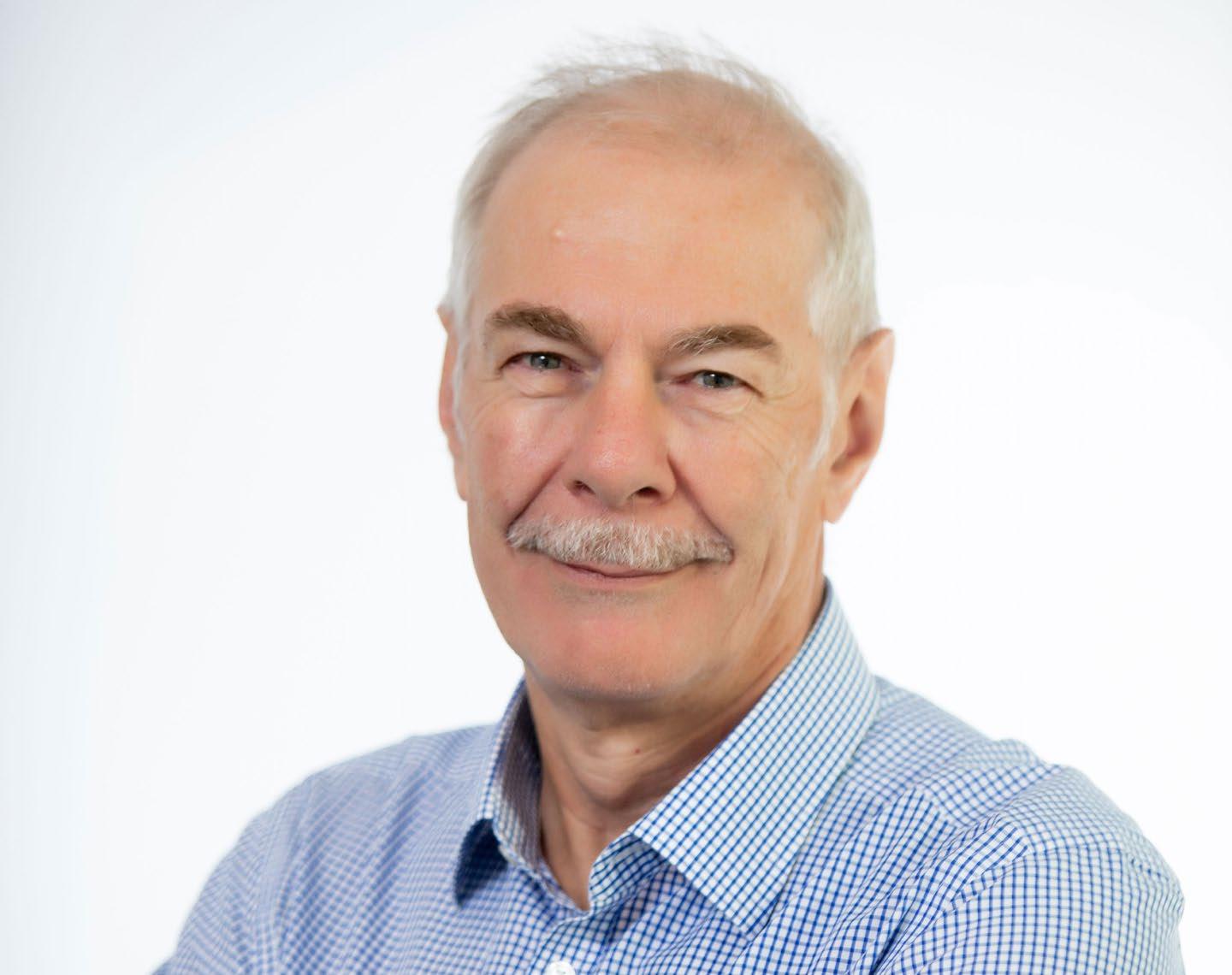
11 minute read
A Message From Weld Australia’s Chair
David Lake (Chair, Weld Australia).
Advertisement
I recently travelled to Tokyo, Japan to represent Australia at the 75th International Institute of Welding (IIW) Annual Assembly and International Conference on Welding and Joining.
An Overview of the IIW IIW is recognised as the largest worldwide network and centre of reference for welding and allied joining technologies. It operates as the global body for the science and application of joining technologies, providing a forum for networking and knowledge exchange among scientists, researchers, industry and educators, and disseminating leading-edge information and best practices.
Researchers, industry, educators, students and young professionals from over 51 countries worldwide are all part of the collaborative working platform of the IIW. Weld Australia is the Australian representative member of the IIW.
Through the work of its Technical Working Units, the IIW’s technical focus encompasses the joining, cutting and surface treatment of metallic and non-metallic materials by such processes as welding, brazing, soldering, thermal cutting, thermal spraying, adhesive bonding, microjoining and additive manufacturing. IIW’s work also embraces allied fields including quality assurance, non-destructive testing, standardisation, inspection, health and safety, education, training, qualification, certification, design and fabrication.
The IIW is a standardising body approved by the International Organisation for Standardisation (ISO) to develop standards in the field of welding and related processes. IIW’s Technical Database constitutes the world’s largest online resource for welding information available today. The most outstanding papers are published in the prestigious journal ‘Welding in the World’ registered in Thomson Reuters Science Citation Index® since 2009.
IIW international education, training qualification and certification programs for welding personnel and companies are recognised worldwide. The systems developed for education and training are paving the way towards one global education and qualification system for welding personnel. Weld Australia is an IIW Authorised National Body (ANB) and an Authorised Training Body (ATB).
IIW Annual Assembly The Annual Assembly provides an opportunity for IIW Technical Commissions and Working Units to meet. There are currently 18
IIW Commissions, each of which is focused on a specific area of interest, from additive manufacturing and power beam processes, through to structural performance of welded joints and pressure vessels, boilers and pipelines.
Weld Australia representatives attended and participated in many of the commissions and have developed contacts from many parts of the world, with Weld Australia having access to the working of all 18 Commissions. The Chair of Weld Australia’s Qualification, Certification and Standards Committee, Doug Hawkes, is the elected board member to the IIW IAB representing Oceania and South Africa, where he has been very active over the last couple of years.
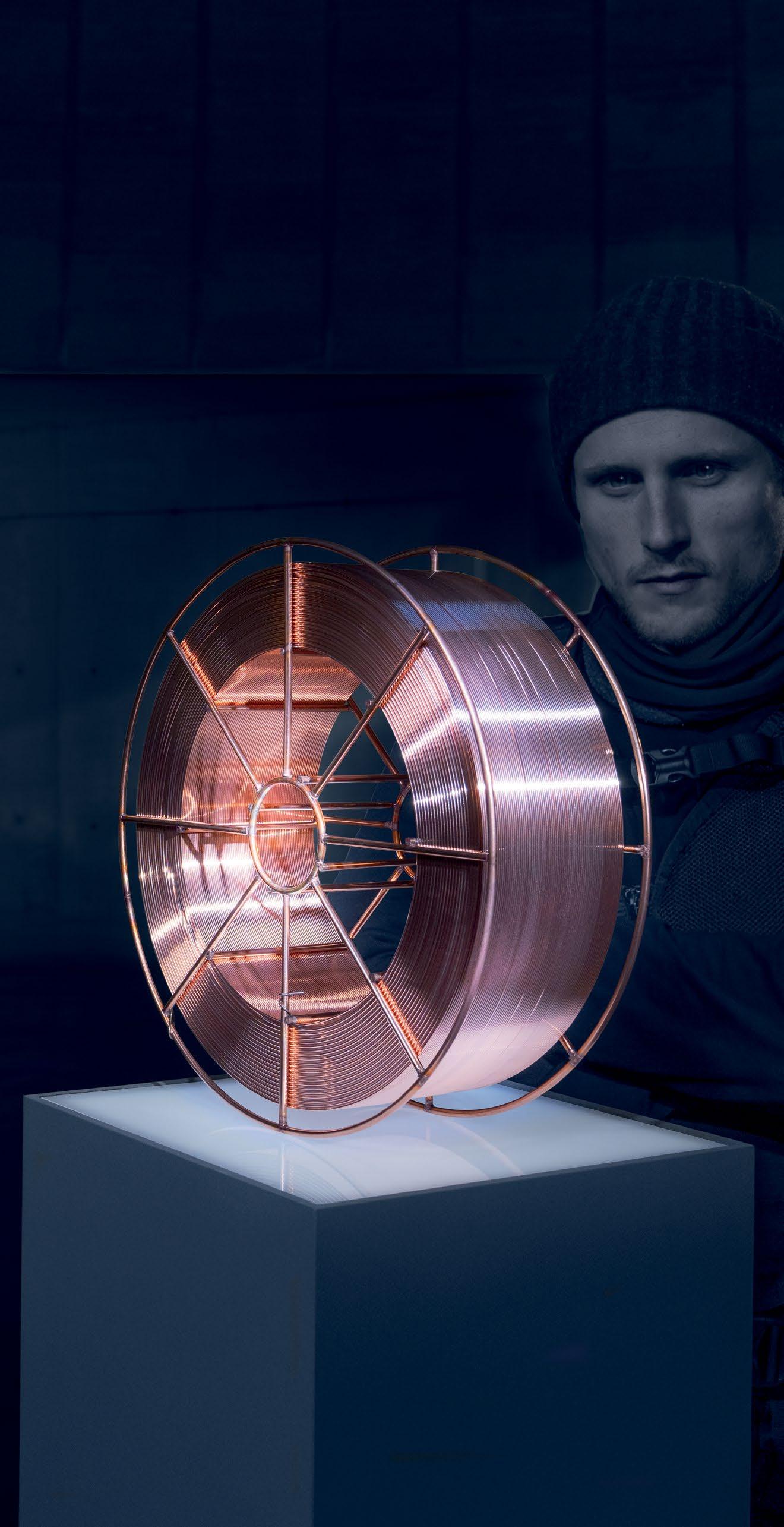
I’d also like to congratulate Bruce Cannon (Principal Welding Engineer, Weld Australia) on winning the IIW 2022 Thomas Medal. Bruce was presented with the award at the Opening Ceremony of the Annual Assembly. (For further details, see the article on page 40.)
IIW International Conference The theme of this year’s International Conference was Innovative Welding and Joining Technologies to Achieve Carbon Neutrality and Promote Sustainable Development. The program featured a range of engaging presentations on topics such as welder training, welding automation, laser processes, non-destructive testing, metallurgy, new materials, artificial intelligence, digital transformation, additive manufacturing and more.
The plenary talks given by both a minister and a respected member of the Japanese government, showed the rest of the world how seriously they are taking the need for carbon neutrality and the importance they assign to having a thriving welding industry to develop off shore wind farms and also in obtaining green Hydrogen from Australia.
The 2022 Japan International Welding Show was held in conjunction with the IIW International Conference. Attracting over 100,000 attendees and hundreds of exhibitors, the Show featured exciting demonstrations of the latest welding technology.
by Böhler Welding
THE BEST FOR THE BEST.
diamondspark seamless cored wires
diamondspark. A cored wire of highest quality and performance. Designed by the leading pioneers in filler materials, diamondspark wires are tailored to match the highest requirements for demanding applications. diamondspark – the best seamless cored wires for the best welders.
Curious? See the full video OPERATION: DIAMONDSPARK online on our website!
Weld Australia has released the results of its 2022 Member Survey. The results demonstrate that significant concerns remain for Australia’s welding industry. In particular, Australia’s fabricators are being forced to turn down work due to a severe shortage of skilled welders.
According to Geoff Crittenden (CEO, Weld Australia), “Distributed in June 2022 and completed by approximately 140 companies, our 2022 Member Survey indicates that skills shortages, local content and sustainability remain high on the agenda for the welding industry.”
“When asked what they are most concerned about, almost 64% of senior managers cited lack of skilled staff in an extremely constrained recruitment market (see Figure 1). This comes as little surprise, with Australia facing a looming shortage of skilled welders—70,000 additional welders will be needed by the end of the decade.”
“With a considerable volume of work being onshored in the wake of international supply chain disruptions, most Australian fabrication companies are so strapped for skilled welders that they are working at anywhere between 30% and 50% of their full capacity. They are being forced to turn down jobs because they simply don’t have the manpower to complete the work. This is having a major impact on production and causing delays throughout downstream industries including building and construction, mining, oil and gas, and manufacturing,” said Crittenden. It is little wonder that half (see Figure 2) of survey respondents have a pipeline of work that extends for six months or longer—this protracted pipeline is necessary in the face of these ongoing skills shortages. By way of context, this is a marked increase on Weld Australia’s 2020 member survey results. In the wake of the COVID-19 pandemic, the most common answers were a pipeline of work that extended less than one month (at 28%), one month (19%), and two months (16%).
Given the concern over Australia’s looming skills crisis, it makes sense that 95% of respondents support the concept of free TAFE, increased funding to upgrade TAFE facilities, or both initiatives. Clearly, the welding industry is looking to the government to help increase the supply of skilled labour over the coming years.
Inflation & rising costs
22.7% Reliability & affordability of power supply 4.5%
Lack of skilled labour
63.7% Over 6 months 27.3% Less than 1 month 9.1%
1 month 4.6%
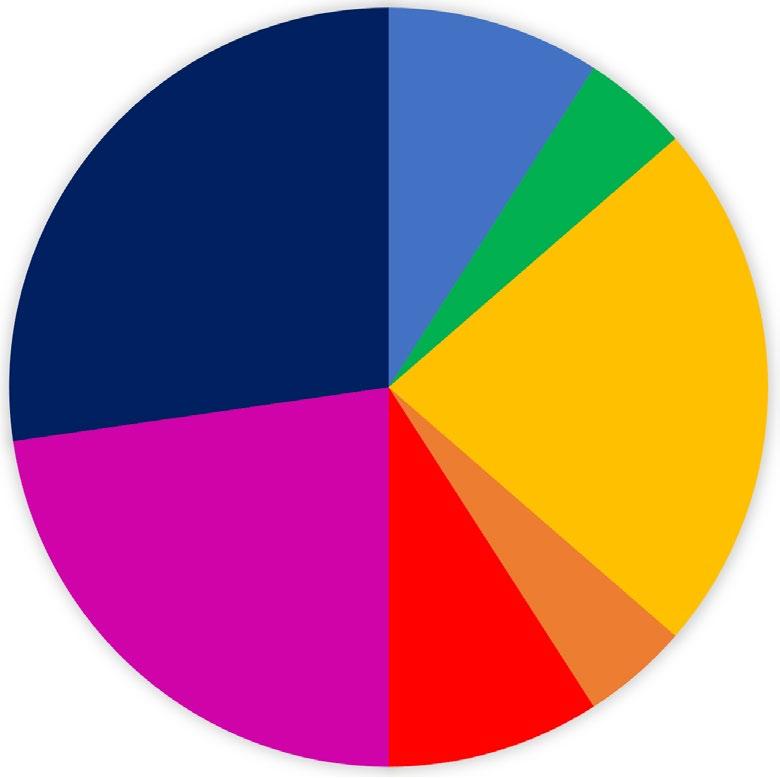
Weak international supply chains 9.1%
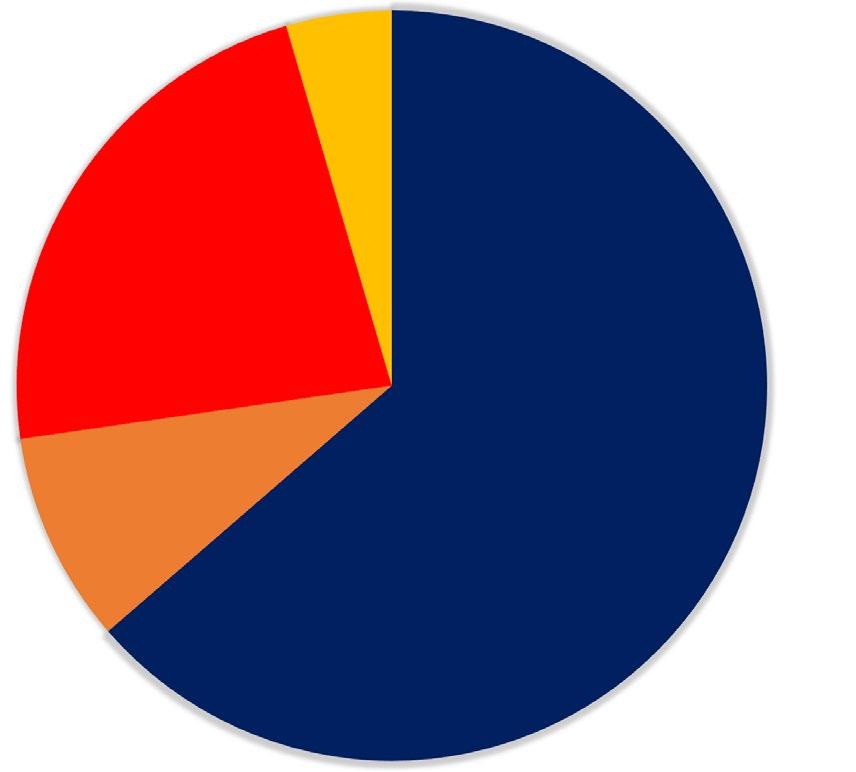
Figure 1. As a business owner, or senior manager, which issue are you most concerned about?
2 months 22.7%
6 months 22.7%
4 months 9.1%
Figure 2. How many months ahead does your pipeline of work extend?
3 months 4.5%
“Our members are also investing in their own welder training programs. BHP, Komatsu, JRS Manufacturing, Maxi-Trans and Precision Manufacturing Group have all established their own schools. While industry appreciates the rollout of government-funded TAFE places, it remains to be seen whether this initiative will translate into high completion rates. Moreover, while encouraging more students into TAFE is always a positive, government spending also needs to focus on resources for TAFEs, teachers and equipment—TAFEs need the right tools to teach this sudden influx of students,” said Crittenden.
Industry is also investing in advanced welding technology to help overcome skills shortages. Over 28% of respondents indicated that their company or the company they work for has purchased robots or cobots, and 25% has invested in Industry 4.0 capabilities (see Figure 6). A range of other types of technology was also mentioned, from drones and automated welders, through to various software solutions.
Despite the skills shortages, local procurement and content targets remain top of mind for the welding industry. 100% of respondents confirmed that they would support Federal and State Government policies to increase Australia’s Survey Respondent Demographics
The majority of survey respondents were based in Queensland (at 28%), followed closely by New South Wales (23%), Victoria (19%) and Western Australia (16%).
The largest age group was over 65, accounting for 16% of respondents. In line with industry trends, 78% of respondents were over the age of 40 (see Figure 3).
The most commonly cited highest level of education was an apprenticeship or vocational training at 30%, followed by International Welding Specialist at 23%, Bachelor Degree at 13% and Masters Degree at 9%.
Salaries are relatively healthy compared to Australia’s average wage (of $67,860 per annum); 20% of respondents indicated that their salary is between $100,000 and $125,000, and 17% take home over $150,000 per annum.
Overwhelmingly, respondents are employed full-time (72%). Another 16% indicated that they are business owners and 9% are either employed part-time or as a sub-contractor. The remaining 3% are retired. At 23%, the majority of respondents have worked for their current employer for over 20 years (see Figure 4).
Over 51% of respondents work for a business in the fabrication, manufacturing or engineering industry, 12% work for a business in the mining and resources industry, 10% in the education and training industry, and 7% in testing and NDT. The vast majority of these businesses are quite large; 32% of respondents indicated that the company they work for has over 500 staff.
However, SMEs were also well represented, with 16% of respondents confirming that the business they work for has under 10 staff members (see Figure 5).
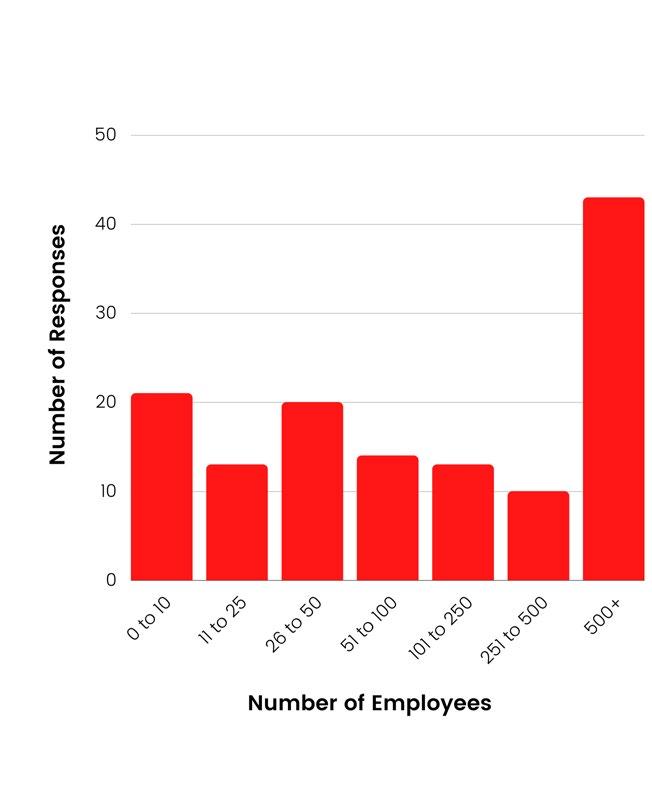

Figure 3. What is your age? Figure 4. How long have you worked for your current employer? Figure 5. What is the size of your business, or the business you work for?


share of fabricated steel product to at least 75% as part of a joint government-industry plan to grow the manufacturing industry.
“Importantly, whether it is imported or locally manufactured, all fabricated steel erected in Australia must comply with Australian Standards. Weld Australia is committed to ensuring that no Australian lives are lost through an accident caused by noncompliant welding, without causing undue regulatory burden on industry. We firmly believe in quality welding for structural safety,” said Crittenden.
Inflation and rising costs were also of concern for approximately 23% of respondents, followed by weak international supply chains (9%) and reliability and affordability of power supply (4%).
Environmental Sustainability and Corporate Responsibility Australia is rapidly moving from carbon fuelled power generation to a renewable energy system. In June 2022, Prime Minister Anthony Albanese announced more ambitious climate targets. Albanese pledged to cut carbon emissions by 43% from 2005 levels by 2030, up from the previous government’s target of between 26% and 28%. Given these targets, private companies will play a key role, making sustainability a priority for many businesses. As such, our 2022 member survey asked a series of environmental sustainability focused questions.
Welders are environmentally responsible. 30% of respondents support the target of zero emissions before 2050; 20% prefer cutting emissions by 35% by 2030; and another 17% support cutting emissions by 43% by 2030. In addition, 74% of respondents would support a Federal Government package to help employees transfer from carbon intensive to carbon free industries.
Clearly, Australia’s welding industry is already taking steps to reduce its carbon emissions. While 41% of respondents have already installed solar panels to supplement power supply, another 53% have installed LED or sensor lighting, 46% have waste reduction programs in place, 46% operate recycling, up-cycling or repurposing programs, and 13% have a net zero carbon plan in place.
When asked if an electric or hybrid ute was available in Australia at a competitive price would you buy them for your company or employees as fleet cars, 50% of respondents answered in the affirmative. Interestingly, 63% of respondents would buy an electric or hybrid UTE for themselves.
Corporate responsibility remains a growing area of focus for the welding industry. Over 63% of respondents indicated that they have initiatives aimed at improving opportunities for women; 63% promote opportunities for apprentices and trainees; 63% have diversity and inclusion initiatives in place; 59% have mental health and fitness initiatives in place; and 31% have a Reconciliation Action Plan.
Weak
18.2% Very Strong 27.3%
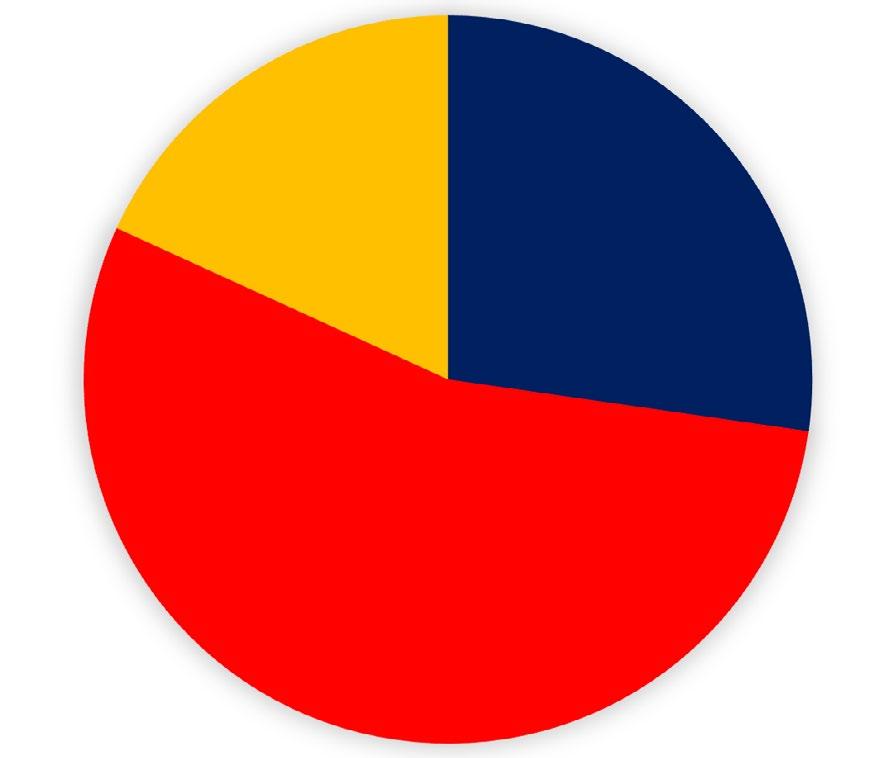
Figure 6. Has your business, or the business you work for, invested in advanced welding technology? Figure 7. How would you rate the prospects of your business over the next six to 12 months?
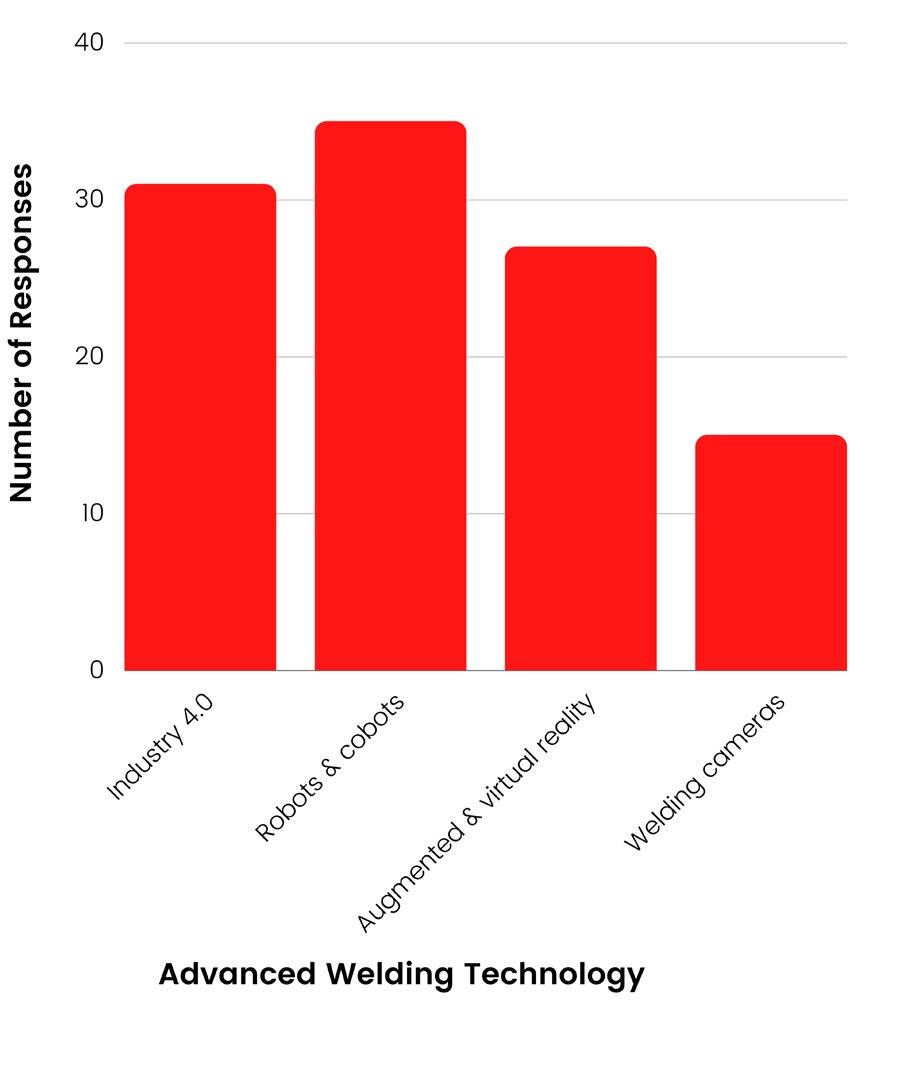
Strong 54.5%