed time limit on c hallenges. The siting and permitting language was initially the only area of agreement between the Governor, Senate, and House of Representatives.
As reported by CommonWealth Beacon, the measure also includes several priorities of the House of Representatives, including language promoting the development of battery storage facilities and tweaking the current regulatory process for procuring offshore wind. The bill also includes firstof-its-kind language extending renewable energy
subsidies to fusion power, if and when it becomes a reality and also redefines c lean energy under Massachusetts law to include power from existing New England nuclear plants – Millstone, based in Waterford, Connecticut and Seabrook Station, in Seabrook, New Hampshire. Among Senate priorities, the c ompromise bill c hanges the legal definition of natural gas utilities to give them license to deliver geothermal power, a possible first step in changing the business model of natural gas utilities.
Of particular interest to UCANE members, the legislation pushes the Electric Vehicle Infrastructure Coordinating Council (EVICC), a task force of state agencies charged with planning the Commonwealth’s electric vehicle infrastructure, to finally focus on the needs of the medium and heavy-duty truck market. To that end, the language
Legislative Update continued from page 9
requires the EVICC to create estimates of the number of zero-emission medium and heavy-duty vehicle charging stations required to meet the commonwealth’s emission limits and sublimits pursuant under Mass. Gen. Laws chapter 21N. The EVICC is further required to foster a discussion of costs, permitting processes, and estimated timelines for installing charging stations for medium and heavyduty vehicles.
With respect to certain controversial measures included in the bill, the compromise legislation did not include language favored by the Senate and the Governor that would have shut down the retail electricity supply industry in Massachusetts. The new bill also does not include an expansion of the state’s bottle deposit law that the Senate had included in its proposal, but, instead, includes a commission requiring manufacturers to study their use of plastic resources.
To review a copy of the Conference Committee’s final report on the c lean energy legislation, please visit: https://malegislature.gov/Bills/193/ S2967.
continued on page 13
MATERIALS AVAILABLE FOR PURCHASE:
• 1” MINUS PROCESSED GRAVEL
• ¾” & 1½” CRUSHED STONE
• SCREENED LOAM
• SCREENED SAND
• BROKEN ASPHALT
• NON & REINFORCED CONCRETE
• CONCRETE WITH WIRE MESH
• ROCK
• BL ASTED LEDGE
PLANT LOCATION: 200 LEGACY BLVD. DEDHAM, MA 02026 Plant: 617-590-0024
OFFICE: 1039 EAST STREET DEDHAM, MA 02026 Office: 781-329-4111 Fax: 781-329-1039
HOURS OF OPERATION:
MONDAY-FRIDAY: 6:30 A.M. – 4:00 P.M. SATURDAY: 7:00 A.M. – 12:00 P.M.
DELIVERIES AVAILABLE ON LARGE ORDERS. PLEASE CALL FOR PRICING. MATERIALS ACCEPTED:
Whatever the job requires, Sunbelt Rentals has the equipment you need to make it happen.
Trench Safety
Steel & Aluminum Trench Shields | Buildable Trench Shields | Road Plates| Hydraulic Shores | Bedding Boxes | Manhole Shields | Slide Rail & Engineered Designs
Pump Solutions
Electric and Diesel Centrifugal Pumps | Hydraulic Pumps | Submersible Pumps | Filtration | Remote
Monitoring & Telematics with PumpSentri
Earth Moving
Large Excavators | Wheel Loaders | Dozers and Crawler Loaders | Skid Steer Loaders | Dirt Rollers | Articulated Dump Trucks | Backhoes
Explore our services at sunbeltrentals.com or contact us at 888.846.1078 to see how we can help
The Healey-Driscoll Administration recently announced that it has awarded more than $17 million in Skills Capital Lab Modernization Grants to 18 schools across Massachusetts. Career technical education and training programs can use this funding to purchase and install equipment related to high demand industries and occupations, such as advanced manufacturing, health care, information technology, construction/skilled trades, and life sciences. Announced during STEM Week, these grants modernize and upgrade equipment, ensuring that students and workers are prepared for the rapidly evolving demands of today’s job market through expanded career programs for young people and adults and increased capacity in workforce training programs.
This Skills Capital Lab Modernization Grants allow for the purchase of equipment to upgrade and expand career technical education and training programs that are aligned to regional economic and
workforce development priorities for in-demand industries. Applicants increasing the number of students able to participate in an existing program, creating a new program to meet demonstrated demand, and/or increasing the availability and utilization of the equipment in partnership with other organizations outside of the organization’s normal working hours (e.g., after 5 p.m. Saturday and/or Sunday) to serve additional students were prioritized.
Among the awardees were:
• Bay Path Regional Vocational Technical High School (Charlton): Diesel Technology/ Information Support Services & Networking: $700,000
• Greater Lawrence Technical High School (Andover): Auto Technician/Advanced Manufacturing: $750,000
continued on page 15
serving major contractors for more than 60 years, the Driscoll Agency truly understands the unique risks, insurance requirements, and surety demands of the construction industry.
• Greater Lowell Technical High School (Tynsborough): Electricity: $1,000,000
• Greater New Bedford Regional Vocational Technical High School (New Bedford): Carpentry/Electricity: $1,000,000
• Taconic High School (Pittsfield): M etal Fabrication and Joining/Horticulture: $1,000,000
• Shawsheen Valley Technical High School (Billerica): Advanced Manufacturing/Metal Fabrication & Joining: $1,000,000
The Skills Capital Grants are part of the administration’s Workforce Skills Cabinet, which aligns the Executive O ffices of Education, L abor and Workforce Development, Health and Human Services and Housing and Economic Development toward a comprehensive economic growth agenda. The Cabinet is charged with creating and implementing a strategy to ensure that individuals can develop and continuously improve their skills and knowledge to meet the varying needs of employers in the Commonwealth.
For more information about the Skills Capital Grants program, please visit: https://www.mass.gov/ upgrading-technology-with-skills-capital-grants.
Update continued from page 13 continued on page 17
Patrick Di Cerbo
• Pre-mark the location of intended excavation using white stakes, paint or flags.
• In MA, ME, NH, RI and VT, notify Dig Safe® at least 72 hours in advance, not including weekends and holidays.
• Notify non-member facility owners.
• Maintain the marks placed by underground facility owners.
• Use caution and dig by hand when working within 18” of a marked facility.
• If a line is damaged, do not backfill. Notify the affected utility company immediately if the facility, its protective coating, or a tracer wire is damaged.
• Call 911 in the event of a gas leak, or if a damaged facility poses a risk to public safety.
• Know your state’s excavation requirements.
• Go to digsafe.com for educational material and current laws.
Dennis voters gave their final approval Tuesday to the first phase of a $248 million wastewater plan at a special election following unanimous approval of the plan a week before at a special town meeting. According to the Cape C od Times, the unofficial results from the election were 1,150 yes to 212 no, representing a total of 10.24% of the Town’s voters. The ballot approval was required for the Proposition 2 ½ debt exclusion question.
of a sewer collection system along the commercial planning district on Route 28, residential areas along Bass River and both sides of Route 134. By approving the projects now, the Town will be able to save more than $100 million from 0% financing and 30% debt forgiveness through the Massachusetts State Revolving Fund and the Clean Water Protection Fund.
Wastewater plans are mandated for all towns on the Cape under state regulations, issued by the MassDEP, to address elevated nitrogen levels, primarily from septic systems, and to prevent excessive nutrient-loading of local water bodies. Several Cape towns have responded to the mandate with similar projects.
More information about the Town of Dennis’ wastewater plan can be found at: https://www.town. dennis.ma.us/DocumentCenter/View/1920/Comprehensive-Wastewater-Management-Plan-PDF.
continued on page 19
The Town’s Wastewater Implementation Committee’s program was designed to address wastewater management needs, protect drinking water sources, protect freshwater ponds, and restore valuable saltwater estuaries, according to its executive report. The Phase I plan, developed over the past 23 years, will include the design, permitting, and construction of a wastewater treatment plant off Theophilus F. Smith Road, construction Ferguson offers a complete line of products to cover all your water, sewer and storm water management needs, and our relationships with the waterworks industry’s top vendors give our customers peace of mind through unmatched customer service, on-time delivery, and industry leading fill rates.
In mid-October, the Healey-Driscoll Administration announced $5.2 million in grants to support Massachusetts coastal communities in combating climate change impacts. In offering these grants, the Office of Coastal Zone Management (CZM) is helping fund 16 innovative projects through the Coastal Resilience Grant Program. These projects are designed to enhance local planning and shoreline management, empowering communities to proactively combat the immediate impacts of climate change. This funding is crucial for building resilience and sustainability along the state’s coastlines as communities face more frequent storms, storm surge, flooding, erosion, and sea level rise.
CZM’s Coastal Resilience Grant Program provides funding and technical assistance to evaluate local vulnerabilities to c oastal fl ooding and erosion. It also aims to raise community awareness and action on these issues, plan for changing conditions, redesign vulnerable community facilities and infrastructure, and restore shoreline systems to enhance
natural resources and provide storm damage protection. Grants advance feasibility assessments, public outreach and engagement, design, permitting, and implementation of projects.
According to a press release from the agency, over $51 million has been invested in 235 resilience improvement projects in 60 communities through the Coastal Resilience Grant Program since 2014. This funding has supported comprehensive planning, infrastructure improvement, and shoreline restoration projects to reduce wave energy, erosion, and flooding impacts.
Among some of the 16 projects receiving a total of $5.2 million in Coastal Resilience Grants are:
• Falmouth, Feasibility of Beach and Dune Nourishment to Build Resiliency for Surf Drive, $153,466. The Town of Falmouth will evaluate the performance and longevity of beach and dune nourishment designs under storm conditions for the Surf Drive area.
continued on page 21
single source for precast concrete solutions
Bridge Structures
Pump Stations, Buildings
Underground Tunneling
Culverts/Arches
Retaining Walls
Prestress/NEXT Beams
Custom Structures
Update continued from page 19
• Hanover, Beal Water Treatment Plant and Wellfield Flood Resilience - Planning and Conceptual Design, $116,423. The Town of Hanover will conduct a planning study and develop conceptual designs to address fl ooding vulnerabilities to the Beal Water Treatment Plant, wellfield, and proposed PFAS (per- and polyfluoroalkyl substances) treatment facility.
• Marion, Silvershell Pump Station Resiliency Improvement Project, $85,000. The Town of Marion will complete improvements at the Silvershell Pump Station to address coastal storm risks. The project includes the construction of a bypass connection and the assessment of additional fl ood resilience measures for the pump station, force main pipe, and standby generator.
• Marshfield, Town of Marshfield Bay Avenue Beach Nourishment Project, Continued Implementation, $1,998,885. The Town of Marshfield will c ontinue c onstruction of a beach nourishment project along Bay Avenue with the placement of 36,190 cubic yards of sand, gravel, and c obble, enhancing fl ood and erosion protection for nearby infrastructure.
• Wareham Land Trust, North Water Street
Beach Shoreline Resiliency Project, $85,000. The Wareham Land Trust will document the existing condition of North Water Street Beach and associated infrastructure, evaluate present and future vulnerabilities, and develop a suite of feasible alternatives to improve the long-term resilience of the site.
The M assachusetts O ffice of C oastal Zone M anagement is the lead policy and planning agency on coastal and ocean issues within the Executive Office of Energy and Environmental Affairs. Through planning, technical and grant assistance, and public information programs, CZM seeks to balance the impacts of human activity with the protection of coastal and marine resources. The agency’s work includes helping coastal communities address the challenges of storms, sea level rise, and other effects of climate change; working with state, regional, and federal partners to balance current and new uses of ocean waters while protecting ocean habitats and promoting sustainable economic development; and partnering with communities and other organizations to protect and restore coastal water quality and habitats.
To learn more about the Coastal Resilience Grant program, please visit: https://www.mass.gov/ info-details/coastal-resilience-grant-program.
continued on page 23
•
•
Update continued from page 21
• September Tax Revenues; Up Again Due to Fair Share Surtax. The Massachusetts Department of Revenue (DOR) announced that preliminary revenue collections for September totaled $4.518 billion, $331 million or 7.9% more than actual collections in September 2023, but $29 million or 0.6% below benchmark. FY2025 year-to-date collections totaled approximately $9.826 billion, which is $541 million or 5.8% more than actual collections in the same period of FY2024, but $44 million or 0.4% below the year-to-date benchmark. DOR estimates that roughly $54 million of the year-over-year increase in September reflects a temporary, one-time event in sales and use tax, without which September 2024 revenue would be about $277 million or 6.6% more than actual collections in September 2023 and $83 million below benchmark. Without this onetime payment, year-to-date collections would be $98 million below benchmark for FY2025. The increase in non-withholding income tax is primarily driven by the pass-through-entity tax
and a likely increase in surtax revenue. The increase in sales and use tax is primarily the result of typical timing factors in collections and a temporary, one-time event. The decrease in ‘all other’ tax is due, in part, to estate tax, a category that tends to fluctuate.” In general, September is a significant month for revenues because many individuals and corporations are required to make estimated payments. Historically, roughly 10% of annual revenue, on average, has been received during September.
• McGee to Chair MBTA Board. Governor Healey announced that she is appointing former legislator and former Mayor Thomas M. McGee as the next Chair of the Massachusetts Bay Transportation Association (MBTA) Board of Directors. Mr. McGee has served on the MBTA Board of Directors since April 2023 and on the MassDOT Board of Directors since June 2023. He was Mayor of the City of Lynn from 2018 to 2022. Previously, he served as Massachusetts State Senator from the Third Essex district. He was a member of the Joint Committee on Transportation starting in 2003 and served as Senate Chair of the committee from 2011 to 2018. Before his election to the Senate in 2002, McGee served four terms in the Massachusetts House of Representatives where he represented West Lynn and Nahant. Mr. McGee is a life-long resident of Lynn where he lives with his wife Maria and has two children.
150 Grossman Drive Suite 200 Braintree, MA 02184 (617) 773-9200
LEXINGTON 238 Bedford Street Lexington, MA 02420 (781) 861-1800
• MWRA Advisory Board Expands Offerings. As you may know, the Massachusetts Water Resources Authority (MWRA) is aided by a number of advisory groups, covering areas of water and wastewater. Among these groups is the MWRA Advisory Board, which elects three members of the Board of Directors, and is made up of a representative from each customer community. By statute, the Advisory Board reviews and comments on all MWRA’s operating and capital budgets. The Advisory Board views itself as a “constructive critic” helping the MWRA to better achieve its core mission. To that end, the MWRA advisory has revamped its web presence and blog with links to a wide variety of resources. Check it out at: https://www.mwraadvisoryboard.com/ connect-with-us-dont-miss-the-latest-updates-and-resources/. n
COMPONENT
Representative Christopher Worrell was born and raised in Dorchester, Massachusetts by two immigrant parents from Jamaica and Barbados. He was raised in a traditional Caribbean American household that stressed strong family values, academic success, and a love for one’s community. He was a METCO student at Lincoln-Sudbury Regional High School and subsequently attended Bunker Hill Community College. He worked in several customer service positions before working for the Massachusetts Historical Society as the Manager of Visitor Relations. This instilled a deep-seated love for Massachusetts history and politics, which led him to working as the Director of Constituent Services for State Senator Nick Collins. This position is what prompted him to become more involved in Boston politics and eventually run for state office. In November of 2022, he was elected and in January of 2023 was inaugurated and became the State Representative of the community that raised him, the Massachusetts’ 5th Suffolk district.
As costs continue to rise, please give your thoughts on how the state will continue to support local aid to cities and towns to help support basic municipal services, specifically water, wastewater, and underground utility infrastructure.
The Healey-Driscoll administration has done an admirable job of identifying and proactively assisting municipalities around the state in need of municipal service funding and enhancements. This past September, the administration announced over $13.9 million in grants for repairing dams and coastal infrastructure across Massachusetts, aiding 23 municipalities and nonprofit organizations to mitigate risks from severe weather and rising sea levels. On October 16, 2024, the administration announced a new agreement between MassHealth, the Department of Transitional Assistance (DTA), and five utility companies to provide automatic utility bill discounts for hundreds of thousands of low-income Massachusetts residents. This partnership offers MassHealth and DTA members discounts of up to 25% on gas expenses and 42% on electric expenses, bringing hundreds of dollars in savings to residents this coming winter. In addition to the new projects and funding allocations, the administration has maintained dozens of unique agencies, programs, grants, and loans for municipalities to fund and update their water and infrastructure including the Massachu-
setts Clean Water Trust and the “Community Development Block Grant Program” administered by the MA Department of Environmental Protection.
Representing the 5th Suffolk District within the City of Boston, what are the biggest challenges for your district and the accompanying region with regard to continued economic growth?
The 5th Suffolk District has large immigrant populations and among the lowest median incomes in Massachusetts. The average net worth of Black Households in Boston is $8. The wealth gap that persists in the 5th Suffolk District and similar communities makes it challenging for residents to afford homeownership, start businesses, and build generational wealth.
Through my work as the State Representative, I have worked with business, government, nonprofits, educational institutions, and other community stakeholders to lift our communities up and connect residents with Boston’s thriving economic engine.
I have held community job fairs and partnered with different
continued on page 26
industries across the region to create pathways to careers less traditionally pursued in our communities. I have worked with housing advocates and developers to intentionally build housing for seniors and low-income families so that our residents can put roots down in the community that they love. I have partnered with all the health centers in my district to help advocate for their needs at the state level and ensure they are meeting the needs of their patients through pharmacy programs and mobile medical services. My office has been diligently working with our constituents and the City of Boston to establish more community processes for transportation and infrastructure projects. All this work is to promote enhanced resources and in turn economic growth for the members of the 5th Suffolk district.
Q:The #InvestInWaterMA campaign, sponsored by UCANE, highlights the importance of water infrastructure to a wide variety of industries. Please share a sampling of some of the specific industries in your district that benefit from our investments in water infrastructure?
A:Water and wastewater infrastructure affect economic development. When communities have reliable water infrastructure, there is ample
opportunity for fast economic development, but communities without it face many more roadblocks. In the 5th Suffolk, we greatly benefit from improved water infrastructure to continue operating breweries, food manufacturers, and hotels that dominate the workforce in the region. Water infrastructure investments also greatly benefit our construction and real estate industries by laying the groundwork for housing development. These systems, although frequently forgotten, are a key to economic development.
Q:Will you share your thoughts on how the construction industry might be able to meet its growing workforce needs as older members of the industry retire?
We must provide more access points for young people to enter the construction trades. There must be better communication between government, schools, unions, and industry to identify needs and provide pathways through vocational education to meet the demands of a 21st century economy. As someone whose career path did not take the “traditional” high school to college route, I understand the importance of connecting our youth with vocational programming and training that is engaging and provides a variety of ways to access a successful career.
continued on page 27
Interview continued from page 26
There are some great success stories of this sort of collaboration in Massachusetts, so it is imperative that we learn from what is working and scale it across every region in the Commonwealth.
Will you please share some of your other legislative or regulatory priorities during the current or upcoming legislative session?
This past October, Governor Maura Healey signed my first bill into law expanding the liquor license cap in the City of Boston. The bill instructs the Boston Licensing Board to create five non-transferable liquor licenses, in 13 zip codes, for three years to increase entrepreneurship, restaurant development, and economic development in under-invested communities. During my second term in the legislature, I plan to introduce a variety of legislation to better the lives of my constituents and the Commonwealth.
In continuation with some of my current priorities, I will focus legislative efforts on investing in our public schools, expanding access to homeownership, supporting small businesses and encouraging entrepreneurship, supporting economic growth and investment (especially in underserved communities), and taking on the affordability crisis. n
Construction & Public Contracts Group, Hinckley Allen, LLP
Last September, we discussed a new Department of Labor (“DOL”) “Final Rule” relating to the Davis-Bacon Act and Related Acts (“Davis-Bacon”). According to the DOL, the Final Rule was designed to “update regulations that implement” Davis-Bacon in order “to better the needs of construction workers on federal construction investments.” The DOL had commented that the new updates – which became effective on October 23, 2023 –were the “most comprehensive in decades.”
The DOL had summarized notable changes as follows:
• Creating new efficiencies in the prevailing wage update system and making sure prevailing wage rates keep up with actual wages which, over time, would mean higher wages for workers.
• Returning to the definition of “prevailing wage” used from 1935 to 1983 to ensure prevailing wages reflect actual wages paid to workers in the local community.
• Periodically updating prevailing wage rates to address out-of-date wage determinations.
• Providing broader authority to adopt state or local wage determinations when certain criteria are met.
• Issuing supplemental rates for key job c lassifications when no survey data exists.
• Updating the regulatory language to better reflect modern construction practices.
• Strengthening worker protections and enforcement, including debarment and anti-retaliation provisions. However, the Final Rule is extremely detailed and included content beyond what the DOL had summarized above. A complete and detailed summary of the Final Rule is beyond the scope of this article. Not long after the DOL announced its new Final Rule, the DOL faced a legal c hallenge. In the final
quarter of 2023, a group of plaintiffs (including a nationwide association representing general contractors) filed an action in the United States District C ourt for the N orthern District of Texas c hallenging specific portions of the Final Rule that they alleged would adversely impact contractors, namely:
• The Final Rule’s “operation of law” provision purporting to automatically impose Davis-Bacon requirements upon certain contracts even if not spelled out for such contracts as required by statute.
• The Final Rule’s “material supplier” provision, which purported to extend Davis-Bacon beyond mechanics and laborers to include certain material supply workers.
continued on page 31
• The Final Rule’s “onsite trucking” provision, which purported to extend the scope of Davis-Bacon to trucker time spent on site that is not de minimis.
The Court granted the plaintiffs’ request for a nationwide injunction barring implementation of these provisions of the Final Rule. The decision is now pending on appeal before the United States Court of Appeals for the Fifth Circuit. Given there is often room for interpretation, it is not yet clear how the Fifth Circuit will rule on appeal. In the meantime, the following is a very high-level summary of the Court’s decision, which is both detailed and dense.
As described by the Court, the Final Rule included a provision that purported to incorporate labor standards contract clauses and wage determinations “even when they have been wrongly omitted from a covered contract.” Under this provision, neither the DOL nor any other federal administrative body would be required to make a determination of the applicability of Davis-Bacon to a given contract. The Court described this provision as follows: “the Final Rule amends [Davis-Bacon] by imposing a self-implementing [Davis-Bacon] requirement into contracts by
an operation-of-law provision that contradicts the express statutory language of [Davis-Bacon].”
The plaintiffs alleged that automatic applicability provision would adversely impact the bidding process. The Court agreed, stating that “[c]ontractors bidding a contract need to know up front what the requirements are for the contract so that they can bid accordingly.” As to whether the requirements of Davis-Bacon apply to a given contract, the Court stated that “contractors must know if the [Davis-Bacon] requirements are in the contract or not.” The Court went on to note that “traditionally, the [Davis-Bacon] requirements are explicitly included in a provision in the contract, as required by the express language of [Davis-Bacon].”
If the operation-of-law provision were to remain in effect, c ontractors c ould find themselves bound by Davis-Bacon requirements even if not spelled out in the contract. This was problematic because – in light of the COVID-19 pandemic – “there was an increase of federal funds that went to areas and construction projects that traditionally never received federal funds or rarely received federal funds.” Thus, there were a host of projects that were suddenly subject to Davis-Bacon requirements even though they would not have been subject to Davis-Bacon requirements historically.
continued on page 32
Lawrence-Lynch Corp.
P.O. Box 913 • Falmouth, MA 02541
396 Gifford Street • Falmouth, MA 02540
PH 508-548-1800 • FX 508-457-1825
White Bros. – Lynch Corp.
P.O. Box 155 • Oak Bluffs, MA 02557 20 Vineyard Ave. • Oak Bluffs, MA 02557
PH 508-693-0845 • FX 509-693-0312
Visit our website @ www.lawrencelynch.com
The Court acknowledged that contractors could be “adversely impacted when the [Davis-Bacon] provisions are not included in the bid specification and contract at the time of bid but are then added later during the project or after the project is completed.” The Court added that retroactive application of DavisBacon requirements (including with respect to subcontractors that had already completed their work) would be “nearly impossible.” The Court concluded that this provision failed to provide contractors with sufficient notice of Davis-Bacon requirements in violation of basic contract and procedural due process principles.
The Court also took issue with the aspect of the Final Rule that would require contractors that have material supply operations to “pay prevailing wages and administer the [Davis-Bacon] requirements where they use their own material supply operations on their projects.” The Court acknowledged that some contractors “have a material supply operation because it is an investment in their business and enables them to gain a competitive advantage over those contractors that do not have a material supply operation.” However, those that have a material supply operation would find
themselves at a “competitive[] disadvantage[]” under the Final Rule because their material supply operation would need to comply with Davis-Bacon, whereas “their competitors who only provide material supply on the same project” would not be subject to Davis-Bacon under the Final Rule. According to the Court, the Final Rule “amount[ed] to a fundamental amendment to [Davis-Bacon]” which “would reclassify employees of bona fide material suppliers as ‘mechanics and laborers,’ in a manner clearly contrary to the plain language of [Davis-Bacon].” In so doing, the Final Rule “arbitrarily and capriciously discriminates” against contractors that also have material supply operations.
The Court also found that contractors would be adversely affected by the “on site trucking” provision of the Final Rule which purported to “require contractors to track their truck drivers’ time on the jobsite to ensure any time that is more than a de minimis amount of time spent on-site is recorded on the certified payroll records and paid at least the applicable [Davis-Bacon] rate.” The Final Rule did not define what c onstituted a de miminis amount of time. Therefore, the Final Rule would require contractors to undertake the administrative costs and burdens
continued on page 33
associated with attempting to track truck drivers’ time or incur the costs of applying the Davis-Bacon rate to the “entire time” so as not to “run afoul” of the Final Rule. The Court stated that these costs could “be the difference between winning a bid and not.” The Court concluded that this provision violated the “plain,” “simple” and “unambiguous” language of the statute, which applies “only to ‘mechanics and laborers employed directly on the site of the work.’”
The plaintiffs alleged that these provisions of the Final Rule were unconstitutional, unlawfully extended Davis-Bacon, and issued in excess of the DOL’s statutory authority. The Court agreed, and granted the plaintiffs’ request for a nationwide injunction halting implementation and enforcement of these specific aspects of the Final Rule. The Court concluded that the DOL exceeded its statutory authority and engaged in “egregious violations” of the Constitution by “usurp[ing] Congress’ lawmaking power” by attempting to impose substantive amendments to the statute via its Final Rule. At least for now, this injunction remains in effect. The injunction is limited to the specifically challenged aspects of the Final Rule. n
UCANE’s Construction Outlook magazine editors recently caught up with Mark Brown at the Sunbelt Rental Store in Shrewsbury, MA. Mark is the Northeast Area Safety Director for UCANE member Sunbelt Rentals, Inc. a national company specializing in construction equipment rentals with more than 1,200 locations across the country. We were able to get a few minutes of Mark’s time to talk about the importance of Safety in the construction equipment rental business and in the construction industry in general.
over two decades total and had contracts with numerous high profile Construction Managers and Owners. My work during this time spanned across the Eastern coast. I was eventually referred by a friend to Bill Cove, a 25 year Safety Director at Sunbelt Rentals, and after a long process and background checks, I was hired this past summer.
Please describe your role at Sunbelt? What geographic area do you cover and how
Privately held and family owned businesses often face unique issues and challenges. Hinckley Allen attorneys have been advising such businesses for decades and have accumulated deep expertise.
We understand that the issues faced by a privately held or family owned business often reverberate through the broader family dynamic, and that a clearly defined strategy for running and transitioning the business is essential for both corporate and familial harmony.
Our attorneys can assist with a variety of legal issues: including succession and tax planning issues, employment-related issues, retaining quality outside directors and advisors, and managing exit transactions.
Learn more about our offering at www.hinckleyallen.com
Jennifer V. Doran Chair, Privately Held & Family Owned Businesses
617-378-4128
jdoran@hinckleyallen.com
Safety & Compliance continued from page 35
many Sunbelt Rental Stores are you overseeing?
I am a Regional Safety, Health and Environmental Manager at Sunbelt. I am responsible for the safety of 31 branches spread throughout a very wide territory covering all of New England and New York (NOT NYC).
With such a wide array of construction equipment available to rent, and with equipment constantly evolving, how do you keep yourself and Sunbelt personnel up to date on safety concerns with all this equipment?
Moving from the construction safety business to the equipment rental safety business is an adjustment but at the same time exciting. Attending Sunbelt University is required of all our new team members and that has helped me with this transition. The majority of Sunbelt employees are company veterans, well versed in Safety and in the operation of equipment that we rent. At this point they are teaching me as much as I’m teaching them. The rental equipment is always changing, but upper management offers great support and some great new ways to approach safety.
In addition to that, I am old school in regard to my approach with safety and make sure I listen to the Branch managers and employees when I visit the rental stores. Sunbelt also uses video safety meetings with real team members every week, which helps to show new issues and injury trends.
I also have learned to review our leading and lagging indicator dashboards to aid with injury prevention. New technology such as Microsoft Teams helps tremendously with keeping up with new trends and issues we face. Case in point, we recently converted from hardhats to helmets for the thousands of drivers unloading and loading, and we are now pushing the use of impact gloves since hand injuries have shown a recent increase.
Please tell us about the culture of safety that exists at Sunbelt Rentals?
It is excellent. I have never had such support in my whole career. The Sunbelt Safety culture is one of constant engagement. The essence of Sunbelt accident prevention is with its team and unified approach to safety based around a strong network of professional peers and colleagues. It is refresh -
continued on page 39
Safety & Compliance continued from page 37
ing and comforting knowing you have a great support team at all levels.
The construction industry should take note, Sunbelt is more engaged when it comes to safety than any contractor I have worked for. Hence my decision to come here.
What are some of the greatest challenges you face as a Safety Professional?
In my past (not at Sunbelt) it was upper management allowing toxic employees to continue working since they are good at their job. This destroys company culture and creates a culture of nepotism. Teamwork is more important than aggressive personalities that are cynical. Gaining the trust and support of the 300+ employees in my district is important for any safety supervisor’s position. For such
a large service area, that doesn’t happen overnight, but in my first year here it is progressing well.
What advice do you have for young students, or for those considering a career change, to become a Safety Professional in the construction or equipment rental industries?
Both industries are expanding when it comes to opportunities for safety professionals. For someone considering entering the safety industry I would be sure to spend some time vetting the company before you go for an interview. Learn about their operation and maybe check their OSHA history. Ask to visit a jobsite or a store.
There is currently a strong demand for safety professionals. Stay away if the company does not have a good safety record or culture starting at the top. Choose your employer and your future wisely. n
508-587-6953
This year, the U.S. construction industry will need to hire roughly half a million workers on top of the normal pace of hiring to meet demand, according to a projection from Associated Builders and Contractors.
The labor shortage is hitting organizations from all angles. On the one hand, retirement levels are high; on the other hand, newcomers to the industry may be put off by what they perceive as a staid career path, or they may be quick to leave for other industries. Meanwhile, managers and other midlevel employees — the very people expected to maneuver companies through this moment — are quitting at elevated rates.
As someone who helps construction companies around the country source skilled talent, from superintendents to project managers and engineers, I’ve seen firsthand how tempting it is to identify one area or potential solution as a silver bullet. “If only we could hire more entry-level talent,” one might say, or “If only we could outsource more work to third parties.”
The list goes on. But narrow efforts, while understandable, c an end up a lot like “whack-a-mole.” Instead, a multifaceted problem requires a multifaceted solution.
One size does not fit all for c onstruction c ompanies navigating today’s labor shortage. For instance, executives regularly complain that they spend lots of time and money developing entry-level talent — but right as they’re about to see a return on investment, those employees leave for another job.
My response? If you look at hiring entry-level tal -
ent as just a proportion of your overall staffing strategy and understand turnover rates, you can make sure you’re not adding more employees at this level than is profitable. A holistic, multipronged approach should help meet current demand and be understood as a long-term play.
A few of those prongs include:
Internal resources and talent acquisition teams — These are important, especially when it comes to ingraining your organization in local universities, engineering schools and technical colleges to attract new talent at the start of the pipeline, be it through internships and apprenticeships, training and education programs, or simply heightened visibility with potential hires.
Outsourcing — An outsourcing strategy is another important lever to pull, empowering companies to leverage external expertise, enhance efficiencies and cut down on certain talent costs. Key functions worth exploring include project management, design and engineering services, IT and technology, and sustainability consulting, among others.
continued on page 42
continued from page 41
Consultants — Finally, hiring consultants who can help provide access to talent could round out a holistic strategy, especially given the current burdens on internal resources. For example, consultants could supplement internal efforts by bringing in more midlevel resources on an assignment basis to relieve pressure on managers.
Of course, enacting a multifaceted talent strategy is no simple feat. Here are a few best practices that construction executives should keep in mind as they get started.
Get the right internal systems and processes in place — Some companies are great at getting their names out there and attracting skilled workers but don’t have the systems in place to bring them in, whether it’s ineffective payroll processes, a lack of onboarding resources or an inability to find the right talent from their own inbound application systems. (I’ve heard from qualified people who have applied to jobs for three years at one well-known company without hearing back.) Streamlining systems and processes is critical; it might also help to engage and “try out” new employees on a contingent basis before making a full-time hire.
Avoid manager meltdowns — Engaging new employees has never been more important, but managers navigating a talent deficit and changing workplace norms are increasingly burnt out. Ensuring new hires get what they need without sacrificing managers’ productivity and well-being requires striking a delicate balance. This starts from the top: Construction executives should provide a sense of security and stability for frontline managers by offering additional resources and support, as well as relieving some of the burden of developing new talent by leveraging a more multifaceted talent strategy.
Personalization is key to employee engagement — Personalization should improve engagement across the organization. This entails employers and managers taking consistent, genuine interest in their people and being willing to have difficult conversations. This doesn’t mean micromanaging. For instance, asking, “What can I offer or help with to make you feel more comfortable or successful?” is very different than saying, “Today I expect you to call Jess, calculate these figures like this, tackle the project in this order and report back on how far you get by the end of the day.”
Offer training that finds a happy medium between what your company needs and what employees want — Today’s construction companies can’t just tell their up-and-coming employees to stay in their lane. They want opportunities to develop their skills and grow in their careers, which, in our fastpaced business landscape, is one way to engender employee loyalty. So don’t thrust all the menial work
How to Solidify continued from page 42
on new hires because that’s what you had to do when you started out. In fact, simply making cross-training/ career progression tools and programming available can build trust and let employees know you’re listening.
Update your value proposition — Some construction companies are still selling themselves like they did two decades ago, highlighting benefits packages or employee-owned business models. While those are great, newer employees rarely see the value in them in the near term. What they want is practical (and meaningful) work experience and skills that will set them up for success. They also want to work on projects they can get excited about, like a new sports stadium or educational facility.
Hire more diversely — The construction industry is finally waking up to the vast, untapped potential of women and workers from other underrepresented groups. However, this must go beyond marketing language. It comes down to accountability: If this is who you want to be as an organization, you must hold people accountable should they act counter to your values.
Keep an open mind — Today’s construction leaders can’t afford to require every new hire to meet all the bullets in the job description. Understand that you’re going to need to teach and coach new employees no matter what, so it’s OK to be more flexible in
certain cases. Similarly, try not to brand employees as “good” or “bad.” There could be a great employee who simply went through something difficult in their personal life or is struggling and doesn’t know how to ask for help. It doesn’t mean that, with the right care and management, they won’t be a top performer. Treat people the way they need to be treated, and they’ll flourish.
Broadening your talent pool and strategy offers significant benefits for today’s c onstruction c ompanies, many of which will need to institutionalize existing knowledge and pass it along as a wave of workers retire. New hires can also bring new energy to an organization through the embrace of emerging technologies like artificial intelligence, fresh perspectives or different ways of c ollaborating.
Getting there may be an uphill climb given present challenges. That’s why executives should harness every tool in their arsenal to address this complex problem from all sides — and usher in the next generation of construction talent.
Written by Joe Supino. This article was originally published in the September 2024 issue of Construction Business Owner magazine. Visit https://www.constructionbusinessowner.com/ management/how-solidify-your-hiring-retention-strategies to read more. n
We make decisions about risk every day in our personal and business lives. For construction business owners (and everyone in the construction industry), bad outcomes can mean the difference between staying in business or not. Here are five risk myths that get in the way of thinking about important risks you may be overlooking — and accepting.
It is true that the larger the company, the more resources and time can be spent taking a broader look at risk. But for smaller companies, risk can be much more dangerous. Your margin for error with limited financial resources and c ash fl ow is more c ritical than for most large firms. Less resilience means you need to pay close attention and think about how you identify and manage r isk for your firm. You c an use simple, cost-effective risk tools in place of the expensive consultants, complicated analyses and dedicated internal teams that larger firms deploy.
Start with avoiding simple mistakes like overlooking things you know. How? Use checklists. Busy people who work with complex processes and systems are prone to forgetting a simple step, a required form, a critical safety check, etc. Those unforced errors can be costly. Dr. Atul Gawande wrote “The Checklist Manifesto” in 2010. He noted the dramatic effect checklists had on reducing and eliminating errors when used by doctors, pilots and even investment fund managers: “[T]hey chose to accept their fallibilities. They recognized the simplicity and power of a checklist.”
Too simple? You are already using one: your
submittal schedule. Checklists can be made, refined and used for everything from corporate filings and license renewals to field issues like safety and equipment maintenance. The most important ones for your company should be your go/no-go checklist for project screening and your risk register for project-specific risks. Using checklists regularly for all your company’s operations will benefit your bottom line, over and over.
It is easy to fi xate on external r isks, but many of the most dangerous risks you face lurk inside your company. Because you understand your business and your company so well, there can be a tendency to discount your own risk — but that can also create a blind spot right under your nose. In a Harvard Business Review article, Robert S. Kaplan of Harvard and Anette Mikes of Oxford University call these internal risks within an organization “preventable risks” that “are controllable and ought to be eliminated or avoided.” O ften, it is in your most profitable times that you are likely to overlook these risks.
Vince Lombardi said: “You block and tackle better than the team you’re playing, you win.” What is
continued on page 46
5 Myths Demolished continued from page 45
blocking and tackling for a construction company? Start with the start. What do you have in place to determine whether to pursue a new opportunity or not? A go/no-go process can screen out later failures and losses where you say: “I should have seen it coming!”
For projects that are won, do a thorough risk register. Identify risks to successful performance, develop mitigation measures and continually update the plan during the execution. During performance, track and manage change orders, payment and quality requirements. Reading and understanding the processes and requirements of the contract documents will make sure you are managing this specific project, and not defaulting to the usual practices you have adopted over time. These risks, and the losses they create, are the easiest for you to eliminate.
It is only human nature to spend our time worrying about the biggest things, such as the biggest construction projects. You have probably been told the “80/20 rule” says you should spend 80% of your time working on the 20% of things that matter (usually meaning most profitable). But the saying, “It’s the little things that come up to bite you” exists for a reason: We overlook the little things. Sometimes these are “pet projects”
or an opportunity to get a foot in the door — projects that are taken on for various reasons but do not match the company’s typical project size or type (or both). Small projects tend to suffer from a lack of sustained management interest, a lack of sufficient experienced staffing, and a lack of planning and risk identification. When one of these projects results in a claim or lawsuit, you may find your small project just brought on a big exposure. Physical injuries, consequential damages like lost profits and regulatory enforcement can mean you will have expenses that dwarf the small profit you could have made — if all had gone well. Many small projects miss a formal go/no-go process and a risk register because it “just wasn’t worth it.” Bottom line: Risk can be ver y disproportionate to project size.
Mark Ingebretsen, author of “Why Companies Fail,” wrote: “Perhaps nothing can bring a company down with such amazing speed as misconduct.” Employee misconduct happens in smaller companies, and by people who friends and coworkers know as nice, quiet and respected.
Florida Atlantic University College of Business (FAU) reports that “smaller businesses (less than 100 employees) are more vulnerable to fraud than larger ones. … ” A business.org survey found 22% of small continued on page 47
businesses had employees steal from them. FAU points to several causes: lack of internal controls, higher rates of fraud by small business owners and executives, and the tendency to have a single person in charge of many areas without effective oversight. But this couldn’t possibly happen to your company, where you know everyone, right? According to a 2016 article by Andrew Donohoe and Stephanie Allgeyer with VonLehman CPA, 85% of employees committing fraud are first-time offenders. It happens over and over to the least suspecting.
You won’t recognize anyone in your company as being someone capable of fraud, theft or any other type of misconduct. If you could, you wouldn’t have hired them in the first place. Internal systems and financial controls have to be in place for this reason — by the time you realize someone was stealing from you or engaging in other types of misconduct, it may be too late for your company to survive.
Many employees, from the CEO to your front-line workers, think insurance takes care of everything. Other companies may think of your insurance that way too: “Just submit the claim to your carrier. What do you care?” Anyone who has been through the underwriting process for policy applications or renewals knows how important your company’s loss experience is to the cost of insurance. Just as important to the insurer is how you manage your business, including claims and settlements. Premiums, coverage offered, exclusions, and deductibles or self-insured retentions — all are impacted by how you treat an insurer’s coverage. Is it with as much care as you would show for your own money? Those claim payments are recaptured in future premiums — think of it more as loss financing than loss c overage. Over time you will be paying it back.
Treat your broker and insurers as your partners. Simon Burtwell with EY advises: “Don’t think about an insurance product as a commodity that is bought simply on price; it must be a service solution that is bought based on perceived value to reduce risk and manage loss.” Experienced construction brokers and insurers, including sureties, want to help you manage your r isk. It financially benefits them; it financially benefits you. Take advantage of their resources, from webinars and articles to contract review services and site audits. Your bottom line will be better off avoiding claims and having fewer of them to pay.
Written by Bruce Gerheardt. This article was originally published in the May 2024 issue of Construction Business Owner magazine. Visit https://www. constructionbusinessowner.com/management/5risk-myths-demolished to read more. n
Christopher Clark World Insurance Associates, Inc.
In recent years, floods have become one of the most devastating natural disasters worldwide, fueled by climate change and urban expansion. From catastrophic river overflows to coastal surges these events have inflicted severe damage on communities, businesses, and infrastructure. The construction sector has suffered significant setbacks, with project delays, equipment and property destroyed, and cost to rebuild and replace skyrocketing.
Flood insurance is crucial for construction companies for several reasons, particularly regarding equipment, property, materials, and financial r isk management but many companies are not adequately covered.
Construction projects involve substantial investments in assets such as equipment, materials, and temporary structures. Flood insurance protects these investments by covering losses related to water damage. W ithout insurance, a single fl ood c ould lead to devastating financial c onsequences, jeopardizing the entire project or even the company.
• Equipment Loss: Heavy machinery is often onsite and vulnerable. Repairs or replacements can be exorbitantly expensive without coverage.
• High Value: Construction equipment, such as excavators, bulldozers, and cranes, represent a significant financial investment.
• Damage Risk: Flooding can cause extensive damage to equipment, leading to costly repairs or total loss, which can halt projects and impact timelines.
• Insurance Coverage: Flood insurance ensures
that if equipment is damaged or destroyed by flooding, the c ompany c an recover losses and replace essential tools without c rippling their finances.
• Physical Premises: O ffices, storage facilities, and jobsites are often vulnerable to fl ooding, especially in areas prone to heavy rainfall or near bodies of water.
• Restoration Costs: Flooding can lead to structural damage and costly restoration efforts. Insurance
continued on page 50
helps cover these expenses, minimizing disruptions in operations.
• Liability Concerns: In case of a flood, there could be liability issues related to employee safety and property damage to clients or subcontractors, which insurance can help address.
• Investment in Materials: Construction projects often require significant investments in materials, which can be lost or damaged during a flood.
• Insurance Coverage: Flood insurance can cover losses of materials that are typically expensive and essential for project completion, ensuring continuity and reducing financial knock-on effects.
Flood insurance provides financial security in the face of unexpected challenges. Construction projects typically operate on tight margins, making it vital to manage costs effectively.
• Business Interruption: Flood damage can lead to significant downtime, impacting cash flow. Insurance can mitigate some of this uncertainty.
• Credit and Bonding: Having flood insurance can
improve a construction company’s credit profile and bonding capacity, as lenders and bonding companies look favorably on businesses that manage risk adequately.
• Long-Term Stability: Investing in flood insurance is a proactive risk management strategy, promoting long-term business stability and resilience against environmental changes.
• Mitigation of Cost Overruns: In the event of a flood, insurance can cover restoration and replacement expenses, helping to avoid significant cost overruns that can threaten project viability.
• Cash Flow Stability: Insurance coverage ensures that companies have the necessary funds to recover and continue operations, preventing cash flow disruptions that could halt progress.
Many contracts require proof of insurance before construction work begins. Flood insurance may be a stipulated necessity, especially for projects in floodprone areas.
• Meeting Regulatory Requirements: Some local governments mandate flood insurance for con-
Let us review your programs and recommend improvements to ensure you are fully protected should the unexpected happen.
RISK MANAGEMENT SOLUTIONS
• All forms of liability and property coverages
• Bonds including Express Bond Program
• Competitive terms
• Personalized service
• Employee and executive benefits
• Retirement planning services
• Investment advisory services
• Private wealth management
• Personal and high-net-worth portfolios
• Highly experienced with Construction programs CHRISTOPHER CLARK, PRINCIPAL, CLIENT ADVISOR World Insurance Associates LLC, 50 Prospect Street, Waltham, MA 02453 O 781-642-9000 | D 781-398-9318 | M 508-400-4010 | christopherclark@worldinsurance.com worldinsurance.com
struction in designated flood zones, ensuring compliance with regulations.
• Protecting Client Interests: Providing insurance proves to clients that their investments are safeguarded, enhancing your company’s credibility and marketability.
Incorporating fl ood insurance into a broader r isk management strategy is vital for long-term success.
• Enhanced Planning: Having insurance encourages better planning for fl ood-related c ontingencies, prompting companies to devise strategies that minimize potential damage and downtime.
• Building Resilience: Companies that invest in flood insurance demonstrate a c ommitment to resilience and sustainability, aligning with growing environmental consciences in the construction industry.
Flood insurance is not merely an optional safeguard; it is a crucial component of successful construction project management. By protecting valuable assets, ensuring financial stability, meeting c ompliance requirements, and fostering a resilient operational framework, fl ood insurance plays an essential
role in mitigating risk and enhancing a company’s ability to deliver projects on time and within budget.
Embracing flood insurance contributes to the overall sustainability and reliability of construction practices, ensuring that companies are well-equipped to face the challenges posed by nature. In a world where flooding is an increasing reality, proactive measures such as investing in flood insurance are essential for any construction project’s success.n
Manufacturer & Installer of Bituminous Concrete Products:
Holden Trap Rock Co. 2077 N. Main Street (Route 122 A)
Holden, MA 01520
Tel: 508-829-5353
Fax: 508-829-9346
Tel: 978-838-9999
Fax: 978-838-9916
With over two decades of experience across diverse industry sectors, Je brings his insights and experience with complex transactions, as well as an extraordinary ability to resolve disputes to Hinckley Allen’s nationally ranked Construction & Public Contracts Group.
CONTACT: Je D. Bernarducci
617-378-4155
JBernarducci@hinckleyallen.com
EPA announces new final regulations and availability of $2.6 Billion in nationwide funding to accomplish the task
WASHINGTON – October 8, the Administration took action to accelerate lead drinking water pipe replacements by issuing a Final Rule requiring drinking water system owners across the country to identify and replace lead pipes within 10 years. The Lead and Copper Rule Improvements (LCRI) also require more rigorous testing of drinking water and a lower threshold requiring communities to take action to protect people from lead exposure in water. In addition, the final rule improves communication within communities so that families are better informed about the risk of lead in drinking water, the location of lead pipes, and plans for replacing them. This final rule is part of the administration’s commitment to replace every lead pipe in the country within a decade, making sure that all communities can turn on the tap and drink clean water.
The newly available $2.6 billion is part of the 2021 Bipartisan Infrastructure Law that provided an historic $15 billion in funding for lead pipe removals and another $11.7 billion to be used for both drinking water and lead pipe removal projects. The $2.6 billion will fl ow through the Drinking Water State Revolving Funds (DWSRFs) and will also support both lead pipe inventory and removal projects. Additionally, 49% of the funding must be provided to disadvantaged communities as grant funding or principal forgiveness that does not have to be repaid. EPA is also announcing the availability of $35 million in competitive grant funding for reducing lead in drinking water. Communities are invited to apply directly for grant funding through this program.
The science is clear: Lead is a potent neurotoxin and there is no safe level of lead exposure, particularly for children. In children, lead can severely harm mental and physical development, slow down learning and irreversibly damage the brain. In adults, lead can cause increased blood pressure, heart disease, decreased kidney function, and cancer. If someone is impacted by lead exposure, there is no known antidote, according to the Centers for Disease Control and Prevention. The LCRI strengthens nationwide requirements to protect children and adults from these significant and irreversible health effects from lead in drinking water.
EPA estimates that up to nine million homes are served through legacy lead pipes across the country,
many of which are in lower-income communities and communities of color, creating disproportionate lead exposure burden for these families
EPA Region 1 announces partnerships with six Massachusetts cities to accelerate replacement of lead water pipes and protect public health
“Everyone deserves to have safe, clean water in their homes, no matter where they live or how much they earn. With today's announcement, we're helping six communities in Massachusetts accelerate the replacement of lead pipes, protecting children and families from the harmful effects of lead exposure," said EPA Regional Administrator David W. Cash. continued on page 55
• Chelsea, MA: Chelsea will be assisted with identifying lead pipes through the review of historical records and c onducting of field verifications, which will include door-to-door service line identification and excavation work. Additionally, Chelsea will receive help developing a comprehensive lead service line replacement plan, increasing community outreach and education, and applying for funding. Community engagement efforts will include creating materials like door hangers and bill inserts, supporting public events, and offering translation services.
• Fall River, MA: Fall River will be supported in identifying lead pipes through a t argeted field verification plan. This will involve door-to-door efforts to identify private service lines and map out high priority areas for future investigation. The city will also benefit from expanded community outreach and education, including the development of outreach materials, support for public events, and translation services to ensure wide community participation.
• Malden, MA: Malden will receive assistance with lead pipe identification through field verifications and doorto-door efforts to identify private service lines, along with excavation work. Additionally, Malden will also receive help developing a comprehensive community engagement plan aimed at improving outreach efforts, encouraging customer participation, and providing translation services for better community involvement.
• Melrose, MA: Melrose will be assisted with identifying lead pipes through field verifications, door-to-door identification efforts, and excavation work. Melrose will also be assisted in developing lead service line replacement plans and in applying for lead service line replacement funding.
• Revere, MA: Revere will receive support in identifying
lead p ipes t hrough t he d evelopment of a fi eld verification p lan a nd c onducting excavations. Revere will also be assisted in creating a lead service line replacement plan, and community outreach by developing engagement materials, supporting public events, and offering translation services to reach as many residents as possible.
• Taunton, MA: Taunton will be assisted in developing a field verification plan to identify lead pipes, conducting door-to-door service line identification, and performing excavation work. Technical Assistance will also help enhance the city's community outreach and education efforts by creating engagement materials, supporting public events, and providing translation services to better serve its residents. n
Let us take a refresher today on personal fall arrest systems (PFAS) and its usage and requirements. Fall protection equipment is necessary, and sometimes life-saving, for anyone who works on surfaces six feet above the ground or higher. It's specifically designed to prevent, protect, or rescue someone before, during, or after a fall. The Occupational Safety and Health Administration (OSHA) recognizes falls as one of the most common causes of serious work-related injury or death, especially in construction work. Thus, OSHA requires that you utilize fall protection and safety equipment to keep you and your workers safe.
From the chart 1 items 1 through 3, there are controls to be considered by the contractor in order to prevent falls or to eliminate the hazard of falling. Item 4 (Fall Arrest Systems) is not a method to control the fall hazard, it is the method to protect the worker AFTER THE FALL occurs. In the scope of jobsite safety plans and OSHA regulations that often seek ZERO accidents, the Fall Arrest System is somewhat unusual in that it acknowledges that certain job activities may result in an accidental fall and it is the responsibility of the employer to protect the worker in case that occurs.
In all truth, it is not the fall that will cause the injury but the stop at the end so we must lessen the force of that stop with our PFAS.
In the event of a fall gravity will pull a worker down at 32 feet per second, and the speed of descent will accelerate during the fall until either there is a stop or you reach terminal velocity – approximately 120 miles per hour. To put it in perspective, count two seconds; one Mississippi, two Mississippi. A worker just fell 6 4 feet or five stories with a force exceeding 12,000 pounds or more depending on surface struck or part of the body struck.
continued on page 58
Safety Corner continued from page 57
Fall protection equipment is necessary, and sometimes life-saving, for anyone who works on surfaces six feet above the ground or higher. It's specifically designed to prevent, protect, or rescue someone before, during, or after a fall.
mon causes of serious work-related injury or death, especially in construction work. Thus, OSHA requires that you utilize fall protection and safety equipment to keep you and your workers safe.
The Occupational Safety and Health Administration (OSHA) recognizes falls as one of the most comA complete PFAS includes: Anchor Point + Body Wear + Connector
Let’s look at the personal fall arrest system, its components, requirements, and limitations. I use information from the OSHA standards, ANSI Z359 and manufacturers’ instructions. The Biggest, Baddest Ditch Witch Hydrovac to ever hit the wild ...
Introducing the most powerful Ditch Witch truck vac to ever hit the open road — the Warlock Series W12. With a 2,800 PSI water system, 12 cubic yard debris tank capacity, and a 5,000 CFM, 27″ Hg vac system, this beast-of-a-machine easily devours jobs of all shapes and sizes.
continued on page 59
South Plainfield, NJ: 908-753-8080
Shrewsbury, MA: 508-719-0200 Lumberton, NJ: 609-534-7477 Beacon, NY: 845-831-1800 Deer Park, NY: 631-392-2605 Middletown, DE: 302-376-0784 Baltimore, MD 410-687-1700
FOR
Safety Corner continued from page 58
• Standard harness, lanyard, and anchor have weight limit between 130 – 325 pounds for user, clothing, and gear.
• User should “Ensure your health and physical condition allow you to safely withstand all of the forces associated with working at heights. Consult with your doctor if you have any questions regarding your ability to use this equipment.” (excerpt from DBI Sala manual)
• With self-retracting devices, avoid sudden or quick movements as device may lock up.
• “X” manufacturers’ equipment is designed for use with “X” approved components and subsystems only. Substitutions or replacements made with non-approved (i.e. others) components or sub systems may jeopardize compatibility of equip ment and may affect safety and reliability of the complete system.
• Limit arresting force to 1,800 pounds maximum. (Most systems will reduce this force anywhere from 400 pounds to 1,100 pounds depending on fall distance.)
• Limit free fall to six feet or less.
Of course, the best solution is to not work at heights or not fall. Most people believe this only is germane to buildings but I have seen trenches and excavations that are 30 feet deep or more. Keeping our workers from falling into a trench, manhole, or excavation should be our primary focus in planning, not putting them in a PFAS, which can pose a hazard if they fall. n
• Worker must be trained in proper donning, wear, cleaning and inspection of system components.
• Always inspect all components before use.
• Assess the tasks and conditions where system will be used to determine best components to use, anchor point (fixed or moveable) and fall distance to lower level.
Anchor points can sometimes cause an issue as there is not always an anchor point over a worker’s head. It could be at the side or at their feet. An example of this and its affect on fall distance is: 6-foot lanyard with 3-foot decelerator:
• Anchor point above lower level is 17 feet.
• Anchor point at feet requires 21 feet beneath the worker.
When used in a mobile elevating work platform, you must use fall restraint up to 19 feet off the ground then you can use fall arrest above that.
The PFAS system you choose will also require you to have a rescue plan. This is due to the effects of suspension trauma on the body when free hanging from a PFAS. Some harnesses today have self-rescue capabilities and others have leg straps to aid in reducing suspension trauma but ALL require proper training.
Vactor Service/Hydro Excavation
● 24/7 Emergency Service
● Plant Maintenance
● Catch Basin Cleaning
● Filter Media Removed from Tanks
● Lift Stations and Pump Chamber Cleaning
● High Velocity Water Jetting
● Clean Sewer and Drain Lines
The Utility Contractors Association of New England, Inc. (UCANE) was honored to join many of our members at the second annual Workforce Development Trades Day, a significant event generously hosted by W. L. French at their state-of-the-art facility in Billerica, MA. This event, held on Thursday, October 17, 2024, brought together approximately 200 students from various Massachusetts trade schools, offering them firsthand exposure to the dynamic, well-paying careers available in the construction industry.
UCANE’s Executive Director Joseph Nolan, alongside Member Services and Educational Manager Mike Lenihan, joined the W.L. French team and UCANE members including C. N. Wood Co., Inc. United Rentals, and Milton CAT. Together, they introduced students to the skills, opportunities, and rewards that come with a career in construction. In addition to meeting industry professionals, students were able to engage with hands-on demonstrations and presentations that showcased the technology, tools, and skills central to modern construction work.
One of the greatest challenges our industry faces today is attracting and recruiting new talent to serve our growing member companies. Skilled professionals are essential to support infrastructure projects, meet the rising demand for sustainable practices, and advance safety standards in the field. Events like this provide a unique opportunity to highlight the financial and personal rewards of working in construction, especially for students who may not want the financial
burden of a traditional college education. The event’s open discussions and live demonstrations allowed students to imagine their own futures in the industry, making a c omfortable and fulfilling living while c ontributing to the communities they live in.
It was a beautiful day for such an impactful event. UCANE extends a heartfelt thank you to Lisa FrenchKelley, Bill French Jr., Jessica French, and Tom Dion at W. L. French for allowing us to participate, and of course for their hard work in organizing and hosting this important event. Their commitment to workforce development is inspiring, and we look forward to working together with them in the coming years to provide opportunities in construction to future generations of students.n
The MBTA recently announced that the Agency will receive nearly a half-billion dollars in competitively sought federal funds to replace a Depression-era drawbridge over the Charles River, the largest federal grant the MBTA has ever won. The Grants were competitively sought by state agencies across the country as part of a program within the Bi-partisan Infrastructure Bill.
The MBTA received the largest single grant among 44 Grants totaling $5.3B. The funds will be used to replace Drawbridge One that runs adjacent to the Leonard P. Zakim Bunker Hill Memorial Bridge and connects Boston to Cambridge. The 93-year-old bridge carries more than 11 million passengers per year on both the commuter rail and Amtrak trains. Work also includes renovations at North Station and upgrades to train infrastructure in the area, according to state authorities.
The grant — $472,300,616, to be precise — comes from the National Infrastructure Project Assistance program, also known as The Mega Program. According to the Transportation Department, it “sup -
ports large, c omplex projects that are difficult to fund by other means and are likely to generate national or regional economic, mobility, or safety benefits.”
O ther recent awards, G overnor Healy’s office said, include more than $67 million for accessibility upgrades at MBTA Green Line stations and nearly $40 million toward replacing diesel-fueled buses at the Quincy Bus Maintenance Facility with batterypowered buses.
The state has also drawn $1.2 billion to replace the Cape Cod Bridges, $335 million for a major highway upgrade project on the Massachusetts Turnpike in Allston and $108 million for a cross-state WestEast Rail line.
Massachusetts Bay Transportation Authority
Boston, Massachusetts Urban
Mega Award: $472,300,616 (FY 25 - $283,235,887, FY 26 - $189,064,729)
Project Description:
The project will replace the Draw 1 rail drawbridge used by Amtrak and MBTA, extend and activate a platform with two tracks at North Station, and replace track, signals, and switches throughout the project area, including for an interlocking utilized by a local construction aggregate material supplier.
Project Benefits:
The project is strong in State of Good Repair and Climate Change, Resiliency, and the Environment. The Draw 1 bridge is a crucial access point for MBTA and Amtrak, serving 11 million riders annually. The project will reduce operational and maintenance costs for MBTA and includes a resilient design to prevent floods and account for sea-level rise in the bridge. The project will improve environmental outcomes by reducing fuel consumption and allow for future electrification if MBTA chooses to adopt it. It will also facilitate greater freight efficiency for producing and disseminating construction materials in the region. This project is expected to utilize union labor in construction.
In a major victory for the Town of Dennis, voters at the October 1, 2024 Special Town Meeting attended by more than 400 residents, unanimously approved “The Dennis Plan” for wastewater management. The plan, estimated at a $248 million cost over 30 years, is designed to protect the town’s valuable water resources including drinking water, freshwater ponds, and saltwater beaches, and estuaries.
Current financing options available through MassDEP will provide significant financial savings to taxpayers by leveraging zero percent financing and 3 0 percent debt forgiveness through the Massachusetts State Revolving Fund (SRF). Additionally, the state’s Clean Water Trust is another revenue source set up to solely benefit c ommunities on Cape Cod, Martha’s Vineyard, and Nantucket. Its source of revenue is a 2.75% excise tax on traditional lodging and short-term rentals. All tolled, the excise tax revenue, zero interest loan, and partial loan forgiveness is estimated to save the town more than $100 million in financing costs.
The wastewater initiative is the culmination of decades of work by the Dennis Wastewater Team, which has been diligently designing, planning, and securing permits to ensure the town's long-term environmental sustainability. This team has explored every option to create a comprehensive solution to address the town’s growing wastewater management needs, ensuring the plan complies with local, state, and federal environmental standards.
The long-term wastewater plan will be implemented in eight phases, but Select Board Chair Chris Lambton noted that the treatment plant would be an expensive early project but a one-time cost. When
one resident asked if the state could pay for the entire project, Lambton said the state said no. “We either pay for wastewater now or (homeowners) put in all new septic systems at $50,000 to $60,000 each,” he said. “The most important reason to do this is for the next generation.”
Phase 1 of the “Dennis Plan” includes the design, permitting and construction of a wastewater treatment plant off Theophilus F. Smith Road, construction of a sewer collection system along the commercial planning district on Route 28, residential areas along Bass River, and both sides of Route 134.
On October 8, at the Town’s Election meeting, Dennis voters overwhelmingly voted in support of the tax over-ride required for Phase 1 to commence.
continued on page 66
Spotlight on Cape Cod continued from page 65
Yarmouth: The town of Yarmouth has been a bit ahead of Dennis in addressing their Section 208 wastewater needs. In April of 2023 the Town approved financing of their own $208 million wastewater management plan. Over the last two years the Town has undertaken several major sewer pipeline projects and recently received bids for two more pipeline projects expected to start in 2025.
In the summer of 2024 Yarmouth received bids on their $90M Wastewater Recovery Facility and the town opened bids in September of 2024 for contracts 5 and 6 of the pipeline distribution system.
Harwich: In October of 2024 the town awarded two more pipeline contracts – Phase 3 - to (UCANE member) Robert B. Our Co., Inc. at a combined cost of $41,835,925. The projects will also include limited water service replacements coordinated by the water/wastewater department and replacement of old catch basins and limited new stormwater systems. The construction duration is expected to take two-and-a-half to three years for Phase 3. Starting by mid-November, traveling about in East Harwich will once again not be an easy task. Residents of the area know what to expect, having experienced similar temporary delays and detours during the Phase 2 pipeline work in that section of town.
The months of September and October 2024 saw multiple sewer projects being bid on Cape Cod as the Section 208 Wastewater Management Plans continue to move forward. As usual, UCANE Contractors continue to show their expertise and their competitiveness when sealed bids are opened at Town Halls throughout the Cape.
The months of September and October 2024 saw multiple sewer projects being bid on Cape Cod as the Section 208 Wastewater Management Plans continue to move forward. As usual, UCANE Contractors continue to show their expertise and their competitiveness when sealed bids are opened at Town Halls throughout the Cape.
Dennis Phase 1 – Contract 1 - WWTP (MWH)Methuen Const, Inc. $83,400,000
Dennis Phase 1 – Contract 2 - Pipelines Robert B. Our Co., Inc. $29,800,000
Dennis Phase 1 Contract 3 - Pipelines Dig It ConstrucJon, LLC $14,200,000
Dennis Phase 1 – Contract 4 - Pipelines RJV ConstrucJon Corp. $20,300,000
Yarmouth Phase 1 – Contract 5 - Pipelines Robert B. Our Co., Inc. $19,000,000
Yarmouth Phase 1 – Contract 6 - Pipelines Dig It ConstrucJon, LLC $19,300,000
continued on page 69
The clean water advocacy group is asking Congress to spend $1.2 billion for repairs to New Bedford’s aging sewer system, which would stem repeated combined sewer overflows that contaminate Buzzards Bay.
$1.2 billion.
That’s how much the Buzzards Bay Coalition says the federal government should spend to clean up New Bedford’s combined sewer system, after rains from summer storms caused its pipes to repeatedly overflow and spill raw sewage into the harbor.
These events, known as combined sewer overflows, c an shut down shellfish beds and swimming at public beaches, given the public health risks that raw sewage-contaminated waters present. They also led the Coalition to cancel the 31st Buzzards Bay Swim.
On the night of June 21, rain flowed into the city’s sewer pipes, causing roughly 7 million gallons of raw sewage and stormwater to spill over into the New Bedford harbor and Clarks Cove. Roughly 2 million gallons were discharged from discharge valves near the event’s starting line, and near the city’s swimming beaches.
Those overflows did not shut down swimming at city beaches, nor did they exceed state public health thresholds. Still, the Coalition determined that they posed enough of a health risk to cancel its popular summer fundraiser. It was scheduled for the morning of June 22. The Buzzards Bay Swim from Cisco Brewers Kitchen & Bar to Fort Phoenix attracts hundreds of open-water swimmers every year.
CSO off of East Rodney French Boulevard that was built in the 1920s, according to the city. During activations, it will release sewage. Credit: Michael Morrissey / The New Bedford Light
“We are reaching out to you to do much more to help the City of New Bedford fi x this problem once and for all,” wrote Buzzards Bay Coalition President Mark Rasmussen in a Monday letter to U.S. Senators Ed Markey and Elizabeth Warren and U.S. Representative Bill Keating.
Addressing the problems of New Bedford’s roughly 250-mile combined sewer system has been
continued on page 70
Spotlight on Cape Cod continued from page 69
a slow, challenging, and expensive process.
The sewer system was built in the 19th century, and was designed to handle sewage and stormwater in the same pipes. It features a series of relief valves that discharge untreated sewage and stormwater into local waters when the pipes exceed capacity during rains.
These overflows protect New Bedford’s wastewater treatment plant from getting overwhelmed during storms. They also keep sewage from backing up into homes and businesses. But the untreated sewage in New Bedford’s overflows c an pollute Buzzards Bay waters with viruses and bacteria.
Being exposed to raw sewage-contaminated water can lead to vomiting, diarrhea, skin rashes, liver disease and respiratory illnesses.
New Bedford has been addressing the problems from its combined sewer system under Environmental Protection Agency oversight. The city invested roughly $430 million to improve its collection and treatment systems for wastewater and stormwater between 1990 and 2017.
It has since been working on several more improvements at an estimated cost of roughly $140 million, as part of a 2017 Long Term CSO Control and Integrated Capital Improvements Plan.
As a result, New Bedford has reduced its combined sewer overflow volumes by more than 9 0%, eliminated 11 c ombined sewer overflow discharge valves, and separated combined sewer lines for hundreds of acres of service area.
Still, the city’s sewer system has 27 combined sewer overflow discharge valves remaining, and there are many more miles of sewer to separate. The Northeast has been getting wetter, which may lead to more frequent and larger combined sewer overflows in New Bedford.
After all of the projects in the current 20-year combined sewer remediation and capital improvement plan are completed, the city will still be seeking roughly $1 billion for upgrades to further modernize the sewer and stop combined sewer overflows from occurring.
Major wastewater projects in Massachusetts are largely funded by low-interest loans, which must be paid off by sewer users. Yet New Bedford residents already face high sewer rates, Rasmussen said. So the region needs the federal government to provide money for addressing the issue, he said.
In 2017, New Bedford officials estimated that fully remediating the city’s combined sewer system will cost at least $1.2 billion.
The local congressional delegation has secured continued on page 71
Spotlight on Cape Cod continued from page 70
more than $1 billion in grant funding for a project replacing the Cape Cod bridges, Rasmussen said. This project, he argued, carries similar regional importance.
“We all benefit from c lean water in southeastern MA, not just swimmers,” Rasmussen wrote.
“Our region’s aquaculture and wild shellfish industry, tourism base, and New Bedford’s continued economic development demand it.”
Written by Adam Goldstein. Reprinted
from newbedfordlight.org n
Concrete Systems, Inc.: Manholes & Catch Basins, Box Culverts, Utility Structures, Special Box Structures, Containment Vaults, Fire Cisterns, CSI Arc-Span™ Bridges, Rigid Bridge ™ Systems, Bridge Deck Slabs, Permanent & Temporary Median Barrier, Uwall™ Retaining Wall Systems, Stablewall™ Retaining Wall, Headwalls & Wingwalls. Clampcrete Construction Systems: TL-4 Anchored Barrier for Roadway Structures. Tunnel Systems: Precision Segmental Tunnel Lining Rings. Cleco Manufacturing: Precision Fabricated Forms & Forming Systems, Complete Plant Design, Batch Plant Computer Automation, Countercurrent Mixers & Concrete Delivery Systems.