
6 minute read
3DP-AM
Design for Additive Manufacturing
Stat stacks show the growth in additive manufacturing
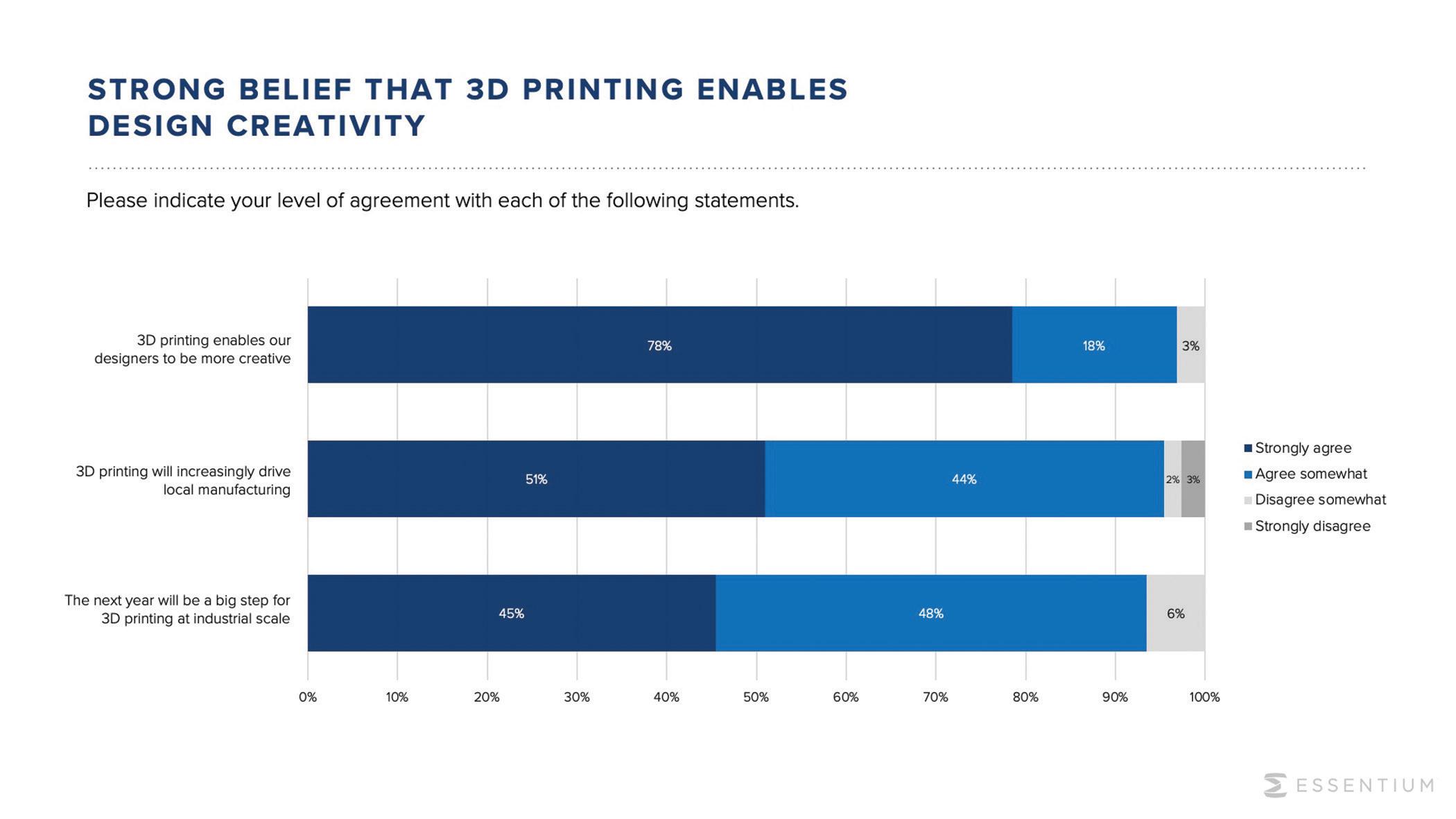
In the thirty plus years since
the founding of the 3D printing industry, countless printing technologies have been invented, patented, and commercialized - om fused fi lament fabrication to digital light processing, selective laser melting to binder jetting, material jetting to sheet lamination, and every unique printing technology in between. With every new technology, the additive manufacturing market has grown its ability to expand into new applications, end-users, and industries. This industry continues to innovate. A recent innovation highlighted by IDTechEx in a recent report1 is bound metal extrusion (BME, also known as metal-polymer fi lament extrusion). The report claims it is one of the fastestgrowing innovations today. BME is a take on classic thermoplastic fi lament extrusion. It involves loading metal powder into a thermoplastic fi lament, which acts as a temporary binder for the metal powder. This metalpolymer fi lament is extruded into a part, a er which the green part undergoes debinding in a furnace to remove residual polymer and sintered in a furnace to fully densi the part. A version of BME is that introduced about four years ago by Desktop Metal. Since then, other companies have launched their own iterations on BME, including Markforged, BASF, BCN3D, 3DGence, and FuseLab. BME has brought interest to the overall printing method of using polymer fi lament or resins as binders to print metals or ceramics; this growing category includes BME as well as ceramic and metal vat photopolymerization companies like 3D Ceram, Incus, Admatec, and Lithoz. Another innovation is set to come om Xerox. The company is preparing to debut its ElemX 3D printer, which uses the company’s proprietary magnetohydrodynamic deposition to print molten metals like aluminum. And American start-up Evolve Additive Solutions recently delivered its fi rst printer

using Selective Thermoplastic Electrophotographic Process (STEP), a technology-based more on 2D laser printing than any existing 3D printing process. Carbon earlier announced fi ndings om a survey2 it conducted with the American Society of Mechanical Engineers (ASME). The survey of practicing engineers involved in the design or development of plastic parts found that 88% of respondents now use 3D printing/ additive manufacturing in some way. And the technology, previously best known for its use in creating prototypes, is increasingly being used for the production of fi nished parts. 40% of respondents said they now use additive manufacturing to produce products. The report says that the technology has secured footholds broadly across industries and that its growing adoption is based on three categories of attributes: its speed, fl exibility in timing and design, and cost-e ciency. In various ways, digitally-driven product development is making major inroads into industries and manufacturing processes long dominated by two older methods that are less fl exible and tend to be more capital intensive: milling and injection molding.
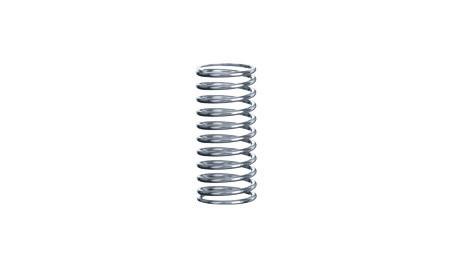
Key fi ndings om the report include: • For the development of polymer products, 3D printing is used more o en than either injection molding or milling. • 3D printing is still the most o en used process for prototyping. • Engineers within the life sciences and industrial machinery sectors reported the highest levels of familiarity with 3D printing. • Use of and familiarity with 3D printing is heavily infl uenced by age and company size — the younger the engineer and the larger the company, the greater the embrace of 3D.

MakerBot also recently released a report, the “2022 State of 3D printing.” According to the report, 3D printing is demonstrating its value to enhance product development. 77% of the global survey respondents invested in 3D printing technology in 2021, driven by its ability to: • Improve R&D (67%) • Accelerate short-run manufacturing (45%) • Reduce dependencies on external suppliers (39%) • Streamline operation
Of the 77% of the respondents, 84% plan to continue making hardware and materials investments in 2022 to increase their capabilities.
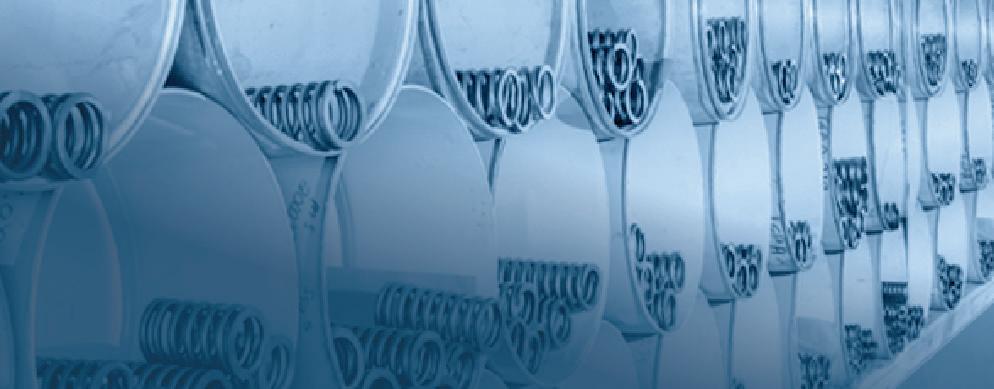
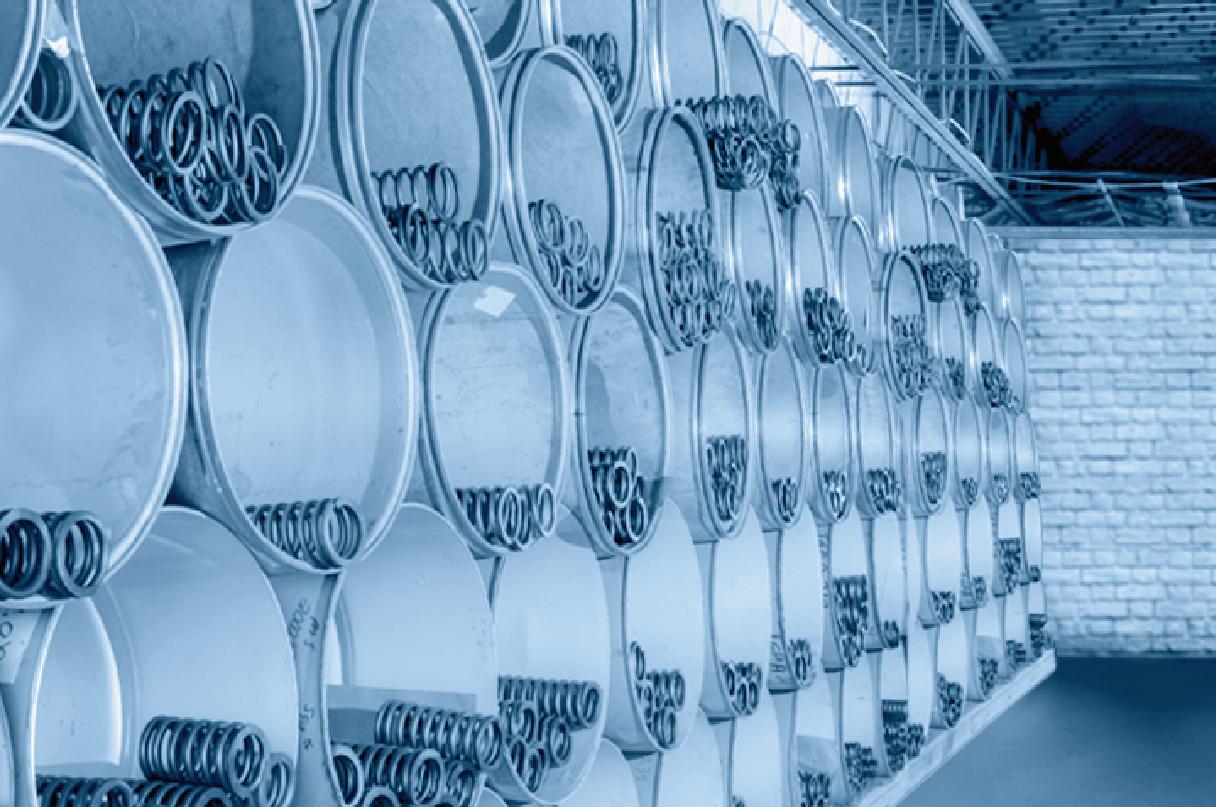


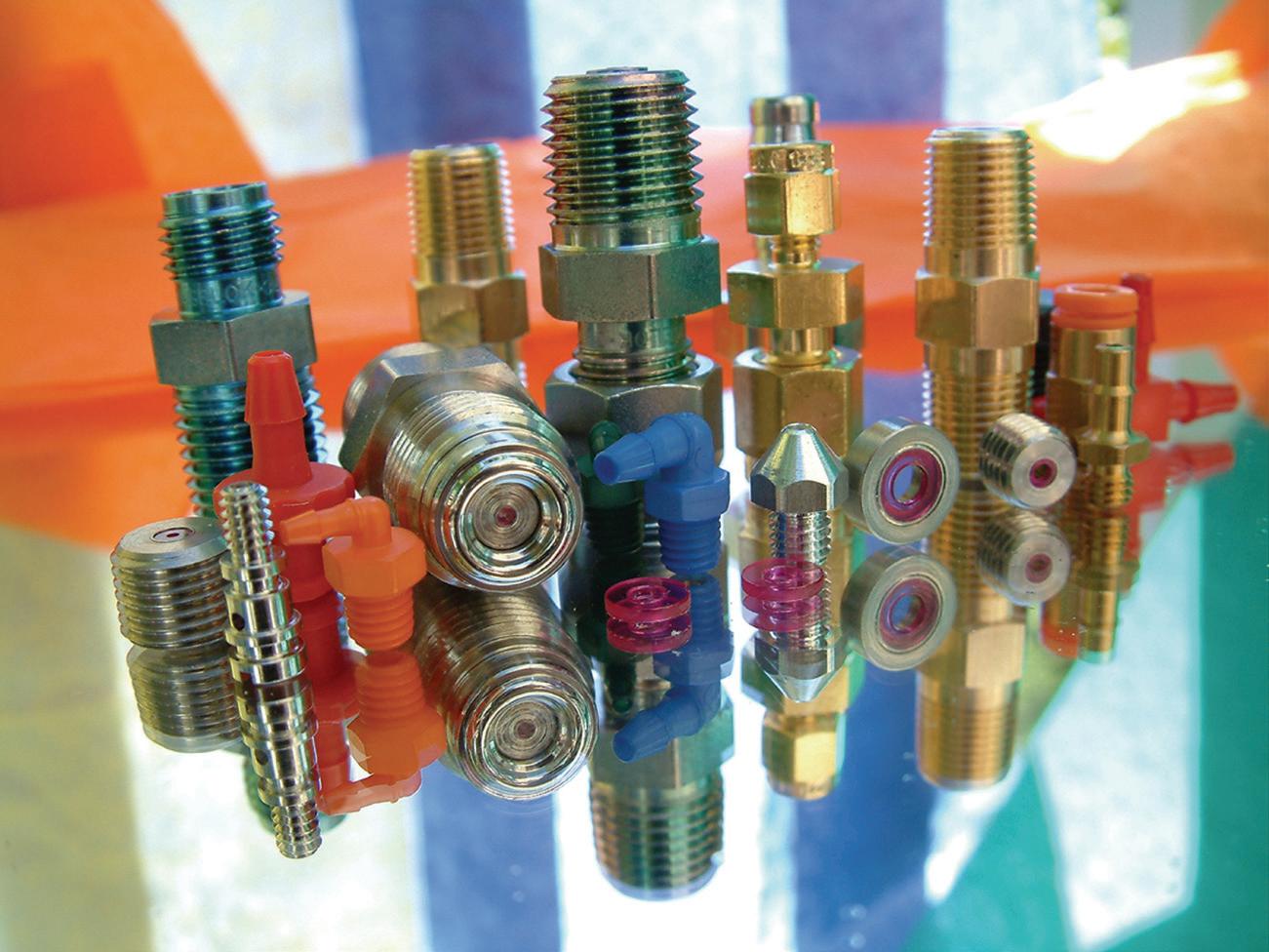
Millions of Springs
Design for Additive Manufacturing
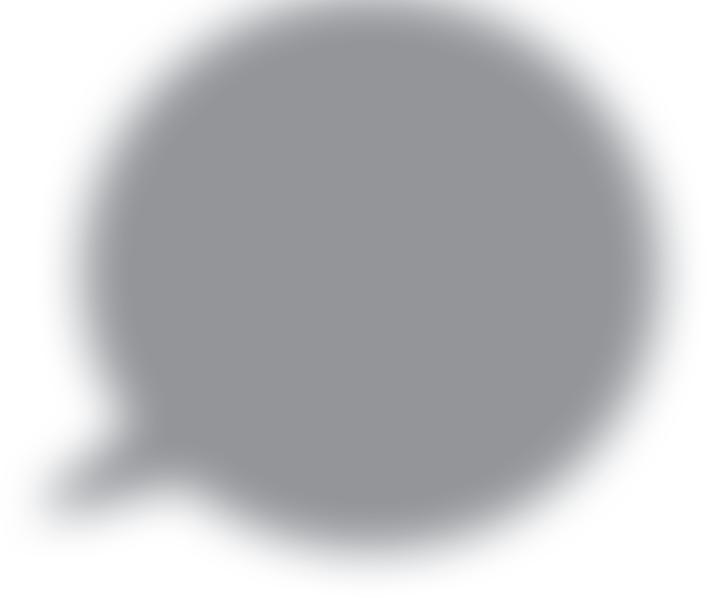
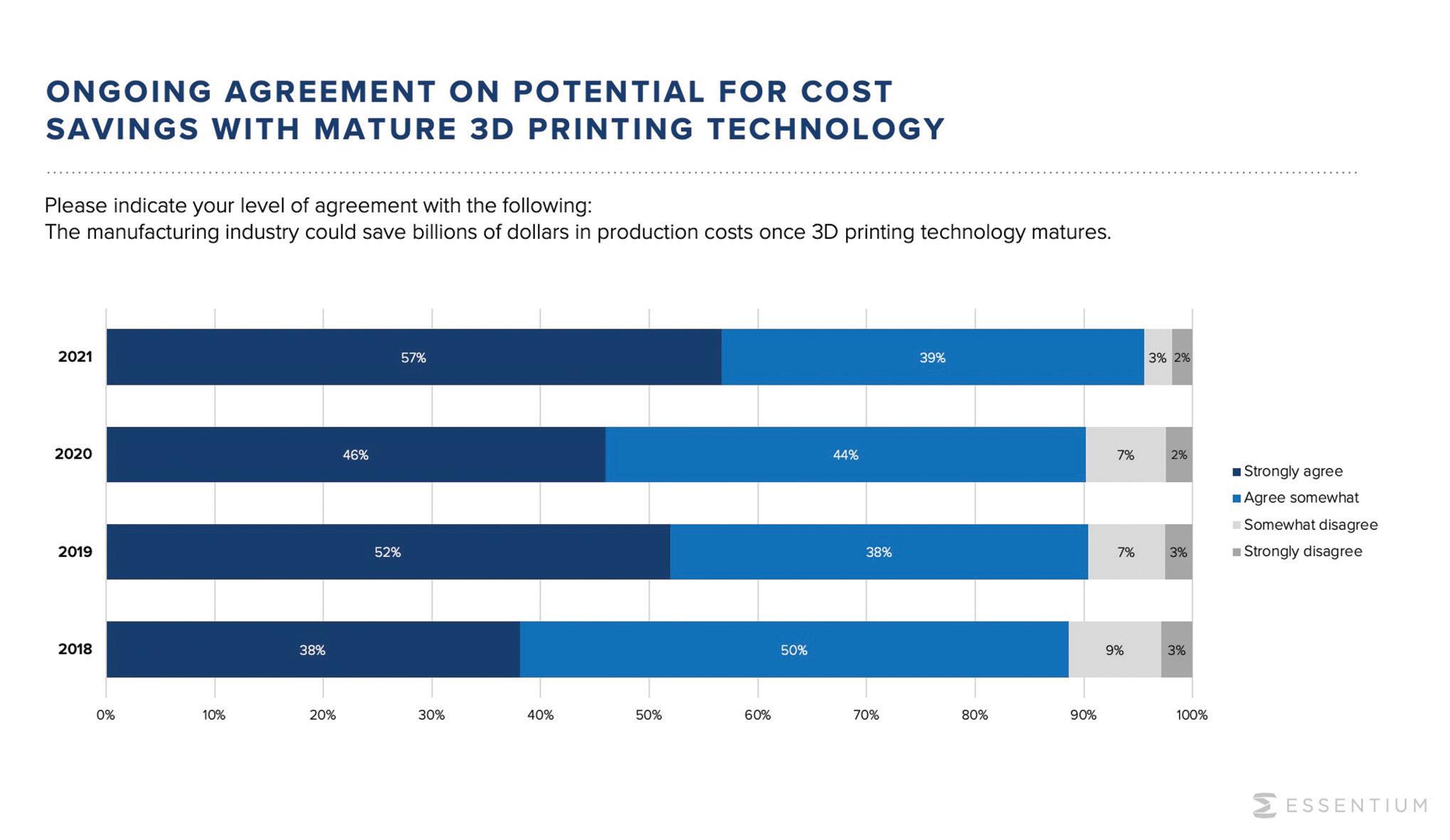
Nearly 60% of all respondents plan to increase their use in 2022, while 69% plan to also invest this year, with 13% planning to make purchases of $10,000 or more. Some of the increase in uses include: • Exploring new applications, om tooling to enduse part production (81%) • Testing new and diff erent materials (42%) • Expanding the use of diff erent 3D printing technologies (22%) • Expanding to mass production (9%)
In addition to prototyping and printing complex geometries, respondents said they plan to use 3D printing to: • Improve their R&D projects (57%) • Reduce dependencies on external suppliers (35%) • Enable large scale manufacturing (8%)
However, respondents would still like the technology to improve in the following areas: • Better print quality (83%) • Increased printing speeds (65%) • Larger build volume (52%)
Respondents were also questioned on what they would like to see with 3D printing in the next 3-5 years: • 3D printing to play a bigger role in the supply chain (44%) • Better sustainability and recyclability eff orts for 3D printing equipment and materials (38%) • Increased use to localize manufacturing (32%)
FDM/FFF continues to be the most widely used 3D printing technology at 93%, with VAT polymerization at 32% and powder bed fusion at 15%. Prototyping and modeling remain the top two applications for 3D printing. But respondents indicate an increase in its use for R&D, tooling, and replacement parts. Roughly 5% of respondents said that they use 3D printing for mass production now. As 3D printing vendors improve their systems, that number could increase within the next few years. Thermoplastics continue to be the number one 3D printing material used in projects, likely due to the lower cost of 3D printing plastics compared to other materials like resins or metals. According to respondents, print accuracy, ease of use, and build volume were the top three most important features they look for in a 3D printer. Respondents also stated that they consider the diverse range of materials (53%) and faster 3D printing speeds (47%) in their purchase decisions. The range of 3D printers on the market today have allowed users to be more selective about their decisions. And Essentium also recently released a report indicating growing confi dence in additive technology. Almost all (96%) manufacturing executives Essentium surveyed agree the industry could save billions in production costs once the technology matures, up om 88% in 2018. The research also revealed a growing number of manufacturers believe that 3D printing at scale can increase revenues, with 56% agreeing that AM will lead to a signifi cant increase in revenue, up om 37% in 2020. The study showed 3D printing technology is empowering designers to invent new ways to fabricate parts at multiple points in the production line, including manufacturing tools, jigs, fi xtures, fi t tests, and end-use parts. The majority (97%) of survey respondents reported that 3D printing allows their designers to be more creative. Continuous innovation is required to realize the full potential of industrial 3D printing at scale. Designers and engineering prioritize improved design and management of platforms (40%), operations teams want better so ware (35%), and procurement and fi nance want to see enhanced workforce development (32%). In addition, while all reported that their 3D printing vendors must be part of an open ecosystem, 74% said it was very important. DW
Resources: 3D Printing Hardware 2022-2032: Technology and Market Outlook” “Additive Manufacturing/3D Printing Adoption om Prototype to Production”