BECOME A MASTER OF SAFETY TRAINING
Take Your Safety Training
From Good to Great
Lack of safety training is often cited as the reason behind accidents and fatalities. Part of the problem could be how the training is being delivered and how much vital information is being passed from trainers to workers.
Improve your training skills, discover the principles that o er maximum impact, and learn the secrets of instruction for relevance and results by downloading the How to Become a Master of Safety Training guide today.
Anthony Towey, Director, OSHA Training Institute
By Lawrence P. Halprin, Ch.E., J.D., M.B.A. Finance, Partner, Keller & Heckman LLP
BySharon Lipinski, CEO, Habit Mastery Consulting
By Frank King, The Mental Health Comedian
Kara Apperson, Bechtel National Inc.
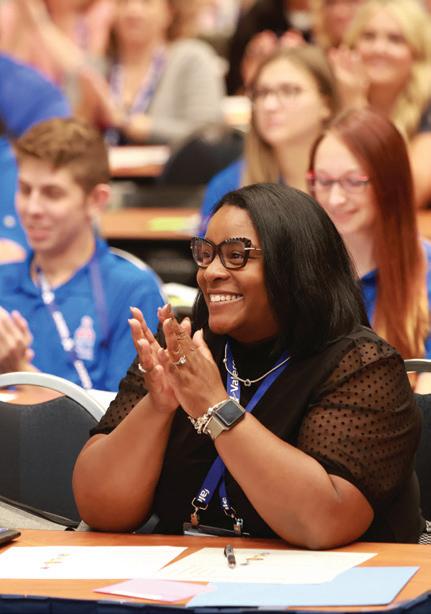
By Adele L. Abrams, Esq., ASP, CMSP, Law Office of Adele L. Abrams PC
By Dan Corcoran, Ph. D., CIH, CSP®, Columbia Southern University
A Message From the VPPPA Executive Director
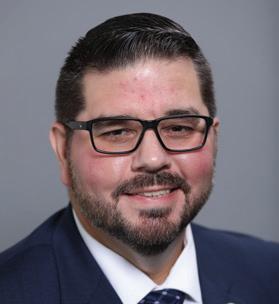
On the Job Training at Safety+
The 2022 Safety+ Symposium in Washington, D.C. is officially in the books, and I couldn’t have asked for a better—or busier—week. The entire VPPPA team—board members, staff, volunteers—worked together to create a conference that delivered the networking, learning, and fellowship that members and attendees have come to expect from our association. Everyone I met during the course of Safety+ spoke about how great it was to be back in person, learning from one another, and taking that next step forward in their personal and professional safety journeys.
Myself included.
Even though I’ve been around the EHS&S world on the construction side for almost two decades now, it’s only been since July 1 that I’ve officially been in my current position as Executive Director of VPPPA. That’s about 7 weeks from my first day to the Opening General Session. To say that Safety+ was on-the-job training, even with my background, would be an understatement.
Everyone I met during the course of Safety+ spoke about how great it was to be back in person, learning from one another, and taking that next step forward in their personal and professional safety journeys.
Being familiar with VPPPA was certainly helpful, but nothing can equate to the experience of meeting and engaging in-person with the members and attendees, and hearing firsthand what VPP, VPPPA, and collaborative safety & health culture mean to our association’s—and our profession’s—mission. The entire week reinforced my passion—our passion—for our shared, singular goal: to send every worker home in the same, or better, condition than which they arrived on the job. And, like our Safety+ attendees, I left Washington, D.C. armed with the information and knowledge to continue working toward that goal.
Now the work begins.
I joined VPPPA because of my passion for workplace safety, health, and sustainability (the other “S” in EHS&S), but also because of what, and who, VPPPA represents—the very best of the best when it comes to EHS&S people, processes, and performance. Our association truly is the premier global safety and health organization—where worldclass safety comes to evolve. Coming from construction, I’ve seen how VPP transforms safety cultures to unlock the potential of the labor, management, and regulatory collaborative environment and create the conditions for long-term success.
VPPPA has that same potential.
Much like our members, VPPPA is on its own continuous improvement journey. Our mission applies beyond VPP itself, to companies and sites small and large. Our association is uniquely positioned to harness the collective knowledge of our members on what it takes to achieve safety excellence and help others along their journey. We have the opportunity to develop the next generation of safety & health leaders using the principles of VPP and outstanding performance as our foundation. Most importantly, we have the responsibility to engage and educate industry, so that others need not experience the tragic, catastrophic moments that, sadly, form the basis of many of our “safety why” stories.
Our shared journey is one of continuous, incremental improvement through education, training, developing, and sharing best practices. After experiencing Safety+ together, I’m confident that we’re ready to forge ahead toward our shared goal.
Let’s get to work.
Stay safe, —Chris Williams, CAE Executive Director


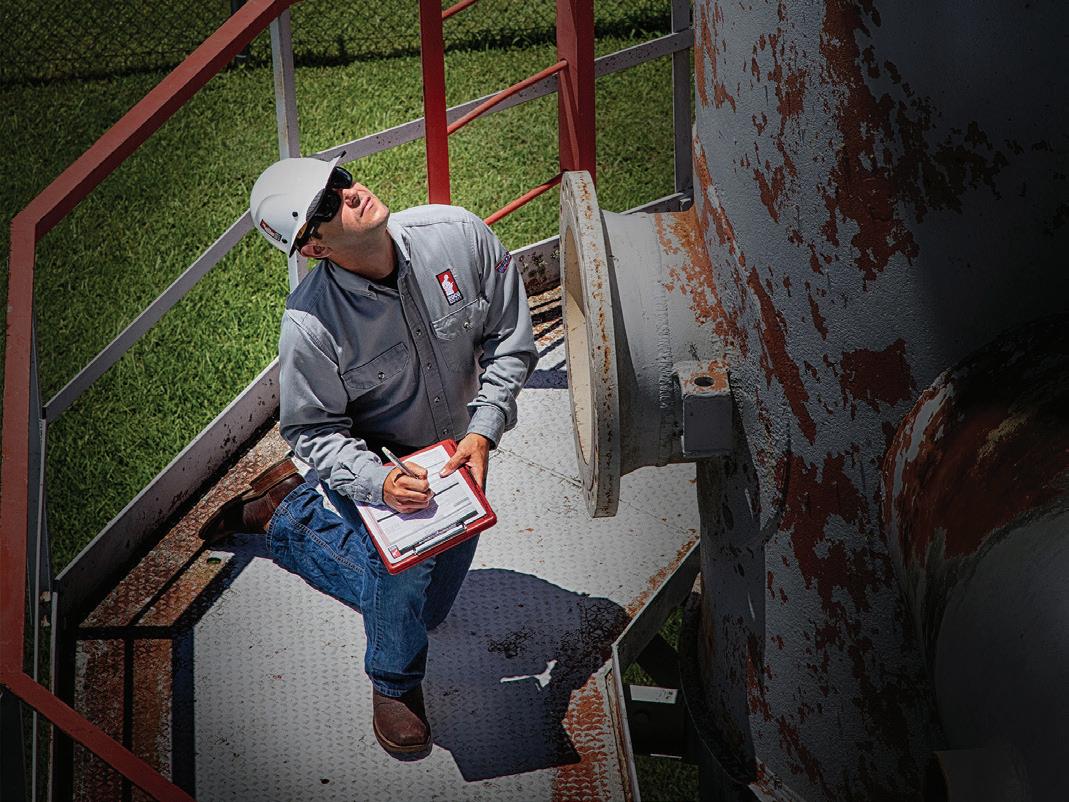
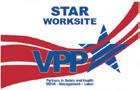
Women in Safety
VPPPA Presents…
Women in Safety
While the safety industry is still a male-dominated industry, the number of women is increasing each year. It’s important to identify and communicate the issues that women face. In each issue of the Leader, we will be including an article from a prominent woman working in the safety and health industry. If you, or someone you know, would like to write for this column, please contact VPPPA at communications@ vpppa.org
By Melanie Laird Field Control Analytics Chief Strategy OfficerBuilding the Way for Women in Construction
As the chief strategy officer at Field Control Analytics (FCA), a firm dedicated to providing construction workforce data and analytics, I focus on strategic vision, planning, and forging new business relationships, including responsibility for directing execution of the company’s goals. As a female in the construction industry spanning over two decades, it was difficult for me for many years to navigate the waters in an industry heavily dominated by men. Today, the industry is still predominantly male, but the tides are turning. One explanation for this gravitational change is a massive recruiting effort needed in great part by the industry-wide shortage of skilled labor.
Since the 1920’s, women have filled workforce shortages in the United States. Currently, however, challenges produced by gaps that still exist between salaries by genders in the same positions, complications with childcare responsibilities created during COVID, and competing jobs that offer remote/flexible working environments, have made recruiting women into the construction workforce challenging.
Organizations that have been successful recruiting
women are doing several consistent practices. These organizations create safe working environments for female employees in maledominated spaces. This involves implementing inclusion policies addressing discrimination, harassment, and bullying. Companies ensure fair hiring practices by offering female applicants an equal opportunity, and these organizations select new hires based on merit and have taken steps to stop gender-biased hiring and promotion decisionmaking practices. Pay rates within these organizations are consistent regardless of gender.
Essential management traits make women desirable hires into the industry. Women are excellent communicators. Women adapt quickly in fluid situations that are common on construction sites. The ability to adapt quickly is noticeable during crisis management situations and in times when employees are forced to remain calm in stressful situations; for example, with upset clients or employees.
Scientifically, it is proven that male and female brains are equipped for different optimizations, meaning women logically solve problems differently than men. Take, for example, creating or reviewing a site logistics plan, a site-specific safety manual, or resolving a subcontractor
contract dispute. Women will bring a different approach to new ideas and ways of thinking or problem resolution. Diverse thinking drives innovation. Creating and maintaining a diversity of ideas is healthy and desirable. Avoiding group think tank mentality is equally desirable. Women introduce techniques, new methodologies, and approaches unexplored previously by male counterparts. Diversity wins.
Organizations are beginning to promote more women into supervisory and managerial positions. Often times, employees connect with and prefer female supervisors. Generally speaking, astute women leaders are assertive, well-organized, empathetic, show genuine care for subordinates, and are eager to jump into the trenches when employees require help.
As more women join our field, there will continue to be better support, inclusion, acceptance, training, and continuing education.
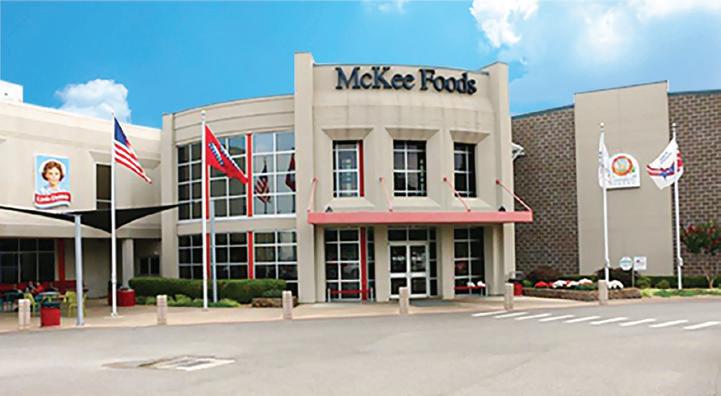
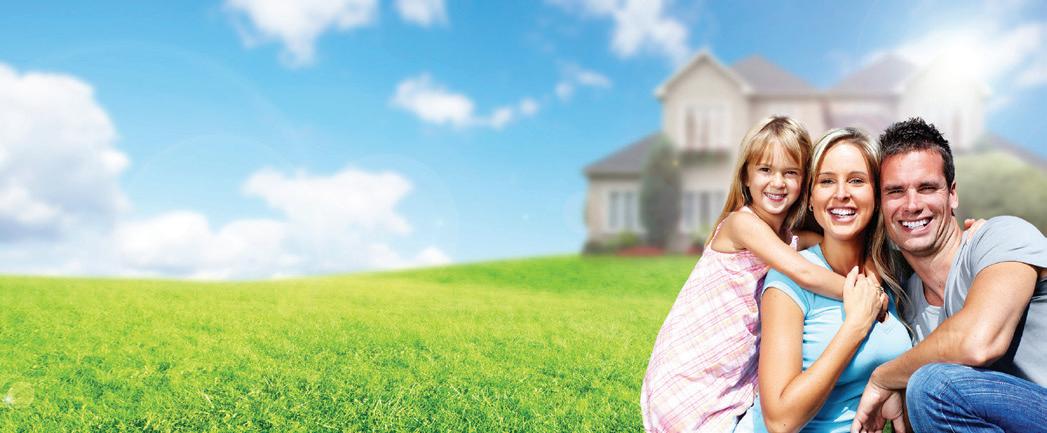
Female executives are now using their influence to inspire younger generations to follow in their footsteps. I personally started a female mentoring program at my firm in 2019. This program allows young ladies the opportunity to apply into a six-month course with mentors made up of female executives that are part of the FCA leadership team.
As more and more women enter into the construction field, construction training and properly fitted personal protective equipment (PPE) becomes significant, as does continuing education.
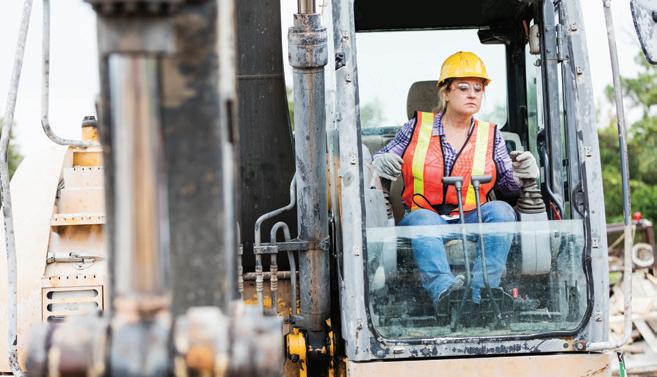
In the past, PPE was sized for men. Ill-fitting PPE leads to safety hazards that compromise personal safety. Women were more susceptible to injuries on the worksite than men due to ill-fitting PPE. Today, that has changed. Companies that supply PPE have designed and now sell products that cater to properly fitting equipment and tools for women. All employees, at a minimum,
deserve and require PPE that fit individual body measurements, is comfortable, and is not damaged from wear or defect. Women are no exception. There are many resources and inclusive groups today dedicated to woman in construction. These groups offer female training programs, and sources for female-designed PPE. My favorite groups include The National Association of Women in Construction (NAWIC) (www.nawic.org) and Professional Women in Construction (PWC) (www.pwcusa.org). These groups offer networking opportunities, support, and advocacy for women in construction. They offer education and training for women—professional and tradeswomen. Specific to health and safety, NAWIC offers information, guidance, and access to training resources on reducing and preventing exposure to ergonomic hazards, sanitation hazards, issues related to PPE, and construction workers with specific needs.
Female professionals are still nationally underrepresented, but the numbers are rising. There is a new High School in Las Vegas dedicated to construction trades opening in 2023. In my opinion, the future for women in construction has never been brighter. Roles traditionally held by men up and down the ladder are now gender fluid. What used to be considered a “man’s job” is now open to women. As more women join our field, there will continue to be better support, inclusion, acceptance, training, and continuing education.
Fifteen years ago, I was the only female on a national construction association safety and health committee. In the last six years, a national construction safety and health committee was twice chaired by women. I was lucky to be one of those women. Times are changing.
The best women I know are in construction. These women are highly intelligent, passionately driven, and dedicated to the industry. Each spearhead their organization’s efforts at recruiting women as a priority. Given the dangerous shortage of craftsmen in our industry, this should be a priority for all construction firms. Women historically have answered the call and accepted the challenge to fill these workforce shortages. The industry, led by associations like NAWIC and PWC, is answering that response by taking the necessary steps to level the playing field through inclusivity, equality, recognition, the production of quality training, and the development of educational materials catered to women.
Women in construction today are building the foundation for our daughters to design AND build the next great monuments of the world.
Scientifically it is proven that male and female brains are equipped for different optimizations, meaning women logically solve problems differently than men.
Two and a half years ago, we set a goal to make Nucor the World’s Safest Steel Company. Our team rose to the challenge, and in 2021 achieved a record year in safety for the second year in a row. As for improving yet again in 2022, the Nucor team can sum it up in just two words:
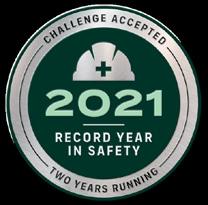
CHALLENGE ACCEPTED
Congratulations and thank you to our more than 30,000 dedicated Nucor teammates for always putting safety first.
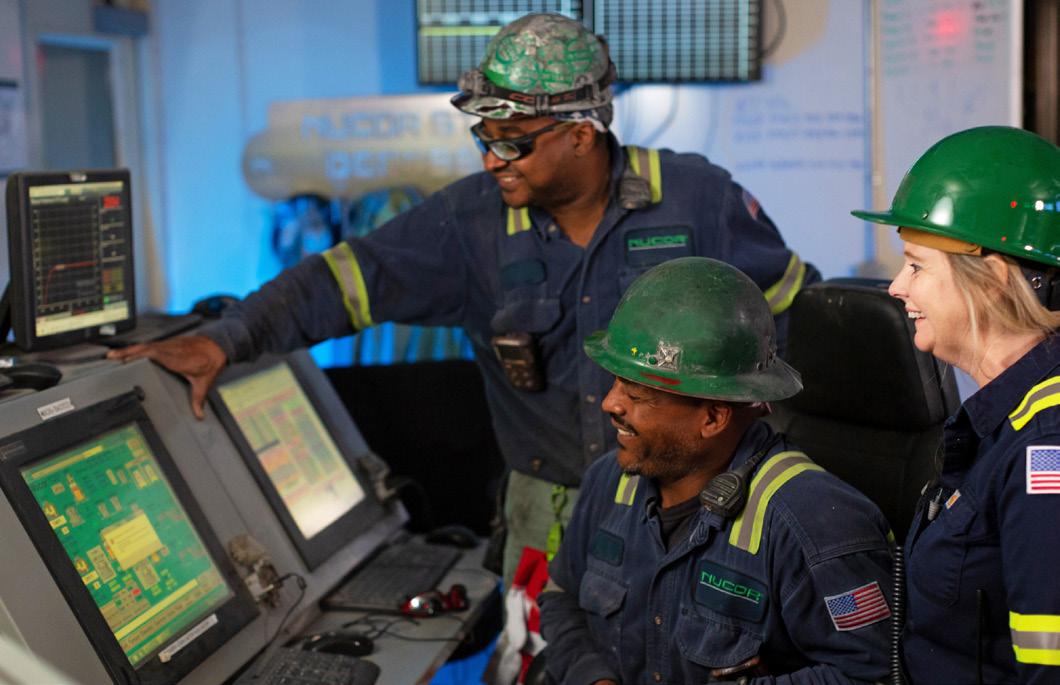
Application: The Key to Continuing Education
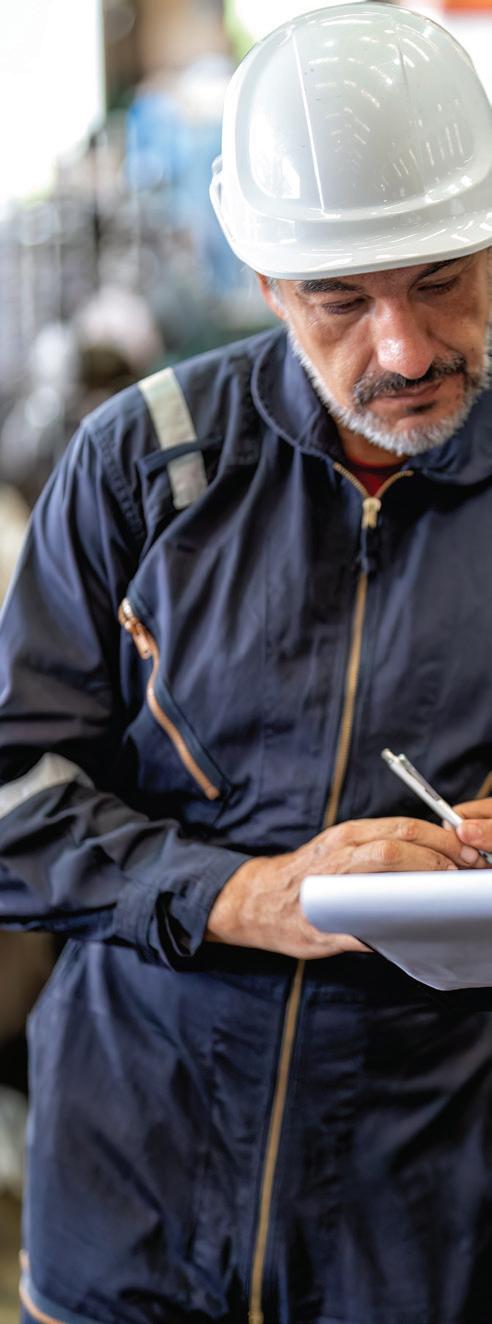
Continuing education is essential for highperforming individuals in any profession. We have all been in a training course where the trainer went through one PowerPoint presentation after another. The training could have lasted one hour, two hours, one day, or maybe more. It could have been online or in-person. While the trainer likely made key points essential to your professional development, at the end, you may have realized you learned little to nothing at all. Highly skilled trainers define this as “Death by PowerPoint.”
Adults learn by making mistakes and learning from those mistakes. They also learn from their successes after practicing what they need to know. If we tell them, show them, and let them do it themselves, we will see the transfer of knowledge and skill to the learner.

Achild’s brain is like a sponge. They hear, learn, and retain. An adult, on the other hand, needs to be engaged during the training event. Adults need to apply and practice what they are trying to learn. At the OSHA Training Institute (OTI), we use the term, “one-third instruction and two-thirds application.” The instruction portion of the lesson must be short, while the application portion of the lesson must be much longer.
Suppose a trainer is going to teach someone how to inspect a machine for safety hazards. They may provide a short overview of machine hazards using a couple of PowerPoint slides, but the learner will spend a greater portion of the lesson viewing a machine and performing the inspection.
During the inspection, the trainer will provide the learner with feedback. Adults learn by making mistakes and learning from those mistakes. They also learn from their successes after practicing what they
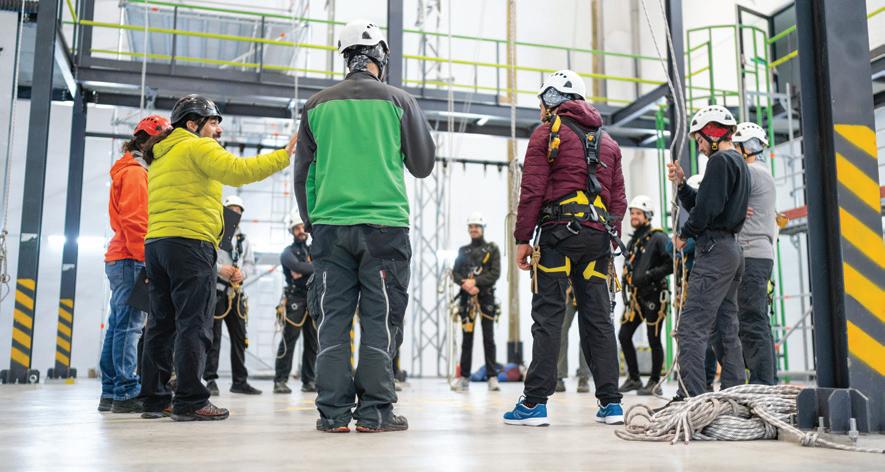
need to know. If we tell them, show them, and let them do it themselves, we will see the transfer of knowledge and skill to the learner.
How does OTI create this practice and application for our desired training events? Every trainer should use an organized method to develop training. At OTI, we use the ADDIE Model—Analyze, Design, Development, Implementation, and Evaluation.1 When the trainer begins the Design and Development phases, they must identify application and practice exercises that place the learner in an environment that aligns with the desired outcomes of the lesson objectives. Examples of application and practice include role play, group exercises, document reviews, creating documents, evaluating a piece of equipment or work environment, using Augmented Reality (AR) or Virtual Reality (VR), and gamification.
Role play allow the learner to experience a situation
replicating what they will do in the real world. The trainer must create supplemental documents and scripts with a fact set that the learner can use to prepare for the role play. After a short preparation period, the learner will play themselves during the exercise, and another person will occupy the other part. The trainer must evaluate the activity and provide feedback after the role play.
Group exercises create an environment that requires critical thinking and problemsolving. Believe it or not, learners can learn more from discussions with their fellow learners than from hearing the trainer talk for long periods of time. Adults have a short attention span. During a long lecture, the learner must continually refocus on the trainer’s words, and they may not remember a majority of what the trainer said. Role play requires the creation of documents with fact sets supporting learning outcomes. The trainer might also develop
a series of questions associated with the role play. The group is given time to solve their problem and report their answers. These activities allow the learners to teach one another within their groups and teach the entire audience when reporting out, creating the potential for additional dialogue among the audience. The trainer must facilitate these discussions and keep track of time.
Document review exercises require the development of documents with many errors or deficiencies. During the exercise, the learner must identify the mistakes or deficiencies. At the conclusion of the exercise, the trainer might evaluate the learners’ documents or use a report-out for a full group discussion on the exercise.
Document creation exercises are very useful when the objectives require learning


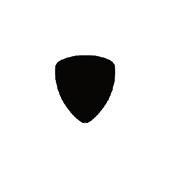
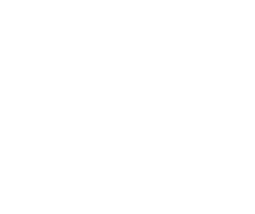
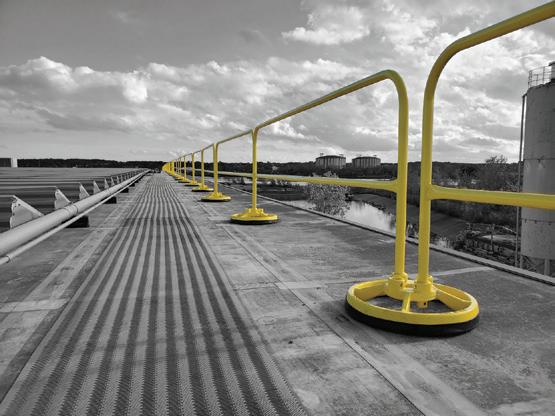

how to write something. This could be technical, such as writing a specific safety and health program. A good example is a Lockout/Tagout program. The developer will need photos depicting a specific machine or operation. They will also need information on the environment, such as equipment-specific specifications, operational procedures, and who is responsible for equipment and activities in the area. The trainer will provide the supplemental information to the learner, who must create the desired document during the exercise. The trainer will review the newly created documents and provide feedback at the end of the exercise.
Performing an actual evaluation of a piece of equipment, equipment operation, or work environment is the best form
of practice and application. The learner is placed in a similar or real environment where they are expected to apply the newly acquired knowledge or skill. If the equipment is small, the trainer will bring this equipment into the classroom for evaluation. The trainer must bring the learner to the equipment if it is too large for onsite operation. These types of activities require a great deal of logistical planning and preparation. However, handson is necessary for many skills taught during a training event. The learner can practice in a controlled environment and receive immediate feedback. Technology now allows trainers to bring learners into the work environment or operate a piece of equipment using simulators, AR, and VR. Simulators supplement hands-on operation. The learner must always
Continuing education is essential for high-performing individuals in any profession.
operate a real machine with supervision before being allowed to operate independently. Military and construction training facilities have been using simulators for many years. The learner can understand the equipment’s operation by using it in a simulated environment, which eliminates the potential for an accident while the learner is mastering the skill. Simulators assess the user’s skills in real-time while in use. They provide immediate assessment and grades after an exercise. After many hours training on a simulator, the learner can practice on a real piece of equipment.
Simulations using VR and AR are becoming a popular training method. In addition to purchasing the AR/VR equipment, the simulation must be developed and purchased based on training needs. Currently, this application development is costly but is expected to become less expensive in the future. OTI recently procured an
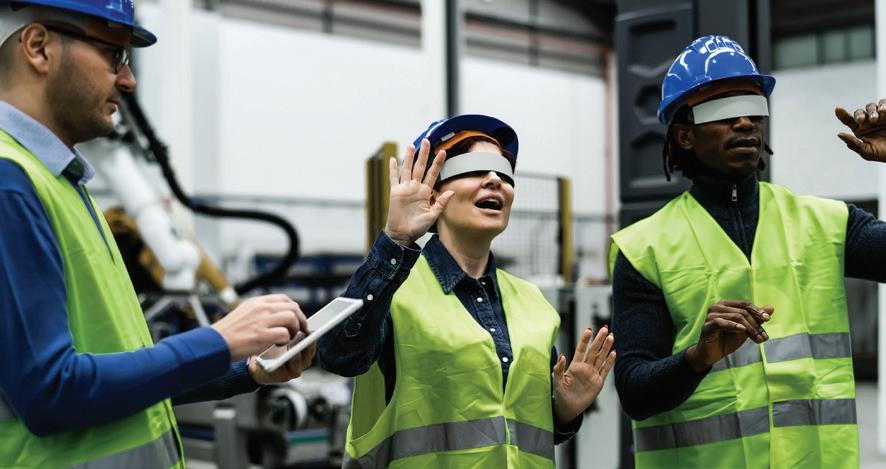
AR application and several HoloLens for training purposes. OTI worked with a developer to make a trenching and excavation inspection application for use on HoloLens headsets for trenching and excavation lessons. The instructors show 3-D images through the HoloLens and perform the entire lesson in an augmented environment. The application has various scenes with different types of trenches and multiple types of cavein protection. The instructor manipulates the scenes to add and remove equipment and create numerous types of hazardous trenches. The application is equipped with an assessment tool so the instructor can test the students at the end of the lesson.
Incorporating games into your lesson can help learners become more engaged. There are off-the-shelf television gameshow games that are relatively inexpensive. This type of application usually requires the trainer to do some programming. The trainer
can also include the use of apps or computer games that allow the learners to compete against each other in groups or individually against the computer. OTI recently began using construction inspection computers. The learners work through the program to identify construction safety and health hazards. Each learner receives an assessment of their performance and feedback on hazards not identified during the game.
The key takeaway to educating is to engage them during a training event to help increase the likelihood of knowledge and skill transfer.
Trainers must identify ways to incorporate more application and practice into their course delivery. When learners feel engaged, they enjoy the training experience, and they learn.
ENDNOTES
1 Florida State University Center for Education and Technology, Tallahassee, Florida, initially developed the ADDIE framework in 1975: https://apps.dtic.mil/sti/ pdfs/ADA019486.pdf
Adults need to apply and practice what they are trying to learn.
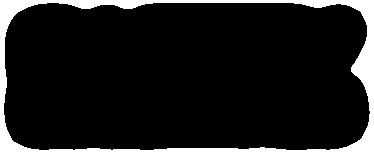
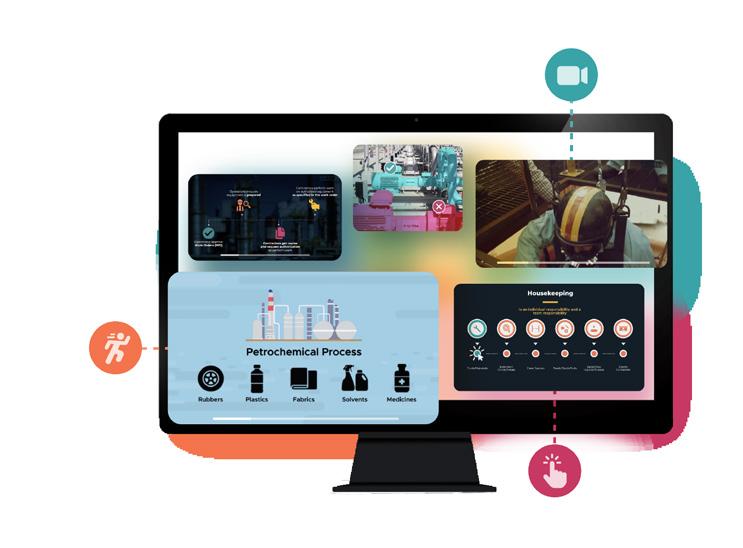
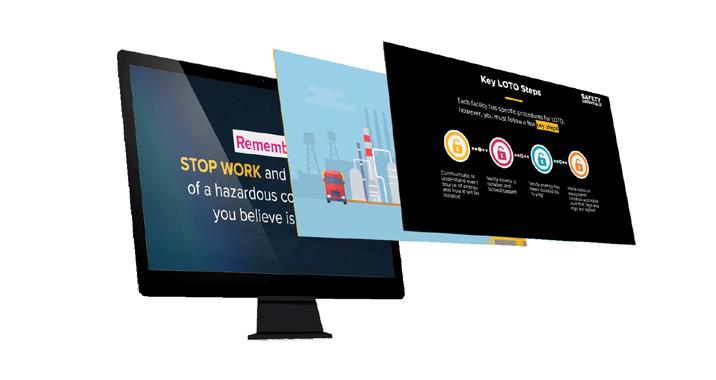
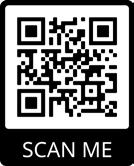
DIDN’T
TRAINING WE DO ON THAT?
Teach Your Coworkers
Learning happens best when attendees get the opportunity to practice and reflect on what they’ve learned, which makes a post training peer-to-peer learning event a powerful strategy for amplifying the effectiveness of a past training. If just a single team member has attended a training, that attendee can present the highlights to their peers. If multiple coworkers or an entire team attended the same training, assign different parts among groups or individuals who can then present and teach on their assigned content.
Ask attendees to review the training materials which might include the training manual, their notes, job aids, and a bibliography of additional sources of information. After reviewing those materials, coworkers can present to their peers on the key concepts.
By Sharon Lipinski, CEO, Habit Mastery Consulting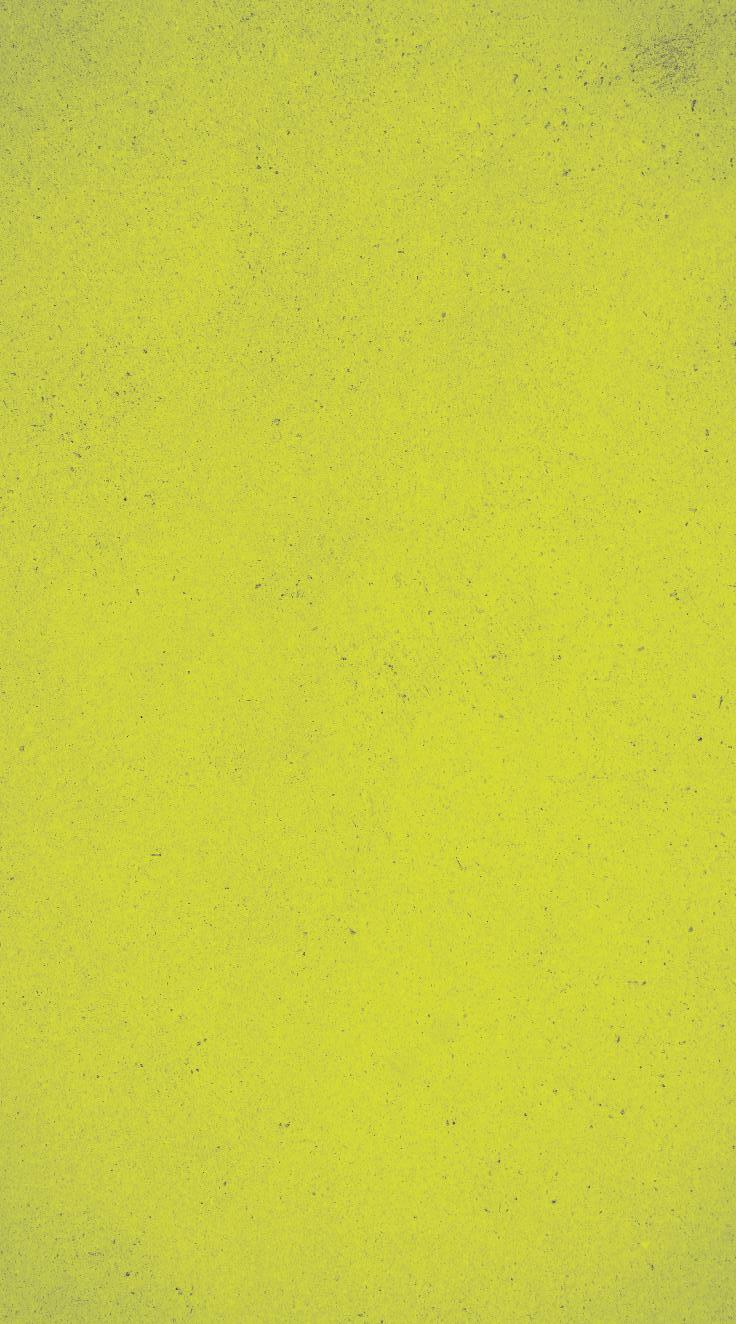
If you held a training program that didn’t stick, you’re not alone. According to a McKinsey study, only 25% of managers reported that training changes an employees’ performance. The other 75% are left wondering, “Didn’t we do training on that?”
At VPPPA’s 2022 Safety+ Symposium, held in Washington, D.C., the author shared a 5-phase process to help ensure you avoid ineffective training events in the future. However, if it’s already happened, good news: All is not lost.
Here are 4 strategies for reigniting a past training, so you finally get the results you want. These strategies can be used individually, or as the case study will show, combined for powerful results.
Some key questions for attendees to cover in their presentation might include:
• What did you find interesting?
• What do your peers need to know about this?
• What did you change, or should you have changed, as a result of this training?
• What should your peers change?
1After the presentation, facilitate a discussion that allows the team to share their impressions, add personal experiences that add more context to the training, and identify action items they want to follow up on or implement as a result of this training.
4 strategies to reignite a past training
Facilitated Discussion
If the situation does not lend itself to a peer-to-peer presentation, a facilitated discussion can still be very effective. For example, we worked with a mechanical contractor whose supervisors had previously received leadership training. While they had adopted some new behaviors, there was room for more growth. We guided attendees in recreating their training while they shared their insights on how their communication skills impacted their teams. Attendees identified where they had opportunities for improvement and a skill that would take their leadership to the next level.
Gamification
Reviewing past material can be boring for attendees. Especially when it’s material they’ve heard multiple times. In that case, gamification can turn the review into a fun and competitive experience that allows attendees to demonstrate how much they know and be reintroduced to material they may have forgotten. Quiz shows and matching games are easy ways to cover key information in a short period of time, but if you’re looking to gauge competency with equipment, tools or processes, you could set up multiple stations for employees to demonstrate mastery before moving on to the next station.
Challenges
CASE STUDY
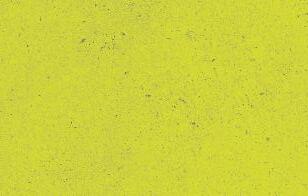
Here’s an example of how to pull these pieces together to successfully rekindle a past training to increase a desired behavior.
A leader at an international utility company reached out to Habit Mastery Consulting for help improving his team’s safe driving practices, many of whom could be driving hundreds of miles a day from one site to another. They had already been through extensive driving training over a period of years. They did not need more driving training. They needed an opportunity to practice the driving skills they already knew they needed, so that it became a habit.
3We designed the “Amazing(ly Safe) Race” as a gamified training experience themed around dinosaurs and vehicles. Participants divided into teams and moved around a racetrack by giving correct answers on safe driving practices while avoiding hazards— like vehicle-destroying dinosaurs. In smaller groups, attendees discussed how safe driving practices impacted them and why it was important that they drive safely. By the end of the training, participants had chosen a safe driving practice that would make the biggest improvement in their own personal safety on the road. For example, attendees chose behaviors like driving the speed limit, leaving more space between vehicles, not using a cell phone, backing into parking spots, and conducting a 360 walk around before entering the vehicle.
Immediately after the training, participants began practicing their desired safe driving practice in a 60-day challenge. Via their mobile phones, participants received daily reminders and tracked their successes and failures in completing their desired safe driving behavior each day.
Overall, attendees enjoyed the unique training experience. It offered a fun way to revisit material they were already familiar with and provided strategies to put their knowledge into action. At the end of the challenge, participants reported a 157% increase in the safe driving practice they had targeted. In a follow up survey four months after the training, they reported sticking with it and being very confident they would continue to stick with it.
When it’s simply a matter of getting enough practice with a new technique, piece of equipment, or skill, a challenge can encourage people to repeat it regularly until they’ve created new habits around this area. For a limited period of time, participants track their successes. Participants can compete with themselves or their peers to string together more and more successes. Meanwhile, they are building familiarity, confidence, and experience with the targeted behavior.
CONCLUSION
More training isn’t always the answer, especially when employees have been through a training on the topic already. Instead, dust off the materials, think outside of the box, and encourage employees to revisit the topic.
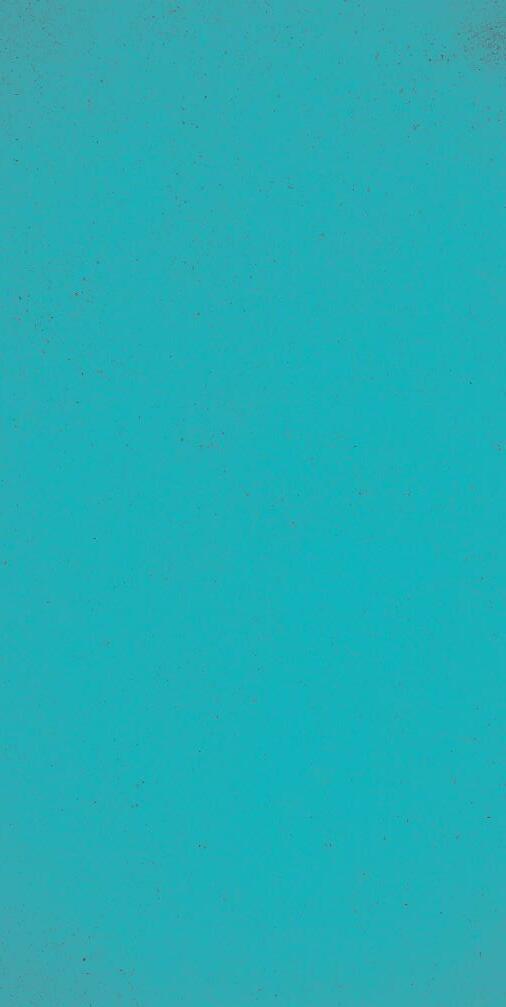
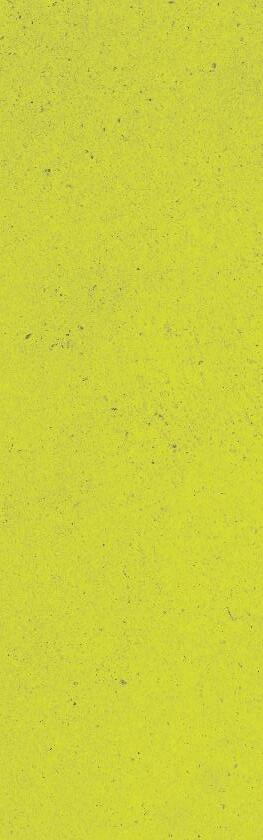
Learning happens best when attendees get the opportunity to practice and reflect on what they’ve learned.By Frank King The Mental Health Comedian
Construction is the number one at-risk occupation for suicide. Each year, roughly 1,000 construction workers die by accident, and on average 5,000 die by suicide. Which means that in construction, you are five times more likely to jump off a building than to fall off.
Construction is followed by excavation, fishing, farming, forestry, dentistry, veterinary medicine, healthcare, and the legal profession. Men die by suicide in other age groups, ethnic groups, and industries, but these predominate.
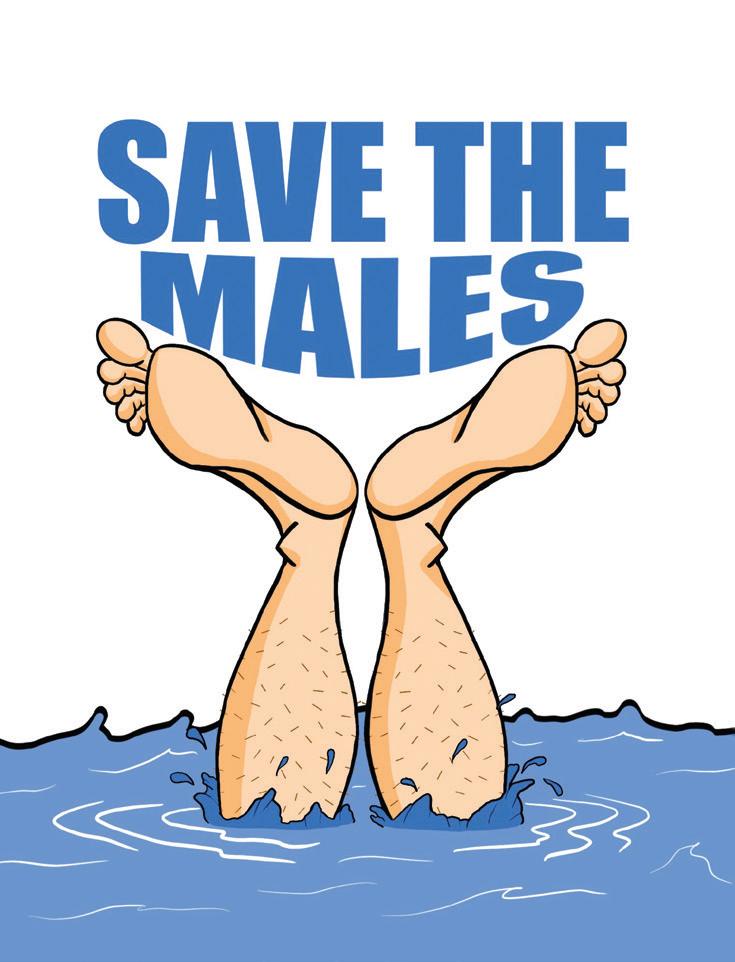
The trouble is, hardly anyone is doing much about it…until now. My coauthors, Dr. Sally Spencer Thomas and Sarah Gaer, MA, and I literally wrote the book on it. Actually, we wrote a four-book series on it, Guts, Grit, and the Grind; a Mental Mechanics Manual www.gutsgritgrind.com, available on Amazon.
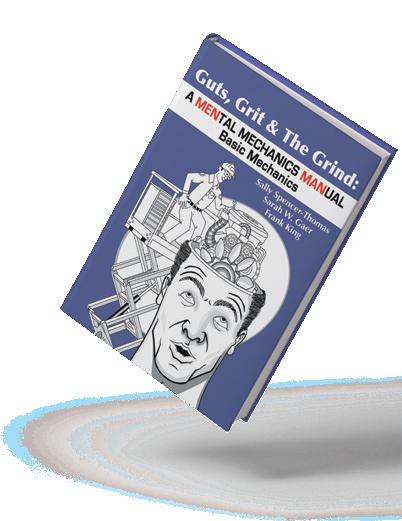
At this point, you may be thinking, Why just focus on men, what about the women? Excellent question. Men kill themselves roughly four times as often as women. Women attempt three times as often as men, but men tend to complete a suicide because they generally use a firearm.
(I said complete a suicide, as the preferred verbiage is no longer committed suicide, because the word commit carries some heavy-duty stigma. You commit a crime, you commit a sin, and so forth. To reduce the stigma, the recommended verbiage is died by suicide, or completed a suicide.)
And, as it turns out, the majority of our books on men’s mental health are sold to women. We believe the reason is because women have a man in their life—a father, brother, husband, coworker, or a friend—who is struggling with a mental challenge, and they want to help these men, but are often unsure on how to go about it.
If you are a woman and you’re reading this, don’t feel bad that perhaps you don’t understand the men in your life who are struggling. Often, the men don’t understand themselves.
Someone who does understand suicidal men quite well is Dr. Paul Quinnett, Founder of the QPR Institute, Past President of the American Association of Suicidology, and avid fisherman. He is the kind gentleman who created the Suicide Prevention Curriculum, QPR (question, persuade, refer), which you can read more about at www.QPRInstitute.com, and who wrote the foreword for our first book. In it, he says, “I’ve spent most of my adult life trying to help men not kill themselves. So have the authors of this book.”
For my side of the work, I’ve written articles, stories, book chapters, led seminars, and given lectures all over the world about men and suicide. The
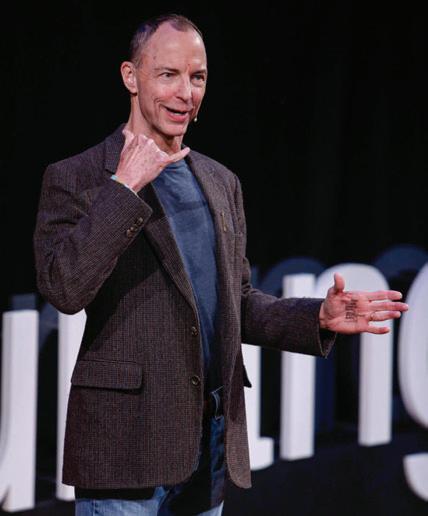
source code for my observations about men and suicide were men themselves; men I saw in my 30-year practice as a clinical psychologist. Most of these men were sent to me by other clinicians who were, frankly, too frightened to treat them themselves for fear they might take their own lives and leave their families to sue them for malpractice.
Me? I like to work with suicidal men. I specialized in them and saw hundreds. Men who work hard in therapy, quit drinking or drugging, and stop doing stupid stuff are always grateful.
Men believe in paying it back and paying it forward. Do a man a favor and he says, “I owe you one.” And he means it. Called “male reciprocity,” men understand that when you accept something it is never free, but that a price must be paid; back to the giver, or to someone else into the future. It’s about paying one’s debts. It’s about the code of fair play and fair dealing. It’s about honor. It’s why mentored men mentor other men. Heartfelt reciprocity is the mark of manhood.
And it’s about why the men you will meet in Guts, Grit and the Grid are willing to tell their stories. They are paying it forward.
Only a few lucky men find their way into competent care and it usually takes a lifethreatening crisis to get them there. In general, men wait too long for most health-related issues. The engine-to-brain metaphor used as device is a good one, and one I have been using for decades with my male patients. As I joke with men, “If you took care of your car’s engine like you’re taking care of your brain, you’d better get used to walking or taking the bus.”
Not reaching out for help has many causes, not the
least of which is that when in extreme pain, our brains tell us, “Nothing can help, you’re too far gone.” It’s called the “helpnegation effect,” and its real, and it costs us all too dearly.
To get some men into treatment takes some true persuasion. “You either go to counseling with me or I’m leaving.” “Clean up your act, or you’re fired.” “If you’re late one more Monday morning, you can pack your bags.”
Do men wait too long to ask for help with suicidal thoughts?
Of course, they do.
What man in his right mind would tell anyone they are thinking of killing themselves? Certainly, no physician. Certainly, no commercial airline pilot. A cop? A judge? A pastor? A farmer? Give me a break. Yet, I have seen all these men, and

Humans learn best and fastest by imitation, by watching what happens to other people, especially bad things.
not one of them got into my office prompted by following the thought: “Oh golly, I wonder if these thoughts of killing myself might have something to do with my mental health. Gee, I think I’ll go see a psychologist.”
Not one. All these men and many, many more were somehow “obligated” to see me. With one exception.
Tom was a suicidal businessman from a distant town. When asked why he had come to see me, he said, “I saw you on television.” Since I’m no actor, the only reason I’m on TV is because I give interviews about suicide. Like picking an expert mechanic for his ride, Tom brought his brain to me for diagnostics and repair, both of which were straightforward enough.
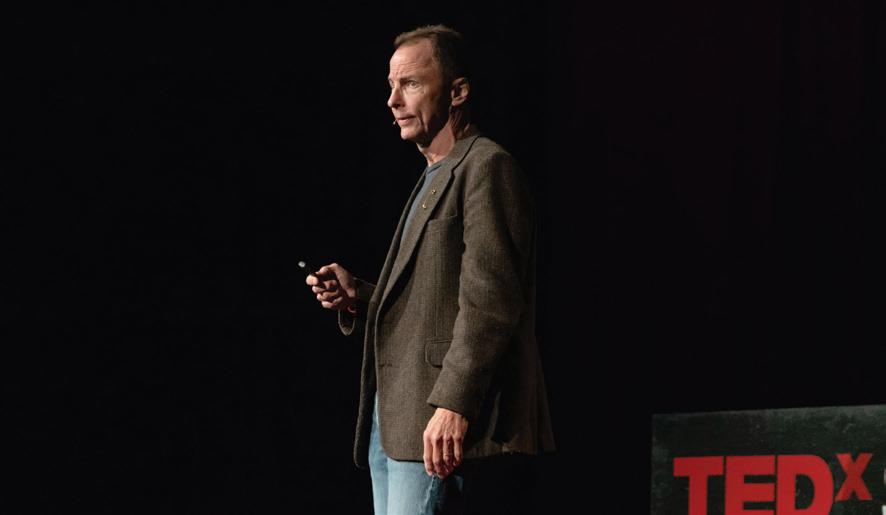
There’s a reason men don’t ask strangers for help. If you’re a man, asking for help from a stranger is dangerous. Until proven otherwise, strangers are enemies, and in ancient
times, if you were a stranger in a strange land, and other men caught you on their turf, they had a right to kill you on sight. This has been true forever, from the Bible to English Common Law to West Side Story, unwelcome male trespassers are subject to the death penalty. Or, capture and torture, slavery, and sexual assault. Every man who has to ask a stranger for help hears banjo music (from the film Deliverance), and we all know how that turned out.
The authors of this book have set about to change things in the world of men, and in how men see and think about themselves, not only in helpseeking, but help-accepting. Guys may not ask for help, but they will accept it if offered when needed, like when they are stuck in a ditch and need a push or a pull. Or in a fight against the bad guys like in everything from the Seven Samurai to The Hobbit.
Men will also accept help if they know it won’t kill them. Along with my fellow coauthors, we went directly to men in recovery and asked them to tell other men how they not only survived their own personal shit storm, but how they thrived in the aftermath.
To my knowledge, no other authors have done this before. Humans learn best and fastest by imitation, by watching what happens to other people, especially bad things. It’s why we all rubberneck car crashes. It’s why we go to scary movies. It’s why we need role modelsboth good and bad - so that we can give ourselves life lessons as in, “Holy crap! Did you see what happened to him? I think I’ll skip freestyle rock climbing.”
In Guts, Grit, and the Grind you will find life-saving stories about how men sunk down and climbed up and out
again. Delivered by real men with courage and integrity, this first-person storytelling changes lives, and for the better. Reading these personal accounts will help suicidal men take a step back and say, “Hell, if he can make it, so can I!”
The day you read this introduction, roughly another 2,000 men will kill themselves. That’s roughly a regiment of soldiers a day. Imagine that. Another 2,000 men will die tomorrow. And another 2,000 men the day after that, and on and on until we all do something about it.
To understand how men work you must lift the hood and poke around. You have to understand traditional male values. You have to understand “warrior psychology”—an emergent term that helps explain so much of what makes many men tic and why.
You have to understand team psychology, small group dynamics, and why men do best when on a mission of importance within a small band of like-minded other men who share the same vision, mission, and goal. And you have to read about how tough it was for the men in this book to find their way forward in a world that chooses to ignore their reality.
Lastly, my thanks to my coauthor, and creator of the Guts, Grit, and the Grind series, Sarah Gaer, MA, and my other coauthor, and project manager, Dr. Sally Spencer Thomas
(without whom, I’m not sure this project, as good an idea as it is, would have ever been finished), and of course to the ever wise and gracious, Dr. Paul Quinnet, Ph.D. avid fisherman.
If you would like a free, unabridged audiobook version, of the first book in our four-book series, just go to my website, www. thementalhealthcomedian. com (yes, you read that right, comedian…it’s a long story), enter an email address, and you can download the MP3 for free (I am the narrator).
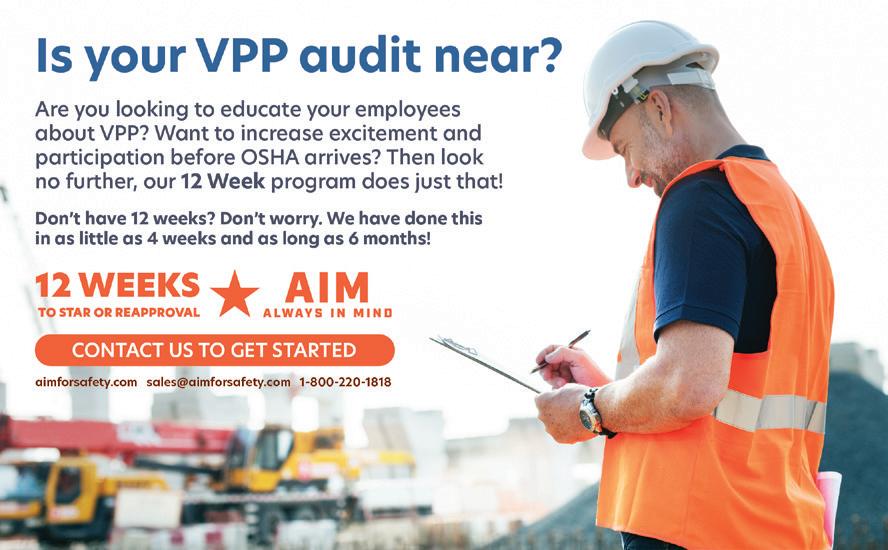
Construction is the number one at-risk occupation for suicide. Each year, roughly 1,000 construction workers die by accident, and on average 5,000 die by suicide.
There Is No Cure for Curiosity!
By Adele L. Abrams, Esq., ASP, CMSP President, Law Office of Adele L. Abrams PC www.safety-law.comRecently, I participated on a panel of senior occupational safety and health (OHS) professionals at a conference of the American Society of Safety Professionals (ASSP). The panel was asked to share experiences and recommendations on a career in OHS. It forced me to think back on how I entered the profession, and to have gratitude for the employer-supported, post-graduate education and professional development that truly shaped my OHS profession and prepared me for the work I’ve done in my 30-plus-year career.
As a bit of background, OHS was not my first profession and was definitely not on my radar. Straight out of college, I began work as a radio DJ in Washington, D.C., and stayed on the air for 14 years. But I discovered OHS when I began working in government affairs for construction/mining trade organizations (overlapping with part-time radio work). OSHA, MSHA, and a few other governmental acronyms were thrown at me as part of my written and lobbying responsibilities, but while I could read the Federal Register and prepare comments, I knew that I lacked the foundational basis to truly comprehend the issues and advise my employer and our members on the best path forward.
I realized that I needed to study up. That would require support from my employer or others in the field in order to competently perform my duties. I knew I could not learn the technical skills adequately on my own. I had a BS degree in journalism and broadcasting, and graduate studies in public relations and marketing. These disciplines prepared me for being a trainer, or communicator, but were not geared toward understanding the nuts and bolts of OHS requirements for construction, manufacturing, and mining operations.
I have since learned how common it is for individuals to enter the OHS profession without initially having any safety-related degrees or specific training. On-the-job training is great if someone is there to pass along their knowledge, but often that continuity is lacking if the predecessor retired, quit, or was fired without any transition period. This is a dangerous period for the employer as well, as best practices can be lost in the shuffle, and backsliding can occur.
Issues Relevant to Advancing Worker Well-being Using Total Worker Health® Approaches
Prevention and Control of Hazards and Exposures
• Biological Agents
• Chemicals
• Ergonomic Factors
• Psychosocial Factors
• Risk Assessment and Management
Built Environment Supports
• Accessible and Affordable Health Enhancing Options
• Clean and Equipped Breakrooms, Restrooms, and Lactation Facilities
• Healthy Workspace Design and Environment
• Inclusive and Universal Design
• Safe and Secure Facilities
Community Supports
• Access to Safe Green Spaces and Pathways
• Healthy Community Design
• Safe and Clean Environment (Air and Water Quality, Noise Levels, Tobacco-Free)
• Safe, Healthy, and Affordable Housing Options
• Transportation and Commuting Assistance
Compensation and Benefits
• Adequate Wages and Prevention of Wage Theft
• Affordable, Comprehensive, and Confidential healthcare Services
• Chronic Disease Prevention and Management Programs
• Continual Learning, Training, and (Re-)Skilling Opportunities
• Disability Insurance (Short-and Long-Term)
• Employee Assistance and Substance Use Disorder Programs
• Equitable Pay, Performance Appraisals, and Promotions
• Minimum Guaranteed Hours
• Paid Time Off (Sick, Vacation, Caregiving, Parental)
• Prevention of Healthcare Cost Shifting to Workers
• Retirement Planning and Benefits
• Work-Life Programs
• Workers’ Compensation Benefits
Healthy Leadership
• Collaborative and Participatory Environment
• Corporate Social Responsibility
• Responsible Business Decision-Making
• Supportive Managers, Supervisors, and Executives
• Training
• Worker Recognition, Appreciation, and Respect
Organization of Work
• Adequate Breaks
• Comprehensive Resources
• Fatigue, Burnout, Loneliness, and Stress Prevention
• Job Quality and Quantity
• Meaningful and Engaging Work
• Safe Staffing
• Work Intensification Prevention
• Work-Life Fit Policies
• Elimination of Bullying, Violence, Harassment, and Discrimination
• Equal Employment Opportunity
• Family and Medical Leave
• Human and Natural Resource Sustainability
• Information Privacy
• Judicious Monitoring of Workers and Biomonitoring Practices
• Reasonable Accommodations
• Transparent Reporting Practices
• Whistleblower Protection
• Worker Well-Being Centered
• Workplace Supported Recovery Programs
Technology
• Artificial Intelligence
• Robotics
• Sensors
Work Arrangements
• Contracting and Subcontracting
• Free-Lance
• Global and Multinational
• Multi-Employer
• Non-Standard
• Organizational Restructuring, Downsizing, and Mergers
• Precarious and Contingent
• Small- and Medium-Sized Employers
• Temporary
• Unemployment and Underemployment
• Virtual
Workforce Demographics
• Diversity and Inclusivity
• Multigenerational
• Productive Aging across Lifecourse
• Vulnerable Workers
• Workers with Disabilities
Total Worker Health® is a registered trademark of the US Department of Health and Human Services Chart courtesy of NIOSH
In retrospect, I realize how fortunate I was to have professional development support available to me from the outset. This initially was via membership and participation in the National Safety Council (NSC) starting in 1989, where I got heavily involved in the section for my industry sector and met my first OHS mentors and lifelong friends in the industry. These mentors helped guide me to other courses I should explore, and ultimately encouraged me to achieve my first professional certification: Certified Mine
Safety Professional (CMSP). I have maintained that for over 20 years and remain an MSHAapproved (Mine Safety and Health Administration) trainer.
But I also did a deep dive in studying the OSHA side of safety and health, including eventually completing OSHA’s “train the trainer” course, which enabled me to conduct the 10- and 30-hour courses for others. It was a long time coming, but since the pandemic provided extra time for study, I was able to finally sit for and pass the ASP certification exam last year. Next stop, CSP.
Professional development and learning is a lifelong process.
On a parallel track to my OHS educational efforts, my employer also supported me in attending law school at night while maintaining full time employment, as it was related to my regulatory and legislative activities. This enabled me to complete my JD in four years relatively debtfree, and to remain dedicated to the practice of OHS law and outreach, often in support of small businesses that lack internal safety personnel.
Employers play a crucial role in supporting employees who wish to enhance their OHS knowledge or seek additional formal education in the OHS field. Providing paid time off for attending professional development conferences, for examinations when an employee is attending night school, or for maintenance of continuing education requirements, is important in supporting workers who undertake these off-duty activities. The ultimate result is having qualified, certified OHS professionals at the helm of a company’s program, which benefits the employer’s OHS performance and enhances its credibility with OSHA and third parties.
The National Institute for Occupational Safety & Health (NIOSH) has included “continual learning, training and (re)skilling opportunities” among the items in the “Compensation and
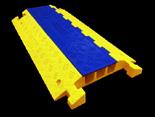
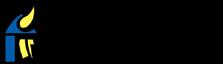
Benefits” silo of its Total Worker Health (TWH) initiative. At a time when employee recruitment and retention are at a crisis point, it is worth reviewing the NIOSH recommendations as the TWH elements will make an employer attractive to candidates. It is also critical for employers to recognize that supporting employees in obtaining professional certifications is not a “one and done” endeavor. If an employee is a CSP, ASP, CHST, CMSP, or CIH, expect that they will have to maintain professional memberships that help them access timely information about new regulations as well as to share best practices that reduce accidents and injuries, and will also be subject to CEU requirements on a periodic basis.
As I write this, I am attending the NSC’s annual Congress for the thirty-second time. I’m the old-timer now, presenting
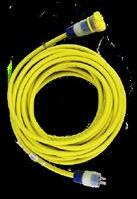
sessions on construction safety, MSHA, and OSHA compliance and best practices for incident prevention. I know I am passing along much of the knowledge that I first learned at NSC sessions and from my mentors decades ago. OHS professionals can preserve valuable institutional knowledge by sharing it while also mentoring others and presenting that knowledge via webinars, live presentations, podcasts, contributing to textbooks, and writing articles. For those of us with professional certifications, such volunteer work is expected to develop the next generation of OHS professionals. Why did a professional career in safety attract me to begin with? Because I realized the practical implications of my work, training, auditing, performing gap analysis to help improve existing programs so that workers can be better
protected. Simply put, OHS professionals save lives, even if we cannot quantify the results with precision.
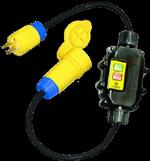
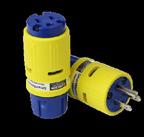
As a safety attorney I defend employers who are cited by OSHA and MSHA. I also teach employment law at two universities, and cover OSHA as part of the course content. But much of my time is dedicated to OHS consulting and training where I can share the professional knowledge that I have acquired along the way, and hopefully leave each company or individual with whom I work a bit safer than before. I’ve long had the slogan, “There’s no cure for curiosity.” I was that child who read the encyclopedia, and now I immerse myself in OHS professional development. It’s my passion and I want to know more and share the information to help save lives. Remain curious, friends!

HOW WE THE WORLD
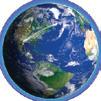

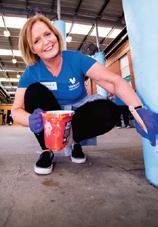
More than $60 million in donations and fundraising. 90,600 volunteer hours.
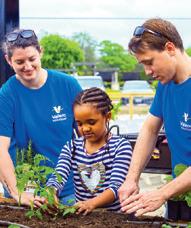
We’re energized by giving back to the communities where we work and live. It’s a culture that makes us proud, and a commitment that will remain a part of who we are.

GOING BEYOND TRADITIONAL
(CONTROL OF HAZARDOUS ENERGY) Policies and Training to Minimize the Potential for Adverse Incidents

SHA adopted its General Requirements for [Machine Guarding] All Machines Standard (20 CFR 1910.212) for General Industry in 1971, its Lockout/Tagout Procedures provision for Construction in 1988, its Lockout/Tagout (LOTO, Control of Hazardous Energy) Standard for General Industry in 1989, and its Electrical Safety-Related Work Practices Standard in 1990. Despite many years of employer experience, and OSHA enforcement and outreach under these standards, the General Industry Machine Guarding and LOTO Standards continue to be, year after year, two of the top ten most frequently cited OSHA standards.2 The United States Bureau of Labor Statistics (BLS) estimated that, in 2020, there

were 10,900 lost workday cases3 and 894 fatalities resulting from workers caught in running equipment or machinery, and 2,220 lost workday cases and 126 fatalities resulting from workers exposed to electricity. There are other types of events tracked by BLS that also fall within the scope of these four standards.
Clearly, there is a significant frequency of harmful exposure to the hazards addressed by these four standards, and much more can and should be done to reduce the frequency and severity of these events. It does not help that the minimal OSHA General Requirements for Machine Guarding Standard is wholly inadequate,5 the OSHA LOTO Standard for General Industry was at least 10 years out of date at the time it was adopted,6 and the minimal OSHA LOTO Procedures for Construction is wholly inadequate.7
A persuasive case can be made for the proposition
that the essential and clearly interrelated elements of an effective program for the control of hazardous energy are:
1. Properly designed and maintained machinery and electrical equipment;
2. A sound and effective written program for the control of hazardous energy (with clearly stated requirements and expectations);
3. Hiring employees committed to working safely, successfully modifying the behavior of those who are not, or, if that cannot be accomplished, terminating those employees or reassigning them to a job that does not expose them to these types of hazards;
4. Providing effective training, supervision and support to employees; and
5. Providing employees with the necessary tools, testing
equipment and PPE to perform tasks safely.
I have investigated numerous accidents, written numerous incident investigation reports, and reviewed and audited numerous energy control programs. My experience is that the most significant shortcomings in a site’s hazardous energy control program generally stem from inadequate personnel management practices and inadequate policies in the written energy control program, which fail to account for human behavior by both management and line personnel. Unfortunately, these underlying shortcomings on fundamental principles too often lead to inappropriate personnel assignments and inadequate training, supervision, and support, which result in avoidable accidents.
The written programs for the control of hazardous energy in
place at most of the industrial sites I have evaluated generally have the standard verbiage expected by OSHA inspectors, but that is often not adequate to ensure a safe workplace. Beyond the standard language describing traditional lockout/ tagout, an effective program must adequately address those maintenance and servicing tasks (as broadly defined in 29 CFR 1910.147) that present a potentially harmful exposure to hazardous energy sources and, as a practical matter, need to be performed with something less than complete lockout/tagout for the entire duration of the task. These tasks generally involve minor servicing activities or testing (including troubleshooting) or positioning activities.
The written energy control program should identify each maintenance and servicing task and the alternative control measures to be utilized to provide effective protection when performing that task without complete lockout/tagout. In the alternative, the written program should require a permit to work, approved by a qualified individual, before performing any such task. Otherwise, individual employees are left to their own devices based on their personal hazard assessments and/or risk assessments. Given uneven or inadequate knowledge and the pressures of the workplace, that is not a burden that should be placed on the individual employee.
Furthermore, experience has shown that even the seemingly comprehensive and foolproof protective scheme described above is not adequate. If left to individual hazard and/or risk assessments, personnel do not always agree on what poses a potentially harmful exposure to a hazardous energy source. In addition, there is a potential problem with “mission creep” (an unplanned expansion of the
assigned task) without adequate consideration of the potential impact on safety. To minimize these scenarios, I have found four fundamental rules should be followed:
1. Removal or bypassing of protective measures should be permitted only when the hazardous energy sources are locked out or the removal/bypass is authorized by a permit to work under which effective alternative protective measures have been identified and implemented;
2. No one should ever place a hand or other body part in any location before conclusively confirming the body part will not be exposed to, or (where appropriate) will be adequately protected from, any hazardous energy source. This should protect an employee in a situation in which a guard may be missing or an area has not been guarded in a way that facilitates safe performance of the task. Generally, this should require visual confirmation8 with special measures for energy sources such as ionizing radiation
ENDNOTES
or non-ionizing radiation (e.g., lasers).
3. No one should ever be awkwardly positioned (e.g., squatting, kneeling) in any location before conclusively confirming that a loss of balance will not expose the individual to harm from a hazardous energy source. Again, this should require visual confirmation.
4. To avoid any misunderstandings or inappropriate reliance on subjective hazard or risk assessments by the individual performing a maintenance or servicing task, there should be a clear understanding on the following points: a. The minimum distance an employee must maintain between an exposed mechanical point of operation or zone of danger and the nearest part of the employee’s body. (This assessment must take into account relevant elevations, the potential for an inadvertent loss of balance by an employee in an awkward position, etc.); and
b. The nature of the barrier or other device adequate to prevent the employee from encroaching on that minimum distance. In my experience, the primary cause of injury from maintenance and servicing activities is that the machine or equipment was not shut down/ off. In evaluating a site’s policies for controlling exposure to hazardous energy, it is worth remembering the following. The 1981 BLS Work Injury Report Study13 relied upon by OSHA in adopting the LOTO Standard reviewed 833 injuries to 833 workers. Of the 833 cases, 735 involved an injury from moving machine parts and 45 involved contact with energized parts (a hazard covered by Subchapter S standards). In 653 cases, the equipment was not turned off before the work was performed. The foregoing recommendations are designed to address the primary reason for injuries incurred during maintenance and servicing activities today and back in 1981—failure to shut down/off the machine/ equipment on which the work is being performed.
1 This article is not intended to and does not provide legal advice. It represents only the personal views of the author on some of the important components of an effective program for the control of hazardous energy sources in the workplace, and does not necessarily represent the views of VPPPA or Keller & Heckman LLP or any of its clients.
2 https://www.osha.gov/top10citedstandards
3 TABLE R70. Number of nonfatal occupational injuries and illnesses involving days away from work by event or exposure leading to injury or illness and number of days away from work, and median number of days away from work, private industry, 2020. https://www.bls.gov/web/osh/cd_r70.htm
4 https://www.bls.gov/charts/census-of-fatal-occupational-injuries/fatal-occupational-injuries-by-eventdrilldown.htm
5 For comparison, see https://www.assp.org/standards/standards-topics/machine-guarding-b11 and https://ec.europa.eu/docsroom/documents/49995
6 OSHA formally began work on the OSHA LOTO Standard in January 1977 and published the initial final rule on September 1, 1989. 54 Fed. Reg. 36644. Its much-delayed effort to update the LOTO Standard to recognize and take advantage of the enhanced protections and efficiencies offered by modern technology is briefly described https://www.reginfo.gov/public/do/eAgendaViewRule?pubId=202204&RIN=1218-AD00. OSHA’s reference in this entry to “recent technological advancements” would have been more appropriate 20 years ago.
7 See the limitations of the OSHA LOTO Procedures for Construction identified in Secretary of Labor v. Roy Rock LLC, OSHRC Docket 18-0068 (July 22, 2021). https://www.oshrc.gov/assets/1/18/Roy_Rock_LLC%5E180068%5EComm_Decision_and_ALJ_Decision%5E072221.pdf?11768
8 In other words, don’t place your hand in a place you cannot clearly see to be free of hazards. One can purchase what is described on Amazon.com as a waterproof, dual lens endoscope/borescope HD snake inspection camera with LED lights and a 10 foot cable for as little as $55.00.
TheNot-So-Secret SustainableSaucetoaHealthand SafetyCulture
By Kara Apperson ES&H Data Coordinator, Bechtel National Inc.OSHA marks education and training as one of the cornerstones for a successfully executed safety and health program along with management engagement and worker participation, workplace analysis, hazard prevention and control, and program evaluation and improvement.1 Creating engaging, flexible, and multifaceted education programs for employees that are intentionally woven into each of these pillars of a health and safety program will set a foundation for a positive and, most importantly, sustainable safety culture in the workplace.
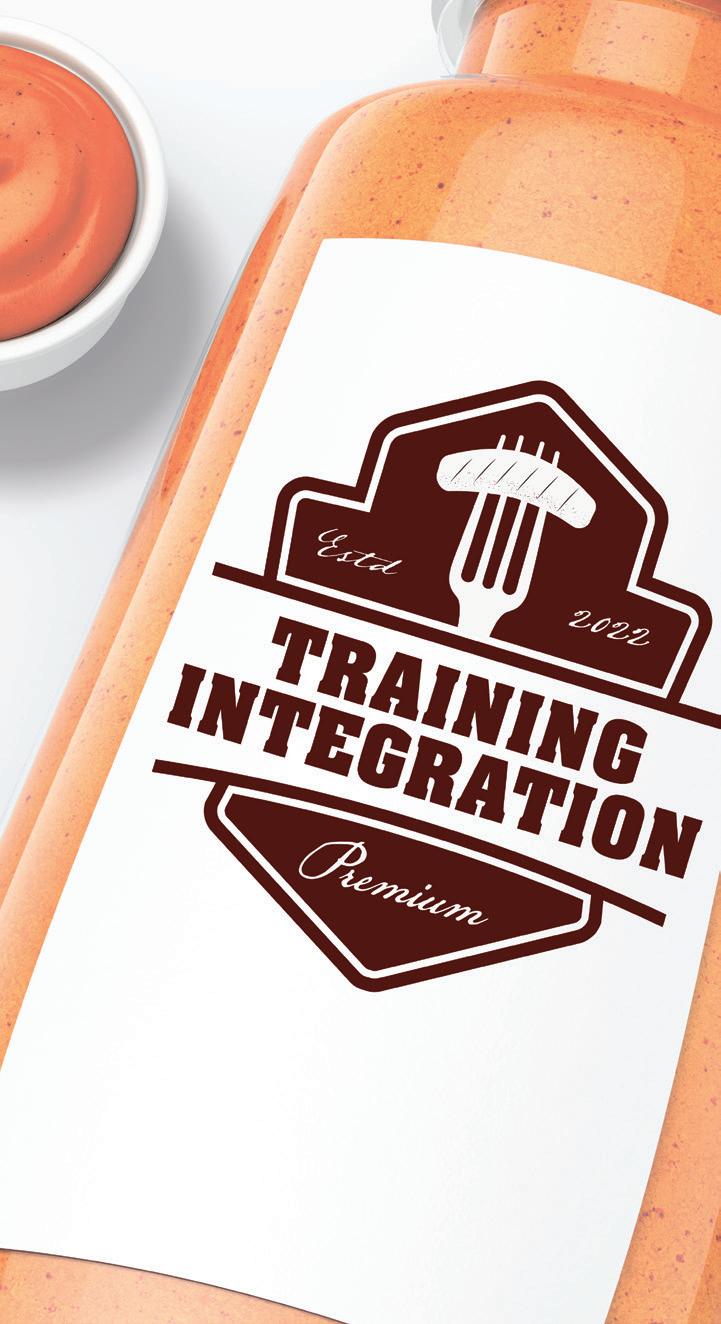
Creating Engaging Programs
In a perfect world, organizations would be able to tailor education programs to each employee to optimize their experience and learning. Realistically, organizations may have no idea what type of learners their employees are, and safety and health education programs need to be flexible enough to cater to whoever walks through the door.
Learning Styles
A quick Google search will show you there are about a million different ways people learn and process information. In general, though, it’s still widely accepted that individual’s learning styles fall into one or more of four categories: visual, auditory, kinesthetic, and reading/ writing.2 Visual and auditory learning styles are pretty self-explanatory, with folks who process information best through these modalities preferring learning tools like images and oral instruction, respectively. Reading and writing learners are also sometimes referred to as tactile learners, and need to read, highlight, underline, and take notes to absorb information. Lastly, kinesthetic learners are hands-on. They need to walk through examples and physically interact to best understand what they are learning.
Mix It Up
It’s probably safe to assume everyone reading this article has had to endure a death by PowerPoint training at one time or another. Sitting in a classroom or on a computer flipping through slide after slide with lines and lines of text can be completely depleting and is unnecessary
with all the options available to bring training and education to life. Even in situations where a slideshow is perhaps the only method of facilitation, there are things that can be integrated into the sessions to mix it up and get students involved. Adding a poll or asking for feedback and ideas to foster discussion in the class is an easy way to break up a lecture-style training and help those in class make personal connections to the material that will make it more meaningful. Utilizing interactive methods like a physical hazard school or demonstration training on a worksite rather than walking through a slideshow are also great ways to create lasting impressions on employees, because they are provided with real-world examples to bring back to the field.
Teach to Your Audience
Along with mixing up modalities and understanding the way employees may best interpret information, it’s imperative to know your audience. Are you conducting a training where you have a mixed bag of employees from different departments or trades? Are you working with a group of higher-level management or maybe college interns? Every group will come into health and safety education with varying levels of baseline knowledge and experiences, and it is the job of the instructor to meet their students where they’re at to help them successfully learn what’s being taught.
Adding to the Culture
Circling back to what was previously touched on with OSHA, training and education is just one piece of the puzzle. All components of a successful safety and health program
work together to build a positive safety culture in the workplace. I could write a book on the interplaying dynamics of each part of a safety program, but to keep it digestible, and on topic, I’ll focus on a couple of ways education and training can be incorporated continuously to meaningfully add to the safety culture.
Tie it to the Work Training and education should be relevant to the work employees are doing. Before a training program is implemented in the field or even in an office setting, evaluate and analyze the working environment to create useful training and education opportunities for employees.
Here are some questions to ask when thinking of a new training program:
• What are some of the critical path activities coming up in the next 3-6 months on the site?
• What incident trends has the project seen in the last few months or this time last year?
• What software programs are being used on the site and how are they being used?
• How can you tailor training to help employees utilize tools and technologies in the way they specifically need, instead of just a generalized how-to?
These are things to incorporate and anticipate, to create a robust and sustainable training and education
program within safety and health.
Continuing Education
Learning is a continuous process and the more you hear and interact with the material the better you remember what you need to know.3 Continuing education doesn’t just have to be a yearly class for employees who feel dragged into it, begrudgingly. Part of building a positive culture in health and safety is consistency. In fact, education and training doesn’t always happen in a classroom. Small snippets of key information can be integrated into refreshers and conversations like toolbox talks and pre-job briefings. Quick blurbs like a safety share at the start of a meeting can serve as poignant reminders and spark critical thinking. There are endless ways to plug concepts from organizational health and safety education into every aspect of the work process. Incorporating these refreshers and reminders in different ways to continually expose employees will only strengthen their knowledge and ability to apply it in their everyday work.
Be Like Taylor Swift
Taylor Swift is arguably one of the most meticulously organized and calculating individuals in the entertainment industry. She is the queen of intentional planning and grand web building; planning her album releases, shows, and appearances three years in advance. Every video she
Organizations may have no idea what type of learners their employees are, and safety and health education programs need to be flexible enough to cater to whoever walks through the door.
releases, social media post she makes, or clothing she wears has a subtle hint or intentional meaning to what she has up her sleeve next. To top it off, her planning and execution is centered around one constant: her fans.
Health and safety educators can take a beat from Taylor when it comes to building their own programs. Forethought and planning can make or break a training and education program’s success, because education is ever evolving with new modalities and different learning groups.
Even work environments and sites are constantly changing and evolving, and safety and health education should be synchronized and anticipatory of the different phases of work.
Wrapping
It Up Approach your safety and health programs strategically: Look through a training and education lens; Constantly assess your educational programs; Improve, plan, integrate, and above all,
END NOTES
remain focused on employees. This will build a strong, sustainable health and safety program. Training and education programs should be dynamic, engaging, and flexible to effectively reach employees right where they are. This will bolster their safety base and health knowledge so they can be a part of building a sustainable and successful health and safety culture no matter the workplace.
1 Occupational Safety and Health Administration. “Recommended Practices for Safety and Health Programs.” Safety Management Education and Training | Occupational Safety and Health Administration, https://www.osha.gov/safety-management/ education-training.
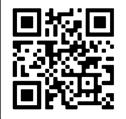
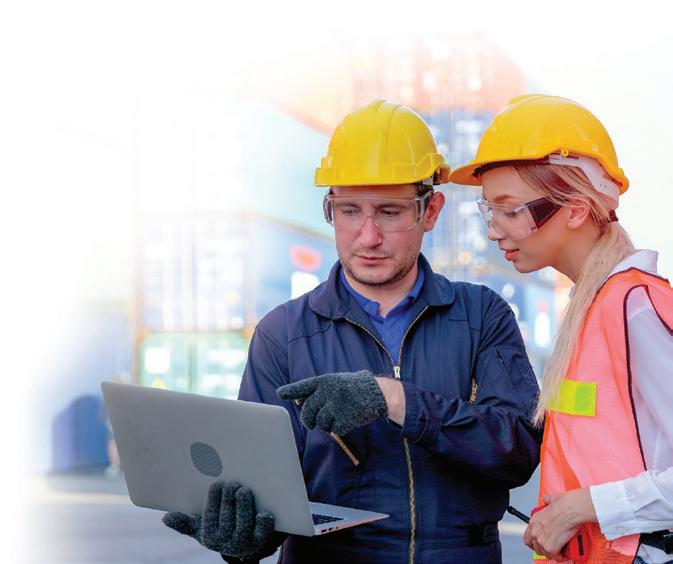
2 Drago, W.A. and Wagner, R.J. (2004), “Vark preferred learning styles and online education”, Management Research News, Vol. 27 No. 7, pp. 1-13. https://doi.org/10.1108/01409170410784211
3 Kang, Sean H. “Spaced Repetition Promotes Efficient and Effective Learning.” Policy Insights from the Behavioral and Brain Sciences, vol. 3, no. 1, 2016, pp. 12–19., https://doi.org/10.1177/2372732215624708.
Is your company a safety leader?
Whether you answered yes or no, BCSP has solutions to help your organization. We understand that providing a safe and healthy environment isn’t just the right thing to do for your employees, but also the smart thing to do for your business. With tools built for organizations like yours, you can reduce risk, enable your workforce, and build a strong safety culture – all of which impact your bottom line.
Organizations may have no idea what type of learners their employees are, and safety and health education programs need to be flexible enough to cater to whoever walks through the door.
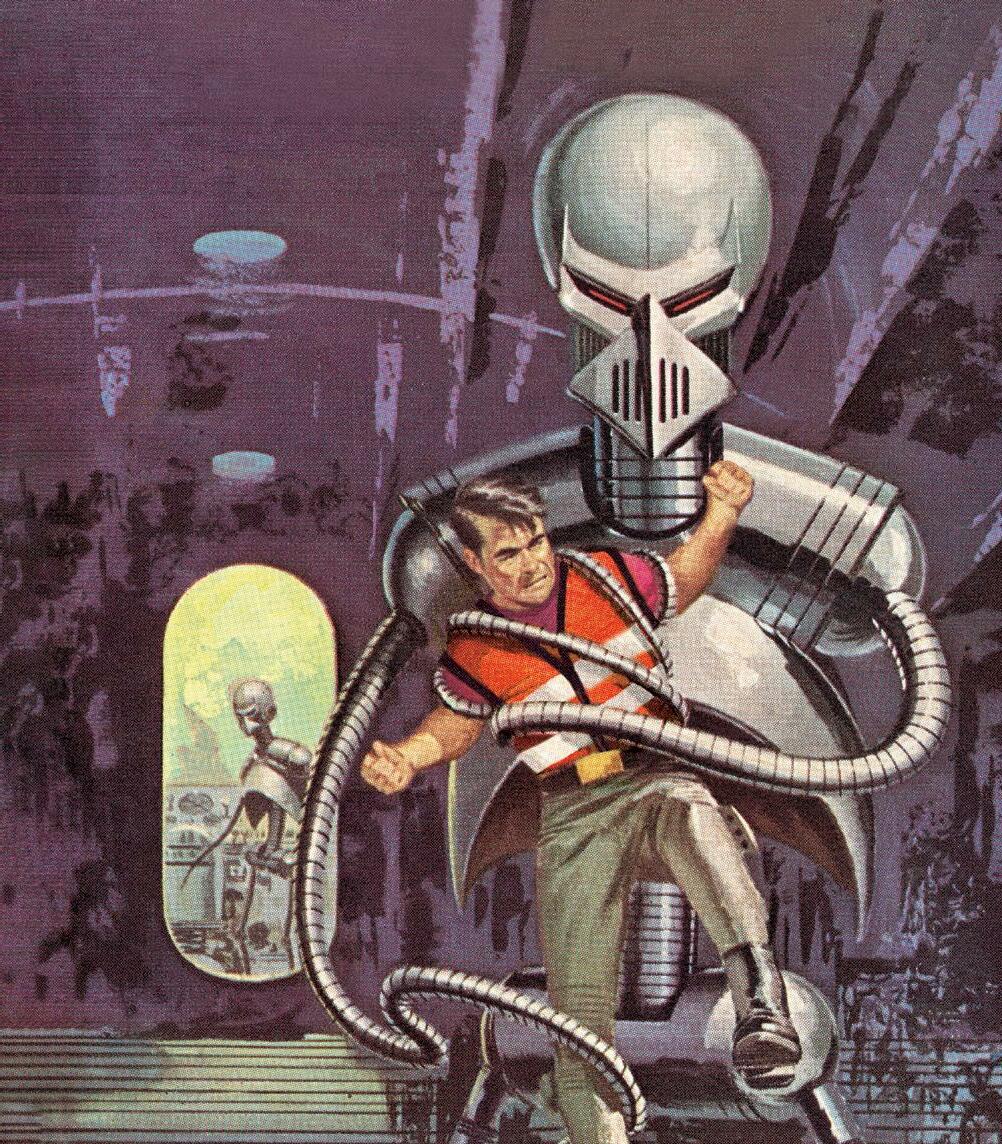
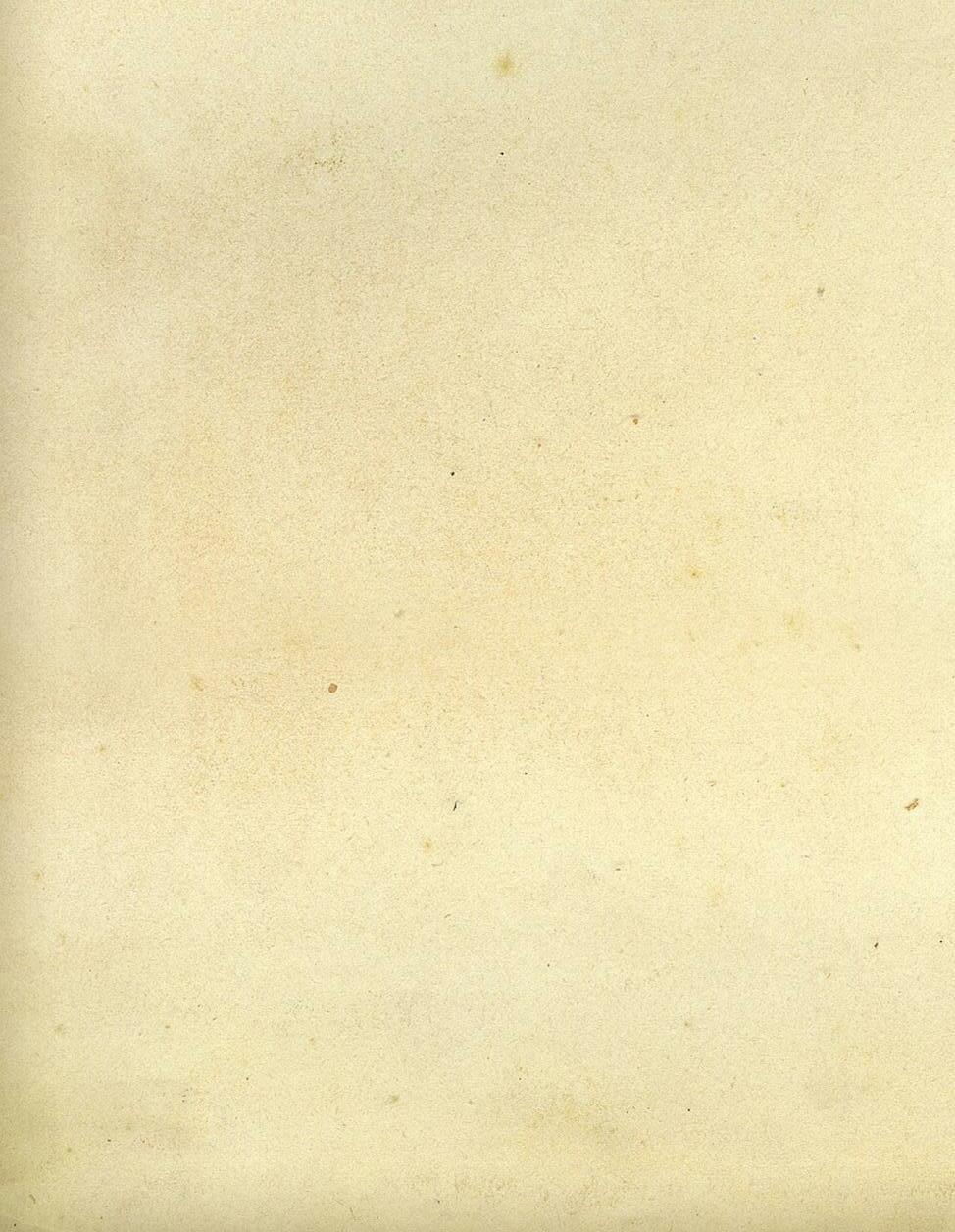
Education & Training Can Support Safety and Health Success
By Dan Corcoran, Ph. D., CIH, CSP®, Columbia Southern UniversityMost anybody who has been involved with the Voluntary Protection Programs or general safety and health management systems understands there are a number of elements inherent in the system that work together to ensure successful outcomes.
These elements include a high degree of management commitment, employee involvement in the facility’s safety and health endeavors, a well-planned process for hazard identification and assessment, hazard prevention and control, education and training, and program evaluation and improvement. These elements must be effectively implemented for the approach to work.
Education and training are key elements of the approach. If those who are involved with system’s operations do not understand their roles, it is unlikely the system will succeed. Given the importance that education and training play to the safety management systems approach, this article will discuss safety and health training from a couple of perspectives. First, it is important to consider training from the perspective of roles in the safety and health structure. Secondly, consider training from the perspective of conveying the actual safety and health knowledge that managers and workers need to know.
Awareness and Support Training
When it comes to training and education, anyone who plays a part in occupational safety and health—essentially every person on site—needs to understand their roles and responsibilities. This includes managers, workers, contractors, and temporary employees, as well.
Awareness training is important for individuals who are new to the facility to make sure they understand how to report hazards, injuries and illnesses, what to do in an emergency, points of contact, general policies and procedures, and so on. Additional training and education will need to be provided, of course, as individuals become more immersed in the organization and take on roles within the occupational safety and health structure.
Employees who hold leadership roles in the safety and health management structure need to understand the responsibilities of those roles to ensure the system continues to run well. This applies to both formal leadership roles, such as an official safety and health program manager, as well as for semi-formal leadership roles, such as a chair of an ergonomics committee that may be held by a facility worker like a lead maintenance mechanic. Understanding policies and
procedures for individuals in leadership roles is important given that individuals such as these have key roles in the occupational safety and health structure. Such training and education may focus the key functions of the position, and internal formal and informal reporting structures related to safety and health processes, as management systems approaches frequently overlap formal reporting structures. Managers and supervisors also need to be trained on their oversight responsibilities to ensure performance systems are properly administered so that safety and health efforts do not take a back seat to productivity.
Safety and Health Training
Given the high degree of employee involvement at a Voluntary Protection Program site, for instance, it is very likely that both managers and workers will be involved in safetyand health-related activities such as hazard analysis and
investigating injuries, illnesses, and near misses at the facility. It is subsequently vital to ensure that individuals who participate in such activities have been provided with the training to perform these functions. Safety and health training related to regulatory compliance programs that apply to the site should be done such as emergency response, personal protective equipment, confined space, lockout tagout, bloodborne pathogens, and hazard communication training. Workers should also be trained to recognize the hazards they may encounter at their jobs, and the appropriate hazard controls to minimize exposure.
Continuing Education
Individuals who work at higher levels of the organization may require more advanced, specialized training and education from third-party sources such as the American Society of Safety Professionals, the National Safety Council, or OSHA Educational Centers.

If those who are involved with system’s operations do not understand their roles, it is unlikely the system will succeed.
Formal education is also an option for individuals who are interested in pursuing a career in occupational safety and health. Given the option of being able to take courses online, it is now possible to obtain accredited undergraduate and advanced degrees in occupational safety and health. Working adults can subsequently earn their degrees from the comfort of their own homes at a pace that works for them.
Conclusion
Educating and training in an organization that has implemented a safety management system approach requires a great deal of planning and effort. Awareness training is something that needs to be performed for anybody entering the site. Educating individuals about
their roles within the safety and health organizational structure is necessary to ensure the safety management system is supported with knowledgeable individuals. Educating the workforce as a whole in workplace safety and health requirements is also vital.
For those with more advanced safety responsibilities, it is frequently necessary for

REFERENCES
individuals to be provided with continuing education opportunities. One option for those interested in pursuing or advancing a career in occupational safety and health is to attend a university degree program in the field. There are quite a few accredited programs available online for individuals who face barriers to attending traditional university programs.
US Occupational Safety and Health Administration (n.d.). Recommended practices for safety and health programs. https://www.osha.gov/safety-management
US Occupational Safety and Health Administration (n.d.). Voluntary Protection Programs. https://www.osha.gov/vpp
ABOUT COLUMBIA SOUTHERN UNIVERSITY
As an innovator in online education, CSU was established in 1993 to provide an alternative to the traditional university experience. CSU offers online associate, bachelor’s, master’s and doctoral degrees such as business administration, criminal justice, fire administration and occupational safety and health. Visit ColumbiaSouthern.edu or call (877) 347-6050 to learn more.
®
• Keeps extension ladders from slipping on slick surfaces such as composite decking
•Unique design of foam creates tiny suction cups that grip the surface, even when wet
•Light weight for easy use, weighs less than 6 pounds
•Works on smooth surfaces, plastic, wood, concrete, etc., even when wet
•Prevents marring and scratches to deck caused by ladder feet
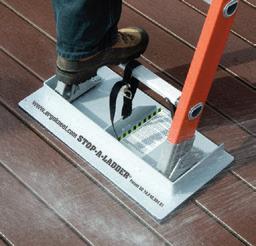
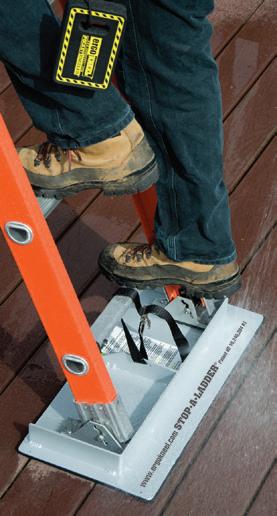
•Attaches to the bottom ladder rung, with adjustable strap, for easy movement of ladder along wall
•Fits most extension ladders, up to 21” wide
Ladder falls –2nd leading cause of work-related injuries!*
* https://www.cdc.gov/niosh/ nioshtic-2/20034690.html
•Replaceable self-adhesive foam pad Working Concepts, Inc. 888-456-3372 • www.softknees.com • info@softknees.com Patent Pending
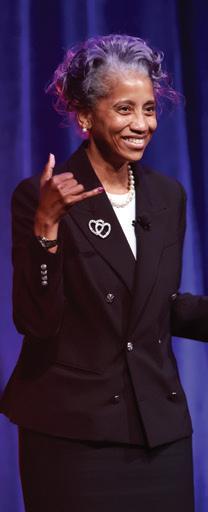
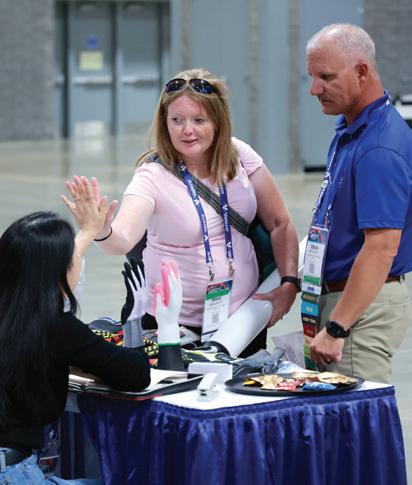
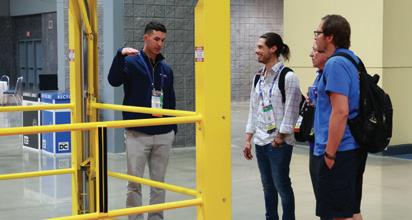
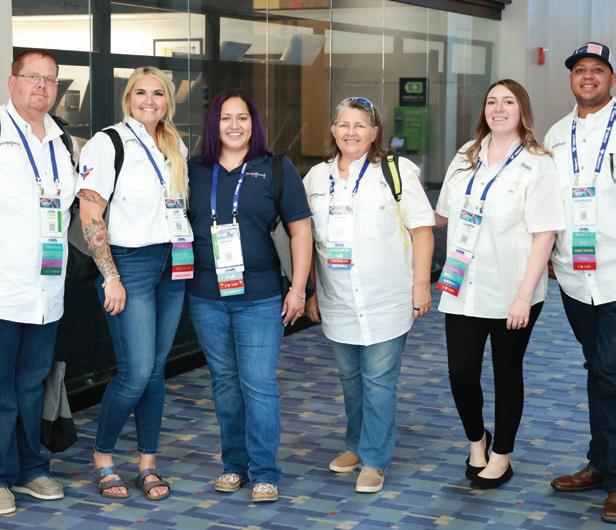
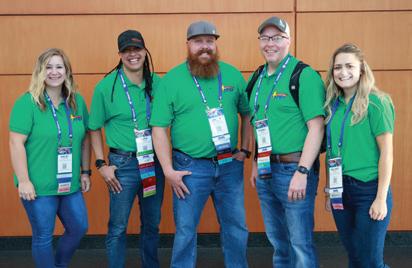


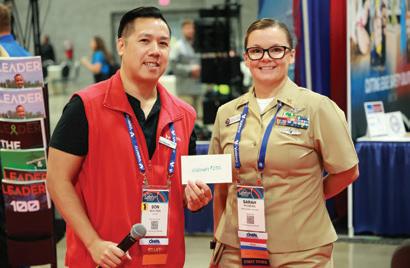
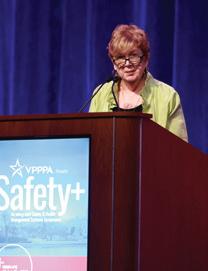
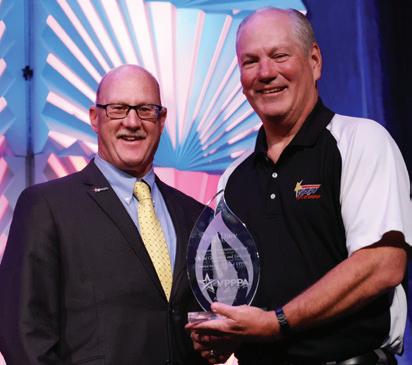

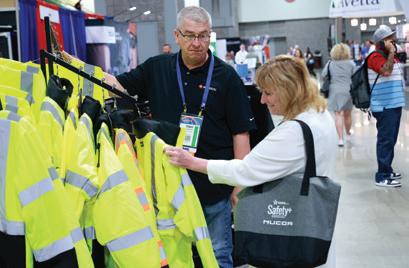
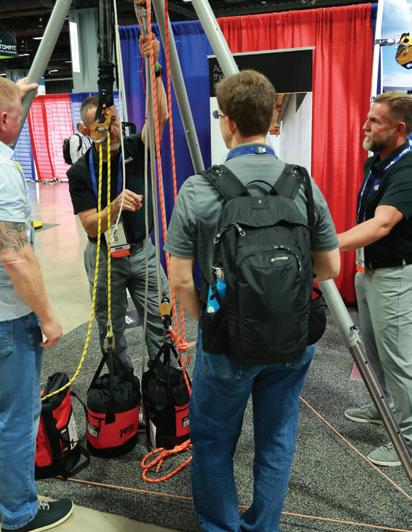
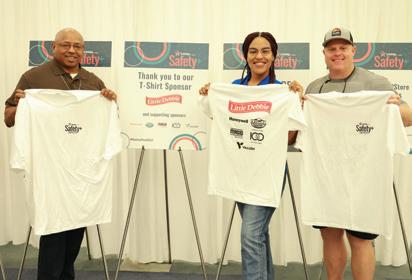
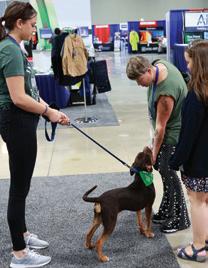
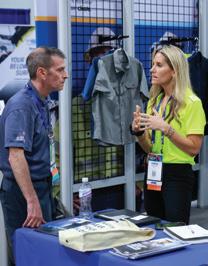
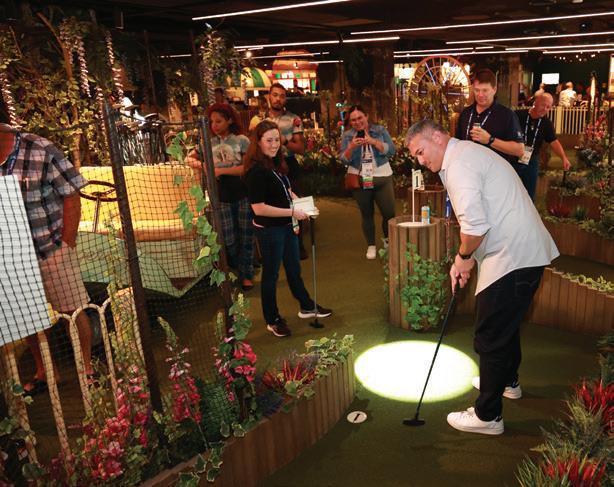
A big thank you to all our attendees, speakers, exhibitors, sponsors, staff, and volunteers, who helped make this year's Symposium a great success. See you next year in Orlando!
VPPPA’s Safety Star of the Quarter
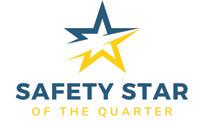
The VPPPA Safety Star of the Quarter is a program to honor and recognize an employee’s achievements in safety performance and professionalism. Thank you to all our VPPPA Safety Stars and VPPPA members for their continued contributions to the safety and health community. Safety Stars of the Quarter will be featured on our website, social media, Leader magazine, On the Level e-newsletter, and receive a certificate.
4th Quarter Safety Star
Tempe, AZ (Region IX)
To learn more about Tyler, or to submit someone to be considered as a Safety Star, please visit our website: https://www.vpppa.org/ membership/safety-star/. You can also email membership@vpppa.org
Follow us on social media!
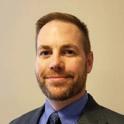
LinkedIn: VPPPA, Inc.
Facebook @VPPPA Twitter: @VPPPA Instagram: @VPPPA_Inc
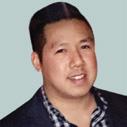
A Note from VPPPA’s Membership & Outreach Manager, Son Nguyen
The holiday season is going to be here before you know it. And with this time of year comes everyone’s favorite shopping holiday: Black Friday. During this day, we hope to find savings and exclusive deals on items we need and want. However, you are eligible to receive savings all year as a VPPPA member.
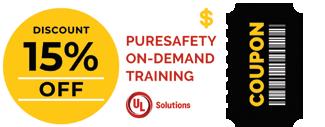
Being a member of the organization offers numerous advantages, including access to networking with other safety professionals, educational webinars, and discounts on conference registrations. But VPPPA membership also includes a variety of discounts and special promos for our members and from our members.
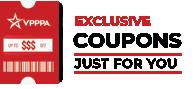
Member coupons
You can save money on products and services for your professional or personal use by taking advantage of members-only discounts. To access your coupons, log into the VPPPA Member Portal and click on the Additional Resources tab.
How do I submit a coupon?
Submitting a coupon is an exclusive benefit of Tier 2 and Tier 3 Affiliate membership. Those tiers have the unique benefit to create a special offer to VPPPA members that appears on the Coupons page and on their description in the Member Directory. If you’d like to upgrade your Affiliate membership, please contact membership@vpppa.org.
Tuition Discount
VPPPA Members, as well as their spouses and children, receive a 10% discount on tuition for Columbia Southern University. In addition, application fees are waived for members, and they also receive textbooks at no cost. CSU offers online degree programs, open enrollment, affordable rates, and a flexible learning style designed to accommodate your busy life. CSU offers associate, bachelor, master, and certificate programs.
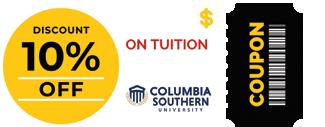
Feel free to contact us at membership@vpppa.org if you have any questions about benefits.
VPPPA & AuditSoft created the VPP Online platform to help your team collaborate on the elements of the self-evaluation, automatically calculate injury and illness rates, and generate a professional looking report for your VPP Manager, making it easier and faster than ever to complete this critical process.
Pricing: A subscription to the VPP online platform is $699 for members and $999 for non-members.
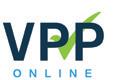
Multi-site savings package:
• 3-5 sites—5% savings per site
• 6-10 sites—10% savings per site
• 11+ sites—20% savings per site
VPP Online—The new cloud-based platform to help you maintain your VPP status.
VPP Online by VPPPA & AuditSoft Isn’t Just for VPP Sites!
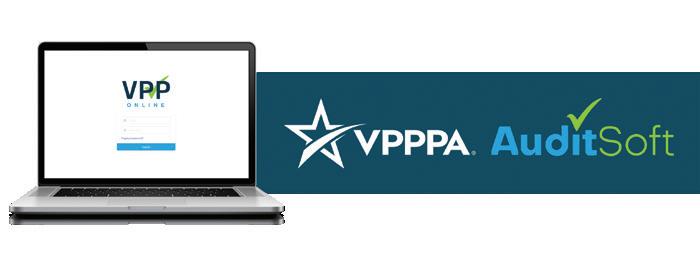
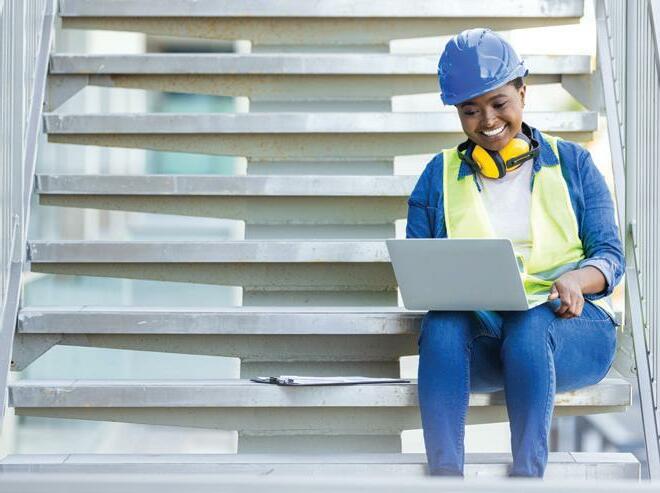

VPP Online can be used by any company or site that is committed to strengthening their EHS&S program. This valuable evaluation and improvement tool may be right for you if:
• You are interested in applying for VPP, but want to complete an internal self-evaluation to measure your current safety program first;
• You want a way to organize your safety initiatives and have a platform to collaborate with colleagues on your safety team;
• You want a professionally formatted report to share with your leadership or board and create an action plan for continuous improvement;
• You are new in the Safety role at your company and want to create a central hub for your safety management system reporting.
If you are interested in a 30-minute demo, please contact Pete Spence at Peter.Spence@AuditSoft.co
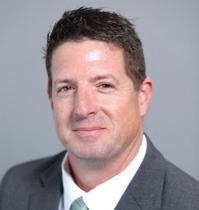
For more information visit vpppa.org/vpp-online or contact Heidi Hill at 703-761-6511 or email hhill@vpppa.org
To learn more about VPP Online and to sign up for access, visit our website at vpppa.org/vpp-online/
Don’t Miss Out on VPPPA’s Labor Summit Webinar Series
The Labor Summits are monthly 30-minute webinars showcasing a diverse mix of speakers and topics designed to engage workers, both represented and nonrepresented, to jointly and collectively discuss workplace safety. Labor summits last 30 minutes to minimize impacts to work schedules and are available as recordings the same day. Topics range from women in the workforce to building safety culture within your workplace, new workplace hazards, worker trainer programs, and more.
Learn more at www.vpppa.org/webinars
Regional Events
Many VPPPA Regions are hosting events in the coming year. Make sure to visit www.vpppa.org/ regional-events for the most up-todate information on regional events.
VPPPA Welcomes New 2022-2023 National Board Member We are pleased to introduce Tim Belitz as a new member of the VPPPA National Board of Directors! Tim Belitz Director-At-Largewww.vpppa.org
VPPPA National Board of Directors
Chairperson
Terry Schulte, NuStar Energy Vice Chairperson
Dan Lazorcak, Honeywell
Secretary
Bill Linneweh, CSP, Hendrickson International
Treasurer
Sean Horne, Valero
Director from a Site With a Collective Bargaining Unit
Jack Griffith, Central Plateau Cleanup Company
Director from a Site Without a Collective Bargaining Agent Vacant
Director from a DOE-VPP Site
Michelle Keever, United Cleanup Oak Ridge (UCOR)
Director from a VPP Contractor/ Construction Site
Brad Gibson, S&B Engineers and Constructors Director-at-Large Tim Belitz, Honeywell Director-at-Large
Daniel Charles, Brandenburg Industrial Service Company Director-at-Large
Andy Foster, Central Plateau Cleanup Company
Director-at-Large Shelly Ettel, Amentum Director-at-Large Saprena Lyons, Fluor Idaho Director-at-Large Christina Ross, Morton Salt
Editor
Kerri Usher, VPPPA, Inc.
Associate Editor
Ariana Hanaity, VPPPA, Inc.
EDITORIAL MISSION
The Leader (ISSN 1081-261X) is published quarterly for VPPPA members. The Leader delivers articles from members for members, safety and health best practices, developments in the field of occupational safety and health, association activities, educational and networking opportunities and the latest VPP approvals.
Ideas and opinions expressed within the Leader represent the independent views of the authors.
Postmaster >> Please send address changes to:
VPPPA, Inc. • 7600 Leesburg Pike, East Building, Suite 100 • Falls Church, VA 22043-2004
VPPPA, Inc., the premier global safety and health organization, is a nonprofit 501(c)(3) charitable organization that promotes advances in worker safety and health excellence through best practices and cooperative efforts among workers, employers, the government and communities.
Ad Index
Advertiser
Website Page
A.I.M. (Always In Mind) www.aimforsafety.com 21
Amazon www.amazon.com 28
AP Safety Training www.apsafetytraining.com 20
BCSP www.bcsp.org 32
Cintas www.cintas.com 44
Columbia Southern www.csu.edu 43 University
Ericson www.ericson.com 24
Health and Safety www.hasc.com 15 Council McKee Foods www.mckeefoods.com 7 Nucor www.nucor.com 9
Roco Rescue www.rocorescue.com 5 SafeStart www.safestart.com 2 Safety Rail www.safetyrail.com 13 Valero www.valero.com 25
Working Concepts www.softknees.com 37
VPPPA contacts
Chris Williams Executive Director cwilliams@vpppa.org
Sara A. Taylor, CMP Director of Operations staylor@vpppa.org
Heidi Hill Partnership Manager hhill@vpppa.org
To reach the VPPPA National Office, call (703) 761-1146 or visit www.vpppa.org. To reach a particular staff member, please refer to the contact information below.
Lisa Silber Senior Event Sales & Advertising Coordinator lsilber@vpppa.org
Kerri Usher Communications & Outreach Manager kusher@vpppa.org
Ariana Hanaity Communications Coordinator ahanaity@vpppa.org
Sierra Johnson Senior Education Coordinator sjohnson@vpppa.org
Son Nguyen Membership & Outreach Manager snguyen@vpppa.org
Bryan Knight UX Web Services Programmer bknight@vpppa.org
“Confidence. I have gained so much more confidence in my career since starting with my first course at CSU.”
Shawna Fraser Nagle M.S. Occupational Safety and HealthWhen Your Job is Safety, Trust the Leaders
The Leader in Safety Education
The Board of Certified Safety Professionals recognizes CSU’s bachelor’s and master’s in occupational safety and health as Qualified Academic Programs.

» Bachelor’s in Occupational Safety & Health
– Oil and Gas, Fire Science and Construction Safety Concentrations Available
» Master’s in Occupational Safety & Health

– Environmental Management Concentration Available
Safety practitioners who graduate from these programs are eligible to apply for the Graduate Safety Practitioner® designation prior to becoming a Certified Safety Professional®. Through its Learning Partnership with the VPPPA, CSU is proud to offer its members and their families a 10% tuition discount.
Always Forward. Always Online.
ColumbiaSouthern.edu/VPPPA » 877.347.6050
Located in Orange Beach, Alabama.
7600 Leesburg Pike, East Building, Suite 100 Falls Church, VA 22043-2004
Tel: (703) 761-1146 Fax: (703) 761-1148 www.vpppa.org
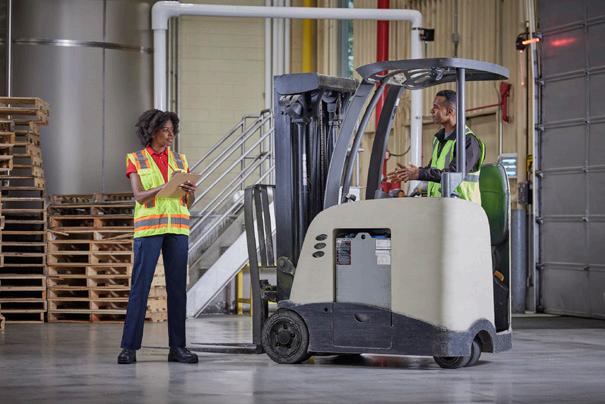
