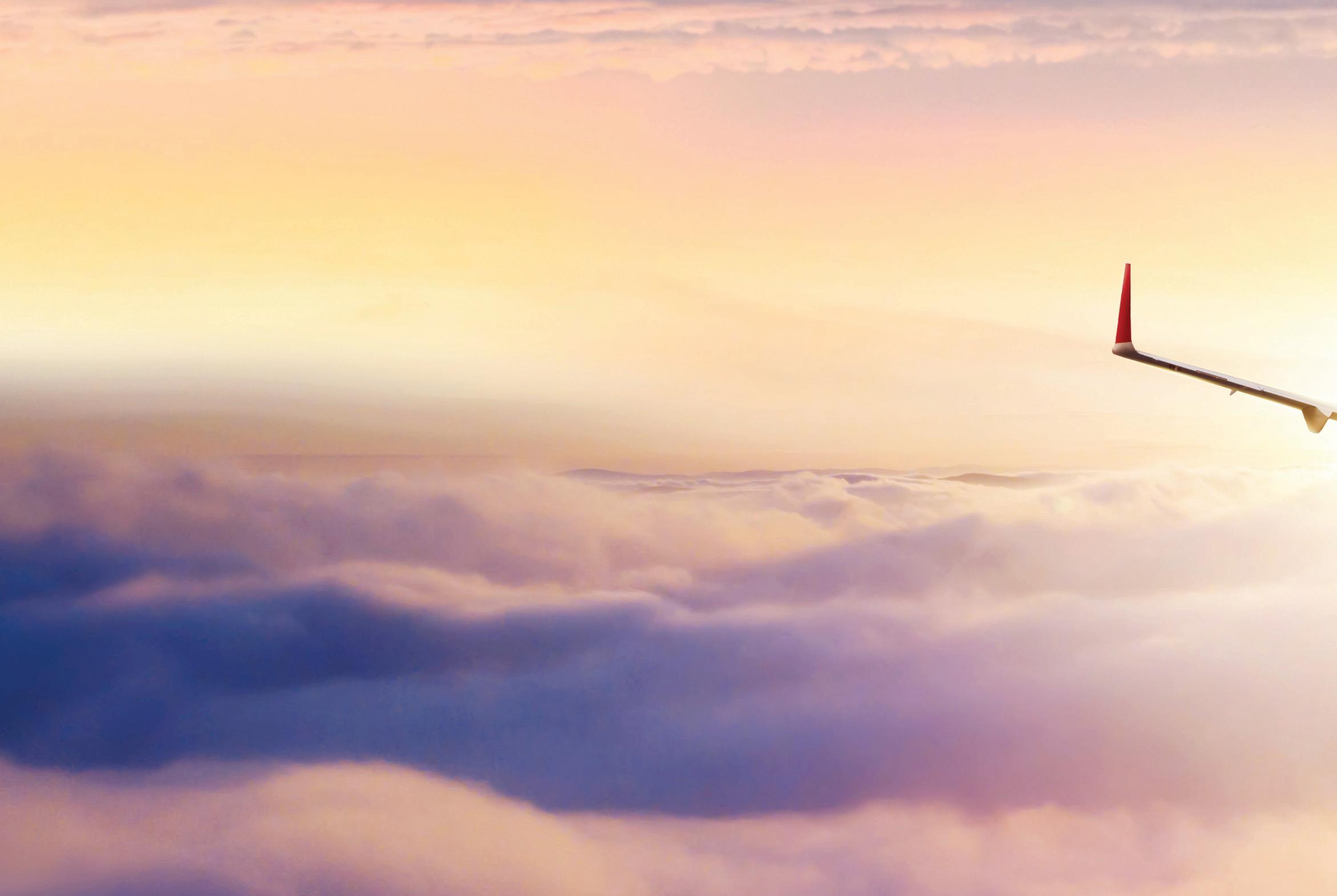
6 minute read
Airworthiness: Be Diligent as Flying Demand Grows
If you’re experiencing increased activity in your flight department, it’s time to sharpen your alertness, particularly where airworthiness is concerned. Andre Fodor shares anecdotes to illustrate why…
Regardless of how much professional experience you might have, a career in aviation always challenges flight department personnel with new learning opportunities. Aviation has a habit of providing rude awakenings for the complacent, the less proficient, or those who fail to follow Standard Operating Procedures (SOPs).
Advertisement
Not long ago, I learned a valuable lesson when called upon to crew an airplane after one of the operation’s regular pilots was ill. Although I already knew the captain, this was the first time that we had worked together on board an airplane.
After a short briefing, I conducted a pre-flight inspection, connected the batteries, and verified that all covers and pins were removed. I proceeded to start the APU and prepare the airplane for its flight. The captain greeted passengers and settled the FBO bill.
After our return to the home airport, I powered down the airplane again and cleared up the interior. Upon exiting the airplane, I noticed that all landing gear pins had been installed, and so assumed that the other pilot had conducted the post-flight check.
Heading to the nose section of the airplane, I disconnected the main battery and installed the pitot and AOA covers, before walking over to the FBO.
Two days later, I received a call from the chief pilot asking whether I’d noticed a broken piece of flap trim that was found missing on a subsequent pre-flight check. This had caused the airplane to miss its next trip.
While I could truthfully have replied that I was not the one who conducted the post-flight check, I was truly embarrassed because I couldn’t even confirm whether the other pilot had conducted a post-flight check – and that put me at fault!
Going by the evidence of the pins, I had assumed a post-flight check had been completed, but I didn’t ask any questions (the answers to which would surely have triggered a post-flight walk-around).
Swallowing my pride, I shared this valuable lesson with everyone at my flight department’s weekly team meeting, and now I’m sharing it with you. I do so in the hope that none of us will ever repeat my mistake. If we fail to stay alert to situations within our flight operations, we may end up operating a non-airworthy aircraft.
To help us all remain alert in this regard, let’s illustrate with some simple ‘gotchas’.
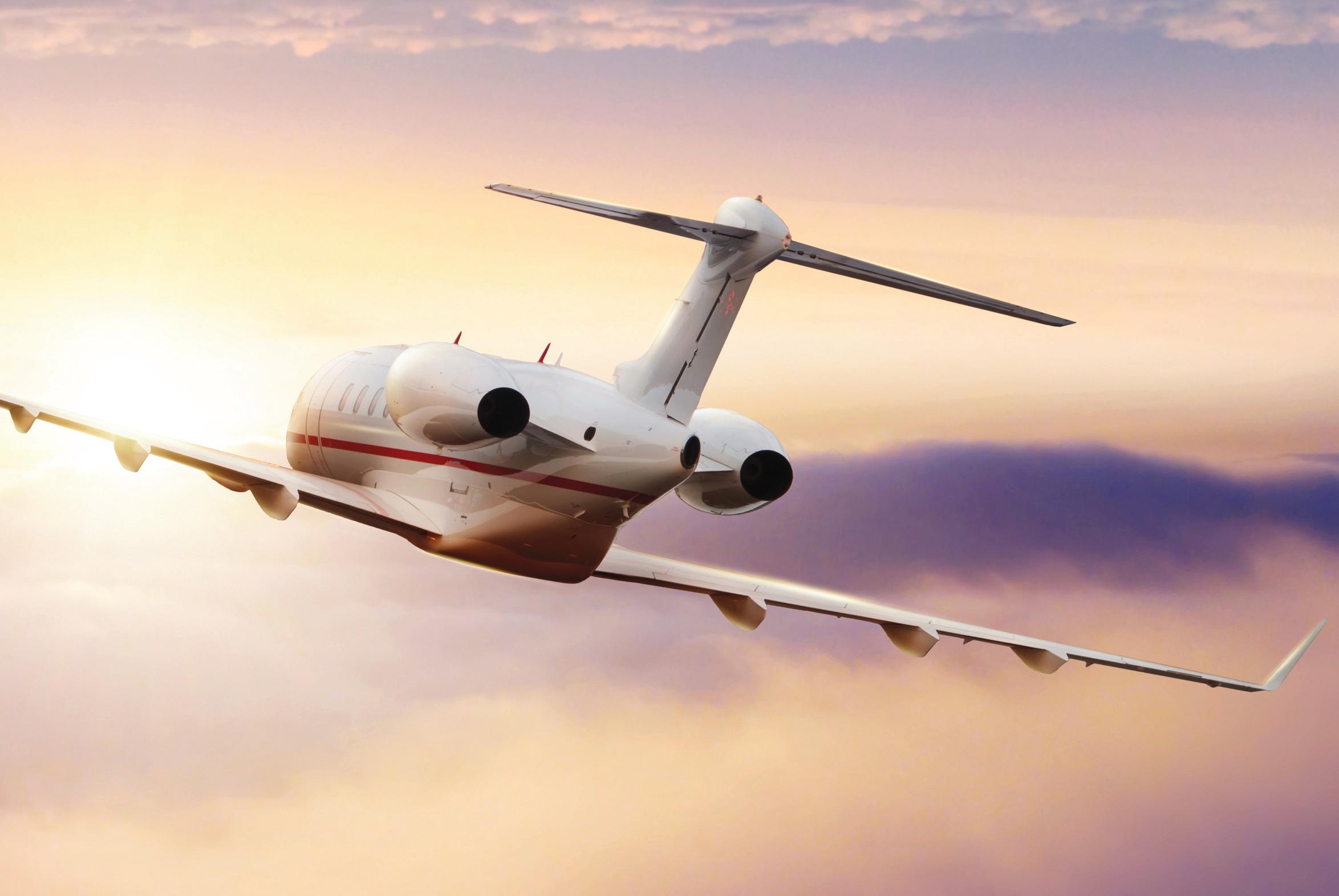
Understand the Op-Specs
The majority of our flying occurs under IFR regulations and at higher flight levels. As such, our self-made checklists should alert us that the aircraft may require a VOR monthly check (if this task is not integrated into a monthly or periodic compliance check) – particularly under Part 91 operations. Moreover, RVSM monitoring and its documentation are requirements for full highaltitude operational airworthiness.
Working for a major OEM, I was once assigned to ferry an aircraft operated by a charter company back to the factory for rework. Checking the documentation revealed that the RVSM certificate was issued under a fleet license and was directly tied to the charter certificate.
Since I was not an employee of that company, and wasn’t trained under the company’s OpsSpecs, I was not entitled to utilize its Letter of Authorization for that operation. Thus, we ended up ferrying the airplane at FL290 and below for the entire journey.
Know Your Maintenance Cycles
Maintenance cycles represent a pesky opportunity for accidentally operating an un-airworthy aircraft. The cycles of maintenance and inspections can be confusing since aircraft have calendar and hourly inspections.
Aircraft managers and directors of maintenance do their best to align the calendar inspection to the hourly due times, minimizing downtime and accumulating as many tasks during one maintenance event, but it can be challenging to predict the accumulation of hours with an everchanging schedule.
To help manage this challenge, maintenance manuals may allow for some flexibility with the allowance of extra days or flight hours which help facilitate matching these events.
But, having a tight handle on your upcoming maintenance events is yet another essential tool in your management toolbox. Failure to do so may cause your airplane to become un-airworthy midtrip. If discovered during a ramp inspection, this could cause far greater issues than the annoyance of a cancelled leg.
Within our operation, the Director of Maintenance dispatches the aircraft only after reviewing all upcoming due items. Moreover, our electronic record-keeping system does a fine job in generating a due list that includes a written airworthiness report which we can carry on all international trips.
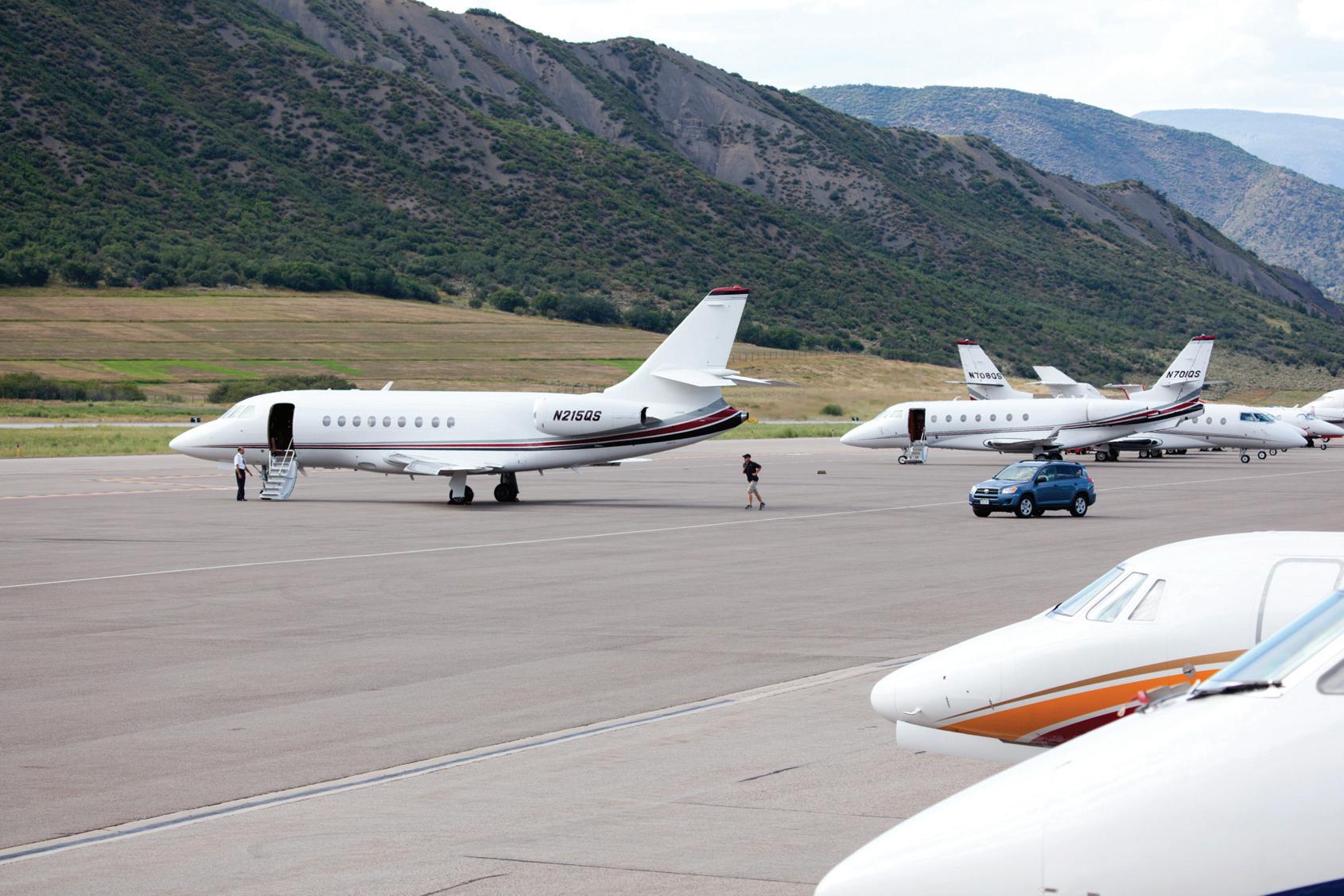
Caveat: As previously discussed in a past article, e-records only produce results as accurate as the data entered into the database. Bad data input will equal bad data output!
Master your MEL Management
As we become busier once again in our flight operations, we’ll invariably find our aircraft being operated under the relief of an approved Minimum Equipment List (MEL) or a NonEssential Equipment Deviation List (which often covers items such as cabin trim, cabinetry and other non-essential items).
However, it is not uncommon for crews to lack mastery of MEL management, causing an aircraft to technically be flown when it is non-airworthy.
Consider that the MEL has several components: • First, the ATA chapter guides you to the item to be deferred. • Second, who can defer – crew or maintenance?
What actions lead to deferment? • Third, how long can the item be deferred? • Fourth, what is the process to manage the deferral, and which indicators – such as tags and inoperative stickers – must be clearly installed? To Summarize…
To illustrate airworthiness challenges, a friend recently called with an interesting issue: The airplane he flies operates under Part 91 for its owner, and Part 135 rules for hire. As he calculated the hours required to fulfil all upcoming flying obligations, he realized that there were more hours booked than there were available hours prior to an upcoming inspection.
There were two options: Either dispatch a mechanic to perform an inspection during a twoday downtime, or drop the Part 135 (revenue-generating) trips. The mechanic packed his bags and tools, and hit the road!
We are all experiencing a fast uptick in our trip requirements, currently. Charter operators are running at full capacity and can barely satisfy the demand. The chances of operational mishaps increase during peak demand times, and we should all be alert, raising our awareness, and sharpening the pencils for planning and forecasting.
Reinforce good habits within your flight department with regard to airworthiness. Be a great coach, increasing your team’s performance, proficiency, and good practices. The payback is well worthwhile. ❚
ANDRE FODOR
With a focused approach on global excellence and creativity, Andre Fodor has managed flight operations for the U.N. and Flight Options as well as being a senior demonstration pilot and instructor for Embraer Aircraft. He is the Aviation Director for his current employer. https://www.linkedin.com/in/andrefodor/
MAKE MORE INFORMED FLIGHT DEPARTMENT MANAGEMENT DECISIONS with AvBUYER.com