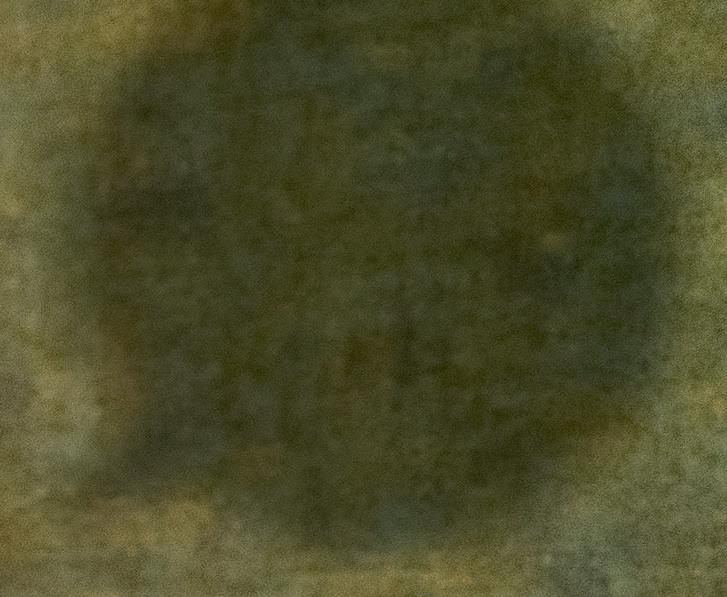
13 minute read
Design Notes
Touchless technology takes elevator call buttons to new “highs”
Edited by Mike Santora • Managing Editor

Shown here is a commercial elevator application for the HoverTap.
Vancouver-based NZ Technologies — a designer and
manufacturer of human-machine interfaces (HMIs) primarily for the medical market — recently entered into a Manufacturing Collaboration Agreement with Dupar Controls to produce a modern take on elevator call buttons and panels. The latter is a maker of elevator and keypad components. Together, the companies are manufacturing a no-touch HMI and control product called the HoverTap Li to replace traditional elevator call buttons and panels — making the elevator experience more hygienic. The NZ Technologies engineering team will provide the core hardware. Dupar Controls will market the product to its extensive customer base. How HoverTap technology works HoverTap has two main components — capacitive sensor hardware (panel or LCD screen) and a controller loaded with programming that incorporates an AI algorithm. Together, the hardware and so ware allow accurate real-time 3D detection of users’ fi ngertips without any latency associated with other touchless screens. The so ware interprets these positions as command inputs.
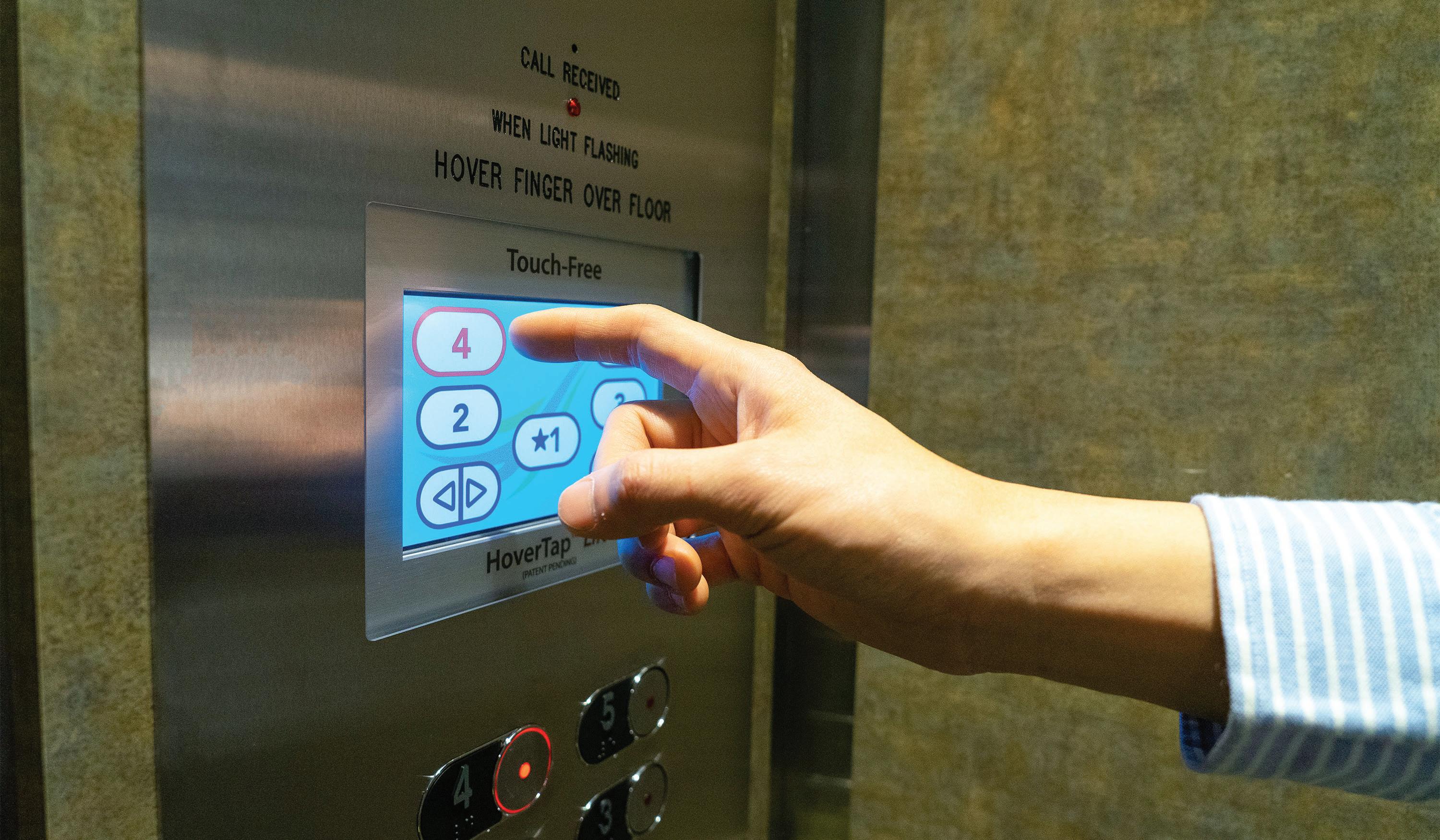
Here, we see an uninstalled HoverTap commercial HMI cabin elevator switch control.
Again, the HoverTap touchless technology for the elevator system comes in two off erings:
• HoverTap Li — the sensor panel is installed above a lit LCD touchscreen in the elevator car operating panel (COP), displaying virtual buttons to allow touchless taps in the air for destination fl oor selection.
• HoverTap Swipe — the sensor panel is installed behind pressure-contact control buttons to allow contactless control with simple gestures like swipes or taps in the air to call the elevator.
Designed with easy integration in mind, both HoverTap Li , and Swipe have a picture- ame form-factor that fi ts over a surface to enable touchless interactions. Flush panel mounting supports maintenance, aesthetics, and code compliance. The product solely relies on preloaded so ware and no cumbersome installation of apps. Also, there are no camera sensors in the product,
The HoverTap combines a capacitive touchscreen with programming that leverages AI for touch-free elevator controls. HoverTap technology can turn various high-touch public surfaces (including ATMs and kiosks) into touchless and intuitive user interfaces.

eliminating privacy concerns and bypassing various common hindrances to vision-based sensing problems, including ambient light fl uctuations and obstructions. The inspiration behind HoverTap is the TIPSO AirPad — a product developed to give surgeons contactless equipment controls in operating rooms during surgery. The HoverTap technology was fi rst installed for commercial use at the Ronald McDonald House in Vancouver, British Columbia, Canada. Now the technology is also employed in other buildings in Greater Vancouver to ensure a safe and healthy return-towork environment for employees and visitors. Future HoverTap installations are targeted to educational institutes, airports, railway stations, medical buildings, and commercial o ces — and the hospitality and hotel industry in their eff orts to minimize the spread of COVID-19 and maximize facility cleanliness and convenience. DW
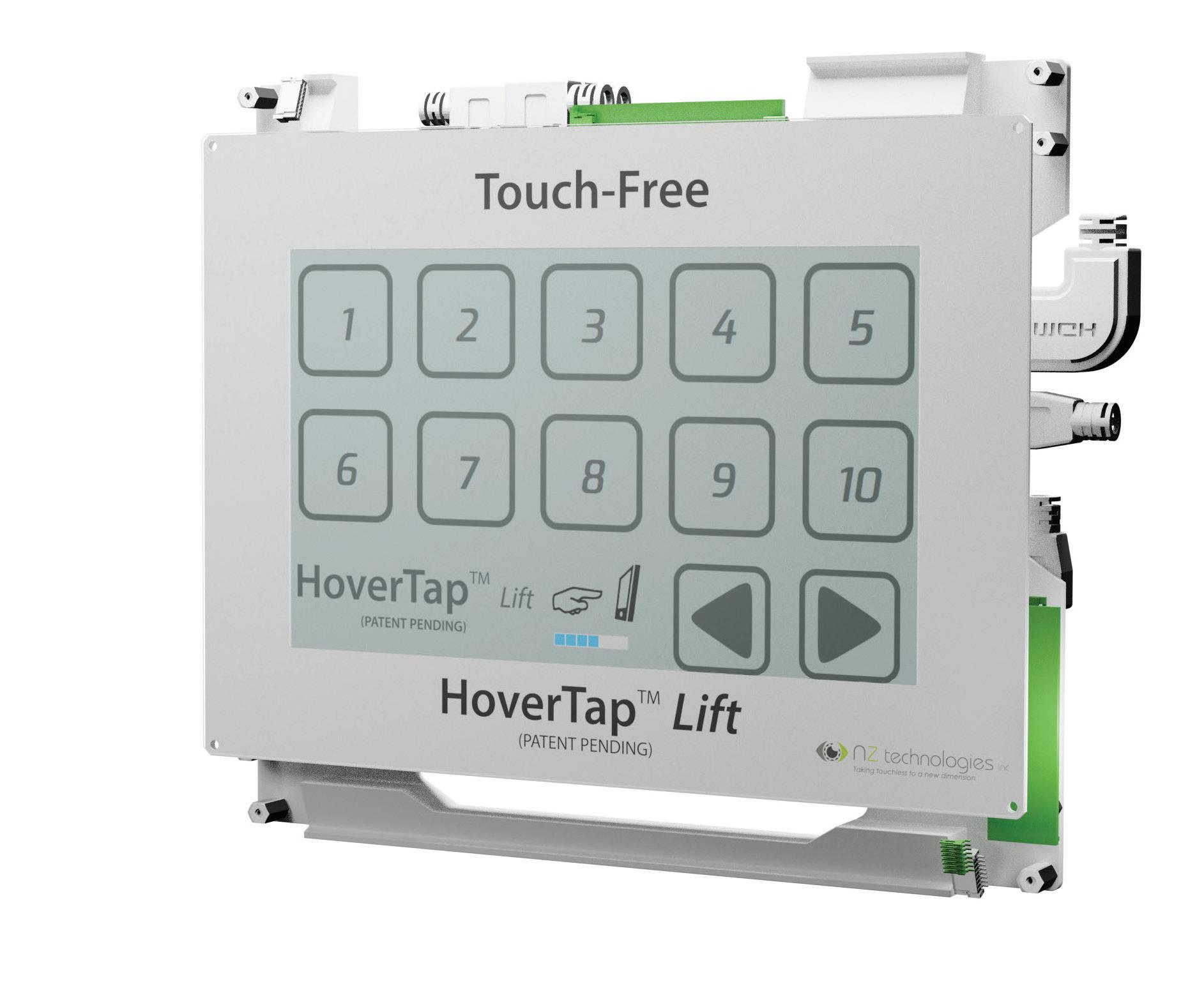
NZ Technologies nztech.ca

Design Notes
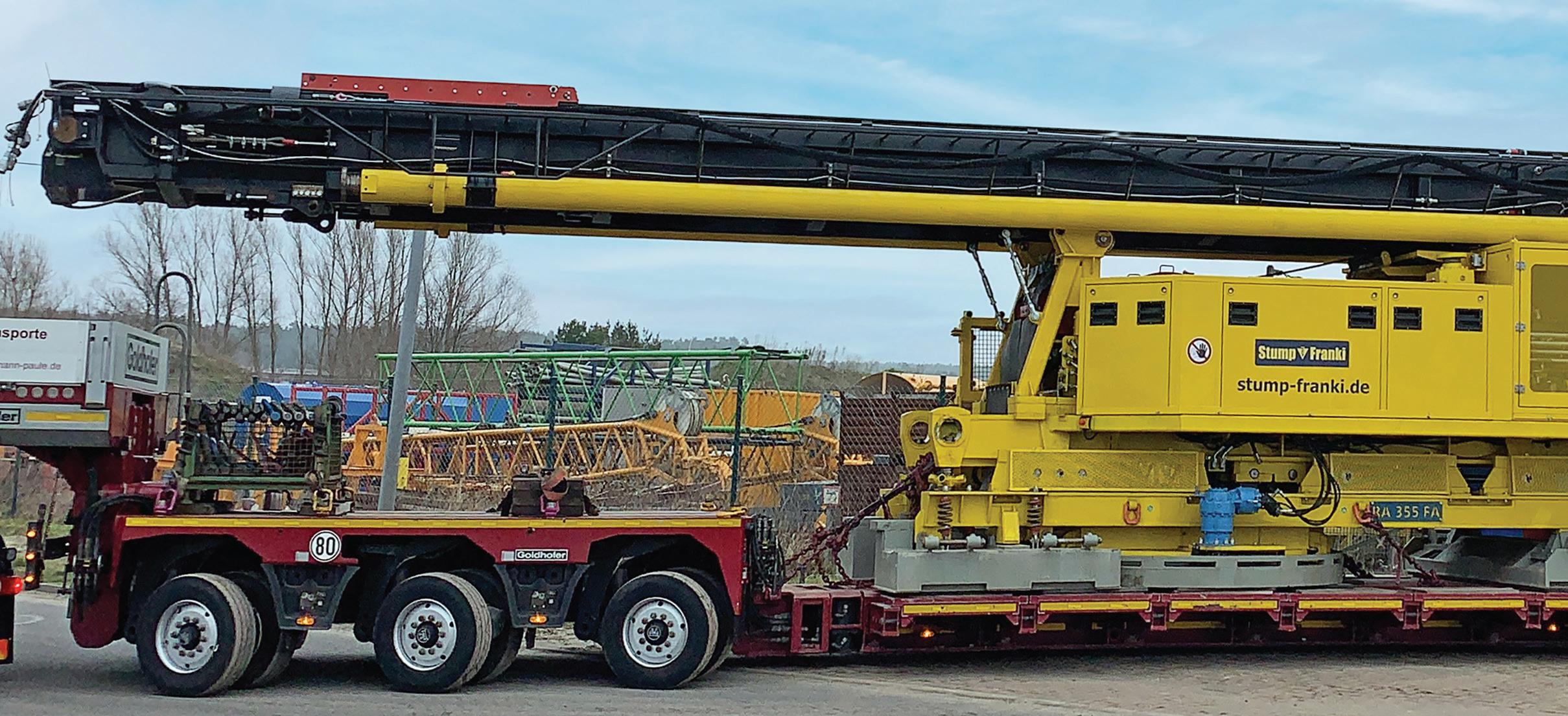
Position monitoring in free fall
Edited by Mike Santora Managing Editor
Heavy machinery in specialist civil engineering requires that precise components perform reliably. The absolute rotary encoder WV58MR om SIKO GmbH, manufacturer of sensors and positioning systems, is part of the safety concept for the pile drivers om Stump-Franki Spezialtie au GmbH. They are attached to three winches to detect the positions of the respective elements attached to them. Franki manufactures its own pile drivers, which are used to construct foundation piles. The piles are used to divert loads of a structure into deeper layers. “We have our own mechanical engineering department to develop, design, assemble, and commission. We then use the equipment that suits us,” explained Stefan Hemmerle, Head of Mechanical Engineering at Stump-Franki. Especially with the pile drivers, self-construction was the best option: Until the 1960s, the pile drivers could still be purchased in Belgium. Subsequently, Franki Germany began to manufacture its own machines, like the Franki rams and Atlas devices, starting in 2000. “For us, this is a clear competitive advantage to build these machines according to our ideas, so that we can also use our own processes to the advantage of our customers,” said Hemmerle. The Franki pile driver has four winches installed at the top — including three SIKO rotary encoders for position monitoring. In the ont area is the so-called leader, a ame to which the pile or driving pipe made of steel is attached, which is open at the top and bottom. A plug of concrete and gravel is fi lled into the driving pipe (1), and with the
The pile drivers can be used fl exibly and are transported to the respective construction site with special transporters.
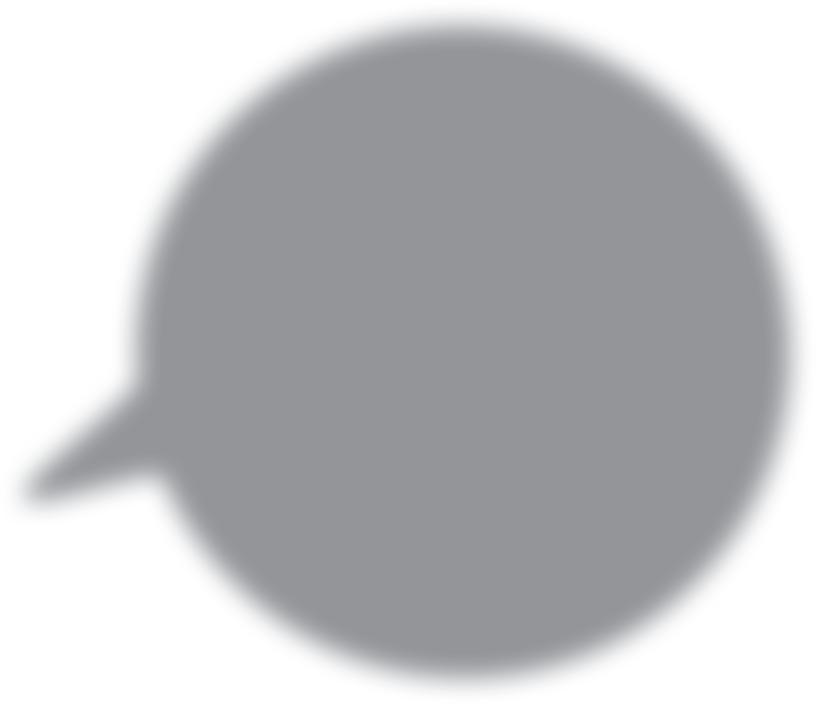
| ©Stump-Franki Spezialtiefbau GmbH
pile driver, a solid block of steel, the plug is compacted with small blows (2). The pile driver is a ee-fall system. Once the plug is fi rmly wedged in the pipe by the blows, the drop height increases, and the driving pipe is brought to the fi nal depth in the load-bearing subsoil. Then the plug is impacted with the pile driver (3). The so-called “Franki foot” is formed, acting as a dowel. A er the foot has been fabricated, the reinforcement cage is adjusted, and plastic concrete is refi lled (4) so that a continuous pile is formed. A er the concrete has hardened and the pile head (5) has been capped, the pile is ready to receive the load.

Monitoring of the four winches The four winches have diff erent tasks during the driving process: A winch is used to pull the driving pipe, a second is used to drive the pile driver, a bucket for fi lling with concrete and gravel is attached to the third, and fi nally there is an auxiliary winch by which a reinforcement cage is li ed in place. Three of the four winches are monitored with a rotary encoder om SIKO so that it is clear where the pile driver, the auxiliary li , and the bucket are located. The auxiliary rope is a safety design to ensure that the pile driver shuts off before a hook passes through a rope pulley. Therefore, this rotary encoder has an end-position point beyond which the winch must not rotate. The pipe pulling winch is the most sensitive area of the system; despite the hard blows into the driving pipe. The rotary encoders are integrated into an automatic control system, which permanently queries the positions and thus also controls the tracking of the cable.
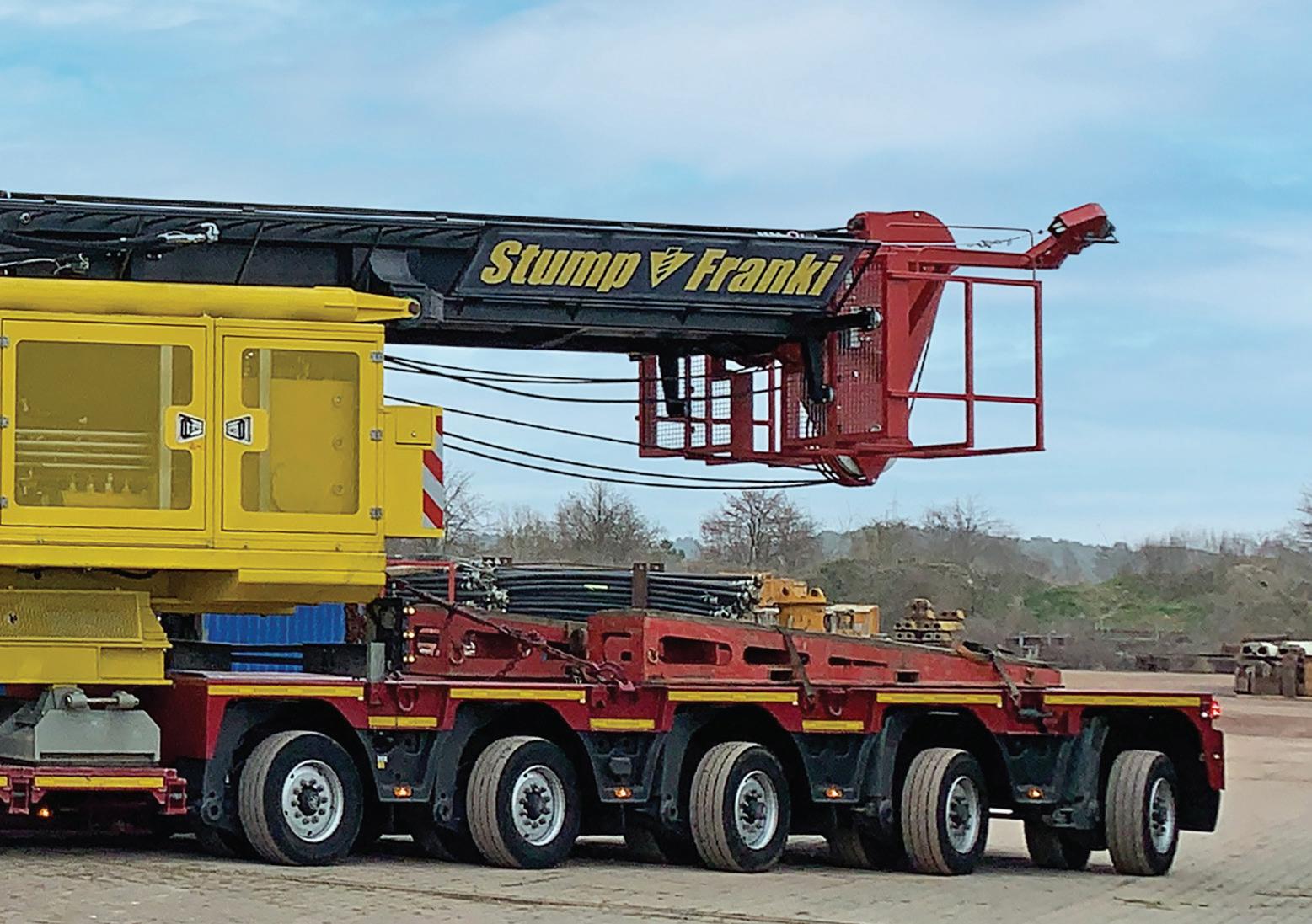
Rotary encoders with safety performance level PLd “What is most important to us is the precision of the position detection and the redundancy as a safety function of the rotary encoder,” said Hemmerle. “As a multi-turn encoder, it can detect up to 4,096 revolutions of the winch in absolute terms. In addition, we have
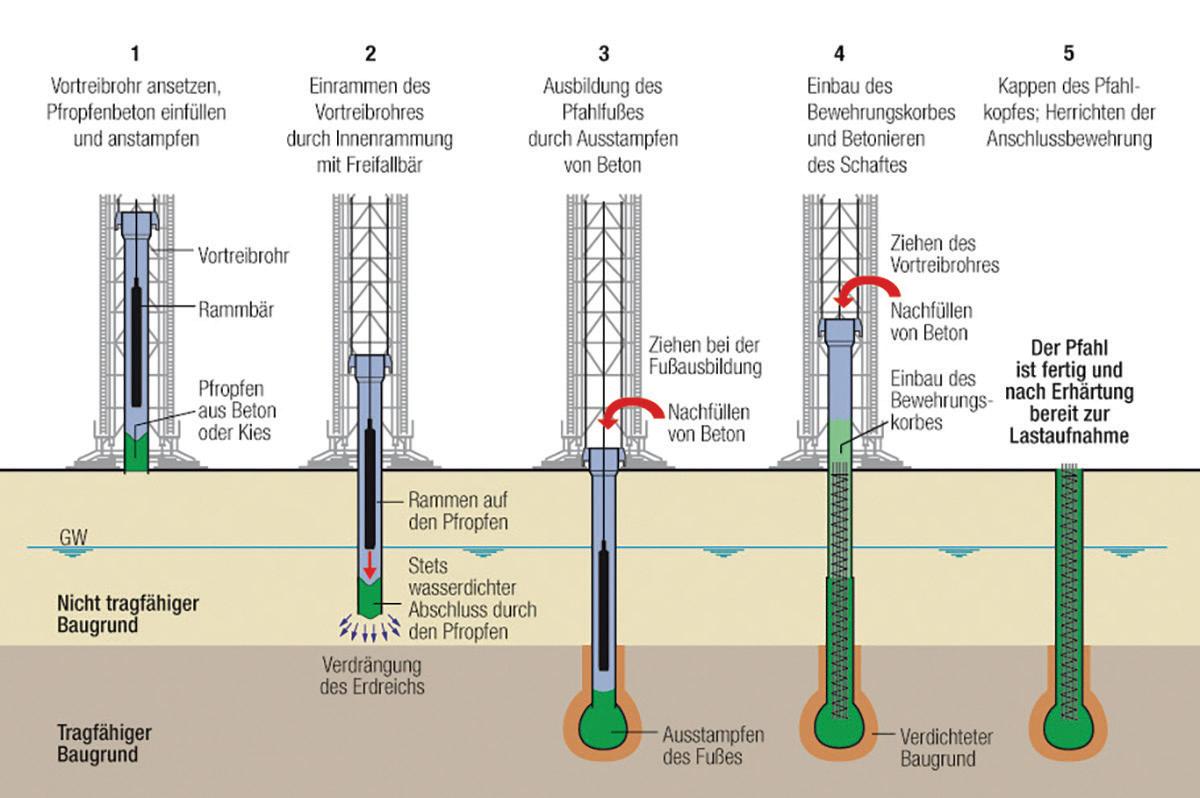
Production of the Franki pile by driving.
| ©Stump-Franki Spezialtiefbau GmbH
Design Notes
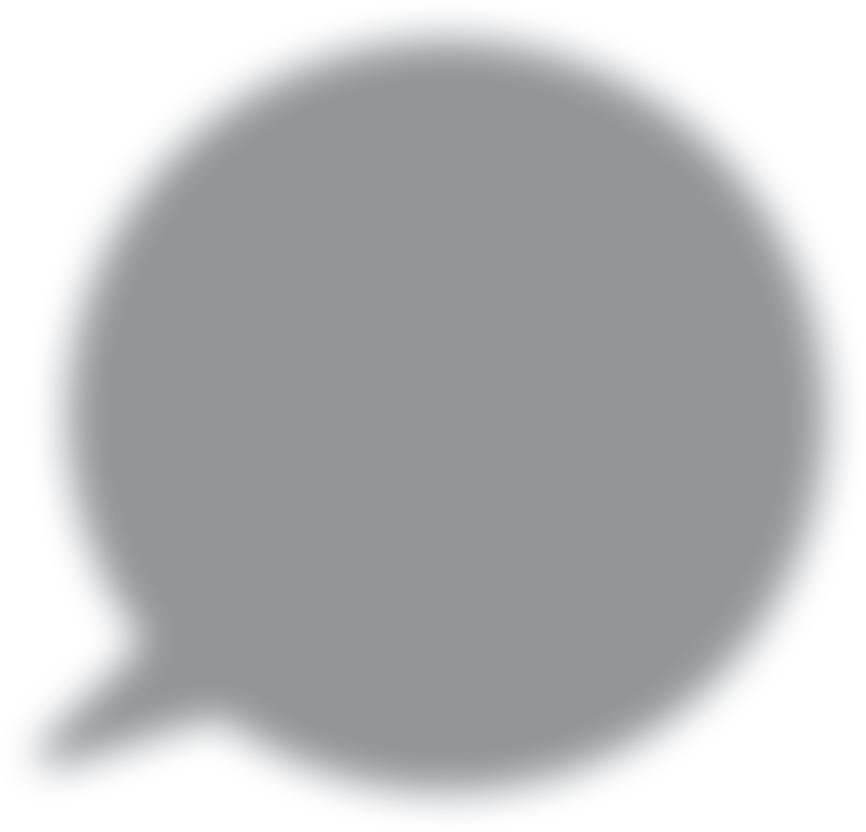


The Franki rams in action: With enormous weight, the free-fall hammer falls into the driving pipe to compact concrete and gravel to the stable foot of the foundation
pile. The SIKO rotary encoder WV58MR also integrated a gear ratio so that we receive monitors, among other things, the an enormous number of signals that enable us an enormous number of signals that enable us positions of the winches. to detect the position permanently.” Because failures of individual components can have to detect the position permanently.” Because failures of individual components can have | ©Stump-Franki Spezialtiefbau GmbH serious eff ects in such an application with heavy serious eff ects in such an application with heavy equipment, the safety function of the rotary encoder equipment, the safety function of the rotary encoder with safety class PLd is decisive. It is entirely redundant with safety class PLd is decisive. It is entirely redundant with two separate sensor circuits and thus ensures safe with two separate sensor circuits and thus ensures safe handling. Additionally, it is an absolute encoder, which recognizes its position precisely even in the de-energized state and does not require reference travel. In this case, the integration into the controller takes place via a CANopen safety interface. “What is also important for our application is the absolute robustness. The rotary encoders must be able to withstand the loads — and they do.” The magnetic measuring principle of the rotary encoders, which is ideally suited for use in harsh environments, also meets this requirement. Foundation piles in case of poor soil and heavy load The driving of foundation piles is necessary in the case of poor soil quality and particularly heavy structures. “The advantage of our Franki pile system is that it is a full displacement pile system. As a result, we have no excavated soil and do not have to dispose of anything,” explained Hemmerle. “With the impacted foot, we can adapt to any soil. If it is not possible to drive particularly deep, we can simply impact the foot a little larger and compact it more strongly, thus giving the structure the necessary stability.” DW
SIKO www.siko-global.com
As an absolute encoder with redundant position detection, the WV58MR has been specially developed for challenging measuring tasks in mobile machines.
| ©SIKO Gmbh
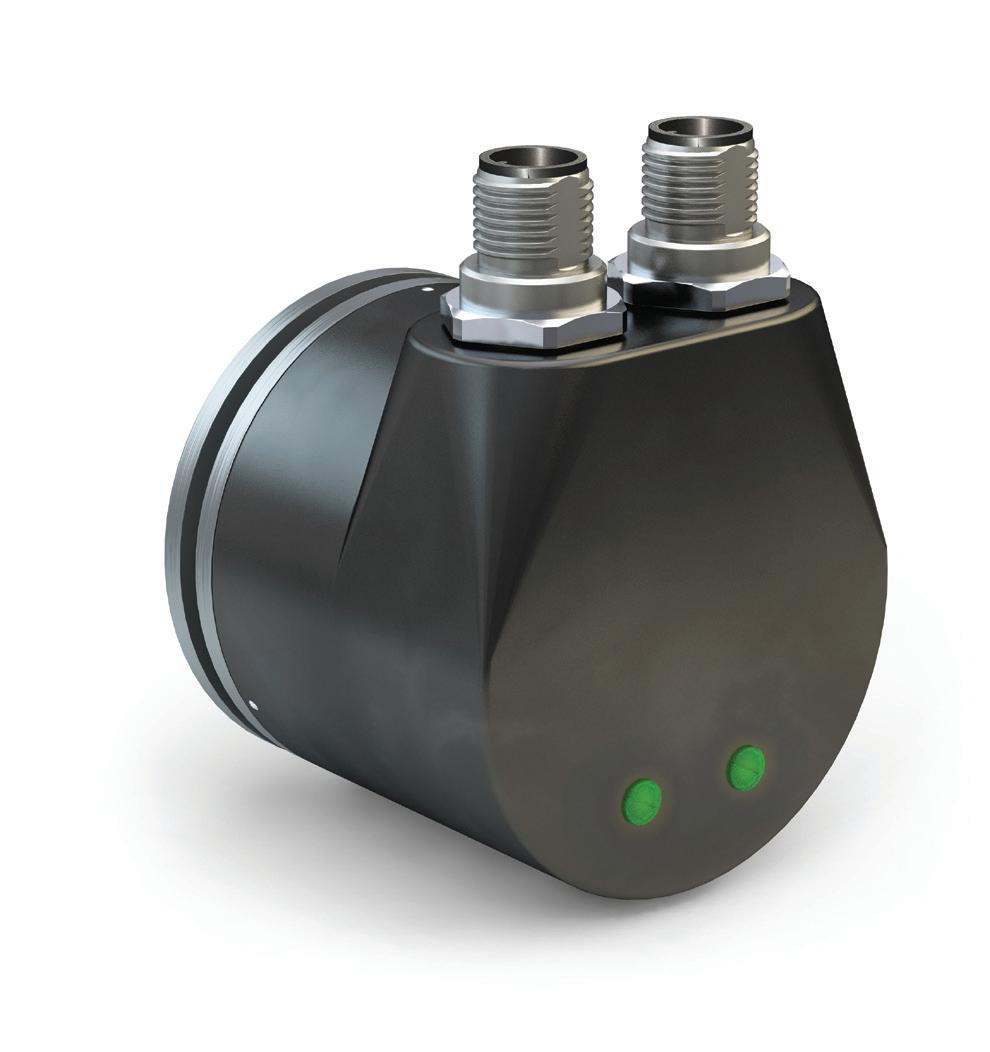

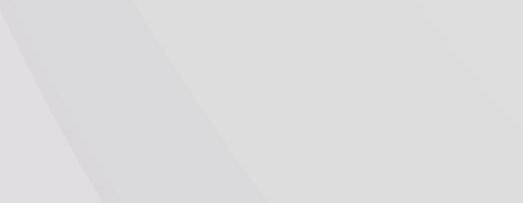
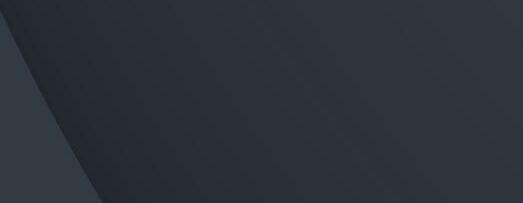
Congratulates
on 4
Since 1982 Sorbothane has provided Engineers and Entrepreneurs with proven Shock, Vibration and Noise Reducing Solutions. Our team stands ready to meet your specific requirements with a Custom Engineered Solution or with one of over 600 Standard Sorbothane Products.
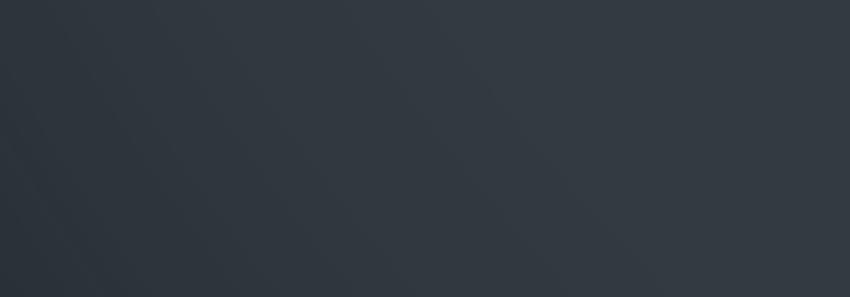
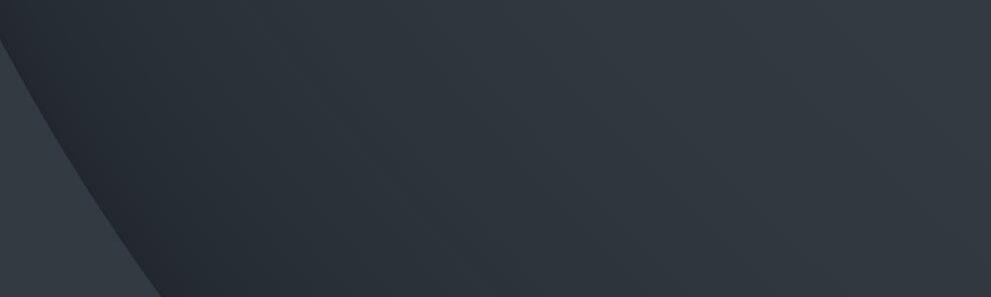
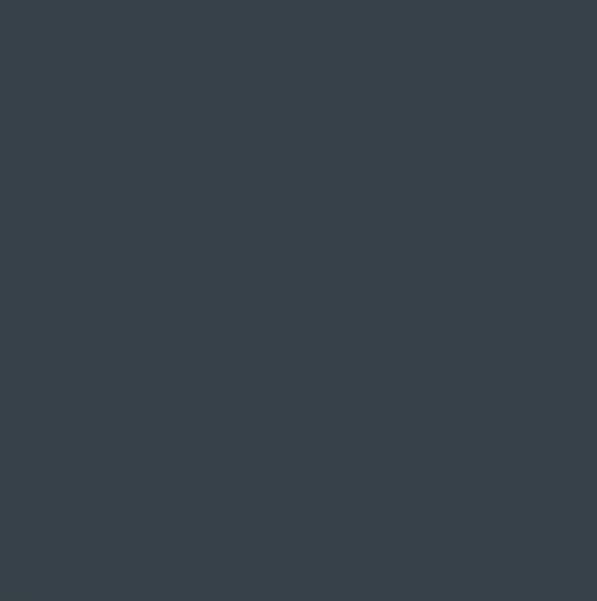
Visit our website for Technical Data, Case Examples and Design Engineering Resources.
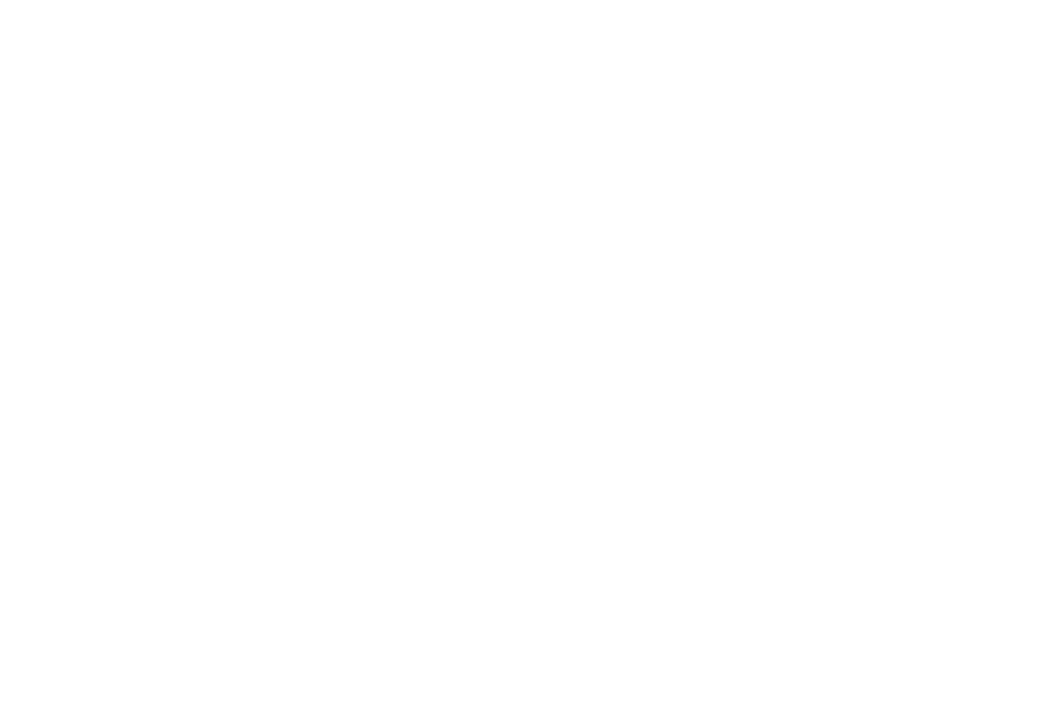
Design Notes
Robot solution for automating the lettuce harvest
Edited by Mike Santora • Managing Editor
Machine vision and AI
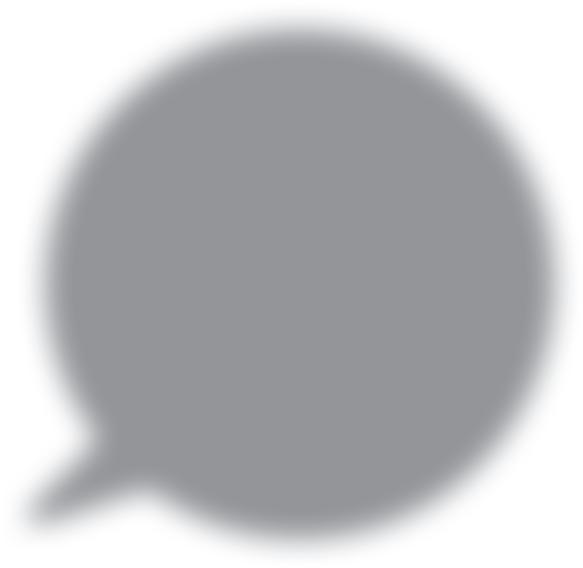
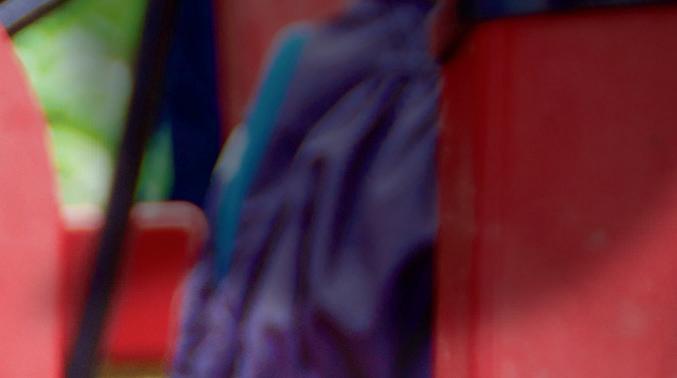
Lettuce is a valuable crop in Europe and the USA. But labor
shortages make it di cult to harvest this valuable fi eld vegetable, as sourcing su cient seasonal labor to meet harvesting commitments is one of the sector’s biggest challenges. Moreover, with wage infl ation rising faster than producer prices, margins are tight. In England, agricultural technology and machinery experts are working with IDS Imaging Development Systems to develop a robotic solution to automate lettuce harvesting. The team is working on a project funded by Innovate UK. It includes experts om the Grimme agricultural machinery factory, the Agri-EPI Centre (Edinburgh UK), Harper Adams University (Newport UK), the Centre for Machine Vision at the University of the West of England (Bristol), and two of the UK’s largest salad producers, G’s Fresh and PDM Produce. Within the project, existing leek harvesting machinery is adapted to li the lettuce clear om the ground and grip it in between pinch belts. The lettuce’s outer, or “wrapper,” leaves will be mechanically removed to expose the stem. Machine vision and artifi cial intelligence are then used to identi a precise cut point on the stem to neatly separate the head of lettuce. “The cutting process of an iceberg is the most technically complicated step in the process to automate, according to teammates
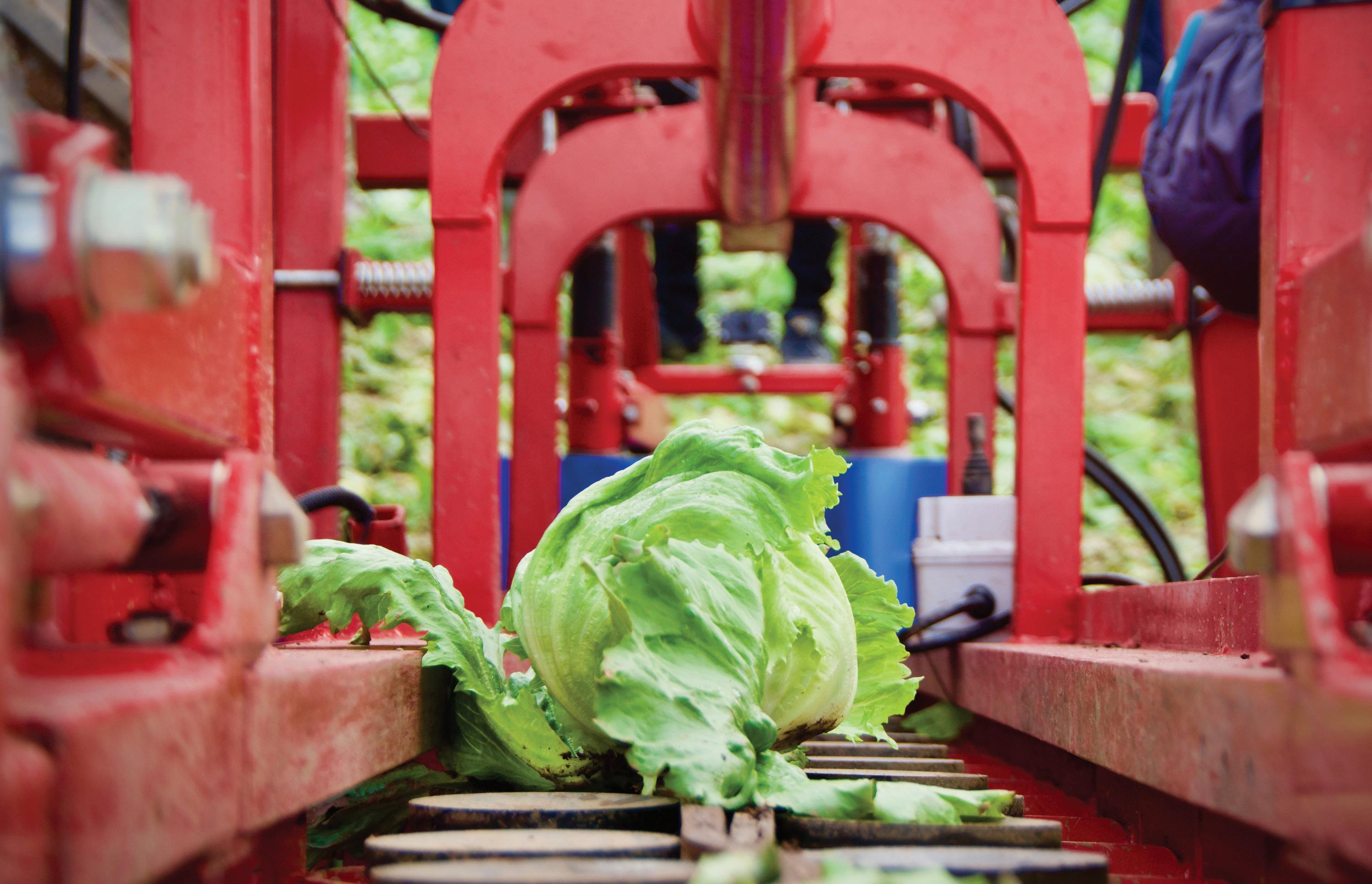
om G subsidiary Salad Harvesting Services Ltd.,” explained IDS Product Sales Specialist Rob Webb. “The prototype harvesting robot being built incorporates a GigE Vision camera om the uEye FA family. It is particularly robust and is therefore ideally suited to demanding environments. “As this is an outdoor application, a housing with IP65/67 protection is required here,” Webb pointed out. The choice fell on the GV-5280FAC-HQ model with the compact 2/3-in. global shutter CMOS sensor IMX264 om Sony. “The sensor was chosen mainly because of its versatility. We don’t need full resolution for AI processing, so sensitivity can be increased by binning. The larger sensor format means that wide-angle optics are not needed either,” Webb summarized the requirements. In the application, the CMOS sensor shows
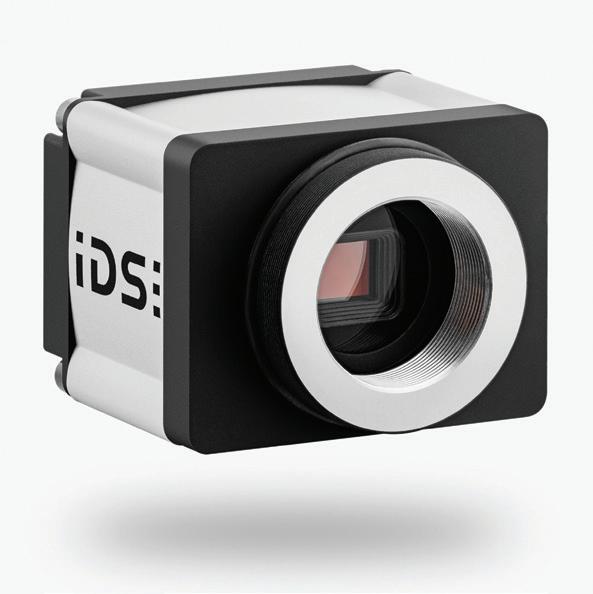
excellent image quality, light sensitivity, and high dynamic range. It delivers almost noise- ee, high-contrast 5 MP images in 5:4 format at 22 fps — even in applications with fl uctuating light conditions. The extensive range of accessories, such as lens tubes and trailing cables, is just as tough as the camera housing and the screwable connectors (8-pin M12 connector with X-coding and 8-pin Binder connector). Another advantage: camera-internal functions such as pixel pre-processing, LUT, or gamma reduce the required computing power to a minimum. The prototype of the robotic mower will be used for fi eld trials in England towards the end of the 2021 season. “We are delighted to be involved in the project and look forward to seeing the results. We are convinced of its potential to automate and increase the e ciency of the lettuce harvest, not only in terms of compensating for the lack of seasonal workers,” a rmed Jan Hartmann, Managing Director of IDS Imaging Development Systems GmbH. The challenges facing the agricultural sector are indeed complex. According to the United Nations Food and Agriculture Organisation (FAO), agricultural productivity will have to increase by almost 50% by 2050 compared to 2012 due to the dramatic increase in population. Such a yield expectation means an enormous challenge for the agricultural industry, which is still in its infancy in terms of digitalization compared to other sectors and is already under high pressure to innovate given climatic changes and labor shortages. The agriculture of the future is based on networked devices and automation. Cameras are an important building block, and artifi cial intelligence is a central technology here. Smart applications such as harvesting robots can make a signifi cant contribution to this. DW
IDS www.ids-imaging.us
Angled NEMA Cords
Made in AMERICA!
Interpower® offers eight different angles of the NEMA 5-15 cord. Why let limited space and impossible angles slow you down? Angled cords provide directional solutions in connecting equipment to outlets while reducing strain on the cord, especially near the plug. Multiple cord angles allow connectivity options for the tightest of spaces, keeping bend radius at a minimum. Manufactured in and shipped from the U.S.A—same day shipping is available on in-stock products. No minimum order requirements.
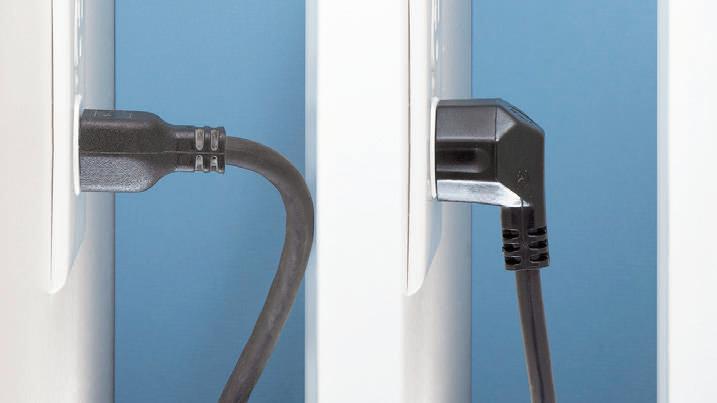

Toll-Free Phone: (800) 662-2290 E-mail: info@interpower.com
Business Hours:
7 a.m.–6 p.m. CST