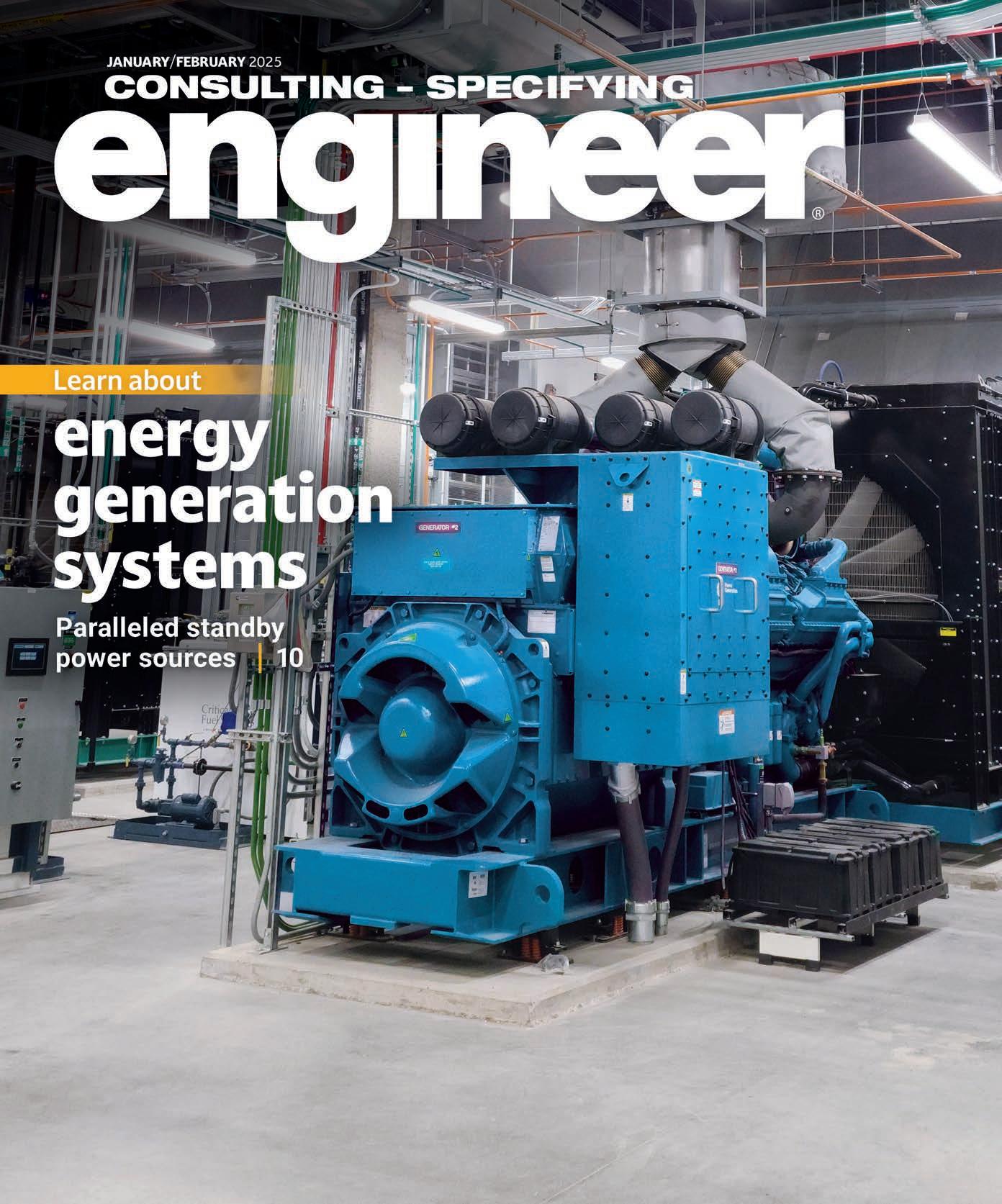
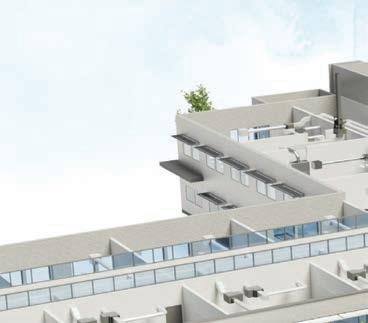
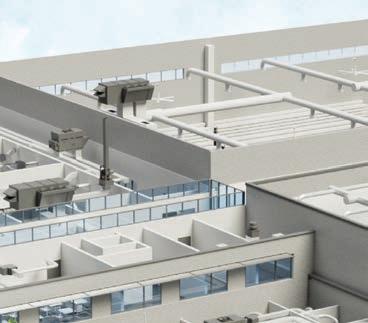
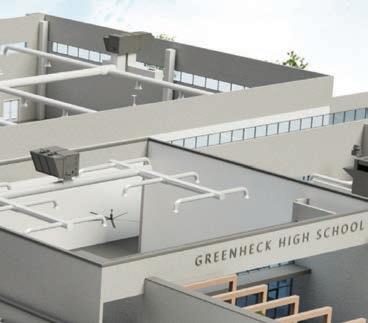

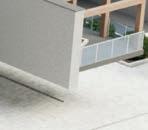
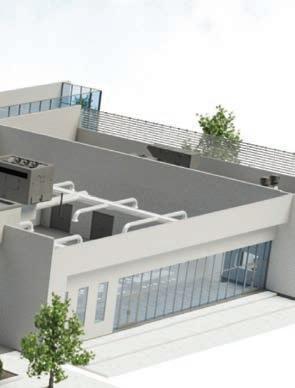
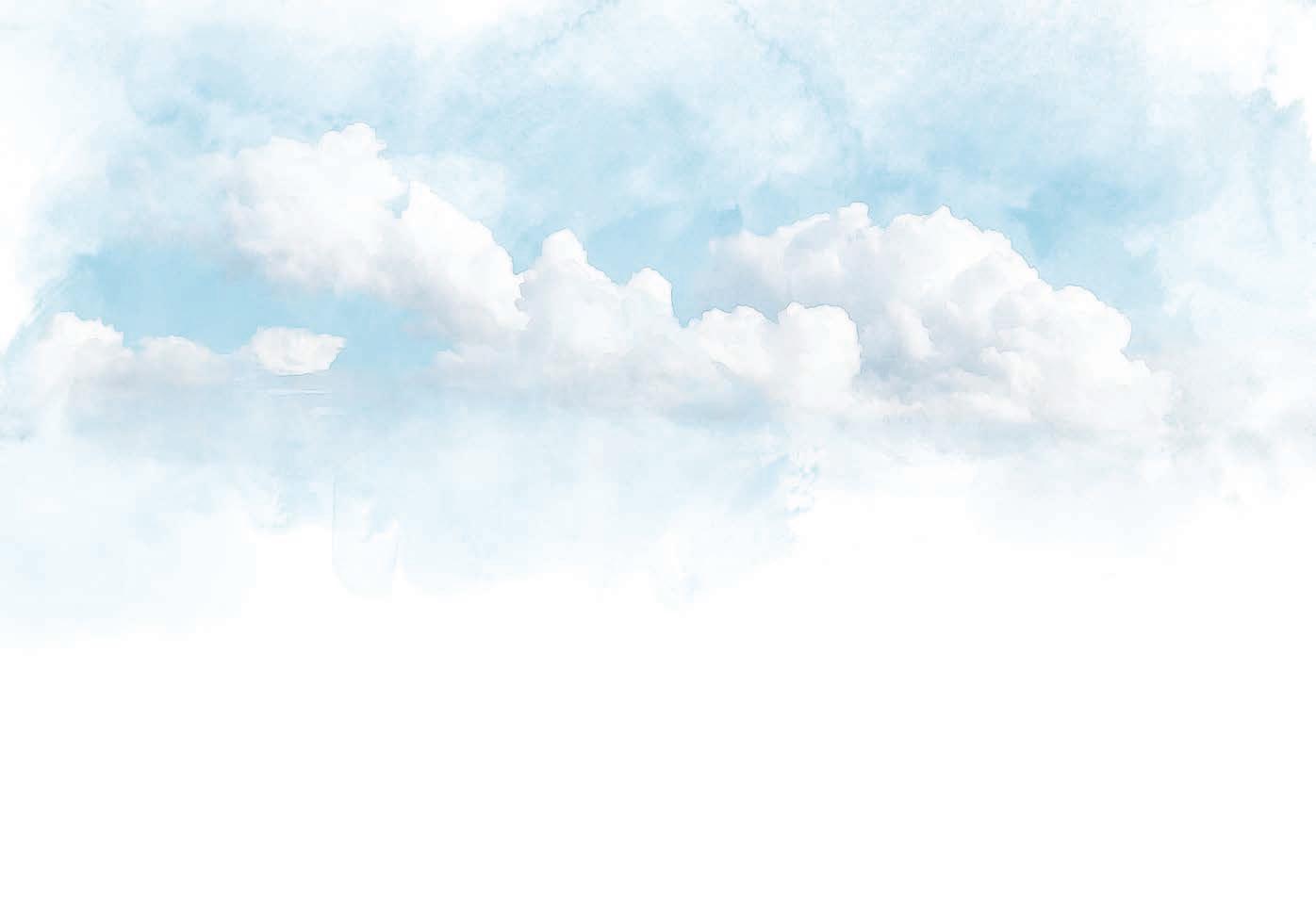

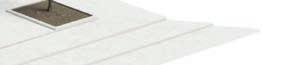
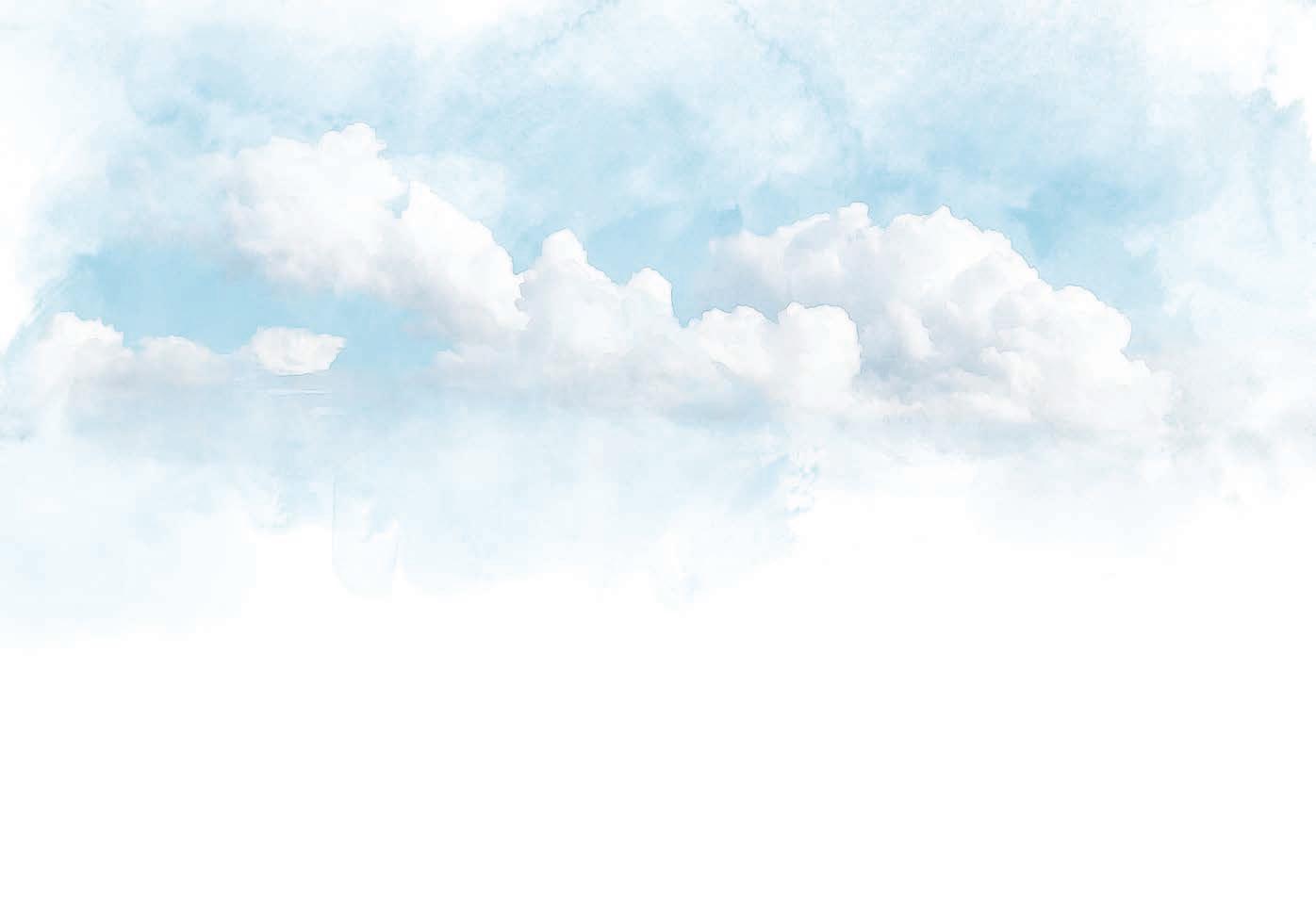
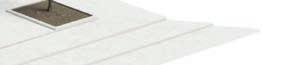
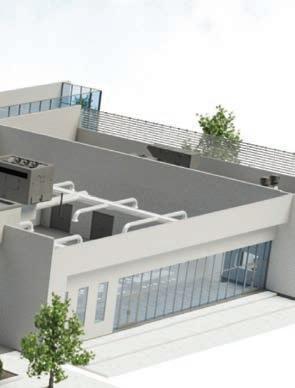
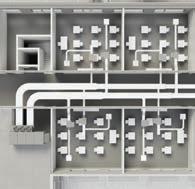
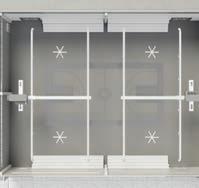
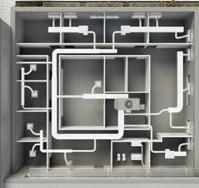


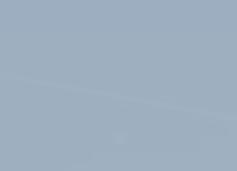

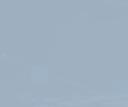







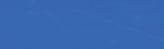
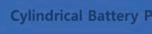


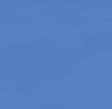
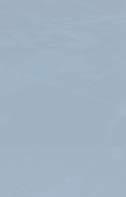

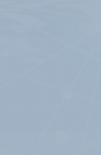

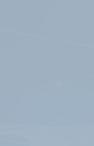

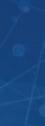



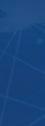


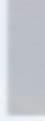

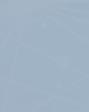


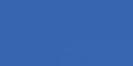

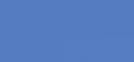

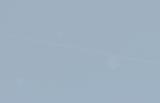


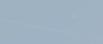
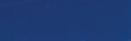


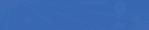
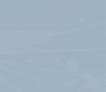

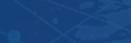

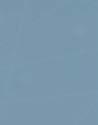




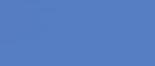
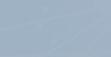
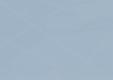






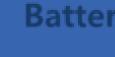











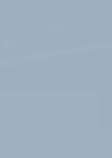







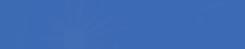
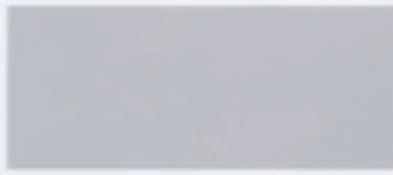
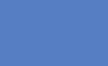

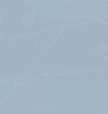
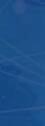




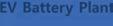

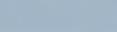

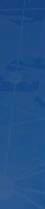
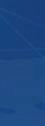










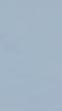




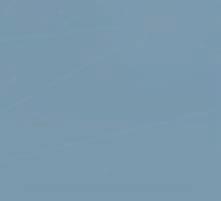




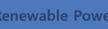



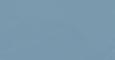
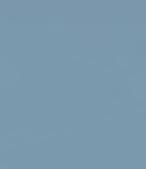








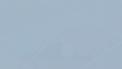
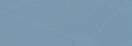









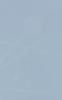



















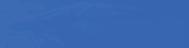









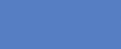




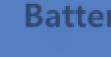

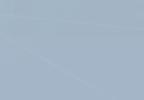







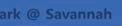







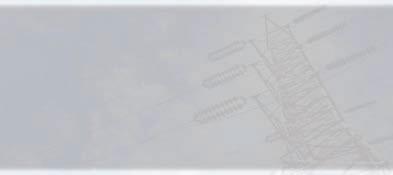
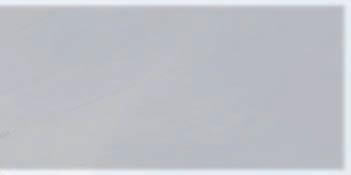
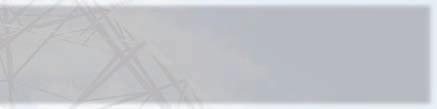
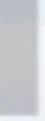
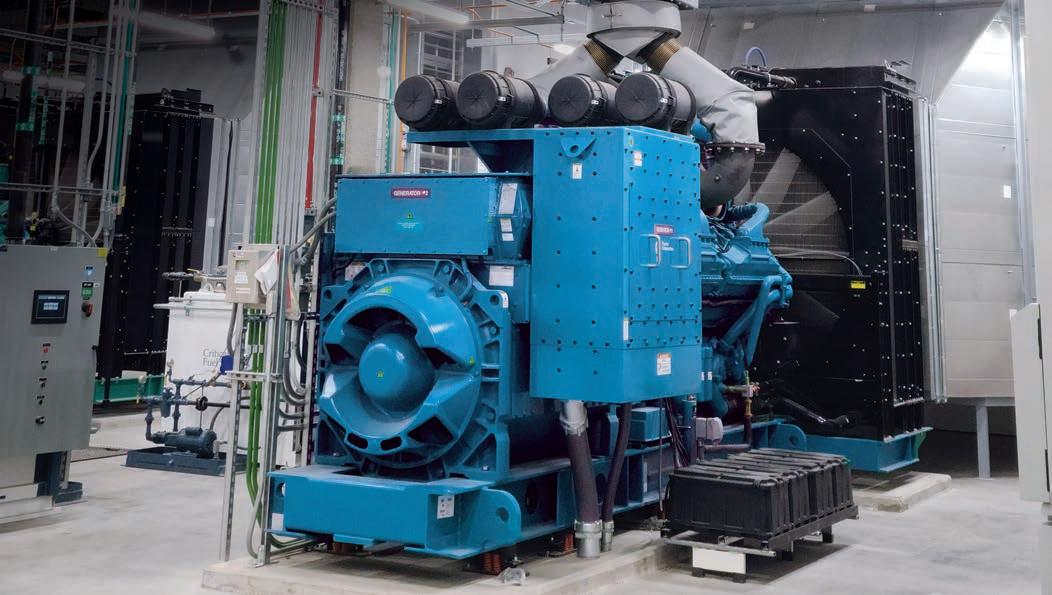
5 | How building integration is becoming a trend to watch
Integrating systems within MEP/FP design is no longer simply a trend, but a necessity.
6 | Salary survey: Respondents earned more this year than ever
Respondents to the 2024 salary survey were paid better, especially bonuses.
10 | The need for paralleled energy converter systems
Key factors to determine if energy generation systems should include paralleling.
16 | How to choose or troubleshoot a variable frequency drive
Proper VFD installation requires the right enclosure, voltage compatibility and more.
20 | Smar t buildings: From technology trends to strategic processes
Understand what current processes aren't working to design better smart buildings.
ON THE COVER: One of two medium-voltage generator sets serving as a Level 1 emergency power supply for a new 469,000square-foot hospital. Courtesy: IMEG
28 | Choosing a consultant, integrator or contractor for smart buildings
Navigate the smart building marketplace with this guide to consultants, integrators and contractors.
34 | Advanced HVAC control systems in commercial buildings
Advanced direct digital controls for HVAC systems offer improved climate management, energy costs and comfort.
38 | Building a workplace electrical safety program
Corporate electrical safety programs must be supported by leadership and understood by employees to be effective.
44 | Flexibility, sustainability and smar t technology in office building design
Office building design trends focus on
and smar t technologies.
$120/yr; Canada/Mexico, $150/yr (includes 7% GST, GST#123397457); International air delivery $260/yr. Except for special issues where price changes are
copies are
for $30 US and $35 foreign. Please address all subscription mail to CONSULTING-SPECIFYING ENGINEER, 1111 Superior Ave., Suite 2600, Cleveland, OH 44114. Printed in the USA. WTWH Media, LLC, does not assume and hereby disclaims any
to any
for any
or
caused by errors or omissions in the
contained herein, regardless of whether such errors result from negligence, accident or any other cause whatsoever.
for your next big high efficiency commercial heating application
Cascade up to 32 units and common vent up to 4 units for a wide range of heating outputs.
Patented Navien designed and built ASME-Certified “H” stamped stainless steel fire tube heat exchanger.
Intuitive 7" touch screen control for easy set up and diagnostics.
Built-in hardware for boiler pump, 3 heating zones or indirect tank control.
To learn more about all the big things happening at Navien, visit navieninc.com.
AMARA ROZGUS, Editor-in-Chief ARozgus@WTWHMedia.com
ANNA STEINGRUBER, Associate Editor ASteingruber@WTWHMedia.com
AMANDA PELLICCIONE, Marketing Research Manager APelliccione@WTWHMedia.com
MICHAEL SMITH, Art Director MSmith@WTWHMedia.com
DARREN BRUCE, PE, LEED AP BD+C, Director of Strategic Planning, Mid-Atlantic Region, NV5, Arlington, Va.
MICHAEL CHOW, PE, CEM, CXA, LEED AP BD+C, Principal, Metro CD Engineering LLC, Columbus, Ohio
CINDY COGIL, PE, FASHRAE, Vice President, SmithGroup, Chicago
TOM DIVINE, PE, Senior Electrical Engineer, Johnston, LLC, Houston
CORY DUGGIN, PE, LEED AP BD+C, BEMP, Energy Modeling Wizard, TLC Engineering Solutions, Brentwood, Tenn.
ROBERT J. GARRA JR., PE, CDT, Vice President, Electrical Engineer, CannonDesign, Grand Island, N.Y.
JASON GERKE, PE, LEED AP BD+C, CXA, Senior Design Phase Manager, JP Cullen, Milwaukee
JOSHUA D. GREENE, PE, Associate Principal, Simpson Gumpertz & Heger, Waltham, Mass.
RAYMOND GRILL, PE, FSFPE, LEED AP, Principal, Ray Grill Consulting, PLLC, Clifton, Va.
DANNA JENSEN, PE, LEED AP BD+C, Principal, Certus, Carrollton, Texas
WILLIAM KOFFEL, PE, FSFPE, President, Koffel Associates Inc., Columbia, Md.
WILLIAM KOSIK, PE, CEM, LEGACY LEED AP BD+C, Lead Senior Mechanical Engineer, kW Mission Critical Engineering/WSP, Milwaukee
KENNETH KUTSMEDA, PE, LEED AP, Engineering Manager, Jacobs, Philadelphia
DAVID LOWREY, Chief Fire Marshal, Boulder (Colo.) Fire Rescue
JASON MAJERUS, PE, CEM, LEED AP, Principal, DLR Group, Cleveland
JUSTIN MILNE, PE, PMP, Senior Engineer, Southcentral Region, Jensen Hughes, Allen, Texas
GREGORY QUINN, PE, NCEES, LEED AP, Principal, Health Care Market Leader, Affiliated Engineers Inc., Madison, Wis.
CRAIG ROBERTS, CEM, Account Executive, National Technical Services, McKinstry, Powell, Tenn.
SUNONDO ROY, PE, LEED AP, Director, Design Group, Romeoville, Ill.
JONATHAN SAJDAK, PE, Senior Associate/Fire Protection Engineer, Page, Houston
RANDY SCHRECENGOST, PE, CEM, Austin Operations Group Manager/Senior Mechanical Engineer, Stanley Consultants, Austin, Texas
MATT SHORT, PE, Project Manager/Mechanical Engineer, Smith Seckman Reid, Houston
MARIO VECCHIARELLO, PE, CEM, GBE, Senior Vice President, CDM Smith Inc., Boston
RICHARD VEDVIK, PE, Senior Electrical Engineer and Acoustics Engineer, IMEG Corp., Rock Island, Ill.
TOBY WHITE, PE, LEED AP, Associate, Boston Fire & Life Safety Leader, Arup, Boston
APRIL WOODS, PE, LEED AP BD+C, Vice President, WSP USA, Orlando, Fla.
JOHN YOON, PE, LEED AP ID+C, Lead Electrical Engineer, McGuire Engineers Inc., Chicago
Integrating systems within MEP/FP design is no longer simply a trend, but a necessity.
The engineering industry is at a crossroads in 2025, driven by the convergence of technology advancements, sustainability imperatives and a demand for integrated solutions. For mechanical, electrical and fire protection (MEP/FP) engineers, the ability to design and specify systems that communicate and collaborate seamlessly has shifted from a competitive advantage to a baseline expectation.
The integration of individual products and systems is the key to addressing energy efficiency, decarbonization and safety in modern commercial buildings.
Fire protection systems have historically operated independently of other building systems, but this siloed approach is changing. Integrated fire protection solutions now combine electrical and mechanical systems for enhanced safety and compliance. Smart sprinklers and smoke detectors linked to building automation systems can provide real-time alerts, activate ventilation systems to control smoke and ensure safe evacuation.
Editor-in-Chief
Case in point: Electrical systems are no longer standalone entities. They are increasingly intertwined with renewable energy sources, energy storage systems and smart technologies. For example, integrating electric vehicle charging infrastructure into power distribution systems has become a crucial step in meeting building sustainability goals.
For mechanical systems, integration is critical for advancing indoor air quality and decarbonization efforts. Heating, ventilation and air conditioning (HVAC) systems are increasingly reliant on sensors and automation to balance comfort, energy use and sustainability. For instance, real-time air quality monitoring systems that adjust ventilation rates based on occupancy and pollutant levels are becoming standard in commercial buildings.
While the U.S. is making progress in adopting integrated solutions, global leaders are setting benchmarks. European nations excel in energy-efficient building mandates, and Asian countries are leveraging artificial intelligence and smart technologies to revolutionize HVAC and energy systems. Engineers in the U.S. must learn from these examples, pushing for more ambitious integration standards.
As 2025 unfolds, integration is not just a trend but a necessity for MEP/ FP engineers. By embracing integrated solutions, engineers can deliver buildings that are energy-efficient, sustainable, safer and more adaptable. The question is not whether to integrate, but how effectively engineers can turn this vision into reality. cse
By Amara Rozgus, Editor-in-Chief, and Amanda Pelliccione, Marketing Research Manager
Respondents to the 2024 salary study were paid better, especially bonuses.
The 10th annual Consulting-Specifying Engineer salary survey of mechanical, electrical, fire protection and lighting engineers shows that the average base annual salary in 2023 was $118,310, an increase of 3.4% over 2022 data. More than half (62%) of this year’s respondents received a salary of more than $100,000.
Eight in 10 (84%) respondents reported their total compensation increased from 2022 to 2023. A third (38%) said the increase was up to 4%, 29% said 5% to 9%, and 17% said 10% or more.
About one in 10 (13%) reported no change in compensation.
The average base salary among engineering professionals has increased 19.3% between 2014 and 2023, according to the annual report. Average salaries rose from $99,100 in 2014 to $118,310 in 2023. Average nonsalary compensation has also increased by 89.3% since 2014, with a huge jump in 2023 bonuses. See Figure 1 for detail on how salaries have grown.
Nearly eight in 10 (77%) respondents received nonsalary compensation (e.g., bonus, profit sharing, stock shares) in 2023. The average amount received was $24,081.
From the 2023 study results, 29% are 60 or older, 21% are 50-59 years old, 19% are 40-49 years old and 20% are 30-39 years old. Only 11% are under 30 years old (see Figure 2).
Younger staff, defined by the U.S. Department of Labor as 40 or younger, equate to 31% — about the same as last year’s survey respondents, which reported 27% in this age group.
Challenges this year included:
• Changing client expectations and demands: 38%
• Pressure to reduce project timelines and costs: 37%
• Poor communication between consultants, architect, etc.: 26%
• Not enough junior team members to prepare for the future: 25%
• Not enough people working on a project: 22%
‘Those who specify fire protection/life safety systems made the most, making an average of $162,634.’
Total compensation went up in 2023 in both base salary and nonsalary compensation. Nonsalary compensation was awarded for two primary reasons:
• C ompany profitability: 52%, up from 48% last year.
• Personal performance or promotion: 45%, up from 41%.
When comparing compensation, the numbers changed again this year. Those who specify fire protection/life safety systems made the most, making an average of $162,634, a significant jump from $102,500. Electrical/power system designers came in second, earning $145,255, a slight decrease from $147,182. Mechanical engineers came in next, earning $134,458, an increase from $123,477. See Figure 3.
Most (59%) of respondents directly manage another employee, and 39% manage up to five people. And when asked about challenges, 17% said they didn’t receive enough training or mentoring. See the compensation tables for a more detailed breakdown. Download the full report online.
According to the survey, 10% of respondents are looking to change jobs in the next year and 24% aren’t sure, meaning about one-third of employees could be looking for a new position. A consistent two-thirds of respondents are not looking for a new job.
Though they aren’t looking for jobs, they are looking ahead to technologies that will significantly change their jobs. The top five responses:
FIGURE 2: As in years past, fire protection engineers made a lot of money. This year, responses from lighting designers seems skewed, with only a few respondents earning a big bonus. Courtesy: Consulting-Specifying Engineer
FIGURE 3: Most respondents fell in the middle of the age range, with 40% of respondents indicating they were between 40 and 60 years old. Courtesy: Consulting-Specifying Engineer
‘
Mechanical compensation (including HVAC,
• Artificial intelligence replacing human decision-making: 36%
• Shift toward sustainable and green building practices: 35%
• Difficulty keeping up with new technologies and software: 33%
• Rapid changes in building codes and regulations: 33%
• Cybersecurity threats to engineered systems and data: 30%
A survey was emailed to Consulting-Specifying Engineer audience members and information was collected in September and October 2024. A total of 261 qualified responses were returned, with a margin of error of +/-6.1% at a 95% confidence level. Participants frequently had the option to select more than one response, thus totals do not always equal 100%. cse
u Explore the 10th annual Consulting-Specifying Engineer salary survey to uncover key insights into compensation trends for mechanical, electrical, fire protection and lighting engineers, including a 3.4% rise in average base salary to $118,310 in 2023 and significant growth in nonsalary bonuses.
u Dive into the full report to understand how industry challenges, shifting demographics and emerging technologies are shaping the future of engineering careers — download it now for detailed data and analysis.
Addison solutions offer significant benefits for data centers. These include:
• Available in both Air-Source and Water-Source Heat Pump Configurations
• Adaptable for every application requiring dedicated outdoor air, mixed air, and dehumidification
• Supplies conditioned make-up air to replace exhaust air as well as outside air needed for occupants
• Modular Design
• Adaptable for every application requiring dedicated outdoor air, mixed air, or recirculation
• Available in both Air-Source and Water-Source heat pump applications
• Available with HybridAir Technology
• Dedicated Outdoor Air or Recirculating Cooling/Dehumidification Operation
• Optional Water-Source Heat Pump Operation
• Compact Design
• Compatible with every application requiring indoor units for ventilation, cooling and/or dehumidification
• Dedicated Outdoor Air or Recirculating Cooling/ Dehumidification Operation
• Optional Heat Pump Operation
• Modular Design - allows installation in tight spaces
• Ideal for every application requiring split systems for ventilation, cooling and/or dehumidification
• Downflow Air Tower available as a DX split system or a chilled-water AHU
Addison products excel in data centers for our unmatched reliability, efficiency and redundancy features. Engineered to maintain precise environmental conditions, Addison products ensure uninterrupted operation of sensitive equipment. Our customizable options make them the ideal choice for safeguarding critical infrastructure. Addison solutions also boast unbeatable 12-week lead times for standard products ensuring prompt deployment and minimal downtime for data center operations. www.addison-hvac.com/data-centers Stop by the Addison Booth at the AHR
Richard Vedvik PE, CHEPP, IMEG, Rock Island, Illinois
This article discusses the factors that designers can consider when determining if energy generation systems should include paralleling and what concepts can be part of the design.
The growing complexity and size of mission critical buildings, like hospitals, data centers and industrial plants, has driven an increased demand for large standby power systems. In many cases, paralleled generator systems provide a robust solution to meet these demands in lieu of a single, large generator system.
• Learn the options for paralleled standby power sources.
• Understand the features of energy converters.
• Know about space requirements, testing and other code-driven requirements for generators.
NFPA 110: Standard for Emergency and Standby Power Systems recognizes more options for designers, including fuel cell systems with a variety of approved fuel types. Multiple energy converters offer increased redundancy and the system can be designed to provide scalability and operational flexibility, ensuring minimal disruption to facility operations during maintenance or expansions.
Paralleled standby energy systems offer the ability to handle larger loads by combining the output of multiple sources. While this capability is essential in facilities where continuous power is critical to operations and any disruption could lead to risk to human life.
Hospitals, as regulated by NFPA 99: Health Care Facilities Code, require reliable backup power systems that ensure continued operation of life safety and critical care systems during a utility power outage. While standby power is required for mission critical facilities, there are other building types that can benefit from large standby energy systems.
One strong argument for standby power is when financial loss is a concern when utility power is lost. If a building is trying to remain operational during an extended outage, the designer and client should determine what building systems are required to remain online. When building heating and cooling systems are added to the system, the capacity requirements are increased.
One of the key advantages of parallel systems is their modularity. By paralleling energy sources, redundancy can be provided for the required branches while optional systems can also be brought online. Designers have the option to size the space and systems for future growth, allowing for initial installations to serve required loads initially. This is a common option when cost is a limiting factor, but the client wants future flexibility.
This also allows for additional energy sources as the facility grows or as demand increases.
Designing a system for scalability is recommended when long-term planning for universities, hospitals, manufacturing and data centers. Designers can further improve system resiliency by using a variety of standby energy sources, such as combining generator sets with fuel cells and battery systems. In paralleled systems, synchronization of the generators is what ensures a stable and reliable power supply through the ability to have N 1 sizing for emergency and critical loads. While serving a facility with one large generator and a temporary connection is a code-compliant solution, it’s rarely the preferred option due to a lack of redundancy and the hassle of renting a temporary generator for maintenance outages.
When designing a parallel standby energy system, it is critical to assess both the existing and future electrical load requirements. Facilities that frequently experience growth in power demand
‘If a building is trying to remain operational during an extended outage, the designer and client should determine what building systems are required to remain online.’
over time, due to expansions or increased reliance on technology, commonly need systems that are scalable.
As industry tackles the push to move buildings off fossil fuels and onto electrical systems for building conditioning, the impact to energy demands on heating systems will force massive changes to the sizing of associated electrical distribution. Where buildings either need or want the heating system to be on standby power, the impact to system design will be substantial. A recent study of a large health care campus revealed the need for 1,000 brake horsepower of heating, which would have required 10 megawatts of generator power if the heating plant moved from natural gas to electric. Many of the heating systems in the northern half of the
FIGURE 1: Mechanical penthouse in a new hospital with redundant equipment branch feeds for each air handling unit (AHU), allowing for 50% of the fans in each AHU to continue operation if one of the two equipment branches is taken out of service or fails for any reason. Courtesy: IMEG
2: Wiring inside large transfer switches requires coordination with the vendor to determine when rear access is required. Courtesy: IMEG
country are based on natural gas, requiring little electrical demand. As these systems are moved to electric, careful studies are required to evaluate the impact on the electrical systems feeding this equipment.
While paralleled energy storage systems offer numerous benefits, their successful implementation requires careful consideration of environmental and design factors. These factors include ventilation, fuel storage, noise control and location selection, all of which are essential to ensuring the long-term reliability and performance of the system.
The 2022 edition of NFPA 110 Chapter 7 outlines the specific environmental considerations that must be accounted for during the design phase, including the need for protection against natural disasters, such as flooding and wind damage. Designers should also be aware of possible damage from building system failures, such as sewer water backup, fire protection systems or firefighting efforts, which means drainage of the space must be a part of the design. This section of NFPA is not limited to energy storage systems but covers Level 1 and Level 2 emergency power supply system (EPSS) equipment, which includes transfer switches.
While it is not common to put generators in basements or below grade, it does exist. In some cases, generators may be located below grade to be physically hardened in areas where flooding is not a typical concern, but tornadoes are. Transfer switches and generator paralleling gear or distribution switchgear are commonly located in separate rooms and tend to be located in basements or lower levels. To comply with Chapter 7, designers should plan for a way to get water out of the room such that pumping systems are not required.
The requirement for airflow in the emergency power supply (EPS) room varies based on the type
‘In facilities with multiple generators, uneven airflow distribution can become a problem, leading to overheating and reduced performance. ’
of energy source. Exterior ventilation is a critical design element in generator rooms, particularly for paralleled systems where multiple generators operate simultaneously. Generators produce significant heat during operation and without adequate radiator airflow, their rated output can be severely affected.
According to NFPA 110 Section 7.7, the airflow requirements for generator rooms must be calculated based on the rating, placement and quantity of units. This includes ensuring that intake air pathways are properly sized and positioned to deliver sufficient combustion air and cooling air.
When fuel cells are used, the manufacturer will have recommended temperature ranges that may force the designer to provide cooling systems. Redundancy and scalability of the heating, ventilation and air conditioning (HVAC) system is just as important as the capacity of the system for indoor energy storage and converter systems. Further requirements exist based on the type of fuel being stored in the room.
In facilities with multiple generators, uneven airflow distribution can become a problem, leading to overheating and reduced performance in some units. To prevent this, engineers must design intake and exhaust systems that provide uniform airflow across all generators. This requires coordination with the architectural design team for roof access or exterior wall access and sometimes remote-mounted radiators are needed.
The benefit of a remote radiator is a reduced risk of pulling precipitation or debris into the EPS room. The downside is a potential failure point for the power source of the remote radiator fan. One solution is to power the radiator fan directly from the generator output lugs, so there is no delay in power delivery, in lieu of powering through a transfer switch.
In colder climates, it may be necessary to install heating systems and heat-traced drains to prevent snow and ice from accumulating in air intakes. It is a requirement of 2022 NFPA Chapter 7.7.6 for exterior generators in cold climates to include unit heaters for the enclosure, engine block heaters and battery warmers.
Noise and vibration are common byproducts of generator operation, especially in paralleled systems where multiple units operate at the same time. Excessive noise can disrupt facility occupants, particularly in health care environments where Facility Guidelines Institute sets limits on maximum noise levels in occupied spaces. To address this issue, engineers typically conduct acoustic studies to determine the acceptable noise levels and implement noise abatement strategies accordingly.
The primary sources of noise in generator systems are the radiator fans, exhaust systems and generators. Vibration is another concern, particularly when generators are installed within the building. In such cases, isolation springs and rubber mounts are used on connected piping and conduit to reduce the transmission of vibrations to the building’s structure.
The use of acoustic louvers and sound attenuators is also recommended in environments where
site noise control is a concern. When properly designed, these systems not only help maintain the desired airflow, as discussed previously, but help ensure compliance with local noise ordinances. For indoor installations, particularly in multistory buildings, the routing of exhaust piping must be carefully designed to minimize heat and noise concerns within the building.
The proximity of generator exhaust outlets to building air intakes should also be studied to avoid the recirculation of exhaust fumes into the facility’s HVAC systems. While not common, adding sound absorption on generator room walls can help control the overall noise level in that space and adjacent spaces.
Noise control also extends to the placement of the generators themselves. NFPA 110 recommends that generator systems be located away from occupied areas whenever possible. For outdoor installations, this may involve positioning generators at a distance from the main facility, which presents challenges for feeder design and increased feeder costs. All generator location designs should consider noise to neighborhoods, residences and adjacent properties.
Fuel storage of standby energy storage systems is yet another important design aspect. The
2022 edition of NFPA 110 Chapter 4.2 specifies Class of emergency power supply systems, which determines runtime, with minimum requirements varying based on the type of facility. For health care facilities, NFPA 99 mandates that emergency power systems maintain a minimum of 24 hours of runtime on-site, with a plan to keep the system online for 96 hours, to ensure continuous operation during extended outages, which is a Class X classification.
Designing fuel storage systems for paralleled generator systems presents unique challenges. In addition to the storage capacity requirements, designers must ensure that the fuel supply lines are routed properly to prevent leaks or blockages. Ideally, fuel return piping should be arranged to allow for gravity drainage, which reduces the need for pumps and solenoid valves.
In facilities where fuel storage is shared with other systems, such as heating boilers, designers must take care to ensure that the generator system’s fuel supply does not interfere with the operation of other systems that rely on the same fuel supply. When expanding the system capacity, designers must evaluate how runtime is impacted as energy production is increased.
In some cases, particularly in regions prone to natural disasters, it may be necessary to install
larger fuel storage tanks capable of holding several days’ worth of fuel. These tanks may be located underground or aboveground, depending on the site’s physical constraints and the client’s preference. To ensure fuel quality over long periods of storage, the designer can incorporate fuel polishing systems to keep the fuel clean by removing water, contaminants and prevent degradation. These systems are particularly important in disaster-prone areas, where emergency fuel supplies must be maintained for extended periods without the possibility of refueling. Refueling locations should be considered, ensuring that in areas where standby power systems are elevated to protect from flooding, the refueling location is also elevated.
The final component of any energy storage or production system design is the commissioning process, which ensures that all systems function as expected before the system is put into full operation. While designers may expect specifications to cover the requirement for functionality, a full commissioning effort will far exceed anything the specifications would cover while ensuring all aspects of the system function, including testing all programmed delays. NFPA 110 emphasizes the impor-
tance of commissioning and routine testing for emergency power systems, particularly in mission critical environments where system failure could have impactful consequences.
Commissioning a paralleled generator system involves a comprehensive series of tests designed to verify the system’s performance under various operating conditions. These tests typically begin with a full load test, during which the generators are run at maximum capacity to ensure that they can handle the facility’s peak power demands. The system’s automatic transfer switches (ATS) also are tested to ensure that they can seamlessly switch between the normal utility power source and the emergency generators without interrupting operations.
During commissioning, the parallel controls are tested to ensure that the generators can start, stop and synchronize correctly under load. The system is also tested for redundancy, ensuring that if one generator fails, the remaining units can continue to supply power. Manual controls should be tested to verify that facility personnel can operate the system manually in the event of an automation failure. This experiment should be documented and the procedure for manual paralleling should be available to authorized facility staff. Posting this information on the face of the paralleling gear is a recommended process, since access to the EPSS room should already be restricted to authorized personnel.
Routine testing and maintenance are equally important to ensuring the long-term reliability of paralleled generator systems. NFPA 110 mandates regular inspections and testing, including monthly load bank tests and annual full-load tests. These tests help identify potential issues before they lead to system failures, such as fuel contamination or battery degradation. Parallel systems offer the added benefit of allowing maintenance to be performed on individual generators without taking the entire system offline, which is particularly important in facilities that must always remain operational.
Regular maintenance is crucial for the longterm reliability of paralleled generator systems. NFPA 110 requires that all components of the sys-
tem, including the generators, fuel systems, batteries and ATS, be inspected and tested on a regular basis. One of the primary benefits of parallel systems is that maintenance can often be performed without interrupting the facility’s operations. Because parallel generators provide built-in redundancy, individual units can be taken offline for maintenance while the remaining generators continue to supply power.
Maintenance routines typically include checks of fuel quality, battery condition and generator performance under load. Fuel systems require regular inspection to ensure that fuel lines are clear and that tanks are free of contaminants. Fuel polishing systems are often used to maintain fuel quality, particularly in facilities that store large quantities of fuel for disaster preparedness. Battery testing is another critical component of maintenance, as battery failure is one of the leading causes of generator start-up issues.
In mission critical environments, it is important to develop a maintenance schedule that aligns with the facility’s operational needs. For example, maintenance is often performed during off-peak hours or in conjunction with scheduled power outages to minimize disruption to the facility operation. By carefully planning maintenance activities and using the redundancy provided by parallel systems, facility operators can ensure that their emergency power systems always remain operational. cse
Richard Vedvik PE, CHEPP, is a senior electrical engineer and acoustic engineer with IMEG. He is a member of the Consulting-Specifying Engineer editorial advisory board.
FIGURE 5: A unit substation with an oil-filled transformer is used to step-down from medium voltage generators to feed the emergency side of 480/277 V transfer switches. Courtesy: IMEG
csemag.com
Energy and power insights
u Paralleled standby power systems are increasingly favored for mission critical facilities, such as hospitals and data centers, due to their modularity, scalability and enhanced redundancy, allowing for seamless energy load management and future growth.
u These systems, guided by NFPA standards, address critical considerations like fuel storage, ventilation, noise control and maintenance, ensuring reliable performance while minimizing disruptions and adapting to evolving energy demands.
Tony Gabriele, Yaskawa, Armstrong Creek, Wisconsin
Proper VFD installation requires selecting the right enclosure, ensuring voltage compatibility, addressing harmonics and mitigating common faults for optimal performance and longevity.
While location is essential to any real estate transaction, you could also apply this requirement to a variable frequency drive (VFD) installation. Selecting the appropriate enclosure for the VFD location will provide the best opportunity for long life. There are four primary enclosure types for both indoor and outdoor applications. Types 1 and 12 fall into the indoor category. Type 3R and Type 4X are the outdoor category.
When specifying VFDs indoors, consider the surrounding environment.
• Is it clean and conditioned air?
• Discover how to choose or troubleshoot a variable frequency drive (VFD).
• Learn about the VFD installation environment, input power and VFD ratings versus motor requirements.
• Understand protection devices and other options.
• Is it a dusty manufacturing environment?
• What is the ambient temperature?
enclosure would be appropriate for an indoor area with dripping water or dust — think mechanical room or manufacturing environment with mist spray, dust or other airborne contaminants. The Type 12 enclosure will have filtered ventilation. Types 3R and 4X would be appropriate for an outdoor application where exposure to rain, snow, ice and other precipitation will occur.
Outdoor enclosures will have filtered ventilation and sometimes include a space heater to prevent the formation of condensation. Consider the addition of a space heater in an outdoor application; this small investment upfront that may save the facility manager a big headache down the road. Type 3R is suitable for most outdoor applications. Type 4X can be designed as a totally enclosed with an air conditioner to remove enclosure heat. Type 4X or stainless steel
• Are there chilled water pipes overhead that are sweating and dripping water?
A clean and conditioned environment would be appropriate for a Type 1 enclosure. A Type 12
FIGURE 1: Type 1 and 12 enclosures are typically used for indoor installations. Courtesy: Yaskawa
would be ideal if the enclosure was exposed to corrosive elements. Always consider the cost of Type 4X as it could be multiples higher than a comparable Type 3R.
Most VFDs are rated for sustained maximum output current at 104°F. If the location could exceed this ambient temperature, confirm the manufacturer’s de-rated amperage for higher ambient temperatures. Engineers may have to oversize the VFD for higher ambient temperatures.
Before a building owner installs or powers up a VFD, be sure to check the nameplate data and confirm the voltage to be applied is appropriate. Many VFDs have been damaged on power up because the wrong voltage was applied. Verify all three phases are present or, if single phasing (yes, you can apply single phase power to a standard 6-pulse VFD and generate 3-phase output) that the proper de-rate is applied.
Most populated areas will have clean and true 3-phase power. Outside of major metropolitan areas, power quality may not be as high as expected. Open delta systems are more common in rural areas and may present problems that are beyond the scope of this article. VFD de-rating may be required.
Be sure to confirm motor horsepower (hp) and full-load amps (FLA) and select the appropriate VFD size. The VFD rated output current must meet or exceed the motor FLA. Most motors will have a NFPA 70: National Electrical Code (NEC) amperage to horsepower ratio that will allow for sizing based on horsepower. And most fan or pump applications will use a 2- or 4-pole motor, which is more likely to have common NEC horsepower/amperage ratings. Industrial applications that require more torque may use a 6-pole motor and may have higher FLA requirements versus NEC ratings. If this is the case, consider upsizing the VFD to achieve maximum motor speed under full load.
Some VFD manufacturers may indicate a specific short-circuit current rating (SCCR) or kilo ampere interrupting capacity (kAIC), typically between 65 and 100 kAIC. But to attain this specific level, you must specify upstream branch circuit protection. Circuit breakers and/or fuses are installed upstream of the VFD and will interrupt the power in the event of a phase-to-phase or phase-to-ground short circuit. These components and specific SCCR/kAIC requirements exist to lower the risk of an arc flash. Always refer to the manufacturer’s literature to confirm a suitable branch circuit protection for a specific application.
FIGURE 2: Type 3R and 4X are typically used for outdoor installations. Courtesy: Yaskawa
The most common type of VFD design is often referred to as a 6-pulse VFD. The 6-pulse VFD has three main parts:
• The input diode bridge, the rectifier where alternating current (ac)-to-direct current (dc) conversion occurs
• The dc bus capacitor bank
• The output transistors or inverter
The power conversion process on a 6-pulse drive may create harmonics (voltage or current distortion) that could adversely affect operation of other equipment on the power system or standby generators. Devices such as reactors or chokes, which add impedance and smooth out the current draw from the VFD rectifier, will help to reduce harmonics and are sometimes built into the VFD in the dc bus circuit. If harmonics are of concern, such as might be the case in a hospital or airport, proper selection in the preliminary stages of a project is very important. VFDs with direct ac-to-ac conversion and other lower harmonic options are available for these situations.
One common fault is an over-voltage. An over-voltage refers to the dc bus voltage exceeding a defined level. The drive disengages motor control and faults out when the dc bus voltage rises too high. Let’s tie some of the information presented earlier together to help you understand how a 6-pulse VFD works. The input diodes pass the current to keep the dc bus level charged and stable. As the output transistor switches on and off rapidly, creating a simulated ac sinewave, the motor shaft will begin to turn.
‘Before a building owner installs or powers up a VFD, be sure to check the nameplate data and confirm the voltage to be applied is appropriate.’
FIGURE 3: Harmonic performance can affect how you choose to set up your variable frequency drive (VFD).
Courtesy: Yaskawa
FIGURE 4: Example of motor nameplate data.
Courtesy: Yaskawa
csemag.com
VFD insights
uLocation considerations are important when it comes to choosing the proper variable frequency drive (VFD).
uConfirming the proper voltage for a VFD is critical before powering it up.
uMotor horsepower and full load amps should be taken into consideration before selecting a VFD.
A common condition is a regenerative load. Environmental conditions like wind or equipment like additional fans in a plenum may turn the motor shaft faster than the VFD output frequency. If the motor shaft exceeds the rotational magnetic field created by the motor stator the motor has now become a generator. Excess power is now being funneled back to the dc bus through the flyback diodes that are part of the VFD output transistor circuit.
Think of the output side of the VFD as a two-way street. Power goes out but can also come back in.
The dc bus has a limited capacity and voltage rise will inevitably trip an over-voltage fault. Once the rotational magnetic field is lost, such as when output frequency ceases upon fault, the motor will freely spin.
Single-phase input is a viable option. Precise motor control is derived from high-speed switching of the transistors on the output side of the VFD that uses dc bus power. This conversion process isolates the ac line side from the output side. One caveat with single-phase input is that the VFD must be oversized due to the capacity of the dc bus to maintain a stable charge when under load. When one of three phases is eliminated feeding the VFD, the bus voltage will drop too quickly between the next phase. This creates a condition referred to as dc bus ripple, which could damage the capacitors if left unchecked. Most VFDs have a detection circuit to monitor dc bus ripple.
The suggestions only scratch the surface of troubleshooting VFDs. It’s critical to consult the technical information from the VFD manufacturer for specific product questions. cse
Tony Gabriele is an HVAC application engineer at Yaskawa.
Will Maxwell, SmartScore AP, Smith Seckman Reid, Inc. Nashville, Tenn. and David Stoller, FPC Global, Nashville, Tenn.
deliver the future of smart buildings, engineers need to recognize why current processes aren't working and what can be done differently.
In an era where innovation reshapes every facet of our lives, understanding the true essence of smart buildings—not merely as a collection of trendy technologies, but as a strategic process — is imperative for all stakeholders in the architecture, engineering and construction (AEC) industries.
The goal of this article is to explore the landscape of smart buildings. Not as a series of products that combine make a smart building, but a process that facilitates building smart, including market factors driving changes, the people involved, the value chain of the built environment as it stands in late 2024 and how to improve outcomes for everyone involved.
Before going into the specifics, it is important to take a step back and look at what is driving the demand for smart buildings. Innovations in the last 20 years have resulted in evolving industries worldwide, increased efficiency and radically redesigned operations and processes to account for all new technology. While these changes are evident in daily lives, the AEC industry has remained relatively unchanged.
A study from the University of Chicago commissioned by the National Bureau of Economic Research found that the design and construction industry has lost productivity by an average of 1% every year since 1970. While it's impossible to identify a single reason for this loss, it's not unrealistic to consider that the radical changes in technology, building systems and the information technology (IT) landscape have contributed, due to the added complexity and need for extensive cross-discipline coordination. More specifically, the industry’s inability to effectively adapt, adopt, implement and utilize technology efficiently has been a contributing factor. A process exists that will deliver resilient, more efficient and “smart” buildings that realize the promises of recent innovations while reducing construction costs and timelines when managed correctly.
Real estate has always been about keeping up with the competition. When developers across sectors establish a differentiator, be it concierge services, keyless entry, fault detection or diagnostics, others are quick to adopt these features as well. Smart buildings are no different. The difference in smart buildings is that there is no single-point solution; they aren't an app or an analytics platform. They are simply the connected infrastructure, systems and applications a developer needs to achieve
specific goals. Those goals can be simple and single-use, or complex and multifaceted depending on their asset class or a developer’s strategy.
Who contributes to creating a smart building?
To better understand how this impacts design, it is necessary to understand how each person along the value chain is involved and impacted. Starting with the developer. There are two primary types of developments; build and hold or build and flip. Build and flip developers are focused on building an asset, getting tenants to lease the space and selling it to a real estate investment trust. They tend to be shortterm focused, which leads them to be less concerned with the full lifecycle of an asset’s performance. Build and hold developers, on the other hand, are committed to owning an asset for the long term. These developers are ultimately finance-focused and non-technical. They often do not know what the options for a building are or how they impact things in both the short or long term.
On the design side, the primary stakeholders are architects, engineers and specialty consultants. Architects usually lead the process, often bringing in engineers as part of their teams. Consultants cover a broad range of scopes, including sustainability and smart building systems. These stakeholders are often under pressure to propose competitive fees to clients who may not fully understand what is needed to achieve their lofty goals. Design fees typically correlate to the perceived amount of effort and labor required, sometimes leading design professionals to complete their work quickly rather than delivering the best set of drawings.
Architects and engineers value creativity and innovation but are often hampered by financial constraints imposed by the developer. In most cases, unless the owner is specifically invested in innovation, the focus shifts to value engineering; the practice of minimizing costs while maintaining the overall function of the project. This approach can discourage risk-taking, as architects and engineers prioritize reducing rework and staying within budget over exploring new, potentially transformative ideas. Specialty consultants, such as those focused on sustainability or smart building systems, occupy a slightly different role. They are typically brought in either directly by the owner or through the architect to help the project achieve specific goals. However, when these consultants are not fully integrated with the design team, their ideas seldom are included in the final construction drawings and specifications. The lack of integration can hinder the overall effectiveness of the smart building solutions being proposed.
The general contractor’s focus is to finish a job under budget. This is often done through procurement. As most specifications are “performance” based, a general contractor will shop the market until they find the minimum viable product. These are systems that fit the letter of the requirements but may miss the intention and functionality of the design, particularly when integration is central to the design. When this becomes an issue during construction, the general contractor will point out that it meets specifications, the engineer is blamed, and the developer is then responsible for paying a change order. These issues are all too common but could be mitigated with proper processes that fill the gap.
FIGURE 2: A diagrammatic comparison of traditional building system silos and integrated operational technology networks. Courtesy: Smith Seckman Reid, Inc.
• Identify relevant stakeholders and responsibilities for successfully developing a smart building.
• Understand common terminology of smart buildings.
• Learn the economic impacts of adopting a smart building process.
‘After all, a building is only smart if it meets the needs of its specific users.’
One of the things holding back the smart building movement is a lack of agreement or understanding of the terminology being used. The most common complaint is that there is no standard definition for what makes a building “smart.” There are some groups, such as WiredScore or UL, who are trying to set standards for this through certifications. While this makes sense for some applications it would be more beneficial if mindsets were shifted from viewing smart buildings as a “product” to seeing them as a “process.” After all, a building is only smart if it meets the needs of its specific users.
The list below has some terms for which certain definitions are more commonly (although not entirely) accepted by the industry:
• Single pane of glass: An integrated control platform that allows all building systems to be viewed and controlled from a single application.
• Operational Technology (OT) - All networkable technologies that serve the operations of a building i.e., BAS, access control, lighting, etc.
• Internet of Things (IoT): Devices with sensors, processing ability, software and other technologies that connect and exchange data with other devices and systems over the internet or other communication networks.
• Converged infrastructure network: A centralized backbone that acts as a core network for all systems versus each sub-system running its own network.
• Independent data layer: A software solution that serves as a central systems integration hub that can connect different OT devices to each other and other IT or software solutions.
• Digital twin: A representation of an asset as either raw data or an image rendering. A digital twin can be used to model hypothetical changes to the system based on different variables.
• Fault detection and diagnostics: An application that leverages the connected infrastructure devices and systems to proactively identify prospective failures in a system.
The promise of smart or intelligent buildings has been around for decades, dating back to the first electronic control systems in the 20th century. Over time, new innovations such as digital direct
controls, the internet and machine learning have entered the market, each promising to revolutionize how we manage and interact with buildings. Most recently, the advent of the IoT and artificial intelligence has generated significant buzz around the potential for smart buildings to be more efficient, sustainable and user-friendly than ever before. Combined with the rapid advances in consumer technology, expectations are higher than ever for building systems to be smarter. Every developer working on a new project wants to be able to market the “building of the future” that will support them for decades to come.
Despite these high expectations, reality has often fallen short. Rather than seeing a new era of buildings that seamlessly integrate these technologies, we are faced with many of the same challenges that have plagued the industry for years. Vendor lock-in, where building owners are tied to specific vendors due to proprietary systems, is one of the most significant issues. This lack of standardization and open platforms results in increased costs and inefficiencies as owners are forced to rely on a single provider for upgrades, maintenance and support. Additionally, concerns about cybersecurity, data management and the shrinking pool of skilled labor capable of managing these systems have made the deployment of smart buildings more challenging than anticipated. Adding more solutions, vendors and consultants on top of a broken system will not fix it. A more holistic look at the building design process is the only way to truly achieve smart buildings.
When it comes to smart buildings, it's important to understand the relevant stakeholders that are involved and how they make money, this determines how they create value and what metrics are important to them regarding Smart Buildings. At the start of the value chain is the developer. The developer is ultimately a speculator who believes they can lease/sell a property for less than it buys, builds, operationalizes and finances it for. Developers are usually from the finance space and thus look at the world through the lens of what is called a proforma. A proforma is a financial model that quantifies every aspect of a project from inception to operationalization and onward into lifetime value creation. For the sake of our needs, a proforma only has metrics we can impact or be concerned
‘Starting at the beginning of the project lifecycle, there is a clear need to develop actual use cases for a project that will in turn dictate the technology or integrations.’
with, including construction costs, net operating income, capitalization rate and asset value. Construction cost is simply the combination of all costs to build an asset. Net operating income is the total revenue of a property minus the expenses. The capitalization rate is the rate at which an investment generates. A return and asset value is what the property is worth.
Within the construction industry, we are all too familiar with the constant drive to reduce construction costs. While saving money is important, when we put it in the context of a pro forma we can shift the mindset around cost-cutting and value engineering. Engineers must know how to shift the conversation away from the simple cost of one system or another to focus instead on the holistic value a system may bring. A prime example would be something like the power of Ethernet lighting systems. While the system may have a 20% premium versus a traditional system, the process of deploying that system does not require an electrician, is significantly faster and can be remotely commissioned. This saves on labor costs and construction timelines that far exceed the materials premium. It also reduces the overall load required for the overall projects. Communicating how a system holistically impacts a project in terms contractors, developers and building owners understand is instrumental to getting their buy-in.
As mentioned earlier, engineers have been incentivized by the existing value chain to not take risks or change the way they design building sys-
tems to minimize the time spent on each project. This often results in a copy and paste of performance specifications and general notes instead of making sure owners are getting the newest and best technologies in their buildings. A prime example of this would be controls. Control vendors, with a lack of pressure from the specifying engineers and owners to use open protocol platforms, install systems that only the controls company can service, so they can lock in long-term maintenance agreements. They see this as necessary to recoup the money they often lose on the installation to win the bid. Operating expenses, like service agreements, are often handled by different departments than the capital expenses in construction, so there is rarely someone involved in the construction process to advocate for the net savings of open-platform control systems.
IoT vendors are in a similar position, often requiring that their own proprietary gateways be used in order for their devices to function, so while an owner may have expected to purchase a system, they are instead locked into a software subscription to keep the gateways operational. The design team currently has little incentive to address these kinds of issues since there is a greater level of coordination needed to do so, but few owners are willing to pay for it simply because they don't understand the whole picture.
A major contributor to this situation is that as the industry has changed, some scope gaps have been created or expanded that need to be better
FIGURE 3: New roles in design and construction for smart buildings help create the highest quality outcome for all
involved.
Courtesy: Smith Seck-
man
Reid, Inc.
addressed, specifically around integration and controls. Starting at the beginning of the project lifecycle, there is a clear need to develop actual use cases for a project that will in turn dictate the technology or integrations. Developers, architects and engineers may attempt to fill this scope, but if a champion isn’t assigned to flesh out and track these use cases throughout design and construction, they are not likely to make it into the final product. At a more technical level, someone must be responsible for specifying the integrations, controls and other technology that will be used to satisfy the use cases. Engineers cover some of this scope, but few have the technical expertise or understanding of control systems and networks to fully address this gap. Instead, many rely on controls vendors or other solution providers to cover it during construction. Finally, the best-laid plans mean nothing if the contractor cannot implement them. Someone must be able to coordinate between all of the trades for the integration of their systems and few general contractors have the technical expertise needed.
For too long the answer when a client wanted a smart build was to recommend a phone application or double down on controls, and while those certainly can be components of a smart building, they are ultimately just point solutions. To deliver a smart building is not simply a matter of adding technology, it's updating the project delivery process. The breadth and depth of technology have expanded so much and so rapidly that it stretches the capacity of any existing stakeholder, most of whom are already responsible for a bevy of other deliverables. That is why engineers need to update our delivery process and include personnel who are solely responsible for the experiential, technological and connected solutions that are central to a modern building.
Three key roles that fills the gaps in the value chain and clarifies responsibilities are:
• The digital building consultant (DBC): This role is responsible for the development or use cases and their technological enablement requirements.
‘The
path to realizing true smart buildings requires a fundamental shift from viewing them as a collection of disconnected technologies and stakeholders to embracing a holistic, process-driven approach.
’
csemag.com
Smart building insights
u Smart buildings are best realized not as a collection of technologies, but as a process-driven approach that aligns all stakeholders to long-term operational goals and user needs.
u New roles like digital building consultants, master system planners and master system integrators help bridge coordination gaps and ensure the successful integration of smart building technologies.
They act as champions for the owner’s building technology program. They work closely with the client and other stakeholders to shepherd them through the process of defining their vision for a building, its operations and the way people experience it. This process results in a basis of design that stipulates the precise outcomes required and the systems needed to deliver it. While there are many opinions on what the title of this role should be (“smart” vs “digital”), DBC is gaining momentum as it carries less baggage and is a more accurate descriptor.
• The master system planner: This role is part of the design team and works across all the relevant technology groups (mechanical, electrical and plumbing; IT; network; access control; fire and life safety; software, automation, etc.) to ensure proper system specification, integration requirements and prescriptive outcomes. The result is a complete set of construction documents with integration requirements down to the method of integration, communication protocol, data transfer requirements and intervals.
• The master system integrator: This role works as part of the construction team overseeing the specific technology implementations relevant to the
different trades. They act as a technical resource for installation teams and ensure the proper systems are procured. This helps to mitigate change orders and maximize system functionality. The final output of their work is a fully commissioned smart building that executes the use cases defined by the smart building consultant and designed by the master system planner.
These roles and responsibilities are not set in stone. It is important on every project to review the responsibility matrix and make sure that each one is assigned to the party best equipped to handle it. Engineers should leverage their technical aptitude and project management skills to take on as much as they can. Helping owners develop use cases for the smart technology available is consulting work that typically comes with higher margins and is great for building a reputation as a trusted adviser. By adding controls and integration experts to their teams, engineers are the ideal candidates to serve as master system planners, giving them more control over their designs. By covering this scope and issuing a division 25 specification that covers the integrated controls they are positioned to oversee the work of the master system integrating, making them invaluable to the client.
This extra coordination is also likely to result in fewer requests for information or revisions related to building systems and technology, which lowers effort during the construction phase. Regardless of how much responsibility a firm wants to take for the smart building outcomes, they should be closely examining all of the scope to plan coordination efforts and identify gaps. Being able to clearly articulate these scopes and explain the effort and value being delivered to the owner is the first step in securing higher fees and greater profitability on smart building projects. This journey will look different for firms of different sizes and focuses, but it is not an area that can be ignored.
In conclusion, the path to realizing true smart buildings requires a fundamental shift from viewing them as a collection of disconnected technologies and stakeholders to embracing a holistic, process-driven approach. The complexity of modern buildings, combined with rapidly advancing technology, demands a reevaluation of traditional roles and workflows. Smart building success hinges on collaboration across disciplines, with new roles such as smart building consultants, master system planners and master system integrators filling the gaps in coordination, specification and implementation. These roles ensure that the goals of developers, designers and solution providers are aligned and that buildings are designed with long-term operational efficiency, flexibility and user experience in mind. A comprehensive approach that integrates all stakeholders, from initial design through final commissioning, will allow engineers to overcome the barriers of conflicting incentives, fragmented solutions and legacy processes that have slowed the industry’s evolution. Smart buildings are not just about technology. They represent a broader cultural and procedural transformation within the built environment that ultimately benefits all involved, from developers to end-users, through improved outcomes, reduced costs and enhanced functionality. Let’s stop trying to build smart buildings and instead build smarter. cse
Will Maxwell, SmartScore AP, Smith Seckman Reid, Inc. Nashville, TN. Will is a Smart Building Consultant that handles the development, design, and execution of smart building projects along with guiding SSR’s standards and strategies for smart building design.
David Stoller, FPC Global, Nashville, TN. With over a decade of experience spanning technology, sustainability and real estate, David brings a comprehensive understanding of the value chain from development to implementation. Currently, as the leader of strategic development and client relations for FPC Global in the Americas, David excels in crafting scalable, vendor-agnostic solutions that drive
Geremy Wolff, senior director of technical service, McKinstry, Seattle
Navigate the smart building marketplace with this guide to consultants, integrators and contractors. Understand specific roles, strengths and when to combine or separate services for optimal results.
The smart building marketplace is crowded. There are numerous products and it’s difficult to navigate the sea of service providers. Not only are there regional variations, but providers are also affiliated with certain manufacturers, independents and manufacturers.
To simplify things, roles within the smart buildings service provider space can effectively be grouped into several categories:
• Smart building consultants.
• Master systems integrators.
• System integrators.
• Controls contractors.
• Identify the differences between smart building consultants, master systems integrators, system integrators and controls contractors.
• Understand how these roles can be combined or overlap for best project results.
Although service providers frequently combine these roles, each brings varying strengths and focuses to the work. This guide will classify these providers’ strengths by role to get the best outcomes. It is also worth noting that there are circumstances where combining these roles into one service provider is advantageous and others that benefit from segmented roles to promote neutrality, quality verification, and other advantages.
A smart building consultant, or operational technology (OT) consultant, works at a higher level
of an organization than the other roles. They support long-term planning and organization of all the technologies that work to support facility technologies such as:
• Asset management systems.
• C omputerized maintenance management systems.
• Work order systems.
• Project management systems.
• Energy/carbon management and reporting systems.
• Building automation systems.
Smart building consultants are operational technology experts with experience in engineering, design and support of any technology used to operate a building. They work with executives to direct the selection, adoption and integration of technology platforms.
Areas of expertise and qualifications of a smart building consultant include:
• Platform and hardware agnostic.
• National footprint.
• Principally focused on engineering.
• Industry market savvy.
• Multidisciplined on most building sciences.
• Cybersecurity focused.
• Database fluent.
• Business continuity and workflow optimization.
• Change management focused.
A master systems integrator (MSI) fills a role beyond controls contractors and system integrators (SI). They are unique because of their strong and diverse field of expertise, which is needed to actualize smart buildings by uniting diverse technology
at executive levels and with multiple organizational silos. MSIs are engaged at the project level and focused on the detailed mechanics and implementation of projects.
’
and platforms. Extra skillsets include information technology (IT), database engineering and software development. These skill sets must be combined with a very strong knowledge of traditional building technology fields such as heating ventilation and air conditioning (HVAC), energy management, lighting, access control and video, as well as experience with nontraditional building technology fields like environmental quality, workplace performance and occupant wellness. Lastly, it is important that MSIs are platform collaboration experts able to bring together disparate systems across organizational silos to create turnkey solutions that fulfill their clients’ overall objectives. MSIs can be viewed as the primary provider to unite every building technology and the building technology expert for the building owner or occupant.
Key functions of a MSI include:
• Addresses division 25.
• OT infrastructure commissioning support.
• OT network implementation.
• Non-standard communication and complex integration support.
• Energy management and analysis services.
• Equipment performance monitoring.
• Integrated data validation.
• Data normalization and transformation.
• Custom software development.
Smart building consultants engage at executive levels and with multiple organizational silos, such as C-suite, IT, new construction and operations. Additionally, smart building consultants are long-term planners and enterprise architects who work with capital planning to align stakeholders to organizational values with business goals. MSIs are typically engaged at the project level and generally
FIGURE 1: Smart building consultant’s roles often overlap. Understanding when to separate and when to combine roles is key to a successful project. Courtesy: McKinstry
focused on the detailed mechanics and implementation of projects. While they often can design and engineer integrations, it is best to have an independent party perform these tasks. MSIs often have a strong consultative aspect due to the nature of the work, but it is a mistake to think that any MSI can perform the role of a smart building consultant. Most successful MSIs have both OT and IT specialists who implement the building technology network and software specialists who can perform complex application programming interface integrations that go beyond traditional building open communication protocols like BACnet or Modbus. In addition, strong MSIs have in-house database experts to manage ‘big-data’ databases as well as custom-built analytics toolsets. Lastly, MSIs are often affiliated with the integration platform they
‘A systems integrator is a step bet ween a controls contractor and an MSI. They perform integrations but at the building or campus level, usually in the HVAC control platforms.
represent or build. This is not a bad thing, as that role should be a technical expert in the integration platform, but it also makes the case for the presence of a platform-agnostic smart building consultant performing the engineering at an earlier stage and a higher organizational level.
A systems integrator (SI) is a step between a controls contractor and an MSI. They perform integrations but at the building or campus level, usually in the HVAC control platforms. An SI will integrate HVAC, controls, metering, access controls and lighting. They would not perform integrations at the enterprise level, such as work order or asset management systems. A strong SI has extensive knowledge of HVAC systems, communication protocols and controller programming. They are most frequently engaged in linking disparate HVAC control systems together or connecting disparate physical systems, such as HVAC and lighting. While SIs have multiple vendor expertise,
they are typically focused on specific brands so that they can hone their skills.
Key SI functions include:
• Addresses divisions 25 and 23.
• Large-scale Internet of things deployments.
• Cross-system functionality expertise.
• Specific system expertise.
• System service providers.
• Disparate vendor integration expertise.
MSIs and SIs can both be engaged on projects, although the SI skillset often is well within an MSI’s abilities. For this reason, two vendors fulfilling each role is infrequent. However, there are use cases where this may be good practice. For enterprises with national or global footprints, an MSI would be employed to perform the integrations for the entire enterprise but might struggle to mobilize
24_012108_Consulting_Specifying_Engineer_JAN Mod: November 6, 2024 9:29 AM Print: 11/19/24 page 1 v2.5
csemag.com
uSystems integrators specialize in building-level integrations of HVAC, lighting and access controls, while controls contractors handle on-site installations and programming for specific systems.
uMaster systems integrators bridge information technology and traditional building technologies.
uSmart building consultants focus on longterm technology planning, offering platform-agnostic expertise and aligning organizational goals with business strategies.
Continued from pg 30
the manpower to perform the on-site integrations across a broad geographical area. Additionally, where a large amount of work is being performed in a short time frame, it makes sense to delegate the SI role to an additional provider for parallel efforts. It is more about having a cohesive team with cooperation from both parties to successfully fulfill the technology roadmap. SIs are starting to offer a wider selection of integration services. However, integrating a broader selection of systems should not be confused with the activities of an MSI. An SI is not capable of addressing all the disparate components at all levels of a smart building. They do not build software or deliver on a client’s master plan of shaping the solution to meet the specific objectives.
Controls contractors are the providers performing the lion’s share of installations, programming and startup. This role requires a heavy on-site pres-
ence, usually with trucks and tradesman staff. They are often part of a mechanical or electrical contracting firm.
The largest differentiator here will consist of the type of devices being implemented. Controls contractors are primarily in the HVAC space, often with a small set of vendors they support. Additionally, the data infrastructure space is addressed by the SI and not a controls contractor.
Key functions of controls contractors include:
• Addresses division 23
• Large-scale HVAC control deployments.
• Large manpower force.
• Specific system expertise.
• System service providers. cse
Geremy Wolff is the senior director of technical service at McKinstry.
From the world’s #1 air conditioning company, discover a new level of technology, comfort, and sustainability!
Daikin continues its tradition of providing localized HVAC solutions for the North American market with a comprehensive VRV lineup engineered for commercial application performance and flexibility. The Daikin VRV EMERION o ers a broad range of indoor model application flexibility for both heat pump as well as heat recovery systems with simultaneous heating and cooling.
From the world’s #1 air conditioning company, discover the cloud connected benefits of VRV EMERION provided by Daikin’s HERO Cloud Services
Leon Menard, senior director of service, McKinstry, Seattle
HVAC systems with advanced direct digital controls offer precise climate management, lower energy costs and improved comfort.
As businesses strive to improve efficiency and lower operational costs, one area often overlooked is the performance of heating, ventilation and air conditioning (HVAC) systems. Outdated or poorly maintained systems lead to inefficiency, higher maintenance costs and reduced comfort for occupants. Fortunately, advancements in HVAC controls, particularly direct digital control (DDC) systems, are changing the landscape for commercial buildings.
For many businesses, managing heating and cooling needs involves outdated pneumatic systems that require manual adjustments and are prone to inefficiency. These systems often result in inconsistent temperatures, leading to discomfort for building occupants and excessive energy consumption. Additionally, the cost of maintaining these older systems increases over time due to frequent breakdowns and the need for specialized knowledge to make manual adjustments. This is a significant concern for industries where precise climate control is critical, such as education and health care.
Advanced HVAC controls offer a solution to these operational challenges. DDC systems are at the forefront, providing precise, automated control over temperature, ventilation and humidity in different building zones. Unlike pneumatic systems, DDC systems rely on sensors and connected thermostats that monitor conditions in real time and make adjustments as needed.
For example, each temperature-controlled zone within a building containing a DDC system has a thermostat or sensor that communicates with the DDC controller. This system allows facility managers to monitor performance, detect potential heating or cooling issues early and make adjustments remotely — long before these issues impact the comfort of building occupants.
DDC systems in particular offer advantages, including:
• Energy efficiency: By fine-tuning HVAC operations, DDC systems can significantly reduce energy consumption. They optimize heating and cooling based on occupancy patterns, external weather conditions and specific zone requirements.
• Occupant comfort and safety: Whether in a school, hospital or office, maintaining a consistent, comfortable environment is critical. DDC systems ensure that temperature and air quality are precisely controlled to enhance overall comfort.
• Predictive maintenance: These systems can predict equipment failure by tracking performance metrics over time. This proactive approach reduces costly unscheduled maintenance and minimizes equipment downtime.
• Cost savings: While upgrading to a DDC system requires an upfront investment, the return on investment (ROI) can be substantial. HVAC projects often deliver an ROI between 25% and 50%, depending on the age and size of the existing unit.
Each industry has unique demands for HVAC controls and advanced systems are particularly valuable in K-12 schools, higher education campuses and health care facilities.
• K-12 schools: Schools often face strict budgets and aging infrastructure. Advanced HVAC controls help these institutions manage heating and cooling more effectively, reducing energy costs. In addition, maintaining a consistent indoor environment is
• Identify key benefits of implementing advanced HAVC control systems, like direct digital controls.
• Understand the return on investment for HVAC control systems in a variety of building types.
• Learn what industries require specific considerations for air quality and temperature controls.
UPGRADING HVAC CONTROLS at Washington State University’s North Puget Sound Campus demonstrates the benefits of advanced HVAC systems
One prime example of how advanced heating, ventilation and air conditioning (HVAC) systems can transform a facility is McKinstry’s work at Washington State University (WSU) North Puget Sound Campus. This project involved upgrading HVAC controls across multiple buildings, leading to a dramatic improvement in energy efficiency and occupant comfort.
At WSU, the installation of advanced HVAC systems, including direct digital controls (DDCs), allowed the university to monitor and manage different zones more effectively. The new system provided better climate control in classrooms, offices and laboratories while reducing overall energy consumption. By focusing on predictive maintenance and real-time monitoring, the facility management team was able to detect potential issues early, reducing downtime and minimizing repair costs. This project illustrates the significant benefits that can be achieved through modern HVAC controls, especially in complex environments like university campuses.
‘
This project involved upgrading HVAC controls across multiple buildings, leading to a dramatic improvement in energy efficiency and occupant comfort.
For many businesses, the question is not whether advanced HVAC controls are beneficial, but whether the investment is worth it. The answer is a resounding yes. The typical return on investment (ROI) for upgrading to a DDC system ranges between 25% and 50%, depending on the age and efficiency of the existing HVAC equipment. Factors influencing ROI include energy savings, reduced maintenance costs and the longevity of new systems.
Moreover, beyond the financial ROI, the impact on employee or occupant satisfaction can be substantial. A more comfortable working or learning environment leads to increased productivity, fewer complaints and potential health benefits from better indoor air quality. This is particularly important in health care and education, where comfort and safety are paramount.
Upgrading HVAC control systems can significantly improve ROI by helping businesses comply with regulations, like Washington's Building Performance Standards. These standards focus on energy efficiency and emissions reduction, aligning with broader sustainability goals. Modern DDC systems enable precise energy management, reducing waste and operational costs. By upgrading controls, companies can achieve compliance with local, state and federal regulations while benefiting from energy savings. Control system upgrades become the vehicle to meet these standards, ensuring long-term financial and environmental benefits for building operators.
‘Upgrading to advanced HVAC controls, such as DDC systems, provides businesses with the tools they need to optimize their heating and cooling operations.
critical for student comfort and performance, especially in extreme climates. By optimizing HVAC performance, schools can also address issues like poor air quality, which impacts student health and absenteeism.
csemag.com
Control insights
u Advancements like direct digital control systems allow commercial buildings to have more control over temperature and air quality.
u Implementing advanced HVAC control systems offers building owners a high return on investment compared to keeping older systems.
• Higher education: Universities and colleges typically consist of diverse building types; from classrooms and laboratories to student residences. Each space has different HVAC needs, and DDC systems provide the flexibility to manage varied environments efficiently. For example, laboratories may require stricter temperature and humidity control, while dormitories might focus more on energy efficiency. Upgrading to a DDC system allows facility managers to ensure each building’s unique requirements are met without wasting energy or compromising comfort.
• Health care facilities: In health care settings, HVAC control is essential for maintaining air quality and ensuring patient comfort. Hospitals, in particular, need precise control over temperature, humidity and airflow to prevent the spread of infections and support patient recovery. The ability to adjust settings remotely and resolve issues
before they affect indoor air quality is a significant advantage of advanced HVAC controls in these wenvironments.
In today’s commercial environments, managing energy consumption and ensuring occupant comfort are more critical than ever. Upgrading to advanced HVAC controls, such as DDC systems, provides businesses with the tools they need to optimize their heating and cooling operations. Whether it’s reducing energy costs, improving air quality or ensuring consistent temperatures across different zones, the benefits of these systems are clear.
For industries like K-12 education, higher education and health care, the ROI is not just financial. It’s also about creating spaces that support better learning, work and care environments. By investing in advanced controls, businesses can future-proof their operations, enhance the occupant experience and achieve significant cost savings in the process. cse
Leon Menard is the senior director of service for McKinstry.
Peter Andersen, PE, LEED AP, Dewberry, Raliegh N.C.; Andrew Watt, CSP, CHST, CEST, Dewberry, Long Beach, Calif.;
Jon Long, PE, LEED AP, Dewberry, Nashville, Tenn.
A corporate electrical safety program built around NFPA 70E must be supported by leadership and understood by employees to be effective.
Engineers and facility designers routinely encounter electrical hazards associated with live equipment in their daily tasks. Without adequate knowledge of safety protocols, they could unknowingly breach NFPA 70E: Standard for Electrical Safety in the Workplace, putting themselves and their company at risk. Examples include unqualified workers entering within shock and arc flash boundaries. Secur-
ing safety is the highest priority. At the same time, companies need to mitigate risks linked to workplace incidents. The direct and indirect costs of a workplace injury can be staggering, going far beyond medical bills. So, a comprehensive, formal and integrated corporate electrical safety program is a must for any consulting-specifying engineering firm.
Such a program should be based on a recognized national safety standard. NFPA 70E provides guidance and requirements for electrical safety practices to protect personnel from electrical hazards. By fully complying with NFPA 70E, organizations can effectively reduce their risk for the types of commonly encountered electrical hazards.
While most engineering firms possess some semblance of an electrical safety program, too often these initiatives lack formality. Engineers may also mistakenly rely on their technical degree or professional licensure to navigate electrical hazards, neglecting protocols, procedures and training. When this occurs, the company’s safety and liability risks escalate.
The benefits of a formal electrical safety program extend beyond accident prevention and injury mitigation.
They include:
• Upholding reputation: Demonstrating commitment to safety enhances a firm’s image, strengthening its ability to attract and retain talent.
of a workplace injury can be staggering, going far beyond medical bills. ’
• Managing injury and insurance rates: Effective safety measures help control injury rates and associated insurance costs.
• Enhancing competitiveness in proposals: Clients prioritize safety records and favor firms with exemplary safety practices.
• Fostering a culture of safety: Demonstrating concern for employee well-being inspires loyalty among staff.
• Reducing litigation risks: A robust safety program could reduce the likelihood of litigation involving injuries to workers.
• Increasing productivity: Effective safety measures reduce lost time injuries and support production by helping employees do their jobs more effectively.
• Greater clarity: A clear safety “playbook” backed by executive support increases staff effectiveness.
Companies wishing to develop a corporate electrical safety program based on NFPA 70E should possess a thorough understanding of the standard. They should also have a clear framework for applying requirements to establish safe work practices and reduce exposure to potential electrical hazards.
NFPA 70E is widely viewed as the gold standard for safeguarding personnel from electrical risks in the workplace. Companies that structure safety programs in alignment with NFPA 70E guidelines can reduce the likelihood of electrical incidents, fostering the safest possible workplace environment. To gain a deeper understanding of NFPA 70E, it is beneficial to consider the historical context in which safety standards emerged and how pivotal events influenced their development.
Founded in 1896, NFPA was created with the aim of eliminating injury, death and loss from fire and electrical hazards, reflecting a growing awareness of the need for standardized safety measures. However, shortly after forming, it became apparent that electrical wiring practices lacked uniformity and consistency. Standardization was needed to create safer living and working environments. In response, NFPA developed NFPA 70: National Electrical Code (NEC) in 1897 to outline equipment and installation requirements.
Fourteen years later, in 1911, the tragic events of the Triangle Shirtwaist Factory fire in New York City served as a wake-up call for more comprehensive safety regulations in workplaces. While the catastrophic fire, which claimed the lives of 146 workers, was not related directly to an electrical issue, it exposed numerous safety deficiencies and prompted reforms to prevent similar disasters. Ultimately, the incident helped shape more comprehensive regulations for electrical safety in workplaces.
Fast forward to 1970, rising electrical-related accidents in workplaces led to the enactment of the Occupational Health and Safety Administration (OSHA) under the Nixon administration. Since the NEC already covered electrical equipment and installation requirements, OSHA adopted the code as a consensus standard.
After OSHA adopted the NEC, NFPA established the NFPA 70E committee in 1976. Three years later, in 1979, the first publication of NFPA 70E: Standard for Electrical Safety in the Workplace was released. Since then, updates to NFPA 70E have been released every three years to incorporate changes in technology, regulations and industry best practices.
FIGURE 2: Employees inspect electrical equipment and verify breakers settings with electrical equipment in safe working condition.
Courtesy: Dewberry
• Understand why a corporate electrical safety program is necessary.
• Learn recommended components of an electrical safety program.
• Know how to overcome challenges associated with developing an electrical safety program.
Those wishing to stay informed about future NFPA 70E changes or to obtain their own copy can visit nfpa.org. Additionally, electrical safety consulting firms knowledgeable of NFPA 70E can help organizations develop and implement their own electrical safety program and train staff on electrical safety best practices.
The NFPA 70E standard is organized into three chapters, each addressing distinct aspects of electrical safety:
Chapter 1 delineates the roles and responsibilities of both employers and employees concerning electrical safety. Employers are mandated to eradicate electrical hazards and establish electrically safe working conditions for their personnel. The chapter emphasizes the importance of developing a written electrical safety program tailored to the specific risks associated with electrical hazards in the workplace. The program should cover risk assessment procedures, job safety planning, inspections, lockout/tagout (LOTO) programs, audits, training, electrical safety principles and other electrical safety procedures.
Article 120 within Chapter 1 provides guidance on establishing electrically safe work conditions through a written LOTO program to ensure the safety of workers when performing maintenance, repair or testing activities on electrical systems. This program should encompass procedures for identifying energy sources, equipment shutdown, verifying absence of voltage and establishing grounding methods if necessary.
Article 130 of Chapter 1 addresses work involving electrical hazards and prescribes practices aimed at mitigating exposure to such hazards. It emphasizes the importance of conducting shock and arc flash risk assessments to delineate safe work boundaries, restricted access areas, limited approach and arc flash boundaries. Article 130 also
provides guidance on selecting suitable personal protective equipment (PPE) based on the nature of the task and the associated electrical system.
Notably, Chapter 1 distinguishes between qualified and unqualified personnel. It defines qualified individuals as those possessing requisite skills and knowledge related to the construction and operation of electrical equipment, including safety training, to identify and mitigate hazards. Employers are tasked with providing qualified employees with appropriate training and verifying their competence for performing qualified tasks. Conversely, unqualified employees lack the necessary training and knowledge to safely work on or near energized electrical equipment. Employers have the responsibility to identify unqualified employees and make sure they do not perform any tasks that could expose them to electrical hazards, which should be accomplished through awareness-level training
Some companies may even choose to establish intermediate or hybrid classifications for electrical workers beyond these two designations. This could be necessary if the unqualified classification is overly limiting for certain electrical field tasks, while the qualified classification may impose excessive training requirements and PPE mandates. Supervisors are urged to develop a clear understanding of the distinctions between each type of personnel, along with the respective requirements for each designation, and promote education related to the designation level for each employee. Lastly, promoting awareness among all employees regarding their roles and responsibilities is crucial for reducing incidents and fostering a safe work environment.
Comprising 11 articles, Chapter 2 outlines practical safety-related maintenance requirements for various electrical equipment and installations in workplaces. This includes substations, switchgear, switchboards, panelboards, motor control centers, disconnect switches, controller equipment, fuses, circuit breakers, rotating equipment, hazardous locations, batteries and portable electrical equipment. Adhering to these guidelines during maintenance operations can reduce the risk of electrical incidents.
This chapter delineates the best practices employers should adhere to when working with or on special equipment. Emphasis is placed on the responsibility of employers to train employees in safe practices when working with special equipment such as electrolytic cells, batteries, lasers, power electronic equipment, research and development laboratories or capacitors. Employers who implement these safe work practices can help eliminate or mitigate the risks associated with these types of equipment.
As companies develop a thorough knowledge of the tenets of NFPA 70E and prepare to embark on their electrical safety program journey, it’s crucial they are first aware of key criteria that are essential for a successful program. To begin with, companies should put an organization wide commitment to safety in place. This commitment should involve executives, safety advocates, operational managers and employees. Buy-in across all company strata is necessary for the program’s effectiveness.
Moreover, companies should recognize that developing an electrical safety program transcends the implementation of rules and procedures. Instead, it must integrate electrical safety practices into the company’s ethos. This integration requires active support and involvement from operational leadership who must champion electrical safety to make it a core principle. Without such backing, the investment of resources into program development risks being lost.
Companies are also advised to investigate the regulatory requirements applicable to their industry. These requirements can be found in NFPA 70E guidelines. Discussions with peers from other firms in their industry who have successfully developed similar programs can also be helpful.
Companies should analyze the tasks performed by their employees to identify the hazards and risks they routinely encounter. An effective program should address and mitigate the hazards specific to employees’ roles and activities without including provisions for hazards they never encounter. For instance, a program that extensively mitigates hazards associated with working on high voltage trans-
SOMETIMES a “near miss” or injury can be a catalyst for change. However, an electrical safety program can prevent injury and risk before they occur.
Sometimes, it is an injury or a “near miss” that catalyzes the implementation of an electrical safety program (ESP). It doesn’t need to be that way. NFPA 70E: Standard for Electrical Safety in the Workplace enables firms to tap into the wisdom and guidance of industry experts concerning proven electrical safety practices.
Consider the following scenario: An untrained and unqualified employee enters a restricted area and inadvertently is exposed to electrical hazards. The employee could be injured or experience a “near miss,” which is a safety incident that does not result in an injury. A co-worker recognizes that a possible safety violation has occurred and reports it, which is critical for identifying and addressing lapses or gaps in safety. Importantly, the person reporting the possible safety violation must feel supported by the company’s culture of safety to step forward. And when the person does, they should be commended for integrity.
From the incident, a review of internal procedures and electrical safety training is in order. Employees need to be equipped with the knowledge to safely navigate their work environment, avoid potential hazards and comply with safety protocols.
A near miss highlights the need to revisit the ESP. A collaboration of a firm’s operational leaders and the health, safety and environment (HSE) team can lead to enhanced ESP requirements. The HSE team’s primary objective is to gain a comprehensive understanding of the firm’s operational activities relevant to NFPA 70E. Armed with these insights, the HSE team can develop an updated program and align it with NFPA 70E conditions, while also tailoring it to the specific tasks performed by the firm’s operations staff.
After finishing the ESP, training requirements can be determined. In this scenario, an operational leadership pledge for all employees potentially exposed to electrical hazards to receive training on updated and enhanced firm electrical safety procedures and industry best practices is crucial. These include adherence to safety zones and boundaries, distinguishing between qualified and unqualified electrical persons and fulfilling documentation requirements for tasks involving exposure to electrical hazards.
The successful development, training and implementation of this program is only possible by promoting a culture where leadership guides the way and prioritizes its people. Demonstrating commitment to the employee’s health and well-being boosts team morale and enhances understanding of regulatory compliance and industry best practices. Developing an ESP that is intertwined with operations should be considered an industry best practice that all employers strive for.
mission lines for a group that never works with equipment operating above 600 volts would not only waste resources in program development but also lead employees to question the program’s effectiveness upon implementation.
With preparations made and the groundwork laid, a company should be poised to begin developing the relevant policies and procedures of a program within the framework of NFPA 70E.
To start, Chapter 1 of the standard recommends that any electrical safety program include the following:
• Guiding principles upon which the program is based: For guiding principles, Annex E of NFPA 70E provides some suggestions, such as using the correct job tools, assessing staff abilities, identifying hazards and protecting employees from them.
• Controls for measuring and monitoring a program: Risk management controls provide companies with a means to determine the effectiveness of their safety program. In the context of electrical safety, controls primarily revolve around mitigating electrical hazard risks through proper training, principles, policies and procedures. They should focus on identifying and evaluating the sources of risks and then determining a mitigation strategy for each one.
• Safety procedures to follow before performing electrical work: Safety procedures must be developed in alignment with at least the minimum NFPA 70E standards and include both policies and methodologies intended for individuals in the field to safeguard themselves and others. The procedures are manifold and should be focused on managing risks before work is started, such as LOTO procedures.
• Methods for performing an electrical risk assessment: Risk assessment training is fundamental to the development of a comprehensive electrical safety program. NFPA 70E, Annex F offers guidance on electrical risk assessment protocols. The assessment process should include identifying sources of risk, analyzing them for risk level and determining appropriate measures for mitigation. These risks include both arc flash and electric shock hazards. Understanding work boundaries such as limited approach and arc flash boundaries, being aware of the operating voltage present and heeding warning labels are crucial elements in effectively managing these risks.
• Job safety planning or briefing requirements: An essential prework assessment includes job safety planning, which may involve completing a daily
risk assessment form. For more complex and hazardous electrical work, safety briefings should be held before initiating tasks. Ideally, this planning should be scaled to the level of risk and the certification level of the workers involved.
• Incident investigation steps, even for close calls or near misses: By examining incidents, close calls and near misses, organizations can pinpoint areas where additional training or program modifications are needed, such as emergency response training. This process reinforces the program’s principles through corporate stewardship.
• Program compliance auditing: Programs should also incorporate auditing conducted by internal or third-party safety advocates. These audits, typically conducted every three years, aim to verify that the program’s principles and procedures, including the auditing of fieldwork safety, align with the chosen safety standard and corporate safety mandates.
Once a program is developed, a three-pronged approach can help with implementation:
• Executives endorsing the program: Nothing cements the importance of a safety program across an organization more than public endorsement by corporate executives. But a one-time endorsement is not enough. No program will have a lasting impact without an executive-level champion to periodically monitor its implementation and create accountability. An executive champion can make necessary changes to the program, resulting in proper outcomes.
• Safety advocates overseeing the program: Someone in the organization must own the program. Whether safety duties are a primary profession or a secondary responsibility assignment, this role is the driving force for implementing and maintaining the program. The advocate should lead the roll-out of the program, schedule training sessions, perform the necessary safety training (if certified and authorized) and periodically report to executives on the health and outcomes of the program. Regularly scheduled safety training videos with accountability measures are an excellent way to compel, remind, refresh and instruct new and existing employees of the program’s goals and practices. While in-person training for larger organizations can be time-consuming, they’re important for soliciting feedback and answering questions. This
training also allows managers and executives to reinforce the importance of the program and show their support.
• Engineers executing the program: Mid-level managers who supervise the engineering staff at risk must be the ones who understand, support and execute the day-in, day-out safety program requirements. No executive or cadre of advocates can adequately supervise the regular, on-site work where these best practices should be implemented. Executives holding their managers accountable and those same managers holding their staff accountable is the key to program implementation success.
Among the most important approaches that can be incorporated, training stands out as fundamental for the success of any program. However, the inherent challenge of a training program that centers on NFPA 70E is the technical complexity of the standard, much of which focuses on compliance. Communicating this information to hundreds or thousands of employees, many of whom lack electrical training, can be exceedingly challenging.
Therefore, the primary goal of training is to translate this technical content into easily understandable terms for a broad audience, so that the information is not only effective but also readily comprehensible. Here, a team-based approach often proves useful. It should involve safety advocates with subject matter expertise who possess a deep understanding of corporate risk.
A training program must also prepare employees to prioritize safety as a top-of-mind awareness when they go out in the field. They need to be empowered to make wise decisions when it comes to practicing safety. In the field, there may not always be direct supervision when it comes to safety practices.
However, if they understand expectations during training and have all their questions answered, they will be well-prepared for success when they transition to fieldwork. This readiness includes situations and conditions with inherent risks or exposures.
Additionally, training should not be treated as a singular event but rather as an ongoing journey and continual process. It requires a commitment to learning every single day and breaking bad habits. It also serves to reinforce safer actions and deci-
sions. Training should be consistent, with regular refreshers. Throughout their careers, employees should undergo knowledge checks to verify that the information is retained.
For many legacy engineering professionals, adapting to a new way of conducting their work can be a difficult undertaking. Some may have been operating without a structured program for 20 or 30 years. A corporate electrical safety program should also relate to all technical personnel working in the field and not solely to electrical engineers. This is because electrical hazards can exist in any construction site or operational facility, even though the risk to non-electrical staff may be comparatively lower.
To support this transition, leaders who are closely connected with their teams and able to address questions, while certifying compliance, are invaluable. They play a crucial role in guiding and supporting employees through the necessary changes. Those leaders may identify who is trained and certified as qualified or unqualified electrical workers based on the program’s certification definitions. Hybrid safety certifications that exist somewhere between NFPA 70E qualified and unqualified are options and need to be clearly defined in the program, with careful consideration given the lack of NFPA 70E guidance.
A successful corporate electrical safety program is not only about compliance, mitigating risks or avoiding accidents. It’s also about cultivating an environment where electrical safety becomes a shared value. This is where a program lays the groundwork for an enduring electrical safety culture across the organization. A culture of electrical safety emerges when employees recognize their well-being is a top priority—instilling a sense of responsibility and loyalty among them. Such a culture, underpinned by strong safety performance, plays a vital role in upholding positive corporate morale and reputation, and, ultimately, building a resilient foundation for long-term success. cse
Peter Andersen, PE, LEED AP, is a vice president and chief electrical engineer for Dewberry. Andrew Watt, CSP, CHST, CEST, is a health, safety and environment manager for Dewberry. Jon Long, PE, LEED AP, is a senior associate and business unit manager for Dewberry.
‘ A successful corporate electrical safety program is not only about compliance, mitigating risks or avoiding accidents.’
csemag.com u
Electrical safety insights
uDeveloping an electrical safety program requires organizationwide commitment.
uRegular and eff ective training is crucial to making NFPA 70E's technical standards accessible to all employees.
Office building design trends focus on flexibility, sustainability and smart technologies to support hybrid work, decarbonization and future adaptability.
CSE: What are the biggest current trends for office building design?
Jarron Gass: The biggest trend currently is flexibility. The rise of remote work has required commercial office leasing agents to offer maximum flexibility for both employees and employers. This includes creating adaptable spaces and incorporating modular furniture with collaboration zones and focus zones to support both in-office and remote work scenarios simultaneously. Employers are increasingly adopting a hybrid approach, blending in-person and remote work across various teams or divisions, and they must adapt to these changes while maintaining efficiency and productivity.
Danielle Passaglia: Due to the popularity of hybrid work culture post-pandemic, offices are looking at ways to provide flexibility to their workers. This includes adaptable work stations, the ability to densify the floors as needed and planning for future re-organization with adaptable designs to accommodate future needs. Carbon levels and indoor air qual-
ity (IAQ) have also become larger considerations for clients. We are seeing higher priority for increased filtration, ventilation and metering. Additionally, due to decarbonization efforts, there is a push for increased electrification. These efforts are not solely intended for tenant fit out but also should be evaluated by landlords and developers that are looking toward electrification and sustainable technology in the core and shell systems.
CSE: What future trends do you anticipate for these kinds of buildings?
• Identify present and future trends for office building design.
• Understand how hybrid work environments are changing system designs in offices.
John Yoon: In mature markets with a large base of existing office buildings, the largest trend is redevelopment and conversion of existing properties to other occupancy types (mixed-use, residential, data center, warehouse, etc.). Office occupancy rates will not return to pre-pandemic levels anytime soon. In the meantime, having buildings sit empty is not an option for owners or local governments. Because empty buildings generate less real estate tax revenue, many local governments are motivated to provide incentives (tax increment financing, property tax abatements, business district tax rebates, etc.) to encourage this type of repositioning. Existing buildings in suburban areas are having a harder time than those within dense urban environments/central business districts. There are multiple reasons, including access to financing, unwalkable neighborhoods, lack of public transportation and opposition to new warehouses.
Jarron Gass: The integration of smart technology, such as the Internet of Things (IoT), enables connected systems for lighting, temperature control, access and virtually any type of automation imaginable. Smart meeting rooms are becoming increasingly common, featuring advanced audio/video technology for virtual collaboration and immersive 3D environments. Another area of growth is touchless technology for doors, elevators and other facilities, which enhances convenience and hygiene.
Danielle Passaglia: There will be ongoing advancements in metering, trending and data collection regarding energy, carbon tracking, thermal comfort, occupancy tracking and climate conditions. Developers leasing spaces to companies will begin transitioning and retrofitting to more carbon-friendly systems like heat pumps, heat recovery chillers and electric boilers. New constructions will incorporate heat pumps and radiant or geothermal systems when feasible. With more companies providing consulting services for identifying tax breaks, grants, city incentive programs and life cycle cost analysis, these systems with a higher initial cost may become more attractive and widely adopted.
Jarron Gass, PE, CFPS
Fire Protection Discipline Leader
CDM Smith Pittsburgh
Danielle Passaglia, PE, LEED GA
Mechanical engineer
SmithGroup Chicago
John Yoon: From an engineering standpoint, electrification to address decarbonization is a significant future design trend. Regardless of emerging technologies, like more efficient low-ambient temperature air source heat pump air handling units, an all-electric building will still be more expensive to operate than one using natural gas. This will only be made worse by the trend of increased electrical rates caused by utility decarbonization and overall increased electrical demand. For example, PJM (a regional transmission organization responsible for managing the grid in 13 states) has a capacity auction every year to ensure there is sufficient generation and transmission capacity to support the load on the grid. During the last auction for the 2025/26 delivery year, cost to consumers increased from $2.2 billion to 14.7 billion - more than a 600% increase. With these types of potential energy cost escalations, there will likely be an emphasis on exploring marginal gains in efficiency, including building envelope improvements and increased controllability of systems, which may not have been cost-effective before.
CSE: What trends do you anticipate as hybrid work continues to be the norm for many companies?
Jarron Gass: I anticipate that the hybrid
approach will remain a prevalent strategy across many industries as they strive to balance employee productivity and efficiency with convenience. At the same time, companies must continue fostering growth and career development through mentorship and collaboration within internal teams. Both in-person and remote work scenarios have merits and drawbacks that organizations must carefully navigate when developing policies to maintain employee satisfaction and retention.
Danielle Passaglia: With hybrid work, companies will be looking to revise typical space layouts within their offices to best utilize their space, depending on the quantity of daily in-person employees. Mechanical, electrical and plumbing (MEP) systems will need to be designed to easily adapt to these changes as average employee attendance will vary across each workday and offices will be fitted with various flexible furniture arrangements.
John Yoon: There is a concept in commercial real estate known as the 3-30-300 rule. This states that for a generic office, the yearly cost for utilities is $3, rent is $30 and payroll is $300. Although the exact costs may vary, this relationship is generally valid. So, while employees may prefer working from home, if their productivity drops by 10%, it can severely impact the business' bottom line. Because of the
John Yoon, PE, LEED AP
Principal
McGuire Engineers, Inc. Chicago
perception that working from home negatively impacts productivity, the emphasis has been on finding ways to make workers want to come back to the office. The typical solution is providing things that they can't get at home; health/wellness features, amenities (restaurants, recreational facilities, etc.) and more open-plan designs that emphasize collaboration to increase effectiveness. These design prerogatives can both have poor space utilization and increase the cost of supporting MEP infrastructure. But, their cost pales in comparison to that of the people in it. At that point, it simply becomes a cost of business. Traditional options to reduce real estate costs, such as creating super dense hoteling office spaces, usually have the reverse effect of making workers disconnect from the people around them and make them not want to return.
CSE: What types of office building assessment programs are owners adding to ensure tenants are breathing healthy, clean air?
Jarron Gass: COVID-19 provided a valuable learning opportunity for everyone. For office buildings with a captive environment, often with immovable
windows, the most significant area of improvement was filter management in HVAC systems. For many buildings, the starting point was enhancing efficiency and conducting air quality monitoring and testing. This helped develop a plan to achieve optimal air quality through adjustments to ventilation and filtration systems. It also led to considerations for upgrading equipment or adding new devices, such as advanced air filters (e.g., HEPA or MERV-13) that provide a higher level of filtration. Additionally, this process might identify the need to increase the frequency of filter changes as part of an enhanced maintenance program.
Danielle Passaglia: LEED and WELL have become common certification programs in the industry. Fitwel certification is becoming another popular assessment that focuses specifically on IAQ and healthy building criteria. Fitwel is used as a certification, evaluation and benchmarking tool for offices. BREEAM is another certification method that focuses on net zero carbon goals and continues to gain popularity as we to assess our carbon impact through the life span of a building.
John Yoon: ASHRAE Standard 62.1: Ventilation for Acceptable Indoor Air Quality is still the gold standard for IAQ assessments. Traditionally, the focus has
been ensuring that the air handling systems can provide at least the minimum code-required ventilation. It takes a more holistic approach, with the idea that good IAQ is more than just providing a minimum cubic feet per minute value. Identifying and addressing contamination sources (moisture, dirt, etc.) is critical for providing good IAQ. However, when deficiencies are discovered during an assessment, the cost of corrections can often be prohibitive.
CSE: How are engineers designing office facilities to keep costs down while offering appealing features, complying with relevant codes and meeting client needs?
Jarron Gass: Engineers are adopting innovative strategies to design cost-effective, attractive and code-compliant office facilities that meet modern demands. Flexible layouts and shared amenities are prioritized to maximize utility and reduce wasted space. Energy-efficient systems, such as smart lighting, HVAC and IoT sensors, help minimize operational costs while also supporting sustainability certifications like LEED. Modular construction and prefabricated materials are increasingly used to lower labor expenses and speed up project timelines.
The use of durable, cost-effective green materials, along with maximizing natural lighting, enhances both the aesthetics of the building and tenant satisfaction. Value engineering is employed to find cost-effective alternatives that do not compromise compliance while building information modeling tools help prevent costly errors and rework.
Sustainable water and waste systems, along with touchless technologies, help reduce long-term maintenance costs and appeal to eco-conscious tenants. The core-and-shell approach provides flexibility, allowing tenants to customize their spaces while lowering upfront costs. Close collaboration with clients ensures engineers can prioritize features effectively, balancing budgets with functionality. These strategies ensure that modern office designs remain efficient, adaptable and appealing to tenants, while also achieving sustainability and efficiency goals.
Danielle Passaglia: First and foremost, engineers advocate for a robust building envelope for new construction to help reduce envelope gains to the space with high-efficiency windows and a tight envelope. This approach helps lower energy expenditure, which is beneficial for the owner. As MEP systems constantly improve, engineers are finding ways to adapt existing systems to more electric hybridization or advocate for more energy efficient systems at initial buildout. For tenant interior fit outs, engineers are providing guidance and consulting service to clients before choosing a potential location based on which sites may offer clients more energy savings and future flexibility during their lease. Additionally, ensuring buildings have adequate tracking and metering data is crucial to track actual energy use. Engineers are honing in on controls and building automation at the beginning phases to ensure that efficiencies can be operated as intended and to reduce the need to overwrite measures while in operation.
John Yoon: It all begins with making the client a true partner in the design process. Code-related items are generally non negotiable, and most clients will understand that. Unfortunately, beyond code requirements, it is seldom fleshed out exactly what the client wants from a functionality and budget standpoint. However, do you know if you're providing the most effective design solution if you're not certain of what the client wants? Creating a set of formal owner project requirements (OPR) goes a long way toward bridging that gap. Much of the time and effort in developing an OPR goes toward client education since most do not have sufficient expertise regarding the systems we specify.
CSE: What should engineers target when designing office buildings with a focus on long-term adaptability and resiliency for future technological and societal changes?
Jarron Gass: Engineers designing modern office buildings should prioritize flexible layouts with modular designs and multipurpose spaces to accommodate evolving work styles and future needs. Technological infrastructure should be future-proof, incorporating high-capacity broadband, IoT-enabled systems and provisions for emerging technologies like 5G, augmented reality and artificial intelligence. Sustainability is a key consideration, with energy-efficient systems, renewable energy sources and climate-adaptive features to reduce environmental impact. Additionally, promoting tenant health through advanced air filtration systems, ergonomic workspaces, and natural light is essential for well-being.
Buildings should be designed with scalability in mind, featuring open layouts and modular mechanical systems that facilitate easy upgrades as needs change. Disaster preparedness, including backup power systems and robust
cybersecurity measures, is crucial to ensure operational continuity. These strategies help future-proof office buildings, ensuring they remain adaptable and competitive in the face of technological advancements and societal shifts.
Danielle Passaglia: Engineers should always be designing their systems with the future in mind. By initially asking clients how they anticipate utilizing their space in 1, 3, 5 and 10 years, the engineers should develop a concept for future expansion of the day one system. Some concepts include providing space within MEP rooms for future equipment, designing systems to mitigate system downtime for any expansion and providing metering to evaluate usage data on a granular basis.
John Yoon: There will always be the potential for black swan events, like the pandemic, that are nearly impossible to
u Office buildings are increasingly adopting flexible layouts, modular designs, and smart technologies to support hybrid work.
u To ensure long-term adaptability, engineers are prioritizing resilient, future-proof designs with scalable infrastructure.
u Sustainability and decarbonization are driving the adoption of energy-efficient systems like heat pumps, enhanced filtration and electrification in both new and existing office buildings.
predict. Although it is impossible to plan for every scenario, that doesn't mean that you cannot incorporate resiliency into your design. After all, 'adaptability' infers an ability to easily change. Large monolithic design solutions that use proprietary technologies are inherently difficult to change and subject to single points of failure. So, unless those design solutions can work efficiently under a variety of different operating conditions, there should be a compelling usage case to necessitate that versus a more modular design. cse
VP,
Sales
MWaddell@WTWHMedia.com 312-961-6840
BGross@WTWHMedia.com 847-946-3668
Sales Account Manager
Richard Groth RGroth@WTWHMedia.com 774-277-7266
Sales Account Manager
Robert Levinger RLevinger@WTWHMedia.com 516-209-8587
Sales Account Manager
Patrick Lynch, Senior Vice President, Sales & Strategy 847-452-1191, PLynch@WTWHMedia.com
McKenzie Burns, Marketing Manager MBurns@WTWHmedia.com
Cour tney New, Program Manager, Content Studio CNew@WTWHMedia.com
Paul Brouch, Operations Manager 708-743-5278, PBrouch@WTWHMedia.com
Rick Ellis, Director, Audience Growth 303-246-1250, REllis@WTWHMedia.com
Custom reprints, print/electronic: Paul Brouch, PBrouch@WTWHMedia.com
Information: For a Media Kit or Editorial Calendar, go to https://www.csemag.com/advertise-with-us.
Letters to the editor: Please email us your opinions to ARozgus@WTWHMedia.com. Letters should include name, company and contact details, and may be edited.
Proper HVAC system operation is essential for maintaining safe and healthy indoor air quality (IAQ). Belimo’s range of sensors, meters, and gas monitors delivers exceptional accuracy, reliability, and ease of installation, while seamlessly integrating with leading Building Management Systems (BMS). Products include field-selectable multi-sensors that measure CO2, humidity, temperature, and VOCs, as well as thermal energy meters designed to EN1434 standards for IoT-based billing, ensuring accurate flow and energy measurement. These solutions help guarantee occupant safety, comfort, and productivity in any building.
The latest addition to our award-winning Centum™ Series. Powered by the robust QSK78 engine and designed to meet the needs for right-sized power and reduced emissions in the most critical applications. Stay powered with Centum.