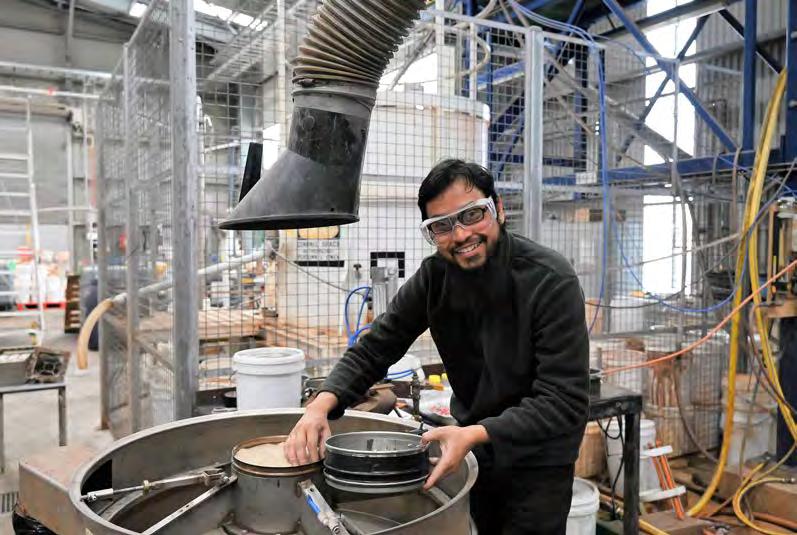
4 minute read
TECHNOLOGY AND SKILL SHARING: SINK-HOLE FLUIDISER
from ARC Centre for Excellence for Enabling Eco-Efficient Beneficiation of Minerals - 2022 Annual Report
Sharing newly invented technology and associated knowledge and skills across multiple node universities and team members has many benefits, including:
Centre members gain the ability to work on cutting edge technologies in mineral processing
Researchers build ‘hands on’ familiarity and skills with Centre-developed innovation and research infrastructure
It expands research possibilities. Different, complementary testing applications can roll out concurrently
It fuels close collaboration and delivers a more cohesive approach to research programs within the Centre overall
It raises the overall awareness of Centre innovation, as each node has unique institutional/METS networks; an important step in the technology development life cycle
Accelerating the pace of learning and novel technology development timelines may enable the Centre to address and solve problems in the mining industry faster than single-node approaches
Advancing blue-sky technology
The Sink-Hole Fluidiser is a novel dry separation technology that produces sharp separations based on mineral density, originating from the Centre’s UON node. It is being shared in the form of a physical set-up at Curtin (as part of ‘Project 16’) for further testing. Parallel workflow accelerates the pace of learning, and ideally, helps to move the invention towards the next stage of development.
The novel technology goes beyond water reduction benefits during beneficiation, as it needs no water for dense mineral separation. Using a ‘dry separation’ technique, it predominantly uses gently upward flowing air and vibrations (energy/signals) to sort and separate dense mineral particles, leveraging the principle that gangue (waste) and mineral particles have different densities.
Earlier Sink-Hole Fluidiser technology tests with sand/silica were relatively simplistic. Current multinode trials test the physical separation of actual gold ores, representing the next phase of scientific research. Simulating industry application enables better understanding about and optimisation of how the device works.
Computational modelling and simulation are also occurring at both UON and Curtin nodes, which enables better understanding of the behaviour of the physical system.
Large reductions in energy (and, it goes without saying, water) consumption can be made using the device and delivering very ‘sharp’ or ‘clean’ separations of dense mineral particles during the early stage of processing. This is very exciting from a research point of view, and very interesting to industry. Other techniques available today cannot efficiently separate dense mineral like low-grade gold ores in this way.
The combined insights of physical testing and computational modelling help discover the further potential of the technology and build a case for future industrial trials, and perhaps one day technology commercialisation and application in industry. So far proof of concept for the technology has between established (to a TRL between 2 and 3).
According to Prof Chris Aldrich: “Having the new technology at Curtin paves the way for closer involvement of industry on the campus site, and with the WA School of Mining’s industrial partners, as we further test and refine the device to help solve industry and environmental challenges with the equipment being used today.”
Collaborative & connected ways of working
Prof Chris Aldrich says, “This project is redefining the state-of-the-art through innovative exploitation of some of the complex physical phenomena associated with granular fluid flow.”
Enabling multiple project team members access to the technology helps establish what may become a major new, Centre-developed technology.
Sharing the experimental device and related computational research across nodes provides enhanced lab test opportunities and brings the increased capacity for parallel research beyond any one campus or team. It also expands the amount of physical experimentation and data generation, fast tracking the learning through parallel experimentations and further validation of the model. It also upskills multiple Centre teams on novel minerals processing techniques.
“Working with the technology builds new skills, which are supported in-person visits where members work closely and collaboratively across nodes. Further the experience gained can be applied to other Centre projects,” Prof Chris Aldrich shared.
The combination of physical experimental and computational modelling being conducted at both
UON and Curtin provides insights into the fundamental mechanisms of separation, drawing on different but complementary data points from advanced sensors and application of data analytics in both systems.
The multiple diagnostic and predictive insights from the numerical modelling are shared among the group, guiding future physical experimental work, enabling the systems to be optimised while guiding equipment development. The combined and collaborative approach contributes to validating the model.
Curtin-based researchers are conducting fundamental research in modelling of granular fluid flow and gaining first-hand insights into fluid flow phenomena and vibration signals through proprietary data algorithms.
Next steps
As more data is collected - from the physical research being undertaken at UON and Curtinthere is potential for machine learning to be applied. Soon, modelling will be able to simulate and predict the results of physical experiments (in Project 16 and related Project 17) with potential application for other Centre projects over time.
The next phase of the Sink-Hole Fluidiser technology development will be validation under continuous steady-state conditions. Positive results for this phase could lead to up-scaling, ultimately with wide-reaching implications for technology application beyond gold for separation of other high-density particles, including many critical minerals.
How the Sink-Hole Fluidiser Works
The device utilises a fluidised bed with vibration applied as an additional energy source to disrupt the tendency of the excess air to pass through as ‘bubbles’, although there is no water present. It consists of a pair of fine mesh screen mounted on top of a vibrated ‘fluidised bed’. The upper mesh contains a large hole in its centre, referred to as a ‘sink-hole’
A combination of vibration and gently upward flowing air fluidises the granular media, inducing a specific state of stress. The ‘media’ consists of fine sand
Once vibrated, the fine particles expand up and through the large sink-hole spreading across the upper mesh
Some of the large particles (only those with highest density) sift back down into the lower bed
- The density of the large particles at the mouth of the sink-hole exceed the bulk density of the fluidised medium, and often also the density of the granular particles in the bed. Despite this, particles denser than the medium float, while those of even higher density sink. The fact that the separation density is higher than the density of the medium is unexpected. Our goal is to establish why such a high separation density can be achieved, and to control the separation density.
By adjusting the mix of vibration, the velocity of the upward flowing air and mass of media, it is possible to vary the separation density
COEMinerals ECR
Tariqul Islam (UON) demonstrates the Sink-Hole Fluidiser