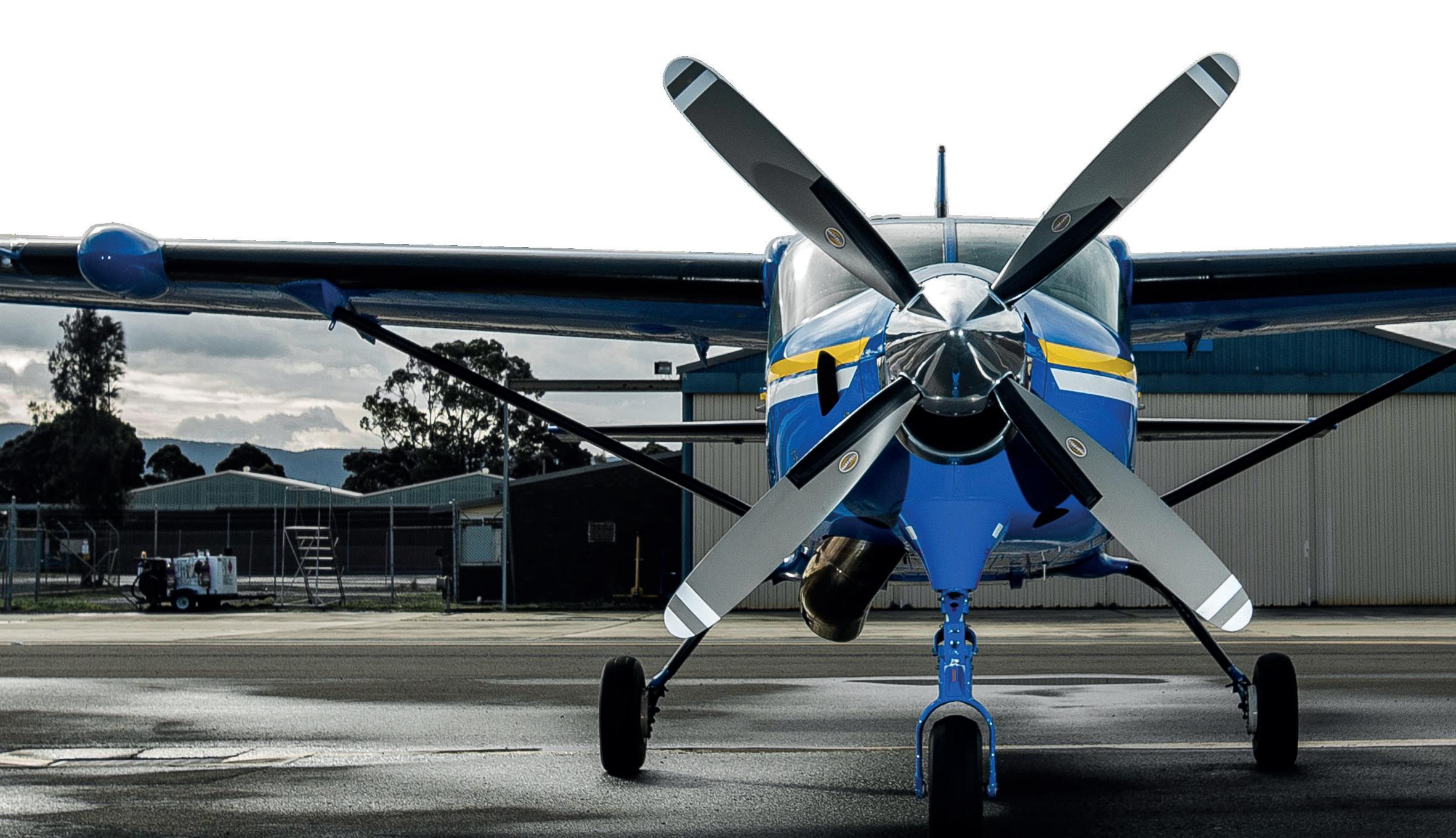
8 minute read
TURBINE 37
Engage the power of TAE Aerospace
For over 30 years TAE Aerospace has been supporting worldwide operators of the TPE331 engine with world-class maintenance, repair and overhaul services.
Advertisement
Commercial and military operators have come to rely on TAE Aerospace to maximise the performance of their TPE331 engines and minimise the impact on aircraft availability during routine and unplanned maintenance events. With Honeywell Authorized Service Centres across the globe, we are one of the world’s largest TPE331 engine service providers covering engines, LRU components, fuel controls and engine component repairs. With multiple Airworthiness Approvals from around the world, OEM correlated dynamometer test cells and prop stands for pre- and post-maintenance testing, vibration analysis and performance runs, we make sure you get the best from your TPE331. We deliver customer value by offering a high-quality service at a price that will reduce your maintenance cost. Contact Tomas on +420 725 908 515 or email tomas.benes@taeaerospace.com to find out more about why customers rely on us.
Benefits of using an Authorized Honeywell Service Centre
• Access to 100% guaranteed OEM certified parts • Reduced downtime due to part availability and guaranteed stock levels • Access to OEM support and warranties • TAE Aerospace technicians have access to the latest Honeywell technical documentation and training • Unparalleled global experience • Cost efficiencies through access to approved dealer discounts
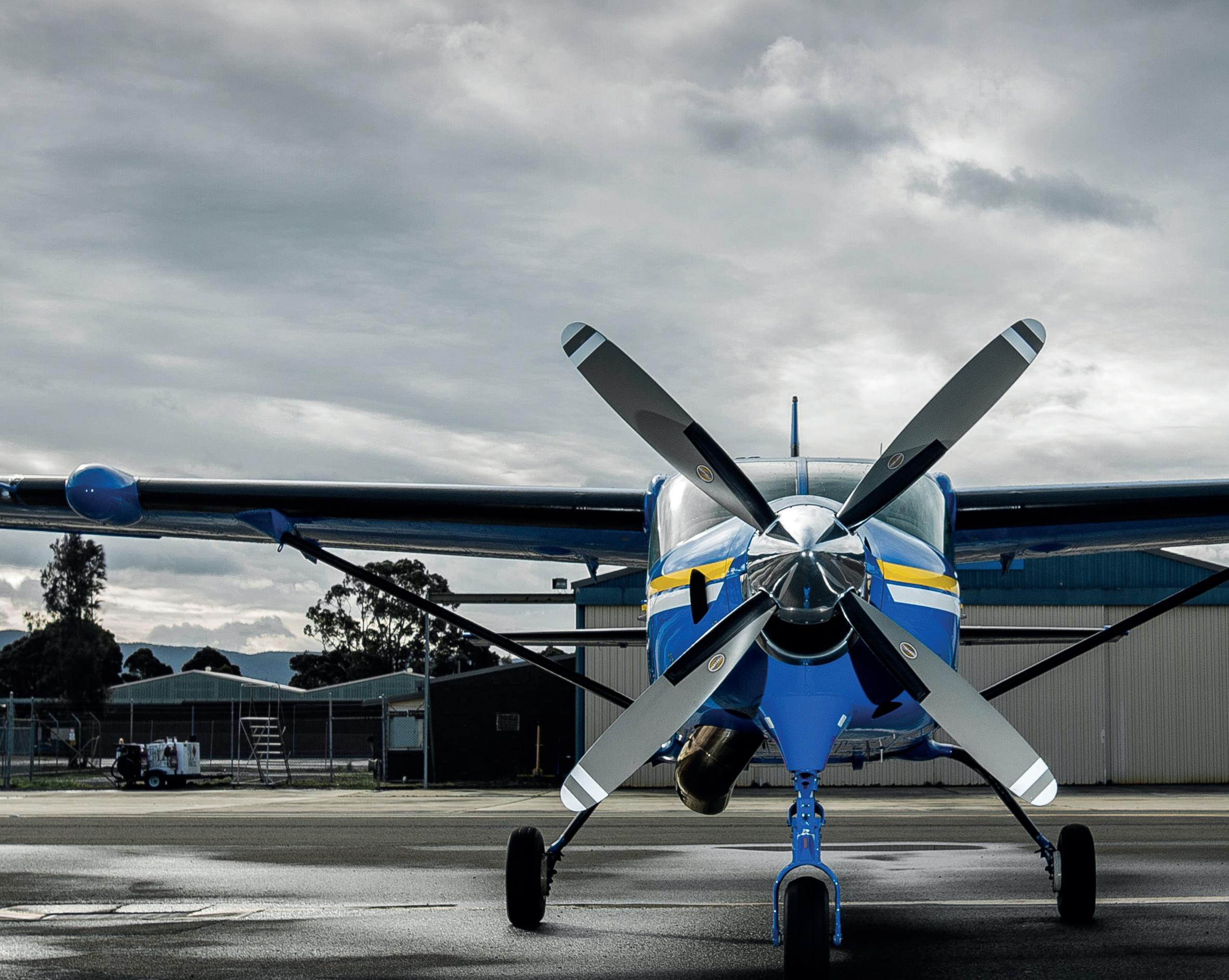
AERIAL EUROPE
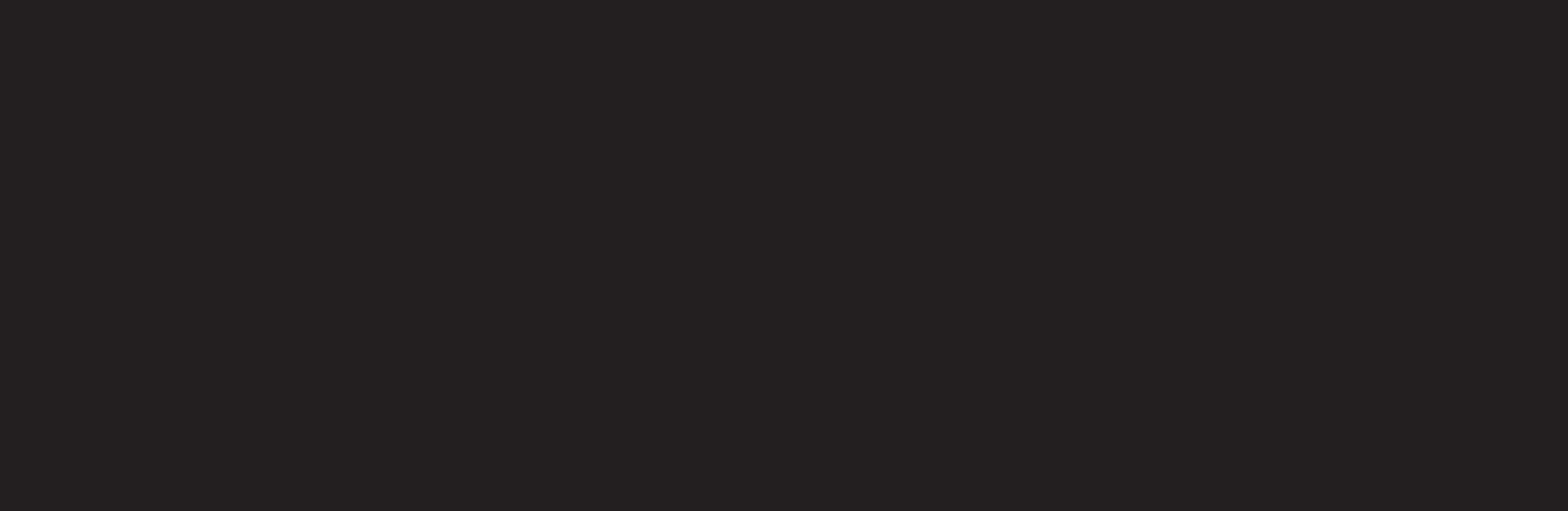
WORK MULTI MISSIONS • INTEGRATION • TECHNOLOGIES • SERVICES +44 208 255 4000 www.AvBuyer.com DECEMBER 2021

Frank Chapman (right) was the lead project test pilot for the A350-1000.
FLIGHT TESTING
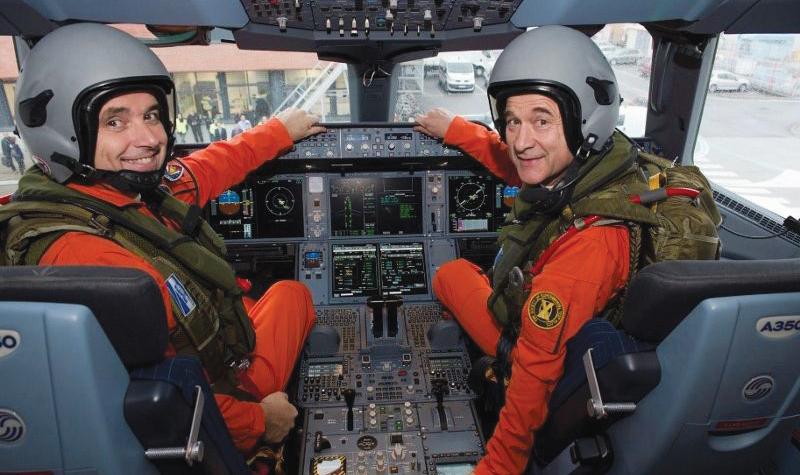
The Chuck Yeagers of Aerial Work Aviation
Have you ever heard of the Aerial Work Flight Testing sector? Do you know what this specialised Aerial Work aviation sector actually does? Patrick Ryan ‘Flight Checks’ the answer and highlights many interesting aspects of this unique ‘Right Stuff’ aviation sector.
As far as pushing the limits, few Aerial Work aviation sectors can compete with Flight Testing. Other types of sectors, Aerial Fire Fighting and Aerobatics, have substantial risks, but most jobs don’t require you to willingly come as close to total aircraft failure to get the job done. And yet, that’s precisely what the Flight Testing sector does in Aerial Work aviation. The job of the Flight Testing sector is to explore the unknown, which was true at the being of manned flight and is true today. No matter how advanced design and testing technology becomes, computers can only simulate what is known. The unknown is always, in a sense, not predictable. A computer can deduce what should occur as a logical extension of what has occurred up to that moment, but the outcome cannot be assured until it is tested in actual conditions. Flight testing is where that examination occurs. It is that point where the rubber meets the runway, where the aircraft, the test team and the actual flight conditions come together for the first time. And because Flight Testing investigates that fine edge between the known and the unknown, it is a placewhere finding the known happens. The Purpose of Flight Testing
At its core, the objective of Flight Testing is to compare the airplane’s performance against set specifications it is supposed to meet. However, not to confuse it with Flight Research, the difference between Flight Testing and Flight Research sits not in the mechanics of each operation but in the questions that drive the work and how unexpected findings are viewed. The idea is not to explore new realms of aeronautical knowledge but to ensure that a new aircraft design or configuration performs acceptably. Unless the anomaly is better-than-predicted performance, unexpected results in a flight test programme indicate problems that need fixing. The information gained through flight testing is also directed toward a specific end-user concerning a specific platform, modification, or system. Not a One-Off Effort
technical standards, professionals, aircraft, and instruments with a focused effort to support turning unknowns to knowns regarding both aircraft and the individual components integrated into these platforms. Flight Testing undertakes a wide range of valuable specialised tasks or efforts, including: Aircraft Performance Testing – This type of testing is intended to assess general handling qualities of an aircraft, operational performance, airfield noise emission, and systems operation in normal mode, failure scenarios, and extreme conditions.
Aircraft Stability and Control Testing – Stability and control testing involve an airplane’s static and dynamic stability and control characteristics. Aircraft Avionics and Systems Testing – Aircraft avionics and systems testing entails verifying how avionics and other systems are installed in an aircraft. Designers and flight test teams must validate precisely how they will operate under every conceivable condition that may occur during flight.
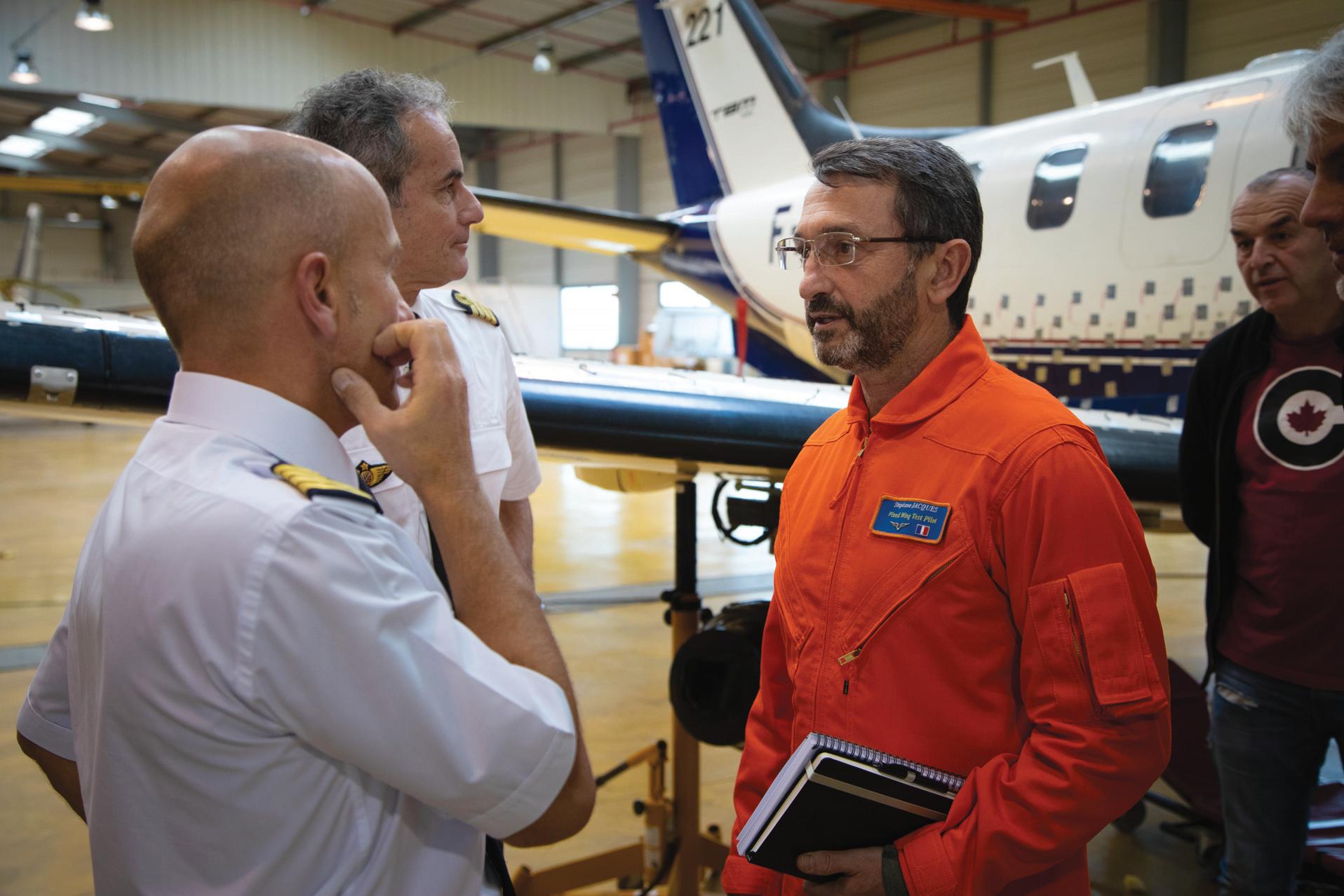
Unique Aircraft and Systems Testing – Unique aircraft and systems testing are just that, testing unique systems or modifications that may have flight type implications that influence a certified aircraft’s performance or handling characteristics. This includes any systems changes likely to affect aircraft operation, consequences for the pilot and crew, or anything that requires an amendment to the Aircraft Flight Manual. Examples of this are:
• Radar/Antenna Domes • Sensor Lifts • Sensor Operator Workstations • And many more… Post Maintenance Testing – Post Maintenance flight test is an operational check flight after an aircraft has undertaken maintenance in a way that may have significantly changed its flight characteristics or substantially affected its operational capabilities. Mitigating the Risk
As mentioned before, Flight Testing pushes the limits of flying to the edges of the unknown, e.g., will there be a catastrophic failure while flying at extreme altitudes or high speeds and put test pilots and others in harm’s way. In the past, Flight Testing was a hazardous business. In the 1950s, the doctrine of Flight Testing was “fly, crash, fix, fly.” Flight testing teams of that period would often watch with interest until an accident occurred, pinpoint and fix the problem, and then fly again to see if the solution worked. The flight test community averaged about 25 accidents a year or once every two weeks during that period! And this was the Glory Days of General Charles “Chuck” Yeager and Flight Testing! Platforms
Not like other Aerial Work sectors, Flight Testing, by nature, involves dealing with pretty much every type of aircraft and platform before the general aerospace and aviation community can safely fly it. Outside of testing a newly designed aircraft from nose-to-tail, the Flight Test sector also does some unique or specific testing with some distinctive aircraft. Some of these types of testing and the aircraft utilised are:
In the 1960s, with the cost of prototype aircraft development increasing rapidly, the emerging flight testing sector, airframe manufacturers and governments could not afford to lose expensive prototypes at such an alarming rate. With this, the System-safety concept was born along with improvements in computer-based simulation, which allowed designers and system-safety experts to mitigate risk before any actual flight. In addition, this new capability allowed the engineers to determine how much redundancy was required to obtain the required level of safety. The three significant consequences of this route to System-safety became clear: • Not waiting for an accident to occur during testing. • Identify design deficiencies early. • Make changes in designs before production or prototype execution. As a result, System-safety is sometimes delineated as a ‘cradle-to-grave’ safety process, where highly refined safety principles are applied throughout the entire lifecycle of a platform or system, not just during its flight test. Tools of the Trade Like other Aerial Work sectors, the Flight Testing sector operates with preferred capabilities and testing instruments to get the job done. The type of aircraft or instruments depends on the type of testing. This can vary from testing a prototype wide-body airline aircraft (e.g., Airbus 320neo) to a single aircraft component, e.g., a high-performance, low noise aircraft propeller system for production aircraft. • Gulfstream G-III – Testing jammer pods, atmospheric research optical sensors, etc. • Columbia 400, Piper M600, and the Cirrus SF50 Vision Jet – Testing the Garmin Autoland system. • Learjet – Testing (refueling probe-equipped) of UAV Automated Aerial Refueling systems, Electro-Optical/Infra-Red (EO/IR) sensors, and external radars for UAV Sense and Avoid programs, etc. • Saab 340 – Testing F-16 fire control radars along with EO/IR sensors. • Rolls-Royce ‘Spirit of Innovation’ – Testing an electric powertrain and power-dense battery packs. Instruments When it comes to the systems the Flight Testing community utilises, they operate some of the most leading-edge Flight Test Instrumentation (FTI) in the industry from companies like Curtis Wright, SAFRAN, and FTI. The main purpose of these instruments is to monitor and record. FTI equipment are integrated into aircraft during flight test. It is mainly used on experimental, prototype, and development aircraft and can examine various elements from the speed of the engines to temperatures of specific components. The information is displayed in the cockpit or cabin to allow the test team to observe the platform in real-time during the flight and is usually recorded for post-flight analysis. The primary types of test instruments include data acquisition systems, recorders, switches, high speed and HD cameras, RF transmitters, transceivers and receivers, flight safety systems, wireless transmitters, transponders, and transceivers gateways (Ethernet and PCM), and display and analysis software. The Life of a Test Pilot Based on the career title alone, Test Pilots have one of the world’s most inspiring jobs. But ‘Right Stuff’ moments aside, the life of a test pilot demands meticulous ❯
The QinetiQ-operated Empire Test Pilots' School ETPS provides world-leading training for flight test professionals.
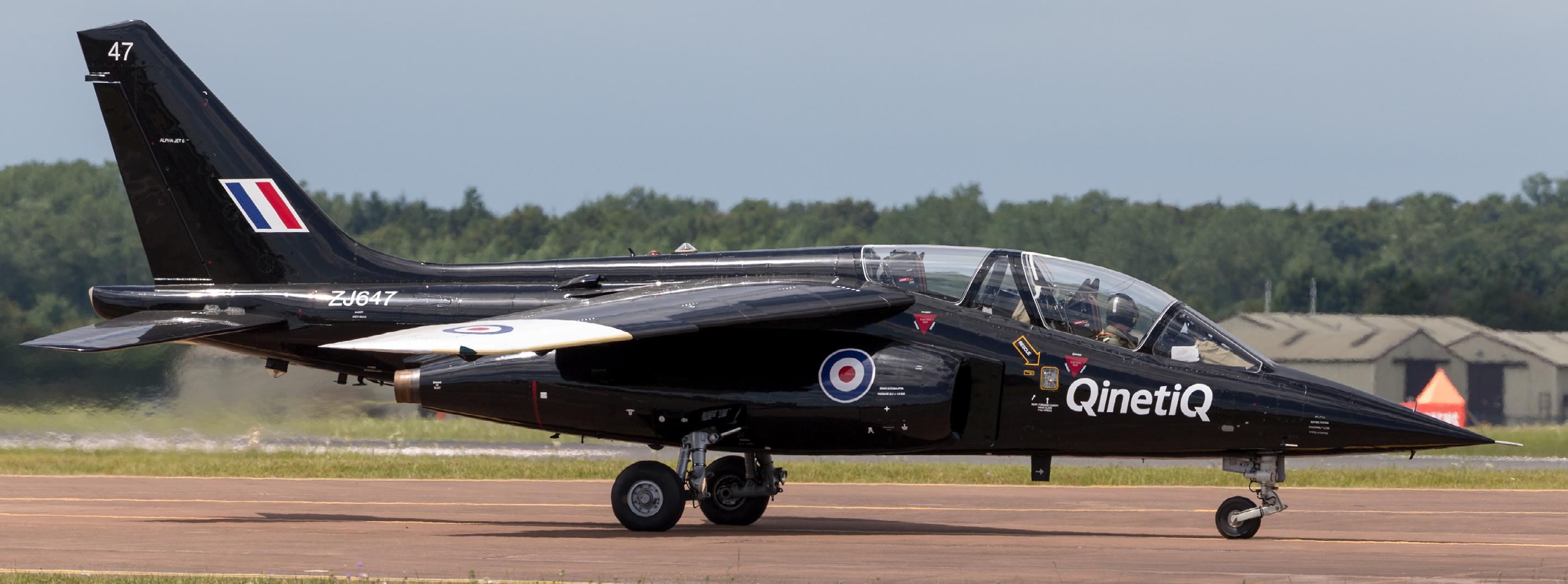