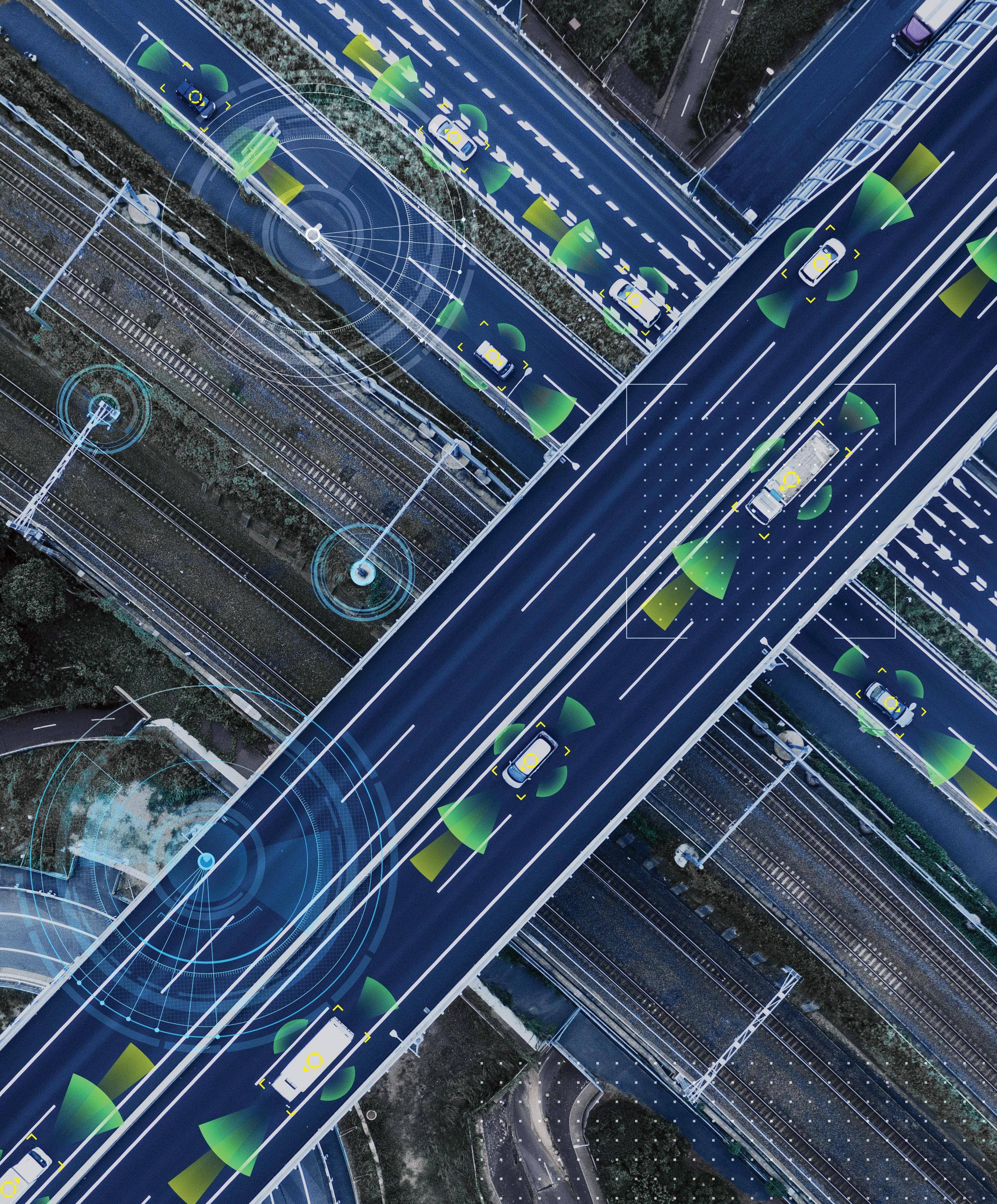
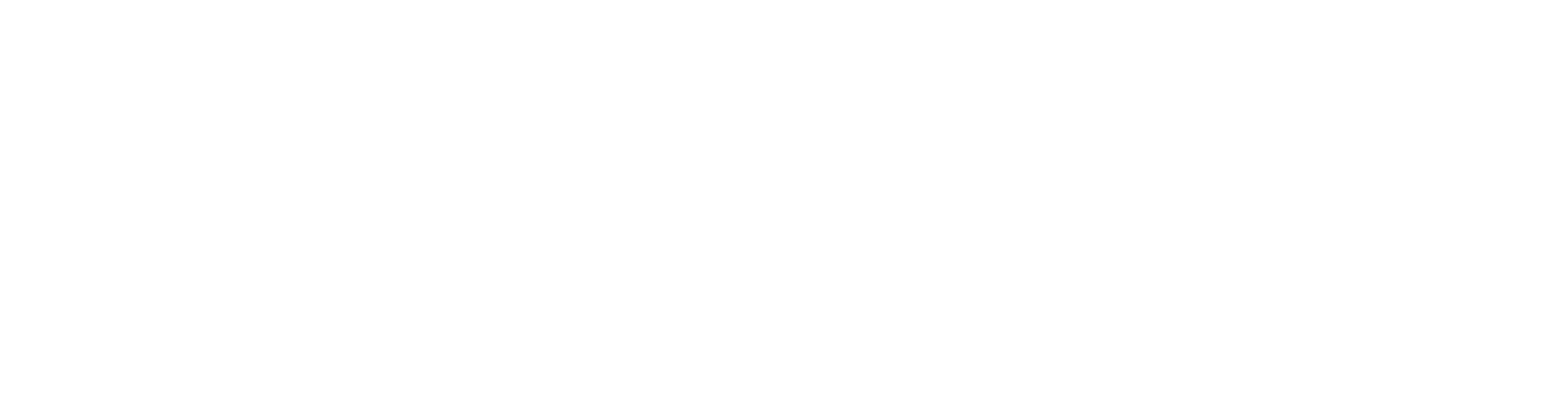
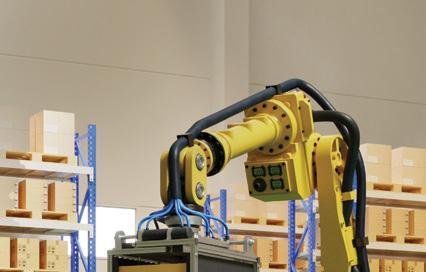

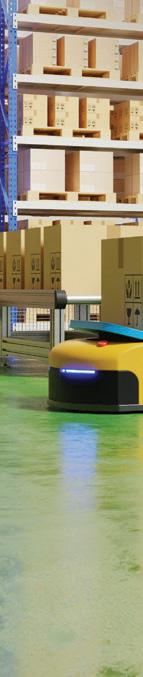
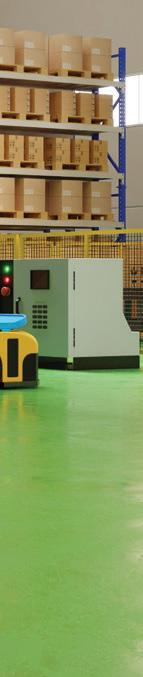
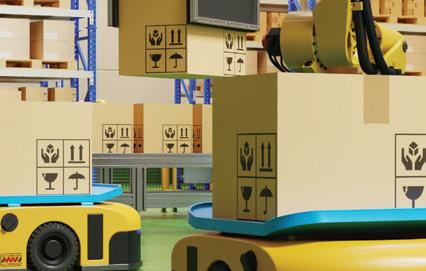
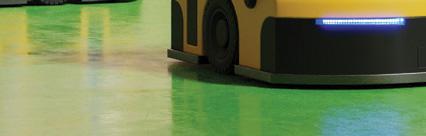
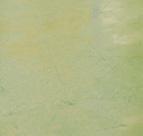
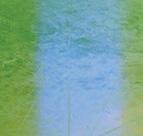
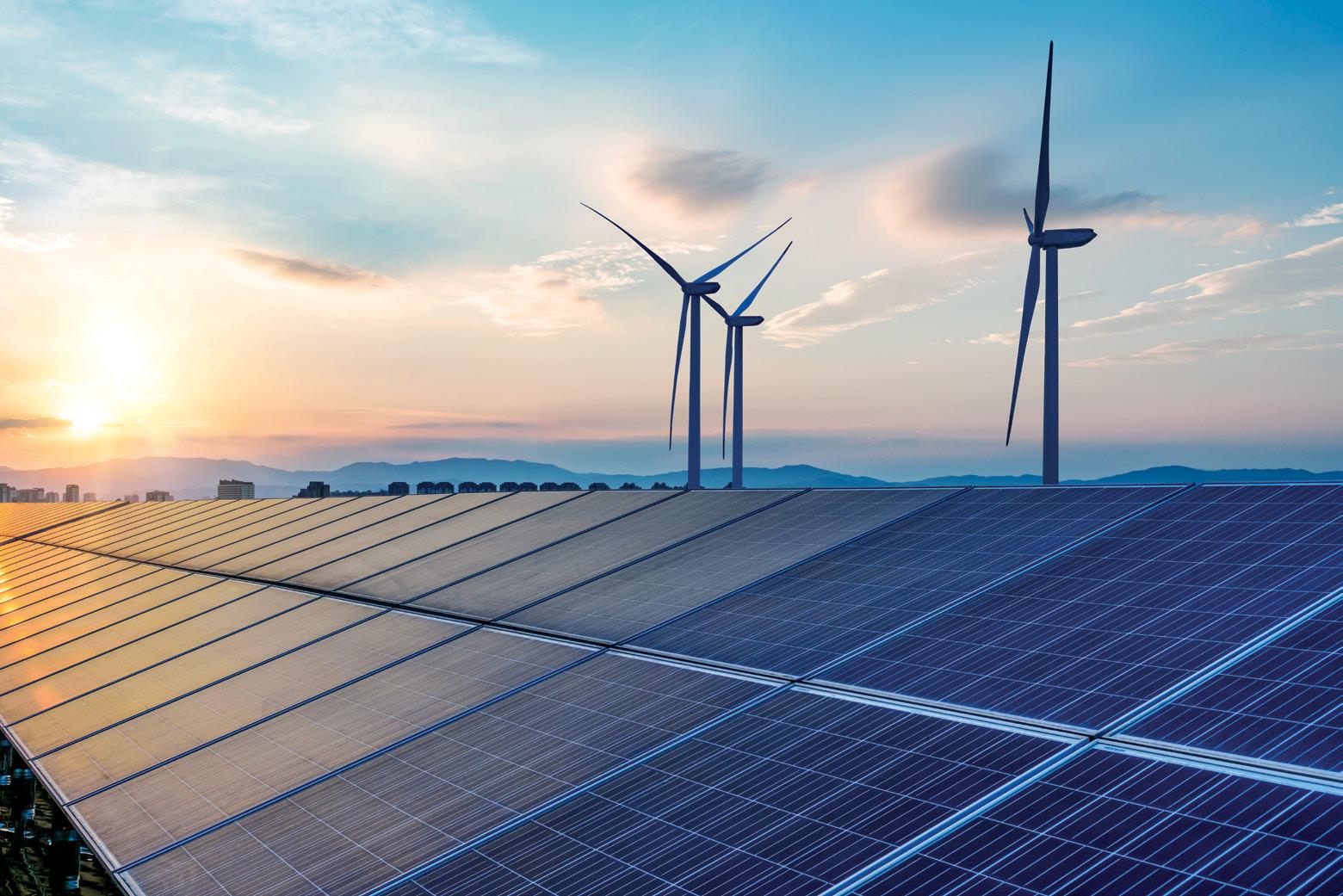
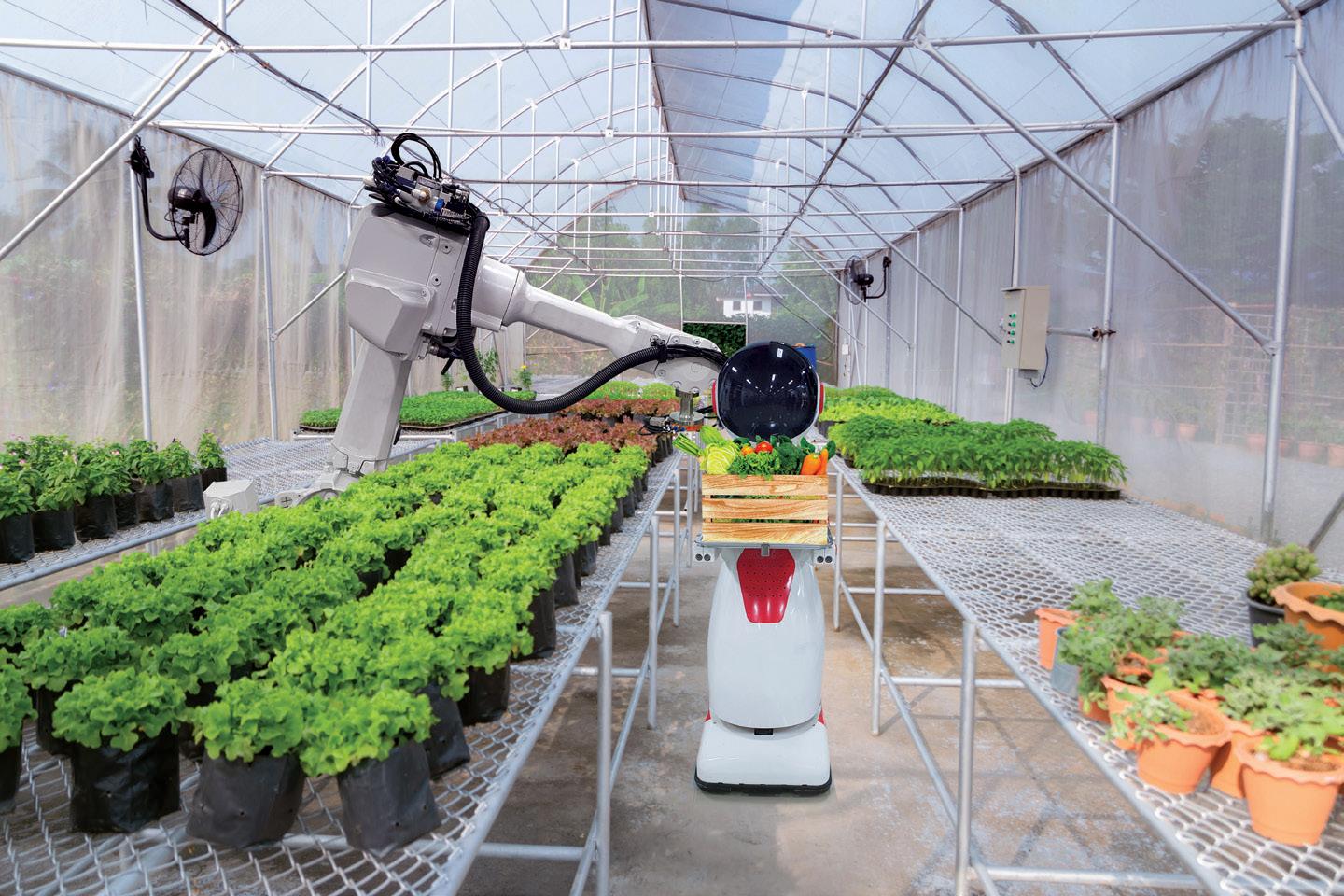
Allegro current sensors improve efficiency and power density in DC/DC converters and OBCs, so drivers can spend more time behind the wheel and less time plugged in.
• Reduce Weight and Extend Range with Small, Compact Technology
• Charge Faster with High-Power Capable ICs
• Achieve Efficient Power Conversion with Industry-leading Sensor Accuracy and Bandwidth
• Get to Market Faster with Plug-and-Play Solutions
06 Smarter, safer, cheaper: how Ethernet will enable the car of the future
The implementation of Ethernet as a universal standard throughout the automotive industry can optimize vehicle performance by reducing the number of electronic control units (ECUs) and associated wiring, thus enabling a smarter, cheaper, and safer future car.
10 Multiple-channel power monitors for automotive applications
MCPMs can simplify system design and contribute to the overall performance and reliability of the electronic system.
12 Zonal E/E will transform automotive architectures
The transition from numerous ECUs to zones will occur over several years from roughly 2025 to 2030. Each OEM will use its own architecture.
15 The future of autonomy for on-highway vehicles
The road to fully autonomous commercial vehicles is paved with unique challenges but accelerated technologies to smooth the way.
18 How do MCUs support automotive infotainment systems?
Depending on the system architecture and functions included, IVIs can be implemented with highperformance MCUs or with SoCs.
22 Advancing automotive networks: robust ESD protection for Ethernet applications
ESD protection devices act in synergy with the rest of the circuitry resulting in a robust system against destructive ESD and EMC.
27 What is a traction motor and when should you use one?
Traction motors are optimized for locomotives, EVs, elevators, and other situations where high torque at start-up and low speed is needed.
32 Testing batteries for an evolving world
Battery testing enables vehicle manufactures, owners, and researchers to make informed decision, optimize vehicle performance, and enhance overall user experience.
Today’s electronic engineers are challenged by multiple factors. Research over the years has illustrated common trends that you, as engineers, deal with including keeping your skills up-to-date, shrinking time-to-market windows, fewer engineers and smaller design teams for large projects and evolving technological trends. The bottom line is that you must continually update your engineering knowledge base to be successful in your work.
Throughout 2023, we are presenting a series of online educational days where you can learn how to address specific design challenges, learn about new techniques, or just brush up your engineering skills. We are offering eight different Training Days. Each day will focus on helping you address a specific design challenge or problem. These are not company sales pitches! The focus is on helping you with your work.
AVAILABLE ON DEMAND THERMAL MANAGEMENT
JUNE 14TH DESIGNING FOR SUSTAINABILITY
JULY 12TH EMI/RFI/EMC
AUGUST 9TH BATTERY MANAGEMENT
SEPTEMBER 13TH MOTOR DRIVES DESIGN
OCTOBER 11TH IOT DESIGN / WIRELESS
For more information and to register for these webinars, go to:
EETRAININGDAYS.COM
NOVEMBER 8TH ELECTRIC VEHICLE DESIGN
DECEMBER 6TH 5G / RF DESIGN
EDITORIAL
VP, Editorial Director Paul J. Heney pheney@wtwhmedia.com
@wtwh_paulheney
Editor In-Chief Aimee Kalnoskas akalnoskas@wtwhmedia.com @eeworld_aimee
Senior Technical Editor Martin Rowe mrowe@wtwhmedia.com @measurementblue
Associate Editor Emma Lutjen elutjen@wtwhmedia.com
CREATIVE SERVICES & PRINT PRODUCTION
VP, Creative Services
Matthew Claney mclaney@wtwhmedia.com @wtwh_designer
Art Director Allison Washko awashko@wtwhmedia.com @wtwh_allison
Senior Graphic Designer Mariel Evans mevans@wtwhmedia.com @wtwh_mariel
Graphic Designer Shannon Pipik mevans@wtwhmedia.com
Director, Audience Development Bruce Sprague bsprague@wtwhmedia.com
VP, Digital Marketing Virginia Goulding vgoulding@wtwhmedia.com @wtwh_virginia
Digital Marketing Coordinator Francesca Barrett fbarrett@wtwhmedia.com @Francesca_WTWH
Digital Design Manager Samantha King sking@wtwhmedia.com
Marketing Graphic Designer Hannah Bragg hbragg@wtwhmedia.com
Webinar Manager Matt Boblett mboblett@wtwhmedia.com
Webinar Coordinator Emira Winingerr emira@wtwhmedia.com
FINANCE
Controller Brian Korsberg bkorsberg@wtwhmedia.com
Accounts Receivable Specialist Jamila Milton jmilton@wtwhmedia.com
Web Development Manager B. David Miyares dmiyares@wtwhmedia.com @wtwh_WebDave
Senior Digital Media Manager Patrick Curran pcurran@wtwhmedia.com @wtwhseopatrick
VIDEOGRAPHY SERVICES
Video Manager Bradley Voyten bvoyten@wtwhmedia.com @bv10wtwh
Videographer Garrett McCafferty gmccafferty@wtwhmedia.com
Videographer Kara Singleton ksingleton@wtwhmedia.com
PRODUCTION SERVICES
Customer Service Manager Stephanie Hulett shulett@wtwhmedia.com
Customer Service Representative Tracy Powers tpowers@wtwhmedia.com
Customer Service Representative JoAnn Martin jmartin@wtwhmedia.com
Customer Service Representative Renee Massey-Linston renee@wtwhmedia.com
Customer Service Representative Trinidy Longgood tlonggood@wtwhmedia.com
WTWH Media, LLC
1111 Superior Ave., Suite 2600
Cleveland, OH 44114
Ph: 888.543.2447
FAX: 888.543.2447
DESIGN WORLD does not pass judgment on subjects of controversy nor enter into dispute with or between any individuals or organizations. DESIGN WORLD is also an independent forum for the expression of opinions relevant to industry issues. Letters to the editor and by-lined articles express the views of the author and not necessarily of the publisher or the publication. Every effort is made to provide accurate information; however, publisher assumes no responsibility for accuracy of submitted advertising and editorial information. Non-commissioned articles and news releases cannot be acknowledged. Unsolicited materials cannot be returned nor will this organization assume responsibility for their care.
DESIGN WORLD does not endorse any products, programs or services of advertisers or editorial contributors. Copyright© 2022 by WTWH Media, LLC. No part of this publication may be reproduced in any form or by any means, electronic or mechanical, or by recording, or by any information storage or retrieval system, without written permission from the publisher.
SUBSCRIPTION RATES: Free and controlled circulation to qualified subscribers. Non-qualified persons may subscribe at the following rates: U.S. and possessions: 1 year: $125; 2 years: $200; 3 years: $275; Canadian and foreign, 1 year: $195; only US funds are accepted. Single copies $15 each. Subscriptions are prepaid, and check or money orders only.
SUBSCRIBER SERVICES: To order a subscription or change your address, please email: designworld@omeda.com, or visit our web site at www.designworldonline.com
POSTMASTER: Send address changes to: Design World, 1111 Superior Ave., Suite 2600, Cleveland, OH 44114
FOR UPCOMING AND ON-DEMAND WEBINARS, GO TO: www.designworldonline.com/designworld-online-events-and-webinars
DESIGN WORLD WEBINAR SERIES: Where manufacturers share their experiences and expertise to help design engineers better understand technology, product related issues and challenges.
has become a common refrain among buyers of new cars to say, “It feels like I’m driving a spaceship.” In some regards, that feeling is valid — beneath the hood, modern vehicles, like spaceships, run akin to supercomputers. Thus, OEMs are feeling increased pressure to simultaneously increase the ability for vehicles to quickly process ever-growing amounts of data while simultaneously decreasing vehicle network architecture.
As vehicles continue to evolve and offer everything from more immersive entertainment features to safer, more precise autonomy, this problem will worsen. One solution, however, has the potential to enable the next evolution of automobiles: Ethernet.
Robert Metcalfe and his colleagues at the Xerox Palo Alto Research Center invented Ethernet in the 1970s to, in Metcalfe's words, solve the problem of connecting a building full of personal computers without creating a centralized “rat’s nest” of wires. Ethernet, simply, is the single-cable solution that Robert and his team ultimately created.
In an automotive capacity, Ethernet acts largely the same: when combined with sufficiently advanced chipsets, it significantly reduces the complexity of a typical vehicle’s networking system. In automotive terms, that equates to domain vehicle architecture (Figure 1) versus Ethernet-based centralized vehicle architecture (Figure 2). Automotive Ethernet, however, is built to withstand more difficult conditions than faced by a typical data center — automotive Ethernet is built to operate in environments of varying climates and terrains of varying toughness.
Vehicle architectures today are evolving away from domain-centric controllers and thus, vehicular networking capacity must be able to process the higher data rates necessitated by advanced applications like Advanced DriverAssisted Systems (ADAS), autonomous driving (AD), and a wide range of software updates delivered over the air (OTA). Challengingly, the future vehicle must meet these demands while simultaneously delivering improved reliability and security.
Ethernovia’s Ethernet-based architecture is designed to enable a seamless, holistic,
The implementation of Ethernet as a universal standard throughout the automotive industry can optimize vehicle performance by reducing the number of electronic control units (ECUs) and associated wiring, thus enabling a smarter, cheaper, and safer future car.
Shirani, Ethernovia CEO and Co-Founder
and streamlined hardware and software system that meets this demand through the integration of advanced networking features targeting the future of software-defined vehicles.
Ethernet actually began to appear in mainstream automotive implementations a decade ago. BMW were the first to introduce Ethernet in consumer vehicles back in 2008; since then, more than 90 percent of car manufacturers have incorporated Ethernet in their vehicles.
Several features then laid the path for Ethernet’s wider automotive adoption. Ethernet ‘T1’ transceivers were designed to meet the stringent OEM EMI/RFI requirements for the automotive market as well as reducing 75 percent of the copper cable, by operating over a single pair as opposed to the four pairs used for Enterprise Ethernet. This reduction had a significant impact on the weight and cost of the wiring harness. Additionally, Ethernet’s open standard environment meant there were several suppliers creating solutions as opposed to the single vendor solution for some of the legacy automotive technologies — driving innovation and providing secondsource options, which are key for automotive OEMs.
Finally, enhancing network protocols took traditional ‘best-effort’ Ethernet and provided time-bound, guaranteed delivery of in-vehicle data.
In the last decade, and with the continuous forward momentum in features and speeds available, we have seen Ethernet move from deployment in diagnostics and infotainment to deployment throughout all domains in the vehicle.
As shown in Figure 1, many different networks exist in cars today to connect
ECUs in the vehicle. With the advent of new features making cars ever smarter, there is a perpetually increasing amount of bandwidth in the car to support these applications. OEMs need increasing compute resources to deal with this data while simultaneously simplifying the vehicles with the consolidation of ECUs. The result? A huge demand for high bandwidth, low latency, and secure networking technology to efficiently move data around the vehicle.
In 2022, Forbes solicited predictions from technology experts on the features they expected to see in future vehicles. The predictions were wide-ranging: autonomy, of course; cars serving as fully functioning office spaces with 5G connectivity; advanced artificial intelligence and machine learning capabilities; enhanced privacy and cybersecurity; augmented reality navigation; and more.
Future vehicles with these capabilities can never be built on the networking infrastructure most automakers have in place today given the requisite increase in processing demand. An Ethernet-based, in-vehicle, end-to-end networking solution as the backbone, auto engineers and designers will be empowered to realize the smart ‘future cars’ the technology industry and automotive evangelists prognosticate about today.
A subset of the smart(er) vehicles is ADAS and AU, which have evolved significantly over the past decade. The two exist across six levels of complexity:
Level 0: Manual driving
Level 1: Driver assistance
Level 2: Partial automation (“feet off”)
Level 3: Conditional automation (“hands off”)
Level 4: High automation (“eyes off”)
Level 5: Full automation (“mind off”)
The majority of cars today actually exist at
level zero — fully manual — with newer vehicles implementing level one and level two. Progressing beyond those levels requires an exponentiating amount of bandwidth which can be seen in Figure 3. Such progression, however, is necessary to ultimately improve safety on the road. A 2017 report from the U.S. Department of Transportation National Highway Traffic Safety Administration found human error to be the “major factor” in 94 percent of all fatal crashes. A 2018 report from Automotive Management stated:
The growing penetration of ADAS, such as automated emergency braking, blind spot monitoring, and lane assist will result in a 15% reduction in the number of accidents in the four main European markets (France, Germany, Italy, and the UK) by 2030.
Sufficiently advancing ADAS and AU technology begins with a capable vehicle network — and that begins with an Ethernet and silicon-based solution.
Moving forward, OEMs are trying to further consolidate ECUs and functions. Ethernet aggregates traffic into a single backbone, reducing the need for a complex wiring harness, associated connectors, and myriad required legacy transceivers. This aggregation provides a significant cost saving to the OEMs with the added benefit of security, simplicity, and — very importantly — weight reduction using the ‘T1’ single-pair automotive transceivers.
For consumers, lighter vehicles equate to greater fuel economy. According to the U.S. Department of Energy, “a 10 percent reduction in vehicle weight can result in a 6 percent-8 percent fuel economy improvement.” The Department of Energy also underscores the importance of weight reduction in enabling longer-range electric vehicles:
While any vehicle can use lightweight materials, they are especially important for hybrid electric, plug-in hybrid electric, and electric vehicles. Using lightweight materials in these vehicles can offset the weight of power systems such as batteries and electric motors, improving the efficiency and increasing their all-electric range. Alternatively, the use of lightweight materials could result in needing a smaller and lower-cost battery while keeping the allelectric range of plug-in vehicles constant.
Range anxiety represents one of the top concerns hindering the broader purchasing of electric vehicles, with the World Economic Forum, citing a 2022 study by EY, noting about onethird of drivers worldwide express concerns about driving long distances in these vehicles.
So, by making vehicles lighter, OEMs benefit in manufacturing costs, consumers benefit in extended fuel range, and the planet, by extension, benefits from the wider adoption of non-carbon-emitting vehicles.
A major proof point in the market’s belief in the further complexification of vehicles is the forecasted segment growth over the next decade. Future Market Insights estimates the global automotive connectivity market to grow from $33.42 billion today to $190.29 billion by 2033.
Consumers have seen the promise of vehicular innovation and the promises they hold for smarter, safer, and cheaper driving options. That future will be realized, but only if networks can process increasing demand. Ethernet is the best solution to meet that demand.
Designed by Engineers for Engineers, our DC-DC Optimizer helps you find the optimal power inductors for your converter designs quickly and easily, reducing your design cycle time.
Coilcraft’s MAGPro suite of online inductor analysis tools are designed to enable inductor selection and circuit optimization based on sound engineering principles and measured data.
The DC-DC Optimizer starts with your power converter parameters, calculates the needed inductor specifications, identifies off-the-shelf part numbers, and provides
side-by-side performance analysis.
The tool identifies optimal inductors for buck, boost, and buck-boost converters. With just a few clicks you can go from VIN/VOUT converter requirements to inductor selection complete with losses and saturation analysis, all based on verified inductor data.
Reduce your design cycle time with confidence at www.coilcraft.com/tools.
sensing and power monitoring are essential design aspects of several automotive systems. Moreover, some kinds of automotive modules may need more than one of these sensing/monitoring operations. Multi-channel power management (MCPM) ICs can help in this regard. They can incorporate up to four energy monitoring channels, including bus voltage monitors and current sense amplifiers. Thanks to their recent Automotive Electronics Council (AEC) AEC-Q100 stress test qualification for packaged integrated circuits (ICs), these MCPM devices can serve in several automotive applications.
The measurement, monitoring, and control of power is increasingly important for all kinds of electronic systems. Power management can promote power efficiency, optimize the remaining battery life or enhance other power-related system functions. At its most basic level, power monitoring circuitry usually consists of a sense amplifier circuit operating across a sense resistor. This basic configuration can monitor current, voltage, and power data through an analog output. The sense amp is typically energized continuously and lacks more advanced functions such as the ability to poll the circuitry and interrupt circuit operation to reduce power consumption.
Contrast this basic current sensing with the actions of a digital power monitor or precision power monitor. This scheme is also called a high-side current sensor and can have other monikers as well. An IC capable of making and digitally communicating more than a single current sensor measurement is more accurately described as an MCPM.
An MCPM can connect to a higher voltage rail without the need for additional protection devices. The newest family members (PAC194X/5X) can measure 0 to 32 V. Measured values go digitally over a two-wire I2C/SMBus to a host computer. The power monitor calculates power consumption on-chip independently of the host controller and makes this value available in a register. This approach saves software overhead, development time, and reduces code complexity associated with monitoring one or more current sensors.
With the appropriate data, the host can proactively disconnect loads to save power and reconnect them as needed. This process also saves time in the awake state while the sensor accumulates data. Additionally, power monitoring activities managed by the host processor can be put to sleep, leaving more of the remaining
processing power for the other activities.
The PAC194X/5X is a family of MCPM ICs with up to four bidirectional, high-side/low-side current-sensing channels. Also included are precision voltage measurement capabilities, an integrated power calculation, and a power accumulator. PAC194X devices are specifically designed for lower voltage applications. With 16 bits of resolution, the voltage rail spans 0 to 9 V without requiring additional circuitry. Such qualities make the chips good candidates for dual-cell Li-Ion battery applications. A configuration
MCPMs can simplify system design and contribute to the overall performance and reliability of the electronic system.
of 0-to-4.5-V single-cell Li-Ion applications can be realized with the same 16 bits of precision. This allows the ICs to be used for accelerator cards, field-programmable gate arrays (FPGAs), graphics, telematics, computing, and more.
Two flexible alert outputs can help define, capture, warn, and report to the host, alerting it to take the appropriate actions. Thanks to two digital outputs, a spurious current event can be captured separately from a spurious voltage event; consequently, the ICs can respond distinctively differently to the two kinds of anomalies. Another option would be to measure or mask over-voltage (OV), over-current (OC), and over-power (OP) as well as under-current (UC) and undervoltage (UV) occurrences. Such options greatly simplify and improve the system’s response to different power situations.
MCPMs can measure the voltage and current simultaneously with a 16-bits resolution for each. The measurement limits of the two flexible alerts can easily be adjusted by configuring a 16-bit limit register for desired current-voltage events and a wider register for power events.
One challenge in power monitoring is the amount of current consumed when measuring power. A single power monitor can draw up to 360 µA or more. In contrast, an MCPM can use at least 31% less current than a single-channel device that makes two measurements. In this case, the twochannel system only pulls 495 µA compared to 720 µA for two single devices.
The difference in current consumption is even greater with more channels; it is 54% lower with a three-channel system and 66% with a four-channel system. The need to draw less current with multiple devices also saves printed circuit board (PCB) space and simplifies layout.
MCPMs are also suitable for use in vehicles. It is interesting to note that in a typical automotive telematics or radio head module, there can easily be three or more current/voltage nodes to monitor.
The PAC194X/5X MCPMs have passed AEC-Q100. The Automotive Electronics Council established AEC-Q100 as a failuremechanism-based stress test qualification for packaged ICs employed in automotive applications. AEC-Q100 basically extends IEC and Jedec specifications for automotive uses. An AECQ100-qualified device has passed specified stress tests that guarantee a certain level of quality/reliability. For example, AEC-Q100 for grade-two semiconductor components requires high-temperature operating life (HTOL) testing of 1,000 hours at 125°C. Typical automotive application examples include graphics cards, dc-dc converters, power inverters, fan control, and more.
Electrostatic discharge also plays a significant role in automotive quality. The PAC194X/5X devices tolerate 7,500-V HBM (human-body model) and 4,000V CDM (charged-device model). HBM simulates ESD caused by discharge from human beings. CDM simulates the discharge of a charged device when it touches a conductive material.
There are two versions of the PAC195X. PAC195X-1 devices are for high-side current sensing; PAC195X-2 devices are for lowside current sensing or floating Vbus applications. The high impedance input of the PAC194X/5X design allows for longer traces on the PCB (up to 1 kΩ) associated with the sense resistors. Thus, sense resistors can be physically separated as is often necessary for quantifying multiple (up to four) current flows from disparate sources.
The PAC194X provides a unique 16-bit resolution on lower Vbus measurements supporting 4.5 and 9 V, while the PAC195X supports 16 and 32 V (with 40 V being the absolute maximum for both families). For applications up to 60 V, a floating voltage node with a resistor divider can be used to keep the voltage under 40 V.
The PAC194X/5X family features a wide dynamic measurement range that enables low-power events — such as trickle charging — and high power-consumption events — such as battery charging — to use the same voltage rail. This feature eliminates the need for separate coding specific to each of these events. It is the 16bit resolution in the PAC194X/5X family that makes this simplification possible.
In addition, extensive driver support, including MPLAB Code Configurator, MPLAB Harmony, Python code, and Windows 10/11 drivers, is available with Linux drivers coming soon to simplify software development.
For prototyping, a burst mode measurement allows increasing the measurement speed or sampling rate for one rail and using it for better singlechannel characterization and prototyping. Power accumulation registers additionally help the designer to better understand the system over time.
LONGbefore the smartphone, the number of interconnected electronics and electrical equipment on automobiles, especially high-end vehicles, led pundits to describe a car as a computer on wheels or digital car. More recently, with IoT terminology attached to any wired or wireless electronic product connected to the Internet, cars have now become the IoT on wheels. To continue the progress yesterday’s interconnected vehicle into the future, the electrical/electronics (E/E) architecture must evolve to address increasing complexity, speed of getting to production, ongoing updates during the life of the vehicle, and network/vehicle-wide security, all while offsetting computing cost increases by reducing system integration costs.
Today, automotive experts are proud to cite the presence of 60 to 100 traditional electronic control units (ECUs) on an average vehicle, each with a computing core — microcontroller (MCU) — to provide the various features and functions that car buyers want. This number should shrink as the vehicle architecture changes from distributed to zonal designs with central computer systems (CCS). With all the legacy hardware and software that currently provides the desired functions and proven reliability, the transition will not occur without intermediate steps. Besides timing considerations, safety and security must be paramount to obtain the full benefits of the transition.
From roughly 2025 to 2030, computing could be based on using two or more central computer systems with several zone controllers that aggregate functions from previous ECUs. Figure 1 shows Infineon’s vision of how this could occur. In addition to the various zone modules, power distribution systems (PDS) will also be a critical element of new vehicles.
In today’s vehicle architecture, an ECU typically controls an entire domain such as
a powertrain or chassis. It’s cumbersome to control and difficult to update the software because the ECU has no direct connection to the outside world. In the new zonal approach, the geographic arrangement aggregates hardware and software independent of the domain, which means fewer, easily softwareupdateable ECUs. Several CCSs perform high-level processing. One CCS could address cockpit domain control (CDC) and networking functions — typical body electronics systems. A second CCS would handle advanced driver assistance systems (ADAS) including image processing.
In the 1990s, OEM efforts to develop a standard approach to vehicle network communications led to SAE J1850 with unique versions for Chrysler, Ford, and GM. Other OEMs are also taking their own unique paths for zonal architectures.
In this approach, the central computers do the high-level processing with actions carried out by the zone control units (ZCUs). These ZCUs interface with satellite sensors and actuator modules at the edge of the vehicle’s platform. The ZCU middleware enables a future with flexible softwaredefined vehicle (SDV) features, constantly updated by the OEMs.
Another variation of this architecture for the 2028-30 timeframe is the layered approach. This architecture consists of:
• An upper, high-performance central computing layer consisting of modules for real-time control and for Adaptive AUTOSAR (AA) or POSIX;
• A layer with as many as 5 to 10 zones that are ASIL D capable and include chassis, body, and safety ECUs;
• The lowest layer that has intelligent edge devices including a mix of smart sensors and small ECUs, PDS elements, and other miscellaneous legacy hardware.
The transition from numerous ECUs to zones will occur over several years from roughly 2025 to 2030. Each OEM will use its own architecture.
Ray Notarantonio, Jeff Kelley, and Seongman Jeong , Infineon Technologies
OEMs are initially pulling body systems into zones. In this transition phase, the powertrain in battery electric vehicles (BEVs) could be among the last to have a zone. Some possible implementations mix body and safety domains into a zone. Others doing zone controllers try to avoid ASIL A and ASIL B overlap because if they co-exist, then both require ASIL-B qualification and work products. That means higher costs and greater system complexity.
Another system aspect is how OEMs deal with wake-up considerations. Today, many inputs can wake-up a car: door handles, remote keyless entry (RKE), the liftgate, smartphones, and more. Since these wake-up inputs can go into different ECUs, coordinating and managing the wake-up at the vehicle level is challenging. When to wake-up and how to wake-up a vehicle will become much more decentralized and software dependent in future vehicles.
One of the design goals of these new architectures will be over-the-air (OTA) updatability, to provide unprecedented flexibility in new features, updates, and services. OTA introduces greater security risks and offers solutions to resolve them. The new ISO21434: Road vehicles — Cybersecurity engineering, outlines processes and methods to support security in these new automotive architectures.
Because the complete ramifications of any new architecture are not fully understood at this point, OEMs could react quite differently based on their design considerations and strategies. ZCUs tend to be body applications, but at some OEMs, they could be body and safety or safety and powertrain applications, or even vehicle motion, chassis, and propulsion in one. Those are different implementations that could be put into zones. The zone concept itself is the common theme with the CCS on top and legacy systems below that do not have to significantly change. For example, in the legacy portion, a fuel pump does not need to change very much because its function — innovation is not required. It is probably not going to be incorporated into a zone controller because the electronics could even be embedded in the fuel pump itself and it just needs network connectivity.
New E/E architectures will ultimately change the way engineers design and implement vehicle electronics. These changes, however, will take several years to implement because they will not replace legacy ECUs all at once. While existing vehicle models will not be redesigned to fit a new or transitional architecture, the need to have OTA updateable software and software-based services could accelerate the timing.
THEThe promise of fully autonomous on-highway vehicles has enthralled manufacturers, consumers, and media alike. The world awaits a future where trucks, buses, and emergency vehicles can be operated entirely by automation and respond to ever-changing environmental and traffic conditions. The automated trucks and buses market is expected to grow to 1.2 million vehicles by 2032, or 19% of the total market. China will lead the way in the adoption of autonomous commercial vehicles, with 38.5% share, followed by Europe and North America with 29% and 26% share, respectively.
In this brave new world, fully autonomous commercial vehicles will operate on a 24/7 basis: overcoming driver shortages and fatigue, smoothing out traffic, and reducing gridlock and accidents. Fleet operators will be able to handle more cargo, driving more revenues while reducing the total cost of ownership of trucks by 45%.
Commercial vehicles can sense and respond instantly and seamlessly to traffic light changes, road congestion, heavy rain and snowfall, pedestrians, and more. In addition, automated trucks,
The road to fully autonomous commercial vehicles is paved with unique challenges but accelerated technologies to smooth the way.
Lisa Viazanko, Vice President, and CTO of Industrial, Commercial Transportation, TE Connectivity
buses, and emergency vehicles won’t be prey to unsafe drivers who take unnecessary risks, such as failing to signal, making unexpected lane changes, weaving in and out of traffic, and suddenly stopping. Since 94% of vehicle accidents are due to driver distraction or error, traffic injuries and fatalities will ultimately plummet.
So, where are we headed, and what can commercial vehicle makers and logistics operators expect from their original equipment manufacturer (OEM) and component manufacturer partners? After all, investors have invested more than $330 billion in automation, connectivity, electrification, and smart mobility (ACES) companies since 2010, with more than a third going to autonomous vehicle technologies. Why haven’t manufacturers deployed fully autonomous commercial vehicles on the road yet?
Automated vehicles are rated on a scale of Level 0, or no automation, to Level 5, or full automation. The on-highway vehicle industry is currently at Level 2, or partial automation. Drivers benefit from technology such as advanced driver assistance systems (ADAS), which help them maneuver and park oversized commercial vehicles.
Commercial vehicle manufacturers are also borrowing best practices from auto manufacturers, which are leading in innovation thanks to significant funding in the space. Auto manufacturers such as Tesla and General Motors offer automated driving functionality classified as Society of Automotive Engineers (SAE) Level 2 in the U.S. At the same time, Mercedes-Benz has achieved approval in Germany in 2022 for Level 3 automated driving and is the first carmaker to achieve approval in Nevada USA to deploy cars with Level 3 automated driving. Pony.ai has launched robotaxis in China with a safety driver monitoring service, while Waymo and Cruise are about to do the same in San Francisco.
With so much investment and innovation, Level 5 automation for both on-highway and passenger vehicles will likely be achieved this decade. Industry watchers believe that fully autonomous trucks will lead the way, as highway driving is easier to master than the unpredictable urban and suburban driving conditions experienced by route vehicles such as buses and passenger vehicles. In addition, the expected 45% reduction in the total cost
of ownership for autonomous trucks more than justifies the investment in the higher level of computing, AI, and sensor performance, removing cost as a barrier to adoption.
Numerous technical obstacles must be overcome before manufacturers can gain regulatory approval for fully automated commercial vehicles produce and deploy them at scale.
These challenges include:
Aligning electrification and automation objectives:
Commercial vehicles are electrifying at a fast pace. Vehicle manufacturers want to futureproof their businesses, while fleet operators want to pivot away from using fossil fuels and reduce energy costs. There are multiple paths to electrifying commercial vehicles, including developing conventional hybrids, plugin hybrids, battery electric vehicles, and hydrogen fuel electric vehicles.
This means that more technology, including high-voltage equipment, is now going under the hood of vehicles, which is why component manufacturers are miniaturizing systems where possible. One strategy is to co-locate power and data transmissions using electromagnetic shielding in a hybrid connector. By doing so, commercial vehicle manufacturers can minimize space while enabling the side-by-side location and transmission of electrical current and highspeed data signals.
Ensuring pervasive communications: Each autonomous vehicle will be packed with technology, including sensors, connectivity, and artificial intelligence. Trucks, buses, and emergency vehicles collect data from multiple devices, including RADAR/LiDAR, cameras, antennas, displays, and telematics.
This technology will ultimately capture vast amounts of data at more than 25 gigabits per second. The industry will evolve from powering in-vehicle communications governing systems like ADAS to enabling vehicle-to-vehicle (V2V) and vehicle-toeverything communications (V2X). Achieving this vision is some years ahead. Automation and artificial intelligence need to process data in real time, enabling vehicles to react to changing road conditions and the actions of other vehicles. That’s much more challenging for commercial vehicles, which can’t react as quickly as smaller passenger vehicles. So, suppliers of connectivity and sensor solutions must consider the physics of key processes, such as unexpected braking, and recalibrate commercial solutions to react faster to enable preventative actions.
Currently, many commercial vehicles use CAN networks that transmit data at slower speeds. As a result, automobile, OEM, and component manufacturers are working on developing new Ethernet standards that will enable ultra-fast communications in harsh environments. The 100 BASE-T1 and 1000 BASE-T1 Ethernet protocols can transmit high amounts of data using an unshielded twisted pair, compared to only 400 kB with CAN and 1 MB with CAN-FD. Meanwhile, the automotive ethernet is at 25 Gbps and will reach 100 Gbps soon. Commercial vehicles typically require 1000BASE-T1bp Type B, which provides a longer channel length that accommodates the longer distances between systems like cameras and displays in commercial vehicles. Next-generation architectures will use a mix of CAN and Ethernet protocols, aligning them to the
functionality they support. Systems and devices are interconnected via onboard networks, enabling high speeds of data transmissions. Data is then processed via one or more electronic control units to create a real-time view of vehicle performance, conditions, and the surrounding environment. Ethernet connectors help enable data connectivity by providing wire-to-wire connections supporting digital services and operations, such as multifunction displays, telematics, telemetry units, infotainment modules, and media access controllers. They are sealed to ensure flawless performance with heavyduty usage and have secondary locking to ensure contact retention.
Commercial vehicles must withstand punishing operational and environmental conditions. They may operate around the clock for years on end, must withstand vibration and shock, and often operate in environments characterized by extreme temperatures ranging from -40°C to 125°C, dust and gravel, moisture, and corrosive fluids. Finally, tractors and trailers may be connected and unconnected frequently, which is hard on connector solutions. Component manufacturers are developing solutions, such as rugged connectors that can withstand these operating and environmental conditions and can be serviced in the field to
vehicles up and running again. Connectors with low insertion force can handle more wear and tear, such as trailers being connected and disconnected constantly while still preserving data connectivity.
Gaining
to deploy new functionality: Commercial vehicle manufacturers and technology providers are testing new functionality, such as automated lane changing in controlled environments, to test and learn how vehicles perform and solve issues before seeking regulatory approval. They’re learning from passenger vehicle trials which are now happening globally. Commercial vehicle manufacturers want to know that technology is safe and works effectively before deploying automated capabilities at scale. They need to ensure regulatory and public acceptance of new systems, while technology providers want to avoid the liability of accidents occurring due to unproven systems.
OEM and component manufacturers who develop products according to the latest standards and best practices can help commercial vehicle manufacturers meet exacting regulatory requirements.
Commercial vehicle manufacturers have invested hundreds of millions of dollars researching new technology, developing next-generation architectures, and testing solutions. Teams at these leading companies want to work with partners with the demonstrated expertise, breadth of solutions, and global manufacturing expertise to help them close the last mile of autonomous driving. Leading component manufacturers
can provide the full breadth of sensors, antennas, connectors, cable assemblies, and data connectivity required for autonomous capabilities. They offer both standardized and customized solutions to meet customer needs. Component manufacturers can use 3D printing and injection molds to fabricate customized connectors and provide wire harnesses for customer testing if customization is required. Doing so at pace enables commercial vehicle manufacturers to maintain their desired rate of innovation. Component manufacturers must meet customer requirements for:
• Increasing safety: Providing solutions that offer extreme reliability and responsiveness amidst changing conditions.
• Enabling greater productivity: Delivering the full range of solutions that will allow greater automation of commercial vehicles so that operators can run them 24/7 to increase delivery throughput.
• Improving sustainability: Providing solutions that support vehicle electrification; reduce componentry weight; and use sustainable, affordable resins, materials, and processes.
• Creating a connected world: Those component manufacturers that run diversified businesses can bring insights, best practices, and solutions from other divisions, such as energy, engines, infrastructure, and passenger vehicles, to bear on innovating solutions for commercial vehicle manufacturers.
Commercial vehicle manufacturers and their partners have created a solid foundation for developing autonomous vehicles. They’re solving challenges around electrification, component miniaturization, data connectivity, and performance in harsh environments that will unlock faster innovation in the future.
Commercial transportation will increasingly become autonomous within the next decade, unlocking new business gains for manufacturers and operators while contributing to a safer, more sustainable world.
INvehicle infotainment (IVI) systems are increasingly important and complex. What’s needed from a microcontroller (MCU) in an IVI? A lot, but exactly what depends on the sophistication and mix of info and ‘tainment. Multiple cores are often needed, and so are hardware accelerators for compute-intensive functions. Considerations include connectivity, human-machine interfaces (HMIs) beyond simple flat panel displays, memory management, and more. Software-defined functionality and over-the-air (OTA) updates are also important.
This article begins with a brief overview of IVI functions including emerging advanced functions like driver attention monitoring and gesture recognition, looks at the growing demand on IVIs for expanded connectivity, presents a typical IVI system architecture, typical IVI MCU functionalities, and a typical IVI system on chip (SoC) and closes with a brief review of security and safety standards related to IVIs and other automotive systems.
IVIs provide the command center for vehicle operations and support for essential services. The cockpit domain controller coordinates driver information and control functions using touch
Depending on the system architecture and functions included, IVIs can be implemented with high-performance MCUs or with SoCs.
ShepardFigure 1. IVI systems provide a wide range of information and entertainment functions and connectivity (Infineon).
screens, software-defined controls, and voice commands. In advanced designs, the domain controller can also monitor the driver’s attention and focus on driving. A variety of MCUs will be required to support audio and video interfaces for drivers and passengers and to add new comfort and entertainment applications as well as advanced driver assistance capabilities. The trend is toward personalization and flexibility through software-defined functions that are replacing centralized architectures with distributed computing capabilities, more memory, and faster connectivity (Figure 1).
Cars are becoming independently aware of passengers. Advanced systems have been proposed using millimeter wave (mmwave) radar to detect and categorize passengers versus packages and other objects in the cabin, enabling the IVI to be more proactive and interactive. IVI systems are also available that support biometric authentication, like facial recognition or fingerprint scanning, to provide a more secure and personalized experience. Biometrics can also be used to limit access to specific features and prevent theft. Driver
monitoring systems are beginning to appear and are expected to be mandated by safety regulatory bodies. These systems will require an IVI that can identify the driver and monitor facial features to determine driver attention.
Gesture control is being developed for IVI systems. Technologies for gesture recognition include mmwave radar and ultrasonics. Vertical-cavity surface-emitting laser (VCSEL) technology is also being considered for gesture recognition. IVI SoCs will incorporate machine learning accelerators to support improved accuracy.
A connected vehicle has been defined as one equipped with Internet connectivity and able to send and receive data. Today, that’s only the beginning. IVI MCUs are required to manage connections to Wi-Fi (including the creation of local networks), smartphones, wireless sensors, GPS, and other devices. Various levels of connectivity are emerging that support value-added services for drivers and passengers. For a deeper dive into these developments, check out the FAQ on “What
are the five levels of vehicle connectivity?”
Smartphone connectivity is growing in importance in IVI systems. It includes Wi-Fi networking and wireless charging. Bring-yourown-device (BYOD) connectivity is supported by several IVI SoCs that tightly integrate users’ smartphones with the IVI system. And the IVI connects to the car’s CAN bus, Ethernet, USB, PCIe, and other wired networks.
5G is replacing 4G as the standard for IVI systems. Its higher speeds can support higher definition maps, updated in real-time with weather and traffic information, and new services ranging from vehicle diagnostics to interactive entertainment. IVIs are beginning to incorporate graphic processing units (GPUs) to support gaming and subscriptionbased services.
OTA updates are becoming important for IVI systems. OTA improves system operation over time by allowing car makers to update existing features and fix bugs. 5G cloud connectivity is becoming a key element supporting OTA for IVIs and for the overall vehicle.
IVI control units support a wide range of functions like (Figure 2):
• Wired connectivity including CAN-FD, Ethernet, USB, display connectivity, and others.
• Sensors including cameras, MEMS microphones, gesture recognition subsystems, inertial measurement units (IMUs), and so on.
• Audio including a mix of class AB and class D amplifiers, surround systems, and adaptive audio.
• Positioning including MEMS IMUs and GNSS receivers.
• Wireless connectivity for broadcast signals, Bluetooth, near-field connectivity, and Wi-Fi.
A typical IVI MCU, like the one illustrated in the Control Unit in the center of Figure 2 above, includes a 32-bit RISC processor with enhanced security features, cryptographic accelerators, and improved flash memory capability up to 500 kcycles with 15 years of data retention. To improve performance, it uses the Thumb-2 instruction set that’s an enhancement to the 16-bit Thumb instruction set. Thumb 2 adds 32-bit instructions that can be freely intermixed with 16-bit instructions
in a program and enables an MCU with Thumb-2 to cover the full functionality of the ARM instruction set.
The use of two CPUs in lockstep mode plus error detection in sensitive memories and hardware logic provides strong and multiple protection mechanisms for high detection coverage and supports the development of highly secure software.
Two series communication slave interfaces are compatible with ISO/IEC 7816-3 and a single wire protocol (SWP) that supports near-field communications with smart cards and similar devices in secure applications. Other communications interfaces include a master/slave serial peripheral interface (SPI) and I2C. The slave SPI operates up to 48 MHz, and the master is rated up to 15 MHz. The I2C interface operates at up to 1 Mbit/s.
Multiple timers are integrated including a permanent timer (PMT) with a count capability in low-power mode, three general-purpose 16-bit timers, and a watchdog timer.
Security is a primary concern and includes hardware accelerators and
advanced cryptographic functions like:
• Platform and flash memory loader security certification target under a Common Criteria framework that enables designers to specify security functional requirements (SFRs) and security assurance requirements (SARs).
• The 3-key triple DES accelerator (EDES+) peripheral supports a data encryption standard (DES) hardware security-enhanced accelerator.
• A NESCRYPT (NExt Step CRYPToprocessor) light low power (LLP) cryptoprocessor efficiently supports the public key algorithm.
• The advanced encryption standard (AES) and SM4 security-enhanced accelerators ensure secure and fast AES and SM4 implementations.
• 16- and 32-bit cyclic redundancy check (CRC) calculation blocks that support standards like ISO 13239 and IEEE 802.3.
• An active shield that protects against faults caused by probing or manipulating signals and adding or removing features from the MCU.
• A true random number generator (TRNG) for producing random numbers instead of a pseudo-random number generator, which uses deterministic algorithms to produce a sequence of numbers that appear random but are not.
To support IVI systems, SoCs have been developed with multiple cores like a 32-bit ARM multicore processor with an out-oforder superscalar pipeline running at up to 2.5 GHz that can support concurrent applications. Additional lower power cores are included to support real-time interrupt-intensive activities, and GPUs are included for high-performance HMIs. Some IVI SoCs also include a high-performance DSP for applications like voice recognition, surround-view stitched video, and various software-defined functions.
Entertainment is an important aspect of IVI systems, and it's common for the display subsystem to simultaneously support multiple 1080p screens with higher resolutions and larger displays in advanced systems. IVI SoCs also include hardware accelerators that can support high-def video decoding and encoding. Audio processing is an important aspect of the info and ‘tainment functions including speech processing, voice recognition, active noise canceling and multi-zone audio (Figure 3).
With increasing connectivity and OTA updates, security is critical to IVI system implementations. The SOC needs to address cybersecurity threats and vulnerabilities. Several standards have been developed to ensure the safety and security of IVIs including:
ISO 21434 is specific to cybersecurity in the automotive industry. Coverage includes the design and development of secure systems in vehicles. It addresses management of software updates and the use and management of open-source software.
ISO 21448 focuses on the safety of the intended functionality (SOTIF) in automotive systems. Coverage includes
the safety of advanced driver assistance systems (ADAS) and autonomous driving systems (ADS). It also addresses the need to identify and mitigate cybersecurity threats and vulnerabilities.
ISO 26262 includes guidelines related to functional safety in vehicles and the development of safe systems, including the identification of hazards and the implementation of measures to mitigate them. Management of software updates is also covered.
Summary
IVIs are important systems in modern vehicles providing drivers with information, passengers with entertainment plus information, and are beginning to monitor driver attention and awareness.
References
Automotive and Infotainment Technologies, Mistral https://www.mistralsolutions.com/blog/ automotive-infotainment-overview/
Designing In-Vehicle Infotainment Systems in 2023, Tremend https://tremend.com/blog/automotive/ designing-in-vehicle-infotainmentsystems-2023/
How do MCUs support automotive infotainment systems, Infineon https://www.infineon.com/cms/en/ applications/automotive/infotainment/ Infotainment Head Unit,
STMicroelectronics
https://www.st.com/en/applications/ in-vehicle-infotainment-ivi/infotainmenthead-unit.html
Today’s high-end infotainment soon becoming mainstream, Texas Instruments https://www.ti.com/lit/wp/spry261/ spry261.pdf
technology has emerged as a robust and reliable solution for data communication in various industrial and computing applications. While its adoption in the automotive sector has been relatively limited, automotive Ethernet is gaining momentum due to its ability to deliver fast and resilient data transfer. With its high bandwidth, flexibility in bus topologies, and support for multiple electronic control units (ECUs), Ethernet technologies are strong contenders for advancing automotive networks from domain-based to zonal architectures. This article delves into the requirements and properties of modern semiconductor electrostatic discharge (ESD) protection devices, specifically in connection with the 100BASE-T1 and 1000BASE-T1 standards, and explores how these devices, when synergistically integrated with the rest of the circuitry, contribute to the creation of a robust system that defends against destructive ESD events and electromagnetic compatibility (EMC) issues.
Ethernet solutions have a long-standing presence in industrial and computing applications. However, the automotive industry has traditionally been less inclined to embrace this technology. Nevertheless, recognizing the immense potential of automotive Ethernet, the One Pair
Ethernet Network (OPEN) Alliance committees, along with the Institute of Electrical and Electronic Engineers (IEEE),
have collaborated to develop standards specifically tailored to meet the unique demands of the automotive sector. In 2016, the 100BASE-T1 and 1000BASE-T1 standards were drafted, and in more recent years, the OPEN Alliance has been actively working on developing two additional standards, namely 10BASE-T1s and MGB-T1. The OPEN Alliance, comprising multiple technical committees, strives to standardize Ethernetbased technologies in the automotive market. At the same time, the IEEE has taken charge of the 100BASE-T1 and 1000BASE-T1 standards, addressing automotive requirements, particularly those related to EMC. This collaborative effort ensures that Ethernet technology in the automotive
domain aligns with industry-wide standards and undergoes rigorous testing to ensure compliance and performance.
1000BASE-T1
Automotive applications greatly benefit from the flexibility offered by Ethernet connections. Star topologies can employ these connections, where a switch serves as a central point, interconnecting multiple domains such as Advanced Driver Assistance Systems (ADAS), infotainment, and more. Alternatively, Ethernet can be utilized in a bus topology, similar to the traditional CAN and FlexRay applications (Figure 1).
Notably, the standardization of
ESD protection devices act in synergy with the rest of the circuitry resulting in a robust system against destructive ESD and EMC.
Andreas Hardock, NexperiaFigure 1: Typical configuration of Ethernet nodes in a modern vehicle.
100BASE-T1 and 1000BASE-T1 employs unshielded twisted pair (UTP) cables (Fig. 2), commonly used in the automotive industry due to their widespread availability and cost-effectiveness. However, UTP cables present challenges related to EMC behavior, particularly regarding electromagnetic interference (EMI) in bundled cable configurations.
In a modern vehicle, numerous electrical units are interconnected by hundreds of meters of cables, ranging from simple climate control units to powerful generators. These cables are often bundled together, increasing the risk of electromagnetic interference (EMI) between them. Extensive investigations have revealed that, in worst-case scenarios, this EMI can induce peak voltage amplitudes of up to 100V in unshielded twisted pair (UTP) cables. This poses a challenge as stable data transfer is required during normal operation, highlighting the need for robust Ethernet circuitry to withstand these EMC issues.
The circuitry of each node in the Ethernet system, standardized by the OPEN Alliance, includes a common mode choke (CMC) to filter out unwanted common mode noise that couples in the UTP. In conjunction with common mode termination, the CMC addresses these EMC concerns. The properties of the CMC for 100BASE-T1 and 1000BASE-T1 are defined in the CMC Test Specifications specific to these standards. Apart from its filtering and EMC characteristics, the CMC also plays a crucial role in electrostatic discharge (ESD) protection, which will be discussed in the following section.
From the perspective of ESD protection devices, there are several important considerations. Firstly, considering the potential electromagnetic noise on the UTP, the ESD device should remain inactive within a voltage range of up to 100 V. In terms of ESD
device parameters, the triggering threshold for the ESD device is set above 100 V, as shown in Figure 3 of the Transient Voltage Suppressor (TVS) graph. While this voltage threshold may seem high, it is important to note that the specific circuitry configuration, including the CMC, provides robust protection for the physical layer (PHY) components, such as highperformance cameras and displays.
Secondly, the ESD protection device is subjected to rigorous testing to ensure its robustness, with requirements of withstanding 15kV ESD discharges for a minimum of 1000 cycles. This stringent requirement underscores the criticality of reliable operation for Ethernet-based applications in the demanding automotive environment.
Combined with the 24 V operating voltage, similar to that of CAN
applications, these specific requirements create a unique set of criteria, as shown in Table 1.
In addition to the requirements outlined in Table 1, more tests need to be performed to ensure the effectiveness of OPEN Alliance ESD protections. ESD vendors typically conduct these tests, and their results can be valuable for hardware design engineers.
When it comes to 100BASE-T1 and 1000BASE-T1, the tests are quite similar,
but they have different pass criteria. The first two tests focus on the impact of the ESD protection device on signal integrity (SI) in automotive Ethernet applications. It is important to assess how the device affects SI by measuring insertion loss (IL), return loss (RL), and common mode rejection ratio (CMMR), as shown in Figure 4. To ensure compliance, specific limits for these parameters are provided in the "Specification of the ESD protection for 100BASE-T1 and 1000BASE-T1" document.
In the automotive domain, there is a new factor to consider — the ESD discharge current, which quantifies the current flowing into the PHY during an ESD event. It is crucial to evaluate this current to ensure proper protection. Additionally, RF clamping is employed to simulate the noise on the UTP, taking into account the > 100 V requirement.
By conducting these additional tests, engineers can gain a deeper understanding of how the ESD protection devices perform in terms of signal integrity and current flow, ensuring the robustness and reliability of the Ethernet system in automotive applications.
Let's dive into the crucial aspects of placing, routing, and laying out the ESD protection devices in an Ethernet design. It's not just about the performance of the ESD device itself; its implementation on the PCB plays a vital role. Figure 3 gives us a visual representation, highlighting the importance of placing the ESD device at the connector. This strategic placement ensures that any ESD pulse is immediately clamped down to ground right at the connector, safeguarding the entire circuitry, including the CMC, CMT, and PHY. For a tangible demonstration of the significance of placement, refer to Figure 5.
In Figure 5, a field scan of the Ethernet circuitry during an ESD event reveals areas of high current density, indicated by red. The OPEN
Alliance (OA) approach demonstrates that having the ESD device close to the connector results in the lowest current density at the PHY location. Consequently, the entire circuitry exhibits optimal ESD performance for the system.
It's important to grasp the role of the CMC in reducing ESD stress for the PHY. To understand this, let's examine
the behavior of the CMC under pulsed conditions, as depicted in Figure 6. We utilize the transmission line pulse (TLP) method to illustrate the blocking and saturation phases of the CMC. When a transient pulse, such as an ESD pulse, heads towards the CMC, it initially blocks the current for a specific period of time during the blocking phase (phase II), with
the peak (in phase I) being a measurement artifact. The duration of the blocking phase depends on the voltage level of the pulse the higher the voltage, the shorter the blocking phase. After the blocking phase, the CMC enters the saturation phase (phase III), acting as an inductor driven into saturation by the pulse. Once saturation occurs, the CMC starts conducting the current, leading to a drop in voltage across it.
This intriguing finding demonstrates that when an ESD pulse approaches the 100BASE-T1 or 1000BASE-T1 circuit, the CMC effectively blocks the current for the first few nanoseconds. Simultaneously, the voltage across the ESD protection device increases. When the voltage reaches the trigger level, typically around 140 V (Figure 3), the ESD device clamps the ESD pulse to ground. As a result, the voltage across the entire circuit drops to the clamping voltage of the ESD device, typically ranging from 30 to 40 V (see TLP plot in Figure 3).
This showcases the synergistic effect of combining a high-trigger ESD protection device with a CMC during ESD events. It's worth noting that a CMC with an inductance in the range of approximately 100µH exhibits sufficient blocking behavior, which is already covered by the CMC specification.
ESD protection devices are typically
available in various packages. One widely used package is the SOT23, a common and established choice in automotive applications. Another option is the DFN1006BD (SOD882BD), a leadless package. Figure 7 illustrates different options for routing the differential lines to and from the package, and their rankings are provided in Table 3.
When routing the ESD packages, it's generally advisable to keep the routes straight, avoiding any stubs or bends. Specifically, for ESD considerations, the traces of the differential lines should pass over the pad of the ESD device, as depicted in options [A] and [C] for SOT23, as well as for DFN1006BD in option [A]. It's crucial to avoid stubs and ensure that the impedance of the differential lines remains at 100Ω to maintain signal integrity (SI). This
can be achieved by keeping the lines separated. For SOT23, options [B] and [C] are preferable, while for DFN1006BD, option [A] is the recommended choice.
As a general rule, try to minimize unnecessary layer changes to achieve optimal signal integrity. Layer changes will inevitably impact SI and electromagnetic compatibility (EMC). If you must change layers, route the signal over the pad of the ESD device, as shown in Figure 8 (left and right). Avoid routing signals via stubs, as depicted in Figure 8 (middle).
By following these guidelines for placement, routing, and layout, you can effectively enhance the performance, reliability, and protection of ESD in your Ethernet design.
The article emphasizes the unique circuitry and ESD protection requirements in 1000BASE-T1 and 100BASE-T1 applications. It highlights the strong synergy between ESD protection devices and the blocking capability of the CMC, resulting in a highly robust Ethernet system that effectively combats EMC noise and ESD. The significance of positioning the ESD protection directly at the connector is underscored through an EMI scanner. Additionally, it should be noted that discussions within the OPEN Alliance committees are underway for an additional standard,
10BASE-T1S, which is expected to have similar requirements regarding the high trigger voltage, given the similarity in topology with 1000BASE-T1 and 100BASE-T1. Further research and development in this area will contribute to the continuous improvement of ESD protection solutions and their role in supporting automotive Ethernet applications.
Traction motors are optimized for locomotives, EVs, elevators, and other situations where high torque at start-up and low speed is needed.
Bill Schweberare essential components in several applications, powering equipment in many industries. In simple terms, a motor is a device that converts electrical energy into mechanical energy, generating motion or providing rotational force. Different types of motors have variations in design, each with specific features such as power, speed, torque, size, and control precision.
A traction motor is an electric motor optimized for drive or propulsion, where high torque and low speed are required. These motors are often used in electric vehicles (EVs), locomotives, elevators, and other equipment.
Traction motors can be designed as DC or AC motors, including synchronous, asynchronous (induction), and multiphase AC motors. Modern motor-control electronics tend to favor multiphase AC drives. However, AC induction motors and permanent-magnet synchronous motors (PMSM) are most commonly used in EVs. Each manufacturer has engineering and market reasons for choosing a specific motor arrangement.
The type should be carefully assessed to best fit an application based on design, performance, reliability, and cost. Additionally, the motor’s physical structure should be evaluated, including its lamination layout, windings arrangement, and the amount of copper wiring and iron used. The electrical schematic of a traction-optimized motor and another type might be the same on paper, but the physical details differ.
Motor design is continually evolving, driven by demands for increased efficiency, improved performance, and reduced costs and environmental impacts. Advances in motor-related control algorithms and power-switching devices mean that previous limitations and conventional wisdom may no longer apply.
A motor that was once an ideal choice for an application might be outdated, so design engineers must do their due diligence.
For example, the classic brushed motor
is generally only useful for low-end toys or products requiring little motion control. This type of motor is typically avoided in advanced applications. However, a recent design of a medical infusion pump shows that a modern brushed motor is an ideal choice to meet its performance objectives.
Given today’s advances, it’s no longer appropriate to associate one type of motor with a specific application. Motors come with deceptively simple electrical schematics that rarely exemplify their full features and capabilities. Unfortunately, motor family trees are unreliable as shown in Figures 1 and 2 because they only focus
on the motor’s design and fail to include its applications.
Ensuring the ideal choice for an application means considering the motor’s features (including its efficiency, capacity, durability, and control capabilities) and its compatibility with other system components (such as the size, weight, and torque requirements). Additional factors such as maintenance needs, costeffectiveness, and regulatory or environmental considerations should be evaluated before deciding on a motor.
Traction motors differ significantly from industrial motors, including those with similar power ratings. Whereas industrial motors usually power equipment or machinery in enclosed spaces and within a rated or limited range of operating conditions, traction motors are designed for mobile applications.
Traction motors are critical for converting electrical energy into mechanical energy to propel an application (such as an electric vehicle) forward.
For this reason, they require efficient power conversion, including:
• High torque for start-up acceleration
• Low speed for the general operation
• Low torque for high-speed cruising and frequent starts/stops
• The capacity and reliability for a range of operations, particularly in terms of speed (Figure 3)
Overall, traction motors must withstand a high rate of acceleration and
deceleration, with variations in speed and torque.
In most installations, traction motors also lead a “hard life” with respect to shock and vibration, temperature extremes, exposure to dirt and debris, and start /stop operation. They can span tens to several thousand horsepower (roughly ten to several thousand kilowatts). The lowest value might be for an electric forklift truck, which only operates at low speeds and where acceleration is not an issue.
An EV and full-power railway locomotive require greater power. A typical electricvehicle traction motor is rated at around 200 kW. Of course, these higher power levels necessitate heavy electrical conductors, strong cable portions, and connectors that can endure.
As traction motors are used to provide propulsion, they’re commonly used in railway locomotives, including diesel-electric and overhead catenarypowered all-electric
locomotives, urban light-rail vehicles (LRVs or trams), and suburban LRVs.
Traction motors are also finding use as electric drives in heavy construction equipment. To power such heavy-duty equipment, these motors are similar to a diesel-electric locomotive with an onboard fuel tank and a fixed-speed diesel engine — driving a generator to power the various motors (Figure 4).
Most notably, traction motors have become a popular choice for use in hybrid and electric vehicles. In terms of EVs, traction motors offer several advantages. Since they’re designed for high efficiency, they can optimize the conversion of electrical energy from a vehicle’s battery into mechanical energy, maximizing its range and performance.
This has spurred R&D in mid-range traction motors and their driver circuits and components. For instance, traction motors can integrate with a vehicle’s control system (such as its sensors, motor controllers, and software algorithms) to ensure precise speed, torque, and power output control.
What’s more: traction motors can incorporate regenerative braking capabilities, allowing them to act as a generator during deceleration. This feature lets the motor recover and convert a portion of a vehicle’s kinetic energy back to electrical energy, which can be stored in the battery for later use.
In the early 20th century, when electric traction was first developed, DC and AC motors were tried and tested. DC motors were favored because they provided the necessary torque characteristic for railway operation and
Figure 2. Another family tree shows less detail but gives comparable attention to both AC- and DC-powered motors (Image: Monolithic Power Systems).were easier to control then.
For example, the first electric motor was the brushed DC motor. The brushes (springloaded contacts) press against an armature extension called the commutator (Figure 5). As the magnetic fields of the stator and commutator fields interact, the commutator rotates, and the brushes “switch” the current direction so the field reverses and continues to push the rotor.
The high current results in strong magnetic fields and high starting torque (turning force), so it’s well-suited for starting a heavy object like a train. Controlling the speed and torque over a wide range, however, is difficult and was done by manually switching resistors in and out, and in series and parallel, to match the applied current and current to the load, speed, and torque objectives.
By the ’80s, power electronics had significantly progressed, and three-phase AC motors became a more efficient alternative in most cases. They’re far simpler to construct, require no mechanical contacts (brushes) to wear or fail, and are lighter than DC motors of the same power output.
Today, AC motors can be processor controlled with sophisticated algorithms that improve performance, control adhesion and slippage, and offer several operational advantages. They’re also more reliable and easier to maintain than DC motors. For this reason, most new systems use AC-driven motors.
Although it should be noted that while AC became the preferred choice for decades), advances in electronics provide greater freedom of choice. AC was once easier to step
up and down from a primary power source, such as a generator at the power plant to the desired voltage for the transmission line. But the availability of high-performance solidstate devices, such as insulated bipolar gate transistors (IGBTs, which act as fast switching devices) and thyristors, makes it possible to step up and down DC effectively. For some applications, such as long-transmission lines, DC has advantages.
There are two types of AC motors: synchronous and asynchronous (induction) motors. The synchronous motor rotates by alternating the AC current applied to its windings. It rotates at
the same speed as its stator rotating magnetic field.
This is not the case with asynchronous motors, which operate at a speed slightly below the synchronous speed. This speed difference, known as slip, is necessary for the motor to generate an induced voltage and rotor current — creating the torque required for motor operation.
An advantage of the AC motor is that it requires zero brushes since there’s no electrical connection between the armature and the fields. The armature can also be made of steel laminations instead of the numerous windings required in other motors. These features make it more reliable and cost-effective than a DC-based commutator motor.
AC motors can be single or three-phase, with three-phase motors used in bulk or higher power-conversion applications. The threephase traction motor is controlled by feeding in three AC currents, which cause a machine to turn. The three phases are most easily provided by an inverter that supplies the three variable-voltage, variable-frequency (VVVF) inputs, with voltage and frequency variations electronically controlled and optimized.
The frequency of its supply determines the speed of a three-phase AC motor. At the same time, the power must be varied to
Figure 5. The classic DC-driven motor requires no electronics, as it self-communicates the current via the conductive brushes which alternate the current’s direction and thus reverse the magnetic field (Image: The Railway Technical Website).match the load and torque requirements. Modern electronics, such as the IGBT, make the asynchronous AC drive practical for applications, such as EVs (Figure 6).
Permanent magnet (PM) motors are electric motors that use magnets in the rotor instead of electromagnets. The interaction between the PMs and the electromagnetic field produced by the stator windings generates the required torque for motor operation.
The PM motor is a three-phase AC synchronous motor, where the typical squirrel cage construction is replaced by magnets fixed in the motor. It requires a complex control system, but it can be up to 25% smaller than conventional threephase motors with the same power rating. The PM design provides lower operating temperatures, so cooling requirements are simplified.
Some traction motors use PMs. For example, Tesla uses a combination of motors, including PMs, because the vehicle space is limited (Figure 7). A few of Europe’s 25 AGV high-speed train sets and LRV trams also rely on PM motors, such as those in France and Prague. The reduced size is particularly attractive in low-floor LRVs where hub motors can be combined in a compact bogie.
With few exceptions, a traction motor is mounted on or in part of the wheel axle that it’s driving. It’s typically a direct-drive system with minimal or no intervening gearing. This means a reduced parts count in an application. A traction motor’s low weight and small size are also advantages.
In most locomotives, there’s only one motor per axle on the train bogie (the bogie or “truck” is the chassis or framework that carries a wheelset). One of the challenges in railroad design involves offsetting the weight of the motor on the un-sprung wheel axles and placing it on the sprung part of the bogie for better balancing and handling (Figure 8). For lighter-service engines, only one axle is powered.
In other applications, one motor powers both axles of the bogie, referred to as a mono-motor bogie. The ideal design depends on the vehicle size, weight restrictions, required speed, and other factors.
Controllers or inverters play a critical role in controlling the operation of a traction motor, which is responsible for driving a vehicle’s wheels or propulsion system. Most are custom designed to meet application characteristics and ensure optimal performance. Take an electric vehicle, for instance, where a percentage point or two in efficiency is critical due to cooling needs and range objectives. However, there are certain standard power and controller units for traction motors, depending on the make. CurtissWright recently introduced 100-800 VDC input/420-kW (at 700 VDC) inverters for single-motor (CWTI-S420) or dual-motor
Figure 6. The modern 3-phase AC motor is controlled by three variable-voltage, variable-frequency (VVVF) inputs; while complicated, it offers many operational benefits (Image: The Railway Technical Website).(CWTI-D420) applications in electric busses, hybrid vehicles, and dieselelectric off-road vehicles (Figure 9).
For flexibility, both models can feed power to a range of motor technologies, including AC induction, PM motors, and interior permanent-magnet (IPM) types. IPMs incorporate permanent magnets within the rotor core, which creates a magnetic field that interacts with the stator windings to generate torque for motor operation.
According to Curtiss-Wright, its advanced motor-control software runs adaptive tuning to get two percent higher levels of efficiency between the inverter and motor. These traction inverters offer shortcircuit and fault protection, as current and temperature are measured directly on the IGBTs. The inverters also use vehicle-grade components certified to AEC Q-100, 101, and 200 standards, adhering to ISO 26262 — an international safety standard for developing electrical and electronic systems in vehicles.
Figure
inverter (dimensions shown are in millimeters) can deliver up to 420-kW from 700 VDC inverters electric busses, hybrid vehicles, and diesel-electric off-road vehicles; it embeds advanced algorithms to optimally drive different traction-motor types with high efficiency and safety (Image: Curtiss-Wright Corp.).
Traction motors are an important class of electric motors optimized for high torque at start-up and low speed. They can power small movers such as forklifts and large systems such as all-electric locomotives and EVs.
With the increased development of consumer electric vehicles, there are several advances in motor performance and design. Modern electronics have made the older brushed DC motor less attractive, replacing them with AC-based motors using IGBTs for power switching under processor control. The ideal choice depends on the application space, design, power requirements, and overall project budget.
DEMAND for electric vehicles is amping up. Every one of these vehicles needs large batteries, and the industry is responding by building plants. Energy.gov forecasts that by 2030 electric vehicle battery manufacturing capacity in North America will grow 20 times, eventually supporting 10-13 million electric vehicles per year. Testing those batteries is a critical part of battery production. The first reason for testing is for safety. Due to a chemistry that supports runaway thermal events and sustains fire, Lithium-ion (Li-ion) batteries are dangerous. After exposure to vibration and high ambient temperatures, even small manufacturing anomalies can lead to catastrophic failure. Recently, Li-ion scooter batteries have been blamed for devastating building fires, and Jaguar Land Rover issued a recall of more than 6000 vehicles after eight customer fires were caused by battery thermal events. Additionally, buyers want to know exactly how far they can
drive on a charge. Battery testing can simulate the load placed on a battery during driving conditions and predict a vehicle’s driving range.
While battery volume is rising, testing is becoming more challenging. As vehicle buyers demand more storage for greater range, the capacity of batteries is increasing. What’s more, pulse testing requires exponentially more current than the battery’s ampere-hour rating. Given all this current, safety becomes paramount. Fire is a real risk caused by voltage or current exceeding the limits of the battery cells’ internal structures during charging or discharging.
For example, if a technician forgets to set a voltage limit during a constant current discharge, then the temperature of a battery cell could rise from 23 to 400 degrees Celsius in milliseconds. Catastrophic explosions are also possible. In fact,
Battery testing enables vehicle manufactures, owners, and researchers to make informed decision, optimize vehicle performance, and enhance overall user experience.
Russ Gaubatz, EA Elektro-Automatic
some manufacturers have built explosion-proof rooms for their automotive battery testing.
Add to high power the need for throughput — testing multiple batteries at the same time — and the battery automated test equipment (ATE) must be capable of sinking and sourcing many kWs of power. In some facilities, there isn’t enough space on the production floor to add multiple racks of the power supplies used in the test system.
Higher voltages are another challenge for testing. To reduce the weight of conductors in the vehicle and to reduce heat caused by electrical resistance, vehicle drivetrain voltages have climbed to 450 V and now are in the 800 V range. While test engineers can add more power supplies to increase the power of their test systems, they cannot change the maximum voltage rating of their test systems. Current EV modules require testing at up to 900 V.
Figure 1. An ATE system for battery testing includes bidirectional power supplies, a controller, safe connectors, CAN Bus, an industrial PC, software, a software environmental chamber, and a chiller. The main production-line tests for battery manufacturers include:
• Battery cycle test
• Drive cycle simulations
• Insulation resistance
• DCIR testing
To perform these tests, test systems use multiple bidirectional power supplies in parallel. A DC bidirectional power supply operates in quadrants I and II, meaning it is capable of both sourcing and sinking DC power.
It is not unusual for engineers to be confused when selecting a power supply system. Looking at the batteries they expect to test, they think they need a 30-kW system. But they forget the formula P=IV, which says at 1500 V the highest current a 30-kW power supply can output will be 20 A. If the test engineer needs the power supply to output more current, say 60 A, then they need to lower the voltage or buy a test system offering 90 kW.
In conventional bidirectional power supplies, two operating ranges are supplied, a high and a low. These are shown as rectangular boxes in Figure 2. As the test voltage rises or falls, a technician may need to stop the test and manually switch ranges on the power supply.
Some battery tests require a supply of constant power while varying current or resistance. A programmable power supply with a conventional rectangular output will supply maximum power only at the point of maximum current and maximum voltage. In contrast, some power supplies have a feature called auto-ranging. The power supply will automatically output more current when the load operates at
Figure 1. An ATE system for battery testing includes bidirectional power supplies, a controller, safe connectors, CAN Bus, an industrial PC, software, a software environmental chamber, and a chiller.
a lower voltage. This allows the power supply to maintain a constant power load across that load’s full power operating range.
The red line in Figure 2 shows the output of a true auto-ranging power supply. Without switching ranges, the power supply can output from 500 V to 166.6 V while maintaining 5 kW of constant power. Without this feature, the wattage of the power supply must be oversized, or double the number of power supplies will be required, and therefore the test system will be more costly.
Figure 2: Output of a true auto-ranging power supply
As the power levels in batteries rise, one of the challenges is testing across increasingly wide ranges of power and voltage. In the plant’s research lab, technicians may test individual cells at 2.5 to 4.2 V, test modules at 420 V, and test complete automotive battery packs at 840 V. True auto-ranging helps engineers test from system level all the way down to cell level using one power supply system.
Slew rate is an important consideration for automotive battery drive-cycle or pulse-test testing, during which the output voltage or output current changes frequently. The slew rate is the speed at which an output changes from its current state to its programmed state.
The faster the slew rate, the squarer the pulses in the output, which allows for more precise testing. The consequence of this is that power supplies with a slow slew rate cannot accurately measure the driving distance of a battery. If the test system has a fast slew rate, the more accurate test may result in publishing a longer driving range, which is supremely important to consumers.
During production testing, the battery management system (BMS) reports measurements to the test system. Temperature, current, and voltage are recorded about once a second. The purpose of production testing is to validate key parameters, once a second is sufficient.
Battery research, on the other hand, requires more complex testing. Engineers need to verify that the BMS is reporting accurately, understand the health of individual cells, and check the connections between components. On a vibration table, an intermittent event resulting from a broken connection may last only a millisecond. If the data acquisition speed is too slow, then testing may miss such events.
Slow data acquisition speed may also introduce imprecision. This can show up when testing identical batteries with a drive profile test. The result for the first battery may be 400 miles, and the result for the second battery may be 405 miles. Actually, the driving ranges are essentially
identical, but a slow data acquisition rate limits the accuracy of the testing. This can happen when a company buys a test system made for production and uses it in the lab.
Figure 3. Considerations for battery test systems include how much space is available on the production floor. Some systems, like the EA 10300 Series from EA Elektro-Automatik shown here, use SiC technology to offer a power-dense 300 kW in a single rack.
The above considerations will help engineers prepare for a future where automotive batteries are a dominant aspect of automotive manufacturing. According to EYs Mobility Consumer Index, more than 50% of people planning to buy a car will choose either a fully electric, plug-in hybrid, or hybrid vehicle. Fast, accurate, and economical battery testing is necessary to anticipate consumer demand
Jami Brownlee jbrownlee@wtwhmedia.com 224.760.1055
Jim Dempsey jdempsey@wtwhmedia.com 216.387.1916
Mike Francesconi mfrancesconi@wtwhmedia.com 630.488.9029
Courtney Nagle cseel@wtwhmedia.com 440.523.1685
Jim Powers jpowers@wtwhmedia.com 312.925.7793
LEADERSHIP
Publisher Mike Emich memich@wtwhmedia.com 508.446.1823
Managing Director Scott McCafferty smccafferty@wtwhmedia.com 310.279.3844
EVP Marshall Matheson mmatheson@wtwhmedia.com
• Dual Voltage ranges that support over voltage testing on 480V based systems
• Instrument Setups for quickly re-establishing the known instrument state
• 500uS time resolution for Transients
• Virtual Panels control software included
• Non-Linear current waveform programming during Load mode
• Phase coordination among multiple units (LKM/LKS)
• Powerful set of analog controls for PHIL and Modulation tests
• Trigger In & Out to permit extensive coordination with external systems
• Extensive Onboard diagnostics
• Digital I/O, including RS232, USB, Ethernet (GPIB optional)
• Intuitive 5” color display for ease of navigation
• Auto-paralleling for maximum flexibility with multi-chassis configurations
• Separate terminal blocks for single phase and 3 phase outputs
Gas-filled contactors for reliable disconnection of high DC voltages
The HVC series by TDK has been designed to meet the requirements of high voltage DC disconnection applications. The hermetically sealed design based on our gas filled technology experience exhibits excellent reliability in harsh environments. The HVC series are made for fast and reliable switching.
Applications
• DC fast charging stations
• EV traction Battery Disconnect Units (BDU)
• Electrical energy storage systems (ESS)