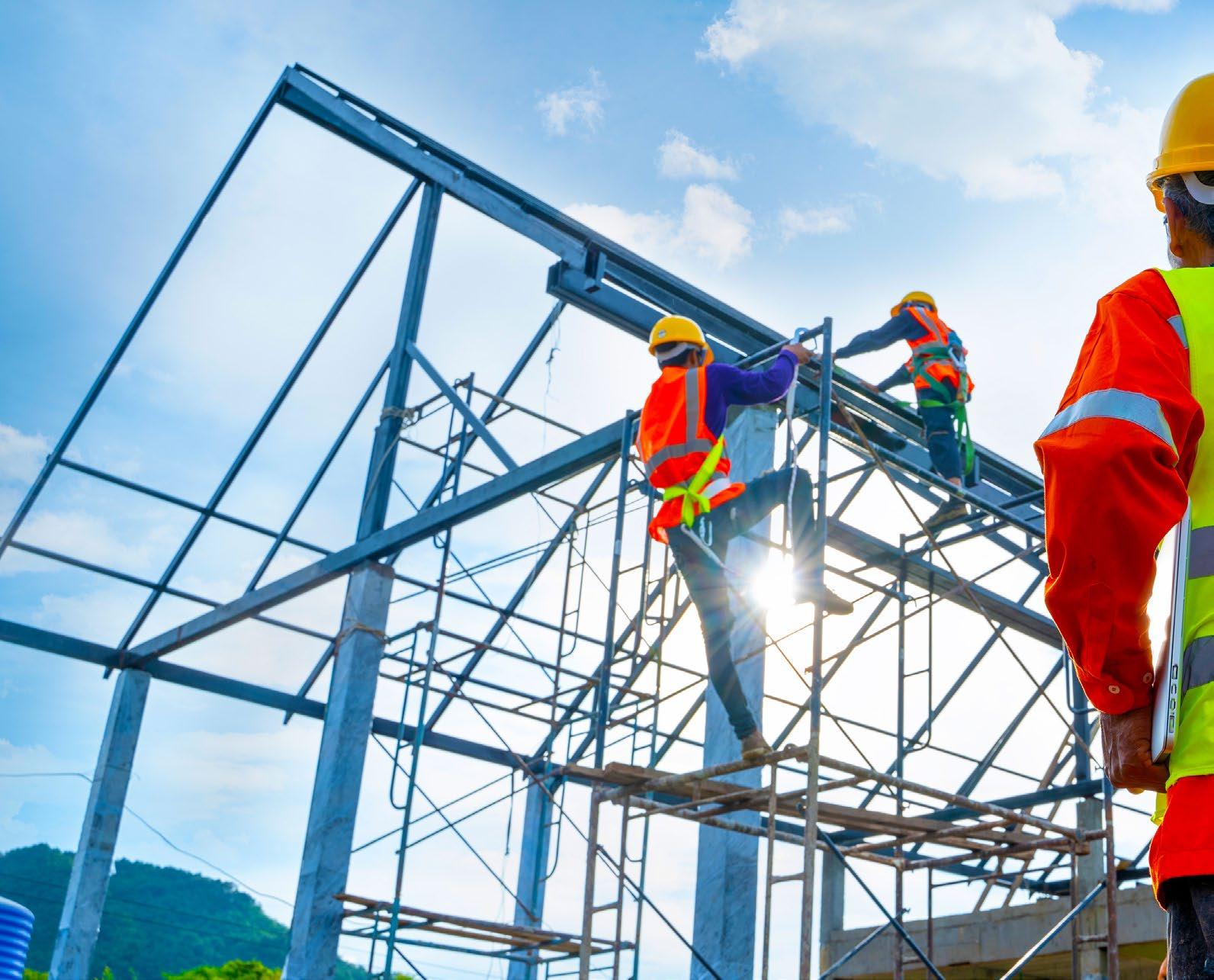
53 minute read
Business Essentials
UNDERSTANDING THE RIGHTS AND RESPONSIBILITIES OF CONTRACTORS
Determining whether your workers are employees or contractors is important—it affects your tax, superannuation and other obligations. And, in some cases, penalties and charges may apply if you get the classification wrong. Contractors run their own business and sell their services to others, unlike employees who work in someone else’s business. Contractors generally use their own processes, tools and methods to complete the work. They usually negotiate their own fees and working arrangements, and can work for more than one client at a time.
Advertisement
The Differences Between Employees and Contractors An employee works in your business and is part of your business. A contractor is running their own business. Published by the Australian Taxation Office (ATO), the table opposite outlines six of the factors that, taken together, determine whether a worker is an employee or contractor for tax and superannuation purposes.
If you’re still not sure, you can use the ATO’s Employee or Contractor Decision Tool to work out if your worker is an employee or contractor for tax and superannuation purposes. Simply answer questions about the working arrangement and you’ll generate a report you can keep for your records. If you answer each question accurately and honestly, you can rely on the results.
It’s important to note that some workers are always treated as employees, including: • Apprentices • Trainees • Labourers • Trades assistants
Apprentices and trainees undertake both work and recognised training to get a qualification, certificate or diploma. They can be full-time, parttime or school-based and usually have a formal training agreement with the business they work for. This is registered through a state or territory training authority or completed under a relevant law. In most cases Labour Hire or On-hire If you hired your worker through a labour hire or on-hire firm and pay that firm for the work undertaken in your business, your business has a contract with the labour hire firm and they are responsible for pay as you go (PAYG) withholding, superannuation and fringe benefits tax obligations.
Labour hire firms may be called different names, including recruitment services or group training organisations. They will refer to your business as the ‘host employer’.
they are paid under an award and receive specific pay and conditions. You must meet the same tax and superannuation obligations as you do for any other employees.
Companies, Trusts and Partnerships An employee must be a person. If you’ve hired a company, trust or partnership to do the work, this is a contracting relationship for tax and super purposes. The people who do the work may be directors, partners or employees of the contractor but they’re not your employees.
DIFFERENCES BETWEEN EMPLOYEES AND CONTRACTORS
Factor
Ability to subcontract
Basis of payment Employee
The worker can't subcontract or delegate the work – they can't pay someone else to do the work. The worker can subcontract or delegate the work – they can pay someone else to do the work.
The worker is paid either: • For the time worked • A price per item or activity • A commission The worker is paid for a result achieved based on the quote they provided. A quote can be calculated using hourly rates or price per item to work out the total cost of the work.
Contractor
Equipment, tools and other assets
Commercial risks • Your business provides all or most of the equipment, tools and other assets required to complete the work, or • The worker provides all or most of the equipment, tools and other assets required to complete the work, but your business provides them with an allowance or reimburses them for the cost of the equipment, tools and other assets. • The worker provides all or most of the equipment, tools and other assets required to complete the work • The worker does not receive an allowance or reimbursement for the cost of this equipment, tools and other assets.
The worker takes no commercial risks. Your business is legally responsible for the work done by the worker and liable for the cost of rectifying any defect in the work. The worker takes commercial risks, with the worker being legally responsible for their work and liable for the cost of rectifying any defect in their work.
Control over the work Your business has the right to direct the way in which the worker does their work. The worker has freedom in the way the work is done, subject to the specific terms in any contract or agreement.
Independence The worker is not operating independently of your business. They work within and are considered part of your business. The worker is operating their own business independently of your business. The worker performs services as specified in their contract or agreement and is free to accept or refuse additional work.

What Happens if Employees are Treated as Contractors? It’s against the law for a business to incorrectly treat their employees as contractors. Businesses that do this are illegally lowering their labour costs by: • Not meeting their tax and super obligations • Denying workers their employee entitlements
Businesses that behave this way can often undercut their competitors and obtain an unfair competitive advantage. Businesses also risk receiving penalties and charges, including: • PAYG withholding penalty – for failing to deduct tax from worker payments and send it to the ATO • Super guarantee charge, made up of: • Super guarantee shortfall amounts – the amount of super contributions that should have been paid into a complying fund • Interest charges • An administration fee • Additional super guarantee charge of up to 200%.
In addition to the super guarantee charge – which imposes nominal interest and an administrative charge in all cases on top of the super guarantee shortfall – the ATO can impose additional penalties of up to 200% of the super guarantee charge.
For further information, visit the ATO website: https://www.ato.gov.au
Disclaimer: this article is for informational purposes only. You should consult a professional for advice that is directly related to your business.
WOMEN IN WELDING:
First year apprentice Boilermaker Haylee Megahey, 19, is one of three new apprentices who joined Bradken’s Australian-based Mining Services team in 2022, working at the company’s Mt Thorley workshop in the historic Hunter Valley mining region of New South Wales.
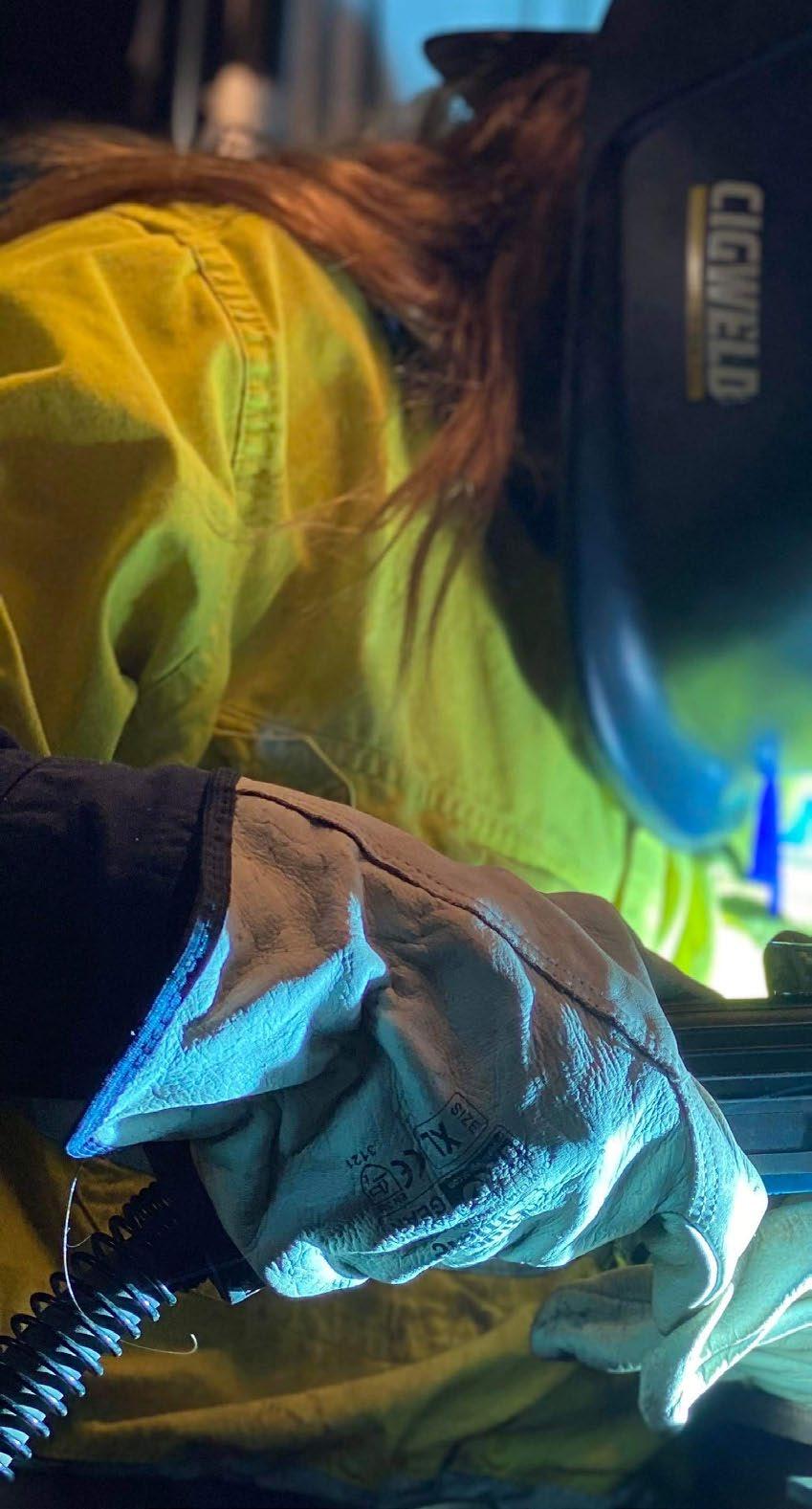
Through her younger years, Hayley aspired to be a teacher and so after leaving school she initially gained certification and began working in early childcare. But after a year she started to feel a pull towards something very different and, thanks to an informal introduction to the Boilermaking trade from her partner, she caught the welding bug and hasn’t stopped since.
Photo: Haylee Megahey, hard at work.
Celebrating 100 years in operation this year, Bradken has a proud history of supporting fresh tradespeople, and in particular welders, through their apprenticeships and into their new careers. The company has an almost 20 year partnership with established group training organisation MIGAS (Manufacturing Industries Group Apprenticeship Scheme), through which Haylee and Bradken made their connection.
Her boss, Mining Services Manager for Bradken, Darryl Pyne, said despite only having been part of the team for six months, Haylee was making the most of every opportunity put in front of her and has made a place for herself amongst her more experienced colleagues.
“For this old boilermaker, seeing Haylee thrive and be interested and curious and hungry to learn the trade makes me very proud indeed. It’s a privilege for us to be hosting someone that knows the value of listening and learning from those around her and really soaks all that knowledge in. Her attitude has earned her the respect of the whole team and I feel she’s well on her way to becoming an exceptional welder.”
Bradken has a number of women welders working at its sites around the world, including the ‘A Team’, six highly skilled welders based in Bassendean, Western Australia, who are regarded as the best-of-the-best welders across the company. Haylee is the newest addition to this talented group. She took time out to answer some questions about her welding career so far.
Can you describe your job? At the moment my job is to learn! I’m about half way through the first year of my apprenticeship at Bradken’s Mining Services workshop in Mt Thorley and I’m really enjoying the experience so far. I work on a lot of different types of projects in the workshop, with the help of the Leading Hands and other tradesmen, but my tasks mostly include welding wear plates to mining size truck trays, excavator buckets and shovel jaws, grinding and small fabrication jobs. I also try to get involved in as many other aspects of the operation as I can, like being on the site safety committee.
What inspired you to choose a career in welding? I’ve always had a passion for learning new things and so I knew I wanted to do something that would challenge me. Coming out of childcare I knew I wanted to go down the trade path, something more hands-on as I do much better learning in a more practical ‘doing’ environment, but wasn’t sure which one was right for me.
I came across welding through my partner. He’s a welder and would often be working on things at home and suggested I give it a try. So, I did and straight away I knew I had to pursue a career in it.
Why do you think women should consider a career in welding? I think women should consider Boilermaking as a career path if they are keen on learning new things, and aren’t afraid of getting dirty and

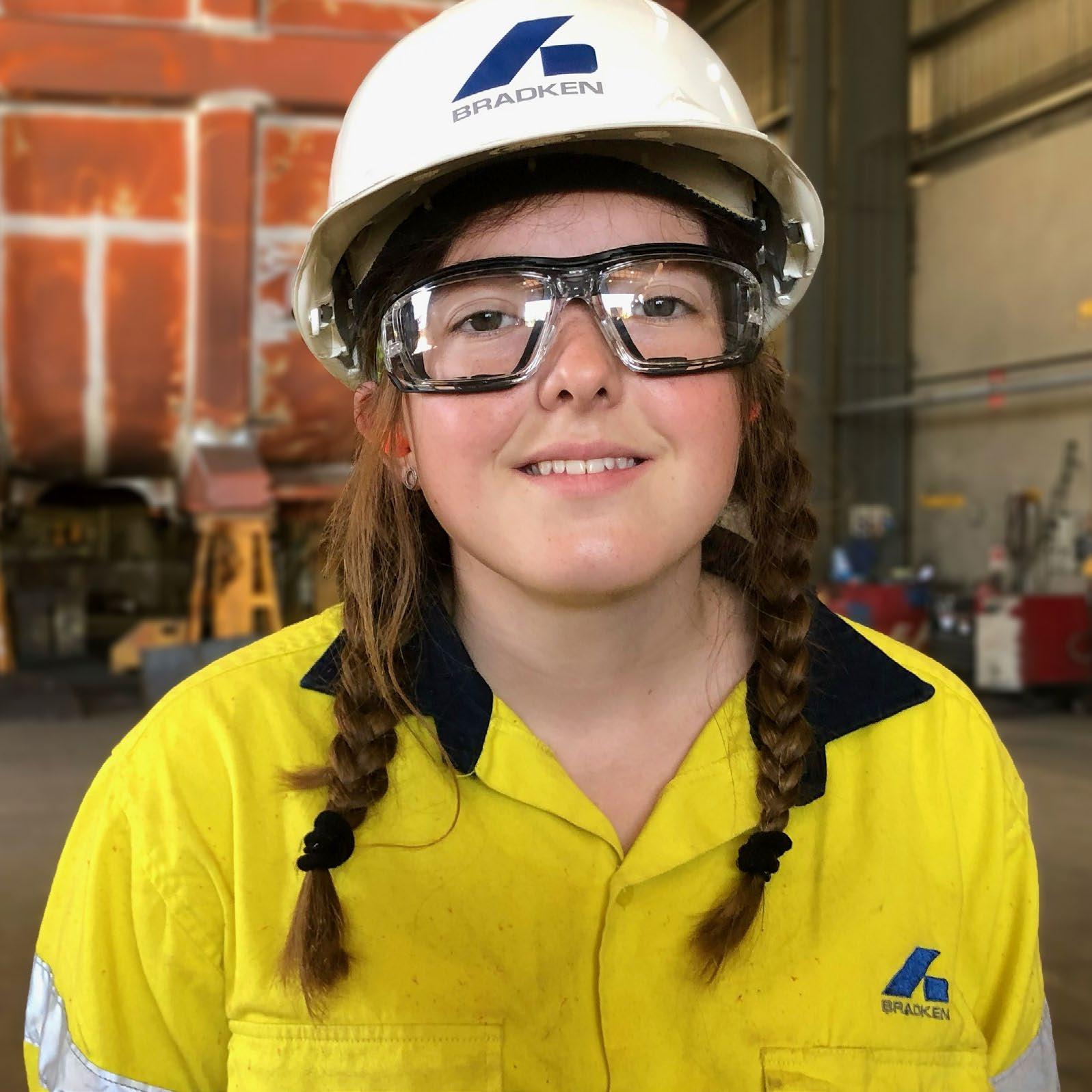
Photo: Haylee Megahey, a first year Boilermaker apprentice at Bradken.
picking up the tools. Being Bradken’s only female apprentice at the moment, I want to encourage other women to think about this trade and about welding in general as an option for them. As women we’re just as capable as anyone else, it’s all about the willingness to learn – you do well at things when you’re passionate about them.
Do you have any advice for women considering a career in welding? I say go for it! Don’t be worried about getting messy, or messing up because that’s part of the learning process. Just give it your all and have fun. Make sure you ask a lot of questions as learning from other people gives you a better understanding of the trade.
My Bradken teammates have given me a lot of support. From the start they’ve been willing to share their knowledge with me and have never hesitated or doubted me when I’ve asked to try something new, making me feel comfortable and confident that this was the right career move for me. How have you found working in a traditionally male-dominated industry? I’ll admit, at first I was a bit nervous about taking on a mostly male trade and joining an all-male team, but it turns out that was just a fear of the unknown based on an out-of-date idea about what the industry’s like.
Everyone at Bradken has been so welcoming and willing to help and I know they want me to become the best tradesperson I can be. All I can say is work hard and we can be just as successful as anyone else in this trade.
What is the most interesting project you’ve worked on? A lot of the projects I work on are interesting as most are fairly new to me and each one is different to the next, even if only slightly. I’m really enjoying the fabrication tasks as they’re usually a bit more difficult and more involved and that really interests me.
Who has inspired you professionally? I’m inspired by all the welders around me like my partner and my Bradken teammates, both tradesmen who are all at different points in their careers and have different tips and tricks to share from their time in the trade, and the other apprentices who are ahead of me and are always keen to show me things. Another person who inspired me is my Dad, who knew the path I wanted to take and supported me the whole way.
What do you believe is the biggest challenge for the welding industry at the moment? I don’t think there’s too many challenges for the welding industry, but I believe the most important one, and the one that provides the biggest opportunity, is bringing more women welders into the trade.
We have the potential to create a different energy in the workshop environment, bring a new perspective and new ideas to the table.
I’m excited to see what doors my trade will open up for me in the future and hope others like me will consider giving it a go.
A FIRST FOR AUSTRALIAN WELDING
CAgroup invests in robotics to undertake gas tungsten arc welding of lead
Established in Melbourne in the 1930s, CAgroup was originally a base metal smelter and refiner. Over the years, the company has grown and diversified into several sectors of operation, namely building solutions, industrial solutions, metals trading and anode solution. Working with major industry players like BHP, Thales and Bunnings, CAgroup continues to evolve with new products and market sectors and remains firmly focused on innovating in line with the needs of their clients—now and into the future. It is for this reason that CAgroup recently invested in an ABB robot, complete with a SMENCO welding arm. In an Australian first, the robot utilises gas tungsten arc welding for lead, rather than the traditional oxy-acetylene process.
CAgroup traces its origins back to the 1930s. Established in Melbourne, the company was called Consolidated Alloys, and was known as a base metal smelter and refiner. In 1974, Consolidated Alloys was acquired by London-based firm Amalgamated Metal Corporation, and remains a 100% owned subsidiary today.
According to Sebastian Ortega Galli (Sales Manager, CAgroup), “CAgroup has grown to become a diversified manufacturing and distribution company with sales and distribution centres right across Australia and New Zealand. Our manufacturing site and head office is located at Thomastown in Melbourne. We warehouse and sell a full range of products through our own distribution centres in Melbourne, Sydney, Brisbane and Perth. Over 2,500 products are sold to over 4,000 customers across Australia, New Zealand and around the world. We sell into four distinct market sectors: Residential Building, Industrial Manufacturers, Metals Trading and Electrowinning (EW) Anode Manufacture,” said Sebastian.
CAgroup’s Building Solutions team sells a full range of roof flashings, damp proof course products, silicone sealants, insulation foil, brazing alloys, concrete expansion jointing and polythene underlay along with a range of other building products. These are sold to a wide range of both large and small building and plumbing merchants across the country.
In terms of Industrial Solutions, CAgroup has over 80 years of experience in the manufacture and fabrication of lead based products. Products include solders, fluxes, radiation shielding, window counter weights, leadlight came and plating anodes as well as many other custom designed parts for a diverse range of industries. This includes supply to both the domestic and international
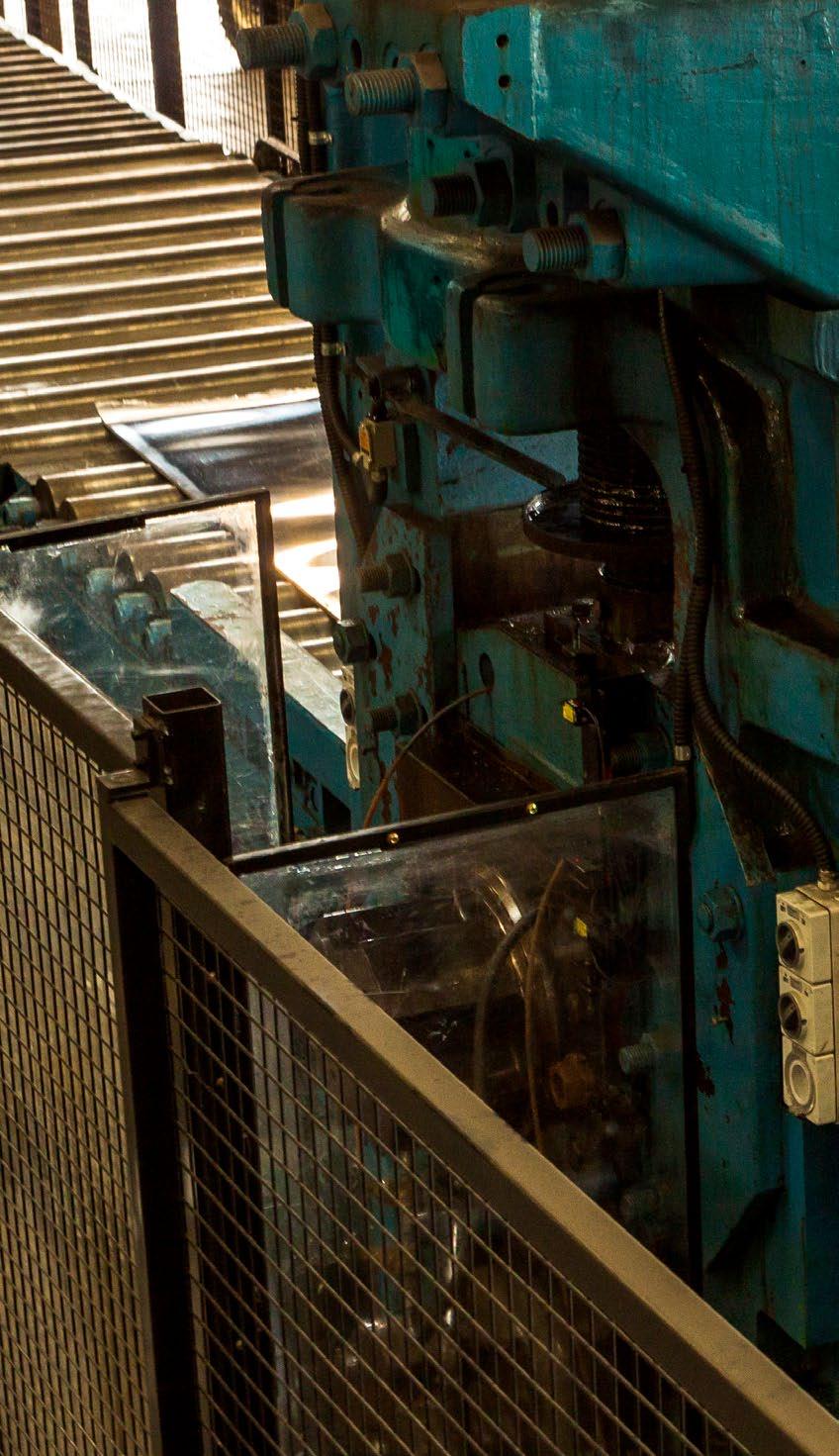


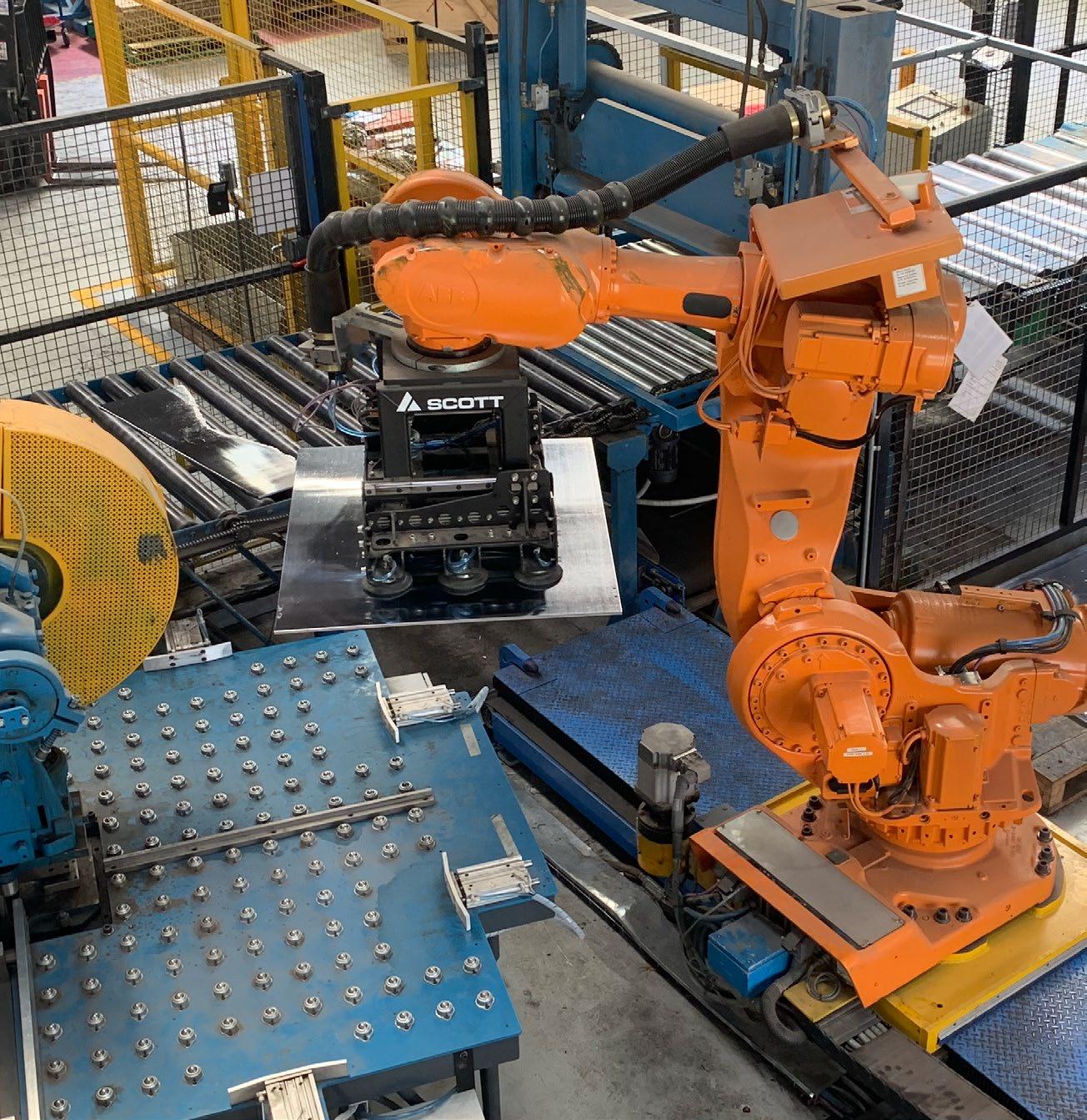
Photos (clockwise from top) Rolling mill Robotic profiler Rolled lead anode for copper electrowinning (EW)
defence industries, the mining industry and the automotive industry.
When it comes to Metals Trading, CAgroup trades in both prime and secondary metals, and can buy or sell copper, tin, zinc, lead and a broad range of other non-ferrous metals. Their Anode Solutions team provides high quality rolled lead anodes to clients across the globe, as well as recycling services to reduce the amount of scrap metal that would otherwise end up in landfill.
CAgroup utilises the finest primary calcium, tin and lead alloys along their our proprietary TMCR (thermo mechanically controlled rolling) process, which was developed and refined in-house by CAgroup engineers to achieve anode life spans of greater than 10 years.
Client Focused R&D
CAgroup continues to evolve with new products and market sectors
Silver Lead Anodes for Metalúrgica MET MEX Peñoles in Mexico
CAgroup is delivering silver lead anodes to Metalúrgica MET MEX Peñoles plant in Torreón, Coahuila, Mexico.
Under the contract, CAgroup is supplying Jumbo Silver Lead rolled anodes for their main cellhouses. The anodes will be used by Metalúrgica MET MEX Peñoles for recovering and refining zinc.

According to Sebastian, “We commenced work on the order from Metalúrgica MET MEX Peñoles prior to the installation and commissioning of our new robotic welder. The timing was perfect—it is the perfect type of project for the robot. The anodes are very heavy but, with the help of the robot, less operators need to be involved in their manufacture. This improves things from a safety point of view. In addition, our productivity improved considerably, as did the quality and consistency,” said Sebastian.
Jumbo silver lead rolled anode.
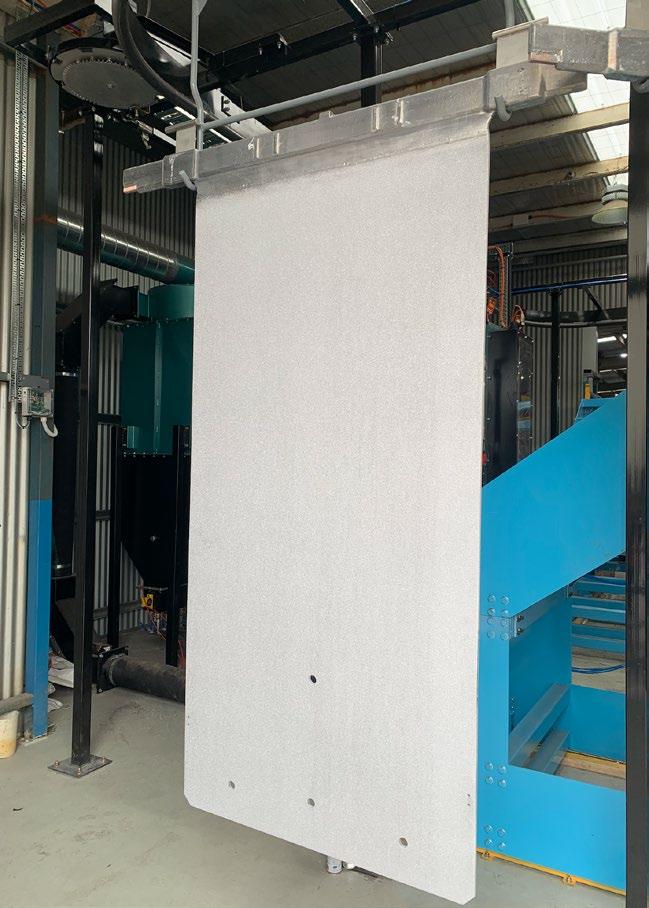
Jumbo anodes packed, ready to be shipped. Rolled lead anodes installed in electrowinning (EW) cell (Chile).
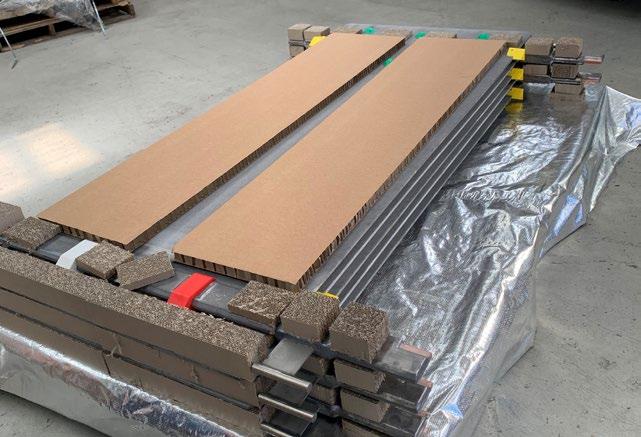
and remains squarely focused on meeting customer demands now and into the future.
“Our key strengths include lowcost operations, strong brands which are synonymous with high product quality and an extensive and efficient distribution network around Australia and New Zealand. Product development and quality control are supported by our modern in-house laboratory,” said Sebastian.
“We focus on our clients and their needs. Throughout our history, CAgroup has developed many products, for the simple reason that our clients asked us to do so. We’ve worked with many clients to develop products that suit their needs and, in doing so, have developed strong long-term relationships with our clients.”
Srikanth Vegi (Quality Manager, CAgroup) agreed. “Companies regularly approach us looking for anodes for new processes. As we have our own mill, we regularly develop these products and then expand our range to supply companies throughout the world. Flexibility and a strong customer focus is what makes CAgroup so successful. We also pride ourselves on fast deliveries and turnaround times to help ensure that our clients can continue operating without delay.”
“Finally, we’re always looking to invest in technology. If our clients require something, and we don’t have the in-house capability, we look for technology that can help. At the moment, this approach has seen us investing in robotics,” said Srikanth.
A First: Robotic Gas Tungsten Arc Welding of Lead CAgroup recently invested in an ABB robot, complete with a SMENCO welding arm. In an Australian first, the robot utilises gas tungsten arc welding for lead, rather than the traditional oxy-acetylene process.
“Although lead welding is nothing new, for the last 60 or so years, this has been done using oxy welding. Our new robotic system uses gas tungsten arc welding on lead. This is a brand new technology that no one has used in Australia before,” said Srikanth.
“The robot is installed in the middle of two cells. Both cells feature a jig, with all the components of an anode. While the robot is welding in one cell,
Robotic welder.

our team can load the components in the other cell. In this way, the welding process is continuous. It has resulted in significant productivity improvements in the workshop. Productivity improvements are particularly important when it comes to anodes—we may be producing thousands and thousands of units. We need to reduce our manpower, ensure quality and improve productivity for these types of projects,” said Sebastian.
“In addition, the robot is very safe. The operator can only access the cell when it is not in use—we have barriers that stop entry. This means that the operator remains at a safe distance from the welding process at all times. We also have a state-of-theart extraction system to remove the fumes produced during welding.”
“In terms of space, the robotic cells are smaller than a regular station for this type of anode. This means that we can have the robotic cell working at the same time as manual welding stations. As such, we can produce different projects in parallel. CAgroup often has three or four major projects underway at any one time, so we need a manufacturing area that is flexible. So, even if our welders are busy in the manual cells, we can utilise the robots,” said Sebastian.
According to Srikanth, the decision to invest in robotic welding technology was driven primarily by a lack of manpower. “We are having a hard time sourcing the manpower for our projects. Investing in robotics gives us the flexibility to produce orders of all sizes simultaneously.”
A Long Lead Time “We started this project in 2020, working with Scott Automation. We have a good history with Scott Automation—they had commissioned two robots for us previously and were very clear on the project scope, having undertaken something similar for Glencore’s cathode welding process,” said Sebastian.
“We started out with some trials, but the first results were not satisfactory. We knew we needed someone with in-depth understanding and experience in welding. Weld Australia was the perfect partner. Victor Blain (Weld Australia’s Engineering Team Manager – South and West) did some research, and worked with CAgroup and Scott Automation throughout the project. He understood the technical parameters we needed to change after the trial,” said Sebastian. “We commissioned the robot early this year and entered production in February. Every time we have a new design, we enlist the help of Weld Australia. We are very happy with the engagement of both Scott Automation (who is more about the equipment) and Weld Australia (who is more about the science of welding).”
For other companies considering investing in robotics, CAgroup has this sound advice. “It’s worth doing. It takes time but there is a good chance that if you have a process, or a step in your process, that you want to improve, robotics is a good possibility,” said Sebastian.
Srikanth agreed. “Investing in robotics keeps manufacturing in Australia. It also ensures that you’re producing good quality products locally. Instead of outsourcing manufacturing overseas, and it taking months and months for your delivery to arrive, you can produce better quality products with robotics.”
Further Information For further information, visit: cagroup.com.au or caanodes.com
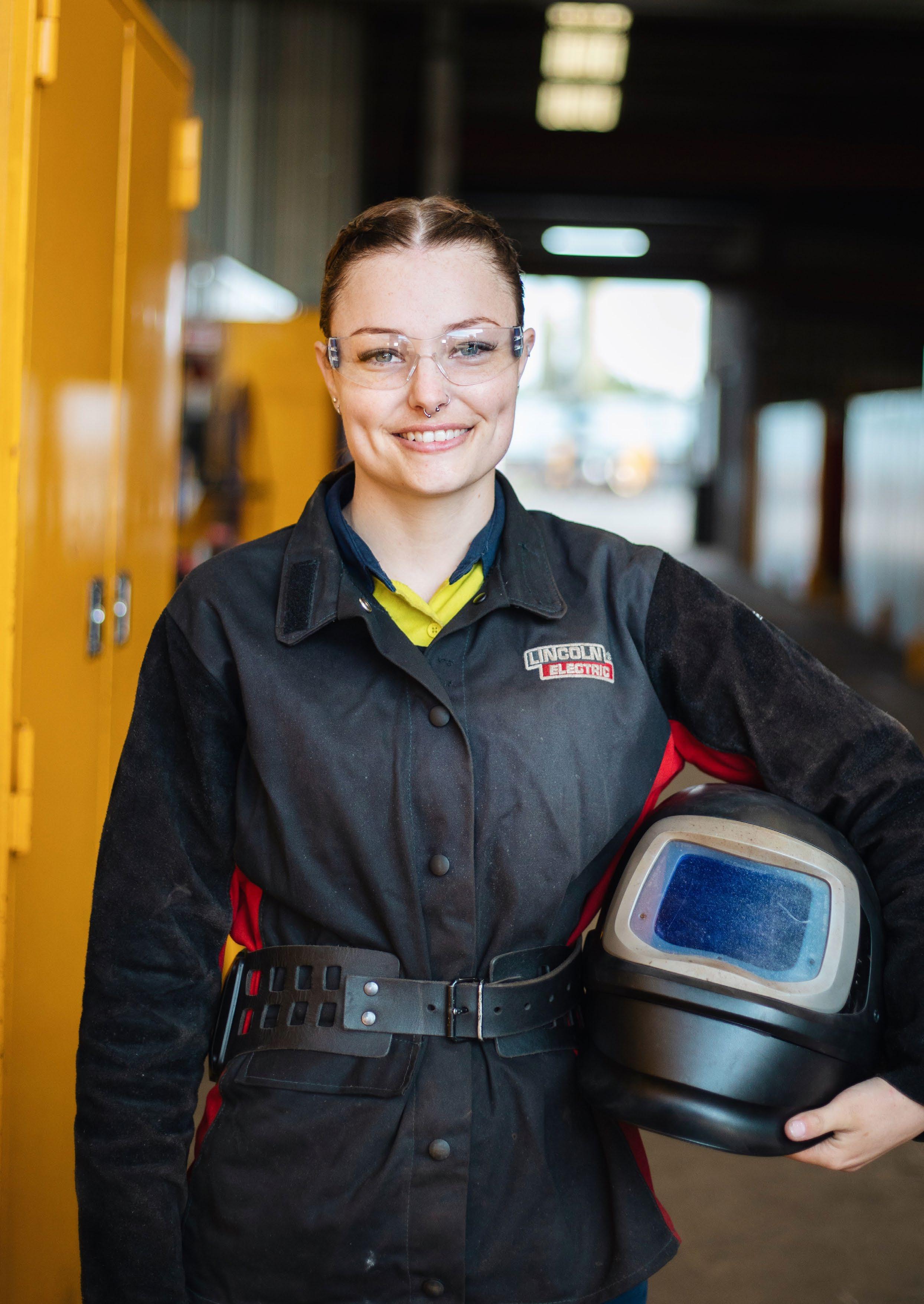
WOMEN IN WELDING
Brittany Hague is a first year apprentice boilermaker at JRS Manufacturing Group. Based in Toowoomba, JRS Manufacturing Group is a steel fabrication and welding company that specialises in plate, pipe and structural steel products for clients in the civil, energy, mining, agricultural, oil and gas industries. Brittany joined the JRS team earlier this year, and is really enjoying a career in the welding industry. Brittany took some time away from the workshop to answer a few questions about her welding career so far.
Can you describe your job? I work as an apprentice boilermaker in a fast paced, dynamic, exciting manufacturing company that specialises in metallics. I work on a lot of complex, geometric, medium to heavy steel products that require grinding, forming, fabricating, welding and testing.
What inspired you to choose a career in welding? Four years ago, a friend gave me an opportunity to try welding and I found I loved it. At first, I wasn’t confident that I could do it but I’ve jumped in and had a crack and its now my career!!
Why do you think women should consider a career in welding? Why not?! Its fun, its creative and it’s challenging in ways most jobs aren’t. Do you have any advice for women considering a career in welding? Jump in and have a go!!!
How have you found working in a traditionally male-dominated industry? In some places I’ve found you have to challenge the perception of what a woman can do in industry and instructions are unnecessarily dumbed down but overall its been positive and welcoming.
What is the most interesting project you’ve worked on? I’ve recently been able to contribute to the building of the worlds first fully automated mill relining product the RME SKYWAY – it’s exciting to see technology and traditional manufacturing come together. Who has inspired you professionally? At the moment, it’s the tradespeople I work alongside because they take the time to coach and mentor me so I can improve my skills. I hope to be able to do the same one day for other apprentices.
What do you believe is the biggest challenge for the welding industry? I think the greatest challenge is finding ways to integrate technology into traditional manufacturing practices to be ready for the future.
What about the biggest opportunity for the welding industry? Innovating our training models to deliver the next generation of Boilermakers to industry.

About JRS Manufacturing Group Established in 2014 with a small team of five people, JRS Manufacturing Group originally rented a small shed and focused on boilermaking. In the years that followed, JRS grew quickly. The company expanded its service offering, quickly realising that in-house sandblasting and painting capabilities were needed to complement their fabrication services. In 2015, JRS purchased a separate paint shop, which increased their fabrication output. In 2019, with a strong future firmly on the horizon, JRS purchased a much larger workshop. Today, the company boasts a workforce of more than 50 people and is looking to employ a lot more apprentices to handle the company’s expected future growth. Their services encompass pressure pipe fabrication and welding, abrasive blasting and coating, medium to heavy plate fabrication, specialised surface treatments, CNC and general machining and assembly.
By Geoff Crittenden (CEO, Weld Australia)
Australia’s prison population continues to grow at a rate that is four times that of the general population. According to the most recent figures from the Australian Bureau of Statistics, from 30 June 2020 to 30 June 2021, the total number of Australian prisoners increased by 5% to 42,970.
Australia’s imprisonment rate also increased by 5% from 205 to 214 prisoners per 100,000 adult population. This rate well exceeds that found across countless nations, from Scandinavia, Western Europe, Canada and the United Kingdom,
Geoff Crittenden and Jeff Wanliss inspect a prisoner’s welding at the Welding Employment Expo through to Iraq, Saudi Arabia, China and New Zealand.
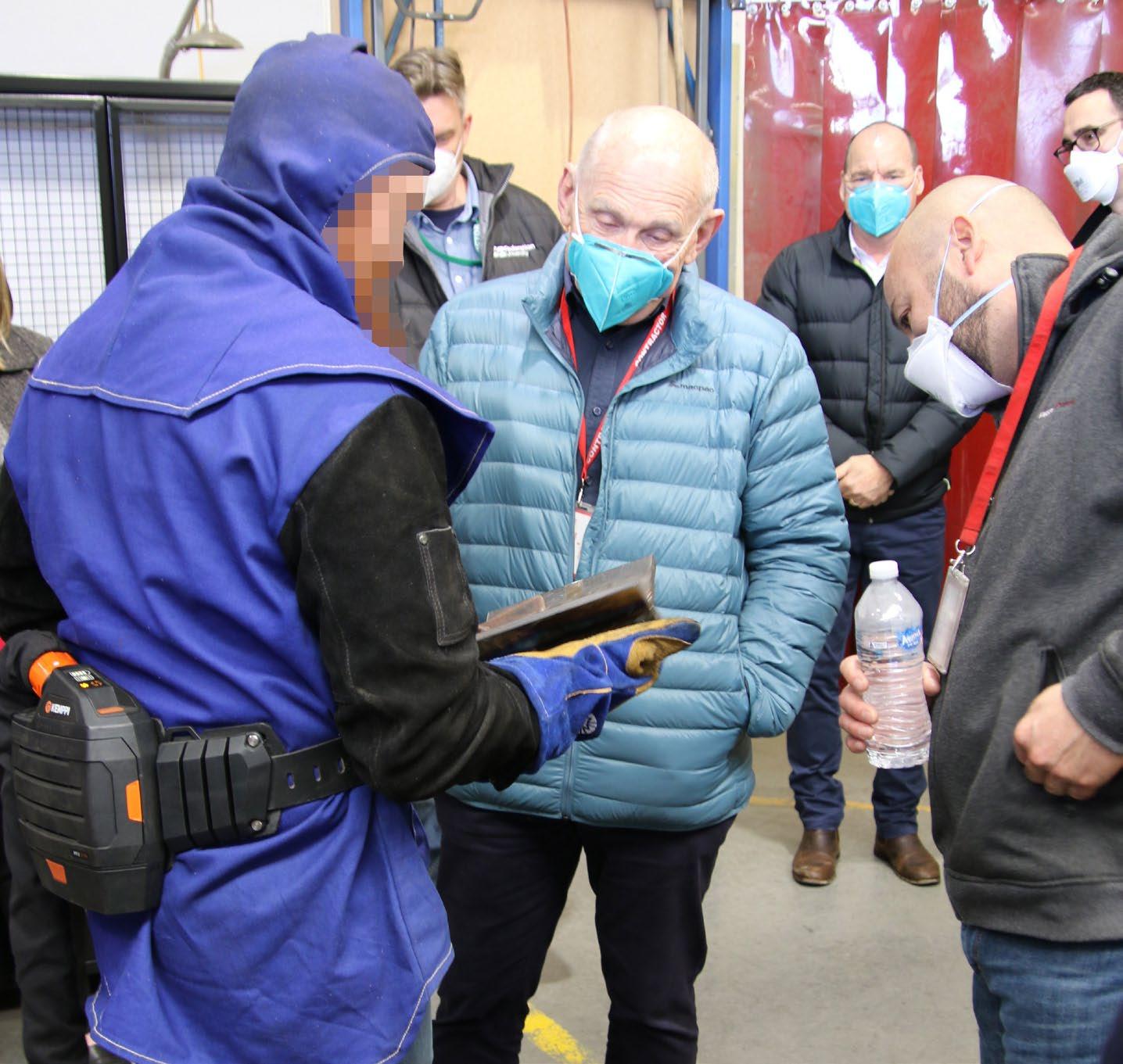
As at 30 June 2021, the median age was 35.6 years for all prisoners. When comparing the prison population to the general adult population, prisoners are much younger—2 in 3 (65%) prisoners were under 40, compared with about 2 in 5 (40%) in the general adult population.
And, possibly most concerning, once prisoners enter the correctional system, finding their way out can be tough. The Australian Bureau of Statistics latest report showed that prisoners with prior adult
imprisonment increased by 5% from 30 June 2020 to 30 June 2021.
All these statistics paint a clear picture: our prison population is rapidly expanding, and is increasingly comprised of younger people and reoffenders. This gives rise to the need for practical rehabilitation and vocational education and training (VET) programs that can help alleviate recidivism.
Rehabilitation and Training Programs Many prisoners have education and skill levels well below the Australian average. Almost 2 in 3 (63%) prisoners have an education level of Year 8 or below.
The introduction of VET programs as part of prisoner rehabilitation offers opportunities for prisoners to reduce this disadvantage, increasing the likelihood of successful re-integration into the community and reducing the risk of reoffending.
A recent study confirmed that participation in VET whilst incarcerated helps prisoners to remain custody free post-release. In fact, prisoners who successfully completed VET were 59.96% more likely to remain custody free at two years post-release; and 78.23% more likely to remain custody free at five years post-release.
VET and rehabilitative efforts are generally successful in reducing recidivism. In fact, there is some evidence to suggest that without rehabilitation, sanctions and incarceration alone may result in increased rates of reoffending.
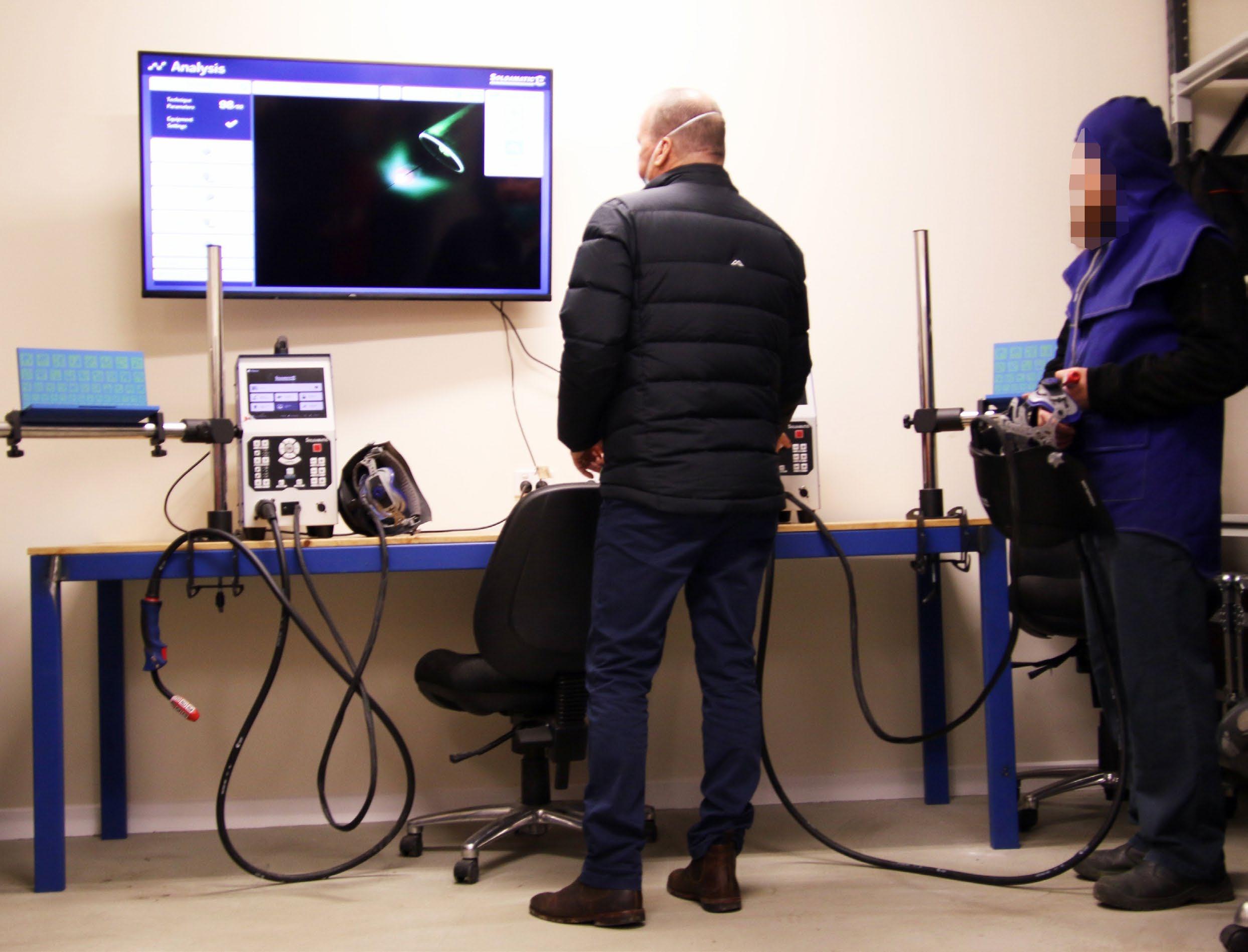
VET Centre of Excellence in Welding at HM Prison Langi Kal Kal Given the proven success of VET programs for prisoner rehabilitation, in 2022, Corrections Victoria expanded the VET Centre of Excellence model to deliver Fusion Welding to ISO 9606 certification standard to complement their Metal Fabrication industry at Langi Kal Kal Prison. Federation University delivers the training program with the support of Weld Australia and on-site prison industry staff.
As part of the program, augmented reality training was introduced to expand the welding skills of the prisoner learners to meet international standards. A welding workshop sits alongside the augmented reality training room so that participants can work on projects to use and practice their welding skills in the physical as well as virtual environments.
To participate in the program, prisoners are invited to submit an Expression of Interest and then selected through an interview process. Up to eight participants can be accommodated in the intensive 14-week program. According to Andrew Glisson (Teacher, Federation TAFE), “The students all demonstrate potential and are showing excellent aptitude and skill development as we move forward through the course.”
“It has been enjoyable watching the students have ‘light bulb’ moments in their own personal skill development. It has also been rewarding to see a student develop confidence when they discover they are capable of more than they thought.”
Student *Daine said, “I wanted to take part in this course to not only further my knowledge and experience of welding but to be able to give myself the ability to provide a positive, reliable, and sustainable future for my family.”
“When I am released, I am keen to find as much work as possible in the engineering trade working in the railways, or similar areas that require good welders. I don’t see my life revolving around prison and I want to have real work opportunities in the community when I’m released.”
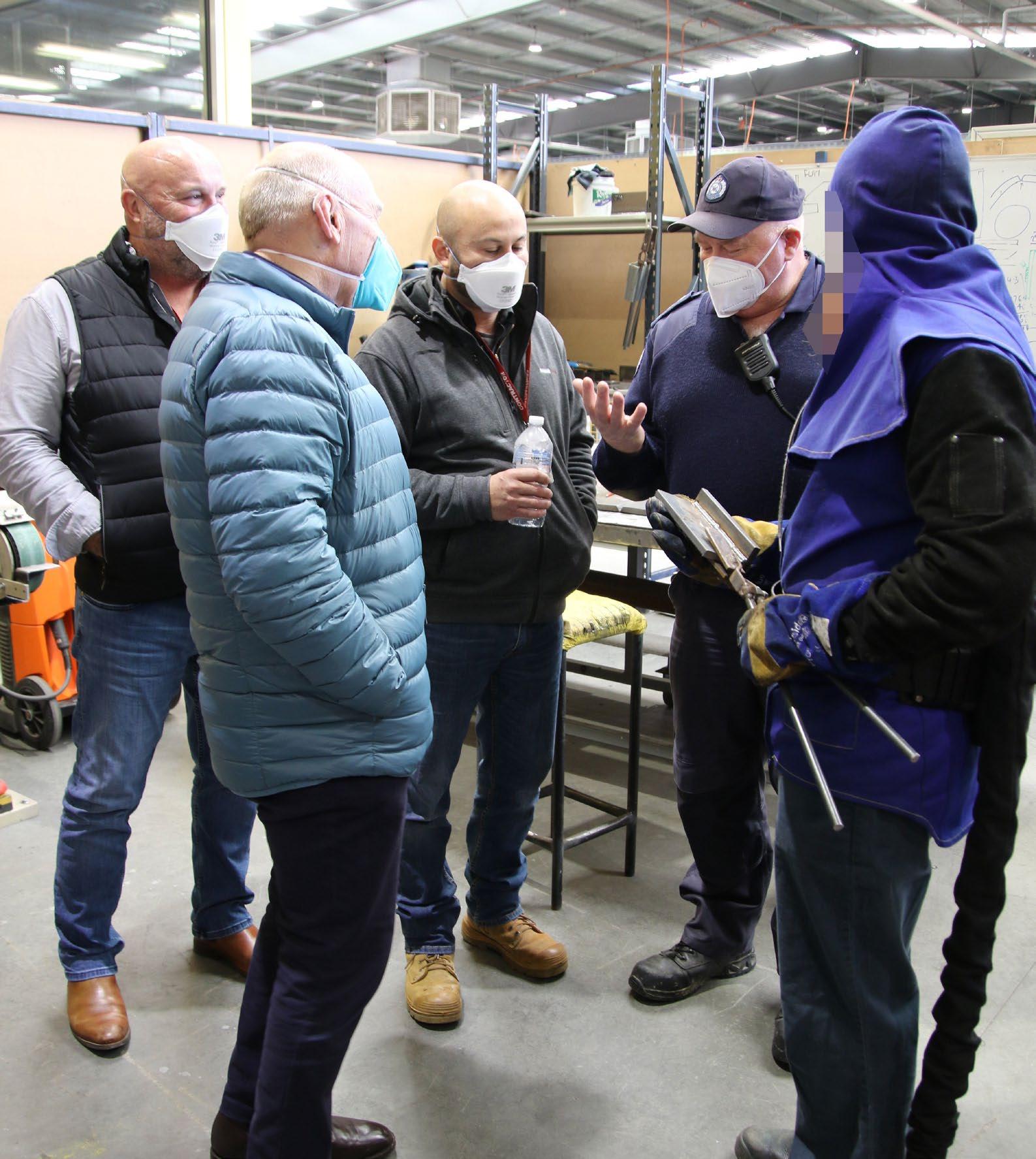
Attendees at the Welding Employment Expo at HM Prison Langi Kal Kal.
Gaining and Maintaining Employment The ability to gain and maintain employment post-release is equally as important as training when it comes to the successful reintegration of former prisoners into the community. And yet, few ex-prisoners are able to find meaningful work.
Prisoners often come from a socioeconomic group that already faces difficulties in gaining employment. They generally have high levels of drug and alcohol misuse, high levels of mental health issues, and poor work histories. Imprisonment adds to this mix, making it even more difficult for prisoners to find a job.
According to the Australian Institute of Health and Welfare fewer than 1 in 4 (22%) of former prisoners national wide report that they have paid employment organised to start within two weeks of release from prison. This can also be exacerbated at times by parole conditions that make full-time employment more difficult to manage.
The VET Centre of Excellence model links participating prisoners with prospective employers and pre- and post-release support service providers. These connections provide prisoners with sustainable pathways to employment and support to reintegrate to society post-release.
In conjunction with Weld Australia, Langi Kal Kal Prison recently hosted a Welding Employment Expo to help facilitate connections between prisoners and prospective employers. The Expo was attended by several Weld Australia members, including representatives from MaxiTrans and Hanlon Industries, as well as Jeff Wanliss (Engineering and Business Development Manager, Keppel Prince). Based in Portland, Victoria, Keppel Prince specialises in the construction, fabrication and maintenance of industrial structures and equipment, ranging from wind farms to bridges.
“I didn’t really know what to expect from the Employment Expo, but the experience was a big eye-opener for me. I was very impressed by the facilities at Langi Kal Kal. The equipment is excellent and in line with industry standards, which helps ensure the prisoners are prepared to walk into any workshop—they’ll be comfortable from day one,” said Wanliss.
“The level of instruction was top class. The welding supervisor was equipped with a wealth of knowledge and experience, having previous experience as a boilermaker. The level of passion from all the correctional officers was clear. They’re all dedicated to working with the prisoners, bringing out the best in them, and giving them a solid grounding in the skills needed for life.”
“During the tour of the facilities, one of the prisoners produced an industry standard vertical up weld—one of the hardest welds to do. We would have accepted that weld in our workshop. It can be difficult to find potential employees with the skills and experience needed in our workshop. I’d definitely consider employing any of the guys based on the standard of welding they’re doing.”
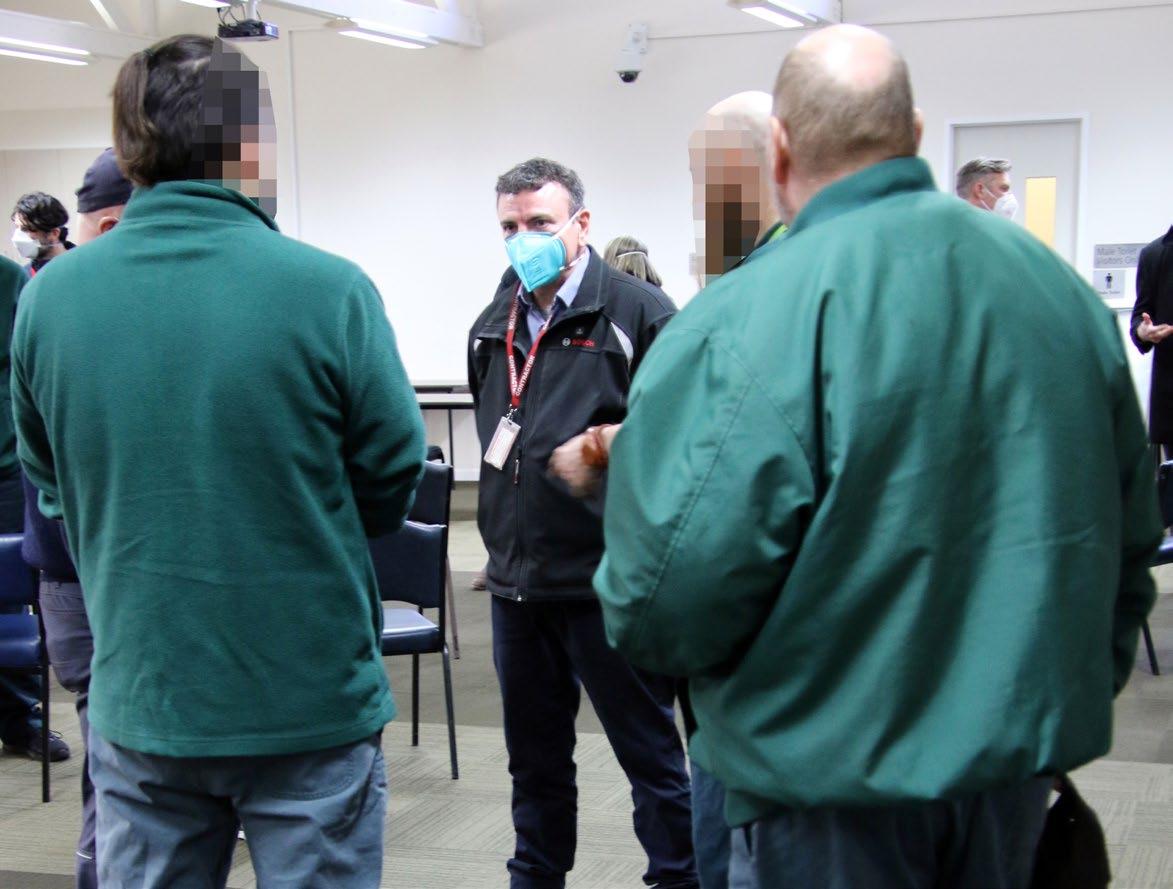
“These types of training and rehabilitation programs are so important. They help give prisoners purpose. Many of the prisoners have obviously faced challenges in the past, but, this is a delineation point—it’s like drawing a line in the sand and saying ‘the past is the past’.”
“VET and training programs like this one equip prisoners with knowledge and give them practical skills that they can use on release. It is an essential step to ensuring that their future is successful,” said Wanliss.
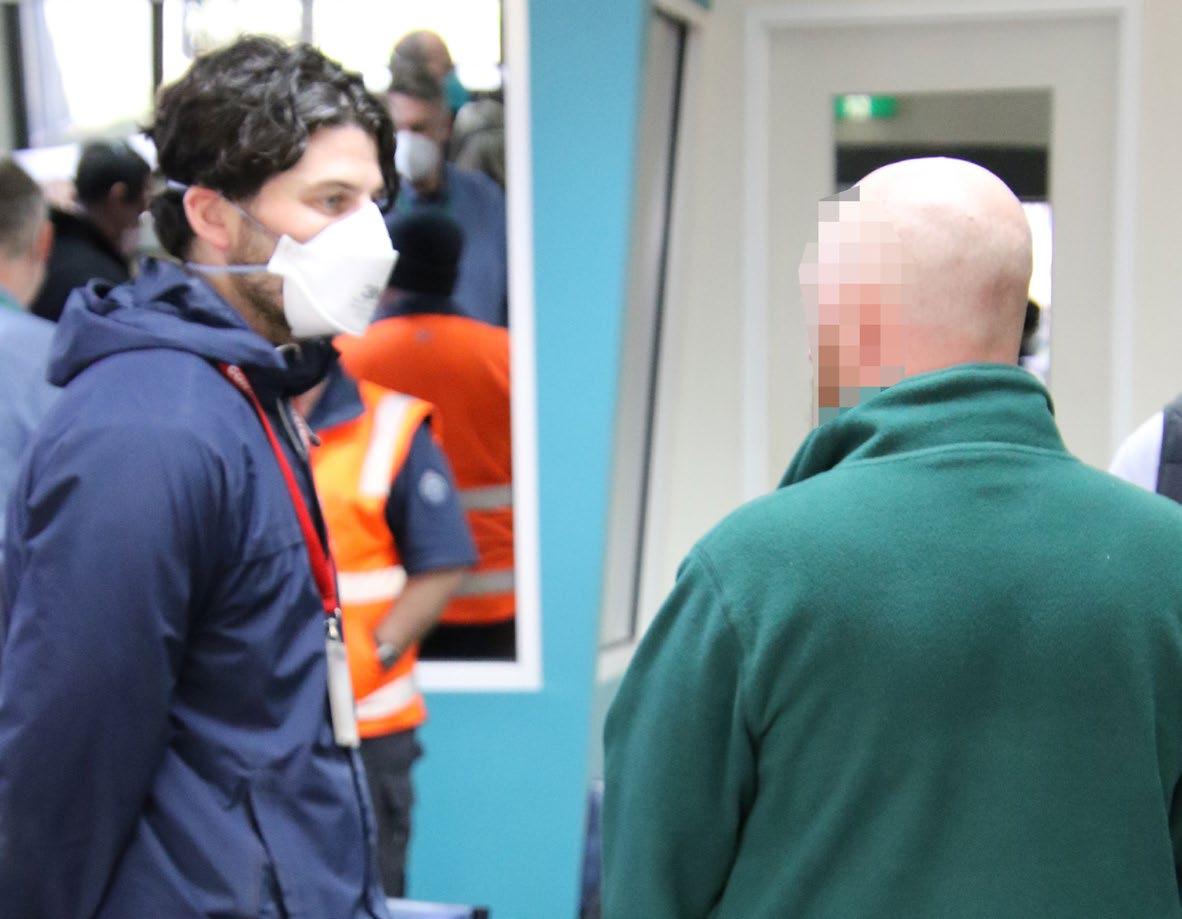
A Successful Future
Australia is facing a looming shortage of skilled welders—70,000 additional welders will be needed in the next 10 years. Welders are more in demand than ever with several large-scale, highvalue projects on the horizon, from the Federal Government’s $90 billion Naval Shipbuilding Program, through to major infrastructure projects such as the $16 billion WestConnex project, $12 billion Sydney Metro project, and the $11 billion Melbourne Metro Tunnel.
VET training and employment pathways as part of prisoner rehabilitation could help alleviate some of these skills shortages. However, this will require commitment and collaboration from industry and government—not only to fund VET training in Australia’s prisons—but to help provide secure employment opportunities post-release.
Further Information
For further information, or if you would like to get involved as a prospective employer, please complete this Expression of Interest Form.
Welding Employment Expo at HM Prison Langi Kal Kal.
Welding Employment Expo at HM Prison Langi Kal Kal.
About HM Prison Langi Kal Kal
The land where Langi Kal Kal Prison is located was first settled as a 70,000-acre farming property in about 1838. A substantial farmhouse was built in approximately 1900. After World War II, the land was subdivided and the central area, including the farmhouse, was set aside for prison purposes. The first prisoners arrived in September 1950 and the prison was officially opened in February 1951. In 1965 the prison became a youth training centre, but again became an adult prison in June 1993.
Situated on the Western Highway at Trawalla approximately 140km west of Melbourne, Langi Kal Kal is an open camp, minimum security protection prison with all prisoners required to work during their stay unless they are over retirement age. As a pre-release prison, Langi Kal Kal specialises in getting prisoners ready for release through on-the job training and employment in a range of industries.
BRIDGEMAN
Where social conscious is synonymous with success
Social conscious is synonymous with success for Queensland metal manufacturing and construction company, Bridgeman. An Indigenous owned, operated and Supply Nation certified company, Bridgeman prides itself on its commitment to the community, as well as its highly experienced staff and leadingedge capability. The company works with Traditional Owners to engage with the community, and with Australian Government agencies, to improve employment and training outcomes for Indigenous People across Australia.
Bridgeman has been delivering end-to-end solutions in Queensland and across Australia for more than 25 years. Originally founded in 1997 as a metal manufacturing company, Bridgeman has transitioned into one of Australia’s most trusted and respected multi-faceted solutions providers. With a presence in Brisbane, Townsville and Cairns, Bridgeman boasts an advanced manufacturing facility of over 2,700m2, which is equipped with the latest machinery.
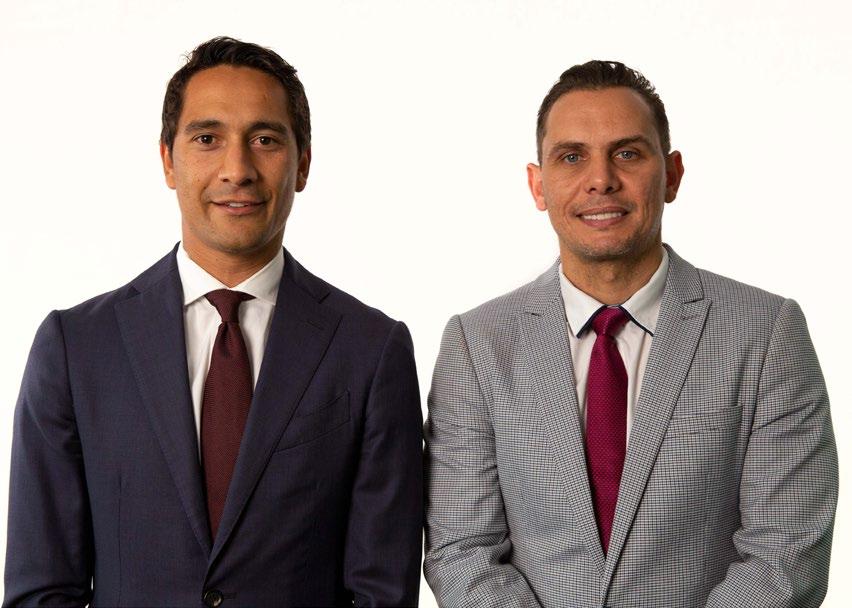
Having been an Executive Director of Bridgeman for over five years, Adam Sarota became an Owner and Managing Director of Bridgeman in April 2021. Adam is a former Socceroo, and a proud Traditional Owner and Yidinji man. Subsequently, Jade North joined Bridgeman as an Owner and Managing Partner. Jade is also a former Socceroo, Olympian, NAIDOC Sportsperson of the year, current Co-Chair of Football Australia’s National Indigenous Advisory Group and a proud Indigenous man from Biripi Country.
Since the new ownership of the company commenced, Bridgeman has increased its staff numbers from 40 to 90 employees, including 20 apprentices and 11 Indigenous employees. The company has also expanded into new areas of operation, with its entities now encompassing Bridgeman Manufacturing, Bridgeman Building Group, and Bridgeman Defence, Government and Infrastructure. In addition, sustainability, governance and environmental planning have been paramount through the creation of an executive team with significant and diverse experience that continues to drive Bridgeman’s evolution.
According to Managing Director, Adam Sarota, “The last couple of years with COVID-19 have been difficult for everyone and, like many other manufacturing businesses, we’ve had to face a lot of new challenges. We’ve had to adapt and diversify into other areas, and we are really proud of the fact that we’ve managed to diversify our business into different sectors and doubled the business whilst attaining several ISO accreditations, and creating new social and Indigenous life changing initiatives.”
“Our company operates across the primary areas of metal manufacturing solutions and construction. We are compliant with all relevant accreditations and ISO certified and have the ability to provide a multifaceted range of solutions which deliver quality, cost effective, and
Adam Sarota and Jade North.
timely results to our clients, across sites of all sizes and scopes through a single point of contact.”
“Bridgeman’s expertise is unrivalled, whether it’s manufacturing, engineering, drafting or fully customised design and manufacturing, including galvanising, powder-coating, anodising, and state-ofthe-art laser cutting,” said Adam.
“We work across all metals including, stainless steel, mild steel, aluminium, brass and copper. Bridgeman has in-house welding operators qualified to AS/NZS 1554.6 and AS/NZS 1554.l. Our team includes Weld Australia qualified welding supervisors (AS1796 Cert 10), and an International Welding Specialist (IWS).”
“One of our key strengths is our capability to adapt and diversify when and where needed. From minor refurbishments to major construction projects, we pride ourselves on our capability and capacity to provide flexible solutions, over and above the scope requirements. Our priority is the health and safety of our people, our clients, contractors, and our community,” said Adam.
INDIGENOUS OWNED AND OPERATED As an Indigenous owned, operated and Supply Nation certified company, Bridgeman is committed to ensuring that they provide leadership, support, opportunity, and encouragement to Aboriginal and Torres Strait Islander peoples and the broader community.
“We aim to demonstrate an increased Indigenous participation beyond traditional levels and provide more advanced roles for Aboriginal and Torres Strait Islander people through various initiatives,” said Managing Partner, Jade North.
“Our goal is to set the benchmark for Indigenous participation and inspire the Indigenous business community in helping to break down stereotypes and unconscious bias. Bridgeman continuously liaises and works with Traditional Owners on a range of community engagement matters, including cultural protocols and to seek advice on recognition and acknowledgment of Traditional Owners within specific regions.”
“We also work alongside other Australian Government Agencies, such as the Department of Seniors, Disability Services and Aboriginal and Torres Strait Islander Partnerships (DATSIP), to facilitate the alignment of businesses and employment and training outcomes for Indigenous Peoples. Bridgeman proudly has Indigenous Employment and Procurement First Policies to encourage greater social and economic benefits within the communities in which we work.”
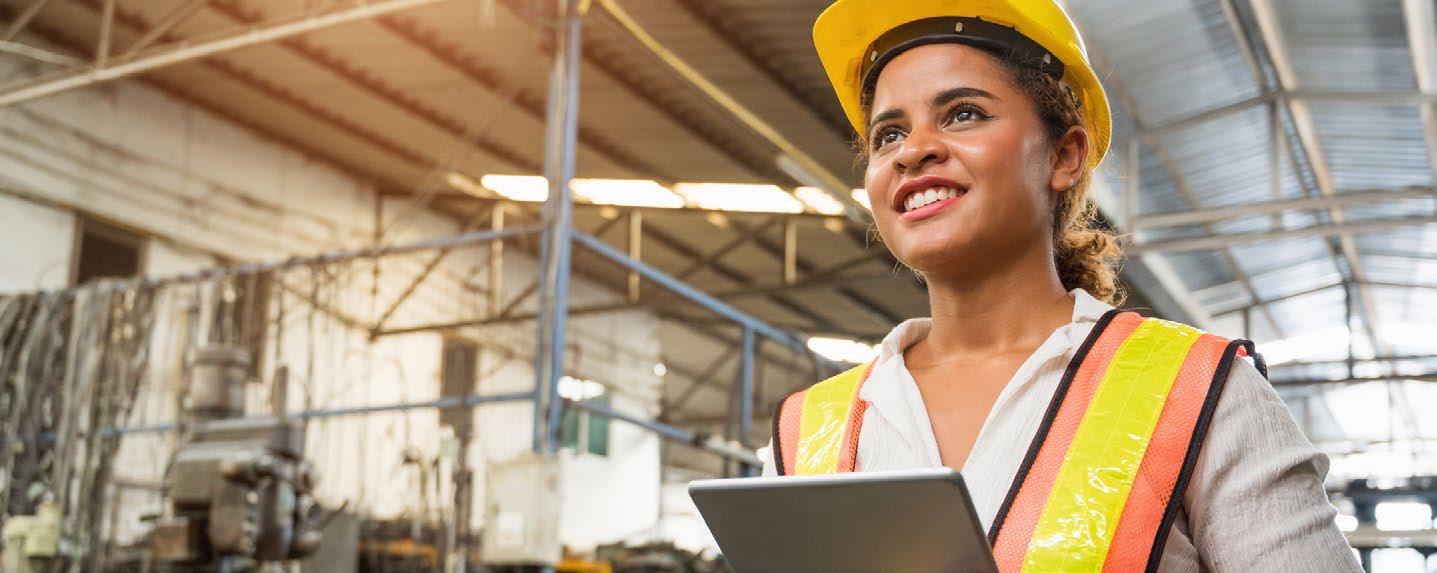
They have created the Bridgeman Yarning Circle, a unique Indigenous supply chain network that provides companies with genuine, pre-qualified, accredited and compliant Indigenous companies. Bridgeman’s ‘Multiplier’ goal—designed to create meaningful change through tangible outcomes— is to convert every $1 contracted to Bridgeman into $3 within the Indigenous business community.
“We are working to create as many opportunities for Indigenous businesses within our supply chain as possible and working with our non-indigenous supply chain partners to create more opportunities for Indigenous people and businesses within their supply chains. This process is creating real opportunities and genuine outcomes which is really pleasing but only the start for us,” said Adam.
SOCIAL INITIATIVES ENHANCING THE LIVES OF QUEENSLANDERS Bridgeman was recently awarded the 2022 Dickson Small Business of the Year Award by Hon Peter Dutton MP, in recognition of their Outstanding Service and Leadership for the Indigenous Community. Some examples of Bridgeman’s social initiatives that enhance the lives of Queenslanders are outlined below.
Futures Program “Our Futures Program focuses on training and retaining Australian apprentices and trainees for the long term. It enables Bridgeman to create and develop our future workforce. Apprentices and trainees work alongside our qualified tradespeople who assist with on-the-job training and allows them the opportunity to build new skills in a hands-on learning environment. Working with our Bridgeman experts in their trades helps develop invaluable skills and experience in a varied environment,” said Jade. As a result, Bridgeman currently employs 20 full-time apprentices across their operations.
One Mob Initiative Bridgeman’s One Mob Initiative (OMI) was developed to engage and provide positive educational and work experiences for Aboriginal and
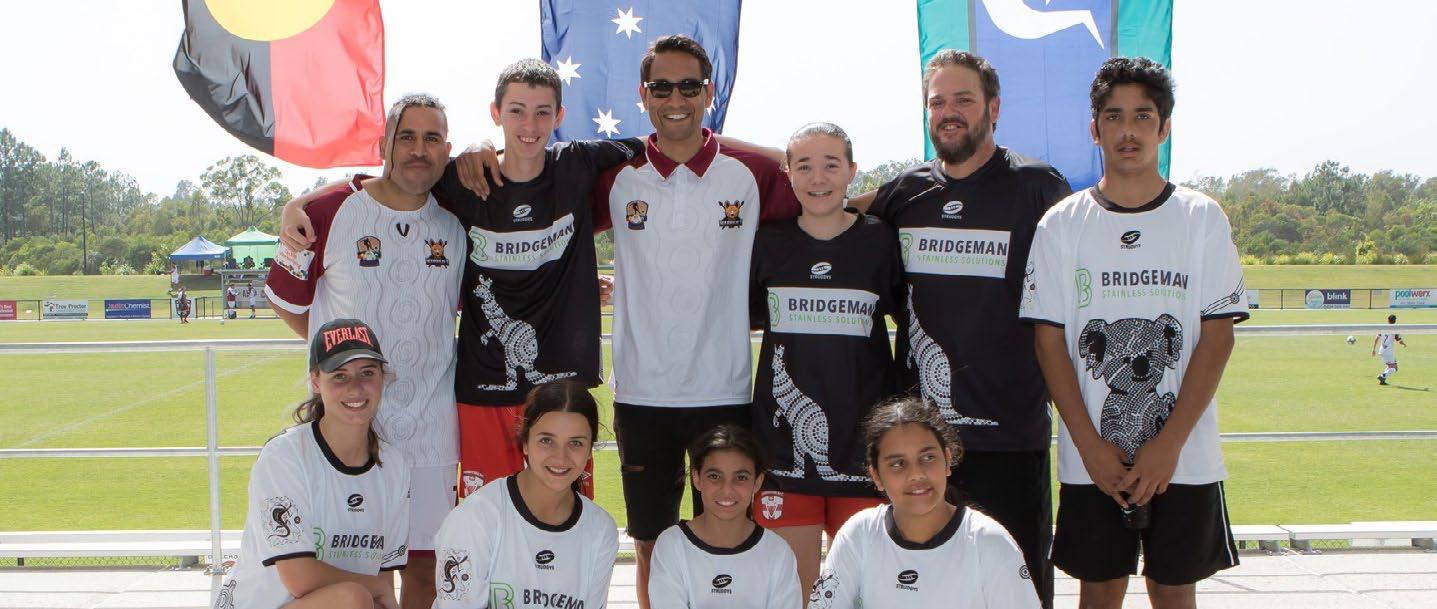
Kickin With A Cuz iniative.
Women in Construction Pathway.
Torres Strait Islander Peoples. OMI builds a pathway for those seeking to pursue tertiary education and employment, particularly vulnerable and disadvantaged Indigenous.
“We proudly support the recipients of this initiative with vocational and financial support to assist with this journey. We see the significance and draw on the skills, capability and unique life experiences that Aboriginal and Torres Strait Island Peoples can bring. We want the forefront of our business to drive inclusiveness and diversity. We currently employ 11 Indigenous full-time employees through our One Mob Initiative,” said Jade.
Bridgeman also partners with companies on selected projects allowing them to share the journey and help improve the livelihood and future for Indigenous and underprivileged people.
Career Transition Program “Bridgeman created our Career Transition Program to assist former professional athletes, service men and women and people with disabilities who are struggling to transition into the mainstream workforce. We understand the unique challenges and hardships people face when transitioning from one career to another. The goal of the program is to build confidence and enhance skills and knowledge through practical experience, mentorship and support,” said Jade.
Bridgeman currently employs three full-time employees via this program.
Bridging the Gap This program targets Indigenous and Non-Indigenous high school students, providing real-life learning opportunities for students by mentoring and supporting them through the transition from high school to work life. “Bridging the Gap offers pathways post school and most importantly, provides kids with the inspiration and drive to transition from school to the real world. We assist in closing the gap of intergenerational welfare and long-term unemployment by providing support and mentoring by key people and senior members within our business to help students gain confidence, reach their full potential and achieve success in their chosen field,” said Jade.
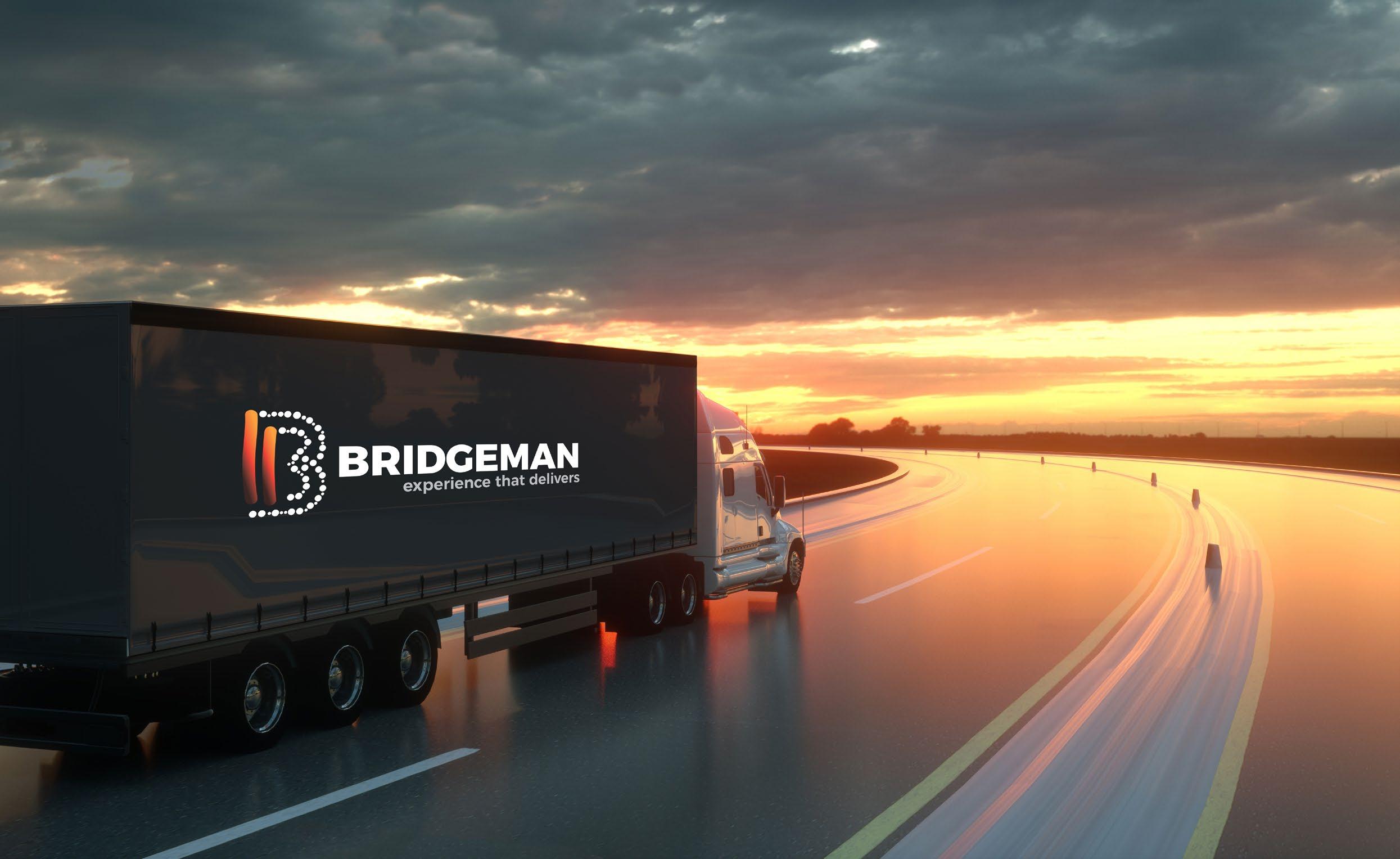
Women in Construction Pathway Bridgeman is dedicated to providing and creating career opportunities to boost female participation within the construction industry.
“Our Women in Construction Pathway Program assists women in their professional growth and ongoing success in our company where we appreciate the distinctive qualities they can bring to Bridgeman and the construction industry. The pathway has been designed to provide more opportunities for females in front-line delivery roles where the program offers apprenticeships, tertiary education, and internal promotion opportunities along with trade-specific courses such as project management,” said Jade.
Bridgeman employs three women via this pathway, with one studying project management.
Bridgeman also supports the following initiatives: • Kickin’ with a Cuz: created by Jade North, to teach young Indigenous and under privileged children a viable pathway to make better life choices • Givit Foundation: Jade North is an active
Indigenous Ambassador for Givit which provides support to Indigenous and Torres Strait Islander
Peoples who are experiencing hardship • Prime Minister’s Veteran’s Employment Program: providing employment opportunities to Veterans leaving the Australian Defence Force • Cairns Safer Streets: Adam Sarota is an active
Indigenous Ambassador encouraging young people and their families to take part in activities together Bunk Beds Boost for Jobs, Safety and Offender Rehabilitation
Bridgeman has successfully manufactured and installed over 2,700 bunk beds and cell furniture in the last five years alone in live Correctional Centres including Lotus Glen, Townsville, Brisbane, Maryborough and Wolston Correctional Centres. Projects include Bridgeman’s current 827 bunk bed and cell furniture rollout program for QBuild.
Working with Correctional Centres is deeply personal for Bridgeman’s Owners Adam Sarota and Jade North. They are passionate about providing opportunities for those who are going through or facing hardship, particularly past offenders.
As a result, Bridgeman has developed a four step system that sees the company involved in prevention and rehabilitation of both past and current offenders.
Bridgeman’s recent bunk bed and cell furniture project created 17 new full time employment positions of which 23.5% were Indigenous, 17.6% were past offenders and 23.5% were newly created apprenticeships.
Further Information For further information about Bridgeman and their programs visit: bridgeman.com.au
BHP FUTUREFIT ACADEMY
Preparing Australians for a career in mining
BHP’s FutureFit Academy seeks to forge new territory in the way the company prepares their people for a career in mining. Launched in 2020, the Academy is part of a new national training program designed to bolster Australia’s skills base and create new career pathways into the mining sector. Offering an innovative approach to training, the Academy’s fit-for-purpose maintenance and production training programs are run in dedicated learning centres in Perth, Western Australia, and Mackay in Queensland.
In the last two years, BHP’s FutureFit Academy has welcomed over 590 apprentices and trainees, with more than 80% women and over 20% per cent Indigenous learners. The average age is about 30 years old, and most are from regional communities. There have already been over 220 graduates deployed to permanent jobs across BHP’s Australian operations. With strong demand for future intakes, BHP expects to train 2,500 new apprentices and trainees over the next five years.
According to Michelle Gibson (Head of Learning and Development, BHP), “When first establishing the BHP FutureFit Academy, we set out to dream big and think differently. Our goal was to develop an inclusive learning environment where students and leaders would feel welcomed and supported. Two years later, we are seeing greater retention and these results are testament to the strength of the BHP FutureFit Academy’s program and its focus on a supportive culture and developing career pathways,” said Michelle.
From day one at the Academy, students are a permanent BHP employee, earning a salary while they’re studying. The purpose-built learning centres feature the latest immersive virtual reality technology combined with workshop learning designed to provide students with the training they need to competently and safely carry out their work in the field.
The Academy offers the following pathways: • Trade Apprenticeship: Over 24 months students earn a full trade qualification and the skills to perform preventative maintenance, diagnostics and repairs. BHP is offering apprenticeships in Heavy Diesel Fitting, Mechanical Fitting,
Fabrication and Conveyor Belt-
Splicing (Polymer Fabrication), with new Auto Electrical and
Electrical trades coming in the 2023 financial year. • Traineeships are offered over 12 months in either: • Maintenance: Students complete specific modules to a Certificate II level to equip them to be trained, competent and authorised to perform a range of preventative maintenance tasks as a Heavy Diesel Maintenance Associate or Mechanical Fitter Maintenance Associate. • Production: Students complete a Certificate III in Surface Extraction Operations to equip them to be trained, competent and authorised as a Production Operator.
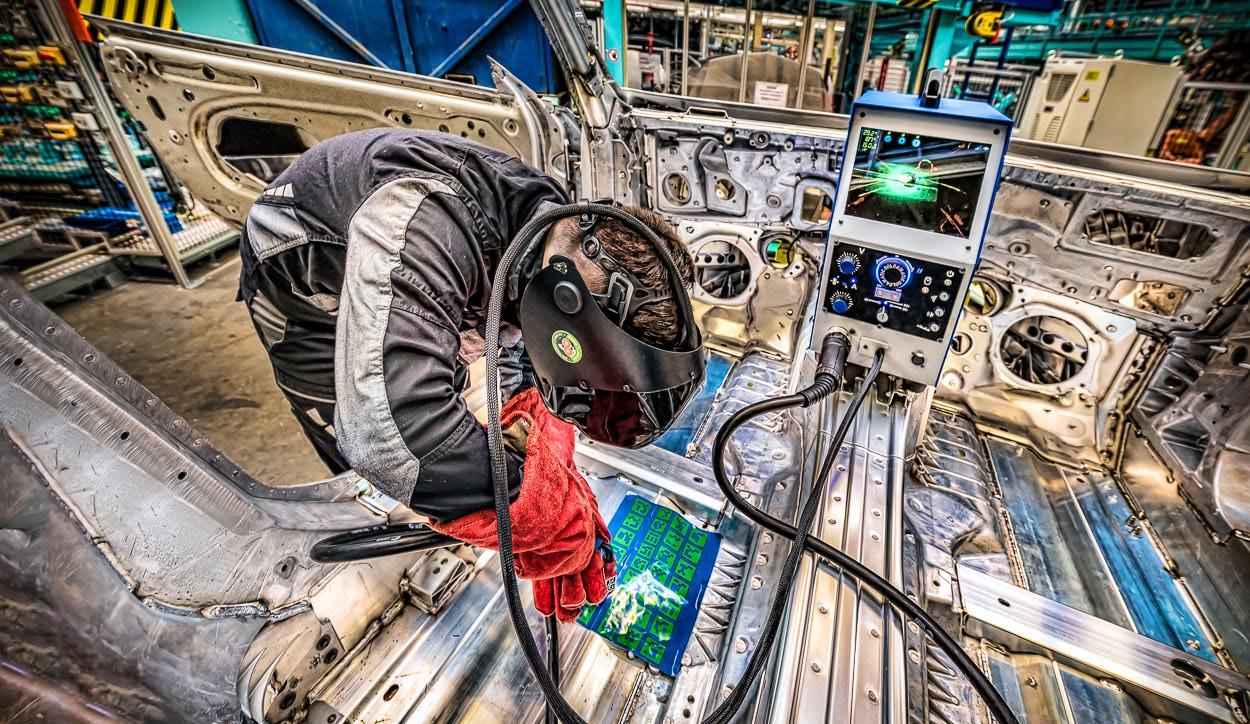
Photo: Soldamatic augmented reality welding simulators are student-focused, allowing individual students to progress at their own pace. Welding apprentices learn and understand welding procedures and techniques through a more interactive training method, gaining hands-on experience in a controlled, safe environment. Augmented reality transforms training from boring theory and text books into high-quality interactive experiences that capture the imagination.
Academy programs are nationally accredited and supported by BHP’s partnerships with Central Queensland University (CQU) Australia and North Metropolitan TAFE (NMTAFE), Western Australia.
According to Laura Tyler (Chief Technical Officer, BHP), “We are an industry that offers a diverse range of rewarding career opportunities that suit any passion or skill set. But it is not always easy to gain the skills to get in the door.”
“Our FutureFit Academy national training program is designed to create exciting career pathways into the mining sector. We offer mining apprenticeships and traineeships, backed by nationally recognised curricula.”
“Importantly, the Academies are not just for school leavers. We have welcomed students from all walks of life such as Lisa Berwick at our Perth Academy, who is a 49-year-old mother of three with no prior mining experience. Lisa now works on BHP shutdowns after graduating from a 12-month maintenance traineeship with FutureFit Academy,” said Laura.
Augmented Reality Welder Training The FutureFit Academy in Perth offers training programs in fabrication. Students commence their training using Soldamatic augmented reality welding simulators.
Welding apprentices learn and understand welding procedures and techniques through a more interactive training method, gaining handson experience in a controlled, safe environment. With zero risks involved, apprentices can respond to realistic scenarios without pressure or fear of injury. Augmented and virtual reality When first establishing the BHP FutureFit Academy, we set out to dream big and think differently. Our goal was to develop an inclusive learning environment where students and leaders would feel welcomed and supported.”
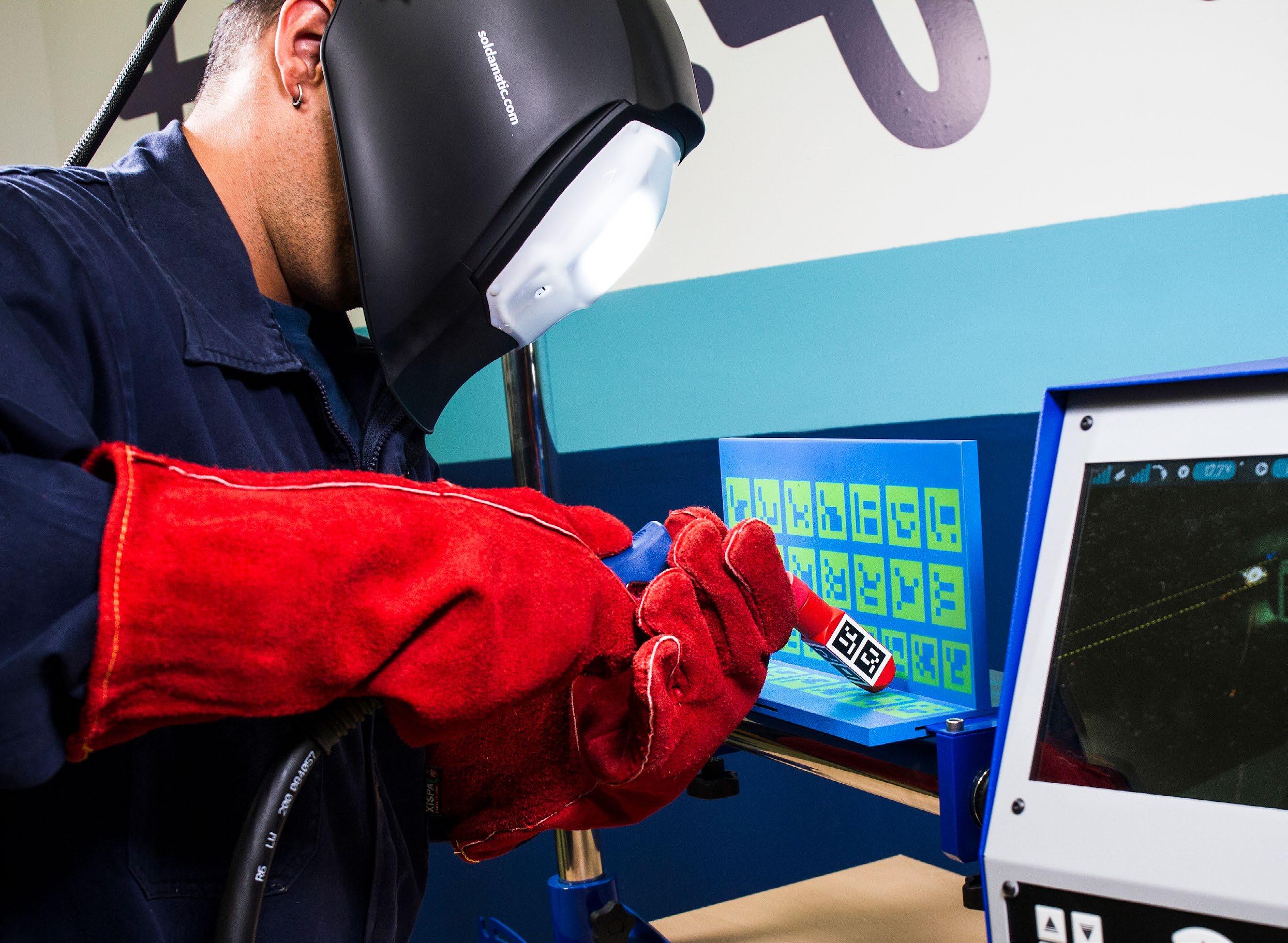
Jimblebar, Western Australia
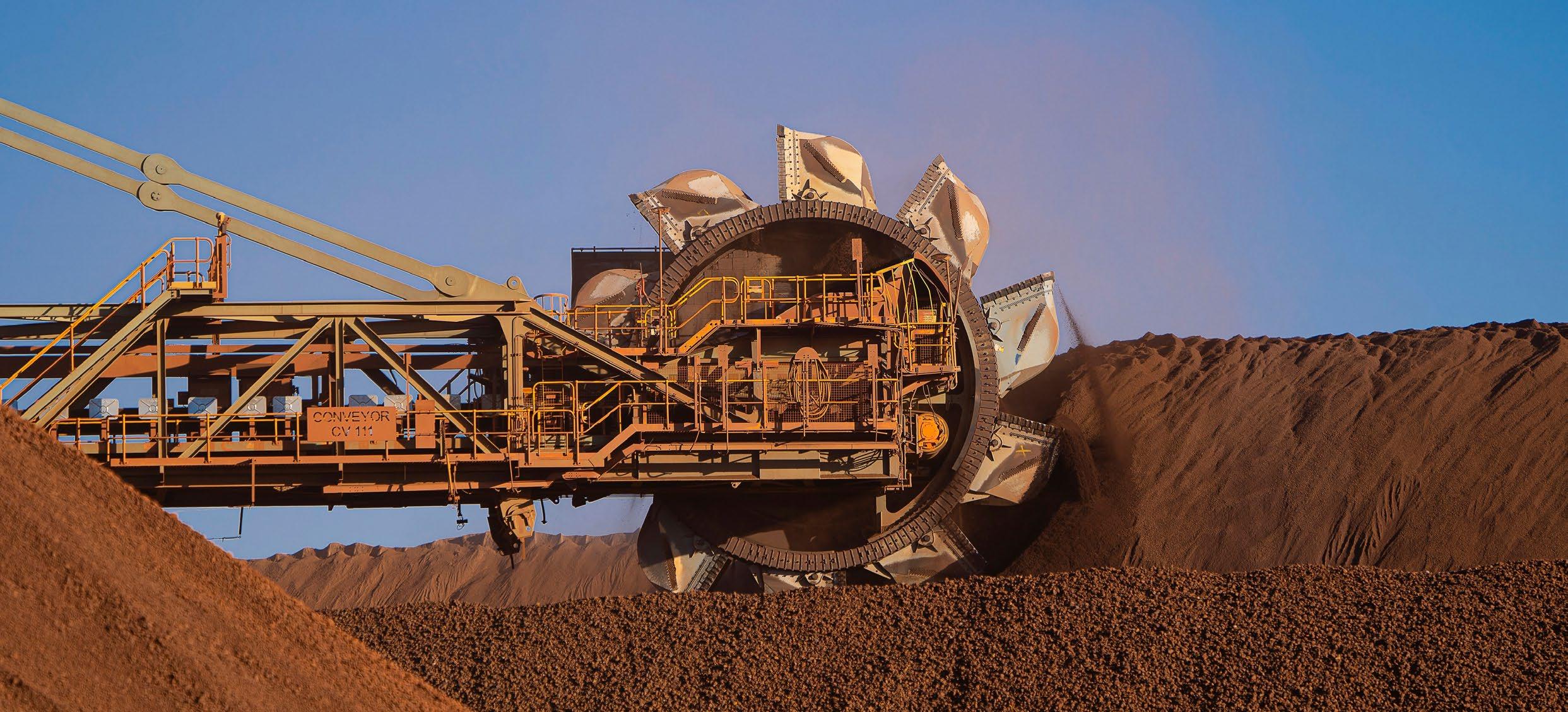
Get to Know FutureFit Academy Student Rachael Almond
When she’s not restoring classic cars, Rachael Almond is studying to become a Mechanical Fitter at BHP’s FutureFit Academy. Rachael talks about her journey so far, the support she’s received since joining the FutureFit Academy, and her excitement for the future.
Tell us about your journey so far with the FutureFit Academy? I was blown away when I found out I was accepted into the FutureFit Academy. It was like winning the lotto! My journey has been amazing with the greatest thing being the support provided to every student. An example of this is late last year on New Year’s morning my son lost his house and his belongings in a house fire. It was incredibly sad and my fellow students, teachers, superintendents and the people in the office reached out to provide support. You’re not just a number at the FFA!
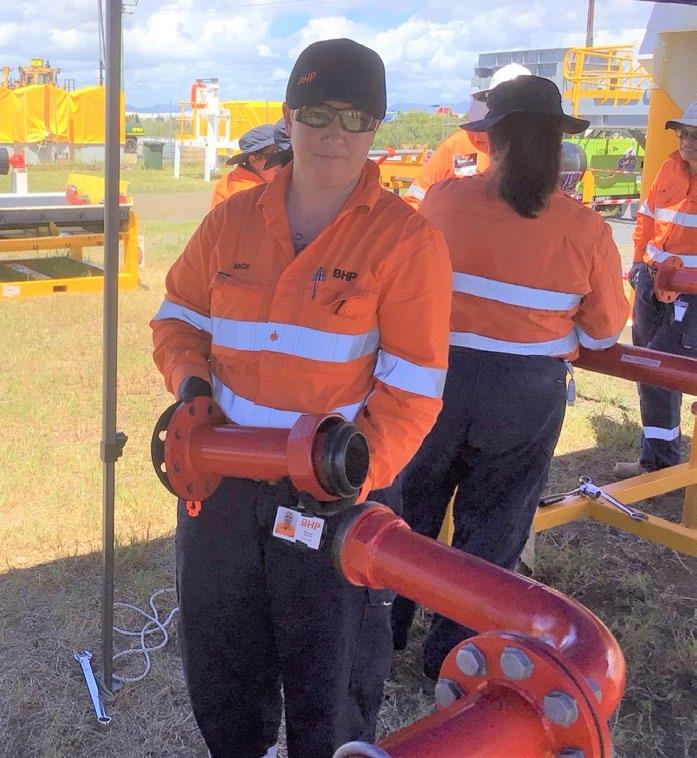
Why did you join the FutureFit Academy? I joined the FFA for the opportunity! I’m 39 years old and no one gets a fresh start in a career as an apprentice new to industry trade at 39! I joined for my future, to try something different, and to go somewhere I’ve never been before in my career.
What does a typical day look like as a FutureFit Academy student at CQUniversity (CQU) Mackay? We start every day with a pre-start meeting and safety share. This ensures that we identify things from yesterday that could be done better - or safer - and plan out what we might face today. Safety is a major focus and everyone wants to be sure you go home in the same condition you arrived in. Every day is a joyful experience and our trainers and supervisors are always there to help. No question is too silly and no question goes unanswered. Everyone here wants to drive you in the right direction and help you achieve and succeed
What’s been your highlight so far? Making things! If you had asked me 12 months ago to make a drill gauge I would have replied with “a what?” Yes, I can now actually make a drill gauge from a flat piece of steel. I enjoy tool time as I love pulling things apart and putting them back together.
What do you like to get up to when you’re not studying? Before I relocated to Mackay, I was from Sydney where I harboured a passion for cars. I enjoy working on cars with my dad and restoring the old classics like mustangs, XY falcons and everything in between. As long as it sounds tough and has the horsepower! I have a soft spot for animals, my horse Apollo, and my dogs Johnny Cash and Ruby. My partner and I recently brought a caravan and plan on exploring North Queensland on our days off.
training is enabling future welders to acquire the skills and the selfconfidence they need before moving into real-world workshops.
Indigenous Employment Target Reached Ahead of Schedule In April 2022, BHP achieved its national Indigenous employment target of 8% three years ahead of schedule.
BHP has a targeted Indigenous recruitment campaign, which includes a tailored application process to take into account the cultural needs of applicants. The Academy attracts more Indigenous individuals into education through the proximity of training centres to local communities, a holistic curriculum specially designed for new to industry people, and the inclusion of sessions dealing with culture, capability and life skills.
This is supported by BHP’s partnerships with CQUniversity (CQU) and North Metropolitan TAFE (NMTAFE), who offer students weekly support sessions with face-to-face interactions, support in literacy and numeracy, Indigenous support and access to library resources.
BHP President Minerals Australia Edgar Basto said BHP was committed to creating a diverse and inclusive workforce and supporting the local communities in which it operates.
“Creating more opportunities for Indigenous people, particularly in the Pilbara and other local communities in which we operate, is an important focus of BHP. Combined with our commitment to accelerated training programs, I am proud that we are providing more opportunities for Indigenous people. Reaching this target ahead of schedule is a great achievement for the whole team but our commitment doesn’t end there - we know there is plenty more work to be done,” said Edgar.
“Our commitment to the Indigenous community—from employment, engagement with traditional owners and Indigenous businesses—is vital to our ongoing and sustaining relationship with Indigenous and Traditional Owner communities.”
In Western Australia, the Indigenous employment rate is higher than the national average – increasing from 9.2% in 2019 to 10.5% in 2021. Of the 231 apprentices and trainees currently in training at BHP’s Future Fit Academy in Welshpool, which provides heavy diesel mechanics and mechanical fitters for BHP’s iron ore operations in Western Australia, 20% are Indigenous.
The BHP FutureFit Academy recently took home the bronze award in the World Federation of Technical Colleges and Polytechnics (WFCP) Awards for Excellence alongside its partner training organisations CQUniversity and North Metropolitan TAFE (NMTAFE). Recognised in the top three on the world stage out of over 100 nominations for its contribution to Indigenous Education, this is a phenomenal achievement for the BHP FutureFit Academy.
South Flank, Western Australia Bowen Basin, Queensland
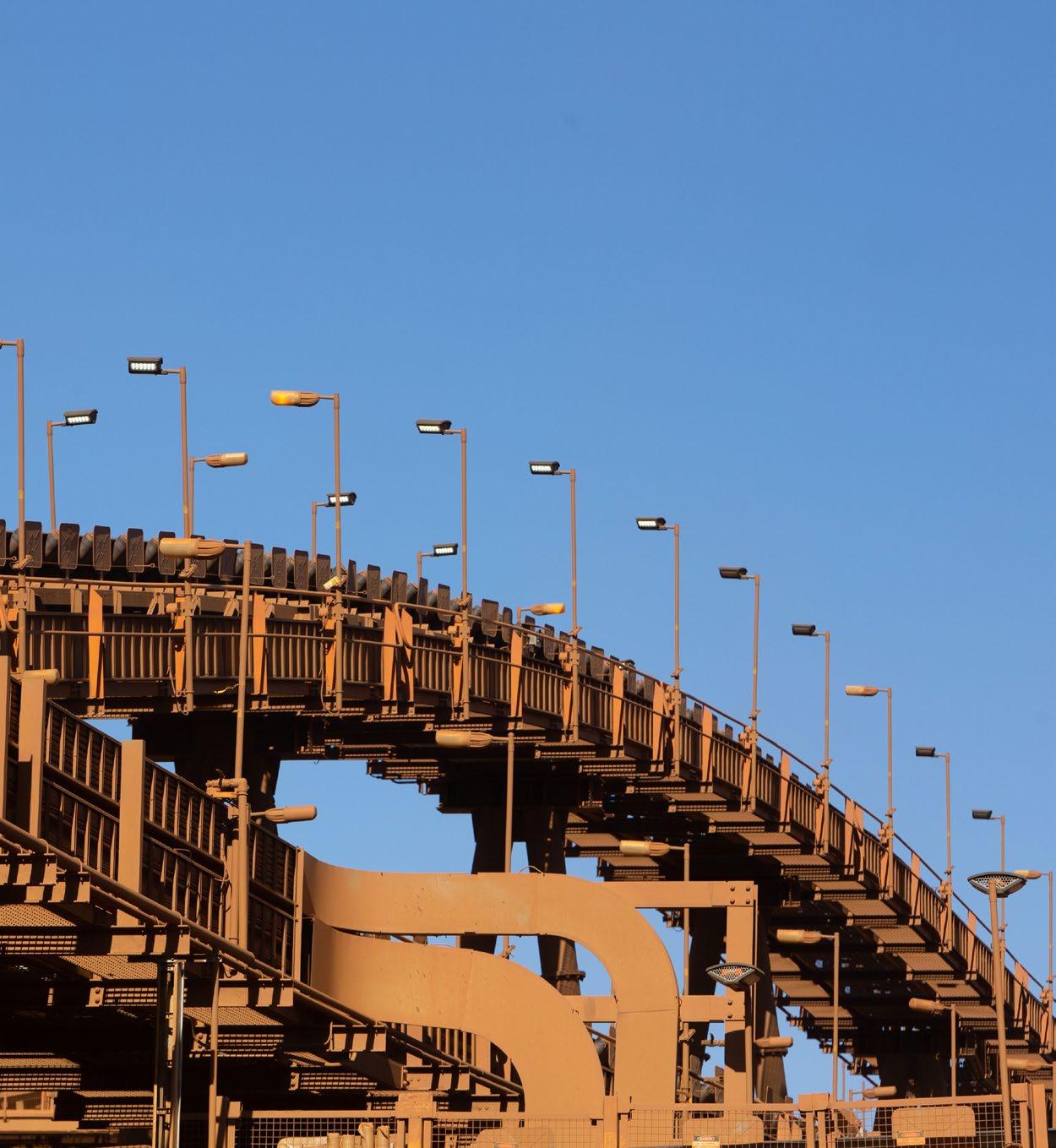
Further Information For further information about the BHP FutureFit Academy visit: bhp.com.au
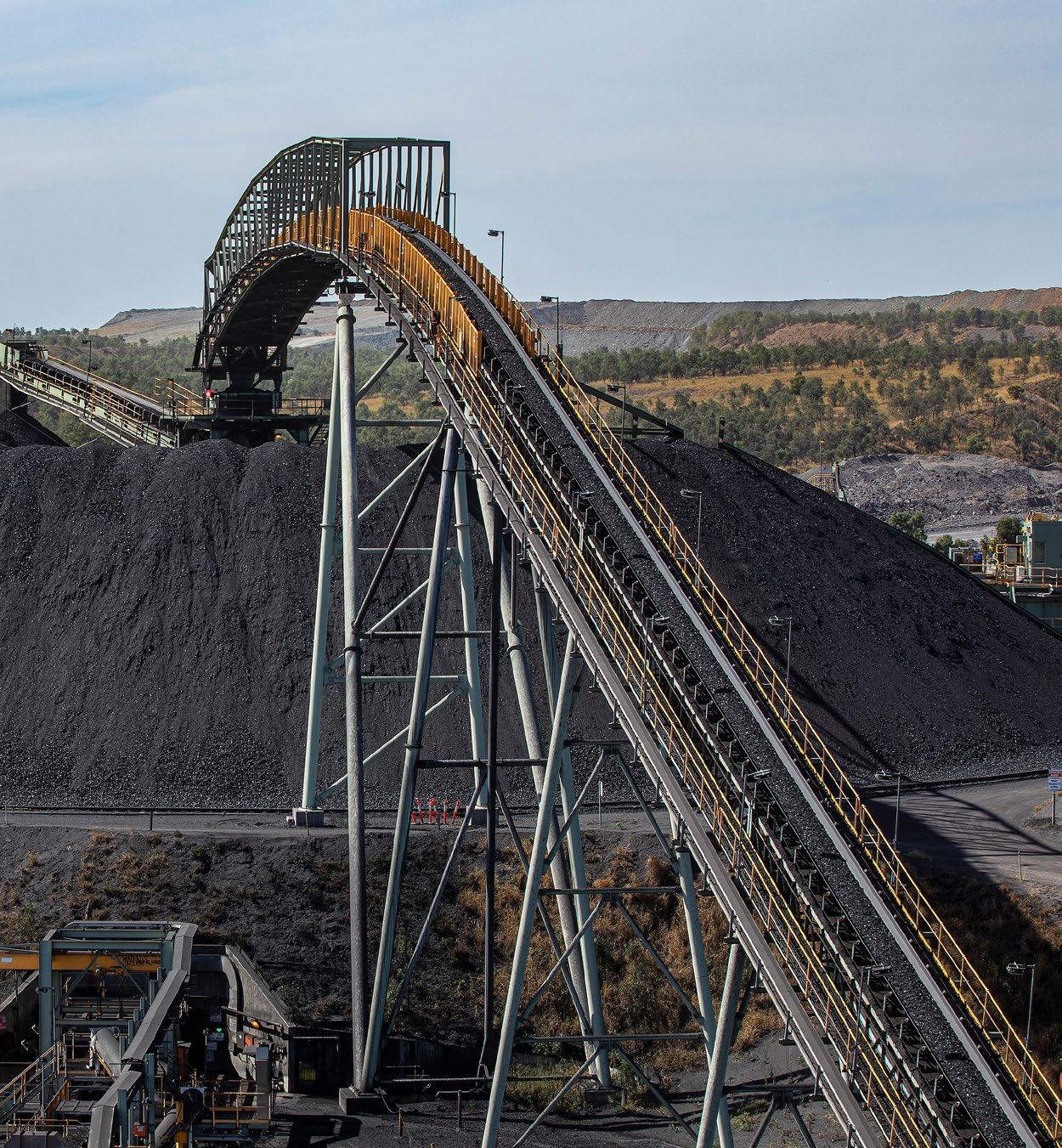
BRUCE CANNON WINS THE INTERNATIONAL INSTITUTE OF WELDING 2022 THOMAS MEDAL
Weld Australia would like to congratulate Bruce Cannon (Principal Welding Engineer, Weld Australia) on winning the International Institute of Welding (IIW) 2022 Thomas Medal. Bruce was presented with the award at the Opening Ceremony of the 75th IIW Annual Assembly of the International Institute of Welding (IIW) in Tokyo. Established in 1997, the Thomas Medal is awarded to an individual who has been involved in IIW and ISO international standards activities for over 10 years, and is recognised by their peers as having actively promoted international welding standardisation.

An Exceptional Contribution Bruce Cannon has made an exceptional contribution to the Australian welding industry over the last 40 years. He has helped to ensure that welding quality standards are paramount, improving safety both for welders, as well as members of the general public. Since 2004, he has been instrumental in the direct adoption of over ten ISO standards.
His involvement with ISO commenced in 2001 as Chair of the Australian and New Zealand standards committee WD-003 Welding of steel structures. He has also been the Australian representative for several other Standards Committees, including Terms and Definitions (WD-001), Health and Safety (WD-004), Weld Testing (WD-006) and Steel Structures (BD-001).
In these voluntary positions, Bruce has liaised with Pacific Rim countries, reviewed countless standards and other documentation, advising Standards Australia accordingly. In particular, Bruce’s review of ISO 9606-1 Qualification testing of welders – Fusion welding led to much of it being adopted in Australia within AS 2980 in 2004, and New Zealand in 2007. with BHP in 1977 after graduating with a Batchelor of Applied Science (Metallurgy) from what is now Federation University. Early in his career, he worked in areas such as mechanical testing, metallography and marketing before joining BHP Steel’s welding development group in 1985. He was involved in the welding and weldability testing of steels, weld repairs, electroslag roll reclamation, weldability of quenched and tempered steels, quality management and technical advice.
From 1993 to 1995, Bruce was seconded to Weld Australia (then the WTIA) as its welding engineer, providing technical support to the welding industry.
In July 1995, Bruce returned to BHP Steel, continuing to be involved in specialist weldability testing, resistance welding, weld monitoring, hot tapping, and customer support. He was a guest lecturer at the University of Wollongong for International Welding Technologist (IWT) and Engineer (IWE) students, and liaised with various research groups. Bruce’s work in Australian standards continued and in April 2001, he was appointed as Chair of committee WD-003 Welding of structures. In 2015, Bruce retired from BlueScope and joined Weld Australia as its Technical Publications Manager in February 2016. His duties include the revision of key technical literature as required, peer reviewing of technical reports, and engagement with standards organisations including attendance at relevant ISO meetings. Further details of Bruce’s involvement in standards is outlined below.
Chair of WD-003 In 1994, Bruce became a representative on a number of standards committees, including Welding of Structures (WD-003), Terms and Definitions (WD-001), Health and Safety (WD-004), Weld Testing (WD-006) and Steel Structures (BD-001). In 2001, Bruce was appointed as Chair of Committee WD-003 and a number of its subcommittees—a position he currently holds.
AS/NZS 1554 Series Arising out of the secondment and following his appointment as Chair of WD-003, it was apparent there were issues with the understanding of the AS/NZS1554 series and in particular, the qualification of welders was problematic. Bruce used his position to collate questions arising from industry and implement changes into the standards, as well as explanations in Technical Note 11 to further assist users. One major challenge he has managed is the use of dumped steel
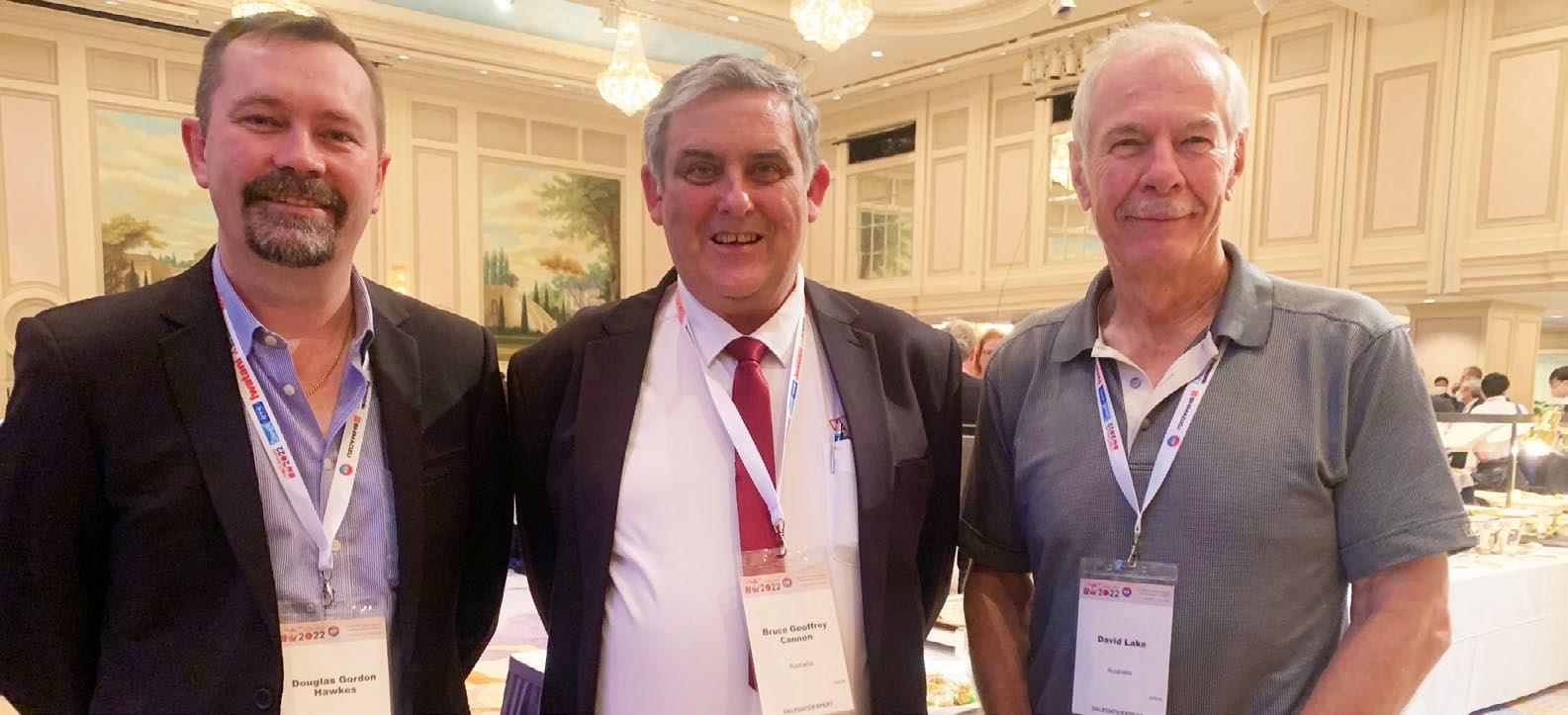
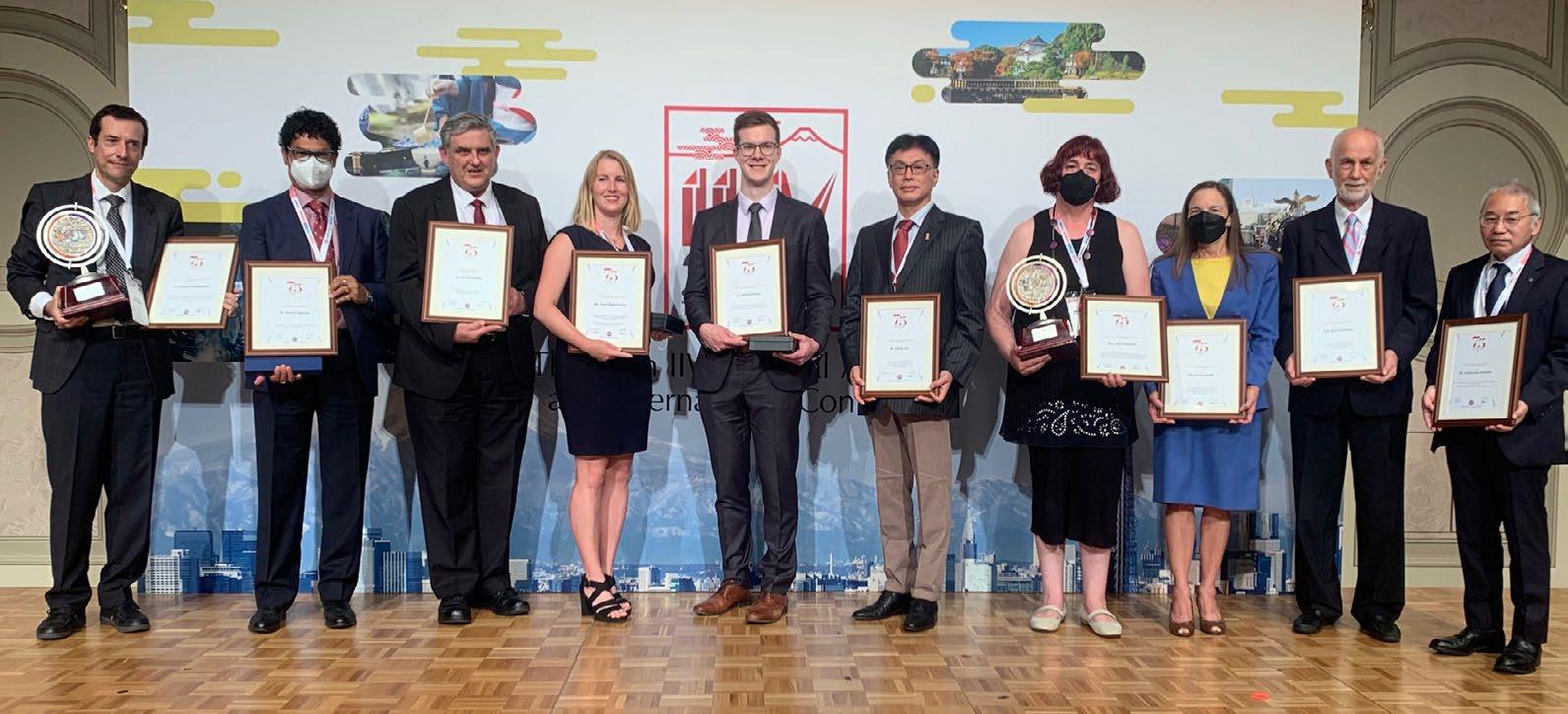
Photos
Left: Bruce Cannon is presented with the Thomas Medal in Tokyo by Dr Rick Polanin, President of AWS. Top: L to R: Doug Hawkes, Bruce Cannon and David Lake (Chair, Weld Australia). Bottom: The winners of the 2022 IIW Awards. Third from the left: Bruce Cannon.
contaminated with boron.
AS/NZS 2980 AS 2980:1987 had the weakness that it could not be used for the GTAW process. In 2003, Bruce reviewed the content of the then ISO 96061 and prepared a draft to align the requirements of AS 2980 with ISO 9606-1 and give cognisance to ISO drafts in circulation. A problem that Australia, USA and Canada identified at the time was the ISO draft was aligned with European thinking. Bruce recommended that Australia vote to support the position taken by the USA and Canada. He actively worked with the USA to assist in the production of a workable draft that could be considered for adoption in Australia. A standard was eventually produced that achieved consensus in 2012.
The innovations introduced to AS/NZS 2980 and the AS/NZS 1554 series proved revolutionary and of great benefit to the welding industry: 1. A table of welder qualification positions (both standards) was included that was identical to the then ISO 9606-1. 2. When published, AS/NZS 2980:2007 was approximately 90% aligned with what is now
ISO 9606-1. 3. AS/NZS 2980 allowed for portability of qualifications, a
concept adopted by some independent inspectors and training organisations.
AS/NZS 2980:2007 was well ahead of its time. Being aligned with ISO 9606-1, it paved the way for ISO 9606-1 to be introduced in Australia in 2017.
AS/NZS ISO 3834 In 2017, Bruce travelled to Berlin to present a request on behalf of Australia to the subcommittee for an interpretation on the status of ISO 3834. It was ruled to be a factory production control system. As a result of his work, the Bridge Code (AS 5100 series) was modified to mandate ISO 3834 conformance by fabricators, and more recently, it was mandated within AS/NZS 5131. There are now over 100 companies certified to ISO 3834.
AS/NZS ISO 9606.1 In 2016, with the short list of tenders for the various Federal Ship Building Programs all European based, Bruce recognised that the tenders would most likely mandate the use of ISO 9606-1 for welder qualifications. Accordingly, he submitted a project to Standards Australia to adopt ISO 9606-1 as AS/NZS ISO 9606.1. The project was accepted and the standard was published in 2017. To facilitate the adoption and use of AS/NZS ISO 9606.1, Bruce submitted project proposals for the adoption of key referenced testing and other ISO standards, all of which were accepted and have since been published.
In 2017 and 2018, Bruce attended three committee meetings in relation ISO 9606-1 and, at the Miami 2018 meeting, provided first hand feedback to the committee on Australia’s experiences with the standard. He remains a member of working groups on ISO 9606 at ISO, presenting an Australian perspective on this important standard.
AS/NZS 5131 and AS 4100 Bruce was heavily involved with the development of these ground breaking standards.
AS 3992 Recognising that AS/NZS ISO 9606-1 is here to stay, Committee ME-001 agreed that AS/NZS ISO 9606.1 be incorporated within AS 3992. As the drafting leader for the 2020 revision of AS 3992, Bruce ensured that AS/NZS ISO 9606.1 was given full recognition within the pressure equipment industry. It is anticipated that in a future revision of AS 3992, welder qualification will likely refer to AS/NZS ISO 9606.1, simplifying the welder qualification process.