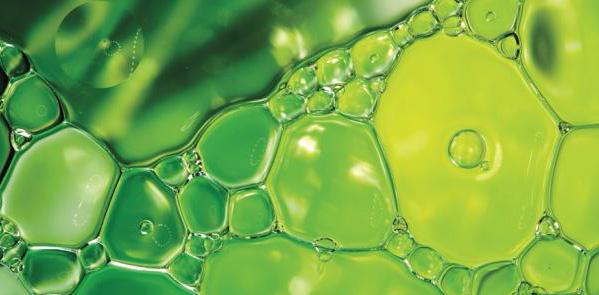
3 minute read
GENSETS
DIESEL GENERATOR SETS NOW APPROVED FOR USE WITH HYDROTREATED VEGETABLE OIL FUEL
Cummins Inc. has announced approval for its entire line of diesel generator sets for use with paraffinic fuels (EN15940), including hydrotreated vegetable oil (HVO), when used in standby applications. This announcement comes as part of Cummins overall commitment to develop innovative solutions that enable decarbonization, and proactively advance the company’s current technology to achieve industry leading emissions. “Our customers are continuously making advances towards decarbonization and Cummins is committed to helping them achieve their sustainability goals. The ability to run generator sets on HVO fuel supports these goals by lowering their carbon footprint.” said Vipul Tandon, Executive Director, Global Power Generation. HVO is derived from the same feedstocks used to produce biodiesel, however, it is produced via a hydrotreated process vs. transesterification process, which helps improve its oxidation stability. It has a very low life cycle carbon emission, making it attractive as a sustainable fuel. Constituent emissions are equivalent to or lower than they are with diesel, and existing emissions data sheets and EPA Tier 2 certifications apply while operating generator sets on HVO. Additionally, it is not prone to bacterial growth making it suitable for applications that require extended fuel storage, including backup power standby applications. HVO is also compatible and can be blended in any proportion with diesel, easing the transition at existing facilities with diesel back-up power generators. Cummins continues to work closely with industry partners to develop solutions that solve the industry’s needs for reliable and sustainable power. As part of the effort to demonstrate performance and reliability, Cummins partnered with Microsoft Corp. at their Des Moines, Iowa and Phoenix, Arizona data centre sites to power QSK95 generator sets on HVO fuel. “Microsoft is a valued partner and we are delighted to collaborate with them and support their sustainability goals for cleaner power,” said Tandon. “Cummins has over 100 years of experience in integrating proven power system solutions with evolving technologies. “This experience has provided us with the flexibility to meet and exceed changing global standards, as well as the unique requirements of our customers,” he concludes. Cummins Inc. announced this month that it is expanding its industry-leading powertrain platforms, leveraging a range of lower carbon fuel types. As the industry’s first unified, fuel-ag nostic engines, these platforms will use engine blocks and core components that share common architectures and will be optimized for different low-carbon fuel types. “Getting to zero is not a light-switch event. Carbon emissions that we put into the atmosphere today will have a lasting impact. This means anything we can do to start reducing the carbon footprint today is a win for the planet. We need to take action now,” said Srikanth Padmanabhan, President, Cummins Engine Business. “Having a variety of lower carbon options is particularly important considering the variation in duty cycles and operating environments across the many markets we serve. There is no single solution or “magic bullet” that will work for all application types or all end users.” These new fuel-agnostic engine platforms will feature a series of engine versions that are derived from a common base engine, which means they have a high degree of parts commonality. Below the head gasket of each engine will largely have similar components and above the head gasket will have different components for different fuel types. Each engine version will operate using a different, single fuel. This new design approach will be applied across the company’s legendary B, L and X-Series engine portfolios, which will be available for diesel, natural gas and hydrogen. “This is a new way of designing and developing lower emission internal combustion powertrains which meet the unique needs of the transportation industry while leveraging the benefits of a common product architecture and footprint where possible,” said Jonathon White, Vice President of Engineering, Engine Business. “This unique technology approach will allow end users to more seamlessly pick the right powertrain for their application with the lowest CO2 impact.” Parts commonality will offer increased benefits for both OEMs and end users, including similar engine footprints, diagnoses and service intervals. Learn more at cummins.com.
Advertisement
