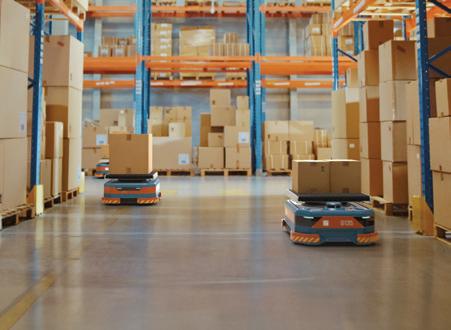
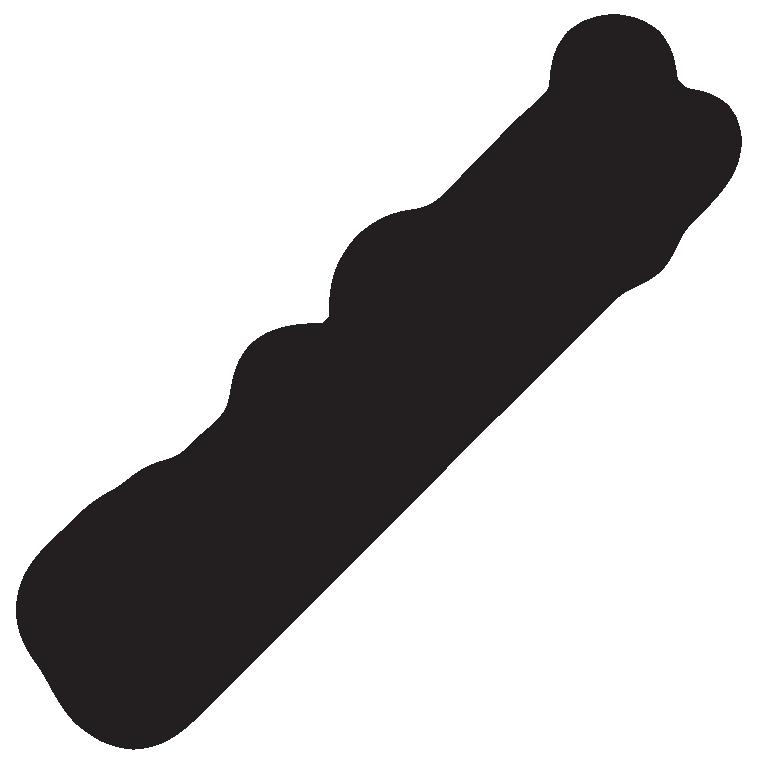
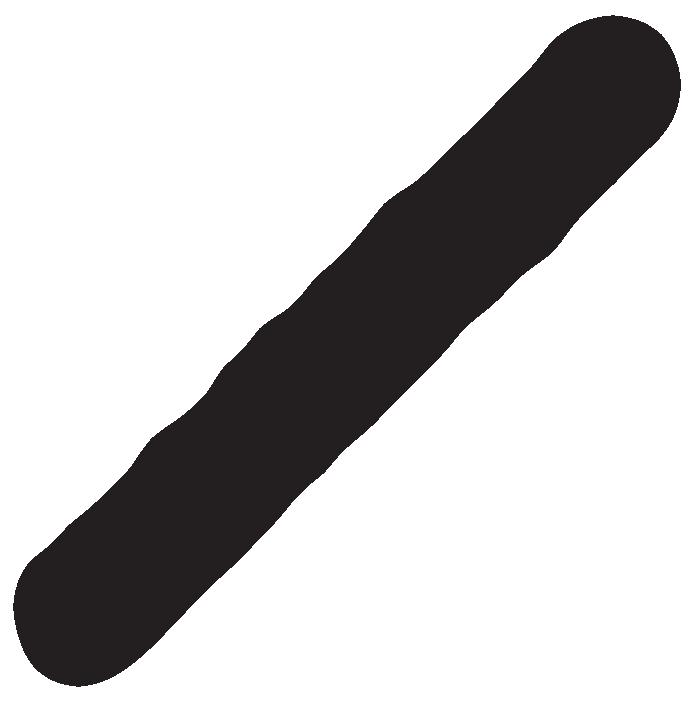
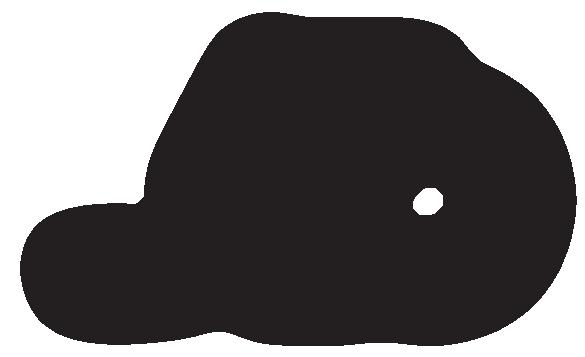
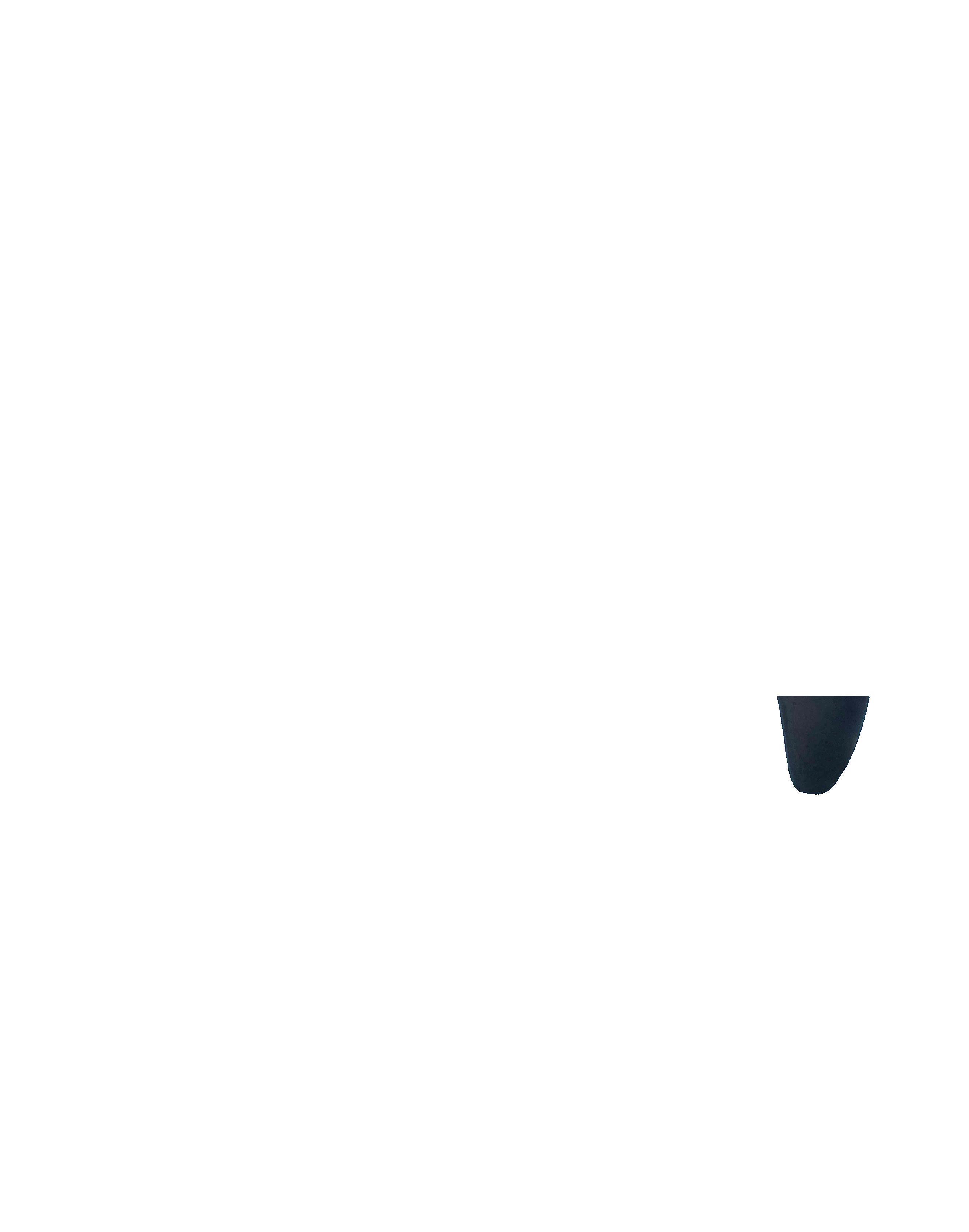
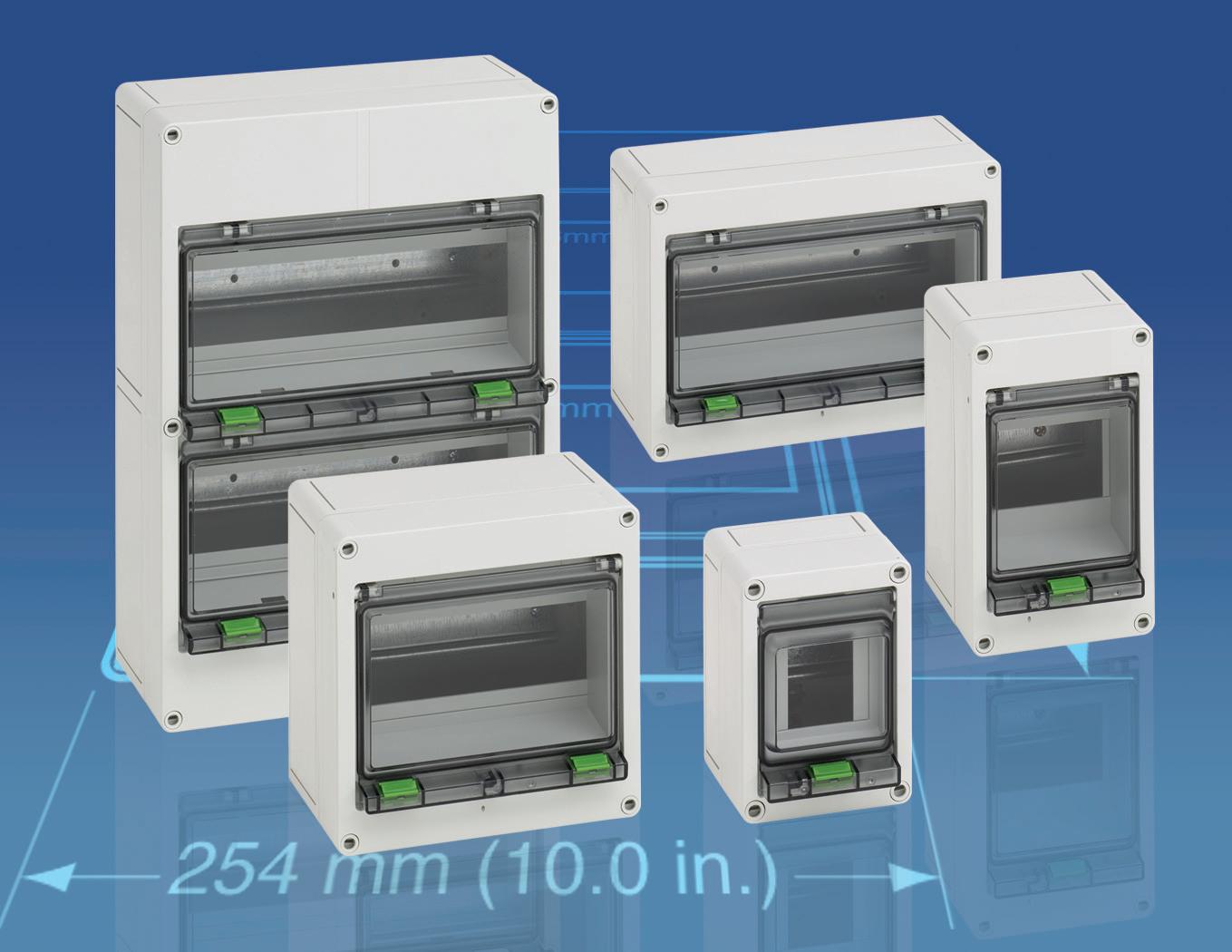
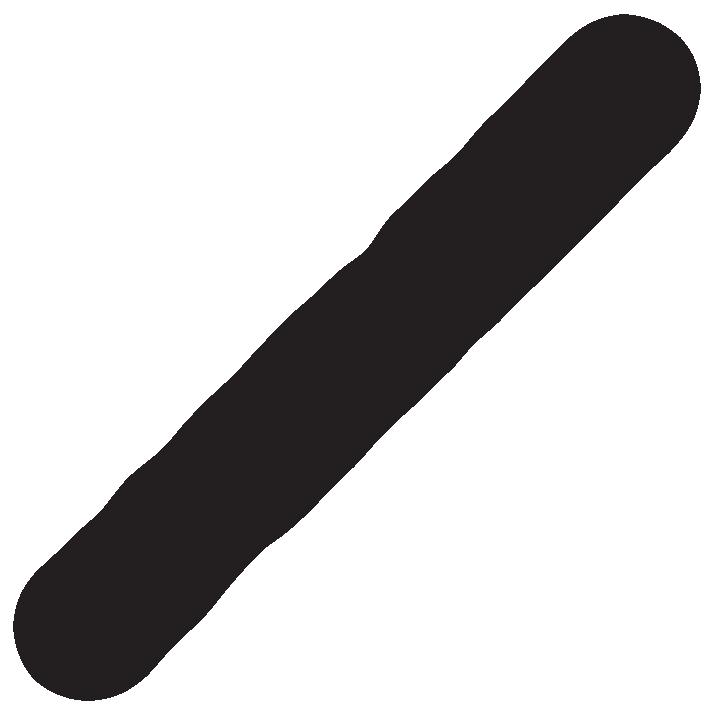
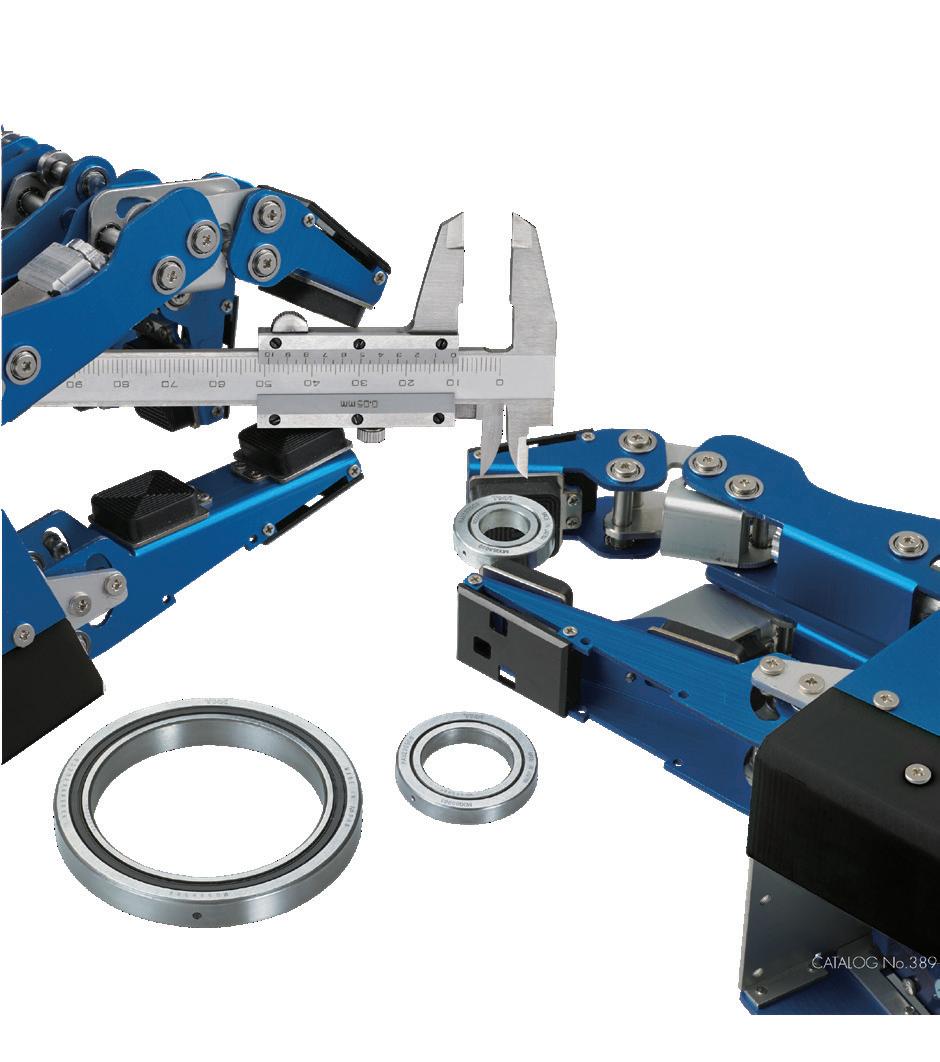
THK is a leading manufacturer of high quality and ultra precise miniature linear guides, ball screws, cross roller rings and actuators for a wide range of industries, including industrial automation, medical, aerospace, semiconductor, machine tool and robotics.
LM Guides - SRS Series - Featuring patented THK Caged Technology, the SRS Miniature LM guides perform with smooth and quiet motion, long-term maintenance free operation, increased speed and accuracy, low dust generation and a long life.
Cross Roller Rings - RAU Series - THK Micro Cross Roller Ring Series RAU are compact and lightweight and even more rigid than a double row angular contact ball bearing type. Spacer retainers enable smooth movement and high rotation accuracy.
Ball Screws - BNK and MTF Series - BNK with finished shaft ends and MTF Roll-Formed screw shaft are known for their high accuracy, low noise, smooth movement and long-term maintenance free operation.
Actuators - KR Series - KR Actuators consist of LM guide units on the ends and ball screw unit in the center making them highly rigid and highly accurate in a minimal space.
To learn more, call us at 1-800-763-5459 or visit www.thk.com.
SRS MTF(100W)
Starting at $964.00 (100W system with cables and I/O breakout)
LS Electric iX7 servo systems offer advanced multi-axis motion control along with EtherCAT networking. The EtherCAT protocol provides extremely fast, real-time, deterministic, and synchronized communication for high precision motion.
• 9 standard servo systems from 100W to 3.5kW
• Multiple input power options:
• 110VAC single-phase up to 400W
• 230VAC single-phase up to 2.2k
• 230VAC three-phase in all sizes
• Use with any CANopen over EtherCAT (CoE) compatible PLC/host controller or one with ModbusTCP capability
• Fully digital with 1kHz velocity loop response
• 45-day money-back guarantee
• One-year warranty
EtherCAT® is a registered trademark and patented technology, licensed by Beckhoff Automation GmbH, Germany.
Need an EtherCAT controller?
LS Electric® XGB PLC CPUs starting at $299.00 (w/FREE software)
The LS Electric XGB PLC controls up to 16 axes of EtherCAT® motion with several positioning methods including linear, circular, helical, and ellipse interpolation. Seven homing routines are also available and the FREE software offers a graphical interface so you can see the motion in action! The XGB series PLC is a perfect control solution for:
• Palletizers
• Pick-and-place applications
• Rotary tables
• Flying cutoff systems
• Precision machining tools
• Automated welding systems
• and much more
Systems with a 4-axis EtherCAT positioning module starting at $691.00 (not including servo system(s))
316
316
- brushed or bldc motors
- 5 amps per axis
- 16 analog inputs
- 16 on/off drivers
- home and limit in - live tech support
- made in the USA
I’m going to veer off the normal engineering focus of this column for a month to dabble in a scientific field that’s close to my heart: astronomy. We’re a month out from this year’s big heavenly spectacle in the U.S., the total solar eclipse on April 8th. This eclipse will sweep across the country from Texas to Maine, giving people close to the centerline almost four minutes of totality.
First attracted to astronomy in the mid-1980s with the passing of Halley’s Comet, I was soon swept up in the excitement leading up to a total solar eclipse in Baja California in July 1991. I saved up enough money in college to travel to see that eclipse and was awestruck. I’ve seen two more since, but I have been waiting for most of my life for the 2024 eclipse to come to me, and my hometown of Cleveland.
You may recall the “Great American” eclipse in August 2017, which swept across the nation from Oregon to South Carolina, affording so many people the opportunity to see this incredible event. My family drove to Tennessee to see it. But afterward, I was crestfallen to hear reports from so many friends that they saw it, too — “It was more than 97% here” or “We were right near the center, it was more than 90% covered at maximum for us ... pretty cool.”
The key to total solar eclipses is the total part. One of the strangest coincidences about life here on Earth is that our Moon is 400 times closer to us (on average) than the Sun, but the Sun is 400 times larger. Thus, the two objects have about the same apparent size in our sky. There’s no law of physics that
says this must be so. In fact, in a few billion years, the Moon will be noticeably smaller when viewed from the Earth’s surface. But this coincidence of apparent sizes today means that the geometry of the moon basely covering the sun is somewhat rare and provides an incredible spectacle when it happens.
Totality, when 100% of the sun is covered, is the magic part. You no longer need to use the darkened glasses (as long as you know how much time is left before the sun peeks out again), and you can see fiery red solar flares; the sun’s outer atmosphere, the corona; and brighter stars and planets. The leadup to this 100% coverup can include a drop in temperature, windy conditions, strange moving light bands on the ground, and animals behaving strangely. You’ve spent your entire life observing (actively or passively) sunsets and twilight — and having that 45-minute process compressed into a minute or so is mindbending and astounding.
But again, if you aren’t in the narrow, hundred-mile-wide band of totality, you’ll miss all that. The difference between 99% and 100% is everything. In the years since the 2017 eclipse, I’ve finally found the words to explain this to friends who missed totality back then:
“If you drove 99% of the way to your favorite restaurant and then turned around and came home — and I asked you how the meal was — would you reconsider your choice?”
I hope you all are able to make your way into the shadow of the moon on April 8th, and let’s all cross our fingers for clear skies that day! DW
GPL Robotic Planetary
Backlash ≤0.1 arcmin for the life of the gearbox
Vibration-free for high positional accuracy
GSL Strain Wave
Backlash ≤0.5 arcmin
Harmonic-type gearing
High torque density
Easy integration
GCL Cycloidal
Backlash ≤1.0 arcmin
Impact resistance 5x nominal torque. Available with integral pre-stage
GML Planetary
Backlash ≤10 arcmin
Servo ready. Heavy duty bearings. Rotating hub design eliminates overhung load, ideal for pulleys or wheel drives
GAM robotic gearboxes are designed with the flexibility to fit your application. Rotate the flange or outer housing, add a housing cover, a motor adapter, or a pre-stage gearbox.
GAM offers a full range of robotic and servo gearboxes, along with rack & pinion, servo couplings, and linear mount products for motion control and robotic applications. With our broad product offerings, as well as the in-house engineering design experts and U.S. manufacturing capabilities to develop customized solutions, we can help with your application.
GAM Can.
www.gamweb.com
BXR Brakes
· Up to 480 in-lbs static
· Up to a 1.125'' bore
· 19 watts or less
· Produced for over 10 years
Our Innovative design features a very thin profile, reducing weight and space.
For more information:
Call: 800.533.1731 www.mikipulley-us.com
Late last Spring, my family and I decided to grow our first garden. We tilled dirt, built fencing, and wasted no time planning for our future backyard bounty. It was a disaster. There is not a green thumb among us, and apparently, optimism and good intentions are no substitute for sunlight and viable soil. Could technology have helped me? Perhaps one of the many gardening apps available at the touch of a button? It got me thinking.
What if this little undertaking wasn’t just a summer hobby? What if this was my livelihood? For folks in commercial agriculture, results are mandatory. The good news for farmers is that many experts think the Ag industry is about to undergo a substantial technological transformation for the better. Earlier this year, the Association of Equipment Manufacturers (AEM) listed Ag’s tech transformation as one of their 4 Equipment Manufacturing Trends to Watch In 2024. In the article, AEM Director of Agriculture Austin Gellings wrote that the advances will be considerable and not limited to mere improvements in existing agriculture technology.
“Agriculture is experiencing a seismic shift related to its underlying technologies, incorporating advancements from other industries while also leading the way in its own evolution.”
As technologies like automation and robotics become industry standard, the integration of AI and machine learning will likely follow suit. Gellings believes this may be just the beginning.
“While providing for more integration and connectivity, these
systems are also leading to other new challenges and opportunities. One is actual connectivity to equipment, allowing for the transfer of data to the cloud and its use in offline decisionmaking by end users.”
Additionally, in a Global AgTech Initiative article titled, 5 AgTech Trends to Watch in 2024, Agmatix CEO Ron Baruchi explained that Generative AI will be responsible for generating significant actionable data for farmers.
“These tools enhance crop management by analyzing big agronomic data, providing AI-supported insights to optimize production practices. This helps farmers understand patterns affecting the performance of crop varieties and production on their specific farms and tracks climate trends to help farmers become more resilient to the changing climate.”
These advances in interconnectivity won’t be without challenges (cybersecurity firms must be salivating), but the rewards seem to more than outweigh the risks. Better soil health, improved water and air quality, better labor conditions, and more, are just a few of the benefits we might see soon. So, while I myself won’t be setting up a stand at the farmer’s market anytime soon, it’s good to see that our agriculturalists might have some new tools at their disposal for the upcoming growing season. I’m interested to see how it plays out. I wish them luck.
DWTrends in drives and controls
Drive and control technology has moved fast in the last decade. We asked leading industry experts to get us up to speed on the trends of today, and what to expect in the near future.
Without a cam follower, a cam would not be of much use, as cams must make contact with followers to transfer rotary motion into linear motion.
Help us honor the companies that have provided the most leadership in engineering
It has been a fascinating decade for all businesses, including manufacturers. We’ve seen the difficult supply chain issues brought on by the worldwide pandemic, along with a shortage of qualified workers and the strong reshoring trends in many industries. If nothing else, this helps to show how resilient manufacturers can be.
These companies represent the best and brightest, and they reflect the continued vision, integrity, and creativity of their design (and manufacturing) engineers.
We think they deserve recognition from you, too. Vote online for one or more of the companies listed through October.
EDITORIAL
VP, Editorial Director Paul J. Heney pheney@wtwhmedia.com @wtwh_paulheney
Managing Editor Mike Santora msantora@wtwhmedia.com @dw_mikesantora
Executive Editor Lisa Eitel leitel@wtwhmedia.com @dw_lisaeitel
Senior Editor Miles Budimir mbudimir@wtwhmedia.com @dw_motion
Senior Editor Mary Gannon mgannon@wtwhmedia.com @dw_marygannon
Senior Editor Rachael Pasini rpasini@wtwhmedia.com @WTWH_Rachael
Associate Editor Heather Hall hhall@wtwhmedia.com @wtwh_heathhall
CREATIVE SERVICES
VP, Creative Director Matthew Claney mclaney@wtwhmedia.com @wtwh_designer
Art Director Allison Washko awashko@wtwhmedia.com
Senior Graphic Designer Mariel Evans mevans@wtwhmedia.com @wtwh_mariel
Graphic Designer Shannon Pipik spipik@wtwhmedia.com @wtwh_shannon
Director, Audience Development Bruce Sprague bsprague@wtwhmedia.com
WEB DEV / DIGITAL OPERATIONS
Web Development Manager B. David Miyares dmiyares@wtwhmedia.com @wtwh_webdave
Senior Digital Media Manager Patrick Curran pcurran@wtwhmedia.com @wtwhseopatrick
Front End Developer Melissa Annand mannand@wtwhmedia.com
Software Engineer David Bozentka dbozentka@wtwhmedia.com
DIGITAL MARKETING
VP, Digital Marketing Virginia Goulding vgoulding@wtwhmedia.com @wtwh_virginia
Digital Marketing Manager Taylor Meade tmeade@wtwhmedia.com @WTWH_Taylor
Digital Marketing Coordinator Meagan Konvalin mkonvalin@wtwhmedia.com
Webinar Coordinator Emira Wininger ewininger@wtwhmedia.com
Webinar Coordinator Dan Santarelli dsantarelli@wtwhmedia.com
EVENTS
Events Manager Jen Osborne josborne@wtwhmedia.com @wtwh_jen
Events Manager Brittany Belko bbelko@wtwhmedia.com
Event Marketing Specialist Olivia Zemanek ozemanek@wtwhmedia.com
FINANCE
Controller
Brian Korsberg bkorsberg@wtwhmedia.com
Accounts Receivable Specialist Jamila Milton jmilton@wtwhmedia.com
VIDEO SERVICES
Videographer
Kara Singleton ksingleton@wtwhmedia.com
Videographer Cole Kistler cole@wtwhmedia.com
PRODUCTION SERVICES
Customer Service Manager Stephanie Hulett shulett@wtwhmedia.com
Customer Service Representative
Tracy Powers tpowers@wtwhmedia.com
Customer Service Representative
JoAnn Martin jmartin@wtwhmedia.com
Customer Service Representative
Renee Massey-Linston renee@wtwhmedia.com
Customer Service Representative Trinidy Longgood tlonggood@wtwhmedia.com
Digital Production Manager
Reggie Hall rhall@wtwhmedia.com
Digital Production Specialist Nicole Johnson njohnson@wtwhmedia.com
Digital Design Manager Samantha King sking@wtwhmedia.com
Marketing Graphic Designer
Hannah Bragg hbragg@wtwhmedia.com
Digital Production Specialist
Elise Ondak eondak@wtwhmedia.com
WTWH Media, LLC
1111 Superior Ave. 26th Floor Cleveland, OH 44114 Ph: 888.543.2447
Servo drive systems are crucial in packaging applications as they offer precise, flexible, and efficient control over machine motion. Siemens has recently updated its well-known Sinamics S210 servo drive system with a new hardware architecture and V6 software generation, suitable for high dynamics applications ranging from 50 W to 7 kW.
The new generation of Sinamics S210 includes a second encoder interface and an optional connection to a direct measuring system that compensates for mechanical looseness and tolerances. This leads to significant improvements in precision, enabling more applications. It also complies with SIL3 (EN 61508) and PL e (EN ISO 13849-1) requirements, providing
Basic and Extended Safety Integrated functions and new Security Integrated functions with user management and access protection.
Apart from the Profinet IRT, the Sinamics S210 system also offers communication via EtherNet/IP. The servo system can connect to thirdparty controllers, providing a more comprehensive range of applications,
especially in the U.S. market. With its new 3C3 (H2S and SO2) coating, it is highly robust and resistant to aggressive environmental influences and challenging production conditions.
The EPOS single positioner is now a technology function module that implements high-precision motion control positioning tasks in the converter. Calculating positioning tasks directly in the drive reduces computing power in the controller, enabling it to compute more complex tasks or a larger number of drive axes.
Engineers can use the DriveSim Advanced simulation software to create a digital twin of the Sinamics S210 system in the TIA Portal, allowing them to commission the drive system virtually in advance and perform engineering tasks. The digital twin also enables virtual training and demonstrations and helps optimize real machines. The integrated Web server supports the new Web server platform and operating philosophy of the new Sinamics inverter generation (Sinamics S200 and Sinamics G220). The Web server enables efficient commissioning, fast diagnostics, and maintenance from tablets, PCs, and other devices. DW
Siemens • siemens.com
Tomorrow-R1 and Tomorrow-R2, the world’s first commercially built weather-radar satellites, were launched last year and orbit 550 km above Earth. These pathfinders include active and passive sensors for global weather forecasting, climate observation, and near realtime scans of precipitation and atmospheric profiles for any point on Earth. But to make use of all the data, they need reliable antennas.
Vitesse Systems announced the successful delivery of its first additively manufactured satellite antenna integrated into the Tomorrow-R1 satellite. The antenna was designed and tested at Vitesse Systems’ Longmont location (previously Custom Microwave). Since acquiring the business in 2021, Vitesse Systems has invested in two additional metal additive manufacturing machines and increased its design engineering capacity to streamline the development of complex antenna solutions. Vitesse Systems has also developed a range of proprietary finishing processes that enhance the surface characteristics of its antenna solutions, overcoming the limitations previously associated with additively manufactured antennae.
The company began working with satellite developer Tomorrow.io in 2020. As the team developed the preliminary antenna design, they realized they could optimize radio frequency (RF) performance and reduce the overall mass of the antenna with additive manufacturing.
Tomorro.io recently reported that its satellites now demonstrate high levels of accuracy over a wide range of precipitation rates and types. With AI playing a significant factor in weather forecasting capabilities, the datasets fueling AI are proving to be the differentiating performance factor. DW
Vitesse Systems • vitessesys.com
WHITTET-HIGGINS manufactures quality oriented, stocks abundantly and delivers quickly the best quality and largest array of adjustable, heavy thrust bearing, and torque load carrying retaining devices for bearing, power transmission and other industrial assemblies; and specialized tools for their careful assembly.
Visit our website–whittet-higgins.com–to peruse the many possibilities to improve your assemblies. Much technical detail delineated as well as 2D and 3D CAD models for engineering assistance. Call your local or a good distributor.
Emerson recently collaborated with Sartorius, an international biopharmaceutical company, to natively integrate Sartorius’s Biostat STR Generation 3 family of bioreactors with Emerson’s DeltaV distributed control system (DCS). A manufacturing plant’s DCS provides critical automation of operations for faster, safer production. Life sciences companies often struggle to connect process equipment to their plant’s automation system because engineering and configuring equipment is complex and time-consuming. Biostat STR Generation 3, natively-integrated with a plant’s DeltaV DCS, eliminates this complexity for one of the most frequently used components of biopharmaceutical manufacturing. The bioreactors are specifically designed and pre-engineered with DeltaV components from the ground up by Sartorius. The configuration toolkit developed by Emerson and Sartorius has a library of templates that provide standardized configuration.
By integrating Emerson software and technology into our new Biostat STR DeltaV variant, we help our customers rapidly bring their operations online.
Using the library, teams can integrate bioreactors into their control system quickly and easily out of the box. Commercial manufacturing sites expect to save up to 80% of their equipment integration time, helping them take advantage of the enhanced features and diagnostics inherent in the DeltaV DCS more quickly and easily. The increased automation reduces the need for manual operation, ultimately increasing quality and speeding up time-to-market.
“One of the biggest barriers to fast delivery of new treatments is the time it takes to connect new equipment to the plant’s control system,” said Nathan Pettus, president of Emerson’s process systems and solutions business.
Biostat STR Generation 3 bioreactors integrated with Emerson’s DeltaV DCS are built with technologies, including DeltaV Electronic Marshalling with CHARMs devices, to reduce wiring and configuration work during installation. The bioreactors can integrate seamlessly with Emerson’s DeltaV PK Controller and S-Series and M-Series controllers. Built-in templates provide standardized configurations for the most common uses, allowing teams to use standard setups out of the box to bring operations online rapidly and safely and allow them to change those operations quickly to meet shifting market needs.
“The biopharmaceutical industry requires modular and scalable bioprocess equipment to help quickly and easily manufacture the treatments patients around the world are waiting for,” said Mario Becker, head of bioreactor technologies at Sartorius. “By integrating Emerson software and technology into our new Biostat STR DeltaV variant, we help our customers rapidly bring their operations online.”
The easy configuration and integration of the Biostat STR Generation 3 bioreactors integrated with the DeltaV DCS helps life sciences manufacturers build a connected plant, a core strategy of reaching level 3 of the Biophorum Digital Plant Maturity Model.
In addition, increased access to advanced automation strategies and diagnostics from the DeltaV DCS helps prepare the plant for the more predictive technologies necessary to meet level 4. Each step change in digital maturity brings plants closer to autonomous operations. DW
Emerson • Emerson.com
Subsea applications are characterized by constantly harsh conditions and extreme environments. In marine environments, various applications involve propeller shafts and components for underwater robots and telecommunication systems. However, in the presence of water, salt, and harsh elements, selecting just any bearing won't suffice — it's crucial to choose the right one for optimal performance and durability.
The World Corrosion Organization has reported that the global annual cost of corrosion amounts to $2.2 trillion, equivalent to more than 3% of the world's gross domestic product (GDP). When a bearing in a subsea industrial application begins to experience corrosion, it sets off a chain of detrimental effects.
First and foremost, the corrosion accelerates wear on the bearing’s raceways, rolling elements, and cages. This heightened wear and compromised surface integrity increases the bearing's susceptibility to the intrusion of abrasive particles and contaminants. These contaminants can further exacerbate wear and damage in critical components such as seals, gears, and other bearings.
Swift intervention and corrosionresistant bearings are vital to mitigate these risks and ensure the integrity and longevity of subsea equipment.
The lifespan of a bearing can be significantly affected when fully submerged, depending on the material composition. Take 440-grade stainless steel bearings as an example. While they exhibit high resistance to fresh water and weak chemicals, they are
prone to rapid corrosion when exposed to salt water or fully immersed in water.
440 grade stainless steel bearings struggle to withstand the corrosive nature of these environments, even with external protection such as passivation, leading to reduced performance and premature failure.
Passivation involves a metal finishing process that uses nitric acid or citric acid to eliminate free iron from the surface. This chemical treatment results in a protective oxide layer, reducing the likelihood of chemical reactions with air and preventing corrosion. However, in a marine environment, without protection from the elements, the passivated metal will eventually corrode. So, which material is best for subsea applications?
Ceramic bearings excel in corrosive environments, although they may
come at a higher initial cost. Ceramic bearings, such as Si3N4 bearings, don’t react with saltwater and many harsh chemicals, which can add consistent performance even when they are permanently submerged.
Reduced friction and wear
Ceramic bearings offer significantly lower friction coefficients than their steel counterparts, reducing energy consumption, improved overall system efficiency, and increased lifespan.
Zirconia (ZrO2) and silicon nitride (Si3N4), for ceramic bearings, have excellent corrosion resistance. These materials have a low friction coefficient, so they can even be used without lubrication in lower-speed applications. The exceptional hardness of ceramic materials also contributes to lower wear rates, extending the service life of
the bearing and reducing downtime for maintenance and replacements.
Resistance to debris and contamination
Subsea environments often expose bearings to debris, sand, and other contaminants. Traditional steel bearings will suffer from accelerated wear and failure under such conditions.
Because of their much greater hardness, ceramic bearings exhibit improved resistance to particle intrusion, although care should be taken to prevent contaminants from entering any bearing to ensure reliable operation. This feature lessens the risk of failure and enhances the durability of subsea equipment.
In applications such as subsea telecommunication systems, the choice of bearing is critical to ensure reliable and efficient signal transmission across undersea fiber optic cables.
One of the critical benefits of ceramic bearings is their non-magnetic properties, which play a crucial role in preventing electromagnetic interference with signal transmission. As subsea telecommunication systems rely on precise data transfer over vast distances, any magnetic interference could lead to signal disruptions and data loss.
By using non-magnetic ceramic bearings, these systems can maintain the integrity of their signal transmission, ensuring uninterrupted communication between continents and enhancing the overall reliability and performance of subsea telecommunication networks.
Full ceramic bearings, made from zirconia or silicon nitride with PEEK cages and seals, offer superior corrosion resistance in marine applications. Since ceramic bearings are not affected by seawater, they can be used in marine environments where they are permanently submerged and can cope with higher loads.
Ceramic bearings are mainly used in environments that are too hostile for steel bearings, where heavy shock loads are unlikely — due to the brittle nature of ceramics. SMB Bearings ZrO2 bearings possess several advantageous properties. They are non-magnetic and non-conductive, making them suitable for various applications.
Additionally, they exhibit high corrosion resistance against a wide range of chemicals. Their waterresistance further enhances their suitability for marine applications, particularly in fully submerged scenarios or situations where the load or speed exceeds the capabilities of 316 marine grade bearings.
Because corrosion comes at a high cost, and can cause wear and tear on bearings, choosing the most suitable bearing material at an early stage can help subsea operators prevent downtime, unplanned rework, and costly replacement parts. Investing in ceramic bearings, which are completely corrosion-resistant and have a long lifespan, will help avoid disturbing the application and maintain a steady workflow.
SMB Bearings • www.smbbearings.com
Interpower North American and international cord sets
Interpower manufactures state-of-the-art electrical cord sets for global markets with no minimum order requirements. Interpower cords and components are
in accordance with its product quality plan: hipot testing, continuity testing, and ground testing with multiple inspections. Interpower offers value-added options such as lengths, colors, packaging and labeling!
The tangential laser-centrifuge process is suitable for manufacturing small and very detailed parts, such as microchannel cooling devices used as heat sinks for CPUs typically performed in vacuum or clean room environments. Inserts for injection molding dies with tiny channels can also benefit from the tangential machine process by focusing the laser on very small areas to remove metal. Conversely, conventional machining uses very small bits that can easily break while removing material. This technology allows for making deep holes without debris precipitation on the sides of the hole that ablation machining produces.
Tangential machining removes material and can deposit material, such as in 3D printing. Using a spinning
mass of material with a pulsed laser, microdroplets directed in a straight line can be deposited on a substrate to build up material layers. Through precise control of the substrate position, complex parts can be formed. Since the laser can pulse in femtoseconds, the material stream can be deposited faster than current 3D printer technology.
Tangential Systems background
Lasers have been used for both cutting and machining. Light from the laser heats the workpiece material, which must be removed. For laser cutting, the molten material, dross, is usually blown from the cut with a jet of air or gas and can spray on surfaces that then require cleaning. In laser machining, the laser pulses are short and powerful. The
intense laser light ablates material, which ejects as a vapor plume that condenses and precipitates on surfaces. The vapor can also create byproducts that can be noxious. Thus, removing the heated debris requires additional technologies to mitigate.
The Tangential System (Patent US7933680B2) provides significant advantages by attaching the workpiece to a centrifuge. The laser-heated material is removed instantly by centrifugal force. The released material can fuse to a substrate to form a separate object (using the released material for 3D printing).
Advantages of the Tangential System include:
• High-speed material removal. The Tangential System removes material at more than twice the rate compared to typical high speed CNC machining.
• No tooling. Instead, the material is energized and released by a laser, eliminating the time to change tools.
• Materials to be formed. Lasers can inherently process a vast multitude of materials, including plastics, metals, composites, glass, and minerals. The type of laser can be matched with the material to achieve good energy absorption.
• Shapes and setups. Virtually any shape can be formed using this system as long as the working
surface is visible to the laser beam.
• Machine mass and energy. In the Tangential System, all that touches the workpiece are laser beams. Thus, the entire system can be made of lightweight materials.
• Minimal heat affected zone. The centrifuge instantly removes all hot material from the surface. Therefore, heat in the debris has no time to warm the surrounding work.
• Precision. Debris is instantly removed so the new shape can be measured virtually and concurrently with material removal.
• Efficiency. The laser only needs to provide enough energy to release the material, which lowers the energy requirement of the laser. Additionally, some of the energy used to rotate the centrifuge can be retrieved through regenerative braking. The total energy required for material removal is minimized. As a further benefit, the removed material can be concurrently used to manufacture additional forms.
• Cleanliness. The debris is removed from the workpiece in a specific path. The debris material can then be used to form another object or stored for later use. The minimal heat used minimizes noxious gases and byproducts.
• Concurrent subtractive and additive manufacturing. The material released by the laser can be directed to add the hot material to a separate structure.
How Tangential System manufacturing machines work
The Tangential System can perform material removal and addition
concurrently. Material removal is performed by attaching a solid workpiece to a centrifuge. When the centrifuge turns, centrifugal force acts on the workpiece and creates radial acceleration, which can be many times the acceleration of gravity. As the centrifuge spins, a laser beam focused on the workpiece adds energy to the bonds that hold the material together. As the bonds are weakened, the heated material is released and travels in a tangential path away from the workpiece. The released material is typically hot and travels at high speed. A substrate placed in the tangential path acts as a target for this material. With each turn of the centrifuge, additional material is added to the substrate in a directed and controlled manner. As a result, formed objects can be created concurrently — first, from the workpiece on the centrifuge as the material is removed and then on the substrate as the material is deposited.
Figure 1 shows the basic components of the machine, Figure 2 shows the process in four steps, and Figure 3 shows configurations that can be made from the basic design.
This manufacturing technique can be used in many applications because of its ability to process any type of solid in an accurate, precise, fast, and efficient manner. The Tangential System provides the technology for material removal rates many times that of traditional technology. This energy-efficient system can effectively process many types of materials and does not require investments in cutting tools or heavy machinery. In
conventional machining and laser ablation machining, vibration and the explosive removal of material induce stresses in the workpiece material, changing the material properties and the heat-affected zone. The Tangential System does not have these side effects and can produce detailed features in fragile materials that would otherwise be impossible to manufacture. Advanced additive manufacturing can also be achieved where composite materials are formed in product construction.
Additionally, there is a need for both subtractive and additive manufacturing in space applications. A machine for these tasks must have low mass to enter orbit, and the Tangential System meets such requirements. Further, it provides the flexibility to process a variety of materials and construct composite structures while using minimal energy. DW
Thelast decade has seen advancements in controls and motor drive technologies to boost efficiency, safety, and ease of use. Now commonplace are drives that:
• Let end users leverage autotuning functions for faster commissioning
• Detect and correct for vibration issues — including the shaping of power into motors to avoid resonances
• Spur increasingly compact motors to beyond rated speeds
• House sensing capabilities and memory to support predictive maintenance initiatives
• Perform realtime monitoring for continual efficiency optimization
• Sport safely limited speed and safedirection features.
Controls on the other hand are the basis of software-based automation in applications requiring flexible solutions for frequent changeovers; digitaltransformation connectivity; and distributed control using ruggedized control components. We recently asked industry experts for their own observations and insights into the most important drive and control trends today. Here’s what they had to say.
T. Burke: Products in general are becoming more sophisticated and competitive. For example, servodrives are now equipped
with torque measurement and encoder technology that is so accurate that it can automatically detect vibrations, manage acceleration, and deceleration. At the same time, improvements in components and manufacturing processes are delivering greater tolerances and quality in hardware. In the case of communications, the latest technology is gigabit Ethernet and the ability to schedule communications through time sensitive networking (TSN). CC-Link IE TSN is a leading performance industrial Ethernet network technology available in a broad range of vendor products.
Worsnopp: Two trends in servodrives we’re seeing include ease of integration and advanced safety. From the sizing and selection of servos to their configuration and programming, machine builders today expect the use of servodrives to be easier than ever. After
all, we’re all surrounded by consumer technology such as smartphones, smart TVs, and cars that are exceptionally easy to use. This leaves us all with the impression that technology should be accessible. Manufacturers have also improved servodrive buying processes. For example, Festo provides easy-touse tools for sizing servo axes and configuring their servodrives along with function blocks to simplify servodrive programming.
Guitart: Rockwell Automation and Infinitum are jointly developing a motor system combining Rockwell’s PowerFlex drive technology and Infinitum’s high-
Festo provides easy-to-use tools for sizing a servo axis and configuring servodrives. Festo units feature function blocks to simplify programming the servodrives. Shown here are the EMMT servomotor and CMMT-MP multiprotocol drive.
With encoders so essential to motor drive systems for position feedback, velocity control, and error correction, safety capabilities, and diagnostics, it’s no surprise their design and application have advanced as well. Here’s what four industry experts had to say on this.
Brimage: Encoders provide realtime feedback on load position, which is critical for high-precision, linear motion applications. We’ve seen increased application of encoders due to linear motion systems requiring more precision than ever. The demand for highprecision systems in medical, life sciences, and factory automation is saddled with demand for more compact systems as well.
Beckstoffer: Motor feedback is always critical in medical applications, particularly drug-delivery devices, to ensure accurate dosing to the patient. With these devices getting smaller to enable patient mobility, feedback devices must continue to shrink in size while providing the proper counts per revolution. Magnetic encoder technology is allowing the size reduction for closing the loop for dc motors.
Brimage: In support of the industry pushing toward miniaturization, we have also seen an increased demand for smaller encoders. Thomson has a complete offering of stepper motor linear actuators with integrated encoders to enhance precision positioning control with a range of sizes that are compatible with small motors.
Soltero: We’ve observed a trend towards absolute encoders with analog outputs to help systems efficiently handle higher resolutions. In some cases, when customers seek to increase the resolution of their existing incremental encoder designs, they typically use a higher pole-count ring magnet (if one is currently used) as well as digital-output Hall-effect latches. This combination is employed because higher pole-count magnets produce a weaker magnetic field, necessitating a high-sensitivity Hall-effect latch. At some point, the design reaches a limit on the number of poles due to costs associated with the magnets and latches. Once this limit is reached, designers typically transition to absolute encoders with analog outputs.
Graham: The latest trend we’re seeing in motor feedback is encoders assuming more sensing tasks with a common communication channel back to the drive-control system through the encoder interface. Things such as temperature sensing, vibration sensing, and torque sensing are all possible to do with the integration of certain encoders. As we move to support these features, we’ve also improved our communication interface with EnDat 3.
efficiency Aircore EC motor system. The solution aims to help companies reduce their carbon footprint with a motor system that’s 50% smaller and lighter than traditional iron-core motors all while using 66% less copper and consuming 10% less energy. The motor and lowvoltage drive solution will be distributed through Rockwell to let global industrialsector clients deploy a sustainable motor system and cut energy consumption.
Worsnopp: It is still early in this trend, but we are seeing more requests for servodrives that incorporate advanced safety functions such as safe limited speed. Historically, servodrive safety was implemented outside the servodrive using safety relays and safety controllers. Over time, more safety functions have integrated into the servodrives themselves; this in turn saves machine builders time and increases machine reliability. For example, safe torque off (STO) is now a standard safety function included in many servodrives. STO
makes it possible for the machine builder to easily cut power to the motor … and that makes it safer for an operator using the machine.
As automation becomes more sophisticated, machine builders are likewise requiring more advanced safety functions that let them run their machine and reduce the risk of harming personnel. For example, with safe limited speed on a servodrive, it’s possible for machine builders to keep a machine in motion (typically at a safe reduced speed) and monitor that speed to ensure it’s prevented from accidentally moving too fast.
Advanced safety functions are becoming more common on servodrives, and we can expect to see more manufacturers offer them in the future.
Korkowski: LinMot’s Multi-Interface drive is compatible with Ethernet IP, PROFINET, EtherCAT, Powerlink, SERCOS, and CC-Link. As a single product to satisfy multiple designs, this
drive offers quick lead times. Our drives also feature process monitoring for pass or fail and force control as a software solution to support various design options.
Ledoux: We are seeing an increased demand in motor speed controllers to be installed in remote areas requiring outdoor packaging dedicated to the component instead of what is typically provided — a climate-controlled building.
Guitart: Integrated motor and drive solutions from Infinitum are making installation and serviceability in the field easier … and improving uptime and equipment reliability. For instance, new designs feature user alerts that identify specific problems for faster resolutions as well as removable access panels for easier access to terminals, connectors, and programming ports.
With conventional motors, it can take up to two weeks to have service requests fulfilled. New Infinitum motors are built for end user serviceability.
Infinitum can train a company’s internal technical service team to do repairs in about 15 minutes, so end users have more control and flexibility. In data centers and manufacturing lines where uptime is of key importance, this is a desirable and differentiating capability.
Luchars: ECM recently launched an integrated and customizable electric motor controller — a 5-kW Unum Potentia controller leveraging PCB Stator and PrintStator Motor CAD platform while helping deliver 98% efficiency. When combined with a PrintStatordesigned machine, the controller allows IE5 ultraefficiency electric-motor performance. With a near100% efficient controller versus one having 80% to 90% efficiency, the system consumes less energy than traditional alternatives.
The new motor controller will be available to PrintStator SaaS clients and partners for roughly a tenth the cost of controllers supporting similar electric-motor kW ranges. With this controller, engineers can fully integrate PrintStator designs and design a drive-controller perfectly tuned to the full electric system.
PrintStator software allows the custom design, manufacture, and integration of PCB Stator electric motors. The motor controller is customizable via PrintStator and structurally and thermally integrated to the resulting motor housing for a compact footprint (and full motorsystem optimization). In fact, the software can output motor-tuning parameters and translate those into a code file that uploads to the controller. This makes the motor system design truly plug and play. The controllers can run 3 to 8-kW motors board-component changes; the board footprint always stays same. The Unum Potentia controller also operates and 480 three-phase ac offers sensorless control of running motors down rpm; and (with its FETs) upwards of 100 kHz. DW
• Dave Beckstoffer: Industry manager • Portescap
• Kurt Ledoux: Business director — medium voltage drives • Yaskawa
• Lindsey Brimage: Product line manager – lead and acme screws • Thomson Industries
• Manny Soltero: Product marketing engineer • Texas Instruments
• Mike Korkowski: Operations manager LinMot USA
• Ramon Guitart: VP of engineering — electric motors • Infinitum
• Robert Luchars: Executive VP • ECM PCB Stator Technology
• Stuart Graham: Business Development Specialist • HEIDENHAIN Corp.
• Thomas Burke: Global strategic advisor • CC Link Partner Association (CLPA)
• Tom Worsnopp:
Without a cam follower, a cam would not be of much use, as cams must make contact with followers to transfer rotary motion into linear motion.
One of the most crucial components and systems within machinery is the cam and follower set. Cams are rotating elements that vary in shape and size and are typically attached to a rotating shaft. A cam follower directly contacts the cam, typically riding atop of it, and transmits the rotary motion of the cam into a linear motion.
As for the cam followers themselves, they are devices with a rotary bearing core that bears load while serving as the interface between independently moving machine sections. Another way to think of cam followers is that they are essentially a type of bearing, typically a needle or roller bearing, designed in a way to follow a cam lobe profile.
Perhaps the most well-known example of a cam and follower is that of a camshaft in a car. The goal of a cam is to convert rotary motion to linear motion and there are multiple types of cams, including cylindrical and plate varieties.
Cam follower bearings, also known as track followers, can come in various designs, but are generally made with an extra thick outer ring. This design allows cam follower bearings to handle high radial loads, while a soft core can accept extreme shock loads without threat of fracturing the part. Depending on the application, cam followers may require either ball or needle rollers or even special materials such as stainless steel or chrome.
The outer diameter (OD) of the cam-follower bearing assembly is its working face — typically made of steel, nylon, urethane, polyamide, or other engineered material. This OD mates with some machine surface; traditionally this was a mechanical cam of some type, such as the precision barrel of an indexing table. Such mechanically automated indexing tables have a motion profile cut into a cam drum that engages the followers, which in turn transmits the power to an output.
Cam followers assemble onto machines in one of two ways. Stud-type cam followers include a partially threaded shaft fixed to the follower inner diameter (ID) for assembly onto a machine frame with a nut or similar fastening device. Yoke cam-follower variations (identifiable by their open ID) often mate to machine frames via press fit at a hardened inner race usually held by the follower’s end plates. Because they’re not a cantilevered design, yoke followers exhibit minimal deflection. But stud cam followers are indispensable in an array of applications — including those that are subject to high loads.
The most common cam-follower design employs needle rollers to carry high radial loads; where applications require the axis to run at high speeds, a cage can separate the rollers.
Where loads are particularly high and the axis needs high dynamic load capacity, cam followers can include twin rows of standard rollers. In fact, some lightload cam followers are even built around simple plain (sleeve) bearings.
Note that cam followers differ from their rollerbearing cousins in a few ways. Because the latter are typically interference fit into assemblies, they get circumferential reinforcement from the surrounding machine frame or housing. In contrast, the outer race of a cam follower must be thick to prevent deformation, especially under the localized line of loading. In addition, many cam followers include lubrication ports and more ruggedized surface finishes to withstand exposure to environments during operation — particularly those that operate exposed on unprotected machine sections.
Many cam followers have flat OD profiles, while others (especially those for linear-motion applications) include crowned, edge-flanged, or vee-shaped ODs to engage tracks and rails that are engineered with mating geometry.
Crowned cam followers can compensate for ten times as much misalignment as traditional flat-profile cam followers.
Interested? Get your free sample now:
This press applies up to 3000 tons to
form composite automobile panels. Delta’s RMC does multi-axis control of position and pressure to keep every moving part in perfect synchronization.
Look to Delta RMC motion controllers and graphical RMCTools software to make complex motion design easier, smoother, and more precise.
For the complete case study featuring Wuxi LANLI Machine Tool Co. or others relevant to your industry or application, visit our website.
Watch our training videos to witness firsthand how Delta Motion can make your application work in perfect, precise harmony.
Some cam followers serve as track followers by engaging rails to deliver linear motion. These designs are increasingly common in automated storage and retrieval systems (AS/RS) and seventh-axis robot transfer units (RTUs).
That’s because cam-follower-based linear systems outperform the linear bearings known as profile guides where compactness and ultra-high accuracy are less important than ruggedness, quick and forgiving installation, high-speed reversals, and long life.
Applications for cam and follower sets range widely over many uses and industries, including in machine tools, industrial robots, electronic parts production, and office automation equipment. More specifically, cam followers are found in rotary indexing tables and turntable conveyors, longstroke RTUs, and an array of highly customized machinery. Cam followers also find use in assemblies that pair them with linear tracks and other engineered paths on customized assemblies.
More recently, new cam follower designs for limited space are being offered by manufacturers. For instance, IKO International’s CFC…B Series of short stud-type cam followers have a unique mounting structure that solves space limitations that often exist on the stud side of the assembly region, thereby satisfying mounting requirements without sacrificing performance.
The CFC…B cam follower’s mounting structure consists of a hexagon socket head bolt and a dedicated flange nut that not only creates a more compact cam follower, it reduces the required mounting space on the stud side by up to nearly 34% — far more than conventional cam followers. By providing greater design freedom, this cam follower family can enhance production efficiency for a wide range of applications across many industries such as robots, electronic devices, manufacturing, and automated equipment.
Packaging machinery uses cutting-edge automation, and it’s no wonder. Facilities that parcel products need to deliver high throughput, but modern consumers demand smart packaging in the form of no-fuss containers that protect everything from M&Ms to patio furniture. What’s more, there’s a continuous drive to customize packages and let consumer-facing companies wrap products for bulk distribution, single-item sales, and everything in between.
To satisfy these design objectives, packaging machinery over the last decade has become increasingly adaptive. That’s been evident in a range of motion components and fully integrated designs at recent Pack Expo events. More specifically, the newest adaptive machines are:
• Modular (so they can be reprogrammed if not physically reconfigured on the fly)
• Fitted with HMIs (to let operators feed high-level operational data into machines as needed)
• Based on components that satisfy the efficiency, safety, and networking standards of multiple regions.
At the core of all these sophisticated elements are motion-control and power-transmission mainstays. Most all packaging machines include mechanical frame and powertransmission elements (including linear motion drives and guides); motors and drives; and motion controllers not unlike those used for the last 40 years in mechanizing and automating equipment. However, the accuracies and other performance characteristics of these machines’ power-transmission elements have steadily evolved and improved to complement the latest servomotor offerings (synchronous ac and otherwise) as well as increasingly advanced electronic control capabilities.
Though the accuracy and repeatability requirements of packaging equipment can be more modest than those for medical or semiconductor manufacture, the need for throughput is unrivalled — with many machines processing thousands of items per minute. Accompanying this need for high output is a need for reliability and consistency. That’s true whether discrete product pieces are of some consistent mass or (in the case of filling and packing) variable.
Consider the retail-ready packaging that some machines assemble — the product-packed pallets increasingly common in club stores such as Costco and BJs. The machines that put these shelf-ready displays together rely heavily on servo-driven stations and robotic arms that usually interface a conveyor. In a typical setup, the conveyor takes product to a station that orients individual units for grouping; then the modules travel on the conveyor to subsequent stations that group packs into patterns that let retailers use larger cartons for shipping, stacking, and displaying items once they’re in stores. Setup of such machines is almost always through HMIs.
In many cases, next-generation machines capable of assembling retailready displays must also incorporate sensors and networking fast enough to log dozens of mixed stock keeping units (SKU product codes) per minute.
For example, a maker of pita bread and sandwiches might employ servodriven cartoning machines to boost productivity and flexibility. For this application, vertical cartoner arrangements can assemble cartons having different item counts. For large retailers and club stores, this might involve four, six, 12, and 14-count cartons … necessitating a machine design that lets operators (via a touchscreen HMI) make speedy changeovers to different carton sizes — typically a dozen or more times a week. With modern drives and controls, such changeovers can take as little as 10 to 15 minutes.
In many cases, even the OEMs who build such cartoner packaging machines benefit from the automation and reduced mechanical part counts of servodrive-based equipment.
Automation in packaging has reduced labor costs and boosted efficiency for large makers of consumer goods. Now, smaller operations up and down the supply chain have also found ways to leverage automation’s benefits.
Just about any product made of metal, food, cosmetics, medical supplies, plastics, or boxes moves on a conveyor during manufacture. No wonder that conveyors come in all shapes and sizes — from belt widths of less than 2 in. (for moving extremely small parts) to several feet wide for transferring bulk substances.
Conveyors are classified by both their conveyance media and application: Some conveyors serve to transport bulk or discrete product in a steady stream with little interaction with transported goods along the way. These are ruggedized units optimized for high throughput. Slightly more demanding conveyor installations shuttle product between locations or machines. Still more demanding are
conveyors to move materials into or out of machines or stations. These actually require positioning capabilities to ensure proper handling of product. The most demanding conveyors run workpieces and other goods through assembly or other workstations and machinery without break. Many such conveyors for this demanding task employ custom workpiece pucks to steady product while machines perform work on the items.
Conveyors for moving arrays of discrete product — applications associated with motion control — take various forms. Some employ thin flat belt made of engineered fabric with nylon, PVC, styrene-butadiene synthetic rubber (SBR), or other durable synthetic materials.
Specially shaped motor-driven pulleys engage (with tensionmaintained friction) the conveyor belt and make it (and any product riding on it) advance. Benefits of this design include simplicity and costeffectiveness; thinness of conveyance medium for easier transfers off and onto the conveyor-belt ends
even for very small objects; the ability to withstand a wide range of temperatures; and customizable surfaces — for easy release of baked confections, for example.
In other instances, conveyors consist of a series of both unpowered and powered cylindrical rollers. These roller-based conveyors work best for transporting flat-bottomed objects such as carboard boxes or molded part pucks.
Simple conveyors with only unpowered rollers work as manual conveyors (to let personnel push items along the low-friction conveying surface) or gravity conveyors which incorporate downward slopes — often as diverting-conveyor offramps to feed items to their final workplace or collection destinations. Here a competitive conveyor option is the ball-table conveyor — studded with freewheeling spherical rollers to let conveyed product freely glide along. The motorized rollers on roller-based conveyors can either couple to a gearmotor on the conveyor flank or directly integrate motors called drum
motors inside their cylindrical bodies — in turn usually made of steel or (if intended for washdown settings) stainless steel.
Conveyors to position items with moderate accuracy (say, for simple spacing of boxes) might employ only motorized rollers. In contrast, systems or sections of conveyor with laxer requirements (or relying on peripheral systems for final positioning functions) might gang a few unpowered rollers to each powered roller via cords or bands made of round polyurethane belt. These bands loop around and nestle into grooves on the powered and unpowered roller ends; tension keeps the round bands firmly set in their grooves and facilitates the transmission of power from motorized roller to ganged passive rollers.
Linear-motor conveyors, also called smart transport systems by those who aim to differentiate the offering, are costly but enable very sophisticated applications. Some modular linear-
Constant Force Lead Screw applies uniform pressure to the nut at all stages of travel along our quality CNC rolled lead screws. World class NEMA motors combined with an integrated lead screw make for one of the most accurate lead screw assemblies on the market.
Our miniature ball screw assemblies combine fine leads with small screw diameters, and utilize a compact internal ball return system to yield high precision linear motion for a range of small-scale applications. In addition, our ball screws are precision-rolled, making them a critical asset to laboratory machines, medical devices, and mechatronic applications.
transport systems can trim machine footprints by half when used to replace indexing and conveying equipment.
The movers on some such systems can travel independently of one another or in groups along several customizable rail systems. High dynamics and precision help the system excel in gapping and diverting applications — and a new hygienic version is aimed at pharmaceutical, biotech, packaging, and food and beverage environments.
Modular linear transport systems are not designed to replace other conveying systems. However, traceability with the system can reduce the scans required for each piece through an operation. Because movers are mapped as individual servo axes, controls never lose track of items being transported. Such
traceability in traditional architectures can require innumerable scanners ... so the component and labor reductions of intelligent transport systems are worthwhile in some cases.
Other options for conveyance of specialty goods are two-axis airbearing stages and planar motors. Air-bearing stages suspend the carried load on a cushion of air and for motion rely on linear motors— often with an ironless forcer design for smooth actuation. Driving is typically centered near the center of mass to maximize the straightness and minimize the angular errors of each motion. In contrast, planar motors use the electromagnetic behavior of its motors for both the movement and suspension of loads … which is why they’re occasionally called magnetic levitation or maglev stages. Some such
systems levitate the magnetic movers with six degrees of motion up to 5 mm above planar motor tiles.
Future packaging machines will also be judged by how well they integrate into so-called connected industry concepts. Here, the idea is to let design engineers build machines and networks to connect operational technology or OT — the drive, control, and even process and manufacturing components and software that they integrate everyday — with those of information technology or IT … here, the managerial, sales, ERP, supplychain, and inventory tools of an organization.
Several motion-component suppliers have over the last 15 years purchased or developed software to
let packaging-plant management and ERP-level data dictate what happens on factory floors. Others have established partnerships with Cisco and similar companies to offer these functions to OEMs and end users. Much of the integration here uses Ethernet to connect to IT data for IT/ OT convergence — relevant to many industries but particularly beneficial to packaging for the regulation of output to better meet demand … as well as product safety through tracking.
Formats for individual products— stand-up pouches, child-resistant (CR) packaging, anti-bacterial wraps, multifunction container lids, and custom-sized cartons — also continue to proliferate. In fact, market reports from the Flexible Packaging Association, a trade
association for converters of flexible packaging and industry suppliers, global use of specialty packaging has grown unabated over the last decade and now exceeds $30 billion. That’s thanks to better automation as well as advances in materials and processes. For example, some OEMs that build form-fill-seal machines for pouch products are switching from heat sealing to ultrasonic sealing, as the latter is more forgiving and efficient. Ultrasonic welding also improves beverage packaging. One technique from Germany-based Xolution (not to be confused with OXO) ultrasonically welds polypropylene lids to aluminum cans for a portable mug design that otherwise lets beverage companies can drinks by traditional means. OEM
This system offers plug-in convenience allowing up to 32 switches to be run in series. The system features redundant cascading OSSD outputs which eliminates the possibility of fault masking (TR24119) and offers superior diagnostics and communication via IO-Link, NFC or PLC.
908-806-9400
908-806-9490 (FAX)
info@altechcorp.com
www.altechcorp.com
to ensure we stayed on track. So, they returned to remediate the floor some more, and it worked. We did all our receiving, got our pallets received, and then had to clear the floor again.
DW: Were there any other surprises or unplanned tasks?
Schulte: The AutoStore was built while we worked with other vendors. We had to get electrical to support what was going into the AutoStore. We had to get data run for the pick ports because each pick port needed its own data.
We had a huge ceiling fan right above the AutoStore, so we had to move it because we didn’t want it to hit anyone on the grid. We also had skylights above the AutoStore and hired roofers to cover them to avoid the risk of leaking.
Then, we found out about our fire suppression requirements. We needed
a fire pump, which was pretty expensive and something we didn’t expect. We also had to get a VESDA alarm system for very early smoke detection. If there's any smoke in the air, it triggers an alarm, the robots huddle together, and the AutoStore stops. We spent a lot of time and effort making sure that got done in our timeframe. We started talking to the fire suppression people in January 2023, and it was the last thing completed in the project. The final pump inspection occurred the week we went live, so it took the full 10 months to get the fire suppression done.
But we had a great group of contractors help us get ready. The electricians pretty much lived here for three months. We had a construction company build the pump room, and they were always here, as were the fire suppression people. So, we grew
great friendships and spent a lot of time together, supporting them and giving them what they needed to ensure the work got done well and on time. Having those people to work with is essential to ensure success.
The Kardex team started building about the week after the Fourth of July and was done toward the end of August. The grid was built quickly, and the people were here every day. The whole process and everything we’ve done with Kardex has been a great experience.
DW: How was the experience for anyseals employees?
Schulte: There was a lot of skepticism from employees while the machine was being built. They’d say, “There's no way this machine will be faster than us. We're so fast. We're going to be better than the machine.” Now that it’s installed, they're
trying to get as much stuff into it as possible because it makes picking much easier and faster. So, it's the flip-flop of people fighting it initially and then loving it at the end.
Overall, though, it was exciting for them. It was also quite tiresome, but we made it through. It’s important to have a great group of people to work with and engage your employees so they understand what's happening and that they're a big part of it. There was a lot of change and work to get through, but everybody's excited about it now.
DW: What are some other tips or lessons learned?
Schulte: Project costs are obviously a big factor, and with projects of this size, you usually have a lot of change requests. We went slightly over budget with only three change requests. For example, in the middle of the project, we decided to add an extra pick port before everything shipped from outside the country because it would be cheaper than ordering it later. There are also seismic towers that hold the grid in place. We planned on having six but needed eight to make the structure safe and sturdy. So, there was another slight change, but nothing shocking.
During the first two weeks of September, Kardex inducted all the bins.
Warehouse employees place parts on the scale, the scale interacts with the WMS, and employees fulfill the correct quantity. Leftover parts go back in the bin and then to storage. | anyseals
Our AutoStore has 20,000 bins, so we had truckloads coming in, which took about seven days. We can handle 5,000 more bins, so our AutoStore can hold 25,000 bins in total.
We went live in early October, two weeks ahead of schedule. The WMS went live first, then the AutoStore. From then, we started filling the bins, which can be challenging. It’s important to schedule the time and appropriate people to do the inbound and get inventory into the AutoStore. It’s hard to completely test until you have a good amount of inventory in the AutoStore. So, in the beginning, set up time to get as much inventory in there as possible. And if people are doing outbound, make sure you have people that can do inbound, too.
DW: How’s the system running now?
Schulte: We have 100% uptime. The WMS interaction with the system had a few little glitches, so good, strong communication between the interfaces is important. The WMS must speak to the AutoStore to ensure you successfully integrate the two.
Now, we're starting to put more inventory in and can look at our daily picks from the overstock and AutoStore areas. With the AutoStore, the average time for a bin to come to us is eight
seconds. Nobody could go through the warehouse and pick something in eight seconds.
Our business is unique because we don’t just grab products from the bin, and then the bin goes away. We grab a bag from the bin, place the parts on the scale, and weigh it to ensure we have the correct quantity. The scale and WMS are integrated, so the WMS knows the weight of each item and how many are needed to ensure the correct amount for each customer. So, the bin comes down, we take a bag from the bin, put the parts on the scale, then put the leftovers back into the bin, and the bin goes away.
Previously, our manual picks could take up to 15 minutes per pick because we had to get a lift truck to pull down the pallet, find the box on the pallet, and bring the bag to the scale counters. That could take five to 15 minutes, depending on the inventory's location. Once we weigh and count the customer’s parts requested, we label and send it to the shipping department. In the past, the parts we put back into the bin had to be returned to wherever we got it from. Now, we just leave the parts in the bin, and the bin goes away. So, we’re saving tons of time on the put-away as well.
One of the big things I learned is that the WMS is the brain, and the robots do whatever the WMS tells them to do. For example, when we have rush orders, we can’t wait to get through 200 picks before getting the rush order out. So, we learned how to prioritize within the WMS to ensure orders are shipped on time. Another recent challenge, as we’ve been putting inventory in the AutoStore, is when we call a bin down, we have another bin going out with that same inventory. So, who wins? Does it go inbound or outbound? It should always be outbound to ensure it gets to the customer, but we’ve been working through those learning factors. It’s been a challenge, but it’s been interesting to learn. AW
anyseals • anyseals.com
Powerful, multi-purpose solutions with easy installation and maintenance
High-speed, multi-code, multi-symbology barcode reading
Modular, standard structure gets you up and running faster
Advanced, real-time data and analytics
Mobile robot technology is moving fast, and generative AI is pegged to transform machine vision to enable more integrated solutions.
Vision systems are the bread and butter of AMRs and keep improving as technology evolves.
BY: RACHAEL PASINI SENIOR EDITORAdvanced machine learning and visual processing are major trends in automated mobile robot (AMR) development. According to Gartner’s Emerging Tech Impact Radar, advanced computer vision and AI acceleration will be among the most important influencers within the next two years.
“In the past decade, machine vision changed a lot due to technological improvements. In the beginning stage, machine vision was rule-based, which is still very efficient. But about five years ago, deep learning highly improved accuracy and performance. Now, generative AI is changing machine vision again,” said Magic Pao, AVP of Industrial Cloud and Video Group at Advantech, during a keynote panel at the 2023
Advantech Industrial IoT World Partner Conference in Taipei, Taiwan.
Vision is critical for AMRs to navigate complex environments, avoid obstacles (including human workers), and identify and handle items correctly. AMR vision systems typically consist of:
• Cameras that capture image and video footage of the robot’s surroundings
• Other sensors, such as LiDAR and 3D sensors, that help the robot understand its surroundings, develop depth perception, and detect objects
• An onboard processor to analyze visual and sensor data. This processor runs computer vision algorithms to make sense of the
data, identify objects, detect anomalies, and determine the robot’s position and orientation. It may also run simultaneous localization and mapping (SLAM) algorithms to create maps and localize the robot within the maps.
• A communication interface to send and receive data to other robots or systems, such as a central control system
AMR vision systems must be highspeed and low-latency to be effective and ensure safe operation around humans. They also require technology to transmit and process large amounts of data over various distances. Therefore, Gigabit Multimedia Serial Link (GMSL)
In the past decade, machine vision changed a lot due to technological improvements... Now, generative AI is changing machine vision again
technology is often preferred because it can facilitate high-speed data transmission from cameras to the onboard processor and external devices and systems. It also allows data integration from multiple sensors and sources, enabling more complex, real-time decision-making. The latest generation, GMSL3, supports up to 12 Gbps and can transmit data up to 15 m from its host processor.
“We chose GMSL as our technology to empower our computing unit with visual capabilities,” said Jacky Liu, advanced computer vision head of Industrial Cloud and Video Group at Advantech. “It’s not a new technology and has already been widely used in the automotive industry with features such as high data rates and long-distance transmission. Its robustness and data integrity ensure reliable operation in challenging environments, and the scalability and synchronization allow you to run multiple data streams. With GMSL, our current video capture card can support up to eight channels, even 3D cameras, simultaneously.”
In early 2023, Advantech partnered with e-con Systems, an OEM camera solution provider, on a GMSL camera and AI computing system for automated guided vehicle (AGV) and AMR applications. The MIC733-AO is an industrial AI inference system based on NVIDIA Jetson AGX Orin. It has high AI performance of
up to 275 TOPs, a wide range of I/O interfaces for 5G/4G connectivity, and multiple video inputs, including two GMSL. The GMSL camera from e-con Systems transmits video data over long distances, and the solution can integrate multiple cameras into a single Jetson system.
“Today, the whole value chain is compressed, and each role is trying to integrate more things,” said Pao. “We integrate video acquisition software, called the Advantech CamNavi SDK, with NVIDIA ISAAC SDK and ROS2 (Robotic OS) into one software package. We don’t just pre-install them — we also pre-build and pre-train them. To adapt it for robotics, AMRs, and cobots, we just put application software on top and enable the solution.”
During the keynote panel at the World Partner Conference, Pao reiterated that generative AI is changing machine vision and that NVIDIA’s generative AI SDK is ready on the MIC-733-AO. With generative AI, vision systems can improve data augmentation, search functionalities, and image reconstruction. For example, a company may not have enough images to train an AMR to accurately detect item defects or damage. However, with generative AI, the system needs just a few images as examples and can generate numerous defect images with different aspects to retrain the AMR.
Autonomously transport materials up to 4,200 lb with the industry’s most comprehensive autonomous mobile robots and fleet management software.
$1.5M
saved in the first year at an aerospace facility
6x
throughput increase at a CPG facility
11 month
customer payback period at an automotive facility
“Accelerating AI from developer to deployment is very important,” said Elvis Lee, industrial AI platform manager of Industrial Cloud and Video Group at Advantech. “GPU performance has increased 1,000 times compared to five years ago, and data has increased 10,000 billion times within the past 10 years. The data is moving very fast compared to previous technology.”
While moderating an afternoon panel, Lee mentioned that NVIDIA recently surveyed its customers to understand what sensors and sensor interfaces they use in AMR projects. LiDAR sensors and USB, MIPI, Ethernet, and IR cameras are among the most popular. Mixed-sensor integration is also popular, but driver and compatibility issues and long integration times can delay projects.
“GMSL does not define a consistent camera parameter data structure, so people spend a lot of project time ensuring compatibility between the GMSL capture card and a device,” said Liu during Lee’s panel. “Currently, we are working on defining a camera parameter profile and plan to integrate it into our unit by the second half of 2024. We believe this will help customers easily select a camera, shorten the overall project time, and make the configuration more flexible.”
Advantech isn’t alone in its integration efforts, and as Pao noted, it takes the entire value chain to see widespread industry impact. “The whole value chain is very long. If you start from the chip vendor, system manufacturer, systems integrator, and toward the end user, it’s a long journey,” he said.
For example, on day two of the conference, Pyong W. Pak, CEO of Movensys, spoke about his company’s all-in-one software controller platform for AGVs and AMRs and how it opens doors for engineers.
“One thing that we've heard from our customers is that vision engineers do not know about motion control, and motion control engineers do not know about vision. So, we’re working on an all-in-one solution that ties vision and motion control,” said Pak.
Pak also noted that according to Interact Analysis, though more than four million mobile robots will be installed worldwide by 2027, only 14% of warehouses will deploy at least one AMR by then. However, as vision technology evolves and more companies prioritize integration, adoption barriers may dissolve and make advanced automation a reality for more warehouses. AW
Advantech • advantech.com
Autonomous and collaborative robots are quickly becoming essential warehouse tech. Here’s a look at their differences, the tasks they perform best, and a few important features.
Robotics are a common sight in manufacturing and assembly. These stationary machines are great at handling repetitive or predetermined tasks but are almost useless in a dynamic logistics and materials handling environment. However, warehouse operators are increasingly looking to leverage the many advantages of robotics to transport items through the facility. That’s where an autonomous mobile robot (AMR) or collaborative mobile robot (CMR) is a great fit.
AMRs navigate their environment using semi- or full autonomy. These are basically mobile platforms — often traveling on wheels — outfitted with various features to perform specific tasks. Many AMRs use SLAM (Simultaneous Localization and Mapping) technology, which helps the robot locate
itself in its environment and adapt its behavior to dynamic situations.
AMRs also navigate using cameras, sensors, artificial intelligence, and machine vision. These technologies help avoid collisions with machinery or people and connect with other robots and digital systems to seamlessly integrate with the larger operation.
This ability to choose their own route through the environment sets them apart from their predecessors, autonomous guided vehicles (AGVs), which follow a predetermined path to complete automated tasks under a human operator’s supervision.
AMRs can bring significant benefits to a busy warehouse, including: Worker safety. AMRs take on tasks
that could be dangerous or impossible for human workers to perform. These operations range from cleaning and disinfecting to transporting dangerous materials and heavy loads or working in extreme conditions that are uncomfortable or harmful for humans.
Flexibility. Shop floor operations don’t grind to a halt because a robot encounters a fallen box or a crowd of people. AMRs don’t need the direct supervision of an operator; they can assess and react to their environment in real time while completing their tasks.
Boosting productivity. AMRs tackle low-skill repetitive tasks, such as transporting materials across a production floor, cleaning, and package sorting. Employees can focus on highervalue tasks while the AMR navigates around the workspace.
Generating data. An AMR doesn’t work independently — it’s usually connected to a digital platform and constantly communicates with other robots and company assets. The sensors generate significant amounts of performance data that help create actionable insights about operational efficiency. AMRs also function as mobile data-gathering platforms that empower enterprises to improve business operations from process efficiency to preventative maintenance to workforce behavior.
AMRs add value in a variety of situations and come in a wide range of shapes, sizes, and abilities. Here are a few broad categories:
Picking robots. Picking AMRs identify, pick up, and handle items from fixed shelves. In conventional picking, human pickers physically move from one shelf to another, picking products and carrying them or placing them on conveyors or carts. A picking AMR can take on the work of picking and transporting items between workers and stations, enabling workers to take items without moving around.
Sorting robots. Sorting AMRs scan packages and determine where to deliver them within the warehouse. They autonomously plan and travel the optimal route, then deposit the packages themselves or wait for human operators to accept them.
Autonomous forklifts. These driverless forklifts transport heavy materials across a facility. There are generally two types: a pallet jack, which can transport material from one position on the floor to another, and a pallet stacker, which stacks materials.
Inventory robots. These robots automate inventory management, keep track of inventory levels, product location, and planogram compliance, and can confirm product pricing. Inventory tracking, movement, and reconciliation can be a time-consuming challenge, particularly for large-scale operations, such as fulfillment centers — and inventory AMRs can track inventory with a lower chance of error than a human counterpart.
Drones. Drones are becoming increasingly common for last-mile deliveries, autonomous inspection, and even disaster response. These airborne robots perform accurate and ongoing monitoring of facilities and the workforce. They can deploy high-resolution cameras and other sensors and use AI-powered software for analytics.
Autonomous tow tractors. These AMRs help automate the transportation of materials in dynamic
Non-contact transmission of both power and data offers
– Safe and fast data communication via Ethernet Signals (Profinet, Ethernet IP, etc.)
– High energy transmission (up to 400 Watts)
– Totally wear and maintenance free F180
and high-traffic environments. They reduce trips, particularly when towing many items in cart trains, can increase throughput productivity, and enhance worker safety by reacting to unexpected changes and avoiding collisions.
Automated guided carts. These robots are known for their small chassis and low profile, which enable them to fit under carts or shelves for transportation. These machines navigate small spaces with minimal or zero turn radius and must navigate around workers and other robots.
Cleaning robots. These robots perform tasks such as scrubbing, mopping, vacuuming, and disinfecting. Cleaning AMRs, such as automated scrubbers, are a relatively new entry in the market and are becoming increasingly popular as solutions to labor shortages. Heightened awareness of cleanliness and sanitizing brought on by the COVID-19 pandemic also contribute to their
AMRs are being relied on more and more across a variety of sectors. With the ability to navigate and problem-solve autonomously, they unleash significant potential for increased efficiency, process optimization, data gathering and management, and worker safety. And with more operations connecting to the Internet of Things, robots that dynamically adapt to and enhance the work of human employees could be game changers for the shop floor and entire
Though AGVs and AMRs have become popular, they have limitations. When a task requires more than just moving products around a facility, CMRs are an option. They are equipped with sophisticated sensors and intuitive controls that read human body language, identify and respond to social cues, and anticipate what their human coworkers will do next. To accomplish this, CMRs use LiDAR sensors, 3D depth cameras,
CMRs have a few distinct advantages, www.dornerconveyors.com
Intelligence. Thanks to deep learning and AI, CMRs generate and process information efficiently with little or no need for instructions from a human operator. These machines self-manage and make decisions on the fly. As a result, they execute repetitive or hazardous tasks and adapt to the humans around them in real time.
Connectivity. The increased processing power needed for intelligent automation also means CMRs use machine-to-machine communication to interact with humans through multiple integrated interfaces, such as touchscreens and sensors. In contrast, most AMRs don’t have this level of interactivity.
Flexibility. CMRs adjust the way they work based on changes in their environment, adapting to different layouts or paths through a warehouse.
Improved safety. Intelligent CMRs that can handle and process massive datasets in real time can better predict human actions and perform high-precision movements in response to humans — making these robots safer for people to work alongside. These machines have highly responsive and reliable failsafe mechanisms. AW
To move fast this year, logistics companies will be looking for solutions that automate processes and increase throughput while decreasing costs. End users and OEMs need technologies that don’t require custom design and installation, but rather are standardized, easy to install, operate, and maintain; and solve multiple applications, in place of discrete devices that only satisfy a single need. Also, it will be table stakes for leading companies to expect solutions to include advanced data and analytics capabilities to enable better decision-making and troubleshooting.
While the ultimate goal of logistics companies is to have “dark warehouses” that require few workers and rely on automation and robotics, the reality is that many companies are simply trying to increase the amount of
automation at their warehouses to gain an incremental competitive edge. This is why technology providers have shifted their focus toward the development of standard, easy-to-use vision solutions for logistics, enabled in large part by advanced technologies — such as AI (Artificial Intelligence).
At Cognex Corporation, we’ve committed to creating standard solutions that help facilities advance operations with automation. Most recently, we’ve released our new Modular Vision Tunnels. These flexible scan tunnels offer one-to-six-sided barcode scanning for a range of speeds and box gaps. These solutions are quick and easy to install for reduced
downtime and risk, and address multiple challenging applications, such as inbound receiving, outbound truck loading, and ship sorting.
These solutions are modular, yet compact; customers can set up tunnels with different configurations, add on vision tools such as dimensioning, and choose between DataMan 380 or DataMan 580 image-based barcode readers, which offer multi-symbology decoding, the ability to read multiple codes, and 99.9% read rates. Edge Intelligence data analytics software is built within these tunnels, allowing customers to easily set up and maintain them with real-time insights into performance and maintenance.
Since both end users and OEMs want to increase throughput while ensuring traceability and keeping costs down, it’s important to choose solutions that are standard, yet flexible. Solutions that require custom installation and starting from the ground up each time can be costly and riddled with risk. Logistics companies that want to get ahead need to future-proof their technology investments to ensure that they’re able to scale as their business grows.
For more information, visit www.cognex.com/RobotReportNov and view our Logistics Solutions Guide.
Automated Guided Vehicles (AGVs) and Autonomous Mobile Robots (AMRs) are revolutionizing the way materials and goods are moved within various industries. These innovative robotic systems are designed to optimize efficiency, enhance safety, and streamline logistical operations.
AGVs are wheeled robotic vehicles that are guided along defined pathways within a facility, such as magnetic strips or tracks. They are equipped with sensors and software that enable them to navigate autonomously while carrying out tasks such as transporting materials, components, or finished products. AGVs are adept at performing repetitive and standardized tasks, making them ideal for applications in manufacturing, warehousing, and distribution centers. Their precision and reliability contribute to improved productivity and cost savings for businesses.
On the other hand, Autonomous Mobile Robots (AMRs) are an evolution of AGVs, leveraging advanced technologies such as LiDAR, cameras, and sophisticated algorithms to navigate and operate in dynamic environments without the need for physical guides or markers. AMRs have the flexibility to adapt to changing surroundings, avoiding obstacles, and adjusting their routes in real time. They excel in scenarios where the operational environment is subject to frequent changes, allowing
for seamless integration into workflows alongside human workers. AMRs are increasingly utilized in e-commerce fulfillment centers, hospitals, and other settings where agility and adaptability are paramount.
Both AGVs and AMRs offer substantial benefits to businesses, including increased operational efficiency, reduced labor costs, enhanced workplace safety, and the ability to operate 24/7. Furthermore, these robotic systems contribute to the optimization of supply chain management by facilitating just-in-time delivery, inventory tracking, and order fulfillment. The integration of AGVs and AMRs into existing infrastructure represents a strategic investment for organizations seeking to modernize their operations and gain a competitive edge in a rapidly evolving market landscape.
In conclusion, the proliferation of Automated Guided Vehicles and Autonomous Mobile Robots signifies a paradigm shift in industrial automation, empowering businesses to achieve higher levels of productivity and operational resilience. As these technologies continue to advance, their potential to revolutionize the future of logistics and manufacturing is undeniable. Please contact DieQua to discuss your automated warehouse applications, or to ask us any questions you may have.
In the dynamic landscape of modern warehousing, the integration of conveyors and robotics has emerged as a game-changer, revolutionizing how facilities meet goals of throughput and accuracy. This combination enhances operational efficiency and catapults warehouses into a new era of productivity.
Elevating Throughput with Robotic
Precision:
Robotics, equipped with advanced vision systems and machine learning, are transforming the movement of goods within warehouses. Automated guided vehicles (AGVs) and robotic arms seamlessly collaborate, ensuring a continuous flow of items from receiving to shipping. Conveyors act as the arteries, efficiently transporting products between robotic workstations and amplifying throughput rates. Dorner conveyors specifically act as the Autonomous mobile robots (AMRs) and robotic arms have redefined order picking. Conveyors play a pivotal role in integrating these robotic picking systems, allowing for a smooth transition of items from storage to packing stations. This dynamic interaction ensures that orders are fulfilled rapidly, meeting the demands of today’s fast-paced supply chains.
Dorner’s 2700 Medium Duty series conveyors are designed for AGV/ AMR compatibility, allowing for quick and easy integration of the technology
into existing conveyor systems. With a robust design, increased weight rating, extended widths, and a low-profile aluminum frame, the 2700 series is ideal for applications that require both speed and precision.
Precision at Scale: Conveyors and Robotics Driving Accuracy:
Automated Quality Control: Robotics with computer vision capabilities ensure unparalleled quality control process accuracy. Conveyors serve as a conduit for products to undergo automated inspections by robotic systems, guaranteeing that only defectfree items proceed through the supply chain. This not only reduces errors but also maintains high product quality.
Error-Free Order Fulfillment: Integrated with robotic order fulfillment systems, Conveyors contribute to flawless picking and packing processes. Robots navigate the warehouse, guided by conveyors, ensuring the correct items are selected and efficiently transported to packing stations. This collaborative approach significantly reduces order errors and enhances overall accuracy.
Real-time Inventory Accuracy: In conjunction with conveyors, robots are transforming inventory management. Drones and robotic platforms equipped with RFID technology conduct real-
time inventory checks. Conveyors efficiently transport these robotic platforms, enabling swift and accurate updates to inventory levels. This synergy ensures that warehouses maintain optimal stock levels, reducing the risk of stockouts or excess inventory.
Efficiency:
As modern warehousing continues to evolve, the integration of conveyors and robotics is a testament to technological innovation. This dynamic duo not only meets the demands of today’s throughput and accuracy goals but also positions warehouses for a future of continuous improvement and adaptability. By embracing this integrated approach, warehouses are not merely keeping pace with the times but defining the future of efficient, accurate, and responsive supply chain management.
Enidine’s HD/HDN Series shock absorbers are the compact, reliable solution you have been looking for to extend the service life of your warehouse’s automated storage and retrieval systems and overhead bridge and trolley cranes.
The highly engineered product line features zinc-plated and painted external components or optional epoxy painting, and an internal charged air/ oil accumulator or optional bladder accumulator for higher cycle rates.
Better yet, Enidine’s HD/HDN series solutions provide advanced corrosion resistance, making them ideal for use in harsh environments. Available with bellows, clevis mounts and safety cables. The shock absorbers’ orifices are also fully customizable to meet the specified damping requirements of your warehouse applications.
Customers can also opt for fluids and seal packages to expand the standard operating temperature range from (15º F to 140º F) to (-30º F to 210º F).
While they may have a shorter overall length and reduced weight than other industrial shock absorbers on the market, don’t let the compact size of these advanced solutions fool you. The HD/HDN line of shock absorbers meets the deceleration requirements of loads up to 8 million in-lbs. per cycle, keeping your equipment safe from wear and tear
and your operators safe from the risk of equipment malfunctions. And those protections extend to the environment as well.
All HD/HDN series shock absorbers are made with eco-friendly materials and offer the opportunity to add piston rod extension sensors for re-use safety requirements. The solutions are also certified by global governing bodies including the Occupational Safety and Health Administration (OSHA), the European Federation of Materials Handling and Packaging Manufacturers (FEM), and more.
The team at Enidine understands the importance of reducing downtime at your plant, so all product sizes in its HD/HDN line of heavy-duty hydraulic shock absorbers were engineered to be fully field-repairable. HD/ HDN series solutions are also manufactured and serviced in global locations, making it easier for you to get the support you need when you need it most. That means there will be little to no disruptions to production when maintenance is required – helping to keep your plant running efficiently and on schedule.
To learn more about Enidine’s HD/ HDN series solutions, visit www.enidine.com.
Emerging technologies are revolutionizing supply planning, enhancing supply chain efficiency, agility, and resiliency. Real-time data and advanced analytics driven by connected assets and systems help identify potential disruptions, mitigate risks and make informed decisions. We will discuss key insights into today's supply chain challenges.
What are today’s supply chain challenges?
The constantly evolving global supply chain landscape poses a range of challenges for businesses today that can impact their operational efficiency and effectiveness. Here are the biggest challenges:
• Business disruptions and market volatility: Over the past five years, supply chain operations in various industries faced unexpected events, which resulted in reactive responses. This can impede the ability to meet demand, leading to lost revenue, increased costs, and a decline in overall profit margins.
• Demand predictability: Social media, COVID driven direct-to-consumer (DTC) models, market volatility, and now inflation have made traditional demand forecasting insufficient. Operations are leaning on outdated forecast approaches that also lag and fail to respond adequately to current market dynamics.
• Holistic inventory visibility and optimization: Inventory management is complex and dynamic. The end of 2022-2023 saw excess inventory across many organizations due to COVIDrelated supply chain constraints. This led to higher costs, lower margins, and waste. The long term impact will lead to lost sales, and loss of differentiation, loyalty, and market positioning. Adopting an integrated approach and leveraging advanced technology and best practices, businesses can overcome these challenges - improving supply chain efficiency and resilience.
What is lacking in today’s supply chain strategies?
Supply planning today involves technology, data analysis and stakeholder collaboration. While technical and data analytic advancements have been made, there are still several areas that need improvements in the industry:
• Accurate transparency of data
• Dynamic supply planning and execution based on integrated intelligence and automated decision-making
• Convergence of network modeling, scenario and traditional planning and planning
Businesses want to improve supply chain visibility, predict, and mitigate risks, and optimize performance. Incorporating advanced concepts can enhance agility and resilience, meet customers’ evolving needs, and optimize performance. Below are a few advanced technologies and characteristics that must be included in an organization’s growth plans for supply chain optimization.
• Artificial intelligence and machine learning: Artificial Intelligence (AI) and Machine Learning (ML) can help businesses analyze data, find patterns, and make proactive decisions to mitigate risk. Many planning solutions have already integrated AI/ML into their core plans, but further integration of this can enhance algorithms. This could include detecting shifts and anomalies -- optimizing execution, automating operations such as key planning processes and real time decisions, and more.
• Digital twins and advanced simulation: Digital twins and simulation create virtual versions of physical assets, processes, and systems. These outputs can be used to evaluate scenarios and risk, identify key constraints, optimize, and evaluate alternative configurations.
With data and AI/ML, digital twins can continuously evaluate supply chains and networks, informing businesses in an unprecedented way.
• Automation and autonomous systems: The targeted deployment of automated storage retrieval systems (ASRS), autonomous mobile robots (AMR) and other assets with IoT connectivity, RFID asset tracking and machine vision can mitigate risks ranging from labor shortages to inventory loss. Working in tandem with digital twin and AI/ML, these assets comprise self-optimizing systems that drive higher output and efficiency by learning from both physical and simulated scenarios in the connected warehouse.
The future of supply chain planning requires digitization, automation, connectivity, and data-driven decision-making. Organizations that embrace these technologies create agile, transparent and efficient supply chains that are resilient to market changes and disruptions.
KALYPSO.COM
You can read more in our recent whitepaper, Synchronizing Supply & Demand in 2023 and Beyond.
Ryan Ashdown rashdown@wtwhmedia.com
216.316.6691
Jami Brownlee jbrownlee@wtwhmedia.com
224.760.1055
Mary Ann Cooke mcooke@wtwhmedia.com
781.710.4659
Jim
Mike
Subscriber
POSTMASTER:
My initials were visible on the structure protruding from the roof of the white Jaguar as it approached. The car pulled up and the app signaled I could unlock the door. With a tap, the door handles extended. I entered for my first ride in a fully autonomous vehicle. I found myself alone in a car, feet away from the steering wheel and pedals, with a voice reminding me not to touch anything.
The ride required an app, as rideshares do. There were videos explaining what to expect. I had to agree to a number of things in documents that read like a software EULA. It was clear the system was experimental.
It is not the only time I’ve felt a vehicle was experimental. Every time I get into an unfamiliar car, I feel like a test subject in an experiment. I’m being tested to see if I can figure out how to operate the car. The brake pedals and accelerator are in standard positions. Turn signals are standard. We still use steering wheels. Pretty much everything else needed to operate the car can be anywhere.
The rental car had a touchscreen. It was larger than my first laptop screen, mounted in page orientation dead center of the dash. There were two knobs beneath, one for volume, one for tuning. Many other systems were controlled by the touch screen. Setting the temperature required getting through three screens. Same for sound. More screens for navigation. It felt experimental.
I’m not alone in questioning whether cars becoming computers on wheels is a good thing. A recent study concluded drivers performed worse doing simple tasks in all new touchscreen cars. The best performance came from a 20-yearold Volvo with no screen. Another study concluded touchscreens were worse than cellphones and drunk driving. It seems we’ve all been part of an experiment to determine exactly what constitutes too many distractions.
The rental didn’t have a key, it had a fob. No digging through pockets or purse, a touch unlocks — and a press of a button starts. Turns out fobs are experimental, vulnerable to amplification relay attacks. Keys may be quaint, but I never needed a Faraday cage for keys. How to unlock and start a car is still experimental.
Control locations are inconsistent. I thank Jim Moylan every time I see the Moylan arrow telling me the gas fill location. I need arrows for headlight switches, cruise control and the parking brake. Manufactures are still experimenting with new places to hide them. Think of the experimentation on the steering column levers alone. Windshield wipers could be a push, a pull, or a twist. There can be multiple twisty things on the same lever. And a button to depress on the end, too. The cruise control could be adaptive or not. It is an experiment to get behind the
wheel of an unfamiliar car. I maxed out all the safety gizmos when I bought my car. It makes me less safe when I drive other cars. My car lights up the mirror indicating a car is in my blind spot. I’m trained to go when there is no light. Cars with no blind spot indicators never light up. Their mirrors always tell me to go. My car should light when it is safe to go, no light when it isn’t. Even better, a green light and red light, making it really evident blind spot monitoring is present, and, more importantly, when it isn’t.
My Waymo ride was uneventful. I was never uneasy. I felt safer than in the first moments driving an unfamiliar car. I felt at least as safe as a normal ride share. Hesitations gave the impression the car was deciding what to do. All turns, all accelerations were measured. I can’t say that about every ride share I’ve taken. It was an experimental car, as the bristling sensors announced. I never felt like I was the subject of the experiment. DW
Since 1898, we've partnered with the most innovative companies around the world to solve complex challenges and advance technology.
As industry leaders, you can depend on our decades of experience, unrivaled reliability, and custom cable solutions that power technology from coast to coast and around the globe.