
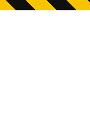
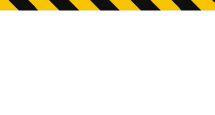
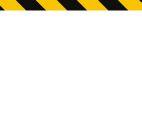


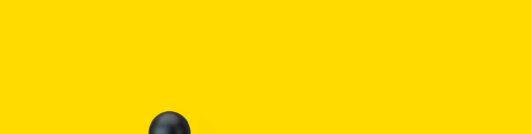





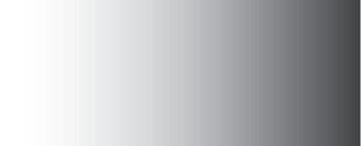
CLICK PLUS PLCs provide the same simple, practical control the CLICK PLC line is known for but with some surprising bells and whistles. Data logging, Wi-Fi connect-ability, MQTT communication, and increased security measures are just a few of the impressive features offered with the CLICK PLUS PLC series.
Using the same FREE streamlined PLC programming software as its predecessor, CLICK PLUS PLCs provide straightforward, no-learning-curve programming. Combine that with a starting at price of just $97.00 and the CLICK PLUS PLC is undoubtedly the unmatched value leader!
For custom stand-alone PLC I/O con gurations that exactly match your application (option module sold separately).
Use any CPU with option module(s) as a complete PLC for small systems or expand the I/O with stackable I/O modules for larger applications.
Starting at $509.00 (FMX11-CA11DS06)
Endress+Hauser submersible level sensors provide continuous liquid level measurement by sensing the hydrostatic pressure produced by the height of liquid above the sensor, providing a 4-20 mA output signal compatible with PLCs, panel meters, data loggers, and other electronic equipment.
• Up to 2 bar (66.9 ftWC) sensing range
• Rugged 316 stainless steel construction
• NSF Certified models for drinking water applications
• Models with FM hazardous location approvals for intrinsically safe applications
Starting at $221.00 (FTI26-CA4MWDG)
Endress+Hauser capacitance level switches are contact sensors that provide pointlevel detection of powders, fine-grained bulk solids, or water-based conductive liquids.
• IO-Link communication output options
• Select models are marked with the 3-A symbol for food and beverage industry hygienic applications
• Select models have hazardous location ratings
Starting at $13.00 (FLS-VM-100)
Level sensors monitor the level of liquids, pellets,
Level sensors monitor the level of liquids, pellets, powders, and other similar products in tanks and process systems.
• Ultrasonic level sensors
• Float, capacitance, and vibration level switches
• Rotating paddle level switches
• Guided wave radar level sensors
• Differential pressure level transmitters
Starting at $22.00
Starting at $22.00 (THMJ-B01L06-01)
• Optris infrared pyrometers
sensors accurate and reliable feedback for temperature control and monitoring
Temperature sensors provide accurate and reliable feedback for temperature control and monitoring applications.
• Temperature switches and transmitters
• Digital temperature switches/transmitters
Starting at $73.00
• Thermocouples, RTDs, and thermowells
Starting at $73.00 (FG1W-100PP-28)
Flow measurement devices monitor media and reliable flow indication, detection, or measurement.
• Mechatronic flow switches and transmitters
• Magnetic-inductive flow meters
• Thermal and vortex flow sensors
• Variable area mechanical flow meters
Starting at $87.00 (QPSL-AP-42)
Flow measurement devices monitor liquid media and provide reliable flow indication, detection, or measurement.
Pressure sensors measure pressure at a specific point in the process and transmit the measured value or trip point to a control device.
• Pressure switches and transmitters
• Digital pressure switches/transmitters
• Differential pressure transmitters
• Winters pressure accessories: siphons, snubbers, and isolation needle valves
Conditioners
Starting at $253.00 (SCU-2502)
isolate input from a wide variety of
ProSense frequency signal conditioners are extremely versatile, affordable, and will convert, transmit, scale, and isolate input signals from a wide variety of process sensors and controller I/O.
• SCU-2200 universal analog-to-frequency converters
• SCU-2501 universal frequency transmitter with analog and relay outputs
• SCU-2502 universal frequency transmitter with (2) relay outputs
• SCU-2503 universal frequency transmitter with analog and frequency outputs
EtherCAT P integrates EtherCAT communication with system and peripheral voltage supply in one 4-wire standard Ethernet cable. The I/O system for EtherCAT P with IP67 protection takes full advantage of One Cable Automation: material and installation costs, as well as the required installation space in drag chains, cable trays and control cabinets are significantly reduced. The compact and robust I/O modules cover a wide signal range, from standard digital I/Os to complex analog signals and measurement technology. More than 100 additional EtherCAT P components are available. Find out more now!
• Why companies need to stop postponing Industry 4.0 transformation: Tom Kelly, Automation Alley
• A Euro view: Collaboration on industry 4.0: Chantelle Kiernan, IDA Ireland
• Scaling Industry 4.0 transformation for the future: Chris Vavra, Control Engineering
• Strategies, considerations for successful Industry 4.0 implementation: Alan Raveling, Dan Riley, Interstates
supply chain
| Sustainable machine design offers real-world benefits 39 | Equipment-as-a-service (EaaS) advantages
18 | COVER: It’s been a dozen years since the I4.0 initiative began. Industry 4.0 expert Jeff Winter asks: “What are your I4.0/smart manufacturing goals, and how’s your progress?” Images courtesy: Jeff Winter, Hitachi Solutions
• Collaborate, improve resilience in an industrial automation supply chain: Sara Cattaneo, ABB From the digital edition click the following headlines or search at www.controleng.com
• Smart manufacturing’s impact: Is it moving fast enough? John Clemons, Rockwell Automation
• How to create PLC ladder logic code with Excel: Mark Magnusen, Applied Control Engineering (ACE)
• PLC programming language fundamentals for improved, operations, maintenance: Frank Lamb, Automation LLC
1) How does your company compare to its competitors?
2) How are you doing against your own Industry 4.0 goals?
44 | New Products for Engineers – See more products in every issue.
Control Engineering offers more products in the print and digital edition in 2023 than in prior years because subscribers said new product coverage was important: Liquid turbine flowmeter, single-axis robot, PLC line with new CPU, IIoT-ready communications, machine circuit board, electromagnetic flowmeter, compact industrial Ethernet switches, thermal imaging sensor, motor controller, power rectifier, conductive fluid flowmeter.
See more products online. www.controleng.com/products
47 | Back to Basics: Optimizing production processes with radar technology
Industrial Cybersecurity Pulse
• Advice for end users securing connected OT, CISA’s push for OT secure by default, Bot attacks on ICS
CE Mechatronics & Motion Control Newsletter
• Innovation at Its Finest: Introducing the 2023 Control Engineering Product of the Year Winners
IIoT Process Control & Automation Newsletter
• Profinet benefits for Industry 4.0, Turning data into information for better context,
• Multi-cloud optimization market expected to quadruple by 2032
Stay ahead. Subscribe. www.controleng.com/newsletters
u Global System Integrator Report (GSIR)
Next edition deadlines are July 31 for articles, Sept. 8 for System Integrator of the Year, Sept. 1 for System Integrator Giants. Contact: kparker@cfemedia.com; cvavra@cfemedia.com. www.controleng.com/GSIR
u Control Engineering eBook series, now available: Summer Edition
Motors and Drives
Motors and drives make manufacturing plants run and keep them efficient. Maintaining motors and drives and keeping them cost-effective is crucial and requires knowledge. Increase your knowledge with this 89-page eBook.
Applying Industrial Analytics
When applying industrial analytics, those involved in manufacturing applications can improve sustainability with advanced analytics applications. Resources in this 58-page eBook help apply data analytics to industrial environments and look at Big Data analysis versus data acquisition tools. Learn more at: www.controleng.com/ebooks
u Control Engineering digital edition
The tablet and digital editions provide links to other related, useful resources. Click on headlines to see online version with more text and often more images and graphics.
www.controleng.com/ magazine
by MSA Safety
Are you looking to optimize energy efficiency and comply with government mandates while supporting ESG goals? Download our white paper, “Energy Efficiency: Using Cloud Connectivity to Take Control of Energy Consumption,” and discover how to transform building performance while aligning with ESG principles.
Buildings account for a substantial 40% of total energy consumption, making energy efficiency a critical focus for sustainable business practices. Our white paper provides a comprehensive guide on implementing an ESG-focused action plan that leverages advanced technologies to reduce energy usage and drive cost savings. By embracing ESG principles, you not only enhance energy efficiency but also contribute to a greener and socially responsible future.
The white paper explores the vital strategy of metering, enabling you to measure and collect data on energy usage at various levels. This empowers you to identify Energy Saving Opportunities (ESOs) and engage in energy-saving initiatives, supporting the social aspect of ESG by promoting sustainability and responsible resource management.
Connectivity is essential in optimizing energy efficiency while adhering to ESG principles. With cloud-enabled connected devices, you gain centralized control and remote management capabilities, allowing you to monitor and control energy-related devices seamlessly.
This connectivity provides holistic insights into energy consumption, empowering you to make informed decisions that align with ESG goals.
Learn how to maximize savings, enhance energy performance, and contribute to a sustainable future while aligning with ESG standards. MSA Safety can assist to get your energy data into the right format or environment that will aid your energy efficiency program.
SCAN CODE AT RIGHT FOR SMARTPHONE ACCESS
Take the first step towards transforming building energy performance and supporting ESG commitments by downloading this white paper today: us.msasafety.com/fieldserver-energy-efficiency
fgfd@msasafety.com msasafety.com/fieldserver
u The Control System Integrators Association (CSIA) recently installed a new board of directors at its 2023 Town Hall Meeting, held at CSIA’s Executive Conference in New Orleans. The updates were affirmed via a quorum.
The new Board of Directors is:
• Board Chair — Karen Griffin, PE, Hargrove Controls & Automation (2023-2025)
• Past Chair — Adrian Fahey, SAGE Group
• Treasurer — Daren Dieleman, Interstates Inc.
• Director — Ray Brown, ESCO Automation
• Director — Stephen Malyszko, Malisko Engineering
• Director — Frank Riordan, DMC Inc.
• Director — Greg Young, Automation NTH
• Director — Wright Sullivan, A&E Engineering
“I am incredibly excited to help lead CSIA as board chair and proud to be the first woman to hold this position,” said Griffin. “The future looks challenging but bright for system integration, and I am honored to have a hand in leading the industry into it.” Since June 2019, Griffin has served as vice president at Hargrove Controls + Automation, based in Mobile, Ala. She takes over the position of board chair from Adrian Fahey, who will now assume the role of past chair. Stepping into Griffin’s former role of treasurer is Daren Dieleman.
New to the board this year is Wright Sullivan of A&E Engineering, a system integrator headquartered in Greer, South Carolina. “Having been involved with CSIA for many years, I am delighted to join its board of directors,” Sullivan said. “After a successful 2023 Executive Conference, I am already looking forward to next year’s event in Dallas.” ce
– Edited from a CSIA press release by CFE Media and Technology. CSIA is a CFE Media and Technology content partner.
u HOT TOPICS in Control Engineering, for articles posted at www.controleng.com from January through June 2023, are:
1. Manufacturer opens packaging and logistics headquarters
2. Six industrial robotics trends for 2023
3. PID loop tuning parameters and control fundamentals
4. Eight frequently-neglected VFD parameters to optimize
5. Analysis: Ability to delay Microsoft DCOM hardening patch ends as of March 2023
6. Control Engineering Career and Salary Survey, 2023,
7. 2023 Control Engineering Product of the Year winners announced
8. Taking control of your control system
9. How to create PLC ladder logic code with Excel
10. Controllers, interfaces provide advanced edge computing capabilities.
Chris Vavra, web content manager, Control Engineering, cvavra@cfemedia.com
u DESPITE years of development, truly autonomous technologies such as self-driving vehicles and delivery drones continue to remain elusive due to safety and reliability concerns.
However, thanks to advances in artificial intelligence (AI), neural networks, a type of machine learning (ML) algorithm, have become an indispensable component of modern autonomous systems, especially in their perception capabilities. In autonomous vehicles, neural networks use data from sensors to map the environment and recognize objects such as traffic signs.
Xiangru Xu, an assistant professor of mechanical engineering at University of Wisconsin-Madison, is using his National Science Foundation CAREER Award to establish a theoretical framework and design control algorithms to ensure the safety of autonomous systems with machine learning components. He is focused on safety-critical systems in which any safety failure will break the product or cause human injury.
MEMBERS of the UW Autonomous & Resilient Controls Laboratory (ARC Lab), directed by Assistant Professor Xiangru Xu, test a drone. Courtesy: Joel Hallberg, University of Wisconsin-Madison
“Surveys show that the American public is very skepticalof autonomous systems,” Xu said. “But, in the future, if there were a self-driving car that came with provable performance guarantees for safe and reliable operation on our streets, it could boost the public’s trust, which is a very important factor in determining the role of autonomous systems in our future society.”
He says there are many fundamental problems in machine learning that he will need to consider as he designs control algorithms. For one, neural networks are very sensitive, so there’s a risk that a small change to the input can lead to an incorrect result for image recognition. If there’s a random sticker affixed to a stop sign, that small alteration could cause a neural network to mistake the sign for something else, potentially causing a self-driving vehicle to miss it entirely. Xu is leveraging his expertise in control theory to tackle this challenge.
“Ultimately, I expect to be able to provide insight on how to design better autonomous systems.”
Adam Malecek, University of Wisconsin-Madison
ce
Travis Giebler and Hayden Serio | LifecycleIQ Services by Rockwell Automation
For many industrial manufacturers, time is running out to digitally transform and update or migrate their legacy distributed control systems (DCSs). Just the thought of a migration makes manufacturers cringe but taking a wait-and-see approach is no longer a viable option. The shelf life on these once stalwart systems is expiring. Installed or updated in the late 80s and 90s, these systems are overwhelmingly fragmented and fraught with challenges. Manufacturers risk losing operational control of their processes.
Compound these issues with the lack of available resources to maintain or repair older equipment and the potential for cybersecurity attacks, safety and environmental risks increase.
Manufacturers must change to keep pace with ever-evolving technology and consumer demands; otherwise, they risk becoming uncompetitive in their markets.
Opportunity abounds for those who want improved asset utilization, access to real-time data, improved control and enhanced connectivity. Manufacturers need to reevaluate existing operations and leverage the new technology found in a modern-day process control system infrastructure.
Today ’s innovative technologies deliver the promise of greater interconnectivity and system visibility across the enterprise. The ease of system access and the ability for personnel to capture data helps improve operational efficiency and performance. Consider the following features and functions where a new and improved DCS can make a competitive impact now and in the future.
CLICK to download the paper now. rok.auto/lifecycle
The mobile robot component market as a whole has been growing in the last several years and is projected to continue to do so. A recent report by Interact Analysis indicates the market will have a projected value of $7.4 billion by 2027 with a compound annual growth rate (CAGR) of almost 45% over the next five years and will positively impact the manufacturing and non-manufacturing market.
Brianna Jackson, a market research analyst for Interact Analysis, who was involved in conducting the survey, discussed some of the findings from the report and where she sees the market heading in the next several years in a video interview.
The impact is being felt in other regions, as well, and the report indicated China is help spur the industry’s growth along with the Asia-Pacific region as a whole. The U.S. continues to have a majority of the revenues, but other areas are catching up. Jackson said some of that is due to the United States putting less emphasis on building new warehouses and facilities were mobile robots might be needed. Companies like Amazon, she said, are working with what they have in the United States rather than what they need.
Jackson described mobile robot components as all the organs that go into the robot. “We’re talking about drives, the motors, the gearboxes, as well as the batteries and the charging stations that are going to supply energy into the battery. Also the sensors that give the robot information on where they are in their environment.”
All of these components are in high demand right now and the market has picked up, Jackson said, thanks in part to the COVID-19 pandemic.
“The growth of e-commerce as a result of the COVID-19 pandemic has been a major boost in the adoption of mobile robots,” she said. “Also, we saw constraints placed on the labor market, which because of labor shortage as well as the cost of labor, has been a driver for industrial automation. But not just in the warehousing and logistics sector, but also in the manufacturing sector.”
“You kind of have the opposite happening in China and the AsiaPacific region as a whole because you have India building warehouses at a rapid rate, as well. You have companies building partnerships with mobile robot providers in the same way Amazon has done,” she said.
The mobile robot market looks bright, and the component market will benefit, Jackson said. With growth comes maturity and consolidation among some suppliers.
“We see bigger industrial players that are going to provide whole system solutions to mobile robot manufacturers and that was expected as the use business scaled up.” ce
-Chris Vavra, web content manager, Control Engineering, CFE Media and Technology, cvavra@cfemedia.com.
The Bundy Group reported 15 automation transactions in the month of June. Thus far, the group has reported 76 transactions during 2023. Courtesy: Bundy Group
SPRING 2023 is continuing to show strength and consistency in terms of mergers and acquisitions and capital placement activity in the automation market. Companies that were recently involved in transactions had such capabilities as control system integration, artificial intelligence, automation products distribution, and manufacturers of custom motion control solutions.
Transactions to note through spring 2023 include Ametek’s acquisition of Bison Gear, Durr Group’s acquisition of BBS Automation, Blackford Capital’s acquisition of PACIV, Motion & Control Enterprises (MCE) simultaneous acquisition of Power & Pumps and Industrial Control Services, and Parkway Venture Capital’s investment in Figure. This list of buyers and investors highlights the attractiveness of the automation market.
Bundy Group’s current engagements and owner relationships include control system integration, automated material handling, automation distribution, artificial intelligence, and cybersecurity. This serves as a leading indicator for submarkets our team anticipates closed transactions in over the coming months. ce
Bundy Group is a CFE Media and Technology content partner and reports on mergers and acquisitions for Control Engineering, Plant Engineering and Industrial Cybersecurity Pulse
uEvan van Hook, the chief sustainability officer for Honeywell, said he speaks on sustainability topics once or twice a week.
“There’s a lot of discussion around it from a strategic perspective,” he said in his presentation, “Why Sustainable Transformation Must Start from Within” at Honeywell Users Group in Orlando. “Everyone these days have sustainability targets. Having initiatives and goals is a great thing.”
The challenge is maintaining it, van Hook said. Honeywell started its sustainability initiative in 2004, he said, well before sustainability hit the mainstream. Even then, van Hook said they were asking a question many companies ask.
“We tried to say, ‘How can we create an organization that creates sustainability? How do you take an organization and actually structure it so it creates this result over time?’”
He said it starts with creating an advanced software-industrial environment with a lean manufacturing culture and not just a series of activities.
“Customers want lower-emitting products,” van Hook said. “About 60% of R&D is being put into environmental and social products.”
Honeywell’s journey in sustainability as part of its core operating system helped, van Hook said, with:
• 93% less greenhouse gases since 2004.
• 70% better energy efficiency.
• A safety ratio of greater than 4x than industries Honeywell operates in.
• Around 6,300 sustainability projects enacted since 2004.
Honeywell has reduced greenhouse gas emissions by more than 90% since 2004 and have embarked in more than 6,000 sustainability projects. Courtesy: Chris Vavra, CFE
Media and Technology
“We started with 22 million metric tons, and we’re down to 1.7 million. If you build sustainability into your system, you can generate results wherever you want.” ce
Chris Vavra, web content manager, CFE Media and Technology, cvavra@cfemedia.com.
MANUFACTURERS embarking on a digital transformation journey need more than innovation and a willingness to begin. Those are important traits on display during the general sessions at Siemens Realize Live 2023 at Mandalay Bay in Las Vegas.
Jane Poynter is founder and co-CEO of Space Perspective, a company sending people to space in a balloon one person at a time. “We have a gentle way of going to space, and we want to make it fun,” she said. “We even have a space lounge.”
Easton LaChapelle, the co-founder and CEO of Unlimited Tomorrow, which makes prosthetic arms and limbs for people using a combination of advanced and additive manufacturing at affordable prices. LaChapelle, who started the company at 18, encouraged people to use curiosity as a tool. In his case, he said the idea started when a little girl saw his robotic arm that he had developed for a robotic fair and realized she had a prosthetic limb that cost $50,000.
“I realized right then I need to solve this,” he said. That’s true for a lot of engineers. They need to solve the problem by using skills in mechanical, electrical, coding or whatever to try to
Easton LaChapelle, the co-founder and CEO of Unlimited Tomorrow, is using digital transformation to help make prosthetic limbs at more affordable prices for people. Courtesy: Chris Vavra, CFE Media and Technology
make the world a better place. Digital transformation and Industry 4.0 offer enormous potential. Companies realize this daily, as the world accelerates and consumers want custom products yesterday.
Don Hnatyshin, senior vice president, chief supply chain officer, Molex, said in his keynote Wednesday his company is trying to move to the speed of the market. Supply chain issues are nothing new and many hidden problems were exposed during the COVID19 pandemic. The trick, he said, is to be agile, flexible and react to the situation as it arises and have tools to transition seamlessly.
Chris Vavra, web content manager, CFE Media and Technology, cvavra@cfemedia.com.
uThe 36th Honeywell Users Group (HUG) event in Orlando kicked off with an emphasis on manufacturers preparing for the future.
“The future is coming fast. The world is transforming, and all industries are transforming,” said Pramesh Maheshwari, president and CEO, Honeywell Process Solutions in his opening statement.
The digital future looks at what is and could be possible. “How can we shape those changes to achieve better outcomes, improve efficiency?” Maheshwari said. “The route to optimize transformation will vary.”
Jason Urso, chief technology officer at Honeywell, led a long discussion about how Honeywell is working to enable changes in its company and for customers.
“Our world is changing and the pace is faster than ever,” he said. He used the analogy of a car, and how it has changed with vehicles become smarter and alerting drivers to situations before they happen. “There’s a parallel in the industrial plant. Technology has made them more reliable and safer than ever before. Digitalization is changing everything we do in plant operations.”
Online controleng.com
XPlanar application for plasma surface treatment
Integrated logistics workcell
PixelPaint non-overspray technology for two-tone painting
CRB 1300 robot with speed and separation monitoring
How end-to-end programming augments, enhances plant floor operations
ARTICLES
Top 5 Control Engineering content: June 12-18, 2023
Machine learning tool accelerates polymer discovery
Framework advances computer vision with pixel processing
Unified environment for control system integration benefits
Pramesh
During a session with media, Maheshwari said customers are asking how things can be done faster and safer.
“It’s all about making workers safer, more productive and giving them more value,” he said.
Digitalization and digital transformation is at the heart of this and empowering them with the right tools, especially the workers who are taking over for millions of Baby Boomers who will be retiring by 2030.
AI-enabled approach helps make autonomous robots safe, reliable
MTP benefits for process automation equipment
Sept. 9-11, Pack Expo Las Vegas 2023, PMMI, https://packexpolasvegas.com
Sept. 26-28, Ignition Community Conference, Inductive Automation, https://inductiveautomation.com/resources/icc# Oct. 17-19, LNS Research: The Industrial Transformation Event
https://www.theixevent.com/s/ The-IX-Event-2023/home
Nov. 6-9, Automation Fair 2023, Boston
https://www.rockwellautomation.com/en-us/ company/events/in-person-events/automation-fair.html
“The new generation learns differently,” he said. “Their learning is so different. We need to adapt and give them the tools and technologies to make it engaging and relevant to them,” he said. “The world is changing. To optimize transformation, we must do it together,” he said.
The company introduced Digital Prime, a cloud-based digital twin for tracking, managing and testing process control changes and system modifications. Digital Prime is designed to allows users to test frequently for more accurate results while reducing reactive maintenance.
It offers quality control through an efficient and collaborative solution for managing changes, running factory acceptance tests and improving project execution and training without having to disrupt the production system. The platform can be used by companies in industries such as oil and gas, sheet manufacturing and chemicals to test modifications during planned shutdown periods, to reduce rework.
Most solutions require dedicated hardware, can be vulnerable to security breaches and do not stay current to match live operations. Digital Prime addresses these challenges by providing a “lab system as a service” that continually updates to reflect changes within the production environment, providing a dependable digital twin.
Digital Prime is a collaborative ecosystem with secure cloud-based connectivity, a virtual engineering platform and built-in security protection. Users can access the digital ecosystem through a subscription service using multi-factor authentication, enabling customers to standardize across the enterprise. It is expected to be available to customers in Q4 2023. ce
Chris Vavra, content manager, CFE Media and Technology, cvavra@cfemedia.com.
MUCH IS MADE about making technology better and more efficient, but the worker shouldn’t be forgotten in the development process.
“How do we improve human reliability to ensure the workplace is safe while providing optimum production?” asked Manas Dutta, general manager for workforce excellence growth initiative at Honeywell in his presentation “Advancing today’s workforce through digital twins, AI and VR,” with Ziad Kaakani, chief technology officer at HPS Lifecycle Solutions & Services at Honeywell. Dutta and Kaakani were among presenters at the 2023 Honeywell Users Group.
Five workforce challenges manufacturers face
The skills gap is nothing new, but this is compounded with a general talent drain. Many workers today are not prepared for the job they are asked to do. Making the human worker better, Dutta said, is an industry challenge for several reasons:
1. Workforce churn. Loss of knowledge accumulated with people leaving or retiring, which creates attrition.
2. Improving efficiency. Companies are asked to do more with less, and that’s not easy if they’re not properly trained.
speed up learning by emphasizing four key targets:
• Evaluate. The program gathers the worker’s skills through assessment tools to determine their operational performance.
• Train. The workforce is trained through the digital platform.
• Predict. The worker can then plan jobs through predictive insights.
• Assist. They can prepare and execute tasks with on-the-job assistance in case there are challenges that aren’t covered in the lesson plan. Dutta said they cover about 70 to 80% of what a worker will see in the facility.
Ziad Kaakani (left) and Manas Dutta during the “Advancing today’s workforce through digital twins, AI and VR” presentation at Honeywell Users Group (HUG) in Orlando. Courtesy: Chris Vavra, CFE Media and Technology
3. Jobs are evolving. The nature of the jobs and their requirements are often changing and demanding frequent upskill and reskilling.
4. Trying to attract and retain top talent. Younger workers don’t stay as long as their older workers, which can lead to knowledge and experience gaps.
5. Worker training. Traditional training methods such as giving an engineer a manual and expecting them to learn like older workers did is ineffective.
“The industrial sector is behind 20 to 30 years of adopting digital transformation and training,” Dutta said. “They do classroom lectures, and new workers don’t like it. They learn completely differently.”
Evaluate, train and develop workers with advanced technology
Dutta described Honeywell’s approach with their Workforce 360 product, which emphasizes providing the worker a digital environment to learn. The digital environment tools can help
Dutta said gamifying the process lets workers learn everything without being exposed to dangerous conditions.
“If you do it for real,” Dutta said, “they might make a mistake during their training that can create a serious problem for the facility and the worker. Virtual, hands-on training lets them learn faster without being exposed to hazardous conditions. Instead of taking two to three years to be considered competent at your job, virtual training can knock it down to anywhere from six to eight months.”
Customizing the workforce program, replicating the plant While a general program is set for the customer, it is designed to be customizable for any facility that might use it.
“The customer can customize the lessons,” Kaakani said. “It’s a continuous evaluation and the user gets a replica of the plant. It’s an environmental digital twin.”
The environmental digital twin is often done with a 3D computer-aided design (CAD) drawing that provides a mostly-accurate view of the plan. Dutta said it ranges from 80 to 90%. From there, photos are often taken of the spots that are missing to give the user an immersive look at the facility that can be done through virtual reality (VR) or on a laptop.
“Technology like this is enabling the workforce to do the job right the first time and every time,” Dutta said. See another graphic with this article online. ce
Chris Vavra, web content manager, CFE Media and Technology, cvavra@cfemedia.com.
uSiemens Realize Live event at Mandalay Bay in Las Vegas emphasized the importance of digital transformation and how it will change manufacturing. It’s more than creating new products, though: It’s the process and the journey in this growing digital world that matters most. Companies need to transform.
“Transformation is top of mind for every single one of our customers and we are here to help them on the digitalization journey,” said Brenda Discher, head of communication and senior vice president of business strategy and marketing for Siemens Digital Industries.
Discher said companies and customers are facing new challenges they didn’t have to consider before “Every customer we work with around the globe is going through incredible headwinds,” she said.
“It’s not just about making the best product anymore. Improving cost, cheaper, better quality.”
She said there are four challenges companies face now: Climate, COVID19, conflict and competition. More than these, Discher said, is clock speed. “How fast can I be a more resilient organization by adopting digitalization? Companies need to automate and quickly deliver a return on investment (ROI),” she said. Many software and hardware tools are available to make it happen, she said. “We’re about enabling customer in their industries to transform everything, including the industry they are in.”
Tony Hemmelgarn, president and CEO of Siemens Digital Industries Software,
CFE Media and Technology
emphasized how the company is emphasizing business transformation and “making it real. The drive to make products faster is relentless, and now more is being asked,” he said. “It’s about being sustainable and building a better product and it has to be an integral part of the process.” He said digitalization across the product lifecycle helps; 80% of a product’s environmental impact is determined at the concept phase. ce
Chris Vavra, web content manager, CFE Media and Technology, cvavra@cfemedia.com.
Archived version of the webcast “Edge series: Edge computing architectures, advantages” is online.
“EDGE COMPUTING architectures, advantages,” a May 25 Control Engineering webcast, examined edge computing architectures for automation and control applications. Webcast attendees had additional questions on edge computing, answered below. The webcast and information below also review resources and research on edge computing. See how system integrators and other experts consider it a means to advance, rather than replace, the benefits controls bring to many mission-critical industry applications. Architecture interactions among edge computing and cloud resources were discussed.
Expert presenters in the webcast are Alan Raveling, OT architect and cybersecurity leader, Interstates; and Aditya Agrawal, 5G CTO, L&T Technology Services. In an exit poll of webcast attendees, 100% of the audience attending live said the speakers helped them understand the edge computing topics covered.
In a webcast poll, audience members attending live were asked how they are using edge computing for automation, controls and instrumentation applications. Prompted replies showed supervisory control and data acquisition (SCADA) applications were the highest, followed by distributed control system or process applications and monitoring remote assets, then control processes, monitoring local assets, humanmachine interface and least use with analytics and decision support at 9%.
In related research of Control Engineering subscribers earlier this year on artificial intelligence and edge computing, SCADA also ranked highest in a similar question. Among subscribers responding, 98% were using edge computing in some way. The top three uses were control processes (51%), SCADA software (50%) and with human-machine interface software (46%): This is a three-way tie, considering margin of error for that research.
During the webcast, Raveling said line-based machines, along with connected input/output (I/O) devices, sensors, programmable logic con-
trollers (PLCs) and other control systems are the richest application data sources, require the quickest responses for applications and often have limited visibility to other lines and machines. Local data centers, central or distributed, can send fast actions to lines and machine and potentially serve as the staging area for cloud-based applications to provide added capabilities. Lessons learned, Raveling said, include ensuring the architecture and staff training can support industrial edge computing applications.
QUESTION: What is return on investment?
Agrawal: There is no fixed answer. Edge compute is typically part of the overall system and typically enterprises should look for ROI on the total cost of ownership, not just the edge compute component.
Q: Can edge compute lower latency?
Agrawal: Latency is the time duration between when the client device starts an action and when it receives a processed result. If a client device is sending packets and receiving a response back from the network that doesn’t require significant compute, then the latency is dominated by network latency, and it is easily measured by using the ping command. Typical LTE network latencies are ~25 to 50ms for wellprovisioned private networks. Wi-Fi latencies are in a similar range for lightly loaded Wi-Fi networks. 5G network latencies with Release 16 gear and ultra-low latency said to be close to 1ms. With significant compute applications, going to the cloud and back can add latency, perhaps hundreds of milliseconds, even seconds. With edge compute, latency can be reduced by an order of magnitude. ce
Edited by Mark T. Hoske, content manager and webcast moderator, Control Engineering, CFE Media and Technology, mhoske@cfemedia.com.
Alan Raveling, OT architect and cybersecurity leader, Interstates and Aditya Agrawal, 5G CTO, L&T Technology Services were expert speakers in the May 25 Control Engineering webcast, “Edge computing architectures, advantages.” Courtesy: Control Engineering webcasts
See 9 more answers with this article online.
controleng.com
KEYWORDS: Industrial edge computing
LEARNING OBJECTIVES
“Edge computing architectures, advantages,” a May 25 Control Engineering webcast explained how edge computing fits into automation and controls.
Discussed how edge computing can make cloud resources more effective and reviewed benefits, examples and lessons learned about edge computing as used with automation and controls. Additional audience questions are answered.
CONSIDER THIS
Have you done the right preparation to support an industrial edge computing architecture?
If you’re a system integrator with demonstrable industry success, Control Engineering and Plant Engineering urge you to enter the 2024 System Integrator of the Year competition. Past System Integrator of the Year winners—Class of 2023, Class of 2022, and Class of 2021—are not eligible to enter the 2024 System Integrator of the Year program.
The chosen System Integrator of the Year winners will receive worldwide recognition from Control Engineering and Plant Engineering. The winners also will be featured as the cover story of the Global System Integrator Report, distributed in December 2023.
Control Engineering and Plant Engineering’s panel of judges will conscientiously evaluate all entries. Three general criteria will be considered for the selection of the System Integrator of the Year:
• Business skills
• Technical competence
• Customer satisfaction
3010 Highland Parkway, Suite 310, Downers Grove, IL 60515. 630-571-4070, Fax 630-214-4504
Content Specialists/Editorial
Mark T. Hoske, Content Manager
630-571-4070, x2227, MHoske@CFEMedia.com
David Miller, Content Manager, 312-481-5068, DMiller@CFEMedia.com
Emily Guenther, Director of Interactive Media 630-571-4070, x2229, eguenther@CFEMedia.com
Amanda Pelliccione, Director of Research 978-302-3463, APelliccione@CFEMedia.com
Gary Cohen, Senior Editor GCohen@CFEMedia.com
Chris Vavra, Web Content Manager CVavra@CFEMedia.com
Contributing Content Specialists
Suzanne Gill, Control Engineering Europe suzanne.gill@imlgroup.co.uk
Agata Abramczyk, Control Engineering Poland agata.abramczyk@trademedia.pl
Lukáš Smelík, Control Engineering Czech Republic lukas.smelik@trademedia.cz
Aileen Jin, Control Engineering China aileenjin@cechina.cn
Editorial Advisory Board
www.controleng.com/EAB
Doug Bell, president, InterConnecting Automation, www.interconnectingautomation.com
David Bishop, chairman and a founder Matrix Technologies, www.matrixti.com
Daniel E. Capano, senior project manager, Gannett Fleming Engineers and Architects, www.gannettfleming.com
Frank Lamb, founder and owner Automation Consulting LLC, www.automationllc.com
Joe Martin, president and founder Martin Control Systems, www.martincsi.com
Rick Pierro, president and co-founder Superior Controls, www.superiorcontrols.com Mark Voigtmann, partner, automation practice lead Faegre Baker Daniels, www.FaegreBD.com
CFE Media and Technology Contributor Guidelines Overview
Content For Engineers. That’s what CFE Media stands for, and what CFE Media is all about – engineers sharing with their peers. We welcome content submissions for all interested parties in engineering. We will use those materials online, on our website, in print and in newsletters to keep engineers informed about the products, solutions and industry trends. www.controleng.com/contribute explains how to submit press releases, products, images, feature articles, case studies, white papers, and other media.
* Content should focus on helping engineers solve problems. Articles that are commercial or are critical of other products or organizations will be rejected. (Technology discussions and comparative tables may be accepted if non-promotional and if contributor corroborates information with sources cited.)
* If the content meets criteria noted in guidelines, expect to see it first on our Websites. Content for our e-newsletters comes from content already available on our Websites. All content for print also will be online. All content that appears in our print magazines will appear as space permits, and we will indicate in print if more content from that article is available online.
* Deadlines for feature articles for the print magazines are at least two months in advance of the publication date. It is best to discuss all feature articles with the appropriate content manager prior to submission.
Learn more at: www.controleng.com/contribute
Consider site tours to broaden understanding of automation and control applications and optimize implementations.
When traveling, think again about asking for a site tour. Tours are fun and educational, and hosts often are pleased to show their applications. Notes follow from tours of Lift, operated by the American Lightweight Materials Manufacturing Innovation Institute (ALMMII), and of Freedman Seating Co. and the co-located Jane Addams Resource Corp. training facility. With related online articles, see more details and 23 photos.
Advanced manufacturing techniques are advancing and on display at Lift in Detroit. Lift is operated by the American Lightweight Materials Manufacturing Innovation Institute (ALMMII). Lift is a public-private partnership among the U.S. Department of Defense, industry and academia, and it is part of the national network of manufacturing innovation institutes. Lift works with Detroit schools to provide training and certifications in welding, robotic welding, computer numerical control (CNC), industrial technology maintenance, machining, metrology, robotics and other areas.
Siemens experts gave the Lift tour during the April Manufacturing in America event in Detroit, covering topics such as digital threads, digital twins, simulation, automation, controls, design, maintenance and industrial machinery. Demonstrations included Siemens-enabled cybersecurity that uses security, orchestration, automation and response (SOAR) methods to detect and respond to anomalies in less than 1 second. Software demonstrated how a simulated redesign of a 1991 Mazda Miata part could optimize design, keeping strength and lowering weight by 30%. Manufacturing process simulation software helped find an interference point between two welding robots, using virtual commissioning to save an estimated 40% time.
FOREGROUND, Tom Hoffman, Siemens Digital Industries Software, explains time and cost savings of digital design and virtual commissioning at the Lift manufacturing innovation institute in Detroit. Courtesy: Mark T. Hoske, Control Engineering
CNC, robots, industrial training Freedman Seating Co. offered tours in association with the Jane Addams Resource Corp. (JARC) Women in Manufacturing event, in March. While automated welding is used, manual welding also is needed. Welding, safety and CNC are among training certifications JARC offers in its training facility co-located at Freedman Seating Co.
Karen Arroyave, M.E., a Freedman Seating manufacturing engineer, gave the Freedman tour. CNC programs are used for cutting fabric and fabricating and forming and tube welding. Vectis Automation provided two automated welding cells that work on mass transit seat bases using Universal Robots’ collaborative robots, wrapped for the application.
The JARC manufacturing training tour included four welding booths, two CNC machines and a 3D printer that help teach manufacturing skills. JARC also provides a wide range of manufacturing-related certifications, life skills, career training and job placement at no cost to participants. ce
Jeff Winter, Hitachi Solutions
2023 marks a dozen years of Industry 4.0. Control Engineering asked an Industry 4.0 expert how companies can tell if they’re moving quickly enough toward smart manufacturing and digital transformation. Are Industry 4.0 benefits passing you by?
It has been a dozen years of Industry 4.0 efforts. Are those involved moving quickly enough? Have others passed them by? Is there an Industry 5.0? How should Industry 4.0 be changing how stakeholders approach automation, controls and instrumentation? Control Engineering asked these questions and others about smart manufacturing and digital transformation to Jeff Winter, senior director industry strategy, manufacturing, Hitachi Solutions, and an industry expert on Industry 4.0 on LinkedIn.
Question: How do companies know if they’re moving quickly enough with Industry 4.0?
Winter: “Quickly enough” really depends on two things: 1) How does your company compare to its competitors? 2) How are you doing against your own Industry 4.0 goals?
For the first part, several maturity models help with evaluation of your company’s digital maturity and progress toward industry 4.0 (such as Acatech’s
Industry 4.0 Maturity Index, INCIT’s Smart Industry Readiness Index, etc.). These allow companies to benchmark performances against industry standards and best practices, often times including a holistic evaluation of the company.
For the second part, companies can track key performance indicators (KPIs) specific to their Industry 4.0 initiatives to measure progress. Popular examples include overall equipment effectiveness (OEE), quality, flexibility and even innovation. World Economic Forum, partnered with McKenzie, is several years into its Lighthouse network program that aims to identify the top facilities that exemplify the leading edge of technology adoption and are implementing advanced manufacturing at scale while seeing significant gains. These gains are all publicized and can be used as a benchmark for realistic KPI improvements.
Q: Do you recommend any Industry 4.0 assessment, akin to a safety risk assessment or cybersecurity assessment?
Winter: Personally, I really like the Smart Industry Readiness Index (SIRI) by INCIT. This tool is good for evaluating and assessing Industry 4.0 progress because it provides a comprehensive, structured and systematic approach to evaluate an organization’s digital transformation journey. The index was developed by the Singapore Economic Development Board, which partnered with TÜV SÜD for certification of assessors. SIRI by INCIT is designed to help manufacturers assess and advance digital readiness. Two things I really like about the SIRI framework are: 1) There are classes to get certified as a SIRI Assessor (or the ability to search for
FIGURE 1, COVER: Digital transformation framework requires changes to how people, processes and technologies use data. Key elements include updated digital infrastructure, system integration, digital skills and training, with appropriate leadership and vision. Image, graphics courtesy: Jeff Winter, Hitachi Solutions
assessors who are certified) and 2) they also provide a prioritization matrix along with the framework that helps with developing an actionable plan after the results of the evaluation.
Q: How is Industry 4.0 changing how companies approach automation, controls and instrumentation?
Winter: Industry 4.0 is the nickname given to the 4th Industrial Revolution. As its name implies, it is a revolution in the way the entire industry operates and the way people work, resulting in a complete change in society. This term was famously announced in 2011 at Hannover Fair as part of the German High-Tech Strategy, and since then it has taken hold across the world.
However, there is no universally accepted definition, as it has taken on different meanings and connotations as it spread across the world. Most would agree that industry 4.0 aims to improve productivity, efficiency, flexibility and overall competitiveness in manufacturing and industrial sectors by leveraging these advanced technologies and concepts, but few agree on the included technologies or scope and reach of the topic.
This means it is up to every company to come up with its own definition to figure out how to take advantage of all these technologies collectively to
‘ Adaptive and flexible automation systems can respond to changing production requirements and customer demands. ’
thrive in this transformative time right now.
The three biggest ways that Industry 4.0 is changing how companies approach automation, controls and instrumentation are:
1. Data-driven decision making and adaptability: The massive amount of data generated by automation, control and instrumentation systems in Industry 4.0 provides valuable insights into industrial processes. Companies are investing in advanced data analytics and visualization tools to make better-informed decisions, optimize processes and improve overall efficiency. Additionally, Industry 4.0 encourages the development of adaptive and flexible automation systems that can respond to changing production requirements and customer demands. This includes the use of modular production lines, collaborative robots (cobots), and reconfigurable manufacturing systems, allowing companies to adjust operations quickly and efficiently.
KEYWORDS: Industry 4.0, smart manufacturing, digital transformation
LEARNING OBJECTIVES
Identify how to determine if your company is moving quickly enough with Industry 4.0 initiatives.
Review differences in Industry 4.0, smart manufacturing and digital transformation.
Understand Industry 4.0 benefits.
CONSIDER THIS
Are you meeting Industry 4.0 metrics for success?
ONLINE
This article is longer online. In the digital edition, click the headline to see more graphics and answers to questions on cyberphysical systems, digital transformation, digital twins and IIoT. Online controleng.com
ENABLERS
Internet of Things
Artificial intelligence
Connectivity and cloud computing
Simulation
Additive manufacturing
Augmented reality
Robotics
Blockchain
Industrial security
ENHANCERS
Digital twin
Digital thread
Terminology and reference models
Decentralization
Modularization
Virtualization
Vertical integration
Horizontal integration
Product transparency
FIGURE 2, TABLE: Smart manufacturing enablers and enhancers include technologies and concepts that help manufacturers take advantage of Industry 4.0 opportunities.
2. Reaction to prediction: Industry 4.0 technologies have enabled a shift from reactive process to predictive and prescriptive ones. In traditional industrial settings, companies would typically rely on human intervention to monitor, analyze and control processes. This reactive approach often led to delayed responses, higher downtime and increased costs due to inefficiencies and errors. By using advanced sensors, smart devices and realtime data analytics, companies can monitor and analyze processes continuously, allowing them to predict potential issues and optimize operations based on historical data and trends.
Predictive maintenance, for example, enables companies to anticipate equipment failures and schedule maintenance to avoid downtime and reduce costs. By employing AI and machine learning algorithms, companies can automatically adjust control parameters and make real-time decisions to achieve optimal performance. These algorithms also can recommend specific actions to operators, ensuring that the right decisions are made at the right time.
3. Enhanced connectivity and interoperability: Industry 4.0 emphasizes seamless connectivity among machines, sensors, control systems and data platforms. This enhanced connectivity allows for better monitoring, control and optimization of industrial processes. Companies are adopting open communication protocols, wireless tech-
nologies and edge computing to facilitate seamless data exchange and integration among various systems. This interconnectedness enables companies to have a comprehensive understanding of their operations, leading to more efficient and agile decision-making.
Q: Is there any official Industry 5.0, or are those using that term merely suggesting that the world isn’t moving quickly enough?
Winter: The term “Industry 5.0” does not have a specific originator, as it has been used and developed by various experts, organizations and governments to describe the next phase of industrial evolution. The definition of Industry 5.0 also has been shaped by these various stakeholders, which include practitioners, academics, policymakers and technology experts. In general, Industry 5.0 envisions a future where humans and advanced technologies like artificial intelligence (AI), robotics and automation work together in a more harmonious and efficient manner, combining the best of human creativity, empathy and judgment with the precision, speed and scalability of advanced technologies.
That being said, since we are just getting started with Industry 4.0, and relatively few people are talking about Industry 5.0 (at least according to Google Trends) in comparison to Industry 4.0, I would say we should focus on Industry 4.0 first!
Q: How does smart manufacturing differ from Industry 4.0?
Winter: The terms Industry 4.0 and smart manufacturing are often used interchangeably, but I would argue they are different concepts with different areas of focus.
Smart manufacturing is an advanced approach to industrial production that leverages cuttingedge technologies, data analytics and automation to optimize manufacturing processes, improve efficiency, and enable more flexible and responsive systems. It represents a paradigm shift in the way products are designed, produced and distributed. The primary objective of smart manufacturing is to increase productivity, efficiency and flexibility while reducing waste, energy consumption and operational costs. The scope typically includes the entire manufacturing value chain including prod-
uct design and development, production planning, supply chain management, production, quality control and distribution.
Joint Working group 21 (JWG21) was established as a collaboration effort between the International Organization for Standardization (ISO) and the International Electrotechnical Commission (IEC) to help formally define “Smart Manufacturing” that could be used in international standards as part of a unifying reference model. In 2021, they came up with the following definition:
Manufacturing that improves its performance aspects with integrated and intelligent use of processes and resources in cyber, physical and human spheres to create and deliver products and services, which also collaborates with other domains within enterprises’ value chains.
Note 1: Performance aspects include agility, efficiency, safety, security, sustainability or any other performance indicators identified by the enterprise.
Note 2: In addition to manufacturing, other enterprise domains can include engineering, logistics, marketing, procurement, sales or any other domains identified by the enterprise.
Industry 4.0, however, is a much broader concept that really describes the current era, the fourth industrial revolution. It refers to the ongoing transformation of traditional industries due to the increasing adoption of digital technologies. Industry 4.0 not only includes smart manufacturing but also extends to other functions, such as logistics and supply chain, transportation, energy and even healthcare and retail. The plan is for the definition to make its way into all other relevant ISO and IEC standards.
Q: What does Industry 4.0 and smart manufacturing mean for industrial automation, controls and instrumentation for end users, machine builders/ original equipment manufacturers and system integrators?
Winter: The main beneficiary of smart manufacturing is obviously manufacturers. From a controls and automation perspective, manufacturers can expect several benefits such as:
• Increased productivity: Advanced automation and control systems can optimize production processes, leading to higher output and better resource utilization.
FIGURE 3: Industrial AI use, according to IoT Consortium, requires considering how to digitize, extract and transform data; analyze, detect and diagnose; optimize; generate; prescribe; predict; and do/act.
• Enhanced process control: End users can monitor and adjust production processes in real-time, ensuring consistent product quality and reducing the likelihood of defects or waste.
• Reduced downtime: Predictive maintenance enabled by advanced automation can help prevent unexpected equipment failures and minimize production downtime.
• Better data-driven decision-making: Real-time data from automated systems can help end users make more informed decisions about process improvements, resource allocation and other aspects of production.
‘ Delivering datadriven solutions requires developing new capabilities in software, analytics and connectivity. ’
Machine builders and system integrators jointly will experience a completely different shift in their business and operating models as a part of Industry 4.0. A few ways machine builder and system integrator businesses will adapt include:
• Value proposition shift: As customers demand more intelligent, interconnected machines, the value proposition of machine builders and systems integrators shifts from simply providing hardware to delivering smart, data-driven solutions. This requires developing new capabilities in software, analytics and connectivity.
FIGURE 4: Triangle of success for digital transformation includes working through new knowledge, skills and attitudes to create a new vision. Digital transformation is a broader concept that encompasses the strategic and organizational changes required to fully leverage digital technologies, which often involve rethinking business models, processes and customer experiences.
• Servitization: Industry 4.0 enables all companies, but especially machine builders and systems integrators, an ability to offer digital services through taking advantage of remote connectivity and the ability to provide additional value from all the data insights gained. This includes things such as remote monitoring, predictive maintenance, over-the-air updates and optimization services. This can even lead to entirely new business models where subscription-based services replace larger CAPEX purchases and outcome-based contracts replace traditional scope of works.
• Collaboration and partnerships: The increased complexity and interdisciplinary nature of Industry 4.0 technologies encourage machine builders and systems integrators to form strategic partnerships with other technology providers, such as software developers, data analytics companies and IoT platform providers. Fewer companies will attempt to be the “one-stop shop” and instead show how they are part of an end-to-end ecosystem that can holistically help manufacturers transform their organizations.
Q:
What are best practices for controls and automation engineers in the era of Industry 4.0?
Winter: The transition from Industry 3.0 to Industry 4.0 has brought significant changes to the knowledge and skills required to be a successful controls and automation engineer. Some of the biggest differences include:
• Continuous learning a growth mindset: Technological innovation and market conditions are changing so quickly failure to react quickly can be catastrophic for a company. It also can make knowledge/skill today be obsolete in a short amount of time. It is imperative to dedicate time to stay updated with the latest developments in automation, controls and Industry 4.0 technologies. This includes pursuing relevant certifications, attending workshops, reading publications and participating in industry conferences.
• Spread your wings into new disciplines: The walls between disconnected fields engineering and organizational departments are becoming very blurry. Embrace a multidisciplinary mindset by understanding the interdependencies between various technologies such as mechanical, electrical, software engineering, IT, networking and other areas. This will help you develop a more holistic understanding of the systems you work with and identify opportunities for improvement.
• Focus on cybersecurity: As Industry 4.0 relies heavily on connected systems and data exchange, cybersecurity is paramount. Familiarize yourself with cybersecurity best practices, such as secure communication protocols, encryption and access control. Also, and ensure they are being implemented in projects.
• Think like an analyst: Those that capture and harness the power of data will be the most successful in the area of Industry 4.0. Develop skills in data analysis and visualization to take advantage of all data generated by smart manufacturing systems. This will enable users to identify trends, detect anomalies and make data-driven decisions to optimize processes and improve overall efficiency. ce
Jeff Winter is senior director industry strategy, manufacturing, Hitachi Solutions, and an industry expert on Industry 4.0 on LinkedIn; edited by Mark T. Hoske, content manager, Control Engineering, CFE Media and Technology, mhoske@cfemedia.com.
Claire Fallon, International Society of Automation (ISA)
While Industry 4.0 and digital transformation often are used interchangeably, they are distinctive concepts, and understanding how they differ can help organizations to implement both more effectively.
Advances in automation technology are transforming the manufacturing landscape. Broadly termed “Industry 4.0” or sometimes “digital transformation,” these smart manufacturing initiatives bring physical and cyber systems together for greater performance, efficiency, sustainability, safety and competitive advantage.
As a term, Industry 4.0 originated in 2011 — widely attributed to a German government strategy unveiled at that year’s Hannover Messe event.
Twelve years later, a lot has changed about manufacturing. In many cases, the fundamental tenets of Industry 4.0 have changed and shifted, being reprioritized, along with industry needs. For example, artificial intelligence and machine learning (AI/ML) likely play a greater part in everyone’s
day-to-day operations than we could have dreamed about in 2011.
However, we are not adapting quickly enough in other ways, and it is because of how we are looking at Industry 4.0 and what it really means.
These two terms are often confused, but there is an important distinction between them.
Industry 4.0 is about using digital platforms, products and services to gain a competitive advantage, much like steam engines, assembly lines, and industrial robots did in previous industrial revolutions. These are new and effective tools, but the focus is not necessarily on changing the behavior of individuals using those tools.
FIGURE 1: Digitalization is an intermediate step on the way to digital transformation that involves taking an existing workflow, such as walking the plant floor with a clipboard, and augments it with technology like tablets or augmented reality glasses to make it easier for engineers and inspectors to access documentation and record measurements. Graphics
Digital transformation is a more substantial change that impacts the way business is conducted — it is as much a shift in mindset as it is the adoption of new technologies.
Digital, digitalization and digital transformation — what's the difference?
There can be confusion about what it really means to enact a digital transformation, and so it's important to consider the different steps along the way. (Figure 1)
Making analog files digital and sharing them across the organization is a clear first step, and something many organizations have already started to do. In fact, many organizations began this practice even before we understood “Industry 4.0” as a concept. This is easy to implement, but relatively low impact in terms of the total digital transformation journey.
An intermediate step is digitalization. Think of an existing workflow, such as walking the plant floor with a clipboard performing inspections. If we digitalize this example, then inspectors may use tablets to update data or may even wear augmented reality tech like smart glasses. This makes it easier for engineers and inspectors to access documentation, and to record measurements, readings and observations in terms of notes, photographs and videos. All of this information can be associated with specific locations, making the processing of a report much more simplistic.
But we are still walking the floor. We are still logging data. We are still creating a report. The engineer’s job is not too different than it was before.
The final step is true digital transformation, where digital tools fundamentally change and even improve the way the organization does its business. An ISA board member recently told a story about how an oil and gas operator was beginning to rely upon ML to identify corrosion on their offshore production platforms through image analysis. An ML engine uses imagery captured throughout the facility for engineering and operations purposes to identify potential areas of corrosion, reducing the need for conventional manual inspection with its potentially biased analysis.
In this scenario, the ML algorithm also may identify potential issues that might otherwise be missed in a large-scale manual effort. When that team of inspectors and engineers no longer has to manually walk the whole facility, time and effort are freed up to manage the most effective ways to troubleshoot and solve the problems initially identified by the machines.
Digital transformation is not a project. It is a journey.
And while I have had the pleasure to work alongside many dedicated and passionate engineers, it is also not something one person can will into reality.
This journey involves so much more than just implementing new technology. It involves the people and culture of an organization, as well as its existing and planned business capabilities. And of course, there are always regulatory and compliance considerations at play.
Earlier this year, the ISA hosted a webinar about Industry 4.0 and digital transformation to understand what people know and what knowledge gaps they have. The vast majority of our attendees had at least some concerns, or faced challenges internally.
42% of respondents said, "We don't know where to start — it's overwhelming." Other concerns
centered around the cost, lack of clarity around who is in charge of the project and whether return on investment (ROI) was demonstrable.
However, 15% of respondents said, "No obstacles here, we are excited!" That's great news, and that type of response will become more common as digital transformation becomes more prevalent in industrial and manufacturing sectors.
If companies are facing resistance, they should seek additional training and resources to help present a case to management. There are many groups supporting professional engineers that can help demystify Industry 4.0 and digital transformation and address common objections.
As smart manufacturing technologies are implemented and mature, new and increased cybersecurity challenges have emerged beyond device-level IT risks. Termed operational technology (OT) cybersecurity, this field refers to the security and safety of industrial environments, and it is of critical importance when it comes to securing infrastructure, supply chains and more.
One of the biggest challenges facing the OT cybersecurity space is legacy equipment found in much of the global critical infrastructure. OT-specific security equipment and platforms are becoming more prevalent in the market to address this challenge, but not all of these are created equal nor are they uniformly adopted.
In 2023 and 2024, we expect government stakeholders and industry asset owners will demand rigorous solutions that present the highest levels of security and interoperability and will look for compliance with recognized international standards like ISA/IEC 62443. Workforce development will be another key area of focus, and plant managers will be even more focused on OT cybersecurity training and certification programs in the years ahead.
Digitalization enabled by the industrial Internet of Things (IIoT) has increased during the past decade with advances in sensor technology offering ever more context about equipment, processes and operations. New applications and advancements could also mean greater vulnerability, which is why a risk management and mitigation strategy is a critical part of digital transformation.
‘ Industry 4.0 vs. 5.0: Industry 4.0 is about improvements to safety, process, efficiency and profitability; Industry 5.0 is about resilient, human-centered and sustainable business strategies. ’
Industry 4.0 is not a destination; it is an ongoing journey. Manufacturers who can best optimize their cyber-physical systems (CPSs) with their workforce will be the winners in their market. Our advice is to do what you can today. Then wake up and do what you can tomorrow. It is never too late to get started.
There is already buzz about the concept of Industry 5.0, which aims to articulate the role and contribution that industry makes to society as a whole. Where Industry 4.0 is about improvements to safety, process, efficiency and profitability, Industry 5.0 is about resilient, human-centered and sustainable business strategies.
Like with Industry 4.0, these ideas may be things organizations are already doing. For example, many corporations have pledged their commitment to sustainability and environmental practices, with some making further commitments toward science-based targets. Like Industry 4.0, the meaningful changes needed to transform a business require mindset shifts. As an association of professionals, ISA focuses on how people can make the world a better place. Perhaps instead of a digital transformation we will call this a human transformation. Regardless, Industry 5.0 does loom large as the next strategic direction for industry and government initiatives. ce
Claire Fallon is executive director at the International Society of Automation (ISA), a CFE Media and Technology content partner. Edited by David Miller, content manager, Control Engineering, CFE Media and Technology, dmiller@cfemedia.com.
controleng.com
KEYWORDS: Industry 4.0, Digital Transformation
LEARNING OBJECTIVES
Learn the difference between Industry 4.0 and digital transformation.
Learn how organizational barriers that hold back digitalization can be overcome.
Learn the steps that lead from manual processes, to digitalization and finally to full-blown digital transformation.
ONLINE
Link to the most relevant topic on our website.
CONSIDER THIS
How can you change the mindset of your workforce to better enable succesful digital transformation?
Nathan Pettus, Emerson Systems
Leverage Industry 4.0 to build the foundation for an industrial architecture that integrates operations to drive data from field to edge to cloud to create a boundless automation future.
Safety, reliability and increased production are still key drivers for industrial process manufacturers. However, shifting corporate goals and public opinion have created an increased focus on sustainability and improved energy, adding yet one more constraint to optimization. Finding the best operating limits to maximize all these requirements necessitates more cross-domain information than ever.
Manufacturers are discovering the traditional architecture of keeping operational technology isolated from the internet is no longer a viable path to best-in-class operational excellence. However, the cybersecurity advancements emerging alongside Industry 4.0 include enhancements providing users the best of both worlds: increased connectivity without the risk of putting systems in harm’s way. Even so, accomplishing these goals requires focusing on integrating multiple operational domains to move data seamlessly from the field to the edge and into the cloud across all data silos — creating a boundless automation architecture. At the heart of this automation vision are nativelyintegrated operations and applications operating within a unified data model as well as secure connectivity between next generation automation technologies regardless of where the data resides, or applications reside.
In coming years, forward-thinking automation suppliers will be integrating technology and software across every domain. They will break down silos, democratize data and bring reliability, sustainability, energy use, quality and other critical operational data together with real-time control to create a unified data model that is interoperable, extensible and scalable. This paradigm shift in automation will empower operations teams across all domains to increase performance while meeting the needs and goals of the organization and the public (Figure 1).
The need to optimize operations is not new, but today’s global marketplace has increased competition and tightened budgets. As a result, few organizations today seek to increase produc-
tion by building new plants. Instead, operations teams are focused on optimizing — or more likely revamping — existing assets to increase flexibility, scalability, throughput and efficiency. However, most teams have been optimizing their plants for years and have reached the point where localized action brings diminishing returns. The next step is improving operations at the enterprise level by leveraging the software and technology available to optimize operations and interaction among multiple plants and process lines.
For example, based on years of instrumenting facilities with affordable sensing technologies, the amount of visibility into real-time operations is the greatest it has ever been. Operations teams can monitor almost every piece of equipment across the enterprise for fleet-level visibility of performance and reliability.
The data from that equipment — if it is free to move across all layers of the enterprise — can be sent to remote domain experts, or even to artificial intelligence and machine learning tools for deep analysis. The results provide a clear picture of process health and can also deliver actionable information to help organizations improve scheduling, reliability and performance across all plants while reducing energy use and waste.
Other teams also are using simulation software and digital twin technologies to replicate processes, or even entire facilities, to test process changes, train personnel and optimize operations. Operators working on a digital twin also can make changes to the process as though they were working on live equipment, with no risk to operations. As the simulation runs, they can see — in real-time or even faster — how the changes they made cascade across all areas of operation. Operators can see not only how a change will impact their own plant or process, but also plants and processes down the line that are dependent on their output.
FIGURE 2: Boundless automation builds an architecture to support the confluence of Industry 4.0 technologies and today’s market needs.
‘ A boundless automation architecture integrates industrial software, Industry 4.0 technologies and a next-generation automation fabric. ’
These tools, and many advanced tools that have yet to emerge in the marketplace, are dependent on a reliable flow of contextualized data, across domain silos and beyond typical data boundaries. The organizations that win the future of manufacturing will not be ones that install a siloed and targeted application to solve a specific problem. Rather, they will be those that can deliver the right data to the right place at the right time to maintain flexible, scalable operations leveraging all the data they already have (Figure 2).
The architecture that will best prepare an organization to meet the future of process manufacturing is based on a boundless automation vision. A boundless automation architecture integrates industrial software, Industry 4.0 technologies and a next-generation automation fabric to democratize data across every operational domain.
Today’s high-performing operations teams expect and rely on instant access and constant visibility to critical information. By providing the right access to information by the right people, organizations foster the innovation that leads to constant improvement and, with the right technologies and collaboration, toward self-optimized facilities. Providing this access means changing the traditional paradigm of operation to decentralize models and eliminate data silos, enabling contextualized data to stream across the enterprise.
controleng.com
KEYWORDS : Industry 4.0, Enterprise Connectivity LEARNING OBJECTIVES
Learn how breaking down data siloes can lead to system- and enterprise-wide efficiencies.
Learn about advances in technology that will enable real-time, enterprise-wide connectivity.
Leveraging real-time data across the enterprise https://www.controleng. com/articles/leveragingreal-time-data-across-theenterprise/
Creating connected industries, technologies with IIoT, Industry 4.0 https://www.controleng. com/articles/creatingconnected-industriestechnologies-with-iiotindustry-4-0/
CONSIDER THIS
What efficiencies can you achieve by focusing on system-wide optimizations?
‘
Non-operation-critical cloud-based apps offer outsourced infrastructure, no software installed on client devices, universal access, elastic scalability, pay-as-you use consumption models and more.’
This model of constant, intuitive, standardized access to data looks much like current, highly integrated business solutions, like enterprise resource planning software.
All operational domains — intelligent field devices, the next generation control system, edge solutions, cloud technologies and more — will be integrated into a single, cohesive software ecosystem.
This type of system will standardize data into a unified data structure, connected to context provided by all the other sources, and made available across the enterprise to cross-functional teams through many tools in natively-integrated industrial software platforms.
uManufacturers are discovering the traditional architecture of keeping operational technology (OT) isolated from the internet is no longer viable.
uImproving operations at the enterprise level by leveraging the software and technology available to optimize operations and interaction among multiple plants and process lines.
uTechnologies and protocols such as Ethernet advanced physical layer (EthernetAPL), 5G communication, OPC UA, hyperconverged infrastructure and containerization are key components of creating a boundless automation future.
A new, more modern technology fabric will provide the critical technologies operations teams will rely upon, such as analytics, simulation, energy management tools, field-based insight applications and more. Technologies and protocols such as Ethernet advanced physical layer (Ethernet-APL), 5G communication, OPC UA, hyperconverged infrastructure and containerization are forming the foundational technology infrastructure that will simplify connectivity among systems and smooth data flow.
Instead of building solutions as an edge layer on top of automation, new technologies will deliver an integrated ecosystem with fit-for-purpose apps, delivering a more intuitive experience between operational technology and information technology. This will be the case whether content originates from the cloud, a field device or an on-premises hyperconverged infrastructure.
Many plants have been around for decades and have reached the point where optimizing operations domain by domain is no longer effective.
Most of the easy fixes and optimization strategies have been found and implemented, and each domain works well in its own silo, but those same silos impede progress.
If a team needs to know the source of wasted energy, but a critical part of the cause is found in reliability data trapped in a siloed system, a key insight may go unrealized. Boundless automation architecture solves this problem by focusing on a broader strategy and tensioning those individual domains against each other to deliver continuous, enterprise-wide optimization.
Within the boundless automation’s integrated ecosystem, data is contextualized, democratized and centralized so it is instantly and securely available to appropriate personnel at any level of the organization. The future industrial edge will be built on hyperconverged infrastructure and universal fleet deployment and support.
Many applications that are not operations-critical can move to the cloud and enjoy the same benefits as IT systems and technologies: outsourced infrastructure, no software installed on client devices, universal access, elastic scalability, pay-asyou use consumption models and more. These systems will integrate with enterprise cloud systems such as enterprise resource planning (ERP), artificial intelligence and machine learning (AI/ML) analytics, simulation systems and more.
Not all the technologies that will drive the boundless automation architecture are available today, but many are here or on the horizon. However, the wide range of Industry 4.0 tools available today are helping teams build the foundation they will need to take advantage of next-generation automation solutions coming in the next five to 10 years. Today’s optimization decisions should be made with that future in mind, looking toward building the flexibility, standardization and visibility necessary to improve performance and efficiency across the enterprise. ce
Nathan Pettus, president, process systems and solutions, Emerson. Edited by David Miller, content manager, Control Engineering, CFE Media and Technology, dmiller@cfemedia.com.
Employing the concept of the Trojan Mouse, process manufacturers should start small to win big when it comes to digital transformation initiatives.
Many have been pitching and working to achieve elements of Industry 4.0 and digital transformation strategies for the last 15 years or more. They can feel vindicated. A recent IDC Report (Figure 1) stated and predicted investment in digital transformation is growing at a compound annual growth rate of 15.5% from 2020 to 2023. By 2023, 75% of organizations will have “comprehensive digital transformation implementation roadmaps,” up from only 27% in 2020.
Fast forward to 2023, and nearly all CEO agendas contain some elements of digital transformation. This is great news for engineers. After all, doesn’t the CEO have the greatest influence on the necessary scale of cultural and sustained change required for successful digital transformation efforts? Perhaps, but then again, perhaps not. Leadership commitment is one piece of the jigsaw. There is a roadmap for digital transformation that does not include huge, scary or costly projects. There is an agile route to digital transformation, innovation and empowerment that minimizes risk while still maintaining value.
Back in 2012, the digital thought leader, Euan Semple, talked about the concept of the Trojan Mouse in an organization’s digital journey. In this concept, he postulated return on investment should not be used as a measure of success when the investment is small because well-placed, small experiments help implementors “learn by doing,” while leaving space to increase value by scaling lessons to grander systems.
The Trojan Mouse concept has since been picked up by others, including Alex Blanes in a 2019 paper
“Why trojan mice are the best-kept secret of successful teams.” The Trojan Mouse has its place in systems theory as a successful approach to break down complex, as opposed to complicated, problems. This classification demands a certain type of emergent “sense and respond” approach to succeed.
Applying big-bang digital technology across a large, complex organization to change employee behavior and processes is, according to systems theory, the wrong approach. We witness this too often in dismal success metrics of large digital projects.
A “platform” approach, facilitates and reduces execution risks of digital Trojan Mice from within the system, is a positive step, provided an organization is set up to embrace it. By democratizing data access, making data manipulation and calculations easier and facilitating easy collaboration for knowledge sharing and reporting through innovative technologies, companies are more likely to roll out successful Trojan Mice and larger digital transformation projects down the road. In fact, many large consulting firms are adapting these methods throughout internal and client-focused digital transformation programs.
In the process industries, this approach is successful when applied to self-service advanced analytics solutions. The value proposition is an ability to serve data from almost any data source, providing a simple but powerful interface for working with small problems in collaborative teams. This sort of software architecture, training and knowledge framework empowers teams to scale successful Trojan Mice organization-wide.
As workplace collaboration thought leader Harold Jarche said, “Collectively, a few Trojan Mice will change more than one Trojan Horse ever could!”
controleng.com
KEYWORDS: Digital transformation, Trojan Mouse LEARNING OBJECTIVES
Learn how a strategy of incremental improvement can drive digital transformation outcomes.
Learn how a platform approach to data can empower employees to take ownership of innovation throughout an organization.
ONLINE
https://www.controleng. com/articles/overcomingorganizational-technicalreadiness-challenges-fordigital-transformation/ https://www.controleng. com/articles/threephases-of-industrial-digitaltransformation/
CONSIDER THIS
Where could your company begin implementing a "Trojan Mouse" strategy?
FIGURE 1: Digital transformation market value by year. Information courtesy: MRFR Database and Analyst Review.
‘ Think carefully about
data decisions: How to generate it, how much to generate, how to store it and how to create insights.’
Clive Humby, the data science entrepreneur, coined the phrase “Data is the new oil” in 2006. While there may be some problems with this analogy, it holds up well for the most part. Data is the new oil. Like oil, data is valuable, but it cannot really be used if it’s unrefined. Oil has to be changed into gas, plastic, chemicals, etc., to create a valuable entity that drives profitable activity. Data must be broken down and analyzed for it to have value. About twothirds of the world’s data is unused, and while data is not a finite resource like oil, it does have a carbon footprint. With data centers expected to account for 8% of world energy usage by 2030, that two-thirds of digital waste is hurting our environment.
People must think carefully about data decisions: How to generate it, how much to generate, how to store it and how to create insights. Thinking about a data strategy, architecture and governance is now the most important aspect of creating new assets. Comprehensive data taxonomies and attribute models for enterprise assets not only speed project delivery and handover, but they also are critical steps for further digital transformation.
Many process engineers are managing a legacy of poor, antiquated data structures and governance, and making appropriate corrections is expensive and time-consuming. Herein lies yet another source of complexity that too frequently proves to be the death of digitalization, digital twins and large business intelligence projects. For these types
of efforts to succeed, excellent data architectures and governance are required.
To provide the speed, flexibility and agility required for successful digital transformation in today’s paradigms, it is essential to bring cloud, edge and software-as-a-service (SaaS) strategies into the mix. This calls back to the Trojan Mouse approach of starting small and scaling rapidly by beginning complex processes with bite-size chunks with the primary objective of learning.
The best initial approach often is improving organizational data access with a cloud-based data platform. This hooks into source data, but only pulls what it needs to generate insights. This data storage is often a short-term cache to execute calculations and deliver visual insight. All data tagging, hierarchies and governance can be built specific to high priority data, serving steady growth and problem solving, as opposed to creating huge corporate taxonomies off the bat. Software might broker connections to real-time data, pulling in what it needs to a short-term cloud cache on demand. This introduces no added data management complexity, so an organization can extract value and democratize the most important data to drive a parallel, agile approach to data governance.
Quoting Sol Rashidi, chief analytics officer at Estée Lauder, organizations need to “know what data matters most, prioritize it, build the discipline to protect and govern it, then democratize it to enable data specialists and end-users to extract the insights they need to innovate.”
Andrew Keen, a digital commentator, posits “Being human in the digital world is about building a digital world for humans.” In other words, the answer to technology overload is not less technology, but more humanity.
This mantra is important for digital transformation projects, but it is especially critical now in the world of challenging demographics for engineering and manufacturing job roles (Figure 2). Multiple surveys agree around 90% of manufacturing companies are suffering a skills gap, estimating a 2.1 to 2.4 million job shortage within the next decade in the U.S. alone, with an economic impact of around $2 trillion.
Strategies for dealing with these problems include hiring more people, training and reskilling
and attracting more young workers and students, but these approaches take time to refine and may not succeed, especially as many required skills in manufacturing rapidly change simultaneously.
For organizations to effectively ride out the storm, they must create cultures of knowledge sharing, collaboration, openness and employee engagement. When these strategies are combined with reskilling and automating tasks where practical, the skills gap’s impact is reduced.While visionary leadership makes a significant contribution in these areas, but technology is fundamental, too. In a successful digital workplace, workers must be able to access all of the data required to do their jobs, empowered to deliver improvements with systems and processes in place to foster efficiency and effectiveness. These include elements like:
1. Self-documenting software, with the ability to share work with the push of a button in a knowledge sharing framework.
2. Automation to speed business processes and break down bureaucracy frustrations.
3. Collaboration tools to remove hierarchical barriers, making work engaging and satisfying.
4. These sorts of touches make workplaces feel more “human,” helping attract and retain the skills companies need to make digital transformation successful. In the words of Michael Jordan, “Talent wins games, but teamwork and intelligence win championships.”
There is more to overcoming the skills gap than training. A culture of engagement, collaboration and speed-to-insight is needed to navigate the skills transformation over the coming years.
Digital transformation victories are difficult to attain. It takes great leadership, courage and trust
to successfully change a culture, foster democratization and empower staff with a simple, collective access to trustworthy data and insightful information. This challenge must be approached with enthusiasm and optimism, especially when initiatives do not go as planned.
For process manufacturers, embracing an advanced analytics platform is critical for providing staff with the right tools to contextualize, analyze and make the right data decisions. Powerful technology itself does not ensure success, but software tools with wide-reaching connectivity, automated data cleansing, cloud access, capable algorithms and intuitive collaboration means cannot be overlooked in organizational digital transformation initiatives.
Companies must nurture, grow and support their “intrapreneurs” with systems and training to allow data-driven digital transformation to blossom. Patience, clear leadership, strategy and flexibility along the way help usher in these results. As Aristotle said, while undoubtedly contemplating digital transformation in the Parthenon at Athens, “The whole is greater than the sum of the parts.” Consider what MIT’s George Westerman added on the topic: “When digital transformation is done right, it's like a caterpillar turning into a butterfly, but when done wrong, all you have is a really fast caterpillar.”
Digital transformation is not just digitalization for the sake of advancement. However, it is meant to elevate human stakeholders. Begin with a plan. Enable and empower. Start small and make scaling easy. Build on successes and learn from shortcomings. ce
Paul Ettridge, digital applications consultant, Seeq. Edited by David Miller, content manager, Control Engineering, CFE Media and Technology, dmiller@cfemedia.com.
FIGURE 2: Largest barriers to successful digital transformation. Information courtesy: McKinsey
Digital Transformation insights
uInvestment in digital transformation is growing at a compound annual growth rate of 15.5% from 2020 to 2023. By 2023, 75% of organizations will have “comprehensive digital transformation implementation roadmaps,” up from only 27% in 2020.
uThe concept of the Trojan Mouse holds that return on investment should not be used as a measure of success when the investment is small because wellplaced, small experiments help implementors “learn by doing,” while leaving space to increase value by scaling lessons to grander systems.
Dulce Maria Varela, Yaskawa America Inc.
IEC 61131-3 offers users a reliable framework to improve programming effectiveness, libraries.
In its third edition, the PLC programming language standards, IEC 61131-3, offers users a reliable framework to develop efficient solutions at all phases of automation processes. The standard has three graphical and two textual programming languages to support PLCopen libraries for various applications and communications with ongoing support, creating reusable code to exist for different builder needs. Programmers get three PLCopen benefits: Multiple supported programming languages, program optimization and troubleshooting support.
While code portability and interoperability among PLCs cannot be guaranteed, the standard supports commonly used languages:
• Graphical programming languages
–Ladder diagram (LD), composed of different types, contacts and coils
–Function block diagram (FBD), consisting of
functions and/or function blocks –Sequential function chart (SFC), composed of steps and transitions.
• Textual programming languages –Structured text (ST), consisting of statements and expressions –Instruction list (IL), a sequence of instructions.
The flexibility allows users to remain consistent in coding if they need to perform a retrofit. It also helps when starting a new project by allowing them to choose the preferred method of programming. In some examples, users may find it beneficial to create function blocks (FBs) from structured text subroutines, integrate PLCopen function blocks to logic for better performance and/or restructure logic due to troubleshooting procedures. The standard’s support for diverse languages makes it feasible to operate and implement various application PLCopen libraries, while users program in their preferred language(s).
Integrated PLCopen libraries on IEC 61131-3 compliant programming environment(s) provide users with guidelines and best practices to help develop efficient and reusable PLC programs, and other tools for users to adapt PLCopen guidelines into code for metrics like desired memory usage or performance of PLC programs. PLCopen libraries are designed and created to support and monitor project logic, motion control, safety, OPC UA-HMI, and XML (project source code export), based on configuration needs. PLCopen libraries support applications: homing, coordinated motion, torque control, camming and gearing. A wide range of functions support users in each step of their process, reducing programming time.
The PLC programming language standards IEC
KEYWORDS: programmable logic controller, PLCopen
LEARNING OBJECTIVES
Understand the types of programming languages supported by PLCopen tools and how they can be used.
Learn about the benefits of program optimization and how users can integrate and reuse code.
Understand how troubleshooting support can help users when they run into problems or issues.
ONLINE
Get more troubleshooting advice with this article online. https://www.controleng.com/control-systems/ programming
CONSIDER THIS
How do you use PLCopen in programming, and what role does it play?
61131-3 also allow users to create variables that can be applied to retain/constant values, while being assigned as a global, local, external, temp or input/ output (I/O) mapping. The standard’s openness for variable creation makes customizing PLCopen libraries with standard FBs (counter, timer, etc.) and functions (Type convert, Bit-string, INTEGER, REAL, etc.) a feasible task. The adaptation of functions/FBs also can help projects run more efficiently while reducing code by granting users the potential to reuse them in other project sections.
When making the most of the PLC programming standards, users can allocate CPU based configuration resources to assign programs to tasks based on default, cyclic, event or system. Users can assign task interval time, priority level and watchdog timing for the assigned programs. The configuration resource capability is a beneficial tool in ensuring applications meet desired timing and execution expectations. PLCopen and PLC programming language IEC 61131-3 guidelines enable users to optimize projects to configure, customize and troubleshoot.
Operating on complaint programming environment(s), PLCopen provides users tools to troubleshoot applications issues in PLCopen libraries including embedded logic to signal error alarms, error ID/codes with potential resolutions. Use tools to troubleshoot PLCopen for syntax errors, logical mistakes, incorrect parameter settings and more. ce
Dulce Maria Varela is a regional motion engineer for Yaskawa America, Inc. Edited by Chris Vavra, web content manager, Control Engineering, CFE Media and Technology, cvavra@cfemedia.com.
2: PLCopen FB MC_ReadAxisError may be used to determine motion control axis errors with ErrorID values providing further description and resolutions.
Eelco van der Wal, PLCopen
IEC 61131-3 deals with programming languages and a programming methodology. PLCopen builds on top of this to increase efficiency, reusability and portability through the definition of standardized libraries with pre-defined functionalities for applications such as motion control, safety and communication.
controleng.com
KEYWORDS: IEC 611311, programmable logic controller, PLC
Understand how PLCopen is used in programmable logic controller (PLC) programming.
Learn about the importance of building libraries.
Understand the role of the PLCopen XML exchange format, called IEC 6113110, and what it will do for PLCopen’s future.
ONLINE
Get more programming help at https://www. controleng.com/ control-systems/ programming/
CONSIDER THIS
How do you use PLC programming in your facility?
This combination offers the programmers a consistent look and feel across the different systems and architectures. This means that a programmer can reuse its knowledge, experience and programming methodology across the different systems, brands and architectures. This could be thought of as a “portability of the mindset” because it widens the scope for the person beyond one system, brand or application. It helps include different brands, application areas and ways of dealing with motion control networks and architectures.
It is advised that the machine builder, application programmer and user create libraries to encompass their knowledge and know-how for applications. By creating these higher-level functionalities, the process of application development can be dramatically reduced, resulting in fewer errors and lower installation costs. In many cases, the application program will be reduced to just a small number of lines of code, which is much easier to maintain. Reusing it on different platforms is much easier and quicker. For the exchange, PLCopen has developed the PLCopen XML exchange format, called IEC 61131-10, which will be supported by many suppliers of development environments, and it will be suitable for different tools such as documentation, code generation and version control. For defining functionalities, choose from differ-
FIGURE: The basis is provided by standardized function blocks. On top, a higher-level functionality is defined in application-oriented functionalities, making the application program small and maintainable. Putting a state machine at the top level create a harmonious look and feel for different machines in a production line.
Courtesy: PLCopen
ent programming languages to fit needs. Languages support object-oriented features. One can present the functionalities in a classical way, helping maintenance people to understand the application easily. By providing a set of function block definitions or libraries, PLCopen provides means to be more effective in creating application software. By implementing the function block libraries on different platforms, one creates a consistent look and feel over different systems and architectures. For PLCopen motion control, this consists of more than 40 suppliers and more than 70 products, to speed application development and reduce errors and installation time. It will save money during maintenance and for updates. This can provide the basis for software-as-a-service (SaaS), where functionalities are added to the application later, while being operated by the customer. ce
Eelco van der Wal is managing director of PLCopen, a CFE Media and Technology content partner. Edited by Chris Vavra, web content manager, cvavra@cfemedia.com.
Chris Vavra, Control Engineering
Additive manufacturers are expanding and enhancing their reach beyond the printing concept and leveraging their expertise and the potential digital technologies they offer.
Additive manufacturing (AM) and other 3D printing technologies advances were showcased at Rapid + TCT, an exhibition and conference sponsored by SME, at McCormick Place in Chicago. Additive manufacturing, which involves the construction of a 3D object from a computer-aided design (CAD) model or a digital reconstruction, has gone through many evolutions over the past several years. Improvements continue in the types of materials used, and researchers from all over keep making new composites designed to be sturdier, stronger and more durable. Like other manufacturing industries, they continue evolving. That’s not new.
What was new at Rapid — and falls in line with other industries — is how additive manufacturers are trying to better control of the lifecycle process including materials, design, creation and integration. It’s not enough to make the composite anymore or sell the printer. They want to be involved in the entire process and become a partner with their customers and provide services as well as solutions.
“We want to be a full-end business and provide end-to-end design for our customers,” said Rich Stephenson, AM business development at Siemens. “Whether it’s physically or digitally, we want to give consumers the full digital thread.”
He also mentioned the Charlotte Advanced Technology Collaboration Hub (CATCH), located in Charlotte, North Carolina, which serves as an ecosystem and a place where people can see how the process works and make it less abstract.
“We want them to use our equipment and let them get their hands dirty,” he said.
David Lakatos, chief product officer for Formlabs, described their production process as more about ensuring they control all aspects of the products they are making.
“We’re about more giving more access to those who make physical products in a professional sense,” he said. “That’s important to us because we want to work with people who are professionals
FIGURE 2: Lumafield
uses an X-ray scanner while spinning a part to produce thousands of images to create a representation of the model, which is reconstructed through an algorithm to a 3D model.
and are serious about this and want to improve.”
Formlabs’ Form 3+ Basic Package 3D printer was designed for the engineer looking to mass-produce items they might need for day-to-day operations. They also provide more than 30 types of resins, and the printing process is proprietary, according to Lakatos, as part of their large-scale plan to produce thousands of machines for their consumers because they are small and portable, which was a contrast from the much larger machines commonly on display at Rapid.
Lumafield wasn’t the only company demonstrating digital technologies at Rapid, but its emphasis on using digital representation was among the strongest.
which might result in a weakened internal structure, and seeing this allows the company to integrate its offerings into some automation solutions.
Cindy Kutchko, additive manufacturing director for PPG, said they use digital twins and modeling to help improve the precision and quality of its products. This is especially important because many of PPG clients are in the aerospace industry, which requires absolute precision. Even a tiny mistake can lead to serious injury or death. Creating a digital model helps in that journey.
“We want to improve productivity and ensure the product reaches peak performance,” she said.
Additive manufacturing is evolving and becoming more focused as companies realize potential and build on what was done before.
Vac-U-Max, for example, has been dealing with vacuums and pump technology for most of its existence. Metal powder, a common element used in additive manufacturing, is helping make existing technologies and processes more efficient.
u
Online controleng.com
KEYWORDS: Additive manufacturing, supply chain management
Learn about what additive manufacturers displayed and showcased at Rapid + TCT.
Understand how the industry is changing and what this means for industrial manufacturers.
ONLINE
See additive manufacturing stories at https://www.plantengineering. com/supply-chain/ additive-manufacturing/
CONSIDER THIS
What role does additive manufacturing play in your facility?
Austin Corder, content marketing generalist for Lumafield, explained how an X-ray scans the part while spinning to produce thousands of images to create a representation of the model, which is reconstructed through an algorithm to a 3D model. He demonstrated a Lithium-ion (Li-Ion) battery reconstructed through this model.
“It’s about safety to scan,” Corder said. “We went to ensure all layers are exactly right, so there aren’t any gaps.”
If there are unintended gaps during the printing process, the algorithm will help them find the gaps so they can be filled in, Corder said.
“It’s aimed at fixing the supply chain, and the beauty of this process is you can use reverse engineering to find the problems and also use it to reshore products they might not have access to,” Corder said.
Andy Stults, senior sales application engineer at Nikon Metrology, discussed a similar process when it comes to quality inspection. “You can scan and reverse engineer a part and make a surface, and then you can make a part from this.”
He also said they can find the voids in the process,
“Metal powders are physically demanding, and what we found is many companies are taking the leftover powder and putting it on the shelf,” said David Kennedy, business development manager for Vac-U-Max. Instead, by containing extra powder and putting it back in the additive manufacturing process reduces waste and downtime. The latter is especially important because the printers are often running 24/7 and cannot afford to stop.
Keeping these printers running efficiently, according to Duygu Gunay, automation project manager at HP, helps in other ways. Not only does it reduce downtime and overall costs, with less printer maintenance.
“It’s about scaling reduction, and there are different avenues for that. Shorter printing times, of course, is one way, but also it’s about lightening labor costs as well as optimizing air and costs.”
The race to efficiency and reduced costs is not new, and additive manufacturers can help in their own unique way in making the supply chain a better and more streamlined system. ce
Chris Vavra, web content manager, CFE Media and Technology, cvavra@cfemedia.com.
AUTOMATION SUPPLY
Azad Jafari, Beckhoff Automation
New equipment designs focused on reducing material waste and energy consumption also can boost margins and system uptime.
Use LED lightbulbs. Properly inflate tires. Get protein from plants. We’ve all heard plenty of advice about how to practice sustainability in our own lives. Engineers across industries have measurable ways to boost sustainability. Implementing sustainable automation technology also can increase the reliability and cost-effectiveness of industrial equipment.
Intralogistics is an example. E-commerce grew exponentially during the pandemic. It provided a lifeline for people to get what they needed, without going into a brick-and-mortar store. The larger number of people ordering (and ordering more often) put the environmental impacts of distribution centers under a microscope, as well. Wasteful packaging and energy also affects companies’ bottom lines. Intralogistics providers and machine builders are exploring new ways to reduce impact.
What does this look like in practice? For starters, new automation technologies enhance the sustainability of packaging for e-commerce, by offering benefits such as right-sized packaging options. This can directly contribute to improving environmental friendliness. Reducing waste can boost profit margins.
Automation technology and intralogistics equipment manufacturers must prioritize sustainability to ensure their design, construction and operation have minimal negative impact on the environment while promoting long-term resource availability. Achieving this goal involves reducing energy consumption, minimizing waste and using environmentally-friendly materials.
Practical sustainability measures for automation technology and intralogistics equipment include designing energy-efficient systems that incorporate
low-power components and limit energy use during idle periods. Using recyclable or compostable materials during the production process and implementing waste reduction systems such as closed-loop material handling systems play an important role. Designing equipment with extended lifetimes and easy repairability also reduces the need for frequent replacements, while environmentally-friendly disposal processes are necessary for end-of-life equipment.
These efforts do more than allow companies to be “green.” In industrial equipment, sustainability and reliability are interdependent; they contribute to the overall success and longevity of a system.
Reliability refers to a system’s consistent and failure-free ability to carry out its intended functions. A reliable system reduces waste and the need for frequent replacements, promoting sustainability by con-
FIGURE 1: Right-sizepackaging machines, such as Kern AG’s PackOnTime system, increase sustainability in intralogistics by reducing waste cardboard and optimizing density in delivery vehicles. Images courtesy: Beckhoff Automation
FIGURE 2: Increased data transparency due to a coordinated system for power supply, fusing and monitoring simplifies energy management in production environments.
serving resources. A sustainable system is designed to minimize negative impacts on the environment and conserve resources, which can improve profitability by reducing the demand for raw materials. A system designed to promote sustainability by conserving resources and minimizing waste is more reliable in the long term.
As a result, it reduces risk of failures and offers a longer lifespan. At the same time, a reliable system that operates consistently and without failure offers greater availability and contributes to sustainability by minimizing waste and preserving resources.
Responsibility for monitoring sustainability and reliability can be shared by several parties, including the equipment manufacturer, operator and any third-party maintenance providers. The end user must ensure equipment is used and maintained in a sustainable and reliable manner.
The frequency and extent of monitoring required for sustainability and reliability depend on the equipment and its usage. Regular monitoring is crucial to ensuring the equipment is being used and maintained to promote sustainability and reliability.
More companies are adding sustainability initiatives across organizations. No matter the industry, machine builders can find the benefits of sustainable equipment to be a key differentiator when launching a new product. For end users, several steps can promote sustainability and reliability with automation technology and intralogistics equipment. Both groups can:
1. Ensure operations and processes are energy efficient in the first place. End users can optimize energy usage and reduce waste by controlling equipment energy consumption, such as turning off equipment when not in use.
controleng.com
KEYWORDS: Sustainability, intralogistics
LEARNING OBJECTIVES
Understand how sustainability initiatives can improve margins.
See how sustainability, energy efficiency, reliability and maintenance are related.
Learn how machine learning can be leveraged to improve energy efficiency.
ONLINE
https://www.controleng. com/articles/howmonitoring-energy-usageimproves-plant-operationsand-sustainability/
CONSIDER THIS
How can automation help sustainability?
To guarantee the equipment lives up to its eco-friendly promises, someone needs to monitor performance and quantify the benefits. Who should monitor? Should they also be responsible for maintenance if performance falls short?
The frequency and extent of monitoring required to ensure the sustainability and reliability of automation technology and intralogistics equipment may vary depending on the equipment and its usage. Nevertheless, some general guidelines include:
1. Regular maintenance: It’s best to implement predictive maintenance technologies to automate regular maintenance efforts.
2. Energy consumption monitoring: Regular energy consumption monitoring can help ensure energy-efficient equipment usage and identify any spikes that can point to a developing problem.
2. Implement power monitoring through automation to enhance sustainability and reliability, as it can signal an upcoming maintenance concern when there is a surge in equipment power consumption. For greenfield applications, this can be built in with data collected by a PC-based machine controller, then sent to the cloud or enterprise level. For brownfield retrofits, adding power monitoring can be as simple as installing several I/O terminals and an internet of Things (IoT) coupler.
3. Machine learning is an effective method to automate energy conservation in industrial environments. ML can be leveraged to optimize the ramp speed of shuttles on an automated storage/retrieval system or identify the most efficient paths for automated guided vehicles/autonomous mobile robots, reducing energy consumption without operator intervention. ce
Azad Jafari, I/O product manager, Beckhoff Automation. Edited by David Miller, content manager, Control Engineering, CFE Media and Technology, dmiller@cfemedia.com.
Brandon Teachman, Vision Control and Automation
Equipment-as-a-service can improve original equipment manufacturers and customer productivity without significant upfront investments.
Manufacturers face the increasingly challenging task of keeping up growth and improving their bottom lines. As a result, many manufacturers are turning to equipment-as-a-service (EaaS). EaaS is a model where original equipment manufacturers (OEMs) provide their customers with the equipment they need on a rental or subscription basis. EaaS allows customers to use the latest technologies and equipment without significant upfront investment. Instead, they can pay for the equipment as they use it, which can help reduce their costs and improve cash flow.
The thing most people think of when they hear of any product as-a-service is likely increased revenue. While this does play a factor, there is more to it than that. Offering equipment on a rental or subscription basis can help improve revenue predictability and stability, reducing the reliance on one-time sales. The other benefits of EaaS include:
1. Increased customer base: EaaS can attract new customers who may not have been able to purchase the equipment outright.
2. Better customer relationships: EaaS also provides OEMs with a method to build ongoing customer relationships. The relationships help to increase customer loyalty and improve customer satisfaction.
3. Better equipment designs: EaaS allows OEMs to collect data on how their equipment is being used and how it is performing. This information is used to discover areas for improvement, create new products, and give insights to customers to assist them in optimizing their operations.
Manufacturers often seek new ways to increase
efficiency, reduce costs and stay competitive. EaaS may be a solution OEMs can help with. EaaS can provides benefits such as:
1. OpEx vs. CapEx: In an EaaS model, the equipment is a rental, which provides end-users with predictable and consistent costs for their equipment. Being a rental allows the user to claim it as an operating expense (OpEx). Operating expenses are often easier to get approval for than larger capital expenses (CapEx). Some manufacturers have even negotiated a price per part rate, allowing companies to correlate to the finished result.
2. Scalability: By allowing end users to add equipment as needed, EaaS can assist end users in scaling their operations more effectively, which results in no significant upfront investment in new machinery to scale up their operations to meet demand.
3. Improved uptime: Manufacturers can reduce the risk of equipment downtime by providing equipment on a rental or subscription basis. The OEM is incentivized to help keep the line up and running. This can be the OEM conducting preventative maintenance, prescriptive maintenance, oncall support, or other time-saving operations.
4. Reduced risk: Manufacturers can reduce the risk of investing in equipment by providing equipment on a rental or subscription basis. If business decreases, companies can choose not to renew the lease. An employee's safety falls on the manufacturer; the OEM will ensure their machine meets local codes.
5. Latest technology: Another benefit of EaaS for the end user is access to the newest technology. Since EaaS providers are responsible for upgrading the equipment, they can ensure the end user can access the latest technology. These updates can include software, firmware and security updates.
6. Environmental impact: EaaS also helps to
KEYWORDS : Equipment-asa-Service, EaaS
LEARNING OBJECTIVES
Learn how EaaS allows customers to use the latest technologies and equipment without significant upfront investment.
Learn how EaaS can increase an equipment provider's customer base, help build better customer relationships and improve future equipment designs.
Learn how IIoT enables EaaS.
ONLINE https://www.controleng. com/articles/optimizemachine-metrics-witha-machine-as-a-servicemodel-blockchain/
Optimize machine metrics with a machine-as-a-service model, blockchain
CONSIDER THIS
Are there any new technologies that EaaS could allow you to adopt without incurring the risk of an upfront purchase?
reduce equipment’s environmental impact. By providing equipment on a rental or subscription basis, manufacturers can reduce the environmental impact of their equipment. This is because when one customer is done using the line, it can be rented out to another customer to ensure continued life and the need to dispose of the equipment.
The industrial Internet of Things (IIoT) plays a critical role in the success of EaaS. With a modern controls infrastructure, it is easy to get manufacturing lines online, and some applications for this data include:
‘ Are digital transformation and IIoT technologies being supported and embraced for EaaS support? ’
1. Predictive maintenance: By collecting and analyzing data from sensors installed on the equipment, IIoT systems can predict when maintenance is needed and prevent equipment breakdowns. This allows EaaS providers to offer a more reliable service to end users, reducing downtime and improving equipment performance.
2. Remote monitoring: With IIoT, EaaS providers can monitor equipment performance in real-time, detect issues early and address them before they cause downtime or impact productivity. This ensures end users can access high-performing equipment.
3. Performance optimization: By collecting and analyzing data on equipment usage, IIoT systems can identify patterns and make recommendations for improving efficiency, reducing waste, and optimizing production. This helps end users maximize the value of their equipment while minimizing their costs and environmental impact.
4. Improved communication: Communication is vital with any customer, but with EaaS, it is critical to provide data that makes it easier for the customer to keep it running effectively. Examples are proactively emailing possible issues to the customer, automatically sending a weekly report showing critical production information or sending a monthly email with the maintenance schedule.
There are a few critical aspects to remember when deciding if EaaS is the best strategy for a company. EaaS, which offers equipment on a rental or subscription basis, can help manufacturers stay competitive and enhance their financial situation. Not all OEMs will benefit from this approach. It is crucial to determine whether EaaS is the best fit. There are some questions to consider when deciding if EaaS is the right choice for the business:
1. Is there a demand for EaaS? Companies should research existing and potential customers to determine if there is a desire for EaaS.
2. Are you making repetitive machines? To lease a machine to multiple people and to justify development investment, customization should be minimal.
3. Is EaaS financially viable? Companies will need to analyze costs and benefits of offering EaaS to determine if it makes financial sense for the business.
4. How will billing be structured? Companies need to decide if it will be hours used, per month flat rate, per piece or some combination.
5. Can you provide necessary support and maintenance services for EaaS? Companies must ensure they have services resources and expertise.
6. Is digital transformation and IIoT technology being supported and embraced? EaaS often uses technology to monitor and optimize equipment performance. Companies must ensure they have the necessary technological infrastructure.
7. Is the necessary legal framework in place? There may be legal requirements companies need to meet to offer EaaS. This will include, but may not be limited to, a contract with the customer. Partner with a legal firm with related experience.
EaaS can aid OEMs in maintaining competitiveness and enhancing financial performance. By offering equipment on a rental or subscription basis, OEMs may improve income streams, lower the risk of investing in unnecessary equipment, strengthen client ties and stay one step ahead of the competition. The sort of equipment the company provides, the sector and company culture should be considered when determining if EaaS is the best fit. ce
Brandon Teachman, application specialist, Vision Control and Automation. Edited by David Miller, content manager, Control Engineering, CFE Media and Technology, dmiller@cfemedia.com.
Armand Prezioso, Rockwell Automation
Process plants with universal I/O can use different I/O types on one I/O card.
Today’s smart sensors and instruments can give process plant personnel deeper insights into their processes and advance warning of potential problems to help them optimize operations and reduce unplanned downtime. For this to happen, process operators need to answer a key question: How are they going to enable their control systems to accept all the new data from these devices?
Traditionally, control systems have been commissioned with a set number and type of input/output (I/O) cards. Making any changes to this I/O card layout, such as to accept data from new sensors or instruments, has been made possible by leaving spare space in an enclosure and stocking up on different I/O card types. This approach can be expensive and risky because it can impact how quickly a system can recover from a failure or even something as routine as scheduled maintenance.
To get around these challenges, process plants are embracing universal I/O, which allows different I/O types to land on one I/O card. With universal I/O, manufacturers can speed set up time while simplifying field wiring, reducing spare module requirements, easing maintenance and realizing other benefits.
Also known as electronic marshalling, universal I/O provides greater flexibility by allowing operators to choose I/O to meet their specific operational needs. A universal I/O module can be configured per channel as analog input or output, including HART-capable, or discrete input or output. Universal I/O modules can also be configured in simplex or duplex. This flexibility gives process operators a wide range of benefits throughout their system’s life cycle.
Universal I/O can simplify field wiring. Revisions and changes are often made to a system as needs evolve during both commissioning and the life of the system. A universal I/O module that allows for various field wiring types can accommodate such changes. This can reduce total installa-
tion cost and help engineers work more efficiently during early design without impacting panel costs.
When a system starts with a universal I/O layout, its power needs, cabling layouts and termination assemblies all can stay the same, even if the I/O type changes later. This also can help save effort and planning. Universal I/O also helps ease long-term system management. Operators no longer need to hold on to different I/O card types for when they need to replace a card for maintenance purposes or add a card as part of a system change. Instead, they carry one card they can configure by channel as analog or digital.
Universal I/O modules are growing in popularity, but it’s important to remember they’re not all the same. Some universal I/O modules can use remote software configuration. This allows a remote operator to dynamically change I/O types without being local to the I/O card. Universal I/O provides a pathway to smart process control that’s simpler and causes fewer headaches than traditional I/O. ce
Armand Prezioso, product manager, Rockwell Automation. Edited by David Miller, content manager, Control Engineering, CFE Media and Technology, dmiller@cfemedia.com.
ALSO KNOWN as electronic marshalling, universal I/O provides greater flexibility by allowing operators to choose I/O to meet their specific operational needs. Courtesy: Rockwell Automation.
controleng.com
KEYWORDS: Universal I/O, Electronic Marshalling LEARNING OBJECTIVES
Learn how Universal I/O can simplify field wiring.
Learn how Universal I/O can save engineers unnecessary effort and planning.
Learn how engineers can reduce programming needs with Universal I/O.
ONLINE https://www.controleng. com/articles/how-smart-i-oenhances-distributed-control/ CONSIDER THIS
How could Universal I/O optimize your operation?
Benjamin Langton, Interstates
It is important to understand what proportional-integral-derivative (PID) control is and the parameters for closedloop, open-loop and cascading loops and the parameters involved.
Tuning a control loop is a complex activity driven by relatively simple control laws. The objective is to orchestrate one or more of the parameters to yield a process that is stable within specified boundaries. This guide is a primer on the process of tuning a proportional-integral-derivative (PID) control loop.
PID control is based on feedback. The output of a device or process is measured and compared with the target or set point. If a difference is detected, a correction is calculated and applied. The output is measured again, and any required correction is recalculated.
which looks at the rate of change being achieved, progressively modifying the correction factor to lessen its effect as the set point is approached. Every process has unique characteristics, even when the equipment is essentially identical. Airflow around ovens will vary, ambient temperatures will alter fluid density and viscosity, and barometric pressure will change from hour to hour. The PID settings (principally, the gain applied to the correction factor along with the time used in the integral and derivative calculations, termed “reset” and “rate”) must be selected to suit these local differences. It may be beneficial to assign the processes to four broad groups:
• Fast loops, such as flow and pressure
• Slow loops, such as temperature
• Integrating processes, such as level and insulated temperature
• Noisy loops, where the measurement is constantly changing.
Online controleng.com
KEYWORDS: PID, proportional-integralderivative, control loop
LEARNING OBJECTIVES
Understand the fundamentals of proportional-integralderivative (PID) tuning and what each element is used for.
Learn how to set PID tuning parameters.
Know the difference between closed-loop and open-loop tuning procedures and where they are best-suited.
CONSIDER THIS
What role does PID tuning play in your facility?
Not every controller uses all three of the mathematical functions in PID. Many processes can be handled to an acceptable level with just the proportional-integral terms. However, fine control, and especially overshoot avoidance, requires the addition of derivative control.
In proportional control, the correction factor is determined by the size of the difference between the set point and the measured value. The problem is that as the difference approaches zero, so does the correction, with the result that the error never goes to zero.
The integral function addresses this problem by considering the cumulative value of the error. The longer the set point-to-actual value difference persists, the greater the correction factor calculated. However, when there is a delay in the response to the correction, this leads to an overshoot and possibly oscillation about the set point. Avoiding this outcome is the purpose of the derivative function,
The first step of tuning a closed loop is to understand the process. Identify the loop that needs tuning and determine the speed of the loop. If the loop has a response time from less than one second to about 10 seconds, the loop is fast, and using a PI controller should be sufficient. If the loop has a response time of several seconds up to about 30 seconds, choose a PI or PID controller. For slow loops with a response time of more than 30 seconds, using a PID controller is recommended.
The second step is to understand the controller. The proportional term could be either a proportional gain or a proportional band. The integral term can be a time constant, a reset rate, or an integral gain (reset rate times proportional gain). The derivative term can be a time constant or a derivative gain (derivative time constant times proportional gain). For this tutorial, proportional gain,
integral reset rate, and derivative gain are assumed. The final step is to watch for a response. Begin by making a small change of set point (less than 5%) or wait for a disturbance in the process. Then watch the process variable and control output response.
• If there is no instantaneous change of the control output or there is no apparent overshoot, increase the proportional gain by 50%.
• If the process variable is unstable or has a sustained oscillation with an overshoot greater than 25%, reduce the proportional gain by 50% and the integral reset rate by 50%.
• If the process variable oscillation persists with tolerable overshoot, reduce the proportional gain by 20% and the integral reset rate by 50%.
• If three or more consecutive peaks occur upon the set point change, reduce the integral reset rate by 30% and increase the derivative gain by 50%.
• If the process variable stays relatively flat and around the set point for a long time after changing the set point or the beginning of a disturbance, increase the integral reset rate by 100%.
• Repeat the above steps until the closed-loop response is satisfactory.
Similar to the closed-loop procedure, begin by knowing the process and controller. For non-integrating loops, use the following process:
• Put the loop in manual control mode, keep the control output constant, and wait for the process to stabilize.
• Make a small step change on the control output (less than 10%) and watch the response.
• Estimate the process model where: –Model gain is equal to the process variable divided by the control output change. –Deadtime is equal to the time lapse between the change of the control output and observable changes on the process variable. –Time constant is equal to the time it takes for the process variable to reach about 63% of the total changes.
• Select the initial PID values such that: –P equals 2 divided by the model gain. –I equals deadtime plus the time constant. –D equals either deadtime divided by 3 or time constant divided by 6.
• These initial PID values should provide a reasonable closed-loop response. Fine-tune the controller by using the closed-loop tuning method.
For cascaded control applications, such as a tank heated by a steam valve, the tuning procedure begins with the inner loop followed by the outer loop. You need to tune one loop at a time due to the interaction of the inner loop dynamics on the outer loop.
• Put the outer loop in manual.
• Do a closed-loop tuning procedure on the inner loop, then put the inner loop in auto.
• Wait for the outer loop to stabilize.
• Do a closed-loop tuning procedure on the outer loop.
PID controllers are typically used in automatic process control applications in the industry to regulate flow, temperature, pressure, level and other process variables. Proportional and integral controllers are essential for most control loops; the derivative mode is often used for motion control. Temperature control often uses all three control modes. ce
Benjamin Langton is senior offer manager at Interstates, a CFE Media and Technology content partner. Edited by Chris Vavra, web content manager, Control Engineering, CFE Media and Technology, cvavra@cfemedia.com.
Adapted with permission of ControlSoft Inc. PID Loop Tuning Pocket Guide. Highland Heights, OH: ControlSoft, Inc., 2022. 6-9.
u
FIGURE: Non-integrating process model. Courtesy: ControlSoft Inc.
uProportional-integralderivative (PID) control is based on feedback with the output of a device or process measured and compared with the set point. This is a constant calculating process.
u PID loop tuning comes in many forms, and it is critical for the engineer to understand which loop tuning is needed for the application as well as the parameters required to help ensure accurate measurements are delivered.
The MIK-LWGY series liquid turbine flowmeter is a speed instrument, which has high accuracy, good repeatability, simple structure, small pressure loss and convenient maintenance. It is used to measure the volume flow of low viscosity liquids in closed pipes. It is ideal for the petroleum, chemical, metallurgy, water supply, paper and other industries and is useful for a wide range of applications. Specifications include: Pipe diameter DN4~DN200; 0.5%R, 1.0%R accuracy; 3.6V lithium battery; 12VDC; 24VDC power supply; IP65 ingress protection; 1.0MPa~6.3MPa pressure; -20 to 120℃ temperature; and Pulse, 4-20mA, RS485 Modbus output.
Meacon Automation, www.meacon.cn
The single axis robot KK Series, developed by TPA Robot, uses partially hardened U-shaped steel base track to significantly increase the robot’s strength and load capacity. To accommo-date different environments, TPA Robot offers three types of linear robot series; The KSR, KNR and KFR, which vary based on the type of cover used. For the return system between the track and the slider, the contact surface between the ball and the ball groove adopts a 2-row Goethe tooth design with a contact angle of 45 degrees.
TPA Robot, www.tparobot.com
AutomationDirect has added the next generation CPU for the Productivity2000 PLC line. The P2-622 CPU has the functionality of the original CPU including up to 50MB ladder memory, embedded OLED status display, remote I/O and multipurpose Ethernet 10/100Base-T (RJ45) ports and a microSD card slot. This new CPU has a lower cost, dual software-configurable serial ports (RJ12 and 4-pin) that support RS232 and RS485, a USB C programming port and a new system architecture that allows for many future enhancements.
AutomationDirect, www.automationdirect.com
The SolaHD SCM module brings network connectivity to its SDN-D high-performance DC power supply, enabling it to serve as an IIoT-ready device providing condition monitoring, asset tracking and quick troubleshooting in addition to serving as a power converter. Connecting the new SolaHD Communication Module (SCM) to an SDN-D power supply lets plant operators continuously monitor its diagnostics over standard EtherNet/IP (ODVA) or HART 7 protocols. Emerson, www.emerson.com
The high-performance Hyper-EHL board from ICP Germany is a cost-effective technology for applications requiring high reliability, such as industrial automation, machine control, traffic engineering and display systems. The Hyper-EHL board can be purchased with two Elkhard Lake CPUs: Variant one with Intel Celeron J6412 offers four processor cores, a base clock frequency of 2.00 GHz, 1.5 MB cache and an Intel processor graphics unit with 400 MHz, while variant two with Intel Celeron N6210 brings two processor cores, 1.20 GHz base clock frequency, 1.50 MB cache an Intel processor graphics unit with 250 MHz.
ICP Deutschland GmbH, www.icp-deutschland.de
Watson-Marlow Fluid Technology Solutions (WMFTS) now offers the Krohne Flexmag 4050 C electromagnetic flowmeter for biopharmaceutical customers. With the Krohne Flexmag 4050 C electromagnetic flowmeter, WMFTS customers can verify the accurate flow conditions of compatible Watson-Marlow pumps. The Krohne flowmeter is the first single-use electromagnetic flowmeter on the market. Unlike other single-use flowmeter technologies, such as those which use ultrasonic technology, the Krohne flowmeter provides accurate readings independent of pressure, temperature and viscosity of the fluid.
Watson-Marlow Fluid Technology Solutions, www.wmfts.com
The Westermo Lynx 3000 series has been designed to provide high levels of performance, reliability and security, with gigabit speeds and advanced functionality to support the requirements of current and future networks. The switches provides layer 2 and layer 3 functionality, enabling the management of complex ring networks and routing solutions. A wide range of models ensure suitability for many use cases, including applications requiring very high performance. With entry-level models optimized for Fast Ethernet application and variants supporting up to 2.5 gigabit speeds, the series is ideal for handling big data, high bandwidth and mission-critical applications. The Westermo WeOS operating system powers the switches. Westermo, www.westermo.us
As industrial laser implementations continue to increase in precision manufacturing applications, reliability and consistency are essential. To help meet application power needs, ABB Power Conversion offers a new liquid-cooled, three-phase, 75V rectifier, the CC7500. Designed for heavy pulse-load applications such as industrial lasers, the rectifier provides the consistent, dependable power needed for precision manufacturing processes. The latest addition to ABB’s CC-series rectifiers, the CC7500 features a low-line 200/208/240VAC input.
ABB Power Conversion, www.abbpowerconversion.com
In the extreme heat environments, a personal computer to monitor process applications can be a recipe for failure. The new Fluke Process Instruments ThermoView TV30 thermal camera enables industrial teams to set up thermal imaging systems without constraints of being connected to a vulnerable computer. The rugged, fixed-installation TV30 measures a wide temperature range from -10 °C to 1300 °C (14 °F to 2372 °F) and provides an unrivaled scope of features and functions. The stand-alone camera provides full connectivity for integration with a PLC via open platform communications unified architecture (OPC UA), or MQ telemetry transport (MQTT). Fluke Corp., www.fluke.com
Nanotec introduced a new controller for integration into devices: the NP5 plug-in motor controller, which is suitable for brushless DC motors (BLDC) as well as for stepper motors. A PCI Express connector allows for rapid and intuitive integration into a customer-specific board, thus offering a compact option that reduces the wiring effort, particularly for multi-axis applications. The motor controller is a fieldbus-capable controller/drive for small BLDC and stepper motors. By means of a PCI Express connector, this plug-in controller can be integrated in a customer-specific board quickly. It provides a compact option for multi-axis applications and reduces the wiring effort. Nanotec Electronic, www.us.nanotec.com
See more New Products for Engineers www.controleng.com/NPE
Circor International Inc., a manufacturer and marketer of differentiated technology products and sub-systems, continuously enhances the digital experience of its consumers by updating its CIRCORSmart app. This app provides a broad range of capabilities, giving users secure, round-theclock access to critical technical information for over 860,000 products from any web-connected device. Updates expand functionality and number of products. A hydrogen ready check feature allows users to check if RTK valves are ready for the hydrogen fuel economy. Where applicable, find cover gaskets, spindle packing, cones, flange connections, seat rings and diaphragms for RTK valves, as well as potentiometer, transmitter and feedback modules.
Circor International Inc., www.circor.com
FMC240 Electromagnetic meters deliver the performance and precision your applications require. These meters are applicable for all conductive liquids, such as water, acids, alkalis, slurries and others. Typical applications are monitoring of liquids, filling, dosing and precise measurement in custody transfer. Other features include: Accuracy: ±0.5% (flow speed > 0.5m/s); theoretical value: Water: Min. 20μS/cm; Other liquid: Min. 5μS/cm; recommended value: 30μS/cm; and strong anti-interference ability. Under normal grounding conditions, the flow value can be displayed with stability.
Asmik Sensors, www.asmiktech.com
PROCESS SAFETY
Non-contacting radar level transmitters can help food manufacturers increase product quality, throughput and safety.
Automated level measurement solutions play an important role in enabling food manufacturers to achieve the production efficiency gains needed to maximize profitability and meet consumer demand. To help ensure that the most suitable level measurement technology is selected for an application, there are certain criteria that need to be considered.
Being able to continuously measure product level in storage, mixing and batch tanks as accurately and reliably as possible is crucial. Precise level measurements help to ensure consistent product quality, increase safety by protecting against overfills and dryrunning pumps, optimize tank utilization and inventory management, and reduce product waste and production costs.
as oil and gas, but have been considered too bulky and costly for food production. The latest instruments can meet food and beverage industry concerns about size and cost.
sensors and age applications can concerns cost.
Level measurement instruments must comply with hygiene and food safety standards and be compatible with process conditions, such as high temperatures, foam and turbulence, which can affect measurement accuracy. Devices need to be cost-effective, to help ensure a fast return on investment and should be easy to install and integrate into an automation system.
A broad range of technologies can provide continuous level measurements, including differential pressure transmitters, capacitance probes and ultrasonic transmitters. While these technologies are relatively inexpensive, disadvantages can include calibration requirements, which increases complexity; being in contact with the product, creating a food safety risk; and being susceptible to changes in process conditions, such as density and temperature affecting measurement accuracy.
Non-contacting radar level transmitters provide some significant advantages when compared to other technology options. They are top-mounted and do not touch the product surface, minimizing contamination risk; changes in product density, viscosity and temperature do not affect accuracy. Frequency modulated continuous wave (FMCW) technology and smart algorithms maximize measurement accuracy and reliability, even when used in space-constrained skids and challenging, fast-filling vessels. They do not require calibration and have minimal maintenance requirements with no moving parts. Radar level sensors have served in safety-critical industries, such
Radar transmitters rely on reflected signals, known as echoes, to perform level measurements. The latest non-contacting level devices use fast sweep technology to provide a continuous echo against the product surface. This enables them to collect up to 40 times more information than legacy instruments, which makes measurements more accurate. Maintaining precise control of product levels in storage tanks helps to keep processes running smoothly and avoids product wastage. Another challenge is to maximize tank utilization. The latest non-contacting radar level transmitters can measure accurately to the top of the tank.
Level measurement devices face a range of challenges in mixing and blending applications, including turbulence, foam, and obstacles such as agitators in the tank. To meet these challenges, the latest non-contacting radar level transmitters use 80 GHz FMCW technology on one electronic chip with embedded smart algorithms. This enables exceptional radar beam focusing, so tank obstructions can be avoided and greater measurement accuracy and reliability achieved.
The latest non-contacting radar devices are IP69-rated and have been designed with robust, easy to clean and food-graded wetted parts, so that performance is unaffected during cleanin-place and sterilize-in-place processes. ce
Felix Glans is a solutions manager for Emerson’s radar level business. This originally appeared on Control Engineering Europe's website. Edited by Chris Vavra, web content manager, cvavra@cfemedia.com.
https://www.controleng. com/processinstrumentation-sensors/ process-safety/ Online controleng.com u
AutomationDirect .C2, 1 .www .automationdirect .com Beckhoff Automation LLC .2 .www .beckhoff .com
CALLING ALL SYSTEM INTEGRATORS… .16 www .controleng .com/events-and-awards/system-integrator-of-the-year-program/
DATAFORTH .48 .www .dataforth .com
Digi-Key ELECTRONICS .4 .WWW .DIGIKEY.COM
FIBERDYNE LABS, INC .46 .www .Fiberdyne .com
MSA Safety .6 .https://us .msasafety .com/fieldserver-energy-efficiency
Otek Corporation .10 .WWW .OTEKCORP.COM
ROCKWELL AUTOMATION .8 .https://info .mavtechglobal .com/cfe-wp-connection-lcs-gated
SEW-EURODRIVE, Inc C4 .www .seweurodrive .com
WAGO Corp .14 .www .wago .us
Yaskawa America, Inc .C3 .www .yaskawa .com
ContentStream
Patrick Lynch, Director of Content Marketing Solutions 630-571-4070 x2210
PLynch@CFEMedia.com
AR, IL, IN, IA, KS, KY, LA, MN, MO, MS, NE, ND, OK, OH, SD, TX, WI, Central Canada
Robert Levinger 630-571-4070 x2218 RLevinger@cfetechnology.com
AK, AZ, CA, CO, HI, ID, MT, NV, NM, OR, UT, WA, WY, Western Canada
Aaron Maassen 816-797-9969 AMaassen@CFEMedia.com
Jim Langhenry, Co-Founder/Publisher, CFE Media JLanghenry@CFEMedia.com
Steve Rourke, Co-Founder, CFE Media SRourke@CFEMedia.com
Courtney Murphy, Marketing Services Manager 630-229-3057 CMurphy@cfemedia.com
McKenzie Burns, Marketing and Events Manager mburns@cfemedia.com
Brian Gross, Marketing Consultant, Global SI Database 630-571-4070, x2217, BGross@CFEMedia.com
Michael Smith, Creative Director 630-779-8910, MSmith@CFEMedia.com
Paul Brouch, Director of Operations PBrouch@CFEMedia.com
Michael Rotz, Print Production Manager 717-422-3622 mike.rotz@frycomm.com
Maria Bartell, Account Director, Infogroup Targeting Solutions 847-378-2275, maria.bartell@infogroup.com
Rick Ellis, Audience Management Director 303-246-1250, REllis@CFEMedia.com
Letters to the editor: Please e-mail us your opinions to MHoske@CFEMedia.com or fax 630-214-4504. Letters should include name, company, and address, and may be edited.
Information: For a Media Kit or Editorial Calendar, go to www.controleng.com/mediainfo.
Marketing consultants: See ad index.
Custom reprints, electronic: Paul Brouch, PBrouch@CFEMedia.com
Eventually, the thoughts of a 3D printing pro move past mere length, width and depth to a more important fourth dimension: TIME.
Servo systems and motion controllers from Yaskawa reduce print time without sacrificing accuracy.
Put your machine light years ahead in speed, precision and reliability. Call Yaskawa today.
Stainless steel servos motors from SEW-EURODRIVE keep things moving wherever machines and systems are subject to particularly intensive cleaning. Whether used for material handling, intralogistics or sanitary applications, their hygienic properties, long operating life, and maintenance friendliness make them optimally suited in permanently wet environments like food and beverage and pharmaceutical industries.