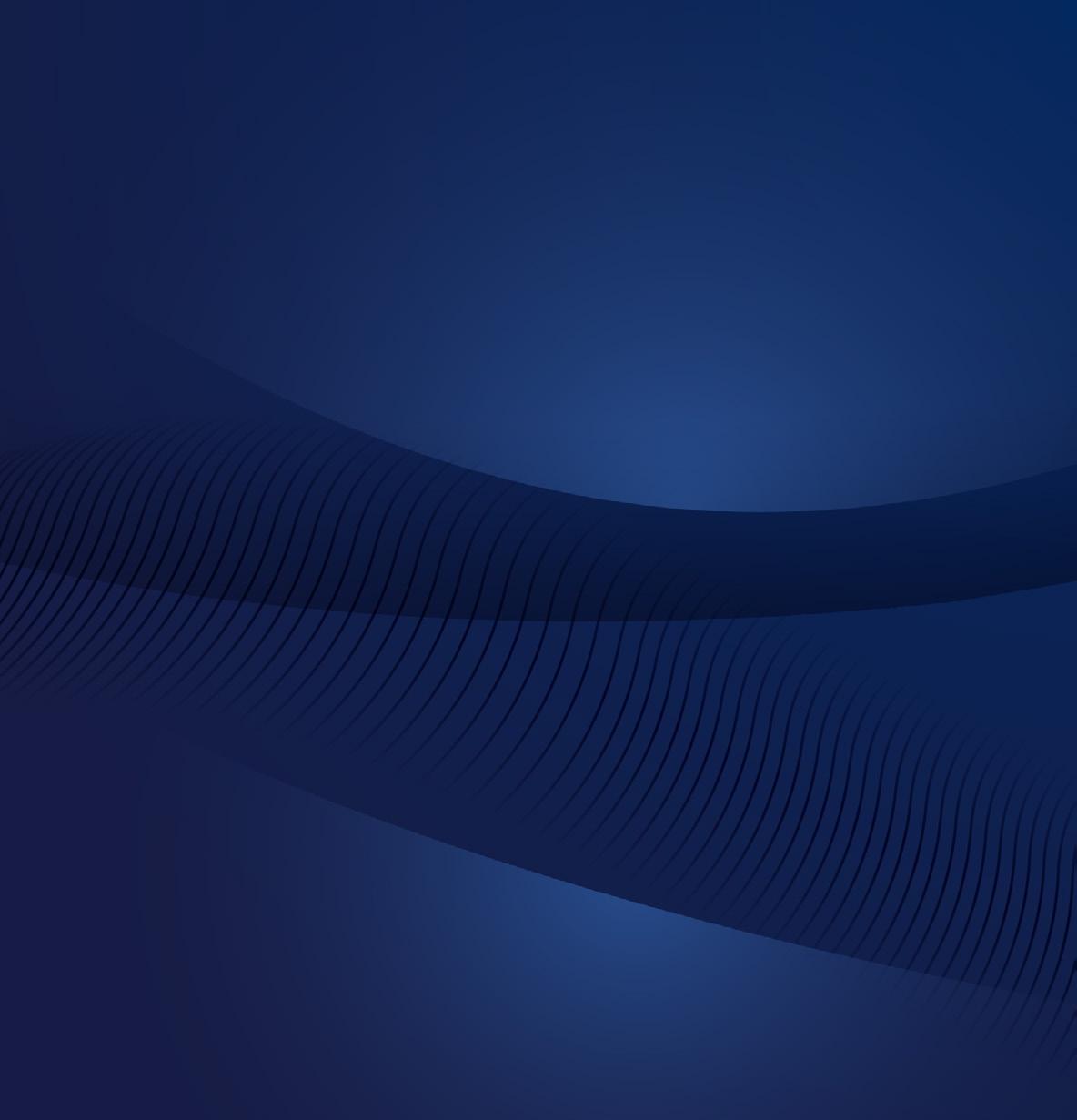

Large, small, or no screen at all, the C-more
Features include:
With the C-more headless HMI, you can display your factory floor data how and where you choose. The new CM5-RHMI has all the powerful functionality of the C-more Touch Panel HMIs, but without display size restrictions. This HDMI-enabled device works with televisions, monitors, projectors, and most any other HDMI display device or use the C-more Remote HMI mobile app and/or the embedded Web Server if you prefer no local display at all. The choice is yours!
C-more Headless HMI priced at: $599.00 (CM5-RHMI)
• HDMI video/audio output with multiple resolutions
• Video: VGA 640x480, SD 720x480, XGA 1024x768, HD 1280x720, FHD 1920x1080
• Audio: use USB audio adapter (not included)
• Works with most HID-compatible resistive and pCap touch screen monitors
• The USB A port allows support for most industrial touch screen monitors in the market
• Multiple connections
• (2) Ethernet, (1) RS-232, (2) RS-485, (1) RS-422 ports support programming and device connections
• USB-B port for programming, monitoring, and configuration
• (4) USB-A ports for USB HID devices such as USB hub, pen drives, touch screen displays, keyboard, mouse, and bar-code scanners
• SD card slot for log files, project memory, or graphic media
• 90MB of user memory
The easy-to-use C-more HMI design software can be downloaded free of charge from our webstore. Get started on your project today or take it for a test drive. Download as often as you need, no license or key required.
Get your copy now at: www.go2adc.com/cmoreswcm5
What makes a company a great place to work? Is it the flexible hours or lunchroom ping pong tournaments? Is it the paid time off or tuition reimbursement? Or maybe the medical benefits and retirement matching?
Everyone has different values and priorities when it comes to employment and workplace satisfaction. To attract the right people, some companies emphasize perks and prestige, while others focus on compensating their employees above the competition.
A few months ago, Design World and our sibling publications asked our audiences to nominate their organizations for the inaugural Top Workplace for Engineers program in partnership with Energage. From the impressive pool of submissions, 34 companies earned this year’s badge of honor.
Collaboration, meaningful projects, innovation, diversity, and creative problem-solving are among the common characteristics of the winners’ missions and cultures, as are transparency, accountability, integrity, and quality. It’s clear that the best workplaces value their people, support personal and professional growth, and nurture work-life balance. Another common theme is that collaboration and creativity flow up and down throughout these organizations, where leadership sets a clear example, and teams nurture trusted relationships.
You can find this year’s list of winners on Engineering.com as well as exclusive interviews
with some of the companies throughout the month. The nomination window for next year’s Top Workplaces for Engineers is already open, so I highly encourage you to consider submitting your organization to highlight its best attributes to the world. Being a Top Workplace builds credibility among job seekers and fosters a sense of pride among current employees. With engineering workforce gaps in the not-so-distant future, this program is designed to give deserving companies a leg up to attract top talent and help skilled engineers find the right workplace to thrive.
Congratulations to this year’s winners! DW
Rachael Pasini
rpasini@wtwhmedia.com
linkedin.com/in/rachaelpasini
As the inventor of the edgewound wave spring with 100+ years of innovation, here’s why Smalley is The Engineer’s Choice®:
ᘩ 11,000+ standard parts in stock
ᘩ Customizable with No-Tooling-Charges™
ᘩ Trusted performance in 25,000+ applications
ᘩ Award-winning quality backed by leading industry certification
Smalley Wave Springs
ᘩ Same Force, Same Travel as a coil spring
ᘩ Lightweight and compact
ᘩ Diameters from .118” to 120” in 40+ materials
Miniaturization makes motion designs small — and in many cases, also makes them more effective, efficient, and faster.
So, what is Teflon exactly? It is a solid fluorocarbon and synthetic fluoropolymer... And it’s fabricated into more fasteners than you might think.
The automotive industry’s evolution through electrification — replacing traditional mechanically driven systems with electric components and systems — is profoundly changing the design of today’s vehicles, which range widely from internal combustion engines to mild hybrids to fully electric architectures.
These
EDITORIAL
VP, Editorial Director Paul J. Heney pheney@wtwhmedia.com
Editor-in-Chief Rachael Pasini rpasini@wtwhmedia.com
Managing Editor Mike Santora msantora@wtwhmedia.com
Executive Editor Lisa Eitel leitel@wtwhmedia.com
Senior Editor Miles Budimir mbudimir@wtwhmedia.com
Senior Editor Mary Gannon mgannon@wtwhmedia.com
PRINT CREATIVE SERVICES
VP, Creative Director Matthew Claney mclaney@wtwhmedia.com
DIGITAL MARKETING
VP, Operations Virginia Goulding vgoulding@wtwhmedia.com
Digital Marketing Manager Taylor Meade tmeade@wtwhmedia.com
PRODUCTION SERVICES
Customer Service Manager Stephanie Hulett shulett@wtwhmedia.com
Customer Service Rep Tracy Powers tpowers@wtwhmedia.com
Customer Service Rep JoAnn Martin jmartin@wtwhmedia.com
Customer Service Rep Renee Massey-Linston renee@wtwhmedia.com
Customer Service Rep Trinidy Longgood tlonggood@wtwhmedia.com
DIGITAL PRODUCTION
Digital Production Manager Reggie Hall rhall@wtwhmedia.com
Digital Production Specialist Nicole Johnson njohnson@wtwhmedia.com
Digital Design Manager Samantha King sking@wtwhmedia.com
Marketing Graphic Designer Hannah Bragg hbragg@wtwhmedia.com
Digital Production Specialist Elise Ondak eondak@wtwhmedia.com
WEB DEVELOPMENT
Web Development Manager B. David Miyares dmiyares@wtwhmedia.com
We
Art Director Allison Washko awashko@wtwhmedia.com
AUDIENCE DEVELOPMENT
Director, Audience Growth Rick Ellis rellis@wtwhmedia.com
Audience Growth Manager Angel Tanner atanner@wtwhmedia.com
Senior Digital Media Manager Patrick Curran pcurran@wtwhmedia.com
Front End Developer Melissa Annand mannand@wtwhmedia.com
Software Engineering Manager David Bozentka dbozentka@wtwhmedia.com
Cable-to-board connectors establish a secure and reliable cable connection between a flexible printed circuit (FBC) and a printed circuit board (PCB). They can be plugged and unplugged easily, and damaged cables can be replaced without extensive effort. Many have locking mechanisms to prevent accidental disconnections, and their design ensures stable signal integrity and power transmission compared to hand-soldered wires.
Hirose has expanded its FPC-to-board product offering to include a two-piece harsh environment connector that simplifies assembly while reducing the size and weight of end products. The compact ZK1 Series connector features a plug side with a terminalless design that switches from discrete wire to FPC. FPC direct connection also simplifies the assembly process, offering time and cost savings compared to traditional discrete wire methods that involve soldering, crimping, and inserting contacts.
Available in a 32-position version, the ZK1 Series connector has a 2 mm pitch and is 44.2 mm long, 19.2 mm wide, and 9.66 mm high. Commonly used in automotive applications, the connector withstands high heat up to 125° C. Its center lock design provides a locking strength greater than 100 N, ensuring vibration resistance and durability. The connector maintains high contact reliability and resistance to dust intrusion due to its two-point contact design.
The receptacle’s design depth prevents contact with terminals, safeguarding against electric shock (equivalent to IP2X). Its design also shields exposed metal and patterns, reducing the risk of electric shock upon touch. Applications include automotive, lighting, motors, battery packs, and chargers. DW
Non-contacting magnetic encoders are position or rotational sensors that use a magnetic field to detect movement without physical contact. Unlike traditional encoders that rely on mechanical components such as brushes, magnetic encoders use magneto-resistive, Halleffect, or other magnetic sensing principles to provide precise feedback on position, speed, or rotation.
Novotechnik recently introduced the MC1-2800 44-Turn magnetic encoder with IO-Link output interface. The patented non-volatile technology retains turn count even when power is lost and reports correct count when power is restored.
The encoder has a measuring range of 15,840° (44 turns), and measures variable information of angle, turns, speed, and limit switch points. It measures rotational speed from 0 to 546 rpm with a resolution of 16-bits, absolute linearity of ≤ ±1°, and repeatability of ≤ ±0.1°.
The mean time to failure (MTTF) is 591 years, and the mechanical life is greater than 50 million movements. Its ingress protection class is rated IP67. The MC1-28000 Series is available with push-on coupling or marked
Novotechnik www.novotechnik.com
quality oriented, stocks abundantly and delivers quickly the best quality and largest array of adjustable, heavy thrust bearing, and torque load carrying retaining devices for bearing, power transmission and other industrial assemblies; and specialized tools for their careful assembly.
Visit our website–whittet-higgins.com–to peruse the many possibilities to improve your assemblies. Much technical detail delineated as well as for engineering assistance. Call your local
As the world’s first ESV, we solve motion control challenges with ingenuity. Evolution Motion Solutions delivers precision-engineered mechanical technologies designed to optimize motion control and enhance system performance. Our Ball Rail and Runner Block program ensures quick access to Bosch Rexroth’s most in-demand profiled ball rails and runner blocks, while our Aluminum Extrusion stocking program provides high-quality framing solutions for a range of industrial applications. Whether you need reliable linear motion components or fully integrated mechanical systems, we have the expertise and inventory to keep your operations moving forward.
994-9184 evolutionmotion.com
or solar photovoltaics, enhance independence and resilience to fluctuating diesel prices, reduce emissions, and may lower operational costs while increasing profit margins.
As such, Molabo is introducing its ISCAD (Intelligent Stator Cage Drive) motor technology to the off-highway, industrial, and commercial markets. The ISCAD technology can deliver 25 to 200 kW peak power and up to 150 kW continuous power at 48 V.
The company’s first off-highway application of this technology is the
Onox, a fully electric tractor equipped with an innovative battery-swapping system.
The tractor integrates four 50 kW Aries 50 drives: two main drives and two power take-offs (PTOs). This configuration provides ample power for tackling tough terrain. The two PTOs deliver clean, quiet electric energy to power farming implements such as hay cutters, balers, disc harrows, mowers, diggers, or grinders.
The Onox tractor’s batteryswapping system eliminates downtime for charging and doesn’t require a powerful grid connection, which can be expensive or unavailable in rural areas. Instead, the batteries
Discover our sleek wearable enclosures, designed for optimal ergonomics. Perfect for smart tech, fitness and medical devices. The cases to be worn like a watch, carried on a lanyard or key ring, and even clipped to a shirt pocket or belt.
Request a sample today!
HYDAC’s square wave air fins deliver maximum heat transfer and exceptional durability with innovative plate-and-bar construction—built for even the toughest environments.
charge from the renewables generated on the farm, and operators swap depleted batteries in just five minutes. Additionally, Onox batteries can serve as auxiliary or emergency energy storage for the facility, helping to stabilize the local electric grid. The tractor is suitable for light farming or homesteading applications and is currently in its final approval and testing phases.
• Less Clogging –Contaminants pass through instead of building up.
• Customizable – Two fin densities balance cooling and clog resistance.
• Optimized Performance – Get localized data for your application.
• Easy Upgrade – Swap any HYDAC cooling element without design changes.
• Lower Maintenance –Reduce costly up-tower cleaning
Today, most electrified off-highway vehicles are built on high-voltage automotive platforms. However, offhighway equipment is often used in remote or rural areas where access to high-voltage trained service personnel and specialized tools may be limited. With Aries drives, service and maintenance can be performed on-site. While the Onox tractor is breaking new ground in the agriculture industry, Molabo technology is also being applied in other heavy-duty sectors, such as generators and factory equipment that previously relied on high-voltage motors. DW
Molabo • www.molabo.com
One axis or fifty. Servo hydraulic or servo electric. Position, velocity, or force control. Direct connection or through EtherCAT.
Permanent magnet ac motors are often favored for electro-hydraulic pump applications because of their efficiency, torque, speed, control, and lower heat generation. Such characteristics provide energy, cost, and space savings for on and off-road vehicles.
Late last year, Parker Hannifin announced the North American release of its NX8M Servo Motor primarily for the mobile electrification market. The NX8M is a suitable solution to electrify hydraulic pumps in low voltage (24, 48, and 96 Vdc) applications.
The motor features high torque density, high efficiency, rated power up to 20 kW, and peak power up to 48 kW. It has mechanical mounting locations on all four sides of the motor housing and an SAE A pump mounting interface. Design engineers can choose between natural convection, water, or oil cooled versions, and the motor can work immersed in oil. The design also includes a breather membrane to minimize internal condensation. The NX8M includes a PT1000
Parker Hannifin www.parker.com
The Triton 7500/3 is the world’s deepest diving three-person acrylic submersible. The innovative DNVcertified vessel, with a fully transparent acrylic pressure hull, can dive to depths of 7,500 ft (2,286 m) for durations exceeding 10 hr, offering unprecedented access to the ocean’s bathypelagic zone, a realm of the ocean that lies between 3,280 to 13,123 ft (1,000 to 4,000 m) below the surface.
Following an upgrade to enhance the Triton 7500/3 capabilities, Base Materials supplied six additional DNVcertified buoyancy modules to achieve the necessary uplift to allow the vessel to dive over 1.4 mi below the ocean’s surface. The modules were precisely CNC-machined and manufactured from Base Material’s DNV-approved Subtec 3,000 buoyancy material
With Interpower cords and cord sets, you don’t have to wait weeks on North American and international cords. With over 2 million cords and components currently in stock to ship the same day, and 1-week U.S. lead times on customized country-specific power cords, you can ease into the new year without stressing about tariffs.
Interpower North American and international cords and cord sets provide the correct AC power for each country-specific customer as to safely connect to each country’s mains power. Interpower tests and inspects their cords after each stage of manufacturing.
— a low-density, high-performance syntactic foam qualified for use at depths down to 3,000 m. With densities from 400 to 650 kg/m3 and grades to suit a range of seawater depths from 2,000 to 11,500 m, the Subtec buoyancy materials comprise high-grade hollow glass microspheres and a novel thermoset polymer matrix, producing ultra-high strength-toweight characteristics with excellent water ingress resistance. From water absorption to hydrostatic crush pressure, density to uniaxial compressive strength, and more, the range is rigorously tested in-house. DW
info@interpower.com
Business Hours: 7 a.m.–5 p.m.
EDITED BY MIKE SANTORA •
ABB has upgraded a variable speed drive to extend the life of NASA’s National Transonic Facility (NTF) wind tunnel by at least 10 years. This service project has boosted the reliability and availability of the world’s largest medium voltage (MV) drive system. To pull it off, drive experts engineered a solution to match the electrical performance and mechanical arrangement of the existing asset. Read on to see how they did it.
As part of an ABB Motion OneCare service agreement, ABB has modernized a variable speed drive (VSD) for NASA (US National Aeronautics and Space Administration) to extend, by at least 10 years, the life of the wind tunnel at its National Transonic Facility (NTF) at Langley Research Center in Hampton, Virginia. The tunnel is used to optimize aircraft performance
and fuel consumption by mimicking flight conditions at high altitudes and close to the speed of sound. It has been used to test the Boeing 777, the Space Shuttle, and its Booster Rocket. In 2021, NASA’s engineers identified a need to upgrade the tunnel’s medium voltage (MV) drive due to the aging of the drive’s components. ABB supplied the drive in 1997 as the most powerful of its
Made in the U.S.A., Interpower North American and international cords allow customers to safely connect to their mains powers no matter what country they live in. Interpower cord sets provide the correct amperages and voltages, so no reconfiguration is needed out of the box. And, if the cords, cord sets, and components are in stock, they will ship the same day.
Interpower tests their cords after each stage of manufacturing. Besides 1-week U.S. lead times, and same-day shipping on in-stock products, cords can be purchased and shipped with no minimum orders.
kind in the world: the 101-megawatt (MW) drive can test models in air or nitrogen flowing at transonic speeds and at ambient or cryogenic temperatures. As a result, the NTF can simulate a wider range of flying conditions than any other wind tunnel, enabling engineers to gain unique insight and hone aircraft designs.
After ABB’s service specialists evaluated the performance and mechanical connections of the existing drive, the next step was to develop a solution based on modern highefficiency power electronic components to match the original drive’s maximum power while achieving high availability and reliability. This resulted in the modernization of the drive — replacing
key components inside the existing footprint with the latest ABB state-ofart technology. The scope included upgrading the small part of the drive (control unit), which minimized the duration and disruption of the project and demonstrated circularity by minimizing waste and logistics as much as possible.
“NASA relied on ABB’s domain expertise, technology, and services to ensure its National Transonic Facility (NTF) provides high reliability and uptime to maximize availability for its testing programs — and optimize the life-cycle value of its assets,” said Oswald Deuchar, Head of Modernization Services, ABB Motion. “Extending the life
of the wind tunnel by at least 10 years supports NASA’s operational goals while upgrading the drive’s key components demonstrates efficiency and circular approach.”
NASA ordered the upgrade project as the first activity under an ABB Motion OneCare service agreement that also covers spare parts and maintenance. This type of agreement provides the flexibility for operators like NASA to bundle together the services they want so that they can optimize the life cycle of their motors, generators, and drives. DW ABB • www.abb.com
• EDITED BY MIKE SANTORA
Major storms like Winter Storm Blair and Hurricanes Helene and Milton aren’t the only threat to the nation’s power grid. Earthquakes, too, can knock out high-voltage electrical grid infrastructure. To protect these assets and other civil structures from seismic stress, engineers manufacture damping systems, some of which reduce vibration by up to 80%. One way to design and tune these high-performance solutions prior to installation is with hydraulically actuated seismic test benches.
To precisely control the position of and pressure to the bench’s cylinders, Diller and his team first replaced the existing valves with three Moog Direct Drive Valves and a Moog 3-Stage Flow Control Servo Valve.
Test benches enable engineers to use a controller and collect data on specimens situated on either side of a bench, separated by a reaction block. A hydraulic shock dyno oscillates dampers at different speeds (from 200 to 2000 mm/sec) and then measures the force of the shock at various velocities. Heavyduty hydraulic cylinders on each side hold their respective test specimens in position against the reaction block. Some of these cylinders can apply up to 800,000 newtons.
Recently, engineers at a facility that manufactures damping systems faced some challenges with their test bench. The engineers wrestled with controlling pressure, collecting data, maintaining up-time, and swapping test specimens in and out. To tackle these challenges, they called Wayland, MI-based Servo Innovations, which specializes in calibrating test systems for the aerospace, automotive, construction, and medical industries.
“The bench wasn’t designed as a closed loop for the PLC, and it had the potential for much more flow control, plus it couldn’t run tests simultaneously
on both sides and periodically leaked hydraulic fluid,” said Troy Diller, CEO of Servo Innovations. “ The engineers also worked harder than necessary to extract all the data for design decisions, and the bench’s safety controls were manual.”
Diller noted several issues. First, test data collected by microphones and cameras was running through Dewesoft Acquisition Software, which required continual calibration. Next, an array of switches was needed to change a test specimen. If there was a problem running a test on one half of the bench, the other side typically shut down. Third, the bench relied on specialized software, and when the test bench manager ran a ramp, the system couldn’t make that happen via both load control and displacement; it was one or the other.
To precisely control the position of and pressure to the bench’s cylinders, Diller and his team first replaced the existing valves with three Moog Direct Drive Valves and a Moog 3-Stage Flow Control Servo Valve. Diller changed the setup for the bench’s servo valves while incorporating Temposonics’ linear position sensors. He then plugged the bench’s cameras and microphone monitoring systems into analog inputs, so the engineers no longer had to pull data off a box to determine displacements.
“Our approach was to precisely set the flow to the cylinders versus trying to slow down the pressure,” added Diller.
Diller’s team replaced the bench controller with a Moog Controller and Moog Control Software. The bench
typically runs bigger seismic tests on one side and shorter ones on the other. Servo Innovations solved the problem of periodic stoppages by running each half with one controller.
“The Moog Control Software also lets the engineers run a test using the Moog components, extract data immediately, and then quickly run a different test,” Diller said. According to Diller, there is now better throughput and data consistency.
“The controller they had in place was ripe for an upgrade, especially when you add multiple valves in parallel or series as we were doing,” said Diller. “You’ll have one or two valves fighting to be the master. So, when you set up something like this, you have offset issues; one valve will feel the other and shift slightly.”
To get the maximum amount of flow, Diller had to strike a balance between a group of valves. The Moog system, says Diller, can shift offsets slightly, and the valves work to balance themselves out. With the previous controller, the test engineers were trying to do this with a series of movements, but each step fell behind the next operation because the system is not fast enough when running at, for example, 10 kHz resolution.
“With the valve configuration we put in place, the operation is a lot faster; they don’t have to worry about the timing problem,” said Diller. “When the controller tells a drive to move, it’s outputted to that valve. One output affects the three valves enabled with a digital I/O, and it’s instant instead of stepped.”
“Load control is very important to a test bench,” Diller noted. “Engineers want to preload the shock and shock configuration to a specific point and zero it out. Then they want to do a rebound for which they can calculate reaction time on a football plot.”
The new servo valves, Moog Controller, Moog Control Software, and integration with the sensors and PLC have streamlined the process and made it repeatable for accurate control every time. DW
moog • www.moog.com
To turn a motion concept for a robotics application into reality, dedicated engineering expertise can be invaluable.
Robotics is among the fastest growing technologies today, transforming a multitude of segments in consumer, industrial, and commercial applications. The increasing use of robotics is enhancing efficiency, safety, and productivity in the manufacturing sector including industrial automation applications. Beyond industrial applications, robots are also enhancing lives in medical settings, such as improving precision in surgery, which can improve patient outcomes and speed up recovery.
This diversity in applications means that, dependent on the robot’s purpose, OEMs have an array of considerations to make in their designs. Central to all robots, whatever the application, is the motion control technology — motors, gears, and feedback devices, that drive the limbs, joints, and end effectors. The application requirements of the robot have significant implications on the design of the motion system.
Not only does motion design require an assessment of the technology that can solve the challenge most efficiently, but it must also satisfy commercial needs for the OEM. This means the motion system must optimally integrate with the overall robot design, while ensuring ease of assembly and regulatory compliance.
Calculating the working points is a primary step for engineers when designing electromechanical systems such as those in robotic applications. Determining torque, radial, and axial loads are critical factors in the motion system design. Alongside these fundamental needs, the kinematic demands of a robot are vital. This includes the motion profile of the device, and how smooth, responsive, and precise this movement should be — all factors that depend on the performance of the motion control system.
Increasingly, for some applications, a crucial element to the dynamic performance of a robot is miniaturization. A compact, lightweight system has low inertia that enables responsiveness, and low mass also optimizes efficiency. Moreover, a micro motion system is essential because of demands on the overall design footprint. To suit the characteristics of many robots and the environments in which they operate, these motion systems must fit within limited physical space and integrate smoothly with other components. In fact, more and more robotic systems being designed and built today feature an increased level of component integration as well as close coupling among components. This leads to reductions in losses and power usage and increases system efficiency and ultimately performance. Yet in achieving this, the motion system must still meet the required operating points and desired motion profile.
In addition to these needs, reliability is also paramount. Maintenance challenges or a failure in an industrial automation setting can mean downtime, but in a medical setting reliability can impact human safety. Miniaturization of the motion system adds complexity considering the demands of thermal management, and engineers must also take into account component compatibility, working points including overload and continuous operation, along with other potential failure modes. The operating environment is also important for reliability, which includes considering temperature and the potential for ingress, so the motion system’s design must ensure adequate protection.
Only after investing time and effort for research into these design considerations, and a concept has been developed, can a design be created. Yet the progression from the conceptual
design of a motion system to one that can be achieved on a manufacturing scale is significant. The need to revise or change technical attributes and previously selected components, or even materials selection, can introduce roadblocks that add significant time to project development.
Prioritizing motion system design requirements at the earliest stage helps to reduce the challenge of moving from prototype to full production. This ranges from the fundamental level of balancing torque output with thermal management and footprint requirements, to longterm reliability considerations involving choice of motor technology and material selection.
This balancing act can be less burdensome with the support of an experienced partner who is well versed in addressing these challenges. Moreover, a motion expert can point towards critical factors, previously unconsidered, that could impact the delivery of the project at
a later timescale — potentially reducing significant time and cost that could otherwise be added in rework.
By relying on motion control experts that offer diverse, applicationspecific solutions, combined with an understanding of manufacturability methods and awareness of commercial challenges, robot developers can achieve the optimum path for motion development. This can also involve the choice between commercial-off-the-shelf (COTS) solutions and customization. What’s more, a significant benefit of working with a dedicated motion expert is the technical support available throughout the entire development process to ensure maximum reliability and integration.
Robotic applications use a diverse range of motor types, depending on application requirements. For instance, miniature brush dc, brushless dc, and stepper motors can be found in the most challenging robotic applications, including collaborative robots, grippers, service robots, prosthetics, exoskeletons, and rehabilitation devices all the way to life critical tools such as surgical robots. And specific application requirements can dictate the type of motor used.
For example, in some cases, frameless motors are a good choice for applications that are space-limited or must strictly control inertial mass. And newer applications such as SCARA robots and their end effectors need torque with low mass in the smallest possible footprint.
Sometimes, helping a customer involves not a custom design but specifying the best motor fit for the application. For example, Portescap recently specified a motion solution for an existing humanoid robot design. The robot manufacturer needed compatibility with their existing drives and controls but wanted to increase torque density and reduce mass. This would be central to improving the robot’s precision by optimizing control of movement, increasing responsiveness, and reducing inertia.
The robot developer also wanted to extend battery lifetime, so the motors needed to have high efficiency. With more than 20 motors per unit, and robots used across a diverse array of environments, reliability was also a priority. The relatively high number of motors per robot, combined with the purchasing demands of the end-user markets, meant that the need to balance cost with value was also important.
The engineering team determined that the characteristics of a brushed dc motor would best fulfil the requirements. Providing simplicity of control, this motor design would ensure integration with the humanoid’s existing architecture. While achieving the cost-point required by the OEM, the inherent characteristics of a brushed dc motor would be well-matched to a humanoid’s close human interaction, where the advantages of high torque at low speed would enable fine control.
Taking into account the array of options in robotic motion development, it’s essential to think beyond the parameters of speed and torque. Not only will the motion system directly impact the robot’s performance, but it will have strong implications for its long-term reliability.
Turning the optimum concept into a manufactured reality is also where expertise can be essential. By partnering with a dedicated motion engineering team, a viable commercial solution, developed to a much closer timescale, is more likely to be achieved. Ideally, this relationship between robot OEM and motion developer should start as early as possible in the project to optimize the outcome. DW
Miniaturization makes motion designs small — and in many cases, also makes them more effective, efficient, and faster.
Lisa Eitel Executive editor
In recent years, the trend towards miniaturization of motion systems (including linear motion) has advanced medical devices, robotics, and designs for automation.
Of course, the term miniature is qualitative and highly dependent on the discrete-automation industry and design type at hand. It term can refer to components and systems with a broad range of footprints. Where miniaturization or a capability such as nanopositioning
isn’t specifically mentioned, design engineers should assume equipment uses mainstay motion technologies. That said, recent decades have seen the unabated spread of small-scale automation that just a decade or two ago was exotic, cost-prohibitive, or downright impossible.
Nowhere are the resulting technologies more specialized than those for new nanopositioning and miniature linear-motion designs — where
a proliferating array of tiny motors, mechanical components, and especially electronics have enabled nanopositioning and miniature machine designs for specialty workcells, handtools, and mobile robotics. These builds often rely on components pre-integrated into subsystems. Some include miniaturized slotless and coreless motors sporting thumbnail-sized drives and encoders within housings are often no larger than a pencil. Others include frameless motors
sans housings and relying on the OEM equipment frame for protection and support. Yet other builds include linear actuators that tightly integrate shapememory alloys; miniature linear stages with linear rails pre-engineered into the build by the supplier; and even piezobased hexapods, stages, and other designs sans the unavoidable bulk of copper-wire-based electromechanical actuation.
In fact, nearly all motion components come in diminutive versions that were unimaginable even a decade ago.
Medical-device manufacturers have developed devices that are less invasive than previous decades’ solutions to better patient comfort and outcomes. So now, implantable heart pumps can sustain a patient for years. Swallowable camera robots can now navigate gastrointestinal systems for noninvasive examinations. Surgical robotics leverage the fine adjustments possible with
today’s miniaturized linear actuation for robot-assisted surgery. Even diagnostic equipment (involving probes, pipettes, and slides in automated laboratories) and prosthetics (such as motorized exoskeletons) are making increased use of compact motion components to enable new precision applications.
Consider infusion and syringe pumps for drug delivery with compact linearmotion systems. These enable dosing that’s more accurate and repeatable than manually operated options. Leadscrews and ballscrews are common here with the latter chosen where efficiency is a priority (as in battery-powered equipment). Eversmaller stepper motors even down the NEMA 6 run closed-loop with encoders enable fine positioning to exact precise fluid dispensing.
Miniaturized linear motion in aerospace
Miniaturized motion systems in aerospace and defense applications actuate satellite mechanisms involved
« Abuse Resistant Belts work where others fail.
« Super Strong Joints are virtually unbreakable.
« High Tension Belts move heavier loads.
« HEHT black belts double capacity.
« Low cost, highly efficient, elastic flat belts.
Split Line-shaft
l High precision. Reasonable price.
l Easy to install. Zero downtime.
in the deployment of small instruments and optical systems. They’re also found on uncrewed aerial vehicles, missileguidance systems, and other launched equipment needing lightweighting while maintaining high precision and (in many cases) long-term reliability even when exposed to extreme temperatures, vibrations, and radiation.
Linear guides complemented by mechanical linear screw drives having anti-backlash features are often applied in these designs. Some feature aluminum, engineered polymer, carbon fiber, titanium, and other alloy subcomponents for reduced weight — especially useful for launched or battery-powered designs. Case in point: In radar, LiDAR, surveillance, and other avionics applications, lightweighted direct-drive actuators are often used to position and stabilize tiny sensors for realtime targeting accuracy. Other
satellite-communication uses are those for antenna beam steering.
Complementing these actuators on guidance systems are often miniature crossed-roller linear guides with features to eliminate backlash. as well as closedloop feedback for micron to sub-micron or better precision.
In many contexts, the term miniaturized robotics refers to the broad class of truly miniscule [think speck to dimesized] assemblies for research and medical devices. Many of these are based on microelectromechanical systems or MEMS combining electrical and mechanical elements for extremely specialized applications. Roboticists forecast that processor and sensor
miniaturization will (for the foreseeable future) continue to help shrink these robotics as well as the broad class of autonomous mobile robots.
But miniaturization has also shrunk the size of six-axis robotics and Cartesian robotics used in manufacturing and other automated operations. For miniature tabletop six-axis robots, enabling motion technologies are miniature high-reduction strain-wave gearing assemblies, widebore frameless motors, compact optical and magnetic absolute encoders, and high-performance servodrives with high-efficiency drive electronics to limit heat generation. For miniature Cartesian robotics used in manufacturing, enabling motion technologies include tiny crossedroller and ball-bearing linear guides (down to 3 and 2 mm across) featuring engineered plastic cages smoothly fitting
around each ball or roller to expose each for more load bearing than metal cages — and to allow closer positioning of the bearing elements for doubling of load capacity in some cases. With patents expired on certain anti-cagecreep mechanisms, some miniature linear guides now feature studded variations that work regardless of the rail orientation to help the linear guide maintain smooth and precise operation.
Look for Part 2 of this article series in a future issue of Design World. DW
Linear Motion Tips linearmotiontips.com
temperatures and then solidify upon cooling.
So, what is Teflon exactly?
Polytetrafluoroethylene (PTFE) is a solid fluorocarbon and synthetic fluoropolymer. The material is made wholly of carbon and fluorine atoms. It has a high molecular weight and is hydrophobic, meaning it does not absorb water.
Fasteners and custom parts made of PTFE are used in applications where high heat and chemical resistance are required. One disadvantage of PTFE is
that it’s not very strong. For instance, it’s so soft you can make an imprint in the material with a fingernail. PTFE is a deformable plastic and is not elastomeric, so it does not naturally retain shape and is subject to creep.
Discovering Teflon
PTFE or polytetrafluoroethylene was accidentally discovered in 1938. At the time, Roy J. Plunket was a chemist with the now multinational chemical company, DuPont, and he attempted to
produce chlorofluoroethylene, which is a refrigerant.
Instead, he accidentally made another discovery: the inside of one bottle was coated with a waxy and extremely slippery material. Teflon became the registered trademark in 1945.
By 1948, a DuPont company, Kinetic Chemicals, partnered with General Motors. They produce more than 900 tons of Teflon per year. The material was initially used by the military in artillery shell fuses and in the production of nuclear material for the Manhattan Project. It was also used to coat valves and seals in pipes at the uranium enrichment plant in Oak Ridge, Tennessee.
By the ‘50s, scientists developed copolymers that kept most of the chemical and mechanical properties of PTFE but made it easier to mold. This opened up more practical applications for the material. One example is non-stick Teflon cookware. Another: Teflon-coated fasteners.
Only a few substances can affect the carbon-fluorine bonds of PTFE, including alkali metals (molten or in solution.) Rare, fluorinated compounds at high temperatures and pressures such as xenon difluoride and cobalt (III) fluoride can also attack the bonds. Additionally, aluminum and magnesium at high temperatures will damage them.
PTFE has one of the lowest coefficients of friction of any solid. This makes it nearly impossible to glue anything to Teflon, regardless of the material or adhesive used.
PTFE is a polymer with a melting point of 326°C or 620°F. In addition, it also maintains its properties such as high strength, toughness, and self-lubrication at extremely low temperatures, such as -268°C or -450°F. At temperatures, above 650°C or 1200°F, PTFE will undergo depolymerization.
Teflon is non-flammable. This is one advantage for fasteners and custom parts. Depending on the applications, engineers often consider Teflon a costeffective material choice for corrosion resistance. It can be a suitable choice over weaker alloys, such as stainless steel.
Thanks to its unique advantages, PTFE is used in many applications, from cookware to aerospace, and many more. The material has excellent dielectric properties. So, about 50% of PTFE production is used in wiring and components for aerospace, computer, and semiconductor applications because of this insulating property.
Another example is in industrial applications because of the material’s low friction. PTFE is fabricated into bearings, gears, gaskets, bushings, and other parts that must operate in a sliding action. This results in energy savings for the operation of some machinery.
Additional applications include medical device manufacturing, food processing plants, construction, plumbing (seals), and others.
The advantages of PTFE include:
• Corrosion resistance — resistant to organic, acid, and alkaline corrosion, with a far higher tensile strength than stainless steel
• Chemical and UV resistance — inert to a range of solvents and chemicals, including sunlight
• Non-flammable and electrically safe — excellent dielectric properties and widely used as an electrical insulator
• Hydrophobic — resists water and moisture absorption (<0.1% in 24 hours)
• Temperature stable — usable between about -350°and 500°F, with a melting point over 600°F
• Highly flexible — pliable, even at below-freezing temperatures
• Low surface friction — the material slides easily much like a lubricant
• Non-stick surface — easy to clean and resists contamination DW
Teflon-coated fasteners are also used in automotive engines to reduce friction or in other industrial machinery to prevent rusting or corrosion due to chemicals in the air or water.
PTFE or Teflon-coated fasteners are highly corrosion resistant, especially at elevated temperatures.
EDITED BY MIKE SANTORA
The automotive industry's evolution through electrification — replacing traditional mechanically driven systems with electric components and systems — is profoundly changing the design of today’s vehicles, which range widely from internal combustion engines to mild hybrids to fully electric architectures.
As systems have evolved from carburetors and simple exhaust systems to precision fuel injectors, emission systems and traction and braking control systems, similar advances have been made in electrification with new architectures, components for electric motors, battery packs, and advanced power electronics. Combined, these advances are pushing engineers to reimagine how vehicles are designed and driven for maximum efficiency, reliability and safety.
Experts from two electronics companies — Matt McWhinney and
Kirk Ulery, business development managers at Molex and Shawn Luke, technical marketing manager at DigiKey — shed light on the current state of the electrification movement and key considerations for the future of the automotive industry.
While the highly watched demand for electric vehicles (EVs) and hybrid vehicles continues to increase, sales of new EVs have slowed over the last several months due to many factors, including market and public policy. Industry experts cite cost
Bayonet locking with 8 contacts > 5.000 mating cycles
PVC/PUR cable in 2 m and 5 m
IP67 mated
and the limited charging infrastructure in the U.S. as two major reasons.
“We’ve had fits and starts on electrification in North America,” Ulery said. “If you’re going more than 100 miles at a time, you know charging infrastructure needs to be addressed.”
Hybrid vehicles, on the other hand, are outpacing EV sales. According to Edmunds data, hybrid purchases in the U.S. saw their biggest surge in 2023, increasing from more than 750,000 sales in 2022 to tipping over one million sales in 2023.
Another emerging category is the mild hybrid, which uses a battery-powered electric motor to supplement gas or diesel usage. Most mild hybrids run on a 48 V electrical system, which is a higher voltage than the electrical systems of a traditional combustion engine vehicle. The 48 V system powers components that are not reliant on the engine, enabling better operational efficiency.
Even with the fast pace of innovation in automotive design, gas-powered vehicles still rule the roadways. According to research by Edmunds, 82% of new vehicles sold today in the U.S. rely on gas. However, the electrification movement is well underway among traditional vehicles to the most advanced high-tech electric models.
“One constant we’re seeing is a lot more electrification — mechanical systems are becoming electrified in all vehicles
for many reasons — especially to drive efficiency,” Ulery noted.
One example is stop-start technology, which turns off the engine when a vehicle stops and automatically restarts when the driver releases the brake or pushes the gas pedal. While this feature can put extra demand on some components, it aims to improve fuel efficiency and reduce greenhouse gas emissions.
Other examples of electrification under the hood are in radiator fans, power steering, HVAC systems, and cooling pumps. All these systems used to be powered by belts off an internal combustion engine (ICE). Electric water pumps are replacing mechanical radiator pumps for more efficient performance, and the precise control with electrical cooling can extend the lifespan of these parts. If there is extended battery management, they also circulate coolant throughout a vehicle to regulate the temperature of the battery pack, electric motors, and power electronics.
Switching to electric-powered modules such as power steering pumps makes the system no longer reliant on the engine, reducing parasitic loads and allowing for more available horsepower. Therefore, automakers can install smaller engines in some vehicles and retain the same driving performance while gaining efficiency benefits and outputting lower emissions.
“Electrification has opened the door to innovative new vehicle designs,” said Luke. “Without the need to accommodate
the ‘belt driven architecture’ with a traditional internal combustion engine, auto manufacturers have more flexibility in where to distribute batteries and charging ports, the ability to increase the amount of space for passengers or cargo, and more.”
Overall, the electrification movement is replacing traditional mechanical with precision electrically controlled systems that can be more efficient. Combined with advances in software control, modern vehicles are cleaner, more energy efficient, and offer performance and sustainability for both passenger and commercial drivers.
Over the last decade, vehicle manufacturers have switched from 12 V to higher voltages, such as 24 V (especially for commercial vehicles) and now to 48 V batteries to increase power capability, reduce vehicle weight, improve acceleration, and realize fuel savings.
Legislation in the U.S. and Europe has been laying the groundwork for emissions reduction in newly built vehicles. A combination of regulatory and market forces is behind the increasing shift to mild hybrid architectures, which include integrated starter generators; 48 V is not only growing in mild hybrids but also seems likely to emerge in more ICE platforms.
The shift to 48 V architecture involves more than just increasing the system voltage. It also requires a change in the
electrical foundation. Feature-rich, higherperformance vehicles rely on lighter and smaller components that deliver the same electrical efficiency as a higher-density model.
“The common thing is that both 12 V and 48 V systems are moving traditional mechanical functions off a serpentine belt to a series of electric motors,” said Ulery. He shared an example of a heavy-duty pickup truck using mechanical energy for its power steering. In many vehicles, this function is becoming electrified. “The amount of energy needed for the power steering takes away from the engine’s horsepower, so by moving it to a separate electrical system, drivers can maintain more power through the drivetrain.”
The automotive industry’s move to higher voltage systems is a gradual one, given the significant impact on the design and manufacturing process. Each manufacturer's transition is on a different timeline based on their products, technical maturity and the requirements of the customers they serve. Plus, all are held to standards and design practices related to the technologies they will be using, including:
• ISO 21780 covers requirements and tests for the electric and electronic components in road vehicles
equipped with an electrical system operating at a nominal voltage of 48 V.
• The VDA Recommendation 320 is published and maintained by the ZVEI-German
Electrical and Electronic Manufacturers’ Association. It covers a wide range of specifications and test requirements for electric and electronic components in motor vehicles to develop the 48 V power supply.
Following the standard to achieve smart battery management is integral to the success of 48 V architecture. With the right design process, automakers can avoid inefficient power storage, increased costs and potential safety risks to drivers.
With vehicles requiring more power than ever to support increasingly sophisticated electrical features, a reliable connector design for 48 V systems relies on several fundamental factors to meet vehicle performance and safety standards.
“Having electronics and the infrastructure — the interconnects to support your vehicle — is essential for safety,” said McWhinney.
Since 48 V systems operate at a higher voltage (than 12 V), connectors and electrical systems must be built with robust materials and proper insulation for safe, reliable performance. This becomes even more important if the voltage is higher than 48 V.
Connector failures can cause vehicle system malfunctions or safety hazards. To prevent disconnections, connectors should include locking mechanisms and strain relief, as well as regular inspections and maintenance checks.
“Safety and monitoring control of the electrical system is more important now than ever,” said McWhinney.
Maintaining signal quality is crucial for higher voltage applications. Poor signal integrity can precipitate malfunctions, so connectors must minimize signal loss and interference with shielded cables, as well as proper grounding and strategic placement. Addressing these considerations requires innovation and expertise, which is where advanced connector solutions come into play.
“It feels so much like table stakes, but it’s underrated how important the interconnect is in automotive design, especially for safety,” added Luke. DW
While the highly watched demand for electric vehicles (EVs) and hybrid vehicles continues to increase, sales of new EVs have slowed over the last several months due to many factors, including market and public policy. Industry experts cite cost and the limited charging infrastructure in the U.S. as two major reasons.
We are passionate about the impact robotics can have on the world.
That’s why for 14 years, the RBR50 Robotics Innovation Awards have honored the most innovative robotics companies, technologies, and applications from around the world.
This year we brought back three major awards: Robot of the Year, Application of the Year, and Startup of the Year. We added a fourth major honor: Robots for Good, which recognizes a robot making a meaningful impact on society.
The RBR50 Gala returns April 30 from 6-8 PM in Boston at the Robotics Summit & Expo. The Gala offers attendees a chance to network with the world’s leading robotics innovators. The Robotics Summit also has a dedicated section on the expo floor highlighting this year’s RBR50 winners. Tickets to the RBR50 Gala are limited and can be purchased online during Robotics Summit & Expo registration.
Complete profiles of all RBR50 winners can be read online at The Robot Report.
Robot of the Year: Waymo robotaxi Waymo is single-handedly keeping the promise of autonomous vehicles (AV) alive in the U.S. In 2024, it steadily scaled its robotaxi operations while others faltered. Waymo last October surpassed 150,000 paid trips per week across its fleets in Los Angeles, Phoenix, and San Francisco. This was after it exceeded 100,000 paid trips per week just two months earlier.
Waymo last year also announced plans to launch robotaxi services in Atlanta and Miami in 2025. It also said it’ll begin
Next Level Performance. Unlock unparalleled precision with our revolutionary strain wave gears. Designed for high-precision applications, these gears are the perfect solution for achieving smooth and efficient motion in your robotic systems. With zero backlash and high-torque density, enhancing dexterity and agility for lifelike movements in humanoid robots is easier than ever.
Benefits of Harmonic Drive® Precision Motion Control Components
• Compact Design: Strain wave gears offer a remarkable power-to-weight ratio. Their compact form allows for more flexibility in design, letting you create humanoid robots that are not only agile but space-efficient and lightweight.
• High Precision: Intricate and precise motion is ensured with zero backlash and industry-leading accuracy and repeatability.
• Superior Load Capacity: Engineered to move in highly dynamic environments, humanoid robots designed for various applications, from industrial automation to advanced research projects.
• Smooth Operation: Say goodbye to jerky movements. Say hello to the new standard of humanoid engineering. With multiple gear teeth always engaged, experience fluid and precise motion throughout your system.
• Built-In Servo Drives: Compatible with a variety of motors and control systems, our integrated actuators, with built-in servo drives, make integration into existing designs smooth and easy.
Explore how our strain wave gear technology can transform your robotics. Visit our website: www. harmonicdrive.net/products/integrated-actuators or reach out to our sales team for more information.
As of October 2024, Waymo robotaxis were providing more than 150,000 paid trips and driving over 1 million fully autonomous miles every week. Waymo
testing in Tokyo for its first international “road trip.”
The AV industry has long been plagued by companies that overpromised and underdelivered. After years of delays, technical setbacks, and high-profile failures, many people question whether AVs will ever become a widespread reality.
Waymo has proven to be the exception to this rule. It further solidified its position as the dominant player in the U.S. robotaxi market in 2024. And, more importantly, it’s showing that safe, autonomous ride-hailing at scale is not just possible – it’s already here.
TEPCO wins Application of the Year
Robots are perfect for tasks that are dull, dirty, or dangerous. And perhaps no job is more dangerous than the one performed by the Application of the Year Winner.
In October 2024, a remote-controlled robot named Telesco successfully retrieved a small piece of radioactive fuel from Japan’s Fukushima Daiichi nuclear plant. This marked a significant step in the decommissioning efforts of three reactors that lost their cooling systems during the 2011 earthquake and tsunami,
leaving behind an estimated 880 tons of radioactive fuel.
The robot is being used by the Tokyo Electric Power Company (TEPCO), which manages the plant. The potential high levels of radiation in the damaged reactors have made it unsafe for humans. Scientists said the sample will provide critical data to refine decommissioning strategies.
The sample returned was the size of a grain of rice. TEPCO said the sample was significantly less radioactive than it
expected. It said more sampling missions are necessary to obtain more data.
The cleanup of nuclear waste is an enormous challenge. TEPCO’s use of robotics is key to ensuring worker safety and minimizing human exposure to radioactive environments.
Mytra is helping its customers optimize warehouse space by automating traditionally manual pallet handling
processes. Its 3D lattice storage system maximizes density and eliminates aisles while allowing flexibility in handling various payloads, from small items up to 3,000 lb. pallets.
Founded in 2022, Mytra’s system has already been deployed by major companies, including Albertsons, a leading North American grocery business. Albertson’s uses it in distribution centers to buffer and sequence inventory before shipping to stores. The Mytra solution is also useful for cross-docking warehouses as it can statically stage and store full pallets, queuing them for the trailer loading process. Across its customer base, Mytra estimates that warehouses save up to 88% of labor hours.
Mytra was founded by Chris Walti and Ahmad Baitalmal, former leaders in robotics and manufacturing at Tesla and Rivian, respectively. Their domain knowledge of logistics and large-scale automation has helped Mytra design a product that directly addresses the inefficiencies they experienced firsthand in modern warehouses.
Hello Robot’s Stretch 3 mobile manipulator has been recognized with the Robots for Good Award for advancing in-home assistive robotics. Built to support individuals with mobility challenges, Stretch 3 is compact, lightweight, and capable in cluttered environments.
Stretch 3 has already gained traction in research institutions across more than 20 countries and is gaining ground in real-world applications. Individuals with severe mobility impairments are using it to regain independence, engage in social interactions, and ease the burden on caregivers.
Henry Evans, a non-speaking adult with quadriplegia, has shared how Stretch allows him to contribute to household chores and connect with his granddaughter in a way that was previously impossible.
Beyond individual use, Stretch 3 is being tested in assistive applications such as an NIH-funded study exploring robotic support for older adults with early-stage
Mytra’s system has already been deployed by major companies, including Albertsons, a leading American grocer.
Mytra
AVAILABLE IN STANDARD, HEAVY LOAD, AND LIGHTWEIGHT CONFIGURATIONS, OFFERING HIGH PRECISION, EFFICIENCY, TORSIONAL RIGIDITY, AND LOW STARTING TORQUE.
LIGHTWEIGHT AND COMPACT DESIGN, EASY TO INSTALL AND MAINTENANCE, VARIETIES OF BEARING TYPES AND SIZES FOR SOLUTION.
EQUIPPED WITH A WATER-COOLED TORQUE MOTOR, HIGH-PRECISION BEARINGS, ANGLE ENCODERS, AND A POWERFUL BRAKE SYSTEM.
ENGINEERS ON-SITE TO ASSIST IN FINDING THE IDEAL SOLUTION.
dementia. Hello Robot has also partnered with the ALS Association to develop solutions tailored to that community’s needs.
With open-source software and continued development, Stretch 3 is accelerating the future of at-home assistive robots.
Other notable winners
We couldn’t create a list of the most innovative robotics developments without humanoids. Agility Robotics’ Digit humanoid, last year’s Robot of the Year winner, returns after landing its first commercial gig.
GXO, the world’s largest pure-play contract logistics provider, deployed a “small fleet” of Digits at a Spanx facility in Georgia under a robotics-as-a-service model. The humanoids pick up totes from 6 River Systems‘ Chuck autonomous mobile robots and places them onto conveyors.
The other humanoid on the list is Boston Dynamics’ new, all-electric Atlas. The electric Atlas is inherently more sustainable and safer than the previous model, boasting new levels of mobility, strength, and dexterity. Its head and torso are capable of unlimited rotation, which
increases efficiency, and many of the new Atlas’ joints are continuous.
The new Atlas is being tested with industry partners, starting with Hyundai, which acquired Boston Dynamics in 2020 for nearly $1 billion.
NASA won an award for the Ingenuity Helicopter, which retired after a threeyear journey on Mars that defied all expectations. Ingenuity was the first-ever aircraft to fly on another planet, hitching a ride to Mars on the Perseverance Rover in February 2021.
Ingenuity then completed 72 flights, flew for over 128 minutes, traveled 11 miles (17.7 kilometers), and reached an altitude of 79 feet (24 meters), dealing with dead sensors, dust storms, emergency landings, frigid Mars temperatures, and more challenges along the way.
Ingenuity’s impact will be felt in many future NASA missions. The organization said it plans to send two more helicopters to aid in the Mars sample return campaign to bring soil samples back to Earth.
We hope you join us at the RBR50 Gala to celebrate this year’s winners and connect with the brightest minds in robotics. RR
Organization: Country: Website: Year Founded: Number of Employees: Award Category: Innovation:
Organization: Country: Website: Year Founded: Number of Employees: Award Category: Innovation:
ABB Robotics U.S. abb.com 1974 500+ Technology Launches next-generation OmniCore robotics control platform Agility Robotics U.S. agilityrobotics.com 2015 101-500 Application
Organization: Country: Website: Year Founded: Number of Employees: Award Category: Innovation:
Organization: Country: Website: Year Founded: Number of Employees: Award Category: Innovation:
Organization: Country: Website: Year Founded: Number of Employees: Award Category: Innovation:
Digit is the first humanoid deployed in a commercial application Amazon Robotics U.S. amazon.jobs/en/teams/amazon-robotics 2003 500+ Application Amazon opens its most automated facility in Shreveport, La. Asensus Surgical U.S. asensus.com 2006 101-500 Application
Senhance system brings minimally-invasive robotic surgery to pediatrics Beewise U.S. beewise.ag 2018 101-500 Application Beewise’s Heat Chamber kills 99% of honeybee mites, chemical-free
Organization: Country: Website: Year Founded: Number of Employees: Award Category: Innovation:
Organization: Country: Website: Year Founded: Number of Employees: Award Category: Innovation:
Boston Dynamics U.S. bostondynamics.com 1992 500+
Technology
Electric version of Atlas is a “game-changer” for humanoid robots Chef Robotics U.S. chefrobotics.ai 2019 11-50
Application
Organization: Country: Website: Year Founded: Number of Employees: Award Category: Innovation:
Organization: Country: Website: Year Founded: Number of Employees: Award Category: Innovation:
Organization: Country: Website: Year Founded: Number of Employees: Award Category: Innovation:
AI-powered robots help food manufacturers increase production Clearpath Robotics by Rockwell Automation Canada clearpathrobotics.com 2009 51-100
Technology
Husky A300 offers rugged, customizable mobile robotics platform Cognibotics Sweden cognibotics.com 2013 11-50
Technology
HKM1800 picking robot enhances productivity of warehouses Collaborative Robotics U.S. co.bot 2022 51-100
Technology
Proxie mobile manipulator simplifies material handling automation
Organization: Country: Website: Year Founded: Number of Employees: Award Category: Innovation:
Organization: Country: Website: Year Founded: Number of Employees: Award Category: Innovation:
Organization: Country: Website: Year Founded: Number of Employees: Award Category: Innovation:
Cyngn U.S. cyngn.com 2013 101-500
Technology
DriveMod enables autonomous navigation across indoor and outdoor spaces
Organization: Country: Website: Year Founded: Number of Employees: Award Category: Innovation:
Organization: Country: Website: Year Founded: Number of Employees: Award Category: Innovation:
Endiatx U.S. endiatx.com 2019 11-50
Technology
Swallowable robot offers real-time, non-invasive stomach diagnostics FBR Australia fbr.com.au 1994 101-500
Application
Hadrian X bricklaying robot builds first five homes in demo program ForceN Canada forcen.tech 2015 11-50
Technology
ForceN redefines force-torque sensing with custom plug-and-play approach
Geek+ U.S. geekplus.com/en 2015 101-500
Application
Geek+ robots help automate Unilever’s largest production facility worldwide
Organization: Country: Website: Year Founded: Number of Employees: Award Category: Innovation:
GrayMatter Robotics U.S. graymatter-robotics.com 2020 50-100
Application Scan&Sand helps automate labor-intensive ambulance manufacturing
Organization: Country: Website: Year Founded: Number of Employees: Award Category: Innovation:
HEBI Robotics U.S. hebirobotics.com 2014 11-50
Technology Inchworm-style robots offer a unique approach to mobility
Organization: Country: Website: Year Founded: Number of Employees: Award Category: Innovation:
Organization: Country: Website: Year Founded: Number of Employees: Award Category: Innovation:
Organization: Country: Website: Year Founded: Number of Employees: Award Category: Innovation:
Organization: Country: Website: Year Founded: Number of Employees: Award Category: Innovation:
Hello Robot U.S. hello-robot.com 2017 11-50
Robots for Good Stretch 3 brings in-home assistive robots to life
Organization: Country: Website: Year Founded: Number of Employees: Award Category: Innovation:
Humotech U.S. humotech.com 2015 1-10
Technology
Caplex system improves prosthetic fitting with real-time emulation
Isochronic Switzerland isochronic.com 2020 11-50
Technology
Simultaneous pick-and-place technology increases industrial throughput Johns Hopkins University U.S. jhu.edu 1876 500+ Technology
Researchers use imitation learning to train surgical robots KUKA Germany kuka.com 1898 500+
Application
Robots assist with larvae breeding on Danish insect farm
Organization: Country: Website: Year Founded: Number of Employees: Award Category: Innovation:
Organization: Country: Website: Year Founded: Number of Employees: Award Category: Innovation:
Levita Magnetics U.S. levita.com 2011 11-50
Application Dual-robot surgery successfully removes human prostate Libiao Robotics China libiaorobot.com 2016 101-500
Application Skechers enhances warehouse efficiency with AirRob system
Organization: Country: Website: Year Founded: Number of Employees: Award Category: Innovation:
Organization: Country: Website: Year Founded: Number of Employees: Award Category: Innovation:
LimX Dynamics China limxdynamics.com/en 2022 11-100
Technology TRON 1 multi-modal biped offers a unique R&D platform
Organization: Country: Website: Year Founded: Number of Employees: Award Category: Innovation:
Locus Robotics U.S. locusrobotics.com 2016 101-500 Business Mobile robots surpass 4 billion picks worldwide MAB Robotics Poland mabrobotics.pl 2016 11-50
Technology Waterproof Honey Badger quadruped navigates land and water
Organization: Country: Website: Year Founded: Number of Employees: Award Category: Innovation:
Organization: Country: Website: Year Founded: Number of Employees: Award Category: Innovation:
MassRobotics U.S. massrobotics.org 2015 11-50
Business
MassRobotics helps startups raise more than $1 billion
Mbodi AI U.S. mbodi.ai 2024 1-10
Technology
Hybrid AI architecture helps robots learn via natural language
Organization: Country: Website: Year Founded: Number of Employees: Award Category: Innovation:
maxon Switzerland robotics.maxongroup.com 1961 500+
Technology
High Efficiency Joints set a new standard for robotic actuators
Organization: Country: Website: Year Founded: Number of Employees: Award Category: Innovation:
Organization: Country: Website: Year Founded: Number of Employees: Award Category: Innovation:
Mytra U.S. mytra.ai 2022 51-100
Startup of the Year
Automated storage system brings simplicity to case and pallet handling NASA U.S. nasa.gov 1958 500+
Technology
Ingenuity Helicopter ends three-year historic run on Mars
Organization: Country: Website: Year Founded: Number of Employees: Award Category: Innovation:
Organization: Country: Website: Year Founded: Number of Employees: Award Category: Innovation:
Northrop Grumman U.S. northropgrumman.com 1939 500+
Technology Manta Ray underwater drone passes first military test NVIDIA U.S. nvidia.com 1993 500+
Technology
Open-source Isaac Lab accelerates robot learning
Organization: Country: Website: Year Founded: Number of Employees: Award Category: Innovation:
Organization: Country: Website: Year Founded: Number of Employees: Award Category: Innovation:
NYU Langone U.S. nyulangone.org 1841
500+
Application
Doctors perform world’s first fully robotic double lung transplant Opteran U.S. opteran.com 2020 11-50
Technology European Space Agency tests Mind autonomy platform for future missions
Organization: Country: Website: Year Founded: Number of Employees: Award Category: Innovation:
Organization: Country: Website: Year Founded: Number of Employees: Award Category: Innovation:
OTTO by Rockwell Automation Canada ottomotors.com 2009 101-500
Application
OTTO solves interoperability issues for large automotive OEM
Organization: Country: Website: Year Founded: Number of Employees: Award Category: Innovation:
Pickle Robot U.S. picklerobot.com 2018 51-100
Application
Pickle Robot unloads more than 1.5 million lb. of Randa apparel
Project CETI U.S. projectceti.org 2020 51-100
Application
Researchers use drones to better understand sperm whales
Organization: Country: Website: Year Founded: Number of Employees: Award Category: Innovation:
Reflex Robotics U.S. reflexrobotics.com 2022 51-50
Technology Wheeled mobile manipulator uses teleoperation to multi-task
Organization: Country: Website: Year Founded: Number of Employees: Award Category: Innovation:
Organization: Country: Website: Year Founded: Number of Employees: Award Category: Innovation:
Organization: Country: Website: Year Founded: Number of Employees: Award Category: Innovation:
Organization: Country: Website: Year Founded: Number of Employees: Award Category: Innovation:
Roboto AI U.S. roboto.ai 2022 1-10
Technology Platform helps robotics developers streamline data analysis
Robust AI U.S. robust.ai 2019 51-100
Technology Carter Pro AMR takes human-robot interaction to the next level
Saildrone U.S. saildrone.com 2015 101-500
Application Voyager maritime drones map unexplored areas of the Gulf of Maine
Shadow Robot U.K. shadowrobot.com 1987 11-50
Technology DEX-EE hand helps Google DeepMind advance robotic manipulation
Organization: Country: Website: Year Founded: Number of Employees: Award Category: Innovation:
Organization: Country: Website: Year Founded: Number of Employees: Award Category: Innovation:
SKA Robotics U.S. skarobotics.com 2015 11-50
Application Custom robot tightens fasteners inside 1GW utility-scale generators
Organization: Country: Website: Year Founded: Number of Employees: Award Category: Innovation:
Symbotic U.S. symbotic.com 2007 500+
Application
BreakPack solution drastically reduces each-picking costs
Tennibot U.S. tennibot.com 2020 1-10
Application Partner robot ball machine gives a glimpse into future of sports training
Organization: Country: Website: Year Founded: Number of Employees: Award Category: Innovation:
Tokyo Electric Power Company (TEPCO) Japan tepco.co.jp/en 1951 500+
Application of the Year Robot removes radioactive material from Fukushima nuclear reactor
Organization: Country: Website: Year Founded: Number of Employees: Award Category: Innovation:
Teradyne U.S. teradyne.com/robotics 1960 500+
Technology MC600 mobile manipulator is positioned to handle heavy objects
Organization: Country: Website: Year Founded: Number of Employees: Award Category: Innovation: Waymo U.S. waymo.com 2009 500+ Robot of the Year Robotaxis surpass 150,000 paid rides per week
The SHA-IDT Series is a family of compact actuators that deliver high torque with exceptional accuracy and repeatability. These hollow shaft servo actuators feature Harmonic Drive® precision strain wave gears combined with a brushless servomotor, a brake, two magnetic absolute encoders and an integrated servo drive with CANopen® communication. This revolutionary product eliminates the need for an external drive and greatly simplifies cabling yet delivers high-positional accuracy and torsional stiffness in a compact housing.
United States
www.HarmonicDrive.net
April 2025
Thomas Barré started The Common Language project internally at Airbus. Now, the effort is on its way to becoming an industry standard for OEMs.
PAGE 73
Stepper motors provide precision for aircraft electronic expansion valves • Page 68 ALSO INSIDE:
Reimagine aircraft design with decentralized hydraulics • Page 64
With 3D printing, brushless dc motors, and high-speed digital controls, Domin is at the forefront of revolutionizing how the aerospace industry uses hydraulics.
Aerospace dramatically influenced hydraulics’ evolution in the last century. The move from manual to hydraulic actuation happened quickly in the 1950s and 1960s, yet fundamental hydraulic designs in aircraft have not changed as much since.
“If you look at some of the pumps on the 787, for example, they are probably identical to the ones that were on the 747 in terms of design — even though there were 40 years between them — for several reasons, not least of which is that they work and they’re good,” said Simon Jones, CTO of Domin.
Today, many aircraft have three central systems, each with multiple pumps and reservoirs. Power transfer units may be present if a pump fails to transfer pressure
between different systems. Each actuator also has redundancies with separate hydraulic and electrical systems. Plus, all this equipment requires extensive piping that adds immense weight, complexity, and assembly time.
“What you end up with are planes lugging between one-and-a-half and twoand-a-half tons of hydraulic equipment around with them all the time and burning hundreds of kilos of fuel per flight just to lift these hydraulics,” said Jones. “They generally all have two-stage valves constantly taking a few kilowatts of quiescent loss the whole time you’re flying. For an eight-hour flight, that’s a huge number of kilowatt hours just to power the hydraulics to do nothing. So, you’re caught in this world where
hydraulics are great, but having that hydraulic system on board is hugely costly in terms of infrastructure, size, weight, and power.”
Jones has an aerospace background and previously worked on gas turbines to reduce the weight of certain parts by tens of grams, even single-digit grams at times. He was hard-pressed to take every little piece of weight he could off the engine to get more out of the fuel. Every hundred grams of weight salvaged improved fuel burn by 0.1% and saved the company hundreds of thousands.
“The scale of waste in terms of the amount of energy needed to carry huge systems around on these aircraft is just baffling,” said Jones. “Hydraulics is great, but electrified systems are also great. The
best solution, therefore, should be bringing those two together and using the best of hydraulics without the clunky central stuff, giving it full digital control, and putting it into an electrified system.”
Domin poses to decentralize hydraulic systems and move toward hybrid-electric aircraft to leverage the best of both worlds while shrinking components, reducing weight, and decreasing energy consumption. Jones stated that hydraulics persists because of its power-dense force transmission but doesn’t lend itself well to lightweight electrified architectures, where digital signal transmission enables asset monitoring and optimization.
“The other nice thing is that you can manage redundancy by having multiple units or multiple redundant systems within a given actuator, for example. You can also locally manage energy storage, harvesting, and reuse,” he said.
However, capturing and reusing energy may not be feasible for all systems. For example, braking would be challenging due to its immense energy requirements, whereas flight controls have fully reversible cycles. Today, a big pump applies constant pressure through valves that are always on alert to lift and lower the flight control surfaces. This could be an opportunity to manage energy and eliminate losses so that no energy would be consumed.
“The reason it’s not done today is because it’s really hard to shrink hydraulics and get them to a point where they are efficient, small, compact, and lightweight. If you buy a pump, a valve, and an accumulator and bring all those together, you then have a big block. It just doesn’t work,” said Jones. “If you look at electrohydrostatic systems today, they look like a Frankenstein thing. There’s a few flying, but it hasn’t taken the industry by storm yet because it’s big, clunky, and generally prone to reliability issues.”
Since hydraulics don’t naturally shrink very well in this case, electromechanical actuators may seem like the sensible solution. However, for applications with high levels of shock, vibration, dirt, and temperature fluctuation, as is common for aircraft brakes, landing gear, and flight controls, such solutions can jam and compromise safety. They also must be sized according to the largest force they’d
have to exert and hold, drawing power the entire time.
“There have been billions spent on electromechanical systems for aerospace, and there are almost none flying. And the ones that are aren’t competitive with traditional hydraulic solutions,” said Jones. “So, we’ve identified this niche in the market where everyone wants to use less energy and have less weight. Everyone wants these modern digital systems, but no one can shrink and integrate traditional hydraulic systems nicely. That is the sweet spot for us.”
Domin’s core technology comprises ultracompact, high-performance pumps and highspeed switching valves. The company uses enabling tools, including metal 3D printing, to develop hydraulic products that allow electricity to generate and modulate pressure in a very complex, high-bandwidth manner. Though large-scale commercial aircraft are on their radar, the team has progressed in validating its products on helicopters.
“We’ve done a lot of work on helicopter braking systems. Today, they’ve got a pump on the top deck and pipe all these things down to the cockpit. The pilots have some pedals, and they control some valves. Then, there are more pipes down to the brakes, and you have a separate parking brake with another pump and accumulator. All those things can come out, and we can drop in a really small — the size of an apple — little hydraulic system next to the brake. That’s all control over wire, effectively, and we’re talking tens of kilos of weight savings, which is significant on one of those aircraft,” said Jones.
Shown here is an exploded view of Domin’s S4 Pro, its smallest direct drive servo valve.
But Jones and his team aren’t just looking to compete in the market — they want to make a positive impact on society while decreasing humanity’s footprint. He isn’t convinced that hydrogen and other solutions will be ready for a long time, so he’s thinking about what he can do right now to improve flying today.
“There’s obviously a trend of people who are motivated to look at the sustainability of things and the scarcity of resources,” he said. “But being sustainable doesn’t mean that people shouldn’t fly. It just means that we should make flying easier with a lower overall penalty to the environment.
“Engineers have the power to increase prosperity across the world. We have the power to deliver things that allow more people to do great things and give more people choices. We would love it if we made technology that meant there weren’t necessarily fewer flights, but more people would get on a flight and go and connect with people or see the world or travel — but while recognizing that the [resources] we have in the world … are scarce. Therefore, we should do our best to deliver things that let more people experience all that, but at a lower penalty than today. That’s where we’d love to get to.” A&D
Domin • www.domin.com
• Offer up to 40% lower DCR than previous best-in-class inductors
• Meet NASA low outgassing specifications
• Pass vibration testing to 80 G and shock testing to 1000 G
• Currently offered in eight sizes with inductance values from 0.11 to 47 µH and current ratings up to 38 A
Rachael Pasini • Editor-in-Chief
Precise, repeatable valve control within an aircraft’s environmental control system is critical for regulating cabin temperature. Here’s why engineers typically select stepper motors for the job.
An environmental control system (ECS) regulates an aircraft’s cabin pressure and temperature and includes an electronic expansion valve to manage air conditioning. This valve is integral to the system and requires precision control to efficiently regulate refrigerant flow, and subsequently, maintain crew and passenger comfort.
An electric motor actuates the electronic expansion valve via signals received from the ECS controller, which monitors cabin temperature. The motor drives precise valve regulation to control refrigerant flow into an evaporator. The evaporator receives air from outside the aircraft, which is heated by compression or through bleed air from the engine, and the blend of refrigerant balances air temperature within the cabin.
The electric motor and controls provide variable modulation, which
requires precision to refine refrigerant flow. Engineers typically choose stepper motors to open and close the expansion valve in small, controlled steps, with each step corresponding to a fixed angular movement. Depending on the motor's resolution, these steps or increments are measured in fractions of a degree, achieving the needed precision and repeatable control. The stepper motor also generates sufficient holding torque to maintain the valve’s position without losing steps when under pressure from the refrigerant.
“Depending on how the motor is designed, you can have large or small steps. For such applications, the best solution is to have quite small steps. So roughly, we can say, the step size is 7° with an accuracy of ±0.5°. In most applications, this is good enough,” said Adrien Mettraux, industry manager for
aerospace and defense at Portescap, a Regal Rexnord brand.
Although an aircraft’s ECS should include redundancy, protecting against motor failure is vital for minimizing maintenance costs and time. The stepper motor's design is inherently durable, as it does not rely on mechanical brushes to achieve commutation, nor does it need a feedback device or a complex closedloop controller. This simplicity also helps decrease procurement costs.
When selecting a motor for an electronic expansion valve, important considerations include torque, temperature, pressure, flow rate, reliability, and weight. Low weight and size improve an aircraft’s fuel efficiency and cargocarrying capability. Stepper motors achieve high torque density for their lowspeed operation requirements and do not require complex external electronics or
Performance Products
• High Temp. Adhesive Tapes
• Engineering Grade Polymer Films
• PTFE Coated & Silicone Coated Fabrics
• Silicone Rubber Sheeting
Converting Capabilities
• Roll Width Slitting
• Adhesive Lamination
• Automated Sheeting
• Die Cutting
• Rapid Prototyping
This simplified diagram shows how high-pressure and high-temperature liquid from the condenser flows through the electronic expansion valve and into the evaporator. The controller receives signals from the pressure and temperature sensors and sends a signal to the electronic expansion valve to adjust refrigerant flow. Rachael Pasini/Design World
feedback. This advantage reduces the total weight and size of the package.
“We are in an aerospace environment, so weight is an important criterion,” said Mettraux. “Most of the time, weight is not as important when you have, let’s say, a system in an industrial building. Ultimately, the systems work in the same way, but in aerospace, you also need to consider weight when designing the complete system. Even at motor level, this is something we consider.”
The motor must also resist corrosion and operate for an extremely long time under varying environmental and operating temperatures.
“Now, we are using more sustainable fluids inside of the system. And the new challenge it creates is that the working temperature of the system is higher than it was in the past. So, we have developed hightemperature stepper motors, mainly driven by the fact that the temperature of the refrigerant is higher in the system,” said Mettraux. “We simulate and calculate the performance of the
motor at different working temperatures — not only at room and environmental temperature, but we also help our customers understand the behavior of the motor when the temperature is very low. You can start the plane at -40° C, so the system should work the same when the motor will be quite hot due to the high temperature of the fluid.”
Stepper motors are not the only solution, but they make sense for an ECS and operate as part of a closedloop system. Engineers often use
Can stack technology achieves reasonable accuracy and moderate torque. Portescap
stepper motors in open-loop systems and can close the loop directly with an encoder that measures the motor's position. However, in an ECS, sensors measure the fluid pressure and temperature. The ECS controller closes the loop by sending a signal to the motor to move the expansion valve and adjust the refrigerant flow. The feedback is not directly done on the motor but through its sensors that communicate to the ECS.
“We are not speaking about extremely high speed compared to other applications for which the motor needs to rotate at 15,000 or 100,000 rpm. So, the stepper motor, in this case, is a good solution because it's open loop and the speed is not extremely high,” said Mettraux.
As an alternative to stepper motors, brushless direct current (BLDC) motors could enhance the speed and efficiency of control, while minimizing form factor and weight. While this design adds cost and needs external electronic controls, it could provide an advantage for aircraft that need more rapid changes in cabin temperature control. The more efficient operation of a BLDC motor can also add reliability and minimize the potential for overheating when under duress. However, engineers must also consider simplicity and cost-efficiency when selecting a motor for an aircraft’s ECS electronic expansion valve.
“The stepper motor is not extremely complex compared to a BLDC motor. It is simpler and more cost-effective for the application than a BLDC,” said Mettraux. “The stepper is a kind of BLDC because
it doesn’t have a brush, but a traditional BLDC motor could be a solution. It has very good efficiency, the speed capability is higher, and one of the main advantages of the BLDC is that you can work way above its continuous operation range. With a stepper motor, you can go above the continuous operation range, but with a BLDC motor, you can go way beyond [it], meaning you can get … more torque. This is due to the way the BLDC motors are designed compared to steppers. In some cases, BLDC could provide advantages … but it also needs a more complex controller driving system, and most of the time this is not required for electronic expansion valves.”
In addition, stack stepper motors can also be advantageous for some electronic expansion valve applications. This permanent magnet stepper motor uses simple techniques and designs to create an effective solution with reasonable accuracy and moderate torque. Customization might be required as part of the motor specification, particularly to enhance design integration. Features such as customized mounting plates, output pinions, and modifications to the motor itself might be necessary. A&D
IDEC Corporation www.idec.com Portescap portescap.com
Regal Rexnord regalrexnord.com
Thomas Barré started The Common Language project internally at Airbus. Now, the effort is on its way to becoming an industry standard for OEMs.
he creation of a common language to store and query data for the aerospace and defense (A&D) industry is underway, with original equipment manufacturers (OEMs) such as Airbus and Boeing set to benefit from widely recognized and accepted terms for parts and operations.
In late January, Thomas Barré, solution architect at Airbus, gave a presentation and answered questions about The Common Language project that he initially developed for internal use at Airbus. He shared this information in a webinar hosted and moderated by James Roche, A&D practice director for CIMdata, an Ann Arbor, Michigan-based
global strategic management consulting and research company focused on product lifecycle management (PLM).
Barré said that by mid-2026, The Common Language project is expected to be ready for application at scale. The language will offer OEMs beyond A&D with easy paths for people and machines to clarify, federate and pose questions to blocks of data.
“Prior to the development of this common language, OEMs have spent tens of thousands of hours searching for data without a Rosetta stone to navigate terminology and definitions. Point-topoint mapping across hundreds of IT applications must be updated each time
an application is added or modified. The [way] to overcome this obstacle is to create a standard — which is a consensus by nature — with key players of the domain. [This is] then available for application within aircraft programs as needed,” said Barré.
The language is built on International Organization for Standardization/ International Electrotechnical Commission (ISO/IEC) 81346, a series of international standards originally developed for construction projects such as buildings.
A next step for supporters of the language could be finishing the introduction of the knowledge created by Airbus into the ISO/IEC 81346 series and
A
•
Solid or hollow shaft, high performance, housed and frameless, brushless motors and matching drives for demanding applications.
Hall or sensorless motors and drives for surgical tools, aerospace, military, and scientific instrument applications. Custom drive programing and designs available.
Motors up to 95% efficient, power up to 1,500 watts.
Highest power density in the industry.
Operating temperatures from -73C to 150C
Slotless and slotted designs. Available with encoders and gearheads and separate or integral electronics.
Quantities 1 to 5,000.
www.koford.com Contact us at mail@koford.com
potentially Institute of Electrical and Electronics Engineers (IEEE) standards, with support from experts of the domains. Additional steps could include expanding the recognition of the standard to other standardization bodies and continuing to promote the language. Adopters and developers could work to set up internal and collaborative use cases of the language. With the support of the authors of the standard, Airbus has already developed extensions for additional domains, including energy transformation plants, manufacturing, processes, aircraft, and properties.
The key action necessary to create the language is the attachment of a common language tag for definition to an object or process. For example, the tag “MMA” would be attached to a hydraulic cylinder. An OEM would not be required to rename the part.
An OEM should clearly differentiate between the tag and the elements that provide meaning about the object. Tags should not carry any meaning. Tags are stable over time and serve only to distinguish one object from another. This allows OEMs to continue using their own naming conventions for data and files. Currently, each actor in the aerospace industry has different naming and modeling policies.
“It would be utopia to move to a single naming and modeling convention. It is acknowledged [this] may be unrealistic,” said Roche.
By connecting data to a shared definition through the common language, the system can retrieve related information from different parties. This enables each actor to maintain their own naming and modeling conventions. This approach simplifies data
Software that automatically suggests definitions for aircraft components.
Thomas Barré of Airbus and the Aerospace & Defense PLM Action Group
management, promotes access and eases integration between OEMs and their supply chain.
According to Barré, the best way to promote the new language is to create a pilot project by using an existing project in which data is already being shared. Alternatively, an OEM could create the pilot program by shadowing the current data exchange methods to demonstrate the language’s performance. If there is no current project, the OEM could develop a new test project to apply the common language principles and showcase the benefits for interoperability.
Infrastructure for implementation and the standard for digital twins
An OEM using the common language should create a reference model that uniquely identifies each element without modifying its existing legacy system. An important step will be to distinguish between conceptual elements and their specific instances. For example, the idea of a bolt versus individual bolts used in operations.
A structured approach should simplify a user’s navigation of data and reduce complexity. The model offers flexibility and acts as a universal framework. An OEM should carefully consider implementation details. Legacy systems and new processes need to coexist.
Another ISO standard, ISO 23247, is applicable to digital twins. The latter is defined as digital models of a physical
product, simulation or process. This ISO standard provides some guidance on naming and identifying a subject’s digital twin. An OEM could merge the two approaches because ISO 81346 and ISO 23247 are fully complementary.
“ISO 81346 provides a language of concepts and definitions, acting as a dictionary and grammar to describe a system. ISO 23247 serves as a framework for digital twins in the industrial sector, helping create specific models of industrial systems for various purposes,” said Barré, adding that an OEM should use the common language from ISO 81346 to describe the elements within the models defined by ISO 23247. ISO 23247 specifies the key information to be included in a digital twin, while ISO 81346 ensures that each item within the model is described unambiguously.
The common language can be applied across industries because it provides a solid foundation for broader adoption.
“Organizations in any domain are encouraged to use this approach to enhance cross-industry understanding and interoperability,” said Barré.
Through his last seven years of work developing and promoting the common language, Barré says the ability to label items required four elements: a standard for naming items that was based on
characteristics of that item, a protocol to attach a label to an item based on characteristics of the item; a means to extract those characteristics from sources in multiple formats, including tables and free form text; and automation of the process for labeling billions of items with a practical level of effort and in a practical timeframe. These elements helped the labeling proceed efficiently and on a massive scale without disruption to a business. Barré also developed artificial intelligence (AI) tools for automated labeling.
Barré is now freely offering the four methods and tools that he developed to peers. OEMs interested in The Common Language project can test the language for their own applications or participate in the standardization of the language by sending an email to common.language@ airbus.com.
One of the most significant statements that Barré made in the January webinar was, “Data is the new gold.” He added that OEMs that can manage and utilize data about parts and processes will be ahead of their peers. They will be able to retrieve any needed information from billions of data. A&D
IDEC Corporation www.idec.com Airbus airbus.com
CIMdata cimdata.com
Boker’s provides custom stamped component parts to accommodate nearly any aerospace and defense application, including avionics, control systems, engines, hydraulic, pneumatic and other equipment that require unique specifications. Boker’s Quality Management System is certified to the stringent AS 9100:2016/ISO 9001:2015 standard, and can comply with DFARS and RoHS, with the ability to manufacture to customer provided AN, NAS, MS and MIL spec standards.
At Boker’s, we know that aerospace and defense OEMs demand manufacturing partnerships with the highest levels of precision, quality management and performance, along with a strong understanding of unique industry requirements ranging from space/non-space qualifications to AMS specifications. For over 100 years, Boker’s continues to meet the evolving design needs of the aerospace, aviation and defense industries.
Bokers, Inc. 3104 Snelling Ave Minneapolis, MN 55406 612-729-9365 • www.bokers.com
This specialized Kapton® tape joins treated polyimide film with 3M™ 966, a 2 mil. high temperature (up to 400°F) acrylic adhesive laminated on one or two sides. The balanced performance properties of polyimide and adhesive with low outgassing lowleachable chloride makes this tape ideal for different aerospace applications; including label overlays, flexible circuit attachments, and wire or harness cable wrapping. Customizable in sheets, rolls, and die cut parts. CS Hyde is your source for custom or short run adhesive lamination of polymer film substrates, including PTFE, Nylon, Mylar, PEEK, ULTEM, and other high-performance films.
CS Hyde Company www.cshyde.com 800-461-4161 • Lake Villa, IL 60046
Why accept a standard product for your custom application? NEWT is committed to being the premier manufacturer of choice for customers requiring specialty wire, cable and extruded tubing to meet existing and emerging worldwide markets. Our custom products and solutions are not only engineered to the exacting specifications of our customers, but designed to perform under the harsh conditions of today’s advanced manufacturing processes. Cables we specialize in are LITZ, multi-conductor cables, hybrid configurations, coaxial, twin axial, miniature and micro-miniature coaxial cables, ultra flexible, high flex life, low/ high temperature cables, braids, and a variety of proprietary cable designs. Contact us today and let us help you dream beyond today’s technology and achieve the impossible.
Sorbothane, Inc. offers three straightforward online calculators to make designing with Sorbothane material easier than ever. The online calculators target Load Rating, Impact and Vibration calculations and are an effective way to help determine the proper Sorbothane shape, geometry, and durometer that is best suited for your application.
The Sorbothane site also has a downloadable Engineering Design Guide to assist engineers with a practical hands-on approach to designing with Sorbothane material.
The Sorbothane Engineering Team is available to provide individual consultation and design assistance.
Ryan Ashdown rashdown@wtwhmedia.com 216.316.6691
Jami Brownlee jbrownlee@wtwhmedia.com 224.760.1055
Mary Ann Cooke mcooke@wtwhmedia.com 781.710.4659
Jim Dempsey jdempsey@wtwhmedia.com 216.387.1916
Mike Francesconi mfrancesconi@wtwhmedia.com 630.488.9029
Jim Powers jpowers@wtwhmedia.com 312.925.7793
Publisher Courtney Nagle cseel@wtwhmedia.com 440.523.1685
CEO Matt Logan mlogan@wtwhmedia.com
Co-Founder
Scott McCafferty smccafferty@wtwhmedia.com 310.279.3844
Co-Founder
Marshall Matheson mmatheson@wtwhmedia.com 805.895.3609
CFO
Ken Gradman kgradman@wtwhmedia.com 773-680-5955
www.linkedin.com/company/design-world-online
DESIGN WORLD does not pass judgment on subjects of controversy nor enter into dispute with or between any individuals or organizations. DESIGN WORLD is also an independent forum for the expression of opinions relevant to industry issues. Letters to the editor and by-lined articles express the views of the author and not necessarily of the publisher or the publication. Every effort is made to provide accurate information; however, publisher assumes no responsibility for accuracy of submitted advertising and editorial information. Non-commissioned articles and news releases cannot be acknowledged. Unsolicited materials cannot be returned nor will this organization assume responsibility for their care.
DESIGN WORLD does not endorse any products, programs or services of advertisers or editorial contributors. Copyright© 2025 by WTWH Media, LLC. No part of this publication may be reproduced in any form or by any means, electronic or mechanical, or by recording, or by any information storage or retrieval system, without written permission from the publisher.
Subscription Rates: Free and controlled circulation to qualified subscribers. Nonqualified persons may subscribe at the following rates: U.S. and possessions: 1 year: $125; 2 years: $200; 3 years: $275; Canadian and foreign, 1 year: $195; only US funds are accepted. Single copies $15 each. Subscriptions are prepaid, and check or money orders only.
Subscriber Services: To order a subscription or change an address visit our website at: www.designworldonline.com
DESIGN WORLD (ISSN 1941-7217) is published monthly by: WTWH Media, LLC; 1111 Superior Ave., Suite 2600, Cleveland, OH 44114. Periodicals postage paid at Cleveland, OH & additional mailing offices.
POSTMASTER:
By Mark Jones
I was in Florida when the alert came telling me my house was in danger of catching fire due to an electrical problem. Not news I wanted to receive while 1,400 miles away from home. An internet-connected device plugged into an outlet detected a problem. Whisker Labs was reaching out to warn me.
A flyer from my insurance company was the first time I’d heard of Whisker Labs or its product, Ting. My insurance company would give me one. Free was compelling, but it also set expectations low.
I called Whisker Labs and was told their heuristics were detecting a floating neutral. The representative was insistent I had an issue. I called my wife and then my utility. The utility, having never heard of Whisker Labs or Ting, seethed with skepticism. A crew took a couple of hours to get to the house, checked everything, and said nothing was wrong. But Whisker Labs doubled down, insisting there was an issue.
Ting provides real-time monitoring and history in an app. In looking at the history, the plot of voltage was variable but consistently in range both high and low. I didn’t know what it should look like, but being in range led me to think it was okay. I called the utility again. Again, the crew did their tests and deemed all was good, more aggressively stating I was wasting their time. Whisker Labs was having none of it. They offered to pay for a certified electrician to check it out. He repeated all the tests I’d watched the utility do, again finding nothing. Before leaving, he said the last thing was to visually inspect the overhead line. With binoculars in hand, we walked from the termination at the house toward the power pole at the street. We didn’t need the binoculars. Close to the street, there was an obvious break in the neutral line. It was completely severed,
the ends over a foot apart. My house had a very dangerous floating neutral, exactly what Whisker Labs detected.
I can’t say for certain Whisker Labs saved my wife, me, or my house. I wanted to learn how a tiny little internet-connected device detected what trained crews couldn’t.
I chatted with Bob Marshall, the company’s co-founder and CEO. I experienced what they call a “save.” Most are arcing. My case is less common. The innocuous-looking Ting hanging from an outlet is a “super sophisticated power quality analyzer.” The inspiration came from a family tragedy, the loss of a home to an electrical fire. Marshall was working in lightning detection, the mother of all earthly arcing events. He challenged his team to detect arcing events in home wiring. If they could, it would prevent one of the major causes of house fires. “We were on the wrong side of the impossible line for a long time,” Marshall said. Eventually, they had a prototype that would detect arcing anywhere within a house. In testing, the machine learning algorithms they employed demonstrated they could detect floating neutrals. In
the couple of years they’ve been on the market, they’ve identified about 5,000 floating neutrals like mine. Ting sensors are now in more than a million homes, identifying 25 saves a day. Their analysis points to preventing more than 80% of electrical fires in Ting-equipped homes. It is the reason a growing list of insurance companies are supplying them and why more homeowners are buying them when their insurance companies don’t.
Their little device probes power quality at about 30 MHz, reporting back to the mother ship. They have built what’s likely the largest grid monitoring system anywhere. They continue to evolve their algorithms. I’ve frequently adhered to the adage, “data is like garbage, you better know what you’re going to do with it before you collect it.” They’ve proved that wrong. Now that they are collecting lots of data, they’re finding innovative ways to use it.
The Ting is a device born out of tragedy. Thinking about the small number of ideas that become products and the even smaller number that exceed expectations, I’m happy the folks at Whisker Labs got on the right side of the impossible line. DW
You’ve created a unique design. Now relax. We’ll take it from here.
Custom precision manufacturing.
Manufacturers of Power Transmission and Motion Control Components
• Real-time adjustable PID control
• Integrated 0 to 10 VDC, 4-20 mA signal, or 3.3 VDC serial communication
• 0 to 10 VDC feedback pressure monitor
• Virtually silent
• No integral bleed required
• Multiple pressure ranges from vacuum to 150 psig
• 2.7 to 65 l/min flow control
digital. Clippard’s Cordis products are revolutionary microcontrollers primed for escape velocity from a proportional control market that has grown stagnant.
With unparalleled performance and flexibility not possible with current analog proportional controllers, the Cordis makes everything from calibration, to sensor variety, to future development opportunities more accessible and less complicated.
Contact your distributor today to learn more about how the Cordis can provide precise, real-time control for your application, or visit clippard.com to request more information.