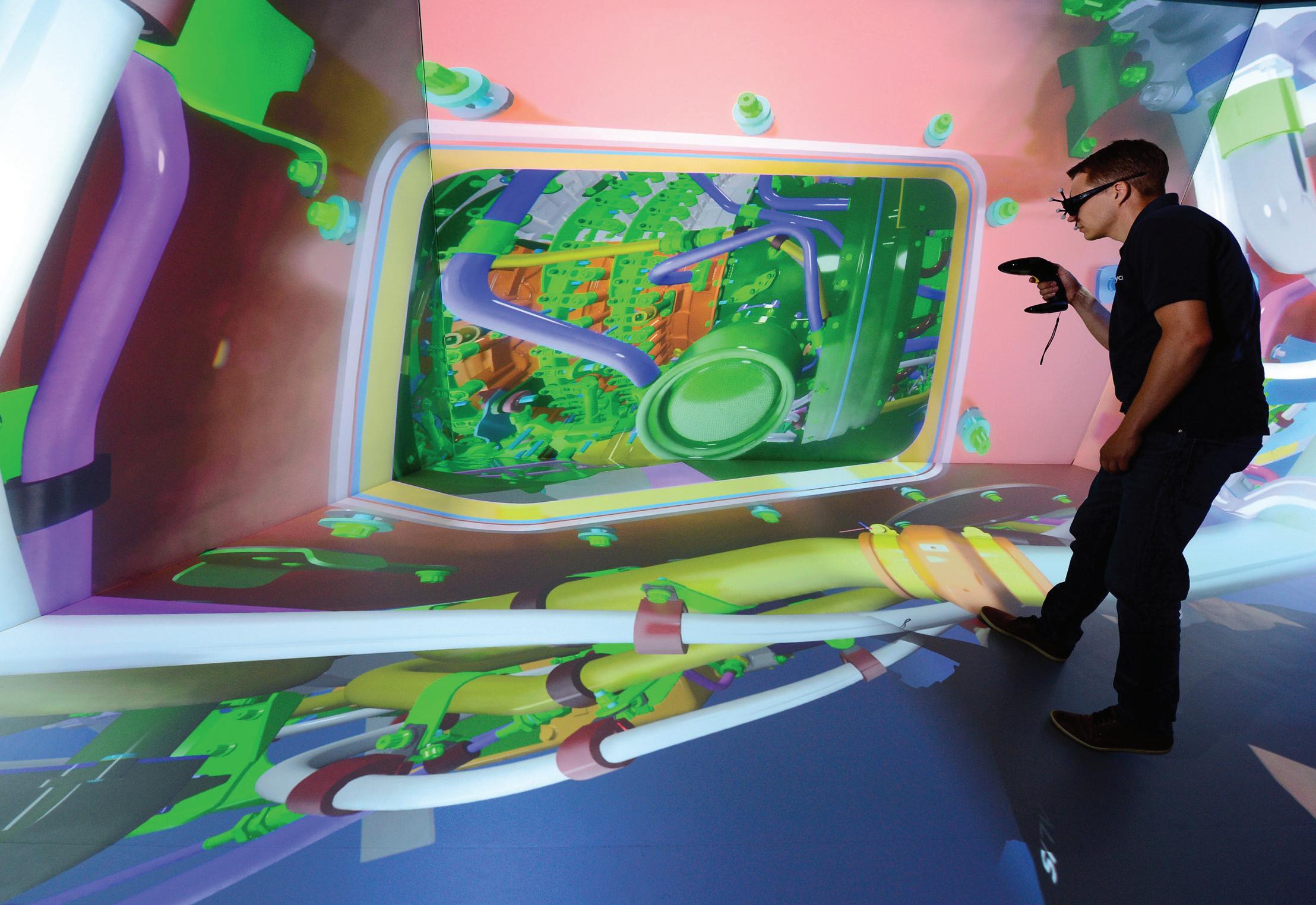
11 minute read
What’s the Future of BizAv Engine Maintenance Training?
As new technologies spread throughout the aviation industry, A&P technicians must familiarize with how they are used to operate and maintain aircraft and their engines. Chris Kjelgaard looks at the future of engine maintenance training…
Advertisement
Almost nobody would claim that the global Covid-19 pandemic has provided a silver lining for humankind, or the world’s economic development. Yet, because the health crisis forcibly limited in-person interactions between people worldwide, its effects have helped hasten a near-revolution in aviation engine maintenance training within the same timeframe.
Before the virus spread globally, engine manufacturers (OEMs) mainly provided maintenance training for their civil aviation customers’ airframe and powerplant (A&P) technicians by means of hands-on residential training courses at the OEMs’ training centers.
In some cases, technicians would travel considerable distances to reach those training centers, spending weeks there learning about the intricacies of the engines on which they would be working, as well as the techniques by which they would maintain and overhaul the engines powering their employers’ aircraft.
Today, however, the situation is different. All the major civil aviation engine manufacturers have embraced remote learning as a fundamental teaching tool as they strive to ensure that, while travel restrictions and gatherings of large groups of people continue to be restricted in many parts of the world, their customers’ technicians continue to receive the maintenance training they need.
“GE Aviation has offered more remote learning opportunities since the pandemic,” says Shannon Korson, Senior Customer Service Manager. In pre-Covid times, “normally, aircraft and jet engine mechanics would travel to one of GE’s or CFM International’s training centers for hands-on learning.
“Due to global travel and social distancing restrictions during the Covid-19 outbreak, more training is being delivered to where customers are – on their laptops and mobile phones.”
Korson notes that initially GE Aviation is focusing its development of new maintenance practices, such as remote learning, primarily towards the customers for its large commercial aviation engines, such as the GE90 and GEnx lines, rather than to customers for its Bizav engines.
One reason for this is that Business Aviation has not been affected by the pandemic to anywhere near the extent that commercial aviation has – in fact, the Covid19 crisis has stimulated some parts of the Bizav and General Aviation sectors, such as the market for used business aircraft. In contrast, many of the world’s airliner operators have had to park vast numbers of large commercial aircraft because of the near-complete ban
PHOTO COURTESY OF ROLLS-ROYCE
on long-distance airline passenger travel.
“Now, more than ever, we’re anticipating our video demonstrations and online learning options can readily help aircraft mechanics of all skill levels manage large, unexpectedly grounded fleets with proper maintenance procedures to protect their engines,” says Korson.
But what is good for the goose is at some point likely to be good for the gander too – and he says GE expects to expand its use of state-of-the-art training techniques and technologies to the customers of its Business Aviation and General Aviation engines too.
Virtual- and Augmented-Reality Training
That also goes for virtual-reality and augmented-reality training technologies, the use of which GE Aviation and the other major BizAv engine manufacturers have been exploring. Increasingly, they are seeing VR/AR as important tools for future engine maintenance training requirements.
“Virtual-reality training integration is part of a longterm plan for GE’s Business Aviation engine maintenance,” Korson confirms. “VR has great benefits but there are cost and development challenges under consideration as we continue to build the business case.
“Over the last five years, GE Aviation has tested a combination of various Augmented Reality tools, most notably Skylight from Upskill, Glass Enterprise Edition smart glasses, and a Wi-Fi-enabled Atlas Copco Saltus MWR-85TA torque wrench.”
Skylight provides a series of customized apps which clients can use to display pertinent information – such as maintenance instructions, required tasks and relevant documents – on the screens of smart glasses, smartphones, tablets, and augmented reality devices in use by A&P technicians as maintenance aids.
Glass Enterprise Edition smart glasses – now offered in the Enterprise Edition 2 generation – were specifically developed by Google for use by businesses, as part of its Google Glass range.
Atlas Copco’s internet-connected Saltus MWR-85TA torque wrench, meanwhile, is part of the Mechatronic MWR tool system. Controlled by Atlas Copco Focus 60 and Focus 61 electronic controllers, the MWR-85TA combines the handling of a click wrench with the controlled-tightening possibilities offered by electronic wrenches.
An optional barcode scanner on the wrench allows the mechanic to add further information on the current task after beginning the work. The Mechatronic system provides feedback through LEDs on the wrench or a separate optional stacklight.
The Focus 60 controller can manage two operators
and assign up to 10 MWR wrenches at a single station, as well as providing data collection of all necessary tightening information, while the Focus 61 offers additional functionalities for assembly processes. Users can manage the process via Atlas Copco’s Open Protocol and the results are transferable to the company’s ToolsNet 8 data collection and processimprovement software system.
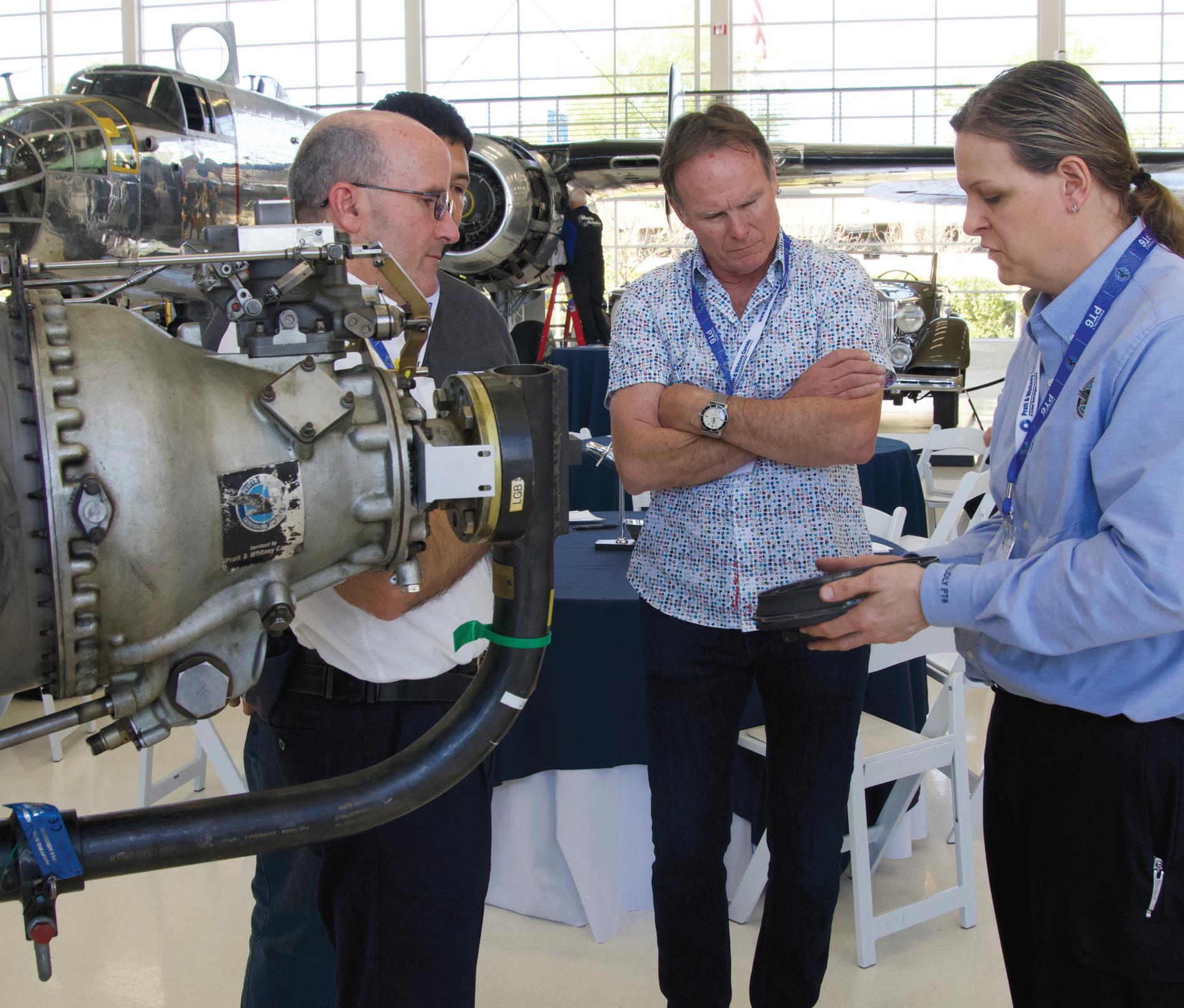
Value & Student Benefit of VR
Rolls-Royce takes virtual-reality maintenance training for its Business Aviation engines very seriously. “We see real value and student benefit in utilizing virtual reality,” says James Prater, Rolls-Royce’s Vice President Customer Support, Business Aviation. “We see the use of virtual reality filling the gap between familiarizations and line- and base-maintenance courses.
“While there can be no substitute for hands-on learning on a real engine, VR is an effective tool for introducing systems description, operation, and servicing,” Prater adds. “It conveys the learning concepts very effectively, while reducing production time loss and travel costs and risks.
“Today, we offer BR725 scheduled servicing and advanced troubleshooting, using VR as the delivery vehicle. Going forward, we plan to use virtual reality on all Business Aviation engines.”
VR has become a key tool for Rolls-Royce for training engine maintenance technicians in interpreting and using the massive amounts of engine condition data provided by the many sensors inside modern BizAv turbine engines.
“We use virtual reality to create synthetic environments such as aircraft flight decks, and we are now able to ‘bring’ the flight deck to the student in the classroom, where we can simulate faults and train students in the use of the central maintenance computer,” Prater explains.
“This ability creates a safe and extremely efficient environment for students to make correlations between the engine, the computer, and the flight deck indications. This level of comprehension is vital, particularly with the modern level of integration and communication between the aircraft, the engine, and the maintenance computer system.”
For instance, the Engine Vibration Health Monitoring Unit (EVHMU) in each Rolls-Royce Pearl business jet turbofan engine monitors 9,000 different operational parameters in the engine and its LRUs – though not all simultaneously. The various software filters used by the artificial intelligence (AI) algorithms at the core of the EVHMU can select many different sub-sets of parameters
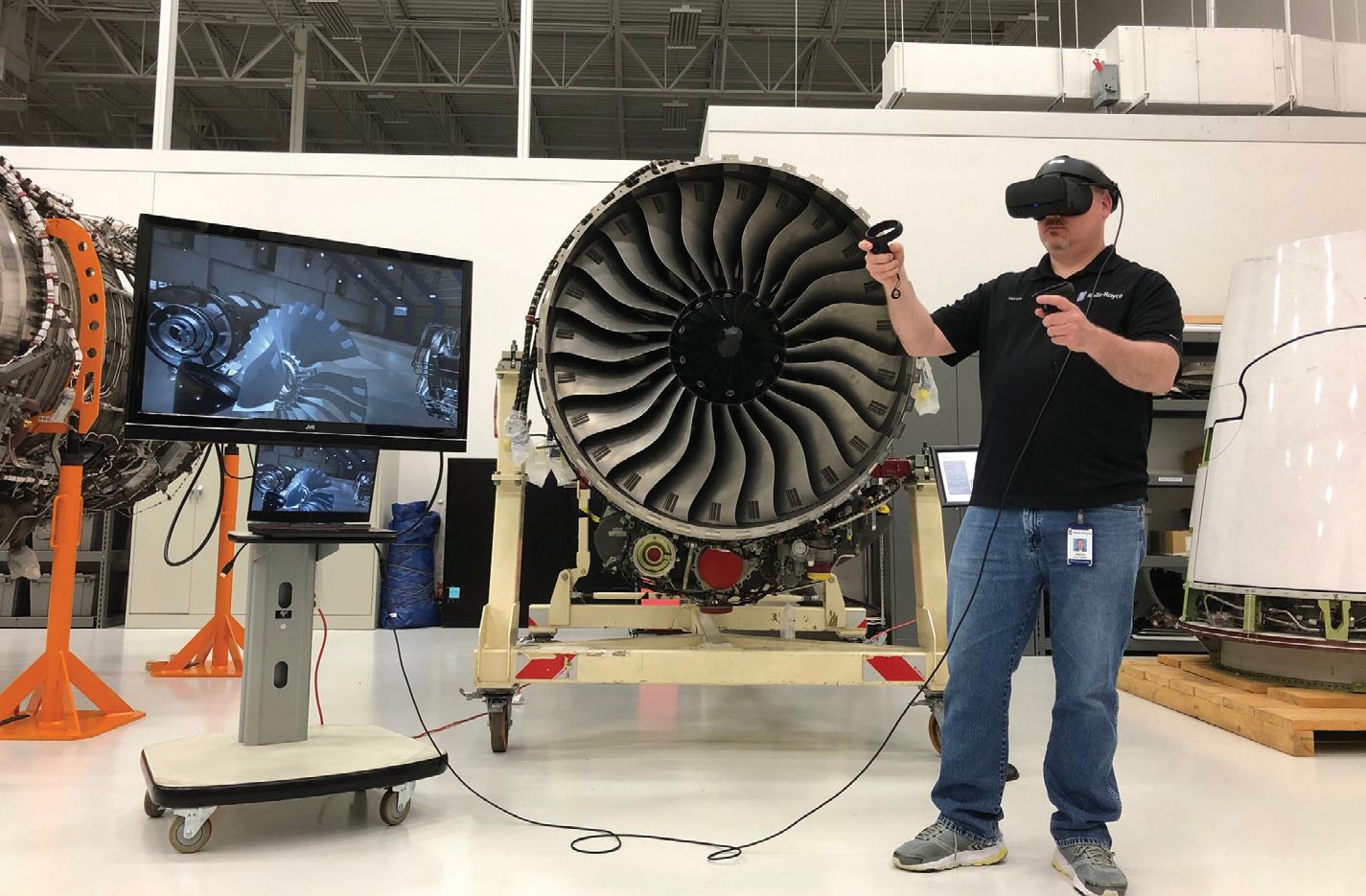
PHOTO COURTESY OF ROLLS-ROYCE
to monitor, one sub-set at a time.
The AI then looks for data patterns within each parameter subset being monitored, and it can match those patterns with specific engine health conditions or issues. This is quickly relayed to the operator’s maintenance department to allow recommended maintenance actions to be performed proactively – in many cases before the issue which the EVHMU has identified has become physically evident within the engine or affected its performance.
Developing a Virtual Engine
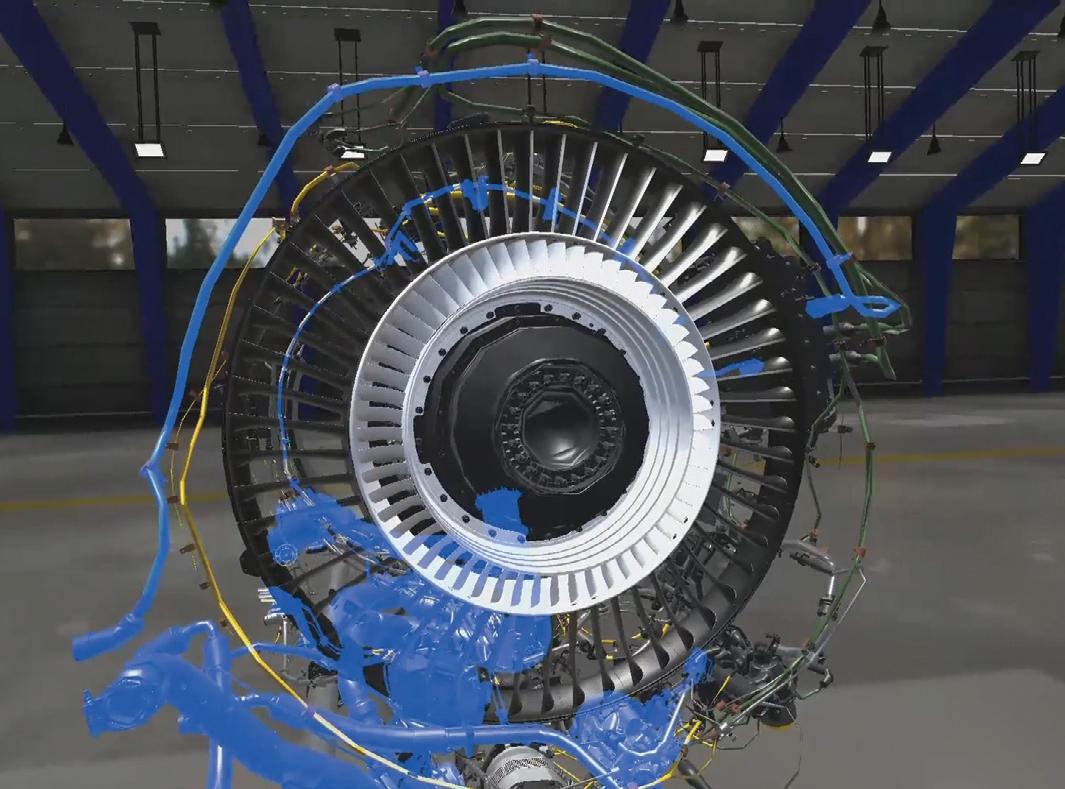
Pratt & Whitney Canada is also becoming heavily invested in using VR technologies and techniques to train A&P mechanics in maintaining its Business Aviation engines.
In combination with engine maintenance training partner FlightSafety International (FSI), which, at its Wichita Maintenance Learning Center, provides a wide range of maintenance courses for P&WC’s entire PT6A range of turboprop and turboshaft engines, and most P&WC BizAv turbofan engine models, P&WC has developed a further wrinkle on virtual-reality maintenance training.
“Working in conjunction, Pratt & Whitney Canada and FSI have developed a virtual engine that allows the technician to explore it down to the component level,” says Scott McElvaine, P&WC’s Vice President of Customer Programs. “This virtual engine also allows for maintenance tasks to be simulated in a step-by-step process.”
As one might expect, FSI has developed enginemaintenance simulations to make use of P&WC’s virtual engine. “FlightSafety…has pivoted into utilizing gamingengine technology to provide real-time, interactive animation of the engine,” McElvaine explains. “Its Virtual Engine Trainers allow instructors and students to view the engine in a new way to improve comprehension of component interaction.
“The virtual engines can be virtually disassembled to perform various Line Replaceable Unit change simulations, and they can also be X-rayed to view any cross-section of choice.
“Versions of the Virtual Engine Trainers are purposely built to simulate an engine inspection used during FSI’s popular borescope courses,” he continues.
“These specific virtual engines have been synthetically damaged to represent various degrees of damage found in a turbine engine. The students will practice assessing these damages as they virtually explore the engine and will be assessed on their proper evaluation of engine health and dispatchability.”
Other New Maintenance Tech
Again emphasizing that it is initially focusing its development and application of new engine maintenance training technologies and techniques on its larger, commercial aviation engine models (but expects to flow them to its BizAv engines in due course), GE Aviation has adopted a range of different methods to enhance its training capabilities.
As is the case with Pratt & Whitney Canada, some of GE’s latest maintenance training methods use simulation techniques.
ROLLS-ROYCE BR725 VR TRAINING
PHOTO COURTESY OF ROLLS-ROYCE
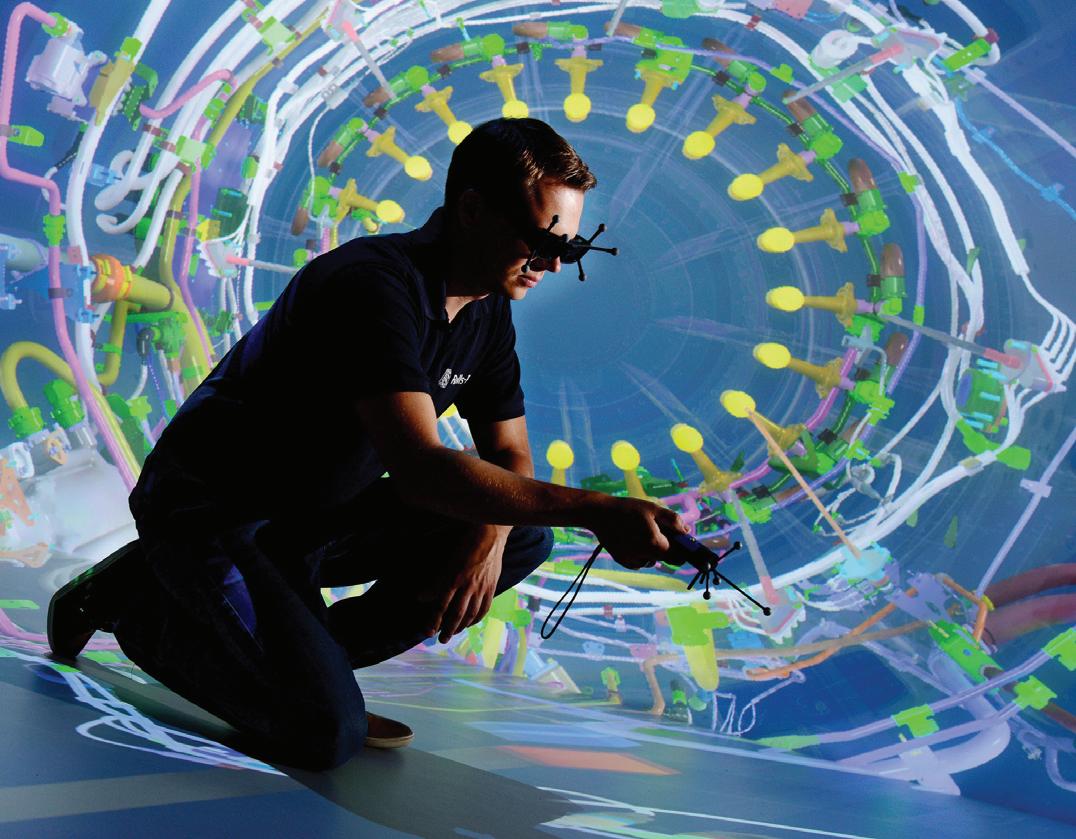
“Our engine maintenance training includes a variety of approaches to ensure learning success, including enhanced classroom, hands-on and 2D/3D interactive digital training modules,” says Korson. “These 2D simulations, [which are now] moving toward 3D content modules, provide an experience that you cannot get with static informational slides and printed handouts.”
Meanwhile, “GE Aviation’s Customer Technical Education Center (CTEC), with locations and partnerships around the world, is providing more virtual options to help meet airline [and BizAv] maintenance needs during this unprecedented time”, he says.
GE Aviation’s CTEC provides training to customers with licensing agreements to perform services on GE, CFM and GE/Honda engines. In addition to commercial and military engines, training is also available for GE Aviation Systems customers for maintenance of electrical components.”
The training partnership between Pratt & Whitney Canada and FlightSafety International is also looking at new ways of providing engine maintenance training in the future, and may adopt them if the training methods under study prove to be effective. Together, the two companies “are always working on emerging technology, and innovation has been a large part of the collaboration to bring our training to the next level,” says McElvaine.
“We are always working with our training collaborators to improve and implement cutting-edge technology to aviation maintenance professionals.”
Similarly, for its future engine maintenance training needs Rolls-Royce is looking beyond its existing wide embrace of virtual-reality and simulation technologies. The company’s Innovation Group “is constantly looking at new technologies” which could be useful for its training needs, says Kevin Fletcher, Rolls-Royce’s Sector Head of Customer & Product Training, Defense & Civil for the US.
“We balance the potential student benefits against the investment required,” says Fletcher. “Our engine shops are experimenting with utilizing robots for inspection and repair techniques of engine components. Here again, benefits of factors such as consistency, precision, fatigue prevention, etc. are weighed against the cost and complexity of the technology.
“Once robots are incorporated into the maintenance process, obviously there will need to be appropriate training developed for technicians.”
Apart from its experiments in using robots for engine maintenance tasks, and the need to offer A&P mechanics training in operating repair robots should their use become routine, Rolls-Royce is also experimenting with the use of technologies such as augmented reality and remote visual inspection – probably using drones – in engine maintenance.
Should these technologies prove fruitful – remember that GE Aviation and Pratt & Whitney Canada are also studying most, if not all, of the same technologies that Rolls-Royce is studying, as potential new training aids – then the maintenance technician of tomorrow will be someone who is far more than an A&P mechanic.
She, or he, will have to be as comfortable in operating a robot and/or a drone, in working with smart tools, in using databases of parts and maintenance records, and in interpreting engine health monitoring data, as they are in tightening a bolt and flush-driving a rivet. ❙
More information from: GE Aviation: www.geaviation.com Pratt & Whitney Canada: www.pwc.ca Rolls-Royce: www.rolls-royce.com/ products-and-services/ civil-aerospace.asp
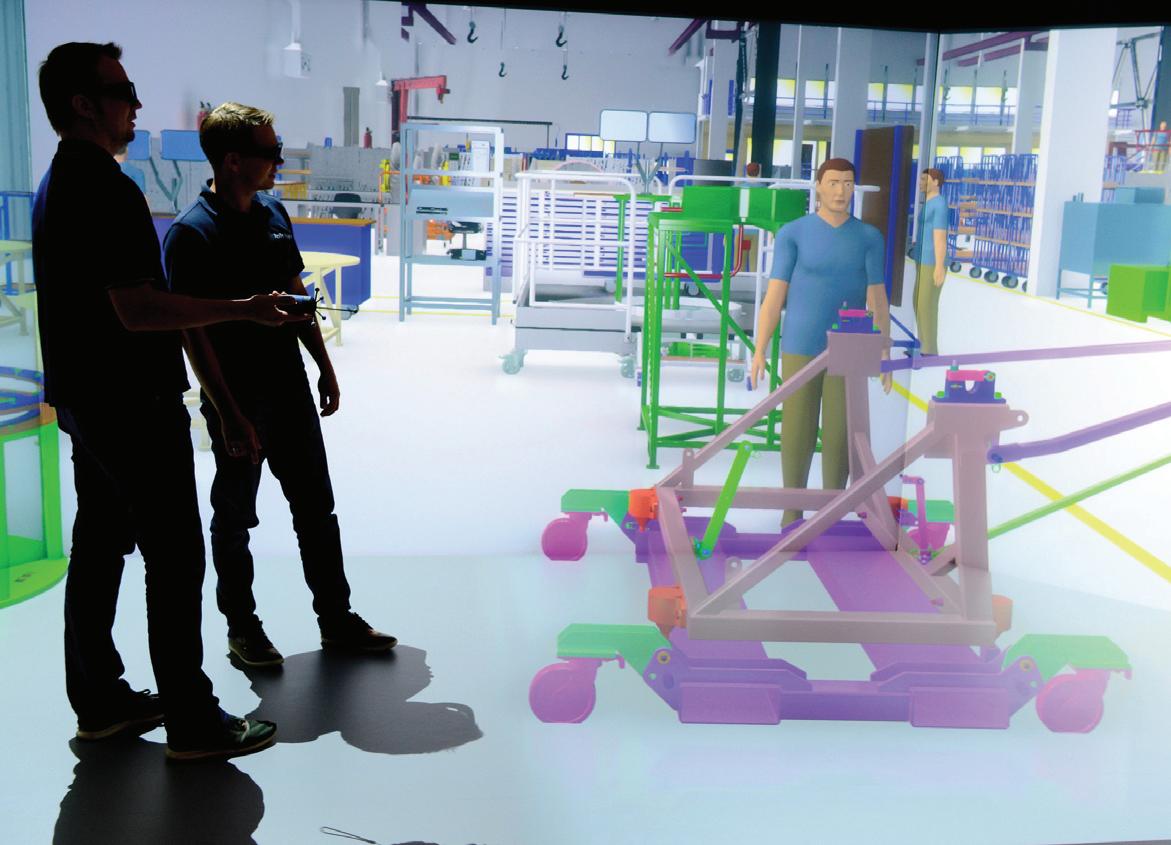
CHRIS KJELGAARD