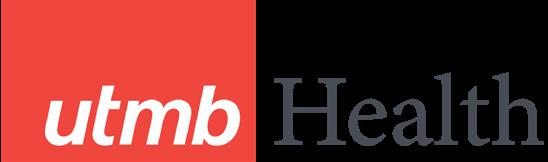
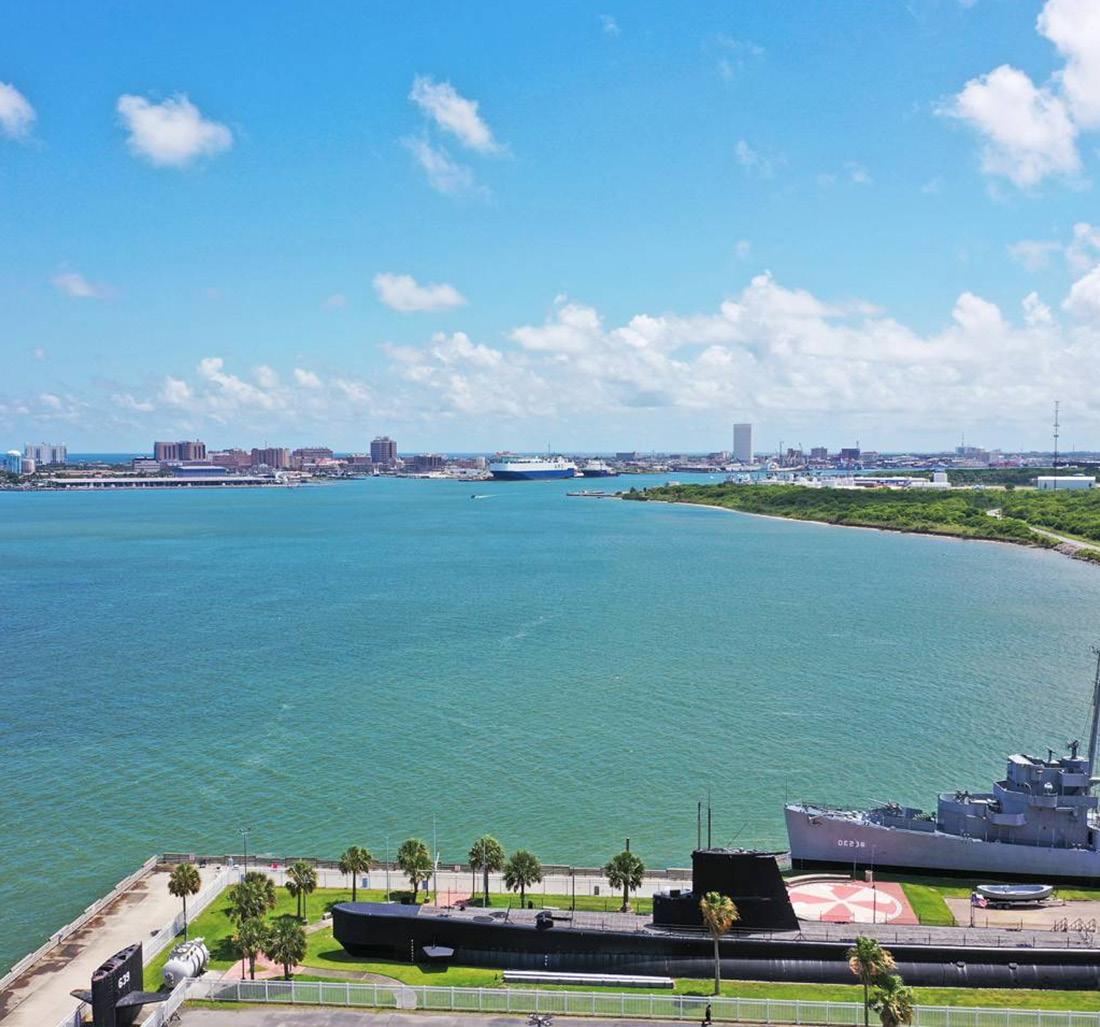
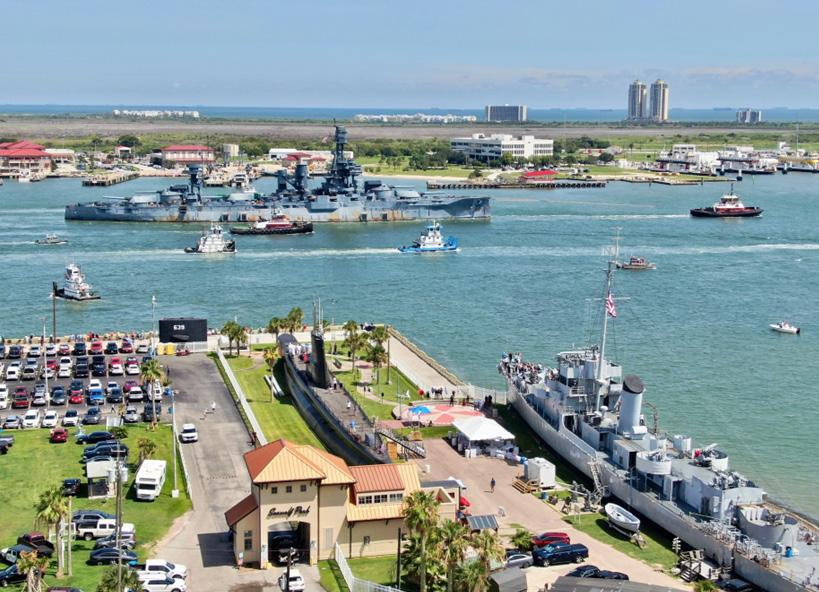
Welcome to the UTMB Environmental Health and Safety (EHS) Annual Report for FY2022. This report is an effort to communicate the most relevant parts of EHS and how our various programs, services, and collaborations work throughout the University.
I would like to highlight our dedicated EHS staff who worked tirelessly throughout the year to ensure the safety of our employees, visitors, and patients through proactive facility inspections, risk assessments, and training. EHS efforts throughout the year also help to ensure UTMB is a good steward of our environmental resources and in compliance with all local, state, and federal regulations.
EHS has updated and implemented safety programs and training to support an environmentally responsible campus and encourage all at UTMB to embrace the safety culture. As always, we hope you find this information to be both interesting and useful.
It is our vision to become a recognized national leader and innovator in campus environmental health and safety providing world class services.
The mission of Environmental Health and Safety is to work with our customers to provide a workplace free of recognized hazards in support of the UTMB mission to improve health for the people of Texas and around the world.
Integrity: Saying what we are going to do, and doing what we say.
Accountability: Holding ourselves and each other accountable for our responsibilities and achieving our goals.
Commitment: To protect the health and safety of our patients, employees, the public, and the environment.
Collaboration: Developing strategic partnerships that foster cooperation and collaboration.
Personifying excellence: Providing the highest level of expertise, competence, and professionalism in our staff.
Quality: Going beyond regulatory “compliance” and aiming for best-inclass.
Environmental Stewardship: Taking the lead to protect the environment and preserve our natural resources.
EHS provides specialized and technical support services for all UTMB facilities to deliver and maintain a protected, safe operational environment.
Environmental Health and Safety is a part of Business Operations & Facilities (BOF). Departments under this group provide institutional support through many businessand facilities-related processes. In addition to EHS, BOF includes the areas of Auxiliary Enterprises, Design & Construction, Portfolio Management, Property Services, and Utilities.
CHARLES P. MOUTON, MD, MS, MBA, PRESIDENT AD INTERIM
STEVEN LEBLANC, PE, MBA, CHFM, VICE PRESIDENT
JACK TARPLEY, MS, CFI, CHMM, ASSOCIATE VICE PRESIDENT CHARLES CARLISLE, MS, CIH, CSP, CHMM, PROGRAM DIRECTOR DE'ANNE MEEH, MS, REM, CHMM, PROGRAM DIRECTOR WILLIAM PATE, DRPH, MBA, LMP, CHP, CIH, CSP, CPP®, CHFM, CHMM, PROGRAM DIRECTOR
Charles Carlisle
Fire & Life Safety Program Director
Todd Perry Dr. Timothy Read Jennifer Riveira Dr. Mario Soares
Principal EHS Specialists
Billy Martin Sr. EHS Specialist
Geraldine Giannotti Walter Mays Brandon Metting Michael Puccetti
EHS Specialists
Clinton Straitwell Corey Wilhite
EHS Technicians
Achieving a safe work environment is realized through dedicated efforts of a highly competent staff of professionals whose fundamental value is to ensure the safest venue possible.
Humberto Espino Sr. Administrative Manager
Victoria Castillo Sr. Business Coordinator
Mariia Arkhypova Business Coordinator
De’Anne Meeh Environmental Protection Program Director
Eddie Stanaland Meagan Thibodaux Principal EHS Specialists
Sergio Garcia Dean Leathers
Jeremy Wilke Sr. EHS Specialists
Dr. William Pate Radiation Safety & Occupational Safety Program Director
Je T’Aime Newton David Stephenson Jim Stone Principal EHS Specialists
Eduardo Reyna Construction Safety & Loss Prevention Manager
Michael Shulke Jordan Sweet EHS Specialists Vacant Sr. EHS Technician
Sharon Walters Sr. Business Coordinator
Morgan Gerami Sr. EHS Specialist
Darla Goodman Adam Jennings Kendle Latiolais
Swan Miller
EHS Specialists
Gale Butler Jeremy Davis Sarah Paredes Samantha Thompson EHS Technicians
Protection System
Safety
Safety
Industrial
• Chemical Safety
• Fall Protection
• Hearing Conservation
• Aerial Lift and Crane Safety
• Respiratory Protection
• Construction Safety
• Radioactive Materials Permitting and Licensing
• X-ray and Laser Registration
• Laboratory Evaluations
• Regulatory Compliance and Support
• Hazardous Waste Management
• Water Quality (Potable, Storm water, and Wastewater)
• Pollution and Spill Prevention
• Air Emission Management
• Emergency Planning & Community Right to Know
• Medical Waste Management
• Compliance Training
• Fire/Life Safety Systems Design, Installation, Testing, and Repair
• Facility Design/Compliance Reviews
• Fire Drills and Institutional Response
• Life Safety/Joint Commission Compliance
• Fire Extinguisher Inspections
• Environment of Care Compliance and Committee Support
• Life Safety Building Inspections
• Interim Life Safety Measures, Hot Work Permitting, and Above Ceiling Work Permitting
• Construction Compliance Management
• Mass Notification Integration
• 24/7 On-Call team providing emergency response capability
• 24/40-hour HAZWOPER trained employees
• Pre-positioned emergency spill response equipment
• Decommissioning pre-planning & coordination
• Hazardous chemical inventory assessment
• Laboratory equipment decontamination
• Hazardous waste determinations and removal
• Environmental Protection Management manages the Public Water System at UTMB
• After a 2-year hiatus, the UTMB Annual Earth Day event is reinstated
• Pre-positioned air monitoring equipment
• Updated standard operating procedures for offsite chemical release response
• Hydrofluoric Acid spill response and casualty decontamination exercise conducted 11/2021
• Supports patient arrival, ambulance, and staff decontamination
• Infectious waste management
• Facilities support training
• Campus-wide mass notification system which integrates overhead voice alerts with fire alarms, Everbridge text alerts, infant abduction alerts and active shooter alerts.
• Construction project safety walks
• Project safety plan reviews
• Crane lift plan reviews
• Root cause analysis & incident investigations
EHS works closely with other campus departments such as: Institutional Preparedness, Design & Construction, Property Services, Healthcare Quality & Safety, Infection Control & Healthcare Epidemiology, Portfolio Management, Utilities, Department of Biosafety, UT System Police, and the University’s schools.
EHS serves as a liaison with regulatory and compliance agencies such as: The Joint Commission, EPA, DEA, U.S. DOT, TCEQ, Texas DSHS, FAA, Texas State Fire Marshal’s Office, AAALAC, and local municipalities. EHS is charged with certain health and safety inspections and compliance for all applicable federal, state, and local regulations and other EHS requirements intended to protect safety, health, and the environment.
EHS serves the entire UTMB community. Our customers include patients, faculty, staff, students, campus visitors, and volunteers.
In FY22 EHS received 243 calls for emergency support ranging from fire alarm activations to hazardous material spills.Port of Galveston, 1877 Tall Ship Elissa is moored to the pier
Every worker, student, visitor, and patient at UTMB should leave our facilities as healthy or healthier than when they arrived.
EHS provides support to four UTMB campuses to ensure healthy and safe operations, protecting students, faculty, staff, visitors, and the environment.
Construction plan review
Serving on regulatory committees
Subject matter experts on health and safety issues to ensure safe design, construction and operation of UTMB facilities
City of Galveston
City of Angleton
City of Webster
City of League City
Odor & Indoor Air Quality response
Hazardous materials shipments
Risk assessments
Accident investigations
Emergency incident response
Exposure monitoring
Respirator fit testing
Occupational Health & Medical Surveillance Program
Environment of Care
Committee Support
TJC documentation
TJC Compliance
Survey support
Risk Assessments
O.R. Fire Safety
Evacuation drills
• 24/7 incident response
Food establishment inspections
Drinking water testing
Identification of slip/ trip/fall hazards
Spill cleanup
Facility Safety Audits
Fire System Repairs
Update and maintain online safety courses
Instructor-led training
• Technical review for renovations
Space evaluations
Fume hood certifications
Lab Audits
Controlled substance disposal
Protocol & permit reviews for committees
Consulting on safe lab practices
Equipment cleanup/ monitoring
Lab setup/closeouts
• Storm Water Programs
Title V Permit Management
Chemical & Biological spill cleanup
Hazardous Waste Disposal
Potable Water System Permit
The Joint Commission (TJC) conducted UTMB’s unannounced triennial accreditation survey May 16th through May 20th, 2022, covering all 6 hospitals and more than 60 clinics. The surveyors reviewed over 10,000 pages of compliance documentation, all hospital areas and many of the clinics. This was the largest, most comprehensive survey UTMB has experienced since it included all 4 campuses for the first time. Surveyors were thorough and cited every deficiency they saw. UTMB’s diligent teams managed to reduce our number of findings in Environment of Care (EOC) and Life Safety (LS) by about 30% from the last triennial survey! There were no significant findings that would result in a conditional status. This was accomplished despite the challenges of the COVID pandemic and weather events that forced us to create new ways to conduct critical business.
EHS specifically coordinated some efforts to always be ready and prepare for TJC audits. Some of these activities included:
• EHS working directly with and hosting third-party audits of our programs, mostly virtual. Performed with Property Services, EHS hosted, tracked, and resolved findings reported.
• EHS, along with Design & Construction and Property Services developed a strike team to survey facilities and correct deficiencies found on-the-spot, as much as possible. Of 2,352 findings, 2,058 were corrected prior to survey (88%). This effort helped to significantly reduce the number of TJC findings from previous surveys.
• EHS developed a significant, comprehensive, and smart digital library of compliance records. Designed to match TJC standards, the system made it easy to help navigate the surveyor through well over 10,000 pages of records. This set a positive tone with the surveyors, which lasted throughout the survey. This library has become a truly integrated effort across departments, including all of EHS, Property Services, Utilities, and Clinical Equipment groups.
• EHS developed a physical and electronic/virtual command center for the survey. Through use of Microsoft Teams (Teams) and other electronic applications, we hosted the survey with a minimal amount of people while having a large resource pool available electronically. Questions from each subject matter expert were typically answered on the spot and scribing information/action items through Microsoft SharePoint (SharePoint) were immediately available for others to immediately correct.
• Drilling for the survey. All the above tactics were pre-tested to ensure they would be effective prior to use.
The LS survey was conducted out of a conference room with Teams running in the background. Field scribes were dedicated to the survey as usual, however this accompanying team utilized SharePoint to keep notes “live” for other team members to monitor and act on in the background. The Teams application was utilized to track the survey’s progress, react quickly to concerns and answer all questions raised by the surveyor that couldn’t be answered by an escort. In short, while the survey was grueling, all of the preparation efforts paid off handsomely.
More than just planning for and executing a well-run survey, EHS holds firm beliefs that we have a key role in keeping our patients, visitors, and employees safe in our facilities. This is our passion executed in the most effective way we know how.
UTMB Galveston
a large quantity generator of hazardous waste,
over one hundred thousand pounds a year. Because of this generator
the Texas Commission on Environmental Quality (TCEQ) requires UTMB Galveston to have projects and programs in place for Source Reduction and Waste Minimization, also known as Pollution Prevention. One project that not only reduc es waste, but also reduces the amount of product purchased in clinical laboratories is solvent distillation. In FY22, the EPM program recycled over 1,631 liters of alco hol, and were able to produce 98% pure alcohol to provide back to Histopathology and Dermatology once alcohol for recycle is generated and distilled. On average, from scientific wholesalers, a liter can cost around $150 per container. This process saved disposal of 430 gallons of alcohol in FY22 and saved clinical labs approxi mately $244,650 in new product.
This year, the TCEQ passed new regulations regarding the management of hazardous pharmaceutical waste. In conjunction with the new Generator Improvement Rules in 40 CFR 262, the new 40 CFR 266 Subpart P regulations focus on the management of pharmaceuticals in a healthcare facility, and more defined requirements for record keeping and reporting. These updated regulations allow holding hazardous pharmaceutical waste for up to one year, regardless of generator status and regular generator status accumulation time limits, as well as no longer having to count total weight of hazardous pharmaceuticals toward the TCEQ Annual Waste Summary. A major change in the regulations focuses on empty containers. In standard hazardous pharmaceutical regulations, any waste container that contained EPA listed waste was still considered hazardous and managed as such. In the new Subpart P regulations, dispensing pharmaceutical containersblister packs, stock bottles, etc. – are no longer managed as hazardous waste. A major process change took place at the Correctional Managed Care (CMC) Pharmacy in Huntsville. Prior to these new regulations, all empty containers of listed waste were managed as hazardous waste, primarily empty Warfarin bottles and blister packs. These new regulations will greatly reduce the volume of hazardous waste being shipped from the CMC Pharmacy due to stock containers and will focus primarily on the management of true RCRA Hazardous Waste Pharmaceuticals. All UTMB campuses and clinics may operate under these Subpart P regulations regarding pharmaceutical waste. All remaining hazardous waste must be managed according to generator status and the new Generator Improvement Rules that were adopted by the TCEQ in February of 2022
In FY22, the EPM program goal was to create a more robust tracking and segregation process for laboratory clean outs by improving the laboratory clean out procedures. Laboratory clean outs are considered chemical pickups with greater than fifty chemicals from a single laboratory at one time, including laboratory moves and close outs. The overall goal was to ensure that all EPM personnel were trained to properly identify and process chemicals at the point of generation, confirm the lab cleanouts are processed appropriately, and performed in an efficient manner. The measured outcomes to complete the goal were as follows:
• Create a living highly hazardous list for reference for unapproved and approved pickups in the EPM Hazardous Waste Database.
• Update the data in the EPM Hazardous Waste Database to better track the lab cleanout process.
• Monitor and determine legacy laboratories (chemical inventory) –formally communicate Lab Cleanout Procedures to the Chemical Safety Committee in collaboration with Occupational Safety and Radiation Safety programs to improve monitoring and identification of legacy laboratories.
• Train EPM staff on in-lab chemical processing to better identify hazardous waste, hazardous and non-hazardous solid waste codes, segregate by waste stream, inventory, and list chemicals into the EPM Hazardous Waste Database.
During the fiscal year, 39 full laboratory clean outs and closures were performed by the EPM personnel, and accounted for over 215 hours of staff time.
The Fire and Life Safety Program (L&FS) has a systemwide mission to provide employees, patients, and visitors with a safe physical environment. To do so, we are actively involved in the built environment from design of facilities, their construction, activation, maintenance and even final decommissioning. We identify potential problems, champion effective solutions and track them to resolution. During the useful life of our facilities, we conduct routine inspections and testing of Life Safety features to ensure code compliance and that they will function properly in times of an emergency. The L&FS group also serves as the liaison to local fire officials, the Joint Commission Life Safety surveyor, and is responsible for fire emergency planning. We help develop departmental plans as well as building-wide and institutional responses to emergencies.
• Fire sprinkled Levin Hall Auditorium in less than 2 months
• Replaced entire fire alarm in the Clear Lake Campus Hospital
• Replaced half of the fire sprinkler system in Trauma garage
• Fire Sprinklered >90% of Moody Medical Library
• Replaced all aging sprinkler heads in ADC hospital and modified for efficient service
• Interconnected Life Safety network with:
◦ Infant abduction system
◦ Active shooter system
◦ Fire alarm/all-clear Everbridge notification
• Upgraded voice notifications in Pharmacology, Child Care building, and Keiller buildings
• Continued support of JSH modernization project
• Updated 150 departmental fire safety programs
• Texas State Fire Marshal audit of TDCJ, Hospital Galveston
• Completed Joint Commission survey
• CDC audit of fire systems for GNL/Keiller/BCU
• Hands-on OR fire safety drills
• On-boarded new life safety vendors
• Updated fire doors in Jennie Sealy and CSW to reset automatically after fire alarms
• Updated mass notification systems to allow outdoor announcements and all-clear announcements
• 772 ATG findings, with 730 closed (95% correction rate)
• Implemented a risk-based EOC tour process
• Inspecting all above-ceiling firewalls in healthcare for deficiencies. Identified 1,000 items and corrected 75%, resulting in a more successful TJC audit
• Created and implemented bi-lingual fire safety training for kitchen staff
Levin Hall Auditorium sprinklering progress• Add fire sprinkler system to School of Allied Health Sciences
• Complete Life Safety upgrades for Moody Medical Library
• Initiate new fire door safety program and execution of new electronic system for tracking
• Hardening and ensuring continuity of campus fire alarm and mass notification/life safety network
• Streamlining of above-ceiling work process
As a part of our ongoing efforts to be good stewards of UTMB resources, EHS constantly strives to reduce costs through competitive bidding of services, close attention to work service, efficiency, and effective maintenance strategies. This has allowed us to do things like reduce the rate of repair costs while the institution has grown.
As part of the Fire and Life Safety mission, we provide employees, students, patients, and visitors with a safe physical environment to conduct business, study, deliver, and receive care. Our staff efficiently tests and inspects Life Safety features to ensure code compliance and that the Life Safety features function properly during an emergency.
The Radiation & Occupational Safety Program (ROccS) works to ensure the safety of laboratory and health care workers. Our technical expertise covers a wide range of areas including radiation safety, laboratory safety, food & potable water safety, and industrial & construction safety. Services offered include sealed source leak tests, receipt & surveying research radioactive material packages, laboratory safety audits, calibration of survey equipment, food safety inspections and permitting, respirator fit tests, and providing training on a wide range of safety topics.
• In response to the COVID-19 pandemic, performed 10,229 respirator fit tests
• Implementation of EHS Assistant to track personnel radiation doses and document ALARA investigations
• Successful planning and performance of a fullscale diesel spill for the EHS On-Call Team, Texas Department of State Health Services x-ray inspection for the Webster Urgent Care Clinic, as well as mammography inspections for the Galveston Campus, Angleton Danbury Campus, and Clear Lake Campus without violations
• Successful communication and support of projects
to import research laboratory hazards chemical inventories into EHS Assistant resulted in more than 95% of research labs coming into compliance with the requirement
• Presented at the College and University Hazardous Materials Conference on “Managing a Respiratory Protection Program during a Global Pandemic”
• Continue to support ongoing and expanded fit testing needs for health care and research staff at all campuses
• Updates to Texas regulations lasers and therapy accelerators which may create impacts to operations
• Laboratory safety audit program focus on time-sensitive chemicals and providing resources to researchers to assist them with effective management of risks
• Anticipated x-ray and radioactive material inspection of Galveston Campus expected in FY23, requiring staff resources to support
Jim Stone, Principal EHS Specialist, providing training to ROccS staff on the use of air monitoring equipmentLaboratory Safety Consultations are an important service to ensure the safety of research operations. On an annual basis, each research laboratory is inspected by team members of the Radiation & Occu pational Safety Program to ensure all expected safety precautions are being used. These efforts directly contribute to the safe and compliant conduct of research at UTMB.
Despite reductions in research use of radioactive material, the use of ionizing and non-ionizing radiation in health care continues to increase. The number of x-ray machines and dosimetry program participants has steadily increased over the years, primarily the result of UTMB health care expansion. Regulatory inspections remain steady, indicating continued need for EHS resources to support institutional compliance.
Fit testing performed by EHS con tinues to be in high demand due to the continuation of the COVID-19 pandemic. Fit testing performed in FY22 nearly reached the amount seen in FY21. Earlier appointment times and adding additional days for fit testing at each regional hospital campus help support health care worker fit testing needs.
The UTMB EHS team responds to small- or large-scale spills 24 hours a day, seven days a week. The first few hours following a spill or release are critical and can have substantial impacts on human health and the environment.
In order to allow laboratory space to be reassigned to new researchers, it must go through a decommissioning process to ensure the safety of the new occupants. Lab decommissioning begins with notification that the researcher intends to vacate (or has already vacated) the space.
Environmental Protection Management manages the Public Water System at UTMB with daily water sampling.
After a 2 year COVID hiatus, UTMB hosted the annual Earth Day event on the plaza in front of the Moody Medical Library on Friday, April 15th.
Off-site chemical incidents, as well as other emergencies within and outside our facilities, can impact UTMB’s ability to fulfill our mission. Being able to respond appropriately to these types of incidents in order to minimize impact and downtime requires careful planning, training, and periodic drills to test our plans. EHS works hard to collaborate with internal and external stakeholders to ensure organizational resiliency and effective responses to emergency incidents.
The UTMB Biocontainment Care Unit (BCU) was established in 2014 to be one of 10 federally funded Regional Emerging and Special Pathogens Treatment Centers (RESPTC) capable of caring for individuals infected with highly contagious pathogens with profound potential societal impact such as Ebola, and other hemorrhagic fever viruses.
EHS is continuing to improve emergency communications on campus through a series of technology innovations and network improvements. Of note, we now have a campus-wide mass notification system which integrates overhead voice alerts with fire alarms, Everbridge text alerts, infant abduction alerts, and active shooter alerts. Now, alerts are automated to some or all users as conditions dictate. An additional benefit is now we are able to issue “All-Clear”, prerecorded messages outside of buildings to allow occupants back in much quicker once the scene is cleared or a drill is over. In some cases, the new notification time from incident report to notification of occupants has dropped by >90% now that they are fully automatic. Note: As before, please call 911 or (409) 772-1111 (Campus Police) to report all emergencies.
The Construction Safety program supports the safe execution of construction activities across all campuses.
The UTMB EHS team, responds to small- or large-scale spills 24 hours a day, seven days a week. The first few hours following a spill or release are critical and can have substantial impacts on human health and the environment. Therefore, rapid response is crucial to mitigate the impacts of an accidental release. In FY22, UTMB had a variety of spills ranging from petroleum products to corrosive materials. The most recent spill occurred when a flange on an aboveground diesel line failed and released several hundred gallons of diesel, some of which made its way into a nearby storm drain. Red diesel (aka off-road diesel) was visible in the storm drain. When a petroleum product reaches the water, it creates a shiny iridescence appearance on the surface of the water comparable to the colors of a rainbow, commonly referred to as a “sheen”. Following the diesel release, UTMB personnel observed a sheen on the water in the underground storm sewer near the spill location. As previously mentioned, response time is critical to containing a spill and lessening the impact on the environment. During this particular incident, EHS responded quickly and was able to contain the spill within the storm water system by isolating the leaking diesel line and using multiple absorbent booms to prevent the product from migrating towards nearby Galveston Bay. UTMB also called in a third-party spill response contractor to help assist in the cleanup efforts. Due to the quick and effective response, EHS recovered the vast majority of the diesel and, more importantly, prevented an impact to Galveston Bay.
At one time or another, a research laboratory on campus will close. This might be due to faculty retirement, moving into new laboratory space, or simply the faculty leaving the university. However, lab closures happen and it is important to realize that a process needs to be followed to ensure the safe shutdown of the lab. EHS works to ensure that laboratories that are no longer in use have been appropriately decommissioned in order to minimize residual safety hazards as well as to ensure the compliant management of hazardous waste streams.
Lab decommissioning begins with notification to EHS that the Principal Investigator (PI) intends to vacate (or has already vacated) the space. EHS tries to stay ahead of these decisions by participating in planning meetings with the Academic Enterprise, but sometimes we do not know what is happening until we get a phone call from the department telling us they want the lab cleaned out so they can reassign it to a new researcher. As soon as we learn that a lab needs to be decommissioned, several processes initiate to ensure that everything is done correctly.
All laboratory equipment used with hazardous materials (chemicals, radiologicals, biologicals) must be decontaminated before it is re located and sent to surplus. EHS provides a laboratory equipment decontamination form online, which once submitted, prompts an EHS employee to go and verify that the equipment has actually been decontaminated and that all warning labels have been re moved from it. EHS provides training to our movers to ensure that they know not to relocate equipment that still has warning stickers or that does not have a decontamination form attached.
EHS will also begin a review of the hazardous chemical inventory for the lab. This review of the hazardous chemical inventory allows us to identify materials that may be of particularly high risk to handlers (time-sensitive, shock-sensitive) or that might have unique waste disposal requirements. Once the inventory is reviewed, EHS will visit the lab to observe its con dition and verify the contents of the inventory. For a lab cleanout that might involve hundreds of chemicals needing to be disposed, this can be a time-consuming process where each chemical is identified, hazards determined, and prepared for off-site shipment and disposal.
The EPM Program manages the UTMB Public Water System for compliance with federal and state public drinking water rules and regulations established by the Environmental Protection Agency (EPA) and the TCEQ. Some of these responsibilities include daily monitoring of chlorine residual disinfectant, total coliform bacteria sampling, lead & copper level sampling, disinfectant byproduct monitoring, and the associated reporting to the TCEQ.
After a 2 year COVID hiatus, UTMB hosted the annual Earth Day event on the plaza in front of the Moody Medical Library on Friday, April 15th. There were many vendors, 2 food trucks, and the guests were given Loblolly Pine seedlings. Dean Leathers, EPM, is the EHS representative for planning and executing Earth Day at UTMB, along with Angela McDowell and Neal Cooper, BOF Sustainability. The Earth Day Committee is strongly supported by UTMB Leadership. This year Aaron LeMay, interim Chief Financial and Business Officer, spoke about green energy.
UTMB is located in a region with a large petrochemical industry. Every day, hundreds of thousands of gallons of chemicals are transported or processed within relatively close proximity to our facilities. Although industry does their best to prevent spills and releases that impact the surrounding community, the reality is that sometimes things happen which are neither expected or desired, having consequences on their neighbors. In one example, the Intercontinental Terminals Company (ITC) experienced a 2019 fire in their Deer Park Facility that burned for days, releasing a plume of toxic smoke that impacted surrounding regions. Fortunately, impact to UTMB facilities was minimal, but exemplified the risk facing our facilities from such large-scale industrial disasters.
In order to minimize the impact from such events, EHS has taken steps to help bolster our internal response capabilities as well as to improve coordination between UTMB and outside organizations. Utilizing Resource Allocation Program (RAP) funding, EHS purchased additional air monitoring equipment. This equipment has been pre-positioned at each of our regional hospital locations, allowing for more rapid response to evaluate atmospheric conditions in a UTMB facility should there be an incident. In addition, we have reviewed and updated existing emergency response plans as well as developed a new plan focused on identifying how we will respond to an off-site incident that might be creating an impact to UTMB facilities.
In FY22, EHS continued to work with internal and external customers to improve emergency response across the campuses, and work with our community to improve regional and institutional response to large-scale chemical releases. We hosted a variety of training this past year as in prior years. Some training included:
• Response coordination with local industry simulating employee exposures to Hydrofluoric acid
• O.R. fire safety and mock patient evacuation training
• Emergency drills starting with a regular fire drill but escalating the “event” to include senior management and review potential evacuation protocols.
The UTMB Biocontainment Care Unit (BCU) was established in 2014 to be one of 10 federally funded Regional Emerging and Special Pathogens Treatment Centers (RESPTC), capable of caring for individuals infected with highly contagious pathogens with profound potential societal impact such as Ebola and other hemorrhagic fever viruses. Providing care for individuals either infected with or under investigation for those diseases requires specialized personal protective equipment for health workers, rigorous waste management protocols, and careful handling of clinical laboratory specimens.
Environmental Health and Safety plays an important role to ensure the safety of the healthcare workers, patient(s), and Emergency Medical Services (EMS) personnel. Our responsibilities start with the first notification that we are receiving a patient and working with our Facilities group to ensure the readiness of the BCU. We are then the first point of contact once the patient arrives to ensure a safe entry into the unit. Our focus then shifts to assisting EMS personnel with waste management and doffing. The success of the EHS BCU team is accomplished by training, drilling, and collaborating with Southeast Texas Regional Advisory Council (SETRAC), National Emerging Special Pathogens Training and Education Center (NETEC) and UTMB Special Pathogens Excellence in Clinical Treatment Readiness & Education Program (SPECTRE).
The author, pastor, and leadership expert, John C. Maxwell once wrote that “if you are proactive, you focus on preparing. If you are reactive, you end up focusing on repairing.” As UTMB continues its more than 130 year tradition of excellence in preparedness and response to emerging infectious diseases, collaborations like this one will help the institution, our region, and the State of Texas be ready for whatever may come next, whether it is already here or not.
EHS is continuing to improve emergency communications on campus through a series of technology innovations and network improvements. Of note, UTMB Health now has a campus-wide mass notification system integrating fire alarms, Everbridge, infant abduction alerts, and active shooter alerts. These integrations allow us to issue automated alerts for each type of emergency both by pre-recorded overhead/outside messages and through Everbridge to select or all users.
An additional benefit is that we are now able to issue “All-Clear”, prerecorded messages outside of buildings, to allow occupants back in much quicker once the scene is cleared or a drill is over. In some cases, the notification time from incident report to notification of occupant has dropped by >90% now that it is fully automatic. Note: As before, please call 911 or (409) 772-1111 (Campus Police) to report all emergencies.
Current systems that have been integrated, providing for rapid, automatic responses include:
• Infant abduction system (aka “Dr. Pink”)
• Active shooter alert (aka “Amber box”)
• Fire alarm (aka “Dr. Red”)
Additionally, EHS has further leveraged the Everbridge system by using “phased templates” to increase speed of communication during events. For internal responses, we now alert staff with the event, requested responders, and resources needed. The system follows the standard Incident Command Response format and allows us to build on the event, send pictures back to the group within that event, update who the incident commander is, additional resources needed, and have a single, continuous communication log to review in the After-Action Report following. As a bonus, the system automatically changes who is notified based on the time of day.
The Construction Safety program supports the safe execution of construction activities across all campuses. The program collaborates with BOF departments to facilitate safety processes on capital projects including construction for deferred maintenance, renovations, infrastructure upgrades, and new development. Recently, the institution has reinitiated participation in the UT System Rolling Owner Controlled Insurance Program (ROCIP) with the John Sealy Hospital Modernization Phase III project. In order to support our commitment to this initiative, an extensive review of the project safety management plan must be conducted, including the approval of contractor safety team members, subcontractors, and designated occupational clinics. Root Cause Analysis (RCA) meetings are held after a high-level observation is identified, an injury, property damage, or when requested by UTMB. Crane operations can be considered a high-risk activity; therefore a comprehensive review of a crane lift plan is conducted prior to a lift is required to ensure compliance with federal and campus requirements. The program has also worked to implement several safety initiatives with Job Order Contracting (JOC) Services which include, contractor safety orientations, monthly project reporting, and recently, full-time safety oversight for these projects.
2022
February
• Certified Safety Professional (CSP)
Je T’Aime Newton, Principal EHS Specialist (ROccS)
• Presented at the College and University Hazardous Material Management Conference presentation titled “Managing a Respiratory Protection Program During the COVID-19
Pandemic”
Jordan Sweet, EHS Specialist (EPM)
• Class D Water Operator License
• Class D Waste Water Operator License
Sarah Paredes, EHS Technician (ROccS)
• Associates of Art Degree (AA)
Morgan Gerami, Sr. EHS Specialist (ROccS)
• Associate Safety Professional (ASP)
• Class D Water License from the Texas Commission on Environmental Quality (TCEQ)
• Associate Safety Professional (ASP)
• Certified Safety Professional (CSP)
Dr Timothy Read, Principal EHS Specialist (F&LS)
• Certified Healthcare Safety Professional (CHSP)
Michael Puccetti, EHS Specialist (F&LS)
• Associates of Applied Sciences (AAS)
Brandon Metting, EHS Specialist (F&LS)
• EST-4 Programmer Certification
Dr. William Pate, Director Radiation & Occupational Safety Program
• Published revised chapter on waste management in the Association for Professionals in Infection Control & Epidemiology (APIC) Text
Sarah Paredes