CONTROLLING PLASTICS AT SOURCE
REPORT PREPARED FOR THE PLASTIC POLLUTION WORKING GROUP (PPWG) OF THE UK & IRELAND SPILL ASSOCIATION ‘GOAL 10’
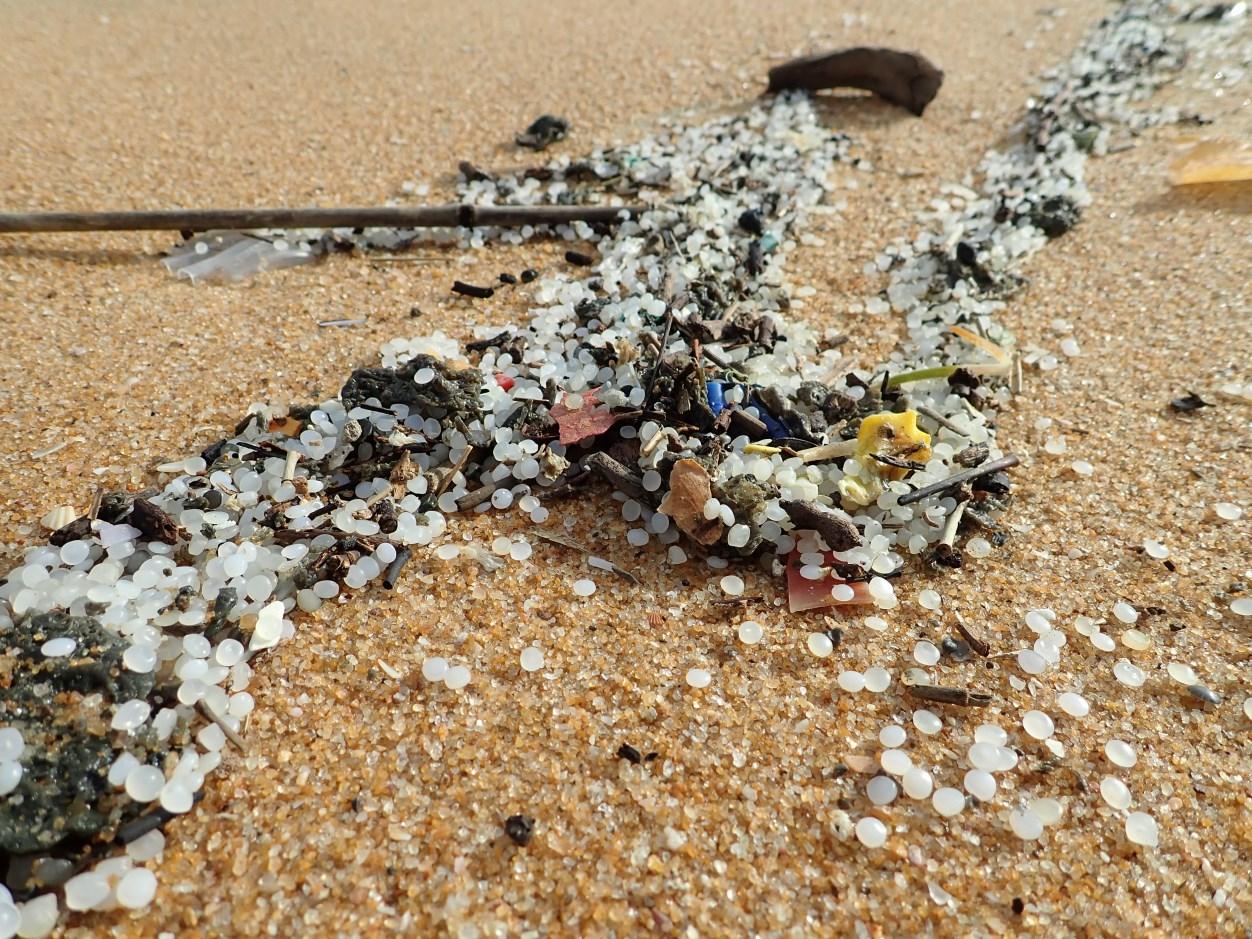
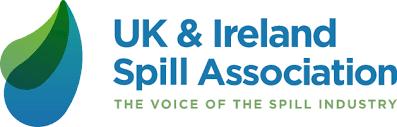
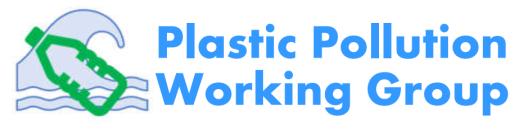
REPORT PREPARED BY ORACLE ENVIRONMENTAL EXPERTS LTD
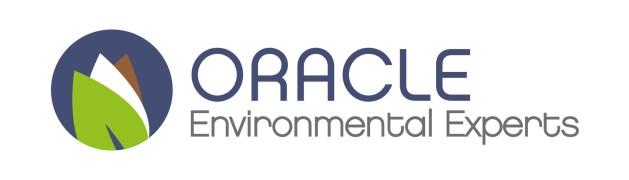
PPWG - Goal 10 Report
No part of this publication may be reproduced, stored in a retrieval system, or transmitted in any form or by any means, electronic, mechanical, photocopying, recording or otherwise, without the prior consent of the PPWG of the UK & Ireland Spill Association
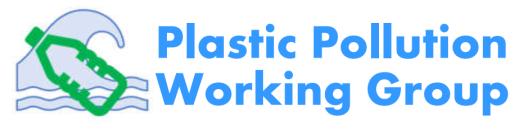
Cover photograph reproduced courtesy of Cedre.
This publication has been developed to support the goals of the PPWG of the UK & Ireland Spill Association. While every effort has been made to ensure the accuracy of the information, it is intended to provide general guidance only. It is not designed to provide legal or other advice, nor should it be relied upon as a substitute for appropriate technical expertise or professional advice. All attempts have been made to ensure that the information is correct at the date of publication. The views and conclusions expressed herein do not necessarily reflect the views of all PPWG and UK & Ireland Spill Association members or the companies and institutions that contributed to this publication.
While reasonable precautions have been taken to ensure that the information contained in this publication is accurate and timely, this publication is distributed without warranty of any kind, express or implied. Neither the PPWG or the UK & Ireland Spill Association endorses or accepts responsibility for the content or availability of any website referred to, or linked to, in this publication. The responsibility for the interpretation and use of this publication lies with the user and in no event will the PPWG of the UK & Ireland Spill Association or any of their members past, present or future, regardless of their negligence, assume liability for any foreseeable or unforeseeable use made thereof, which liability is hereby excluded. Consequently, such use is at the recipient’s own risk on the basis that any use by the recipient constitutes agreement to the terms of this disclaimer. This disclaimer should be construed in accordance with English law.
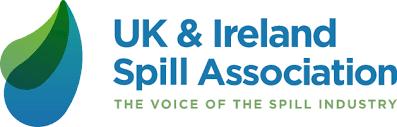
DOCUMENT CONTROL RECORD
Project: Microplastics R&D
Project Reference: OEE R&D 2101
Report Title: Controlling Plastics at Source
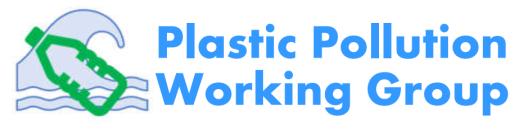
Authors: Kif Cullerne BSc (Hons)
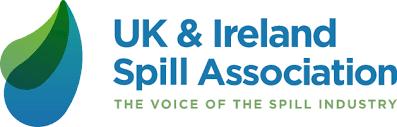
Environmental Consultant – Oracle Environmental Experts Ltd
Joshua Doran MSci MCIWEM FRGS
Environmental Consultant – Oracle Environmental Experts Ltd
Checked and Approved By: Dr Jon Burton BSc PhD FGS MCIWEM CSci MAE
Managing Director – Oracle Environmental Experts Ltd
Version No: 1
Issue Status: Issued
Date Issued: 25 August 2022
Microplastic R&D Page 3 of 30
Controlling Plastics at the Source
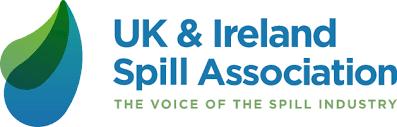
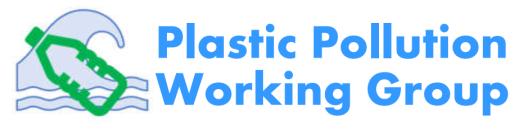
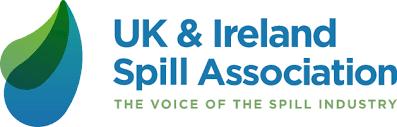
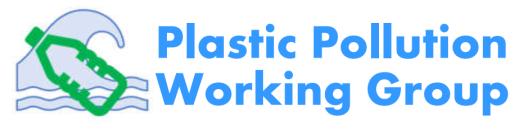
1.0 INTRODUCTION
1.1 Controlling Plastics at the Source
1.1.1 In 2020, 367 million tonnes (Mt) of plastic were produced worldwide (Tiseo, 2021) and is expected to double in the next 20 years (Lebreton and Andrady, 2019). The majority of this plastic ends up in landfills, open waste sites and littered throughout our environment and an increasing proportion ends up in rivers, lakes and oceans. Currently, it is estimated that 19-23 Mt of plastic enter aquatic ecosystems annually from land-based sources (UNEP, 2021). Preventing plastics from being released to the marine environment by limiting the release of plastics from the source (e.g. on site, in drains and in rivers) by using effective tools, equipment and technology is key to reducing the plastic output to our oceans and the wider environment.
1.2 The Plastic Pollution Working Group
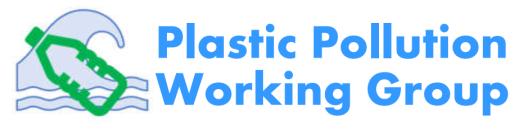
1.2.1 To better understand the issues involving plastic pollution, the UK & Ireland Spill Association and several of its members, formed the Plastic Pollution Working Group (PPWG), in March 2021. The group has set itself 10 ambitious goals to improve our understanding of the impacts of plastic pollution and the way we deal with plastic pollution incidents
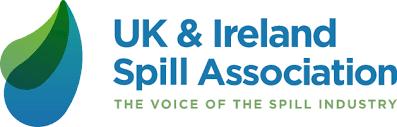
1.2.2 The 10 goals of the PPWG are as follows:
1. Understand the problem – Understand the sources, pathways and impacts of plastic pollution from rivers to the oceans
2. Identification of the most effective equipment for the recovery of macro and microplastics from shorelines and nearshore environments
3. Establish agreed methods for the assessment of ecological impact of plastics recovery operations
4. Establish agreed methods for qualitative (e.g. SCAT) and quantitative (e.g. laboratory analysis) assessment of macro and microplastics in sediments and waters and effective sampling and monitoring techniques
5. Assessment of environmental and health risks associated with macro and micro plastics to assist in clean up end point determination
6. Develop effective approaches for the surveillance and modelling of macro and microplastics to aid in response efforts, prediction of plastic movement and source identification
7. Develop approach to sustainability assessment with respect to plastics recovery endpoints and final destination of recovered plastics / debris
8. Share information gained through the group through webinars, demonstration days, technical publications and liaison with other appropriate organisations (e.g. EA, IMO, Councils, NGOs)
9. Work with International Spill Accreditation Scheme (ISAS) to ensure the Module for Shoreline Plastic Pollution and Marine Debris Recovery is formally released.
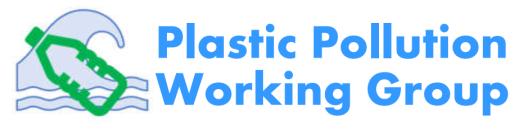
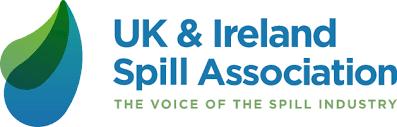
10. Identification of effective tools and equipment for controlling plastics at source (e.g. on site, in drains and in rivers)
1.3 Report Aim
1.3.1 As part of achieving Goal 10 outlined above, this report is intended to identify current tools and equipment for controlling plastics at source (on site, in drains and in rivers), with a particular focus on mitigating pre-production plastic pellet (nurdles) loss at source.
1.3.2 The report highlights products and initiatives that have been developed to address plastic pollution in our environment but by no means presents an exhaustive list of available products and services and will look to be revised as new research and product are released. The report in no way endorses any companies or products but is intended to highlight some of the available solutions aimed at reducing plastic pollution in the environment.
2.0 CONTROLLING PLASTICS IN RIVERS & WATERWAYS
2.1 Plastics in Rivers
2.1.1 Rivers have consistently been identified as one of the most important transport pathways for all sizes of plastic debris (Stothra Bhashyam et al., 2020; Boucher & Friot 2017). Rivers are highly dynamic environments connecting land to sea and along their course, plastic waste will enter rivers through road runoff, agricultural runoff, wastewater inputs including wastewater treatment plants (WWTPs) and through littering (Horton et al , 2018., Stothra Bhashyam et al., 2020). Globally, it is estimated that between 1.15 and 2.41 Mt of plastic waste currently enters the ocean every year from rivers (Lebreton et al., 2017).
2.2 Controlling Plastics in Rivers: Boats & Barges
2.2.1 Introduction
2.2.1.1 In order to stem the flow of plastics from rivers into oceans, various floating plastic processing boats and barges have been developed to collect and recycle plastic waste in river systems These use the process of collecting surface plastic via a combination of conveyor belts, baskets and sieves where, once collected, plastics can then be sent to be recycled onshore.
2.2.2 The Interceptor
2.2.2.1 The Interceptor is an autonomous system for collecting plastic pollution from rivers before it reaches the sea. Developed by a non-profit organization The Ocean Cleanup, Interceptors consist of floating barriers attached to processing plants that resemble barges and are anchored to the riverbed. The barriers funnel plastic waste into the mouth of the plant which is powered by solar panels and can operate without the need for human operators. A conveyor belt separates the waste from the water and moves it up to a shuttle which automatically dumps the waste into containers on a separate barge docked below. When the containers are full, the onboard computer system alerts local partners to bring a boat and tow the barge of plastic waste away for recycling. Each system only spans part of the river so boats and wildlife can manoeuvre around it
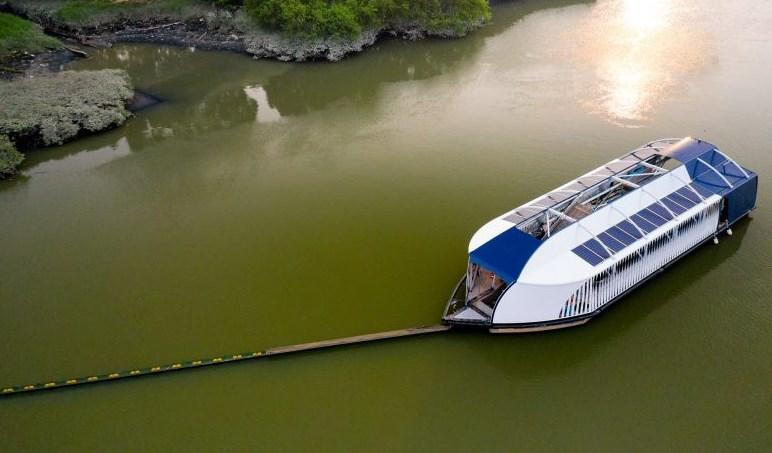
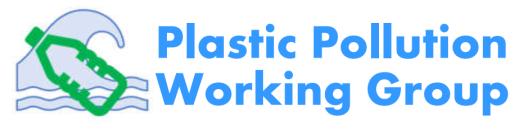
2.2.3 The Interceptor Tender
2.2.3.1 Another system developed by The Ocean Cleanup, the Interceptor Tender is designed to work alongside a floating barrier This small, powered barge uses a conveyer to scoop the litter from the barrier and offload it to containers onshore. The Interceptor Tender is capable of servicing multiple barrier deployments in close proximity.
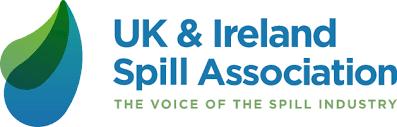
2.2.4.1
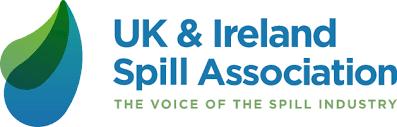
Trash Wheel uses containment booms to collect litter flowing along a river where it is collected using a rake onto a conveyor belt. Mr. Trash Wheel is powered by a combination of solar power and a 14-foot water wheel using the water current in the river. After moving along the conveyor belt, the plastic is dropped onto a separate floating barge where it is taken away to be recycled.

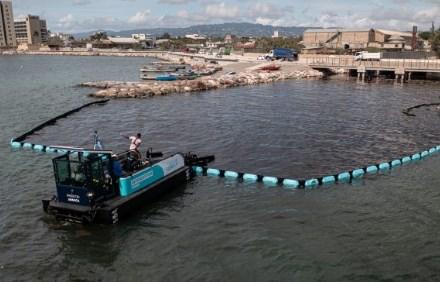
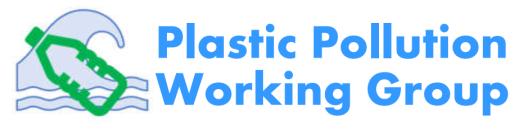
2.2.5.1 Rather than remaining stationary in the water and using containment booms to funnel plastic and debris towards a conveyor belt, the 4ocean Mobile Skimmer uses an onboard motor and retractable arms to skim litter from the surface of the water onto a conveyor belt before collection in large sacks, which are then emptied and replaced once full. The plastic collected is sent for recycling.
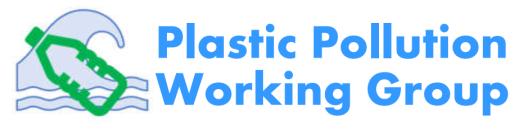
2.2.6.1 The Versi-Cat uses a basket to collect marine litter including plastics and incorporates a series of ‘pods’ that sit between the twin hulls, enabling heavy items to be loaded and unloaded directly onto the quayside without the need for manual handling.
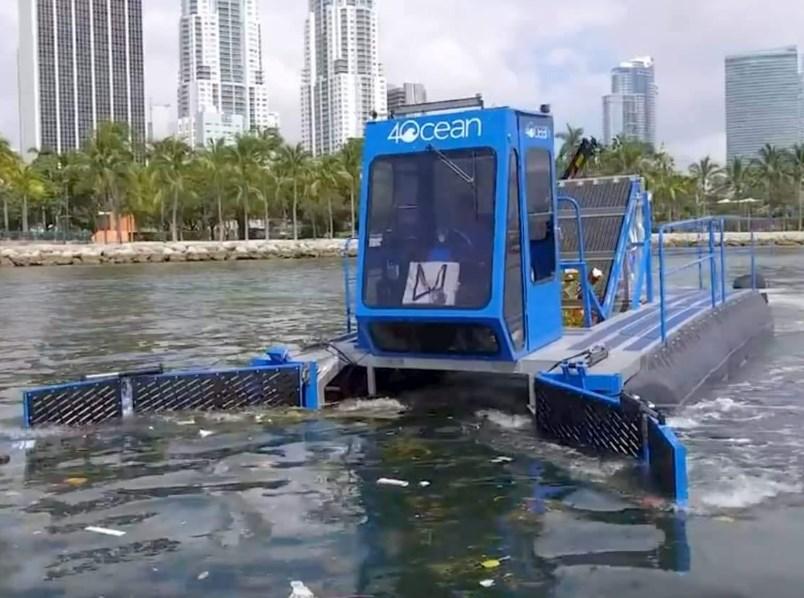
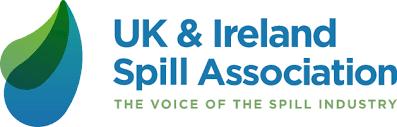
2.3.1 Introduction
2.3.1 Efforts have been made to automate the process of plastic recovery from rivers Autonomous robots and drones are able to operate independently and in some cases clean faster and more efficiently than human operated systems.
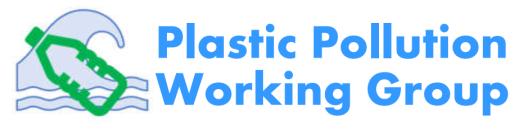
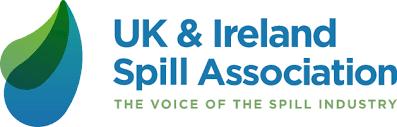
2.3.2 WasteShark
2.3.2.1 WasteShark is an autonomous water drone created by RanMarine technology developed to collect floating waste such as plastic debris before the winds, tides and currents carry it out into the ocean. The WasteShark has been designed to be user-friendly, easily deployable, low cost and suitable for use in smaller hard to reach places.
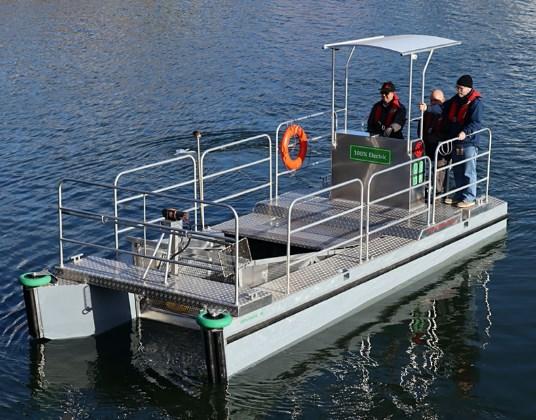
2.3.2.1 Originally designed for use in oceans, FRED is a solar-powered, semi-autonomous marine robotic catamaran capable of collecting macroplastic pollution, which is then transported and recycled onshore. FRED can be customized and scaled for use in lakes, rivers and open oceans.
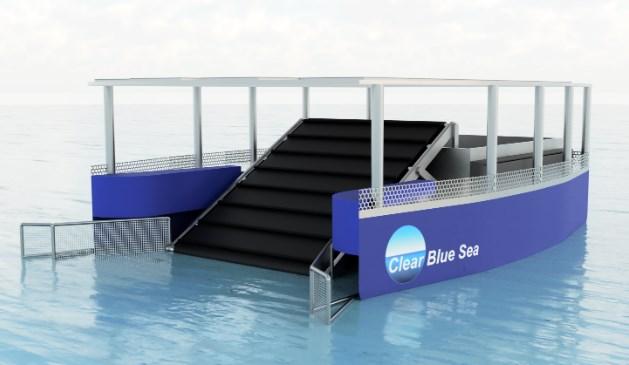
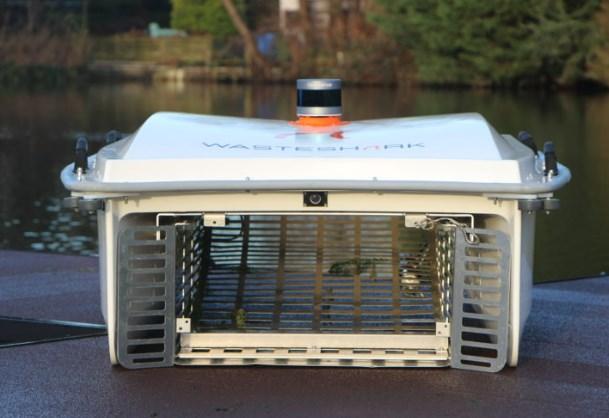
2.3.3.1 The Jellyfishbot is an autonomous, multi-purpose ‘bot’ used for the collection of waste and hydrocarbons including macro and microplastics. The remote-controlled bot is equipped with interchangeable nets (down to 0.15 mm within the water column) which are dragged behind the vehicle to collect contaminants.
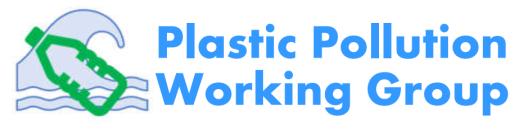
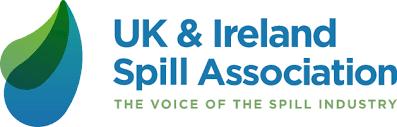
2.4 Controlling Plastics in Rivers: Barriers
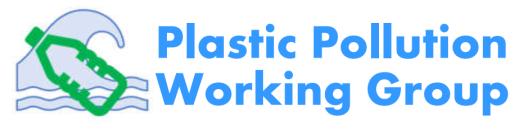
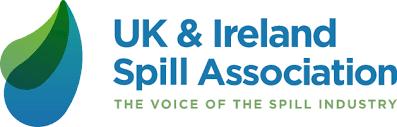
2.4.1 Introduction
2.4.1.1 Barriers work by simply catching and collecting plastics and other debris as it floats down a river system towards the sea using the natural flow and accumulation. Barriers can either be installed across the span of the river or just part of it to allow safe passage of river transport and wildlife. The plastic and debris can then be collected for recycling.
2.4.2 Interceptor Barrier
2.4.2.1 The interceptor barrier, designed by the The Ocean Cleanup, is a variation of the barrier used in conjunction with the Interceptor processing unit (Section 2.2.2), the main difference being that most of the barrier is permeable so it can be optimised for buffering waste in the water. It consists of a floating barrier anchored in a U-shape around the mouth of a small river. This intercepts the plastics and buffers it until it is removed from the water.

2.4.3
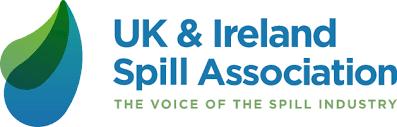
2.4.3.1 CLAIM’s floating boom has been installed in the mouth of the Kifissos River in Athens, Greece. The solar powered system allows material collected by the booms to be fed towards a collection/storage point that can be emptied and changed when filled.
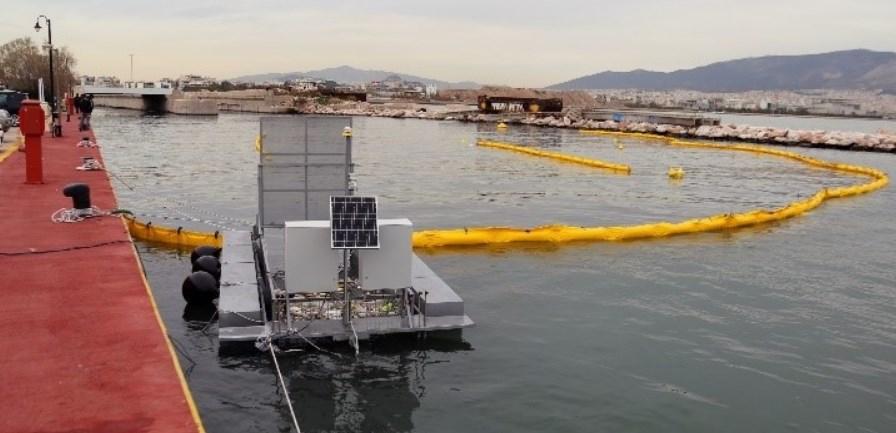

2.4.4 The Great Bubble Barrier
2.4.4.1 The Great Bubble Barrier, developed by a Dutch startup company, uses bubbles to trap and remove plastics from waterways such as rivers. A bubble curtain is created by pumping air through perforated tubes installed on the riverbed. The bubble curtain creates an upward current that directs plastics to the surface. By placing the Bubble Barrier diagonally across the river, the natural flow of water will push the plastic waste to the side for collection by a catchment system. Following collection, the plastics are removed for recycling. The benefits of a bubble system over a conventional barrier are that it does not disrupt transport or wildlife
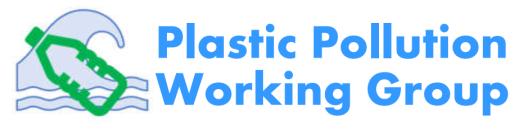
movement on the river and can be used 24 hours a day. In addition, bubble curtains are thought to increase the dissolved oxygen in the water, benefitting the aquatic ecosystem.
2.4.5 River Cleaning System
2.4.5.1 The River Cleaning System is made up a series of rotating floating discs, which are positioned diagonally over course of the river. The plastic waste moving downstream is then intercepted and transported to the riverbank to be stored and subsequently removed for recycling. The system is designed so that wildlife including fish and river transport can navigate the waterway unhindered.
2.4.6 Trashfence
2.4.6.1 Designed by the team at ‘The Ocean Cleanup’, the Trashfence is designed for flash flood environments in highly polluted areas. Inspired by avalanche protection systems, the


Controlling Plastics at the Source
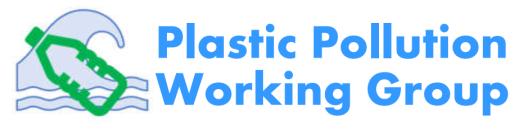
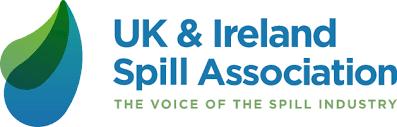
structure is anchored to the banks and bed of a river and captures plastic and other waste along its length for later extraction. This project is currently in a trial phase and is being piloted in Guatemala on one of the world’s most polluting rivers.
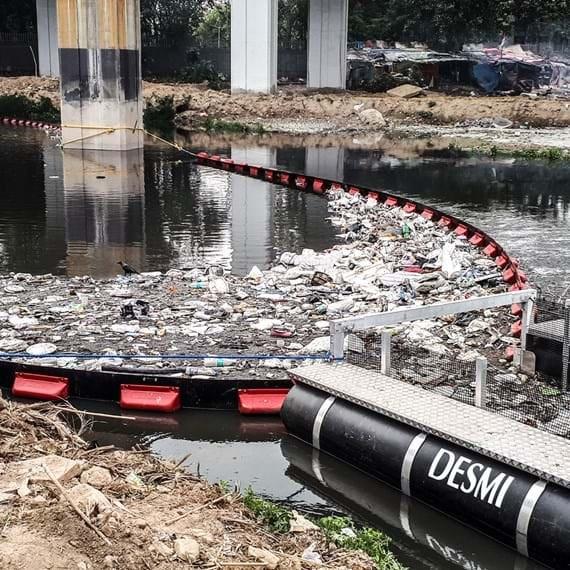

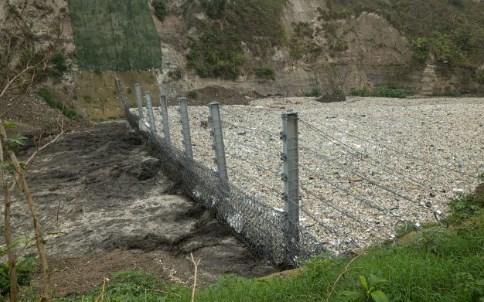
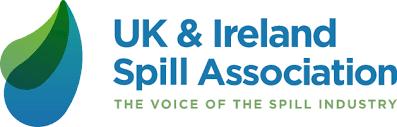
2.4.7 Desmi Automated Trash Remover System
2.4.7.1 Desmi have also designed and installed floating litter containment and collection systems for the removal of floating litter from waterways (Figure 13). Desmi state that these automated systems are designed to guide the marine debris for easy recovery with perforated belt designs. Floating surface debris is removed, while allowing the water to pass and allowing marine life to stay unharmed.
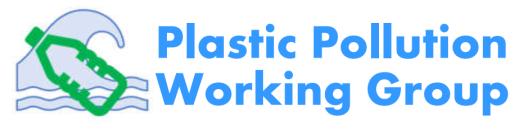
2.4.8 Desmi Treat Unit
2.4.8.1 Desmi have also developed smaller floating litter collection systems for watercourses which contain less litter. The Desmi ‘Treat’ system is marketed as a light-weight low cost, recovery unit, for use in areas with lower capacity demand and with difficult access. The unit is portable and can be deployed from a small boat.
2.4.8.2 The unit requires a couple of guide booms, which guide the litter to a litter bag downstream of the guide booms, and the bag can be removed and replaced as necessary.
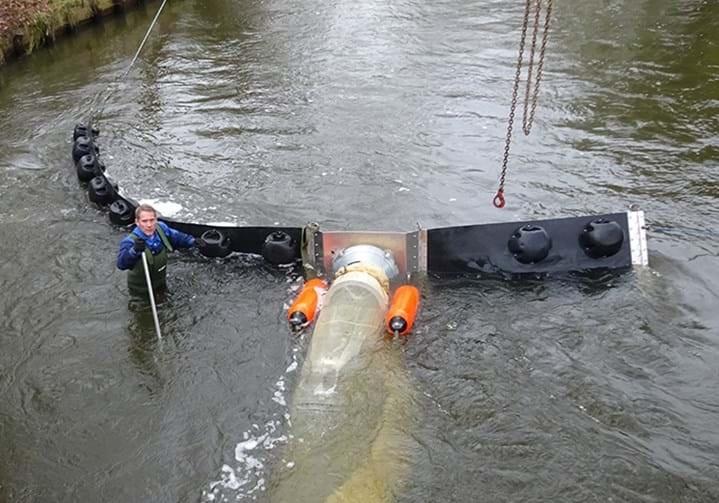
2.5 Controlling Plastics in Rivers: Other Solutions
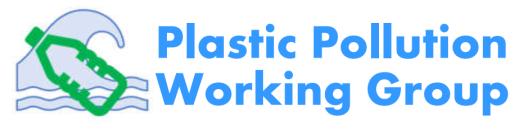
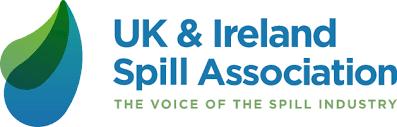
2.5.1 Seabins
2.5.1.1 The Seabin created by ‘The Seabin Project’ is a ‘trash skimmer’ designed to be installed in calm waters such as those found in Marinas, Yacht Clubs and ports. The unit behaves like a floating litter bin by skimming the surface of the water by pumping water into the device. Water is sucked in from the surface and passes through a catch-bag inside the Seabin with a submersible water pump plugged into either a 110V or 220V outlet. The water is then pumped back into the marina leaving litter, including plastics, trapped in the catch-bag. The Seabin can catch an estimated 3.9 kg of floating debris per day including microplastics to 2 mm in diameter
2.5.2.1 Drum screw clean up technologies have been developed and used for decades. Initially designed for jellyfish removal, FishFlow in partnership with the InNoPlastic project have developed and built a full-scale pilot of an Archimedean drum screw screen tailored for use in the screening and removal of macro and possibly microplastic removal whilst allowing 90% of the water flow to pass through.


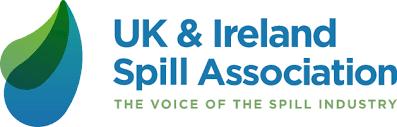
2.5.3
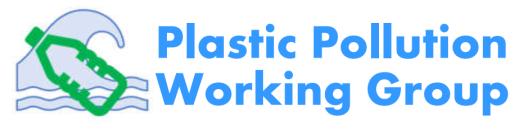
2.5.3.1 Many plastic removal technologies require microplastics to be above a threshold size for removal via sieves. A project by InNoPlastic aims to investigate flocculation on micro and nano plastics in order to form larger aggregates which can then be more easily removed via sieving. In addition, a new innovation in clean-up technologies is the agglomeration of nano- and microparticles in water with the help of ultrasound-clustering. Piezoelectric actuators generate overlapping ultrasonic waves. Microplastics and other particles are pushed along these lines to the nodes of the waves. They agglomerate to consolidated clusters, which in the next step can be treated to the flocculation. A project by InNoPlastic aims to develop an effective way of implementing ultra-sound clustering on an industrial scale.
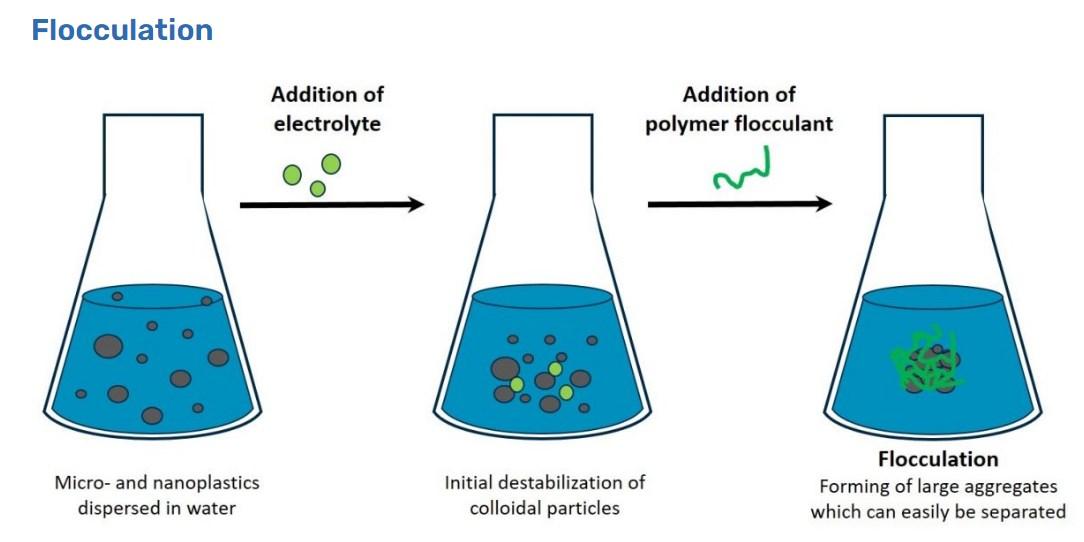
(www.innoplastic.eu )
3.0 CONTROLLING PLASTICS: STORMWATER AND DRAINAGE SOLUTIONS
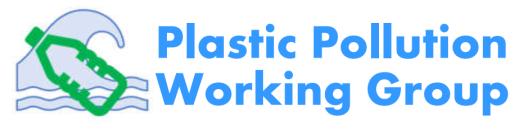
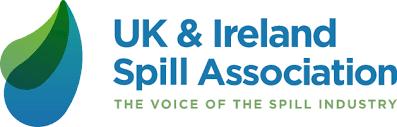
3.1 Controlling Plastics: Stormwater Litter Traps and Filters
3.1.1 Most marine based plastics originate from land-based sources through processes such as surface run-off, wind, littering and other sources This plastic waste often finds its way to marine ecosystems via stormwater drains; stormwater drains allow runoff, which carries plastic litter and other debris, to deposit plastic-filled water into large bodies of water and rivers that carry them into the ocean Stormwater and road runoff have been identified to be significant pathways for plastic pollution (Werbowski et al., 2021; Seigfried et al., 2017). Preventing plastics from entering the stormwater system in the first instance can be achieved by installing litter traps into stormwater drains of plastic polluting hotspots such as pre-
Controlling Plastics at the Source
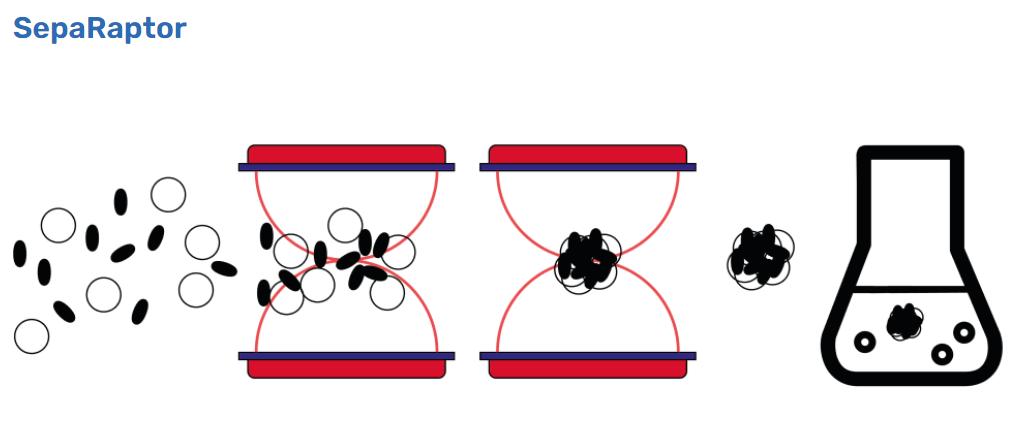
production plastic pellet (nurdles) and plastic production facilities as well as areas with high plastic litter rates such as city centres.
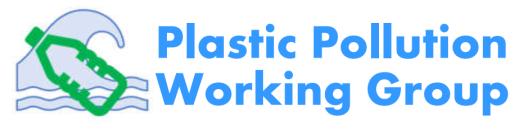
3.2 The Enviropod LittaTrap
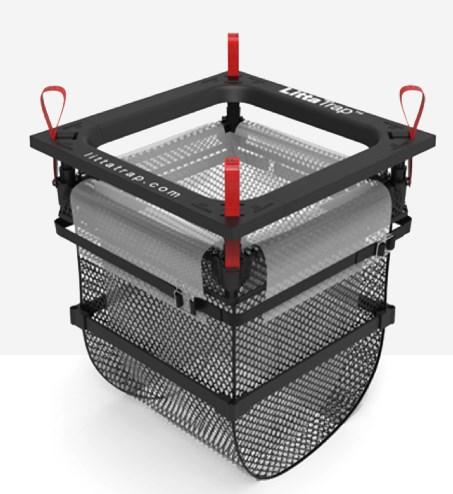
3.2.1 The Enviropod LittaTrap is a catch basin basket that sits inside a stormwater drain and prevents litter and other debris larger than 5 mm carried by stormwater from entering the storm drain system. The LittaTrap can be combined with Liners (meshes) that can target sitespecific pollutants from pre production plastic pellets down to 1 mm in size to use as a pretreatment device targeting pollutants down to 0.2 mm below the water column. Once the filter bag is full, the contents can be manually removed or removed by a vacuum inductor truck. If the filter bag becomes full during high flows, overflow is released through apertures built into the frame.
3.3 End of Pipe Screening Systems
3.3.1 At the other end of the storm water drainage system, end of pipe screening systems can be installed as a last defense, designed to catch larger debris including plastic before it moves into larger water bodies. These systems are usually positioned at the final discharge point to a receiving water body.
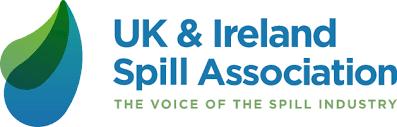
3.4.1 Simple but effective approaches such as painted curbstones next to road drainage gullies provides awareness to pedestrians in an effort to make them conscious of the pathways of pollutants into the oceans. This, combined with other schemes employed by local councils such as ‘No More Rubbish Excuses’ and ‘Don’t Be A Tosser’ posters grab passersby attention in an effort to persuade them to correctly dispose of their waste instead of littering.
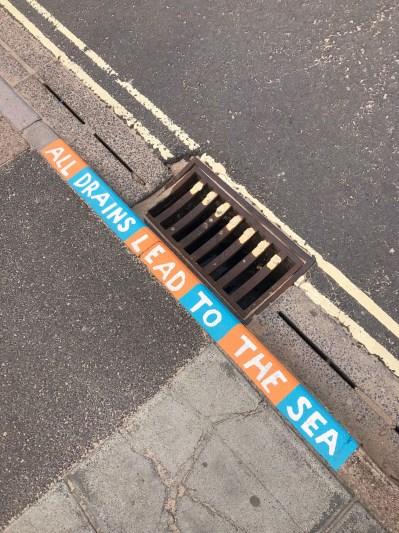

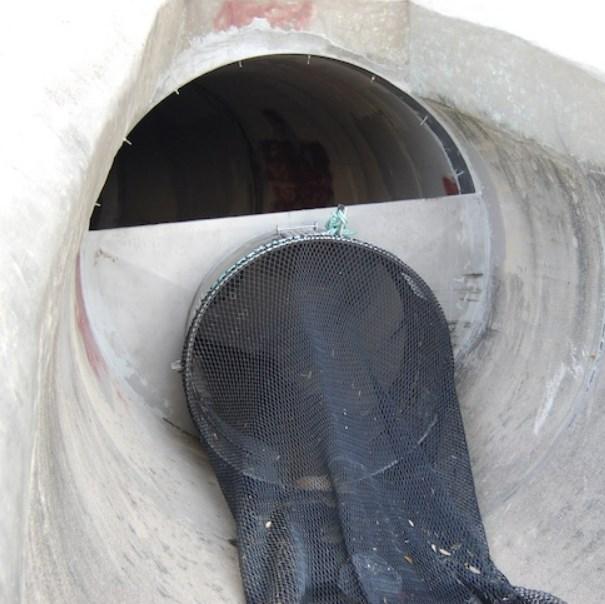
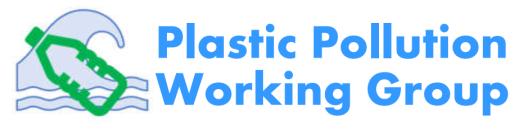
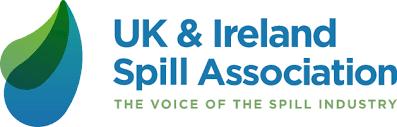
4.0
4.1 Controlling
4.1.1 Wastewater is generally treated at WWTPs which are thought to be effective at removing plastics including microplastics However, removed microplastics are incorporated into sewage sludge which is often used as fertiliser for agriculture, suggesting that agricultural soils are potentially large sinks for microplastics where they can then be re-introduced into marine environments via surface run off (e.g. Harley-Nyang et al , 2022; Koutnick et al., 2021; Hurley et al., 2018). Microplastic fibres have been reported in agricultural fields up to 15 years after sludge was applied, still maintaining their original properties (Zubris & Richards, 2005).
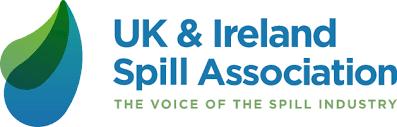
4.1.2 Microplastics can enter WWTPs from a wide range of sources including road run-off and grey water which can include fibres from the washing of clothes (Browne et al , 2011). An important source of microplastic appears to be through sewage contaminated by fibres from washing clothes. In terms of microplastic generation through synthetic textiles, abrasion during laundry, as well as exposure to chemicals and detergents, causes the breakdown of synthetic fibres into smaller microfibres (Browne et al., 2011). They found that up to more than 1900 fibres per garment, per wash, (100‐300 fibres per litre effluent) could be released.
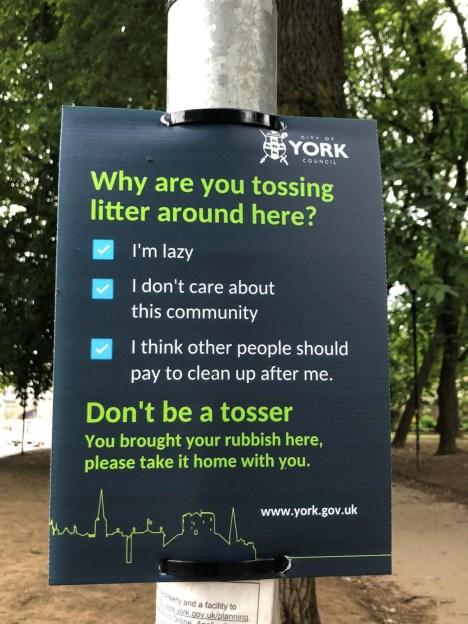
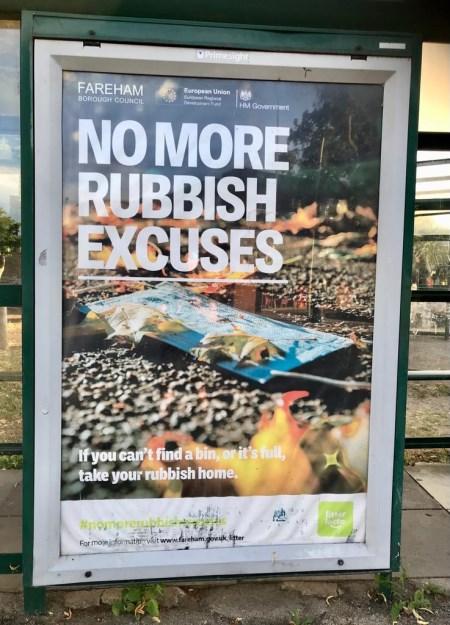
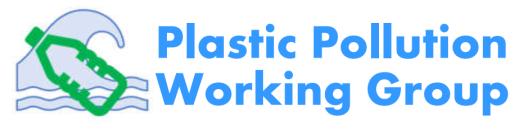
4.2 Controlling Plastics: Washing Machines
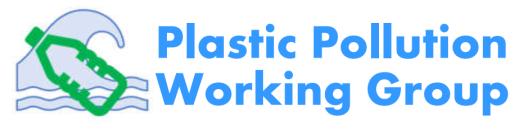
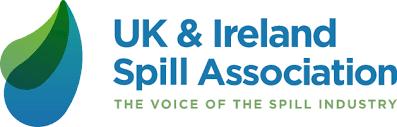
4.2.1
Washing Machine Filters
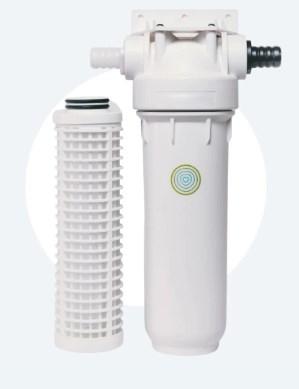
4.2.1.1 When synthetic clothing is washed, tens of thousand of microfibres are released with the wastewater in each load. Some washing machines are now being produced with built-in microplastic filters (e.g. Grundig FiberCatcher). Microfibre filter kits are also available to install onto a standard washing machine (Lint LUV-r, PlanetCare) and claim to prevent 90% of microfibres being released with each laundry load. These kits require cartridges to be changes on a regular basis (every 20 washes). The cartridges are then sent to be recycled.
4.2.2 Washing Machine Laundry Balls
4.2.2.1 Another solution to prevent the release of microplastics in washing cycles is the laundry ball. The Cora ball, for example, is placed inside the washing machine during a laundry cycle and is designed to pick up microfibres by catching them in the stalks or the product. Research by Napper (2020) at the University of Plymouth demonstrated that the Cora Ball prevents 31% of microfibres from flowing down the drain in addition to reducing the overall amount of shedding taking place in a typical wash cycle.
5.0.1 Pellet (nurdle) pollution is the second largest source of direct microplastic pollution to the ocean and is known to cause serious harm to marine biodiversity. An estimated 230,000 tonnes of pellets are lost to the environment every year (Eunomia, 2016). Pellet loss can occur at every stage of the supply chain: pellet production (including recycled pellets), transport, storage, and conversion into plastic products. Technology has rarely addressed the loss of industrial pre-production pellets during shipping, loss during use and improper waste management (Jambeck et al., 2015).
5.0.2 Pellet loss can be prevented by implementing robust procedures, providing spill kits and training staff on how to use them, and putting filters in drains.
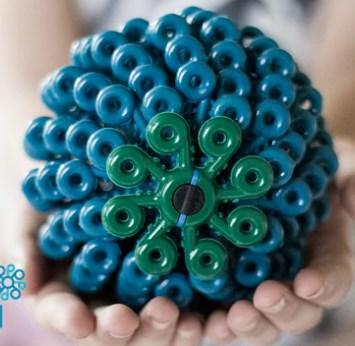
5.1 Pellet Loss Procedures
5.1.1 Currently, plastic production companies can opt to sign up to the Operation Clean Sweep Scheme (OCS), committing to zero pellet loss from their facilities. OCS provides a comprehensive set of guidelines to help companies make sure no pellets are lost from their site There are a number of resources available from the Operation Clean Sweep Website including checklists for site audits, equipment and training, examples of which can be found in Appendix A.
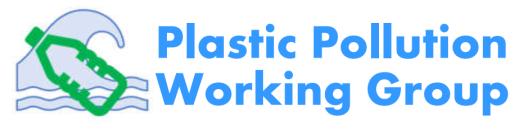
5.1.2 However, signing up to OCS is voluntary and there are no checks on companies to make sure they are following through with their promise after signing up. Nearly 30 years after OCS was created, pellets are still being lost in their billions.
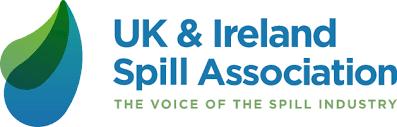
5.2
5.2.1 Companies involved in the production, transfer and use of plastic pellets are encouraged through the OCS scheme to provide spill kits that are easily accessible to employees in the case of a spill, particularly in sites at high risk of a spillage. An example is provided below in Figure 25
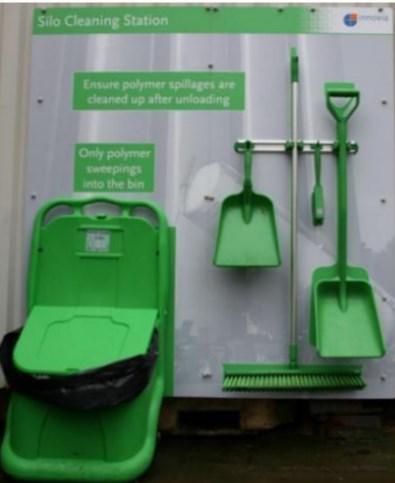
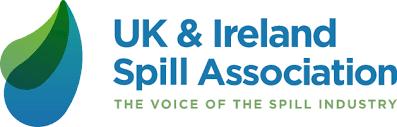
5.3 Vacuums

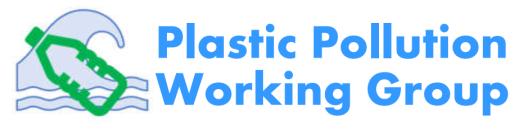
5.3.1 Vacuums are commonly used in cleaning up pellet spills when they occur during their production, transfer or use One example of a vacuum used for nurdle spill cleanup is the Elgee Power-Vac shown in Figure 26. Companies that have committed to OCS are also providing easily accessible hand-held vacuum units for tanker drivers and employees in high-risk spill areas such as silo areas of factories.
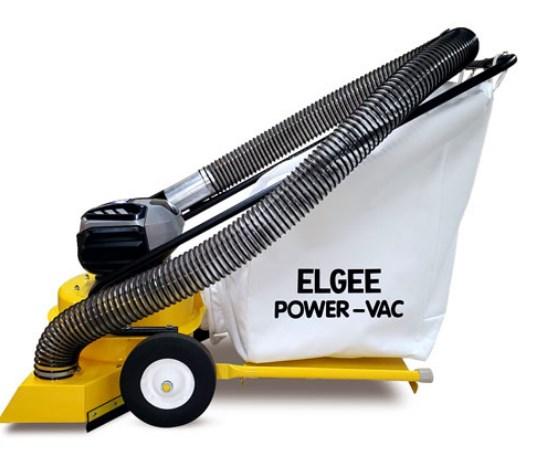
5.4 Catch trays
5.4.1 Catch trays such as the one shown in Figure 28 and 29 can be placed under areas where spills commonly occur such as beneath tankers when they are loading and unloading pellets or beneath silo ports and transfer hosing within factories, preventing pellets from being lost to the ground.
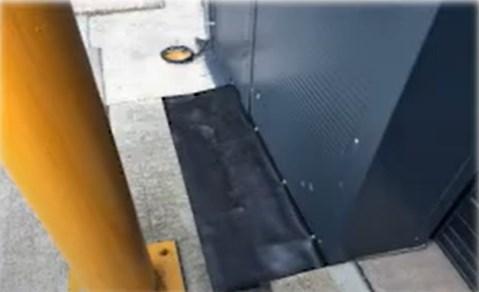
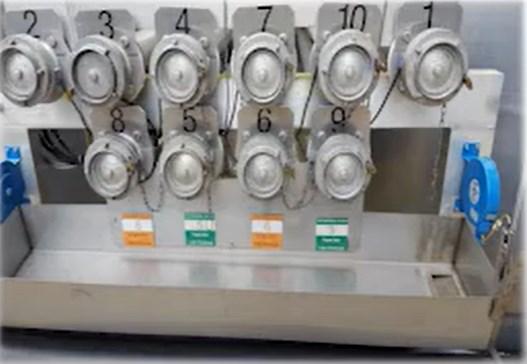
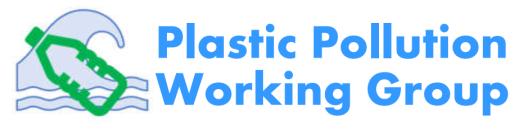
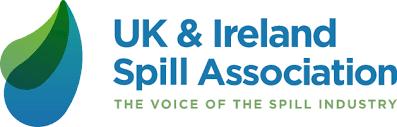
5.5 Storm drain screens
5.5.1 Stormwater drains at plastic production facilities provide an obvious pathway for pellets to enter the stormwater system and thus the wider environment. High risk drains can be covered with rubber sheeting to contain any loose pellets whilst allowing water to pass through as in Figure 30 below. Other, more advanced solutions include the installation of stormwater litter traps as discussed in section 3.1.2. Combined with a routine cleaning schedule, these systems are effective barriers against pellet loss to the wider environment.
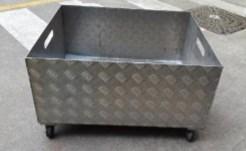
6.1 Plastic pollution is a complex and extensive problem which there is no one simple solution to address it. However, as this review attempts to show, there are a great deal of projects and initiative designs that are continuing to develop to produce effective technologies and solutions designed to help reduce plastic waste at the source; therefore, limit the amount of plastic waste entering our environment
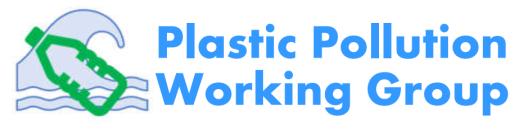
6.2 Current solutions for removing plastics from rivers are largely based on systems that use vehicles such as barges or boats combined with containment booms and conveyor systems, to remove of surface plastics. Innovative solutions, such as The Great Bubble Barrier, aim to create less of an obstruction to wildlife and water traffic whilst encouraging subsurface plastics to float upward for removal In addition as a byproduct this has the added benefit of re-oxygenating the river water. A number of autonomous bots/drones have been developed to remove plastics from watercourses which remove the need for a human operator. However, from the autonomous systems reviewed, these appear to be limited in their effectiveness as they only have capacity to remove relatively small amounts of plastic waste.
6.3 Other solutions to combatting plastics in waterways like the Seabin are established systems designed to skim off floating plastics in still waters such as marinas or harbours. Whereas there are emerging technologies currently in the early stages of research and development, such as the Archimedean drum screw originally designed for jellyfish removal. As well, there is increasing research projects involving the use of flocculation and ultra-sound processes to ‘clump’ together microplastics for easy removal. However, as these projects remains to be seen how effective they are.
6.4 Stormwater drainage is a major pathway for the transport of plastics to the marine environment. There are a number of litter traps and drain filters available which can be installed with filters of various sizes to prevent plastics including microplastics from entering the stormwater system; combined with end of pipe screening systems, these can provide effective protection for watercourses prone to plastic pollution. Although relatively cheap to install, one potential drawback to these systems is that many require regular cleaning to prevent the filter becoming overloaded which may have cost implications, particularly with environments that are identified as plastic pollutant hotspots and have high levels of annual rainfall/flooding.
6.5 Approaches that aim to improve the awareness of the general public as to the potential pathways of plastics to the ocean through visual stimuli such as posters and painted drain curbstones, have been implemented by some local councils. However, the effectiveness of these schemes is yet to be analysed.
6.6 A major source of microplastic pollution at WWTPs appears to be sewage contaminated with fibres from washing clothes; a single garment is expected to produce <1900 fibres per wash. A number of solutions for preventing the release of microfibres form the source have been
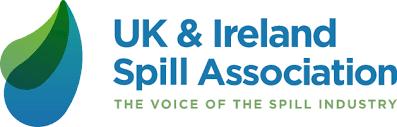
developed, including washing machines with in-built microplastics filters or after-market add on filters such as the PlanetCare filter kit. Encouragingly, washing machines are now more regularly being produced with built in microplastic filters although customers will have to spend more for the privilege. After market filters claim to be equally effective at removing microfibres but need enough space for the installation as well as regular cleaning and cartridge replacement
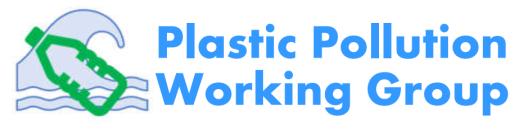
6.7 Simple solutions such as laundry balls are designed to catch fibres during the wash cycle and are simply added in with clothes. Coraball, for example, claims to catch up to 31% of fibres. When used in conjunction with washing machine microfiber filters, the removal rate has been shown to be much higher.
6.8 Pellet (nurdle) pollution is the second largest source of direct microplastic pollution to the ocean and is known to cause serious harm to marine biodiversity. An estimated 230,000 tonnes of pellets are lost to the environment every year. Currently, plastic production facilities can opt into the OCS which aims to provide guidelines for preventing pellet loss at the source. However, this commitment is voluntary and is not enforced.
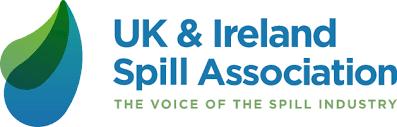
6.9 Clean up solutions for preventing pellet loss at the source (usually plastic production facilities) include the use of spill kits, vacuums, catch trays and stormwater screens/filters in areas at risk of pellet loss such as under tankers, silo hose points and on-site drainage. OCS recommend that these solutions are combined with effective education and training of staff as well as a strict schedule of cleaning and auditing.
6.10 Fundamentally, although not addressed in this review, there needs to be a vast reduction in both the production of plastics and humanity’s reliance on them.
7.0 REFERENCES
Boucher J, Friot D (2017). Primary Microplastics in the Oceans: A Global Evaluation of Sources. Gland, Switzerland: IUCN. 43pp
Browne, M.A., Galloway, T., & Thompson, R. (2007). Microplastic – an emerging contaminant of potential concern? Integrated Environmental Assessment and Management, 3(4):559 561.DOI: 10.1002/ieam.5630030412
Browne, M.A , Crump, P , Niven S , Teuten E, Tonkin, A , Galloway, T , Thompson, R (2011). Accumulation of Microplastic on Shorelines Worldwide: Sources and Sinks. Environmental Science & Technology. Volume 45 (21), 9175-9179
Eunomia (2016). Plastics in the Marine Environment. Bristol: Eunomia Research and Consulting Ltd. http://www.eunomia.co.uk/reports-tools/plasticsin-the-marine-environment/
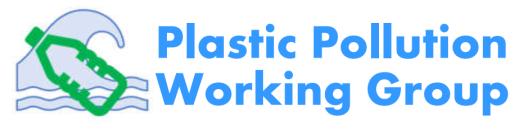
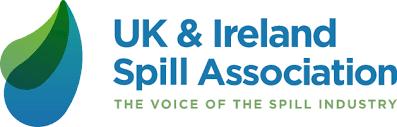
Harley-Nyang, D., Memon, F.A., Jones, N., Galloway, T (2022). Investigation and analysis of microplastics in sewage sludge and biosolids: A case study from one wastewater treatment works in the UK. Science Total Environment.
Horton A A, C. Svendsen, R.J. Williams, D.J. Spurgeon and E. Lahive (2016). Presence and Abundance of Microplastics in Sediments of Tributaries of the River Thames, UK. MICRO 2016. Fate and Impact of Microplastics in Marine Ecosystems. Abstracts from oral presentations.
Hurley R & Nizzetto L (2018). Fate and Occurrence of Micro (Nano)Plastics in Soils: Knowledge Gaps and Possible Risks. Current Opinion Environmental Science & Health. 1. 6-11
Jambeck J, Geyer R, Wilcox C, Siegler T, Perryman M, Andrady A, Narayan R, Law (2015). Plastic Waste Inputs from Land to Sea. Science. Volume 347. Issue 6223. Pp 768 – 771
Koutnik V.S, Leonard J, Alkidim S, De Prima F, Ravi S, Hoek E, Mohanty S (2021). Distribution of Microplastics in Soil & Freshwater Environments: Global Analysis and Framework for Transport Modelling. Environmental Pollution. Volume 274
Lebreton, L and Andrady, A (2019). Future scenarios of global plastic waste generation and disposal. Palgrave Communications. 11 pp.
Lebreton L, van der Zwet J, Damsteeg, JW (2017). River plastic emissions to the world’s oceans. Nat Commun 8, 15611
Harley-Nyang D, Memon FA, Jones N, Galloway T (2022). Investigation and analysis of microplastics in sewage sludge and biosolids: A case study from one wastewater treatment works in the UK. Science Total Environment
Napper, E and Thompson, R (2020). Plastic Debris in the Marine Environment: History and Future Challenges. Global Challenges 2020. 4. 1900081
Controlling Plastics at the Source
Siegfried M, Koelmans A, Besseling E, Kroeze C (2017). Export of Microplastics from Land to Sea. A Modelling Approach. Water Research 127.
Stothra Bhashyam, S Nash, R Deegan, M Pagter, E Frias J (2021). Microplastics in the marine environment: sources, impacts and recommendations Research@THEA
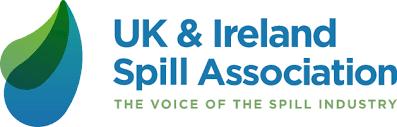
Tiseo I (2022). Global Plastic Production 1950-2020. Statista 2022. https://statista.com/statistics/282732/global-production-of-plastics-since-1950/
UNEP (2021). Drowning in Plastics – Marine Litter and Plastic Waste Vital Graphics. ISBN No: 978-92807-3888-9. Job No: DEP/2386/NA
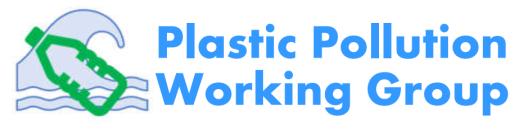
Werbowski AN, Gilbreath L, Munno K, Zhu X, Grbic J, Wu T, Sutton R, Sedlak M, Deshpande A, Rochman C (2021): Urban Stormwater Runoff: A Major Pathway for Anthropogenic Particles, Black Rubbery Fragments and Other Types of Microplastics to Urban Receiving Waters. ACS ES&T Water 1 (6), 1420-1428
Zubris, K and Richards, B (2005). Synthetic Fibres as an Indicator of Land Application of Sludge. Environmental Pollution. Volume 138
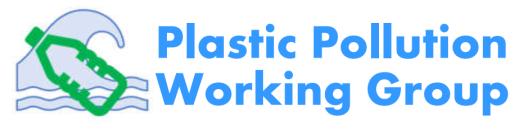
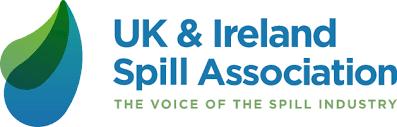