
9 minute read
ACHTERGROND
De chemische industrie staat aan de basis van zo’n beetje alle dagelijkse producten, waaronder kunststoffen. Aan het begin van die keten staan krakers. 1e deel van een serie over de krakers in Nederland.
DOW TERNEUZEN VERDUURZAAMT OP DIVERSE GEBIEDEN DE BESTE KRAKER VAN EUROPA
Advertisement
Krakers
De drie stoomkrakers van Dow Terneuzen staan aan het begin van een keten met aan het einde onder meer kunststoffen voor allerlei toepassingen. Voor het terugdringen van de CO2-uitstoot ziet technology innovation manager Kees Biesheuvel elektrificatie en circulariteit als de meest toekomstbestendige oplossingen. Tekst: Igor Znidarsic
Voor de leken onder ons wil Kees Biesheuvel meteen maar een veel voorkomend misverstand uit de weg ruimen: “Er zijn twee soorten krakers. Ze worden allebei kraker genoemd, maar het zijn fundamenteel andere technologieën en installaties.” Aan de ene kant is er de FCC-kraker (fluid catalytic cracker), waarmee een raffinaderij de zwaardere koolwaterstoffen uit ruwe aardolie met behulp van een katalysator en waterstof omzet in lichtere koolwaterstoffen, zoals paraffine, kerosine, benzine en nafta. Aan de andere kant is er de LHC-kraker (light hydro carbons), doorgaans stoomkraker genoemd, die nafta met behulp van hete stoom (rond 850 °C) omzet in etheen (ethyleen), propeen (propyleen) en butadieen, de zogeheten olefinen. Bij Dow in Terneuzen, waar Biesheuvel technology innovation manager is, staan drie van dergelijke stoomkrakers. De lange koolwaterstoffen uit de nafta met een enkele binding tussen de koolstofatomen worden er omgezet in korte onverzadigde koolwaterstoffen met een dubbele binding. “Die dubbele binding maakt ze een beetje instabiel”, legt Biesheuvel uit. “Ze willen als het ware nog wat, en dat maakt ze geschikt als grondstof voor de chemische industrie.”
Hoe staan die drie krakers er anno 2020 voor? Biesheuvel: “Stoomkraken is een oude technologie, die grotendeels uitontwikkeld is. We zijn steeds op zoek naar verbeteringen, binnen de ruimte die de installaties bieden, maar je loopt op een gegeven moment tegen een grens op. Twee krakers stammen uit begin jaren 70, net als de meeste krakers in Nederland. Ze zijn in de loop der jaren steeds energiezuiniger gemaakt, voor zover mogelijk, maar de basis is niet aangepast. Bij kraker 2 is onder meer in 2000 een nieuwe fornuizensectie geplaatst, die beter energetisch geïntegreerd is en daardoor efficiënter is. In de jaren 90 is er een doorbraak geweest in de technologie van de volgorde waarin je de producten scheidt, en die hebben we kunnen implementeren in kraker 3, die in 2000 is gebouwd. Het is de nieuwste en meest up-to-date kraker in
Europa en daarmee de ETS-benchmark. Maar het gaat niet alleen om energie- en CO2-reductie, ook NOxreductie is belangrijk. Daar hebben wij veel aandacht aan besteed de afgelopen jaren, met steeds upgrades naar de laatste stand van de techniek.”
De grondstof is nafta, waar komt die vandaan? “In Europa is nafta de meest gebruikte voeding voor stoomkrakers. In de VS is dat sinds de schalierevolutie ethaan. De nafta die wij gebruiken komt per schip aan in Terneuzen, van raffinaderijen in bijvoorbeeld het Midden-Oosten, de Botlek of Antwerpen, maar kan ook afkomstig zijn van Zeeland Refinery, al naar gelang de kwaliteit en de prijs op dat moment.”
Hoe verlopen vervolgstappen in het proces? “Een kraker staat nooit op zichzelf, maar is het begin van een geïntegreerd chemisch complex, waarbij de geproduceerde grondstoffen verderop in de locatie verwerkt worden tot plastics of andere chemische bouwblokken. Uit de nafta maken we behalve olefinen ook de cyclische verbindingen benzeen, tolueen en xyleen. Die worden daarna verder verwerkt, niet alleen door Dow maar ook door de op de site aanwezige bedrijven Trinseo, dat plastics, latex en synthetisch rubber produceert, en Olin, dat epoxy maakt. Een aantal kleinere producten worden niet op de site verwerkt maar als halffabricaat doorverkocht. Je kan zo’n site zien als een organisme, met de fabrieken als de organen. Ze hebben elkaar nodig en je kunt er niet zomaar eentje tussenuit halen, want dan overleven de andere niet, omdat ze een groot nadeel krijgen ten opzichte van wel geïntegreerde locaties.”
Een kraker stoot veel CO2 uit. Wat doet Dow Terneuzen om dat te verminderen? “Bij het kraken van nafta komt methaan vrij. Dat zetten wij in als energiebron voor het productieproces, en daarbij komt CO2 vrij. Om die CO2-uitstoot te reduceren onderzoeken we samen met Shell de toepassing van een andere bron van energie: elektriciteit. Dat zien wij
Kees Biesheuvel: ‘Wij zijn een onmisbaar deel van de oplossing.’
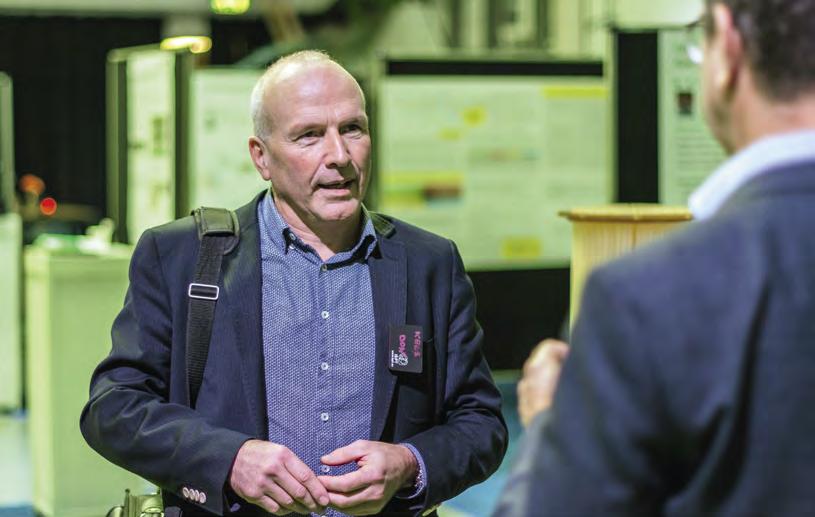
als de structurele oplossing voor de lange termijn, omdat je daarmee niet achteraf CO2 afvangt maar voorkomt dat CO2 ontstaat. CO2 afvangen is een dure exercitie met blijvende kosten, die nooit een goede businesscase kan worden. Elektrificatie is een veel toekomstbestendigere oplossing. Maar de technologische ontwikkeling van een elektrisch fornuis kost tijd, het moet bedacht en ontwikkeld worden en getest. We hebben een bepaalde robuustheid en voorspelbaarheid van de technologie nodig. En het moet passen in de onderhoudscycli – tussen de 6 en de 9 jaar – van krakers. De verwachting is dat tussen 2025 en 2030 de ombouw van bestaande en implementatie van de meest geavanceerde nieuwe technologie zal plaatsvinden. Eerder achten wij niet haalbaar. Wij gebruiken nu een soort aardgas, synthetisch gevormde methaan, qua energieeenheid de schoonste van de fossiele energiebronnen. Om dat te vervangen zou je moeten wachten tot het aanbod van elektriciteit groen genoeg is. Die omslag komt in 2030. Voor die tijd heeft het geen zin om op elektriciteit over te stappen. Stel je zou de technologie – een elektrische kraker – nu al hebben, dan zou het vanwege onvoldoende groene elektriciteit weinig effect hebben op CO2-reductie.”
Speelt biobased feedstock nog een rol bij de verduurzaming? “Er zijn biobased feedstocks beschikbaar die lijken op nafta, zoals een bepaalde olie, een bijproduct uit de papierindustrie. De basis daarvan is de hars uit de bomen. We gebruiken dat, sommige klanten vragen er ook om, maar het is zeer onwaarschijnlijk dat het volledig onze huidige feedstock zal vervangen, omdat het maar beperkt beschikbaar is. Waar we meer op inzetten is chemische plasticrecycling, waarbij je plastic via pyrolyse weer terugbrengt tot de oorspronkelijke primaire vorm. Je begint dan weer van voren af aan met een nafta-equivalent.”
Krakers
Is daarmee uiteindelijk volledige vervanging van de fossiele nafta mogelijk? “Nee. Ten eerste komt niet alle plastic terug. Het streven is 30 procent mechanisch en nog eens 30 procent chemisch recyclen. Dan kom je op 60 tot 70 procent van het plastic die gerecycled kan worden. Ten tweede zijn die processen geen volledig gesloten koolstofketen. Je houdt altijd een deel over dat voor ons onbruikbaar is. Die verliezen zul je moeten aanvullen. Daarnaast moet de grondstof die je in een pyrolyse-installatie stopt aan bepaalde kwaliteiten voldoen, want aan de kwaliteit die nodig is voor een naftakraker zijn strenge voorwaarden gesteld. Er is een grens aan hoeveel ongewenste componenten een naftakraker kan verwerken.”
Dow is ook bezig koolstof uit de rookgassen van de staalindustrie te gebruiken. “De circulariteit van koolstof zal een grote rol gaan spelen, en dan met name koolstof die terugkomt uit plastics en uit bijvoorbeeld staalgas, dat vrijkomt bij de productie van staal. In het Steel to Chemicals-project onderzoeken wij met staalproducenten ArcelorMittal in Gent en Tata Steel in IJmuiden de omvorming van de CO en CO2 die vrijkomt bij de staalproductie met waterstof tot synthetische nafta. In 2019 is bij ArcelorMittal de eerste van twee proeffabrieken gebouwd (de eerste is voor het opzuiveren van het gas en de tweede voor het omzetten daarvan in nafta). Om te onderzoeken of de methode ook geschikt is voor de gassen van Tata Steel verhuist de proeffabriek later naar IJmuiden. De uitdaging is niet alleen technisch maar zeker ook economisch. Want bij 100 dollar per vat olie kan er heel veel, maar bij een te lage olieprijs kan er eigenlijk niks meer. Je kunt dan niet concurreren met andere routes, of dat nou plasticrecycling is of Steel to Chemicals. Die routes vragen extra stappen en daarmee extra investeringen. Het kost gewoon meer en bij een superlage olieprijs haalt de businesscase het niet. Alle technologie wordt op een gegeven moment achterhaald door een vervangende doorbraaktechnologie. Dat gaat ook met de traditionele krakers gebeuren. De vraag is alleen wanneer en of dat op een verstandige manier zal gebeuren. Dergelijke installaties gaan 50, 60 of 70 jaar mee. Daarom kunnen we veel beter investeren in iets dat toekomstbestendig is voor de komende 60 jaar – elektrisch kraken – en de komende 10 jaar gebruiken om dat uit te ontwikkelen, dan dat we dingen gaan doen voor de komende 10 jaar zonder naar de situatie na 2030 te kijken.”
Daarmee komen we vanzelf bij het Klimaatakkoord. “Dat is geen akkoord dat is gesloten met de industrie en de maatschappij, maar een akkoord tussen politieke partijen. Er is niet gekeken naar wat de industrie en de maatschappij ervan vinden, maar naar wat de partijen in de huidige coalitie haalbaar vinden. Dat gaat voorbij aan de technische haalbaarheid en de technische tijdslijn. De regelgeving die nu wordt opgetuigd is niet OVER DOW CHEMICAL Dow Chemical’s portfolio van geavanceerde materialen, industriele tussenproducten en kunststofactiviteiten levert een breed scala aan gedifferentieerde, op technologie gebaseerde producten en oplossingen voor klanten in snelgroeiende markten, zoals verpakkingen, infrastructuur en consumer care. Dow heeft 113 productielocaties in 31 landen en biedt werk aan ongeveer 37.000 mensen wereldwijd. Sinds 1955 is het Amerikaanse Dow ook actief in de Benelux. Het bedrijf telt ongeveer 4000 werknemers op 8 belangrijke locaties in Nederland (Terneuzen, Delfzijl en Dordrecht) en in België (Antwerpen, Brussel, Tertre, Zwijndrecht en, sinds 2016, Seneffe). In Terneuzen is Dow met 17 fabrieken de op één na grootste productielocatie van Dow wereldwijd. In het internationaal Research & Development Center werken specialisten aan innovaties binnen en buiten Dow. Ook is Terneuzen hét centrale punt voor ondersteunende Dow-diensten in Europa, Midden-Oosten, Afrika en India. Samen met partners worden er innovatieve producten en duurzame oplossingen voor het milieu en de leefomgeving gecreëerd. Zo zorgt Dow ervoor dat we minder energie nodig hebben, water kunnen hergebruiken of alternatieve grondstoffen kunnen toepassen. Met ruim 3600 medewerkers met meer dan 50 nationaliteiten is Dow Terneuzen een diverse organisatie.
geschikt om bedrijven te helpen met de transitie. Je moet eerst belasting gaan betalen, geld afdragen dat eigenlijk voor innovatie nodig is, en daarna moet je ook nog gaan innoveren. Dat wordt voor de industrie een lastige opgave. Ik snap dat er veel haast is met de CO2- reductie, en ik kan me er ook volledig in vinden, maar of die haast overeenstemt met de realiteit … Er worden nu kunstmatig dingen gedaan, end of pipe-achtige oplossingen … Je kan niet verwachten dat je een technologie die zich 70 jaar lang doorontwikkeld heeft binnen een paar jaar kunt vervangen. We hebben tijd nodig om de technologie uit te vinden en te kunnen implementeren. Alleen dan krijg je iets dat toekomstbestendig is en daarna ook 70 jaar of langer meegaat.”
En dat plastic ‘duurzaam’ en daarmee populairder maakt. “De publieke opinie is nu dat plastic per definitie slecht is. Natuurlijk zijn er voorbeelden waar je kunt zeggen: daar had je beter geen plastic kunnen gebruiken. Maar dat zijn de uitzonderingen. Nu wordt van de uitzondering de regel gemaakt. De huidige coronacrisis laat echter zien dat het toch wel prettig is dat we mondkapjes en infuuszakken kunnen maken. Wij zijn ook geen voorstander van plastic in rivieren en oceanen. We moeten daarom zorgen dat het plastic weer terugkomt bij ons, als grondstof. Daarom zijn we bezig met circulariteit. Wij zijn een onmisbaar deel van de oplossing.” p