
8 minute read
Fabrication
The goal of the vacuum-forming process is to heat a plastic sheet to most flexible state (ideal forming temperature). Plastic sheets will begin to transition from their more rigid state at room temperature soon after passing the glass transition temperature.
Once the molds have been created, we selected three dominant plastics (LDPE, white sytrene, and black ABS) to use in the workshop. While these three were chosen, nine total option were tested and can be used.
Advertisement
Below are the settings and results for each type of plastic. Content includes vacuum former settings, material properties and vacuum form results.
Tools
Vacuum Former MDF Molds Plastic clippers & cutters Plastic punch
Materials
Plastic sheets (as necessary) Elastic string
Type | Thickness | Workability | Recycling Code
White styrene | 1/16” | Easy | 6
Results from Vacuum TestsResults from Vacuum TestsVacuum FormingVacuum Forming
Below are comparisons of each plastic type after different durations of heating Below are comparisons of each plastic type after different durations of heating Results from Vacuum Tests Results from Vacuum Tests in the vacuum former. For each plastic, the first test was a length of two minutes and the second test was either for a shorter or longer amount of time, depending on material response. in the vacuum former. For each plastic, the first test was a length of two minutes and the second test was either for a shorter or longer amount of time, depending on material response. Below are comparisons of each plastic type after different durations of heating in the vacuum former. For each plastic, the first test was a length of two minutes and the second test was either for a shorter or longer amount of time, depending Below are comparisons of each plastic type after different durations of heating in the vacuum former. For each plastic, the first test was a length of two minutes and the second test was either for a shorter or longer amount of time, depending Results from Vacuum Tests Below are comparisons of each plastic type after different durations of heating Results from Vacuum Tests Below are comparisons of each plastic type after different durations of heating For our workshop, we used white styrene, black ABS, and LDPE. For our workshop, we used white styrene, black ABS, and LDPE. on material response. on material response. in the vacuum former. For each plastic, the first test was a length of two minutes and the second test was either for a shorter or longer amount of time, depending in the vacuum former. For each plastic, the first test was a length of two minutes and the second test was either for a shorter or longer amount of time, depending For our workshop, we used white styrene, black ABS, and LDPE. For our workshop, we used white styrene, black ABS, and LDPE. on material response.on material response. For our workshop, we used white styrene, black ABS, and LDPE. For our workshop, we used white styrene, black ABS, and LDPE.
Black ABS | 1/16” | Easy | 7
white styrene - 1 minutewhite styrene - 1 minute White styrene 1 minute. white styrene - 1 minute white styrene - 2 minutes white styrene - 2 minutes White styrene 2 minutes. white styrene - 2 minutes white styrene - 1 minute white styrene - 2 minutes
white styrene - 1 minutewhite styrene - 1 minute white styrene - 2 minutes white styrene - 2 minutes
LDPE | 1/16” | medium | 4
Cast acrylic | 1/8” | Medium | 7
black ABS - 2 minutes black ABS - 2 minutes black ABS - 3 minutes black ABS - 3 minutes
black ABS - 2 minutes Black ABS 1 minute. black ABS - 3 minutes black ABS - 2 minutes Black ABS 2 minutes. black ABS - 3 minutes
black ABS - 2 minutes black ABS - 2 minutes black ABS - 3 minutes black ABS - 3 minutes
LDPE - 1 minuteLDPE - 1 minute LDPE - 2 minutesLDPE - 2 minutes
LDPE - 1 minute LDPE - 2 minutesLDPE - 1 minute LDPE - 2 minutes
15 15
15 15 LDPE - 2 minutesLDPE - 1 minute LDPE - 2 minutesLDPE - 1 minute Vacuum Forming Vacuum Forming LDPE 1 minute. LDPE 2 minutes.
15 15
cast acrylic - 2 minutes Cast acrylic 1 minute. cast acrylic - 3 minutes cast acrylic - 2 minutes Cast acrylic 2 minutes. cast acrylic - 3 minutes
Type | Thickness | Workability | Recycling Code
PETG | 1/16” | Medium | 1
HDPE | 1/16” | Medium | 2
Polypropylene | 1/16” | Medium | 5
cast acrylic - 2 minutes clear PETG - 2 minutes cast acrylic - 3 minutes cast acrylic - 2 minutes clear PETG - 3 minutesclear PETG - 2 minutes
clear PETG - 2 minutes PETG 1 minute. clear polycarbonate - 2 minutes clear PETG - 3 minutesclear PETG - 2 minutes PETG 2 minutes. clear polycarbonate - 3 minutesclear polycarbonate - 2 minutes
Vacuum FormingVacuum Forming
clear polycarbonate - 2 minutes HDPE - 2 minutes HDPE 1 minute. clear polycarbonate - 3 minutes HDPE - 4 minutes clear polycarbonate - 2 minutes HDPE - 2 minutes HDPE 2 minutes.
16
Vacuum FormingVacuum Forming
HDPE - 2 minutes
HDPE - 4 minutesHDPE - 2 minutes white polypropylene - 3 minutes white polypropylene - 2 minutes white polypropylene - 3 minutes white polypropylene - 2 minutes Polypropylene 1 minute. Polypropylene 2 minutes.16
white polypropylene - 3 minutes white polypropylene - 2 minutes white polypropylene - 3 minutes white polypropylene - 2 minutes PVC 1 minute. PVC 2 minutes.grey PVC - 1 minute grey PVC - 2 minutesgrey PVC - 1 minute grey PVC - 2 minutes
Type | Thickness | Workability | Recycling Code
Polycarbonate | 1/16” | medium / hard | 7
white polypropylene - 3 minutes white polypropylene - 2 minutes white polypropylene - 3 minutes white polypropylene - 2 minutes cast acrylic - 2 minutes cast acrylic - 2 minutes cast acrylic - 3 minutes cast acrylic - 3 minutes
clear PETG - 2 minutesclear PETG - 2 minutesgrey PVC - 1 minutegrey PVC - 1 minute Grey PVC 1 minute. clear PETG - 3 minutesclear PETG - 3 minutesgrey PVC - 2 minutesgrey PVC - 2 minutes Grey PVC 2 minutes.
clear polycarbonate - 2 minutesclear polycarbonate - 2 minuteswhite acrylic - 2 minuteswhite acrylic - 2 minutes Polycarbonate 1 minute. clear polycarbonate - 3 minutesclear polycarbonate - 3 minuteswhite acrylic - 3 minuteswhite acrylic - 3 minutes Polycarbonate 2 minutes.
HDPE - 2 minutesHDPE - 2 minutes
17 17
HDPE - 4 minutesHDPE - 4 minutes
16
16
Notes for Future Workshops
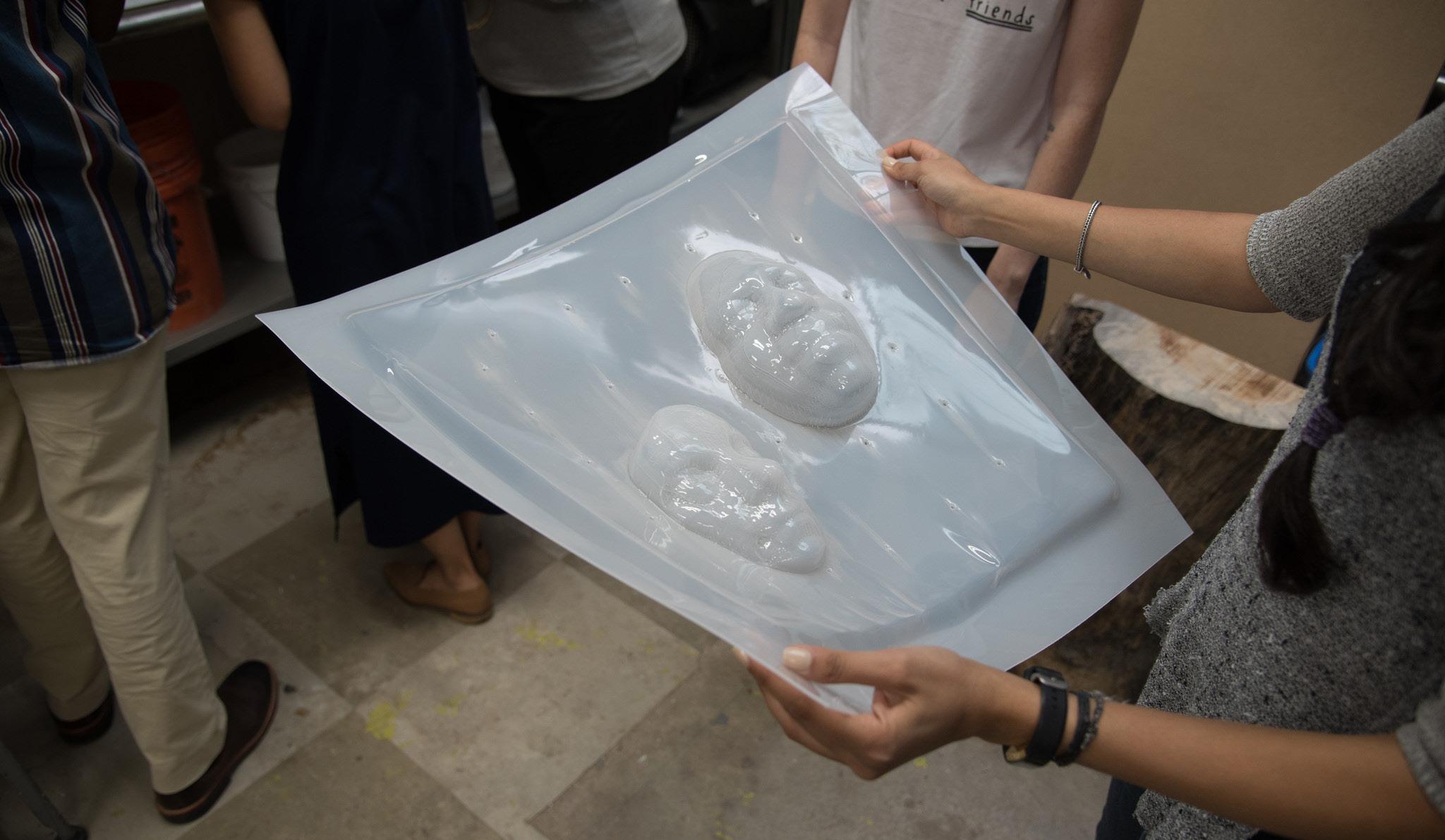
Mold fabrication
- CNC routing molds out of MDF is just one of the ways that this workshop has been conducted. There are many other ways of fabricating molds that could be explored such as casting a negative shape, or CNC routing using other heat-resistant materials for molds.
Subject matter
- The goal of this workshop is to familiarize students at the UTSOA to under-utilized technology. The 3D scanner, CNC router and vacuum former can be utilized to fabricate a wide range of forms for different applications.
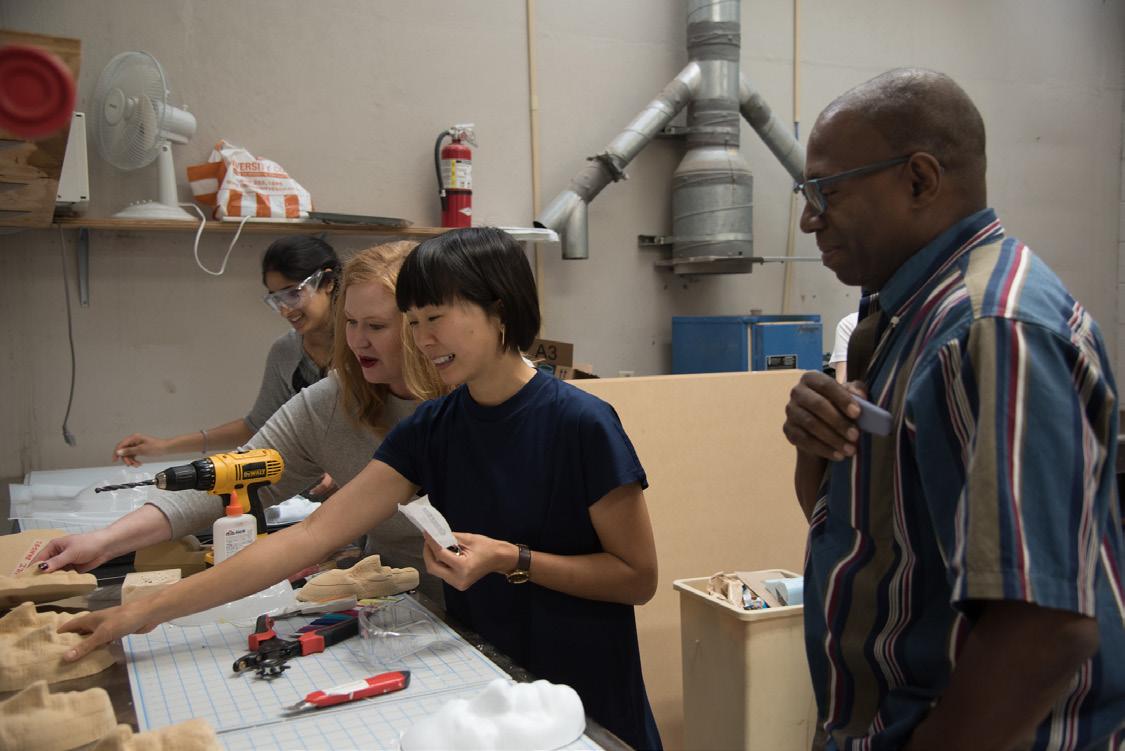

Notes for improvement
- The (2) layers of 1/2” formaldehyde-free MDF used to create the separate transverse cuts of the molds could be rethought. In order to create flush transitions between layers, the excess MDF had to be sanded down on the back of each laminate. In order to avoid this it is possible to glue (4) laminates in order to minimize sanding.
- Additional means should be sought out to educate others with the types of plastics and their advantages/ disadvantages with others.
- Marking the scrap plastic materials with their plastic recycle-ability number is crucial. Materials will not be recycled without the number being on it in some semi-permanent manner.