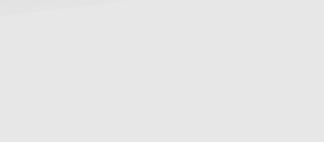
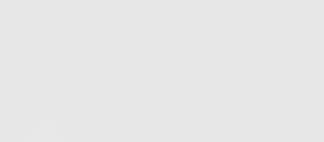
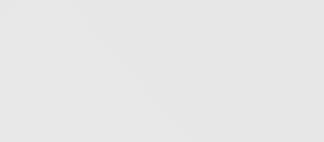
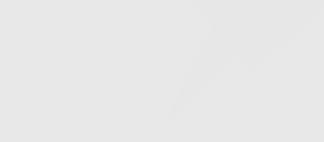

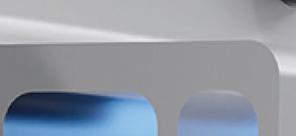
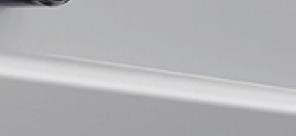
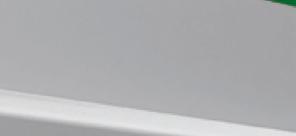
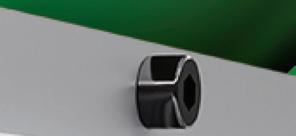

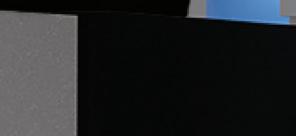
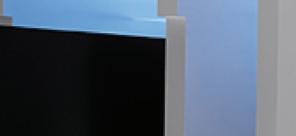
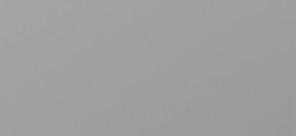
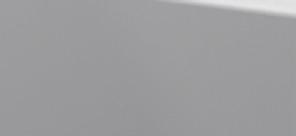
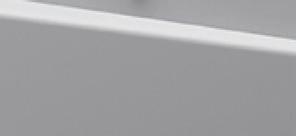

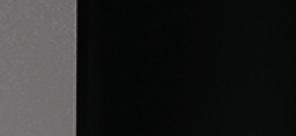

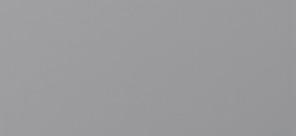
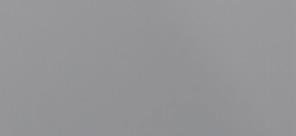
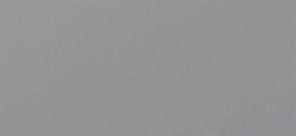
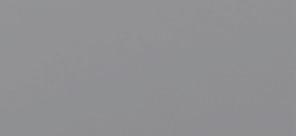
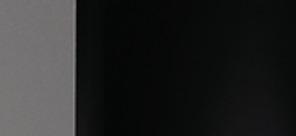
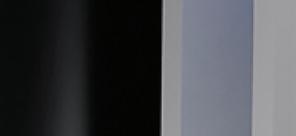
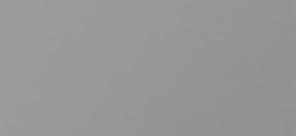
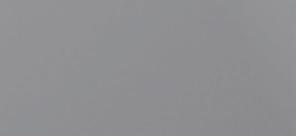
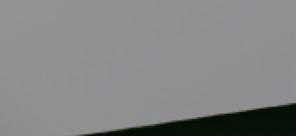
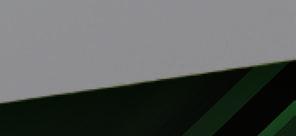
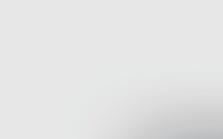

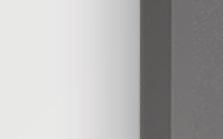
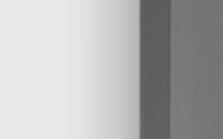
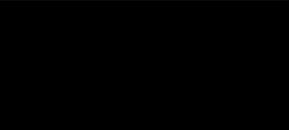
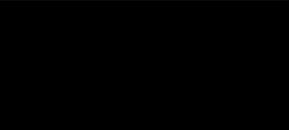
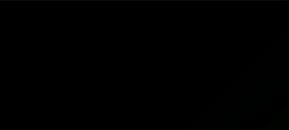

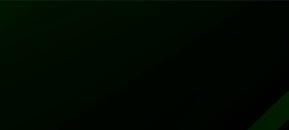
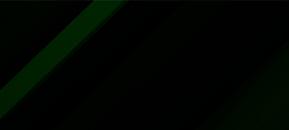
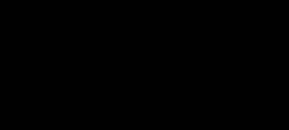
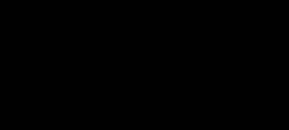
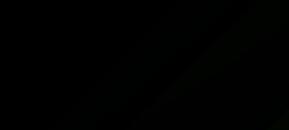
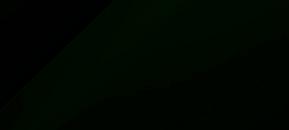
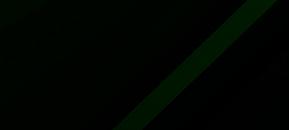
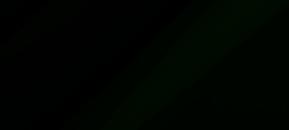
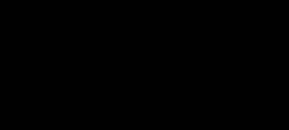
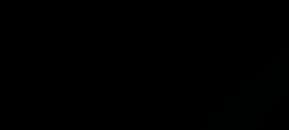
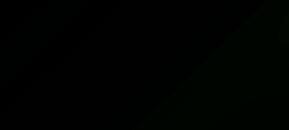
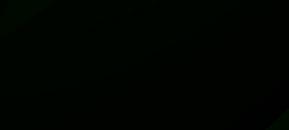
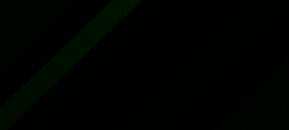
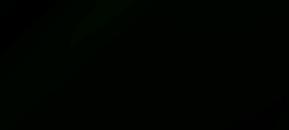
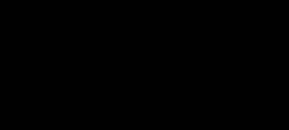
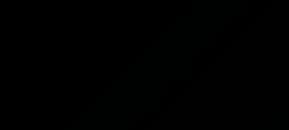
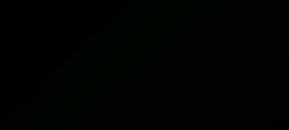

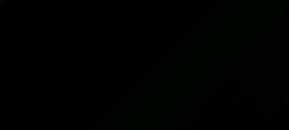
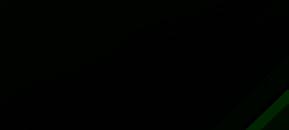

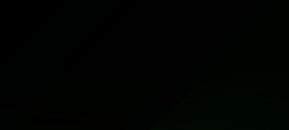
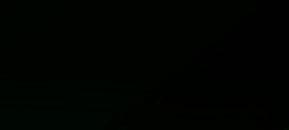
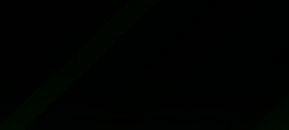
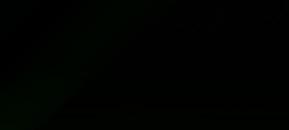
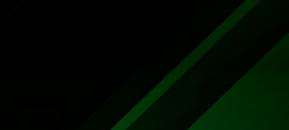
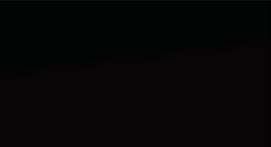
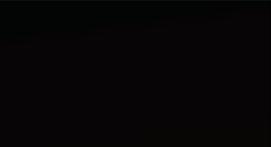
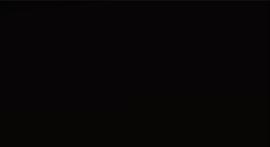

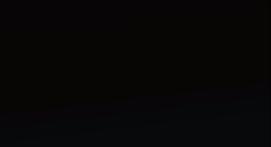
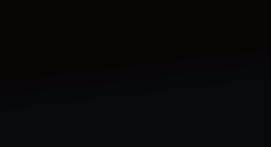
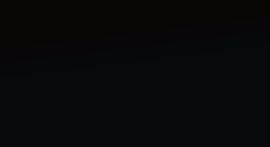
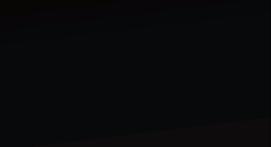

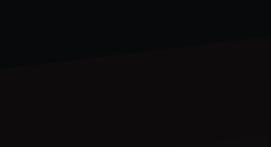
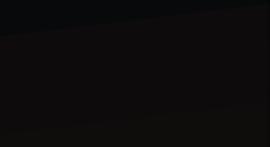

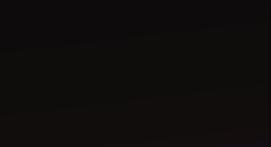
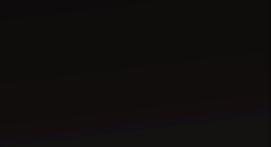
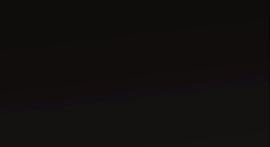
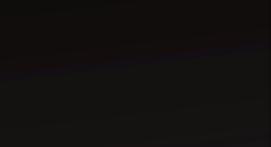
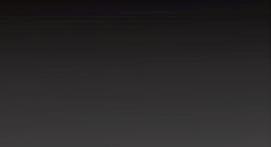
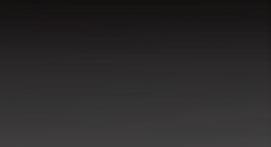
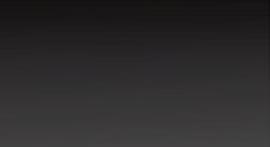
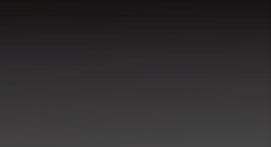

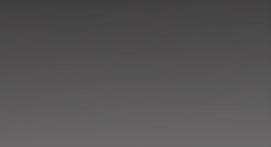
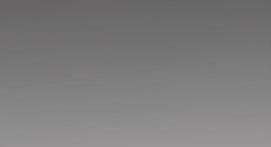
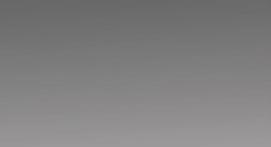
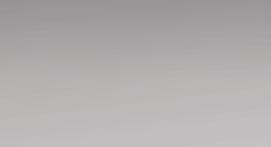
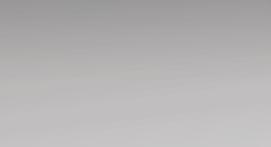
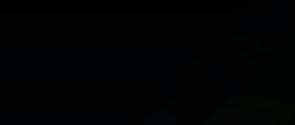

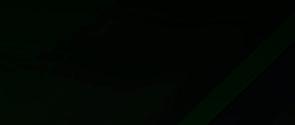
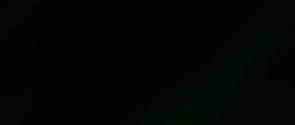
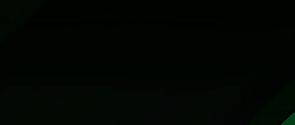
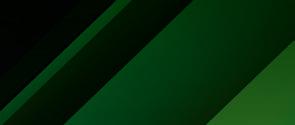
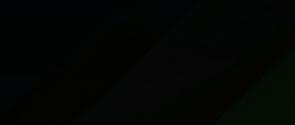
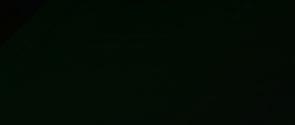
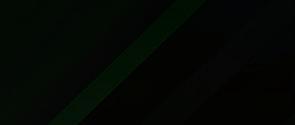
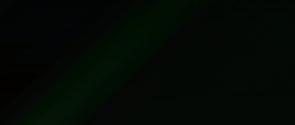
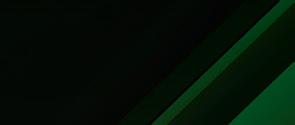
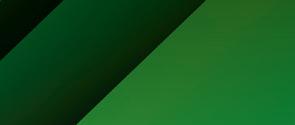
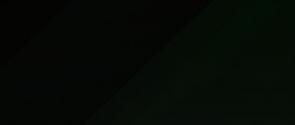


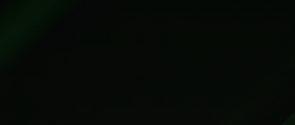
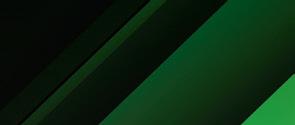
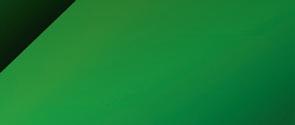
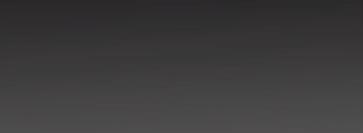
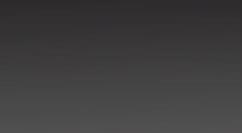


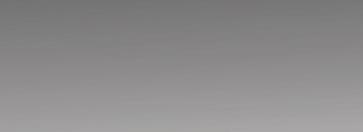
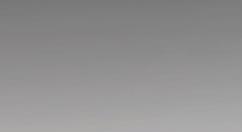


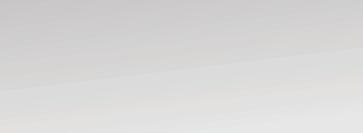
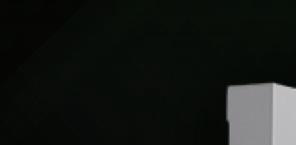
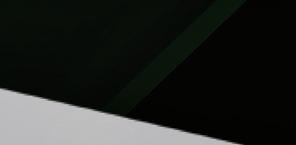
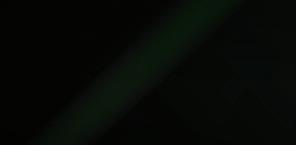
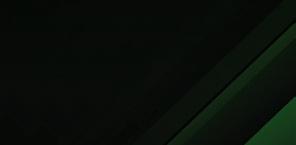
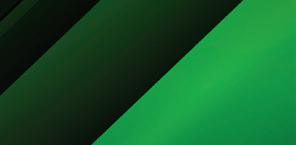
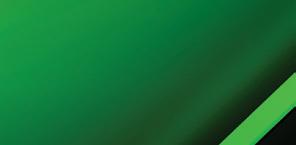
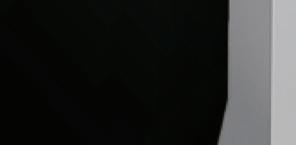
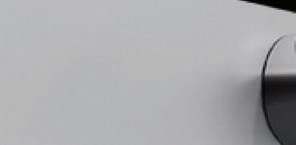
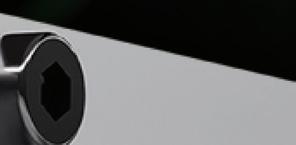
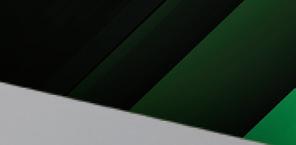
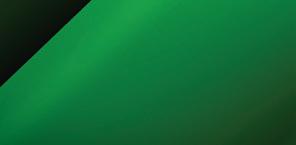
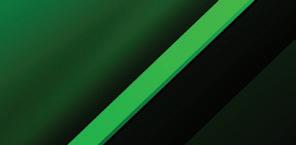
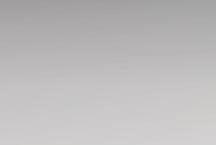
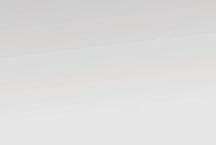
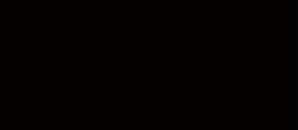
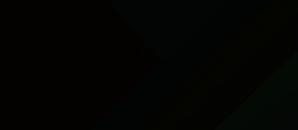
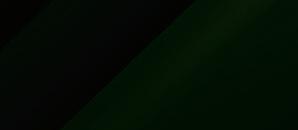
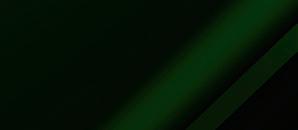
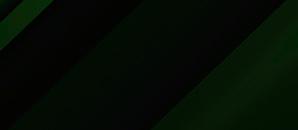

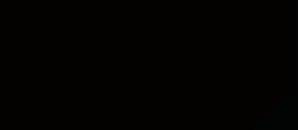


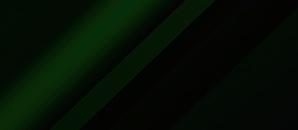
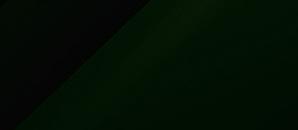
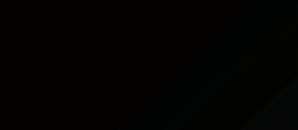
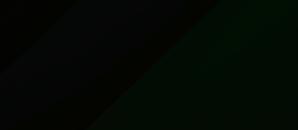
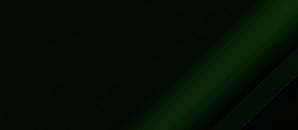

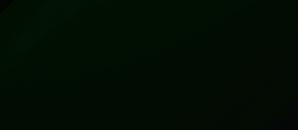
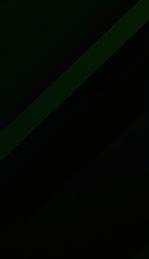

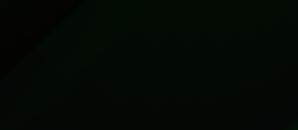
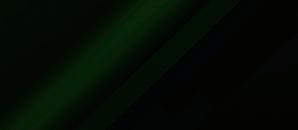
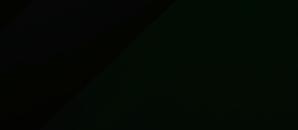
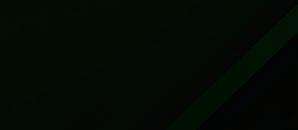
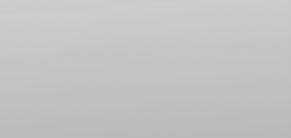

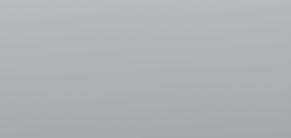
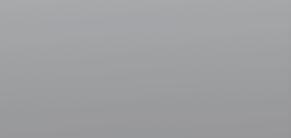
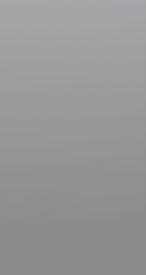
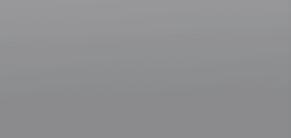
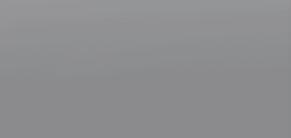

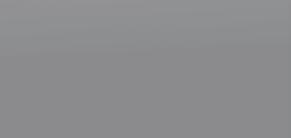
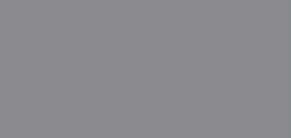
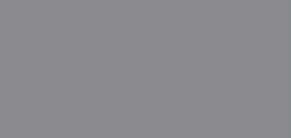
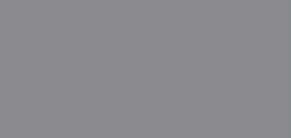
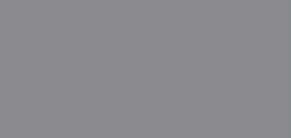
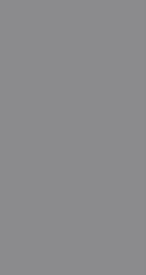
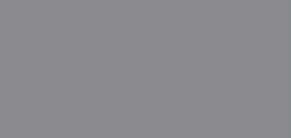
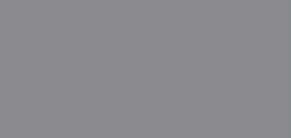
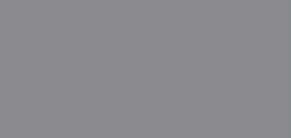
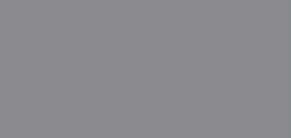
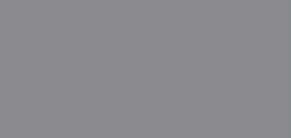
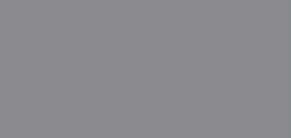
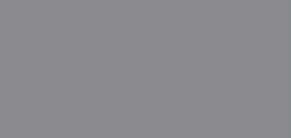
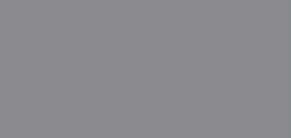
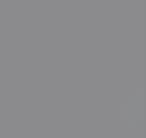
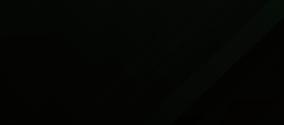
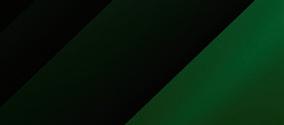
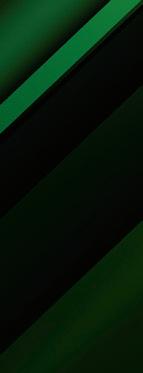
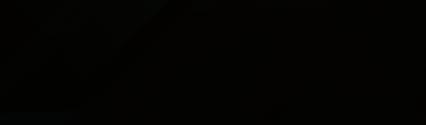
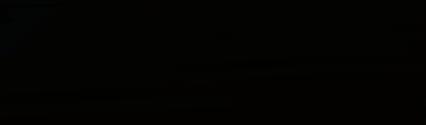
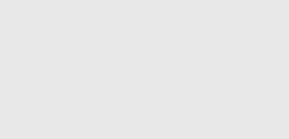
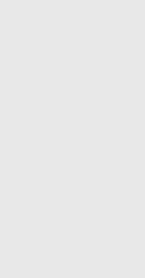
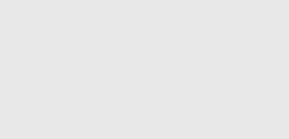
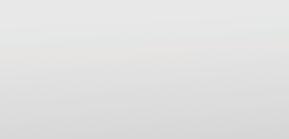
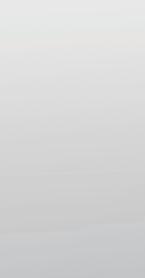
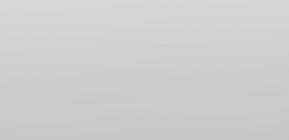
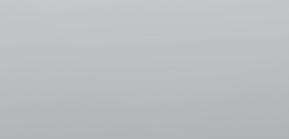
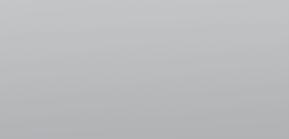
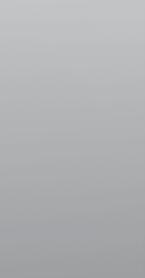
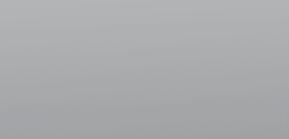

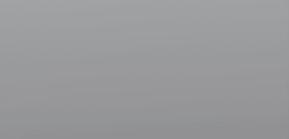
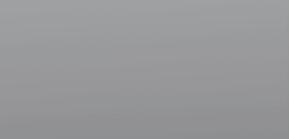
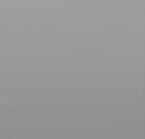
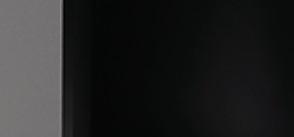
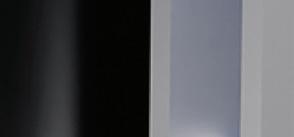
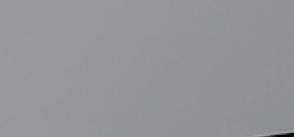
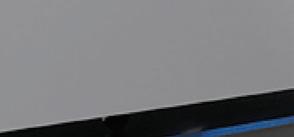
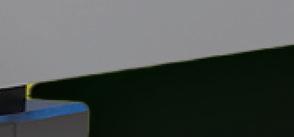
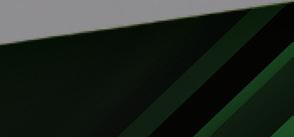
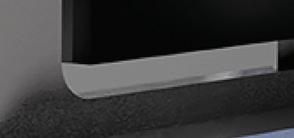

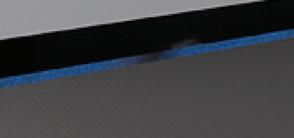
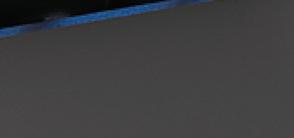
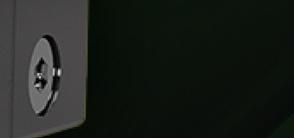
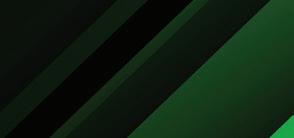
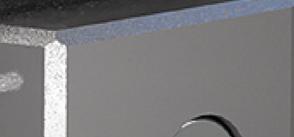
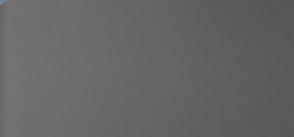
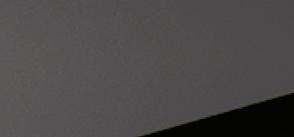
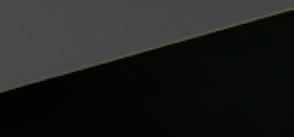
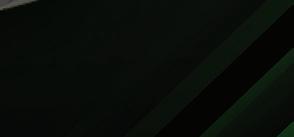
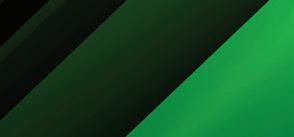
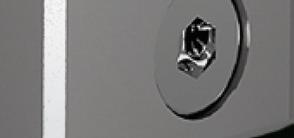
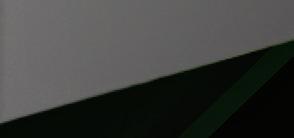
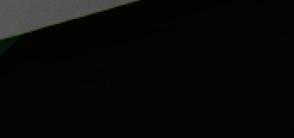
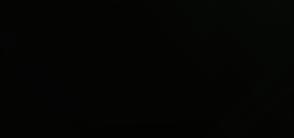
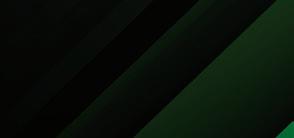
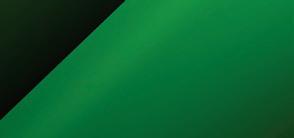
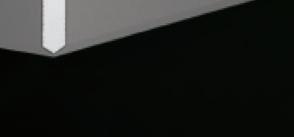
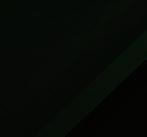

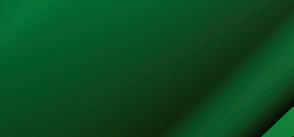
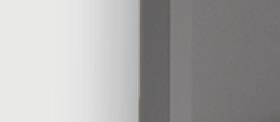
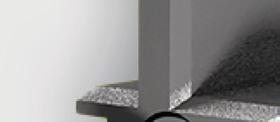
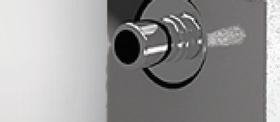
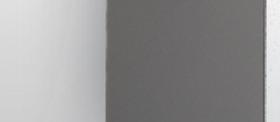
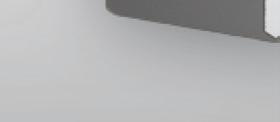
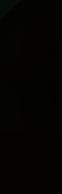
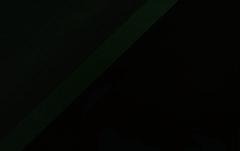

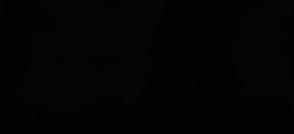
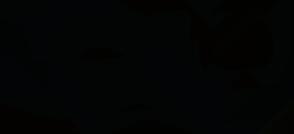
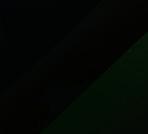

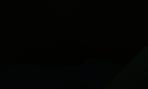
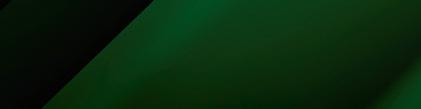
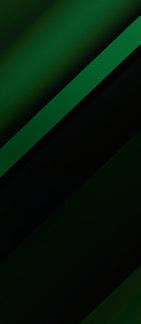
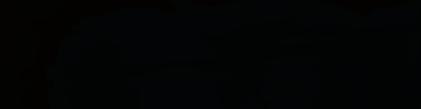
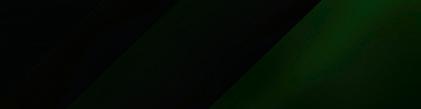
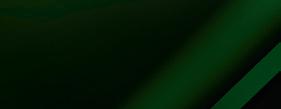
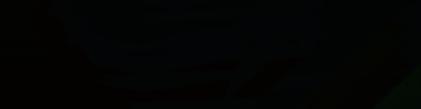
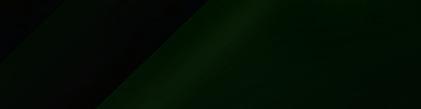
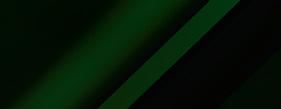
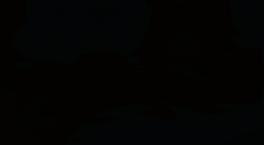
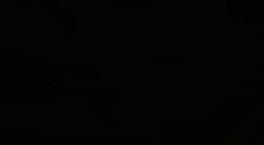
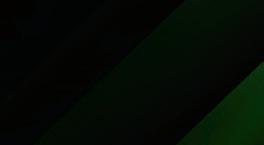


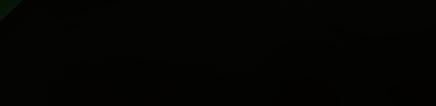
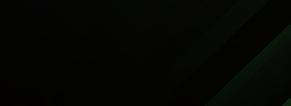
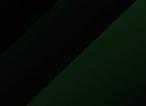
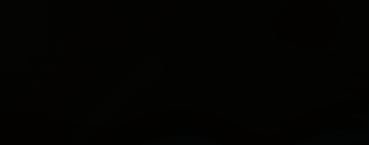
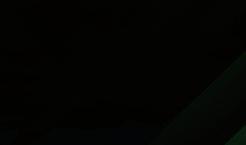


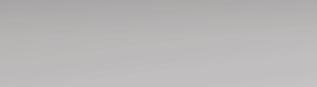


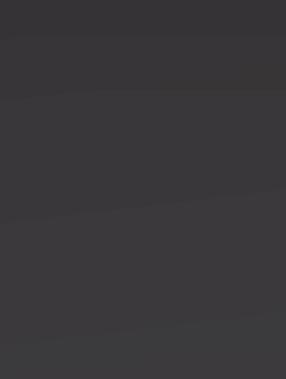
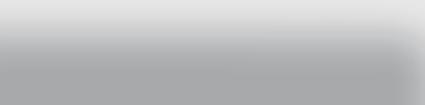

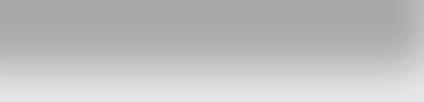
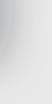
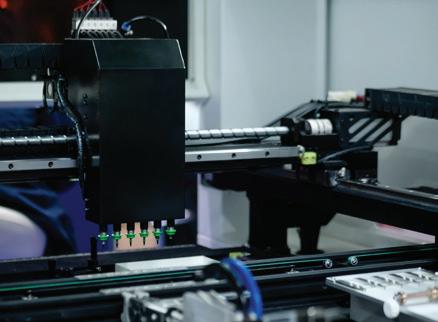
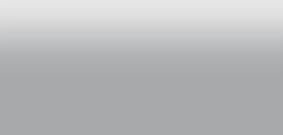


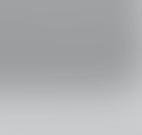

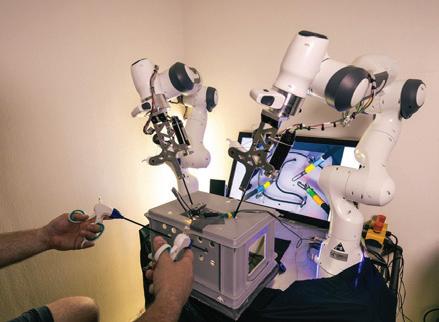
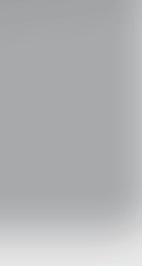
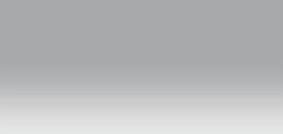

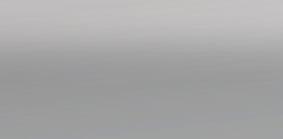

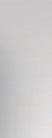
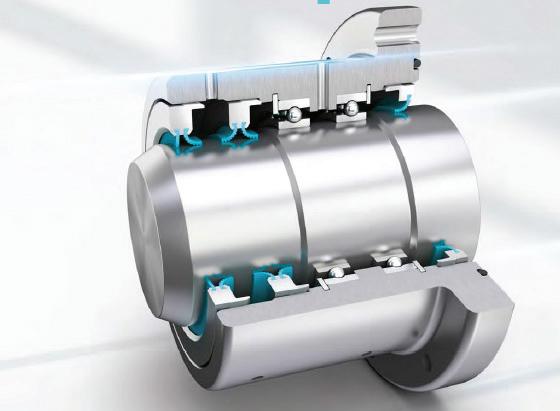



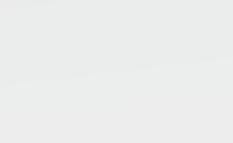
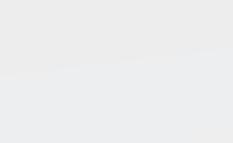
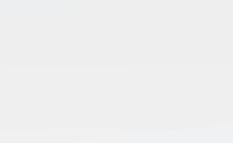
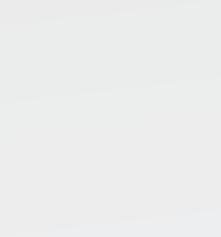
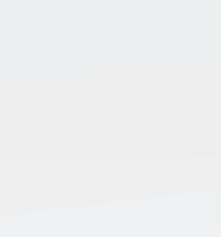

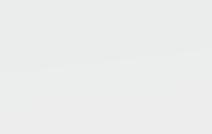

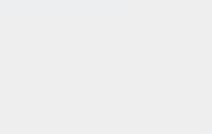

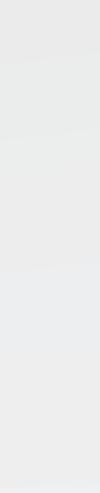
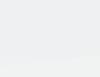
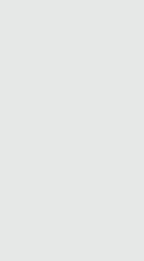
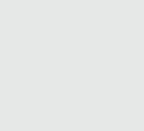
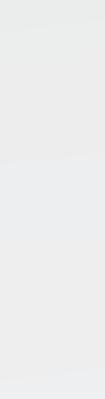
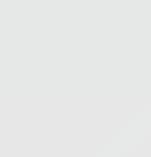
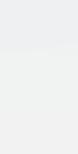
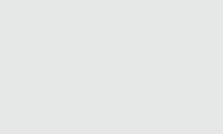
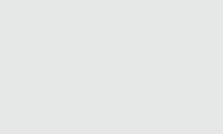
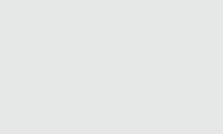
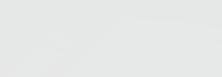
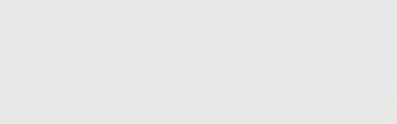
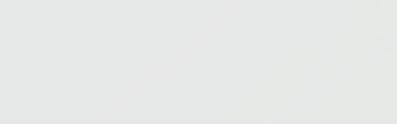
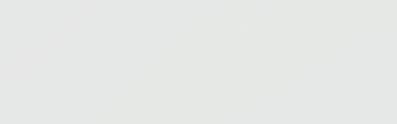

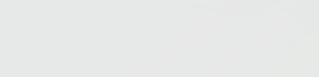
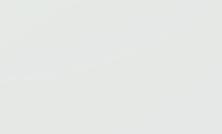
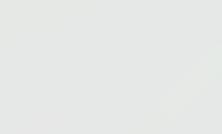

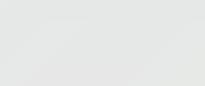
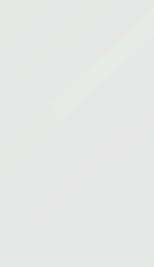


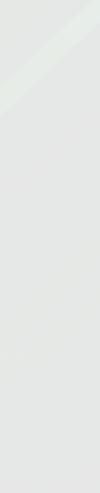
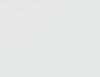
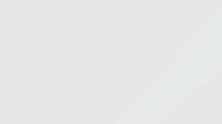
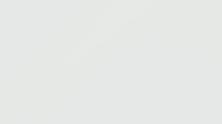
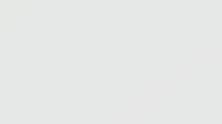
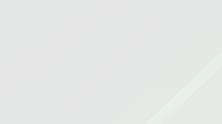
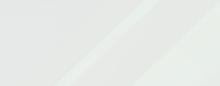
z Custom bearing molds created in days
z 70% faster fulfillment vs. other manufacturers
z Single source: from design to final product
z Maintenance-free and corrosion-resistant
z Calculate accurate service life
z Use our online tool to input your specifications
z Choose from 20+ iglide® materials & 7 geometries
z Compare production methods & pricing instantly
z Download drawings & 3D models of your part
z Components shipped to you in two weeks
We’ve added Stahlin to our line of quality non-metallic enclosures to make it even easier to find the perfect solution for your application. Our new additions include:
• Various series of fiberglass and PVC wall-mounted enclosures ideal for applications where floor space is limited, in a range of sizes, NEMA ratings; additional features such as windows, latches, and door configurations
• Pushbutton enclosures with various in-line and multi-hole configurations, and NEMA rating options
• Miniature fiberglass cases with flush fitting covers, low-profile design, shallow depth, in various NEMA ratings
• Enclosure accessories such as locks, latches, subpanels, vents and more
• 6 Nut Shapes
• 16 Shaft Diameters (4 – 100mm)
• Custom Modi cations Twice As Fast
• 10X Load Capacity*
• Longer Travel Life*
• Nut and Shaft Available in Stainless Steel
No backlash because precisely ground (not drawn) raceways conform to shape of ball in nut and shaft so opposing raceways have same angles of contact.
Wiper Seal.
Anti-rotation torque transmission. Spline shaft is straighter than competitions’ – eliminating rotational vibration.
Greater ball contact in nut permits compact single shaft applications.*
All ball tracks are in contact with racewaysonly half of competitions’ are in contact in any one direction.
The new DiaForce diagonal compact fans.
The revolutionary fan concept combines the advantages of axial and centrifugal fans:
– Up to 50% more air performance
– Up to 6 dB(A) lower sound levels
–Ideal for cooling-intensive IT applications
–Optionally with integrated FanCheck diagnostic tool for calculating the specific remaining service life
More information for your application: ebmpapst.com/diaforce
The National Fluid Power Association’s annual International Economic Outlook Conference, held recently in Chicago, provided an overview of the current economic landscape, exploring both U.S. and global macro trends and the ramifications for fluid power and motion control manufacturers. Here’s a breakdown of some of the main ideas:
• U.S. dominance: With a quarter of the global GDP, the U.S. remains the world’s largest economy. Reshoring and onshoring trends have further catapulted the U.S. to become the second-largest manufacturing country.
• China is stagnating: China, once an epicenter for double-digit growth, is facing some unprecedented challenges. Population decline and companies departing its shores hint at tough times for the Asian superpower.
• Concern about the 2030s: A decrease in population and unfavorable demographic trends in many developed nations will invariably lead to a decrease in demand, setting the stage for a depression-like recession in the 2030s.
• Supply chain moderation: Supply chain pressures, a notable concern for manufacturers, appear to be stabilizing, setting the stage for an economic comeback.
• Tight labor markets: The aging U.S. demographic, combined with diminishing immigration, signifies a labor crunch. For companies, the challenge will be attracting and training the workforce while nurturing the next generation of leadership.
• Financial forecasts: Despite inflation waning and an expectation that the Fed will halt interest rate hikes soon, concerns about regional banking instabilities remain.
On the brighter side, 2025 promises opportunities for organic growth for businesses that strategically invest in the next couple of years.
Sean Metcalfe of Oxford Economics highlighted some key drivers in global manufacturing:
• Inflation and demand: High inflation rates, combined with squeezed household budgets, are redirecting consumer demand from goods to services.
• Renewables: By 2050, renewables will constitute a whopping 65% of the global power mix, marking a significant shift in global energy production.
• Emission targets: Despite the rise of renewables, achieving net-zero emissions by 2050 appears unlikely, hinting at a potential 2° C global warming.
The road ahead
Jim Meil of ACT Research Co. provided a forecast that paints a picture of an economy that’s okay but not great. The good news? He feels we are not headed for a recession for multiple reasons: the jobs market supported solid consumer spending, energy prices fell from 2022 peak levels, businesses and households could cope with higher interest rates, and the Russia-Ukraine war settled into a relative stalemate. In addition, manufacturing did not have any sort of cli -event spiral-down; the regional banking “crisis” was contained with quick fixes, asset prices held up, housing prices mostly rose, and while stocks strayed into bear levels, they have rebounded.
According to Meil, despite showing some signs of weakness, the manufacturing economy is poised for a positive turnaround by the end of 2023 and into 2024. DW
Is it just me, or do the things you buy today break down sooner than they did in the past? In other words, do things just not last very long anymore?
The “things” I’m talking about are the products that we use in our homes — washing machines and dryers, refrigerators and TVs, even our cars and the numerous electronic devices we own these days.
In an admittedly unscientific survey (that is, my own experiences and those of family and friends), there sure seems to be some confirmation of this. Case in point: washing machines.
In the case of my brother’s family, they’ve owned a washing machine, one of the top American brands in the industry, for more than seven years. Over that period, they’ve had a total of four service calls that they’ve had to schedule. Wisely, they opted for the five-year service plan at the time of purchase, which covered any parts and labor for repairs. And it’s a good thing they did, because the washing machine needed a number of repairs including a few PC board replacements, an internal hose that was leaking, and a water sensor. Turns out buying the warranty was a good investment that ended up saving them a lot of money.
Their washing machine was neither the cheapest on the market, nor was it the top-of-the-line model, but somewhere in the middle and closer to the higher end o erings. The most expensive ones even had a WiFi connection, which they passed on.
I can’t help but contrast this with my 20+ year old washing machine, which in all that time has needed exactly one repair; a mechanical part that went bad (as mechanical parts do), and that was it. Mine is also an iconic American brand but on the lower end of the price scale. It also has exactly three knobs on the front panel and from what I can tell few, if any, electronic systems or parts.
Lest you think that this is just another instance of an old man ranting, younger people are taking notice too. For instance, Vox editor Izzie Ramirez spells out her findings about product quality in an article titled “Your stu is actually worse now.” She does some digging to find out why a bra she bought recently degraded significantly after only a few washes, while one she’d owned previously had lasted for 10 years. She finds that the dip in quality is due largely to the use of lower quality materials in order to cut production costs. So as material and other costs have increased over the last decade, consumer expectation is to pay roughly the same that they paid in years past. But to keep that same price-point requires using lower-cost materials, which are usually lower quality than the original. Hence, a clear indicator as to why clothing does not last as long as it once did.
Some of this can be attributed to materials, but in other cases it may have to do with the design itself. That is, as product designs add more functions and features and correspondingly more electronic circuits and computers are added into the mix, the likelihood of some kind of failure goes up. With added complexity come more points of failure so that even a small bug becomes something that requires an expert to repair.
But all of this may also illustrate that old engineering truism that a product can be good, cheap, or fast, but you can only ever have two of the three. Which may just mean that manufacturers have sacrificed the “good” at the altar of the cheap and manufactured quickly. DW
CONTROLLERS
In this new Tech Toolbox, the editors of Design
World detail how PLCs came to replace relay-based controls as well as which PLC logic and memory board arrangements are most common today.
DOWNLOAD NOW TO LEARN MORE!
designworldonline.tradepub.com/ free/w_defa4847/
EDITORIAL
VP, Editorial Director
Paul J. Heney pheney@wtwhmedia.com @wtwh_paulheney
Managing Editor
Mike Santora msantora@wtwhmedia.com @dw_mikesantora
Executive Editor
Lisa Eitel leitel@wtwhmedia.com @dw_lisaeitel
Senior Editor
Miles Budimir mbudimir@wtwhmedia.com @dw_motion
Senior Editor
Mary Gannon mgannon@wtwhmedia.com @dw_marygannon
Senior Editor
Rachael Pasini rpasini@wtwhmedia.com @WTWH_Rachael
Associate Editor
Heather Hall hhall@wtwhmedia.com @wtwh_heathhall
CREATIVE SERVICES
VP, Creative Services
Mark Rook mrook@wtwhmedia.com @wtwh_graphics
Senior Art Director
Matthew Claney mclaney@wtwhmedia.com @wtwh_designer
Allison Washko awashko@wtwhmedia.com
Senior Graphic Designer Mariel Evans mevans@wtwhmedia.com @wtwh_mariel
Graphic Designer
Shannon Pipik spipik@wtwhmedia.com
@wtwh_shannon
Director, Audience Development
Bruce Sprague bsprague@wtwhmedia.com
WEB DEV / DIGITAL OPERATIONS
Web Development Manager B. David Miyares dmiyares@wtwhmedia.com @wtwh_webdave
Senior Digital Media Manager Patrick Curran pcurran@wtwhmedia.com @wtwhseopatrick
Front End Developer Melissa Annand mannand@wtwhmedia.com
Software Engineer David Bozentka dbozentka@wtwhmedia.com
DIGITAL MARKETING
VP, Digital Marketing Virginia Goulding vgoulding@wtwhmedia.com @wtwh_virginia
Digital Marketing Manager Taylor Meade tmeade@wtwhmedia.com @WTWH_Taylor
Digital Marketing Coordinator Meagan Konvalin mkonvalin@wtwhmedia.com
Digital Marketing Coordinator Francesca Barrett fbarrett@wtwhmedia.com
Webinar Coordinator Emira Wininger ewininger@wtwhmedia.com
Webinar Coordinator Dan Santarelli dsantarelli@wtwhmedia.com
FINANCE
Controller Brian Korsberg bkorsberg@wtwhmedia.com
Accounts Receivable Specialist
Jamila Milton jmilton@wtwhmedia.com
EVENTS
Events Manager
Jen Osborne josborne@wtwhmedia.com @wtwh_jen
Events Manager
Brittany Belko bbelko@wtwhmedia.com
Event Marketing Specialist
Olivia Zemanek ozemanek@wtwhmedia.com
VIDEO SERVICES
Videographer
Garrett McCafferty gmccafferty@wtwhmedia.com
Videographer
Kara Singleton ksingleton@wtwhmedia.com
PRODUCTION SERVICES
Customer Service Manager Stephanie Hulett shulett@wtwhmedia.com
Customer Service Representative Tracy Powers tpowers@wtwhmedia.com
Customer Service Representative
JoAnn Martin jmartin@wtwhmedia.com
Customer Service Representative
Renee Massey-Linston renee@wtwhmedia.com
Customer Service Representative Trinidy Longgood tlonggood@wtwhmedia.com
Digital Production Manager Reggie Hall rhall@wtwhmedia.com
Digital Production Specialist
Nicole Johnson njohnson@wtwhmedia.com
Digital Design Manager Samantha King sking@wtwhmedia.com
Marketing Graphic Designer Hannah Bragg hbragg@wtwhmedia.com
Digital Production Specialist
Elise Ondak eondak@wtwhmedia.com
HUMAN RESOURCES
Vice President of Human Resources
Edith Tarter etarter@wtwhmedia.com
The global market demand for innovative, simplified, and safe medical devices is growing at a rapid pace. There is a critical need to apply proven design methodologies that increase the likelihood of meeting or exceeding regulators’ expectations to smooth the path to market launch. One of the best ways to become that “early bird” is to reinvent an older, nearly forgotten tool in the human factors engineering and usability engineering (HFE/UE) toolbox — proactive usability heuristics.
Incorporating HFE/UE processes during medical device development greatly increases the chances that devices will be safe and e ective for intended users in the intended use environments and meet regulatory expectations and requirements.
The HFE/UE process is frequently viewed as a “check-box activity” rather than a foundational component of design and development. When HFE/UE is only considered an exercise during the last steps in the design process to meet regulatory requirements, final human factors validation risks exposing serious usability and safety issues requiring expensive redesign. These issues delay launches, impact the bottom line, and potentially give competition the upper hand in market acceptance.
However, when HFE/UE is prioritized and included at the very beginning of and throughout a project’s design and development, it becomes significantly more likely for a design to achieve
accolades like “intuitive design,” “easy to use,” or “safe and e ective,” and to establish the very foundations from which great design is born. Furthermore, it helps design engineers develop appropriate solutions earlier and incorporate risk control measures. The FDA communicates its expectations that manufacturers demonstrate safe and e ective use by providing a clear link between HFE/ UE and risk management activities. OEMs are responsible for defining and incorporating users, use environments, and use-related hazards into design and development plans and for usability evaluations. Then, human factors practitioners and design engineers can apply usability heuristics to generate risk control measures for the design. The heuristics cited in the
international HFE/UE standard, ANSI/ AAMI/IEC 62366-1:2015+AMD1:2020, are universally accepted as an e cient, low-cost method for evaluating features related to user and patient safety. DW
www.blackhagendesign.com
WANT MORE?
Read more in-depth guidance by visiting designworldonline. com and searching for BlackHagän or by scanning the QR code.
Governments worldwide expect every industry, including semiconductor, aerospace, automotive, and biopharmaceutical, to reduce greenhouse gas emissions and increase energy savings. Subsequently, net-zero targets and e ciency gains drive OEMs to switch from hydraulic to electric motors as greener solutions and for improved product performance.
Electric motors require specific sealing solutions to manage friction and heat generation. The seals must protect
the motor by keeping oil and grease on the rotating shaft and preventing dust and dirt ingress. Seals must also reduce power loss across the system so less energy is consumed. Friction from the bearings and sealing arrangement a ects power loss, so balancing sealing capabilities with minimal friction is challenging.
Currently, there are five International E ciency class ratings, IE1 to IE5, with each level reducing energy loss in motor operation by 10 to 20%. Governments
do not require e ciency higher than IE3, so an IE5 rating is a strong di erentiator. High-performance rotary seals can help OEMs achieve an IE5 rating due to their low-friction qualities, which reduce power loss.
Elastomer radial lip seals are traditionally used in wet-lubricated systems because they have excellent sealing performance and easy installation. However, they struggle with increased rotary speeds, reduced lubrication, or dry-running conditions.
Elastomer seals also create greater friction, resulting in high power loss. Polytetrafluoroethylene (PTFE) rotary lip seals are an excellent alternative that suit the demands of electric motors and high-speed, critical environments. PTFE benefits include:
• Withstanding high speeds of up to 100 m/s
• Extremely low friction performance compared to elastomer radial lip seals
• Operating temperature range from -148° to 500° F (-100 to 260° C)
• Can run dry
• Compatible with most lubricants
• Inert to most chemicals
• Low break-out force and no stick-slip
• High wear resistance
Turn your design challenges into next-generation, marketleading medical devices with our extensive manufacturing capabilities and engineering expertise. We have facilities in Fremont, CA and Santa Ana Sonora Mexico.
PTFE rotary lip seals are proven in applications for leading technologies, such as aerospace and semiconductor manufacturing. Trelleborg’s HighSpin PDR rotary seal has a mechanically retained PTFE sealing element and a precision-manufactured metal body. Its low friction and power consumption contribute to energy savings in demanding environments. DW
Trelleborg Sealing Solutions
www.trelleborg.com/en/seals
Connect and discuss this and other engineering design issues with thousands of professionals online
At higher voltages (48 to 1,800 V), a properly selected contactor can mean the di erence between catastrophic failure and success. Proper system design reduces the risk of a relay erupting, starting a fire, and disabling a critical function. Understanding how to choose high-voltage dc relays can help keep o -highway vehicle designs safe and e cient. When selecting high-voltage relays for EV applications, engineers should consider the following:
1. Levitation
Levitation can occur during an overcurrent condition when the magnetic field created by the current is so strong that it pushes the moving contact away from the stationary contact, creating arcing and chattering. This unsafe event is a consequence of current beyond the relay specification and may damage the relay to the point of catastrophic failure. Instead of a standard fuse, a pyrotechnic safety module (PSM) can be a better option.
WHITTET-HIGGINS manufactures quality oriented, stocks abundantly and delivers quickly the best quality and largest array of adjustable, heavy thrust bearing, and torque load carrying retaining devices for bearing, power transmission and other industrial assemblies; and specialized tools for their careful assembly.
We
« Abuse Resistant Belts work where others fail.
« Super Strong Joints are virtually unbreakable.
« High Tension Belts move heavier loads.
« HEHT black belts double capacity.
« Low cost, highly efficient, elastic flat belts.
Split Line-shaft Spools
l High precision. Reasonable price.
l Easy to install. Zero downtime.
Dura-Belt
800-770-2358
Better
Because of the higher cost, PSMs are usually limited to protecting the main battery disconnect.
2. Circuit protection
Circuit protection coordinated with a relay balances nuisance tripping and excessive contact arcing. In some high-voltage applications, a typical 4- to 5-msec di erential might not be fast enough. Engineers should obtain relevant data from suppliers to coordinate circuit protection with the relay. Also, the relay and fuse combination should be tested to verify strong protection without nuisance tripping.
3. Make/break chart
614-777-0295
Fax: 614-777-9448 www.durabelt.com
Engineers can reduce cost and size by specifying a relay with a lower nominal or continuous rating if the relay will experience a higher-than-rating voltage only rarely. This is the case if the relay doesn’t open or close with a load on it or the vehicle is usually shut down before the relay is opened. While the maximum voltage rating is the ceiling, designers can trade voltage ratings for duty cycles. To help make this decision, consult the manufacturer’s make/break chart, which shows the number of make/break cycles a relay will perform at each voltage and current combination.
4. Polarization
Hook-and-Loop
Tape Holder for Secure Cable Routing
Polarization significantly improves the make/break capability and cycle life, giving polarized contactors double the cycle life of nonpolarized contactors in high-voltage applications. Because they are designed to work with current flowing from the positive input to a negative output, if the polarized relay opens on a circuit with the current reversed, cycle life is significantly reduced. Therefore, a non-polarized contactor is appropriate in applications where the current flows frequently in the reverse direction. Nevertheless, a polarized dc contactor is usually the better choice for EV applications greater than 350 V.
5. Monostable relays
A monostable relay automatically opens when the power is removed. Any other relay style in most high-voltage dc applications is a greater safety risk. Electronic coils, such as dual coils and pulse width modulated coils, reduce the power draw of the safer monostable coils.
Littelfuse www.littelfuse.com
Read more in-depth guidance by visiting designworldonline. com and searching for Littelfuse or by scanning the QR code.
Mobile machines have nonvisible areas known as “blind spots.” Solutions that extend the field of vision traditionally involve rear-view or wing mirrors but can’t cover all hard-to-see areas. Therefore, assistance systems for collision avoidance are increasingly used to prevent accidents with people and damage to the vehicle.
To suit the new system architectures of mobile machines and meet new requirements for “field of vision enhancement,” HYDAC is expanding its extensive sensor range with the digital Ethernet camera HVT 1000. With a range of fields of vision, the camera digitizes the field of view internally, and the lenses are optimized for the increased demands on machines.
The camera resolution and frame rate are limited by the technical capabilities of the display device, and an excessive amount of data from the camera leads to a higher, avoidable processing load in the HMI. Therefore, the amount of data generated is adapted to suit the display and the application. High contrasts, such as backlight, especially lead to problems. For this scenario, the HVT 1000 has a sensor with an HDR mode that takes a series of images with di erent exposures and combines them into one image. This
enables detailed images even in poor light conditions.
To simplify installation or replacement, the HVT 1000 is equipped with two through holes that allow mounting with M6 screws. It also has special protective circuits to work with di erent supply voltages or withstand electrical disturbances on mobile machines.
Ethernet switches can extend the system with additional components to form a network. Even complex control commands can be sent from the display to the camera. Automatic functions can be switched on and o or controlled externally by command. For example, a central control unit can merge several images into one homogeneous top-view image and overlay information from other sensors connected to the HMI.
With several HVT 1000 cameras and ultrasonic and radar sensors, operators can achieve complete 360° environment monitoring around the machine and be aware of potential obstacles. DW
HYDAC | www.hydac.com
With Interpower® having returned to its 1-week lead-times, you won’t experience anxiety from missing the cords you’ve come to love, or always wanted to try.
Interpower 1-week lead-times began in 2008—our cords, cord sets, and components ship straight from the factory. Want them hanked, coiled, tied, bagged and individually boxed? Need 1-D or QR barcodes for easier warehousing? Customize lengths and colors for country-specific cords. And, as always, our cords ship the same day if in stock.
The art of filmmaking and the making of television shows have certainly changed over the years. Gone are the days of rudimentary special e ects, poor lighting, and recording sound e ects on a single track. People watching the cinematic universe today want quality and practical sound recording and high-resolution visuals that transport you away from reality. One company that helps do this is Cannibal Industries. Under the guidance of owner and president Eric Ballew, Cannibal specializes in the manufacture of film and television equipment mobility, particularly in sound recording.
As industrial automation technology grows, the location sound recording industry is attempting to keep pace. Currently, the over-the-shelf power solutions for mobile sound rigs use electrical components that, by today’s standards, would be considered outdated or close to becoming discontinued. To bring these rigs up-to-date, companies like Cannibal look at specific parts to upgrade they can handle the rigors of location sound recording. They have specified four main parts to target for reaching this goal — the Switch Mode Power or AC/DC converter, uninterruptible power supplies, current limiting, and overload protection.
According to Ballew, resonant mode power supplies generate far less electromagnetic interference than their switch mode counterparts, making them a great solution for high-fidelity audio applications.
The main goal of Cannibal was to find a circuit protection solution that could handle the universal current of 12 VDC. To do this, Ballew reached out to WAGO’s customer service team. This prompted Drew Amos, WAGO’s Regional Sales Manager in the area, to contact Cannibal.
The discussion led to Cannibal’s frustration that the server racks they built would not function properly due to the load and heat of products working near each other. “Eric understood that the way these racks were being put together were a hazard,” he said, “and it was costing Cannibal valuable time and money.” The idea was to create an industrial rack capable of handling harsh conditions during location filmmaking. By doing so, Cannibal looked to develop a standardized rig that the location sound recording industry could look to as the model of what could be accomplished.
That search landed Ballew and his team on WAGO’s Electronic Interface product line, particularly their Electronic Circuit Breakers. Understanding the power, space, and number of channel requirements needed, WAGO was able to help direct them to the appropriate product for this application. For Cannibal, the 4-channel variable current breaker for 12 VDC systems was a perfect fit.
Upon the arrival of the first unit, Cannibal immediately began to test the equipment to see if it could handle the rigors of location-based sound recording. Their tests were simple. They provided the unit 15 VDC and then connected three separate dedicated sound recorders to three of the four outputs. The remaining open channel was repeatedly dead shorted to measure both the voltage drop on the main bus, recovery time, and, most importantly, if the sound recorders could continue their operation during a catastrophic event.
They consistently saw a reaction to recovery time of 3.5ms, with the main
WAGO’s rugged Electronic Circuit Breakers ensure Cannibal’s recording rig remains operational through all hazards.
bus voltage never dropping below 80% of the input voltage during the event. The two main sound recorders ran through this test consistently and with no detectible audio artifacts that a catastrophic event had occurred. Unlike the currently available over-the-shelf solutions, this type of event would result in the power supply having to be shut down for other components to cool and reset. When this happens, reaction time is much slower, which can result in corrupted data because the sound recorders cannot stop and save their data.
In the location sound industry and especially in Los Angeles, Ballew said that Cannibal has built a reputation of "uncompromising reliability." They ultimately consider it their “religion.” It was clear that the quality and grade of components available from WAGO met and exceeded what is considered the qualifications needed to earn the moniker "Uncompromisingly dependable."
WAGO | wago.com
Ease your mind with 1-week lead-times on power cords and cord sets. Customers can even lock in prices and have their North American and international power cord sets shipped on predetermined schedules throughout one calendar year—cords when and where you need them.
Interpower cord sets ship straight from the factory. Want them hanked, coiled, tied, bagged and individually boxed? Need 1-D or QR barcodes for easier warehousing? Customize lengths, colors, packaging and labeling for country-specific cords. In-stock cords ship the same day.
Choosing the right gasket material is a critical decision. The first step in material selection is understanding how and where the gasket will be used. Does it need to seal against liquid or gas? Protect electrical equipment against EMI/ RFI? Will it be exposed to the elements?
The most common reason for gaskets to fail or underperform is environment. This includes all the conditions and substances a gasket might be exposed to. Temperature is perhaps the most important factor, as it can change the properties of certain materials. Temperatures above the operating range of a material will cause severe performance degradation over time, while cold temperatures below the operating range may cause some materials to contract, become brittle,
and fracture. This is why it’s crucial to follow the recommended temperature range for whatever material you choose. Exposing the gasket to conditions outside that range — even for a short time — can cause failure. Other environmental factors include exposure to weather, UV light, moisture, solvents, and chemicals.
Many di erent types of materials can be used in gasketing applications.
Some of the most common are foam, rubber, vulcanized fibers, non-asbestos material, cork, plastic, and even metal. Foam and rubber are the two most used gasket materials, largely because of their compressibility, resilience, shock resistance, and easy fabrication into complex shapes. Unlike metal, composite,
or plastic gaskets, foam and rubber can be compressed to fit rough and uneven surfaces, creating a tighter seal. Both materials are used across manufacturers and industries due to their versatility, utility, and ability to be converted to the exact part specifications required.
Open cell foams, as their name implies, have a porous cell structure. Inflating agents, which outgas in the manufacturing process, create interlocking open pores that make up the foam structure. These foams are highly compressible and resilient, allowing more absorption and permeation of gas, vapor, and water. They are suitable for cushioning, insulating, and filtration in applications not exposed to the elements.
There are many di erent types of open cell foam products available. The most common can be divided into two primary categories: low-density polyurethane and high-density micro-cellular polyurethane. Low-density polyurethane foams are more suited to filtration applications because of their breathability. They are suitable as door gaskets, helping to cut down on light, sound, and air infiltration. Highdensity polyurethane foam is ideal for sealing, sound dampening, and vibration mitigation, and insulation. Silicone foam and melamine foams are some other common open cell foam products.
Closed cell foams, on the other hand, have an internal cell structure that remains unconnected within the material because the gas bubbles of the inflating agents remain trapped during the manufacturing process. These trapped bubbles allow closed cell foams to repel water and resist liquid absorption. Closed cell foams are also impervious to air, vapor, and gas. There are various closed cell foams, each with advantages and disadvantages depending on the application. Closed cell foam rubber, like neoprene, EPDM, PVC, silicone sponge, and blended products like vinyl nitrile or blended neoprenes, are widely used. Closed cell plastics foams like polyethylene, polypropylene, and Ethyl Vinyl Acetates are also very common as well. Each category comes in a wide range of compression capabilities and thicknesses.
Solid rubber gaskets
Solid rubber is a tough and durable material with high shock absorption and impact and abrasion
resistance. As an elastomer, it is conformable to surfaces. Under compression, rubber can create a tight, resilient seal that keeps out liquid and moisture. However, compared to closed cell foam gaskets, solid rubber is much less compressible, especially as durometers increase, so it’s important to pay close attention to the product and gasket design tolerances to ensure a proper seal. The hardness or durometer of solid rubber is measured on the Shore A scale. The higher the number, the harder the material.
Rubber is also a stable material and can be engineered to resist harsh environmental conditions such as acids and alkalis, oxidation, ozone and electricity, high temperatures, and flames. The most common rubber materials used are Neoprene, EPDM, Natural Rubber, Nitrile, Silicone, and SBR. To enhance production speed and simplicity, gaskets commonly come cut to the exact shape required, with pressure-sensitive adhesive on one side to a x the gasket in place or to be used as a third hand before attaching with mechanical fasteners. DW
Engineered Materials
www.engineeredmaterialsinc.com
Semiconductor manufacturing, particle physics research, and other valuable processes occur in highvacuum or ultra-high-vacuum (HV/ UHV) conditions. To help develop a better ionization gauge for measuring pressure in HV/UHV environments, instrument manufacturer INFICON of Liechtenstein used multiphysics modeling to test and refine its impressive new design. The Ion Reference Gauge 080 (IRG080), shown in Figure 1, resulted from an international project coordinated by the European Metrology Programme for Innovation and Research (EMPIR) to develop a better tool for quantifying pressure in HV/UHV environments.
“At HV/UHV pressures, there are not enough particles to force a diaphragm to move, nor are we able
to reliably measure heat transfer. This is where we use ionization to determine gas density and corresponding pressure,” said Martin Wüest, head of sensor technology at INFICON.
The most commonly used HV/UHV pressure-measuring tool is a Bayard–Alpert hot-filament ionization gauge placed inside the vacuum chamber. The heart of this instrument consists of the filament (or hot cathode), the grid, and the ion collector. Its operation starts with supplying low-voltage electric current to the filament, causing it to heat up. As the filament becomes hotter, it emits electrons that are attracted to the grid, which is supplied with higher voltage. Some electrons flowing toward and within the grid will collide with any free-floating gas molecules circulating in the vacuum chamber. Electrons that collide with gas molecules form ions that flow toward the collector. This measurable ion current in the collector will be proportional to the density of gas molecules in the chamber.
“We can then convert density to pressure, according to the ideal gas law,” Wüest said. “Pressure will be proportional to the ion current divided by the electron current, divided by a sensitivity factor that is adjusted depending on what gas is in the chamber.”
While the operational principles of these devices are sound, their calibration is too easily compromised
Figure 1. INFICON used COMSOL’s Multiphysics modeling software to design the Ion Reference Gauge 080 to measure pressure in high-vacuum or ultra-highvacuum applications.
| provided by INFICON
by routine use and handling. Along with their sensitivity to heat, the core components of a Bayard–Alpert gauge can become easily misaligned. This can introduce measurement uncertainty of 10 to 20% — an unacceptably wide range of variation.
The project team chose INFICON’s IE514 extractor-type gauge as the current best practice for ionization gauge design. Francesco Scuderi, an INFICON engineer specializing in simulation, used the COMSOL Multiphysics software to model the IE514.
“After constructing the model geometry and mesh, we set boundary conditions for our simulation,” said
Scuderi. “We are looking to express the coupled relationship of electron emissions and filament temperature, which will vary from approximately 1400 to 2000° C across the length of the filament. This variation thermionically a ects the distribution of electrons and the paths they will follow.” (Figure 2)
Next, the model was used to calculate the percentage of electrons that collide with gas particles. From there, ray tracing of the resulting ions was performed, tracing the ions’ paths toward the collector (Figure 3).
“We can then compare the quantity of circulating electrons with the number of ions and their positions. From this, we can extrapolate a value for ion current in the collector and then compute the sensitivity factor,” said Scuderi.
INFICON’s model did an impressive job of generating simulated values that closely aligned with test results from the benchmark prototype. This enabled the team to observe how changes to the modeled design a ected key metrics, including ionization energy, the paths of electrons and ions, emission and transmission current, and sensitivity.
The end product of INFICON’s design process, the IRG080, incorporates many components as existing Bayard–Alpert gauges, but key parts look quite di erent. For example, the new design’s filament is a solid suspended disc, not a thin wire. The
grid is no longer a delicate wire cage but made from stronger-formed metal parts. The collector now consists of two components: a single pin or rod that attracts ions and a solid metal ring that helps direct electron flow away from the collector and toward a Faraday cup. This arrangement, refined through ray tracing simulation, improves accuracy by better separating the paths of ions and electrons (Figure 4).
INFICON built 13 prototypes that underwent evaluation by the project consortium. Testing showed that the IRG080 achieved the goal of reducing measurement uncertainty to below 1%. Regarding sensitivity, the IRG080 performed eight times better than the benchmark.
Of course, this success was not the team’s alone. INFICON benefited from its partners’ insights and support, and in turn, the broader scientific and manufacturing community will benefit from more consistent measurements of HV/UHV conditions. DW
COMSOL | www.comsol.com
Figure3. Ray tracing
models showed the simulated paths of electrons (blue) and ions (red) in the IE514.
The CeraFab S65 3D printer is part of a partnered German Aerospace Center project paving the way for generating green hydrogen via a solarthermochemical process.
| courtesy of Lithoz
Hydrogen is pegged as “the fuel of the future,” yet it often takes fossil fuels to produce. WZR Ceramic Solutions, a German-based material development service provider in ceramic 3D printing, selected Lithoz’s CeraFab S65 System 3D printer for the visionary “Redox3D” project that will produce green hydrogen in solar tower power plants through thermochemical processes. The company will use highprecision lithography-based ceramic manufacturing (LCM) technology to construct cerium oxide components with highly complex lattice structures to achieve the much sought-after breakthrough of generating hydrogen independently from fossil energy sources. The solar-thermochemical process, using a 3D-printed ceramic
material as the key enabler and sunlight as the primary energy source, is considered one of the key solutions in making zero-emission societies a reality.
“We are confident that we will achieve the levels of complexity and intricacy in filigree structures needed to achieve our goals in this project,” said Dieter Nikolay, managing partner of WZR. “Thanks to the speed and highquality surface finish of this technique, we will once again be able to further drive innovation forward, this time with the production of green hydrogen.”
WZR will partner with the DLR (German Aerospace Center) to determine the ideal lattice structure for the optimum solar heat penetration into cerium oxide components. For this important mission, which has received
public funding from the German Federal Ministry for Economics and Climate Action (03EE5124A), WZR identified Lithoz’s industry-leading ceramic 3D printing system as a potential key technology to develop the solution, with the CeraFab S65 being their first own printer using DLP technology.
The project will commence in two phases over three years. The first phase will test and optimize di erent 3D printing techniques to precisely control and process the cerium oxide ceramic material, with the key technology then being selected. In the second phase, the optimal structures will be designed, supported by calculations of project partner DLR, and then applied to complete the project. The filigree structure produced must be extremely
complex to enable the deepest possible penetration of solar energy into the cerium oxide component, which is crucial to achieving the highest efficiency in the energy generation process.
The following describes details about the solar thermal redox chemical production of hydrogen:
As a “receiver module,” the cerium oxide assembly is heated up to 1,400 to 1,500° C (approx. 2,500 to 2,700° F). The ideal shape lattice design (to be defined between WZR and DLR) will ensure that heat penetrates the complex part’s structure as deeply as possible, making the process as efficient as possible.
Within that desired temperature window, cerium oxide releases a fraction of oxygen into the atmosphere. The resulting sesquioxide is still stable in its original phase (meaning no phase change affecting the macro-structure), but it has a higher redox chemical energy level which can now be exploited.
Therefore, the activated cerium sesquioxide receiver module is moved down inside the tower power plant and cooled down. Once it reaches a certain temperature, water vapor is introduced.
In contact with the hot surface, the vapor splits into hydrogen (H2) and oxygen (O2), thermodynamically driven by the diffusion of oxygen into the material bulk to refill the “empty oxygen sites.” H2 remains and enriches the sweeps flux.
After this relaxation, the receiver component can reenter the reduction process by heating it again — the cycle restarts from the beginning. The aim is to achieve specimen stability of several thousand redox cycles.
The resulting “green” hydrogen has therefore been exclusively generated by a redox chemical process only made possible by solar energy and a 3D-printed ceramic key component.
Due to the level of complexity and accuracy achievable via LCM, the high level of intricacy required in the structures can be produced, allowing solar energy to penetrate deeper into the parts and thus enabling a more efficient energy extraction process. The exact reproducibility of these parts is also crucial to the project’s success and is made possible with the LCM technique.
“[We are excited to be part of] such important research, especially because we consider hydrogen generated with renewable energy the number one solution to save our planet from further climate change,” said Johannes Homa, CEO of Lithoz. “Lithoz is committed to supporting such projects using the industrial standard of LCM technology to make zero emission societies a reality.” DW
Density in additively made parts refers to the porosity of a part and can be an issue with laser-sintered additive technology. Parts operating under cyclic loading must be strong (dense) enough to not fatigue or fail under load. Several additive technologies can deliver densities of 98% and higher.
However, in an additive build, usually during a laser sintering process, the layer-by-layer melting can be incomplete before subsequent layers are added. This incomplete melting results in holes, cavities, or pores. Porous areas could fail more easily than others under load. Depending on the part’s application, such failure could be minor or catastrophic.
The impact of porosity extends beyond mechanical concerns, a ecting AM components’ thermal and electrical properties and rendering them more vulnerable to high temperatures, corrosive substances, and other environmental factors. Moreover, porosity’s adverse e ects extend to the functionality of the parts in specific applications. It limits their capacity to retain liquids, gases, or other substances and influences their performance.
Dimensionics Density’s new density determination solution is poised to revolutionize the analysis of component density. With unparalleled accuracy and e ciency, it aims to identify and mitigate porosityrelated issues, bolstering AM parts’ mechanical integrity, durability, and resistance against external stressors and environmental challenges.
| courtesy of Dimensionics Density
“Our technology plays straight into the need for automation in the area of validation and quality control of AM parts, and we have launched an array of tools focused on determining AM part density,” said Philipp Pruesse, head of sales at Dimensionics Density. “For AM to continue disrupting the manufacturing paradigm, the entire AM process chain must move towards automation. Because of this, our density determination solutions are fully automated and
Dimensionics Density technology automatically measures additively manufactured part density in production.
of vital importance and are designed to be used in production settings, not just in the laboratory.”
The automatic measuring process occurs after samples are inserted into universal component carriers. The integrated measurement and control systems monitor and consider numerous environmental factors when calculating the density from the measurement data.
Accuracy is achieved by combining the time-proven Archimedean principle with the latest automation technology and laboratorystandard precision scales. The density of the test object is determined by weighing it in two di erent media. The first measurement is usually made in air, and the second is in a defined liquid medium with a known density. The crucial factor for the accuracy of the result, however, is the positioning on the scale. Deviations from the center of mass and resulting o -center measurements of the component will lead to strong variation. This is why the common manual Archimedes measurement solutions are not viewed
favorably across the industry.
“To counteract this problem and to ensure the repeatability of the measurements, Dimensionics Density o ers a universal carrier which can transport most parts and be easily adapted if necessary for more complex geometries,” said Pruesse. “The determined density is compared with the desired specifications, so qualitatively more accurate assumptions can be made about the density of complex components. With a cycle time of fewer than 2 minutes per component and the possibility of inspecting up to 18 components simultaneously in one inspection process as standard, the Dimensionics Density solution supports the optimization and e ciency of manufacturing processes.”
The density determination technology is non-destructive and, therefore, can be used to verify parts quickly, precisely, and coste ectively. DW
Dimensionics Density
dimensionics-density.com/additive
Samples are inserted into the universal component carriers, then measuring occurs automatically and accounts for environmental factors.
| courtesy of Dimensionics Density
Linear encoders are at work in a range of specific industrial applications — from supertall building elevators to machine tools and beyond.
MILES BUDIMIR • SENIOR EDITOREncoders are critical components in motion systems of all kinds. And when measuring linear position, linear encoders are among the best choices. Linear encoders monitor linear movement and provide position feedback in the form of electrical signals, with common sensing techniques including optical and magnetic technologies.
A range of di erent applications make use of linear encoders, but among the most common involve ultra-precision machining. Here, parts must be machined to singledigit or sub-micron accuracy. A host
of manufacturers o er up leadingedge linear encoders using the latest technology.
Encoders for next-gen elevators
As skyscrapers grow ever taller, elevator manufacturers are considering alternatives to the classic cabled elevator. One such approach borrows from mag-lev trains that use linear motors for propulsion. Such an approach would get rid of the cables used to move elevator cars up and down with the result being more versatile functions where multiple elevator cars that could travel in
the same elevator shaft and even horizontally between di erent shafts. For such cableless elevator designs, HEIDENHAIN o ers their LINA 200, an inductive absolute linear measuring system. The absolute position is calculated via the absolute scale which consists of two tracks with di erent signal periods. A special feature of this scale is that the two tracks are not located in one plane; instead, they face each other. The EnDat 2.2 interface then digitally transmits the position value to further control electronics. The U-shaped scale design not only makes it possible to scan the measuring
standard from both sides, but the double-walled design also protects the graduation and the scanning procedure itself from mechanical and electromagnetic influences. In addition, this type of construction provides maximum rigidity at a low weight. The U-shaped design also brings significant benefits regarding the mechanical sturdiness of the scale and the stability of the encoder signals.
The linear measuring system works like this. The graduation carrier of the LINA 200, with an overall length of 2,400 mm, is attached to the elevator cab. The scale consists of four segments, each with a measuring length of approximately 600 mm. These segments are scanned by scanning heads that are placed in the shaft in a cascading alignment, permitting continuous position measurement over the entire distance traveled. With guide tolerances of ± 5 mm and ± 4 mm, the LINA 200 achieves a small measuring step of approximately 2 µm. This means that it reliably supplies highly accurate positioning signals for the drive control
of the cable-less elevator, while at the same time o ering tolerances that are su cient for permitting a real-world mounting strategy in the elevator shaft as well as for compensating for movements of the building itself.
The LINA 200, which was designed specifically for cable-less elevators, also attains peak values regarding dynamics and passenger comfort. Initial tests showed that traveling speeds of 6 m/sec can be easily achieved, and in the laboratory the LINA 200 provided reliable position values at speeds of up to 18 m/sec. At slow speeds, as well as during acceleration after a stop and braking before a stop, the high resolution of the position values (18 bits) at a measuring length of approximately 600 mm ensures a comfortable and gentle motion.
Machine tools benefit from new linear encoders
Machine tool applications are another area where linear encoders excel. This applies to a range of machines such as milling machines, machining centers, boring machines, and lathes and grinding machines.
of up to 18 m/sec.
For example, the FORTiS enclosed encoder from Renishaw can let machine builders improve machine tool performance and increase uptime while enhancing e ciency of assembly, maintenance, and servicing. The enclosed linear absolute encoder series is designed for use in harsh environments such as machine tools and can also be used in functional safety applications up to SiL2 and PLd.
The FORTiS encoder provides high resistance to the ingress of liquids and solid debris contaminants. It features an extruded enclosure with longitudinally attached interlocking lip seals and sealed end caps. The readhead body is joined to a sealed optical unit by a blade, which travels through the DuraSeal lip seals along the length of the encoder. Linear axis movement causes the readhead and optics to traverse the encoder’s absolute scale (which is fixed to the inside of the enclosure), without mechanical contact.
The encoders also feature integrated, specially-designed tuned mass dampers that help achieve 30 g vibration resistance. The encoders are also designed for quick and easy installation, which helps save manufacturing and servicing time. Plus, in line with the growing industrial trend towards risk reduction for systems and processes, variants for all FORTiS enclosed
The DAX linear encoder family from SICK employs magnetostrictive technology and o ers absolute position feedback. They’re suitable for measuring positions in many applications, including injection molding machines, presses, printing and packaging machines, and in medical equipment, among others.
encoders are o ered with Functional Safety. Certain machinery safety functions, such as Safety Limited Speed (SLS), require the encoder position feedback to be functionally safe. Using an encoder system that is already rated for use in safetyrelated applications can make machine certification significantly easier.
Many of the most common linear encoders use a magnetic sensing technology called magnetostrictive technology. This essentially has the benefit of no moving parts so that they are wear and maintenance free. Unlike optical encoders, magnetic versions are insensitive
to contaminants such as dust, dirt, liquids, and grease, and to shocks and vibrations. Similar to optical encoders, magnetic encoders do require an air gap between the magnetic disk and the sensor. However, the air gap in a magnetic encoder does not need to be clean and transparent, as it does for an optical encoder
For instance, the DAX linear encoder series from SICK feature magnetostrictive technology. They are well suited for highprecision detection of piston positions in hydraulic cylinders and the monitoring of linear movements in machines as well as other industrial applications requiring linear measurement.
Three housing variants are available: a design for integration into industrial hydraulic cylinders, a flat type with block magnets for mounting in tight installation situations, and a version with a slide profile that guides the position magnet, ensuring a precise and repeatable position measurement. The available measuring range is between 50 and 2,500 mm and is individually configurable in 1-mm increments.
The platform concept of DAX o ers a high system flexibility, allowing applicationspecific versions to be generated e ciently and the device to be easily integrated into a variety of machines. This applies not only to the housing designs, but also the position magnets, which can be modified to suit the applicationspecific requirements. This backward compatibility guarantees more flexibility and independence when choosing the encoder and manufacturer.
For electrical installation, the DAX product family o ers a CANopen interface, so the measurement system can output position values with a resolution up to 10 µm, as well as an analog output for either 0-10 Vdc or 4-20 mA. They also feature enclosure ratings of IP65 and IP67 and a temperature range between -40 and +85 °C.
The DAX linear encoders can provide comprehensive diagnostic information via CANopen interface. The sensors monitor operating and limit temperatures,
Renishaw’s FORTiS enclosed encoder helps improve machine tool performance and increase uptime while enhancing e ciency of assembly, maintenance, and servicing. The enclosed linear absolute encoder series is designed for use in harsh environments such as machine tools and can also be used in functional safety applications up to SiL2 and PLd.
as well as the voltage supply for voltage peaks or voltage drops. It performs continuous functional checks of the position magnets, counts piston strokes, adds them to determine total displacements, and records operating hours. All this provides valuable information about the current status during operation and any upcoming maintenance work that may be required on the machine. This can be used to reduce unplanned downtimes and increase the e ciency of the system being used. DW
HEIDENHAIN | www.heidenhain.us
Renishaw | www.renishaw.com
SICK | www.sick.com
Round rail linear guides can offer the lowest overall cost of ownership, but machine designers often specify profilerail for its compactness as well as its higher rigidity, load capacity, and accuracy. Here’s how to extend the life of these linear-motion components.
engineers integrate profilerail (also called square rail) linear guides in various applications — ranging from miniature rails to guide pipettes on laboratory blood analyzers to heavyduty profile rail on large multi-axis robot systems transferring pallets in factories. Profile rails’ high rigidity also makes them suitable for CNC-machine applications and semiconductor production.
As with all linear motion components, durability is primarily a function of application-dictated speed, load, and duty cycle. Within those parameters, diligent lubrication and contamination protection are key to extending the life of profile-rail linear guides. After all, linear bearings are open — in sharp contrast with radial bearings having seals to contain lubrication and shield against contamination.
Other factors a ecting profile-rail durability include sizing, the internal component architecture, and mounting … with all choices having their own tradeo s.
About 75% of all profile rail failures result from inadequate lubrication or contamination. Like an automobile oil change, rail and bearing lubrication must happen regularly to help prevent corrosion caused by solid and liquid contamination. Lubrication flushes out destructive particulates and minimizes friction and wear. Annual relubrication may be su cient in a clean environment such as a medical imaging room, but monthly lubrication intervals may be required if the profile rail operates in a dirty factory.
Most machine end users prefer to align lubrication frequency with routine preventive-maintenance schedules. If inspection indicates that the purged
grease is degraded or that the rail is very dry, the application may need more frequent relubrication. Conversely, operators can extend lubrication intervals if (upon servicing) the purged grease is in good shape and the rail looks adequately lubricated.
One option is self-lubricating reservoirs on the blocks (carriages) with additional seals and scrapers available. Some profile-rail manufacturers o er blocks with spacers between the balls. These spacers dramatically lower the friction between balls and trap lubrication but can also trap certain contaminants. So spacers serve to extend life where contamination is minor, but can shorten life by restricting the lubricant’s ability to purge contaminants if the operational environment is subject to a lot of debris.
It’s also important to choose and properly apply greases that are especially suited for all applicable machine design challenges — for example, food-safe greases and high-temperature greases. Personnel servicing the rail should continue adding lubrication into the blocks’ lubrication ports until fresh grease emerges from the block and then cycle a few times to spread lubrication over the rails.
Machines should never run without lubrication.
Maintenance technicians should also clean seals and wipers often for maximum protection from the environment, and regularly replace worn seals and wipers.
When replacing carriages reaching their end of life, end users should seriously consider new rails because they also wear and can become damaged over time. Mounting a brand-new carriage on an alreadyworn rail may cause the new carriage to prematurely wear or possibly even catastrophically fail without warning.
In summary: It bears repeating that most profile-rail failures result from poor lubrication practices or contamination issues, making proper protection and maintenance a priority over all other considerations.
While the motion profile will dictate overall sizing parameters, there may be room for some variations to improve system life. Nominal profile rail widths range from 5 to 100 mm and are available in lengths of up to six meters as a single piece. For pieces exceeding typical stock lengths of three to four meters, the rails can be butt joined. However, such joining requires special end machining on the butting ends to minimize any gap between the connected rails. Installation alignment is also more critical when sections of rail are joined together as no gap between the rails can exceed onehalf the carriage ball diameter (if smooth operation and long component life are to be achieved).
The larger the linear rail, the greater the load capacity — and using a smaller percentage of a rail’s maximum capacity can extend its life. For example, a 500-lbcapacity rail constantly moving 100 lb will last much longer than the same system continuously tasked with transporting 500 lb.
Some machine builders (in an e ort to extend the life of the entire assembly) oversize the profile-rail linear bearings. Others oversize profile rail for aesthetic purposes — with the thought being that perhaps a half-inch profile rail driving a one-inch ballscrew looks out of balance. Still other machine builders specify linear rail that’s larger than that required by the motion profile for both durability and improved visual balance to justify the added cost.
Linear-rail carriage sizing can also a ect durability. Longer blocks have more load capacity than smaller blocks,
and wider blocks allow for more mounting options.
In fact, if the installation features the correct level of protection against contamination and receives lubrication at intervals recommended by the component supplier, the profile-rail linear bearing’s life will typically far exceed calculated L10 life predictions. Online sizing and selection tools make it easy for designers to get a precise configuration. Such tools also provide technical information, 3D CAD drawings, pricing, and lead times.
Manufacturers can add preload to carriages by oversizing the rolling elements. But machine designers wanting to specify heightened profile-rail preloading to increase rigidity and decrease deflection should first verify whether such preloading is necessary. For most applications, standard manufacturer preloads are usually perfect. What’s more, if a profilerail linear bearing installs on a horizontal axis, preloading may be redundant. That’s because the weight of the payload usually imparts far more rigidity (and decreased deflection) than any preloading could.
Preloading will shorten life. That said, given that preload is only up to 13% of the rated dynamic load capacity, the benefits of preloading where applicable typically outweigh the impact on life. Applications requiring increased preloads include linear bearings used on CNC machining centers. If the design calls for a single rail but the load isn’t on the center line of the rail and carriage, increasing the size of the block and rail and/ or adding preload may be necessary to handle the moment loading. This can be avoided using a two-block and rail assembly with the load between the rails. Twin rails remove the loading moment, reduce the required rail and carriage size, and eliminate the need for preloading.
All else being equal, an assembly with wellaligned subcomponents will outlast one with poorly aligned elements. Alignment is primarily a function of surface preparation. It’s critical to bolt profile rail to a precisely machined
surface. Without a properly prepared mounting surface, the guide will run rough and require replacement more often. Even minor flatness errors in the mounting surface can reduce bearing life by up to 50%, and more severe alignment issues can lead to immediate failure. Large applications such as CNC machines and robotics demand the highest possible rigidity; all items must be secured as tightly as possible to avoid drift during operation.
If proper surface preparation has been achieved, the next issue is creating parallelism between rails. This becomes especially important if the blocks are preloaded, resulting in much less play. Misalignment significantly increases loading and a subsequent drop in bearing life. In larger precision applications, parallelism may require laser measuring to achieve the required level.
Surface preparation can be expensive, however. If a design can tolerate less accuracy and more compliance, money can be saved because less surface preparation is needed. Ultimately, the required amount of surface preparation for a profile rail depends on the arrangement of the rolling elements and the required precision level.
In summary: Proper alignment significantly impacts rail durability. Good alignment depends on su cient investment in mounting surface quality that designers can adjust based on their requirements for accuracy and compliance.
Profile-rail assembly life significantly varies with motion profile, environment, and preventive maintenance practices. Strictly enforced lubrication schedules and corrosion protection are key. Online sizing and selection tools such as this one from Thomson Industries use visual aids to guide users to optimal profile rail choices in mere minutes.
| Courtesy of Thomson Industries Inc.
Machine designers can specify profile rail having rolling elements arranged in a few di erent ways to satisfy target tolerances, compliance, and budgetary constraints, and these in turn a ect the amount of installation surface preparation required. The following profile-rail internal architectures are most common.
A double-backed architecture arranges four ball or roller tracks (each with two contact points) to maximize rigidity and moment arm D.
• A Gothic-arch architecture arranges two larger ball tracks (each with four contact points) to allow smaller rail sizes while minimizing degradation of rigidity and allowing for an intermediate moment arm D.
• A double-faced architecture arranges four ball tracks (each with two contact points) higher on the rail to increase compliance while minimizing degradation of the moment arm D.
The most rigid and accurate rolling element choice is the doublebacked configuration, which requires the most significant investment in surface preparation. The Gothic arch configuration is the next-most rigid and accurate, needing less surface preparation. The double-faced design is the least rigid and most compliant, thus requiring the least investment in surface preparation. But even machine designers not needing maximum accuracy or rigidity can still optimize for longer life by specifying as much surface preparation as the budget will allow.
Profile-rail rolling-element durability mainly depends on which of the three pictured rail architectures is chosen.
| Courtesy of Thomson Industries Inc.
Depending on the application, profile rail can be optimized by width and length.
Image: Thomson Industries Inc.
Manufacturers employ various configuration combinations of their profile bearings. Some use a back-toback or face-to-face configuration with further variations of raceway shapes. Plus, some include a Gothic arch, round arch, oval arch, or V-groove shape. Extensive test reports abound on the advantages of every manufacturer’s chosen method. In practice, every manufacturer’s product meets or exceeds their published L10 life directly dependent on proper sizing, lubrication, and corrosion protection.
Linear profile rail and carriage count
A typical profile rail system involves two rails with two carriages on each rail. Adding rails or carriages to the system usually adds design risk because the application becomes exponentially more complex. However, some project requirements outweigh these challenges. Large application envelopes or prioritizing the absolute minimum deflection are examples where the tradeo s make a higher rail and carriage count worth the increased alignment requirements.
In summary: Choosing oversized rails, avoiding unnecessary preloading, and deploying multiple rails or carriages can also extend profile-rail life. That said, implementing more than two of these introduces complexities that can shorten life if not handled skillfully. DW
Researchers at EPFL have developed the first system that enables four-arm laparoscopic surgery by controlling two additional robotic arms via haptic foot interfaces.
Researchers at EPFL, a public research university in Lausanne, Switzerland, have developed a robotic system that allows surgeons to perform laparoscopic surgeries with four arms by controlling two robotic arms using haptic foot interfaces.
The research was a collaboration between the research group REHAssist and the Learning Algorithms and Systems Laboratory (LASA). It was led by EPFL Ph.D. students Jacob Hernandez and Walid Amanhoud, who developed a system that allows surgeons to control two robotic arms using haptic foot interfaces with five degrees of eedom. In this setup, each of the surgeon’s hands controls a manipulative instrument, while one foot controls an actuated gripper while the other controls an endoscope or camera.
“Actuators in the foot pedals give haptic feedback to the user, guiding the foot towards the target as if following an invisible field-of-forces, and also limit force and movement to ensure that erroneous feet movements do not endanger the patient,” Mohamed Bouri,
head of REHAssist, said. “Our system opens up new possibilities for surgeons to perform 4-handed laparoscopic procedures, allowing a single person to do a task that is usually performed by two, sometimes three people.”
One key aspect of the system is that control is shared between the surgeon and robotic assistants. The researchers designed a control amework that ensures the surgeon and robots can work collaboratively within a concurrent workspace while still
meeting the precision and demands of laparoscopic surgery.
This feature helps to minimize fatigue for surgeons, as the robots can sometimes lead the surgeon’s control of an instrument as it predicts where the surgeon wants to move.
Haptic pedals with force feedback allow the control of two robotic arms using feet to manipulate instruments such as an endoscope or a grasper.
The IDT Series is a family of compact actuators with an integrated servo drive with CANopen® communication. They deliver high torque with exceptional accuracy and repeatability, and feature Harmonic Drive® precision strain wave gears combined with a brushless servomotor. Some models are available with a brake and two magnetic absolute encoders with the second providing output position sensing. This revolutionary product line eliminates the need for an external drive and greatly simplifies cabling, yet delivers high-positional accuracy and torsional stiffness with a compact form factor.
• Actuator with Integrated Servo Drive utilizing CANopen®
• 24 or 48 VDC nominal supply voltage
• A single cable with only 4 conductors is needed: CANH, CANL, +VDC, 0VDC
• Zero Backlash Harmonic Drive® Gearing
• Panel Mount Connectors or Pigtail Cables Available with Radial and Axial Options
• Control Modes include: Torque, Velocity, and Position Control, CSP, CSV, CST
“Controlling four arms simultaneously, moreover with one’s feet, is far from routine and can be quite tiring. To reduce the complexity of the control, the robots actively assist the surgeon by coordinating their movements with the surgeons through active prediction of the surgeon’s intent and adaptive visual tracking of laparoscopic instruments with the camera. Additionally, assistance is offered for more accurate grasping of the tissues,” Professor Aude Billard, head of LASA, said.
Specialists have already been trained on the system and clinical trials are currently ongoing in Geneva. The research team conducted a comprehensive user study with practicing surgeons.
According to Dr. Enrico Broennimann, who has participated in the trials in collaboration with the Swiss Foundation for Innovation and Training in Surgery (SFITS), “The idea to actively use one’s feet to perform robotic-assisted surgery is a good idea, and it’s definitely a learnable skill. I’d like to see it implemented in the operating room, perhaps as a cockpit well away from the patient to increase ergonomics.” RR
Intuitive Surgical president Dave Rosa recently discussed two technological opportunities that will advance surgical robotics and minimally invasive surgery in a major way: improved visualization for surgeons and focal therapy.
“How can we help surgeons see more about what they’re doing? … That, to me, is a huge piece of the puzzle going forward that I’m really excited about,” Rosa said in an interview with DeviceTalks Editorial Director Tom Salemi for our IntuitiveTalks podcast.
The difference between the best and worst surgeons isn’t who can manipulate the instrument better, Rosa said, but rather who has better anatomical knowledge with regard to tissue planes, the subtleties of where bleeding might or might not happen, and the location of nerves or structures like the ureter.
The question is how can device developers help surgeons so they don’t need 1,000 cases to learn that sort of anatomical variation, Rosa said.
“Fluorescence-guided surgery is a big piece of this puzzle, where you can inject a fluorescing marker into the body and using infrared lasers in the system, it lights up. It’s pretty amazing,” Rosa said. “We have a molecule in development that’s specific to prostate cancer, for example. You can inject the drug, turn on the infrared laser, and see the prostate cancer. And if the surgeon has resected the prostate but happens to leave some behind, they can go back and resect that and work for a negative margin. That’s not possible in white light imaging.”
The second area Rosa highlighted is focal therapy, a less invasive treatment for prostate cancer. Focal therapy uses real-time imaging and ablation to destroy small tumors, minimizing the occurrence or severity of side effects from more traditional oncology therapies.
“As work is being done outside of Intuitive for liquid biopsy, better imaging, you see that cancer might be detected earlier, when it’s smaller and not symptomatic,” Rosa said. “If that’s true and you buy that as a thesis — I don’t think we’d argue that — it should be possible to treat it earlier, too, if we can localize it.”
Contactless, no wear and maintenance-free
High positioning accuracy and resolution
Economical, small, compact designs and custom solutions
Flexiblering diameters and measuring lengths
Local stock of absolute and incremental encoders
Lead times as low as 6 weeks on custom encoders
Using its Generative AI approach, TRI has already taught robots more than 60 dexterous behaviors like peeling vegetables, using hand mixers, preparing snacks, and flipping pancakes. TRI said the goal is to teach robots hundreds by the end of 2023 and 1,000 by the end of 2024.
New approach is a step towards building Large Behavior Models for robots, analogous to Large Language wwModels for conversational AI.
Toyota Research Institute
(TRI) recently unveiled how it is using Generative AI to help robots learn new dexterous behaviors om demonstration. TRI said this new approach “is a step towards building ‘Large Behavior Models (LBMs)’ for robots, analogous to the Large Language Models (LLMs) that have recently revolutionized conversational AI.”
TRI said it has already taught robots more than 60 di cult, dexterous skills using the new approach. Some of these skills include pouring liquids, using tools and manipulating deformable objects. These were all realized, according to TRI, without writing a single line of new code; the only change was supplying the robot with new data.
Whether you’re storing, conveying, picking or handling, there’s not a corner of the warehouse that our robots and solutions will not fit.
Sereact, a German-based AI and robotics developer, recently announced PickGPT, a robotics transformer that combines large language models (LLMs) with the company’s computer vision technology.
PickGPT allows robot operators to instruct robots using natural language by enabling robots to process natural language and visual information and correlate multimode data. PickGPT allows robots to perceive their environment with unprecedented intelligence and accuracy and understand and execute instructions in natural language.
“PickGPT enables straightforward communication between humans and robots via voice commands and intuitive interfaces. This simplifies the link with other warehouse systems and enables employees to instruct the robot in a simple way – for example, to define pick points or to blacklist certain items,” Ralf Gulde, CoFounder and CEO of Sereact, said.
The robotics developer is a software-based robotics system that doesn’t require programming or training. Because of this, PickGPT reduces the time needed to set up and customize robots and allows employees to spend that time focusing on other essential tasks. It also expands the range of people who can work with robots as they don’t need a coding background to work with the system.
Along with faster setup, PickGPT offers more flexibility and quality control. With the robotics transformer, robots can respond quickly and easily to new tasks or changing environmental conditions, which are common in warehouse settings.
PickGPT can also recognize and identify objects and products in real time based on their visual characteristics. The transformer automatically analyzes product images and matches them with items in any real-world scenario.
It can also understand and interpret product titles, descriptions, and other textual information to automatically identify and assign related products to regions in an image. This means that PickGPT has a high potential for quality control processes.
The robotics transformer can also simplify the return process for e-commerce companies. PickGPT has the ability to distinguish between packaging material and products in the first step of the return process, and it can then sort the items automatically based on a description or product image, meaning there is no need for barcode scanning.
Sereact was founded in 2021 by Marc Tuscher and Ralf Gulde, who both researched the combination of robotics and AI at the University of Stuttgart. The company is based in StuttgartVaihingen, Germany.
“The tasks that I’m watching these robots perform are simply amazing – even one year ago, I would not have predicted that we were close to this level of diverse dexterity,” said Russ Tedrake, vice president of robotics research at TRI and the Toyota professor of electrical engineering and computer science, aeronautics and astronautics, and mechanical engineering at MIT.
“What is so exciting about this new approach is the rate and reliability with which we can add new skills. Because these skills work directly from camera images and tactile sensing, using only learned representations, they are able to perform well even on tasks that involve deformable objects, cloth, and liquids — all of which have traditionally been extremely difficult for robots.”
“Our research in robotics is aimed at amplifying people rather than replacing them,” said Gill Pratt, CEO of TRI and Chief Scientist for Toyota Motor Corporation. “This new teaching technique is both very efficient and produces very high performing behaviors, enabling robots to much more effectively amplify people in many ways.”
TRI’s robot behavior model learns from haptic demonstrations from a teacher, combined with a language description of the goal. It then uses an AI-based diffusion policy to learn the demonstrated skill. This process allows a new behavior to be deployed autonomously from dozens of demonstrations.
TRI’s approach to robot learning is agnostic to the choice of teleoperation device, and it said it has used a variety of low-cost interfaces such as joysticks. For more dexterous behaviors, it taught via bimanual haptic devices with position-position coupling between the teleoperation device and the robot. Position-position coupling means the input device sends measured pose as commands to the robot and the robot tracks these pose commands using torque-based Operational Space Control. The robot’s pose-tracking error is then converted to a force and sent back to the input device for the teacher to feel. This allows teachers to close the feedback loop with the robot through force and has been critical for many of the most difficult skills we have taught.
When the robot holds a tool with both arms, it creates a closed kinematic chain. For any given configuration of the robot and tool, there is a large range of possible
“Our research in robotics is aimed at amplifying people rather than replacing them”
Introducing Northwire, your ultimate partner for custom cable and interconnect solutions for Test & Measurement applications.
With our cutting-edge technology and expertise, we deliver high-quality, reliable cables tailored to your specific needs. Trust us to provide innovative solutions, exceptional performance, and superior customer service.
Experience the Northwire advantage today!
BENEFITS:
• Superior Access to Engineering services and technical support
• UL/CSA certification
• Ruggedized cable solutions
• High-quality custom products built on proven solid cable solutions platforms
• Vertical integrated supply chain
internal forces that are unobservable visually. Certain force configurations, such as pulling the grippers apart, are inherently unstable and make it likely the robot’s grasp will slip. If human demonstrators do not have access to haptic feedback, they won’t be able to sense or teach proper control of force.
So TRI employs its Soft-Bubble sensors on many of its platforms. These sensors consist of an internal camera observing an inflated deformable outer membrane. They go beyond measuring sparse force signals and allow the robot to perceive spatially dense information about contact patterns, geometry, slip, and force.
Making good use of the information from these sensors has historically been a challenge. But TRI said diffusion provides a natural way for robots to use the full richness these visuotactile sensors afford that allows them to apply them to arbitrary dexterous tasks.
In one test, a human teacher attempted 10 egg-beating demonstrations. With haptic force feedback, the operator succeeded every time. Without this feedback, they failed every time.
Instead of image generation conditioned on natural language, TRI uses diffusion to generate robot actions conditioned on sensor observations and, optionally, natural language. TRI said using diffusion to generate robot behavior provides three benefits over previous approaches:
1. Applicability to multi-modal demonstrations. This means human demonstrators can teach behaviors naturally and not worry about confusing the robot.
2. Suitability to high-dimensional action spaces. This means it’s possible for the robot to plan forward in time which helps avoid
myopic, inconsistent, or erratic behavior.
3. Stable and reliable training. This means it’s possible to train robots at scale and have confidence they will work, without laborious hand-tuning or hunting for golden checkpoints.
According to TRI, Diffusion is well suited for high dimensional output spaces. Generating images, for example, requires predicting hundreds of thousands of individual pixels. For robotics, this is a key advantage and allows diffusion-based behavior models to scale to complex robots with multiple limbs. It also gave TRI the ability to predict intended trajectories of actions instead of single timesteps.
TRI said this Diffusion Policy is “embarrassingly simple” to train; new behaviors can be taught without requiring numerous costly and laborious real-world evaluations to hunt for the
To teach new behaviors, TRI’s approach requires a human operator to teleoperate the robot through demonstrations of the desired task. This usually requires an hour or two of teaching which generally equates to anywhere from a couple dozen to a hundred or so demonstrations.
| Toyota Research Institutebest-performing checkpoints and hyperparameters. Unlike computer vision or natural language applications, AI-based closed-loop systems can not be accurately evaluated with o ine metrics — they must be evaluated in a closed-loop setting which, in robotics, generally requires evaluation on physical hardware.
This means any learning pipeline that requires extensive tuning or hyperparameter optimization becomes impractical due to this bottleneck in real-life evaluation. Because Diffusion Policy works out of the box so consistently, it allowed TRI to bypass this di culty.
Next steps
TRI admitted that “when we teach a robot a new skill, it is brittle.” Skills will work well in circumstances that are similar to those used in teaching, but
the robot will struggle when they differ. TRI said the most common causes of failure cases we observe are:
• States where no recovery has been demonstrated. This can be the result of demonstrations that are too clean.
• Camera viewpoint or background significant changes.
• Test time manipulands that were not encountered during training.
• Distractor objects, for example, significant clutter that was not present during training.
Part of TRI’s technology stack is Drake, a model-based design for robotics that includes a toolbox and simulation platform. Drake’s degree of realism allows TRI to develop in both simulation and in reality and could help overcome these shortcomings going forward.
The SHA-IDT Series is a family of compact actuators that deliver high torque with exceptional accuracy and repeatability. These hollow shaft servo actuators feature Harmonic Drive® precision strain wave gears combined with a brushless servomotor, a brake, two magnetic absolute encoders and an integrated servo drive with CANopen® communication. This revolutionary product eliminates the need for an external drive and greatly simplifies cabling yet delivers high-positional accuracy and torsional stiffness in a compact housing.
TRI’s robots have learned 60 dexterous skills already, with a target of hundreds by the end of 2023 and 1,000 by the end of 2024.
“Existing Large Language Models possess the powerful ability to compose concepts in novel ways and learn om single examples,” TRI said. “In the past year, we’ve seen this enable robots to generalize semantically (for example, pick and place with novel objects). The next big milestone is the creation of equivalently powerful Large Behavior Models that fuse this semantic capability with a high level of physical intelligence and creativity. These models will be critical for generalpurpose robots that are able to richly engage with the world around them and spontaneously create new dexterous behaviors when needed.” RR
Today’s AGVs must be compact and functional robots which are able to move vertically and carry heavy loads. These AGVs cannot fail, and so the choice of their motorization is crucial. There are 5 key points to consider when motorizing an AGV.
1. Choose compact motorization where possible - Drives must fit into restricted spaces, as they are sometimes integrated into existing trucks. A small footprint is critical for applications in logistics.
2. Focus on ease of use – select a plug-and-play solution.
3. Opt for fast delivery of your motor solution
4. Base the design on modularity - Not all AGVs do the same job and therefore having the flexibility to select a solution to match needed specifications is essential.
5. Prioritize safety – select motor options with integrated sensors.
maxon’s IDX motor has a diameter of only 56 mm, its performance is equivalent to that of a motor with a footprint 25% larger. The IDX motorization thus combines performance in a compact size and ideal for AGVs.
Go to Drive.tech for more details. Visit www.maxongroup.us for more maxon solutions.
Advancing innovation for over 100 years
Why accept a standard product for your custom application?
NEWT is committed to being the premier manufacturer of choice for customers requiring specialty wire, cable and extruded tubing to meet existing and emerging worldwide markets. Our custom products and solutions are not only engineered to the exacting specifications of our customers, but designed to perform under the harsh conditions of today’s advanced manufacturing processes. Cables we specialize in are LITZ, multi-conductor cables, hybrid configurations, coaxial, twin axial, miniature and micro-miniature coaxial cables, ultra flexible, high flex life, low/high temperature cables, braids, and a variety of proprietary cable designs. Contact us today and let us help you dream beyond today’s technology and achieve the impossible.
At Northwire, we understand the importance of having the right cable and interconnect solutions for your Test & Measurement applications. With over 50 years of experience, we have the expertise and knowledge to provide you with the highest quality products that are both reliable and durable.
Our team of skilled engineers and technicians work closely with you to ensure that your custom cable and interconnect solutions meet your requirements and exceed expectations. We use only the highest quality materials and advanced manufacturing techniques to deliver products that are built to last.
Whether you need a custom cable for data transfer, power transmission, or any other applications, we have the capabilities to deliver the solution you need. Trust Northwire for excellence and reliability.
Robots are flexible and adaptable. Quickly re-tasking robots for job variety can be challenging.
Some common solutions: Changing workpieces – Quick-change gripper fingers and gripper changeouts are easily automated for workpiece variety or changing workpiece characteristics during manufacturing.
Flexible machine table fixtures – Robots are widely identified for their ability to handle workpieces. They also excel at automatically replacing fixtures and other peripheral tooling.
Automating multiple tasks – Use the robot to accomplish a secondary task. Instead of remaining idle during machining, the robot can automatically deburr workpieces.
Adjustable custom tooling – Use dove tails and adjustable mountings in EOATs to expand tools for changing conditions or reach requirements.
Many standard solutions are available - make the most of your investment with automation expert support today!
Northwire, Inc. 110 Prospect Way
Osceola, WI 540 (715) 294-2121
customercare_northwire@lemo.com
www.northwire.com
SCHUNK: 211 Kitty Hawk Drive, Morrisville, NC 27560
919-572-2705
info@us.schunk.com
SALES
Ryan Ashdown rashdown@wtwhmedia.com
216.316.6691
Jami Brownlee jbrownlee@wtwhmedia.com 224.760.1055
Mary Ann Cooke mcooke@wtwhmedia.com
781.710.4659
Jim Dempsey jdempsey@wtwhmedia.com 216.387.1916
Mike Francesconi mfrancesconi@wtwhmedia.com
630.488.9029
Jim Powers jpowers@wtwhmedia.com 312.925.7793
@jpowers_media
Courtney Nagle cseel@wtwhmedia.com 440.523.1685 @wtwh_CSeel
Publisher Mike Emich memich@wtwhmedia.com
508.446.1823
@wtwh_memich
CEO
Scott McCafferty smccafferty@wtwhmedia.com
310.279.3844
@SMMcCafferty
EVP
Marshall Matheson mmatheson@wtwhmedia.com
805.895.3609
@mmatheson
CFO
Ken Gradman kgradman@wtwhmedia.com
773-680-5955
DESIGN WORLD does not pass judgment on subjects of controversy nor enter into dispute with or between any individuals or organizations. DESIGN WORLD is also an independent forum for the expression of opinions relevant to industry issues. Letters to the editor and by-lined articles express the views of the author and not necessarily of the publisher or the publication. Every effort is made to provide accurate information; however, publisher assumes no responsibility for accuracy of submitted advertising and editorial information. Non-commissioned articles and news releases cannot be acknowledged. Unsolicited materials cannot be returned nor will this organization assume responsibility for their care.
DESIGN WORLD does not endorse any products, programs or services of advertisers or editorial contributors. Copyright© 2023 by WTWH Media, LLC. No part of this publication may be reproduced in any form or by any means, electronic or mechanical, or by recording, or by any information storage or retrieval system, without written permission from the publisher.
Subscription Rates: Free and controlled circulation to qualified subscribers. Nonqualified persons may subscribe at the following rates: U.S. and possessions: 1 year: $125; 2 years: $200; 3 years: $275; Canadian and foreign, 1 year: $195; only US funds are accepted. Single copies $15 each. Subscriptions are prepaid, and check or money orders only.
Subscriber Services: To order a subscription or change your address, please email: designworld@omeda.com or visit our web site at www.designworldonline.com
DESIGN WORLD (ISSN 1941-7217) is published monthly by: WTWH Media, LLC; 1111 Superior Ave., Suite 2600, Cleveland, OH 44114. Periodicals postage paid at Cleveland, OH & additional mailing offices.
POSTMASTER: Send address changes to: Design World, 1111 Superior Ave., Suite 2600, Cleveland, OH 44114
Norfolk Southern train 32N derailed in February in East Palestine, Ohio, while carrying chemicals and other freight. The presence of vinyl chloride and the actions taken to manage it made the derailment big news. Vinyl chloride is correctly described as flammable, toxic, and carcinogenic. It doesn’t sound like something that belongs in rural Ohio. So, why was vinyl chloride on the train?
Pretzels are at least partially to blame.
Vinyl chloride was on the train because it had somewhere to go. The New York Times reported that the cars were headed to Pedricktown, N.J. The Pedricktown facility consumes vinyl chloride shipped in from vinyl chloride production facilities. Vinyl chloride is almost exclusively used for making polymers. It reacts when appropriately catalyzed, polymerizing into polyvinyl chloride, a plastic. Polyvinyl chloride, PVC, is by far the most significant use of vinyl chloride.
Most PVC production is located near vinyl chloride production, allowing transportation in pipes, not trains. That is true for the production of most polymers. The majority of monomers used aren’t shipped. Pellets of polymer are. Shipping vinyl chloride can be avoided by ceasing to make PVC in Pedricktown — instead making it at a facility adjacent to vinyl chloride production.
Why make PVC? PVC production consumes almost all of vinyl chloride produced. PVC is not a particularly strong polymer, softening at temperatures easily encountered. That makes it easy to process. It takes fillers well. It can also be made flexible by the addition of plasticizers. It can be clear — useful in many applications. It survives
environmental exposure well, holds up to sunlight, and resists degradation. It is intrinsically self-extinguishing, a useful feature for wiring and construction applications. It is solvent-weldable, also very useful. And it’s cheap.
PVC does have issues. There is some residual vinyl chloride present that can escape. Industry dropped the amount of residual monomer through process improvements, but there is still some monomer outgassing. Plasticizer use in vinyl, especially phthalate esters, is problematic. The plasticizers leach out and have been implicated in bad health outcomes. When it burns, PVC creates hydrogen chloride, a corrosive acid. The production of vinyl chloride is also associated with the production of dioxins, persistent environmental pollutants.
We all use PVC, knowingly or unwittingly, every minute of every day. If you are connected to a municipal water supply, your water almost certainly passed through PVC pipes. Flip on a switch, and the power moves through PVC insulated wires. You’re likely walking on vinyl flooring, in your house or in commercial buildings. Medical applications include tubing and bags. Miscellaneous uses include consumer packaging, toys, and things like checkbook covers.
There are substitutes for PVC in every one of its applications, but PVC remains in the market because of its value. A complicated supply chain makes it pretty much impossible to stop making PVC. We produce PVC because it is hard to stop. PVC is a major product of one of the foundational technologies of the chemical industry, the chlor-alkali process. It is a coproduct process.
Fortunately, Seinfeld stands ready to explain coproduct processes. Mu ns are a coproduct process. The goodto-eat tops come with unappealing stumps. If you make tops, you get stumps. The chlor-alkali process makes both sodium hydroxide — also known as both caustic soda and lye — and chlorine. Our world is acidic. A chemical base is needed to neutralize acids. Sodium hydroxide is the base of choice, the highest volume industrially produced chemical base. The prices of caustic soda and chlorine fluctuate. Some of the time, caustic soda is more valuable. It is the mu n top and chlorine is the stump. Other times, the chlorine is the top and caustic soda is the stump. Whether top or stump, caustic soda is always needed. It is used in many processes. Without it, there is no aluminum. No titania. No paper. No bleach. Caustic soda is used in water treatment, textile production, soap and detergent production, and food processing. It is used to make baking powder necessary for mu ns. Pretzels are crunchy because they are treated with sodium hydroxide before baking.
Vinyl chloride found its way to rural Ohio because it plays an important role in modern society. Talk of bans on shipment of hazardous material, talk of bans on PVC, ignore society’s appetite for the polymers and related, important products. We all, either directly through the use of PVC, or indirectly by using products made from caustic soda, are responsible for vinyl chloride being in rural Ohio. Our appetite for cheap polymer — and crunchy pretzels — is why vinyl chloride was on train 32N. DW
Designing efficient systems involves much more than simply understanding a few basic principles. There is a true art to balancing the specific requirements of an application in order to achieve the desired goals in the best possible way. Help us understand the unique needs of your application and together, we’ll develop something that surpasses what any of us could have done alone.