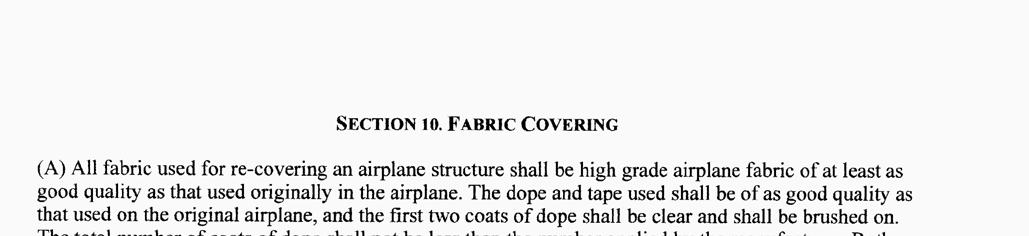
21 minute read
Light Plane Heritage
published in EAA Experimenter DECEMBER 1994
the hows and whys of aircraft tubing
by Bob W ittier EAA 1235
At EAA fly-ins of the 1950s and With a little searching, one can state-of-the-art designs. At the same 1960s, practically all the homebuilt still find and buy plans for hometime, would-be “eyeball engineers” planes were built from plans and built aircraft designed three, four, or find it steadily more difficult to find raw materials purchased from varimore decades ago. People are even aircraft design literature slanted to ous sources. Today, a steadily growbuilding Pietenpols designed more their needs and levels of education. ing percentage of the homebuilts than 60 years ago. Whatever one It becomes obvious on walkat these gatherings have been asmight think of its antiquated aping around at a major fly-in that sembled from kits. many of the people present
It is to be acknowledged are under 50 years of age. that there’s merit in kits. When builders buy a kit from Few indeed Most of these folks have had little if any contact with the a reputable company, people having much enthusiasm but scant aeronautical ex realize what a specialized and basic airplane design litera ture published between 1920 and 1940. That literature, be perience are usually assured that everything going into sophisticated cause it dealt with simpler, slower airplanes, is still useful their homebuilt aircraft is of approved aeronautical qual material aircraft today. But, we still see fewer and fewer new designs created ity. Also, builders save much time and aggravation by or steel tubing is. by modern equivalents of Ber nie Pietenpol, Ed Heath, Les dering kits from one source Long, and O.G. Corben. That instead of searching far afield is something for all of us to be for the many different materials pearance and rather heavy weight, concerned about, because it means needed to construct an airplane. the Pietenpol remains a very pracwe are drifting away from the word
On the other hand, when one tical design for enthusiasts who experimental in the name Experi buys a kit, one pays for the time and want a simple, fun plane that can mental Aircraft Association. effort someone else has put into buybe built from raw materials using The purpose of this article, thereing the material it contains, shapcommon home workshop tools. fore, is to give younger readers ing the parts, and marketing the reWhy are there no plans for upsome exposure to what went on sulting kits. Nevertheless, when we dated versions of simple sport before they were born, and to enconsider the prices of kits for even planes such as the Pietenpol, Heath courage all readers to do some serithe simpler ultralight aircraft, the Parasol, and Baby Ace? A likely anous thinking about the homebuilt thought comes that even such airswer is that today, people fortunate aircraft field. craft can seem quite costly to those enough to have training in aeronauLet’s take aircraft tubing as a who can fly only a modest number tical engineering prefer to use their good subject for discussion. We of hours per year. knowledge to produce modern, have come to take steel tubing for
Editor’s Note: The Light Plane Heritage series in EAA’s Experimenter magazine often touched on aircraft and concepts related to vintage aircraft and their history. Since many of our members have not had the opportunity to read this series, we plan on publishing those LPH articles that would be of interest to VAA members. Enjoy!—HGF
Low-cost tubing for non-aeronautical use is manufactured rapidly from strips of sheet steel called “skelp.” Skelp width is chosen to suit diameter to be made. Rollers curl it into tubular shape and electric-weld the seam automatically. Other rollers make it acceptably round and straight.
granted. We order it as matter of fact as we go shopping for groceries. We know how to cut it and weld it together into airframes, but we don’t know how to think about it because we know nothing about its background and how it’s made.
Few indeed realize what a specialized and sophisticated material aircraft steel tubing is. On one hand, it is very carefully manufactured to strict government specifications. On the other hand, the market for it is very small compared to that for other steel products. Actually, it is as much of a custom-made product as is a fine shotgun barrel or a hand-made sword.
This is reflected in the prices asked for it today. In a 1964 aircraft supplies catalog, we find that the widely used 5/8-inch diameter by 0.035-inch wall thickness size sold for 42 cents per foot. Today we find it listed at $1.79 in one supply catalog and $2.31 in another. Threequarter-inch by 0.035-inch tubing that was 46 cents in 1964 is now $1.87 and $2.38.
For the sake of spurring you to do some thinking, let’s look into wood briefly. The longerons of Pietenpols are 1 inch square in cross section. One current catalog lists a rough blank of Sitka spruce spar stock measuring 1 inch by 6 inches by 16 feet at $130. It can be sawn into five 1-inch longeron strips totaling 80 feet. This works out to 61.5 cents per foot.
Before you exclaim, “But I don’t want to build a homely Pietenpol!” think of the sleek, cantileverwinged, all-wood Jodel, Druine, Piel, Jurca, and other homebuilt designs popular in Europe in the 1950-1970 period and also built from plans in North America. And, we shouldn’t forget that the FAA approves of the use of substitute woods such as Douglas fir and western hemlock, provided they meet aircraft standards of quality. Hemlock, for example, can be substituted for Sitka spruce without changes in the size of materials being used. Currently it’s being sold at a price of $2 per board foot in some parts of the country, which is significantly less than the cost of spruce. Pine is being successfully used in some modern ultralights. Look into lumberyard prices for such woods and start thinking!
Now let’s get back to steel. In olden times very useful implements were made of iron heated in burning charcoal. The iron absorbed carbon from the fuel such as to create a steely surface on that metal. By early in the 19th century Europeans had cut down so much of their forest land for fuel, lumber, and shipbuilding that they were forced to look to coal and iron.
This was especially true of the island-dwelling British, who depended on merchant and naval ships for survival. The rapid growth of railroads from 1825 onward required the building of many new bridges able to stand the weight and pounding of trains. Mortar crumbled in stonework bridges,
Seamless steel tubing is made by feeding a red-hot bar through a roller-and-mandrel process that pierces it. This thick, rough tube is then repeatedly pulled through a die-and-mandrel process that colddraws it into finished tubing. These sketches convey the general idea; modern production machines are very sophisticated.
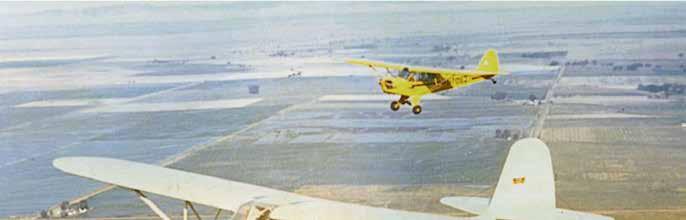
Streamline and square aircraft tubing is made by drawing round tubing through suitably shaped dies. Rounded trailing edge of streamlined tubing is necessary to avoid bending the metal to too sharp a radius. In addition to having better streamline form, frontal area is also reduced. For example, 2-inch diameter round tubing makes streamline tubing only 1.143 inches on its short axis. Drawing at top right shows how round tubing was sometimes streamlined with light wood fairing. Can any readers tell us what kind of machine, cutters, and techniques airplane factories used to shape the wood as shown? Lower right—some lightplanes have used less-expensive streamlined wing strut tubing made with an electric welding process; note more pointed trailing edge.
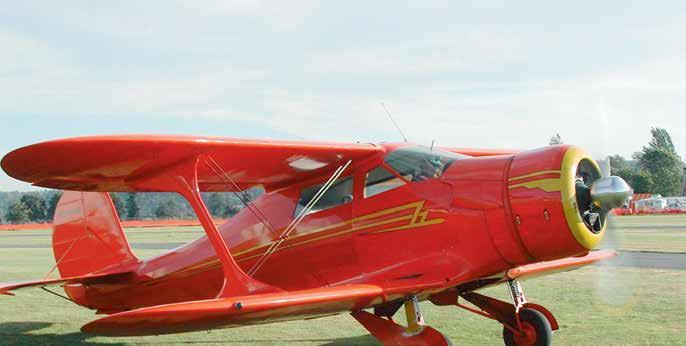
and joints in wooden ones loosened under the shaking. Wooden bridges also caught fire or rotted, so bridge builders turned to metal.
At first cast iron was used, that being the only metal available in large quantities. Because it was weak in tension, bridge builders used the principle of the arch to design bridges in which the iron was under compression. As train weights and speeds increased, they turned to tougher wrought iron to make bridges that were both stronger and longer. This led them to switch from arch-type bridges to ones built of truss work. In these bridges, some members were under compression while others were under tension.
The vastness of North America spurred interest in railroads here, too. On both sides of the Atlantic men who were very well-trained in mathematics developed methods of analyzing stresses in truss work.
For example, in 1847 the mathematician Squire Whipple of Utica, New York, published a book that for the first time accurately analyzed stresses in truss work. In 1858, Professor W.J.M. Rankine of the University of Glasgow in Scotland published a 670-page book, Applied Mechanics, that became a 24 SEPTEMBER 2012
standard manual for engineers of all disciplines up to the 1920s.
All of this is of interest to airplane people today because we use the types of truss work and the methods of analyzing them originated by 19th century railroad bridge builders. Few books on aviation history mention this, but it’s a fact that early airplane designers had this mass of knowledge at their disposal when learning how to make airframes that were both strong and light. Some made use of it, and others didn’t.
During the 1840s the Englishman James Warren created and patented the Warren truss, which has been used for the fuselage truss work in such aircraft as the Fleet trainer, the Taylor and the Piper Cubs, and the Heath LN Parasol of the early 1930s. Also in the 1840s, American bridge designers William Howe and Thomas Pratt developed their trusses. Both were originally used in wooden bridges laced together with wrought iron tie rods. As used in bridges, the Howe truss consisted of stout upper and lower longitudinals, and of verticals with crisscrossed iron tie rods between adjoining uprights. This truss was practically universal in wood-andwire aircraft from 1903 through World War I and into the early 1920s. In fuselages, we call the upper and lower longitudinal members longerons, and the vertical and horizontal cross-members simply struts or tubes.
The introduction in 1856 of the Bessemer process for producing steel in large quantities opened the gates to the use of this muchstronger metal in a wide variety of applications and made possible tall but strong steel-framed buildings, much longer bridges, and you-name-it. By 1880 it was in general use.
Steam engines freed industry from the limited number of sites where dams could be built to operate water wheels. The Industrial Revolution picked up speed with incredible swiftness.
Short lengths of tubing and piping had been made in antiquity by wrapping sheet lead around mandrels and melting the edges together.
Copper tubing began to be made in a similar way, except that the seams were sealed by brazing. Iron pipe came to be made by wrapping red-hot metal around mandrels and hammering the overlapping edges to fuse-weld them together.
It occurred to a German steelmaker, Reinhold Mannesmann,
Drawing 1 shows 1924 Lincoln Sport. Its fuselage used the Howe truss, in which the wooden parts are tied into a rigid structure by crisscrossed wires. Drawing 2 shows railroad bridges using Warren (top) and Pratt (bottom) trusses. Warren was ample for shorter spans or rivers having no marine traffic. Manner in which it hung from abutments led into the zigzag truss work. Pratt suited longer spans or rivers carrying marine traffic. Top girder could be located as high as necessary for a strong truss and to clear locomotive smokestacks, and no part hung below abutment level. Bridge designers developed methods of stress analysis later adopted for aircraft. Drawing 3 is EAA Biplane fuselage using Pratt truss. Drawing 4 is a Warren truss steel tube fuselage designed as an alternative to the Pietenpol’s original wooden fuselage.
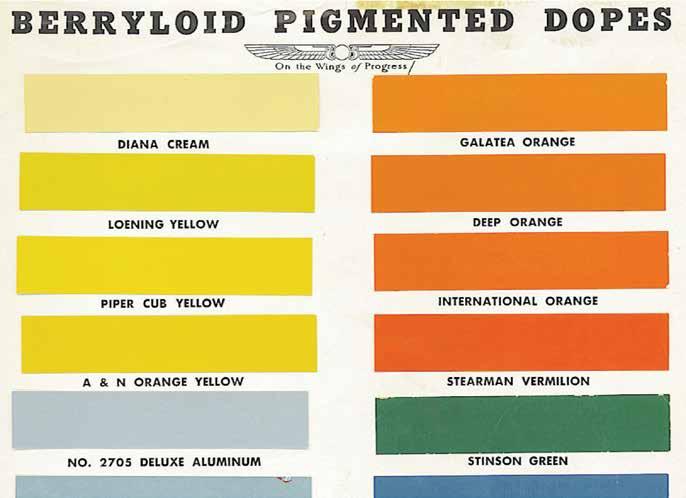
that seamless steel tubing would be much stronger and safer for use in the boilers that generated steam for engines. He thought about the problem for many years and in 1885 patented a process he developed. It made use of two steel rollers set at an angle to one another. These rollers fed a red-hot steel bar into a pointed steel mandrel that pierced it, thereby converting it into a rough, thick-walled tube. Passage through more rollers made this tube thinner and longer.
The resulting still somewhat thick-walled and rough tubes were then processed in another machine using a die-and-mandrel setup that controlled inside and outside diameters precisely, thus producing the desired wall thickness as well as smooth surfaces. This cold-working also increased the metal’s strength.
The tubing we use in aircraft construction is made this way. Making it is highly specialized and calls for much skill and care, plus frequent inspections as the process moves along. Much effort has gone into refining the technique so as to produce the strongest, safest tubing possible. It is therefore fundamentally quite labor-intensive, and this is reflected in the price.
In the past, the steel used was made with both the open-hearth and the electric furnace methods. Today the latter is used, because it uses electric current instead of fuel. The objection to the open-hearth furnace is that conducting a fuel such as gas or oil into the heating chamber can bring in impurities. Bits of material such as sand or slag that find their way into new steel can lead to flaws in finished tubing.
As the originally short, rough tubes move through the drawing process, they are inspected for embedded flakes and slivers of metal that could also become worked-in flaws. The tubes are put through acid baths to remove scale, then dried and coated with graphite or other lubricant before being put into the drawing machine.
The die and mandrel are precision made from very hard steel. The drawing machine’s moving draw-head has a jaw that grips one end of the raw tube, which is flattened for this purpose. Operators must be well-trained to do this work. For example, they must be constantly on the alert for foreign matter on the die and mandrel, which could produce scratches or grooves in the tubing.
If the feed rate is too fast, crosswise cracks from too-vigorous pulling might result. Despite the use of lubricant, dies and mandrels wear rapidly due to the high pressures involved. Government specifications for aircraft tubing allow a modest wall-thickness tolerance to allow for this. When tools become worn too much to draw tubes that
Top: 1925-1930 Travel Air fuselages like this were made of steel tubing in a manner pioneered by Fokker. Forward two bays used the Pratt truss. Welded-in diagonal tubes resisted loosening under engine and landing gear forces. Remainder of the bays used the Howe truss. Welding was simplified and the crisscrossed wires were lighter than the thick 1025 steel tubing used up forward. Lower left: Fokker method used quadrants of smalldiameter tubing as attach points. Simple to weld to the primary structure, and easy to lace brace wires into place. Center: These quadrants did have shortcomings. The welds were under tension, not good practice, and the quadrants could distort under heavy load. Right: Improved design puts the welds more under shear, washers minimize distortion, and this type of lug readily accepts the fork ends of turnbuckles.
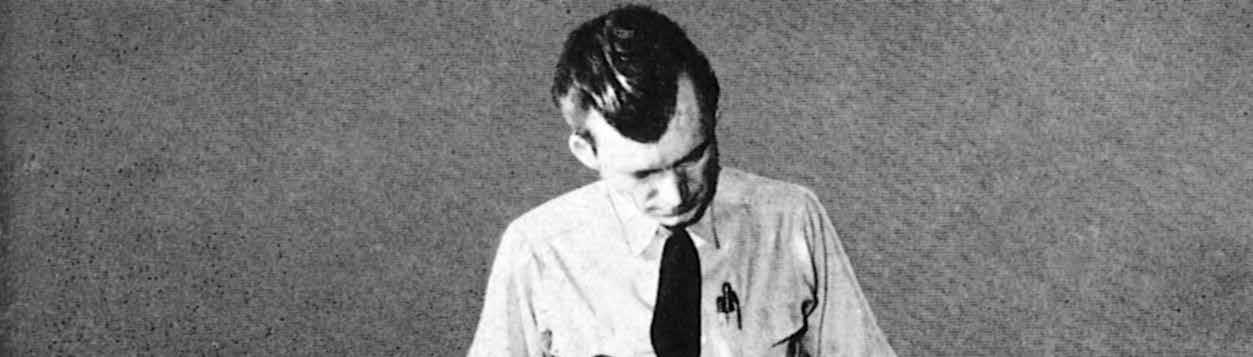
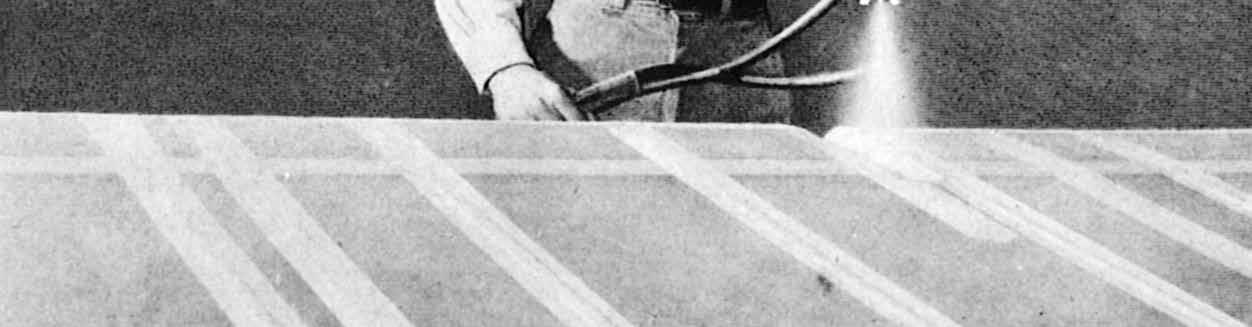
are within these tolerances, they are reworked and used to produce tubing of another size.
Because cold-drawing hardens the steel, it has to be annealed before passing through each subsequent draw-down. The smaller, thinner-walled sizes of tubing of the sizes used in aircraft may go through the drawing-down process a score of times before reaching finished size. As we said, making aircraft tubing is a laborintensive process.
Because the mandrel pushes its point through the inside of a tube, there is no way to control its travel precisely. If it wanders, a tube can result that has unequal wall thickness at various points. Because thin spots can burn through exasperatingly easily when tubing is being welded, and can collapse easily under stress when in service, test spec26 SEPTEMBER 2012
imens are taken out of each batch of tubes for inspection. Some specimens are also pull-tested. A short length of defective aircraft tubing can kill people, so thorough inspection is essential. Quality control is therefore emphasized. Tubes used for testing can’t be sold and don’t bring a profit.
The cold-drawing process tends to produce slightly bowed tubes. So the straightness of each tube is checked by experienced personnel by rolling it on a very true flat surface. Thicker tubing can stand passage through a straightening machine, but thinner tubing of the kind used in small aircraft construction is more delicate and so is carefully hand-straightened by skilled personnel.
Streamlined and square seamless tubing is made by drawing round tubing through suitably shaped dies. The additional processing thus involved increases the cost of these shapes. Several years ago the only firm making streamline tubing in the United States had so much trouble with cracks occurring at the trailing edge of streamlined tubing that it purchased sophisticated testing equipment. Its cost had to be added to the selling price of this product.
Low-cost tubing used in a vast array of non-aeronautical applications is made in a different way. Drums containing long, narrow strips of sheet metal are loaded into a forming machine. This material is called “skelp,” and its width is chosen to suit the diameter of tubing to be made. Grooved rollers bend the flat skelp into tubular form and electric-weld the seam. More rollers shape the tubing into a perfectly round form and straighten it.
Because skelp is a form of sheet metal produced in volume by rolling mills, it is low in cost and quite uniform in wall thickness. Welded tubing is not used in aircraft frames because the electric weld line is assumed to be a weak place where compression loads could readily cause it to buckle. Its use for aircraft has been investigated in the past, but so far it is still not accepted. However, automatic electric welding equipment has undergone continuous improvement and might be worth investigating. Study the nice weld lines in modern electric conduit and auto exhaust piping.
One can’t say anything about airplanes without someone interjecting, “Yes, but…!” Welded tubing actually has been used in aircraft. Early models of the Taylor and Piper Cub used streamlined wing strut material made by welding. Suitable strips of sheet steel were presumably bent around some sort of form to produce the streamline shape, and welded together at the trailing edge. Look at the struts of older Cubs in museums and at fly-ins and you will see that instead of being rounded as with seamless tubing, the trailing edge is flat and about 1/8-inch wide.
This tubing was made 50 and 60 years ago by firms in Michigan and Ohio, but our efforts to trace them or their successors have been fruitless. We showed a Taylor Cub E-2 strut to friends having mechanical and engineering backgrounds, and they agreed that electric welding must have been used. The heat of gas welding would have caused great difficulty with warping.
The reason why welded tubing was acceptable in this application is that the streamline section is quite rigid on its longitudinal axis, and jury struts stiffened the wing struts on the section’s shorter transverse axis by reason of being attached to them midway between their ends. It had acceptable buckling strength.
The Howe truss used in woodand-wire fuselages worked, but had shortcomings. Much fussy work went into making the many steel fittings needed to tie together the longerons and many cross members. Bolts used to secure them in place usually required that holes be drilled through the wooden longerons, thus creating weak spots. Much patient fiddling with the turnbuckles used with the crosswires was needed to pull a fuselage frame into alignment. Engine vibration and the bumps of landing and taxiing in time loosened up the many crosswires.
A number of early builders tried steel tubing, employing the then widely used Howe truss. A welded joint where tubes came together was quicker to make, and if done properly would never loosen up. One early user of tubing was Anthony Fokker. As a youth in Holland in 1910, he became swept up in the craze for aviation. This led
Aircraft Finishing Products STC’d for Certified Aircraft
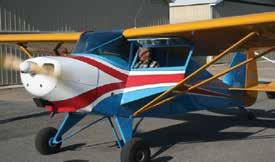
Safe for You, Safe for the World, Safe for Your Airplane
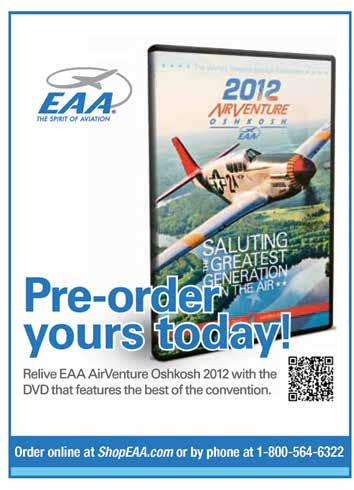
For Certifi ed Aircraft, Stewart Systems is FAA approved for use with any certifi ed fabric. Superfl ite, Ceconite or Polyfi ber EPA Compliant Non-Hazardous Non-Flammable Stewart Aircraft Finishing Systems 5500 Sullivan St., Cashmere, WA 98815 1-888-356-7659 • (1-888-EKO-POLY) www.stewartsystems.aero

him to go to Germany to take an aviation course. In time he gravitated to Johannisthal airfield outside Berlin, then a hotbed of aviation activity.
There he met a welder, Reinhold Platz, and in 1912 the two built a steel-tube fuselage for a new Fokker monoplane. Since Mannesmann had devised a way to make seamless tubing, we can guess that they used it and that it was some kind of weldable mild steel. A crosssectional drawing sent to us by the Museum fur Verkehr und Technik in Berlin shows that during World War I the Germans were using seamless steel tubing for airplane struts. An advertisement in Jane’s All the World’s Aircraft for 1918 shows the British were also making round and streamline tubing. One book indicates the reason we see less tubing in British World War I aircraft is that the alloys they then had did not weld acceptably.
When war broke out in 1914, everyone thought it would be over in a few months. The tiny Fokker shop being much in need of business, Fokker demonstrated his monoplane to the German army and got a modest order.
Then it became evident that the war showed signs of dragging on. One thing led to another, and by 1918 and at the ripe age of 28, Fokker had become a major aircraft manufacturer. However, he had scant loyalty to the German nation and when the war ended managed to smuggle many of his formidable D.VII biplanes to Holland. Some found their way to the United States, and the Army Air Service research facility at McCook Field in Ohio studied them thoroughly both in the air and on the ground.
Researchers realized the superiority of the Fokker type of welded steel tube fuselage. Accordingly they had one U.S. aircraft manufacturer build several fuselages of this material to replace the wooden ones of some of their de Havilland 4 biplanes. These fuselages proved to be lighter, stron28 SEPTEMBER 2012
ger, and more durable.
The Army therefore obtained a supply of aircraft grade tubing and parceled it out to various aircraft manufacturers to use in new designs. And this is how American designers and builders came to adopt welded steel tubing construction. A tip of the hat to Tony Fokker!
It appears that the now-standard SAE 4130 chrome molybdenum tubing did not come into general use until about 1926 to 1928. Around 1925 various manufacturers of civilian airplanes started making welded steel tube fuselages using, for the most part, a general purpose type of mechanical tubing bearing the 1025 specification number. We call it carbon steel to distinguish it from chromoly.
Where the longerons of a fuselage made of 4130 might be 3/4- inch in diameter and have a wall thickness of 0.035 inch, one made of the weaker 1025 would use stock of 7/8-inch diameter and 0.049-inch wall thickness. Use of 4130 made possible a significant reduction in weight. However, the 1025 had advantages for its time. The greater wall thickness made it easier for inexperienced welders to handle, for there was less tendency for hot spots to burn through. Barnstormers found it reasonably easy to find wherever they might be, to make repairs after crackups. The wall thickness afforded good resistance to rusting-through. This is why many 1920s airplanes have survived to be restored and displayed at fly-ins.
Built early in 1927, Lindbergh’s Spirit of St. Louis used 1020 tubing for its fuselage and the wing struts. Taylor and Piper Cubs used 4130 tubing for the more highly stressed fuselage members such as the longerons, and 1025 for lower-stressed members such as diagonals and cross tubes, particularly aft of the cockpit area.
The introduction of 4130 at a time when 1025 was in wide use created a problem for factories. It was easy for someone to mistakenly use a length of weaker 1025 in a location where 4130 was called for. Because manufacturing processes are the same for both grades, 1025 didn’t cost all that much less than 4130, and it passed from the scene. It saved a worthwhile number of dollars only when a large number of planes were being made. Today we use 4130 for both new construction and repair work.
The Society of Automotive Engineers (SAE) long ago devised a fournumber code for identifying the many kinds of alloy steel that have been developed for almost endless applications. The number 1025 means carbon steel (1) containing no alloying metal (0) and 0.25 percent (25) of carbon. The number 4130 indicates a steel containing molybdenum to enhance the homogeneity of the alloy and reduce grain size, and chromium to impart hardness, strength, and resistance to wear and corrosion.
Finished 4130 aircraft tubing is heated to between 1,500 and 1,600 degrees F to “normalize” it. This relieves internal strain and refines the grain structure. This process gives aircraft tubing its characteristic blue-black color.
Next month we’ll have more to say about steel tubing, and take up the subjects of aluminum tubing and welding.