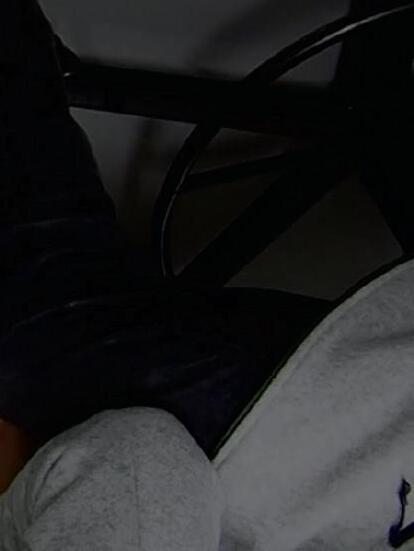
1 minute read
SPHF PRODUCTION
Process Learnings
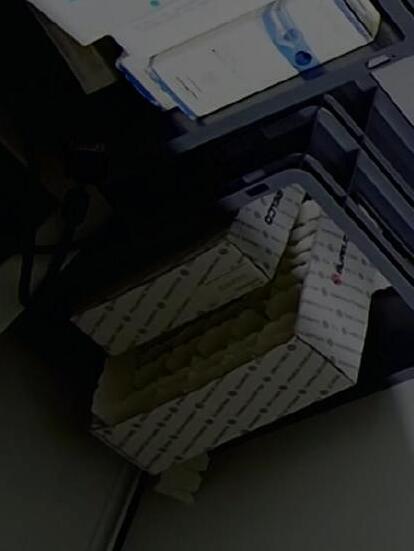
Advertisement
Liquid nitrogen box used for batch 1. Stacking samples inside proved to be a terrible idea as the buttom molds got submerged and cracked after the liquid nitrogen pour or during re-heating from ambient air when pulled out of the box.
5x4 Molds
BATCH 1 FREEZING CHAMBER
~500ml Liquid Nitrogen. Lowest 4 samples and acrylic molds heavily damaged from direct exposure. Redesign freezing chamber.
SHPF MOLDS AFTER BATCH 1NITROGEN LEAKS -- FIXED WITH MYLAR INSULATION
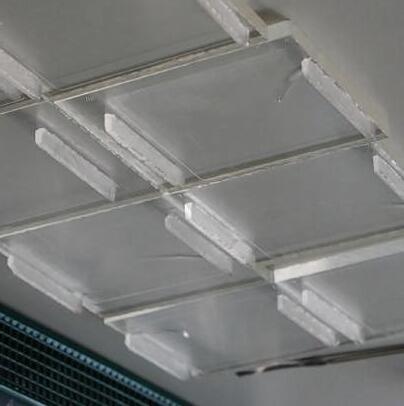
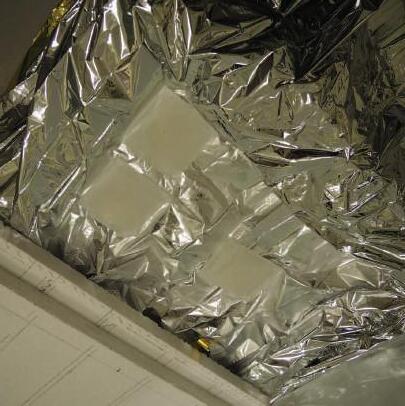
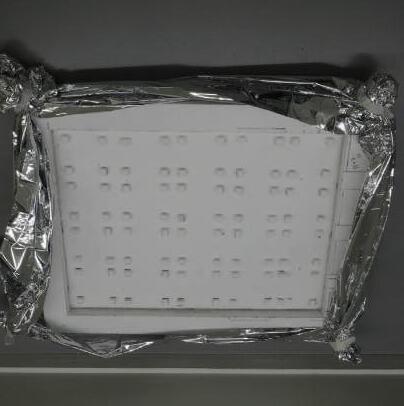
CNC cut accyrlic molds for pouring SHPF samples. Photographed inbetween batch 2 and 3. Cracks are from material contraction and expansion due to heavy cooling. Spacers glued on with acrylic glue, to stack movlds in freezedrier.
BATCH 2 FREEZING CHAMBER
Liquid nitrogen box 2, used for batch 2 and 3. Reinforce and insulate box futher for scaling production, to slow the loss of liquid nitrogen from evaporation. Studs of styrofoam glued in place with silicone caulk to offsett acrylic molds.
When exposed to cryogenic temperatures from liquid nitrogen, the silicone caulk seal binding the styrofoam edge to the base plate contracted tore, creating gaps that leaked liquid nitrogen onto the floor.
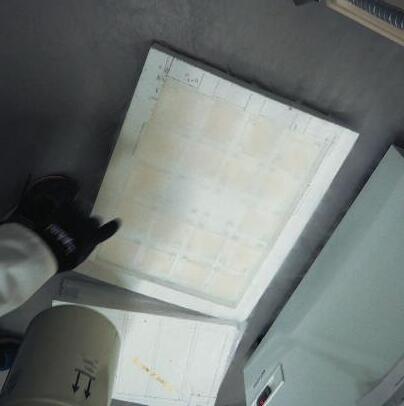
Turns out an improvised insulation lining of mylar is an excellent way of containing liquid nitrogen in the freezing chamber.
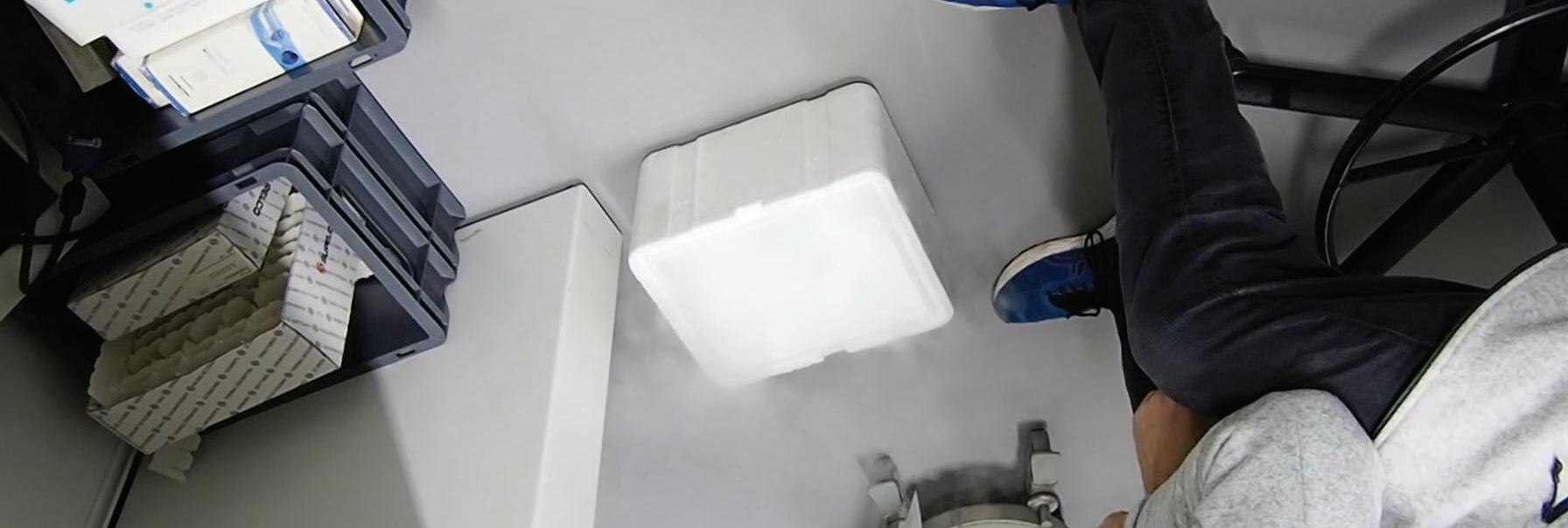
The chemical department at Roskilde University granted access to their old
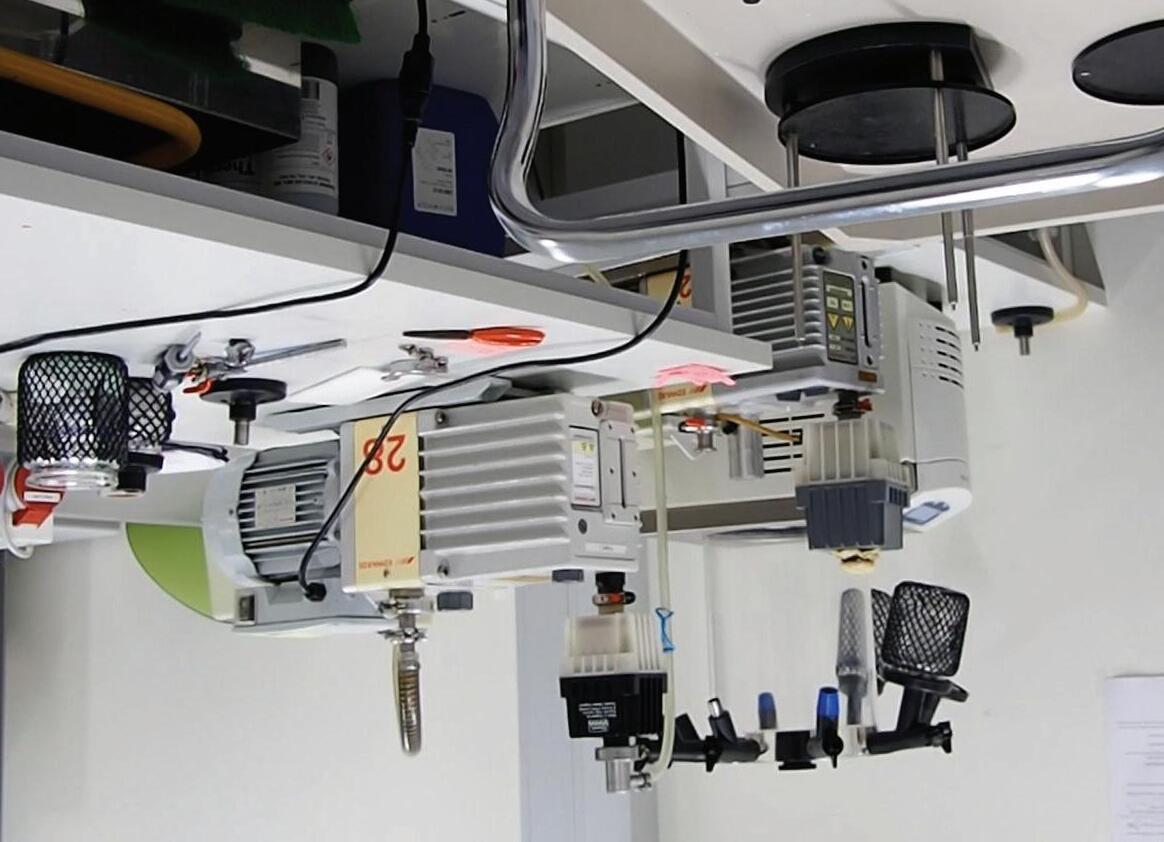
Freeze Drying
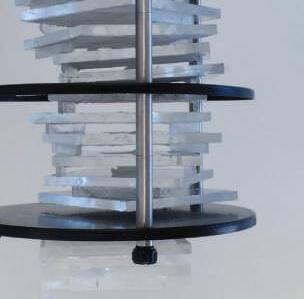
SAMPLE HOLDER
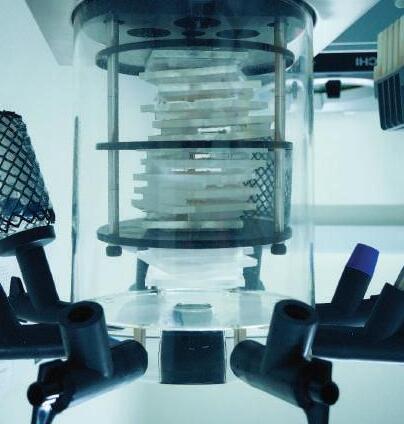