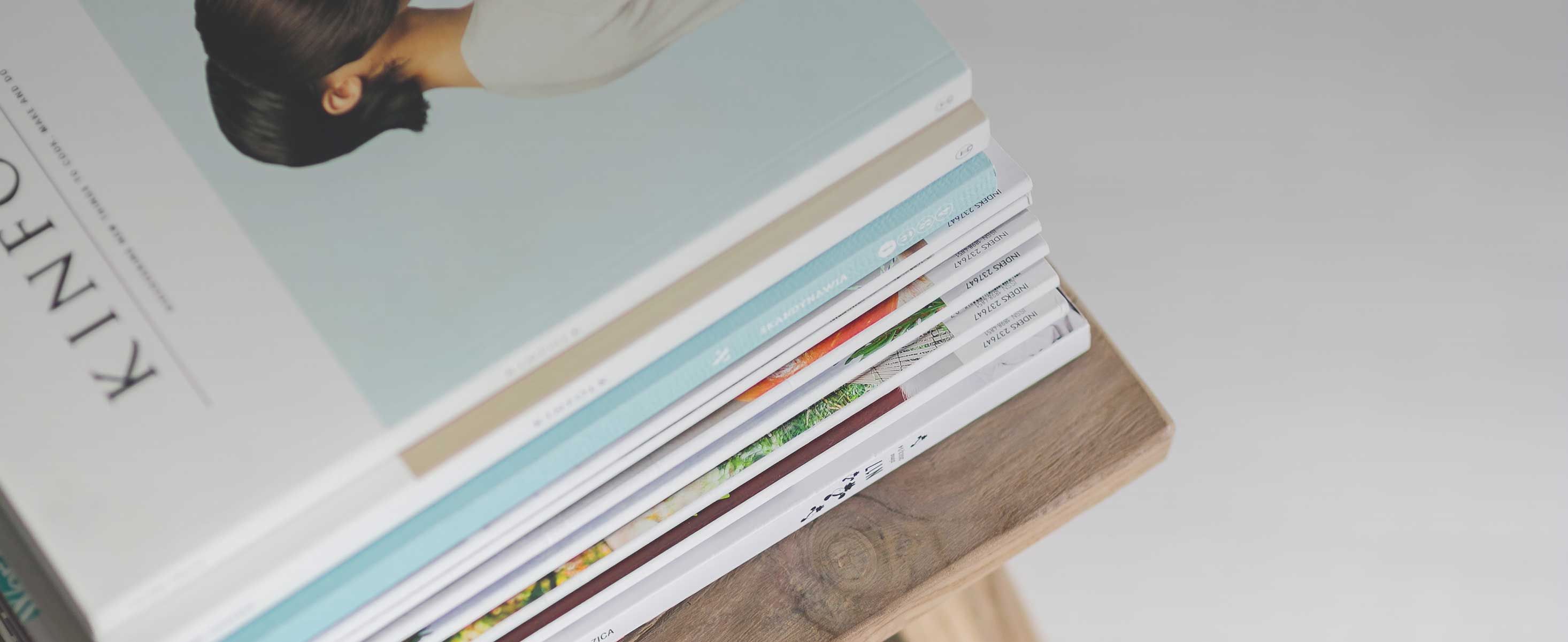
5 minute read
INDUSTRY 4.0
Industry 4.0 offers the potential for smarter, more efficient processes, not only in single factory sites but across supply chains. It also encompasses innovations such as the ‘digital twin’ – a digital replica of an industry process, informed by real-time data, that allows virtual fine-tuning and the diagnosis of faults before they become critical.
In collaboration with industry partners, our researchers are working across the IoT stack – from the hardware within industrial IoT devices through to automated decision making and user acceptance – to realise the full potential of the IoT to improve efficiency, safety and reliability across a range of industry settings.
Improving safety and reliability in the aerospace industry
Advances in energy harvesting and sensor system technologies at Southampton are offering new solutions for aerospace, automotive and other vehicle engineering sectors, where monitoring the condition of engines and other components is crucial.
For example, Southampton is a partner in the EU-funded I2BS project17, working with Safran Aircraft engines and Schaeffler Aerospace to develop a new way to monitor the health of jet engine bearings. As part of this programme, our researchers are examining ways to harvest energy from within the jet
17 https://cordis.europa.eu/project/id/717174 engine, using temperature differentials or the rotation of the shaft itself, to generate small amounts of power for a condition monitoring sensor. The sensors themselves gather data about vibration, temperature and the amount of stress on the bearing, enabling faults to be detected at an early stage to avoid failure.
Our researchers are also developing vibrationpowered energy harvesting systems to monitor other machines and components, including helicopter blades and marine engines.
While the automation and intelligence enabled by IoT devices brings huge benefits for industry processes, it also opens up the risk of cyber and physical attacks, and control systems are one potential point of vulnerability.
Control systems involve communication between computers and machines via a network. It’s possible for an adversary to introduce false inputs to this network, ‘tricking’ the computer into giving a command to the machinery. For example, a false input might cause the computer to open and close a valve more often than is needed, leading to the failure of machinery. In safety-critical industries and infrastructure, such an attack could prove catastrophic.
Building trust within collaborative industry networks
Smart industry IoT systems can enable businesses to work collaboratively, providing greater insight and efficiency across production and supply chains. However, this requires data to be shared between different stakeholders, making data security a concern. Each time information passes a boundary from one data owner to another, the risk of a data breach increases, and this may be an operational risk that businesses are not willing to take.
As well as developing the technical model, the researchers have been investigating the associated operational issues. For example, businesses may be reluctant to share sensitive information about their own systems, so one challenge is to find the right balance – that is, the level of information that is enough to engender trust but that won’t deter companies from participating because of confidentiality concerns.
This work has been developed across several projects in collaboration with industry partners, including the European Connected Factory Platform for Agile Manufacturing18 and the ZDMP: Zero Defect Manufacturing Platform.19
Supporting efficiency and safety in the construction industry
Developing smarter, more secure control systems
Automated industry processes rely on control systems – the computerised systems that control the physical tasks carried out on a production line, for example. The control system uses incoming real-time data gathered by IoT sensors across different parts of the line to monitor and manage activity. One strand of work at Southampton involves the development of mathematical models to optimise the way control systems make decisions based on this data. The algorithms enable the control system to operate more dynamically in response to changing conditions and adjust the production process accordingly, to use resources in the most efficient way and improve productivity.
Southampton researchers have developed a technique called symbolic execution to automatically examine the code underpinning the control system. This method enables the researchers to identify vulnerabilities that could enable this type of attack and suggest additional controls to patch these vulnerabilities.
Improving security across the supply chain
Another aspect of research into IoT system security focuses on the hardware supply chain. For IoT and other devices, most electronics manufacturers procure integrated circuits (ICs) from a network of suppliers, which means they don’t have full oversight of the IC production history. This opens up the risk of manufacturers inadvertently using counterfeit components that don’t meet the design specification, or that contain malware that enables a device to be hacked or attacked.
Our researchers are looking at ways to mitigate this risk, using blockchain and physically unclonable functions to authenticate ICs and track their movement through each stage of manufacture and assembly, so that any tampering can be detected.
To address this, our researchers have developed a risk analysis tool, the System Security Modeller, to analyse the security risks at each transition point and suggest control strategies to mitigate them. Sharing this information among stakeholders builds confidence that the flow of data will not expose any of the collaborative network to cybersecurity risks.
IoT systems are not only being used on production lines – innovations in wearable IoT mean companies can collect data via their workforce to inform business operations and ensure health and safety compliance. Our researchers are helping to improve this type of technology. One example is a project undertaken with Mafic, an SME that produces a system called Safeguard. Safeguard uses intelligent, connected technologies to give construction companies real-time insight into efficiency and safety on their sites. Sensor devices are built into construction workers’ hard hats; these collect and transmit data about workers’ movements, location and environment, which is processed using machine learning techniques to provide information on a range of factors, from levels of noise and dust to the tasks they are undertaking.
Our researchers have helped Mafic to optimise the device, delivering significant improvement in Safeguard’s capabilities. They initially worked on the development of the machine learning algorithms that underpin the technology. More recently, they have been working on two powerrelated challenges to improve the product’s usability – reducing the device’s power consumption and addressing issues around recharging. They applied state-of-the-art low-power techniques to reduce the sensor devices’ power consumption by an order of magnitude, thus extending the battery life.
18 https://www.efpf.org/
19 https://www.zdmp.eu/
They also developed new wireless power transfer techniques for more convenient recharging. Requiring workers to plug their hats in to recharge at the end of their shift was not desirable, but traditional wireless transfer techniques, such as those for mobile phones, require the device to be within 10mm of the power source, which was also not practical for this application. The researchers developed an alternative technique to extend the charging range.
Promoting IoT acceptance on the shop floor
While IoT technologies can bring huge benefits to industry, increased automation inevitably brings about changes for the workforce. One example is a use case where AI-based visual analytics automatically detect whether workers are wearing face masks in spray paint booths, only switching on the necessary equipment when a mask is detected. While this may be attractive to a company in terms of greater safety and efficiency, it requires staff to accept decisions that are not made or mediated by humans – something they may be reluctant to do.
Our researchers are seeking to determine the optimum level of IoT system information that workers need to help them understand the system and build trust and reassurance around its reliability. By providing companies with resources to help them bring their staff on board, the aim is to encourage the uptake of new technologies.