
6 minute read
RAIL WHEEL FACTORY YELAHANKA, KA
Gold
rAIL wheeL fACTOry yeLAhAnkA, kArnATAkA
Advertisement
about the production unit
Rail Wheel Factory (RWF), set up in 1984, is a production unit under the Ministry of Railways. It is an integrated plant undertaking manufacture of cast wheels, forged axles and assembly of wheel sets primarily for Indian Railways applications. Present production capacity of RWF is 1,90,000 wheels, 70000 axles and wheelsets. It is certified as per international standards of ISO 9001,ISO 14001, ISO45001, EnMS 50001, AAR QA5000, IRIS ISO/TS 22163:2017. This is the only production unit of Indian Railway certified as per IRIS standard ISO/ TS 22163:2017 as well as American Standard AAR QA 5000. Its Laboratory is certified as per NABL ISO/IEC 17025:2017 Despite coming in the red category industry, RWF has been all along been in the forefront for taking environment management and pollution control measures. With a lot of greenery inside it, RWF, despite being a red category industry, acts like green lungs for this area.
For a red category energy intensive unit like RWF, getting GreenCo ‘Gold’ rating, and that too with a sufficient margin, is a great achievement. It bears testimony to the continuous endeavour and commitment of the staff, supervisors and officers of RWF towards environmental sustainability and innovation. RWF, despite being located in the midst of Bengaluru city, has taken all efforts to ensure sustainable manufacturing process, pollution control, conservation of energy and natural resources, and above all a balanced eco-system around RWF, so as to make the earth a better place to live in.
Ajai Kumar dubey, General Manager
Key Achievements
1. Switching over from HSD to PNG fuel in all furnaces of Wheel
Shop and Axle Shop, with 32% reduction in Carbon emission. 2. Reclamation of more than 6600 MT of used sand lying for years.
With commissioning of sand reclamation plant, the annual consumption requirement of sand from about 7500 MT to about 2500 MT. 3. Achieved 100% Switching over to LED lighting systems. 4. 2 MW Off-grid roof top solar installation and two hybrids (solar+ wind) off-grid installations, commissioned. 5. Received “JALARUSHI PURASKAR-2020” from Bangalore
Water Supply and Sewage Board in recognition of RWF’s water conservation efforts. 6. Achieved self-sustenance in process water requirement through rain water harvesting and harnessing water through development of water bodies. Total water consumption in plant reduced by 32.58% in last three years. 7. Received Golden Peacock Award for Eco-Innovation in the year 2021 8. RWF received Indian Railways best production unit for
Environment Management Award in the year 2018-19. 9. RWF also received IGBC, Green Building Platinum Rating for its administrative building in the Nov-2018.
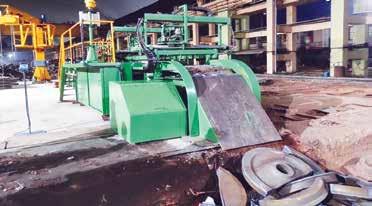
Innovative
sedimentation and Filtration tanks
y Sedimentation and Filtration tanks are designed such that Rain Water from Strom Water Drains near Pump
House is channelized through a series of mesh and Coarse aggregate chambers. The Clean Filtered rain water flows into pump House tank by Gravity. On a good rainy day, the system has 2.5 to 3 lakh litres Rain Water Harvesting
Potential.
automatic scrap Wheel Cutting Machine
y An automatic scrap wheel cutting machine was designed, fabricated and manufactured inhouse in RWF, and commissioned in the month of Jan 2021. Automation of process has helped to provide safer and cleaner working environment for staff, besides improving efficiency with reduced manpower requirement for cutting process.
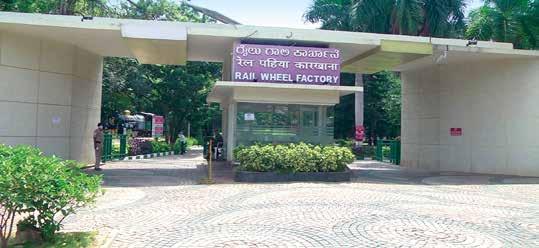
Energy Efficiency
y Efforts by RWF led to reduction in Specific Energy
Consumption in wheel production by about 6% in the last three years. y Switched over to VVVFD drives in all major motor driven machines. Squirrel cage motors replaced by energy efficient induction motors. y All heating and heat treatment furnaces of wheel Shop and
Axle Shop converted from HSD to PNG with 32% direct reduction in carbon Emission and 3 % indirect reduction of
CO2 due to transport reduction of HSD trucks in 2021 as compared to 2017. y As a part of its effort towards renewal energy, RWF installed 2 MWp Solar PV system installation on-site and two 1kWp off grid type Hybrid (Solar +Wind) system Solar water heaters provided in all quarters of its one of its two residential
Colonies. Solar street lights provided in all peripheral roads. y Through all these efforts, RWF’s carbon foot print (annual CO
2
emission) has reduced by 2000 T.
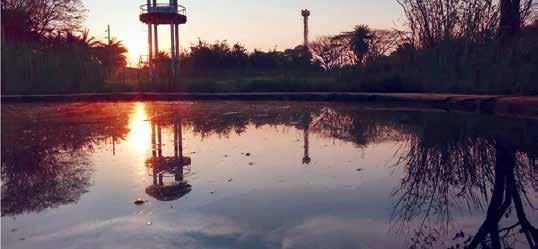
Water Conservation
y RWF has embraced Rain water Harvesting (RWH) techniques to achieve its goal of becoming self reliant on process water requirement. Both Surface runoff harvesting and Roof top harvesting have been adopted. Rain water as collected/ harnessed is proving to be more than enough to meet our daily requirement of upto 3 lakh litres of process water throughout the year. y The projects have resulted in self-sufficiency in process water requirement and RWF has stopped sourcing process water from Bangalore water and Sewage supply board. Thus about 75,000 Kl of water is saved every year- which otherwise would have been taken by RWF from BWSSB. y Work done by RWF in the field of water conservation has been given wide coverage by leading news papers of
Bangalore. y Eco-zone inside plant has been developed and rain water of almost 60% of the Plant area are being channelized to eco zone. The work done by RWF will sensitise people and create awareness about water conservation. y The water of WAP kere is recharging ground water. Our
Plant is situated in densely populated area of Yelahanka. The recharging of ground water is indirectly helping localities around our plant.
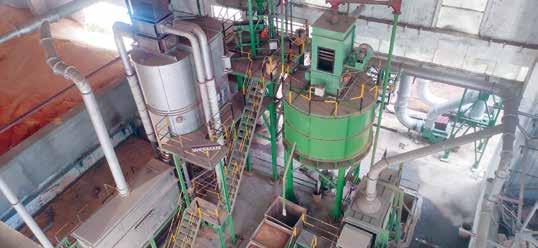
Material Conservation
RWF, being the biggest recycler of scrap (especially rejected wheels, axles, rails etc) has further taken a number of initiatives for material conservation, which besides conservation of resources, has also led to significant saving to Railway by way of cost reduction. Some of the efforts are as follows: » Reduction in MgO C Bricks consumption through reuse of reclaimed bricks for furnace lining and maintaining basicity of bath in range 2 - 2.5 Reduction in consumption of Fused silica powder, Veegum Granules etc by utilizing the left out spray solution at the week-end for next working day without draining. Usage of Graphite dust, ingate sleeves and clay graphite stopper in Furnaces instead of dumping Graphite powder generated from machining of mould blanks is re-used in Furnaces at Steel Melting Shop to manage carbon % in metal. About 250 MT/yr y All RWF products are fully Recyclable except HDPE end cover and bolts which are reusable. y Innovating ways adopted to further reduce packaging materials for wheel-sets by using alternate methods like bulk packaging.
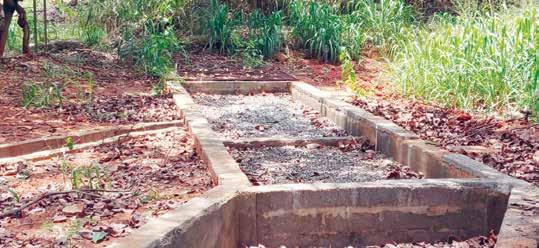
Waste management
natural resource Conservation
Foundry Sand is an important consumable in the process of wheel casting. A thermal sand reclamation plant of capacity 2MT/ hr commissioned in March’2021 to recover used baked sand. The reclamation plant operates on PNG. It recovers 90% of the sand charged. About 6600 MT of sand has been reclaimed in till November 2021. This has. y Conservation of natural resource as more than 90% of used sand is recovered and the same sand can be re-used at 10% loss each time. y Avoiding land pollution by avoiding dumping used resin coated sand into yard. y Drastic reduction in purchase of fresh sand annual cost savings. y Reduction in pollution, greenhouse gas emissions due to reduced requirement of transporting fresh sand.
Contact: mr. n.K. Barnawal, Chief Work Shop Engineer (Wheel) & Chief Environment Officer, Yelahanka, Bangalore, KARNATAKA Phone: +9108501401 | Email: cwe.wheel@rwf.railnet.gov.in