
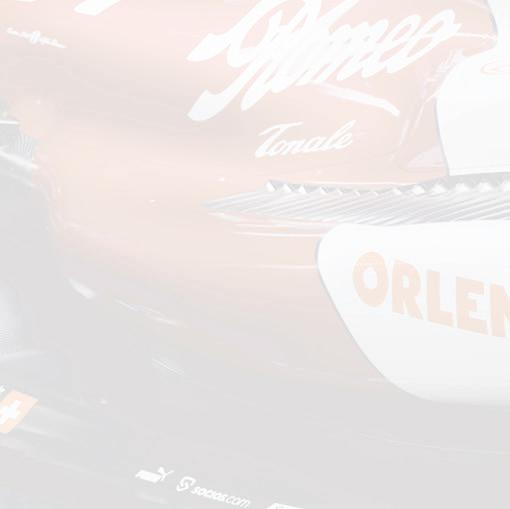
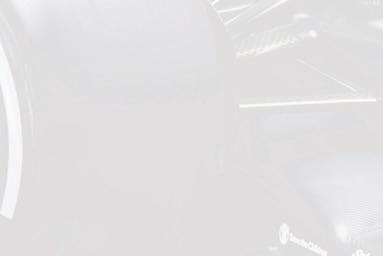
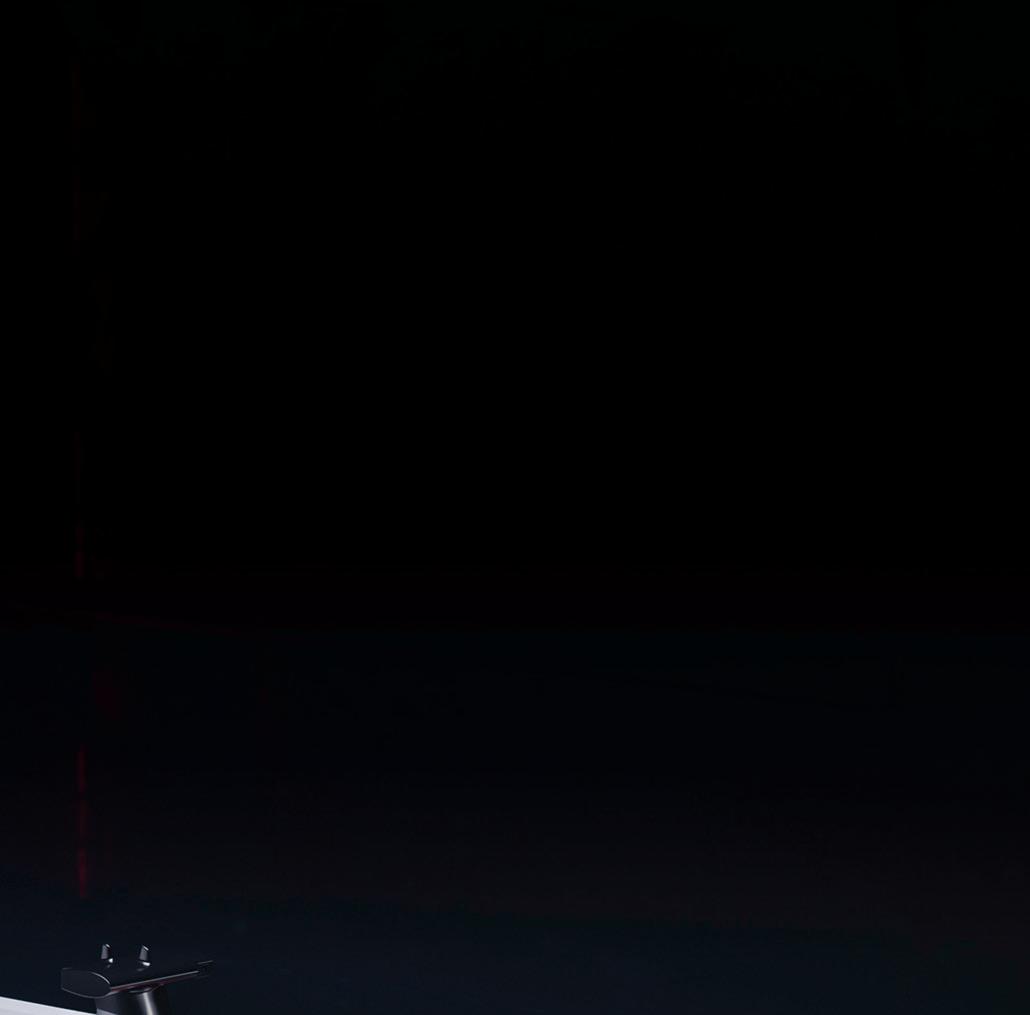




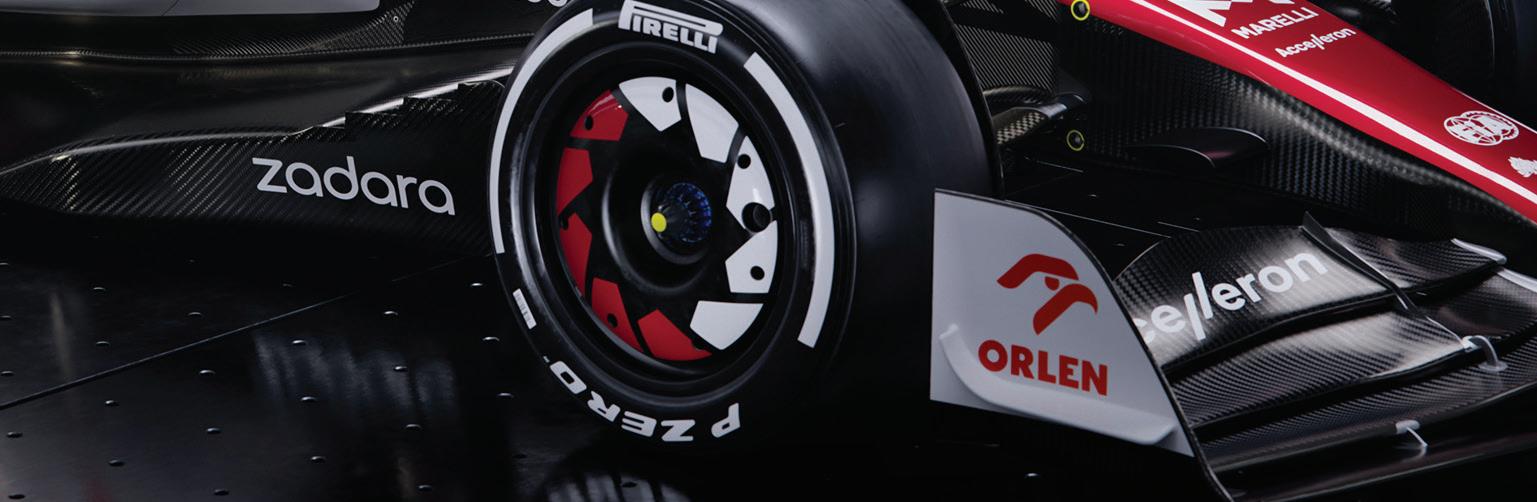

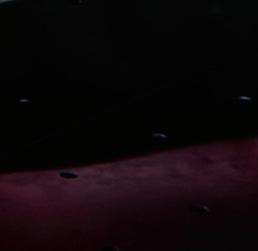

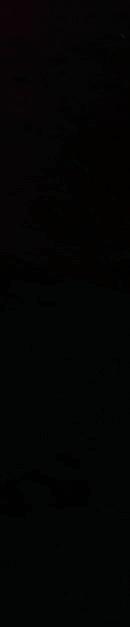
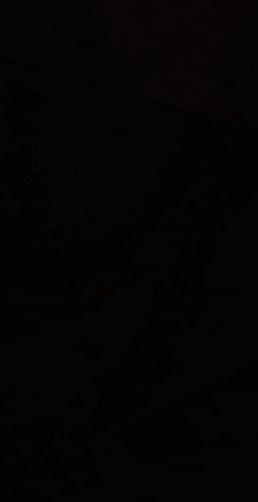
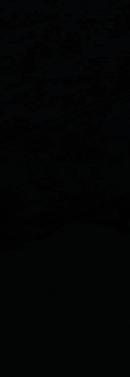
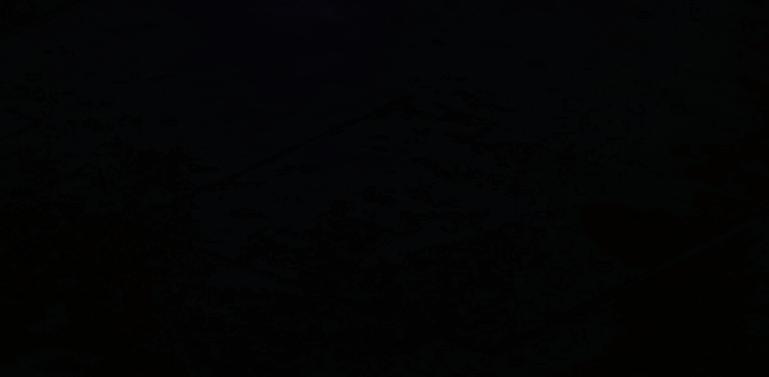
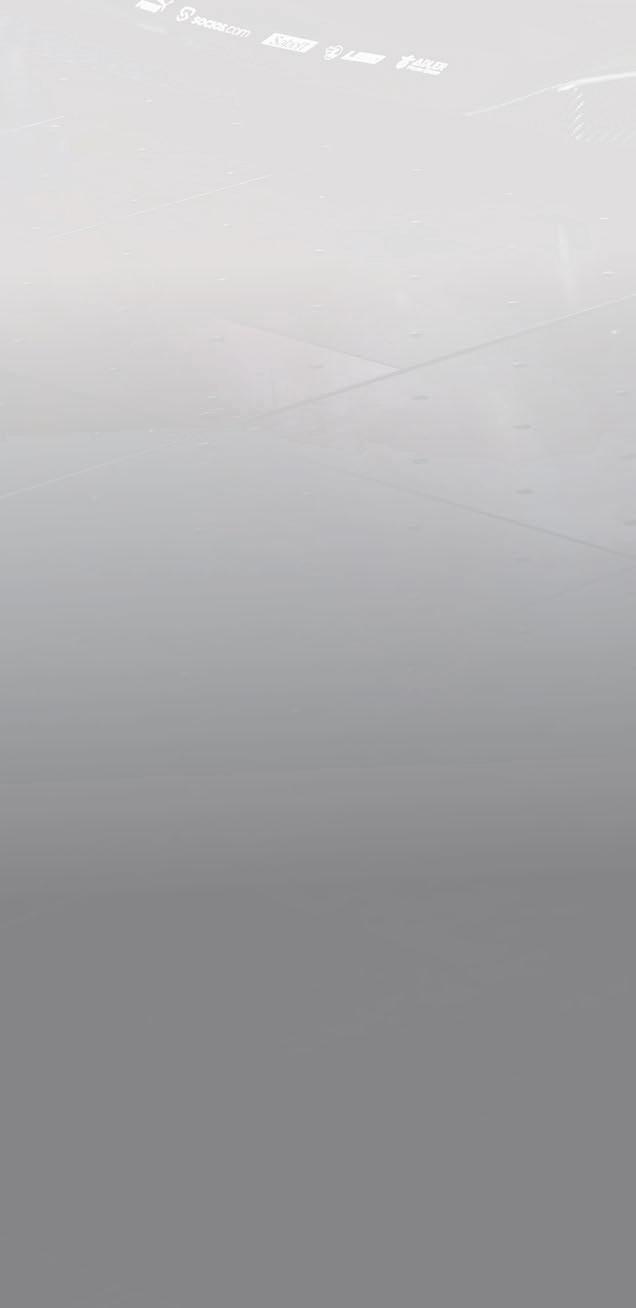



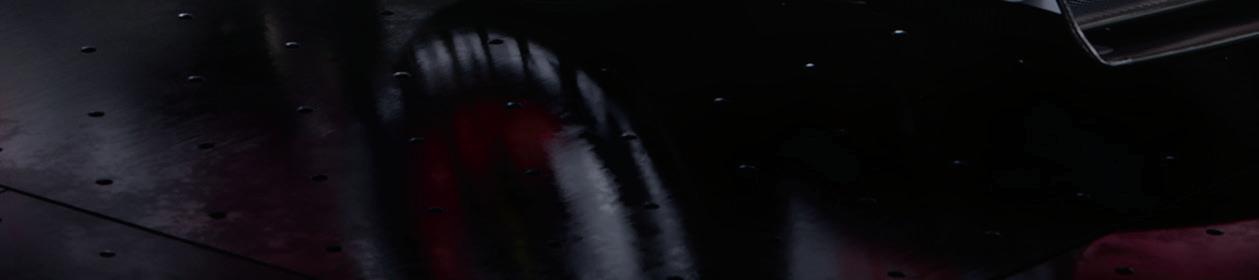

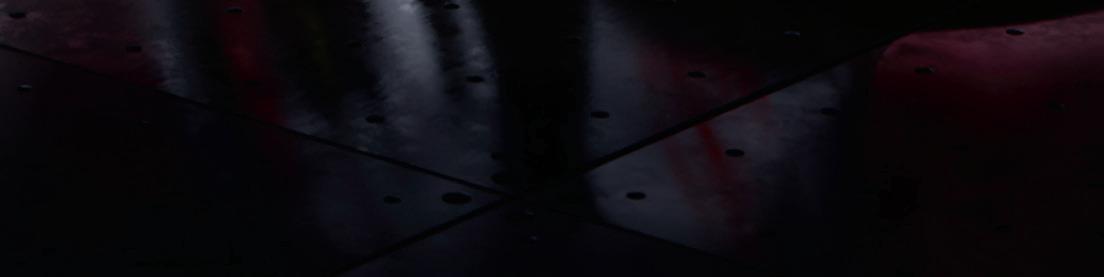

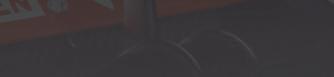
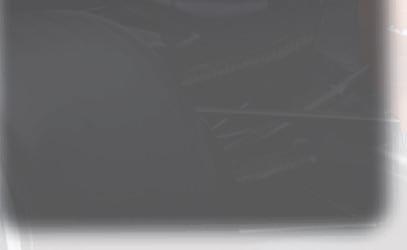



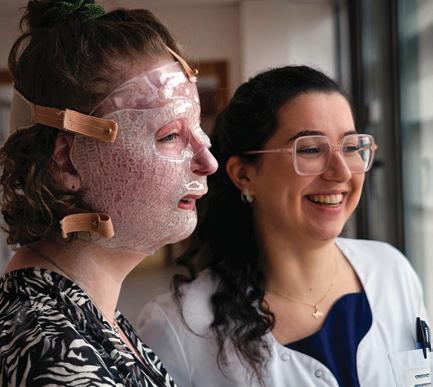
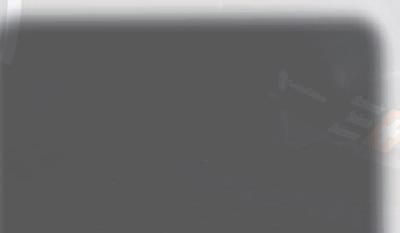

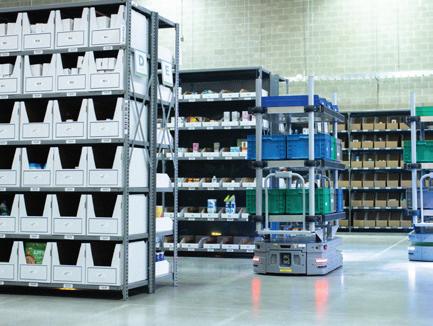
THK is committed to meeting the worldwide demand for linear motion products. We manufacture, assemble, and ship across North America from our location in Hebron, Ohio. We’ve also ramped up our automating processes at existing facilities, including our U.S. manufacturing plant, where over 70% of THK Robotics Components are manufactured. Automated processes at this state-of-the-art facility enable increased production while maintaining the high standard of precision associated with THK products.
To learn more, call us at 1-800-763-5459 or visit www.thk.com.
See us at ATX West, Anaheim CA, Feb. 7 - 9, Booth #4254
See us at: Pack Expo September 11-13 in Las Vegas, NV Booth SU-7878
For custom stand-alone PLC I/O con gurations that exactly match your application (option module sold separately).
CLICK PLUS PLCs provide the same simple, practical control the CLICK PLC line is known for but with some surprising bells and whistles. Data logging, Wi-Fi connect-ability, MQTT communication, and increased security measures are just a few of the impressive features offered with the CLICK PLUS PLC series.
Using the same FREE streamlined PLC programming software as its predecessor, CLICK PLUS PLCs provide straightforward, no-learning-curve programming. Combine that with a starting at price of just $97.00 and the CLICK PLUS PLC is undoubtedly the unmatched value leader!
• Optimized load plates and outer cylinder plus more ball circuits.
• Improves performance of: Machinery and equipment for automation, optics and measuring.
• Floating load plate adjusts clearance.
• Greater ball contact in ground circular arch triples load capacity.
• Floating raceway wiper seal allows unrestricted self-alignment.
• Load plate ends are thinner making center a fulcrum for self-alignment.
• Our raceways are groundnot stamped - a ording precision tolerances.
• Each load plate is
• Light weight components for energy reduction.
and checked for consistency - unlike competitions’ stamped plates.
• Unibody construction for quieter operation.
According to the IEA’s Global EV Outlook 2023, electric car sales saw another record year in 2022, despite supply chain disruptions, macroeconomic and geopolitical uncertainty, and high commodity and energy prices. The growth took place in the context of globally contracting car markets: total car sales in 2022 dipped by 3% relative to 2021. Electric car sales — including battery and plug-in hybrids — exceeded 10 million in 2022, up 55% from 2021. This figure exceeds the total number of cars sold across the entire EU and is nearly half the total number of cars sold in China in 2022.
IEA says that from 2017 to 2022, EV sales jumped from around 1 million to more than 10 million. The share of electric cars sales jumped from 9% in 2021 to 14% in 2022, more than ten times their share in 2017. And as I mentioned in a previous column, I even made the jump to an EV myself earlier this year.
EVs aren’t just about passenger cars, though. Mobile equipment is no stranger to electrics, and OEMs continue to explore EVs in this market. As our own Ken Korane reported this Spring, New Holland Construction has launched its first commercially available EV machine, the E15X electric power mini excavator. The excavator runs on a cobalt-free lithium-ion battery that powers a 21.5-hp motor, making it as powerful as the E14D diesel equivalent. The motor provides plenty of power to the load-sensing hydraulics for smooth and e cient operation in a compact and easily transportable package. On a fully charged battery, the excavator can reportedly operate for eight hours. It can be recharged in 10 hours with a standard 110 V outlet or within an hour with its fast charge features.
Beyond industries like construction, mining, and agriculture, we’re also seeing EVs begin to expand into aerospace and military applications. The coming years are sure to be exciting ones, and design engineers need to keep abreast of this fastchanging technology.
That’s why I’m excited to share the news that a new sister publication to Design World, called EV Engineering, will be launching this Fall. Based online at www. evengineeringonline.com, the new site will be a central point for you to learn about everything EV, from batteries to components, and technology news to testing, safety, and R&D e orts in the field. We’ll also have occasional special print sections dedicated to this technology here in Design World
I invite you to visit the new site and sign up for its newsletter, which will be a great resource for all engineers trying to stay abreast of all things electric. DW
I had the absolute pleasure of attending the 18th Scandinavian International Conference on Fluid Power (SICFP) hosted by the Innovative Hydraulics and Automation (IHA) laboratory at Tampere University in Finland. From May 30 to June 1, 2023, researchers and industry experts from 37 companies, 19 academic institutions, and 17 countries congregated to exchange information and advance technology forward. Tatiana Minav, professor at Tampere University and chairperson of SICFP 2023, artfully gathered fluid power students and professionals to foster relationships and ignite new innovations that align with global sustainability goals.
“If we want to leave this planet for our children and grandchildren, we must act,” said Minav during her opening presentation.
This year, SICFP received 52 research abstracts and accepted 38 peer-reviewed papers into the conference. Topics included electrification and hybrid solutions; condition monitoring; novel drives, transmissions, and actuators; safety and productivity; automation; controls; hydraulic components; and modeling and design methods.
The day-one keynote speakers included Alexander Flaig, SVP of engineering at Bosch Rexroth; Kalle Einola, R&D manager of technology, product safety, and IPR at Ponsse; and Marcus Geimer, professor at Karlsruher Institut für Technology. Each presenter shared words of wisdom and practical guidance on transforming current technology to optimize mobile machinery and reduce emissions.
Incredible research presentations followed, discussing algorithms for electrification and hybrid systems and simulations for predicting failures and improving operations. Safety
was also emphasized in tandem with business and productivity for heavy-duty mobile machines.
In the evening, attendees enjoyed an eloquent dinner at the historic Tuulensuu Palatsi, where Emil Nørregård Olesen, Ph.D. student of AAU Energy in collaboration with Danfoss Power Solutions, was presented with the Best Paper Award, sponsored by IHA and Fluid Power World.
On day two, we returned to Tampere-talo to learn about technology and trends from industry experts Yukio Kamizuru, product owner of Systems Solutions and Digital Services at Bosch Rexroth; Lucien Robroek, CEO of Nuvera Fuel Cells; and Peter Achten, CEO of Innas. The afternoon session covered automation, components, controls, models, electro-hydraulics, and valves. Then, we traveled to the IHA Mobile Lab for live demonstrations and to congratulate Daniel Eriksson (Best Student Paper Award) and Abid Abdul Azeez (Best Presentation Award).
Needless to say, this year’s conference exceeded expectations. Competitors sat at the same table to discuss how research and industry can help meet each country’s net-zero targets. And attendees unanimously agreed that networking was one of the best parts of the conference.
“I can speak many languages, but our common language is fluid power,” said Minav.
We’re all looking forward to reconvening at Tampere University in 2027 to recap how far we’ve come and where we’ll go next. DW
Rachael PasiniOVER 25 YEARS’ EXPERIENCE WITH MANUFACTURING AND SOURCING OF MATERIAL, SUB-ASSEMBLIES AND FULL TURNKEY PRODUCTS.
• PRODUCTS: We offer component manufacturing, engineering, sourcing, custom component manufacturing. Kingway offers components and subassemblies all the way to full box builds.
• LOGISTICS: Kingway can help develop a custom Logistics plan to meet your needs including Expedited Air Freight, Sea Freight and Domestic Warehousing.
• VISION STATEMENT: Kingway Electronics offers Direct Sourcing and Customized Logistics Management by utilizing our 25 plus years of relationships and experience to deliver better Pricing, Shorter Lead Times with the Goal of Maximizing our customers profitability.
What you need to know about
standards
Here’s the lowdown on new U.S. and EU electric motor e ciency standards — and how next-generation CAD can power compliance.
Cartesian robots with the right design upgrades can assume manual transfer operations.
Countries take holidays at di erent times of the year, and the whole world can face downtime during wars and pandemics. However, outcomes from screeching halts can inform future production to make impactful use of IoT data and systems.
EDITORIAL
VP, Editorial Director
Paul J. Heney pheney@wtwhmedia.com @wtwh_paulheney
Managing Editor
Mike Santora msantora@wtwhmedia.com @dw_mikesantora
Executive Editor
Lisa Eitel leitel@wtwhmedia.com @dw_lisaeitel
Senior Editor
Miles Budimir mbudimir@wtwhmedia.com @dw_motion
Senior Editor
Mary Gannon mgannon@wtwhmedia.com @dw_marygannon
Senior Editor
Rachael Pasini rpasini@wtwhmedia.com @WTWH_Rachael
Associate Editor Heather Hall hhall@wtwhmedia.com @wtwh_heathhall
CREATIVE SERVICES
VP, Creative Services
Mark Rook mrook@wtwhmedia.com @wtwh_graphics
Senior Art Director
Matthew Claney mclaney@wtwhmedia.com @wtwh_designer
Art Director
Allison Washko awashko@wtwhmedia.com
Senior Graphic Designer
Mariel Evans mevans@wtwhmedia.com @wtwh_mariel
Graphic Designer
Shannon Pipik spipik@wtwhmedia.com
@wtwh_shannon
Bruce Sprague bsprague@wtwhmedia.com
WEB DEV / DIGITAL OPERATIONS
Web Development Manager B. David Miyares dmiyares@wtwhmedia.com @wtwh_webdave
Senior Digital Media Manager Patrick Curran pcurran@wtwhmedia.com @wtwhseopatrick
Front End Developer Melissa Annand mannand@wtwhmedia.com
Software Engineer David Bozentka dbozentka@wtwhmedia.com
DIGITAL MARKETING
VP, Digital Marketing Virginia Goulding vgoulding@wtwhmedia.com @wtwh_virginia
Digital Marketing Manager Taylor Meade tmeade@wtwhmedia.com @WTWH_Taylor
Digital Marketing Coordinator Meagan Konvalin mkonvalin@wtwhmedia.com
Digital Marketing Coordinator Francesca Barrett fbarrett@wtwhmedia.com
Webinar Coordinator Emira Wininger ewininger@wtwhmedia.com
Webinar Coordinator Dan Santarelli dsantarelli@wtwhmedia.com
FINANCE
Follow the whole team @DesignWorld Medical Design & OUTSOURCING
Controller Brian Korsberg bkorsberg@wtwhmedia.com
Accounts Receivable Specialist
Jamila Milton jmilton@wtwhmedia.com
EVENTS
Events Manager
Jen Osborne josborne@wtwhmedia.com @wtwh_jen
Events Manager
Brittany Belko bbelko@wtwhmedia.com
Event Marketing Specialist
Olivia Zemanek ozemanek@wtwhmedia.com
VIDEO SERVICES
Videographer
Garrett McCafferty gmccafferty@wtwhmedia.com
Videographer
Kara Singleton ksingleton@wtwhmedia.com
PRODUCTION SERVICES
Customer Service Manager
Stephanie Hulett shulett@wtwhmedia.com
Customer Service Representative
Tracy Powers tpowers@wtwhmedia.com
Customer Service Representative
JoAnn Martin jmartin@wtwhmedia.com
Customer Service Representative
Renee Massey-Linston renee@wtwhmedia.com
Customer Service Representative
Trinidy Longgood tlonggood@wtwhmedia.com
Digital Production Manager
Reggie Hall rhall@wtwhmedia.com
Digital Production Specialist
Nicole Johnson njohnson@wtwhmedia.com
Digital Design Manager
Samantha King sking@wtwhmedia.com
Marketing Graphic Designer
Hannah Bragg hbragg@wtwhmedia.com
Digital Production Specialist
Elise Ondak eondak@wtwhmedia.com
HUMAN
Vice President of Human Resources
Edith Tarter etarter@wtwhmedia.com
Accurate drilling has historically required expensive static machine tools or skilled operators to perform the task manually. These days, aerospace companies embrace industrial robots and collaborative robots (cobots) because they are more flexible, adaptable, and less costly than CNC machine tools.
However, commercial industrial robotics systems can struggle to perform critical manufacturing operations, such as drilling, laser welding, light machining, and precise assembly. They require higher robotics intelligence to deliver accuracy and repeatability and to work in path programming mode rather than point-to-point.
Xaba, Toronto-based developer of AI-driven robotics and CNC machine controllers, created a proprietary physics-informed deep artificial neural
network model, xCognition, which aims to solve this challenge.
Lockheed Martin recently collaborated with Xaba to evaluate the automation of crucial manufacturing operations using industrial robots integrated with xCognition. The team identified a use case for a typical robotics work cell used in any aerospace factory to test how xCognition’s “synthetic brain” could empower a commercial robot with greater intelligence and understanding of its body and the task it is about to execute while achieving required quality and tolerances.
The test consisted of two phases:
• Phase 1: Assess the robot’s performance in maintaining accurate and consistent trajectory positioning with and without xCognition.
• Phase 2: Perform drilling tests on an aluminum test plate with specified positional tolerances.
Based on collected data, xCognition improved the accuracy and consistency of the commercial robot by a factor of 10. The test showed how industrial robotics augmented with xCognition can perform crucial manufacturing operations that until now have been exclusively done by more expensive and less flexible CNC machines.
“The accuracy performance of a robotic system limits the type of process it can perform based on the cost e ciency of the accuracy hardware,” said Matthew Galla, applications engineer sta for Lockheed Martin’s Aeronautics business. “The test with the xCognition controller allows us to rethink how we can accelerate innovation in manufacturing.”
Unlike analytical AI used for predictive modeling, industrial AI focuses on the physical world. It can model and drive a vehicle, a complex machining center, and more intricate industrial applications. xCognition empowers commercial robots and cobots with a “synthetic brain” that integrates seamlessly to make robotics more consistent, robust, and autonomous, significantly increasing their applications and throughput. DW
Lockheed Martin | www.lockheedmartin.com
Better
We use 100% virgin urethane (no regrind waste). Makes stronger, longer lasting belts.
« Abuse Resistant Belts work where others fail.
« Super Strong Joints are virtually unbreakable.
« High Tension Belts move heavier loads.
« HEHT black belts double capacity.
« Low cost, highly efficient, elastic flat belts.
Split Line-shaft Spools
l High precision. Reasonable price.
l Easy to install. Zero downtime.
Dura-Belt
Round, Flat, Vee and Poly-V Belts and Pulleys
800-770-2358
614-777-0295
Fax: 614-777-9448 www.durabelt.com
Sustainability has moved from a nice-to-have benefit to a must-have feature in products across every industry. In its 2022 Sustainability Report, Regal Rexnord reiterated its intention to “innovate with purpose” to meet modern challenges while reducing resource consumption and improving energy e ciency.
In alignment with this intention, the company launched the Rexnord 1104 FlushTop MatTop Chain for high-speed critical conveying, pressureless combiners and decombiners, and mass flow conveyor applications in the food and beverage industry. The new conveyor chain is an innovative upgrade for Rexnord 1000 Series and System Plast 2250 FlatTop and FlushGrid chains.
The new product combines the container stability benefits of the FlatTop surface with the cleanability of the FlushGrid chain, allowing operators to run conveyance lines dry, saving both water and lubricant with proper cleaning. The 1104 belt features a low coe cient of friction capable of handling all container types, including aluminum cans, glass, and PET bottles.
The series can simplify maintenance and inventory management and reduce the number of SKUs necessary for lines by providing the same functionality that previously required both FlatTop and FlushGrid surface tops.
The FlushTop chains can be installed in original industry standard conveyor setups using the new Rexnord 1100 Series Sprockets. The new sprockets feature a more robust design for improved product engagement and stability versus legacy Rexnord 1000 Series chains. The sprockets will also work with Rexnord 1040 and 1060 Series, allowing for consistent sprockets in connecting side-flexing areas. DW
Regal
www.regalrexnord.com/1104
Engineers seek more design freedom to build equipment for hygiene-sensitive applications. As such, igus launched an all-new sample box for its igubal Food Contact (FC) spherical bearing product line. The new sample box allows machine builders in the food and beverage industry to evaluate the quality and advantages of food-compliant bearings firsthand. The box contains sample pillow block bearings, fixed flange bearings, rod ends, clevis joints, a magnet, and the newly introduced coupling joint.
Like all igubal FC products, these bearings incorporate optically and magnetically detectable housings made from FDA-compliant igumid FC material, meeting U.S. Food and Drug Administration guidelines and European Commission Regulation EU 10/2011. Due to the high-performance polymers, the new spherical bearing is also dry-running, maintenance-free, vibration-dampening, corrosion-free, and in combination with a spherical ball, suitable for compensating misalignments.
“When selecting the right spherical ball, customers can choose between several materials, depending on their needs,” said Dennis Ste en, product manager for igubal Spherical Bearings at igus. “The insert made of the material iglide A181 can be used to comply with the strict FDA guidelines. The material iglide FC180 guarantees 100% detectability. Both also meet the EU 10/2011 standard for direct food contact. Customers can also choose a stainlesssteel version if a higher tightening torque is required due to the spherical ball.”
As with all igus products, they work without external lubricants, which rule out contamination. In addition, cleaning processes can be carried out regardless of the bearings. DW igus | www.igus.com/info/fda-compliant
Packaging operations are anything but simple. Every day, millions of food items, commodities, and other products must be packaged, sealed, transported, unloaded, mixed, stored, recycled, and sorted, to name a few. To maintain high levels of throughput, packaging machines must be highly adaptable — able to handle fast changeovers, frequent product changes, and a variety of materials.
Meeting these challenges headon is StarterSET, a modular product and software bundle that o ers the functionality of specific packaging machines, including vertical form fill and seal (VFFS) machines, palletizers, case packers, and more. In addition to including all the basic hardware and
software modules for implementation — all of which fit together in a seamless, intelligent way — each StarterSET is extendable, enabling OEMs to build special-purpose machinery, meet customer-specific requirements, and remain adaptable in an increasingly competitive market.
Each package includes preselected drive and control components from the MOVI-C modular automation system, such as servomotors, planetary servo gear units, servo inverters, and higherlevel controllers. Each set also contains software modules that are prewritten and focus on parametrization. Also, a state and mode manager, called MOVIKIT Automation Framework, complies with the Packaging Machine
Language (PackML) standard. I/O modules and HMI for easy machine operation round o the StarterSETs.
Users can also extend StarterSET packages to meet unique or specific requirements, reducing their configuration time, project duration, and overall costs. For example, OEMs can easily add additional motion axes, condition monitoring systems, integrated safety technology, energy modules, or increased controller processing power. No matter the iteration, each kit maintains high product quality and provides fail-safe performance.
At the heart of each StarterSET is the MOVIKIT software bundle consisting of preprogrammed modules embedded in the MOVI-C controller and o ering
various simple to complex drive and motion control functions. In a vertical FFS machine, for example, the software modules enable users to precisely adjust and monitor machine processes related to speed, temperature, and film tension. In fact, these capabilities can dramatically reduce the time it takes to develop and create a machine sequence program.
Here’s a quick overview of how StarterSET software modules make various FFS machine functions possible via simple parameterization:
• Unrolling the film: The software precisely controls how the packaging material is unwound from the rolls and fed into the packaging process. Users control material tension directly via the torque or dancer position.
• Dosing: The software synchronizes volumetric filling in real time — using an auger, for example. Users simply parameterize the filling variant, along with cyclesynchronous actuator control.
• Moving the sealing bars: The StarterSET synchronizes the sealing bar and tongs and moves the sealing bar in relation to the printmark. Once the sealing time has elapsed and the tongs have opened, the bar returns to the starting point.
• Moving the tongs: The software precisely controls the opening and closing of the sealing tongs and maintains the proper machine pressure when sealing the bags.
• Controlling print marks: Via the StarterSET software, the film drive automatically detects print marks and monitors the sealing bar’s synchronized movement. This capability ensures images are properly positioned on bags, demonstrating the precise interplay between servo drives.
In addition to these vertical FFS machine functions, software modules can easily be configured for individual applications due to StarterSET’s use of open-source code. This combination of modularity and flexibility saves users a considerable amount of time. And developers don’t have to waste time programming basic functions.
StarterSET also supports reliable motion control functions for recurring movements and motion profiles, such as synchronizing the flying saw and sealing station with the continuous supply of film. In the past, these functions could be implemented in the drive, motion controller, PLC, or higher-level controller. Due to the various software licenses involved, users had to know in advance where the intelligence in their machine ultimately resided. However, StarterSET moves away from this classic yet cumbersome machine automation pyramid, o ering a comprehensive software bundle tailored to the machine.
Constant Force Lead Screw applies uniform pressure to the nut at all stages of travel along our quality CNC rolled lead screws. World class NEMA motors combined with an integrated lead screw make for one of the most accurate lead screw assemblies on the market.
Our miniature ball screw assemblies combine fine leads with small screw diameters, and utilize a compact internal ball return system to yield high precision linear motion for a range of small-scale applications. In addition, our ball screws are precision-rolled, making them a critical asset to laboratory machines, medical devices, and mechatronic applications.
screws and ball screws in a timely manner to keep your production rolling. Request a FREE product sample
Hydrogen will play a major role in transitioning to a carbonneutral world — both as a fuel source and a storage medium for surplus energy from renewable sources. However, due to its inherent characteristics, hydrogen is di cult to seal.
The challenges include permeation and leakage, as hydrogen is the simplest element with the smallest molecular structure. Another challenge is rapid gas decompression (RGD), where hydrogen in a high-pressure system can be absorbed into a seal. If the pressure in the system is suddenly relieved, gas trapped in the seal can expand, potentially causing the seal to blister and crack as the gas tries to escape.
Also, seals for di erent hydrogen systems need to withstand seriously tough environments, including high pressures of up to 14.34 psi (1,000 bar) — for example, in highpressure valves — and extremely low temperatures down to -418° F (-250° C) — for example, in liquid hydrogen storage and transportation.
To alleviate these challenges, Trelleborg Sealing Solutions recently launched the H2Pro range of sealing materials for every application of the hydrogen value chain — from production, transport, and storage to end use. The solution range includes two new materials specially engineered for hydrogen applications: H2Pro EBT25, a new ethylene propylene diene monomer (EPDM) for high-pressure
environments across a wide range of temperatures, and Zurcon H2Pro ZLT, a unique thermoplastic polyurethane (TPU) for very low temperatures.
All H2Pro materials are designed specifically for application-specific wear and extrusion properties and are validated to key industry standards in a range of challenging conditions typical of hydrogen environments. Trelleborg uses advanced testing rigs to assess materials for oxygen and ozone aging, hydrogen compatibility, leakage, permeation, the ability to withstand RGD, and compliance with relevant international standards.
Zurcon H2Pro ZLT has very low permeability and displays a superior ability to withstand RGD. It has a wide operating service temperature range, outstanding low-temperature capabilities, displays excellent extrusion and wear-resistance properties, and complies with Regulation (EC) 79/2009, SAE J2600, and ANSI CHMC 2. It can be produced as O-rings for static sealing on
valves, filters, refueling nozzles, pumps, connectors, and fittings and as U-cups for static and dynamic applications such as valve stems, actuators, and regulators.
H2Pro EBT25 demonstrates a superior ability to withstand RGD and features low permeability, a wide operating service temperature range, 85 Shore A hardness, and excellent extrusion resistance. It is compliant with Regulation (EC) 79/2009, SAE J2600, and ANSI CHMC 2, and can be manufactured as O-Rings for static sealing on valves, filters, refueling nozzles, pumps, connectors and fittings, and custom molded parts and frame seals for fuel cells and electrolysis equipment.
H2Pro materials are also available in a range of other compounds and seal profiles, including:
• Turcon polytetrafluoroethylene (PTFE) and thermoplastic compounds for use as Varilip lip seals
• V-stack seals for use in static and dynamic applications with cryogenically compressed hydrogen and liquid hydrogen (LH2)
• FKM seals for blue hydrogen
• Lower-hardness EPDM compounds and silicone compounds for lowerpressure applications
• Metal seals for static LH2 applications
• Wear-resistant composite bearings and piston rings for compressor applications
Trelleborg Sealing Solutions
www.trelleborg.com/en/seals
The advantages of using cloud-based technologies continue to grow, enabling adopters to o er more immediate value to the industry.
Tri Tech Automation, an industrial automation systems integrator focused on hybrid and process industries, faced a problem that far too many companies face: customers expecting products to be delivered faster. To meet these expectations, Tri Tech needed to adopt a modern design approach that was more e cient, flexible, and intuitive.
Furthermore, with a dispersed workforce, Tri Tech was keen to explore novel ways of collaborating to reduce the time required for design, programming, and testing while maximizing code reuse through modularization.
“We need to work together, across locations and in real-time. If two people are working in the same file, we need a way to ensure that we don’t lose changes or cause rework,
which wastes resources and introduces the potential for errors,” said Jacob Becker, Controls Team Lead at Tri Tech.
The early bird adopter gets the worm
Both internally and externally, Tri Tech seeks to enhance productivity by exploring diverse approaches, including determining the optimal hardware strategy to mitigate supply chain problems, implementing modular design to facilitate code reuse, and emphasizing technology and workflows that minimize barriers between dispersed locations.
While searching for the right solution to fit their needs, Tri Tech had the opportunity to become an early adopter of what was then a soon-to-be-released solution from Rockwell Automation. There is an inherent risk to adopting technology before the vendor has solved the various kinks that
With over 2 million cords and components in stock, and same day shipping on all in-stock products, Interpower takes the anxiety out of ordering power cords. Besides, our cords have already dealt with their stress after having been tested throughout each stage of production.
Our cord sets ship straight from the factory when and how you want them—hanked, coiled, tied, bagged and individually boxed? Need 1-D or QR barcodes for easier warehousing, a serial number for each cord?
• No supply chain gridlock
• Customized lengths & colors
• No minimum orders
inevitably happen with innovation. Nonetheless, it was advantageous for Tri Tech to gain the opportunity to influence subsequent iterations of the product and gain valuable experience.
Steve McNamer, Senior Controls Engineer for Tri Tech, was ready to try the new product, FactoryTalk Design Studio, a cloud-based, industrial automation design tool available from Rockwell Automation through the FactoryTalk Hub.
“It’s our responsibility to bring innovative ideas to customers. They trust us to be the experts on the technology and it excites us to try new things so we can move forward in better ways,” said McNamer.
Tri Tech was drawn to FactoryTalk Design Studio for two main reasons. First, the FactoryTalk Smart Objects feature allowed for the creation of more modular systems, facilitating structured design and reuse of content through an integrated library. Second, the platform's aim of facilitating simultaneous collaboration among multiple individuals seemed achievable with the integrated git technology, which enabled Tri Tech's engineers to manage conflicting edits and monitor project history.
“Before trying FactoryTalk Design Studio, we were interested in collaborative third-party tools featuring modularity and revision tracking,” continued Becker. “We needed a cloud-based solution to reduce the amount of overhead and software management. This is a problem we wanted to solve, and the opportunity to be an early
The advantages of using cloud-based technologies continues to grow, enabling adopters to o er more immediate value to the industry. As a reflection of the increasing adoption of cloud technology in the manufacturing space, automation technology vendors are releasing more Software-as-a-Service (SaaS) products, one of which is FactoryTalk Design Studio. SaaS products enable faster iteration since the product is managed in the cloud directly by the vendor, as Tri Tech discovered.
“There are many benefits of being an early adopter,” added McNamer, “including how our feedback is contributing to future iterations of the product.”
The adoption of new technologies is necessary to keep up with the evolving workforce and their working styles. As the next generation of automation professionals enters the workforce, they bring with them high expectations for software that is intuitive and flexible. Meanwhile, as experienced employees retire, systems integrators like Tri Tech will face increasingly di cult challenges in finding qualified replacements to fill those roles. With its support for scalable teams and varying skill sets, FactoryTalk Design Studio ensures that Tri Tech can e ciently use its resources and collaborate seamlessly, leading to enhanced productivity and accelerated innovation. Additionally, Tri Tech is now equipped to empower its workforce no matter if they prefer graphical or text-based editing with nextgeneration tools that support both work styles.
“With such a spectrum of employee skills and expectations, it’s going to be even more important to keep things simple and easy to use from day one,” added Becker. “We needed a solution with functionality and intuitiveness that would make it easier to onboard new employees, and it opens the universe of hiring. For example, computer science majors without an industrial automation background can drop into the process and feel comfortable in a familiar environment.”
“The generation retiring, and the generation coming, in have new and di erent expectations of industrial automation,” said McNamer. “The products we use must span all generations and skill levels. That includes even small things, like a feature that allows you to look at a project in graphical editing format but modify the project and work in a text-based format.” DW
www.rockwellautomation.com
Safety and protection top the list of priorities for many when purchasing goods and services. From anti-virus software to car alarms, it seems that everything today comes with a modicum of security, putting consumers’ minds at ease.
Business owners are no exception with many industrial businesses having high-valued goods in their yards and warehouses, such as landscaping, equipment rental facilities, and distribution centers. Anyone who has put their faith in these businesses wants to be reassured that every security measure is taken to protect their prized possessions.
AMAROK, of Columbia, South Carolina, provides perimeter security with solar-powered electric fences and integrated security solutions. AMAROK’s 100% solar-powered electric fences are designed to give customers peace of mind. The fully monitored perimeter stops crime before it happens but delivers a 7000V shock should someone engage. The company is continually looking to innovate and improve its service o ering to give its users the ultimate peace of mind.
Initially, AMAROK’s technology was built by self-wiring a few hundred conductors for its electronics in the field using screw terminals. To streamline its process and be more e ective, the company mass-produced a component that allows all of its units to be wired in-house and then sent into the field.
With over 2 million cords and components in stock, and same day shipping on all in-stock products, Interpower® takes the anxiety out of ordering power cords. Besides, every inflationary dollar aimed at American manufacturing has only made us stronger—we aren’t going anywhere.
WAGO’s TOPJOB S
Terminal Blocks provide a reliable, maintenancefree connection in any environment.
Our cord sets and accessory power systems ship straight from the factory when and how you want them—hanked, coiled, tied, bagged and individually boxed? Need 1-D or QR barcodes for easier warehousing, a serial number for each cord?
New compact KNF NMP 820 diaphragm gas pump offers impressive, efficient flow-to-size performance with exceptionally low noise and vibration.
NMP 820 is ideal for medical point-of-care, medical portable devices, negative pressure wound therapy, non-stationary emission measurement, inkjet printing, and scent diffusion. The brushless four-wire motor variant offers PWM control capabilities.
Learn more at knf.com/en/us/stories-events/news/article/micro-diaphragm-pump-nmp-820
This made wiring easier, and with the color-coding and clear marking solutions, field installation has become much less ambiguous. Screw terminals must be closely guarded and tightened to maintain their connection. Because of this, AMAROK was looking for a new solution that would be relatively lowmaintenance or even maintenance-free.
After many years in business, with lessons learned from previous experiences, AMAROK needed a partner that provided longevity, reliability, and products that could withstand extreme temperatures.
“In most states, we need something that is going to last in extreme environments, whether that be simply temperature, the elements, or a combination of the two,” said J. Bury, VP of Research, Development, and Production for Amarok. Primarily looking for terminal blocks and Ethernet switches, Bury and his associates decided to give WAGO a call to see what solutions they could provide for their production needs.
AMAROK was introduced to WAGO’s TOPJOB S push-button terminal block family. Boasting push-in CAGE CLAMP technology, not only were these terminal blocks maintenance-free but the intuitive orange push buttons made wire termination easy. Another feature that caught Bury’s eye was the marking ability to ensure that wiring inhouse and, in the field, could be communicated e ortlessly.
Technical support would also factor into AMAROK’s decision to team with WAGO.
“We had access to resources at any time, and their support team was helpful in knowing exactly what we wanted to do,” Bury stated.
Of course, cost and supply chain issues were a concern, as they are with nearly every
business today. While these problems may have hampered other companies, there was zero worry with AMAROK and their decision to partner with WAGO. Bury noted that it is an easy relationship, and there haven’t been any such issues to date.
“We’re not concerned about availability or price. We haven’t had to stop production because of lack of products from WAGO like we have with other producers.” He claimed that WAGO’s transparency when it comes to supply and price issues is refreshing and something you don’t get from other companies.
Ultimately, WAGO was able to help AMAROK meet its expectations and has had a hand in doubling its business and helping them grow in new markets. As their needs increase, Bury said there is no doubt that they will move forward with WAGO.
“Our future is wide open with the possibility of PCB solutions, breakers, I/O products for control and data collection…so many opportunities.” Now that they have the confidence in knowing their wiring and manufacturing needs have been met, AMAROK can continue to provide its users with the peace of mind its solutions will protect their property with the ultimate in perimeter security. DW
WAGO | wago.com
All AMAROK’s products, from fences to keypads, are designed and made in-house.
Rooftop heat cables guard against the perilous e ects of ice and snow accumulation. These strategically installed heat cables become hot when an electric current runs through them, and the radiated heat melts snow and ice to allow proper drainage. However, protecting roofs in this way incurs monetary and energy costs.
Powder Watts has developed a patented IoT ecosystem to keep snow and ice from damaging roofs while slashing the cost of powering heat cables. The ecosystem includes a smart rooftop IoT sensor unit, power-switching devices to control and monitor heat cables, and AI to determine the presence of snow and ice. Left unchecked, heavy snowfall on a roof can cause ice dams along the roof’s bottom edge. When that happens, melted snow on the roof’s surface travels backward under shingles and into a structure. The resulting damage can equal tens of thousands of dollars or more for building owners.
According to Powder Watts, sometimes homeowners in snowy climates ask electricians to install thermostats to heat cables to attempt to curtail energy use when temperatures climb above 50° F. Many electricians tend to avoid these jobs because if a thermostat fails or is warmed by sunlight, it can falsely detect warmer weather, shut o heat cables, and allow an ice dam to form.
Thermostats are problematic for another reason. In northern regions,
the air temperature from November to March rarely exceeds 50° F. Despite sub-freezing temperatures, when used correctly, heat cables can e ectively clear channels through the snow along a roof’s edge, meaning a homeowner could temporarily shut o the cables and save power. The challenge is knowing when heat cables have successfully melted drainage channels and when homeowners need to power the cables.
“Electricians, if they even install a thermostat for your heat cables, often set them to turn o the cables when the air temp reaches 50° F or even higher because they don’t want callbacks,” said Thomas Clardy, founder and CEO of Powder Watts. “At 50°, the cables can draw energy into May.”
Clardy and Powder Watts wanted to build and sell technology to eliminate the nearly always-on approach of thermostats and the guesswork by switch-flipping owners. According to Clardy, a smart system relying on IoT technology must employ protocols to
The smart camera, protected by a UVresistant enclosure, is part of a system that sees inside roo op mounds of snow to accurately determine when heat cables need to be on or o . The dualcamera system provides panoramic views of a roof and integrated night vision.
| courtesy of Powder Watts
communicate data e ectively. But the Powder Watts team didn’t like the realworld performance of existing home and business automation protocols.
A smarter approach to snow removal Powder Watts’ solution includes a smart rooftop sensor and AI to monitor heat cables. With its expertise in embedded and networking technology, Grid Connect’s engineers helped Powder Watts develop a smart switch to enable the system to power on and o heat cables based on the conditions that the rooftop smart sensor and AI were interpreting, including the amount of ice and snow and weather conditions, such as humidity and temperature. To do this,
Grid Connect’s engineers assisted in developing a 30 A, 240 V switch to Powder Watts’ specifications that building owners could control with the Powder Watts mobile app.
Grid Connect also manufactured a version of their 20 A Smart In-Wall Outlet to Powder Watts’ specifications. This allows for energy monitoring and independent socket switching, giving homeowners precise and individual segment control of their new or existing 120 V heating cables.
The IoT system consists of five elements: a rooftop smart sensor; a smart hub receiving and sending signals; a smart switch measuring energy and turning on and o the power to the heat cables; AI to evaluate conditions and make switching decisions; and the Powder Watts App to enable full customer insight and control. Each element communicates with the other using a long-range protocol. According to Clardy, LoRaWAN didn’t have the throughput to handle the HD images taken by the rooftop smart sensor.
“Nobody made a long-range high-amp smart switch capable of monitoring energy,” said Clardy. “We didn’t want to run our system on WiFi, so Grid Connect incorporated our long-range protocol leading to outstanding performance.”
Ultimately, Grid Connect helped Powder Watts bring a robust, commercially available IoT switch to market. The Powder Watts system stands up to not only -40° F but also extreme summer heat and severe hail. As for savings opportunities, Clardy said there are approximately 44 million runs of heat cable across the United States. The owners of such heat cables spend hundreds of dollars monthly more than necessary to protect their roofs. Powder Watts’ smart technology typically provides a return on investment in 12 to 24 months.
“This is enhanced further by power company rebates and tax incentives. Compare that with solar payback times and for similar amounts of energy. If you own a home or business and you’re spending
Inside the smart camera is a 30 A, 240 V switch measuring energy and turning on and o the power to the heat cables.
| courtesy of Powder Watts
Our new AC inverter-duty IP-69K rated hollow shaft gearmotors are fully watertight for rigorous daily washdowns. They deliver maintenance-free performance where standard gearmotors can’t survive.
$200 or more per month to power your heat cables, Powder Watts can reduce that by up to 90%,” said Clardy. “It’s exciting to see American engineers creatively solve complex challenges in short timeframes.”
Smartly switching these high-draw heat cables on and o also plays a role in shedding unneeded electric loads o the grid. The cumulative e ect of millions of miles of heat cables running across hundreds of thousands of homes for months on end means wasted energy and unnecessary grid drain. Powder Watts aims to work with a variety of utilities that want to manage these loads e ectively and safely while keeping energy costs in check.
“We help companies and homeowners meet their monitoring
goals for safety and their energy goals for climate and cost,” said Clardy. “Why rely on 1970s thermostat technology or an owner’s watchful eye?”
This season Powder Watts is expanding their energy-saving technology into the heated driveway, walkway, and steps market. These heated surfaces provide great convenience and safety for people but come at great energy expenditure. As with heat cables, using smart sensing technology combined with AI can direct the heating only when needed, resulting in savings for customers and the planet. DW
Powder Watts | powderwatts.com
Grid Connect | gridconnect.com
Grid Connect made a version of its 20 A Smart In-Wall Outlet for energy monitoring and independent socket switching, giving homeowners control of their 120 V heating cables. | courtesy of Powder WattsU.S.
Global electronics manufacturers face an ever-present challenge. That is, how to make the motors in their electrically powered devices compliant with new minimum e ciency performance standards (MEPS) across crucial markets. Two of the largest regional economic blocks are the U.S. and European Union. With an eye on energy savings, the governing bodies of the world’s largest economy and largest free-trade zone continue to advance design guidelines to boost electric motor e ciency.
That is largely motivated by the fact that outdated electric motor systems account for over 40% of the world’s electricity consumption.
What are the key details of U.S. and EU minimum energy performance standards frameworks? How can companies design products that comply with these MEPS electric motor rules? Here we’ll look at a four-part breakdown:
• EU Ecodesign regulations
• U.S. MEPS
• U.S. and EU MEPs: Notable di erences
• Motor CAD for MEPS compliance
To start in the EU, in 2019 the European Parliament passed ecodesign legislation that established a framework for phasing in electric motor e ciency requirements. These new MEPS regulations have a broad scope — covering motors with a power range from 0.12 kW to 1,000 kW — and apply to everything from home appliances to industrial air conditioning. The EU’s ecodesign measures are also guided by the International Electrochemical Commission’s (IEC) e ciency classes, which range from IE1 (Standard E ciency) to IE4 (Super-Premium E ciency).
In July 2023, the EU became the first region in the world to make the international IE4 e ciency class mandatory for some categories of electric motors.
The European Commission’s motor design initiatives also correspond to its energy label framework for electronics and home appliances — which sets a comparative scale from A (most e cient) to G (least e cient). As part of its ecodesign energy legislation, the EU
The
and EU are implementing new minimum efficiency performance standards (MEPS) for electric motors— here’s the lowdown on the standards and how next-generation motor CAD can power compliance.BRIAN CASEY • CEO • ECM PCB STATOR TECHNOLOGY
will periodically rescale these labels to eliminate the worst performing devices from the market.
Altogether, the European Union expects this framework to erase 40 million tons of carbon dioxide emissions annually. Furthermore, the EU projects that its ecodesign motor regulations will save European households $22 billion in energy costs by delivering 110 TWh of annual energy savings by 2030. The latter is equivalent to the current yearly electricity consumption of the Netherlands.
To put that in context, by simply mandating more e cient motors, the EU can save as much energy as its seventh largest economy currently uses in a year.
Similar to its EU trading partner, the U.S. has worked diligently on its own electric motor e ciency regulations with a primary focus on improving energy e ciency and reducing carbon emissions. These
regulations encompass a wide range of motors, from smaller appliances to larger industrial equipment.
While the U.S. regulations are not entirely identical to the EU's ecodesign legislation, they share similarities in their approach to promoting energy-e cient motors. The U.S. government was the first in the world to set minimum e ciency performance standards for motors and has actively collaborated with international bodies, such as the IEC, to adopt e ciency standards that align with global best practices.
In 2007, the U.S. raised its minimum e ciency performance standards to the equivalent of IE3 (Premium E ciency). In 2015, the U.S. broadened that scope to require IE3 standards for small polyphase motors from 0.18 kW up to 2.2 kW and IE2 standards for single-phase motors.
In May 2023, the U.S. Department of Energy (DOE) announced new energy e ciency initiatives that focus specifically
The EU’s ecodesign measures are guided by the IEC e ciency classes, which range from IE1 (Standard E ciency) to IE4 (Super-Premium E ciency). The motor design initiatives also correspond to energy label frameworks for electronics and home appliances—which sets a comparative scale from A (most e cient) to G (least e cient).
| Courtesy of European Commission
on electric motors and appliances. The proposed standards for new dishwashers and beverage vending machines, along with the final standards for electric motors, are part of Congressionally mandated actions aimed at conserving energy and water while reducing harmful carbon emissions.
Though the exact design requirements have not been released, the DOE’s new standards for electric motors will come into e ect in 2027.
The DOE projects these forthcoming guidelines to yield significant benefits. Over the next 30 years, American consumers are anticipated to save up to $8.8 billion in utility bills and carbon dioxide emissions are projected to be reduced by approximately 91.7 million metric tons. This reduction is equivalent to the annual emissions of around 20 million gasoline cars.
These initiatives represent the DOE's latest e orts to promote appliance
Are you looking for a rotary encoder that is easy to install and reliable to operate? Then meet the new R35i and R35iL models from RENCO. Once you’ve used their built-in mounting aid for fast and easy installation, simply push a button to electronically adjust the motor commutation
signals. Afterwards, rest assured in dependable operation thanks to features for monitoring and diagnostics never before implemented in an incremental rotary encoder. That’s what makes these encoders the ideal motor feedback solutions for stepper and BLDC motors.
e ciency, in line with directives from the U.S. Congress, while simultaneously addressing the climate crisis and providing cost savings for American families and businesses.
The MEPS motor regulations in the EU and the U.S. have some notable di erences. In the EU, the regulations are established under ecodesign legislation, focusing on a broad scope of electric motors from 0.12 kW to 1,000 kW, and guided by the IEC e ciency classes ranging from IE1 to IE4. By the end of 2023, the EU will make the IE4 e ciency class mandatory for certain motor categories. Additionally, the EU's motor design initiatives are complemented by an energy label framework, rating devices from A (most e cient) to G (least e cient) and periodically eliminating poorly performing products.
On the other hand, the U.S. follows its own motor e ciency performance standards, having raised standards to the equivalent of IE3 in 2007. The U.S. regulations encompass a wide range of motors and have been expanded to include smaller polyphase and singlephase motors. While the U.S. recognizes national and Canadian testing standards, there's ongoing consideration for adopting the IEC test standard.
Though timelines for electric motor MEPS mandates in both regions di er —
with the EU enacting its latest directives more rapidly than the U.S. — these markets share a common trendline. The United States and the European Union are both on a path to continue strengthening electric motor e ciency requirements as part of their 21st century energy policies.
When it comes to how electronics manufacturers that sell in the U.S. and EU convert hundreds of product lines with electric motors to comply with MEPS, there are still a lot of unanswered questions. Clearly, regulators in both markets owe industry actors more details on engineering requirements, testing, and enforcement. Expect those specifics to be forthcoming.
In the meantime, as an overarching point, the first answer to the question of electric motor MEPS compliance in the U.S. and EU lies in accepting that past practices can’t power the future. DW
ECM PCB Stator Technology pcbstator.comCartesian robots are a suitable choice for depalletizing applications. Such robots consume less floor space than an equivalent six-axis robot and allow access for the execution of manual operations when needed.
Cartesian robots with the right design upgrades can assume manual transfer operations.
Manufacturing and packaging operations using manual material or parts handling operations can reap immediate benefits from automation with long-travel Cartesian robots having custom end-of-arm tooling (EoAT) and advanced sensing capabilities. These robots can support a variety of machines to perform otherwise manual tasks such as machine tending or transferring in-process parts.
Cartesian robots consist of two or more coordinated linear positioning stages … so they may not be the first thing that comes to mind if a design engineer is new to automation. Many equate robots with the six-axis articulated-arm robotics that industry increasingly applies on factory floors. Even experienced automation engineers may give Cartesian robots short shrift … focusing attention on sixaxis models, yet ignoring the benefits of a long-travel.
Cartesian system can be a costly
mistake — especially in applications requiring the robot to:
• Tend multiple machines
• Reach long lengths
• Perform simple and repetitive operations.
For good reason, articulated arm robots are prominent in myriad automated manufacturing and packaging facilities … especially in electronics assembly and the medical industry. When properly sized such robotic arms can handle large payloads with the flexibility to perform many di erent automated tasks commanded by programming (and complemented by end-of-arm tooling changes). But six-axis robots can be expensive and require high robot density. The latter is a term that indicates a facility will likely need a separate robot for every one or two packaging machines. Of course, there exist larger and more expensive six-axis robots with reaches to serve more than
a couple machines, but even these are suboptimal solutions because they force plant engineers to position machines around one very large robot. Articulated arm robots also necessitate safety guarding; consume valuable floor space; and programming and maintenance by skilled employees.
Cartesian robots outperform sixaxis robotic options in large part because they reduce the required robot density. After all, one long-travel Cartesian transfer robot can tend multiple machines sans the need for rearranging machines around the robot.
Transfer robots installed above the machines they tend consume no floor space … which in turn reduces safety-guarding requirements as well. Plus, Cartesian robots require little programming and maintenance after initial setup.
One caveat is that the capabilities of Cartesian robotics systems widely vary. In fact, if engineers research Cartesian robots online, they’ll find many smaller systems optimized for pick-and-place operations on production or assembly machinery. These are essentially linear stages built into o -the-shelf Cartesian solutions — very di erent than the transfer robots useful in larger operations and needing to satisfy the following parameters.
Long travels: Any robot purchased to tend multiple large machines must have strokes to 50-ft or more.
Multiple carriage and custom endof-arm tooling: Long transfer robots are maximally e ective when fitted with multiple independently acting carriages to travel the main axis … allowing a given Cartesian robot the ability to do the work of many. Magnifying this productivity is purpose-built tooling to handle goods more e ectively than o -the-shelf EoAT such as vacuum or finger grippers. In many cases, custom EoAT can also simplify the designs of material handling systems working in conjunction with the Cartesian robot.
Simplified control architecture: Some newer Cartesian robots eschew traditional control architectures based on separate motors, drives, and controllers for integrated servomotors (complete with servodrives) to nix the need for a control cabinet. The most complex Cartesian-robot applications may still demand a traditional architecture … but integrated servomotors deftly handle the point-topoint motion control requirements of most Cartesian robots.
When a design engineer can use integrated servomotors, the latter can help maximize the cost advantage of a Cartesian-based automation.
Some long-travel robot transfer systems feature a moving-motor design (in lieu of a conventional recirculating belt system). Motor weight is no issue. It’s true that engineers frequently choose belt-driven stationary-motor designs to minimize the moving payload … but when Cartesian robot lengths reach 4 m, the belt’s weight typically exceeds that of the moving motor.
Selective use: Because Cartesian robots mount above or behind the machines they tend, they also allow users to run the machines manually when needed — for example, for a short run of a special size. This selective use is di cult with floormounted six-axis robots that can block access to machines.
Some Cartesian robots o er strokes exceeding 50-ft even while delivering speeds to 4 m/sec. Standard carriages might include a dual-belt drive technology; some other carriages contain an upper drive belt that continuously loops within. The latter prevents belt sag in inverted or cantilevered arrangements and allows multiple independent carriages to concurrently operate on an axis.
Long belts complicate Cartesian robot design, as they degrade driveline sti ness (which in turn degrades performance). That’s because maintaining a given tension value
on long belts is challenging … and (making matters worse) belt tension is asymmetrical and variable. The issue renders long recirculating belts an underperforming, finicky, and costly choice for accurate positioning.
In contrast, moving-motor linear stages keep belt lengths short and tight and housed within the carriage so that they can respond to encoder-informed controls. Accuracy is maintained regardless of Cartesian transfer-system length … whether 4 m or 40 m.
Long-travel Cartesian robot transfer units work in feeding, cartoning, and tray-forming applications and can handle palletizing and depalletizing operations. Consider produce packaging. In a recent application for an agricultural packaging company in California’s Central Valley, one manufacturer supplied long-travel transfer robots to seamlessly integrate with the existing IPAK tray-former system. Each robot
Banner’s In-Series Diagnostics (ISD) ensures reliable fault detection, monitors safety networks, and reduces downtime for improved operational reliability.
tends up to four machines at a time, filling them with stacked sheets of corrugated cardboard. The three-axis gantry robots are based on heavyduty belt-driven linear servomotor stages for limitless travel lengths, independently moving carriages, and the ability to mount the stage in any orientation. The longest axis on one such robot runs over the bank of tray formers with a stroke exceeding 50-ft.
To deliver sheets of corrugated cardboard into the four tray-forming machines, a robot first picks a load of cardboard from a custom-built dock holds corrugated cardboardsheet pallets. The robot then delivers a cardboard load to each tray former. Thanks its speed (to 4 m/ sec) the robot can easily pace four tray formers — even at an output to 35 trays per minute.
Safety guarding uses overhead sliding gates and sensors that rise from tended machines to fence the robot as needed for a solution that’s less costly than that for floor-mounted six-axis robots.
Also included in this system are all the controls and custom EoAT capable of working with stacks of corrugated sheets that vary unpredictably in height and weight. The tooling can handle payloads to 50 kg sans issue. The solution relieves operators who once had to lift cardboard bundles from pallets and lean over to put them into the forming machines. Automating these tasks has freed personnel to focus on less grueling work.
Large transfer robots are just one example of what’s possible with Cartesian robot systems in packaging settings. Some suppliers have also
developed palletizing and depalletizing systems based on similar Cartesian approaches. All such robots employ three linear stages fitted with sensors, controls, and end-of-arm tooling for maximally effective and efficient packaging automation. DW
Bell-Everman
Shown here is a Bell-Everman Multi-Axis ServoBelt linear system.
Countries take holidays at different times of the year, and the whole world can face downtime during wars and pandemics. However, outcomes from screeching halts can inform future production to make impactful use of IoT data and systems.
With a real-time communication system, inexperienced workers can receive instructions for daily tasks, troubleshooting, and product changeovers to boost training and factory productivity.
| Dreamstine
"Golden Week" refers to a collection of consecutive national holidays in Japan and China that creates extended time o from work.
(This is not to be confused with Ohio’s former early voting period allowing residents to register and vote on the same day.) During Japan and China’s Golden Week, employees enjoy a long break while manufacturers risk breaking the bank without adequate planning.
Companies worldwide remember the pangs of prolonged downtime during COVID, and many chose to adopt more automation for lights-out production. Such problems persist as manufacturers continue facing worker shortages and supply chain disruptions.
However, challenge breeds innovation, and there are always lessons to be learned. Arjun Chandar, founder and CEO of IndustrialML, knows this well.
“If you don't have production on the weekends, and you don't have an automated system, then it's lights out on Friday. First thing Monday morning, you don't want to waste time ramping up — you want everything done already,” said Chandar.
The same goes for Golden Week or any planned or unplanned period when sta are scarce.
“This year, Japan’s Golden Week holiday was characterized by a significant influx of travelers and the closure of various businesses due to the easing of COVID-19 measures, posing challenges for manufacturers. The resulting disruption from Golden Week often leads to delays in production, hampered logistics, and decreased e ciency,” said Chandar. “Additionally, ongoing pandemic-related issues, such as high cargo demand, sta shortages, port closures, and limited shipping containers, compound the delays caused by the holiday.”
So, how can manufacturers, especially those with IoT ecosystems, refine operations to smooth out the peaks and valleys?
Machine learning (ML) extends IoT capabilities beyond remote monitoring and control, providing insightful analytics, anomaly detection, real-time optimization, and more. But operations include more than machines — there’s
a people component that’s trending downward as experienced workers retire and post-pandemic shortages remain unreplenished.
“Many people in manufacturing are retiring, and younger people operate under a di erent paradigm where they don’t stay in jobs for long. So, with higher turnover, you're losing a lot of domain knowledge,” said Chandar.
IndustrialML integrates data from various sources, including machine sensors, software, video, and audio. Users interact with the information primarily through three modules: real-time data visualization, no-code historical reporting, and a real-time communication system.
“Whenever something important happens inside or outside of a factory, such as when an order changes or a furnace temperature is too high, we can send a real-time alert to people with instructions on what to do,” said Chandar.
The real-time communication system can simultaneously send alerts from the same event to multiple people via di erent methods. For example, the system can send a message to
a manager via Slack, an operator via a headset, and a salesperson via email to expect a delay or indicate an issue.
“That's where the value proposition of real-time communication comes into play,” said Chandar. “Not only do we have a way to identify the issue, but we also can impart the necessary steps to the right people at the right time so they can address the issue without needing 10 years of experience at the factory or memorizing the steps.”
Chandar admits that the system doesn’t do anything new from a technical perspective but dramatically influences how integrated technology can positively impact the workforce.
“You can't lose 100% of your expertise and still operate the factory. Domain knowledge has to come from somewhere, and somebody needs to maintain the content of the alert policies,” said Chandar. “But my ideal goal is that somebody can run a factory 90% as well after half a year as they would have previously done after five years.”
IndustrialML collects data from a factory’s manufacturing execution system (MES), which tracks each order produced on the floor. The MES system sends the order information and all corresponding nominal settings. For example, data for a steel tube might include the outer diameter, thickness, length, and coating.
Di erent products may have di ering requirements, so optimal machine settings change based on the product in production. For example, the ideal temperature might be 450° F for one product and 430° F for another. Ine ciencies or false alerts can arise if the machines and systems don’t communicate. To prevent discrepancies and make actionable use of disparate data, IndustrialML’s alert policy system can perform comparative alerts to send the right information.
“You don't want to set an alert policy that notifies you when something goes above 450° because that might not apply to everything,” said Chandar. “But if you can set a policy to send an alert whenever the temperature is 15° higher than its planned value, then you're synthesizing the actual value from the sensor with the planned value from the ERP system. Data from disparate datasets can be compared against each other in one setting, and you can legitimately o er real-time communication regardless of what product is being made.” DW
Also Inside: Calculate the carbon footprint of additively manufactured parts
Direct-write 3D printing technology uses a micro-dispenser to precisely deposit nanoscale multi-materials over a substrate and produce complex shapes in layers. The direct-write additive manufacturing method employs materials such as metals, composites, and ceramics and offers several benefits, including reduced build times, minimal waste, and lower production costs. This technology will significantly drive the additive manufacturing market, which Research and Markets predict will grow to $83.56 billion by 2030.
With the ability to integrate materials seamlessly and directly embed electronics, industries such as
healthcare, professional sports, and automotive can expect direct-write 3D printing technology to develop new smaller smart objects.
The healthcare industry will benefit from using direct-write technology to develop medical devices, wearables, and monitoring systems. With the precise deposition of inks and highviscosity pastes, direct-write opens new opportunities for improving clinical care.
Integrating embedded sensors into medical treatment equipment, such as casts and braces, allows a patient’s health to be monitored continuously
within and outside clinic walls. Embedded sensors can also help with diagnostic testing for patients needing more in-depth monitoring beyond the clinic.
One example is the smart cast’s electronic package, which comprises sensors directly printed on supports, making them easy to embed in the cast structure. Printed circuits and sensors allow batteries and wiring to be intelligently integrated and distributed, eliminating the need for external elements and bulky components. Where necessary, multiple sensors can also be connected to the embedded circuit, allowing for more comprehensive capabilities.
Alfa Romeo F1 Team Orlen 2022 race car features 150 AdditiveIndustries 3D printed parts. Image courtesy:Direct-write technology also enables researchers to place sensors directly on living tissue, such as bone, cartilage, tendons, and skin, to better understand the body’s health status and tissue response to treatment. This approach allows for precise, real-time monitoring of physiological changes and provides valuable information for clinicians to make informed decisions regarding patient care.
Furthermore, 3D-printed sensors can also provide necessary biofeedback to move from developing therapeutic devices to developing theranostic devices. Theranostics is a rapidly emerging field that combines diagnostic and therapeutic functions into a single device, providing personalized medicine solutions.
The on-demand availability of 3D printing electronics can help researchers bring products to market faster. It will make cutting-edge medical developments more readily available to patients and medical personnel. It also opens opportunities for personalized medical equipment, allowing on-demand development for patients requiring specialized devices.
Personalized patient equipment, such as sensors and casts, enables more precise and effective treatment
tailored to an individual’s anatomy. Thus, 3D printing innovation in healthcare brings cutting-edge technology to further customize treatment plans when a “one-size-fitsall” approach does not adequately address a diagnosis.
Game-changing benefits of directwrite technology in sports
Embedded sensors are increasingly used in sports equipment to monitor critical data, such as athletes’ heart rates or level of impact from a hit. This approach enables vast data collection and helps improve athlete health and equipment safety. As a result, studies focused on these aspects are becoming more prevalent, leading to the widespread adoption of embedded sensors in various sports.
The NFL launched a program to develop mouthguards retrofitted with high-tech sensors to collect kinematic data, such as impact speed, direction, force,
location, and severity. Last year, in partnership with the NFL, the NCAA adopted these high-tech mouthguards in multiple football programs.
Today, the NFL and NCAA use data from these mouthguards to enhance football players’ health and safety. Four NFL clubs are gathering data to analyze impacts during games and practices, informing the league’s approach to injury reduction. Participating NCAA programs will receive team-specific statistical analysis to advance player health and safety, as the sensor data also provide insights for better concussion protocols.
Other direct-write innovations in sports include 3D-printed basketballs and custom cycling saddles. Known for their orange basketballs, Wilson Sporting Goods recently announced the development of a 3D-printed airless basketball prototype, opening new technological opportunities for integrated data within basketball equipment.
Although still in beta, the basketball was used at a recent NBA All-Star slam dunk contest. The prototype showcased the basketball’s performance specifications and demonstrated that the ball meets NBA regulations for weight, size, and rebound. Wilson’s development comes off the heels of Adidas’ innovative 3D-printed running midsole in basketball shoes. These developments pave the way for
embedded sensors to monitor player performance, fall impact, and ball specifications during the game.
Across the pond, German engineers have developed personalized cycling saddles. These patient-specific models use technology to map pressure points and weight distribution, which is then loaded into additive manufacturing interfaces to 3D-print a custom riding saddle. Largely targeted towards professional cyclists, these saddles can be personalized for existing medical conditions, comfort preferences, and performance parameters. Continued innovation paves a path for technology integration on the cycling course to monitor fatigue and other performance data.
These initiatives, alongside many others, will play a crucial role in advancing the development of smaller embedded sensors in sports gear, equipment, and clothing, ultimately benefiting players and their teams.
The automotive industry uses 3D printing technology to develop tools for self-driving and connected cars for custom prototypes. However, directwrite technologies will enable faster design, testing, and deployment of new, smaller parts.
Adopting additively manufactured electronics (AME) will help car manufacturers reduce costs while maintaining quality, as prototypes and components can be developed quickly, enabling faster time-tomarket.
Direct-write technology can produce parts with complex geometries and internal structures that are lighter and stronger than those made through traditional manufacturing methods, improving fuel efficiency and vehicle performance. This strength and durability are due to the flexibility and makeup of 3D-printed parts. Some quality filaments have the same characteristics as steel but without the added cost and weight. Thus, lighter prototypes can be produced without jeopardizing durability and safety standards.
Pairing lighter 3D-printed parts without changing the power under the hood can lead to more fuelefficient and powerful vehicles. Ford Motor Company, NASCAR, F1 Racing, Aston Martin, and others have turned to 3D printing to develop innovative aerodynamics and improve their vehicles’ performance and fuel economy. From 3D-printed driveshafts, embedded sensors in bumpers and tires, and even 3D-printed interiors, the ability to develop lighter parts with improved performance is taking the automotive industry by storm.
Additionally, direct-write technology significantly reduces waste and production costs compared to conventional auto manufacturing, as materials are used only where needed. Reducing waste helps automotive manufacturers provide clean parts beyond reaching emissions standards or innovating hybrid vehicles.
One of the automotive industry’s most significant advantages of 3D printing is its supply chain flexibility. Automotive companies can produce small batches of parts on demand, significantly reducing the need for large inventory stockpiles. This flexibility offers several benefits to manufacturers.
For instance, it helps companies respond quickly to changes in demand, thereby reducing the time to bring new products to market. This is especially critical in the highly competitive automotive industry. Supply chain flexibility also reduces the risk of obsolescence for slow-moving parts. In traditional manufacturing, slow-moving parts can become obsolete if demand for those parts is insufficient to justify continued production. This leads to significant inventory costs and can burden the manufacturer financially. However, with direct-write technology, manufacturers can produce the required number of parts as needed, eliminating the risk of obsolescence. Moreover, tooling costs and other fixed expenses associated with traditional manufacturing increase the cost of producing small batches. However, direct-write technology significantly reduces tooling costs, making it a cost-effective alternative for small-batch production.
By producing small batches of parts on demand, manufacturers can respond quickly to changes in demand, reduce inventory costs, eliminate the risk of obsolescence, and save on costs associated with traditional manufacturing methods. Direct-write technology has the potential to enhance efficiency, facilitate research and development, and tackle supply chain challenges. As such, there is expected to be a growing demand for additive manufacturing technologies across various industries beyond healthcare, sports, and automotive. DW
Eventually, the thoughts of a 3D printing pro move past mere length, width and depth to a more important fourth dimension: TIME.
Servo systems and motion controllers from Yaskawa reduce print time without sacrificing accuracy.
Put your machine light years ahead in speed, precision and reliability. Call Yaskawa today.
FOR MORE INFORMATION:
https://www.yaskawa.com/am
Additive manufacturing is often considered a more sustainable method for its material efficiency, reduced energy consumption, localized production, and design optimization potential. Though the benefits sound great and make sense, more organizations seek reliable data to prove they're not greenwashing their products.
To help engineers make more responsible manufacturing decisions that align with sustainability goals, EOS and its Additive Minds applied engineering group developed the EOS Cost & Carbon Calculator for more
transparency in the additive design and manufacturing life cycle.
“Responsible manufacturing has always been an undercurrent at EOS, and sustainability falls underneath that. We believe additive is inherently more sustainable or opens up sustainable opportunities,” said Dave Krzeminski, senior Additive Minds consultant at EOS.
(If you attended the 2023 AMUG Conference in Chicago, you might remember Krzeminski demonstrating the first 3D-printed basketball produced by Wilson Sporting Goods.)
EOS took its internal cost-perpart tool — a non-cloud-based Excel sheet — and evolved it into a webbased platform, made it available to external users, and added a carbon calculator component. Users can quickly estimate costs and carbon footprint for either metal or polymer materials or perform a full simulation.
The full simulation calculates numerous parameters, including build height, part volume, number of parts, build time, machine type, and material inputs. The result is a detailed breakdown that shows how costs are distributed among
production processes. If a breakdown shows higher costs during powder processing, for example, an engineer has insight into where time should be spent refining production.
EOS collects supply chain information to populate carbon footprint data. Engineers can modify inputs, such as the mode of logistics, to see how changes affect CO2 emissions in the supply chain. They can also play with scenarios to identify sources of CO2 and estimate reductions. For instance, designers can estimate the effects of reducing the part size by half or changing
materials to inform more sustainable design decisions.
The calculator also provides carbon pricing to demonstrate how reducing emissions can reduce production costs. This will prove incredibly useful as more countries adopt and enforce carbon tax legislation.
At this point, the prominent question engineers may ask is: Where does all the data come from? The Additive Minds team is transparent about its data collection and seeks user feedback to improve the tool.
“We roll out updates every three to six months. Some data comes from suppliers, other companies, research papers, and studies. Some of the data is collected by our sustainability team running projects, monitoring machines, and quantifying process information,” said Krzeminski.
Two years ago, EOS partnered with its customer You Mawo and Fraunhofer EMI to conduct a systemic life cycle analysis (LCA) of You Mawo’s 3D-printed glasses. From cradle-to-grave, excluding the use phase, the study compared the environmental impact of additively
and conventionally manufactured eyewear — from material sourcing to production, packaging, and shipping. The study also included a hotspot analysis to identify significant contributors and potential for improvement, including powder refresh rates, powder feedstock, and energy sources used.
The study concluded that 3D-printed eyewear performs significantly better than conventional eyewear in 18 impact categories, including climate change, human toxicity, ozone depletion, and water depletion. For example, the carbon footprint of a customized, 3D-printed eyewear product is around 58% lower compared to conventionally manufactured eyewear. The analysis
also concluded that 3D-printed eyewear compared to conventionally manufactured acetate eyewear creates 80% less waste and can help to avoid lengthy post-processing.
“The 3D-printed eyewear was, in fact, more sustainable from a carbon footprint perspective, and we found that energy sources can be a big contributor,” said Krzeminski. “To that point, we recently rolled out two more sustainable nylon materials. Our Nylon 11 is a climate-neutral substitute for traditional Nylon 11, and we worked with the material supplier to improve the energy sources used to make the material.”
Though the EOS Cost & Carbon Calculator wasn’t designed to replace a thorough LCA, more organizations
“The
3D Printing Surface”
can now draw similar realizations and refine processes and materials to reduce their carbon footprint.
“Within EOS, our Additive Minds brand includes our applied engineering consulting and training groups. We don't just sell you a printer and material and walk away. We interact and support new and existing customers and can create projects,” said Krzeminski. “I kind of think of myself as a travel agent — what do you want to do, and where do you want to go? We can put together educational components to help your team. We can engage with you on a new material project or tune a printer. All that happens under our Additive Minds brand, and in addition to that, we built this tool.”
Additive Minds recently launched another online analysis tool for those exploring additive manufacturing that helps answer the question, “Can I 3D Print This?” Designed for metal and polymer 3D printing, the online tool provides freedom and independent inquiry for those investigating the viability of laser powder bed fusion (LPBF) industrial 3D printing for production.
EOS is transparent about its data collection and continuously updates the tool based on user feedback and needs. Image courtesy: EOS
With the Can I 3D Print This tool, users input information about their current manufacturing methods and the part design file. The tool generates a comprehensive analysis and downloadable report, including cost estimation, predicted production time, a recommended EOS system, and recommended material. The analysis also includes multiple comparisons of cost-per-part (CPP), production timeline, and material
usage when manufacturing with 3D printing rather than traditional processes.
With multiple online tools, more manufacturers have opportunities to leverage 3D printing in responsible ways that improve their products and processes while authentically reducing environmental impacts.
“Our job is to make people aware of all the value that additive can bring,” said Krzeminski. “Some people aren’t even aware of carbon taxes and that you will be taxed that way in some regions. So, we’re helping people become better ambassadors and stakeholders within their organizations.” DW
EOS | eos.info
Design engineers can modify inputs to estimate how costs and carbon emissions would change. Image courtesy: EOS
3D Platform is the trusted source for industrial-strength, large-format 3D printers. Based in Roscoe, Illinois, USA, the 3D Platform team is focused on driving advancements in technology to innovate, design, and build next-generation equipment for additive manufacturing. Our approach to 3D printing focuses on four clear industry demands:
Scalability and increased throughput from high-flow extruders allows smart manufacturers to shed legacy product development cycles and small-scale models for full-size prototypes and production.
Open market-enabled solutions allow users to go bigger with 16 times the speed of competitors’ extruders for faster printing and exceptionally strong parts.
• Quick-Swap dual extruder heads deliver high quality 3D prints.
Affordability of equipment and materials allows SMB’s and Fortune 100 companies to tailor 3D printing to their needs, and quickly develop new products and bring them to the market.
Robust industrial technology stands up to harsh environments and the excessive demands of rapid manufacturing using the world’s leading linear motion mechatronics, reliable motors, and sophisticated control systems.
•
• Modular design accommodates variable nozzle and filament sizes Nozzle flexibility for fine layer resolutions or faster printing and strength.
To learn more about 3D Platform, visit www.3dplatform.com.
3D Platform 6402 E. Rockton Road Roscoe, Illinois 61073 USA
+1.779.771.0000 3dplatform.com
marketing@3dplatform.com
sales@3dplatform.com
CS Hyde Company is your source for high performance adhesive tapes, polymer films, fabrics, and silicone. Our product line is comprised of various types of materials with performance properties required for additive manufacturing, including low friction, nonstick release, and high temperature resistance. Common release surfaces include ULTEM® PEI, TPX®, or Optically Clear FEP/PFA. FDM/FFF printers equipped with PEI sheets benefit from surface durability and a surface that will hold filament in place and remove cleanly when cooled. Aside from printing surfaces, we have helped design engineers with material solutions for LCD screen bonding, silicone gasket designs, and linear rail or carriage friction reduction.
Finding solutions to industry related problems is a huge part of what makes CS Hyde a trusted vendor in the additive industry. Working with hobbyists to 3D machine manufactures has given us insight to the ongoing issues within the additive manufacturing industry regarding printing surfaces, as well as machine component manufacturing. Our polymer knowledge allows us to recommend compatible polymers for property specific applications like UV transparency or material outgassing. With converting machinery expertise, we have been able to produce custom products utilizing adhesive lamination, slitting, sheeting, die cutting, and rapid prototyping.
800-461-4161 resources@cshyde.com
Bring new precision and performance to every stage in your additive machine development with Yaskawa motion control
Rise above the desktop: Shaky, imprecise desktop machines become robust industrial performers with motion control that overcomes vibration, boosts speed and gets you ready for tomorrow's hybrid technologies.
Advance the industry standard: Industrial quality printers benefit from Yaskawa's smooth and precise motion, plus worldwide support that distinguishes your machine in a crowded marketplace.
Restate the state of the art: Top tier manufacturers need new ideas, plus the engineering support to make them work. Yaskawa supplies both, using the latest linear and robotic motion systems and Singular Control to create a seamless, supportable development environment.
Our motion control technology also prepares you for new frontiers in additive manufacturing:
• Robotic systems that produce curvilinear motion for true 3D deposition
• Additive/Subtractive technology which combines the benefits of 3D printing and traditional routing/machining
Yaskawa servos provide smooth, precise motion for additive manufacturing, while the G-code compatible MP3300iec controller can operate any motion device to implement the latest advances in hybrid manufacturing.
IAM Robotics originally developed a complete solution that included a 3D scanner, enterprise software and mobile manipulator robot.
| IAM RoboticsI recently reported on IAM Robotics launching an automated solution designed for person-to-goods (P2G) warehouse workflow. The company is entering a new chapter focused on the hottest segment of autonomous mobile robot (AMR) applications and one that has already been proven through the efforts of companies like Locus Robotics and 6 River Systems.
The rebirth of IAM Robotics is significant because it is the latest chapter in what was a valiant attempt to commercialize mobile manipulators. It’s also a poignant lesson in failed market fit and knowing when to pivot as a robotics startup.
IAM Robotics started in Vlad Altman’s Pittsburgh basement and quickly moved to a local township garage building to model a working warehouse. Co-founder Tom Galuzzo had a passion for mobile robots and a robotics degree om Carnegie Mellon University. At the time, the idea of putting a robot arm onto a mobile platform and using it to pick items om shelves was one of the remaining “holy grail” challenges in robotics.
It was also a year a er Amazon’s historic acquisition of Kiva Systems for $775 million – the potential for robotics in warehousing was in the spotlight. It took until 2015 for IAM Robotics to raise its first seed round and introduce its Swi robot on the promise of automated picking in the warehouse.
This was when IAM Robotics first appeared on my radar as an innovative solution for goods-to-person workflows in the warehouse. At the time, I was leading product management for the mobile robot business at Adept Technology, and no other vendor in the market was commercializing a mobile manipulator for warehousing applications.
The company was pushing the boundaries of robotics technology, simultaneously solving the problems of vision-guided mobile manipulation and developing strategies for AMR perception, obstacle avoidance, and the challenges of battery-supported operations.
The IDT Series is a family of compact actuators with an integrated servo drive with CANopen® communication. They deliver high torque with exceptional accuracy and repeatability, and feature Harmonic Drive® precision strain wave gears combined with a brushless servomotor. Some models are available with a brake and two magnetic absolute encoders with the second providing output position sensing. This revolutionary product line eliminates the need for an external drive and greatly simplifies cabling, yet delivers high-positional accuracy and torsional stiffness with a compact form factor.
• Actuator with Integrated Servo Drive utilizing CANopen®
• 24 or 48 VDC nominal supply voltage
• A single cable with only 4 conductors is needed: CANH, CANL, +VDC, 0VDC
• Zero Backlash Harmonic Drive® Gearing
• Panel Mount Connectors or Pigtail Cables Available with Radial and Axial Options
• Control Modes include: Torque, Velocity, and Position Control, CSP, CSV, CST
What immediately struck me about the Swift robot was that it didn’t pick up individual items from bulk SKU bins stored in the warehouse. Rather, it worked by picking from stock that was stored in organized rows on a shelf, not unlike what you might see in the frontof-house retail space of your corner drugstore.
I had never seen a warehouse space with products organized in neat product rows like this, and that was my first red flag about the viability of Swift. To make the system work, Swift required a 3D model of each product SKU. With the 3D model, the robot’s vision system could then identify the item on the shelf and determine the correct pose of the robot to acquire the item.
The company developed a novel 3D item scanning station called “Flash” that would ingest a new product SKU, image it and add it to the 3D library of items that Swift could now handle.
To function properly, Swift also had to autonomously handle product replenishment, putting items onto the warehouse shelves in those neat and organized rows. The idea to replenish the shelves autonomously looked great on an ROI spreadsheet, but Swift wasn’t fast
IAM Robotics’ new Lumabot is designed specifically for personto-goods automation in a warehouse.
| IAM Robotics
IAM Robotics’ new solution directs the human associates with information about which item to pick and where to place the item for a customer order. The Lumabot then moves items to a pack-out station.
enough (compared to human warehouse associates) at replenishing the shelves in the real world. It also couldn’t easily work side-by-side with human associates in warehouse aisles due to its working dimensions.
Another concern for the viability of Swift was that the target segment of “warehouses with highly organized shelves” was just too small. The majority of warehouses and distribution centers store bulk items contained in bins or boxes on the warehouse shelves. Bulk storage is simply the most efficient and cost-effective method of using precious warehouse space.
Lastly, the inability of Swift to pick items from bins (the “holy grail” application) ultimately sealed its fate. In the warehouse, humans are very adept at pulling individual items from bulk storage. This realization led the company to rethink its portfolio.
Creation of an AMR platform
Fast forward to 2020, and IAM Robotics made the first pivot with the design and launch of its Bolt AMR, using all of the knowledge and experience gained from engineering Swift. The goal of Bolt was to offer a standard AMR base that could be deployed into any AMR application. This
was a competitive market with a large number of established vendors, including companies like OMRON, Fetch Robotics, MiR, OTTO Motors and others.
Unfortunately, this was also the start of the pandemic. While e-commerce was exploding in popularity (along with the demand for automated support for warehouse labor shortages), there were also hundreds of AMR competitors on the market with standard AMR platforms. The novel innovation for Bolt was a swappable battery that could be quickly changed with minimal downtime of the AMR. But it wasn’t enough.
In 2021, the company restructured, hired CEO Lance Vandenbrook, let go of many of the original mobile manipulation-focused engineering teams, hired the necessary enterprise so ware engineering team and entered a self-imposed “stealth mode” to retool.
The company recently re-emerged with a new person-to-goods (P2G) warehouse workflow, leveraging all of the intellectual property om its early days in AMR development and adding a new, robust, fully featured enterprise workflow layer on top.
The new Pyxis (pronounced pix-us) solution is designed to be competitive with existing P2G solutions such as Locus Robotics and 6 River Systems. The focus for IAM Robotics has changed om being a mobile robotics company to a warehouse workflow company, managing the tasks of both human associates and mobile robots.
The company launched a new AMR called Lumabot, taking the Bolt AMR base and outfitting it with a payload of fixed shelves and pick/put-to-light
guides. Human associates interface with the solution through a wearable that communicates customer orders, quantity and SKU locations.
Lumabot robots move autonomously to the pick location where humans pull individual items om bins and place them in outgoing customer order bins. The Lumabots then take assembled customer orders to pack out stations for final consolidation, packaging and labeling.
The Pyxis solution manages the operations of all of the human associates in the warehouse, together with the fleet of Lumabots to manage customer order picking and consolidation. The system is designed to be deployed in either greenfield or brownfield opportunities and offered as a robots-as-a-service (RaaS) business model. RR
These connectors deliver exceptional performance in harsh environments, ensuring long-lasting durability. Whether in industrial automation, medical robotics, or for Rovers and Legged Robots, LEMO connectors provide the ability to connect sensors, actuators, and control systems seamlessly.
• Light weight
• Durable
• Compact
• Ergonomic
At the beginning of the pandemic, the team at ABB Optical struggled with recruiting new associates to perform their manual warehouse processes. Here’s how Locus Robotics came to the rescue.
ABB Optical Group is a leading provider of optical products, services, and business solutions in the eye care industry. They operate through three business pillars: ABB Contact Lens, ABB Labs, and ABB Business Solutions.
ABB is focused on the future of eye care professionals, helping them succeed by making practices more efficient and assisting providers to effectively navigate market changes. ABB Optical is headquartered in Coral Springs, Florida and most recently opened a National Logistics Center in Hebron, Kentucky.
At the beginning of the pandemic, the team at ABB Optical struggled with recruiting new associates to perform their manual warehouse processes. They looked at a number of automation solutions to improve their productivity
and employee satisfaction while ensuring the right item is picked and packed for customers.
“We looked at A-frame automatic dispenses and pickto-light systems, but space constraints were a factor,” said Tom Calhoun, senior vice president of operations, ABB Optical. “One of my colleagues knew someone in the automotive industry that used LocusBots, so we went to see them, and it just made sense for our warehouse.”
Quick implementation speed and cost efficiency were also important points of consideration for ABB Optical when selecting an automation solution.
Locus Robotics, a Wilimington, Mass.-based developer of autonomous mobile robots (AMRs), deployed a warehouse execution platform and 114 AMRs along with a suite of dashboards
Locus Robotics recently announced its AMRs have picked more than two billion units, reinforcing its position as a leading robotics provider for the warehouse and logistics industry.
CGI Motion standard products are designed with customization in mind. Our team of experts will work with you on selecting the optimal base product and craft a unique solution to help di erentiate your product or application. So when you think customization, think standard CGI assemblies.
Connect with us today to explore what CGI Motion can do for you.
and actionable reporting tools at ABB Optical’s warehouses, including its National Logistics Center in Hebron, KY in October of 2022.
The Locus Robotics Origin is an intelligent autonomous mobile robot (AMR) that’s designed specifically for collaborative, high volume order fulfillment. It can carry up to 80 lbs. (36 kg.)
The Kentucky warehouse (100,000 square feet and holding 160,000 SKUs) was built with input from Locus to be a Locus-centric facility down to the aisle width that works best with LocusBots. “Locus Robotics has been a great partner as we make changes, and their help has been beneficial,” stated Calhoun.
In the healthcare industry, it’s crucial to capture lot numbers in real time for compliance. With Locus Robotics, ABB Optical tracks that information and ensures that the right item is picked out of the over 160,000 different SKUs they carry. Before choosing the Locus solution, ABB Optical had an order accuracy rate of well above 95%. Now, with the LocusBots, the accuracy rate is at 98%. LocusBots helped workers improve their average to 250+ units per hour (UPH), with some exceeding 500 UPH.
The warehouse associates at ABB Optical find it easy to work with the LocusBots as the displays are available in multiple languages like English or Spanish. These associates have told Calhoun that they have the easiest position in the warehouse, because the bots are selfexplanatory and simple to use.
The team plans to implement zone picking, which will enable associates to stay in one area instead of walking throughout the large warehouse. “The Locus Robotics solution is cost-efficient and provides real-time information on what’s moving and not moving to plan accordingly,” said Calhoun.
Locus Robotics recently announced that its AMRs have now picked more than two billion units, reinforcing the company’s position as a leading robotics provider for the warehouse and logistics industry. This new milestone comes just 11 months after reaching the industry-first landmark of 1 billion picks.
“Achieving the two billion picks milestone is an incredible accomplishment for our company and for our customers,” said Rick Faulk, CEO of Locus Robotics. “This event is a testament to the dedication and innovation of our incredible team and the dramatic productivity improvements we deliver to drive our customers’ growth and success.”
Reaching this milestone took just 358 days, with the last 100 million picks taking just 27 days – an average of 3.7 million picks per day. By comparison, it took more than six years to make the first billion picks, and 1,542 days to pick the first 100 million units. LocusBots have now traveled more than 37 million miles in customers’
| Locus Roboticswarehouses, the equivalent of more than 1,370 times around the Earth or 77 round trips to the Moon.
“Achieving the remarkable milestone of two billion picks demonstrates how Locus’s intelligent automation solution can transform warehouse operations,” said Keith Price, CIO of Concordance Healthcare, “We look forward to continuing to work with the Locus team to leverage the power of advanced robotics and automation to drive even greater warehouse fulfillment optimization in the years ahead.”
“Locus’s consistent innovation, user-centric approach, and genuine dedication to customer relationships puts them at the forefront of warehouse automation,” said Alan McDonald, vice president of continuous improvement at GEODIS. “This milestone is a testament to its technological leadership and synergistic collaboration. We look forward to building on our work together and driving even greater efficiency improvements in the future.”
The AI and data science-driven LocusOne platform serves as an enterprise-level fleet manager, overseeing complex warehouse
fulfillment workflows that support diverse use cases, clustering tasks to create optimal robot missions and reduce unproductive worker walking time. Locus’s unique multibot approach decouples workers from orders and tasks to dramatically improve worker productivity.
Proven at enterprise scale, laborchallenged 3PL, retail, health care, and manufacturing operators can seamlessly add robots to increase capacity or meet growth in any operation in just minutes to optimize productivity in their operations, reduce costs, and stay competitive in the rapidly evolving e-commerce landscape.
The LocusOne warehouse automation execution platform enables the orchestration of multiple robotic form factors at enterprise-scale within a single coordinated platform. It provides real-time optimization of tasks to be completed within the four walls and across multiple levels in warehousing and manufacturing environments. LocusOne optimizes robotic task allocation, route planning, and resource use, while delivering realtime business insights into warehouse operations.
Locus won an RBR50 Robotics Innovation Award earlier this year for surpassing the 1 billion pick milestone, which it achieved in September 2022. The milestone pick was made at a home improvement retailer warehouse in Florida, where a LocusBot picked a cordless rotary tool kit. Locus completed its billionth pick just 59 days after hitting its 900 millionth pick. To put this into perspective, it took Locus 1,542 days to pick its first 100 million picks.
Retailers and fulfillment warehouse operators are increasingly turning to AMRs to meet growing demand and mitigate labor shortages. Cost-efficient robots are a must-have as e-commerce volumes continue to increase.
And having been deployed at more than 200 sites worldwide, with some sites using as many as 500 LocusBots, Locus is a leading AMR provider that continues to create critical business value for its customers around the world, every day. RR
A Fluid Power World series of webinars focused on mobile hydraulic technologies.
Fluid power technologies are crucial in providing the power density, reliability and control required for mobile machinery. Fundamental Fridays is your platform to highlight technical solutions that enable OEMs to efficiently power, control and regulate machinery, especially as our industry responds to the need for more efficient and sustainable systems.
At CGI we serve a wide array of industries including medical, robotics, aerospace, defense, semiconductor, industrial automation, motion control, and many others. Our core business is manufacturing precision motion control solutions.
CGI’s diverse customer base and wide range of applications have earned us a reputation for quality, reliability, and flexibility. One of the distinct competitive advantages we are able to provide our customers is an engineering team that is knowledgeable and easy to work with. CGI is certified to ISO9001 and ISO13485 quality management systems. In addition, we are FDA and AS9100 compliant. Our unique quality control environment is weaved into the fabric of our manufacturing facility. We work daily with customers who demand both precision and rapid turnarounds.
GAM
GAM provides a full range of robotic flange gearboxes
GAM’s extensive product offering includes three different flange gearboxes: Strain Wave (harmonic), Cycloidal, and the revolutionary Zero-Backlash Planetary. The GAM GPL zero-backlash planetary gearbox features a unique design ensuring backlash of ≤ 0.1 arcmin for the life of the gearbox. The GPL provides vibration-free motion and high positional accuracy for precise smooth path control and repeatability with a life of 20,000 hours. The GCL cycloidal gearbox provides precise point-to-point motion and high impact resistance of 5x nominal torque with the option of an integral pre-stage. The GSL strain wave gearbox uses harmonic-type gearing for high accuracy and drops in for popular competitor gearboxes. With three options, GAM can provide the zero-backlash gearbox for your precision application.
CGI Inc. 3400 Arrowhead Drive Carson City, NV 89706
Toll Free: 1.800.568.4327
Ph: 1.775.882.3422
Fx: 1.775.882.9599
WWW.CGIMOTION.COM
The SHA-IDT Series is a family of compact actuators that deliver high torque with exceptional accuracy and repeatability. These hollow shaft servo actuators feature Harmonic Drive® precision strain wave gears combined with a brushless servomotor, a brake, two magnetic absolute encoders and an integrated servo drive with CANopen® communication. This revolutionary product eliminates the need for an external drive and greatly simplifies cabling yet delivers high-positional accuracy and torsional stiffness in a compact housing.
www.Harmonicdrive.net
LEMO® is the industry leader in the design and production of precise custom interconnect systems. LEMO products are designed and manufactured according to rigorous and controlled processes. Inspection and traceability of products are systematically ensured in compliance with our standards. High-quality LEMO Push-Pull connectors are used in a wide range of challenging application environments, such as medical, test & measurement, research, defense & military, information systems, aerospace & autonomous vehicles, robotics, automotive, industrial control, nuclear, broadcast & audio-video, and communications.
https://www.harmonicdrive.net/products/rotary-actuators/integrated-actuators/sha-integrat
LEMO® has been designing precision connectors for over seven decades. Offering more than 90,000 combinations of products that continue to grow through customer-specific designs, LEMO® and its brands REDEL®, NORTHWIRE®, and COELVER® currently serve more than 100,000 customers in over 80 countries around the world.
LEMO USA, Inc. 635 Park Ct. Rohnert Park, California 94928
Ph: 707.578.8811
E-mail: info_us@lemo.com
Website: https://www.lemo.com/en
An automated guided vehicle (AGV) needs to do the job it is programmed to do; without error, quickly and efficiently
Motors for AGVs must be reliable and low maintenance and they need to be capable of being in operation 24/7 without loss of functionality.
What type of motor do you need for your AGV?
That depends on the type and size of the automated guided vehicle you have, and how much weight it will be expected to transfer at any one time. A motor that is too small won’t be able to function – or at least not for long – and one that is too big and powerful could cause functionality issues. The recommended motors for AGVs are brushless DC motors - they are powerful, quieter and low maintenance.
Parvalux’s brushless motors rarely need maintenance, and are highly efficient with a high starting torque, which means they are consistent in speed. This enables the timings of build on production lines and delivery times to be assessed more accurately. This makes reporting and assessing capacity for the warehouse easier.
Find out more at www.parvalux.com
Renishaw’s FORTiS™ delivers superior repeatability, reduced hysteresis, and improved measurement performance due to an innovative non-contact mechanical design that does not require a mechanical guidance carriage. It provides high resistance to the ingress of liquids and solid debris contaminants. It features an extruded enclosure with longitudinally attached interlocking lip seals and sealed end caps. The readhead body is joined to a sealed optical unit by a blade, which travels through the lip seals along the length of the encoder. Linear axis movement causes the readhead and optics to traverse the encoder’s absolute scale (which is fixed to the inside of the enclosure), without mechanical contact.
Parvalux 125 Dever Drive Taunton, MA 02780 USA
Phone: +1/508-916-6620
email: sales.us@parvalux.com
website: www.parvalux.com
Renishaw, Inc.
1001 Wesemann Dr. West Dundee, IL, 60118
Phone: 847-286-9953
email: usa@renishaw.com
website: www.renishaw.com
When mechanical anchors meet adhesives
Sift through a few headlines, and you’ll likely come across news about labor shortages in several sectors. The trades are not immune.
“Construction Workforce Shortage Tops Half a Million in 2023,” states the Associated Builders and Contractors. “Labor Shortages Forecast to Persist for Years,” predicts The Society for Human Resource Management.
Blame what you will: the pandemic, inflation, supply-chain constraints, an aging workforce, or something else. Ultimately, demands for production are not going anywhere and, in fact, are increasing in most sectors. The resilient industries will be those that innovate and rethink the status quo.
“Skilled labor is one of the biggest cost drivers of any construction or building site,” shares Josh Beasley, a product manager with Hilti North America and past field engineer.
“Unfortunately, it’s becoming increasingly harder to find, which is further driving costs. Add this to strict project deadlines and budget limitations, and it leaves contractors seriously looking for ways to speed and maximize the labor output they do have.”
One way to do so is to ensure a high level of training and experience — challenging, given the skilled labor shortage. Another way is to choose tools and methodologies that simplify and speed operations.
“We’re always focused on developing technology that’s faster, safer, and easier to use, and this is especially important in the current economy,” says Beasley. “Contractors might be limited by the available workforce, but we can support them with solutions that ease some of the burden.”
According to customer feedback, one area of project construction that has drained time and costs — and typically required skilled labor — was adhesive anchoring. So, the team at Hilti decided to do something about it. The company is a global provider and manufacturer of tools, technology, and services to the commercial construction industry.
“It’s been an iterative process that involved identifying the needs of engineers and installers,” he says. “Then, once we had a prototype of the initial product, we took it into the field to seek additional feedback until we narrowed down a technology that best suited both users’ needs.”
The result: a dual-action anchor that combines the high performance of adhesive anchors with the simplicity of screw anchors.
An anchor is a fastener designed to attach one or more fixtures to a concrete surface. Anchors are commonly used in the building and construction industries.
“Given a choice, an installer will almost always prefer a mechanical anchor because they’re quicker to install and cost-effective. An engineer, on the other hand, is likely to specify an adhesive anchor for heavier-duty applications because of the anchor’s high performance,” says Beasley. “So, sometimes there’s a bit of a tug-of-war between contractors and engineers about the ideal product to use, depending on the project.”
An adhesive anchor is a postinstalled fastener that’s inserted into
a drilled hole in hardened concrete, masonry, or stone. Loads are transferred to the base material by the bond between the anchor and the adhesive, and the adhesive and the base material.
“Adhesive anchors are the preferred choice to ensure high performance — whether that be load, edge, or spacing performance. They also offer flexibility over mechanical anchors,” he explains.
However, there is one drawback to conventional adhesive anchors, particularly during a labor shortage.
“Ask any installer on a job site, and they’ll tell you adhesive anchors involve a complex and slow installation process.”
According to Beasley, anchoring involves drilling a hole, blowing out the debris with an air compressor, and
brushing out the surface. The hole must be cleaned until it’s completely free of dust fragments before dispensing the adhesive and waiting for it to cure. A standard adhesive anchor in normal temperature conditions could take up to 30 minutes or longer to cure, which is time-consuming.
“It’s a slow process but an important one because each step is critical for the adhesive anchor to bond properly,” he says. “This means there are opportunities for errors and improper installation, so our team began reassessing what could be done to simplify the anchoring process.”
Enter the Kwik-X Dual Action Anchor, the first anchor of its kind on the market
that uses a high-performance adhesive in combination with a screw anchor. According to Hilti, this dual-action anchor can reduce installation time by up to 70% and save up to 20% of the total cost of installation when compared to conventional adhesive anchoring systems.
“We developed this new anchoring technology with the aim of a better, simpler installation process, which eliminates several traditional steps,” shares Beasley. “For one, there’s no use for an air compressor or brushes because the drilled hole requires zero cleaning. Additionally, the adhesive comes in a pre-apportioned capsule that eliminates the need for dispensers.”
The anchor’s mechanical interlock cuts into the concrete when installed, offering additional holding properties. The special adhesive formulation uses debris from the drilled hole, mixing it
in, which results in an aggregate that supports the adhesive bond.
“This is why we call it a dual-action anchor…it uses a mechanical screw that’s drilled into the concrete and an adhesive,” he says. “The curing time is also reduced from 30 minutes or more for a standard formulation to just 30 seconds.”
Since the adhesive comes in a preapportioned capsule, it also reduces the risk of under or over-filling the hole with adhesive.
“It’s not uncommon for installers to add excessive adhesive to avoid underfilling the hole. This can lead to reduced performance of the anchor and up to 30% waste of the adhesive, which is far from inexpensive,” he says. “So, we wanted to ensure zero waste is associated with this product.”
Overall, Hilti found that the new anchoring system offers up to four times faster installation compared to standard adhesive anchors. It’s also possible to remove and reinstall the dual-action anchor in the same borehole once if necessary.
“By simplifying and speeding up the installation process, we’re eliminating critical points that can go wrong in an adhesive anchor installation process — and saving significant labor costs,” says Beasley. “And given today’s labor climate, that’s a major benefit.”
Currently, the anchor technology is primarily used for buildings to attach primary and secondary steel columns and beams, as well as ledger angles to concrete. It’s also finding use in handrails, platforms, balconies, and even racking applications.
The new dual-action anchor includes a screw anchor and an easy-to-use adhesive that comes in pre-measured capsules.
The anchor’s mechanical interlock cuts into the concrete when installed, offering additional holding properties. The special adhesive formulation uses debris from the drilled hole, mixing it in, which results in an aggregate that supports the adhesive bond.
However, the Kwik-X system took time to develop for the market. It was challenging to determine how to test an anchor that uses both chemical and mechanical anchoring against criteria solely built for one or the other.
“This was the first time a hybrid fastening system was reviewed by the governing bodies that be. Previously, there was no framework for developing or testing a mechanical and adhesive anchor to ensure it measured up to code,” he says. “So, it was an interesting and substantial process to get to the point of launching the Kwik-X in the market.”
Beasley adds: “It’s also very rewarding because we believe the dual-action adhesive anchor is a game-changer for the industry, especially as fewer people are going into the trades. Anything that can make these jobs faster, easier, and more efficient will be essential.” FE
Flat: Generally used for load disbursement
Tab/Lock: Designed to effectively lock an assembly into place
Finishing: Often found on consumer products
Wave: For obtaining loads when the load is static or the working range is small
Belleville: Delivers the highest load capacity of all the spring washers
Fender: Distributes a load evenly across a large surface area
Shim Stacks: Ideal for simple AND complex applications
Boker’s Inc.
3104 Snelling Avenue
Minneapolis, MN 55406-1937
Phone: 612-729-9365
TOLL-FREE: 800-927-4377
(in the US & Canada)
bokers.com
Adhesive anchors typically offer greater flexibility than mechanical anchors, ensuring high performance for heavy-duty applications.Burn patients wear these 3D-printed masks to heal scars and prevent complications. “I almost prefer to have the mask on,” said patient Laura Weibel (pictured
3D printing is helping more patients than ever before through personalized medical devices, faster and cheaper prototyping and more affordable manufacturing.
Recent developments include research into tissue and organ regeneration, lightning-fast responses to supply chain shortages, wearables that improve patient treatment, and major investments by device manufacturers.
Here are some 3D printing advances that show what the future may hold. Go to wtwh.me/3dprinting2023 for links to
Device developers, healthcare providers and 3D printing technology suppliers are collaborating to improve device design, product manufacturing and patient care.
more information about these projects, partnerships and innovations.
Breast tissue regeneration
3D printer manufacturer Stratasys and bioink developer CollPlant have launched a collaboration to take tissue and organ bioprinting to an industrial level. Their first initiative is focused on CollPlant’s regenerative breast implants, which are being developed to regenerate a breast cancer patient’s natural tissue without triggering an immune response.
CollPlant said its bioprinted regenerative tissue formed connective tissue and
neovascular networks in a preclinical, largeanimal study that had no adverse events.
CollPlants said it plans to follow up this year with another large-animal study using commercial-size implants ahead of human studies and product commercialization.
“The combined, pioneering technologies of both companies will streamline the development and production process so that we have the most efficient means to produce our regenerative breast implants and other potential tissues and organs,” CollPlant CEO Yehiel Tal said.
“We believe that our rhCollagen-based regenerative implant has the potential to
overcome the challenges of existing breast procedures that use silicone implants or autologous fat tissue transfer.”
Award-winning innovation
A 3D-printed nasopharyngeal swab patented by the University of South Florida helped healthcare providers manage a global shortage of testing swabs in the COVID-19 pandemic.
The team developed the 3D-printed prototype in one week in March 2020 and shared the design for free with organizations, leading to the production of more than 100 million
swabs. That act of innovative altruism won the Patents for Humanity prize from the U.S. Patent and Trademark Offi ce.
“This recognition by the U.S. Patent and Trademark Offi ce validates both the tremendous power of academic medicine, especially during a crisis, and the values and commitment these teams have for contributing to the greater good,” said Dr. Charles Lockwood, EVP for USF Health.
Anatomical models
3D printing is allowing device developers and surgeons to build personalized models of organs, bones and other bodily structures. It’s possible to use the models for training, education, pre-operative planning or to test new and improved device prototypes.
MIT engineers are 3D printing individualized heart replicas to test how a particular valve implant will affect the performance of a specific patient’s heart.
“We’re not only printing the heart’s anatomy, but also replicating its mechanics and physiology,” MIT mechanical engineering professor Ellen Roche said. “That’s the part that we get excited about.”
Meanwhile, Stratasys and Ricoh are partnering on 3D-printed, personalized anatomic models for clinical settings. The ondemand models provide specific visualizations of a patient’s anatomy to allow practitioners to plan and practice complex surgeries and improve communication between medical staff, the patient and families.
Researchers in Switzerland are working on a 3D-printable ink that can mineralize to form a high-strength, lightweight bio-composite that mimics the structure and properties of bone. This “BactoInk” contains bacteria that trigger the production of calcium carbonate (CaCO3) without the need for the high temperatures necessary for manufacturing ceramics.
And last year, Stryker opened a 156,000 ft² facility for 3D printing in Ireland. It’s the latest investment in the field by the world’s largest orthopedics company, which has been working with additive manufacturing technology for more than 20 years. 3D printing metal joint replacements, for example, allows Stryker to make more porous implant surfaces for better bone fixation.
Mighty Oak Medical uses HP Jet Fusion 5200 3D printers
to make personalized surgical guides for the placement of pedicle screws in spinal surgeries. The medical device developer uses the same 3D printers to make patientspecific bone models for each surgery.
3D-printed face masks are helping pediatric burn patients heal better with personalized treatments.
The new technology also eliminates a potentially traumatic step for burn patients, who previously needed to endure warm plaster bandages to make masks of their faces.
“3D printing is something we’ve dreamed of for quite a long time,” said Christophe Debat, GM of Romans Ferrari pediatric rehabilitation center in France. “We had imagined that a 3D printer would allow us to produce a mask based on the scanned fi le without ever having to touch the patient.”
The team has treated more than 100 patients using a Formlabs Fuse 1 selective laser sintering (SLS) printer.
University of Hawaii researchers are working on a 3D-printed, wearable sweat sensor for health monitoring.
“3D printing enables an entirely new design mode for wearable sweat sensors by allowing us to create fluidic networks and features with unprecedented complexity,” Department of Mechanical Engineering Assistant Professor Tyler Ray said. “With the ‘sweatainer,’ we are utilizing 3D printing to showcase the vast opportunities this approach enables for accessible, innovative and cost-effective prototyping of advanced wearable sweat devices.”
Formlabs this year launched its Automation Ecosystem for manufacturers that want to expand from a single 3D printer to a scalable fleet.
Researchers published a method for 3D-printing an ink that contains calcium carbonate-producing bacteria. The 3D-printed mineralized bio-composite is unprecedently strong, light, and environmentally friendly, with a range of applications from art to biomedicine.
Formlabs said the new offering can increase productivity and reduce materials costs and packaging waste.
“These solutions will enable companies such as dental labs, service bureaus, and internal job shops to ramp up production without increasing labor requirements, or expensive capital investment, making 3D printing for production more cost-effective,” Formlabs
Chief Product Officer Dávid Lakatos said.
First FDA clearance for Stratasys
Stratasys won FDA clearance this year for its TrueDent 3D printing resin for making dentures.
The resin is the company’s first FDAcleared medical device, developed for printing exclusively with the Stratasys J5 DentaJet 3D printer and GrabCAD Print software platform.
“This new solution will be transformative for the dental industry, and we believe it will help our customers signifi cantly reduce the time and cost of producing dentures and temporaries,” Stratasys Dental VP Ronen Lebi said at the time.
Stratasys and Desktop Metal plan to merge in a $1.8 billion deal by the end of 2023. Both companies serve medical device developers and the broader healthcare market.
The companies estimate they’ll have $1.1 billion in 2025 revenue after the combination. The combined companies will have more than 800 scientists and engineers.
“With attractive positions across complementary product offerings, including aerospace, automotive, consumer products, healthcare and dental, as well as one of the largest and most experienced R&D teams, industry-leading go-to-market infrastructure and a robust balance sheet, the combined company will be committed to delivering ongoing innovation while providing outstanding service to customers,” Stratasys CEO Yoav Zeif said.
In April, Stratasys completed its acquisition of Covestro’s additive manufacturing materials business, covering approximately 60 additive manufacturing materials and an IP portfolio with hundreds of patents and patents pending. The deal also included R&D facilities and activities, a global development and sales team in Europe, the U.S. and Asia.
“With this acquisition, we’re not just expanding our materials portfolio for our broad array of 3D printing technologies — we’re also paving the way for more new innovations,” Zeif said at the time. “Additionally, our growing team of inhouse materials experts will be in a stronger position to collaborate with our materials ecosystem partners. Together, we’ll be able to address more applications faster, pushing the boundaries of what’s possible in additive manufacturing.”
It’s good to know where you come from. At Nitto Kohki, we come from a line of engineers and businessmen dedicated to exceptional manufacturing execution. In our line of vacuum and pressure pumps, this is seen in the unique linear-piston design, where one moving part resolves to exceptional reliability, low vibration and noise, high energy efficiency, and long, consistent performance life (>10,000 hrs.) for a host of critical medical applications. It’s why the medical device industry has specied Nitto pumps for over sixty years— the quality in our DNA. Find out how you can use it to your advantage.
Whether it's OpenAI’s ChatGPT or Microsoft’s new Bing, 2023 is the year when generative artificial intelligence entered the popular consciousness.
In the medtech space, it seems as though every company is seeking ways to incorporate some form of AI into the digital features of their products and services.
So what is artificial intelligence good at when it comes to advancing medtech and healthcare in general? Here are seven recent examples:
1. Helping physicians quickly identify medical problems
Interest is growing in artificial intelligence that can help radiologists, gastroenterologists and others better spot potential diseases in the countless images they examine each day.
For example, GI Genius is an AIassisted colonoscopy tool designed to help detect polyps that may lead to colorectal cancer. Medtronic is the exclusive worldwide distributor of the technology, which was developed and manufactured by Cosmo Pharmaceuticals.
Giovanni Di Napoli, president of the Gastrointestinal business at Medtronic, showed some GI Genius footage at our DeviceTalks West event in Santa Clara, California, this past October. Historically, gastroenterologists detected fewer
lesions while performing colonoscopies as their day progressed from morning through the afternoon. GI Genius’ AIbased enhancements help physicians stay focused by placing green boxes around areas that may need extra scrutiny during the diagnostic imaging procedure.
GI Genius could soon get even better. Medtronic has partnered with Nvidia to enhance the tool's AI capabilities, allowing third-party developers to train and validate their AI models using the GI Genius AI Access platform. This technology has the potential to improve patient outcomes and reduce medical variability, while transforming the way healthcare approaches the early detection of colorectal cancer.
In other recent news, Viz.ai secured FDA clearance for its artificial intelligencepowered algorithm designed to detect and triage care for suspected abdominal aortic aneurysms (AAAs). Viz AAA automatically analyzes computed tomography angiography (CTA) scans for suspected AAAs. It alerts clinicians, displaying patient scans on their mobile devices for real-time communication among specialists. Jayme Strauss, chief clinical officer at Viz.ai, thinks Viz AAA will enable care teams to prevent
aortic rupture and other catastrophic aortic emergencies by increasing surveillance. Viz.ai plans to continue expanding its healthcare offerings.
Meanwhile, HeartBeam recently secured a pivotal patent related to artificial intelligence capabilities for its AIMIGo system — a personal, portable vector electrocardiogram (VECG) system. HeartBeam is now partnering with Samsung to boost cardiac diagnostics.
It is hard these days to find a digital health or health monitoring company that is not talking about incorporating artificial intelligence into its offerings. AI has the potential to enable more discreet sensor arrays. The result is that doctors and patients can gain insights from the monitoring with minimal hassle. For example, Sensydia, which has undertaken multiple clinical studies, recently completed enrollment in a 225-subject development study for its AI-powered Cardiac Performance System (CPS). The Los Angeles–based company designed the noninvasive CPS device to analyze heart sound and provide physicians with a full
Control solenoid valves from The Lee Company offer superior quality, proven reliability, and long-lasting performance. For your most demanding medical and scientific applications, choose a valve that hits the mark every time.
Scan to explore our full collection of control solenoid valves.
cardiac assessment of patients in under 5 minutes. The CPS device may enable earlier detection and improved therapy guidance for heart failure and pulmonary hypertension patients.
The CPS uses ultra-sensitive biosensors for the rapid, noninvasive measurement of a number of cardiac metrics, such as ejection fraction, cardiac output, pulmonary artery pressure, and pulmonary capillary wedge pressure. Traditionally, patients need echocardiography and invasive catheterization to obtain these measurements, according to the company.
Sensydia announced in early May that it has raised an additional $8 million from an expanded syndicate of investors. The company plans to submit to the FDA in 2024 for prioritized review as part of the agency's Breakthrough Devices Program.
Meanwhile, Boston-based Biofourmis has AI-driven software to collect and analyze patient data in real-time to identify shifts that require proactive interventions. It partnered with Japanese pharma giant
Chugai to objectively measure pain in women with endometriosis. Their strategy is to use a biosensor and an AI-based algorithm utilizing Biofourmis' Biovitals.
3. AI-enabled prosthetics
Advanced AI algorithms hold promise to better enable people to use myoelectric control — involving discreet electric signals from their muscles — to control robotic prosthetics.
For example, Ottobock has its Myo Plus pattern recognition system for trans-radial users. Myo Plus is meant to allow the system to adjust to natural movements versus requiring the user to adapt to the system.
4. Better visualization during surgery
colon. There was a clear difference in visualization during AI mode.”
Later, study results released from OSU found that that in 17.5% of cases surgeons changed an intraoperative decision based on additional information provided by ActivSight’s advanced visualization.
5. Improved data collection from medical settings
place green boxes around areas that may need extra scrutiny during a colonoscopy, helping to prevent physicians from losing their focus.
Activ Surgical announced in January that it completed the first AI-enabled surgery using its ActivSight Intelligent Light product. Designed to provide enhanced visualization and real-time, on-demand surgical insights in the operating room, the ActivSight model attaches to laparoscopic and robotic systems and integrates with standard monitors. The first AI-enabled ActivSight surgery took place on Dec. 22, 2022, at the Ohio State University Wexner Medical Center. Dr. Matthew Kalady performed a laparoscopic left colectomy using the colorectal AI mode within ActivSight. The company says its goal is for every surgical imaging system to deliver intelligent information, reducing surgical complication rates. >>
“While using one of ActivSight’s intraoperative visual overlays, the dyefree ActivPerfusion Mode, I was able to clearly see key critical structures in the surgical site and tissue perfusion in real-time,” Kalady said in a news release. “With the press of a button, the colorectal AI mode was enabled, removing distractions of background signals from non-bowel tissue and clearly focusing on perfusion to the
Artificial intelligence could help with surgical data collection. A case in point is Proprio, which is rolling its AI-powered surgical navigation system into operating rooms to collect data. The idea is that the data will ultimately help surgeons improve how they perform procedures. The Seattle-based startup said it has placed its Paradigm visualization and navigation system in several U.S. operating rooms to capture surgical data that will be useful for accelerating the system’s development. Proprio announced FDA clearance of the Paradigm system in late April.
6. Making better sense of patient data GE HealthCare last year unveiled its Edison Digital Health Platform, an AIpowered, vendor-agnostic hosting and data aggregation platform. The medtech giant said the aim of the platform is to enable the easy deployment of clinical, workflow, analytics, and AI tools, connecting devices and other data sources into an aggregated clinical data layer. The open and published interfaces on Edison support the integration of healthcare providers and third-party developers' applications into existing workflows. GE HealthCare had plans to integrate and deploy its own apps onto the platform. A company official said the goal was for clinicians to have actionable insights at their fingertips to help better serve their patients.
Sensydia's AI-powered Cardiac Performance System (above) uses ultra-sensitive biosensors for the rapid, noninvasive measurement of a number of cardiac metrics. Traditionally, patients need echocardiography and invasive catheterization (top) to obtain these measurements, according to the company. Image courtesy of Sensydia
DeepMind, which has the same parent company as Google, has an artificial intelligence system called AlphaFold that cracked an extremely difficult scientific problem. It predicted the structure of more than 200 million proteins, which represent almost every known cataloged protein. AlphaFold is capable of making it possible to search for the 3D structure of proteins almost as easily as doing a keyword Google search. It has also made the data freely available to users for any purpose. Applications of the AI system include accelerating the discovery of drugs for neglected diseases, combating antibiotic resistance, studying the nuclear pore complex, developing a novel malaria vaccine, shedding light on genetic variation, gauging the impact of rotavirus on gastroenteritis, and contributing to drug development for cancer and neurological disease.
Emerson’s expertise in plastic joining and fluid control makes complex medical devices more compact and easier to manufacture.
Learn more at Emerson.com/Medical
Abbott says its HeartMate 3 LVAD is clinically proven to extend life by five years or more — but thousands of people in the U.S. still die of heart failure within a year.
Kyree Miller, a 30-year-old college student, navigated seven long years of heart failure with the assistance of an Abbott HeartMate left ventricular assist device (LVAD).
“Before I got my LVAD, there was no way I was getting on a plane. Before I got my LVAD, there was no way I was going back to work. And I was able to do both of those things — and more. To be at Killington [ski resort] with an LVAD, I never thought it would have happened, but it did,” Miller told a group of medtech insiders during our annual DeviceTalks Boston show in May.
In August 2022, Miller received a new heart.
“Having the LVAD was crucial in bridging the gap before the heart transplant,” he said. “Without
it, I don’t think I would have been here to receive the transplant.”
Miller was fortunate to live in Boston, a city that’s one of the nation’s top healthcare and research hubs. He was near top-notch hospitals with access to LVADS such as Brigham and Women’s Hospital, Beth Israel Deaconess Medical Center and Massachusetts General Hospital. Cardiologists at top hospitals knew what LVADs could do.
“Being here with the big centers a stone’s throw away was a big help,” Miller said. His story highlights a challenge that Abbott officials are fighting to answer.
The company’s research has shown that its HeartMate 3 pump can extend the lives of advanced heart patients by at least five years.
However, Abbott estimates the U.S. has 15,000 advanced heart failure patients who are managed with inotropic therapies alone; they have a projected median lifespan under a year.
“Kyree is lucky to be in a place where he can get access, was referred, and had people who made the right referral based upon the disease that he had. And the benefits are obvious,” said Dr. Robert Higgins, president of Brigham and Women’s Hospital and EVP of Mass General Brigham.
“The challenge that we're thinking about is that not everyone has a cardiologist, or access to advanced heart failure therapies,” Higgins continued. “And in particular, [minorities] and women don't necessarily have access to advanced heart failure therapies, which include LVADs, as well as the modern technologies — transplant being one of them.”
Miller later said: “As a gay Black man, the healthcare system can't be one-size-fits-all, either. And in some ways, it feels like it is.”
Implanted through open heart surgery, a left ventricular assist device pumps blood from the lower chambers of the heart to the rest of the body.
It can provide a crucial bridge to keep someone like Miller alive until a donor heart is available for transplant. Even when a person isn’t
eligible for a transplant, it can sometimes still provide years of extra life.
The transformative power of LVADs in the realm of advanced heart failure therapy cannot be overstated. Abbott’s HeartMate devices became the sole LVAD technology available in the U.S. when Medtronic stopped sales of its HVAD in June 2021 due to mounting issues with the platform.
Abbott’s latest generation HeartMate 3 is smaller than a baseball. Its Full
MagLev Flow Technology utilizes a fully magnetically levitated, self-centering rotor that does not require hydrodynamic or mechanical bearings. The result, according to the company, is gentle blood handling to minimize complications and hemocompatibility-related adverse events.
There are over 50,000 patients who have been implanted with Abbott’s HeartMate II or HeartMate 3, and at least 1,000 of those who received the HeartMate II have lived for over 10 years with LVAD support, according Dr. Robert Kormos, division VP of global medical affairs for Abbott’s heart failure tech.
Abbott has some ideas about how to help Even a multibillion-dollar company such as Abbott can’t reform the U.S. healthcare system’s care disparity on its own, but company offi cials think there are things they can do to improve the situation.
They’re working on smaller pumps. And Kevin Bourque — VP of R&D at Abbott — thinks better education could clear up a misunderstanding among some doctors that a HeartMate 3 won’t fit in smaller patients, including women and children.
A recent study found it’s the size of the heart that matters more than the size of the patient, he said.
“A couple of years ago, we got a pediatric approval for our HeartMate 3 devices that are being put into children as young as 7 or 8 years old,” Bourque
said. “... There certainly is some room to go to get into truly small patients, truly small chests. But that's not the whole trick, being smaller. I think we need to be physiologically responsive as well. So we're thinking about how do we make these devices not just be life-savers, but life-optimizers. With all of those strategies in play, I think we can start to reduce the bridge, approaching the value that transplant can bring. We're kind of on the precipice of doing that.”
In general, better education and dissemination of heart failure treatment guidelines among physicians would help, according to Higgins.
“I think education is going to be critically important to help physicians understand not only that there are at-risk populations, women and persons of color, but everybody benefits from an informed provider who can identify heart failure at its earliest stages and get patients into a comprehensive therapy,” Higgins said.
Kormos suspects the medical community may be too focused on treating symptoms while neglecting the underlying cause. “The problem with that is that by the time a patient says, ‘I don't feel good anymore,’ it's too late.”
Access to better cardiac diagnostics and monitoring could catch heart problems earlier so people have time to find out about LVADs as an option.
“We have a pulmonary pressure monitor that we put in people, the CardioMEMS, which is a small dime-size sensor that goes into the pulmonary artery and can measure changes in your pulmonary pressure. We know that with heart failure, that goes up, and as it goes up, your right heart starts to fail,” Kormos said.
According to recent studies, CardioMEMS can nearly halve heart failure hospitalizations and significantly reduce the risk of death.
Miller still has a CardioMEMS inside him.
“I don't necessarily use it, obviously, as much as I used to,” he said. “But every once in a while just to do a check in, we still actually use it just to make sure that things are going in the right direction.”
“Before I got my LVAD, there
I
getting on a plane. Before I got my LVAD, there was no way I was going back to work. And I was able to do both of those thingsAbbott VP of R&D Kevin Bourque Mass General Brigham EVP
If Miller hadn’t gotten into a cutting-edge hospital system he wouldn’t have had access to CardioMEMS or an LVAD — and he wouldn’t be around today, Higgins said. “People are dying waiting for that type of technology.”
Kormos said Abbott and other major medtech companies have been working on more inclusive clinical trials and designing devices to serve more diverse populations.
All of Abbott’s efforts matter because LVADs not only keep people alive, Bourque said, but they enable them to lead productive lives.
Said Bourque: “Every year that Kyree lives is a valuable thing. You’ve returned to society.”
Analytical instrumentation and medical device manufacturers must meet growing demand for high-quality, durable products on accelerated project timelines and within strict regulatory frameworks. These challenges require partnerships with globally accessible, flexible, and experienced engineering teams.
With Emerson, you can rely on a partner that delivers high-performance fluid-handling solutions from prototype phase to shipment, including specific miniature valve designs and fully engineered, turnkey solutions. Our comprehensive portfolio of industry-proven ‘standard catalogue’ valves ship typically within days to support rapid qualification and testing. We’ll also design, manufacture, and deliver customized solutions tailored to exact device specifications on tight turnarounds.
Learn how Emerson can address your delivery and product reliability challenges at: Emerson.com/rapid-engineered-solutions
Nitto Kohki’s DC motor-driven air compressors and vacuum pumps are ideal for applications requiring exceptionally reliable air flow, pressure or vacuum performance. Featuring oil-free operation, a single moving part, low noise, and low vibration, this line of linear air compressors comes in 12V and 24V models. Other benefits include:
• Very low power consumption
• Self-cooling design
• Exceptional service life (rated at 10,000 hours)
• Easy maintenance
Ideal for demanding applications in the medical device and laboratory equipment industry, including dialysis machines, blood separators, blood analyzers, incubators, heart assist devices and more.
SDP/SI creates precision gears, superior mechanical components, and customized motion control solutions for medical device OEMs. With over 70 years of experience and proven performance SDP/SI provides the reliability that the medical industry requires. Partnering with companies that include Abbott Laboratories, Intuitive Surgical, Siemens Healthcare, Medtronic, and many more, we provide support from the early design stage through delivery.
• Precision CNC Manufacturing
• Engineering Development – with years of experience we know how to make systems smaller, lighter, and faster.
• ISO 7 Class 1000 Cleanroom for Assembly
• Gear Cutting / Bevel Gear Cutting
• Custom Drive Systems / Gearboxes
Send an RFQ online, discuss your project with our engineers, visit our facility. We look forward to working with you!
Field-wireable and overmoulded
4+FE, 63 V DC up to 16 A
Degree of protection IP67 (mated)
Solder, dip solder and stranded versions
www.binder-usa.com
SALES
Ryan Ashdown rashdown@wtwhmedia.com 216.316.6691
Jami Brownlee jbrownlee@wtwhmedia.com
224.760.1055
Mary Ann Cooke mcooke@wtwhmedia.com
781.710.4659
Jim Dempsey jdempsey@wtwhmedia.com
216.387.1916
Mike Francesconi mfrancesconi@wtwhmedia.com
630.488.9029
Jim Powers jpowers@wtwhmedia.com
312.925.7793
@jpowers_media
Courtney Nagle cseel@wtwhmedia.com
440.523.1685
@wtwh_CSeel
Publisher Mike Emich memich@wtwhmedia.com
508.446.1823
@wtwh_memich
CEO
Scott McCafferty smccafferty@wtwhmedia.com
310.279.3844
@SMMcCafferty
EVP
Marshall Matheson mmatheson@wtwhmedia.com
805.895.3609
@mmatheson
CFO
Ken Gradman kgradman@wtwhmedia.com
773-680-5955
DESIGN WORLD does not pass judgment on subjects of controversy nor enter into dispute with or between any individuals or organizations. DESIGN WORLD is also an independent forum for the expression of opinions relevant to industry issues. Letters to the editor and by-lined articles express the views of the author and not necessarily of the publisher or the publication. Every effort is made to provide accurate information; however, publisher assumes no responsibility for accuracy of submitted advertising and editorial information. Non-commissioned articles and news releases cannot be acknowledged. Unsolicited materials cannot be returned nor will this organization assume responsibility for their care.
DESIGN WORLD does not endorse any products, programs or services of advertisers or editorial contributors. Copyright© 2023 by WTWH Media, LLC. No part of this publication may be reproduced in any form or by any means, electronic or mechanical, or by recording, or by any information storage or retrieval system, without written permission from the publisher.
Subscription Rates: Free and controlled circulation to qualified subscribers. Nonqualified persons may subscribe at the following rates: U.S. and possessions: 1 year: $125; 2 years: $200; 3 years: $275; Canadian and foreign, 1 year: $195; only US funds are accepted. Single copies $15 each. Subscriptions are prepaid, and check or money orders only.
Subscriber Services: To order a subscription or change your address, please email: designworld@omeda.com, or visit our web site at www.designworldonline.com
DESIGN WORLD (ISSN 1941-7217) is published monthly by: WTWH Media, LLC; 1111 Superior Ave., Suite 2600, Cleveland, OH 44114. Periodicals postage paid at Cleveland, OH & additional mailing offices.
POSTMASTER: Send address changes to: Design World, 1111 Superior Ave., Suite 2600, Cleveland, OH 44114
Detroit, or at least the Detroit Airport, has one clear advantage over other airports. This is thanks, I believe, to Ferruccio Ratti. Research was required to identify Ratti. All I had to go on was my observations of an innovation in action.
Let me begin by saying I don’t like most of the definitions out there for innovation. Most equate innovation and invention. I reserve innovation for an invention put to practice. I reserve innovation for inventions making an impact. A great innovation is inventive, but it must also be useful. It must be in use, making a di erence.
Some innovations are overly complicated. They can require years of work and refinement. Others are startlingly simple. I love the simple ones, those that take your breath away with the purity of the idea. I love the ones where upon seeing it, you almost can’t imagine how no one else thought of it — the ones that appear obvious.
Robert Kearns and his invention of the intermittent windshield wiper is an example. His story is one of the best-known patent infringement cases
and the subject of a New Yorker article subsequently made into a movie. Kearns won cases against Ford and Chrysler. Both claimed his idea for an intermittent wiper was obvious, that it failed to meet the standards of originality and novelty required for a patent. They claimed an invention had to be “non-obvious.” They were wrong. Intermittent wipers are certainly obvious once you see them. Yet, there were no intermittent wipers prior to Kearns. Everyone missed the obvious except him. His capture of the obvious made for a very useful innovation. Intermittent wipers are incredibly handy.
Recently, I travelled from Michigan to Colorado. I was able to experience two large airports in Detroit and Denver and visited the bathroom at both. Walk into a Denver airport men’s room and you’ll find a group waiting while one waves his hands in front of a touchless dispenser hoping to make a towel appear. Sensors in Denver require triggering hand movements before releasing a towel. After each towel, there is a programmed delay, likely
to keep multiple towels from being dispensed. The exact movements required to conjure a towel are elusive, leading users to make a string of ever more frantic hand motions hoping to produce a towel. Everyone is delayed. It was very di erent in Detroit, thanks to a simple innovation. Walk into a Detroit airport men’s room and you are confronted with a paper towel ready to grab. Removal of a towel instantly triggers dispensing another. No handwaving. No lines. Detroit got it right.
Once I realized what was going on, I went searching for the inventor, the person responsible for this beautifully simple innovation. I learned about Ferruccio Ratti, the first to patent a towel dispenser that produces a new towel when a towel is removed. Far from new, Ratti patented his invention in 1973. Ratti’s invention is there for all to use, beautiful in its simplicity. Thankfully, Detroit airport is availing itself of his innovation. As for Denver ... it has some catching up to do. DW
End-to-end and custom automation solutions for less
• 6-axis maintenance-free ReBeL® cobot
• Fully modular Apiro® gearbox system
• Dry-running drylin® linear actuators
• Robot transfer unit for robotic arms
• Lightweight e-chain® cable carriers
• Self-lubricating gantry & delta robots