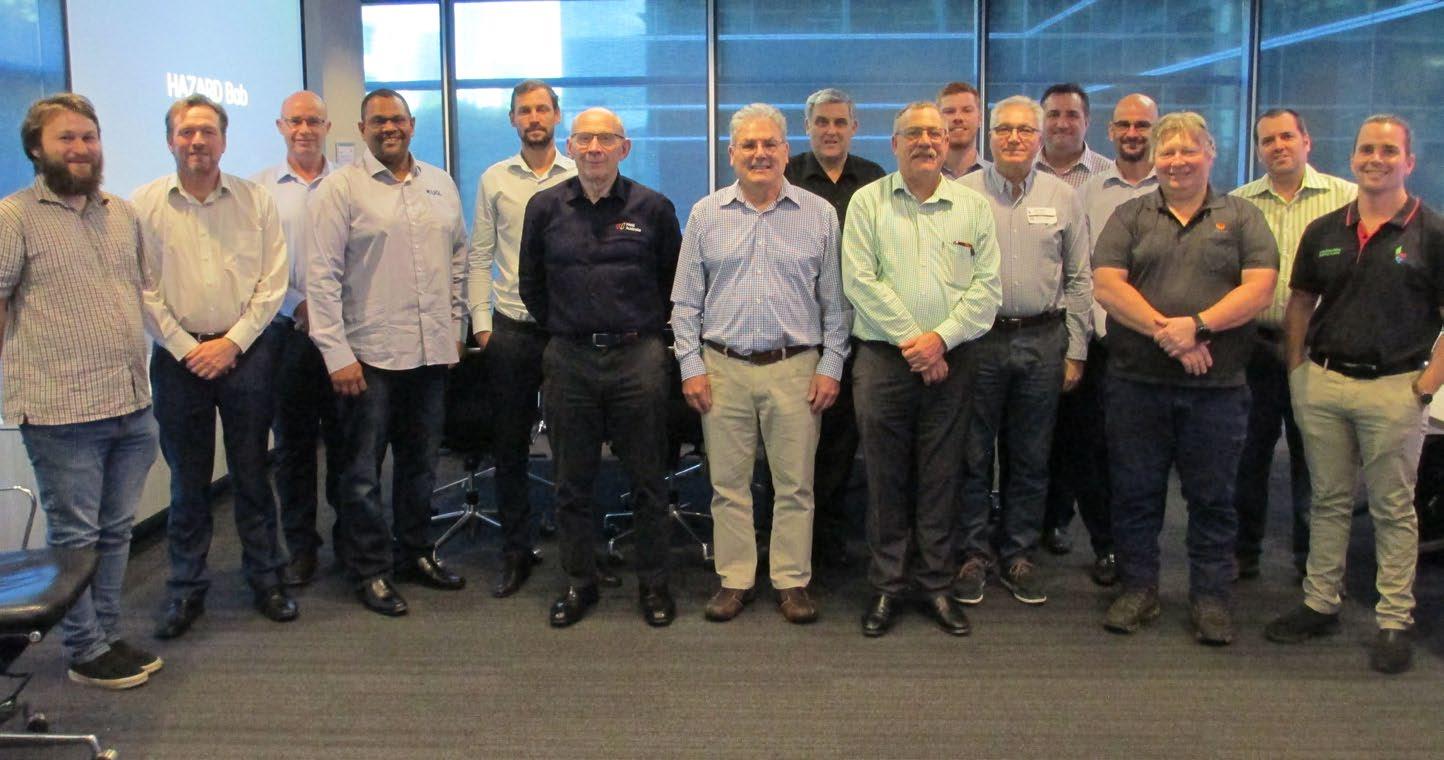
7 minute read
An Update from Weld Australia’s Industry Groups
Weld Australia’s Industry Groups provide a forum for technology transfer and research and development, linking members with industry and research organisations. Weld Australia works with Technology Network members to ensure they remain diverse and resilient in the ever-changing and increasingly challenging global markets.
POWER GENERATION INDUSTRY GROUP Meetings of the Power Generation Industry Group were held in the offices of CS Energy (Brisbane) over 22 and 23 June 2022. A huge vote of thanks to CS Energy who provided excellent facilities, catering and support for the IT systems required to manage the meetings and online attendees.
Advertisement
The Power Generation Industry Group comprises: 1. Boiler Industry Group 2. PG9 Project 3. Process Safety Industry Group 4. Asset Integrity Board
There were four meetings held over two days. The meetings covered a wide range of subject material with many highly detailed presentations.
A summary of each of the meetings is outlined below. normal operating conditions and requirements.
CS Energy also provided an overview of a failure in a reheater cross over tube at Kogan Creek Power Station. The root cause was found to be excessive weld root concavity on one of the connecting welds. These welds were undertaken at the time of manufacture through a robotic welding process. The implication was that all welds would have the same fault.
Boiler Industry Group With 35 people in attendance, the meeting was opened by Geoff Crittenden (CEO, Weld Australia). Geoff provided an industry update, touching on the nation-wide shortage of skilled welders and the MEM2.0 Learning Resources that Weld Australia is developing in conjunction with TAFEs. Geoff also detailed the issues related to wind tower manufacture and the import of towers considered to be non-compliant with Australian Standards. Weld Australia is calling for local manufacture and compliance with Australian Standards.
CS Energy gave a presentation on the dry out and preservation procedures following the major turbine incident at the Callide C4 unit which occurred on 25 May 2021. This process was subjected to a wide range of conditions, issues and constraints arising from the turbine incident which required actions well beyond Energy Australia gave a presentation on layup practices for wet and dry storage of boilers. These practices had been developed at the Mt Piper Power Station covering a number of plant requirements, scenarios and layup durations.
Les Sabo (Managing Director, Uneek Bending) provided an overview of Uneek Bending, which specialises in the bending of tubes and other types of steel. Les also discussed the Acoustic Gas Temperature Measurement System (AGAM) which has been developed by Germanbased Bonnenberg & Drescher. This system uses an array of acoustic transmitters and microphones to measure time differences between sending and receiving and so accurately determine the temperature of flue gases and similar. This is particularly applicable to boiler flue gas exit ducts.
Wayne Hill (Principal Engineer Boilers and Pressure Parts, EnergyAustralia) spoke about an investigation into post
outage boiler tube leaks after major unit outages. One possible scenario was debris which can accumulate in boiler tubes and orifice plates leading to flow starvation and tube failure. This led to a discussion on the use of rice paper during boiler tube weld repairs and the need to use the correct type of paper for draft reduction during weld repairs.
HRL is currently working on a project to review flexible operations for Power Generation Industry Group member power stations. This mode of operation is extremely important, particularly as the industry is transitioning towards net zero carbon by 2050 and phasing out coal fired power stations. HRL’s presentation focused on how a process for flexible operations may be implemented.
The meeting concluded with a discussion of current issues and future directions over the next five to 10 years. The discussion focused on the current market and transition towards the closure of coal fired power stations.
PG9 Project The Power Generation Number 9 Project (PG-9) is being conducted within the Boiler Industry Group. The objective of the project is to develop a database of certified weld procedures which will then be accessible by the project members. The project is funded and managed by the members.
The database is currently well developed and populated. The logistics for access and procedures for future qualifications and certifications are issues being addressed. PG-9 project members conducted a progress meeting.
Process Safety Industry Group With over 30 people in attendance, Geoff Crittenden opened the meeting. This was followed by an open discussion around baseline audits. A number of issues were raised, from skills shortages, process safety, welder certifications, chartered engineers, and the need for process safety to be accompanied by cultural change.
Wade Underhill (CS Energy) gave an update on the progress of implementing process safety at CS Energy. A rigorous program of training is being undertaken across the entire CS Energy organisation, including a separate training package aimed at company leaders. While establishing the systems is easy, the implementation of training and cultural change is hard.
Ryan James (Director, OXT Group) spoke on the topic of risk assessment, focused on improved performance monitoring, and risk control within a commercial environment. Ryan emphasised that process safety cannot succeed without leadership, or cultural change.
Ian Rawlings (Chief Mechanical Engineer, CS Energy) gave a presentation on a near miss incident that occurred on the Callide B2 precipitator inlet duct. Operational conditions caused the dust loading in the duct to accumulate and overload one of the duct supports. The duct did not suffer a failure of the support but was considered to be a near miss.
There were many learnings from this incident, including: • Gas velocities in ducts • Throttling of outlet dampers • Maintenance of precipitators • Process safety risks to be fully assessed in conjunction with health and safety risks
Industry Group members then discussed general safety incidents and learnings. The first incident was an issue with a vertical 9m duct that ran from the top of a boiler to an air heater. A crack had developed in the duct, and an expansion joint was found to be locked up due to a build up of ash. In addition, constant load hangers were found to be out of adjustment. A major failure could have occurred if the crack had developed.
The next incident raised was the discovery of asbestos-looking material around some thermocouples during boiler maintenance. The asbestos register indicated that asbestos had been removed in the area, but did not detail the particular level and location of where the asbestos had been removed. The key takeaway from this incident was that staff need to be trained to be aware of asbestos.
An issue which occurred with the controls on some newly installed tanks was then reviewed. There was a mismatch on the valve identification on the vessels. Testing was carried out on components only and the mismatch was not identified. This underscored the importance of thorough testing of all aspects of tanks.
The TransGrid Tallawarra switchyard transformer failure was raised as a prime example of a catastrophic failure.
Monorails, cranes and lifting equipment are often over looked, but need ongoing maintenance and certification. A near miss was discussed which emphasised the need for ongoing maintenance and certification.
Finally, the Process Safety Good Practice Guide is nearing completion but requires final editing. This is to be undertaken by a smaller committee and presented at the next meeting.
Asset Integrity Board The Asset Integrity Board members discussed high level issues affecting each of the companies, with a focus on flexible and low load operations. The transition from coal will not happen overnight. It will take time and require specialist knowledge in areas like BESS, pumped storage, wind and hydrogen. All members agreed that mentoring and skills development were of the utmost importance.
A range of other issues was discussed, from skills shortages, aging plant, failure modes, and the use of non-destructive testing.
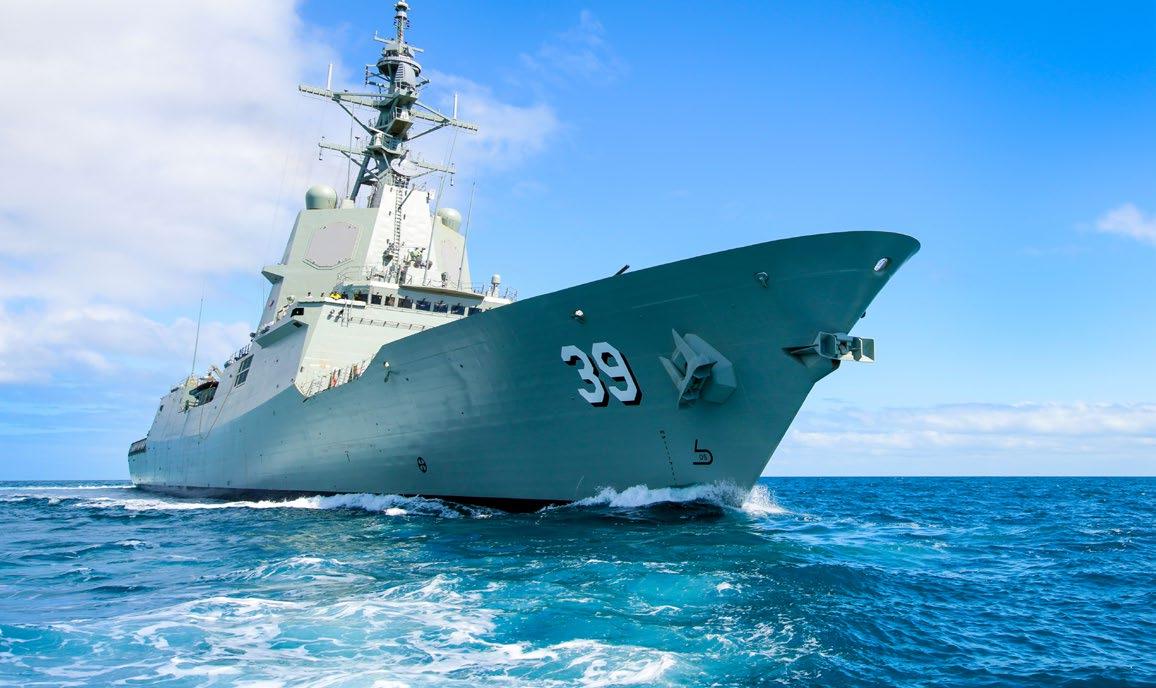
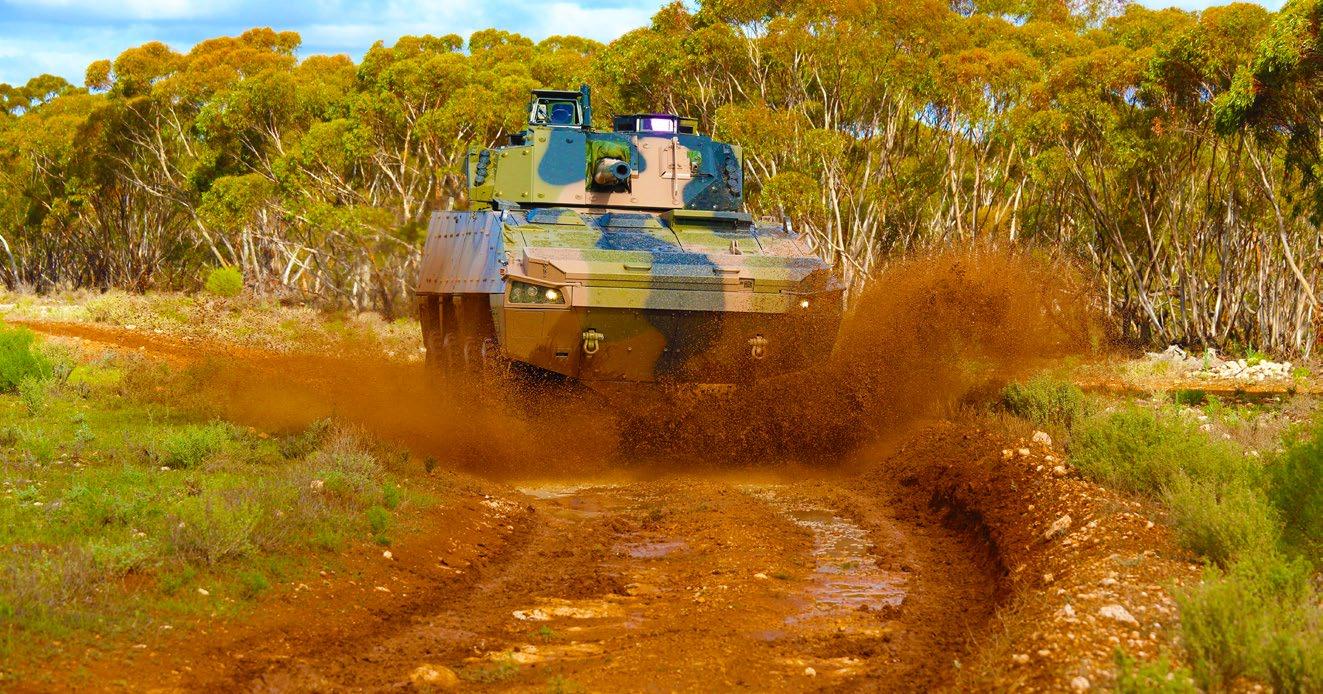
DEFENCE INDUSTRY NETWORK Weld Australia is pleased to announce that it has signed a Memorandum of Understanding (MoU) with the Australian Industry and Defence Network (AIDN).
Together, Weld Australia and AIDN will collaborate on matters related to their members’ commercial participation in defence projects with particular reference to fabrication and advanced manufacturing.
To achieve these objectives, Weld Australia and AIDN will engage in joint events and activities, provide advice and communications on the development and management of a Defence Industry Network and undertake joint promotional activities. and welding issues, discussing supply chain issues and solutions and accessing Weld Australia training, resources and specialist personnel.
Weld Australia will organise and facilitate all meetings, with agendas and areas of interest driven by members. Areas of Proprietary or Confidential Information will be recognised and appropriately managed by all participants.
Further Information For details, contact: Andrew Davies (Manager Technical Industry Networks) on 0438 428 966 or a.davies@weldaustralia.com.au
Interested in Joining? As a result of COVID and a certain amount of industry turbulence, the Weld Australia Defence Industry Network experienced a hiatus. It’s now back—bigger and better than before. The Defence Industry Network will focus on companies who are either already operating in the defence supply chain, or have ambitions of joining. Our aim is to ensure that contractual commitments to Australian Industry Content and Indigenous Participation are honoured.
Membership of the Defence Industry Network will be free of charge for all Weld Australia Premium Corporate Members. Just some of the benefits include: networking with others in the defence industry, addressing technical