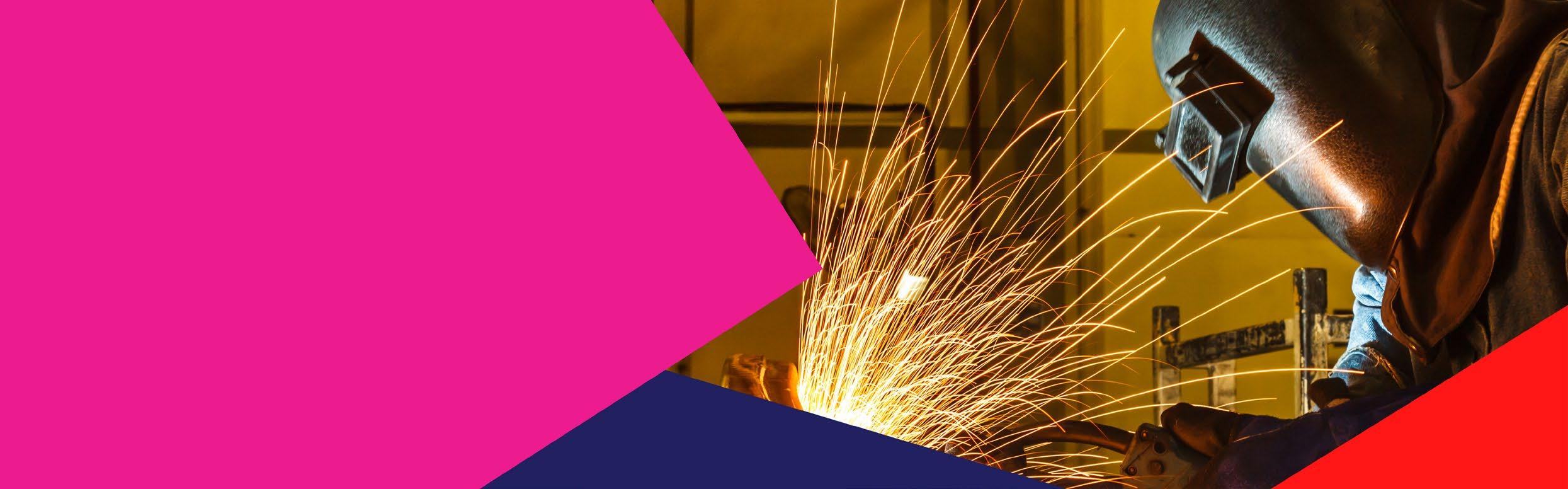
5 minute read
Health & Safety: Five Potential Welding Safety Hazards to Avoid
Welding can and should be considered a safe occupation; when proper precautions are taken, welders have no cause to fear accident or injury. But when safety isn’t taken seriously in the workplace, the risk of a severe incident becomes a real concern. Education is the key to ensuring a safe and productive working environment for everyone. Employers need to invest in thorough and up-to-date training for all their employees to ensure that they understand the risks associated with welding, the mitigation strategies they can use, and the equipment available to prevent accident and injury. Additionally, recognising the risks posed by mental health challenges, and addressing these, is vital to maintaining a healthy workforce.
Weld Australia’s Chief Executive Officer, Geoff Crittenden, believes safety is a critical consideration for welding projects – no matter what scale.
Advertisement
“Welding is a safe occupation when proper precautions are taken. But, if safety measures are ignored, welders and members of the general public face an array of hazards that can be potentially dangerous, from electric shock and electrocution,” he said.
To address safety considerations in the sector, Weld Australia established the Welding Safety Council. The Council enables industry and legislative bodies to work together to minimise the risk of injury and loss of life in the welding and fabrication sector.
“By drawing together key government stakeholders, statutory bodies and industry into a single independent body focused on eradicating welding related injury, the Australian welding industry will be taking a significant step forward in protecting both the general public and welders,” Crittenden said.
While the Council is a step in the right direction, there are several processes that individuals and their respective organisations can follow to ensure increased safety.
Fumes and Gases
Welding fumes and gases contain harmful materials that can be hazardous to an individual’s health. Welders can be exposed to high levels of fumes from welding consumables, or contaminants found in surface coatings. Fumes are generated by heat, which is a common factor in the welding process.
Welding fume exposure may lead to fever, stomach ulcers, and kidney or nervous system damage. In 2017, welding fumes were classified as ‘carcinogenic’, according to the International Agency for Research on Cancer.
It is vital that appropriate strategies are in place to reduce welder exposure to fumes, and prevent the long-term health effects that can result from exposure. All welders should receive training on methods to mitigate the effects of metal fume, including positioning themselves to reduce exposure, and investigating less toxic alternatives where possible.
Local Exhaust Ventilation (LEV) systems capture and extract welding fume at the source and are a proven way of reducing exposure. All workplaces should have fit-for-purpose LEV systems installed and regularly maintained.
Weld Australia has published a range of Technical Guidance Notes, which provide practical advice for industry to follow for fume hazard minimisation.
Electric Shock
Electric shock, or electrocution may occur when a welder makes direct contact with an electrode, a work piece, live parts or though an unearthed tool or cable.
Weld Australia is committed to ongoing education and training for welders. Last year, a virtual forum took place, where 32% of all attendees indicated that they had experienced an electric shock while working with a welding power source.
There are some basic processes that welders and fabricators should undertake to prevent electrocution. Simple actions such as checking that equipment is dry and well maintained, and installing shut down mechanisms such as residual current detectors (RCDs), and ensuring the welding power source has an active voltage reduction device (preferably with an open circuit voltage of 12V DC or less) can save lives.
Ensuring that all employees are equipped with the knowledge and safety equipment required is key to preventing incidents in the workplace.
Non-Compliant Welding Equipment
Welding equipment must be constantly maintained to ensure it operates efficiently and prevents any catastrophic accidents.
Welding safety inspections are critical for undertaking a review of all welding equipment – a ten-minute inspection can prevent serious injuries or fatalities.
“It is important that welders feel empowered to report any unsafe equipment to their supervisor and to ask for new equipment and PPE where it is not provided,” Crittenden said.
Weld Australia recently revised its Daily Inspection and Pre-Start Checklist for welders to assess their equipment, connections, and power sources before they commence a job.
The checklist covers electrical safety requirements and oxy-fuel gas safety requirements.
Insufficient Personal Protective Equipment
Personal Protective Equipment (PPE) provides a safety barrier between a welding practitioner and any dangers that may be present. Insufficient PPE can lead to a range of welding safety hazards.
There are key body parts that should be protected with PPE, including:
• Eyes and face: helmets with a side shield will protect the eyes and skin from exposure to harmful elements. Different shades of lenses are available for different types of welding, and safety glasses can also be worn underneath helmets.
• Feet: leather boots with ankle coverage are essential. Guards may also be worn over shoelaces to prevent materials from entering the boots and protect against falling objects.
Rubber soles should be fitted on all boots.
• Hands: flame-resistant gloves that protect against cuts, burns and electric shock are essential.
• Ears: earmuffs can protect against metal debris, burns, and deafness.
Welders must always wear PPE in optimal condition to prevent an arc flash, or a burn caused by the ultra-violet radiation of electric welding arcs.
Poor Mental Fitness
The work of welders and fabricators requires laser sharp focus and engagement, which is underpinned by a strong mental headspace. However, the statistics paint a different picture.
Around 190 Australians who operate in the construction industry take their own lives each year, which equates to the loss of a construction worker every second day.
Construction workers are also six times more likely to die by taking their own life than by an accident on the job. Currently, the industry is predominantly made up of men, who are also more likely to take their own life than women. In fact, men who die by suicide is double the national road toll each year.
Crittenden said the construction industry has traditionally been an environment where false perceptions of masculinity exist. “Masculine ideals are founded on toughness, control, autonomy and competence. Seeking help, or even admitting a need for help, can be both confronting and challenging for people working or living in such a setting,” he said.
If you, or someone you know needs help, please contact Lifeline on 13 11 14.
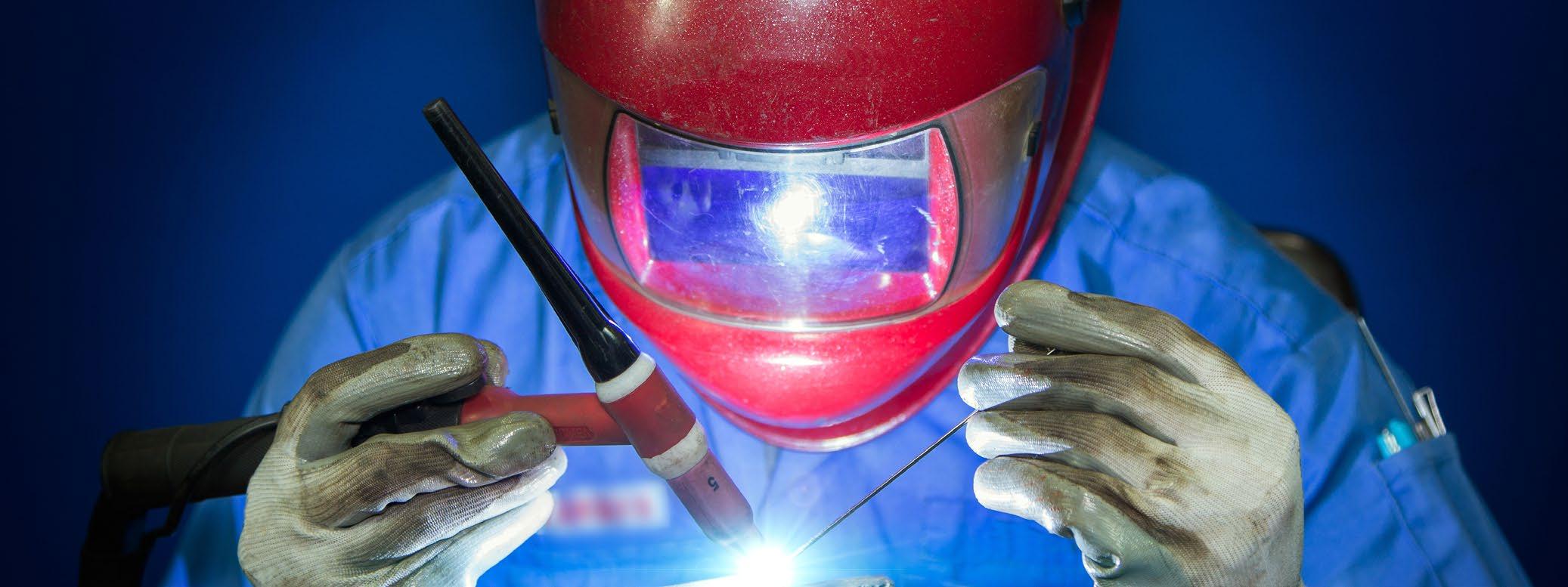