
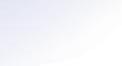
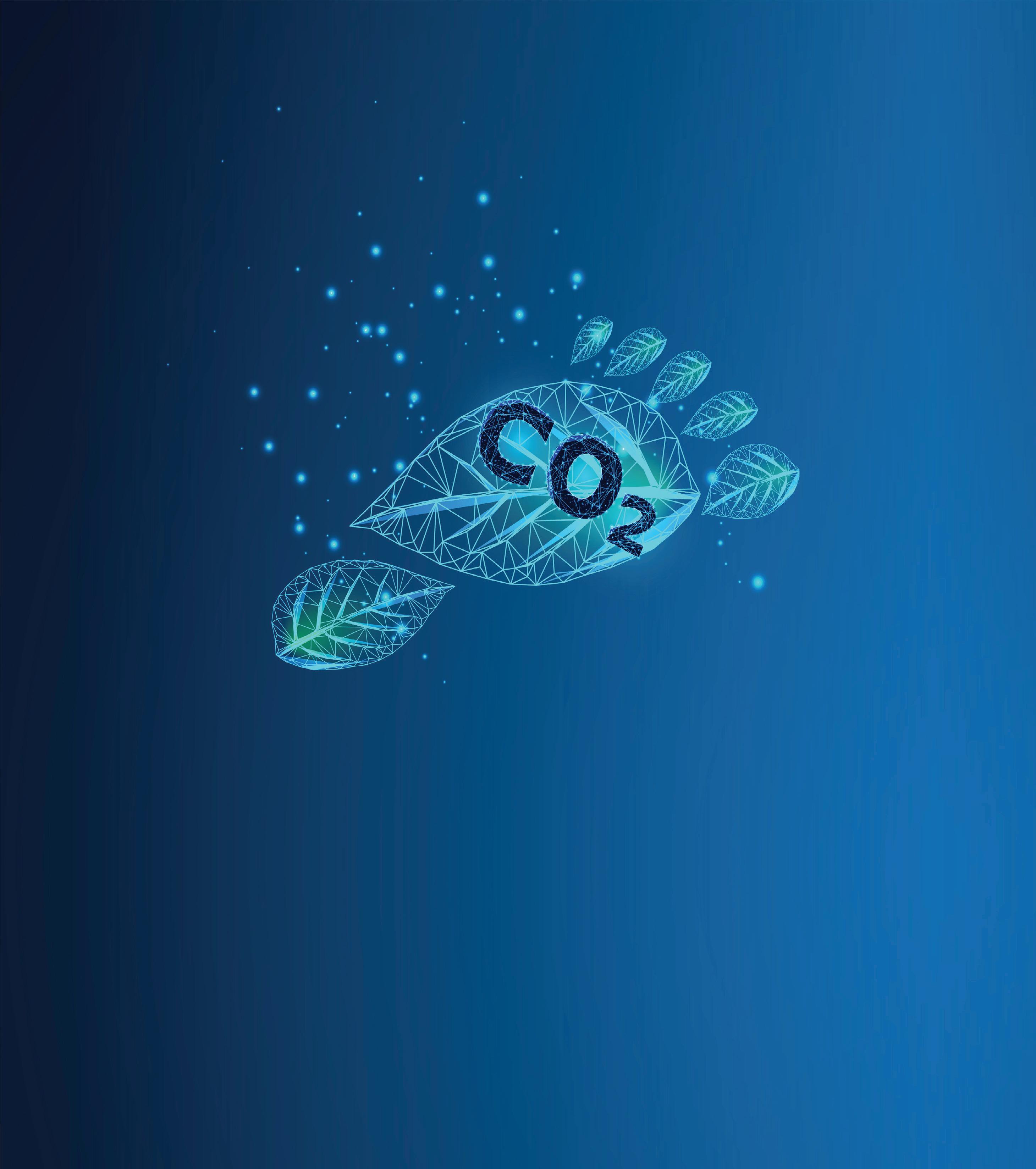
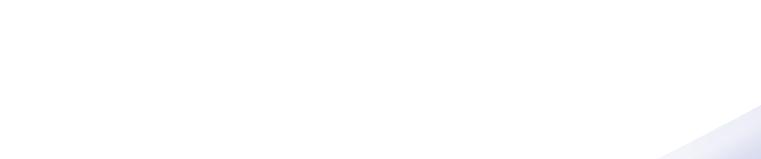
Information technology (IT) systems have traditionally been used to handle information and communication tasks, representing the ‘software’ realm. In contrast, operational technology (OT) systems control real-world production processes through physical devices. As more physical devices are connected to networks, there’s a growing trend towards the merging of IT and OT systems.
The new modular control systems, u-control M3000 and M4000, are at the forefront of this trend, combining control and edge computing systems into one. This integration allows for efficient data preprocessing and precise control directly at the machine, facilitating integration of complex automation solutions and IIoT applications.
These controllers are powered by u-OS, a real-time operating system developed by Weidmüller. It forms the foundation for managing applications, security and access control. Unlike closed systems, u-OS is built as an interoperable platform, ensuring that users are not locked into a proprietary system.
u-OS incorporates industry-standard container solutions like Docker, ensuring secure application integration with the device and flexibility in deploying user-generated apps. For real-time control applications, CODESYS is utilised for its proven compatibility with various fieldbus technologies. Additionally, open-source software like Node-Red is supported, enabling quick connections to industrial IoT and cloud services.
The series features a 1.2 GHz ARM A53 architecture in dual- or quad-core configuration, a generous 16 GB of flash memory for installing multiple applications, as well as 2 or 4 GB of DDR4 RAM. They support on the right side modular I/O expansion and on the left side options for SSD storage, 4G-LTE and more. Operating in ambient temperatures of up to 70°C, they are well suited for demanding edge computing applications.
The importance of OT cybersecurity has increased dramatically in recent times, with the convergence of IT and OT networks introducing greater cyber risk to industrial control systems.
There was a major wake-up call when NotPetya caused billions in damages and affected IT and OT environments alike, and since then attackers have grown more focused on industrial technology, exploiting poor IT/OT segmentation to gain access.
Because of the nature of OT networks and protocols and a lack of standardised technology, traditional IT security tools have generally been eschewed in favour of purposebuilt industrial cybersecurity tools. But due to the nature of exploits such as NotPetya taking advantage of weaknesses in both IT and OT systems, it may be necessary (dare I say it?) for IT and OT cybersecurity teams to de-silo and join forces in approaching cyber threats more holistically. Doing so can only improve communication, shorten incident response times and in the long run save costs on incident prevention and response.
And if modern processing and manufacturing enterprises are to remain competitive, then adopting modern technology infrastructures (such as modular control systems described in one of our articles) becomes an imperative, making the issue of better managing cybersecurity a top priority.
In the same way, modern industrial networks are rapidly moving to an Ethernet-based infrastructure in order to make digitalisation possible, and these networks need to be designed with all the robustness and fault tolerance of legacy technologies.
I hope you enjoy this issue of Process Technology, but as always more detailed daily news and new automation products can be found on processonline.com.au and by subscribing to our biweekly email newsletter.
Until next time...
Glenn Johnson Editor pt@wfmedia.com.au
Professor Tom Raimondo of the University of South Australia said that augmented reality, along with automation, is transforming the mining sector, allowing more work to be done remotely, saving time, money and removing many of the risks and travel for workers.
Professor Raimondo, Dean of Programs for Information Technology and Mathematics at the University of South Australia, is leading the development of VR and AR platforms to enhance core logging with machine learning, create fully digital reconstructions of mining operations and even simulate the drilling process.
This work has been facilitated through the MinEx CRC, the world’s largest mineral exploration collaboration. It includes projects such as the RoXplorer digital twin, an ultra-realistic simulation of the drill site of the future and the Exploration Metaverse, a collection of immersive AR and VR platforms to collaboratively view and analyse complex mining data with colleagues and experts from across the world in real time.
“Globally, it is becoming more difficult and more expensive to discover new mineral deposits because they are deeper than they have ever been,” Raimondo said. “It is also more difficult to extract and process minerals. VR and AR platforms give us a better way to visualise and interpret highly complex data and spatial information and make good decisions about where we should be targeting our exploration efforts.”
The RoXplorer digital twin, which replicates a drill site and its operations, enables industry workers to virtually run repeated drilling simulations safely and efficiently, with zero environmental impact.
“In terms of training workers, it also removes the hazards. Mining is inherently a dangerous activity, so the more we can transition to autonomous systems, the better off the mining industry will be,” he said.
His Project LIVE team in collaboration with UniSA’s Australian Research Centre for Interactive and Virtual Environments (IVE) is also exploring the potential of digital twins for other industries that involve hazardous processes, including forestry, construction and fire management services.
Raimondo explained that these technologies will enable Zero Entry Mining, where all operations are done remotely and the miners of the future will interact with digital twins and autonomous robots rather than rock cuts and blast sites.
Palo Alto Networks has published its ‘State of OT Security: A Comprehensive Guide to Trends, Risks, and Cyber Resilience’ report. The report surveyed 1979 operational technology (OT) and IT business leaders across 23 countries globally, including 103 leaders in Australia, to understand the trends, risks and cyber resilience strategies within OT environments, offering insights into the challenges faced by organisations across the globe.
Industrial operations across Australia are increasingly under regular and widespread cyber attacks, forcing operational shutdowns that result in lost revenue and significant remediation costs. At the same time, operators face increased compliance requirements as well as new risks posed by their adoption of new technologies and processes, including AI, remote access, cloud, 5G and robotics. As a result, industrial operators are increasingly conscious of the need to adapt cybersecurity to the new demands of the day.
Key findings from the report reveal a concerning landscape in OT security: Australian industrial operators the fourth most targeted globally. 82% of Australian respondents stated that their organisations had experienced a cyber attack in the past year — the fourth largest target globally. Equally alarming is the frequency of these attacks, with 70% of respondents experiencing attacks often monthly or weekly.
The report also found that cyber attacks can shut down Australian OT operations.The impact of these attacks has been significant, with over a quarter (28.6%) of Australian organisations having to shut down industrial operations in the last year due to a successful attack, whether as a pre-emptive measure or due to actual disruption.
Friction between OT and IT still a challenge, however. Despite the urgency, there remains a disconnect between OT and IT teams, hindering coordinated responses to threats, especially regarding security investment. When asked to describe the relationship between OT and IT, 40% of respondents stated that it was frictional, with only 14% answering that their teams are aligned.
The WA Government has launched a new prospectus, dubbed ‘Western Australia: Advancing the Future of Manufacturing’.
The prospectus targets the government’s priority sectors for growth, including energy; defence; mining and mining equipment technology and services (METS); space industries; primary industries; and health and medical life sciences.
Stephen Dawson, who serves as Minister Assisting the Minister for State and Industry Development, Jobs and Trade, released the prospectus at the inaugural meeting of the Advanced Manufacturing Council. Established to facilitate engagement between the Western Australian manufacturing sector and government, the Advanced Manufacturing Council will play a role in building the state’s manufacturing capability.
“Advanced manufacturing is not just what we make, but how we make it,” Dawson said. “This prospectus is a game changer and will profile WA’s advanced manufacturing capabilities and achievements on a national and international stage.”
Adopting advanced manufacturing technologies, processes and business models will enable WA manufacturers to increase their competitiveness in domestic and global supply chains and contribute to the value-adding potential of WA’s export industries. Growing advanced manufacturing capability will also help to diversify WA’s economy and generate secure local jobs for Western Australians.
The ANSTO engineering and project team recently installed a new safety shutdown instrumentation and control system (I&C) for the OPAL multipurpose nuclear reactor. The expert engineering team comprising Cristina Flego, Shalini Sharma and Queenie Wong completed the installation and commissioning of the new system during a scheduled shutdown, working with the vendor to design and test the replacement system.
“It is currently up and running smoothly in the background to help with the management of some containment and safety systems, while the reactor is in shutdown mode,” Flego said. “Its primary role when the reactor is operational is to provide frontline monitoring of key reactor parameters and initiate an automatic shutdown for safety purposes if necessary.”
A decision was made to replace the system due to its obsolescence and the unavailability of spare parts from the vendor. The shutdown of the reactor for the replacement of the cold neutron source was an opportune time to complete the complex task.
Over about eight weeks, the team removed and replaced all parts of the system in the rather confined spaces of the cabinets that house the system. This involved replacing all the old equipment, connecting all the interface cabling and then checking that it worked properly.
The system itself was designed as a high reliability safety system and ANSTO provided the necessary additional qualifications required for a nuclear environment.
Konica Minolta Australia has announced that Kinrise Snackfoods, an Australian food manufacturer, has deployed four AMRs from Mobile Industrial Robots (MiR) purchased from its Australia and New Zealand distributor, Konica Minolta Australia, to automate operations across one of its manufacturing facilities.
The four AMRs deployed by Konica Minolta Australia across the Kinrise Snackfoods manufacturing facility automate the pallet handling process while simultaneously minimising manual intervention and increasing operational efficiency and safety. Using AMRs creates a seamless, end-to-end process as they are designed to autonomously transport full pallets from the palletising robot cells to the hood wrapper, and then manage the distribution of empty pallets from an auto de-stacker back into the palletising cells.
“The implementation of MiR robots at Kinrise Snackfoods’ facility has given us greater productivity, greater operational efficiency and improved our safety overall on our site. It has really been a valuable investment for Kinrise Snackfoods,” said Kathy Gavrilidis, Head of Operations, Kinrise Snackfoods.
Alpha HPA has announced it is set to establish the world’s largest single-site, highpurity alumina products refinery following a Final Investment Decision (FID) on Stage Two of the HPA First Project in Gladstone, Queensland.
Alpha HPA’s Managing Director Rimas Kairaitis said the company will now immediately commence project execution for the full-scale, Stage Two facility, having already advanced several key elements of the project’s implementation.
“Construction of the 10 hA, state-of-the-art, full-scale facility will commence mid-2024, on the existing HPA First Project site at Yarwun, near Gladstone, where the company’s Stage One facility is already in small-scale production of its high-purity aluminas and aluminium materials product range,” Kairaitis said. “Stage Two will encompass full-scale production of up to 10,000 tonnes of high-purity aluminium materials per year creating 120 ongoing local jobs on top of 300 jobs during construction.
Alpha HPA’s process allows for the extraction and purification of aluminium from industrial feedstock, producing materials of exceptional purity for high-technology applications, including the semiconductor, lithium-ion battery and LED lighting sectors.
The Australian Government has announced the concept design partners for South Australia’s new Nuclear-Powered Submarine Construction Yard (NPSCY).
In a joint press release, the Minister for Defence and the Minister for Defence Industry announced that Kellogg, Brown and Root (KBR) and an AECOM and Aurecon Joint Venture have been announced as the design partners.
KBR has extensive experience in supporting design and project management for defence infrastructure facilities across the nation and will design the area of the NPSCY that will be used for steel processing and fabrication facilities.
The AECOM and Aurecon Joint Venture will deliver the concept design for the rest of the NPSCY site which will support outfitting, consolidation and commissioning of Australia’s conventionally armed, nuclear-powered submarines.
The design teams collectively bring together nuclear infrastructure specialists and experienced personnel from previous shipyard infrastructure projects at Osborne, Henderson and in AUKUS partner nations.
The press release said that the announcement of the design partners follows the March announcement of Australia’s sovereign submarine build and sustainment partners and continues to demonstrate progress towards building SSN-AUKUS submarines in Adelaide.
The NPSCY development will be in excess of 75 hectares and will be built to the highest security and safety standards.
Constructing the infrastructure at the NPSCY will rely on Australian engineering and design consultants, project controls specialists, project
Downer EDI has announced it has been awarded a contract to deliver water, sewerage and recycled water services in south-east Queensland.
The contract, awarded by Unitywater, commences in May 2024, with an initial five-year term plus three two-year extension options. The contract is valued at an estimated $600 million to Downer over the initial five-year term.
Downer will be responsible for delivering capital works for the water, sewerage and recycled water networks within the Sunshine Coast and Moreton Bay regions, as well as works across Unitywater’s 17 sewerage treatment plants in the Sunshine Coast, Noosa and Moreton Bay regions.
The Chief Executive Officer of Downer Group, Peter Tompkins, said the contract reinforced Downer’s position as a leading provider of water and wastewater services in Australia and New Zealand.
“We look forward to working closely with Unitywater to deliver these vital services to this rapidly growing region in south-east Queensland and contributing to Unitywater’s net zero emissions targets as well as creating sustainable employment outcomes and opportunities for local service providers and suppliers,” he said.
Establishing a converged IT/OT security operations centre presents a unified front against threats to IT and OT assets while reducing overheads.
Until recently, enterprise operational technology (OT) environments have been air-gapped from organisations’ information technology (IT) environments and connections to the internet. As such, OT has long been immune to a great extent from cyber threats, and therefore, cyber defence has not been a priority until relatively recently. The importance of OT cybersecurity has increased dramatically with digital transformation, because the convergence of the distinct worlds of IT and OT introduces cyber risk to highly vulnerable industrial control systems (ICS).
When it comes to the need for strong industrial cybersecurity, many enterprises received a major wake-up call when NotPetya — widely regarded as the one of the costliest and most destructive cyber attacks in history — caused billions in damages and affected IT and OT environments alike. NotPetya’s infiltration of OT was largely unintentional and opportunistic collateral damage made possible by IT/OT convergence. However, in the years since NotPetya, adversaries have grown more deliberate in their targeting of industrial technology, exploiting poor IT/OT segmentation to gain access to targeted systems. To combat the growing threat of cyber attacks against OT, CISOs are faced with the task of protecting industrial technology that was not designed with security in mind.
As the digitisation of OT and other industrial technologies grows increasingly ubiquitous, security leaders cannot afford to leave things to chance when it comes to the threat of a cyber attack against critical infrastructure and industrial processes. That being said, security teams face some unique challenges in defending OT assets. In particular, the use of proprietary protocols, a lack of standardised technology and the complexity of OT environments make traditional IT security tools, legacy systems and network equipment ineffective — thus necessitating purpose-built industrial cybersecurity tools.
While OT does require specific tools for industrial cybersecurity, one area where enterprises can leverage their existing resources and personnel is the security operations centre (SOC). The best industrial cyber defence strategy is to present a unified front against threats to IT and OT assets by establishing a converged SOC that protects these once separate technology environments in a holistic manner.
The SOC is already widely accepted as a hallmark of mature IT security programs. By consolidating OT security with your existing, ITcentric SOC, you can gain greater visibility across the entire enterprise, enhanced security monitoring and comprehensive threat mitigation. IT/OT SOC convergence also enables a standardised approach to enterprise security that facilitates a secure digital transformation by enabling rapid configuration changes, new policy implementation and compliance to new regulations or industry standards from one view. Collectively, these benefits amount to better risk management.
Like any major cybersecurity initiative, executive buy-in is typically a prerequisite for moving forward with a consolidated approach to IT and OT security. To do this, you will need to clearly articulate the benefits of a converged IT/OT SOC.
A holistic approach to IT and OT security grants the CISO a singular, cohesive view of risk for the entire organisation. Moreover, a converged IT/OT SOC team that is accountable for all risks allows for centralised incident response that includes triage, investigation and mitigation. As a result, organisations are able to respond to security incidents faster and more effectively.
Cyber threats to OT almost always enter via the IT network before spreading laterally to the OT environment. For this reason, a singular OT security taskforce that operates separately from existing IT security teams would be far less effective and significantly more costly than an integrated IT/OT SOC.
In addition to delivering the performance advantages described above, properly executed convergence of the SOC to secure IT and OT can significantly reduce technology total cost of ownership (TCO) while utilising the skills of existing staff.
Since the approach to IT/OT SOC consolidation detailed here largely relies on leveraging existing personnel rather than hiring new employees, it is designed to optimise and expand upon current security capabilities with minimal headcount impact. Moreover, this approach requires almost no change in SOC personnels’ method of operation, and an integrated IT/OT SOC eliminates the need for redundant roles across two separate teams.
Executed properly, IT/OT SOC consolidation can also substantially reduce technology TCO and complexity, since this approach encourages the use of existing tools whenever possible. Organisations can maximise ROI on existing security management interfaces, detection and response tools, and network security technologies by integrating OT security datasets, alerts and forensic information with IT security tools and datasets.
When it comes to establishing a converged IT/OT SOC, attaining stakeholder buy-in from leadership is just a precursor to the real work. Below are some essential steps that have proven instrumental in optimising the efficacy, efficiency and implementation time of such initiatives.
Appoint a designated IT/OT cybersecurity program manager
Once you attain the stakeholder support necessary to move forward with IT/OT SOC consolidation, you need to designate one individual to lead this initiative, reporting directly to the CISO. The IT/OT cybersecurity program manager will play a central role throughout the remaining steps described below, so great care should be taken to select a strong, detail-oriented leader to oversee this undertaking.
Ideally, the IT/OT cybersecurity program manager should be appointed internally. In large part, this is because having strong, pre-existing working relationships within the organisation can be valuable for overcoming some of the challenges involved with building such a program. However, given the importance of the role, it should be treated as a full-time position in itself, rather than an additional responsibility taken on.
Achieve optimal alignment with existing cybersecurity capabilities
Since maximising ROI is one of the key advantages of a consolidated IT/OT SOC, it is important to leverage your existing cybersecurity infrastructure as much as possible. This necessitates a thorough assessment of these capabilities, with the objective of identifying areas in which tools already at your disposal can be leveraged, while zeroing in on gaps in existing technology where you will need to bring in new solutions.
A strong, centralised ecosystem of integrations can significantly bolster ease of maintenance and upgrades, while also enabling automatic health checks and monitoring. Integrations also facilitate the incorporation of existing standard operating procedures (SOPs) and other playbooks into the converged IT/OT SOC.
Gain visibility into IT and OT security alerts within the OT environment
With increased interconnectivity to IT networks, OT environments are exposed to IT-centric cyber threats they were previously isolated from. Over the past several years, cyber attacks such as WannaCry and NotPetya have wrought havoc upon OT environments around the globe. While devastating, these attacks have also led to increased awareness of the need to detect the cross-proliferation of IT cyber threats within OT environments.
As shown in Figure 1, cyber threats to OT typically enter the enterprise technology environment via the IT network, before moving laterally to compromise OT assets. Given this typical infection pattern, it is crucial to have unified visibility across IT and OT environments.
Since SOC personnel are already trained to handle IT security alerts, it is often the case that only minimal changes need to be made to existing playbooks to make them applicable to OT. And since your team likely has existing access to IT security technologies capable of detecting IT cyber threats, all that is required of this step is to ensure those abilities are properly applied to your OT environment. However, your team will need purpose-built technology that effectively establishes visibility into the OT environment in order to take advantage of these existing capabilities.
Once your SOC has visibility into IT security alerts, the next task is to gain visibility into
OT-specific alerts. To effectively monitor and defend against threats to their organisation’s OT environment, IT security teams need realtime visibility into three integral dimensions:
• Asset visibility: Having detailed visibility into all devices on an OT network, covering extensive attributes is essential for identifying and assessing vulnerabilities with precision.
• Network visibility: Visibility enables easy, rapid detection of misconfigurations, traffic overloads and other issues which may pose risks to reliability, availability and safety.
• Process visibility: Being able to track OT operations — as well as the code section changes and tag values for all processes which involve OT assets — is also crucial for identifying abnormal changes in OT process values or unusual behaviours indicative of an early-stage attack, operational reliability issues or other potential risks within your industrial environment.
Designate a cybersecurity site leader for each OT site
Likely the most involved step outlined here — depending on the number of sites your team is responsible for securing — will be the need to designate an OT cybersecurity site leader (CSL) at each of your organisation’s physical OT sites who will serve as the eyes and ears of your converged IT/OT SOC for that location.
The CSL for each facility will serve as a critical liaison between OT personnel and the SOC. In contrast with the IT/OT cybersecurity program manager role, which involves a great of strategic leadership, the CSL role is an additional responsibility taken on by a designated onsite staff member to serve as a point person in the event of an incident. As such, the CSL must be knowledgeable about SOC procedures, requirements and objectives — or alternatively, undergo thorough education and training on these subject matters.
Despite the importance of the CSL role, this responsibility can typically be assumed by an existing staff member and be handled alongside their existing work responsibilities. During a security incident, the CSL must be prepared to lead rapid response, coordinating with SOC and site-specific OT personnel. The CSL must be able to accurately gauge the severity of the event and weigh the trade-off between the risk at hand and the potential operational disruptions that mitigation actions could cause.
Having appointed a CSL for each physical OT site, the next step is to establish a security incident response team (SIRT), which will be in charge of overseeing all OT security practices and standard operating procedures (SOPs). By empowering your newly converged IT/ OT SOC with purpose-built SOPs, the SIRT will enable your organisation to strengthen its holistic industrial cybersecurity across IT and OT environments over time by continuously adding new responses and tailoring existing responses as your organisation encounters new types of threats and incidents.
For smaller organisations, the SIRT role(s) could be entrusted to existing employees in order to avoid unnecessary costs of hiring new personnel. Qualified individuals may include members of the security team who are familiar with OT processes or, conversely, personnel from the OT side with cybersecurity knowledge. For organisations with large IT/OT environments, hiring or appointing a dedicated individual or team to focus primarily on operating the SIRT may be beneficial.
When it comes to developing SOPs for your converged IT/OT SOC, it is important to remember that it’s not necessary to reinvent the wheel. It is best to start with some standard SOPs for addressing common scenarios. It must be noted that the same situation may require a different response in an OT context than in an IT context. As such, it’s important for security leaders who are largely unfamiliar with OT to seek guidance and expertise in establishing these initial SOPs.
In any situation where the IT/OT SOC encounters an unfamiliar situation in which
THE BEST INDUSTRIAL CYBER DEFENCE STRATEGY IS TO PRESENT A UNIFIED FRONT AGAINST THREATS TO IT AND OT ASSETS BY ESTABLISHING A CONVERGED SOC THAT PROTECTS THESE ONCE SEPARATE TECHNOLOGY ENVIRONMENTS IN A HOLISTIC MANNER.
existing SOPs are not effective or applicable, they should coordinate with the SIRT to determine the most appropriate course of action. When necessary, the SIRT may escalate the alert to external cybersecurity services, typically in scenarios where the threat is severe and the most effective course of action is unclear.
Once the incident at hand has been addressed, the SIRT will write a new SOP detailing how to respond to the event next time it occurs.
The five essential building blocks of a converged IT/OT SOC described in the previous section are ambitious, but they are necessary for managing risk effectively within industrial environments. The ease, effectiveness, cost efficiency and speed at which they can be implemented can be dramatically enhanced by partnering with a vendor that has tried-and-true expertise, experience and purpose-built technology for securing industrial technology environments.
The Compact Controller 100 offers integrated I/O and supports standard fieldbus protocols for wide interoperability benefits.
LAPP Australia Pty Ltd
https://bit.ly/3VDed9n
The ARK-1125 series is a line of palm-sized intelligent edge computers designed to meet the demands of various IoT applications.
Advantech Australia Pty Ltd
https://bit.ly/3VqzxPa
The Microsonic MIC+ series of ultrasonic sensors offer a sensing distance of up to 8 m, making them suitable for diverse industrial environments.
Pacific Automation
https://bit.ly/4bBMT0B
Featuring a flameproof enclosure, the 78E Series Ex rotary encoder from Pepperl+Fuchs is designed for applications in hazardous areas.
Pepperl+Fuchs (Aust) Pty Ltd
https://bit.ly/3V68p6r
Wastewater and effluent can take many different forms, from relatively clean water that can be safely discharged to the environment with little or no treatment, to extremely challenging effluent containing high levels of dissolved or suspended solids, chemicals and biological material, many of which can no longer be discharged to the environment or even public sewage systems.
The exact types of treatment used will vary depending on many factors; however, evaporation is becoming increasingly popular as a way of effectively separating the liquid and solid waste streams.
Examples of difficult effluents
Landfill leachate is formed from water that has entered the landfill from external sources (rainfall, surface water and groundwater) as well as the putrefaction of waste materials in the landfill. Landfill leachate typically contains both dissolved and suspended materials, such as organic matter, cations, heavy metals and other complex organic molecules like PCBs and dioxins. Where large volumes of building waste or gypsum have been disposed of, hydrogen sulfide may also be an issue.
Industrial wastewater streams can include heavy metals, halogen compounds and other potentially harmful nutrients or suspended solids. Most countries or regions around the world have strict rules on the treatment and discharge of such waste streams, including requirements for the ‘zero discharge’ of wastewater.
High levels of dissolved or suspended organic materials can also make effluent very difficult to treat. A few examples include liquid tannery waste, effluent from fish farms and wastewater streams from abattoirs or even blood-processing laboratories.
Because of this variation in material and treatment situation there is also a wide range of well-known treatment techniques that can be used to treat them. Nowadays, the use of evaporation technologies to separate difficult effluents into water and solid waste streams (or highly concentrated sludges) is becoming increasingly common.
Zero liquid discharge and evaporation
Zero liquid discharge (ZLD) is a liquid waste stream treatment that involves transforming liquid waste streams into clean water (which can be reused) and a minimum volume of solid residues. It is particularly suitable for effluents that are hazardous, toxic or difficult to treat using other methods. A well-designed ZLD system will minimise or eliminate liquid waste streams, resulting in clean water for reuse or environmentally friendly discharge, and a solid residue suitable for further processing or safe disposal.
However, separating the water from the effluent requires large amounts of energy: it takes roughly six times more energy to evaporate water (latent heat) at its boiling point than the energy needed to actually bring it to that boiling point (sensible heat). For this reason, the evaporation processes used for ZLD usually include energy optimisation in the form of multistage evaporators, thermal vapour recompression (TVR) or mechanical vapour recompression (MVR).
HRS has installed a number of evaporation systems to treat difficult effluents. Some of these are true ZLD systems, while others reduce the volume of liquid as sludges to enable more efficient management or further treatment.
Depending on the effluent being processed, a range of technologies can be used to design the most optimal ZLD process. Energy optimisation methods (multistage, TVR, MVR) can be combined with different heat transfer technologies and the overall process is separated into three steps:
• Evaporation/concentration: The product is concentrated to just below its maximum concentration (saturation).
• Cooling: If the maximum solubility curve is steep (large concentration at high temperature, low concentration at low temperature), the product obtained in step 1 is cooled, provoking immediate precipitation of dissolved solids.
• Crystallisation: Crystallisation of the solids produced in step 2 occurs in specially designed crystallisation tanks. A supernatant layer of concentrated solution remains after this stage and is returned to step 1 for reprocessing.
The coolers and evaporators used in these situations must be designed to work with difficult materials with very high fouling potential. For this reason, a typical evaporator will use scraped surface evaporators that are self-cleaning and maintain optimal evaporation rates.
Scraped surface coolers are also used for cooling the saturated solutions that are sent to the crystallisation tanks. The result is an efficient process that can work continuously to treat the most challenging materials and effluents.
The W10 photoelectric proximity sensor from SICK comprises four variants, which differ in their operating distances and mounting options.
The W10 does away with slide switches, potentiometers and rotary knobs by providing a touchscreen display. A screen lock protects the settings against access or unwanted changes. As an alternative to operation on the device, the W10 can also be set easily via IO-Link and can also communicate via this interface. The W10 has two digital outputs for the output of switching signals.
The W10 combines a class 1 laser light source with a fast receiver evaluation line, achieving detection results with high repeat accuracy both in the short-range version with working distances between 25 and 400 mm and in the long-range version with ranges from 25 to 700 mm. In speed mode, the response time is 1.8 ms.
The photoelectric proximity sensor offers individual teach-in options for specific adaptations. In addition to the usual 1-point teach, which detects objects at a defined distance, a 2-point teach enables objects of different heights to be detected. A manual mode extends the teach options for more flexibility. Both the short- and long-range versions of the W10 are available in two housing variants: one for standard mounting with a 1″ hole and one for hybrid mounting via the M18 thread on the front or the 1″ hole on the side.
SICK Pty Ltd www.sick.com.au
The AchieVe PSA series of switchmode power supplies offer basic DC power for general industrial applications. Features include universal AC input voltage range, built-in constant current circuit for reactive loads, adjustable output voltage via potentiometer and quick installation by 35 mm DIN rail mounting.
The PSA series power supplies accept a universal 85–264 VAC/120–375 VDC input voltage and provide 12, 24 or 48 VDC adjustable output (±10%) options in 75, 120 and 240 W models. They offer up to 90% efficiency and are available in rugged aluminium or thermoplastic housings.
AchieVe PSA series of switching power supplies are designed with the essential features needed for industrial applications. With protection as a standard, the PSA series offers overvoltage, overcurrent, short circuit and overtemperature protection. Their overcurrent protection is designed to operate in constant current mode, making the PSA series suitable for inductive and capacitive loads.
All models are UL listed, UL recognised, RoHS compliant, and UKCA and CE marked.
Direct Automation Pty Ltd www.directautomation.com.au
The LevelCon STARPIN is a solar-powered level measurement device for use in industries such as chemical manufacturing and water treatment, as well as for fuel storage monitoring. It has been used for tracking substances like bitumen emulsion and milk in challenging environments, by pairing it with precise radar sensors. STARPIN can also be extended to monitoring an array of materials including fuels, lubricants and gases, fulfilling the critical needs of LP gas and generator fuel level monitoring.
With its mobile-based system and selection of sensors (pressure, sonic, radar, lidar), the STARPIN offers a wide range of remote monitoring capabilities, including temperature, humidity and pressure, providing real-time data for improved decisionmaking. Its data analytics feature anticipates usage patterns and refill needs, minimising risks associated with depletion or overflow. The device’s design provides easy installation across various set-ups, from single tanks to extensive networks, supported by an IP67-rated enclosure and a magnetic base for attachment and operation in extreme conditions.
The STARPIN is designed to enhance operational efficiency, safety and productivity by enabling remote monitoring and reducing the need for manual inspections. Its customisable approach, supported by a user-friendly app and cloud portal for updates, along with features like alarm-capable inputs and automatic sensor checks, makes the STARPIN a solution for modern inventory management challenges.
Metromatics Pty Ltd www.metromatics.com.au
The Beckhoff CX5300 embedded PC series uses Intel Atom processors from the x6 series (Elkhart Lake), helping it to offer up to 60% more computing power than the CX5200 series.
The CX5300 is a fanless system and is available in two device variants: the CX5330 with an x6214RE Intel Atom processor (1.4 GHz, two cores) or the CX5340: with an x6416RE Intel Atom processor (1.7 GHz, four cores).
In the basic configuration, the devices are equipped with 4 or 8 GB of DDR4 RAM, two independent, gigabit-capable Ethernet interfaces, four USB 3.1 interfaces and one DisplayPort. A wide range of additional connection options or gateway functions is available due to an optional interface, which can be fitted ex-factory, and the I/O level, which can consist of either E-bus or K-bus terminals. In addition, a system module or fieldbus module from the CX2000 series can be plugged in via the high-pole connection on the left-hand side of the device.
The CX5300 series also includes an internally electrically isolated power supply unit with UPS OCT capability, the built-in capacitive 1 s UPS for persistent data storage and low power consumption.
Beckhoff Automation Pty Ltd www.beckhoff.com
Since the closure of its vehicle manufacturing, Toyota Australia’s Altona Emissions Testing facility in Victoria has been transformed into a demonstration-scale hydrogen production, storage and refuelling plant.
The primary objective of the project was to demonstrate the process of generating, storing and utilising hydrogen gas, including demonstrating the use of a percentage of renewable energy. As part of the project, Toyota Australia engaged with Emerson to supply the control and safety systems.
The Toyota demonstration project shows that a combination of onsite solar PV with battery storage can provide the facility with reliable and continual power supply. The facility is also connected to the grid. The project demonstrates that hydrogen produced onsite can fuel hydrogen-powered vehicles and supply electricity to the Altona site through the use of a fuel cell. The project also involved the building of a Hydrogen Education Centre to promote hydrogen innovation and awareness.
The challenge for the Emerson project team was to connect a wide array of OEM systems, all using a variety of communications protocols. Engineering connections between the systems ran the risk of building a complex, cumbersome infrastructure that increased costs, while potentially delaying the project and impeding efficient maintenance across the lifecycle of the plant.
The Toyota project team collaborated with Emerson to create a process orchestration layer connecting a system consisting of power meters, an electrolyser, a fuel cell, a hydrogen refueller, a solar and battery inverter system and instrumentation to collect data for system monitoring and reporting. Much of the data collected will be shared with the Australian Renewable Energy Agency (ARENA) to contribute to a nationwide pool of information from ARENA projects. ARENA provided approximately 40% of the Toyota project’s funding.
Toyota used Emerson’s DeltaV Automation Platform to integrate the various OEM systems needed to run the hydrogen system effectively and efficiently. The project team selected the DeltaV Distributed Control System (DCS) and Safety Instrumented System (SIS) to manage operations such as differentiating between deep and normal cycle drawdown of the hydrogen storage vessel.
The DCS and SIS are natively integrated with Emerson’s DeltaV PK controller to eliminate complex configuration between the automation equipment, managing orchestration for the many skids and systems running across the plant. The Toyota team converted a wide variety of communication protocols from the many OEM systems to a common protocol — EtherNet/IP — and directly terminated them on the DeltaV PK controller to reduce communication complexity, lowering project costs and shortening the project schedule.
The Emerson team also saved significant time and effort in integration by deploying the DeltaV DCS and SIS with Emerson’s PACSystems RX3i CPL410 Edge Controller to gather data from the solar PV and battery system via a web-based API. WebAPI connections provide access to renewable energy data, system energy efficiency calculations and data from the site’s existing 500 kW solar array. Rosemount infrared flame detectors also help keep personnel and operations safe.
Toyota’s highly connected architecture readies the plant for future expansion, enabling the organisation to add future requirements such as remote operations and data analytics more easily, without the need for complex engineering.
Emerson www.emerson.com/au/automation
In an era where technological advancement defines progress, the launch of the iC2-Micro by Danfoss, now introduced into the Australian market by Pacific Automation, marks a pivotal moment. As a leading sales channel partner for Danfoss, Pacific Automation is at the forefront, integrating innovation with customer-centric solutions.
A legacy redefined
Building upon the trusted foundation laid by the VLT® Micro Drive FC 51, the iC2-Micro stands as a testament to evolution, embodying more than just an upgrade. It represents a revolution in motor control and application versatility. With a power range extending up to 22 kW and advanced features that cater to a broad spectrum of industrial applications, the iC2-Micro is not just an answer to current needs but a gateway to the future.
Design philosophy: compact, intelligent, powerful
The iC2-Micro has been sculpted with precision to offer an unparalleled blend of power and compactness. The drive boasts user-friendly interfaces, condensed functionality, and simplified commissioning. Its design is a tribute to efficiency, fitting a multitude of applications into a robust and compact package that promises reliability even in the most complex scenarios.
Installation and operation: A streamlined experience
The iC2-Micro simplifies the journey from installation to operation. It features spring-type I/O terminals that ensure fast, secure, and errorfree wiring. The integrated control panel, equipped with LED indicators and an optional external control panel, streamlines commissioning with functionalities such as parameter copy and download.
A commitment to sustainability
With energy conservation at its core, the iC2-Micro offers up to a 40% reduction in energy usage, contributing to a greener footprint. Its compatibility with induction, synchronous permanent magnet (SPM), and interior permanent magnet (IPM) motors reflects a commitment to versatility and efficiency.
Adaptability: A myriad of applications
From pumps to material handling, from textile machinery to general applications, the iC2-Micro adapts seamlessly. It boosts productivity,
integrates eff ortlessly into existing systems, and off ers a reliable retrofit solution for VLT Micro Drive FC51 installations.
Technical specifications: Precision meets performance
The iC2-Micro operates flawlessly up to ambient temperatures of 50°C without derating, a testament to its high reliability. It features various modes, including torque open loop control and kinetic backup, ensuring consistent performance and protection. The built-in Smart Logic Controller optimises drive, motor, and system collaboration, enhancing the functionality and longevity of applications.
Empowering the industry: The digital edge
The MyDrive® Suite’s digital tools support the iC2-Micro, enabling precise drive selection and commissioning. It underscores the drive’s modernity, marrying the mechanical with the digital, to ensure a user experience that is both intuitive and advanced.
Pacific Automation: Your partner in innovation
As this new chapter is ushered in with the iC2-Micro, Pacific Automation stands ready to illuminate the path towards streamlined efficiency and heightened performance. Embrace this compact powerhouse and unlock the potential within your industrial automation, material handling, and manufacturing processes.
For a deeper dive into the iC2 Microdrive’s capabilities and to access detailed technical specifications, use the Danfoss iC2 Microdrive QR code. Equip your operations with the drive that delivers big results in a compact package and transforms operational efficiencies.
Unlock the potential within your industrial automation, material handling, and manufacturing processes with the small drive that delivers big results brought to you by Pacific Automation, your innovation partner.
Distributed control systems (DCSs) have been at the heart of many industrial processes for decades, providing safe, reliable control for industries including, water, energy, metals, minerals and chemicals. While highly capable and offering numerous benefits, DCSs cannot remain static — instead, they must evolve to meet the growing needs and ever-changing challenges facing users.
In an increasingly unpredictable world, a DCS must play a role in helping users adapt to a range of challenges, including fluctuating energy prices, disrupted supply chains and higher compliance costs. Digital solutions tightly connected to the DCS can help resolve issues through greater and more effective data analysis, which is vital today.
Sustainability is also a major driver across society and industry, and users will want the DCS to help integrate process control and energy to ensure they can make reliable use of renewable energy sources.
Customisation of products is another major market demand and the future DCS will need to be more adaptable and scalable to allow its use in smaller plants designed to be more responsive to tightening customers’ needs as well as large facilities in critical infrastructure operating around the clock.
A changing workforce also throws up its own challenges, with retirees taking valuable knowledge and skills developed over time and hard experiences out of the company. A new, more digitally aware group of engineers is expecting to make increased use of AI and augmented reality to monitor and assess plant performance and resolve issues remotely.
Users will also want to take advantage of new business models such as ‘automation as a service’ and new technical innovations, all without disrupting the key DCS attributes of quality, security, resiliency and reliability they have become accustomed to.
Although DCS operators want an adaptable and very capable system, they are reluctant to make big investments in the technology, with all the implications this has for total cost of ownership. This means that the DCS must enable ease of connectivity to allow new technologies to be accessible.
Many leading vendors see the future DCS based on a new process automation
architecture. This will separate an evergreen robust core — one that prioritises reliable, deterministic responses — and an extended, digitally enabled environment that performs fewer time-critical tasks, while also allowing faster innovation and continuous performance improvements.
Moving non-core control system functions to a separate but connected digital environment will allow systems to adapt more easily as needs change now and in the future.
The future DCS core and extended system environments will be virtual, modular domains with cybersecure interfaces and offering integration of OT/IT data so that users can decide where they want their data to reside.
MOVING NON-CORE CONTROL SYSTEM FUNCTIONS TO A SEPARATE BUT CONNECTED DIGITAL ENVIRONMENT WILL ALLOW SYSTEMS TO ADAPT MORE EASILY AS NEEDS CHANGE NOW AND IN THE FUTURE.
Process controller and application software will exist as containerised entities with a specific function. Independent of system hardware, these modules will offer highly flexible deployment and will be used with purpose-built and industrial PC controllers, edge devices, on-premise servers and cloud platforms.
A more agile, modular environment will also enable faster adoption of new and innovative offerings.
This type of extended, more open automation environment will allow secure connectivity with other Industrial Internet of Things (IIoT) initiatives, while ensuring greater collaboration among people, systems and equipment.
One such initiative driving this trend towards openness is the Open Process Automation Forum (OPAF). Made up of users from a broad range of industries and disciplines, system integrators as well as leading automation system manufacturers, OPAF has defined a standards-based, open, secure and interoperable architecture for modern process automation.
This architecture gives DCS users easy access to leading-edge best of breed capabilities, allowing components to be integrated into the DCS. Another goal is to preserve asset owners’ application software and avoid the cost of replacing it. While promoting innovation and value creation and meeting the needs of numerous industries, it is also commercially viable and allows collaboration among both DCS users and suppliers.
The aim is to ensure everything can work seamlessly in an open ecosystem, avoiding the risk of being locked into proprietary systems.
These modular, containerised control engines and applications will require orchestration and management. This represents a major challenge for users of the future DCS — although IT departments might be accustomed to such tasks, operation engineers are focused on running their processes, not managing the systems that control them.
Automation of these system management tasks is therefore vital, preserving the integration that today’s users have come to expect. A control orchestrator manages many of these complexities, while still assuring full control.
Another aspect is project execution — to ensure that DCS users get a rapid return on their investment, future systems will further simplify, accelerate and error-proof automation engineering and project execution.
The decoupling of automation hardware and software engineering allows project tasks to be performed in parallel with different teams. These can work in different locations and even in virtualised cloud engineering environments to speed up deployment of new systems — using virtualisation, emulation and simulation technologies, all implemented in the cloud as a digital twin, engineers can perform virtual application testing and commissioning.
Data is at the heart of powering optimisation at a process, plant or enterprise level. Yet an average plant uses less than 20% of the data it generates. Successful companies will transform more of this data into actionable insights to achieve smarter and more sustainable operations. The transformed, more modular, more flexible DCS will be key to this success.
The challenge for plant owners is to collect and combine the data from different sources, contextualise it, transform it into knowledgeable insights and then ensure that the right people can access it to make the right decisions in a timely manner.
Key elements of this new digital experience will be AI-enabled analytics and
edge software to analyse operational data at the point of production. This flexible, edge-oriented solution will help to predict issues and prescribe actions for better asset operations and to tune production processes.
The main role of today’s automation systems is to execute classical control loops of sensing (‘motor runs too fast’), analysing (‘need to reduce speed’) and acting (‘reduce drive frequency’). They enable low-level processes to run without human intervention under normal conditions. When exceptional or unusual situations occur, human operators can step in to make the decisions needed and carry out any complicated task that these decisions might require.
The future DCS will use autonomous operations and industrial AI, adding another level of intelligence with an outer loop that considers potential conditions and outcomes.
This will first be applied to support remote or hard-to-reach locations, such as offshore wind turbines, oil rigs or mining operations, and will be overseen by teams of remote operators. These can be assisted by subject matter experts located anywhere around the world.
These types of AI augmented systems will help human operators make better decisions, allowing them to use their
KEY ELEMENTS OF THIS NEW DIGITAL EXPERIENCE WILL BE AI-ENABLED ANALYTICS AND EDGE SOFTWARE TO ANALYSE OPERATIONAL DATA AT THE POINT OF PRODUCTION.
cognitive abilities to make better decisions in a timelier manner. This will free expert personnel from mundane, repetitive tasks, allowing them to focus on higher-value activities. In the near term, people and autonomous systems will thus partner, with humans making the final decision.
In the longer term, automation systems will become more autonomous as ever more tasks are handed over to the system.
The future DCS will also help those responsible for the day-to-day management of all aspects of the control system infrastructure. Features and abilities such as self-configuring networks and plugand-produce insertion of new equipment modules will remove the complexity of managing today’s integrated plant systems.
Overall, tomorrow’s DCS users can look forward to reduced cost of ownership, more secure and reliable systems, and improved profitability.
Melbourne Water manages the major water, sewerage and drainage networks across Greater Melbourne, and cares for 25,000 km of rivers and creeks that sustain healthy communities and the environment.
Melbourne Water’s largest water reservoir, the Thomson Reservoir, makes up about 60% of the city’s total water storage capacity, and feeds into one of the largest water supply networks in Australia. It is at the core of water supply for the city of Melbourne and the surrounding suburbs.
To ensure the Thomson River environment downstream of the dam is protected, the flows in the river must be controlled and optimised so that the correct amount of water is released at all times.
Thomson Reservoir is filled by rainfall received by the surrounding catchment. It can transfer over 1 billion litres of water per day to Upper Yarra Reservoir, which in turn supplies Silvan Reservoir. From Silvan Reservoir, water can be distributed throughout metropolitan Melbourne.
Finding the optimal amount of water to release is complex. If too much water is released, the source water is wasted. If too little is released, the environmental conditions downstream of the dam are impacted and Melbourne Water fails to meet its minimum compliance requirements.
Melbourne Water must take into consideration the existing river flow and levels, which are impacted by crop irrigation, rainfall runoff, tributary flow and evaporation. It must also consider fluctuating customer demand. Normally there is a time lag of up to 10 hours from when changes are made to release flows at the dam to when those changes are seen at the furthest compliance point.
The complexity of the network, paired with factors like lag time and multiple environmental variables, made this system a perfect candidate for model predictive control.
Digitalisation consultant Kalypso — a Rockwell Automation business — worked with Melbourne Water to help develop ways to control the water leaving the Thomson Reservoir with increased efficiency and precision by implementing FactoryTalk Analytics Pavilion8 model predictive control technology from Rockwell Automation.
While the water industry is relatively mature when it comes to automation and system optimisation, quality, process variability, outages and downtime are still persistent challenges. The complexity of calculations, the duration of focus, and the speed and precision required are poorly suited to human capabilities. MPC applies a data science layer on top of existing regulatory controls to continuously monitor and predictively optimise process behaviour.
FactoryTalk Analytics Pavilion8 Model Predictive Control (MPC) provides an intelligence layer on top of automation systems that can continuously optimise plant operations in real time. Its flexible hybrid modelling capabilities incorporate available process knowledge to deliver accurate, high-fidelity models, and can handle both nonlinear and linear processes simultaneously.
MPC technology continuously assesses current and predicted operational data, compares them to desired results, and adjusts control targets to reduce process variability, operate within equipment constraints and improve performance.
For Melbourne Water, the MPC system analyses a set of variables (flows from tributaries, rainfall, evaporation, irrigation consumption, etc) in real time and continuously, predicting and driving the set-point adjustments to maintain optimal system function, removing the strain of extended observation from conventional operation and eliminating the root cause of variability, outages and downtime.
Using the new system, Melbourne Water was able to save 2 billion litres of water annually, conserve energy and reduce strain on the workforce while improving compliance. Melbourne Water has thus set the bar for autonomous operations and responsible stewardship over a critical natural resource.
Rockwell Automation Australia www.rockwellautomation.com/en-au.html
Are you looking for an Affordable HMI or Cloud Monitoring Solution or Both
Look no further than Weintek
Starting from $699 (7”, 10”, 15” and others) with Mobile Monitoring, Cloud Integration, Weincloud Dashboarding and with OVER 400+ Communications Drivers you are sure to find every solution to all your needs here. Contact
Advantech has introduced its latest Industrial Communication Gateway series, catering to the evolving needs of the green energy market with the ECU-1370 and ECU-1260.
The ECU-1370 has a Cortex-A53 Quad-core 1.3 GHz processor, 4 GB DDR4 and 32 GB eMMC, offering robust features for demanding applications, and with multiple communication interfaces and operation in extreme temperatures. The ECU-1260 features a Cortex-A35 Dual-core 1 GHz processor, 2 GB DDR3L and 16 GB eMMC, suitable for other diverse industrial settings.
Enhanced with EdgeLink software and Advantech’s EdgeHub SaaS, the series supports over 200 OT drivers and facilitates remote monitoring and management, streamlining edge-to-cloud integration. These features enable seamless management of renewable energy systems like solar and wind power.
Advantech’s commitment to sustainability is evident through its focus on the green energy market, contributing to global efforts to reduce carbon emissions and promote renewable energy sources. The Industrial Communication Gateway series is expected to play a role in managing renewable energy systems, offering technological advancement and environmental sustainability.
Advantech Australia Pty Ltd www.advantech.net.au
The Ewon Netbiter EC360W gateway from HMS Networks now comes with a fully revamped graphical user interface for Netbiter Argos Cloud to enhance the user experience. The Netbiter EC360W is an all-in-one gateway that includes a diversity antenna, making it more robust and more likely to achieve better connectivity in harsh environments.
The Netbiter Argos app will allow push notifications that can be sent and acknowledged via the app.
The Ewon Netbiter EC360W connects field equipment to the Argos cloud via Cellular 4G or Ethernet. The cloud platform displays data via both the web and the Argos mobile app.
With the Netbiter EC360W gateway and the Netbiter Argos cloud, users can receive insights into their equipment’s performance and status. The solution allows remote management of a wide range of field equipment and is designed for monitoring the performance and maintenance of critical equipment in remote locations.
The Netbiter Argos solution is suited to rental companies that manage and monitor various assets used for power generation. Offering an out-of-the-box, end-to-end solution, it allows these businesses to track and service diverse fleets of equipment deployed across numerous locations.
HMS Industrial Networks hms-networks.com
Electromagnetic flowmeter, designed to measure bulk material flows up to 300 t/h.
The meter has no mechanical parts in the flow, is 100% dustproof and erosion free because of ceramic inner pipe.
arbitrary mounting position (inclined/free fall) low headroom required easy to calibrate
Westermo has launched a range of compact, unmanaged industrial Ethernet switches. The SandCat 5-port fast Ethernet switch series offers what the company says is a cost-effective, plug-and-play solution for industrial applications. Supporting 100 Mbps, the devices have been designed to meet the increasing network complexity, reliability and bandwidth demands of the utilities, manufacturing and energy industries.
The SandCat switches provide an option for connecting multiple end devices to the network and the availability of a fibre port enables communication over larger distances or different sites. Although managed switches are used widely to enhance configuration and security of data networks, the SandCat series is suited to extending the port count of managed switches, enabling the installation of more end devices. The switches can also be used when a central device is required to create a physical topology for redundancy and remote access or to act as a simple switch within factory automation applications.
The SandCat series is designed for mission-critical applications using DIN rail mounting in harsh industrial environments allowing Ethernet connections to be established between drives, inverters, HMIs, PLCs and I/O units. The switches meet EMC, isolation, vibration and shock standards. An IP30-grade metal housing, operating temperature of -40 to 75°C, wide power input range, multiple small form-factor pluggable (SFP) transceiver options, and extensive industry approvals and certifications allow application flexibility.
Westermo Teleindustri AB www.westermo.com
• BOILER monitorinG
• LIQUID LEVEL indiCation
• INDIRECT leVel GauGeS
• BOILER WATER monitorinG
• GERmAN expertiSe & quality
Digi International has announced the launch of Digi IX40, a 5G edge computing industrial IoT cellular router, purpose-built for Industry 4.0 use cases such as advanced robotics, predictive maintenance, asset monitoring, industrial automation and smart manufacturing.
The Digi IX40 cellular solution supports 5G connectivity and edge intelligence, allowing enterprises to connect multiple machines (wired or wireless) for the integration of cloud-delivered operational technology (OT) services with information technology. Its all-in-one design, computing capabilities and integrated memory also promote real-time data processing, remote monitoring and precision analytics.
The Digi IX40 integrates Digi Remote Manager (Digi RM) cloud-based solution for configuration, automated security monitoring and simplified management. Digi RM supports secure terminal access for out-of-band management of edge devices via serial ports and a command-line interface.
Key Digi IX40 features include global 5G and LTE support for public and private cellular networks, integrated edge computing capabilities for applications requiring edge intelligence and real-time processing, the Digi Accelerated Linux operating system (DAL OS), Ethernet, SFP, serial, I/O and Modbus bridging and failover options, including fibre and 4G LTE for redundancy.
Mouser Electronics au.mouser.com
Belden has launched the BEETLE Lite single-pair Ethernet (SPE) managed switch from Lumberg Automation. The BEETLE switch is designed to help reduce network complexity by deploying thinner, lighter SPE cables that provide connectivity via a single pair of wires rather than the two or four pairs required by standard Ethernet.
As digital transformation accelerates, companies need to connect more devices and transmit more real-time data while simplifying network infrastructure where possible. With Power over Data Line (PoDL), IP40 protection and low power consumption, the BEETLE Lite managed switch provides SPE connectivity for a future-ready network.
The BEETLE Lite managed switch provides Ethernet for up to at least 1 km, meeting the 10BASE-T1L standard for long-distance Ethernet. Supporting Ethernet transmission via a single wire pair that is lighter and more compact than traditional Ethernet cables reduces network complexity, and sensors and actuators can be directly integrated into the network without the need for an additional gateway.
Belden Australia Pty Ltd www.belden.com
The APLEX SiER-G4201M is an industrial 4-port RS-232/422/485 Modbus gateway designed to meet diverse industrial needs, serving as an industrial panel PC, HMI controller, gateway and industrial display monitor, all in one.
A key method to introduce AIoT into factories is creating a digital information environment. By facilitating data exchange between devices and the edge through networks, Modbus gateways and Ethernet switches become crucial in smart manufacturing. The APLEX SiER series, which includes the SiER-G1101M, SiER-G2201M and SiER-G4201M, provides a range of Modbus gateway solutions, while the SiER-S0802N caters to Ethernet switch needs.
The SiER-G4201M offers four COM ports and two LAN ports, functioning as a conversion bridge between the Modbus TCP protocol and Modbus RTU via RS232/422/485 serial and 10/100Base-TX RJ45 Ethernet ports. It also features an alarm function to alert administrators of any device abnormalities, and includes digital I/O for customised applications, allowing for real-time device status detection and logging.
Constructed with a rugged design, the SiER series has passed shock-proof and vibration-proof testing, ensuring durability in extreme conditions with operating temperatures ranging from -40 to 75°C and with a wide-range 12–48 VDC or 24 VAC power input.
APLEX’s visualisation software system supports edge computing and cloud computing configurations, enhancing the SiER series’ flexibility and capability in smart manufacturing.
Backplane Systems Technology Pty Ltd www.backplane.com.au
Reduce downtime, enhance efficiency and increase sustainability with proactive monitoring.
Downtime is the nemesis of every industry, with hugely detrimental effects on production, output, revenues and sustainability. That’s why it’s crucial for managers and planners to prioritise the reduction and prevention of downtime. By minimising the frequency and duration of downtime, companies can unlock a range of benefits, including cost savings, optimised processes, improved performance and reduced waste, such as energy consumption, product spoilage and rejects.
Industrial networks have significantly enhanced industrial automation by enabling seamless communication between devices and machines. This has resulted in notable improvements in production speed, volume and overall operational efficiency. However, the benefits of industrial networks come with increased complexity, raising the likelihood of issues. A single networking problem can have a devastating impact, bringing the entire production line to a halt and causing costly downtime.
Downtime poses a substantial financial burden on industries worldwide, and the impact of downtime is growing significantly, as just one hour of downtime now costs at least 50% more compared to a few years ago. Unless the company has effective troubleshooting practices in place, the duration of the downtime can be long, exacerbating the problem and its associated consequences.
Happily, there are established techniques to tackle downtime and minimise its impact. Below are five preventive maintenance strategies companies can implement to significantly reduce downtime or even eliminate downtime altogether.
1. Permanent monitoring: shining a light on potential issues
The best way to alleviate the pain of downtime is to be forewarned about any issues in the network. Permanent, realtime monitoring tools provide companies with continuous visibility through userfriendly dashboards and customisable alarm thresholds, enabling timely notifications of potential issues. Armed with comprehensive data, engineers can swiftly address problems
before they cause downtime or expedite the resolution process, minimising its duration.
2. Network segmentation: building a robust infrastructure
Many companies want to keep their legacy fieldbus networks and often choose to expand their networks by adding new devices in a daisy chain topology. However, this approach poses a significant risk, as a problem in one device can cause the entire network to fail.
A more robust solution is to divide the network into separate segments, isolating any issues and preventing them from impacting the entire system. By utilising
multiple tap points, network segmentation not only minimises the risk of downtime but also simplifies troubleshooting by allowing engineers to swiftly identify and resolve issues without disrupting the rest of the network.
3. Be prepared with essential spare parts
Hardware faults will happen eventually. In fact, hardware problems are the biggest cause of network communication faults. To mitigate the impact, it is essential to adopt a proactive approach by maintaining an inventory of critical spare parts, including connectors, cables, terminators, hubs, repeaters and devices. Having these spare parts readily available before they are needed will significantly minimise downtime. It is also important not to compromise on quality by opting for cheaper devices, as the short-term savings can quickly vanish when the equipment proves inadequate for the task at hand.
4. Network insights: leveraging AI for efficient troubleshooting
Troubleshooting errors in industrial networks can be challenging, as it often requires extensive experience and knowledge of various industrial protocols that take engineers years to acquire.
A smart alternative is to use AI software trained on industrial data to quickly and accurately analyse the network to identify the root cause of any issues. This advanced technology reduces the reliance on highly experienced field engineers, streamlining the troubleshooting process and resulting in significant time and cost savings.
5. Train staff and close the knowledge gap
To maintain a healthy industrial network, reliable hardware and software are not enough; companies also need skilled professionals. Certificated training courses offer hands-on experience, enabling engineers to effectively design, install, maintain and troubleshoot industrial networks.
By closing knowledge gaps within their staff, companies can improve network performance and increase uptime.
By implementing a proactive maintenance approach with the right diagnostic tools, spare parts and expertise, companies can significantly reduce the duration of downtime or even eliminate it altogether. On average, downtime can be reduced to approximately two hours per month.
Efficiency in troubleshooting and repair
When it comes to troubleshooting, adopting a proactive approach instead of a reactive approach can significantly enhance efficiency and avoid or reduce downtime.
The reactive approach involves waiting for a problem to occur, which means staff only become aware of the issue when production comes to a halt. Once production has stopped, an engineer must be dispatched to the site to access and analyse the situation, determine the optimal repair strategy and implement the necessary fix. Only after these steps can production be resumed.
Additionally, when relying on reactive maintenance, intermittent faults may not be evident when the engineer arrives, posing a challenge in identifying and resolving the issue. Consequently, it might mean waiting for the problem to reoccur before it can be properly addressed, assuming permanent monitoring has been implemented.
On the other hand, employing permanent monitoring tools eliminates uncertainty and blind spots in the network. These tools provide notifications for all types of problems, whether critical or non-critical, enabling the planning of maintenance activities and addressing issues before they escalate into significant disruptions.
Improving performance and sustainability
Reduced downtime not only improves performance by minimising wasted production hours but also enhances sustainability in several ways. It leads to reduced energy consumption, lower product spoilage and fewer rejects.
After experiencing downtime, companies often need days to restore the right conditions for manufacturing, resulting in unnecessary CO2 emissions, costs and lost production. For example, heavy industries relying on large furnaces may require significant time to regain the required temperature. By minimising downtime, companies can mitigate these negative impacts on the environment, resources and overall productivity.
Enhanced worker safety through remote monitoring
Permanent monitoring solutions offer remote access to network data, eliminating the need for workers to enter unpleasant or potentially hazardous environments to check the network. This increased worker safety not only protects employees from potential dangers but also improves overall efficiency by reducing the time and effort required for manual network inspections.
Beckhoff has released seven EtherCAT analog terminals in a compact HD (high-density) housing, with up to eight channels and 16-bit resolution.
The analog terminals include the EL4374, a combined analog I/O terminal (10 V/20 mA or -20/0/4–20 mA) compatible with a conversion rate of 2 ksps per channel. The two inputs and outputs can be individually parameterised for current or voltage operation via TwinCAT (via CoE). With a technical measuring range of ±107% of the nominal range, this terminal also supports commissioning with sensor values in the limit range and evaluation in accordance with NAMUR NE43. The outputs can provide up to 107% of the nominal value, and the high output power allows a load of up to 750 Ω at 20 mA.
The same features are offered by the EL3072 and EL3074 analog input terminals, which now have 16-bit resolution (previously 12-bit) as 10 V/20 mA universal inputs. The EL3072 is equipped with two individually parameterisable inputs, while the EL3074 has four. Another added feature is the EL3078 version, which facilitates the use of eight channels in the same compact HD housing. The higher resolution and expansion to eight channels have also been implemented for the analog output terminals with the EL4072, EL4074 and EL4078.
Beckhoff Automation Pty Ltd www.beckhoff.com
W & B Instruments has recently released the Status Instruments range of head-mounted temperature transmitters with voltage output.
The SEM206PV and SEM206THV support PT100, PT1000 and thermistor temperature sensors and offer a 0–10 V output with a 3-wire connection.
Configuration is user friendly using the Status USB configuration module, which also powers the transmitter during the set-up and the Status Windows-based USB-Speedlink software.
Other features include sensor correction for reducing sensor errors and sensor burnout detection, allowing upscale or downscale output. Digital circuitry provides more accurate and lower-drift performance.
These transmitters are designed for standard temperature probe head mounting or DIN rail mount with an optional clip.
W&B Instruments Pty Ltd www.wandbinstruments.com.au
SEW-EURODRIVE’s CM3C.. servomotor series are compact, dynamic, and powerful servomotors designed to complement the MOVI-C® modular automation system. With increased inertia and high overload capacity, they are tailored for dynamic applications, ensuring optimal performance. But what sets the CM3C.. series apart is its modularity, seamlessly integrating with the SEW range of gear units and servo controllers to provide customisable solutions that meet the specific needs of various industries.
By increasing the diameter of the rotor, the CM3C.. has a higher mass moment of inertia and so offers control benefits in applications that are themselves characterised by high moments of inertia or large moving masses. This series of motors is available in the sizes 63S ranging to 100L and with continuous standstill torques from 2.7 Nm to 40 Nm. Accordingly, the peak torques range from 8 Nm to 120 Nm. Another feature of the innovative CM3C.. motor design is the significant increase in the base speed. This allows maximum acceleration to be maintained over a much larger speed range.
User benefits
By using the latest winding and magnet technology in combination with high-performance materials, the efficiency is improved dramatically with:
• An increase of continuous standstill torque by approximately 30%
• A reduction of weight by approximately 30%
• A reduction of length by approximately 30%.
Beyond their modern design and enhanced performance, CM3C.. servomotors provide a range of configurable features and optimal adaptability. These versatile servomotors offer a wide range of options across all sizes, which can be combined in almost any configuration. With various encoder systems, cooling types, connection variants, output designs, brake versions, and an extensive range of high performance or standard gearmotor products.
Seamless integration and monitoring with MOVILINK DDI ® Optional to the standard resolver or encoder feedback systems, the MOVILINK DDI® interface when integrated to the CM3C.., makes the servo motor a digital node in the network, not only
providing motor speed feedback but also a large number of data points. These data points are available for creating maintenance forecasts, performing automatic motor start-ups and keeping comprehensive operational data. The data includes encoder, motor start-up parameters, temperature and data of other auxiliary sensors, all relayed directly to the inverter and available to the connected supervisory control system.
As the type designations, serial numbers and logistics data associated with motors are identified and supplied automatically, an inventory of all the drives in a plant can be created automatically at the touch of a button. The use of a DDI hybrid cable that is standard for all SEW motor families, facilitates the intelligent digital connection between motor and application inverter.
Local availability and serviceability
In line with SEW-EURODRIVE’s local support philosophy, the CM3C.. servomotor range is assembled and serviced at SEW EURODRIVE’s Melbourne mechatronics assembly centre, which is supported by a team of local sales and engineering specialists.
SEW-EURODRIVE is your complete motion solutions provider At SEW-EURODRIVE, we pride ourselves on being the go-to provider for complete drive solutions. Whether looking to modernise a current system or requiring a brand-new system, SEW-EURODRIVE offers one of the most extensive ranges of drive technology products, solutions, and services available. One point of contact for motion solution products: that sounds good, doesn’t it?
Driving Australian Industry since 1982.
Visit the website: https://www.sew-eurodrive.com.au/home.html.
With the PTCB single-channel circuit breakers from Phoenix Contact, loads with a supply voltage of 48 VDC are now also electronically protected.
The device protection can be combined with the Clipline terminal block range. The circuit breakers can be quickly and easily integrated into the potential distribution and interconnected using standard terminal block accessories. The 6.2 mm overall width matches the terminal block range and saves important space on the DIN rail.
The circuit breaker is available with a fixed nominal value of 2 A or with adjustable nominal current ranging from 1–6 A. This allows the nominal current to be flexibly adapted to the application and reduces storage costs. The LEDs on the front in intuitive traffic light colours and the floating signal contact make the status of the application transparent to users both locally and remotely. This facilitates the clear detection of faults and supports fault localisation and fast recovery. The multi-stage tripping characteristic with dynamic short-circuit detection is optimised for starting different loads.
In addition to the Clipline terminal blocks, the PTCB circuit breakers can also be combined with Phoenix Contact’s 48 VDC QUINT or Trio power supply units.
Phoenix Contact Pty Ltd www.phoenixcontact.com.au
The Neousys Nuvo-10003 expansion box PC supports Intel 14th/13th/12th-Gen Core processors, including i9, i7, i5, i3, Pentium and Celeron CPUs. It is designed to cater to a wide array of applications, from industrial IoT to vision inspection and machine automation, and to fit into the infrastructure of the fifth industrial revolution.
The Nuvo-10003 model is engineered to balance compactness with high performance, providing one x16 PCIe and two x8 PCIe slots for expansion needs. It also offers eight USB 3.2 Gen2 ports with a screw-lock mechanism, dual display outputs through DP++/HDMI 1.4b and two 2.5 ″ SATA HDD/SSD bays with RAID control. Additionally, it offers network connectivity via 2.5G and 1GbE ports, also with a screw-lock mechanism, for stable connections in rugged environments.
The inclusion of NVIDIA GPU card support, capable of handling up to 115 W TDP, provides the Nuvo10003 with the capability to undertake AI and deep-learning tasks in modern industrial applications. Its combination of a compact footprint with the expansion capabilities of up to seven PCIe/PCI slots makes it a suitable choice for replacing bulky rackmount or wall-mount IPC systems, offering both space efficiency and higher performance.
Backplane Systems Technology Pty Ltd www.backplane.com.au
When deciding it was time to replace multiple dieselpowered industrial compressors throughout their salmon farming operations, one of Australia’s leading aquaculture companies chose electrically-powered Kaishan PMV 2-stage rotary screw compressors to increase the efficiency and reliability of their marine-based operations.
Wanting to increase capacity and allow for future growth, feasibility studies indicated that by replacing the old diesel models with the new compressors they would gain greatly in both efficiency and energy cost savings. The advanced design, engineering and technology built into each Kaishan 2-stage PMV compressor also offered far lower maintenance requirements meaning considerably less downtime. The study indicated that capital investment in the advanced compressors would be returned in cost savings over a relatively short operating time.
The new compressors ranging between 132 to 200 kW capacities were specifically designed and adapted to operate in the harsh ocean-based environment, with stabilised mountings in marinegrade cabinets and stainless steel components to operate 24/7 in gale force winds and stormy seas. The compressors operate from on-site barges throughout the huge salmon pen complexes using compressed air to power various operations including blow feeding, water conditioning and stock movement from the barges.
Variable speed and advanced flow technology allows the compressors to operate at the required output for any application demand at any time, meaning there is no excess or wasted energy use and the exact pressure is generated to match real-time needs. Kaishan’s advanced variable speed drive coupled with the company’s IT systems allows for fully programmed, remote or on-site operational control.
Through systemic optimisation of the air end, the permanent magnet motors (utilising rare earth technology), plus integrated variable speed drives, the new PMV, 2-stage compressors run smoother, cleaner, quieter and with much lower energy input for volume air
output than diesel equivalents. Eliminating fossil fuel emissions also greatly assists in achieving the company’s environmental goals.
While compressed air has been used in aquaculture applications for many years, it is due to recent advances in compressor technology and engineering that the true value is being realised. Kaishan’s world-class, energy-saving technology and seaworthy engineering means that compressed air will be an efficient and effective power source for many aquaculture applications for years to come.
Scott Tamlyn, National Sales manager for Kaishan Compressors said: “By matching the right compressor type to client needs in almost any application, we are gaining big inroads into the supply of innovative compressor technologies that offer a viable power source now and well into the future. With our vast Australian experience and global resources, we are confident in both specifying and sourcing compressors and systems that meet and exceed customer demands.”
Selecting the best gripper technology for your industrial automation application.
Festo Pty Ltd
From electronics manufacturing to automotive assembly, grippers have become an important part of material handling processes in many industries. Their recent growth is tied to the rise of robotics, including the need for robots to take on special tasks and handle increasingly complex workpieces. The result is you now have more grippers to choose from than ever.
With all the recent developments in robotics and gripping technology, it can be difficult to know which gripper is best for your application.
To select the right gripper, it’s important to first consider the nature of the task, operating environment and workpiece — including its size, mass and material. Some key considerations and questions to ask include:
• Environmental considerations: What temperature range will the gripper operate in? Will it be exposed to dirt, dust, oil or moisture?
• Application: Does the application involve food or other hygienic workpieces? Will it be exposed to cleaning processes? Does the application require antistatic materials?
• Design constraints: What direction of motion is needed? What is the maximum operating speed and how large is the work space? Will operators be sharing the space with collaborative robots?
Other factors to keep in mind include upfront, operating and maintenance costs, as well as energy consumption. Grippers fall into several categories, and the answers to the above questions will help determine which type is needed to get the job done as safely and efficiently as possible.
When it comes to handling applications, pneumatic or electromechanical grippers are the most common. Pneumatic grippers, which make up 90% of the market, tend to be more lightweight and cost-effective than their electric counterparts. They also feature higher grip forces, can handle faster cycle rates and are more suitable for harsh environments. Electric grippers, on the other hand, offer greater precision, providing end users with force and travel control. At the same time, they tend to be heavier due to the presence of a motor and other internal components, which also drive up their upfront costs.
Whether electric or pneumatic, mechanical grippers fall into several design classes. Parallel grippers, for example, incorporate fingers that pull directly apart. Two-finger designs are the most common, making up 85% of the mechanical gripper market, while three-finger designs are suitable for handling round objects or performing centring functions. Other examples include radial and angular grippers, which feature fingers that open at an angle. Radial grippers open to 180°, making them suitable for applications involving varying or inconsistent workpiece sizes. Angular grippers tend to be faster than 180° designs and open to roughly 30°.
Other important considerations when selecting a mechanical gripper include the gripping force, the guiding strength of the jaws and the design of the gripper itself — all of which depend on the nature of the workpiece. In general, the longer the gripper fingers, the longer the lever arm, which exerts more torque on the jaws. In addition,
flat finger designs provide a frictionbased grip for bulky or robust parts, while encapsulated designs work best for slippery parts requiring more precision.
Soft and adaptive grippers can handle workpieces of various shapes, sizes and orientations, enabling automation in areas where it previously didn’t exist. Because they don’t have any sharp edges, these types can handle food, glass and other delicate objects without damaging or marking the surface. They’re also ideal for small work areas. Compared to mechanical variants, however, soft and mechanical grippers are less precise and operate at slower speeds. They are also more susceptible to dirt, oil and other contaminants.
Another gripper technology is the vacuum gripper, which combines suction cups and vacuum generators. Compact and flexible, these grippers are ideal for limited work spaces and can handle a variety of objects at high speeds. At the same time, however, vacuum grippers can increase maintenance and operating costs; suction cups are susceptible to quick wear, while generators consume high rates of compressed air and can easily clog in the presence of dust and other contaminants.
When it comes to suction cups, it’s important to consider the nature of the workpiece when selecting a material. Buna suction cups, for example, are ideal for oily or plain workpieces, while silicone is suitable for food, as well as hot or cold objects. In addition, polyurethane is a good choice for oily, plain and rough workpieces; viton is suitable for oily, plain and hot workpieces; and anti-static buna is ideal for electronics. Cup shape is also an important factor, especially when it comes to gripping objects that are flat versus round, slim versus large and sturdy versus delicate:
• Standard cups: for flat or slightly undulating surfaces.
• Bellows type: for pliable workpieces, as well as surfaces that are bevelled, domed or round. This type is also suitable for glass bottles, lightbulbs and other delicate objects.
• Oval type: for slim or oblong workpieces.
• Extra deep: for round and domed workpieces.
Vacuum sources fall into two categories: electromechanical vacuum pumps/ blowers, as well as compressed air-driven vacuum generators/ejectors. In general, electromechanical pumps and blowers can achieve high vacuum and suction rates — up to 99.99% and 1200 m3 per hour, respectively. At the same time, however, these machines tend to be heavy and large,
requiring a reservoir with a complex piping system. Because they run continuously, they also consume a lot of current, which generates heat.
Compressed-air driven generators, especially single-stage units, overcome many of these challenges. Compared to electromechanical pumps and blowers, they are more compact, lightweight and easier to install. They include simpler piping systems, require lower upfront costs and incorporate no electrical connections, eliminating harmful heat build-up. Although these units can run up air consumption rates, many machines now come with energy-saving functions, minimising these effects.
In general, vacuum grippers are ideal for: material handling applications, such as steel fabricators, conveyors, electronic assembly, industrial robotics; food and packaging tasks, including canning, bottling, capping, tray making, filling, bagging and sealing, conveying, box making and labelling; and printing applications, such as sheet feeding and handling.
Lastly, magnetic grippers can handle metallic objects like sheets of metal and are ideal for tasks like de-stacking, fixture tooling and bin picking. Although these grippers are limited to applications involving ferrous metals, they require minimal air consumption to actuate, achieving energy savings up to 90% compared to suction cup grippers. Other benefits include:
• Strong gripping: Magnetic grippers can use a shallow magnetic field that enables material de-stacking.
• True ON/OFF: Magnets can be switched completely off and stay clean; any metal fillings left behind from production processes instantly fall away.
• Fast: Some magnetic grippers can actuate in 250 ms, saving valuable cycle time.
• Safe: Magnetic grippers can also provide failsafe performance and will not drop parts in the event of a power or air loss.
No matter the application, there’s an ideal gripper. Ultimately, the right choice depends on a number of variables, including workpiece size and shape, operating conditions, industry, energy requirements and cost. In some cases, unique handling applications may even require a custom gripping device.
Bürkert has announced the expansion of its product range with the launch of the Type 8743 thermal mass flow controller (MFC) featuring a capillary sensor designed for aggressive gases and gas mixtures. The latest MFC is designed for gas flow measurement and control tasks in the food, chemical and petrochemical industries.
Capillary sensor technology is an indirect measuring method that ensures no direct contact with the gas, therefore providing high chemical resistance and suitability for aggressive gases and mixtures.
The Type 8743 offers IP20 ingress protection, handles flow rates of 0–100 ln/min (nitrogen) and is equipped with both analog and digital interfaces.
The capillary sensor technology in the Type 8743 offers several advantages. The stainless steel capillary tube and sensor elements do not contact the gas, making these devices ideal for use with corrosive and reactive gases.
Laminar flow conditions in the sensor channel ensure a nearly linear relationship between the output signal and flow rate, simplifying gas conversion. Calibrated with nitrogen, the devices can use gas conversion factors, enabling flexible use with various gases and mixtures without the need for real gas calibration.
Burkert Fluid Control Systems www.burkert.com.au
Getac has launched the ZX80, an AI-ready, 8 ″ rugged tablet, powered by the Android operating system.
The ZX80 has been purpose-built for challenging work environments, from busy warehouses and logistics hubs to remote field locations and outdoor facilities. Its lightweight form factor (590 g), wide operating temperature range (-29 to 63°C) and bright 1000-nit 16:10 aspect ratio screen makes it suitable for key tasks such as forklift truck operation and unmanned aerial vehicle (UAV) control, where device performance and reliability are critical. MIL-STD-810H certification, IP67 certification and 1.8 m drop resistance further show it can stand up to the rigours of intensive field work.
For users who need full-shift functionality while working away from charging facilities, the ZX80 is also compatible with Getac’s hot-swappable battery technology, enabling users to switch additional batteries quickly and easily while in the field.
Key features include a dual SIM design (one physical SIM and one eSIM), which allows for rapid switching between carrier networks, while Wi-Fi 6E 802.11ax, Bluetooth v5.2 and an optional dedicated global positioning system (GPS) offer rapid data transfer and location positioning capabilities. The ZX80 can also be configured with 4G/5G LTE, NFC and a barcode reader to fit different applications as needed.
The ZX80’s Qualcomm QCS6490 processor delivers high performance at lower power levels, and the tablet is also AI-ready, taking advantage of Qualcomm’s AI engine to offer ondevice machine learning and the ability to run AI use cases while maintaining battery life. Getac Technology Corp www.getac.com
Siemens has announced it has improved its well-established Sinamics S210 servo drive system with an updated hardware architecture and Version 6 software generation that expand the system’s range of applications. The servo drive system is suitable for applications with high dynamics in the power range between 50 W and 7 kW: eg, machines for packaging, pick-andplace applications and digital printing. To make it easier to control individual axes in the future, the latest generation of the Sinamics S210 comes with a second encoder interface and offers the option to connect a direct measuring system to compensate for mechanical looseness and tolerances. This increases precision, which makes more applications possible. With its Basic and Extended Safety Integrated functions, the Sinamics S210 allows for the implementation of the safety concept in the machine and meets the requirements of SIL3 (EN 61508) and PL e (EN ISO 13849-1).
In addition to Profinet IRT, the Sinamics S210 now offers communication via EtherNet/IP. This means that third-party controllers can also be connected to the servo system, which significantly increases the range of applications. With the 3C3 (H2S and SO2) coating, the latest generation of the Sinamics S210 can resist aggressive environmental influences like sulfur gases. The EPOS single positioner is now also available as a technology function for the Sinamics S210. With this function module, high-precision motion control positioning tasks can be implemented quickly and easily in the converter because positioning tasks can be calculated directly in the drive. Siemens Ltd www.siemens.com.au
Ella Averill-Russell, IICA Sydney Branch Manager
The Safeguard Mechanism under the National Greenhouse and Energy Reporting Act 2007 stands as a critical strategic pathway for the engineering industry to confront Australia’s urgent climate challenges. As temperatures soar, engineering enterprises confront mounting pressures to reign in emissions and comply with rigorous environmental benchmarks.
This mechanism provides a methodical approach by establishing emissions baselines for major facilities, founded upon historical data and scientific assessments. These baselines serve as pivotal yardsticks, guiding engineers in implementing effective emissions curtailment strategies to ensure adherence to environmental statutes. By imposing restrictions on greenhouse gas emissions, the mechanism not only holds sizable facilities accountable but also spurs the adoption of pioneering sustainability practices across industry.
For facilities emitting over 100,000 metric tons of CO 2 e annually, the Safeguard Mechanism unveils a comprehensive regulatory framework. Overshooting emissions baselines triggers exploration into diverse avenues for compliance, encompassing the procurement of Australian Carbon Credit Units (ACCUs) or the implementation of vetted reduction tactics. This facilitates engineers with an opening to propel innovation and capital infusion into sustainable technologies, substantially bolstering national climate aspirations.
Moreover, oversight by the Clean Energy Regulator guarantees transparency and accountability within the mechanism, staving off instances of ‘greenwashing’. This regulatory entity meticulously monitors and governs the execution of clean energy endeavours or undertakings, ensuring strict adherence to entrenched standards and protocols. Such oversight stands as an indispensable bulwark in upholding the integrity of clean energy efforts and instilling faith in the environmental assertions presented by enterprises, thereby adding to the benefit of consumers, investors and policymakers alike.
Recent strides in reporting standards serve to further refine precision and accountability, supplying engineers with the tools to monitor progress and pinpoint areas necessitating refinement in environmental performance. Technological strides occupy a central position in buttressing emissions reduction efforts under the Safeguard Mechanism. Remote monitoring systems and data analytics platforms afford engineers instantaneous insights into emissions trajectories, empowering pre-emptive intervention to address spikes and optimise reduction strategies.
Grounded in empirical validation, technical expertise and transparent governance, this mechanism aligns with Australia’s proactive approach to reducing greenhouse gas emissions and promoting environmental integrity in industrial sectors.
In summary, engineers wield a key role in embracing the Safeguard Mechanism to uphold Australia’s pledge to environmental custodianship and sustainability. By harnessing this framework with technological advancements, we stand poised to make substantial strides towards emissions mitigation, and the advancement of climate objectives within the engineering industry as a whole.
July
Connecting Green Hydrogen APAC Conference & Exhibition
9–11 July 2024
Melbourne Convention and Exhibition Centre
www.apac.gh2events.com
CeMAT Australia
23–25 July 2024
Melbourne Convention and Exhibition Centre www.cemat.com.au
Australasian Waste & Recycling Expo 2024
24–25 July 2024
ICC Sydney awre.com.au
Rockwell Automation ROKLive 2024
30 July–1 August 2024
Adelaide Convention Centre, Australia
www.rockwellautomation.com/en-au/company/ events/in-person-events/roklive-2024-adelaide.html
IICA Technology Expo Gladstone 31 July 2024
Gladstone Entertainment Convention Centre iica.org.au/Web/Web/Events/Event_Display. aspx?EventKey=IICAGLDQLD
August
IICA Technology Expo Melbourne 14 August 2024
Marvel Stadium iica.org.au/Web/Web/Events/Event_Display. aspx?EventKey=IICAMELVIC
IICA Technology Expo Sydney 28 August 2024
Rosehill Gardens iica.org.au/Web/Web/Events/Event_Display. aspx?EventKey=IICASYDNSW
September
IICA TÜV Functional Safety Engineer SIS Training — Melbourne 3–6 September 2024
Novotel Melbourne Central, Melbourne iica.org.au/Web/Web/Events/Event_Display. aspx?EventKey=TUV3SEP
Workplace Health & Safety Show 4–5 September 2024
Sydney Showground, Olympic Park www.whsshow.com.au
October
WA Mining Conference & Exhibition 9–10 October 2024
Perth Convention & Exhibition Centre www.waminingexpo.com.au
IICA Technology Expo Devonport 16 October 2024
Paranaple Convention Centre iica.org.au/Web/Web/Events/Event_Display. aspx?EventKey=IICADVPTAS
The most common determining factors in choosing which logic solver best fits a safety application in a SIS (safety instrumented system) are loop and point counts and the complexity of logic required for safety mitigation.
When dealing with high-density point and loop counts, a larger, more complex logic solver such as a safety PLC may be the best choice. Larger systems enable complex control logic and reliable voting schemes across multiple loops and points. However, the purchase, programming and installation costs for such systems can be notably high, not to mention their high life cycle costs.
For scenarios where only one or a few points need to be monitored in a single SIF loop, a much less expensive and complex single-loop logic solver can be a very effective choice. Single-loop logic solvers, or alarm trips, have advanced significantly in recent years. They now feature programmable inputs, safe password protection, and comprehensive internal, input and sensor diagnostics. Standalone models are less expensive and simpler to program but are limited in handling multiple loops, accepting multiple inputs, performing logic or internal voting, or providing digital communication with a process control system or other host system.
For applications that require higher-density loop and point counts with more advanced logic, and loop monitoring of only a few points or loops, multiloop logic solvers are often a better fit for many SIFs. They can handle multiple I/O points, one to three loops and logic equations, and offer significant flexibility for voting architectures at lower cost and complexity compared to larger safety systems and PLCs. Multiloop logic solvers combine the simplicity of single-loop logic solvers with the advanced functionality of larger systems and PLCs.
When choosing a logic solver, consider whether you need custom or licensed software, then consider its ease of programming to meet your SIS requirements. Many safety PLCs and systems offer proprietary software with high costs and annual licences. Alternatively, there are affordable single and multiloop logic solvers with licence-free programming software, including Field Device Technology (FDT) compliant interfaces.
The rigor of programming and long-term maintenance should always be a key consideration when choosing a suitable logic solver. Implementing logic routines in these safety systems will require someone with significant knowledge of the programming language being used, whether it be ladder logic, function block diagram or structured text. This creates the need for programming expertise and adds additional time and expense to day-to-day operations and long-term maintenance of your safety solution. The litmus test may be to examine how long it would take to reprogram your current 1oo3 voting safety function to a 2oo3 voting scheme. If it takes someone who is not familiar with the logic solver software more than 10 minutes, you may want to reconsider your logic solver choice, especially for such a straightforward application.
Single or multiloop logic solvers offer much more straightforward programming options with easyto-understand dropdown menus, checkboxes, radio buttons, prebuilt common control functions and equation generation utilising Excel-like formulas. While they may have limitations on I/O count, you may be surprised to find out how powerful but easy to program these logic solvers have become.
Bob Myles is Director of Engineering for Moore Industries International. He is an exida-certified Functional Safety Practitioner (FSP) with nearly 40 years’ experience in development of safetycritical systems for the commercial aerospace (DO-178C/ DO-254/ ARP4761/ARP4754), military (DO-160) and process monitoring industries (IEC-61508)
Westwick-Farrow Media
A.B.N. 22 152 305 336 www.wfmedia.com.au
Head Office
Unit 5, 6-8 Byfield Street, North Ryde Locked Bag 2226, North Ryde BC NSW 1670 AUSTRALIA ph: +61 2 9168 2500
Editor
Glenn Johnson pt@wfmedia.com.au
Managing Editor
Carolyn Jackson
Acting Publishing Director/MD
Janice Williams
Art Director/Production Manager
Linda Klobusiak
Art/Production
Marija Tutkovska
Circulation
Dianna Alberry circulation@wfmedia.com.au
Copy Control
Mitchie Mullins copy@wfmedia.com.au
Advertising Sales
Sandra Romanin – 0414 558 464 sromanin@wfmedia.com.au
Tim Thompson – 0421 623 958 tthompson@wfmedia.com.au
If you have any queries regarding our privacy policy please email privacy@wfmedia.com.au
Information