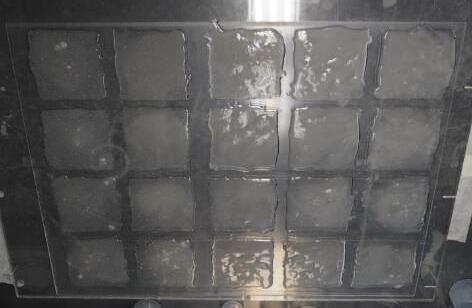
1 minute read
SHPF PRODUCTION 2
Development Of Alternative Simplified Production
Due to the specialized elements needed for the production of SHPF, an alternative and simplified production approach was attempted for creating an SHPF material without, using a regular -25oC freezer instead of liquid nitrogen and silica gel instead of a vacume freezedryer (lyophilizer) The setup was able to surpass the eutectically lowered freezing point, but the produced samples were unviable, as they hadn’t been adequately dried after 1 week. See SCP.
Advertisement
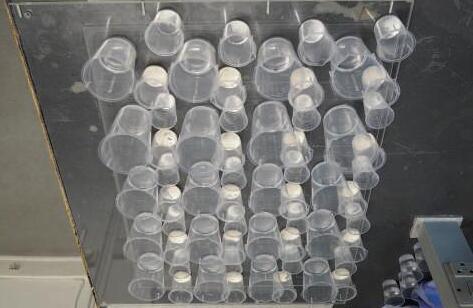
Lithium chloride / water freezing point temperature.
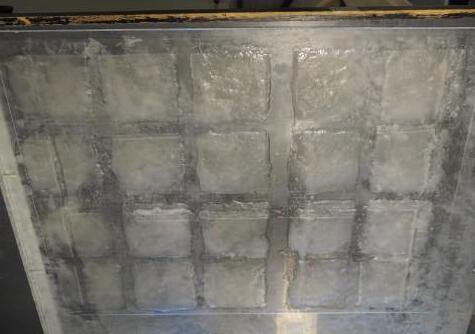
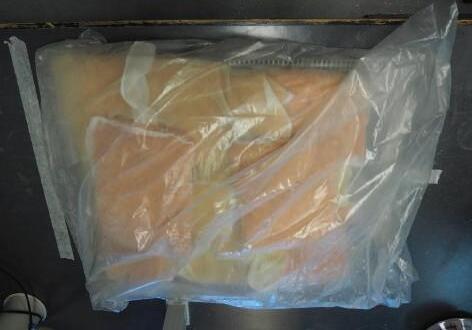
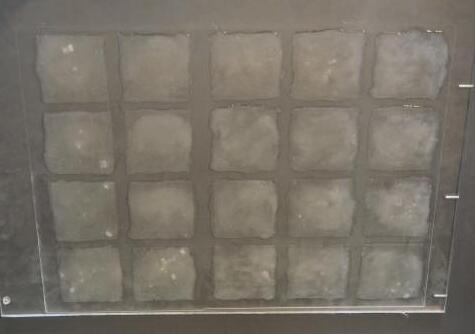
EUTECTIC FREEZING POINT 0.88g LiCl / 10ml water 8.8% = -11OC
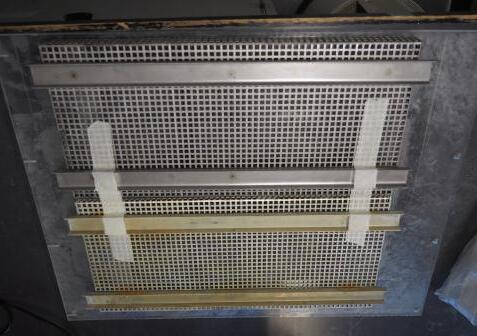
EXPERIMENTAL PRODUCTION: Temperature range: -20-25oC
Additive concentration [weight-%]

1-56-1011-1516-20
Sample Tests 1
The samples proved viable, as they were able to perform absorption/release cycles, but the general quality of the samples inconsistent and low.
Sample 1-8 made up the lowest 2 layers in the stack of samples inside the freezing chamber. The heavy damage to these samples from being submerged in liquid nitrogen during the freeze led me to redesign the cooling setup.
Mixing Ratios
Water: (H2O) 10 ml
Hydroxypropyl Cellulose (HPC) 0.1g (1 wt%)
Konjac Gluccomannan (KGM) 0.44g
Lithium Chloride (LiCl) 0.88g
40-4546-5051-5556-60
Sample Tests 3
After upgrading the liquid nitrogen cooling box the quality and consistency of the samples were much improved. Still a lot of heterogeneity from the manual mixing and pouring of the hydrogel precursor.
Additionally the HPC cellulose content of the samples were increased from 1g/10ml to 1.5g/10ml to give the samples additional tensile strength, based on experience gained from handling the first batch. Based on the data from Guo. et al. (2022) this should have lowered the maximum overall effectiveness of the SHPF slightly, compared to the SHPF described in their paper.
This was not the case for my samples as the absorption/ release amount was improved for batch 3, compared to batch 2, for my testing. I would attribute this to the added strength improving the general consistency of the samples produced form my setup, compared to batch 1. Batch 3 also shows slightly better release values, likely related to a higher presence of cellulose contracting from heat during the release cycle.
Mixing Ratios
Konjac
MEASUREMENT CHAMBER
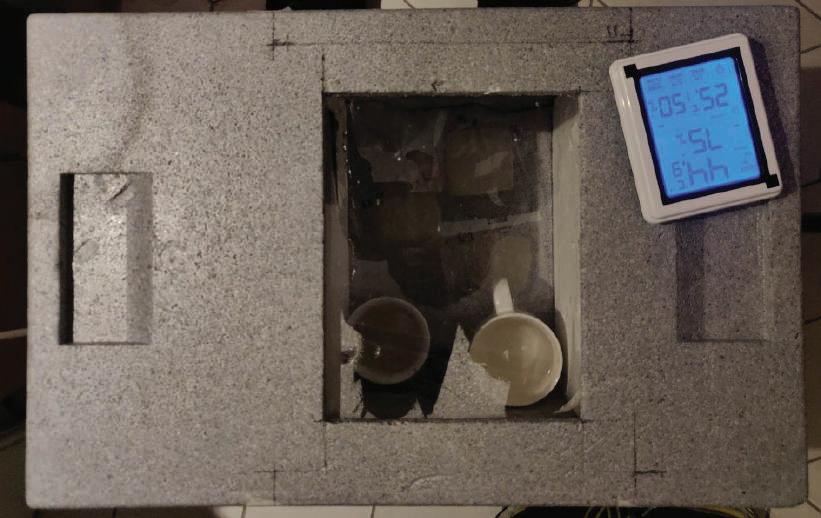