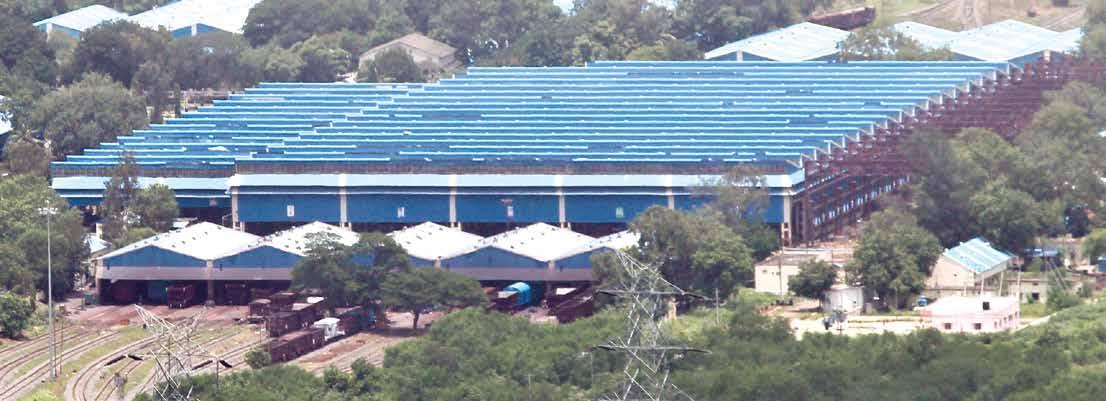
3 minute read
WAGON WORKSHOP GUNTUPALLI, AP
About the workshop
Advertisement
Wagon Workshop, Guntupalli was established in the year 1976 near Vijayawada in South Central Railway to cater the needs of Broad Gauge Wagons Overhauling of Indian Railways with an outturn capacity of 510 wagons/ month. Wagon Workshop is certified to international standards for Quality Management, Environment Management, Occupational Health and Safety, Energy Management, ISO 3834 (Certification for Welding), 5S & Six Sigma and first workshop to achieve GreenCo Platinum.
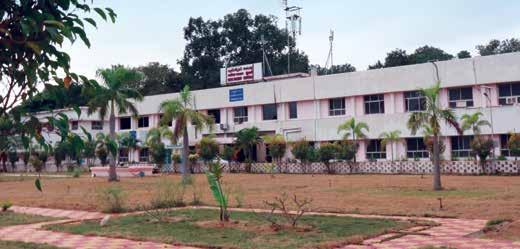
The world is facing severe climatic changes i.e. global warming and every industry needs to address this issue. The Railways has also taken proactive measures in adopting eco-friendly steps. CII has been playing a pivotal and instrumental role in providing the necessary support and guidance to various industries to achieve the goals in doing business in Green ways. In 2017, Wagon Workshop/Guntupalli received “Green Co Gold” rating. Subsequently with further hand-holding and guidance from CII, Wagon Workshop/Guntupalli was able to identify new areas to improve. Accordingly, WWS/Guntupalli achieved “Green Co Platinum” certification due to our continued efforts, administrative will, environmental management and active support of CII. Birendra Sinku, Chief Workshop Manager
Key Achievements
1. Elimination of kerosene by installing CTRB cleaning equipment. 2. 16.5% reduction in specific energy consumption since 2016-17. 3. 10.15% reduction in specific total GHG emissions since 2016-17. Carbon sequestration is 52%. 4. 03 Nos. of reciprocating compressors are replaced by 02 Nos. of screw compressors. 5. By making a setup for overhauling BVZI wheel sets at in house, GHG emission of 23 MT of CO2 eq. is reduced.
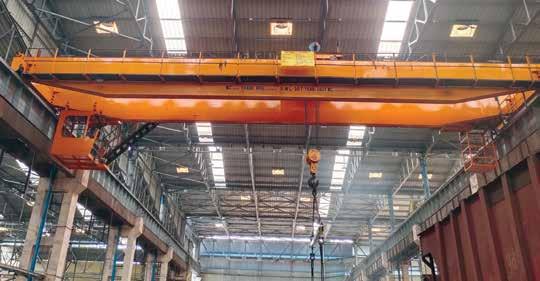
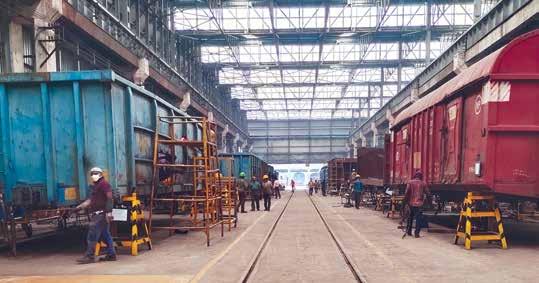
Unique Initiatives
Design of ‘Distributor Valve Cleaning Equipment (In house)’- 1st time in Indian Railways. y Improved cleaning quality and quantity. y Reduce operating cost and rework. y No usage of kerosene oil for cleaning of distributor valve components. Hence, no traces of kerosene fumes and minimize dermal exposure and spillage of cleaning agents by which no affect on the health of the staff working in the vicinity. y Size of Particle on cleaned DV:- Conventional method: 500 microns, Designed DV plant: 150 microns.

Energy Efficiency
y Use of virtual reality arc welding simulator. y Replacement of old machineries with new ones like welding plants etc. y Use of BLDC fans (28W) in place of non-star rated fans (60W). y Energy efficient lights such as use of 100W LED light fittings in place of 500W halogen fittings etc. y Use of star rated air conditioners, water coolers in place of conventional air conditioners & water coolers. y Provision of VVVF drives for EOT cranes, traversors, air compressors etc. y Provision of solar light pipes, solar street lights, solar water heater and solar panels.
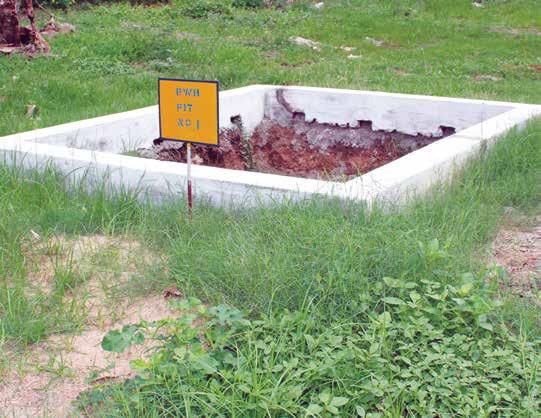
Water Conservation
y Orifices are provided to decrease fresh water consumption. y Water for gardening (10,000 m2) from two percolation ponds which saves the fresh water consumption of 30,000 Litre. y Use of sprinklers for gardening. By using sprinklers for watering the lawn daily 4KL water is saved. y Renovating the water pipelines & providing the lift cocks & push cocks/ grills to prevent entry of monkeys. y Replacement of manual utensil cleaning with automatic dish cleaning machine in canteen. Conservation per month is 36 KL compared to manual cleaning. y Bogie washing by collected rain water. y Arrangement of rain water harvesting pits.

Waste management
y Serviceable released materials from wagons are reused after attending minor repairs. y Zero waste to landfill. y Various pollutants such as SPM, SOx, NOx etc. are monitored monthly and are well better than CPCB prescribed values. y Effluent is recycled for vehicle washing & toilet flushing. y Effluent treatment plant of capacity 75KLD is available. y Water recycling plant of capacity 1,500 Lit/Hr capacity is available.
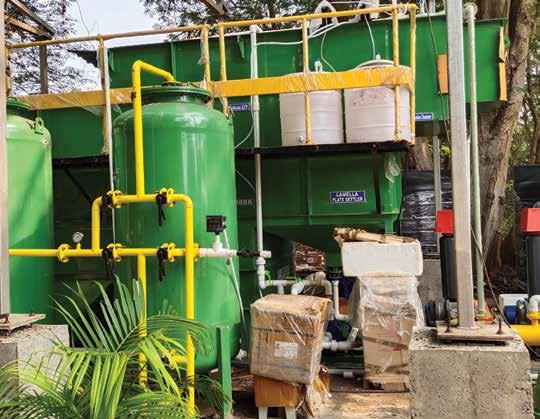
Material Conservation
y Using 100% reusable packing material for dispatch of materials to other divisions. y Reusing released good items like PU rings in bogie shop, rubber hoses in gas repair section. y Reclamation of materials from condemned wagons is approx.
Rs 35 crore per year. y Reclaiming serviceable items eg. operating handles, hand brake wheels, etc.
Contact: mr. Akhil Palliwar, AWM, Wagon Workshop Guntupalli - 521241, Vijayawada, ANDHRA PRADESH Phone: +91 9701379433 | E-mail: iso.wwsgtpl@gmail.com