

PRIME
Advanced Engineering. Prototyping. Product Development. Micro-Manufacturing. Learn More at Resonetics.com
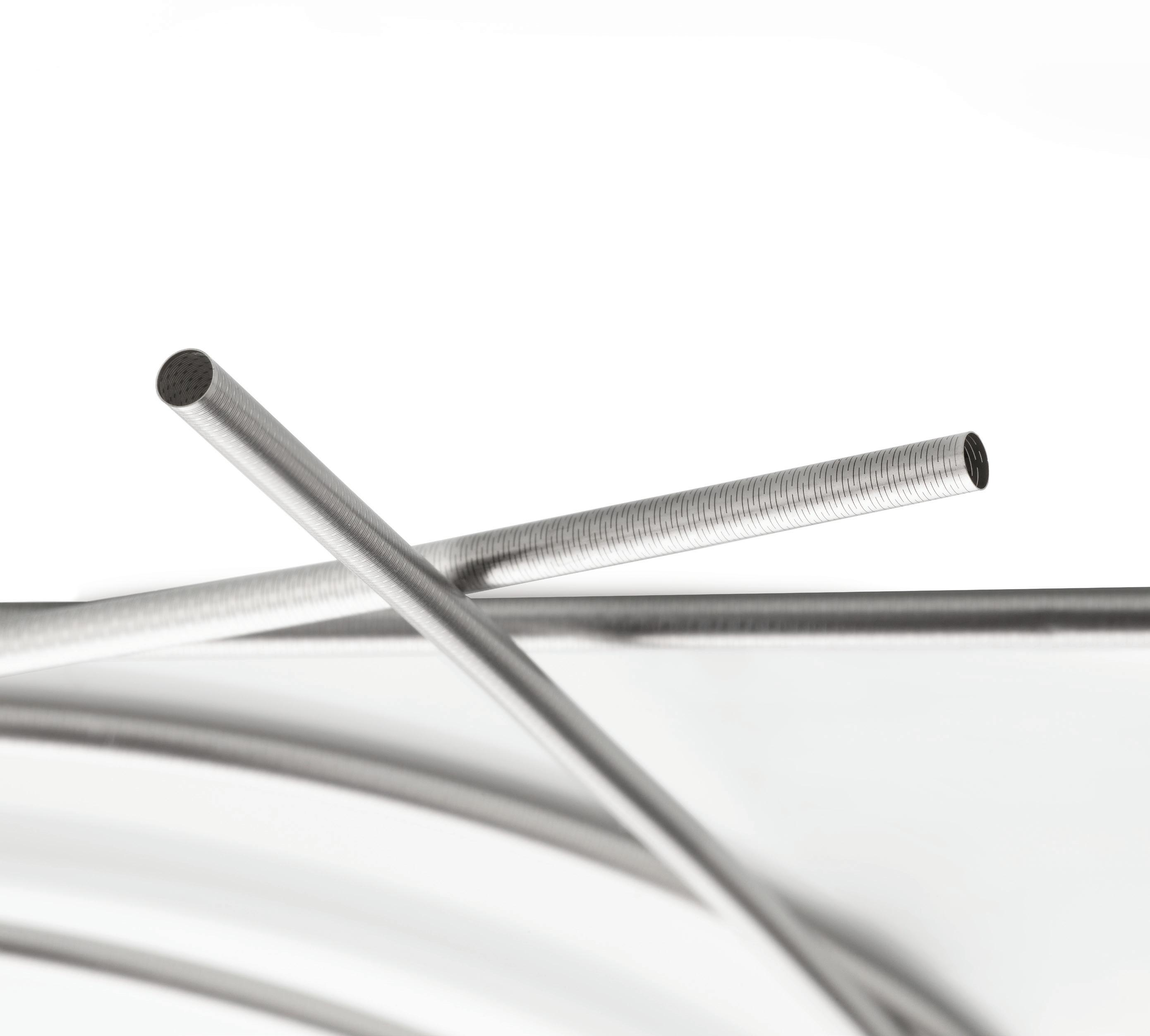
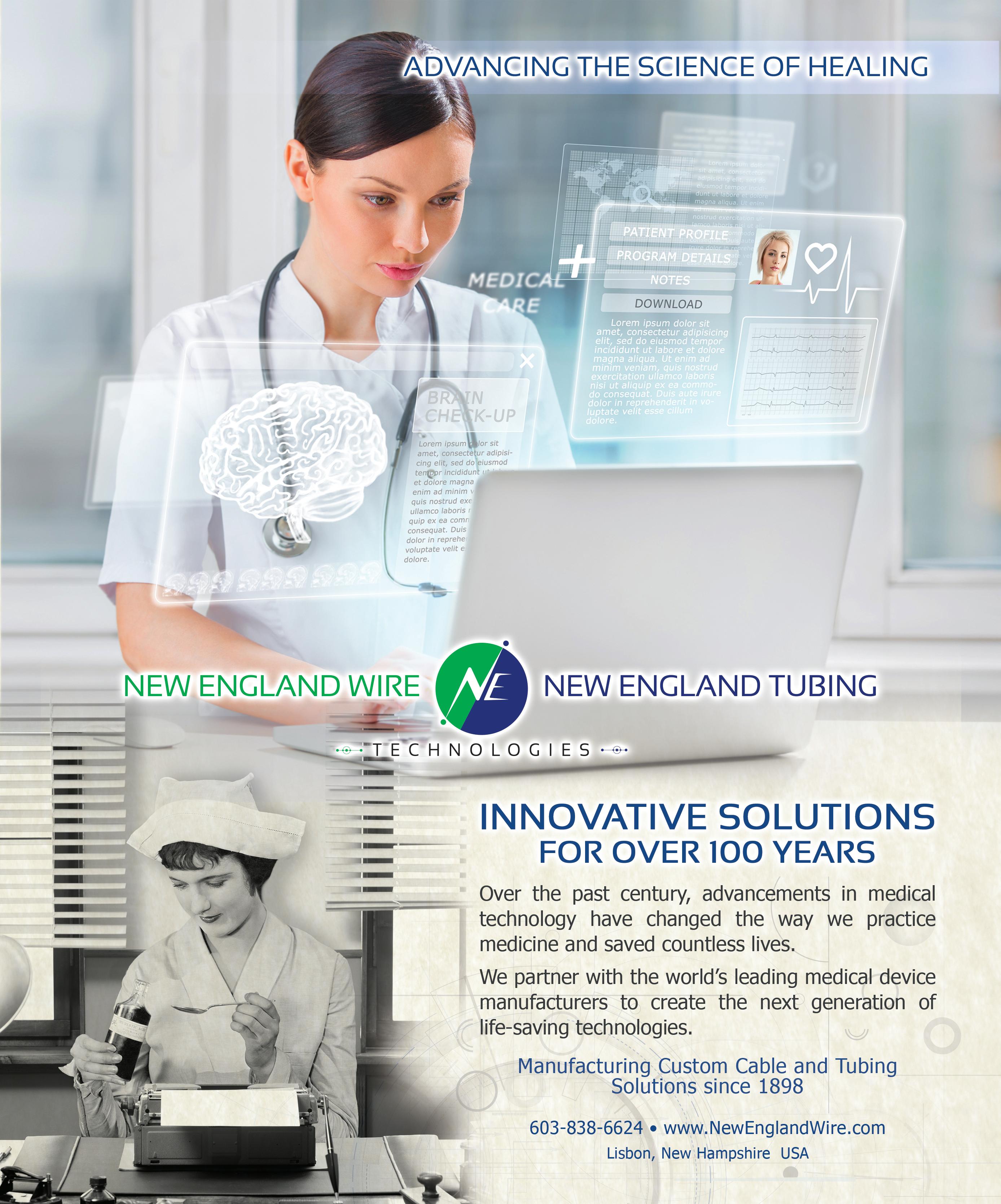
From
It’s where experience, quality and accuracy matter the most.
With a strategic focus on quality and personal service, we help our clients ensure the safety and efficacy of their products by delivering unparalleled testing services with complete, compliant and accurate data.
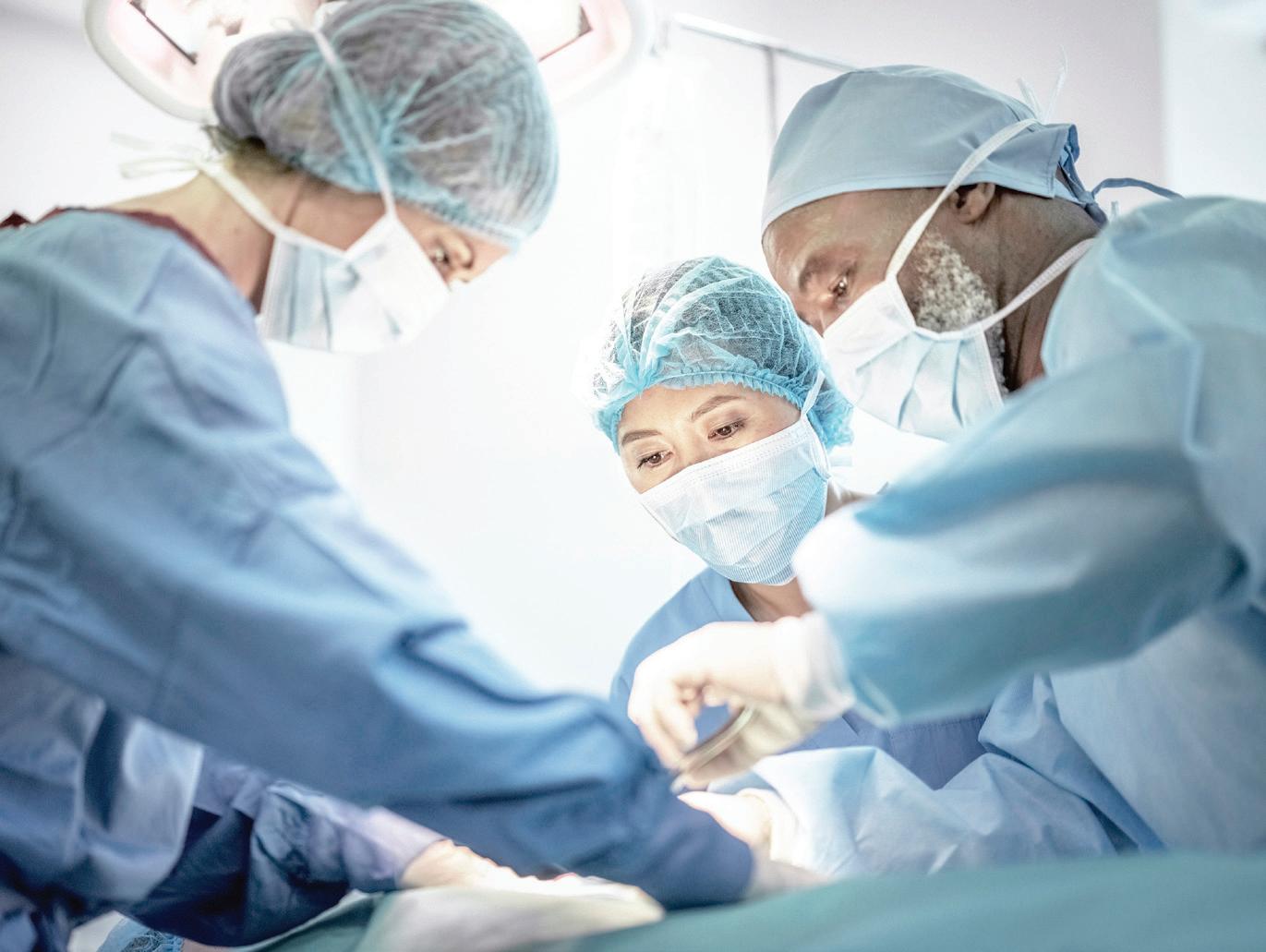
As a trusted partner for over 40 years, let our experience and global reach work for you. Chemical/Physical
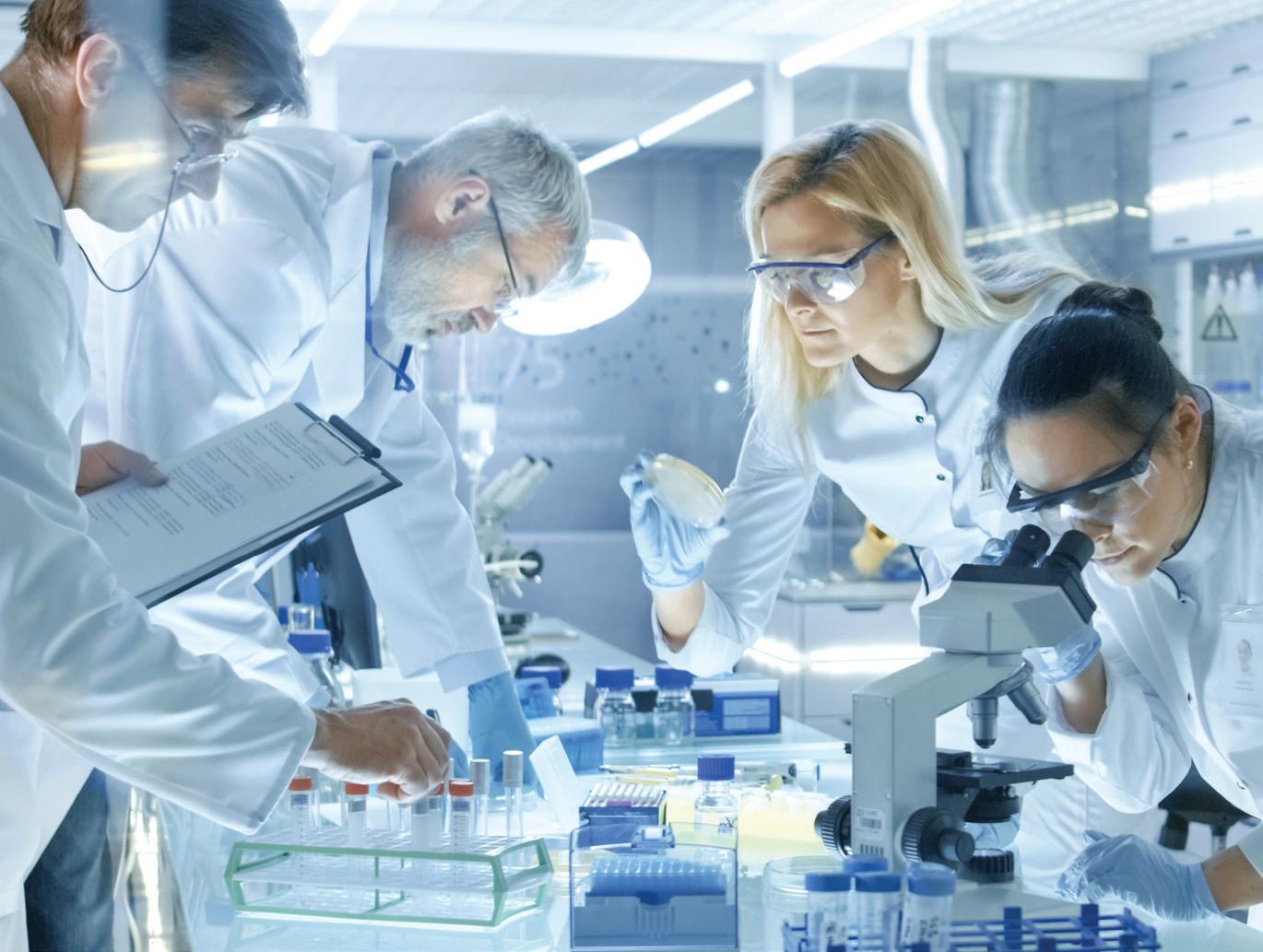
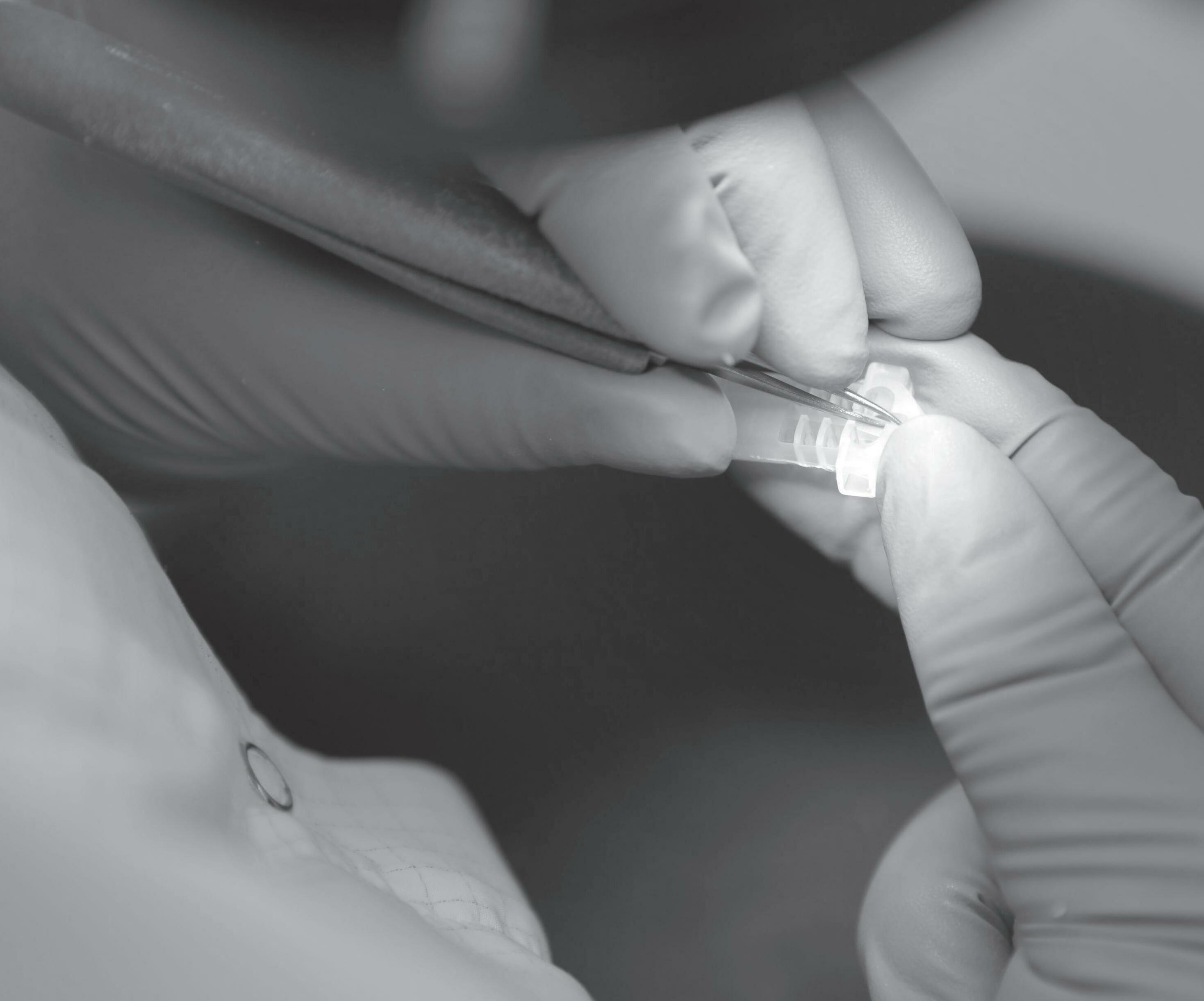
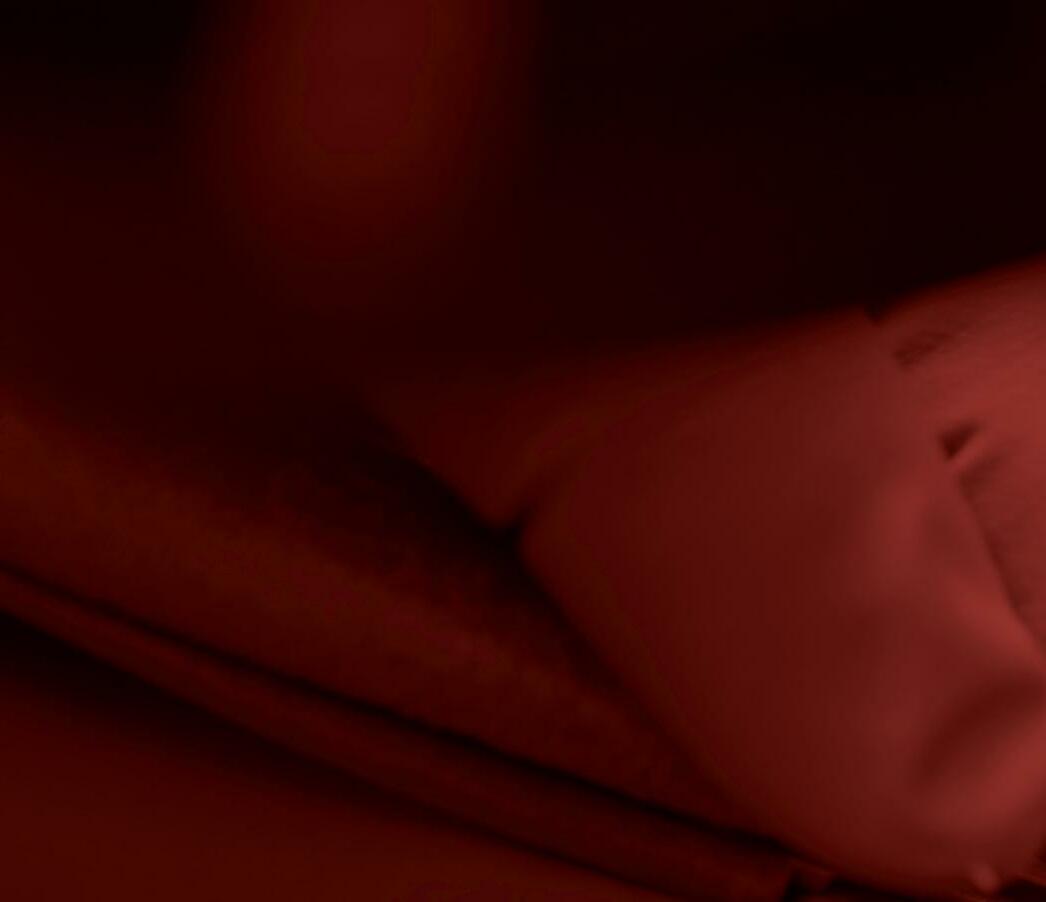

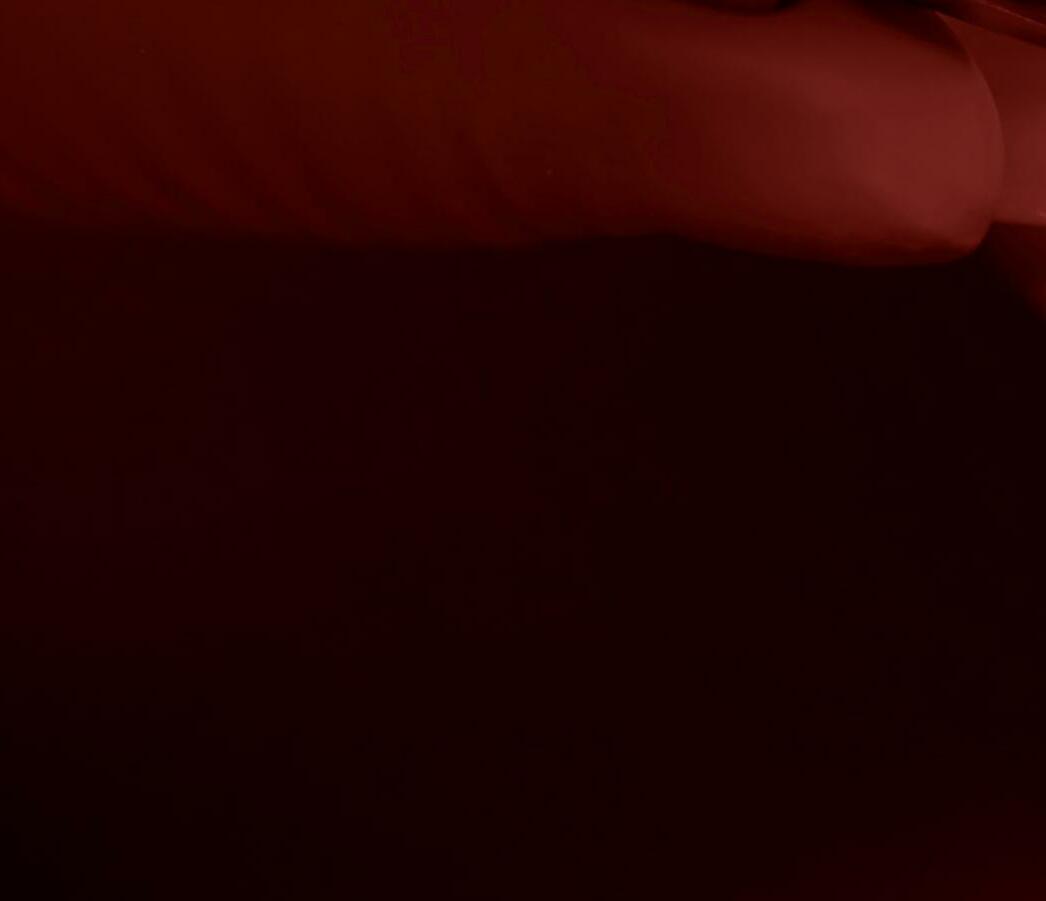
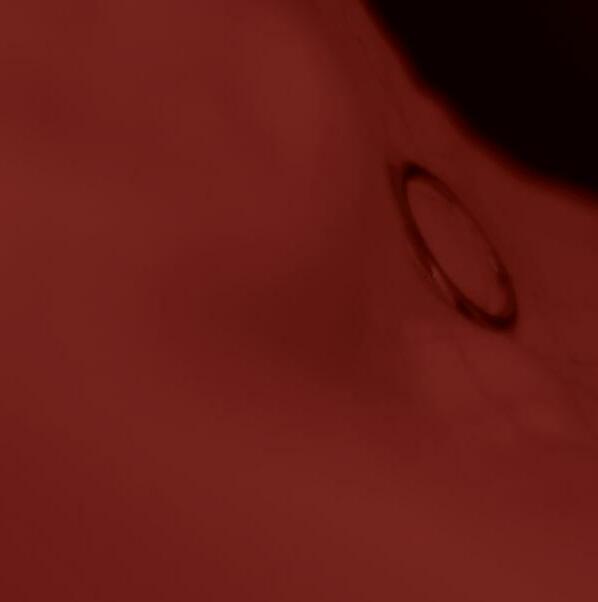

EDITORIAL
VP, Editorial Director
Paul J. Heney pheney@wtwhmedia.com @wtwh_paulheney
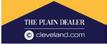
Managing Editor
Mike Santora msantora@wtwhmedia.com @dw_mikesantora
Executive Editor Leland Teschler lteschler@wtwhmedia.com @dw_leeteschler
Executive Editor
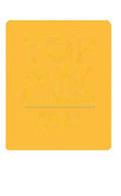
Lisa Eitel leitel@wtwhmedia.com @dw_lisaeitel
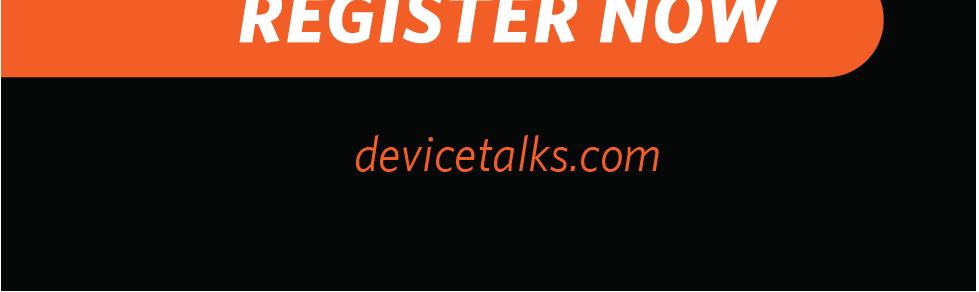
Senior Editor Miles Budimir mbudimir@wtwhmedia.com @dw_motion
Senior Editor Mary Gannon mgannon@wtwhmedia.com @dw_marygannon
Senior Editor Rachael Pasini rpasini@wtwhmedia.com
Associate Editor Heather Hall hhall@wtwhmedia.com @wtwh_heathhall
Senior Contributing Editor Leslie Langnau llangnau@wtwhmedia.com @dw_3dprinting

CREATIVE SERVICES
VP, Creative Services Mark Rook mrook@wtwhmedia.com @wtwh_graphics
Senior Art Director Matthew Claney mclaney@wtwhmedia.com @wtwh_designer
Senior Graphic Designer Allison Washko awashko@wtwhmedia.com @wtwh_allison
Graphic Designer Mariel Evans mevans@wtwhmedia.com @wtwh_mariel
Director, Audience Development Bruce Sprague bsprague@wtwhmedia.com
WEB DEV / DIGITAL OPERATIONS
Web Development Manager

B. David Miyares dmiyares@wtwhmedia.com @wtwh_webdave
Senior Digital Media Manager
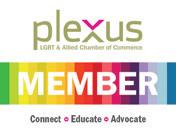
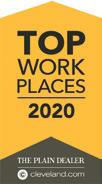




Patrick Curran pcurran@wtwhmedia.com @wtwhseopatrick

Front End Developer Melissa Annand mannand@wtwhmedia.com
Software Engineer David Bozentka dbozentka@wtwhmedia.com
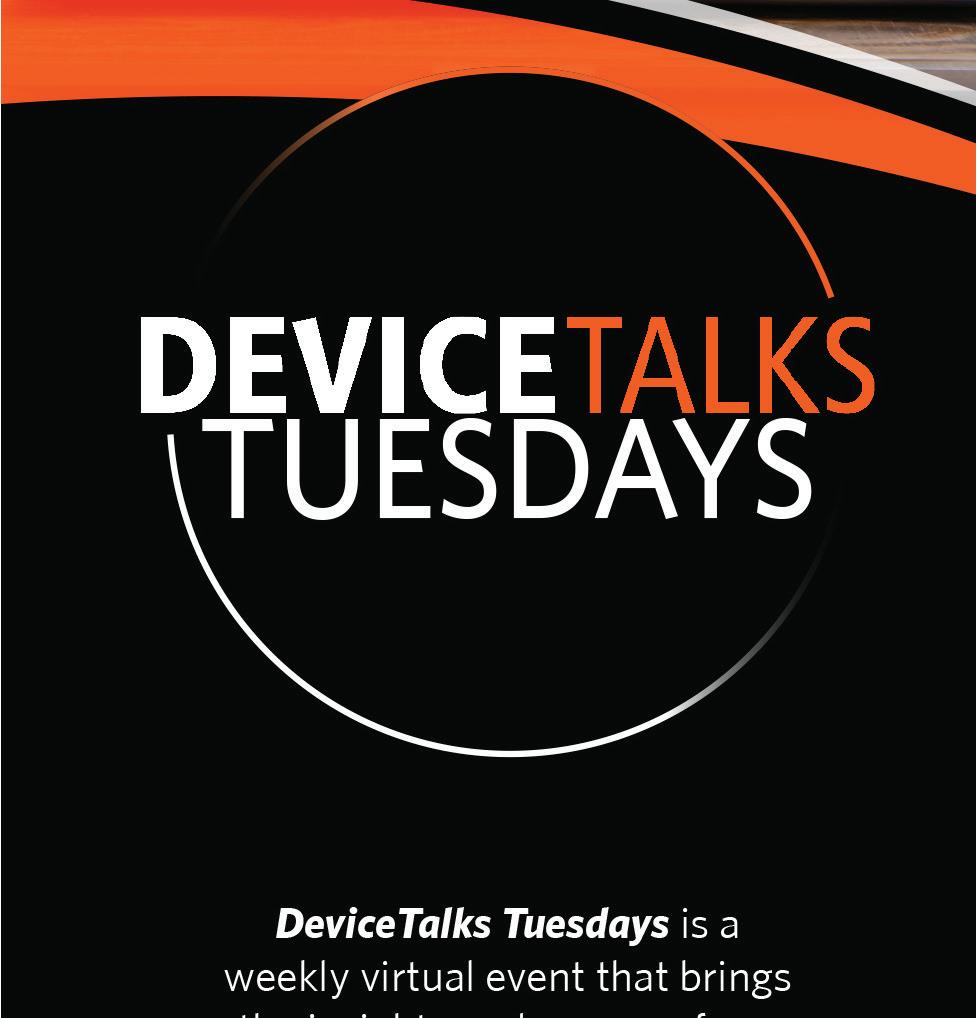
DIGITAL MARKETING
VP, Digital Marketing Virginia Goulding vgoulding@wtwhmedia.com @wtwh_virginia
Digital Marketing Manager Taylor Meade tmeade@wtwhmedia.com @WTWH_Taylor
Digital Marketing Coordinator Jill Bresnahan jbresnahan@wtwhmedia.com @WTWH_Jill Webinar Coordinator Halle Sibly hkirsh@wtwhmedia.com Webinar Coordinator Kim Dorsey kdorsey@wtwhmedia.com
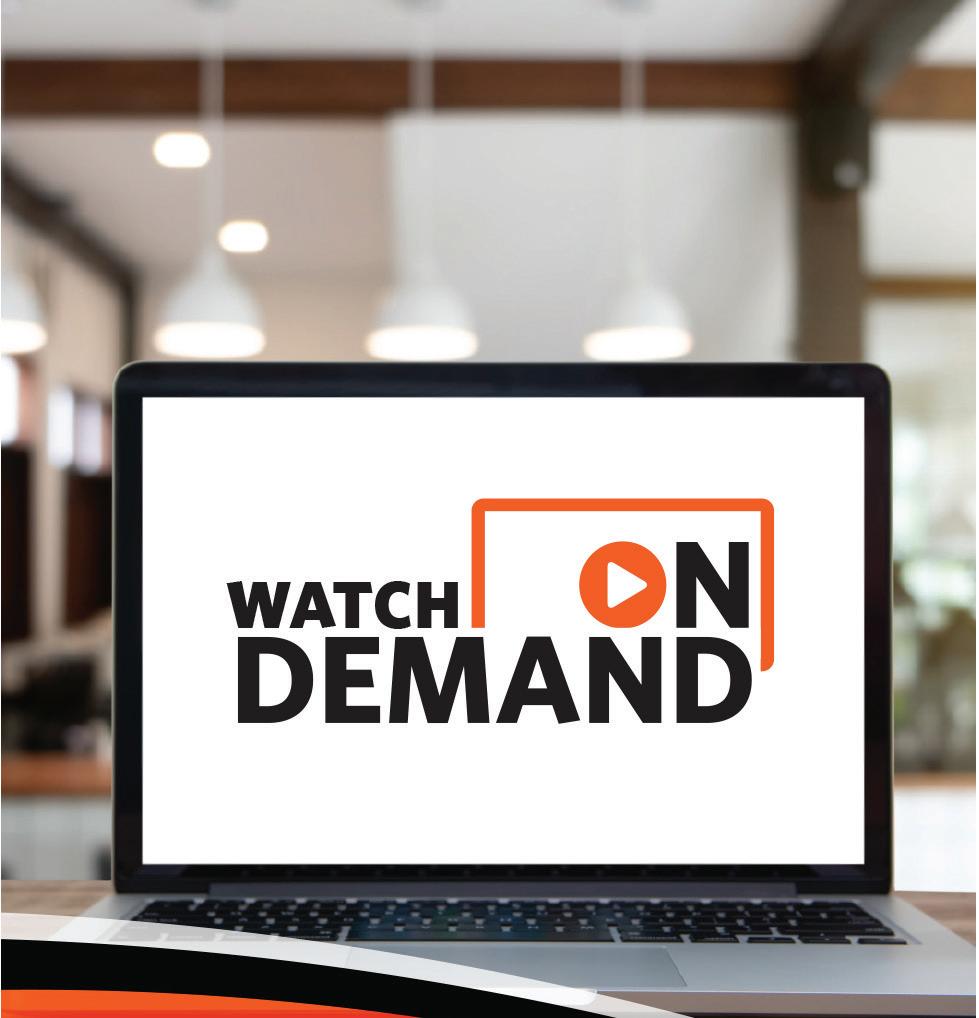
EVENTS

Events Manager Jen Osborne josborne@wtwhmedia.com @wtwh_jen
Events Manager Brittany Belko bbelko@wtwhmedia.com
Event Marketing Specialist Olivia Zemanek ozemanek@wtwhmedia.com
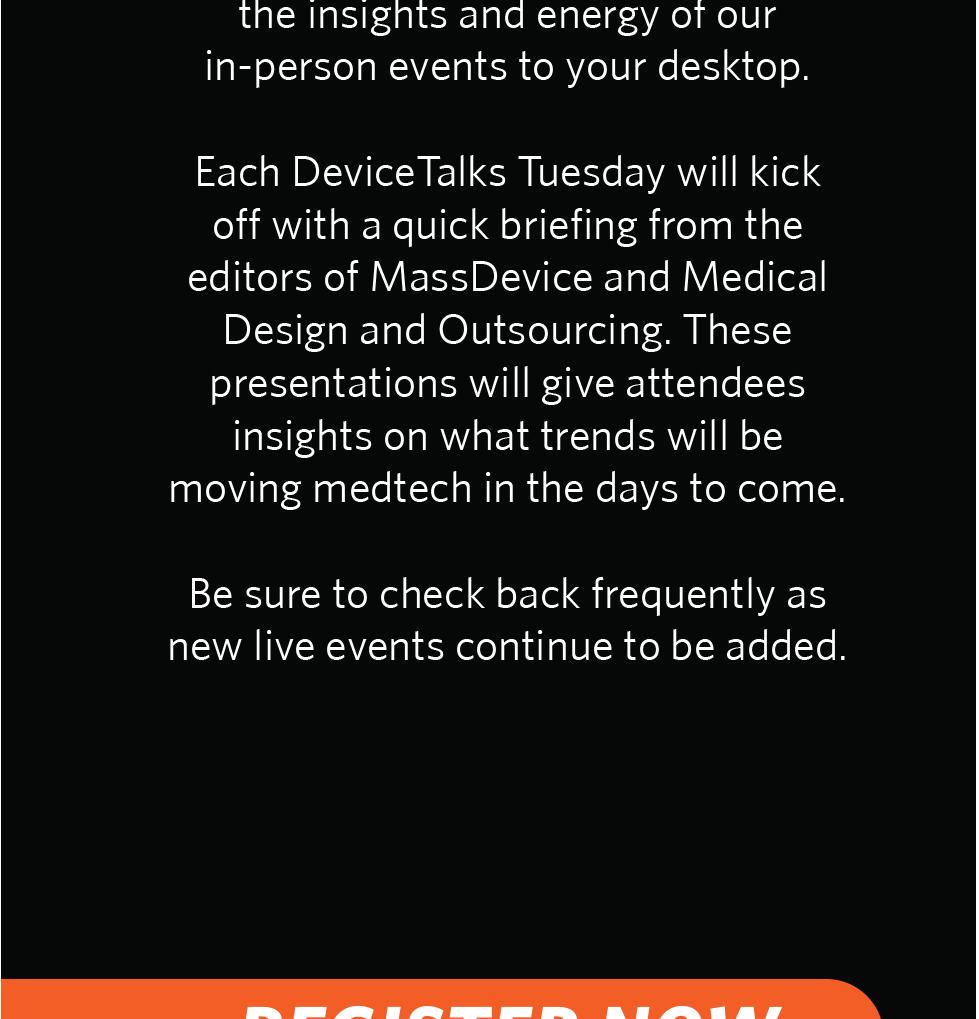
VIDEO SERVICES
Video Manager Bradley Voyten bvoyten@wtwhmedia.com @bv10wtwh
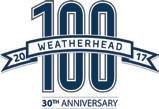
Videographer Garrett McCafferty gmccafferty@wtwhmedia.com
PRODUCTION SERVICES
Customer Service Manager
Stephanie Hulett shulett@wtwhmedia.com
Customer Service Representative Tracy Powers tpowers@wtwhmedia.com
Customer Service Representative JoAnn Martin jmartin@wtwhmedia.com
Customer Service Representative Renee Massey-Linston renee@wtwhmedia.com
Customer Service Representative Trinidy Longgood tlonggood@wtwhmedia.com
Digital Production Manager Reggie Hall rhall@wtwhmedia.com
Digital Production Specialist Nicole Johnson njohnson@wtwhmedia.com
Digital Design Manager Samantha King sking@wtwhmedia.com
Marketing Graphic Designer Hannah Bragg hbragg@wtwhmedia.com
Digital Production Specialist Elise Ondak eondak@wtwhmedia.com
FINANCE
Controller Brian Korsberg bkorsberg@wtwhmedia.com
Accounts Receivable Specialist Jamila Milton jmilton@wtwhmedia.com
check or money orders only. Subscriber Services: To order a subscription or change your address, please email: designworld@omeda.com or visit our web site at www.designworldonline.com
Inspired by Your Challenges
At Clinical Research Strategies, we are inspired by the complexity of the problems we solve for our life sciences clients.
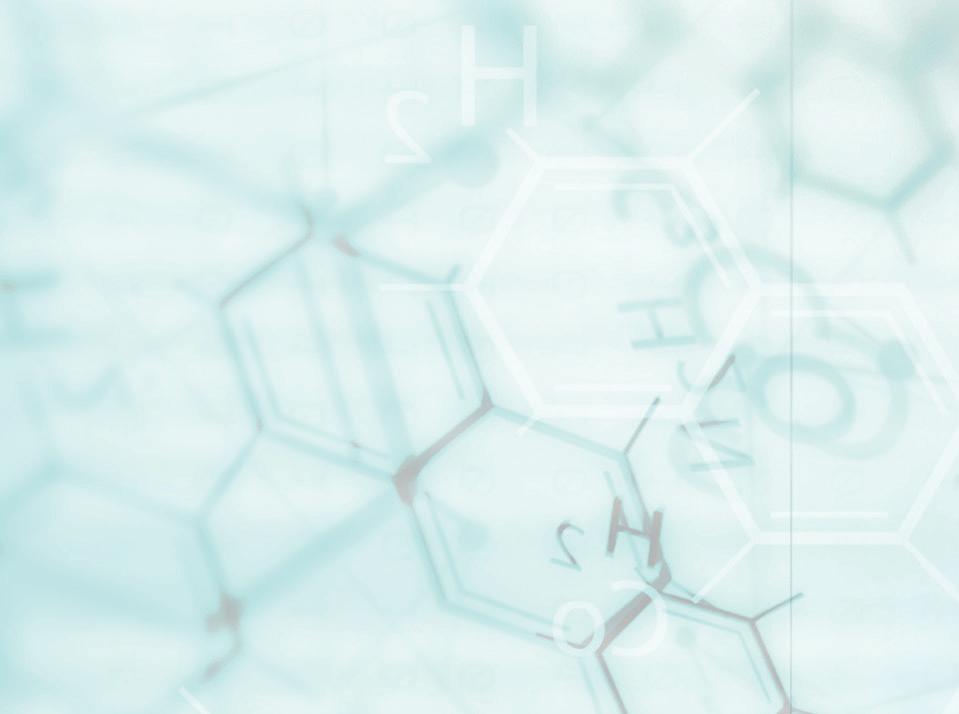

We have a powerful team of experienced device veterans in the highly complementary disciplines of regulatory strategy, quality assurance, risk management, and clinical operations who know how to de-risk programs. And we see each challenge as an opportunity to improve the chances of clearing performance hurdles toward successful commercialization or exit.

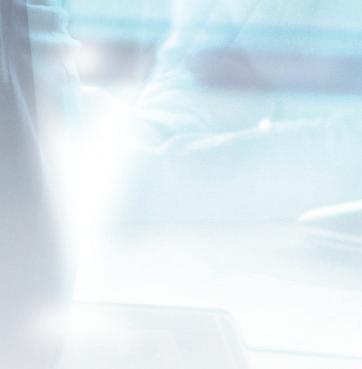
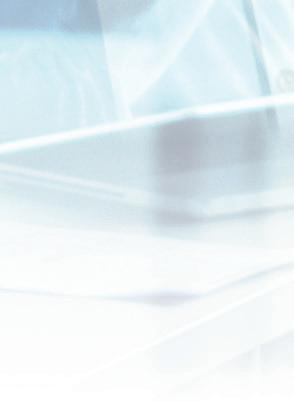

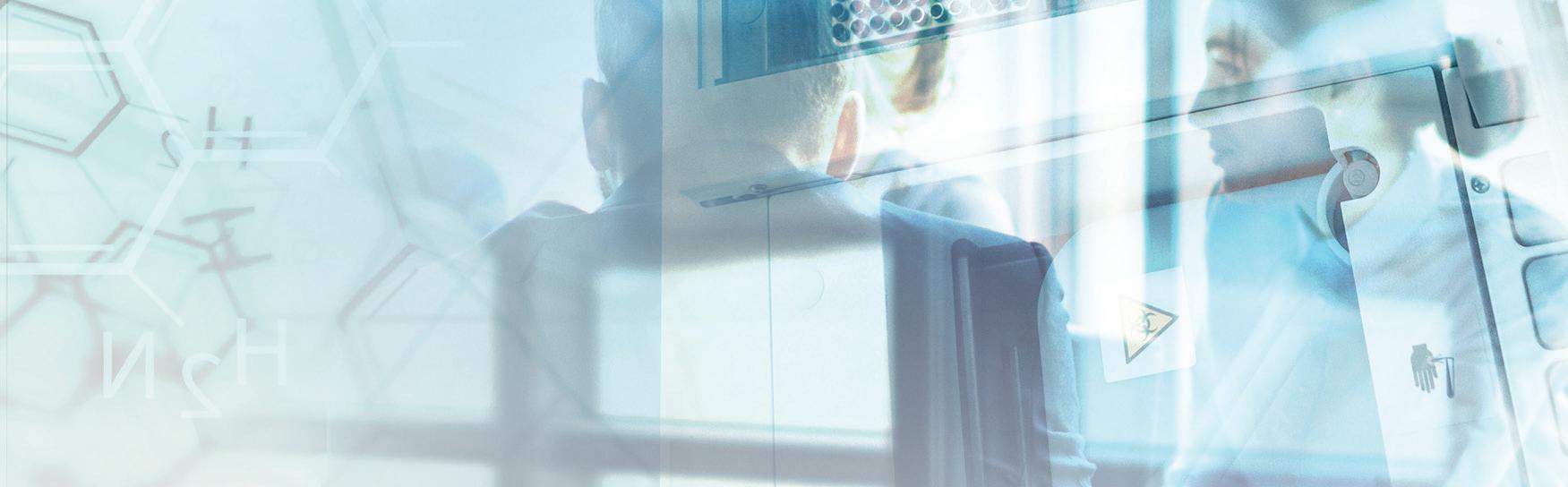
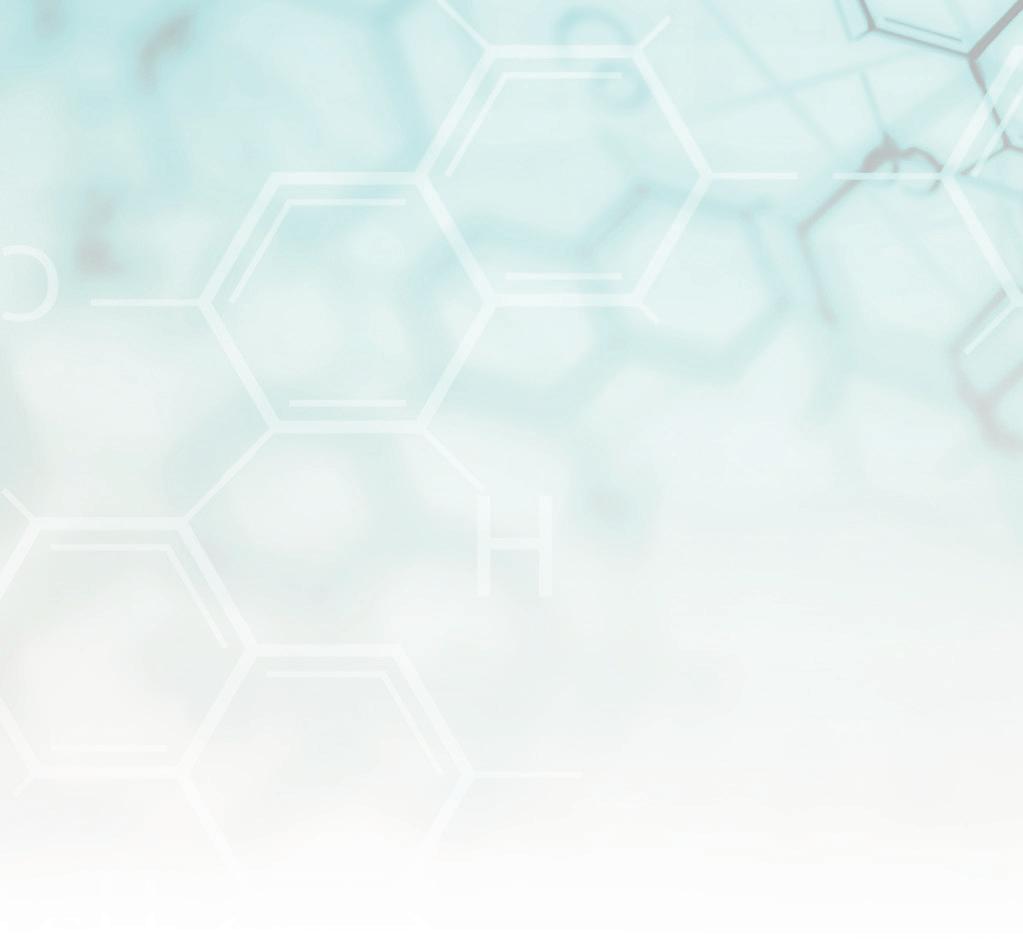
Is your success riding on a shoestring budget?
We’ve been there. We know exactly what it’s like. Our team handles the entire development and execution process with effective competency, high quality, and at a reasonable cost.
The CRS team is prepared to tackle your biggest challenges and help you thrive.
Clinical Research Strategies’ top service areas include medical device (class I-III), IVD, SaMD, and Federated Medicine:
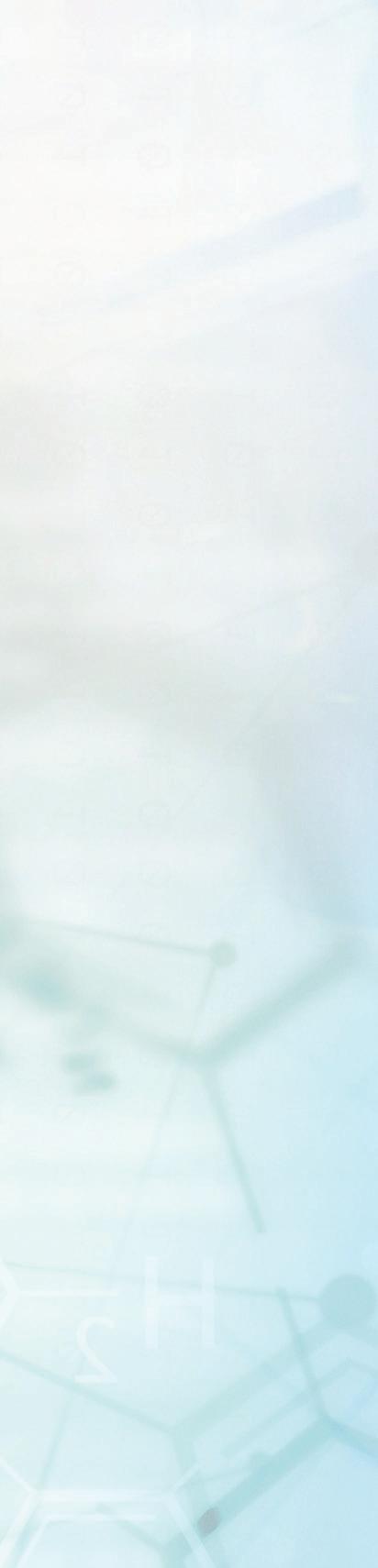
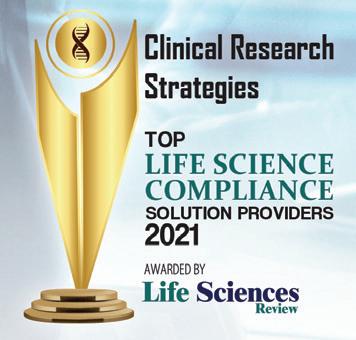
• Design, V&V, QMS, and Risk Management

• Regulatory Pathway Assessments, Regulatory Submissions
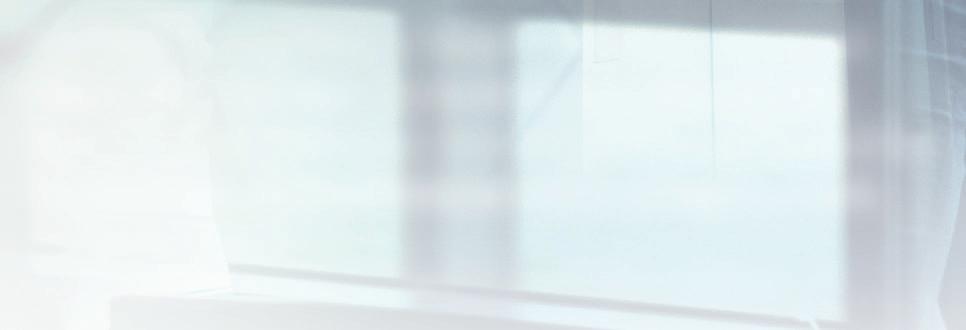

• 483 and Warning Letter Remediation
• Medical Writing, Literature Reviews, and Clinical Evaluations
• Clinical Operations, Clinical Trials, Human Factors & Usability
• Privacy and Corporate Compliance
• Trial Master Files (TMFs), Inspection-Readiness, GxP Audits
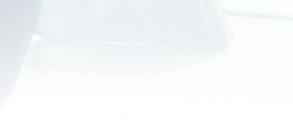
• Advisory Boards, Safety Committees
Contact Clinical Research Strategies today, and let’s talk about the challenges that are keeping you up at night!
Contact Compliance Award-Winner, Alethea Wieland, founder, president & COO of CRS, for a free 30-minute, no-obligation consultation by visiting ClinicalResearchStrategies.com
© 2022 Clinical Research Strategies, LLC. All rights reserved.
HERE’S WHAT WE SEE: ................................................ 12
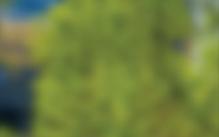
Diverse executive teams bring more innovation to medtech

218 women in executive roles ....................................... 15
Rachel Ellingson, Zimmer Biomet 20 Laura Mauri, Medtronic 26 Lara Simmons, Medline Industries 32
10 women-led medtech startups .................................. 36

Maureen Mulvihill, Actuated Medical 36 Gabi Niederauer, Bluegrass Vascular Technologies 40 Kate Rosenbluth, Cala Health 44
3 questions with women in pharma .............................. 48
AstraZeneca Oncology R&D EVP Dr. Susan Galbraith, Ferring Pharmaceuticals Chief Scientific Officer Dr. Elizabeth Garner and Insmed
CFO Sara Bonstein discuss barriers for women and ways to break through.
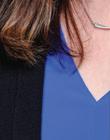
Cathy Burzik's five essential leadership lessons for medtech's next generation of women leaders ............. 52
Burzik, a seasoned senior executive in the healthcare industry, has successfully led major medical device, diagnostic, diagnostic imaging and life sciences businesses.
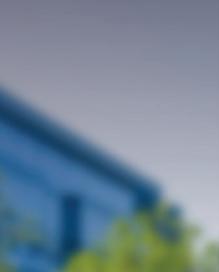
Diversity in medtech: 2022 markedly the best for women in medtech ........... 54
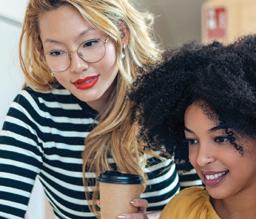
This year has been one of the most formative for women in medtech leadership roles as representation in the C-suite has reached a new high.
How medical device companies can better protect themselves from lawsuits ...................... 62
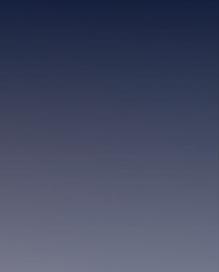
Getting hit with a lawsuit isn't an if, but a when for medical device developers and manufacturers. Greenberg Traurig lawyer Ginger Pigott shares advice for staying secure.
Abbott is looking to address biases for cardiovascular patients .................................................. 66
Jennifer Jones-McMeans, Abbott's divisional VP of global clinical affairs, explains how small anatomical differences compound in cardiac care.
B. Braun - Dawn Kentner ................................................. 71
Carl Stahl Sava Industries - Angelica Flores .................... 72
Clinical Research Strategies - Alethea Wieland ............... 73
Confluent - Christine Trepanier........................................ 74
Cretex Medical - Janelle Swanson .................................. 75


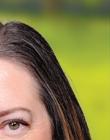
Donatelle - Treasa Springett ............................................ 76
Eurofins - Susan Shorter .................................................. 77
Flexan - Desiree Williford ................................................ 78
Flexcon - Aditi Subramanian ........................................... 79
Hobson & Motzer - Kristin Backus .................................. 80
Integer - Margaret Carthy ............................................... 81
Isometric Micro Molding - Donna M. Bibber ................... 82
Johnson Matthey - Venkata Pokkuluri ............................. 83
Medbio - Christine Marie Nolan ...................................... 84
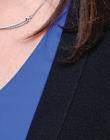
Phillips MediSize - Cheryl Norder ................................... 85
PSN Labs - Laura Beringer, Ph.D. ..................................... 86
Resonetics - Danielle Wingerter ...................................... 87
Tegra Medical - Nidhi Agrawal ........................................ 88
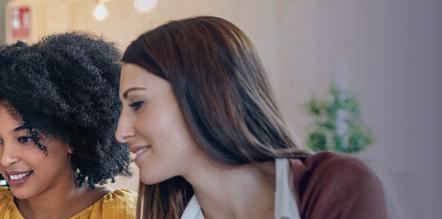
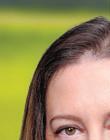
Women in Engineering 2022 Salary and Career Update ................................... 90
Ellen Ferraro 98 Christine Georgia 106 Jasmine Jauregui 114 Kathy Miller 122 Meghan Olds 130 Kate Schneidau 136
Allegro Microsystems
Yejee Choi 146 Allied Electronics & Automation Or Yacobi 147 B&R Industrial Automation Apurva Deota ............................................. 148 B&R Industrial Automation Brittany Langston........................................ 149 Beckhoff Automation Alyssa Hiedeman ........................................ 150 Cinch Connectivity Solutions Karen Vintroux ............................................ 151
Digi-Key Electronics Kristin McKenzie ......................................... 152 Elma Electronic, Inc. Melissa Heckman 153 Encoder Products Melissa Wallin 154 igus Kristen Copeland Moore 155 Infineon Jaya Bindra 156 maxon Nicole Mathieu 157 Microchip Annalisa Regalado 158 Mitsubishi Electric Automation Deana Fu 159 nVent Dana Myers 160 Velo3D Ana Montes 161 Velo3D Maritza Ruiz ................................................ 162
WAGO Corporation Michelle Goeman ....................................... 163 Wind River Kitty Kong ................................................... 164 Wind River Stephanie Moscrip...................................... 165
Würth Industry North America Anna Wint ................................................... 166 Ad Index ................................................. 168
Take Control with Cordis
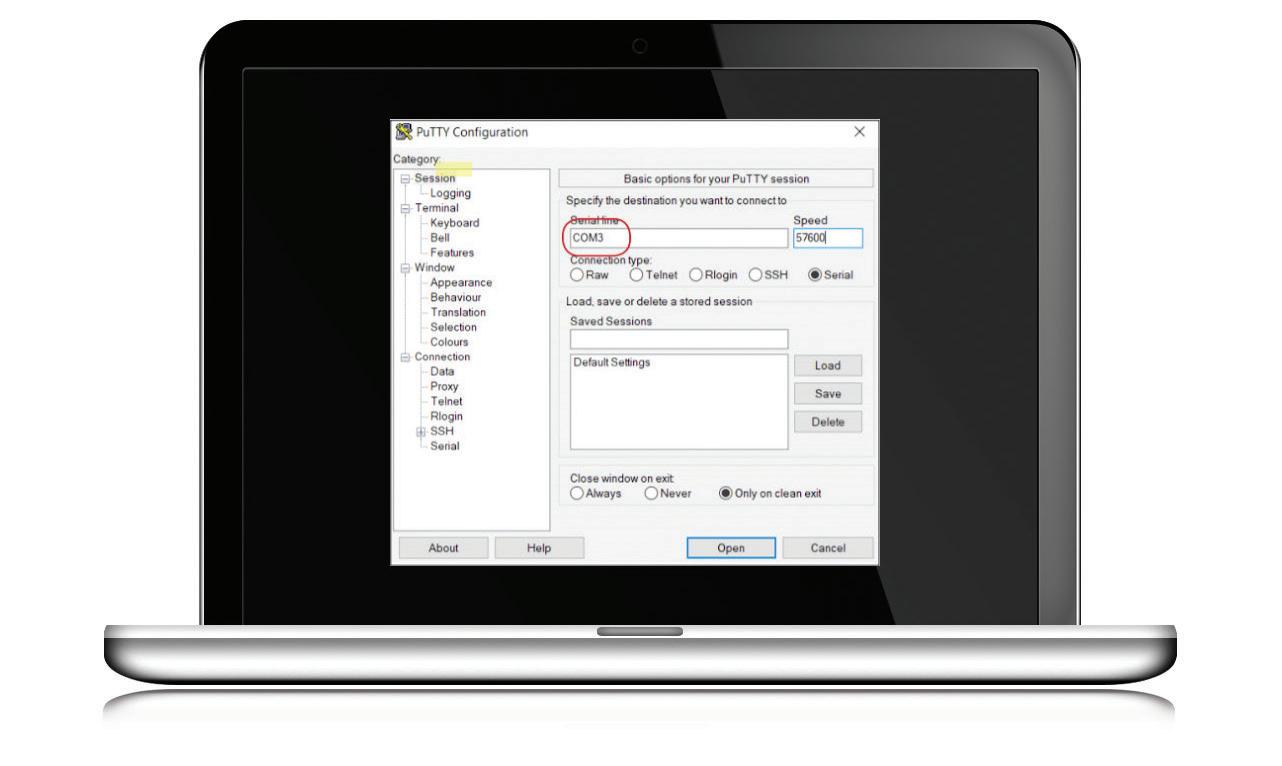

•
•
•
•
•
•
•
•
•
The future of proportional control has arrived— and it’s digital. The Clippard Cordis is a revolutionary microcontroller primed for escape velocity from a proportional control market that has grown stagnant.
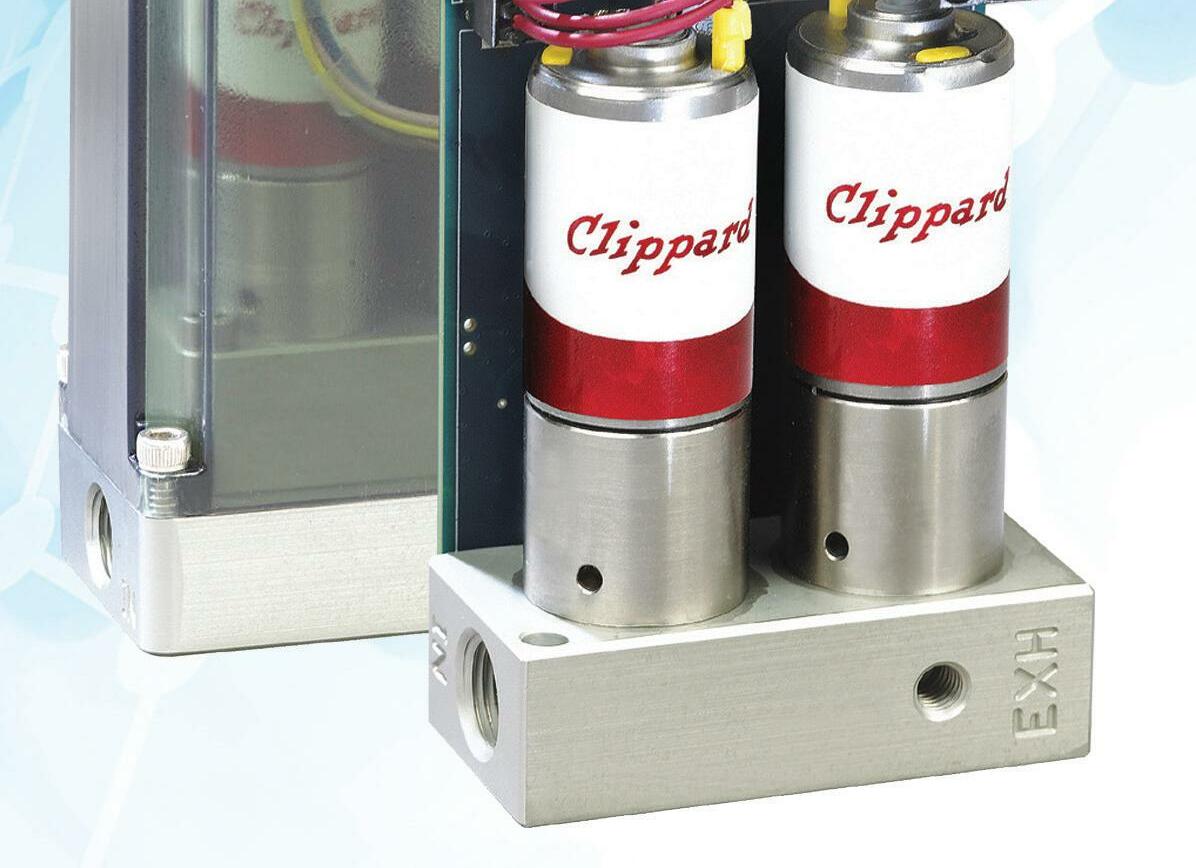
With unparalleled performance and flexibility not possible with current analog proportional controllers, the Cordis makes everything from calibration, to sensor variety, to future development opportunities more accessible and less complicated.
Precise, Linear Digital Pressure Control
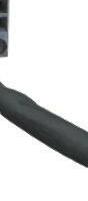
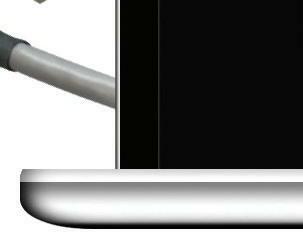

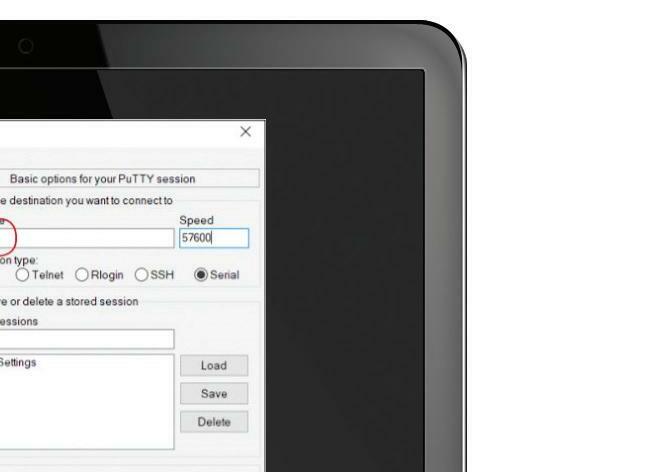
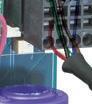
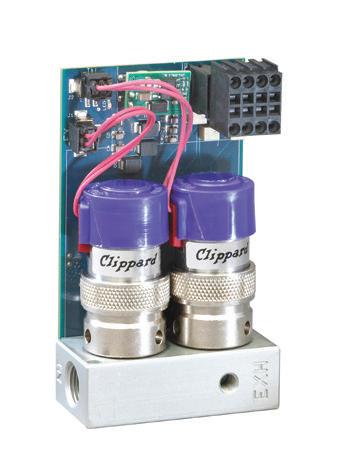
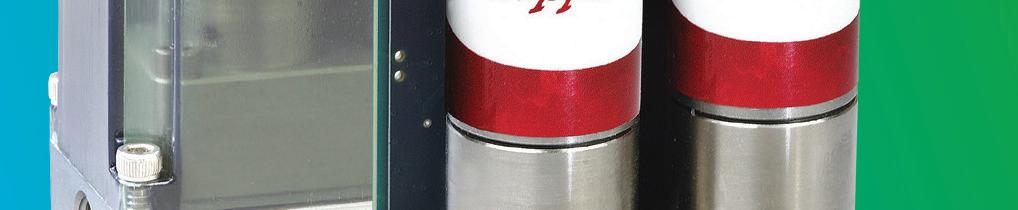
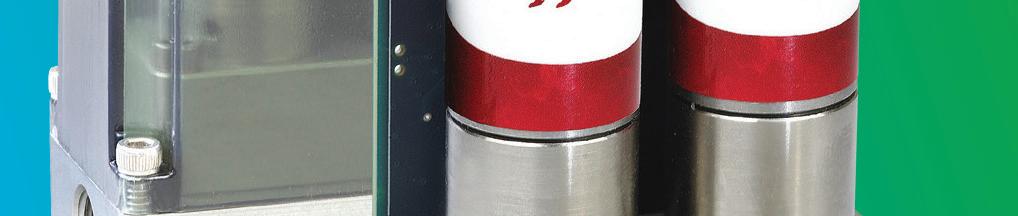

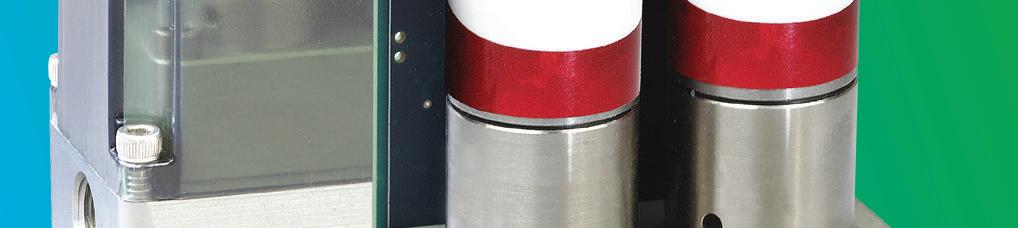
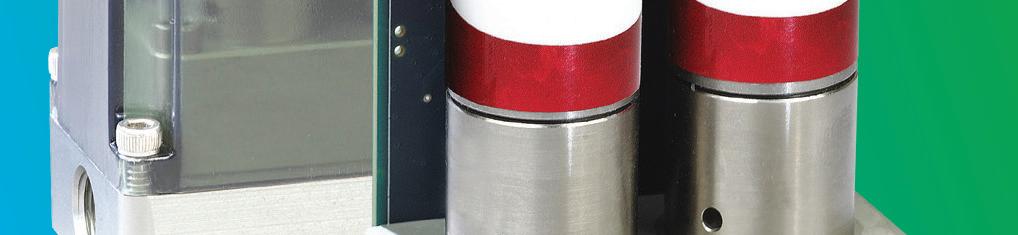
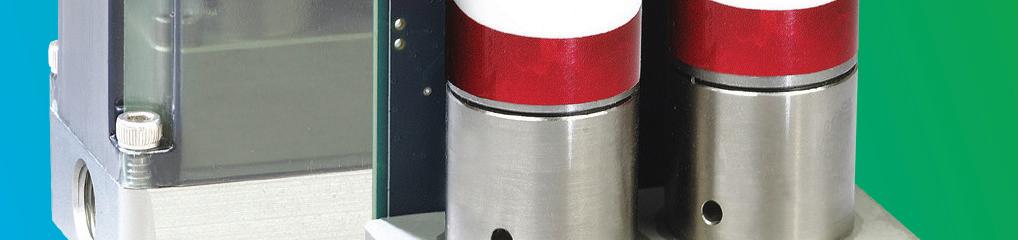
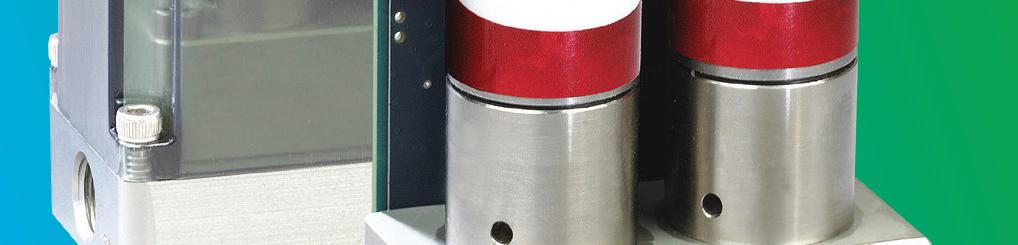

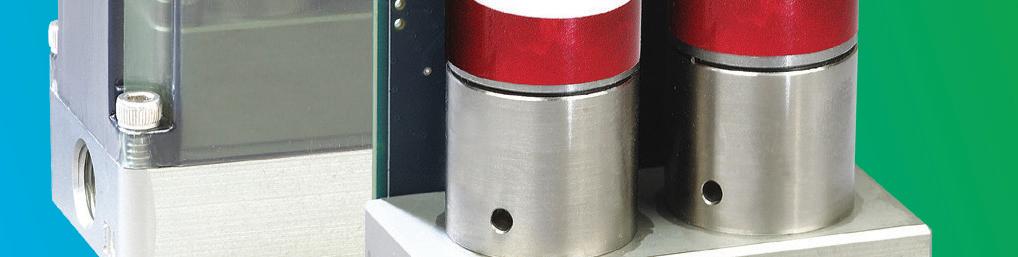
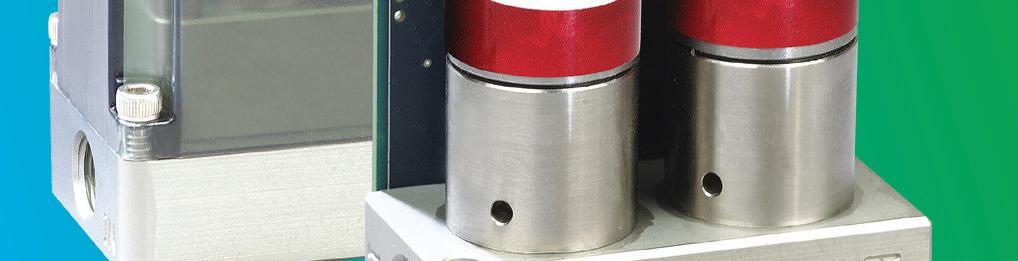
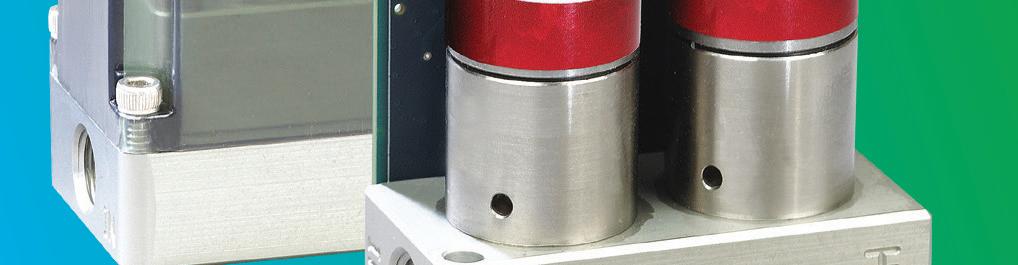


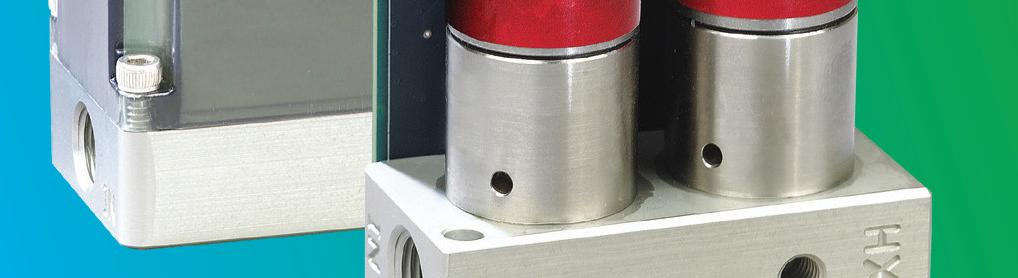
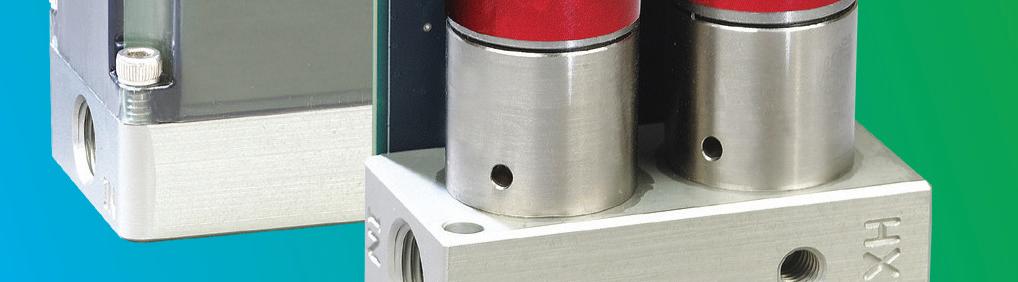
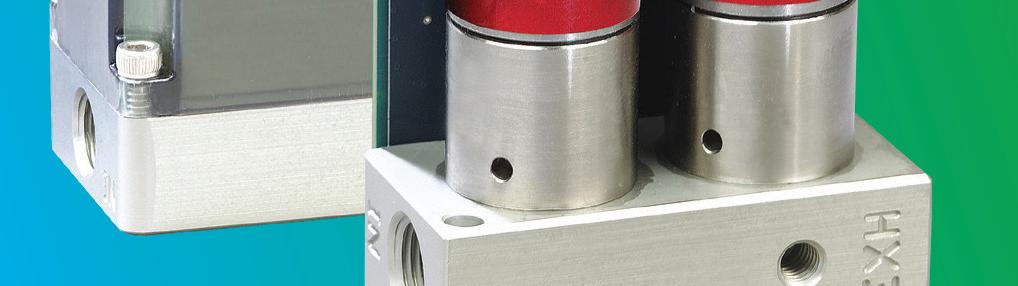
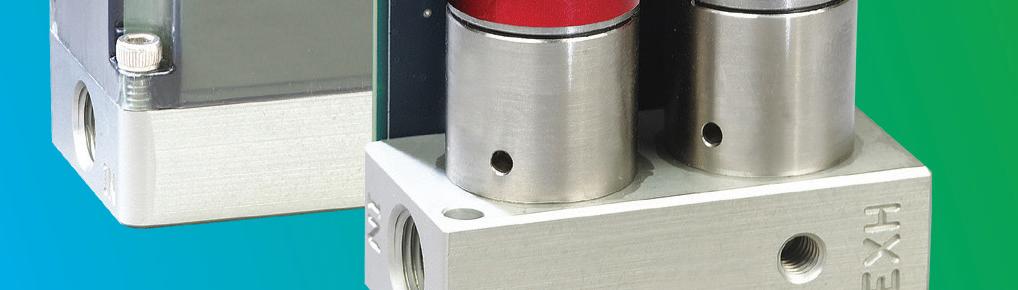
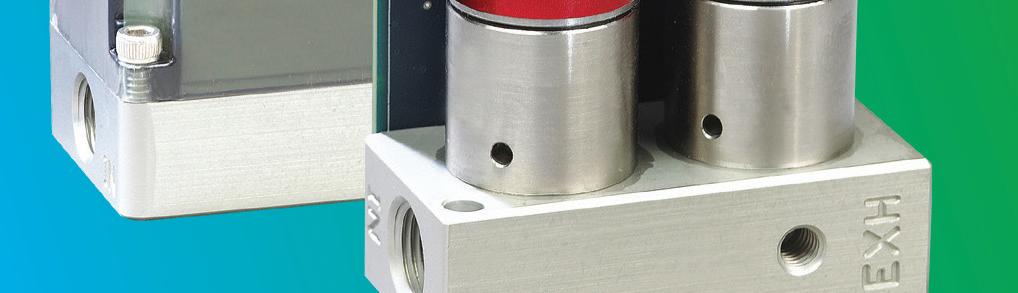
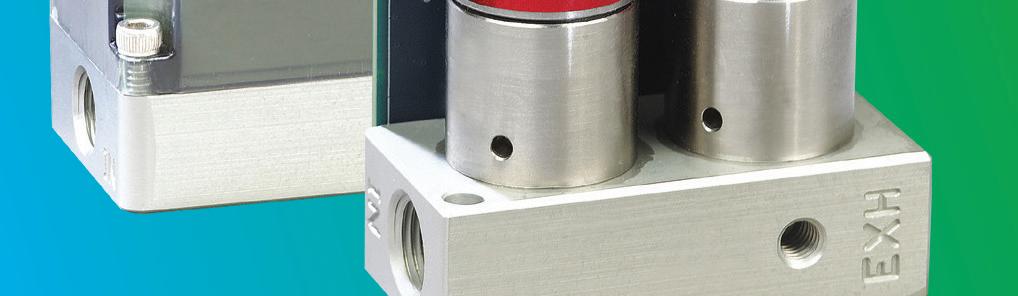
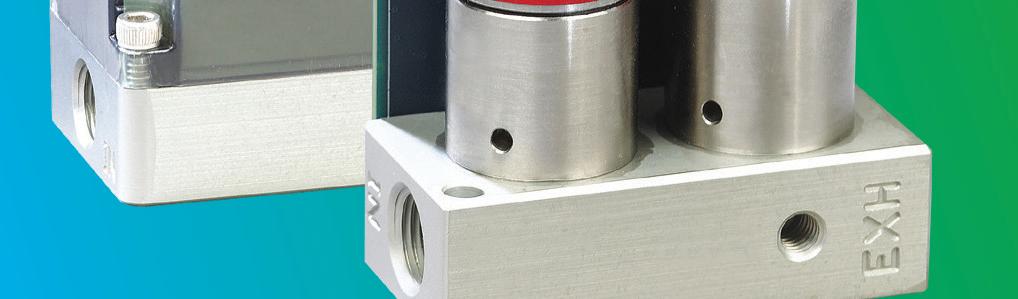

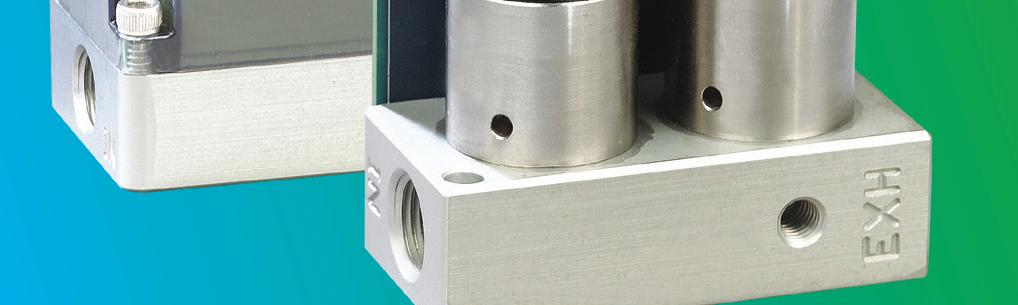
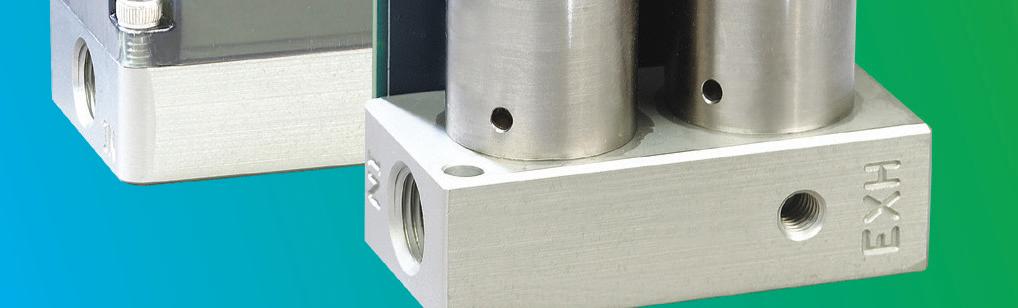
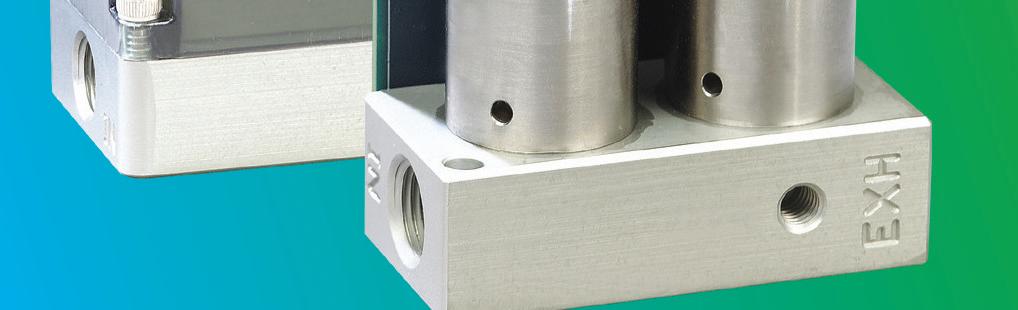

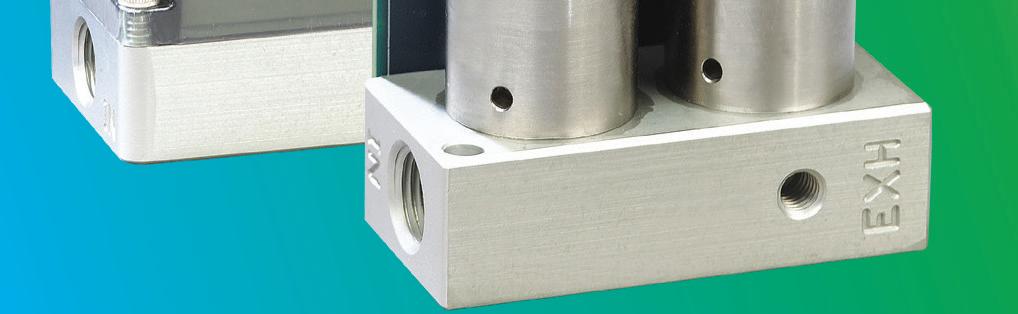
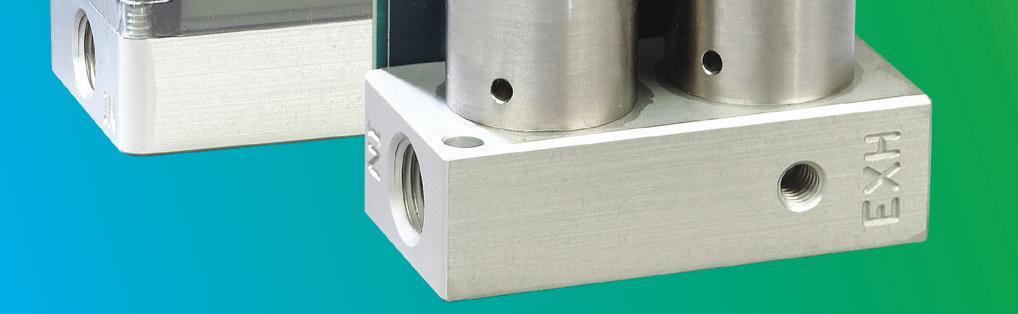
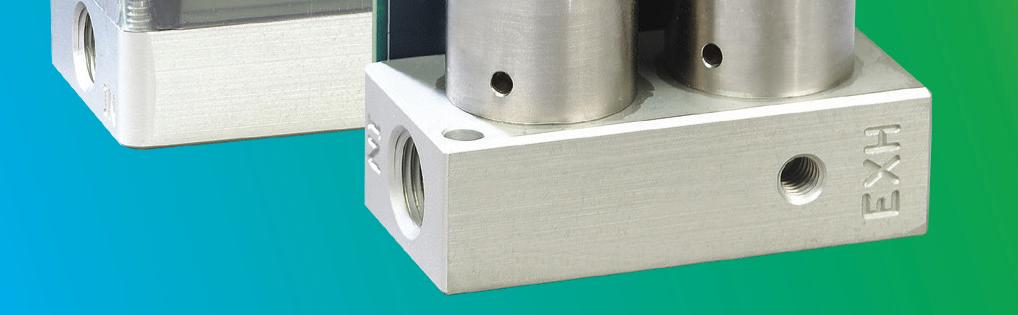

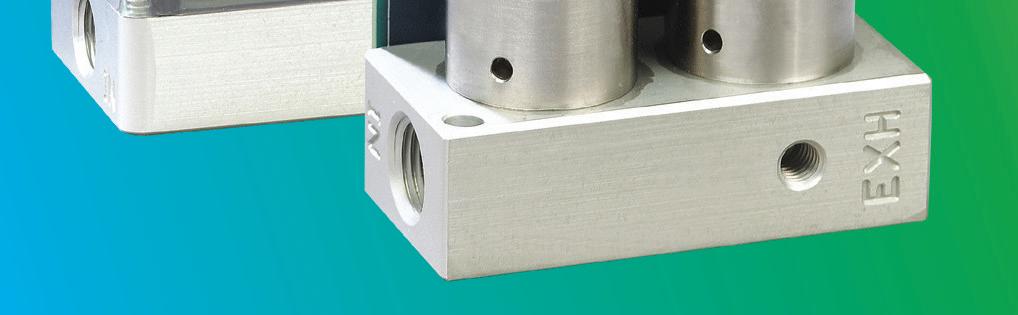
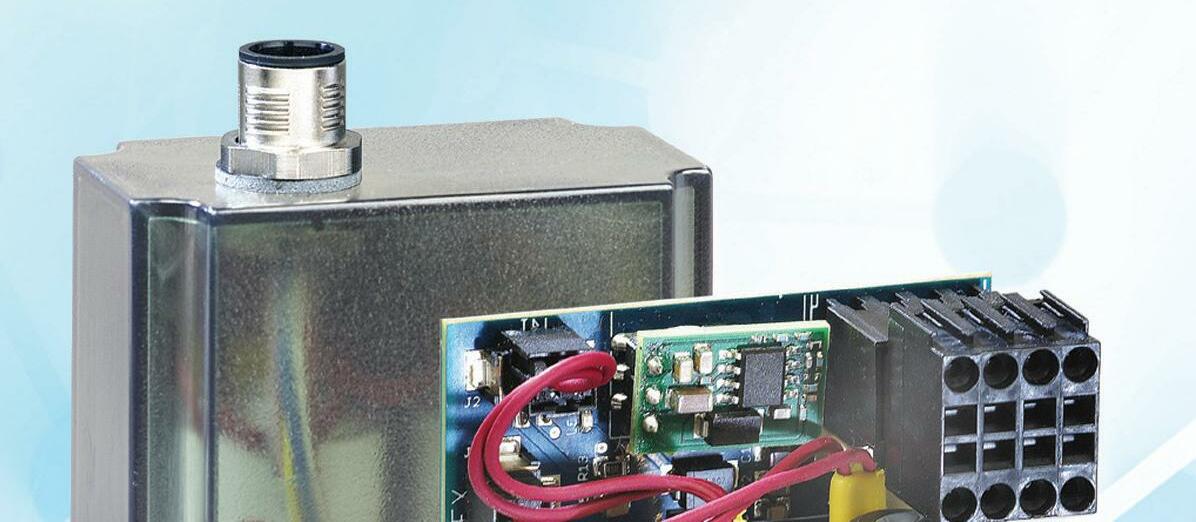
Contact your distributor today to learn more about how the Cordis can provide precise, real-time control for your application, or visit clippard.com to request more information.
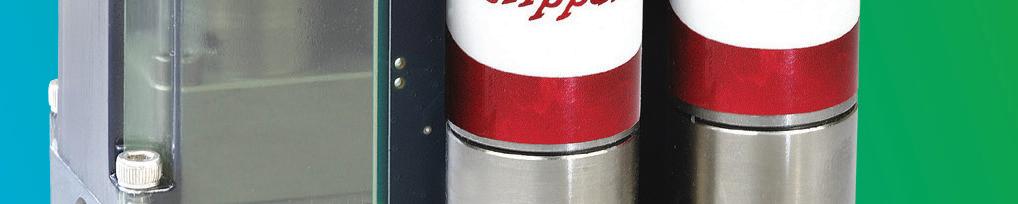
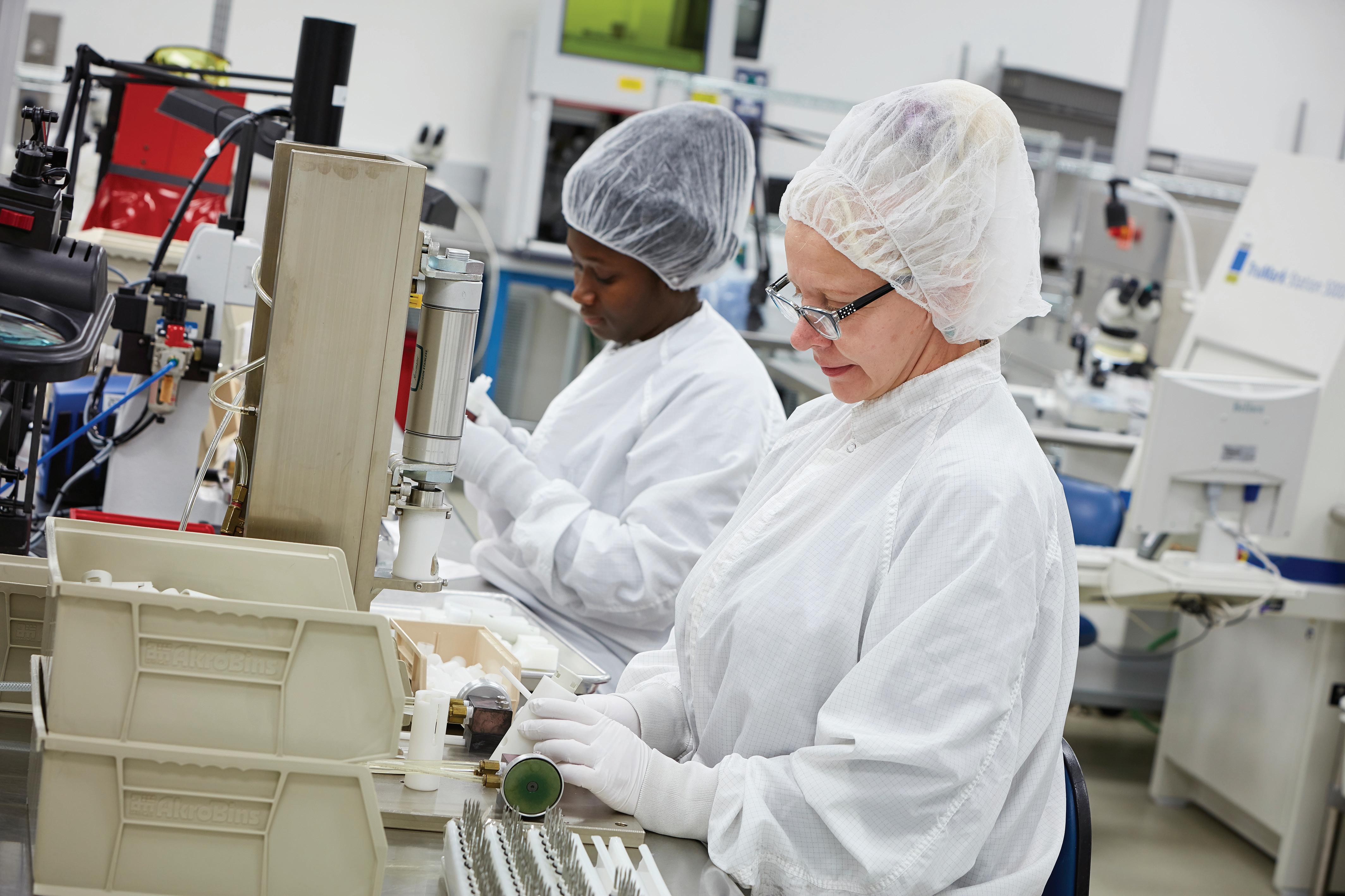
omen in engineering 2022
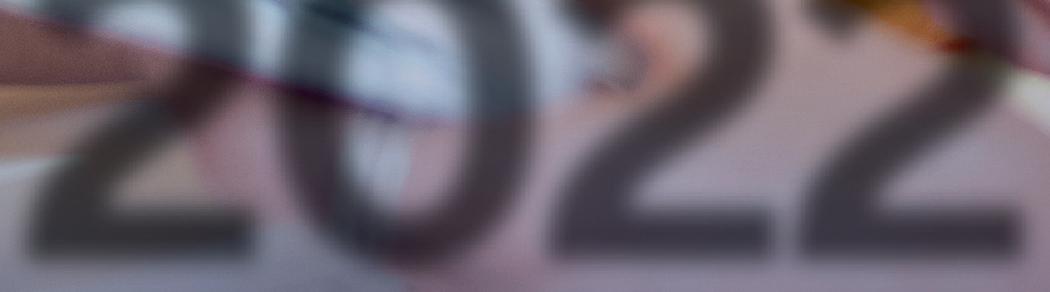



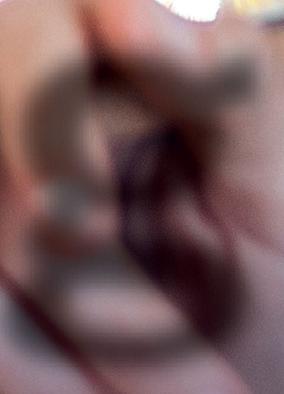




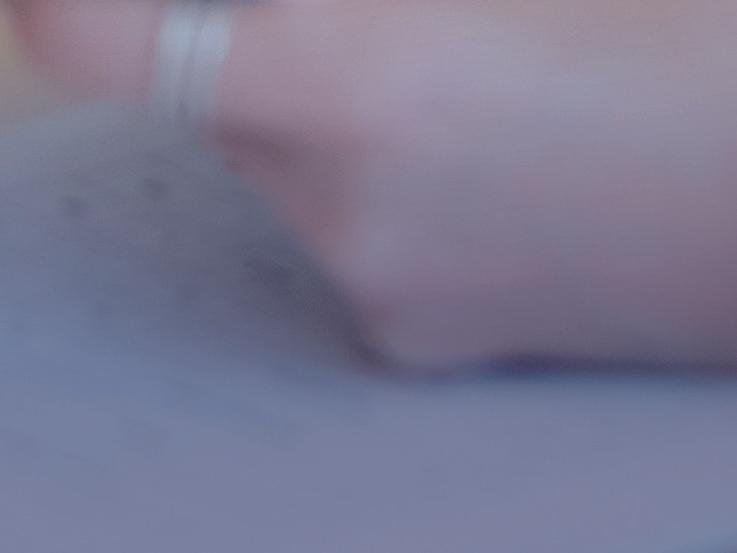
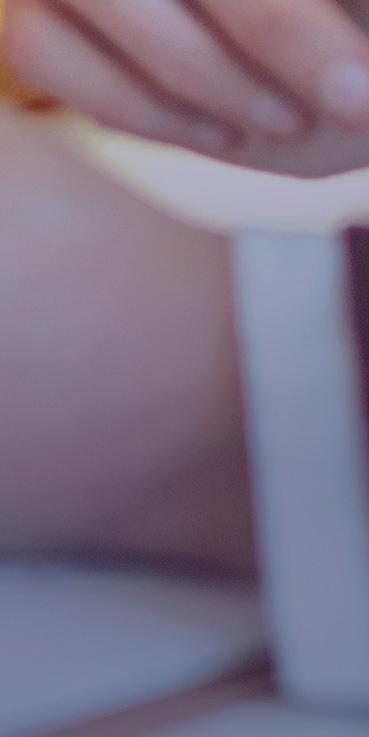

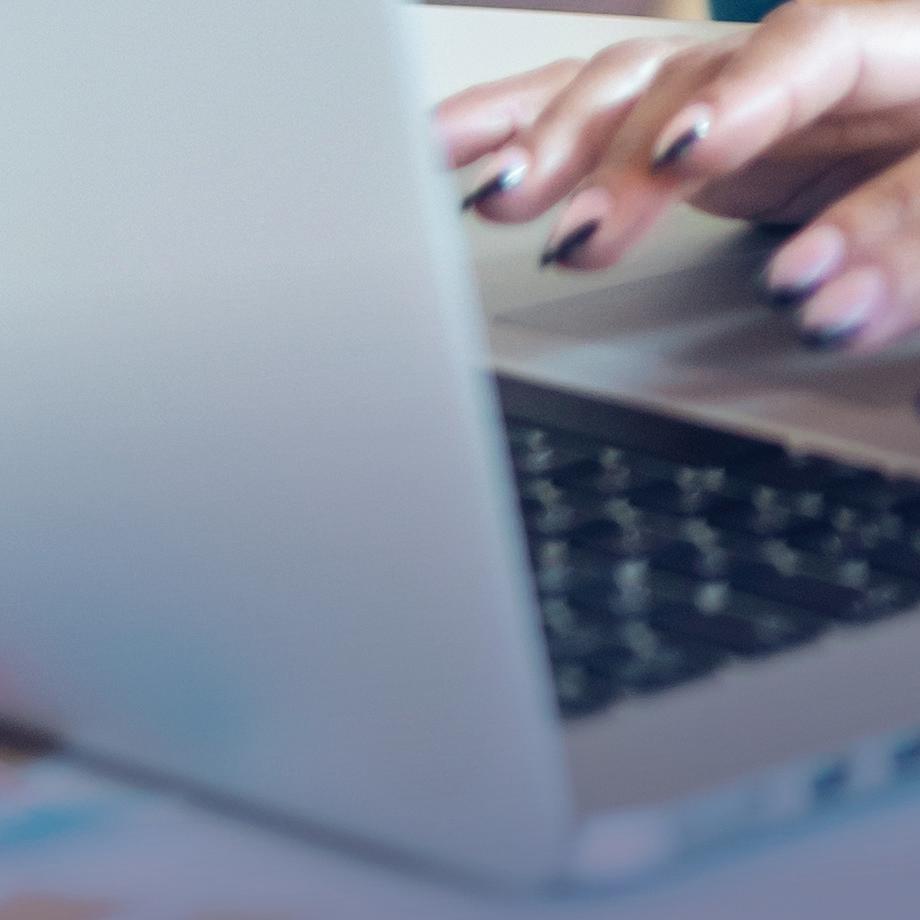
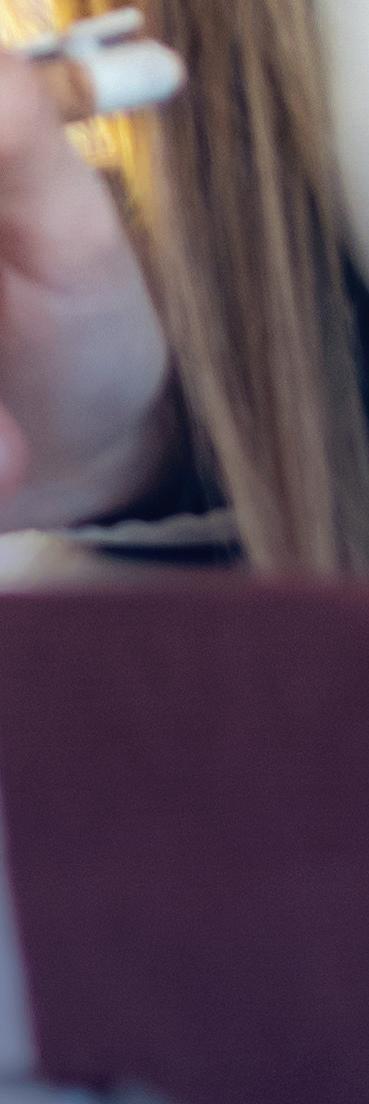

2022 engineering occupations and salaries for women
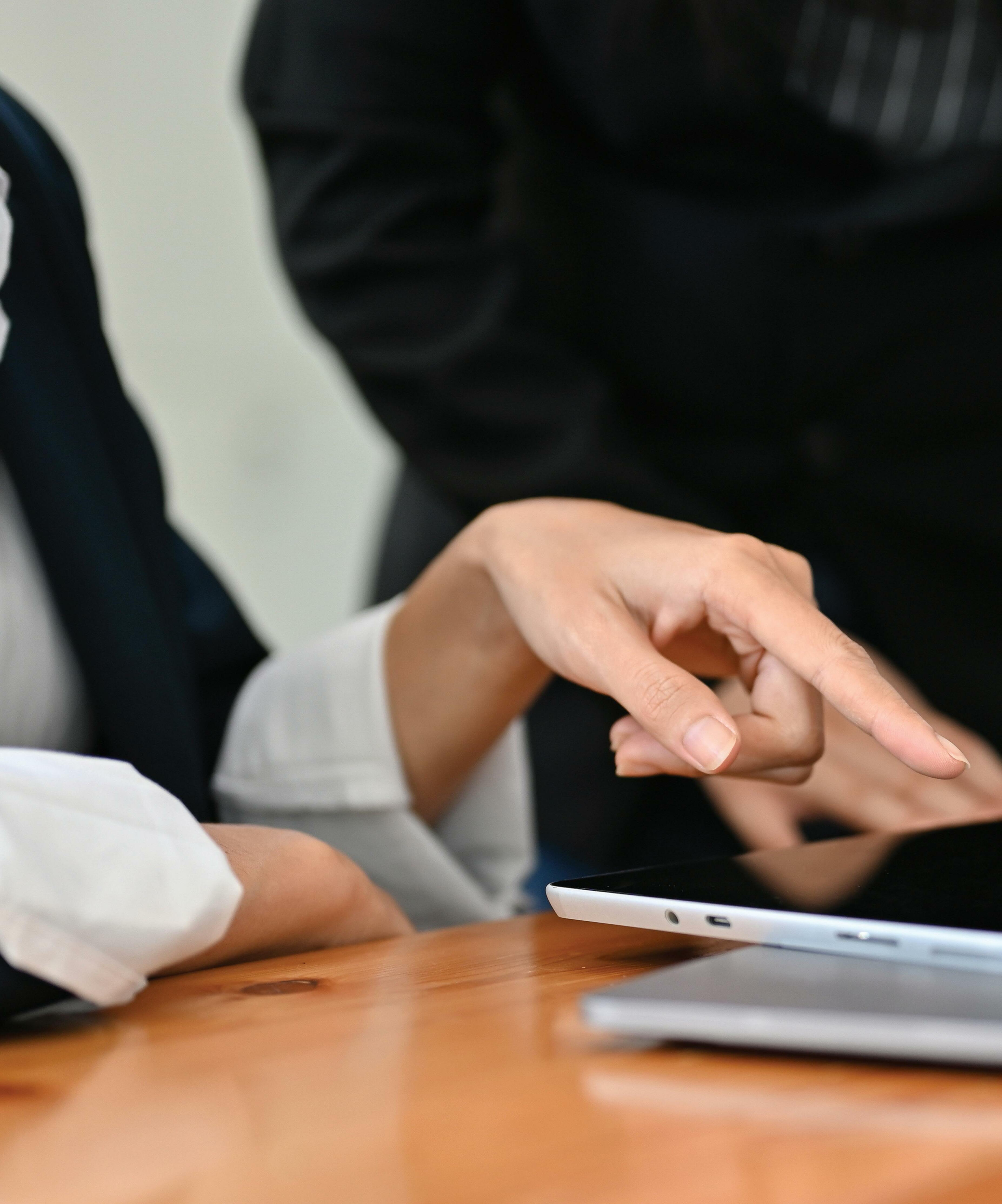
Since our WiE
last salary report
in 2020, the number of women in the U.S. computer-worker and engineering workforces has hovered around 15% or so. That’s according to U.S. Census Bureau data. The number of university-graduate engineers who are female shrank to 20% or so. But those that do pursue engineering continue to be rewarded: Nine out of the 10 most lucrative four-year college degrees for women remain those in engineering fields.
If the field of engineering is financially rewarding for women, why the low representation? According to a study by digital security and privacy solutions company Atlas VPN, more than half of all women believe their gender is a career-limiting factor in technology industries. A lack of promotion opportunities is the most significant barrier to advancement — with some 38% of surveyed women citing this a top factor in their career trajectory.
Other research tends to support these perspectives. McKinsey and Co. analysis of several industries indicate that efforts to hire women for entry-level and C-suite roles (while helpful) fall short. That’s because women receive 15% fewer earlycareer promotions than men … and 48% fewer promotions for engineering and product-management roles. Some have dubbed this the broken-rung problem for women.
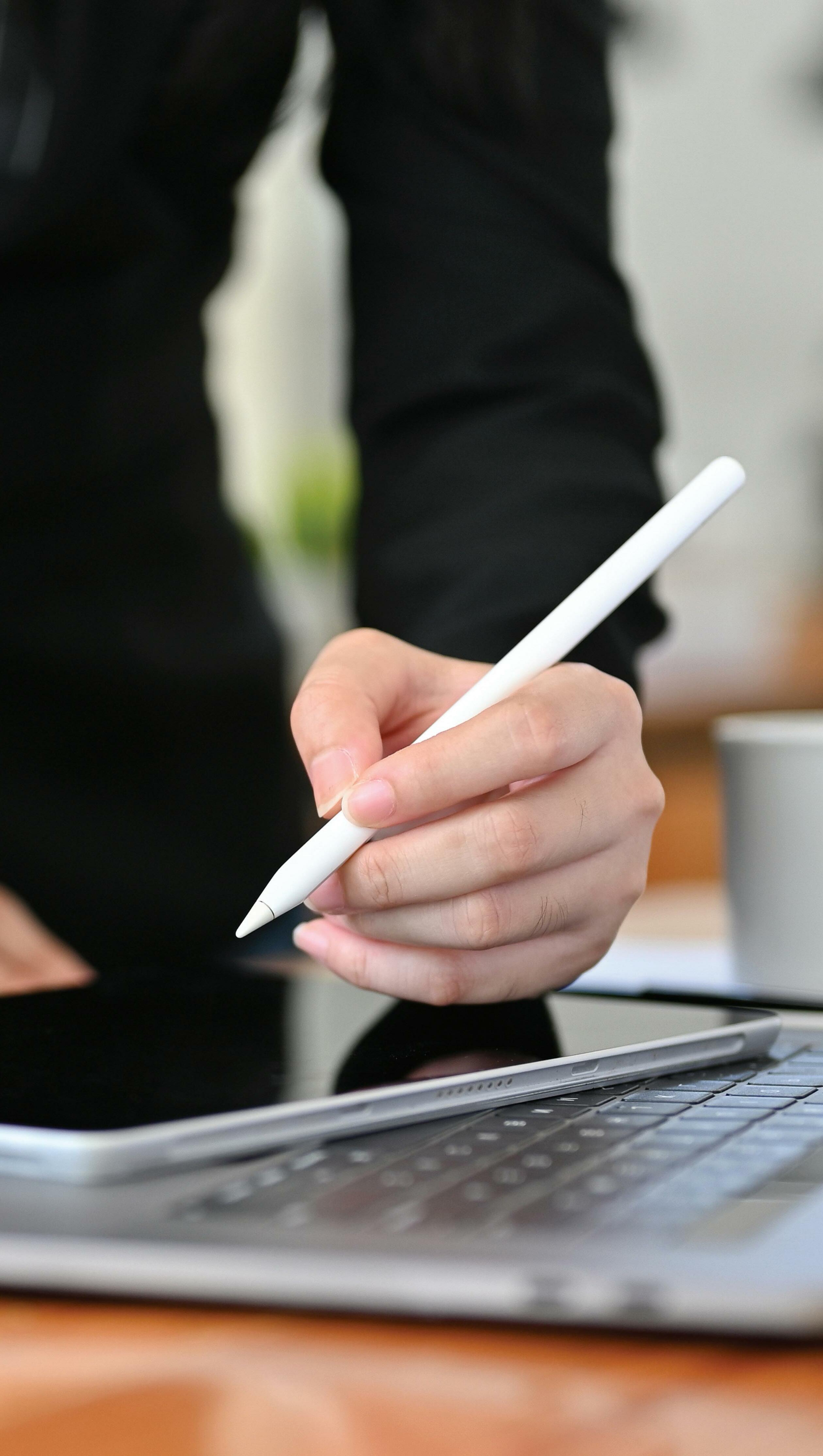
Other challenges include a lack of confidence or lack of relatable senior role models and senior sponsorships.
Representation in engineering slightly worse than in software tech
As of June 2021, women were 29% to 45% of the workforce at top tech companies such as Amazon, Apple, Google, and Microsoft. However, only
about 25% of technical positions are filled by women … and the largest tech companies had more female employees in leadership roles than technical jobs. Contrast these numbers with how female engineers are at best 15% of the nation’s engineering workforce despite earning 20% of all engineering degrees.
Solutions to address diversity shortages
One important report from the National Academies of Sciences, Engineering, and Medicine — Promising Practices for Addressing the Underrepresentation of Women in Science, Engineering, and Medicine — has aggregated data across several fields to serve as a guide to boost diversity in STEMM (including mathematics and medicine). One goal in instituting such practices is to reverse the
early-2000s drop in women graduating with engineering degrees. Often, it’s the efforts of organizations such as the National Society of Black Engineers and Society of Women Engineers that spur change; perhaps more often, it’s the efforts of individual family members or teacher mentors that make a difference.
Consider how Black women continue to outnumber Black men in college two to one, though only about 25% pursue bachelor’s degrees in engineering. The Promising Practices report cites an array of actions that schools, families, faith groups, professional groups, policy makers, and the engineering industry can take to
Women remain a minority in all engineering professions.
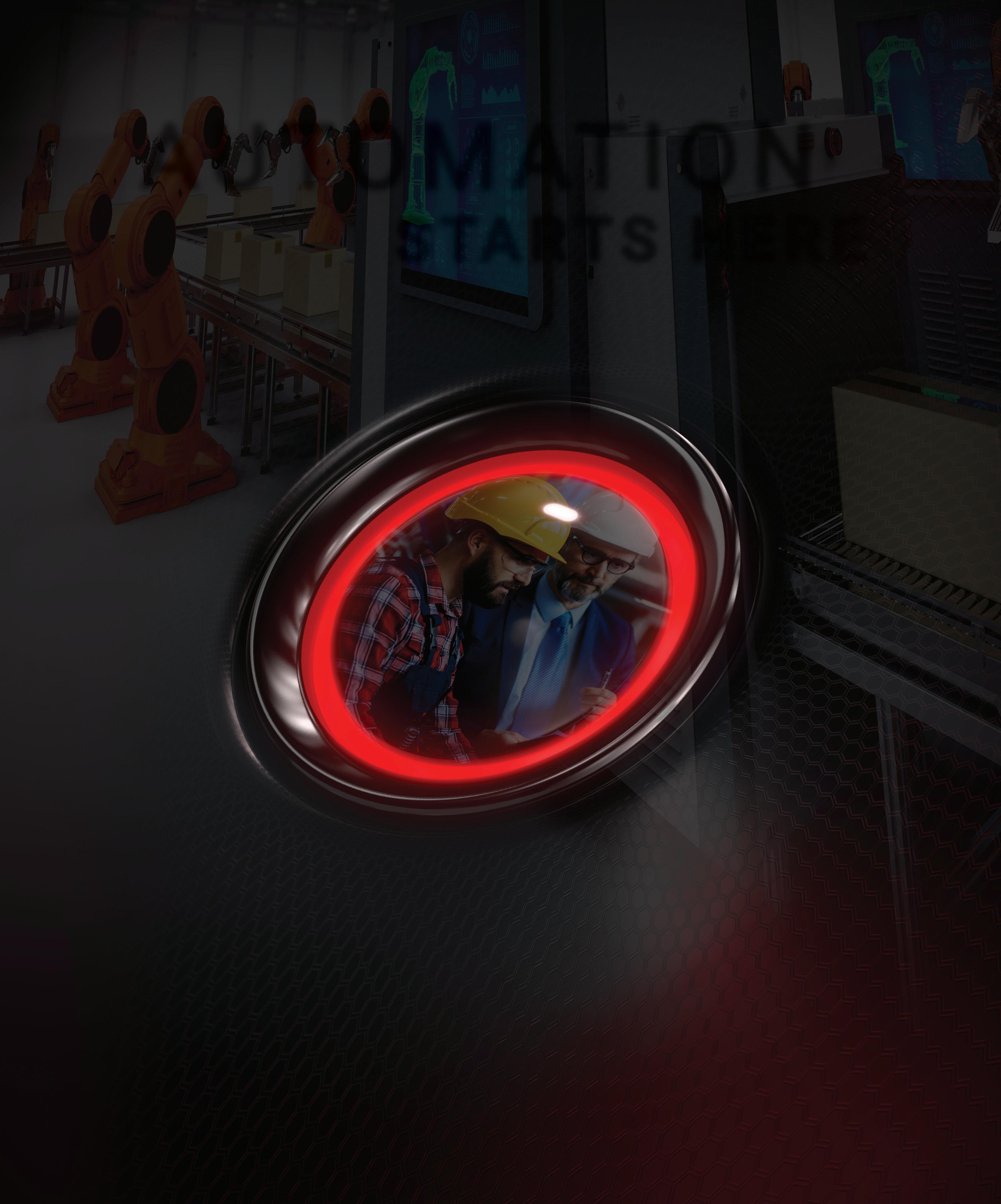

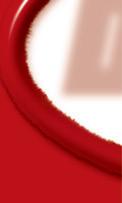
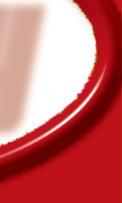
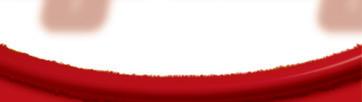
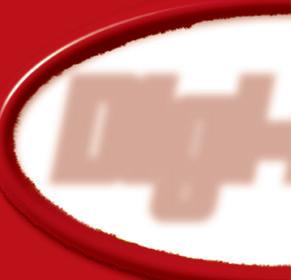
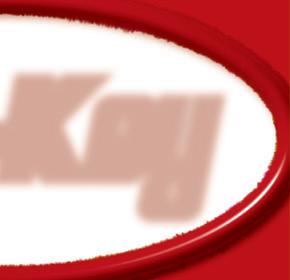
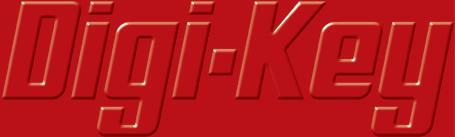
WOMEN IN ENGINEERING SALARY UPDATE
MEDIAN WAGES & SALARIES IN ENGINEERING AND A SAMPLING OF RELATED TECHNICAL OCCUPATIONS
Packaging machine operators
Electronics and electromechanical assemblers
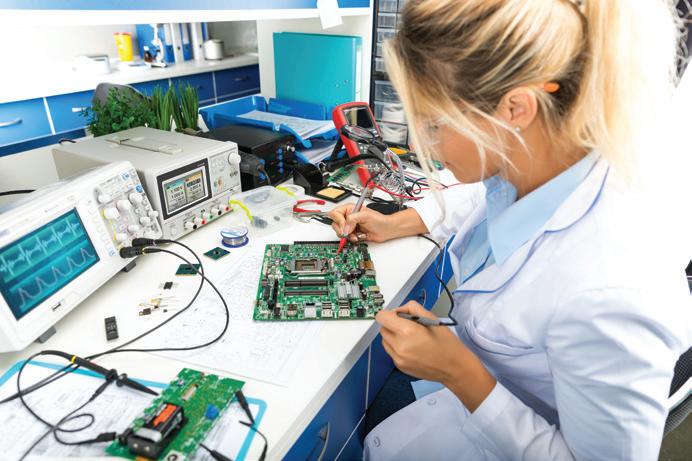
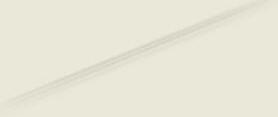
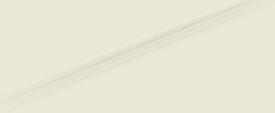
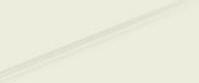
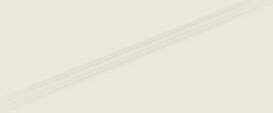
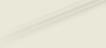

Machine-tool, punch, and press setters and operators
Printing-press operators
Metal and plastic workers
Welding, soldering, and brazing workers
CNC tool operators and programmers
Production managers
Electricians
Engineering technologists
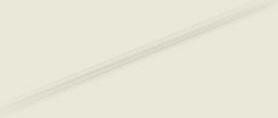

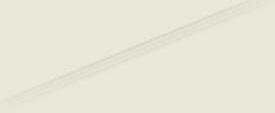
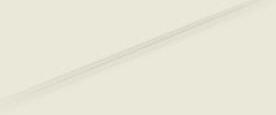
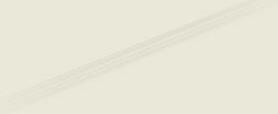
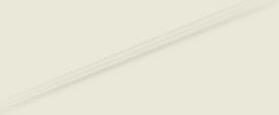

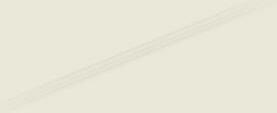
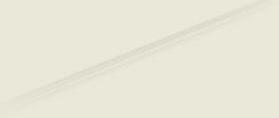
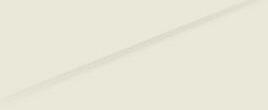
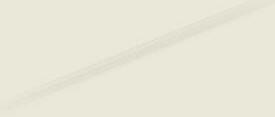
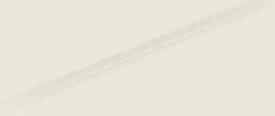
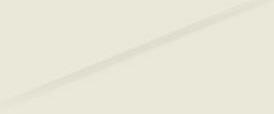
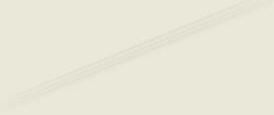
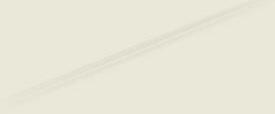


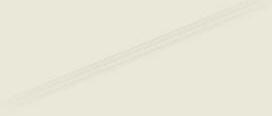













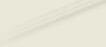
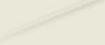
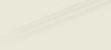
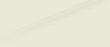













Computer engineers
Mathematical science personnel
Environmental engineers
Mechanical engineers
Civil engineers Project managers
Computer programmers Engineers — all other
Electrical and electronics engineers
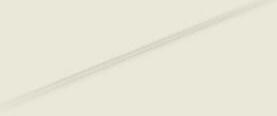

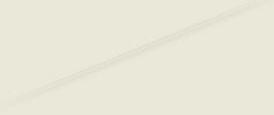



Computer network architects Chemical engineers Aerospace engineers Software engineers
Wage






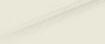
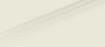
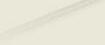
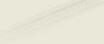
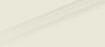

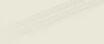

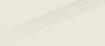
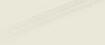

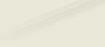
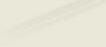
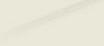
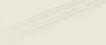
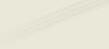
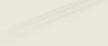






disparities for women in engineering remain relatively low.
Information systems managers Engineering managers Engineering executives 0 20,000 40,000 60,000 80,000 100,000 120,000 140,000 160,000
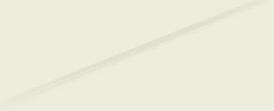




ensure more Black women join, enjoy, and find success in STEMM.
Considering professions related to engineering Engineering fields often offer women an array of technical occupations as well — from packaging-machine operators to engineering executives. Women in these manufacturing, logistics, and other technical fields are paid on average $0.85 for every $1 a man is paid for the same job, which is more parity than in other fields and industries. Overall, women are paid about $0.80 on the dollar of a man’s wages. That’s according to the most recent U.S. Dept. of Labor Women’s Bureau statistics. Female engineers and technical personnel working as engineering managers, mechanical engineers, and electricians enjoyed
the narrowest wage disparities. As noted in past WiE reports, the most work is needed to address genderrelated wage gaps for electrical engineering and productionmanagement roles.
Of the 28 million U.S. jobs requiring STEM expertise, 13 million are satisfied with less than a bachelor’s degree. But women currently miss out on higher wages garnered by relatively short training programs in engineering-related trades. These include machine operating, programming and coding, and laboratory management — for which labor-market prospects are bright. U.S. Department of Education data indicates that for the 100,000 STEM-related vocational degrees men earn at community colleges, about 16,000 women earn the same.
COVID affects engineering careers
The COVID-19 pandemic caused mass burnout that was well documented — and a subsequent wave of so-called quiet quitting in all fields. In fact, women continue to report higher burnout rates than men and in larger numbers than a year ago. A third of all women report they’ve seriously considered scaling back their work or even leaving the workforce, which is an increase from the quarter who said the same in June 2020. Nearly half of all women have thought about leaving their current company.
Another report from the National Academies of Sciences, Engineering, and Medicine attempts to quantify the effect of women in STEMM academia — those pursuing degrees as well as research and education careers in STEM and medicine. There’s evidence that the pandemic degraded
| ScanrailUnleashing the power of the IoT
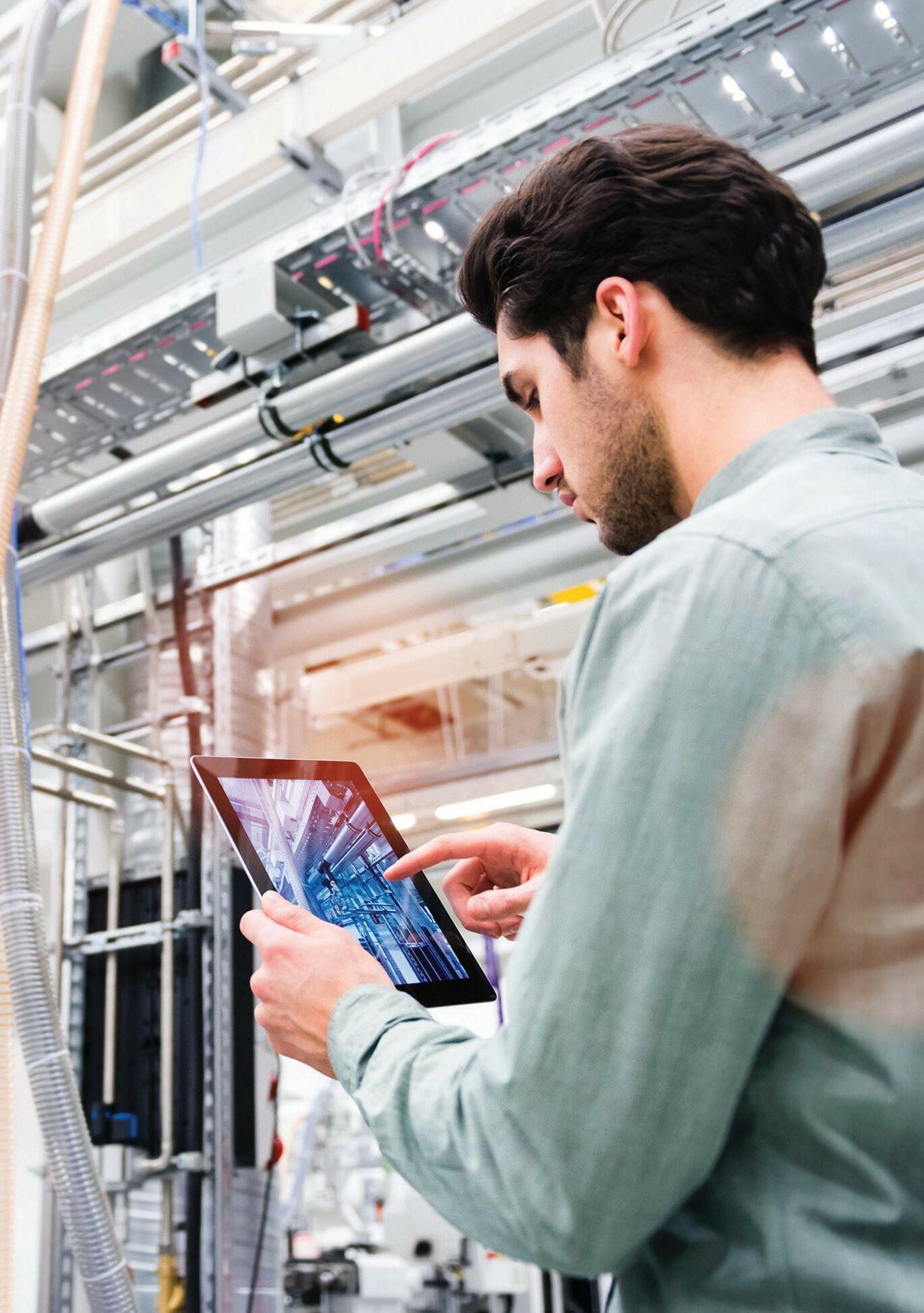
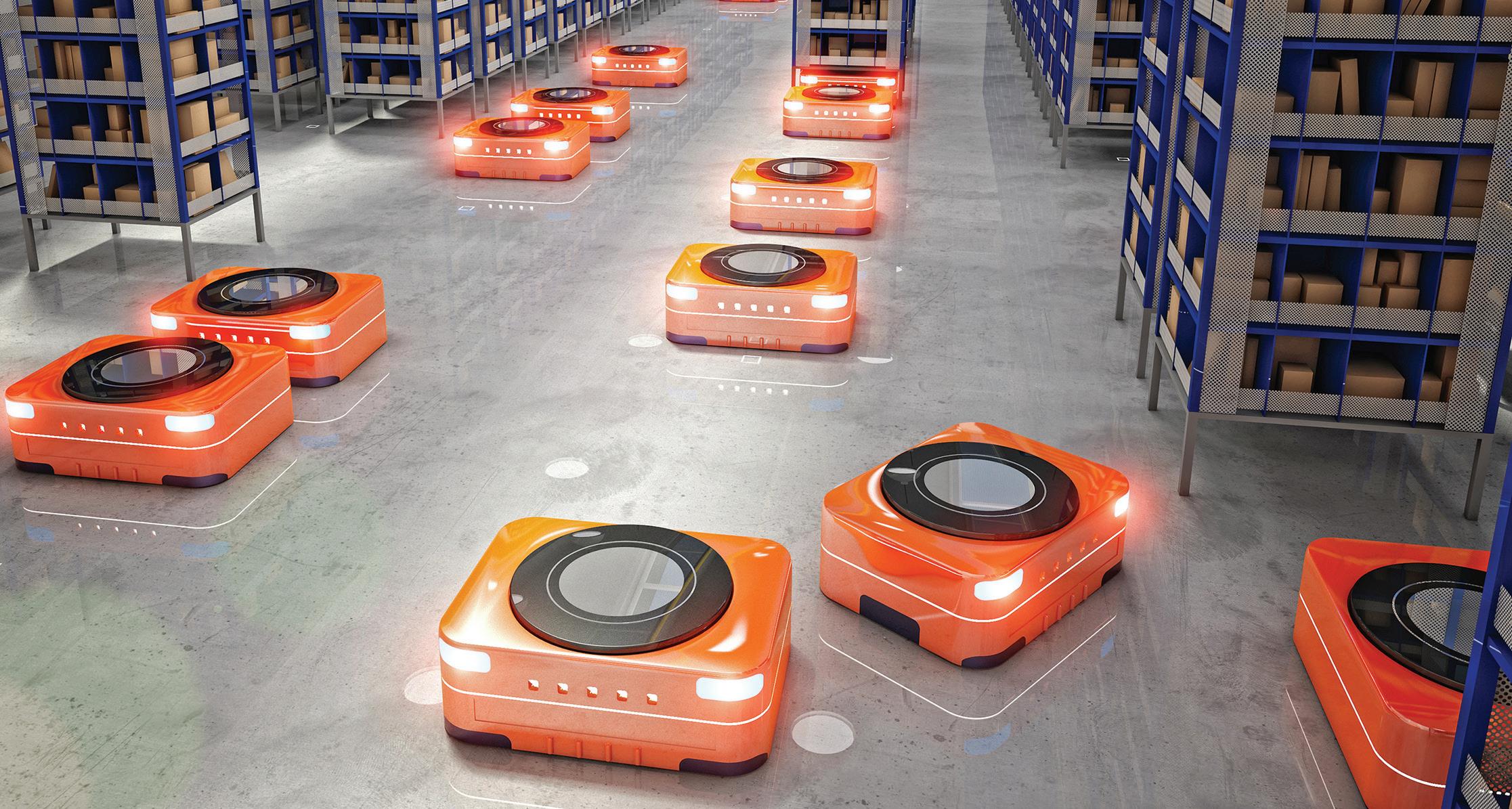
So you can focus on what really matters
Today, we can rely on technology to help us focus on what really matters with intelligent devices connected to the Internet of Things – helping us remember appointments, enhancing our health, or even offering secure mobile payment. Making our lives easier, safer and greener.
With this technology around us, we get back a resource that is so scarce at the moment: time. Time for what really matters. This can only work with accurate sensing, reliable computing, a stable connection, and firm security.
The IoT holds this power, we just have to unleash it. Microelectronics are the heart of the IoT – See how #WeMakeIoTWork
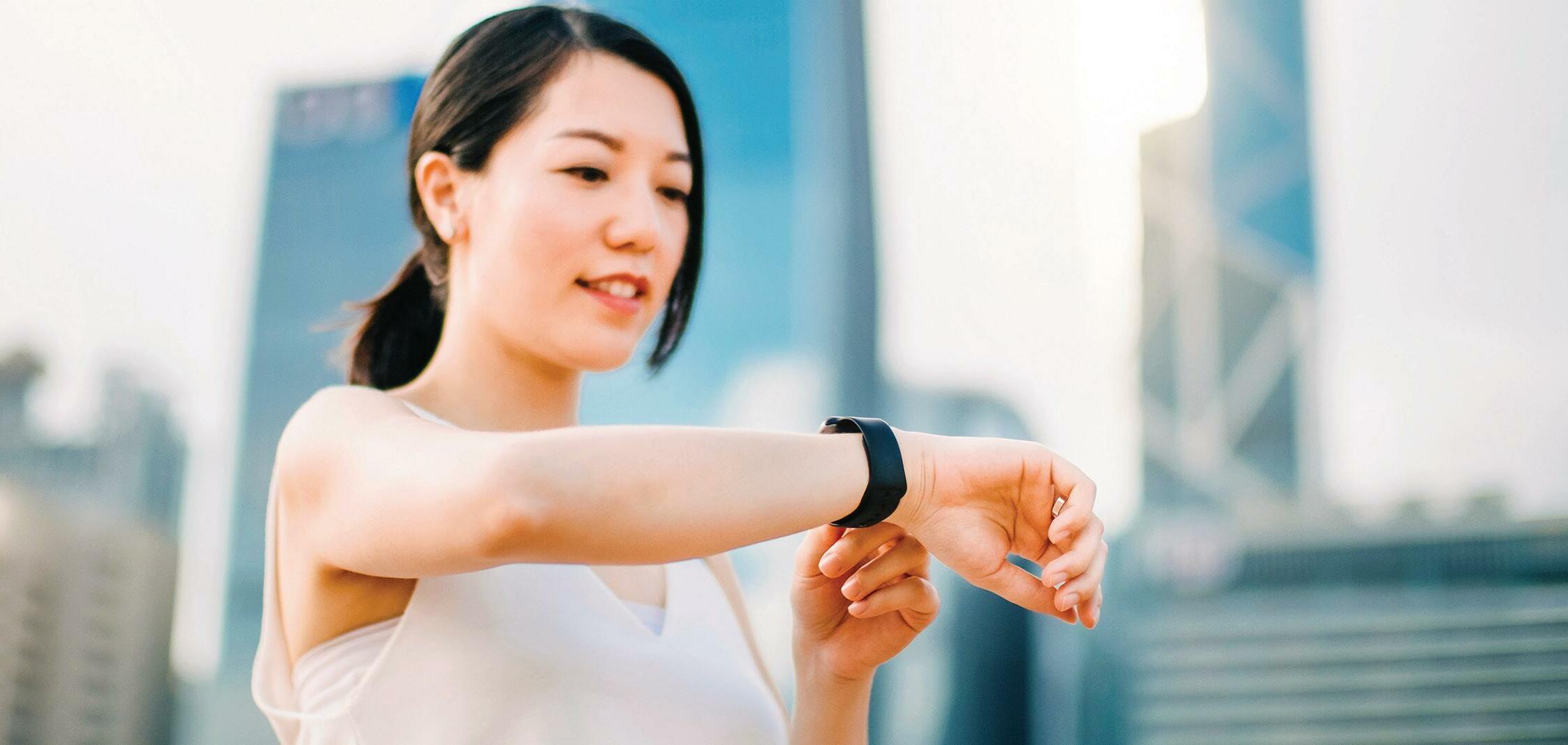
WOMEN IN ENGINEERING SALARY UPDATE
productivity, work/life boundary control, networking, and mental health for women in academic STWMM settings. Increased caregiving responsibilities had disproportionately negative effects on women. The gendered effects of
remote work include more academic isolation for women as well. That said, there’s evidence that COVID-19 also prompted a worldwide increase in the amount of caregiving that men provide for their children. More than half male
respondents to one survey reported a desire to continue working at home to increase time with family. An increase in the number of virtual conferences also boosted their accessibility for those who cannot travel due to existing familial commitments.
SELECT OCCUPATIONS BY SEX AND MEDIAN EARNINGS
TOTAL MEN EMPLOYED WOMEN EMPLOYED PERCENT WOMEN MEN’S EARNINGS WOMEN EMPLOYED FULL TIME WOMEN’S EARNINGS AS PERCENT OF MEN’S
TOTAL STEM OCCUPATIONS 10,769,890 7,890,084 2,879,806 26.7 91,360 76,820 84.1
ENGINEERING OCCUPATIONS 3,270,393 2,780,042 490,351 15 90,930 79,170 87.1
Architectural and engineering managers 174,799 154,808 19,991 11.4 147,093 142,245 96.7
Surveyors, cartographers, and photogrammetrists 38,618 30,916 7,702 19.9 70,273 56,659 UNAVAILABLE
Aerospace engineers 130,727 114,393 16,334 12.5 112,402 101,105 89.9 Agricultural engineers 3,010 2,614 396 13.2 90,716 93,777 UNAVAILABLE
Bioengineers and biomedical engineers 14,712 11,810 2,902 19.7 94,134 90,990 UNAVAILABLE
Chemical engineers 77,299 61,820 15,479 20 105,727 101,296 95.8 Civil engineers 425,576 358,160 67,416 15.8 91,923 79,966 87
Computer hardware engineers 59,146 48,993 10,153 17.2 102,060 90,923 UNAVAILABLE
Electrical and electronics engineers 259,437 236,008 23,429 9 101,802 92,617 91
Environmental engineers 32,561 21,970 10,591 32.5 91,027 80,086 88 Industrial engineers — including health and safety 256,526 205,133 51,393 20 86,334 80,836 93.6
Marine engineers and naval architects 11,739 10,830 909 7.7 86,276 103,672 UNAVAILABLE
Materials engineers 52,724 45,352 7,372 14 87,936 82,210 93.5 Mechanical engineers 328,181 299,637 28,544 8.7 91,189 90,524 99.3
Mining and geological engineers • mining safety engineers 7,552 7,052 500 6.6 110,014 78,145 UNAVAILABLE
Nuclear engineers 7,605 6,376 1,229 16.2 111,834 105,182 UNAVAILABLE
...Petroleum engineers 29,269 24,013 5,256 18 138,456 126,712 UNAVAILABLE
Engineers (all other) 593,540 508,067 85,473 14.4 101,281 91,932 90.8
Architectural and civil drafters 54,878 43,661 11,217 20.4 56,781 46,393 81.7
Other drafters 94,179 74,863 19,316 20.5 58,064 50,363 86.7
Electrical and electronic engineering technologists and technicians 109,786 99,857 9,929 9 65,471 52,401 80
Other engineering technologists and technicians, except drafters 387,073 303,599 83,474 21.6 60,034 48,180 80.3
Surveying and mapping technicians 71,453 65,147 6,306 8.8 53,592 46,654 UNAVAILABLE
Sales engineers 50,003 44,963 5,040 10.1 125,063 91,083 UNAVAILABLE
Means of error data have been removed for space. Source: U.S. Census Bureau American Community Survey

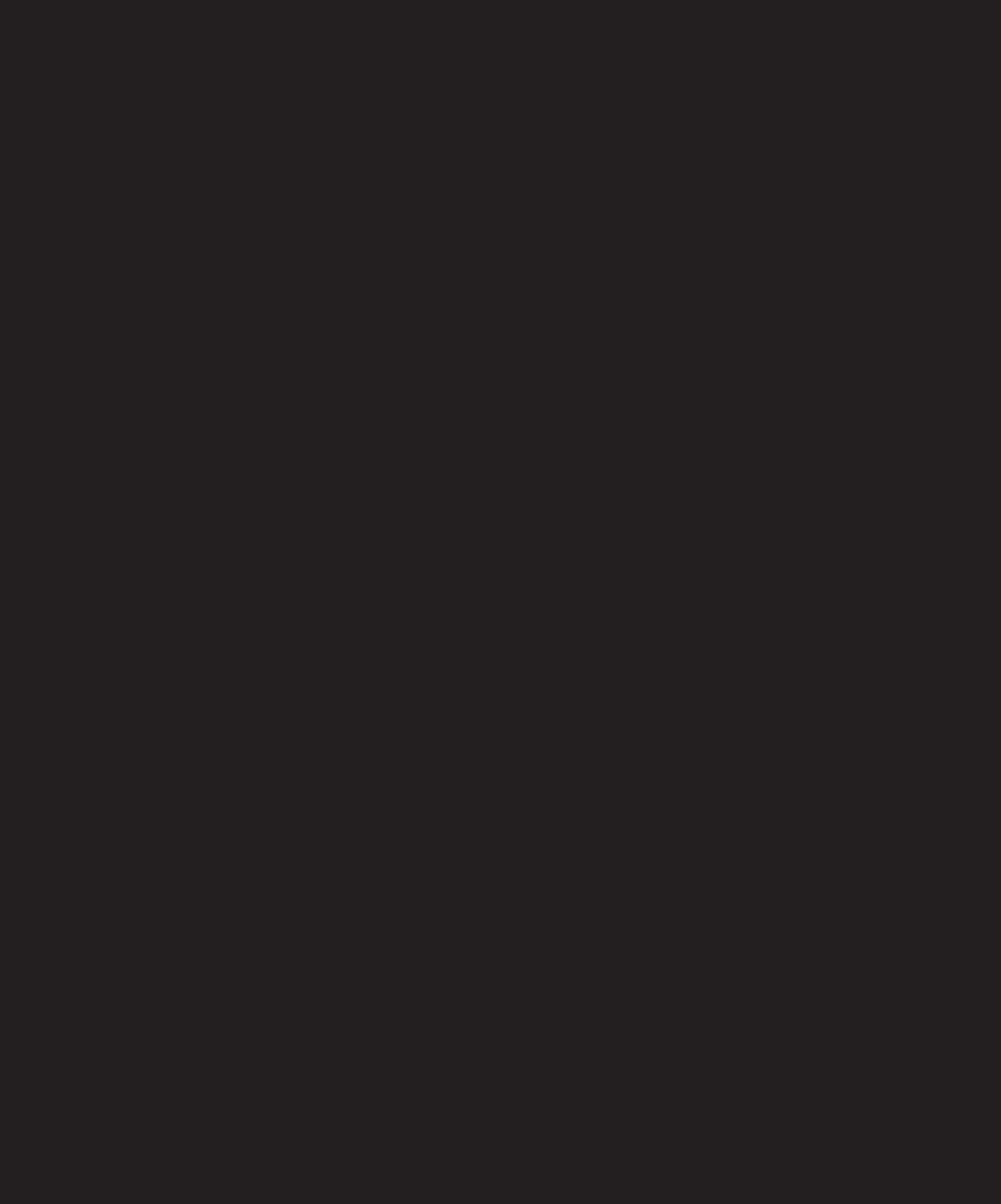
world
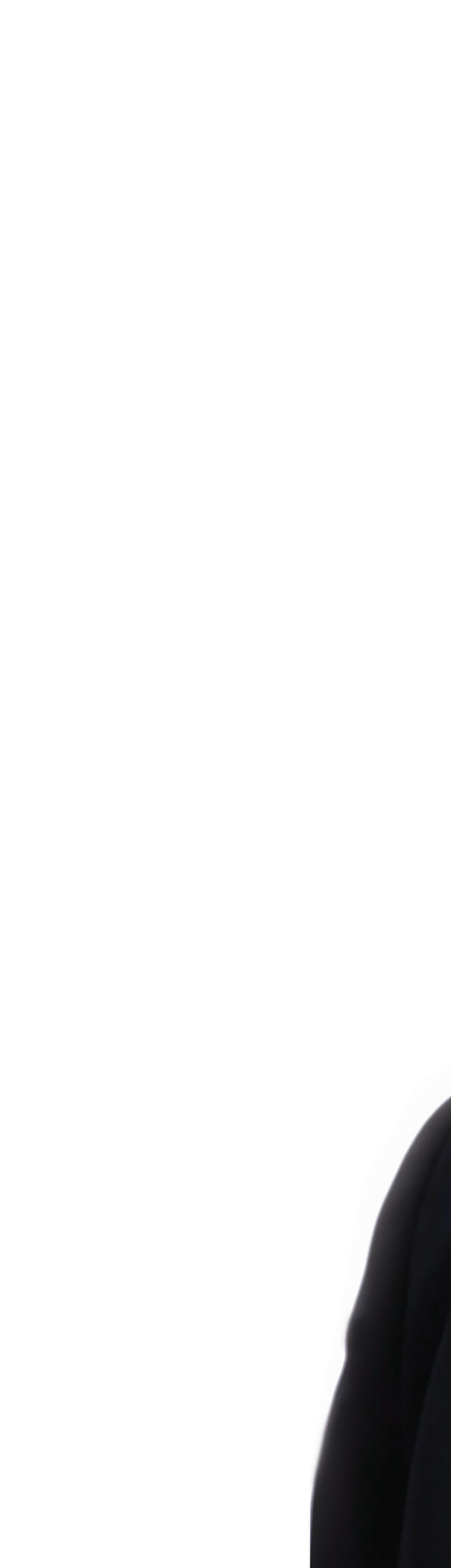
Helping the through engineering
Today’s global engineering challenges require collaboration to solve.
For Ellen Ferraro, the attraction of engineering is the problem solving she gets to do. “Not just problem solving for the sake of problem solving,” she says, “but solving technical issues that have a benefit to society or the world.”
She first realized this preference in graduate school when she received a NASA research fellowship to build an instrument to study the Greenland ice sheet. At that time, global climate change was less understood and scientists needed more data. So, NASA wanted to measure changes in the Earth’s global ice sheets.
The Greenland ice sheet was chosen as it is smaller, making it a bit easier to study, and it’s closer to the United States. The goal was to map Greenland topography to a centimeter-level resolution to measure where there might be melting going off into the ocean and land mass shifting. Ferraro was on the first NASA P-3 aircraft that mapped all of Greenland for a topography baseline.
“My role was developing a radar that had high resolution capability. I worked with glaciologists and other scientists from NASA so that I could understand why we were doing it. My job was to help them figure out how to measure it, and their job was to then take that data and understand what was happening. That was my first, ‘Wow, this is really cool; I can see how what I’m doing impacts the bigger picture’ experience, which in this case is understanding how our climate was changing.”
Ellen J. Ferraro, PhD
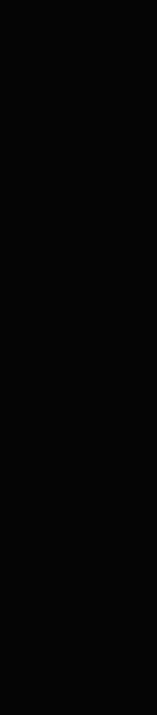
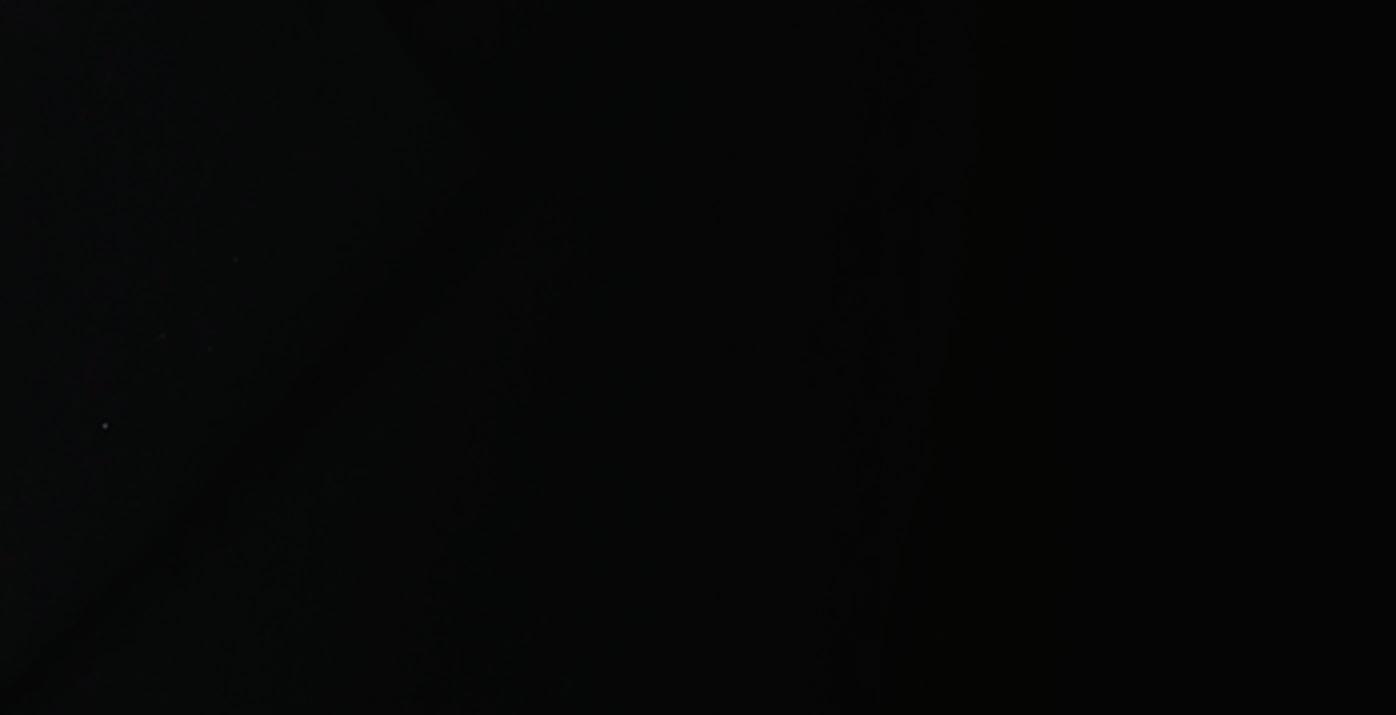

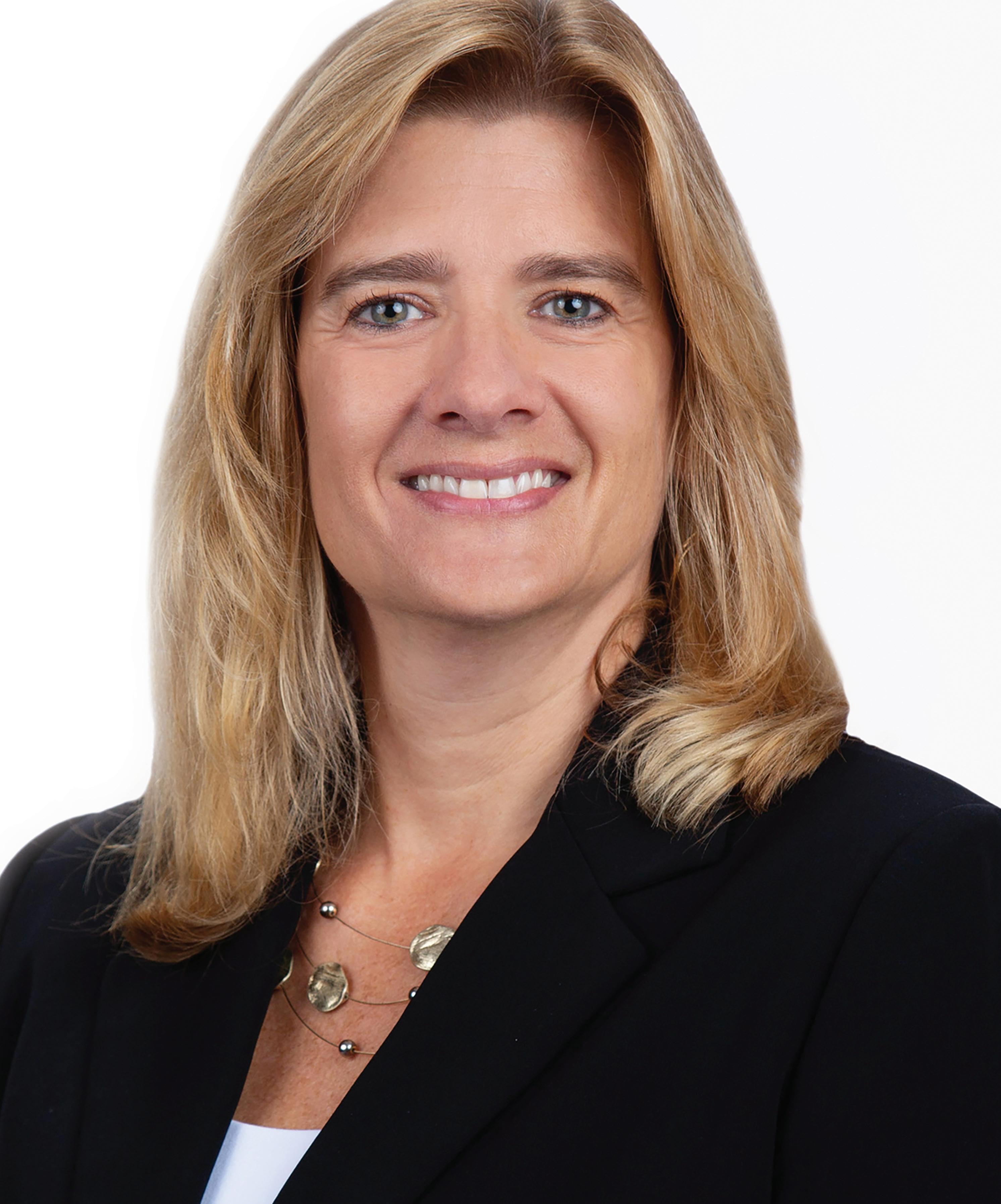
Vice President, Engineering & Mission Assurance, Raytheon Intelligence & Space
B.S. Electrical and Computer Engineering PhD Electrical and Computer Engineering
Women in Engineering
program because I went to college for nine years straight, but I really enjoyed it. I enjoyed the classes, the research, and I found my passion.
Her rise up the corporate ladder led her to a role where she has an impact and can guide what is important to her.
“Deciding on how we invest our dollars today means that we get the best technology in the future to give to the men and women serving our country,” she says. “You want them to have the best possible equipment to protect themselves, and making the investments today to enable that is, to me, really important.
I think the diversity of ideas coming to the table is critical, so I think having men and women, a diverse team, is absolutely important, as long as everyone gets to have their voice heard. You have to have the inclusion piece of it.
— Ellen J. FerraroFerraro is now the vice president of engineering and mission assurance at Raytheon Intelligence & Space. She supervises just under 15,000 engineers and mission assurance professionals. It’s her favorite role now because she can be very strategic in determining where to invest Research and Development dollars.
Ferraro comes from a family of engineers. Her father and oldest brother are chemical engineers; her second oldest brother and her oldest sister are civil engineers.
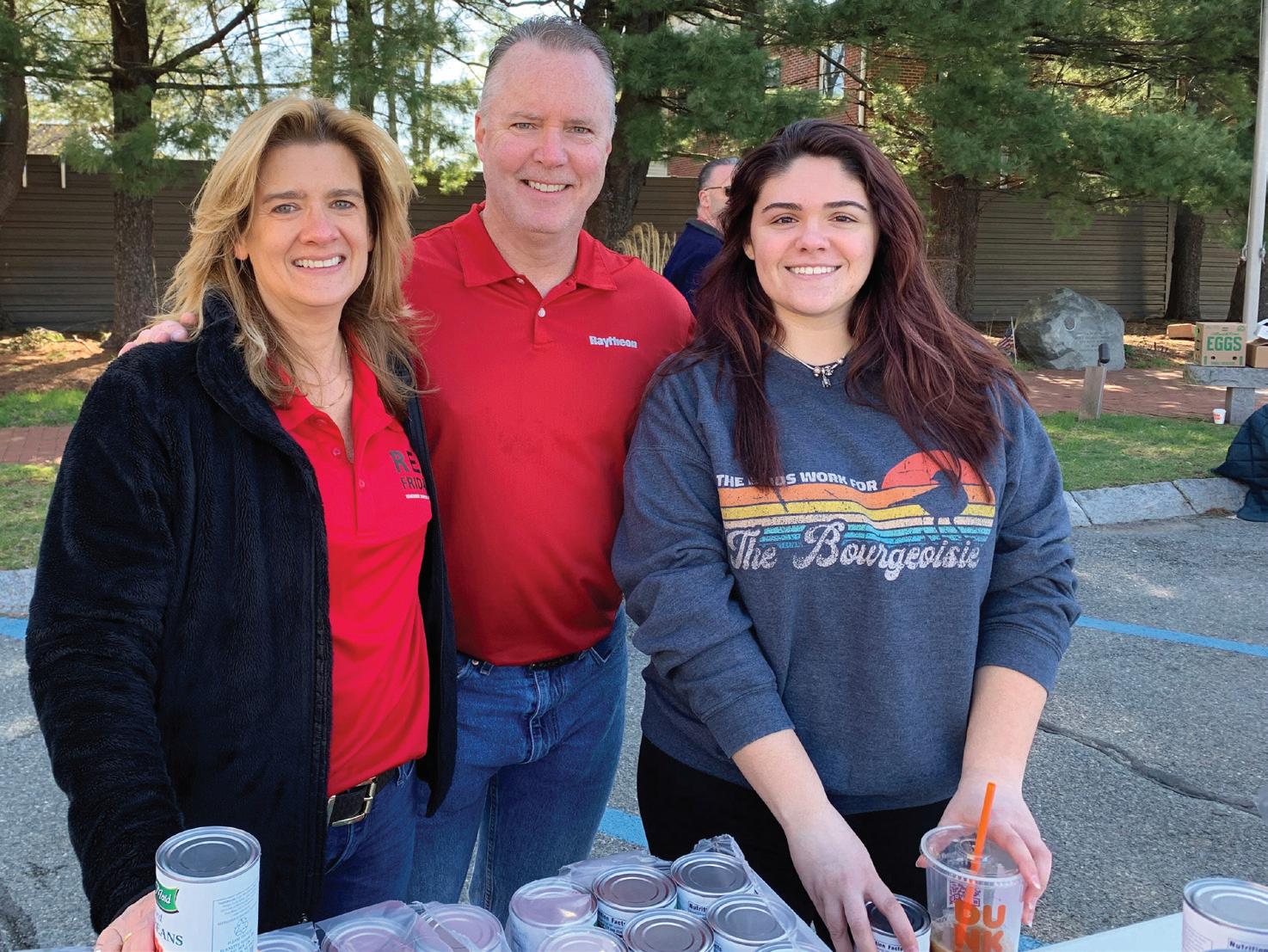
“I always tell everybody it was my destiny to be an engineer,” she says. “The only decision I had to make was what type of engineer. Just to be the rebel in the family, I chose electrical because no one else had taken that path yet. I literally had no idea what electrical and computer engineering was but I decided that was the path I was going to take. Turns out I loved it. I loved it so much that I stayed in school basically as long as I possibly could. My parents thought I was on some kind of work avoidance
“That’s one of the reasons I love my job, and the other is leading a large organization of engineers and helping to develop them and get them into a career path that excites them. Not everybody has the same career goals, so working with a large organization and being able to provide lots of different career path options is meaningful to me.”
Being heard
Through the supervision of that many men and women, Ferraro has become familiar with the different ways each works at their jobs.
“I think the diversity of ideas coming to the table is critical, so I think having men and women, a diverse team, is absolutely important, as long as everyone gets to have their voice heard. You have to have the inclusion piece of it.
“And yes, I see a difference in the way women and men work. Women will approach a problem and collaborate together. The big piece here is making sure that everybody’s voice gets heard. I am fortunate that my boss, the president of Raytheon Intelligence & Space, is very good at that. If I go to speak and someone speaks over me, such as one of my peers, which happens, my boss will say to whoever spoke over me when they’re done, he’ll say, “Ellen, you were going to say something or

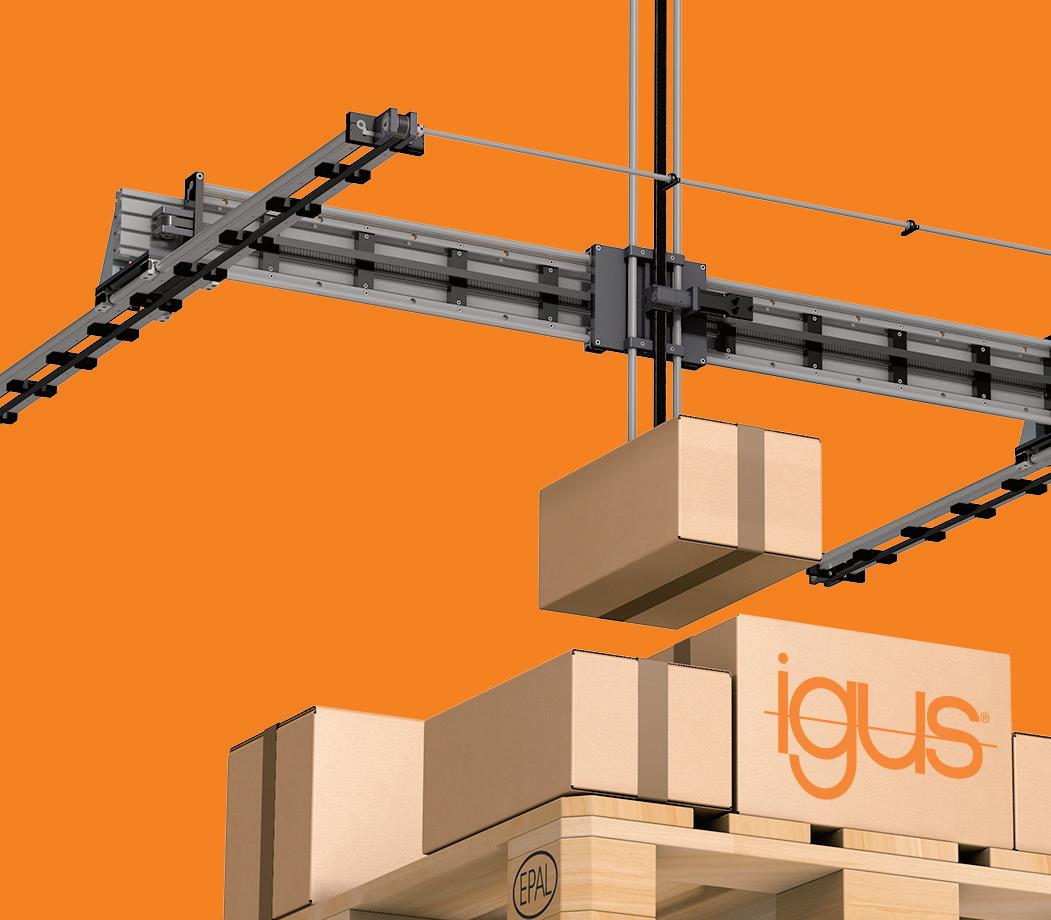
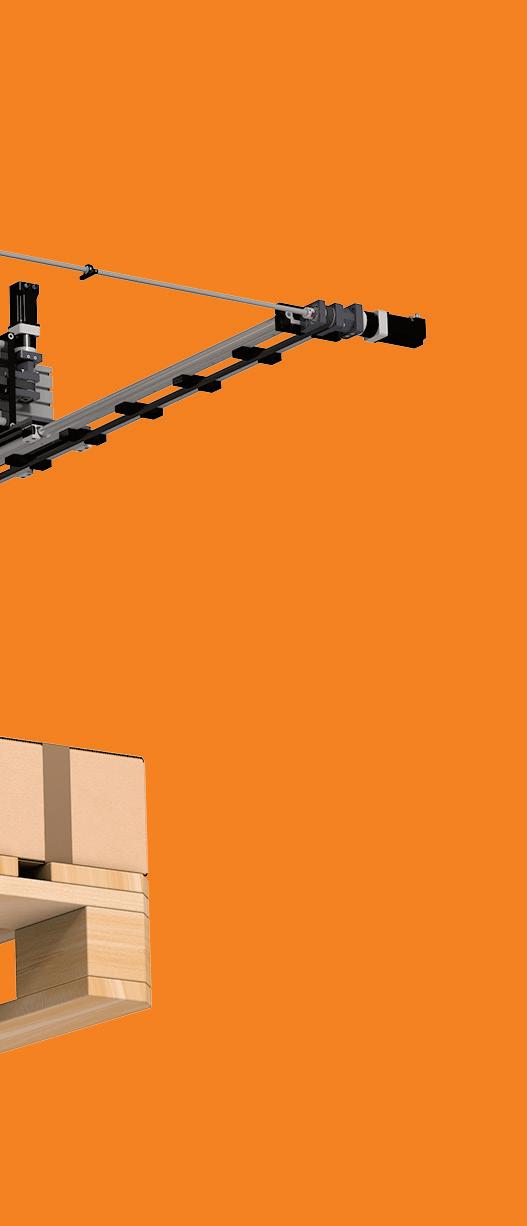
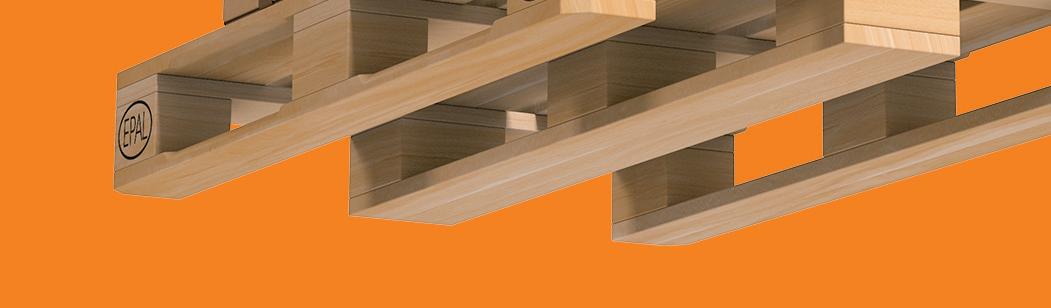
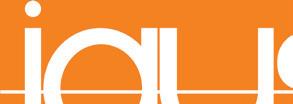
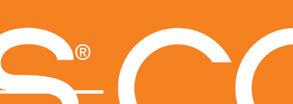
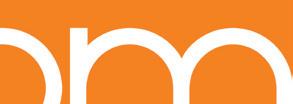
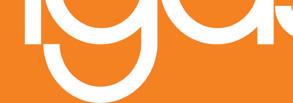
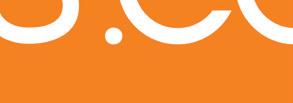

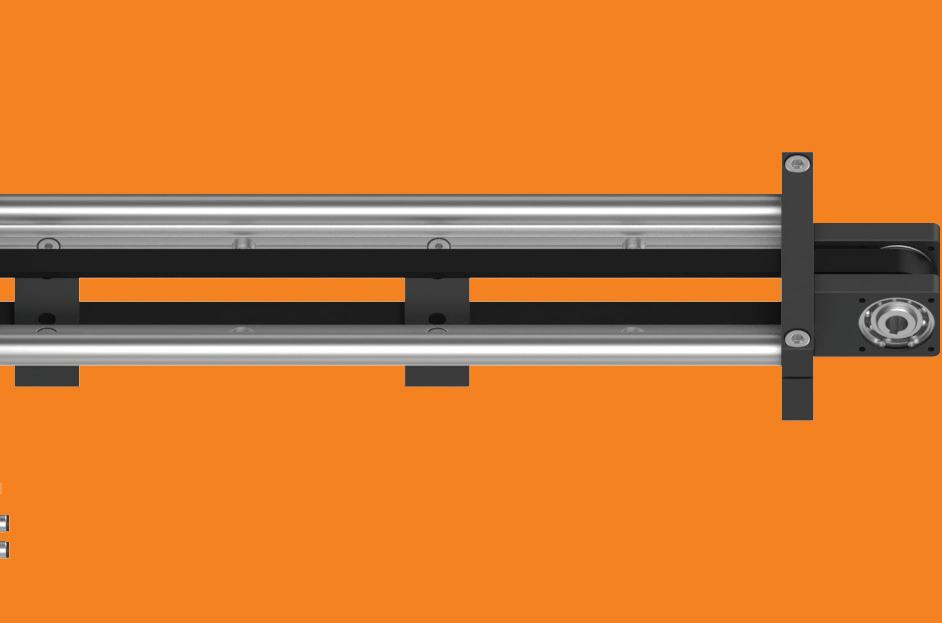

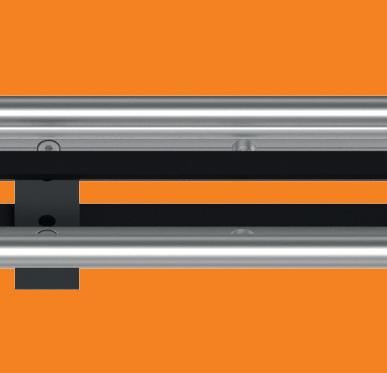
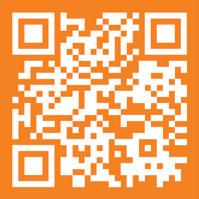
Women in Engineering
you started to say something, what was that,” and pauses everyone else who may want to jump into the conversation, so that my voice is heard. And he doesn’t just do it for me, he does it for everybody on the team. It tends to be the woman on the leadership team that he has to do it for, but he always does it. So, I try to replicate that in my meetings. And I expect my team to do it with their team to flow that culture down so that the dynamic of men and women is something that we are taking advantage of, as opposed to just letting them be two separate ways of thinking.”
Ferraro tells another story of helping others be heard.
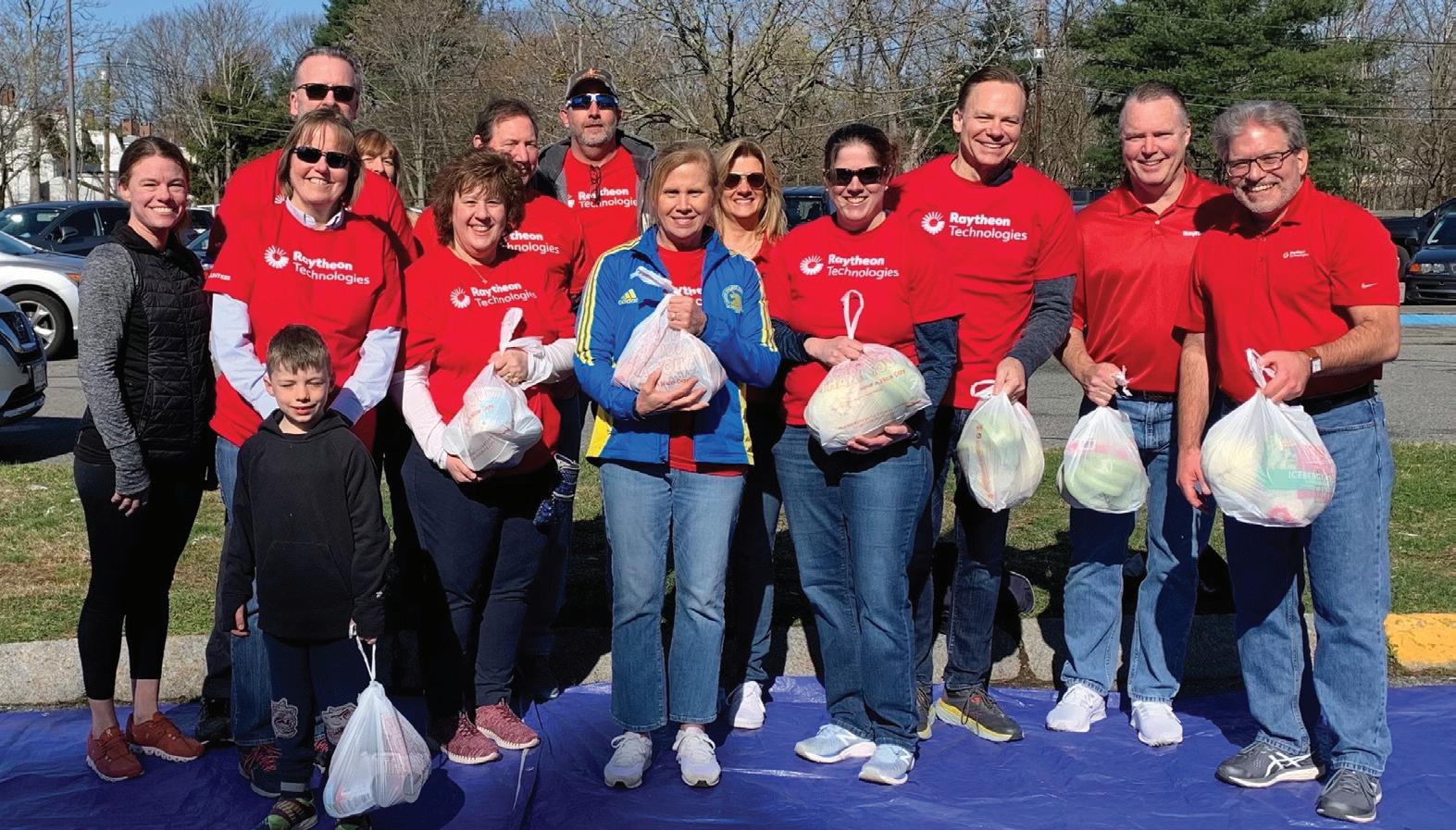
“One of the first leadership roles I had was on a program called Seabased X-band radar. It is a massive radar, sitting on a mobile platform in the middle of the ocean. It’s about 300 feet, so think of a football field size platform sitting in the ocean with a massive radar on it. It’s used as part of our national missile defense. I was working on that radar before it had been built, and I was leading the team that was modeling and

simulating how the radar would work.
“We had a pretty tough schedule and a young and fairly diverse team. One woman in particular, Edna, was probably the brightest one on the team. She knew more about the simulation than anyone else. But whenever we held meetings to brief higher levels in the company, she’d always sit in the back of the conference room and not say anything. When people would ask questions, I knew she knew the answer, but she wouldn’t say a word. She absolutely could have proven that she was smarter person in the room.
So I pulled her aside and said, “ I know you know more than anyone else on this particular subject. I want you to sit at the table next time, not in the back of the room. And when those questions come up in your area, I’m going to look to you and I’m going to say, “Edna knows this,” and I want you to chime in.” And so, she did. This was 15 years ago, and today Edna has done outstanding in the company and she’s stayed as an engineer. Very, very talented. And
to me that was learning how to lead a team, and to bring out the best of the team.”
Ferraro strongly encourages women to speak up and have confidence that their education qualifies them to do the engineering projects they work on. In addition, she points out the importance of having advocates.
“If you know going into a situation that there’s someone who tends to speak over you and take credit for your statements, an advocate can help.”
Most women have faced situations where they made a suggestion, it was ignored, and two minutes later a man says it and suddenly it’s a brilliant idea.
“An advocate can direct the conversation with something like, “You know, Sue just said that, Joe. That was a great idea she had, and you’ve just confirmed it,” or something to that point, adds Ferraro.To find advocates, Ferraro advises talking to a few people about the subject prior to the meeting who will help advocate and get the points across that you need to get across. “I think men develop advocates a little more naturally. I try to work that process not only with my female counterparts, but with my male counterparts to say ‘Hey, can we go into this meeting aligned?’ And I ask a couple of men that are my peers that are huge advocates for me to help get certain topics across.”
As for finding advocates, Ferraro advises finding people who want that role. “Not everybody wants it or is good at it. I think it’s who do you trust. And you build trust in a relationship over time.”
Inspiring young engineers
Multiple efforts have been made to encourage more women to pursue engineering as a career. When Ferraro graduated, she was the president of the Society of Women
One of Ferarro’s early projects was working on the massive Sea-based X-band radar, which sits on a mobile platform in the middle of the ocean. It’s used as part of the U.S. national missile defense.

participates in STEM events and Ferraro is passionate about traveling to middle schools, high schools, and colleges.
Engineers at her college. At that time, the statistics on women in engineering were not high, and have stubbornly remained about the same for many years.
Ferraro thinks it’s absolutely essential to encourage more young women and girls to go into engineering. She is supported in her efforts through the Society of Women Engineers as well as Raytheon Technologies. The company
“A lot of times I go to the SWE student sections to encourage those women to stick with it, because there’s also a high dropout rate of females in engineering. They may go into it, but the dropout rate is higher for females than males.” She also encourages women who have graduated to pay it back. “Once you’ve made it through, please make sure that you spend time encouraging other young women to go into engineering. I think the most important thing is those of us in engineering need to make sure that we’re getting out there, supporting the STEM events. Raytheon does a lot in that area through our corporate sponsorship of events, like First Robotics, but also through our Employee Resource Groups (ERGs), which I feel have a huge impact. For women, African Americans, LGBTQ, each area of society has a resource group. And these ERGs go out into the community and encourage young women and men to go into STEM fields.”
Ferraro notes that it’s important for women engineers to be engaged in organizations like the
the Electrification of Everything
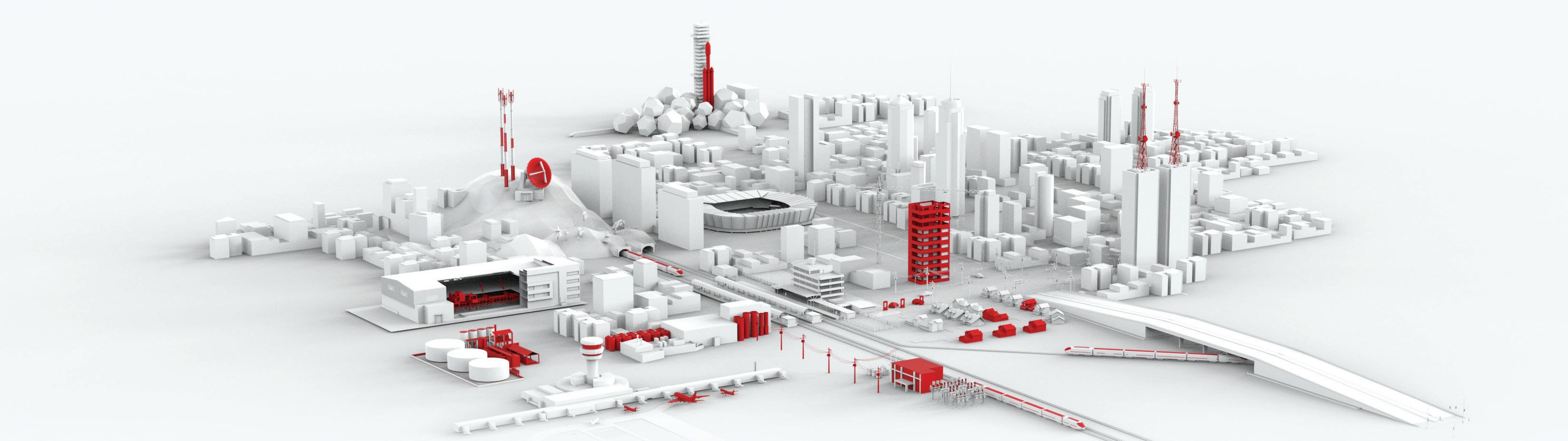
Society of Women Engineers. “It’s showing others the importance of engineering and the value of engineering. SWE played a huge role in my career, even as a student. It really helped me build a network and have confidence to run for an office position in the organization as a student, which was huge for me. It’s how I learned a lot and made a tremendous network of friends that I still have today and have built through the years. I go to the conference every year.
“I can’t say enough about how impactful that can be in helping other women engineers go into engineering, but also stay in engineering.
More often than not, engineering, as a career choice, is not on many people’s radar. “Our society doesn’t advertise much. For example, you won’t see many shows or movies showcasing engineering. I think we also fail at communicating engineering as a profession that helps society. That messaging could make a huge difference, particularly to young girls who are thinking, ‘I want to have an impact on the world, so I’m going to be a doctor,’ or, ‘I’m going to be a teacher,’ where they see what it’s like to be helping others. “I think we need to highlight the stories where engineers are helping others.”
Work the problem
Increasingly, engineering is a team effort, especially when it comes to solving customer problems. A recent challenge for Ferraro involved a technical issue that made it difficult to provide the customer with what they needed.
“When we have problems like that, I’m often awake at night trying to figure it out, but really, it’s all about pulling together the right team because no one individual solves these technical problems. They’re too big to even think about solving on your own. So, I pull in expertise literally from across the company.
We’re a big company, we have 180,000 employees, in pretty much every state. We pull in the right talent, get them engaged, involved, really talking through the technical details, considering all the options until we have a solution.
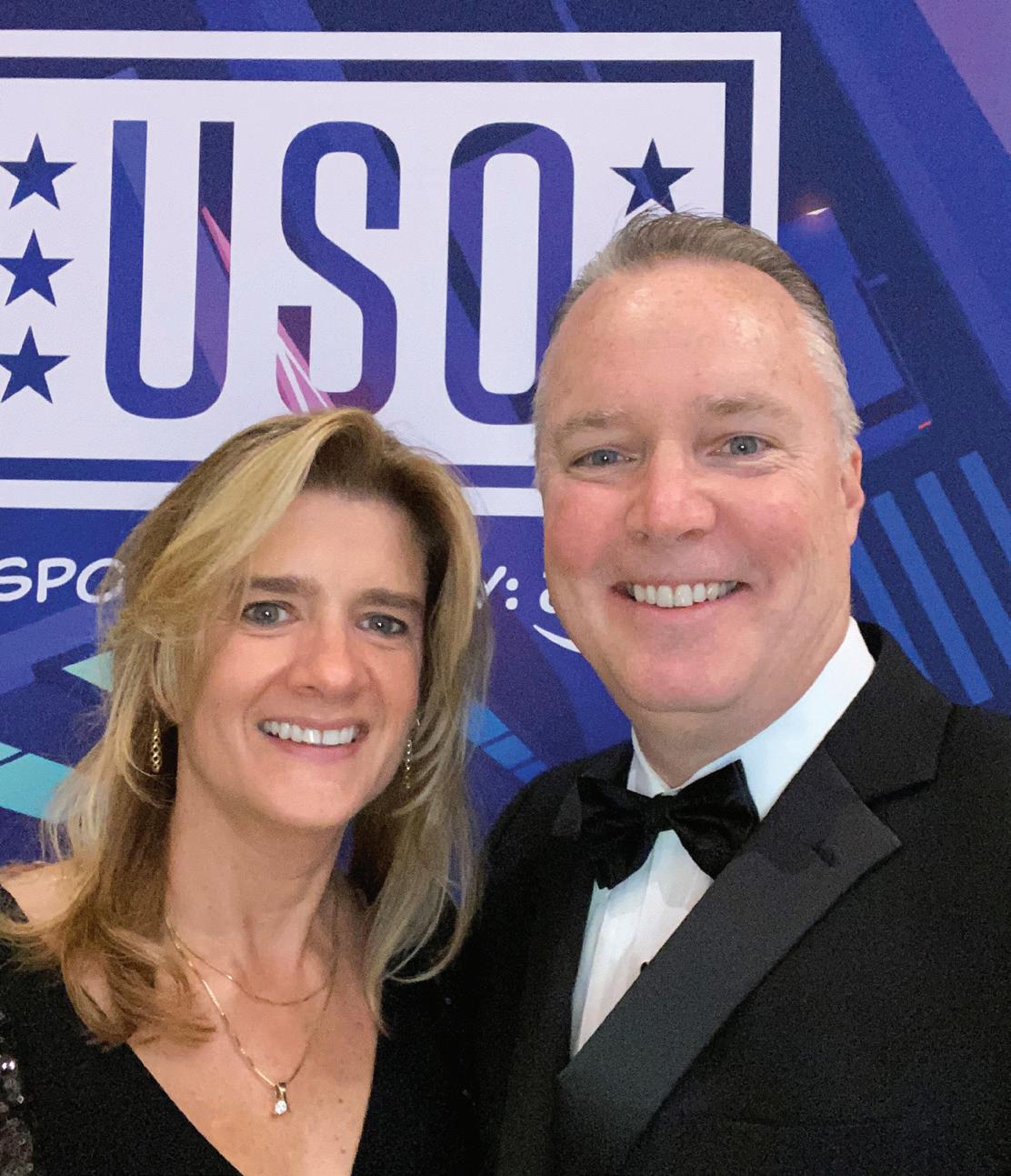
“And I think the important part as you go through each of these challenges, and they happen all the time, is making sure that you learn from them and that others learn from them.
“The team dynamic, or the team problem solving, is one of the things I loved about engineering from very early on, and it’s absolutely essential today. Technology is so deep, meaning we have experts that are specialized, but it’s also very broad in the sense that there’s so many technologies. No one person could possibly solve some of these technically complex issues that we’re trying to resolve. It’s absolutely essential to work as a
team to bring in the right subject matter experts. Never try to do it on your own. And I think this aspect of engineering is not emphasized enough. Many women who might have considered this field might have resisted it thinking it’s a solitary role. And it’s not that way anymore.
“So, whenever I talk about engineering, I try to tell these stories of working in teams. And it’s not just teams of only electrical engineers or only mechanical engineers. I mean, we’re pulling in physicists and mathematicians and every type of engineer, even the finance person. Everybody is in on these, and that’s what I think is exciting. Learning, hearing someone else’s perspective. What is the supply chain person thinking? What is the manufacturing lead thinking? All these different perspectives. So that’s what makes it, to me, a really fun career.”
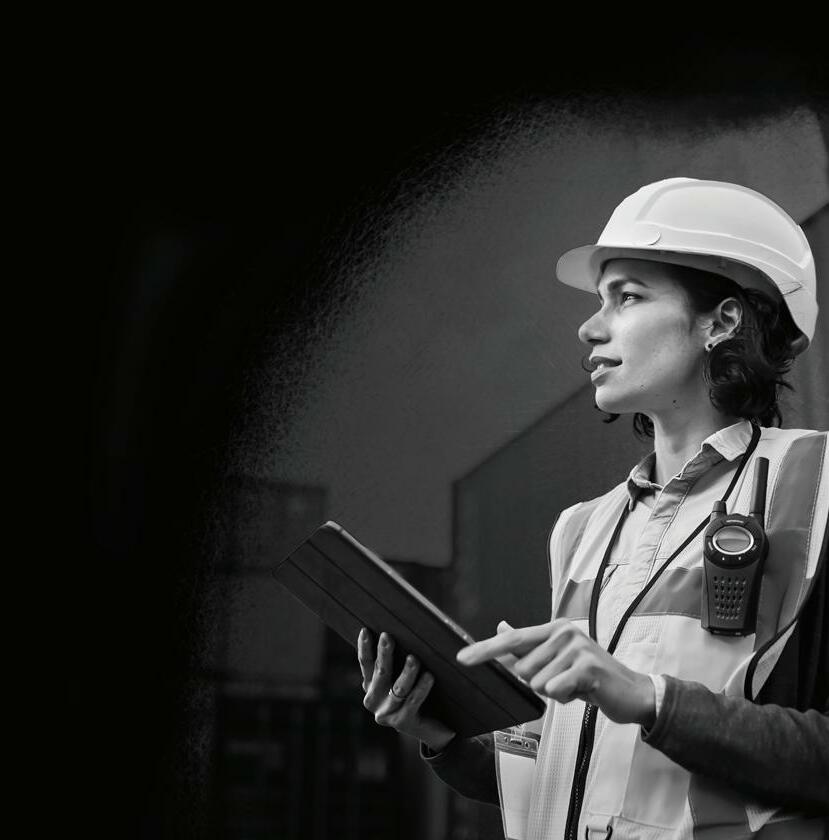

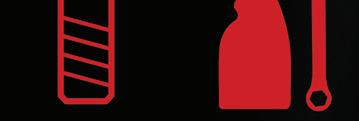
Engineering is a stepping stone to many opportunities
Women don’t have to be perfect in math or science to consider becoming an engineer. Engineering skills can be applied to a range of fields and corporate opportunities.
n France, engineering is a well-known and respected field. Many young people choose it as a career if they have math and science skills and interest. While Christine Georgia did have those skills, engineering was not her first choice. She initially wanted to pursue a career as a writer or artist. However, both her parents were engineers — and thus they were adamant that she obtain an engineering education.
“I very much wanted to write,” she said. “It was hard to forego that goal, but in retrospect now, I am grateful, particularly for my dad who really stood his ground and kind of said, ‘absolutely not.’ And engineering has become, or has turned out to be, much more fulfilling than I thought it would be when I was 16.”

Now a naturalized U.S. citizen, Georgia first came to this country when she was 15 years old; her father had received an opportunity to come to the U.S. to work for a subsidiary of a French company that was based in New Jersey.
“He uprooted the whole family, which, being a teenager at the time was very traumatic and profoundly changed my life,” she said. “I ended up finishing my high school years at a French school in New York City in Manhattan. And you’re 16 and you think you know everything and I just thought, ‘oh, the whole country
Christine Georgia
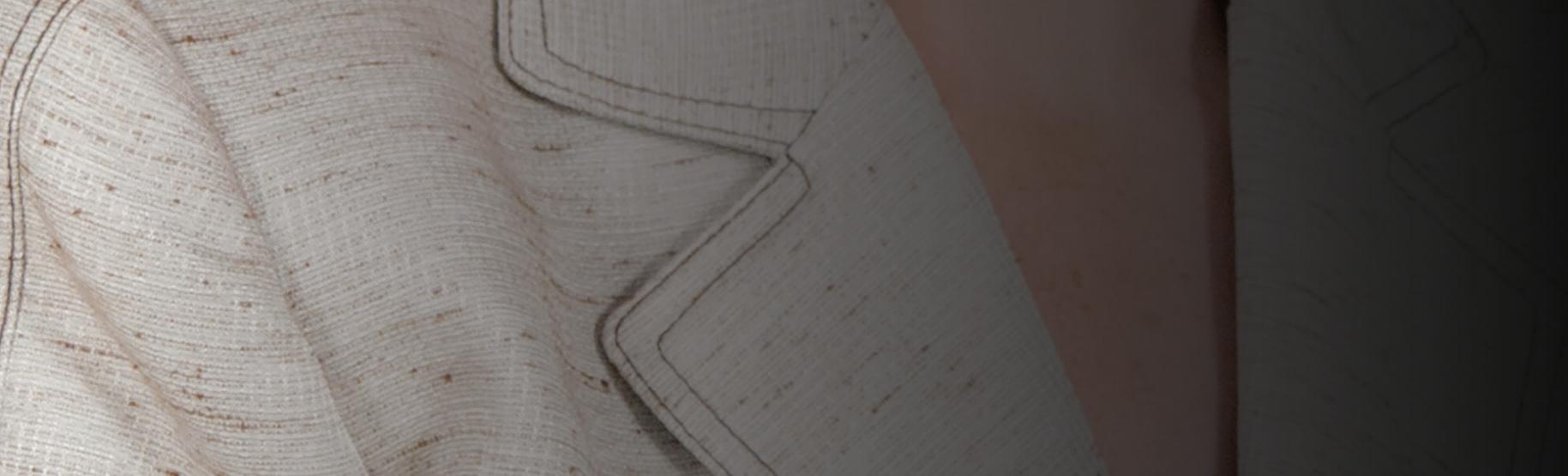
Assistant Dean & Director, Women in Engineering program, Principal Academic Professional, GW Woodruff School of Mechanical Engineering, College of Engineering, Georgia Institute of Technology
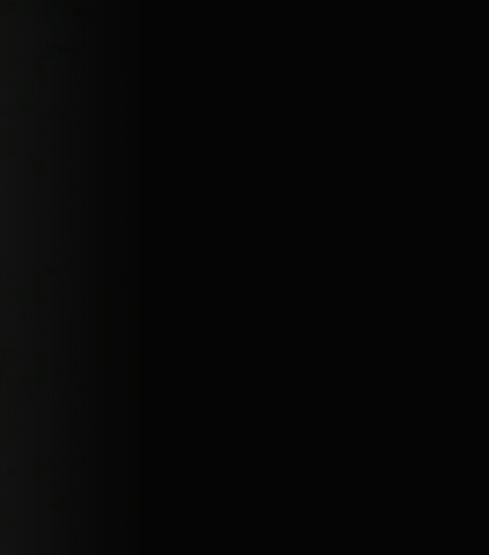
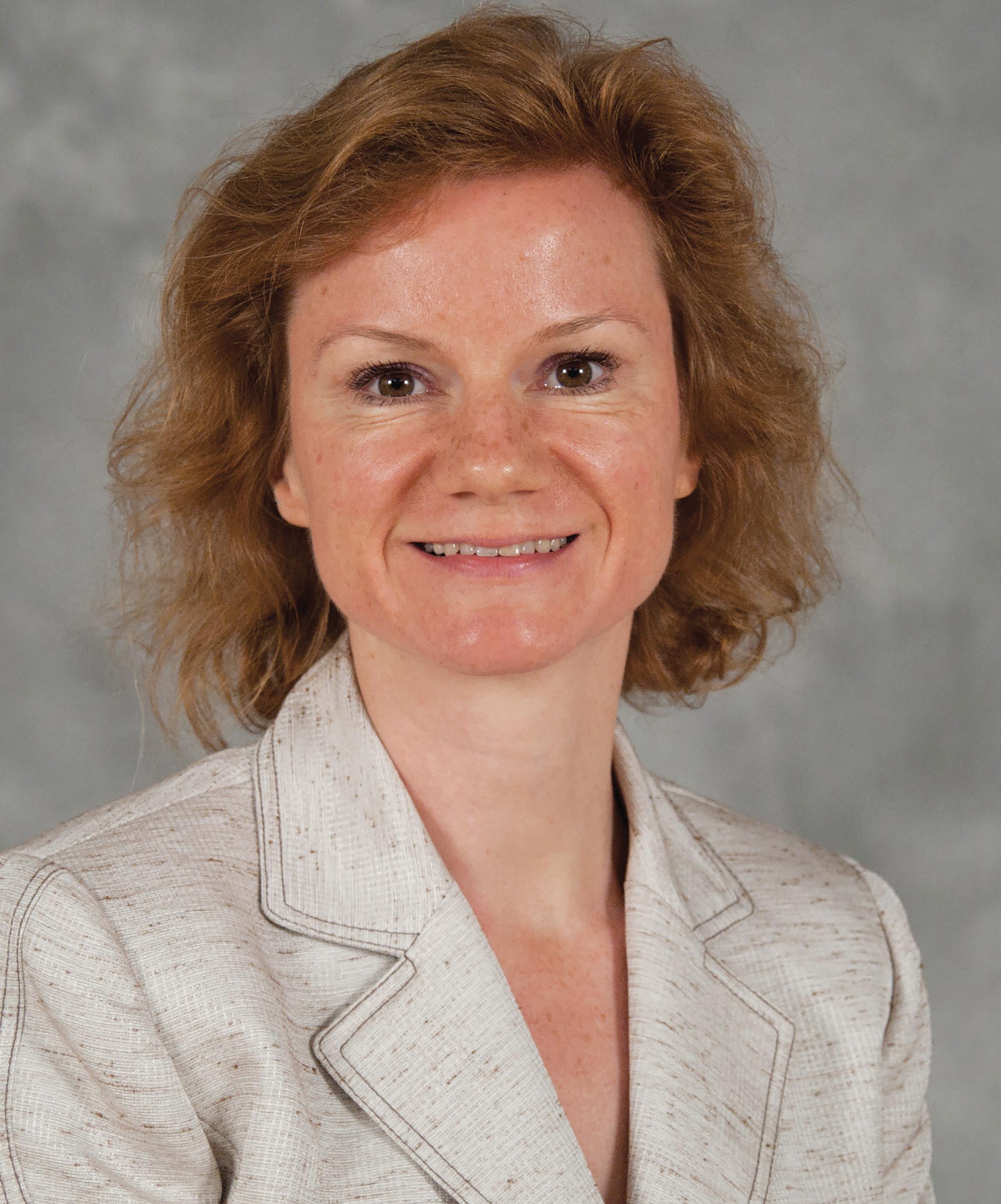
Women in Engineering
hard, still to this day, for companies to hire foreign nationals. Also, I was in a research area that was very defense related. I was looking at cracks in military aircraft. The types of companies that were interested in me definitely did not like the fact that I was a foreign citizen. Every country protects its military, so it makes sense. Still, I had a hard time trying to stay in the States. But being an academic is, still to this day, one of the easiest ways to get the green card, which is the permanent work authorization and then from there, five years later, you can apply for citizenship.
“Therefore, I applied to universities and found out quickly that I love teaching, which I never thought would happen. And so I stayed.”
Engineering can be a stepping stone for so many other fields. The foundation of every engineering field is problem solving skills. So many employers look for people with problem solving skills, including law, medicine, and others.
— Christine Georgia
is like Manhattan. This is amazing. I have to come back.’”
She wanted to go to college in the U.S. but her dad, who was quite cost-conscious, forbid it. So, she went back to France for her first degree in aerospace engineering. The Paris college had a partnership with Georgia Tech, so Georgia received her master’s PhD at Georgia Tech in mechanical engineering.
“I started in aerospace, but then met a professor who sold me on a project for my PhD that was going to be housed in mechanical engineering, so I had to switch majors,” she continued. “I got my PhD from Georgia Tech and basically never left the country, becoming a naturalized citizen in 2008.”
Have degree, will work While Georgia had the necessary degree qualifications for just about any corporate employment, actually getting hired in an engineering field here proved challenging.
“This was 1999. I think part of the situation was with my visa. I was here on a student visa F1, which makes it
She taught at two other universities before returning to Georgia Tech. One was the University of Maine and the other was EmbryRiddle Aeronautical University in Arizona.
Working with young women engineers
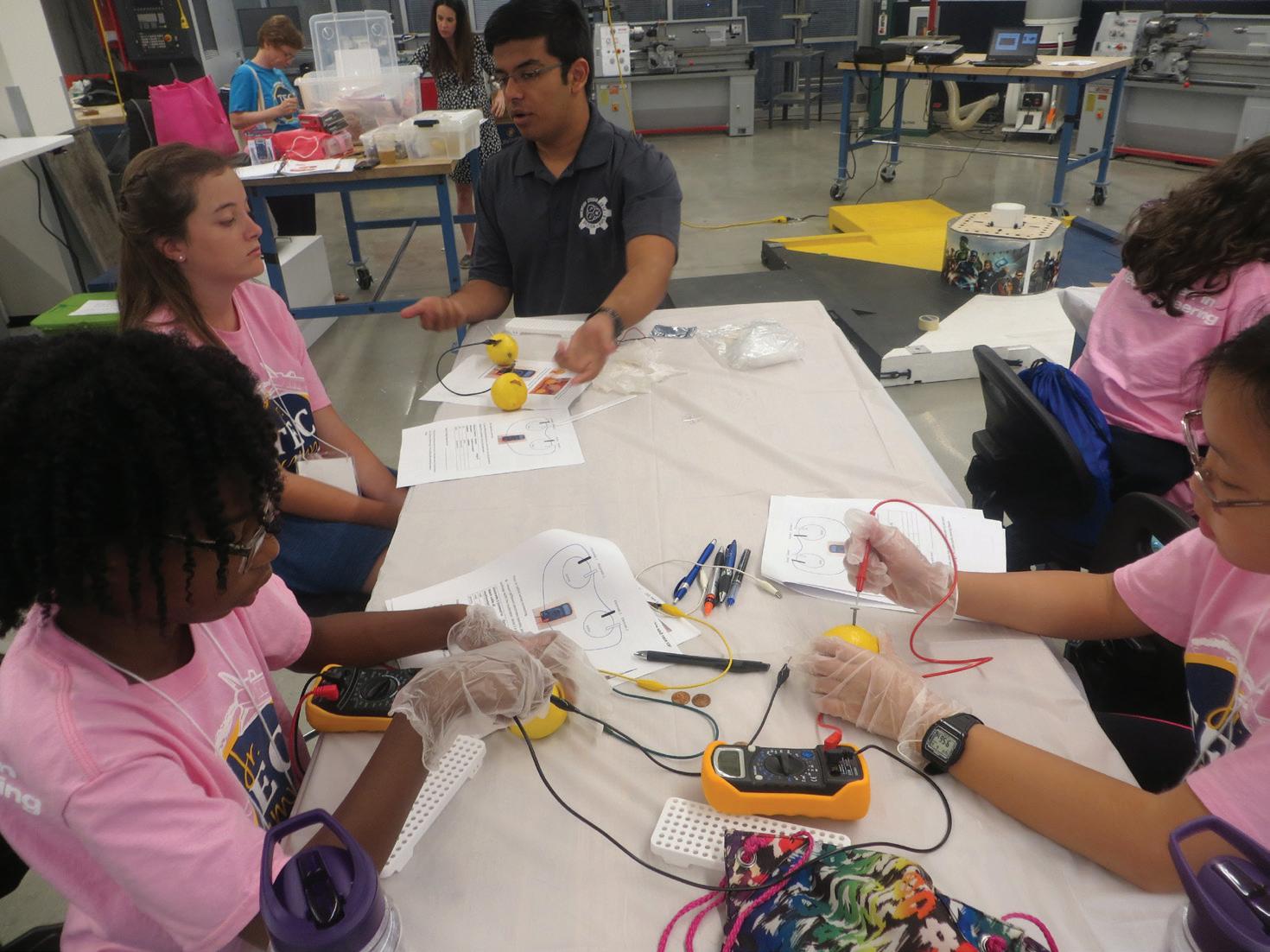
Georgia Tech has been the number one producer of women engineers in the country for more than a decade. Christine has been running the institute’s Women in Engineering program since 2011.
“I think the program’s success is multifactorial,” she said. “The women who come are attracted by different aspects of Georgia Tech. If I had to narrow the biggest factors, number one is the fact that we are academically rigorous as an institution. Women tend to be risk averse. If they’re going to study something, they want to make sure that this is a good degree from a good school that’s going to lead to a good job.”
“And we are good at specific majors that women seem especially interested in. In Biomedical Engineering, for example, the
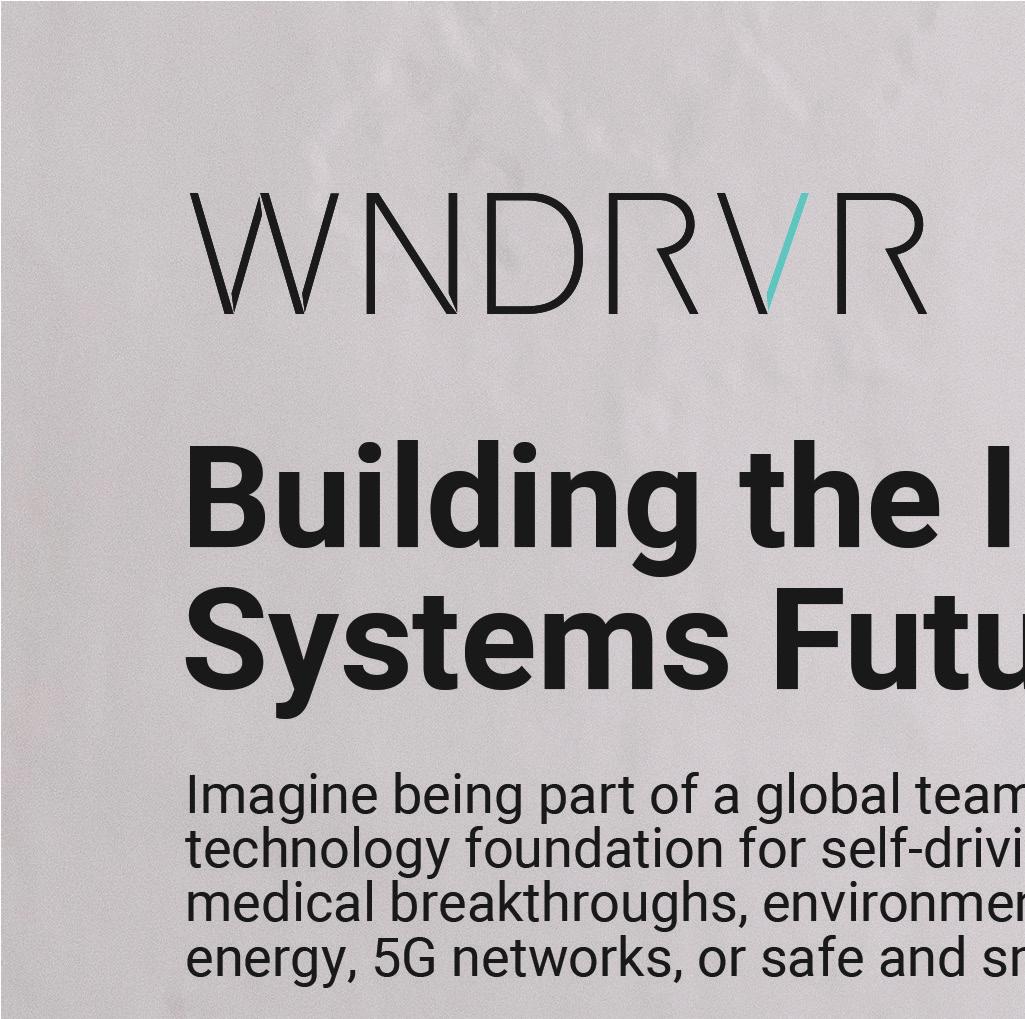
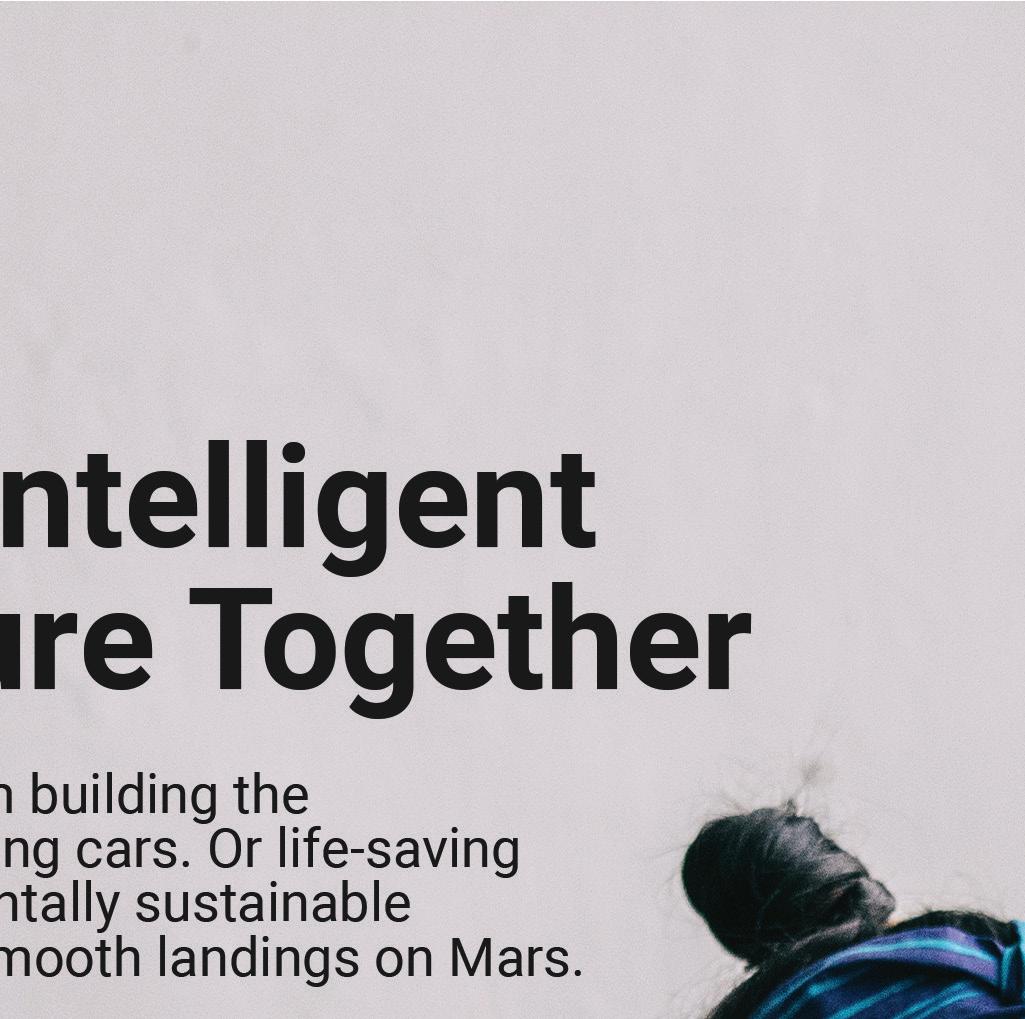


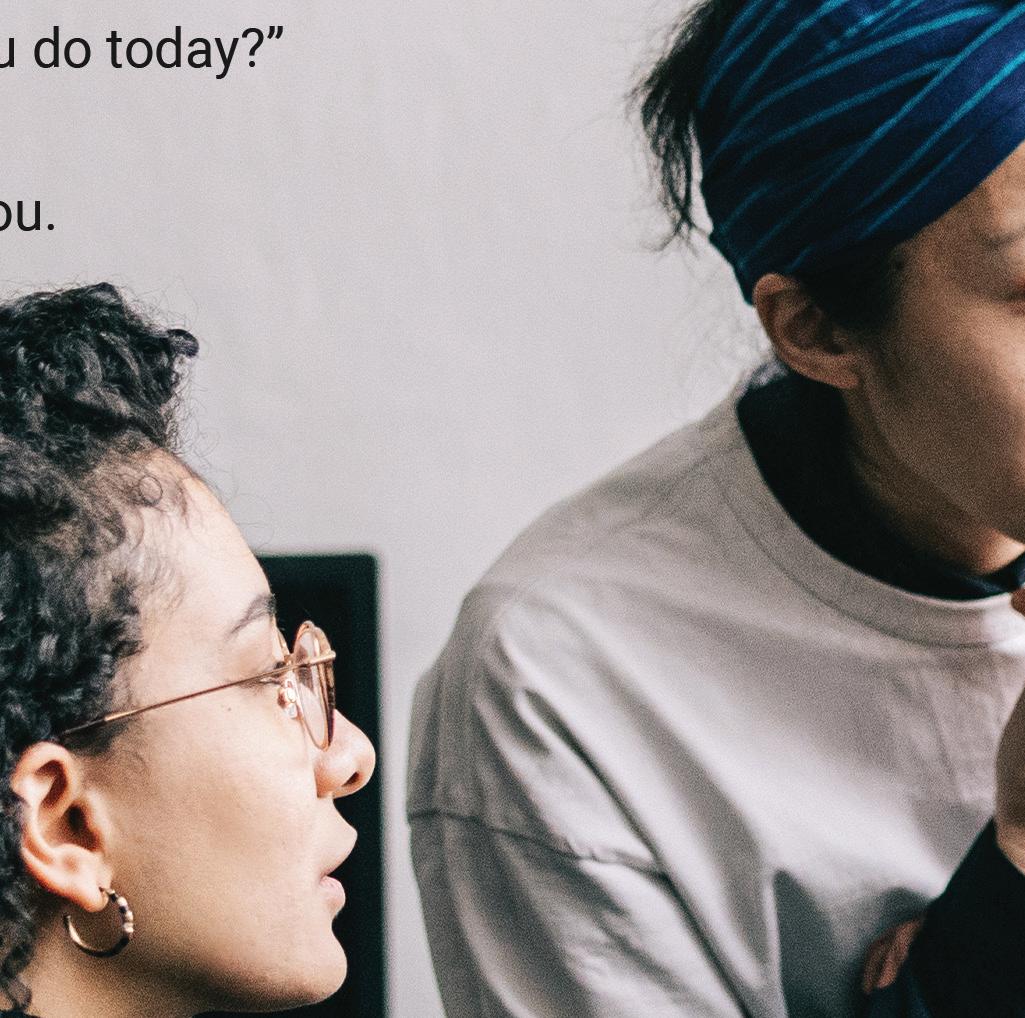
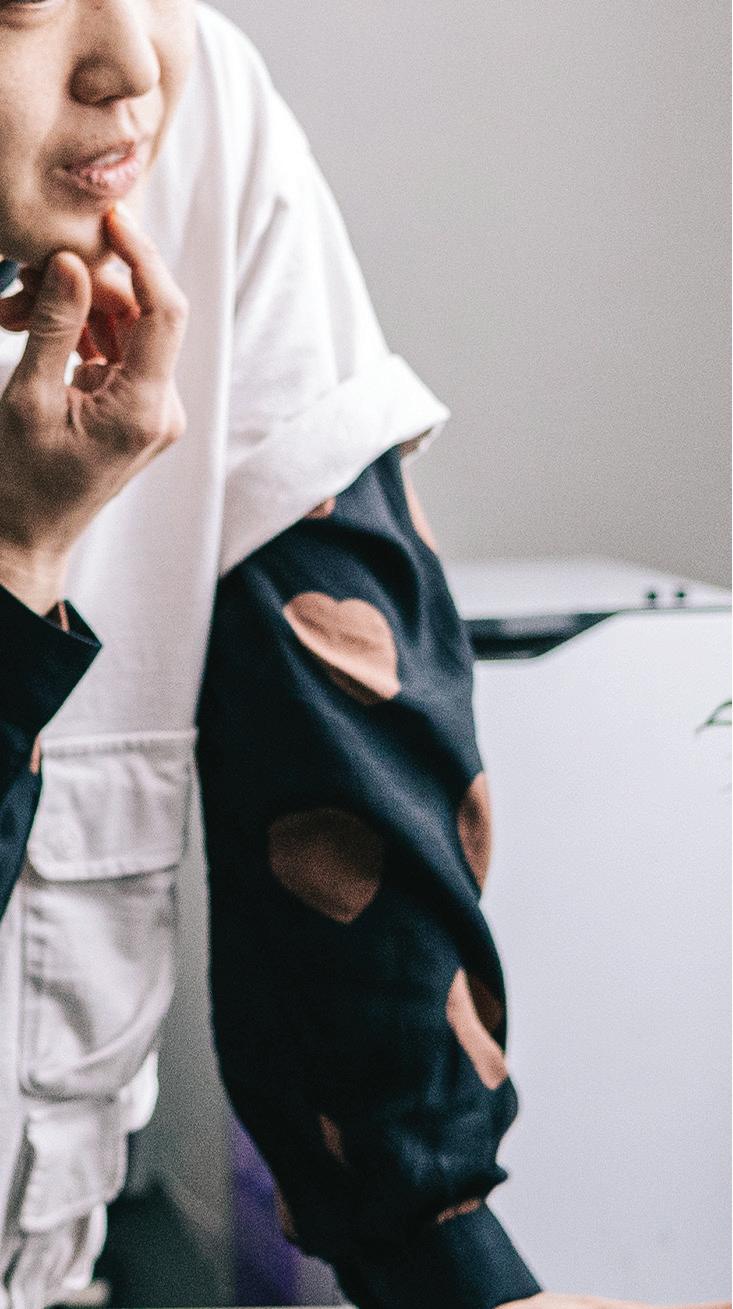
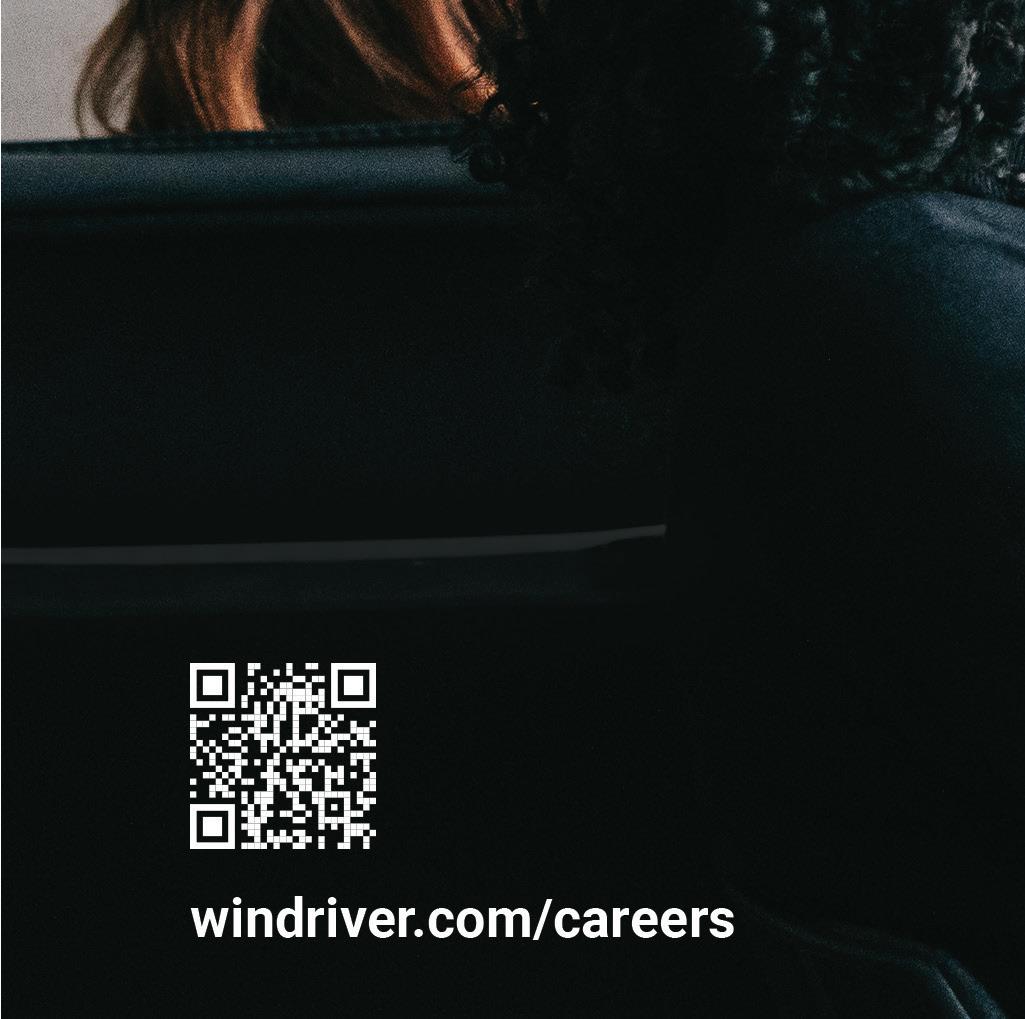

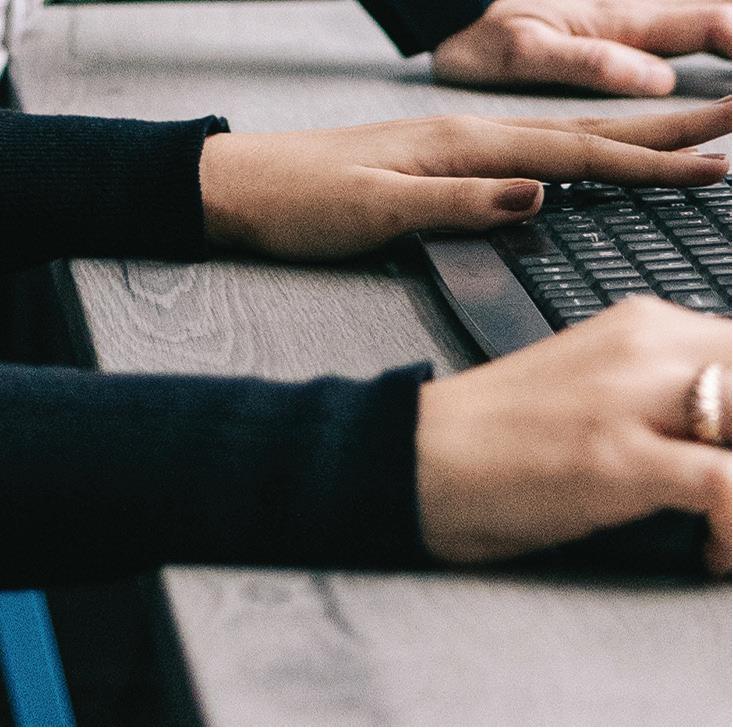

program that we have here has consistently been in the top three in the nation since inception. Industrial Engineering is another popular major for women, number one for over two decades. Environmental Engineering is in the top three, and then Chemical Engineering is in the top five.”
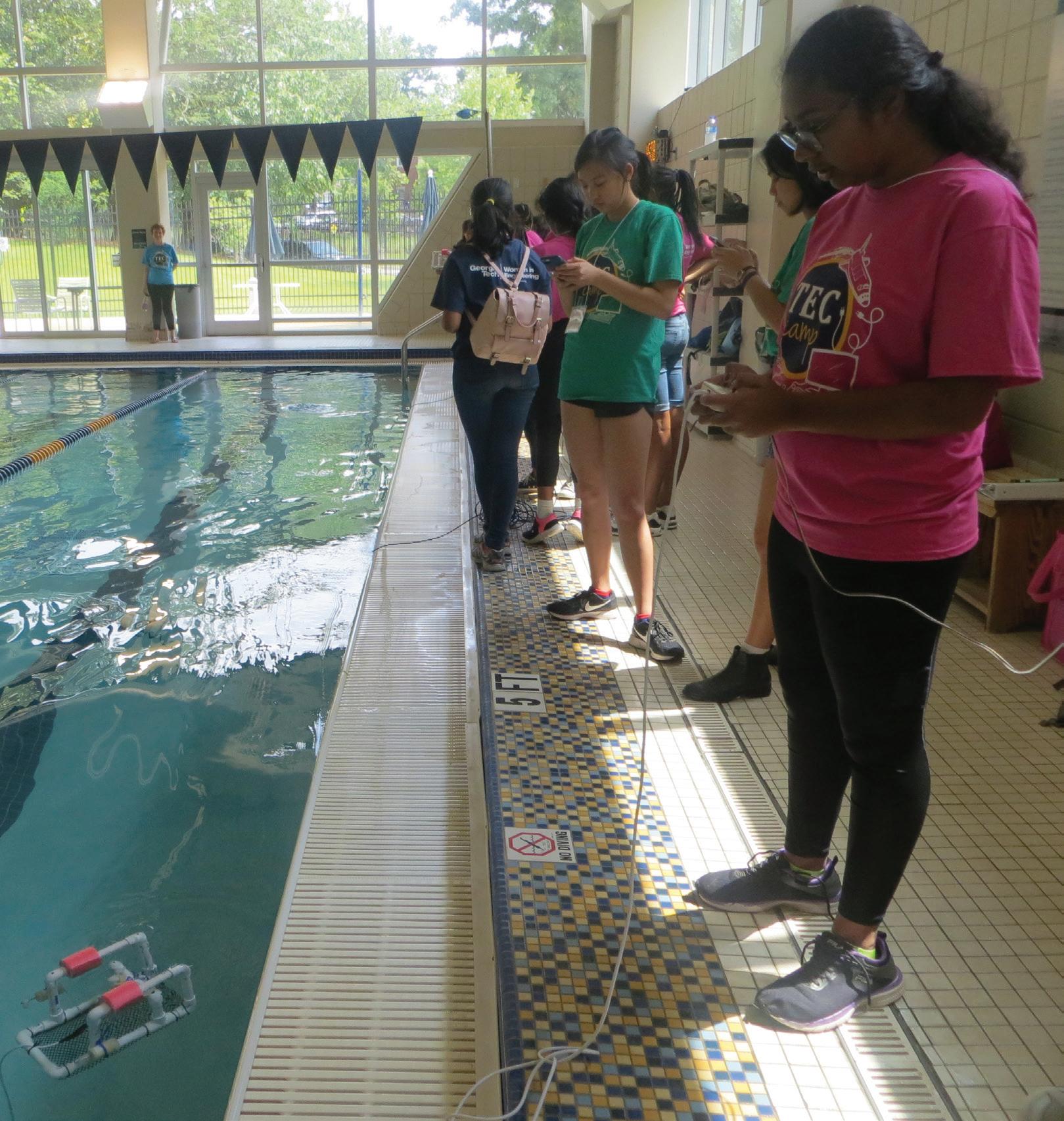
“In general, women seem to be more socialized to help others, so fields like bio-med and environmental engineering strongly connect with women. Industrial engineering is more systems and business oriented and women also tend to like that. And then finally, chemical engineering, I think chemical engineering is attractive because there’s a lot of ties to chemistry and a lot of women are very
strong or really enjoy chemistry in high school. And then, there’s an environmental aspect to chemistry too.”
Challenges in the corporate world
In some cases, gaining the engineering education is the easy part for women. Feeling as though you matter and contribute to various corporate goals can be a challenge. For various reasons, a number of women leave the corporate world after a couple of years. Georgia sees several reasons for this situation.
“I think a lot of this has to do with the individual’s position and the group that she might be in at the company. If you start out as a young woman and don’t see a whole lot of other women around you, that can be very isolating and alienating,” she said. “Another aspect is if women don’t see sufficient opportunities they will leave. Women must also deal with being the dominant care giver to children and spouses, which can force women to take a backseat.”
“Some women, however, will say, ‘I don’t care. I’m just going to power through,’ and they will stick with it. Or they just really, really deeply love the industry or they find some other reason to stay. I’m thinking in particular of one alumna who works in an extremely male dominated field — a railroad company. But she said what she loves about it is that it’s a union job. Her benefits are exceptional and her husband has a medical condition that makes it difficult. So, she sticks it out and she has found ways to make the job interesting and worthwhile for her and her family. Engineering is still very male dominated, and not changing anywhere near as fast as I’d like.”
Being heard
The corporate world can be a challenge for a large number of women engineers. Georgia notes
that such experiences are prevalent in industry and it can also be a common experience at the student level in college.
“What I have found, and research concurs,” she said, “is that anytime you are in a group where you stand out in some way, it could be your gender, it could be your race, it could be the fact that you’re a foreigner and everybody else is native born, it could be your sexual orientation, whatever it may be; if there’s less than 30% like you within the group, you will feel self-conscious. Depending on your personality, you may feel intimidated and taken less seriously than the majority group. And so, 30% is defined at this critical mass where the people with the different characteristic will feel less able to speak up and to be treated the same way as the majority group.”
“If you look at majors like biomedical engineering or chemical engineering, pretty much over 50% or very close to 50% of the students are female. Very few of the students in those classes report not being taken seriously. Whereas if you look at mechanical engineering, I will fairly often hear from female students saying, ‘In my design classes where I’m working in
a group, the groups are assigned by the professors so I don’t have a say in who my teammates are. If I’m in a group with mostly men — guess what, I’m the secretary, I’m the one who writes the report because women are good at writing, right?’ So, it’s hard to be taken seriously.”
“We at the university are very aware of that. And we have mentoring programs within the major in place. We host seminars where we try to teach women skills on how to tackle this. But again, it’s very situation dependent. Such experiences do not apply to every single woman. Although I will say once they are out in the working world, and especially as they rise up in rank, the likelihood that they’re going to encounter a situation like that goes up the higher up you go, just because most of the working world, engineering or not, is still male dominated. This will be a problem that at some point they’re going to have to tackle.”
“We try to let them know that if they’re suffering from lack of selfconfidence and impostor syndrome, all those kinds of things that have been documented for groups that have characteristics that make them minorities within the overall male, white engineering field, first
of all, you are not alone. Second, there are strategies, and third, you get better. I think with those three aspects, it will help. It helps if women get out of their own isolation. It can really distort the picture for you in a number of ways and you realize you’re nowhere near as bad as it seems.”
Full STEM ahead Georgia, in her capacity as director, spends at least half of her time doing K-12 outreach. Georgia Tech has hosted summer camps for elementary school girls and middle school girls. Plus, the institute offers one-day visits for high school female engineering students, giving them an opportunity to talk to faculty and students in the college of engineering about the different majors and how to apply and what exactly is engineering and all of that.
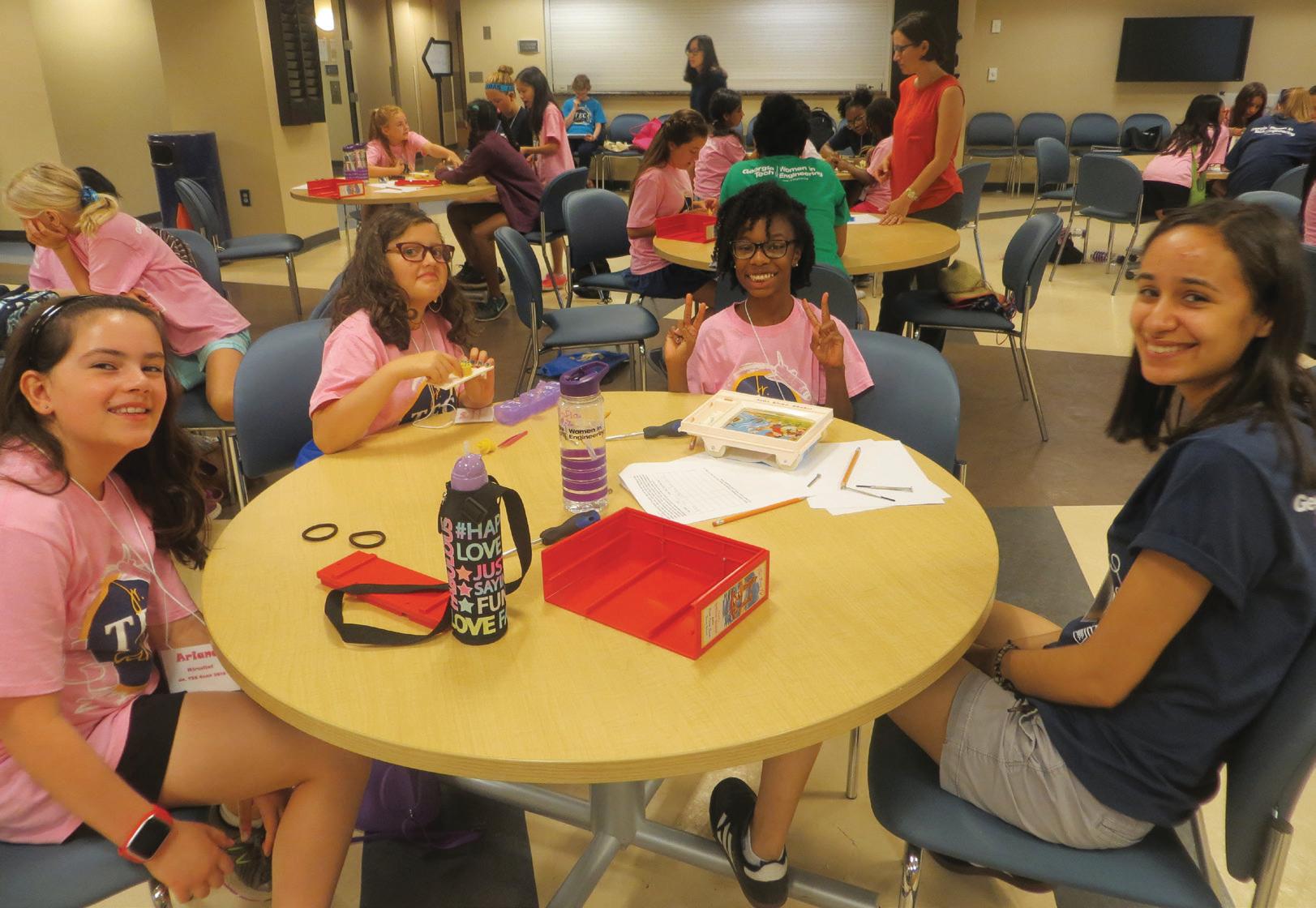
In addition, Georgia Tech has a program to reach out to local schools to reach groups of potential students not strongly represented in engineering fields.
“And we partner with school teachers and principals to go into the classroom and talk to the kids about engineering — and sometimes we do hands-on activities with the kids. We really like that because
we’re in the heart of Atlanta,” she continued. “There’s so much demand even within the city of Atlanta and even more in the state of Georgia in terms of exposing young kids, men and women for that matter, to engineering and not every kid will be able to come to campus. It’s good when we can go out to the schools.”
Engineering not well known Georgia has an international perspective on the field of engineering. She finds that in the U.S., the engineering profession is not as well-known as it is in France, where it is tied more to the military than to other markets. In the U.S., engineering initially was tied to the automotive industry, similar to in Germany and Britain. And now in the more than 50 or 60 years since, the skills used in engineering are gaining a strong association with entertainment and other more lucrative fields, such as law.
She finds that many students feel they lack the math skills to go into this profession. She advised, “The number one, number two, number three thing I would say is to not doubt yourself, don’t think that you need to be an absolute perfect 100 average in math and science to be an engineer. What I find first and foremost is that women tend to think that unless they’re absolute rock stars in math and science, they cannot be an engineer. And I just really want to demystify this. It’s not true. Women suffer from a lack of self confidence in those fields, particularly when they’re young, primarily because of isolation, they don’t have enough peers to connect with.”
“If you have the interest and reasonable ability in those fields, go for it. But definitely do not think that every boy who graduates with an engineering degree is a rockstar because I can promise you that’s not the case.”
Georgia mentioned an alumnus who graduated from Georgia Tech and worked at Kimberly Clark. As an extremely successful black man, he often commented about being a terrible student at the university.
“He was completely open about it and he would regularly come on campus and talk about how he barely graduated because his GPA was so low. And part of it was he was having too much fun as a student, but part of it was also he just was not very committed. He liked math and science, but he was not very serious about his homework,” she said. “Women put so much pressure on themselves.
‘My GPA has to be perfect.’ No, no, no, and no. Obviously if you hate math and science with a passion in high school, then it’s not a good field. But if you like it reasonably well and you have good study skills, you can go really, really far.”
“Women should not think that engineering is just engines and cars. It’s an extremely broad field that you can work with. It can be a very people-oriented field. You really can help others, you can travel, you can make good money. It’s really a wonderful, wonderful field and I hope more women that have the interest and aptitude can go into it because there’s a lot of great opportunities in that area.”
“Engineering can be a stepping stone for so many other fields. The foundation of every engineering field is problem solving skills. So many employers look for people with problem solving skills, including law, medicine, and others.”
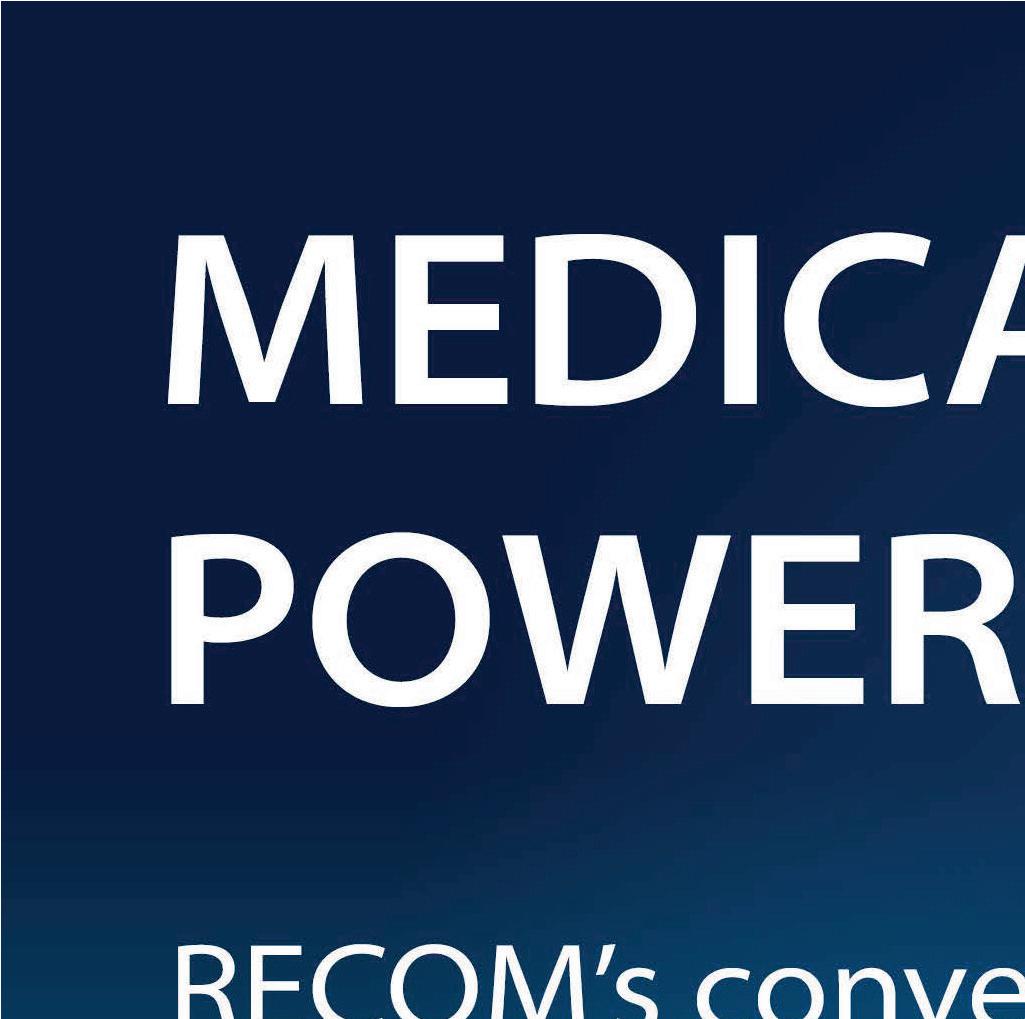

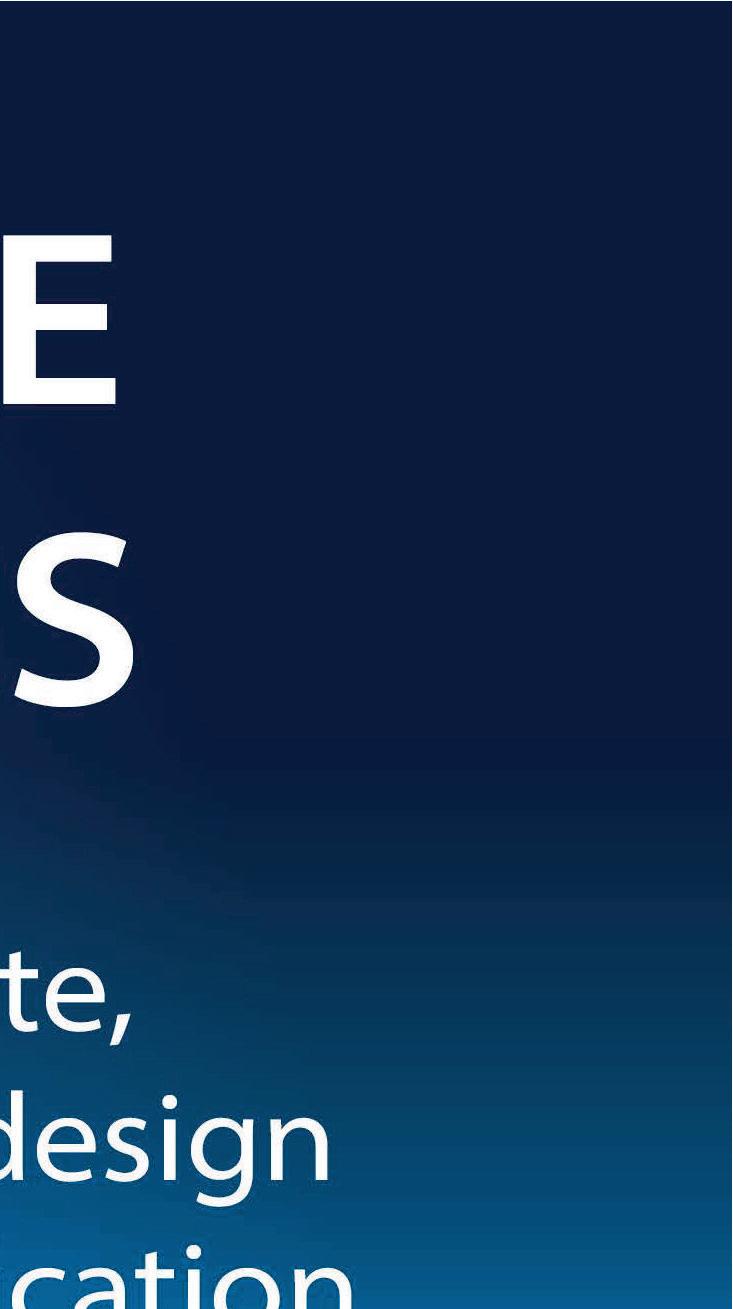
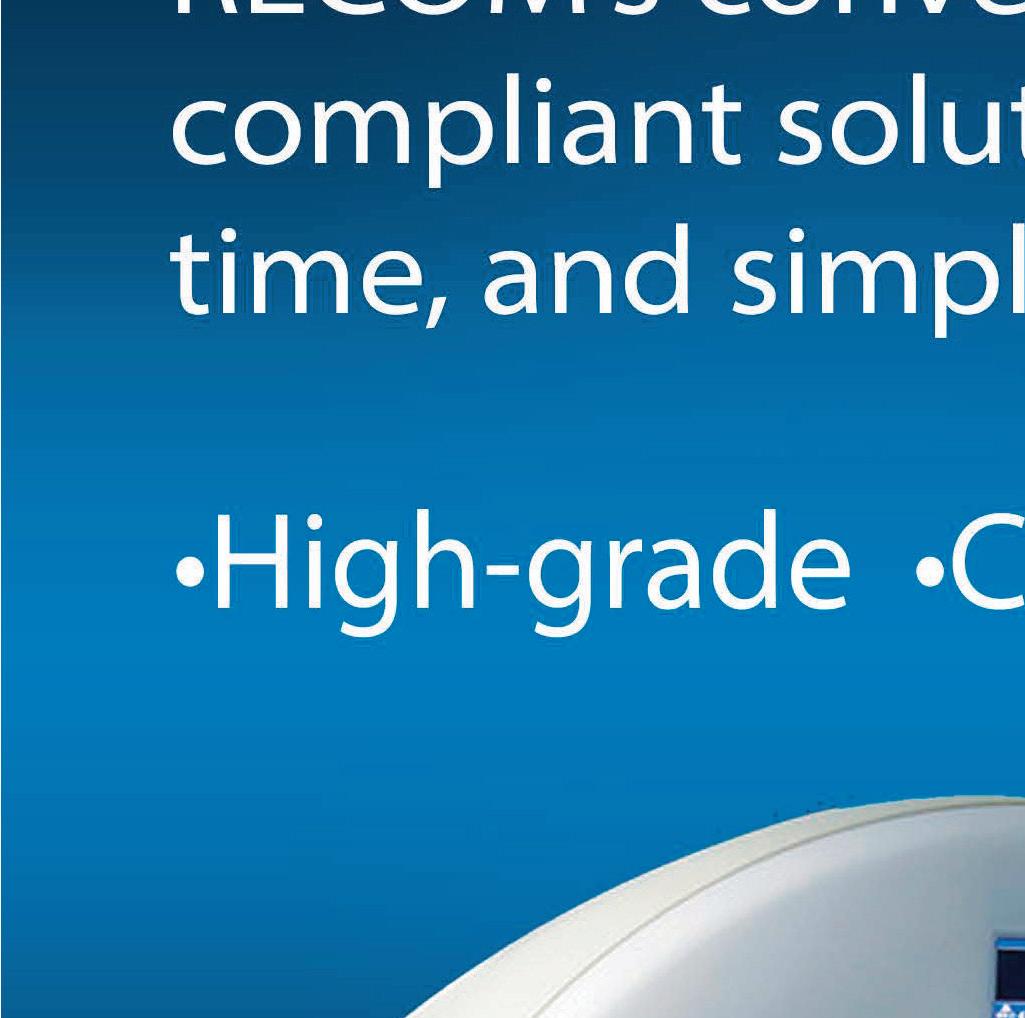
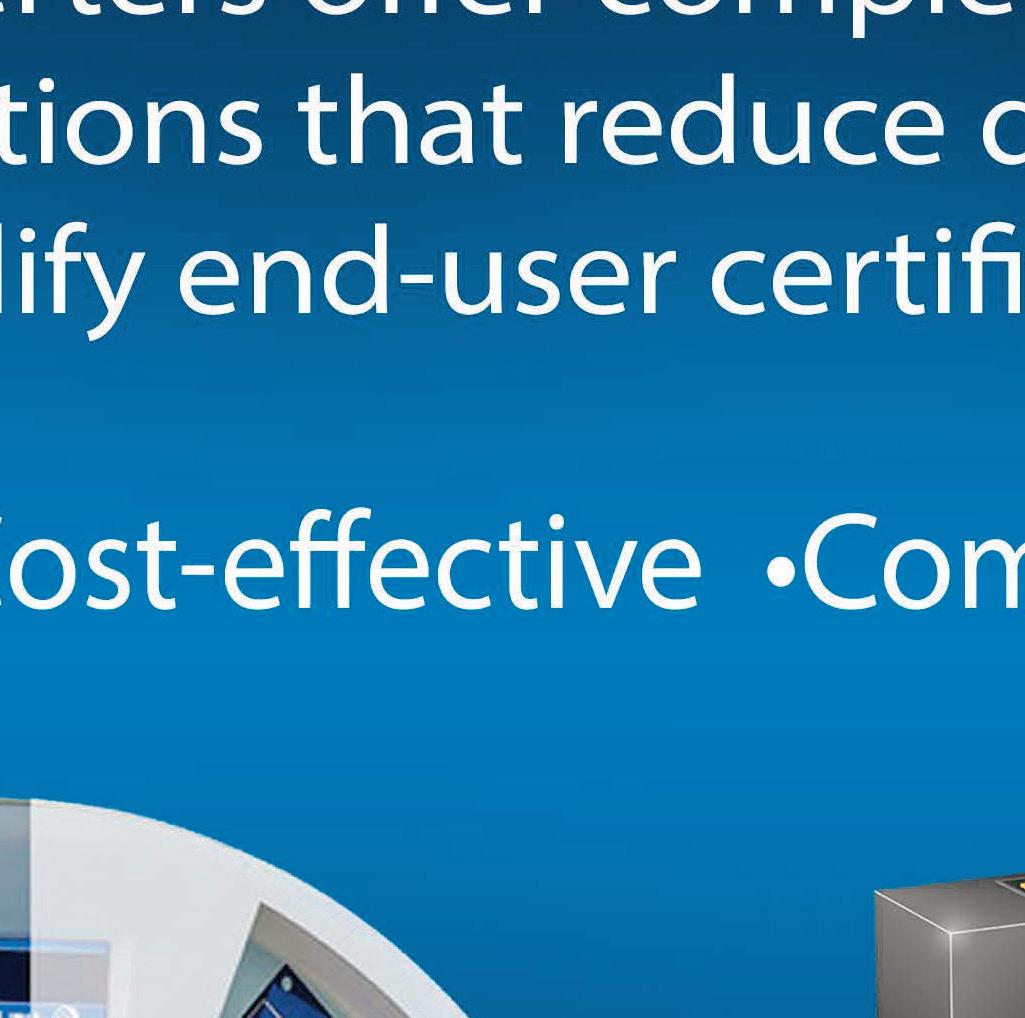
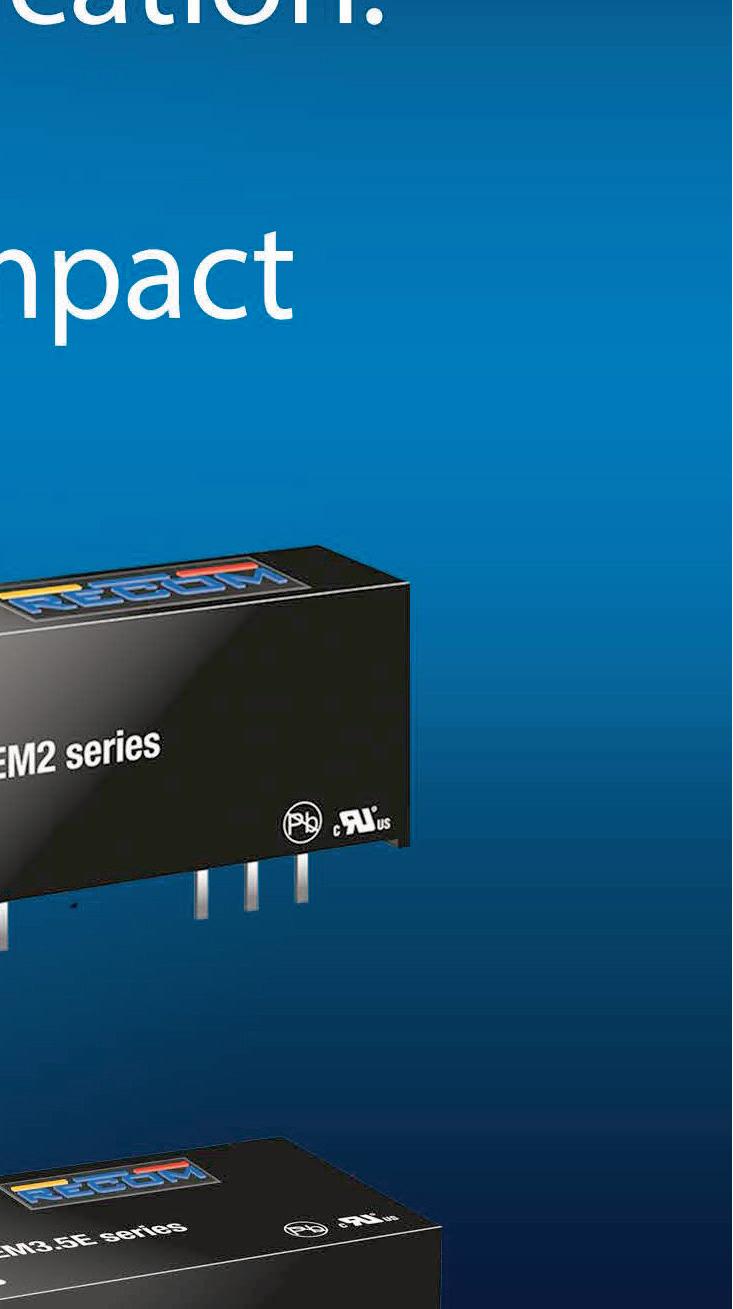
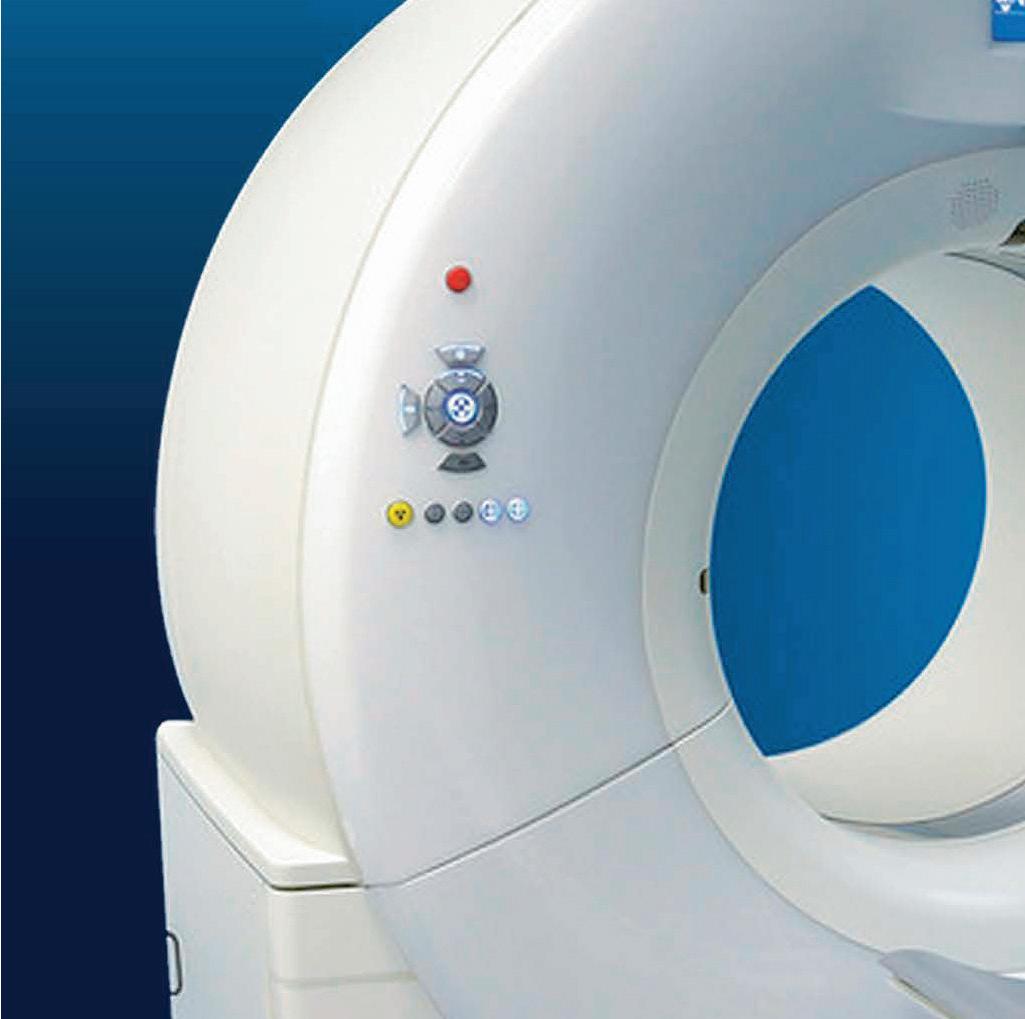
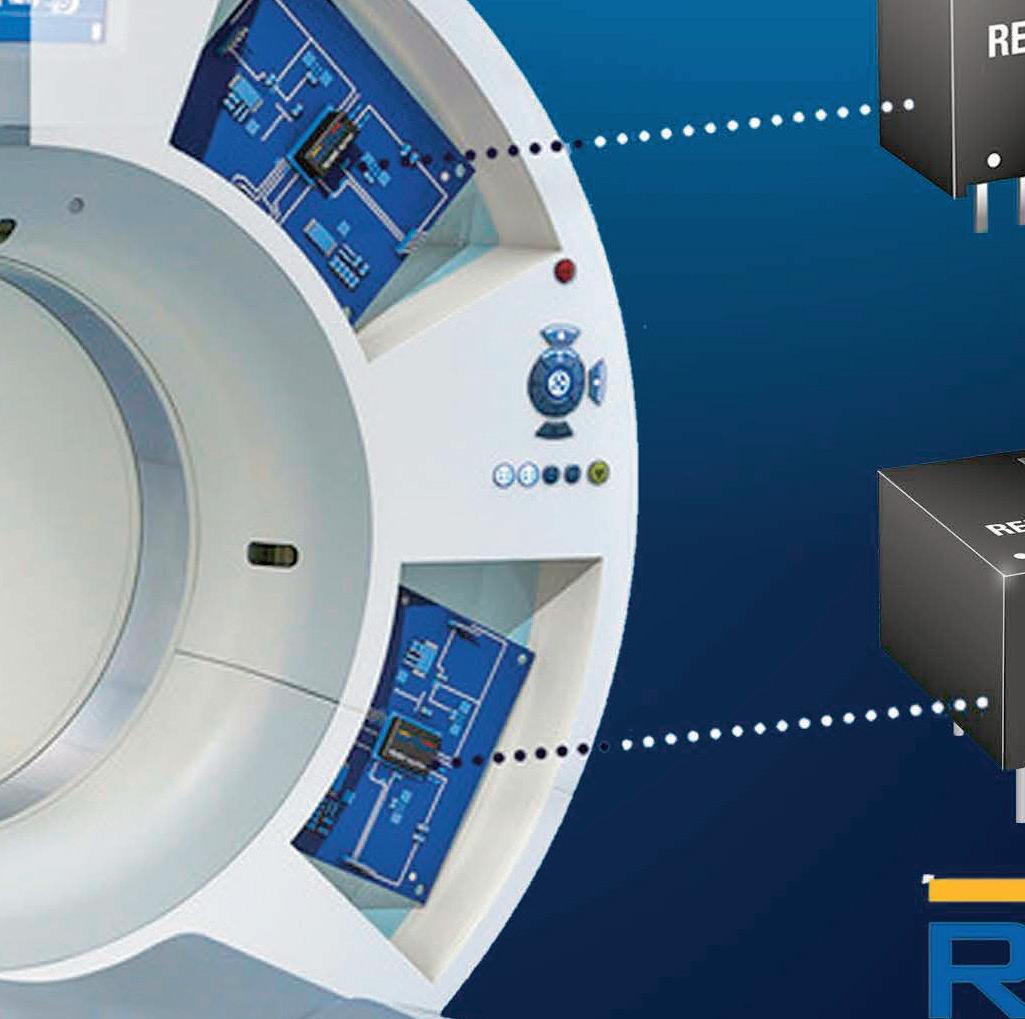
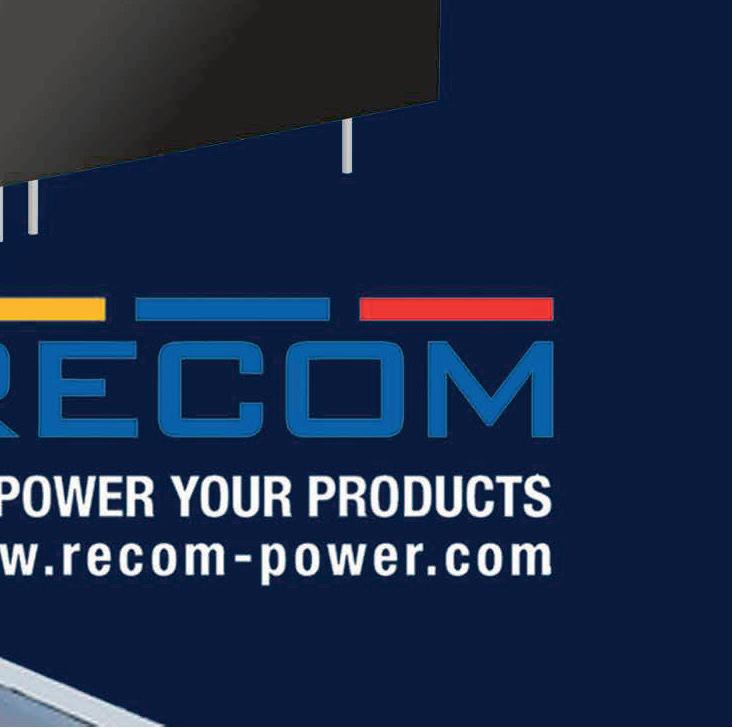

Engineering a life of purpose
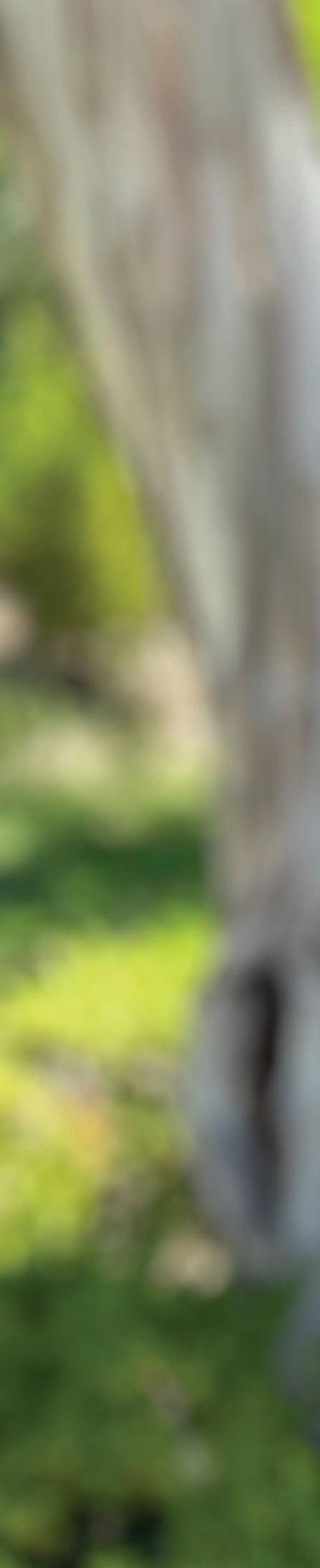
asmine Jauregui has always found that understanding the ‘how’ or ‘why’ of a process is one of the more rewarding aspects of engineering. Like other engineers, she is always curious about how things work and enjoys fixing or improving upon some process or design.
Jauregui was strong in STEM subjects growing up, and this led her to pursue engineering. “I was always encouraged and supported to follow these interests in school and by my family, and that support accelerated my enthusiasm for the field,” she says.Jauregui was a first-generation college student, so her early exposure to engineering was not extensive. “Selecting a major was a new experience for me and my family, but I never felt limited in my choices,” she says. “From what I knew at the time, engineering was a challenging career path, but I had a lot of support to pursue it. Both my mom and dad reached out to neighbors and colleagues that were engineers to talk with me and answer questions I had about the different engineering fields. These conversations gave me confidence and really got me excited to go down the engineering route.”
Problem and solution
As engineers tend to be inherent problem solvers, that characteristic is one of the reasons they go into this field. “Given a problem that needs a resolution, there’s a lot of challenges and creativity that come with that,” Jauregui notes. “The variety of systems involved in engineering also means that I’m constantly learning and growing as an individual.”
Jasmine
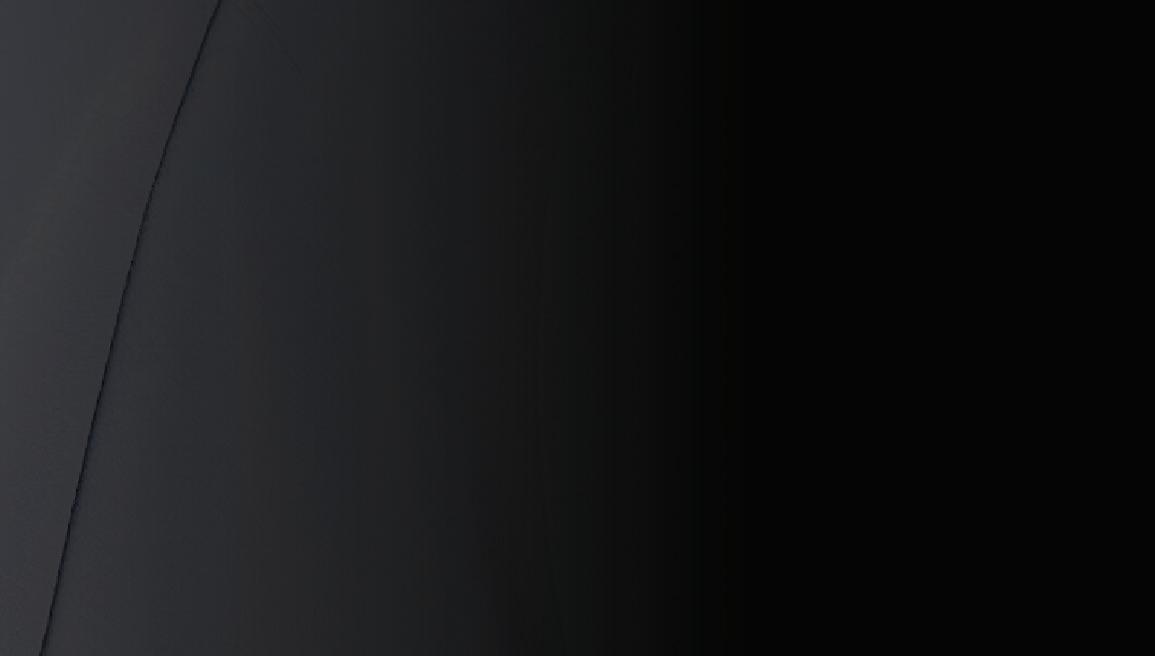
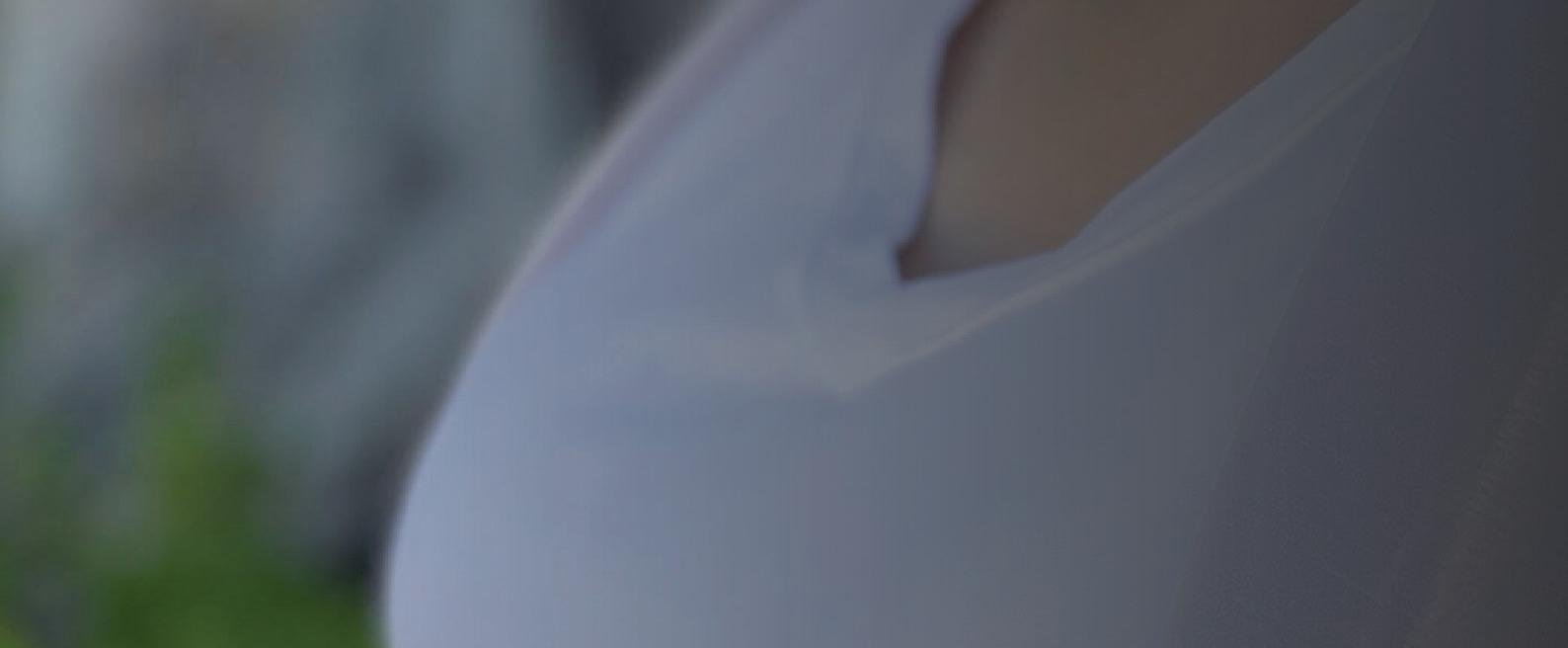
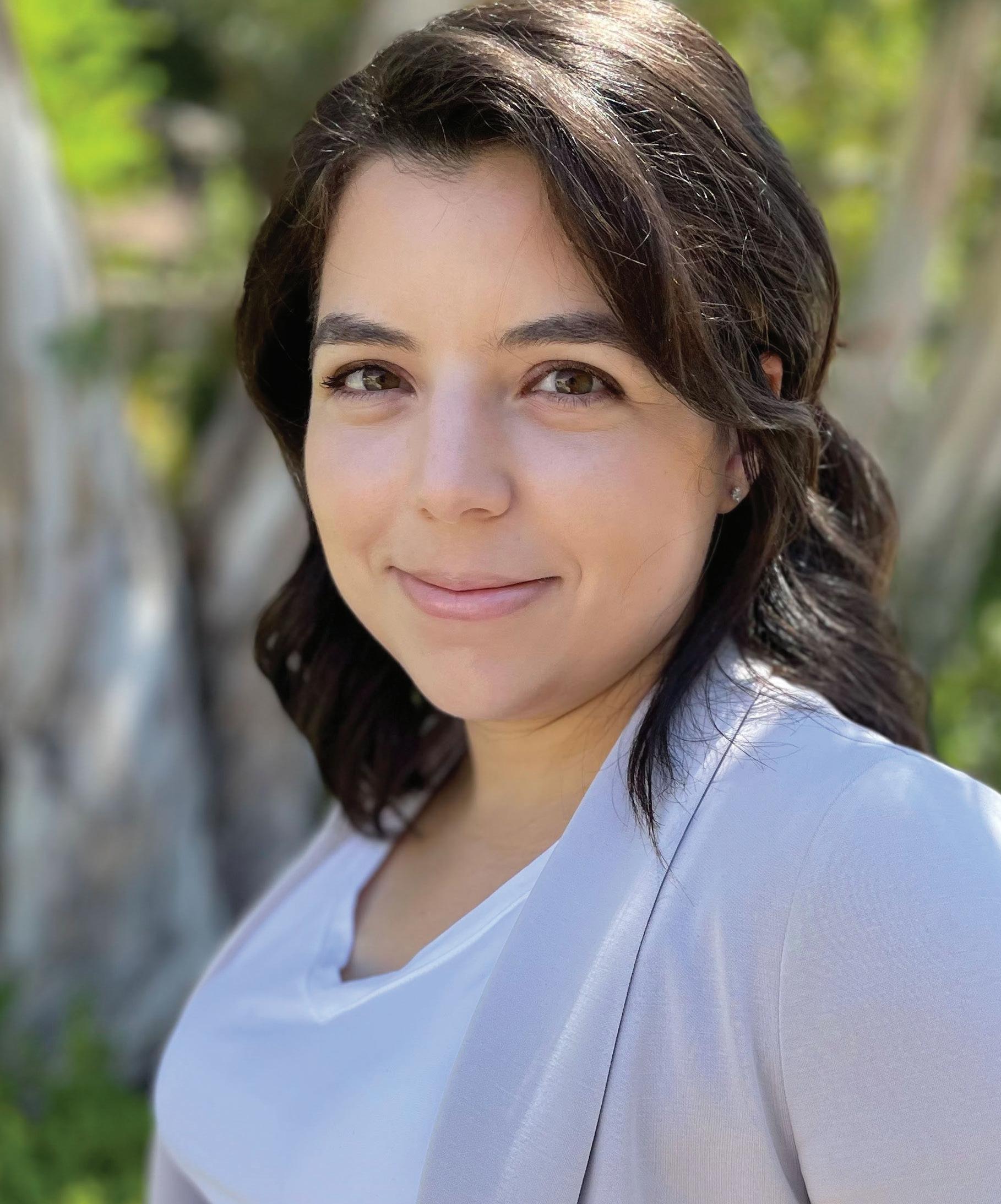
She enjoys problems that require reverse engineering or initial investigations to determine a baseline for moving forward.
“I’ve always enjoyed puzzles and organizing, and problems that require you to reverse engineer what you’re starting with include both of these tasks. Throughout this process, you end up becoming a subject matter expert in the system before moving forward and that depth of knowledge can give you a lot of confidence in the solution you’re proposing and project risks you’re tracking and mitigating. That’s always a good spot to be in when working on a project.”
Jauregui works with a variety of systems and stakeholders, giving her an opportunity to make a significant impact. “With all of this comes a responsibility to our stakeholders (end-users, operations, business units) and this drives a huge sense of purpose for the effort I put into my work,” she adds. “My Loyola Marymount University class motto, a quote by Robert Byrne, was ‘The purpose of life is a life of purpose,’ and this really resonates with me and why I’m in this field.”
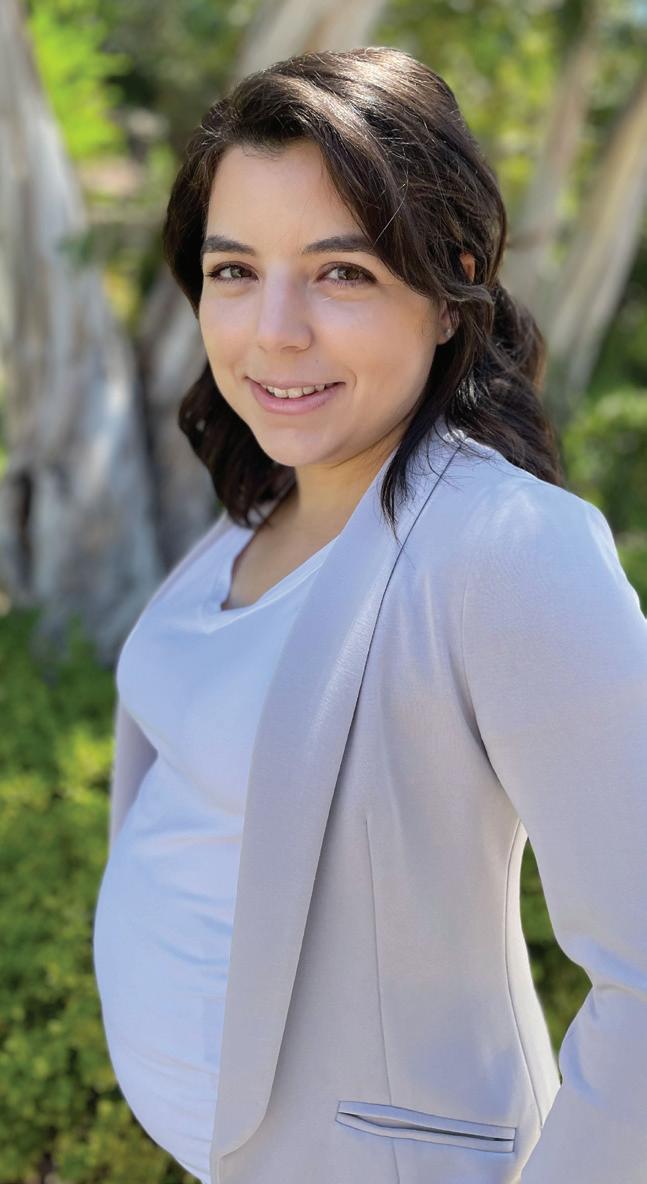
One of Jauregui’s more notable accomplishments involved control system integration. She led this integration project for a water treatment facility that involved adding a new influent source. “It was the first integration project I ran as a technical lead - breaking down the scope into technical tasks, leading other engineers in its execution, testing, and deployment,” she says.
The scope of the project involved coordination, planning, and preparation to ensure her team was prepared to execute the work according to schedule in coordination with construction and operations on site.
“Though it was a new challenge for me, it was well planned, and we were able to deliver on the quality and scope for our client,” she adds.
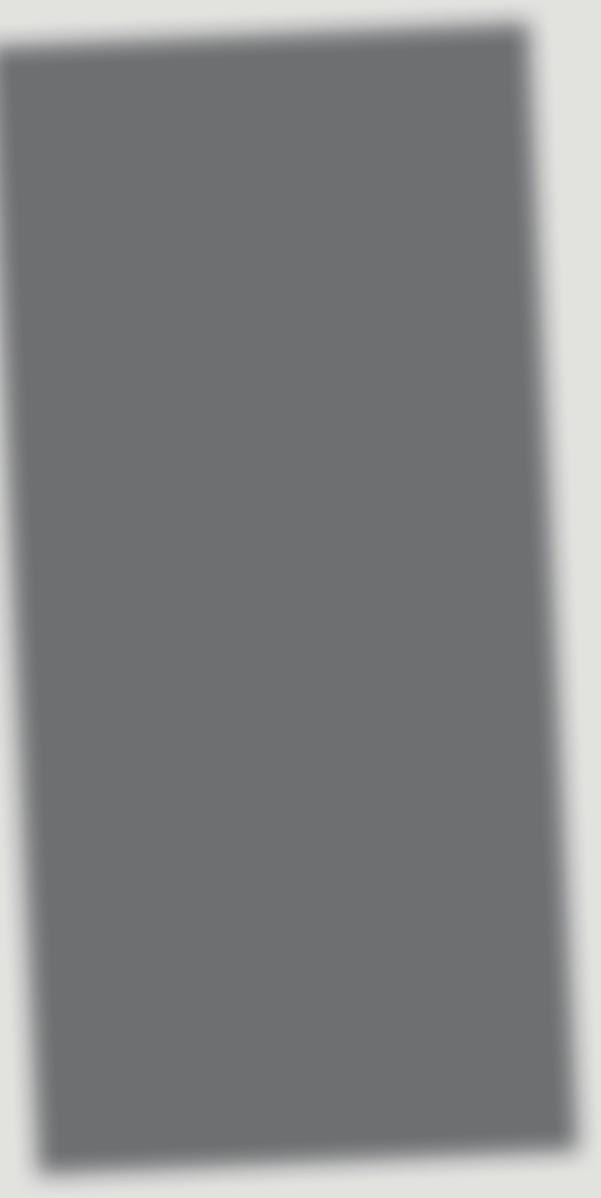
“It was definitely one of those ‘reap what you sow’ experiences that gave me confidence for bigger challenges to come.”
Dealing with a pandemic
One of the challenges for everyone over the past couple of years has been coping with the unknown brought on by the COVID pandemic. Jauregui says that a large part of her team’s success has always been the solid communication and collaboration they have internally as well as externally with clients.
“To deliver on client needs, we tend to become an extension to their staff in understanding their operations for the benefit of the deliverables we provide,” she notes.
“During the pandemic, everyone experienced various forms of isolation and disconnectedness so you can imagine how that affected our team’s workflow. In transitioning to remote work, we made extra efforts to stay connected - every internal and external call became a video call, client visits continued where possible, team activities (such as trivia nights) outside of work continued virtually. I often provided feedback to the company and management on how remote work was going, what was working, what could be better. It’s one of those things where if you’re feeling something is off, chances are you’re not the only one. I enjoy the team I have the privilege to work with and so I’m sensitive to the climate of how things are going with us as a team and the services we provide to our clients. I think this drove some of the efforts to maintain the workflow normalcy we had before the pandemic and routinely provided feedback for improvement along the way.”
While the pandemic was a challenge, an even bigger challenge for Jauregui involved replacing a SCADA system. The system had obsolete SCADA software, so the challenge was to deliver a product
“It’s important to be available to our next generation of engineers to help them recognize opportunities to get involved, ways they can lean into their strengths, and work on areas for improvement,” she notes. “Many times, through mentorship, I have been enlightened as to my true potential to succeed and grow as an engineer and leader.”
— Jasmine Jauregui
All-in-one servo drive and motor The
compact AMI812x servo drive
One connection level covers all interfaces: directly on the servo drive without requiring upstream I/O
The AMI812x integrated servo drive: integrated servo drive for compact drive technology (up to 48 V DC) combines highly compact servomotor, output stage and fieldbus connection for all motion requirements in the power range up to 400 watts for single axes or with daisy-chain solutions on the machine supports machine concepts without control cabinets
IP65 protection degree possible with sealing ring option
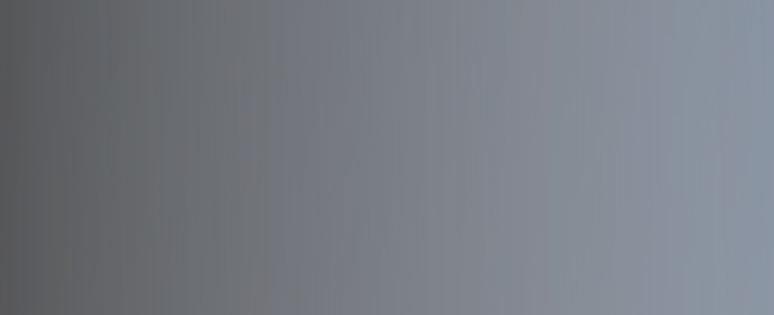
Safe torque off (STO) safety over FSoE (Safety over EtherCAT) reduces installation and integrates seamlessly into safety solutions
Beckhoff offers a complete, compact control solution including a range of compact motion technologies for servo, stepper, DC motors and more Scan to experience the benefits of compact integrated servo drives
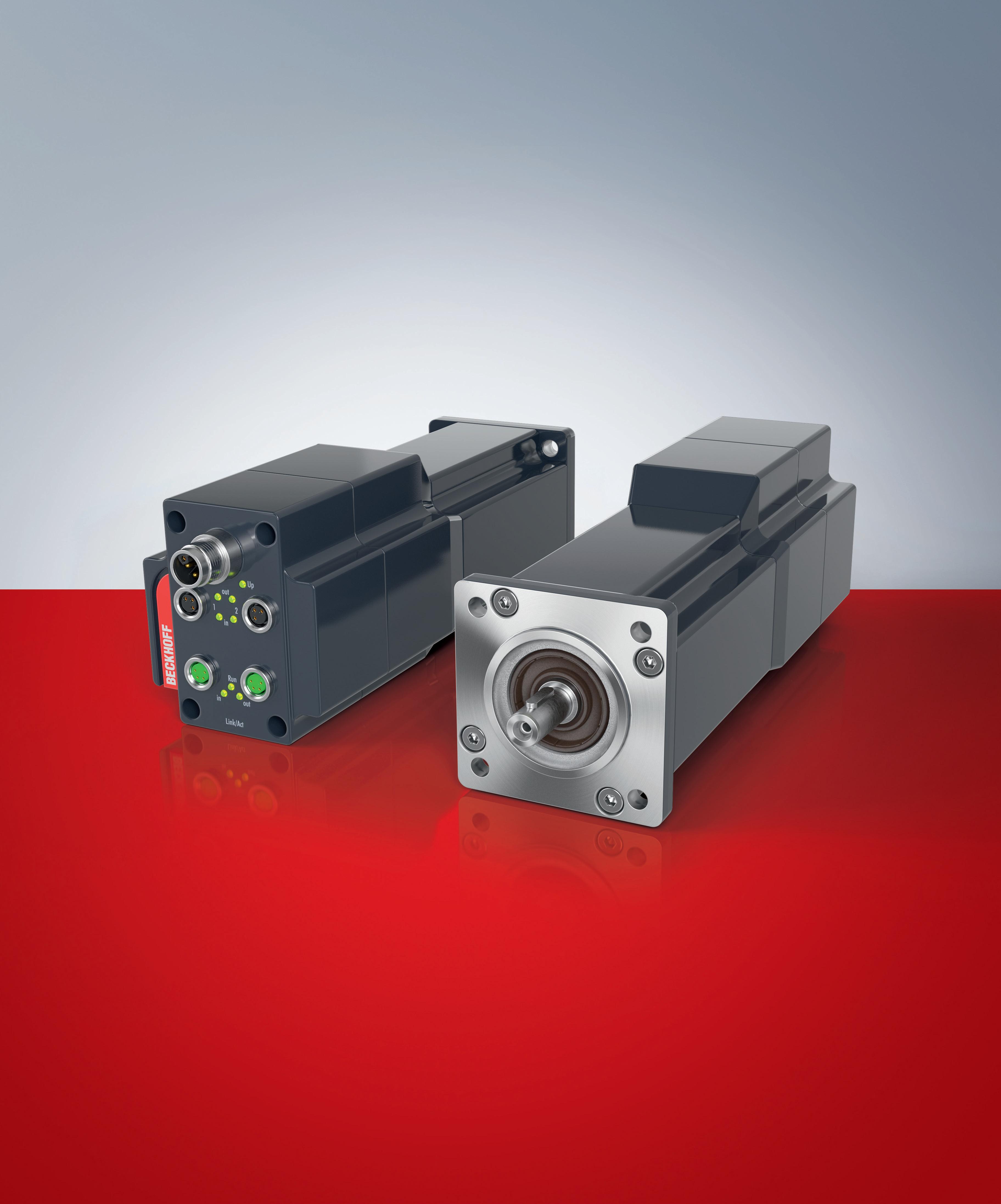
There’s sometimes a narrow perception of what a typical engineer is like - technical communicator, running analytics, risk adverse. In reality, an engineer is someone that can define a problem, identify the facts, make reasonable assumptions, and oftentimes be able to communicate to multiple parties.
that demonstrated consistent standardization and predictability in behavior for operations, short of implementing a completely new control system. Jauregui did extensive investigation and documentation of the existing system.
“With such a large task,” she says, “being methodical, detiled, and capturing potential risks and unknowns along the way helped us have a solid design for moving forward with the replacement. We delivered on the goals for operations without a total overhaul of their system, maximizing the value of their SCADA asset.”
In another example, Jauregui was involved in a PLC conversion project that required taking a given controller and automatically converting it to a newer software version. One of the risks of this conversion was the possibility that some of the programming would change during the automatic conversion process, resulting in the system behaving differently.
To mitigate this risk, she and her team developed a way to compare aspects of the code prior to and after the conversion process. They developed a program that would use text exports of the two projects, extract key aspects of the code, and then compare for differences.
“To validate the program, I developed documentation that defined the specifications for the goals of the program, definitions for various aspects of the exports, and test documentation. It not only provided us a quick means to validate our project work, but the documentation has lived on so it could be leveraged again by other project teams for similar projects,” she adds.
Developing leadership skills
Many women engineers find a large portion of their job involves leading a team. Such assignments provide
opportunities to gain a range of skills in leadership over their careers.
“My engineering work is very much team based,” says Jauregui, “and involves working directly with clients to provide them with comprehensive solutions. In the teams I lead, success for the team is stemming from success of the individuals. Leading by example, as well as coaching and providing feedback, have become instrumental to how I lead my teams.
It’s important for me to enable those around me and being in the engineering field with the projects I’m involved with has helped me develop these skills.
“In my current role as Engineering Manager, having this technical background has given me the insight to understand what kind of support my departments need to succeed. For example, as an engineer, it is always important to me that my manager is accessible, up to date on the work I am doing, and open to conversations regarding my career interests. I am now in a position to be able to provide the same support and leadership for my team’s success.”
Jauregui has learned a number of valuable lessons including managing expectations and fostering employee engagement.
“When I think of times my work has been most rewarding it was because my expectations for tasks, future work, and higher-level decisions were in alignment with the direction the team was headed. I have a lot of trust in my managers and the company when I am not surprised by decisions or events. I have also been really proud of the work I was doing, or most productive on the team when I’ve felt really engaged with my career and the company goals. The satisfaction and autonomy I feel in my role goes a long way. These are two areas I am cognizant of and try to encourage as I work with my team.”
Diversity Drives Innovation
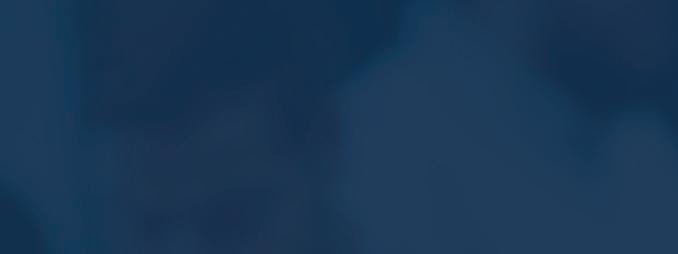
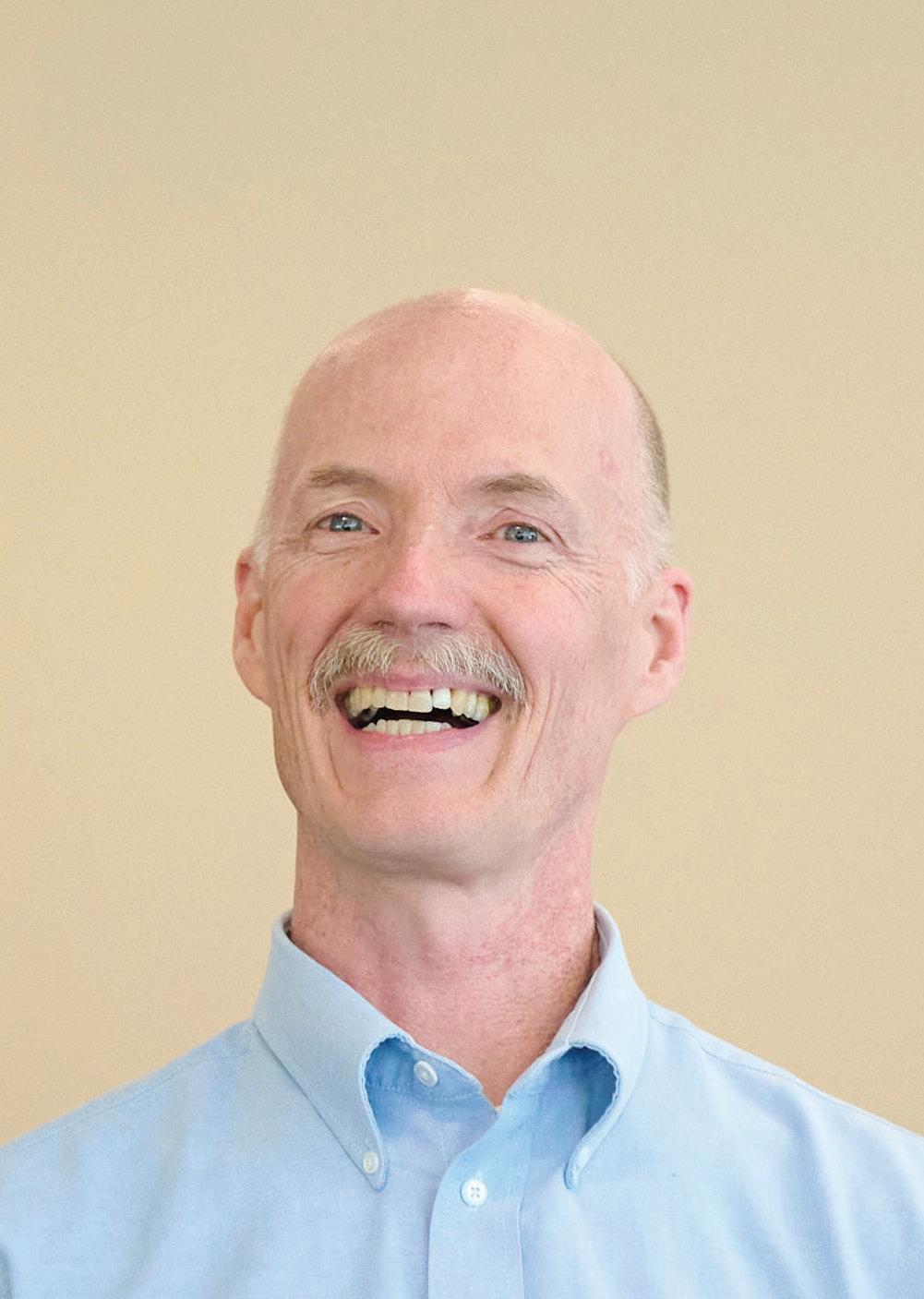
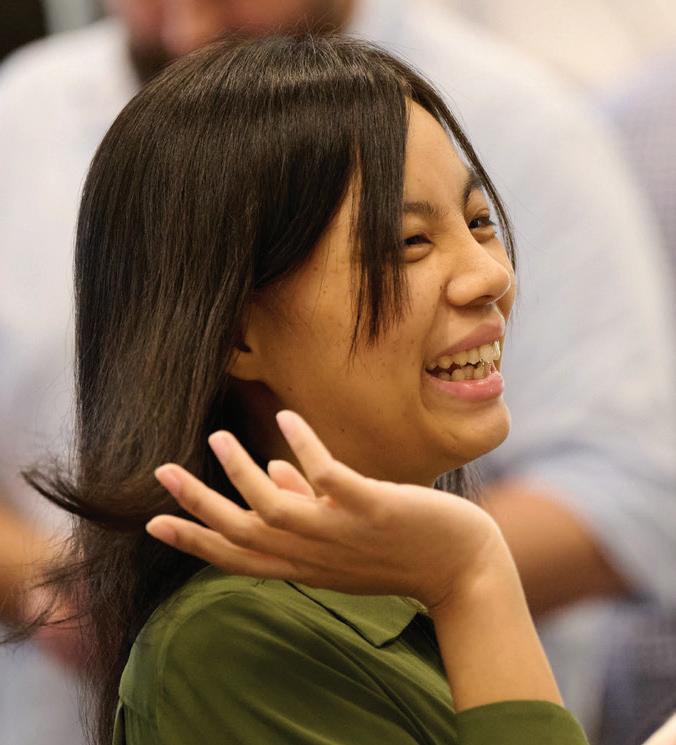
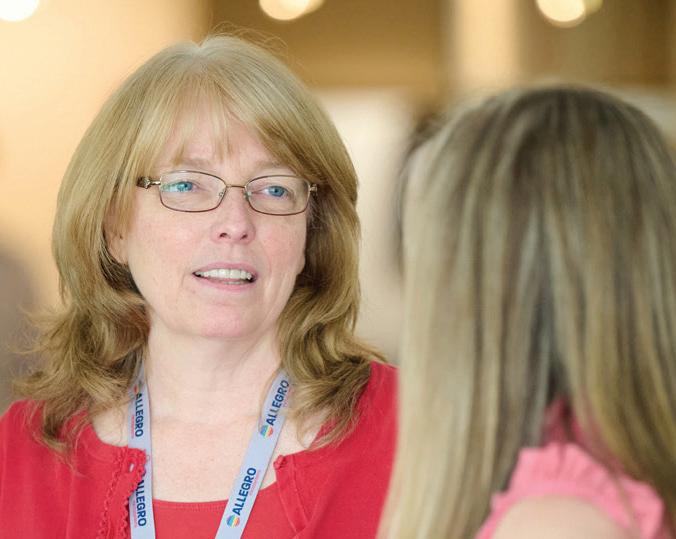

At Allegro, we’re committed to creating an environment that ignites new ideas and empowers everyone to reach their full potential. The diversity of our people, together with their unique ideas and perspectives, drives us to work together toward Allegro’s vision and mission.
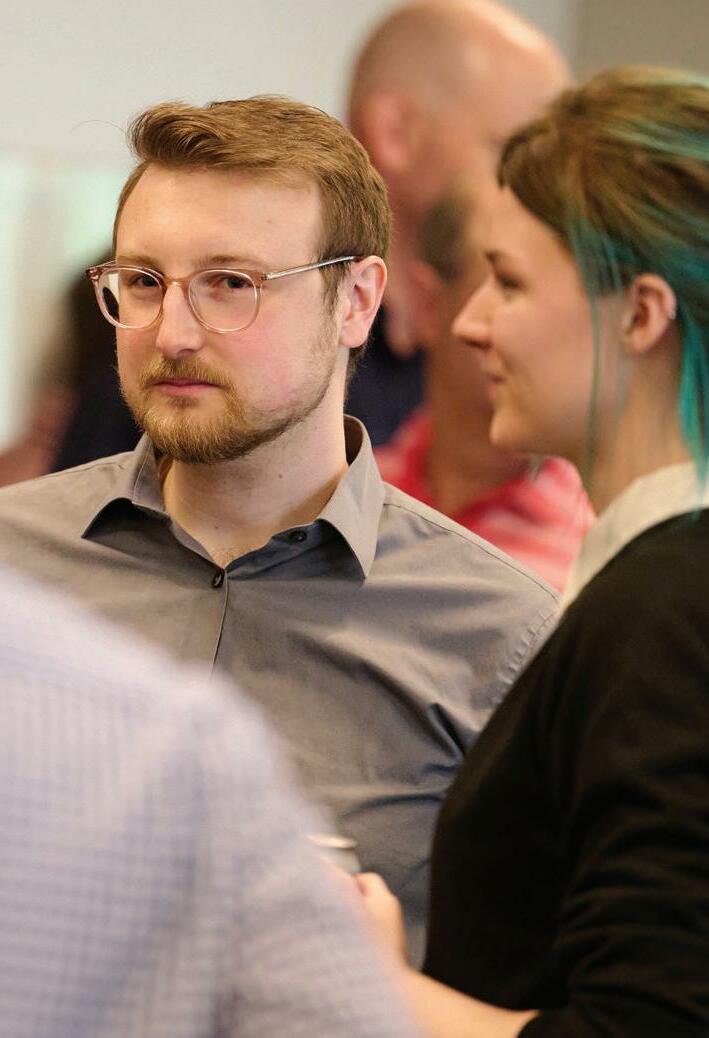

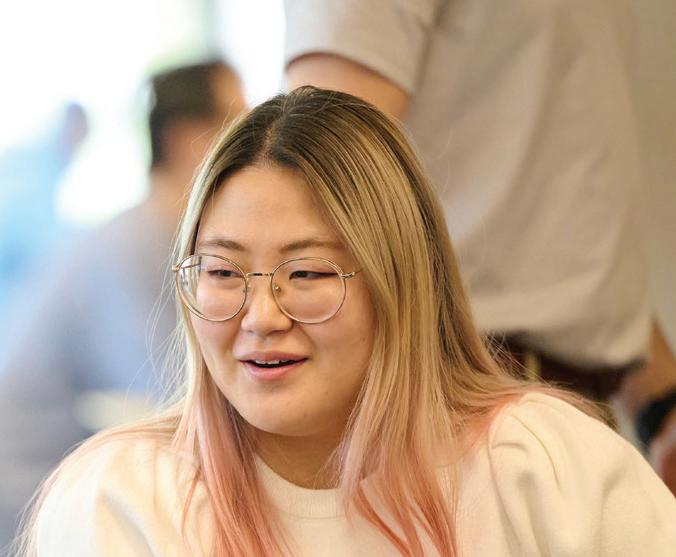
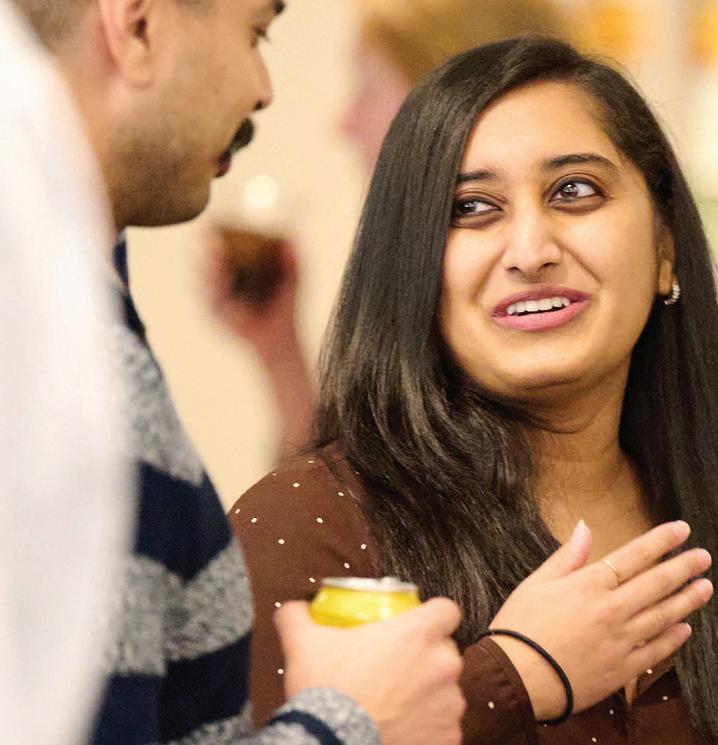
Allegro MicroSystems is redefining the future of power and sensing semiconductor technologies, helping our customers bring breakthrough innovations to life. From clean energy to advanced mobility and motion control systems, Allegro’s intelligent solutions move the world forward and give our customers a competitive edge.
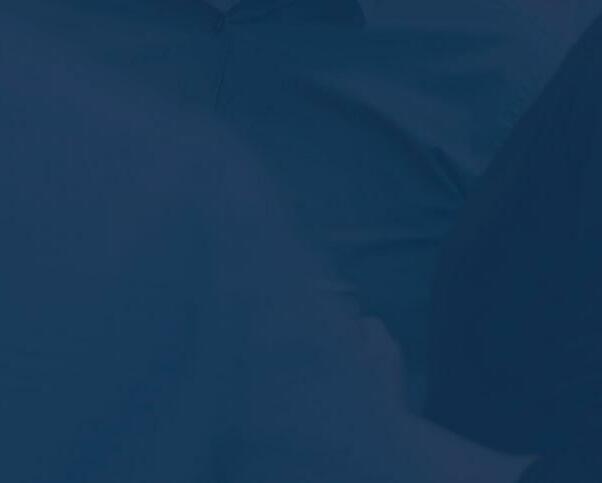
Our global engineering, manufacturing, and support, combined with our agility, make Allegro a trusted partner to both large enterprises and regional market leaders worldwide.
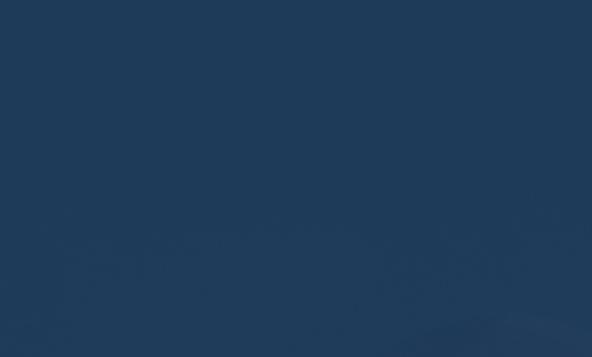
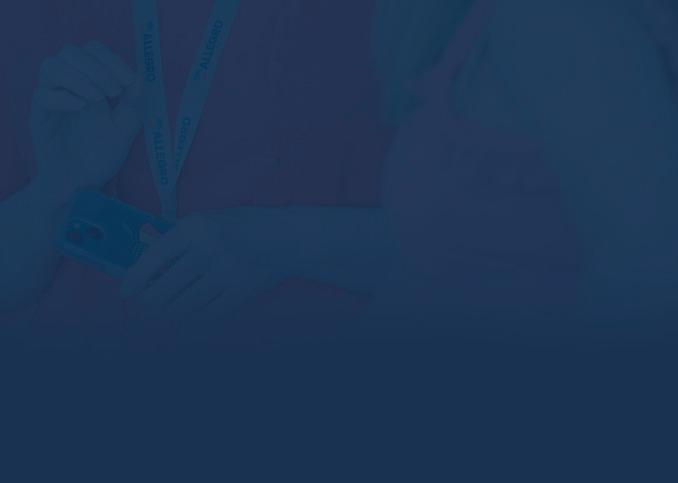
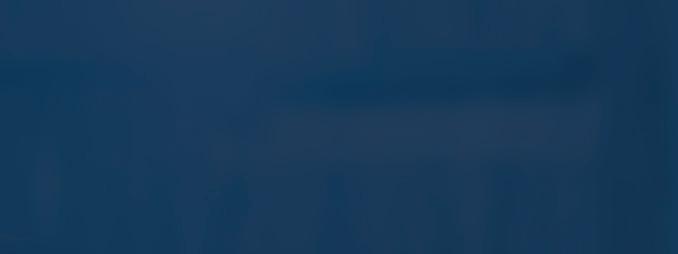
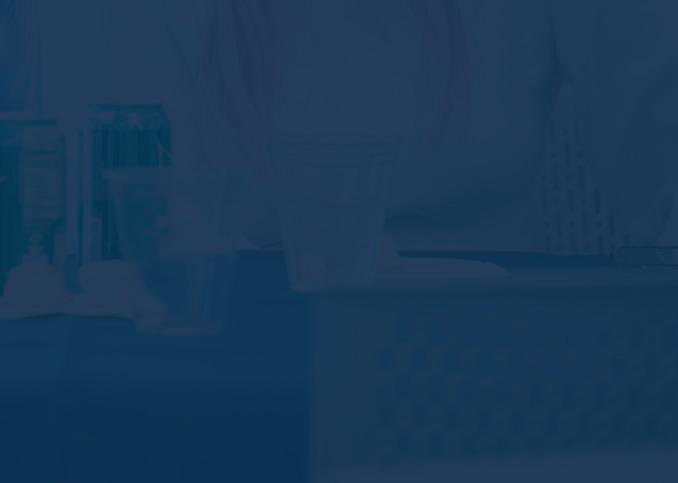

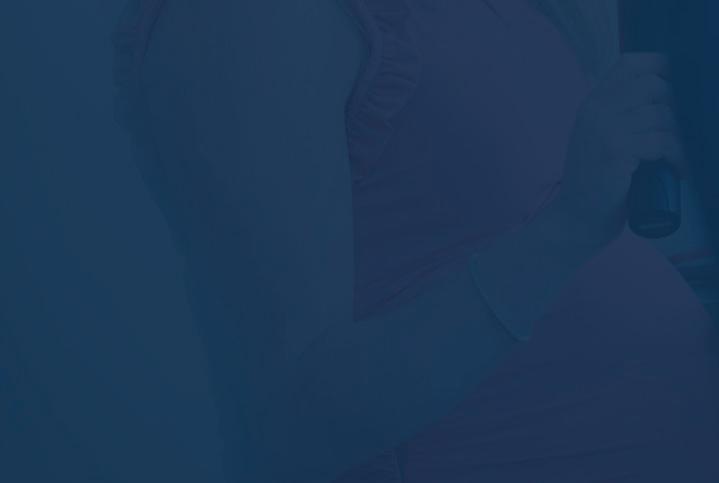
Meeting the expectations fellow women engineers on teams have of the engineering experience is part of Jauregui’s leadership style.
“Most of the women engineers I have worked with have had experiences where they have felt extra pressure to prove themselves successful in the field. This looks like volunteering for more assignments or leadership positions, taking extra steps to ensure they are having experiences outside their comfort zones so that they are growing as a professional, and wanting more opportunities to demonstrate what they add to the team. I’ve noticed that this extends to some of the extra effort, attention to detail, and longer-term planning those women bring to our teams. This is by no means limited to women but it’s a strength I more often see in our women engineers because of their unique experiences.”
Encouraging young women Statistics and reports note that young women are not choosing engineering as a career as often as educators would like to see. Jauregui sees two possible reasons for this. The first is exposure to the experiences of other women in the engineering industry. The engineering community needs to make a greater effort to showcase women in engineering roles and tell their stories; such efforts can have a lasting impression as to the opportunities available and attainable in the field. The second reason is mentorship from women in the industry and from men as well. “It’s important to be available to our next generation of engineers to help them recognize opportunities to get involved, ways they can lean into their strengths, and work on areas for improvement,” she notes.
“Many times, through mentorship, I have been enlightened as to my true
potential to succeed and grow as an engineer and leader.
“There’s sometimes a narrow perception of what a typical engineer is like - technical communicator, running analytics, risk adverse,” she adds. “In reality, an engineer is someone that can define a problem, identify the facts, make reasonable assumptions, and oftentimes be able to communicate to multiple parties. This take on what a typical engineer is like emphasizes more of the methodology of being a strong engineer and is more welcoming of those that may have an interest in becoming an engineer. And I think we should be encouraging those interests and diversity of personalities within the engineering field. What we can accomplish together is better for it.”
Jauregui also notes that if she had understood that enjoying a role and career is more than figuring out the ‘what’ of a technical area when she was younger, it would have helped her discover more opportunities for professional growth earlier.
“It’s not only the systems you work on,” she says, “but also the environment you work in, the responsibilities you take on, the teams and clients you get to work with. All of these are just as important to figure out in terms of where you aspire to be or go in your career. Knowing this sooner would have led to richer professional experiences or career conversations with others in the field as I sought to figure out my career goals earlier on. It’s something I like to share with engineering graduates as they are embarking on their job search.”
CGI Motion standard products are designed with customization in mind. Our team of experts will work with you on selecting the optimal base product and craft a unique solution to help di erentiate your product or application. So when you think customization, think standard CGI assemblies. Connect with us today to explore what CGI Motion can do for you.
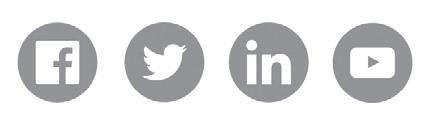

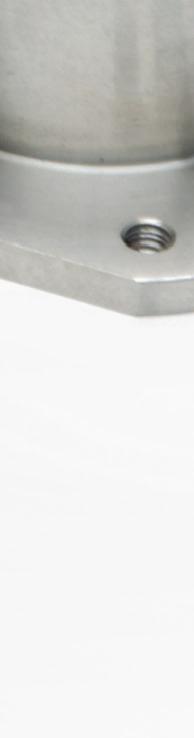
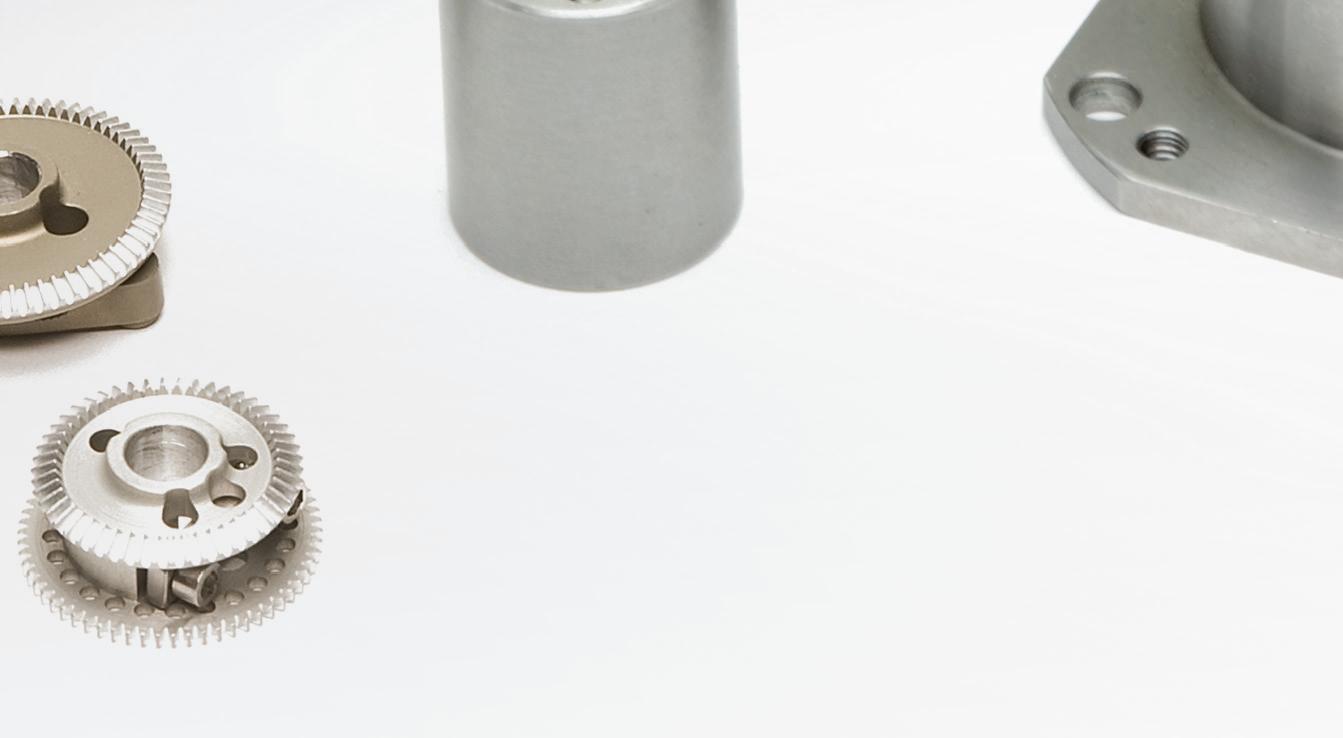
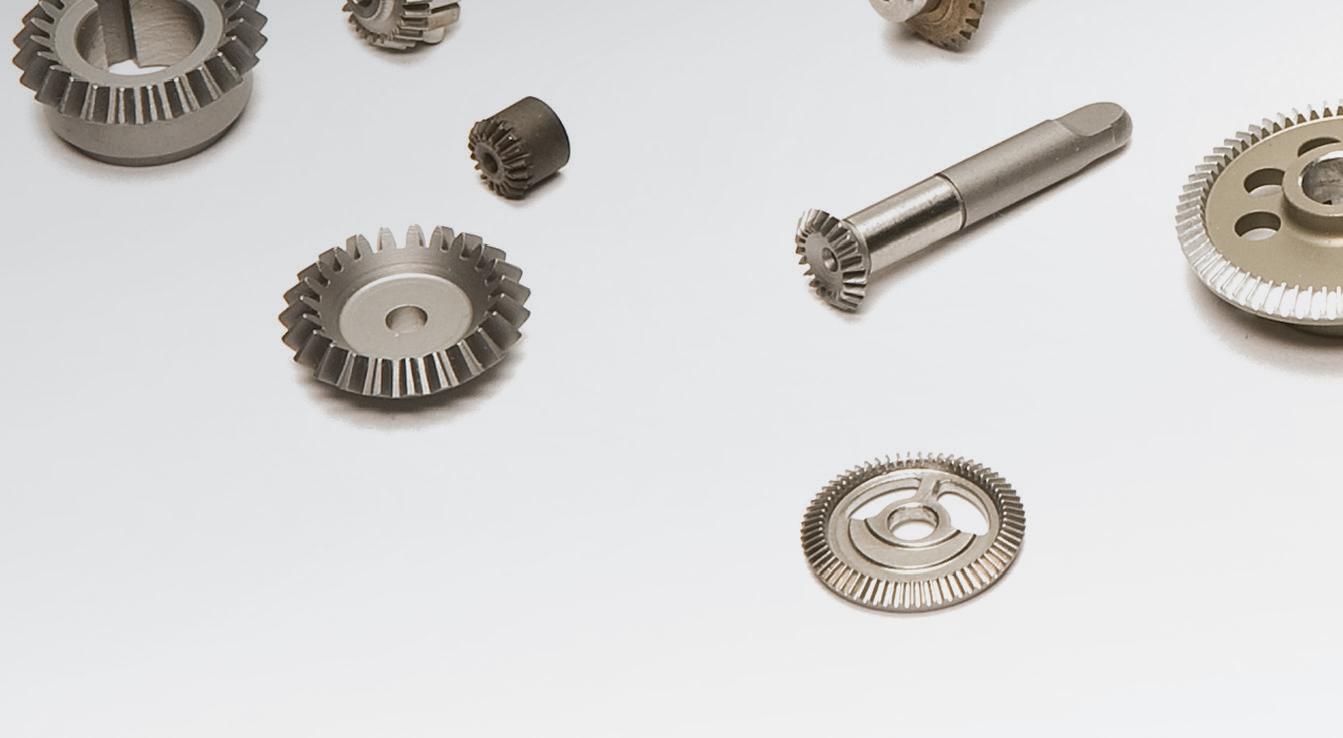
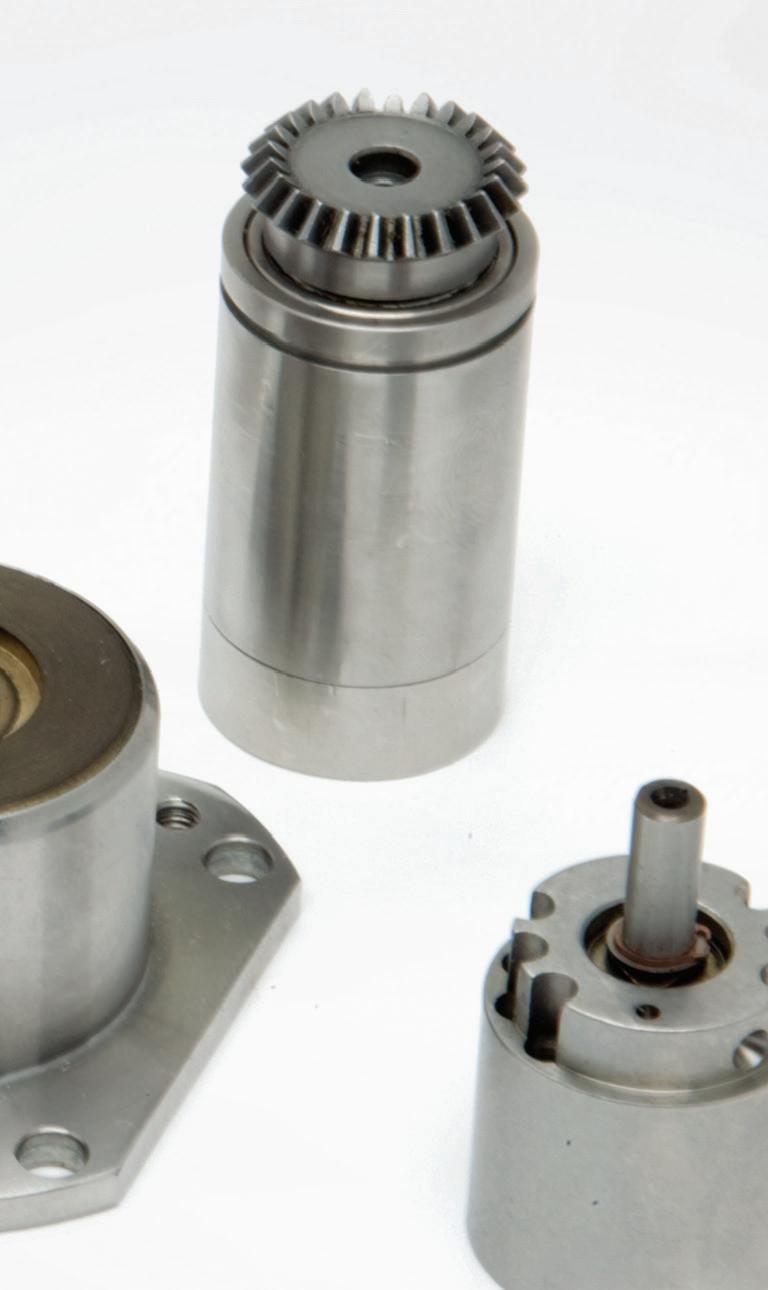
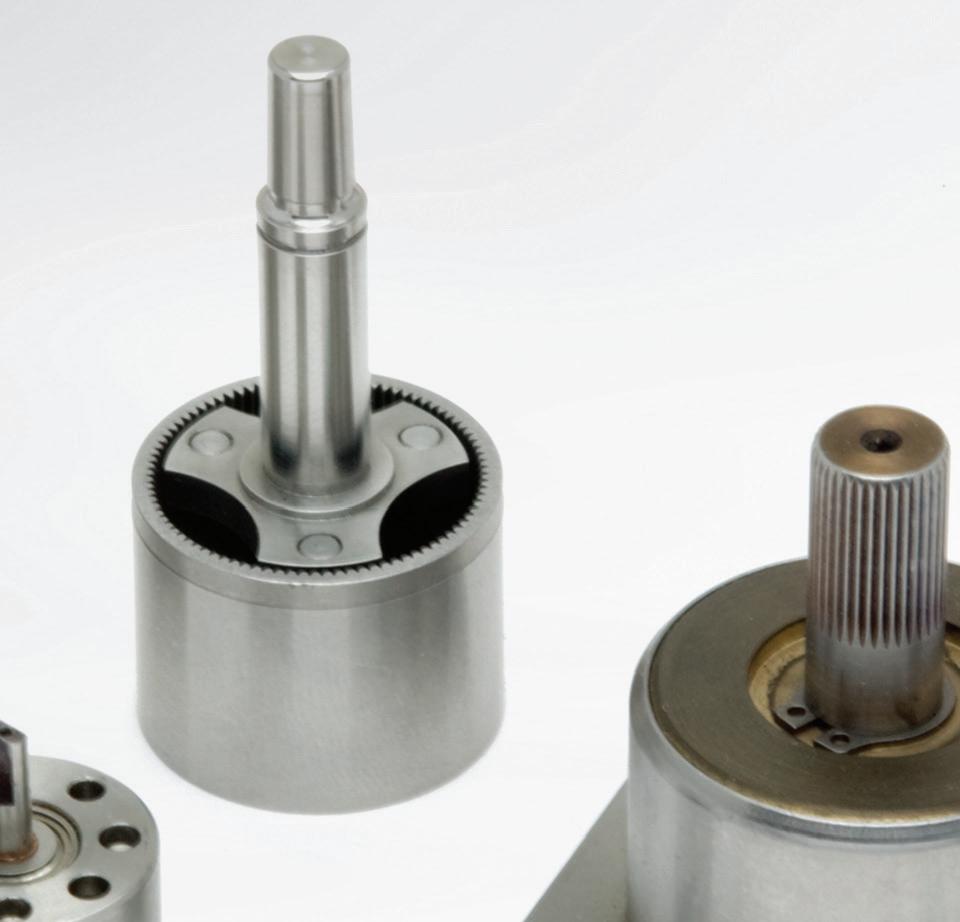

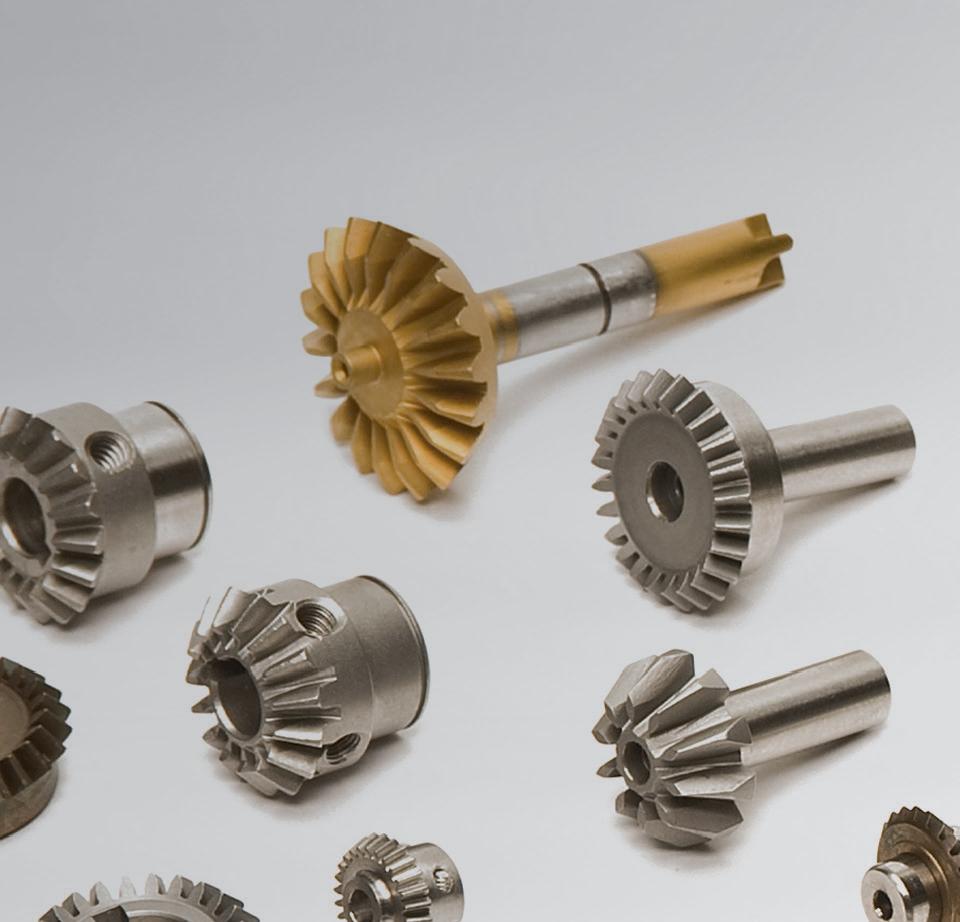
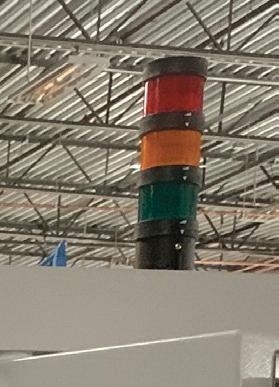
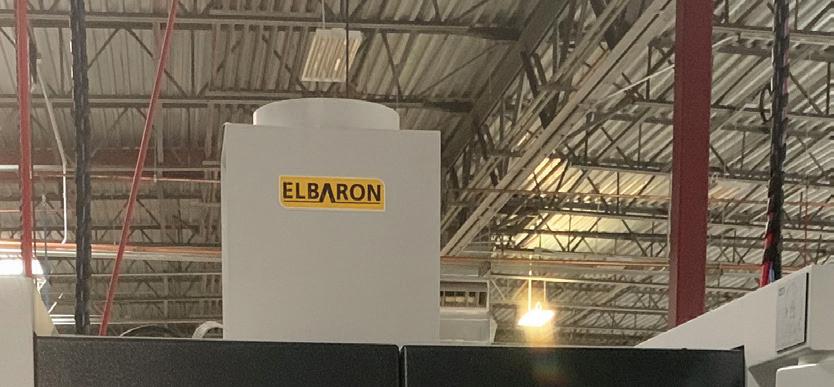
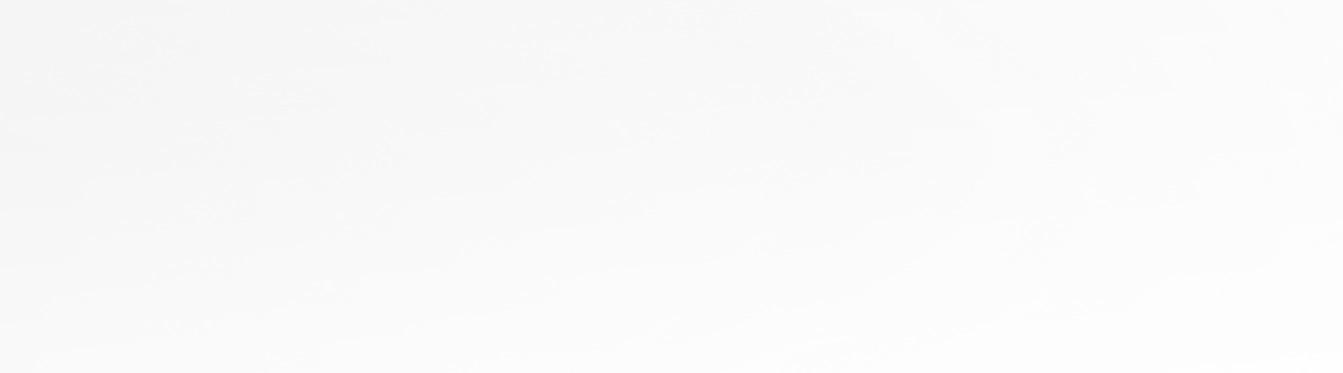
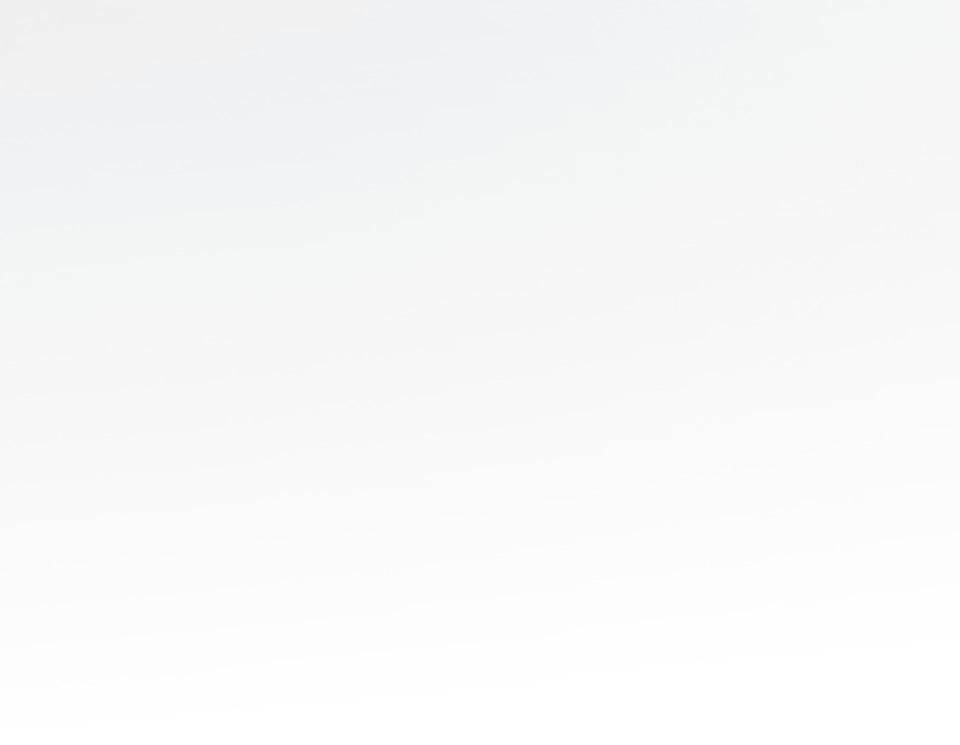
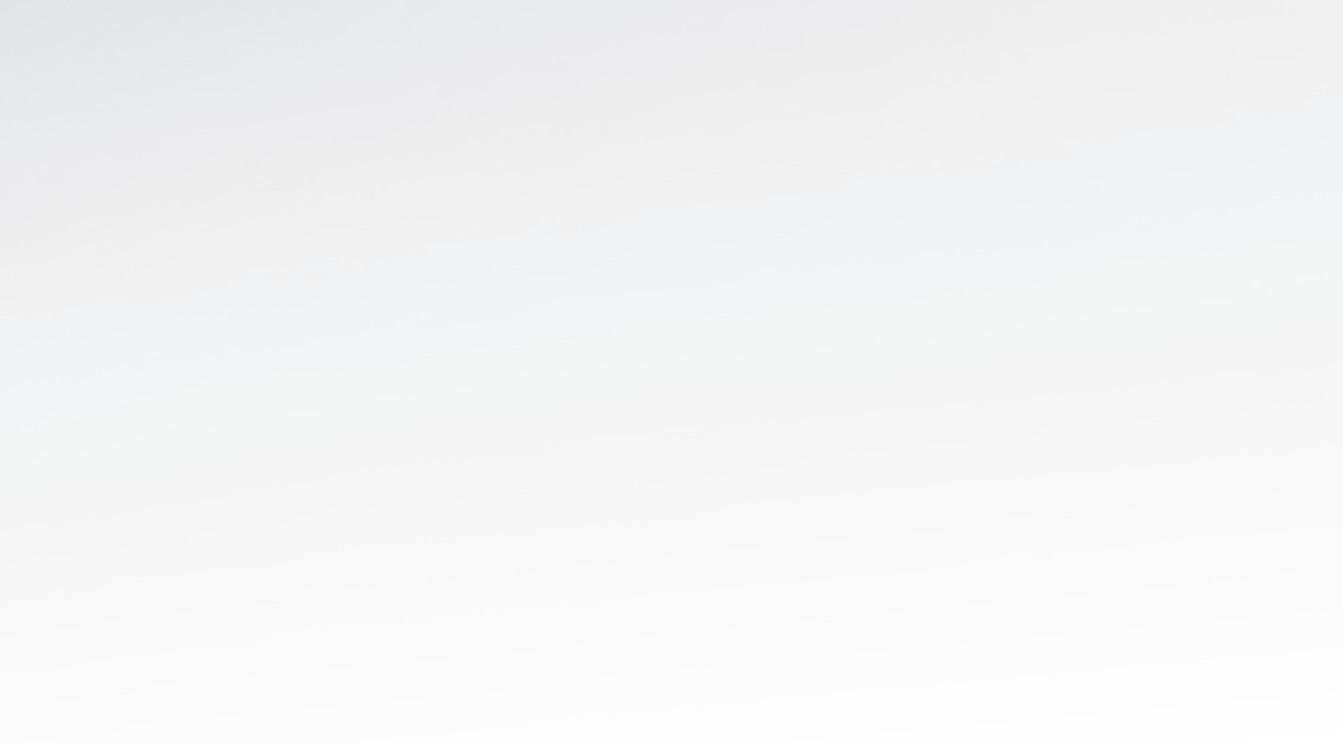
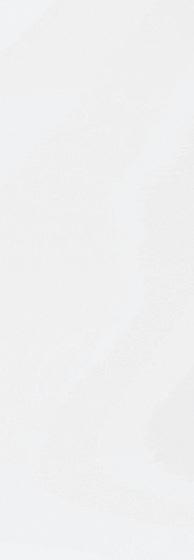
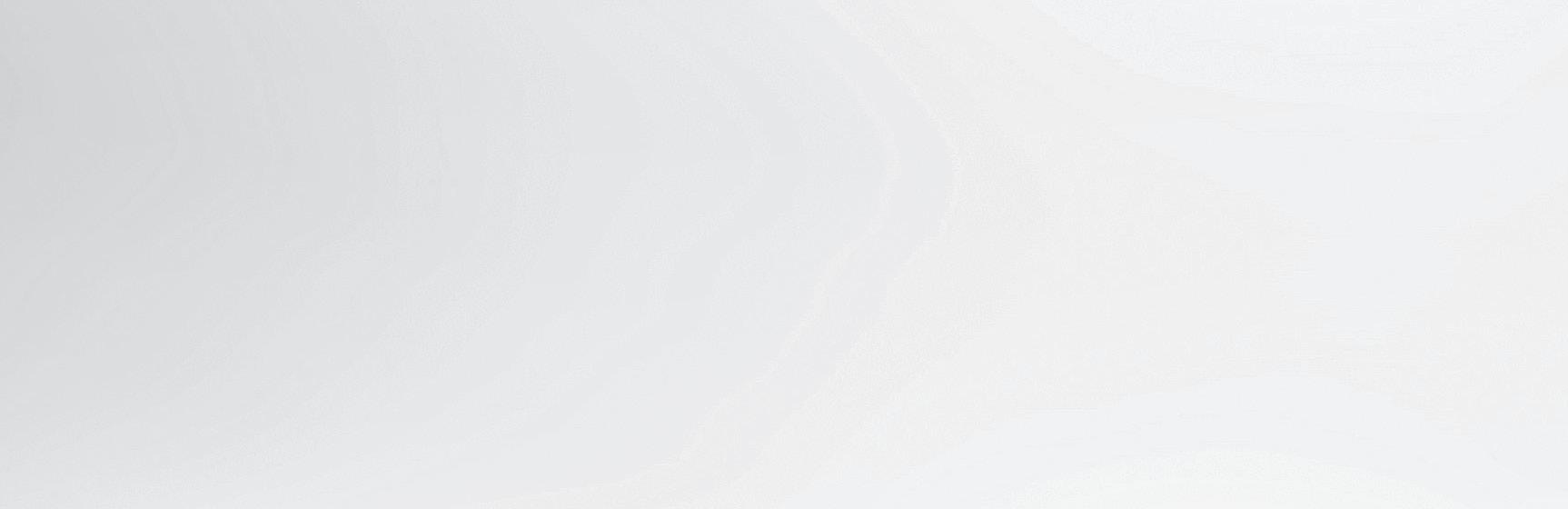
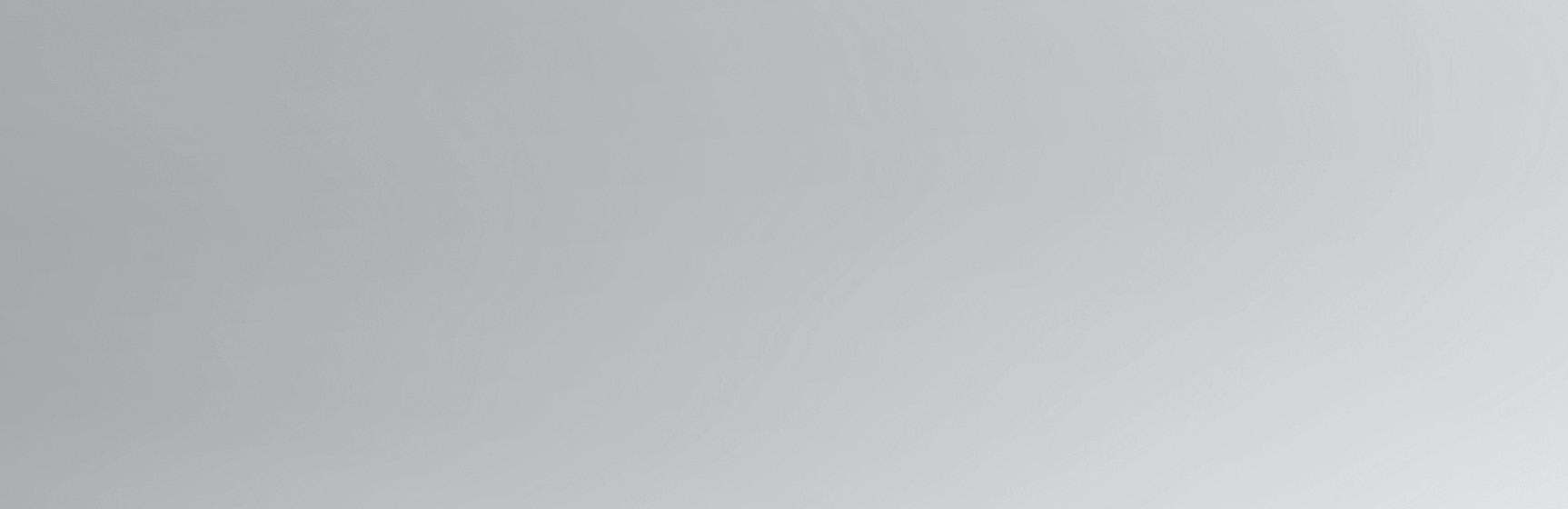
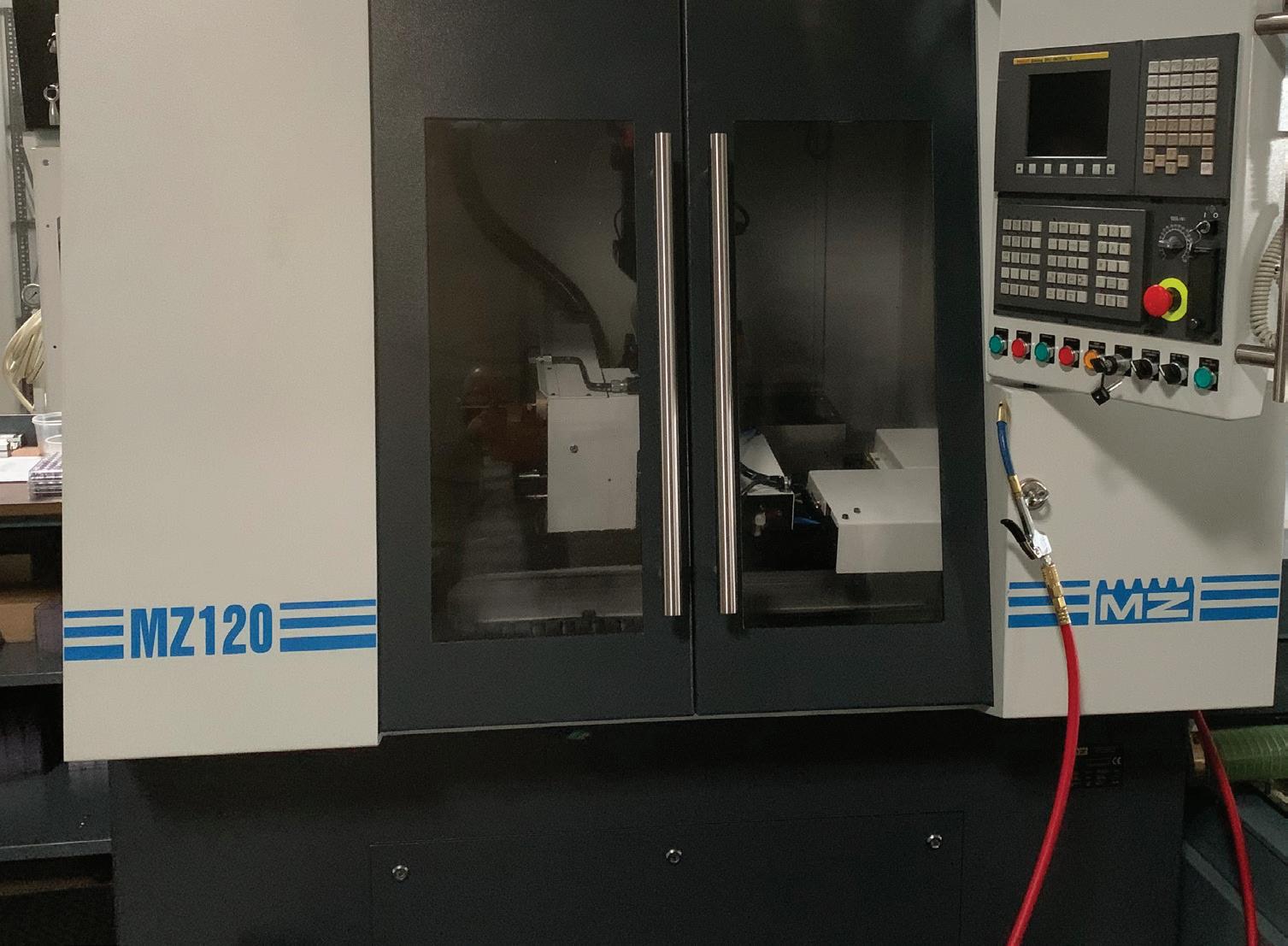
Fromengineer to author
Engineering can be a springboard to a range of careers.
For young students considering an engineering degree, going through a traditional engineering university is only one path. For professional engineers considering their career path, a degree in engineering is a springboard to a range of occupations, including consulting, as Kathy Miller shows.
Miller was a well-rounded student with good grades in all her classes. She could go in any direction she wanted. However, she did not have access to a college fund, so she put herself through college. The choices available to her included schools like Kettering University. Kettering offered a type of work and learn program where students would work six months a year, getting a range of practical experience, and then attend classes for six months.
“My education took five years,” she says, “but the great thing was I had this practical experience. Plus, I was able to come out of school with very little debt and get a really good job after. It was a practical decision rather than a passion decision.” Even though she didn’t have role models for engineering, male or female, Miller chose industrial engineering because she liked the people and the processes.
“When I was a co-op student, I worked in industrial engineering in every single department in the factory, from labor relations through to taking noise surveys to ensure the environment was okay. I did a

Kathy Miller
Professional Coach & Business Transformation Adviser/Speaker/Author/ Sr. Manufacturing Executive Women in Manufacturing Hall of Fame Inductee (2021) most recently the Global Vice President of Vertiv Operating Systems
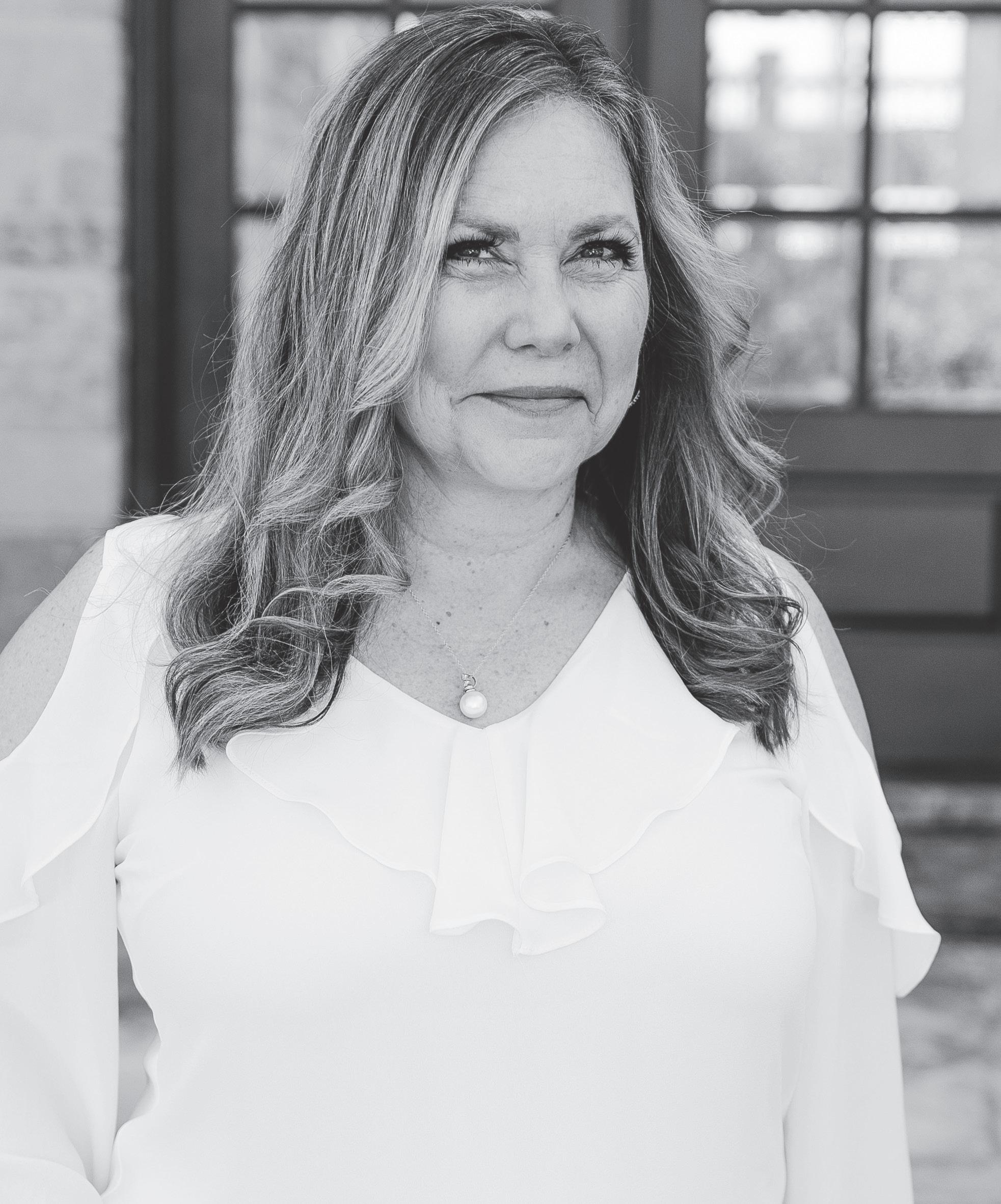
B.S. Industrial Systems Engineering

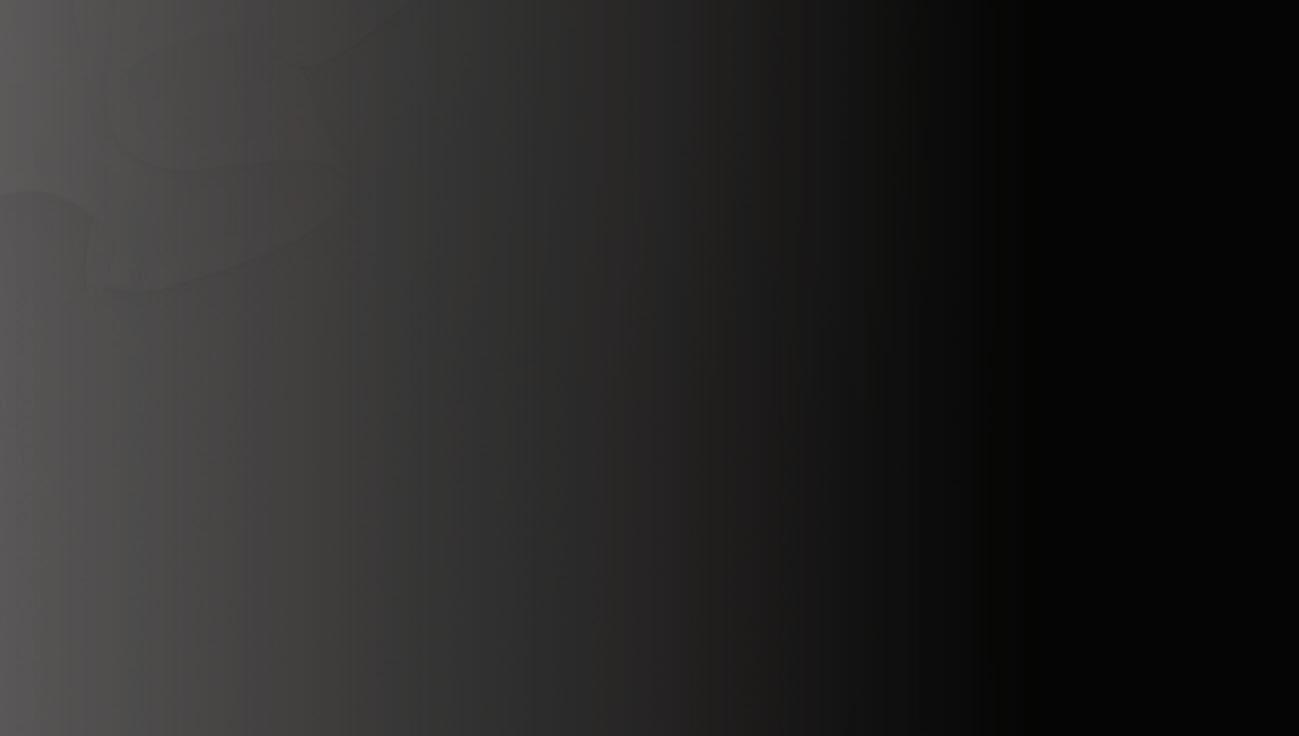
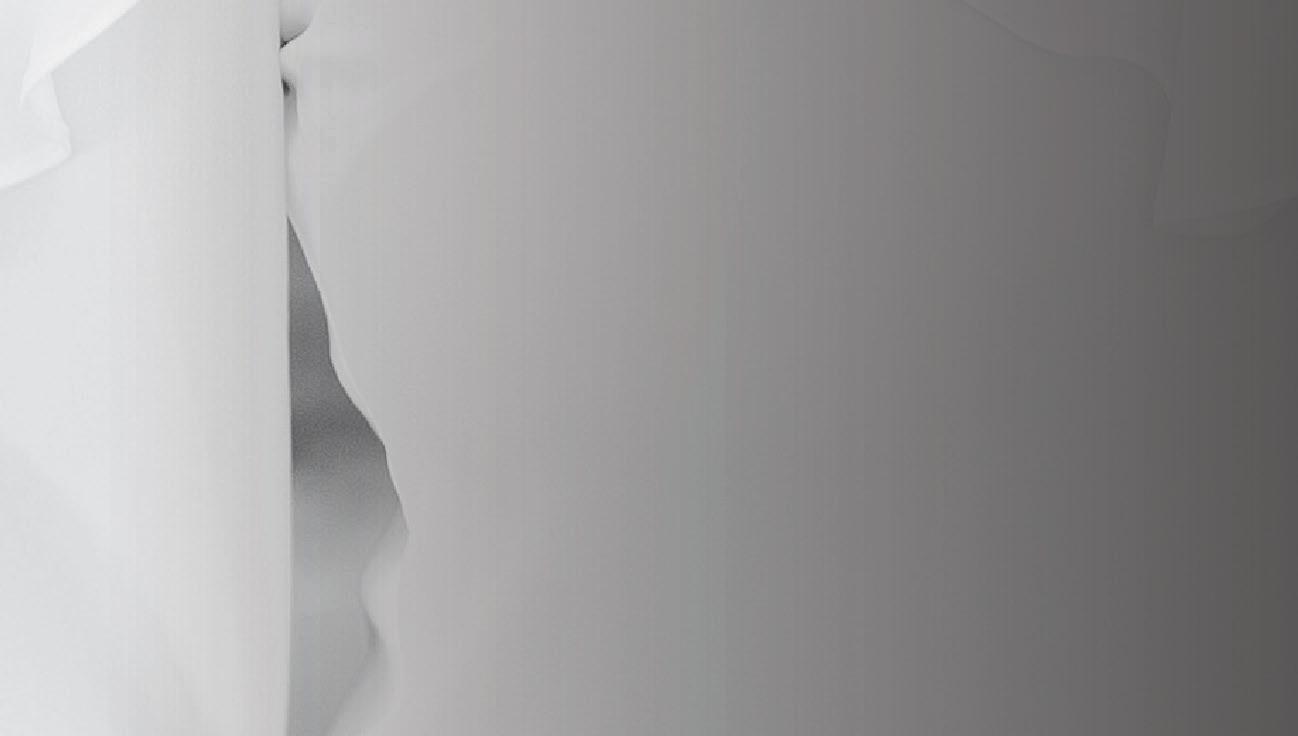
Women in Engineering
Engineering, though, was the practical choice, and it made it easier to find a job with a bachelor’s degree, ensuring a good living and enabling Miller to support herself.
Miller ran the plants at Rolls-Royce Defense globally and was promoted into leadership positions early in her career. She was a supervisor of an industrial design and mechanical engineering department in advanced audio systems.
“I was drawn to the people aspect of this position,” she says. My engineering degree was helpful for supporting the engineers … and providing an environment where they could flourish. We speak the same language, and I understood the challenges they faced and we worked on potential defects they saw in the designs.
The pursuit of her dream led to the publication of her book, Steel Toes and Stilettos. With the publication, Miller started a company with a friend, OPSisters. This is a coaching business that advises and helps manufacturing clients develop a roadmap to transform their businesses.
lot of layouts, moving things around the plant, as well as time studies to make processes more efficient and to balance the assembly line.
“After that, I moved into advanced engineering for instrumentation and audio systems. I worked on ergonomic issues associated with advanced displays.
I was able to do a lot of exciting projects when I first got out of school. And then I went back into the plant.”
Miller enjoyed the tasks of fitting processes and equipment into a cohesive whole and learning the broader picture of how everything interacts in a manufacturing setup.
“It turns out that it was a wonderful background as my career progressed through manufacturing, which is where I chose to take it.”
Changing direction
Miller had a lot of interests in high school, including the humanities.
“After my post grad, I got a Master’s Degree in applied positive psychology. Well, if the truth be known, I wanted to study psychology out of high school.”
“But part of me always wanted to study psychology. After the opportunities at Rolls-Royce, I decided I didn’t need any more operations experience. Life is short and I went back to school to pursue this degree. I felt that the hard work that I had done through the years and the results that I achieved afforded me the opportunity to live in choice and pursue that dream.”
The pursuit of her dream led to the publication of her book, Steel Toes and Stilettos. With the publication, Miller started a company with a friend, OPSisters. This is a coaching business that advises and helps manufacturing clients develop a roadmap to transform their businesses.
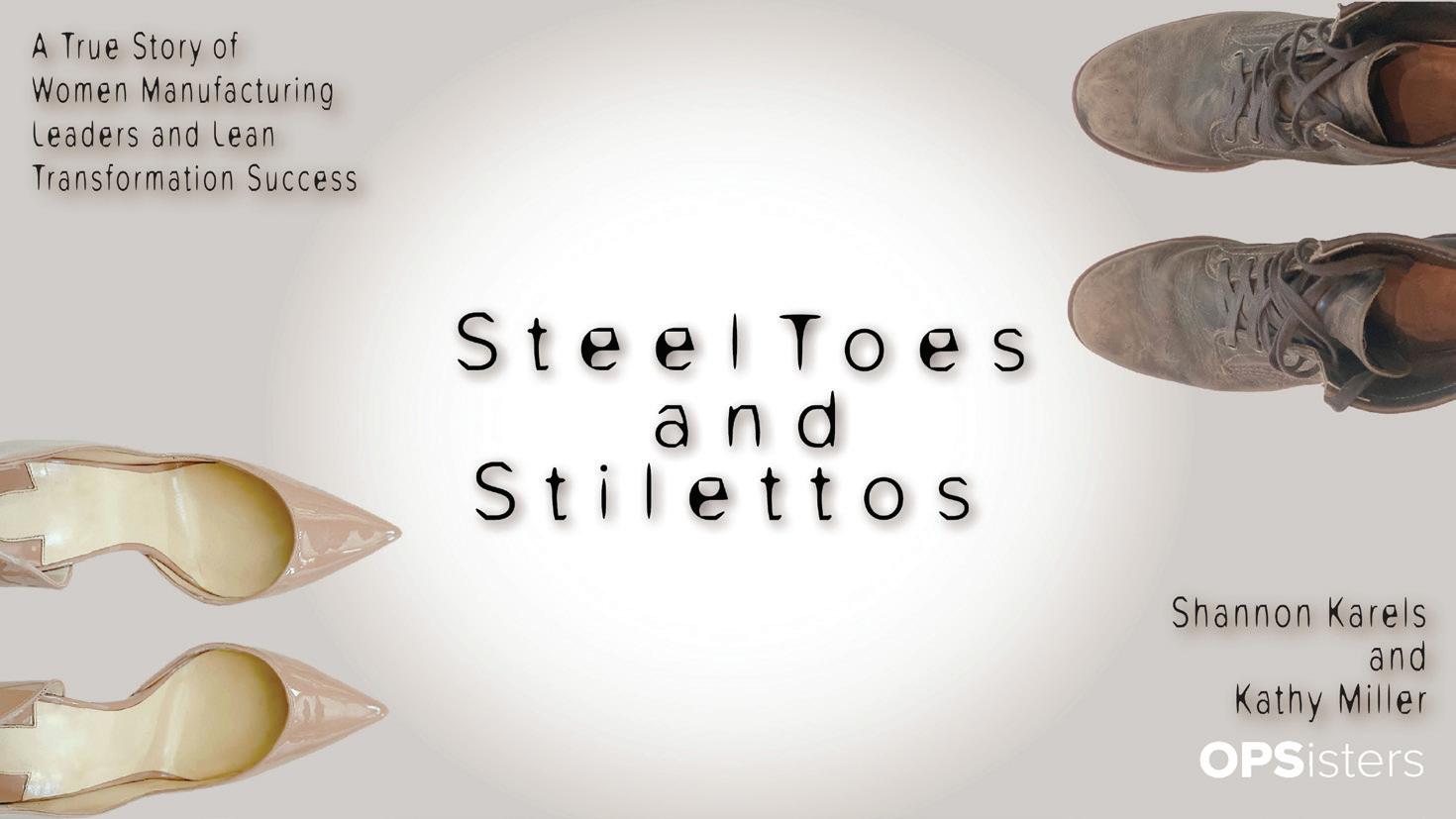
“Since my friend and I have spent the majority of our careers with manufacturing, it made sense. I’m coaching manufacturing leaders at all levels from team leaders through executive management. We have a class on creating lean transformations, and we help clients develop inclusive cultures.”
Miller did her thesis on manufacturing, titled Welcome to the Efficacious Factory. It focused on getting better business results through
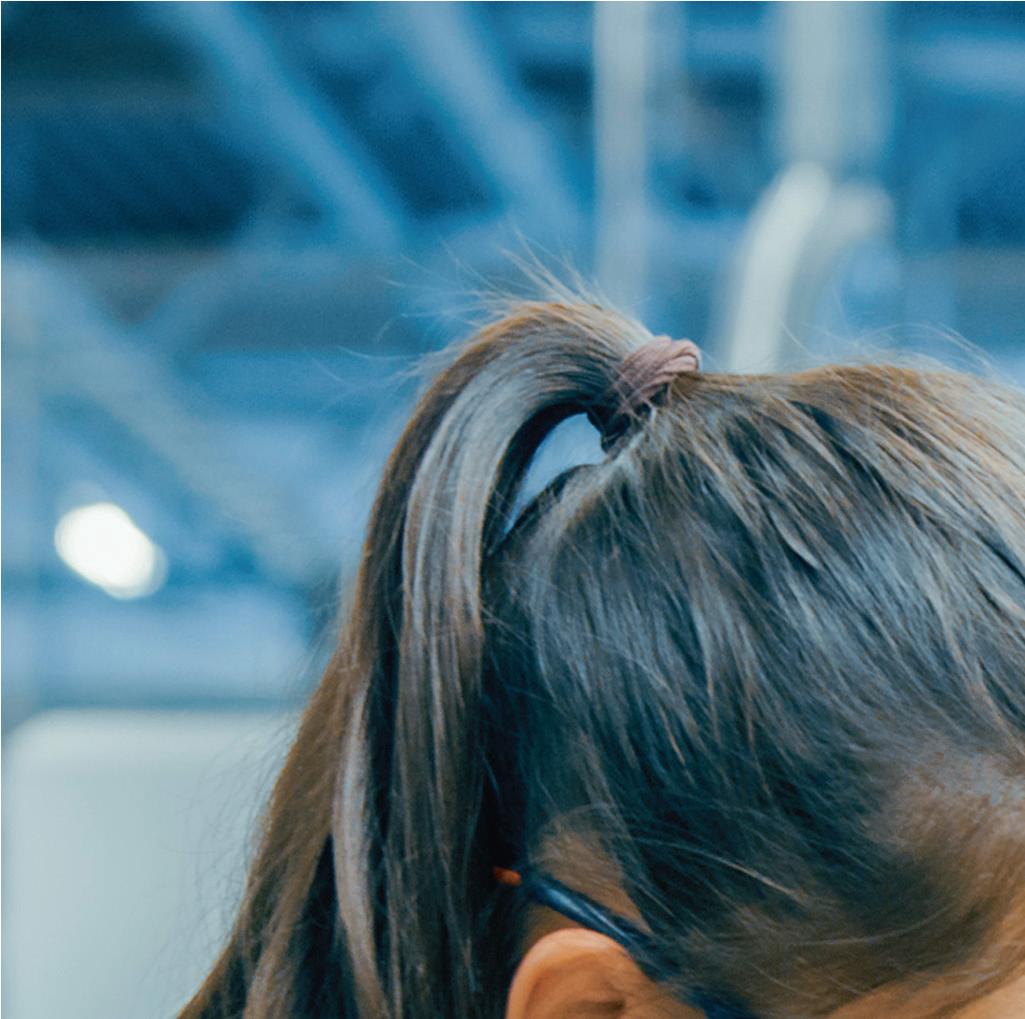
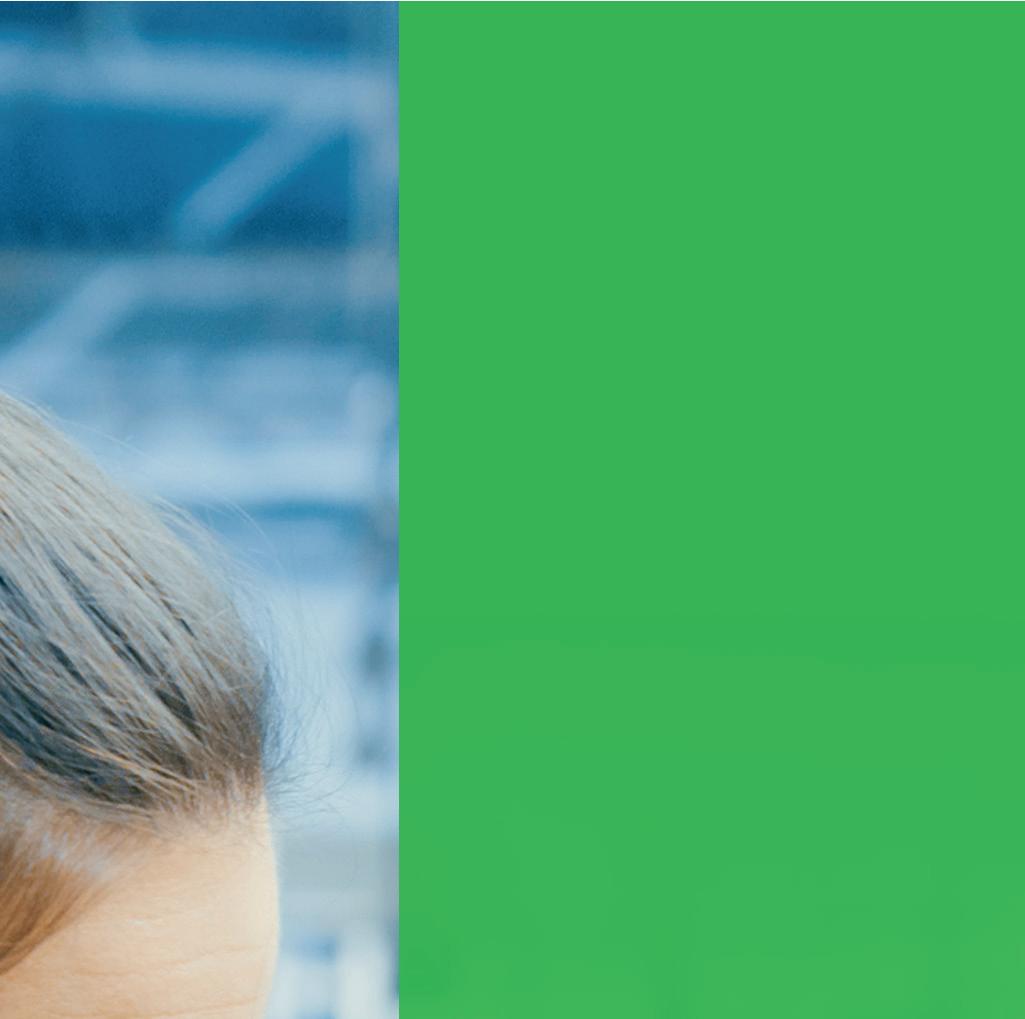

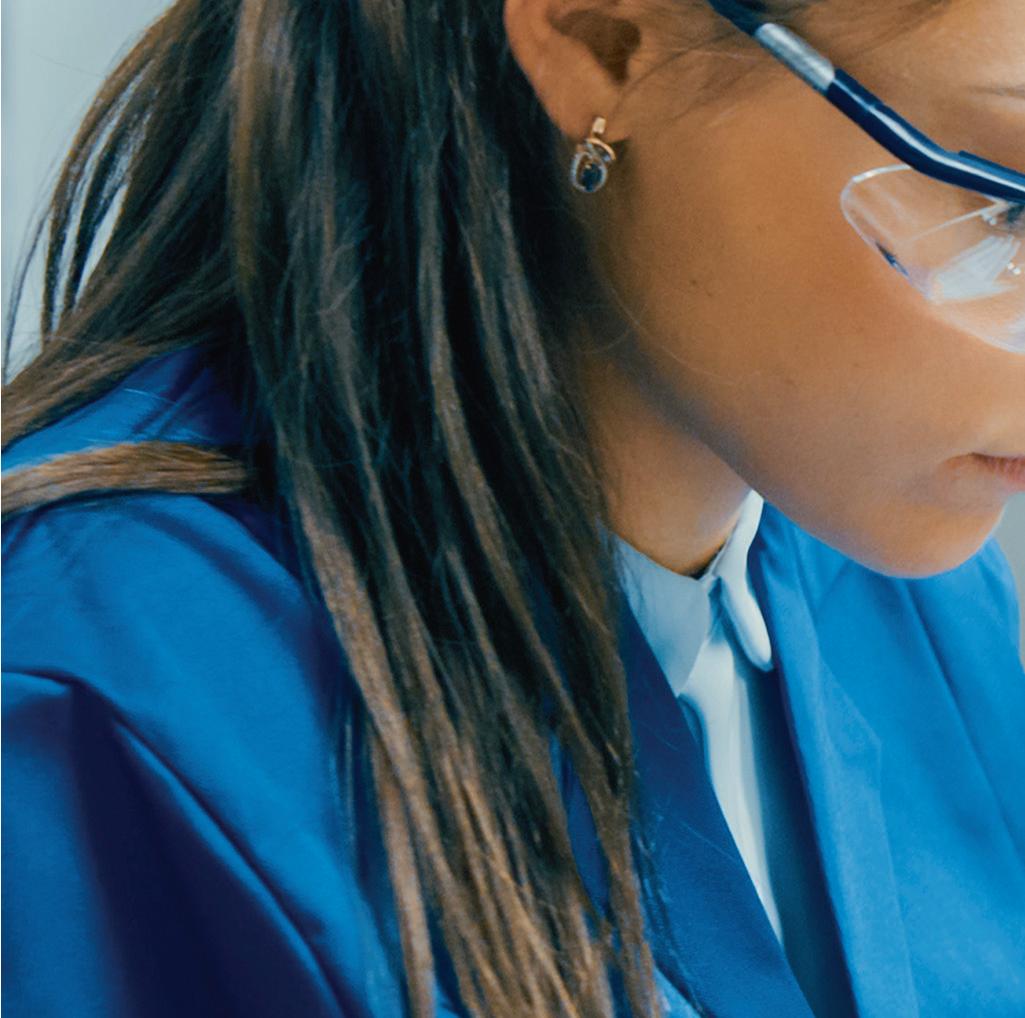

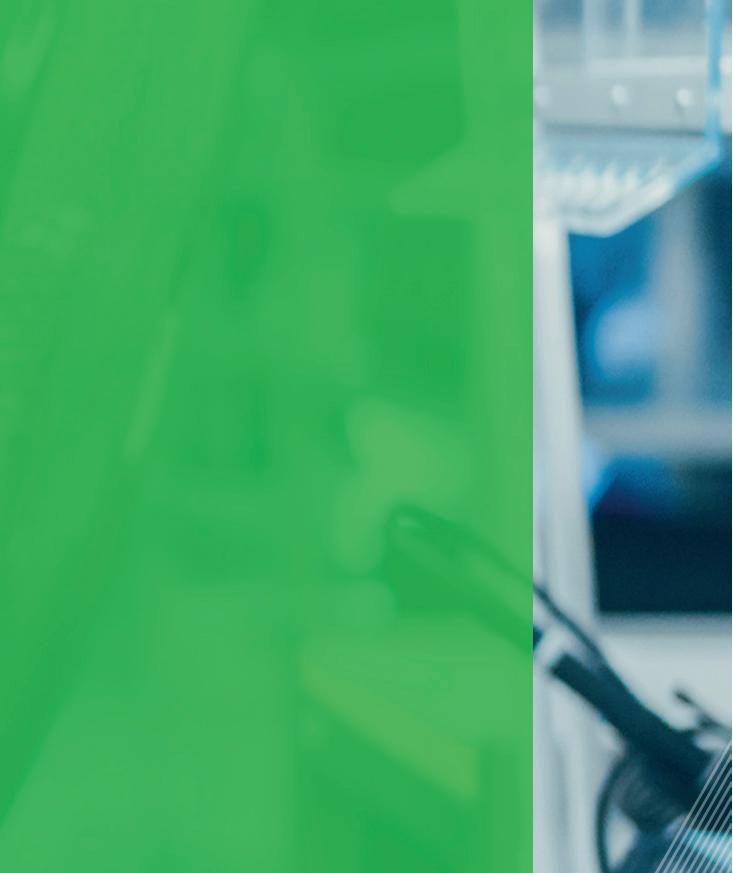
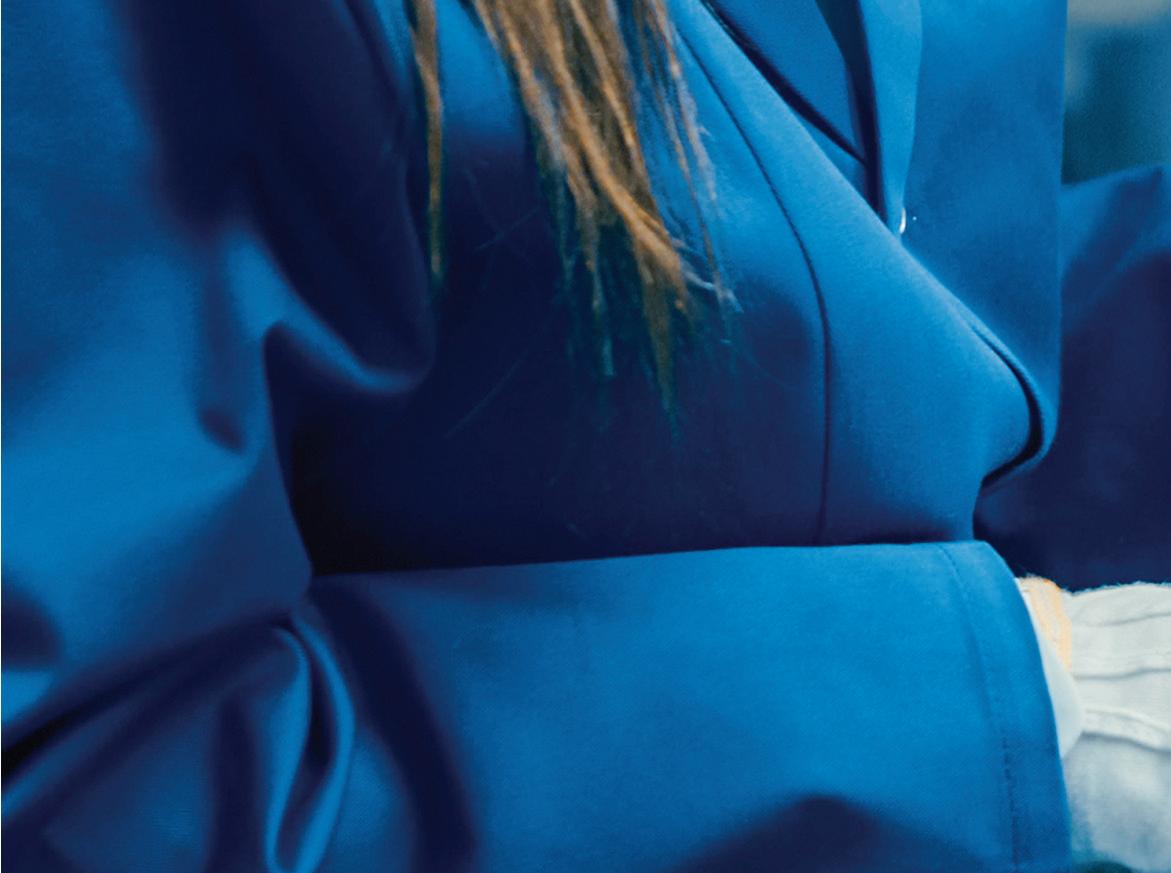

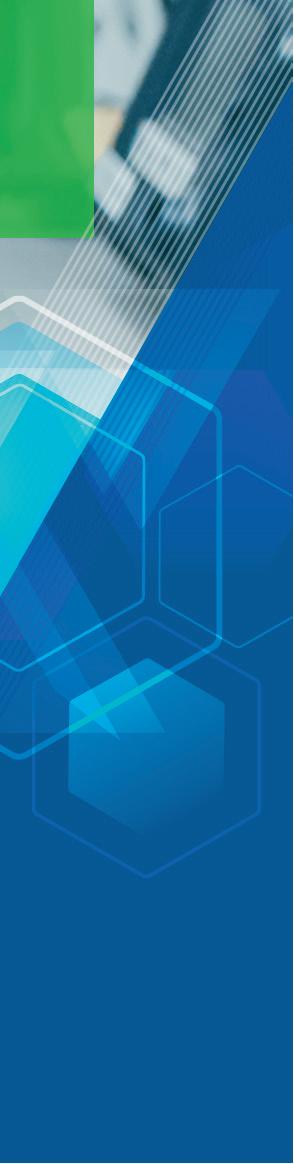
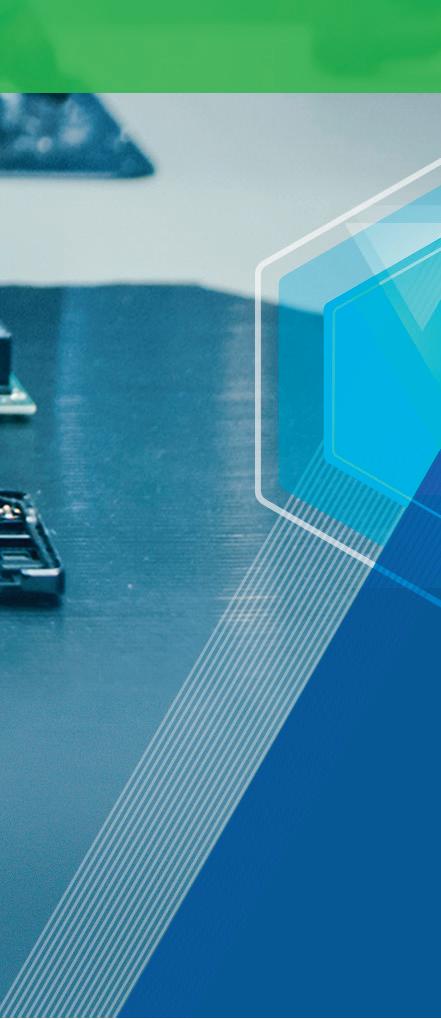
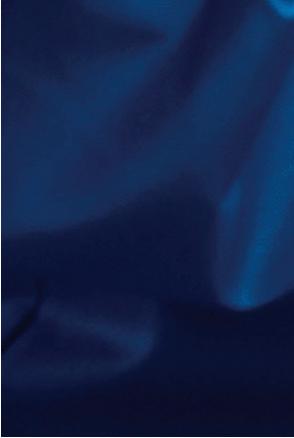
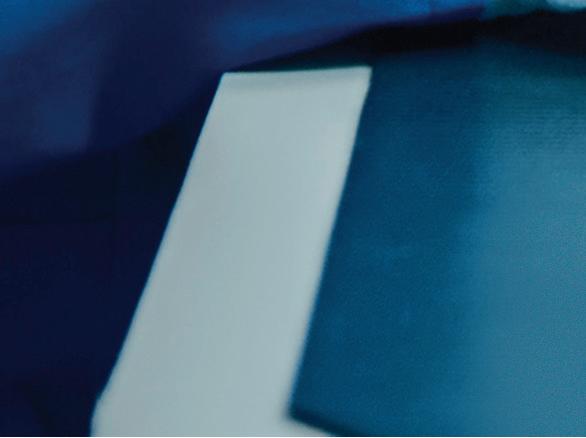
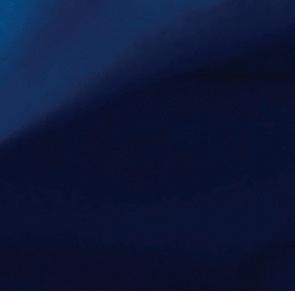

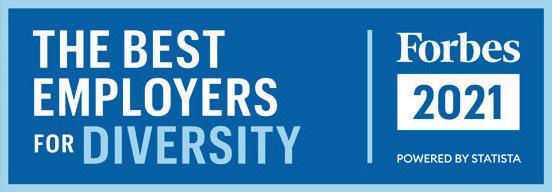
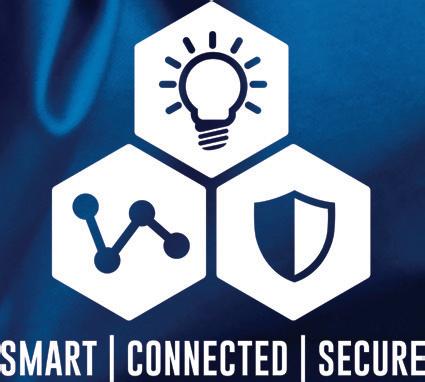
positive workplace relationships, optimism and meaningful work.
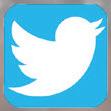

“I learned the science of organizational principles that help people flourish. Now, I have 117 pages of literature review connecting those concepts with business results. And I’ve got years of case studies. It’s a nice combination to help today’s modern factories. And manufacturing is undergoing a huge shift. Whether the industry likes it or not, it’s definitely changing.”
The new manufacturing reality
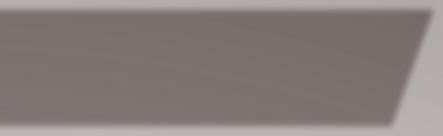
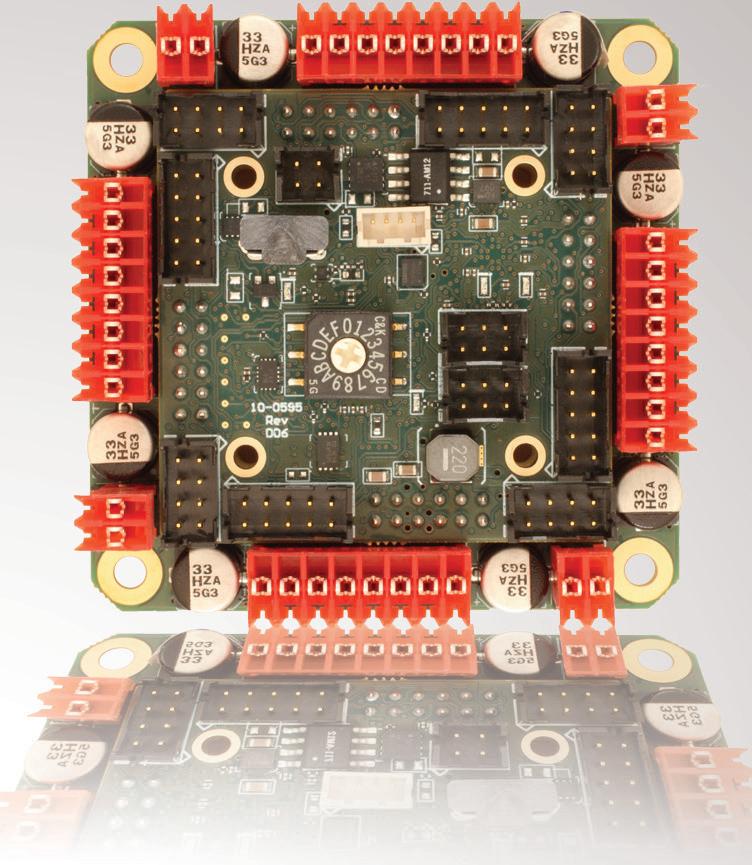
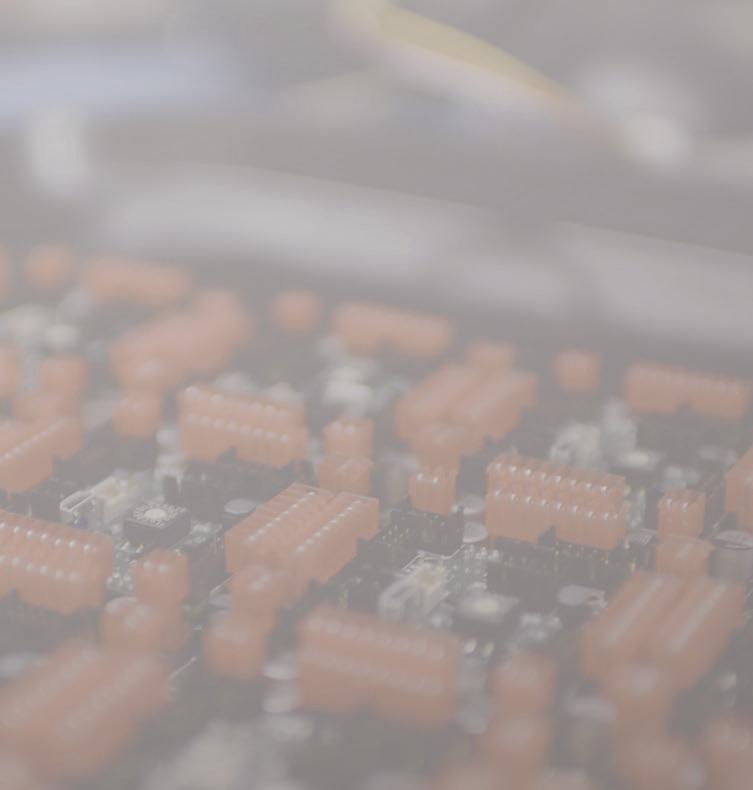
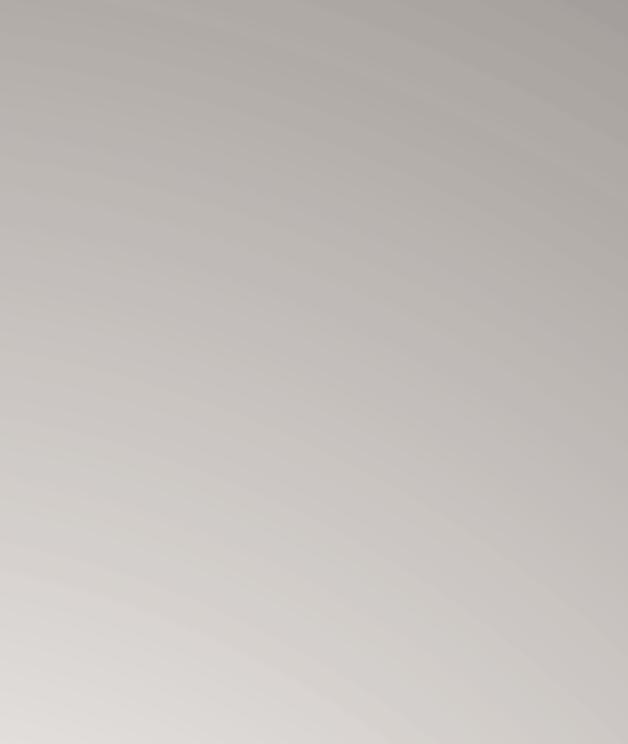
Miller sees a lot of variation on how companies adopt technology, how they include people, and how they treat their facilities. Plus, many manufacturing companies grow by acquisition, often purchasing the problems of the previous sites that now they must handle. Part of the problem is that the buying company attempts to impose its operating preferences on the bought company, leading to operational challenges. Of course, the Pandemic has spotlighted many weaknesses and challenges of supply chains.
“Supply chain issues are always complex, depending on what your philosophy is,” she says. “I think right now, there’s been the normal challenges in supply chain, and then there’s the global pandemic. You’ve got workforce issues, the great resignation, company
or countries turning on and off their supply chains, the lag between when you ordered things and when they’re available and when you shut down your purchase orders and... it’s just like this whole bull whip effect. And I think it’s going to be a while before it stabilizes.”
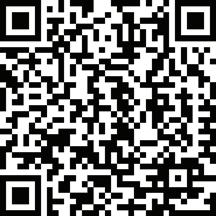
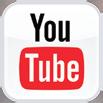
What women bring to engineering But such struggles can also be opportunities for women to “strut their stuff.” Miller says that there is a lot of research on what women bring to engineering problems and businesses. “Particularly as leaders, because women tend to promote cooperative learning versus competitive type cultural behaviors,” notes Miller.
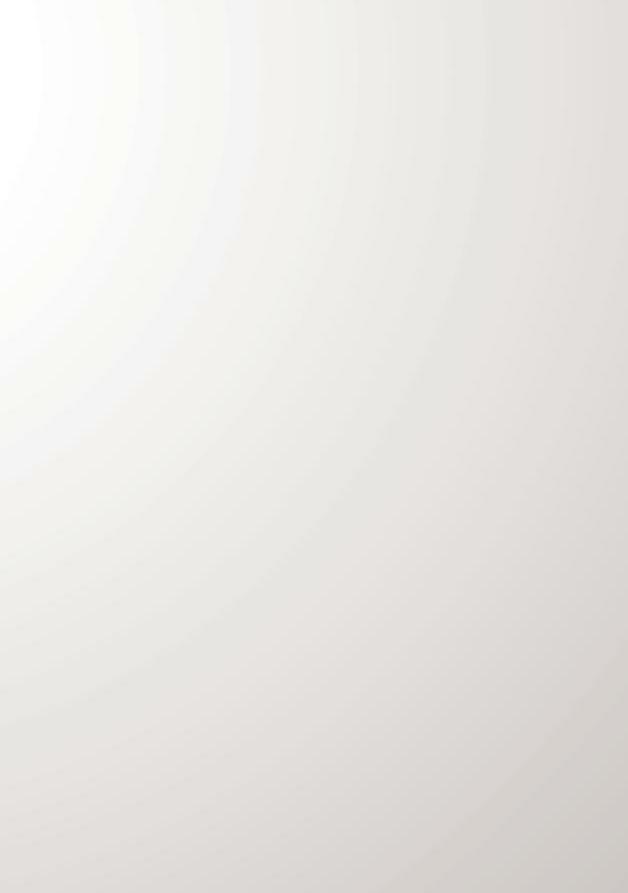
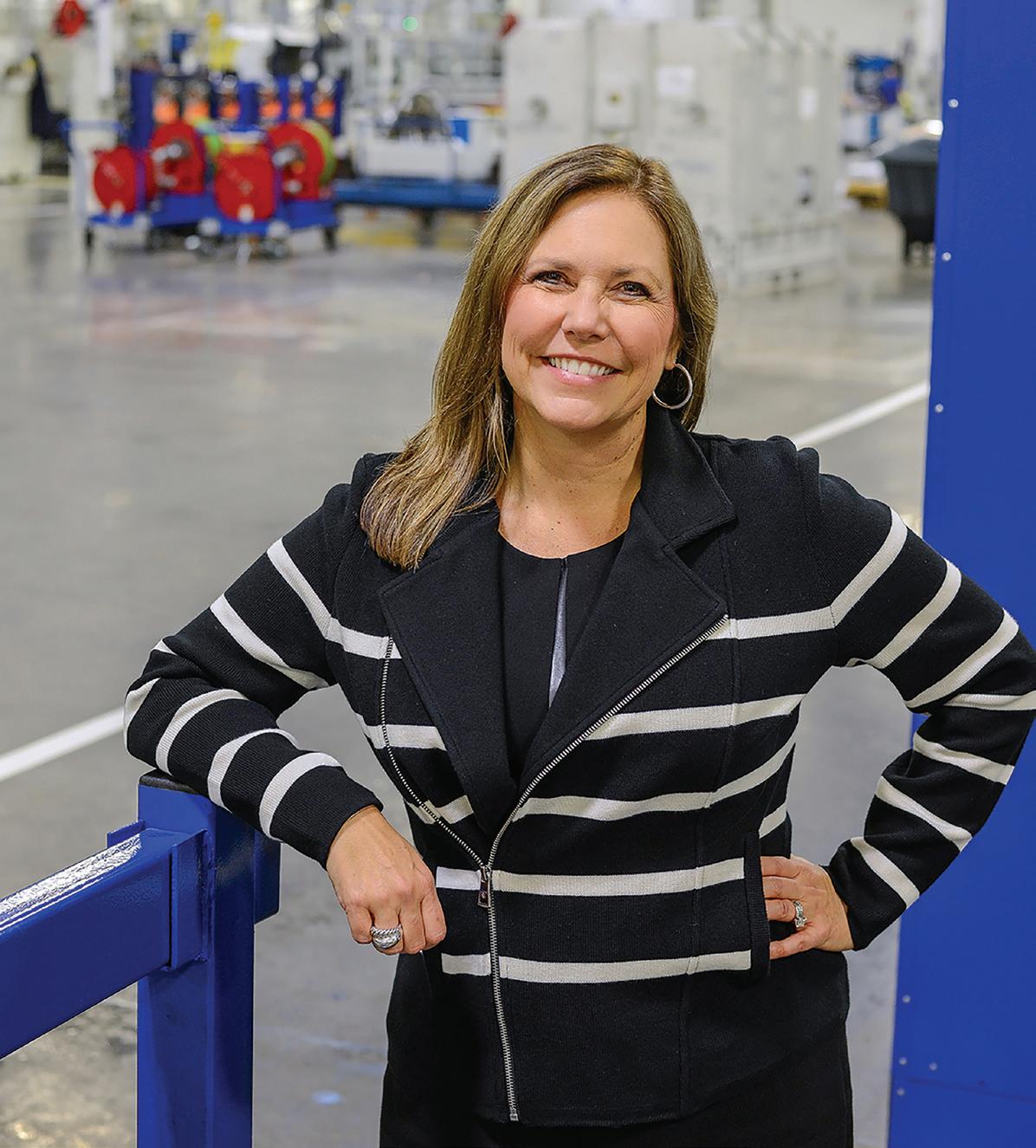
“Women tend to be relationship oriented, so they can get better results from a group versus an individual project. And diversity of thought is so important for getting the most creative solutions.
“Every corporate culture is different, and there are subcultures within corporations that really do well. You can move from one part of a company to another and almost think that you’re in a different company. I always got great results by including everybody and making sure all voices were heard and giving everyone an opportunity to problem
THE COMPLETE ROBOT TRANSFER SOLUTION








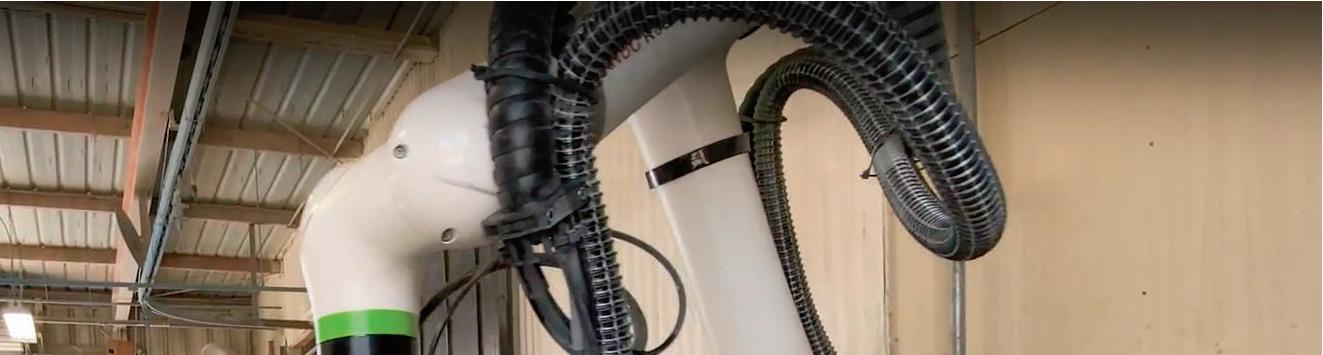
7th Axis Solutions - Robot Transfer Units
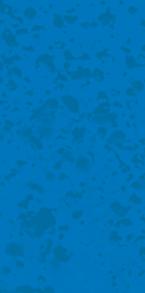
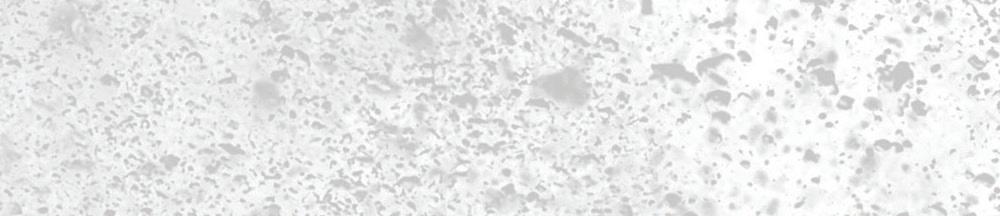
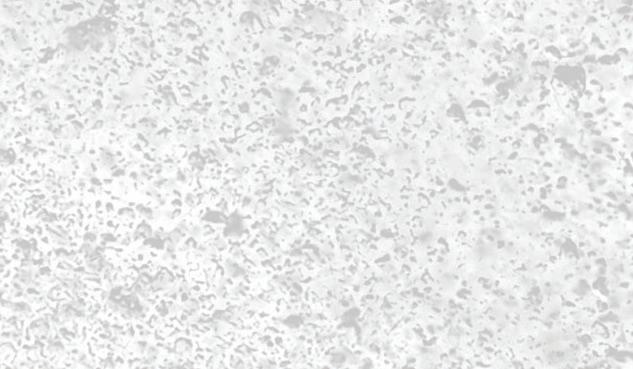
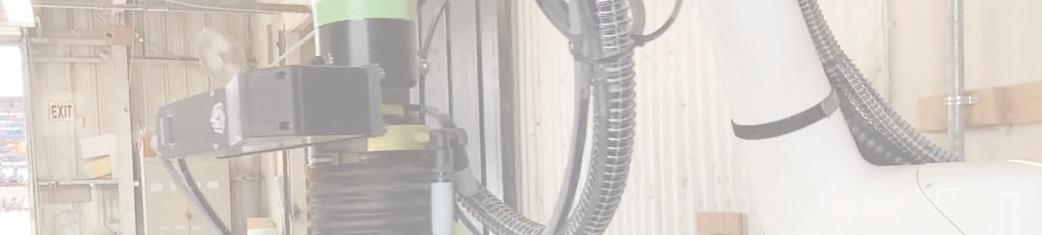


Robot positioning systems provide flexibility in manufacturing and industrial spaces. They allow one robot to reposition between work stations to do the work of several robots and extend a robot’s working area without need for a larger arm.
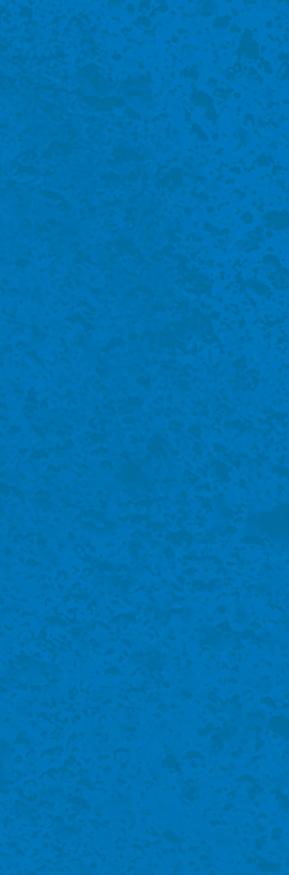
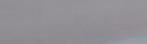



These motion systems are common in aerospace, automotive, warehouse, and manufacturing applications. Both traditional and collaborative robots can benefit from Bishop-Wisecarver’s 7th axis motion solutions, regardless of their size.
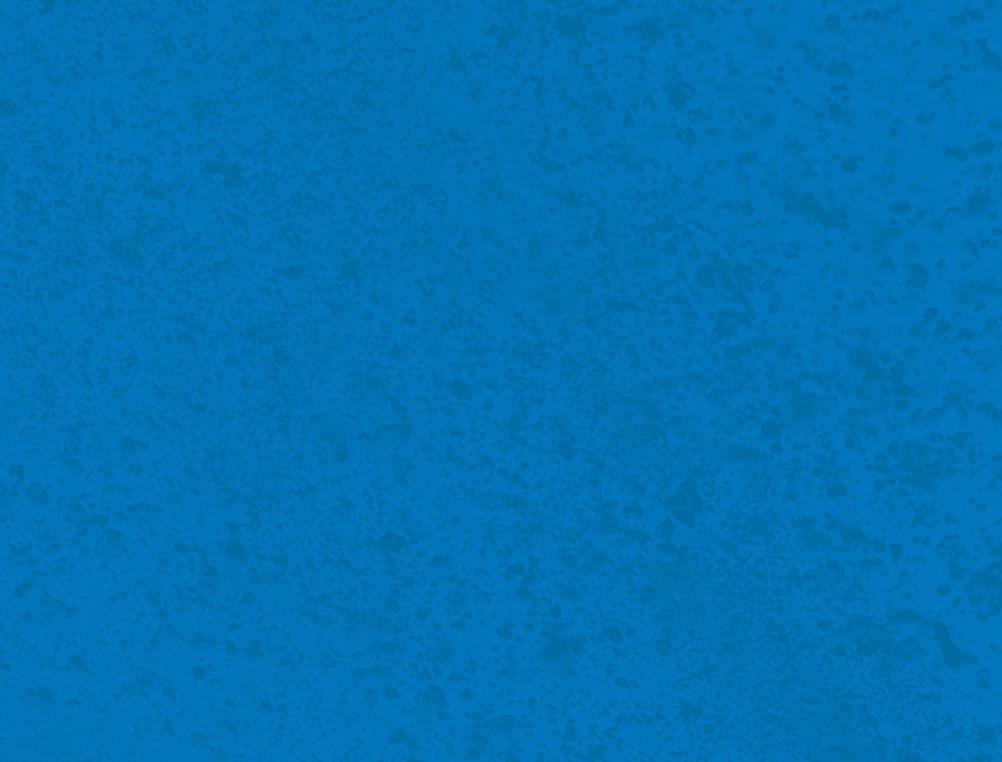
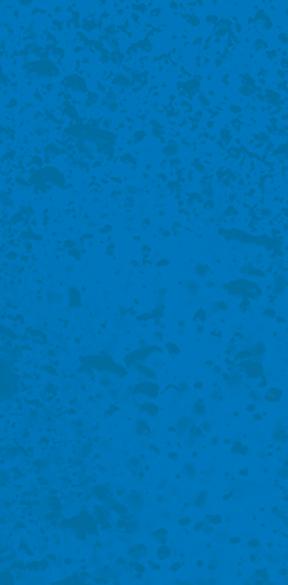


solve. When we had a recordable injury, I made all my staff go to the scene of the accident. Everyone had to contribute to the problem-solving process, even the marketing guy who didn’t want to go. And what you found was people just had different perspectives. My marketing executive came up with amazing solutions for things that he did outside of the plant that we could bring into the plant to help solve problems. So, I think that can be an advantage for female leadership, just that whole inclusivity.”
A woman in a man’s world Women engineers can face challenges of working in a male dominated profession. And each woman handles it differently. Miller used her confidence to handle any situations that came up.
“I always felt that when I got a seat at the table, I had earned it. And I never really made gender an issue unless somebody else did. I grew up with brothers, went to engineering school, I was very comfortable in the male world. And unless someone made some sort of interesting comment, which happens, it wasn’t a big issue for me. I developed really strong relationships with male allies before they were even called male allies.
“What I would say is let your results speak for themselves. As I was leading plants, I just focused on doing a great job and getting great results. And then people would notice and they would come in and say, what’s Kathy doing? Her leadership teams are a little more diverse. Their rate of improvement is above average. Let your results be your calling card.”
Miller believes women should be encouraged to consider engineering. “Since the launch of the book, I’ve been doing a lot of podcasts and encourage women to go into STEM. I work with women in high tech, women in manufacturing. There’s a number of different groups that I’m associated with. Everybody should consider it if they’ve got a propensity towards math and science, but we really want to encourage women to explore it.
“Some people don’t even consider engineering in the first place. It’s just not
something that’s brought up in high schools. Particularly when you look at manufacturing, it’s not considered very glamorous. And thus, is not attractive to people. That’s why I try to get out and tell the stories of how I fell in love with the factory and in doing this.
“When I was at Rolls-Royce, we would sponsor grammar schools. We had problem solving projects for grammar schools. We would bring high schoolers in and take them on tours. They had some hightech facilities that we were able to showcase.”
Unfortunately, keeping women in an engineering occupation is another challenge. Miller has read the studies that show that women don’t stay in the STEM fields very long. She sees that as something to focus on.
“For me, that means providing role models and mentors and allowing women to be authentically who they are. Women may approach things differently than their male counterparts. We shouldn’t make them conform to the male model; we should allow women to live in their strengths.
“We need to provide a support system to women engineers. If they’re the only token female in a male engineering group, someone needs to be an ally to that person. If you are a female, you need to be a role model to other women in your company. I didn’t have female role models. There weren’t many women in manufacturing leadership, or engineering leadership that I had exposure to. So, I had to pave my own way. Ladies in these companies need to reach into the organization and provide support as well as model what it can be to be a successful engineer without giving up your identity. You don’t have to conform to male stereotypes to be successful. And there needs to be male allies who will speak up for them. If a woman’s voice is getting
run over by men, the male allies need to call that out and move attention back to the woman.”
Studies show that when women advocate for themselves, it’s not accepted as widely as when men advocate for them, which is unfortunate, but for whatever reason, it appears to be true.
“Also, management needs to ensure their women engineers get good assignments and work in ways that contribute to the organization. I know when I was in engineering, I worked on many special projects that were beyond the technical aspect of the job. I helped put in a mentoring program. I helped some of the male engineering leaders who were technically astute but had people issues.”
Corporate management has work to do. The traditional pathway to managerial or supervisory roles is so male dominated in perspective that people forget about the people issues. “Some people should never be a manager, even though they’re technically brilliant,” notes Miller.
“Some people should absolutely go up because they have better people skills.
Final thoughts
Miller advises women who find engineering rewarding, but frustrating, to focus on two things. “First of all, develop strong relationships within the organization regardless of people’s gender. I had a lot of amazing male coaches, male mentors, male bosses along the way who are not misogynistic, or just who are amazing leaders. So I don’t want to characterize what I said as being all females have this and all males don’t. It doesn’t work that way.
“And when you’re problem solving, make sure you go to the root of the problem, sort emotion from fact and go where things are happening and you’ll get better results. And the results will come. Let them speak for themselves and you’ll be just fine.”
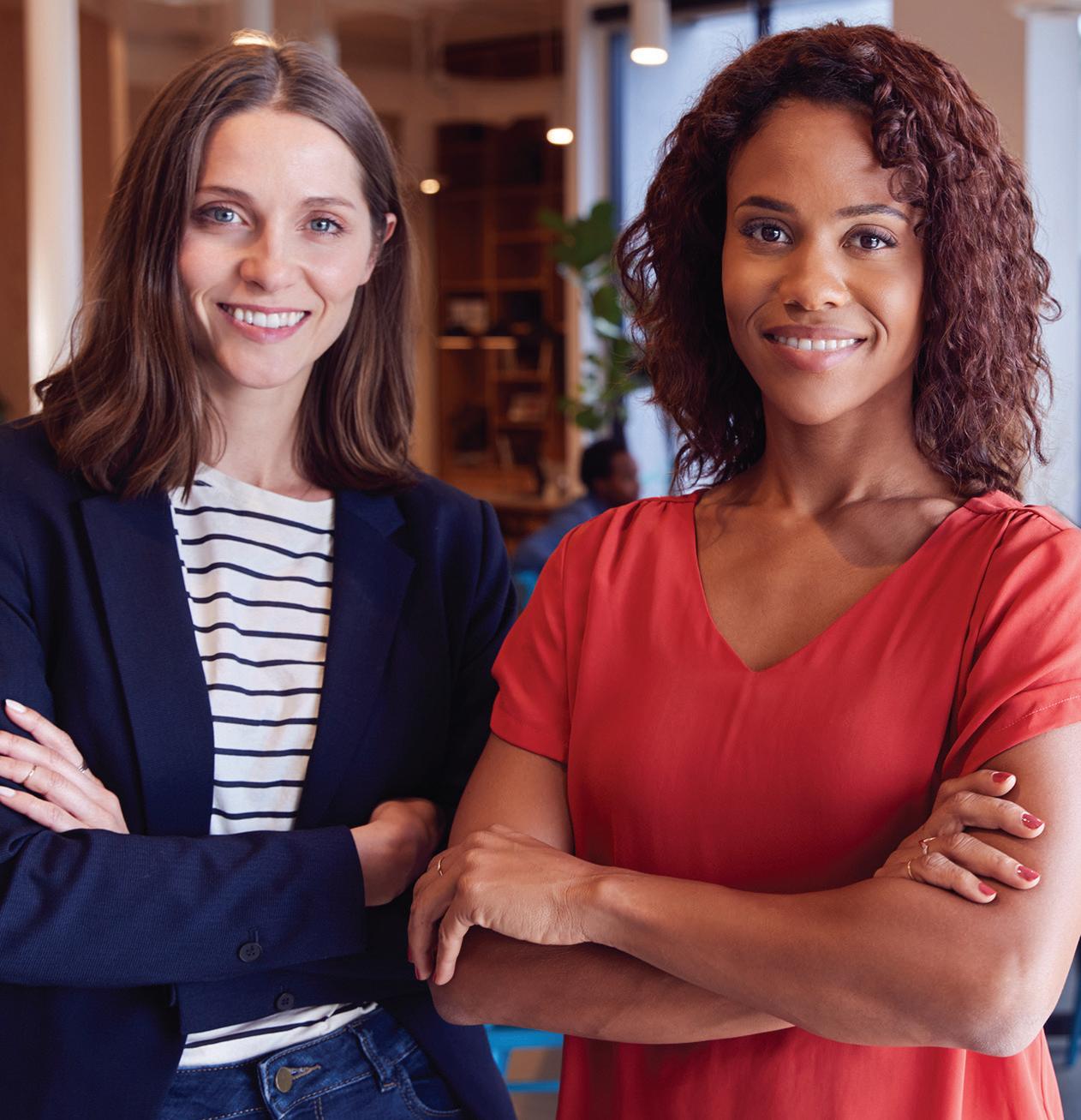

A lovelife-long of engineering
Meghan Olds’ journey with engineering began in elementary school. Encouraging young students to explore their creativity, the school offered an accelerated program that included competitions focused on invention. Thus, when she was in fifth grade, Olds put her problem-solving skills to the test in one of these competitions and created a floor cleaning mop; think of today’s Wet Jet mop that many people use today as an example.
Leslie Langnau • Senior Contributing Editor“I took my mom’s mop, drilled holes in the bottom, Velcroed the water bottle to the handle, and used a tube to run the water bottle to the sponge portion of the mop where I drilled the holes,” said Olds. “I then presented it as an invention that you can put any cleaner you would like in the water bottle and mop the floor with ease.”
Education at her school continued to fuel her love of problem solving. As with many women who study engineering, various teachers and mentors played roles in guiding her engineering abilities.

“I found mentors everywhere. There were too many to count for me to name just one or two,” said Olds.
She found all the science classes interesting. It helped that all of her teachers in chemistry, physics, and calculus made the classes and learning fun. “The science and math teachers seemed to have the best sense of humor,” she said. “I would advise young female students to embrace all the people around you while you’re young. Be curious and follow what ignites your passions.”
Meghan Olds
Director of Operations, Powder Atomization, Oerlikon

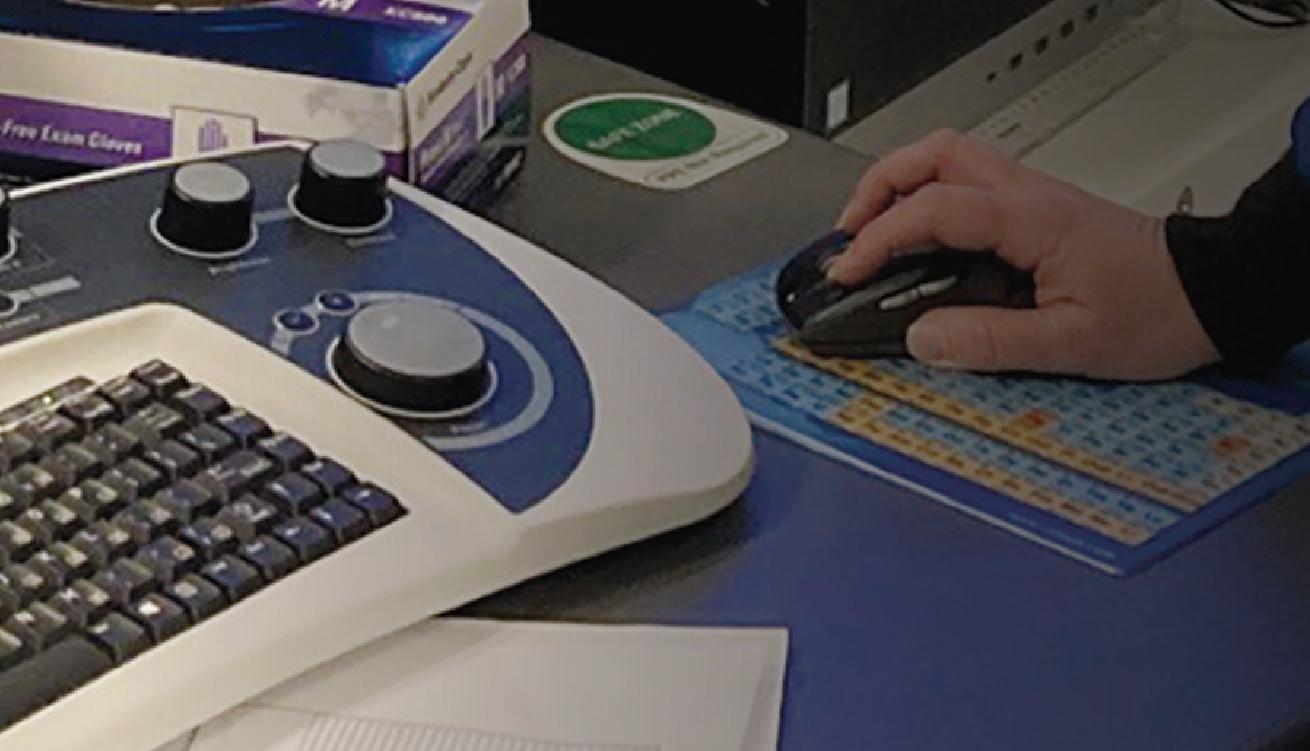
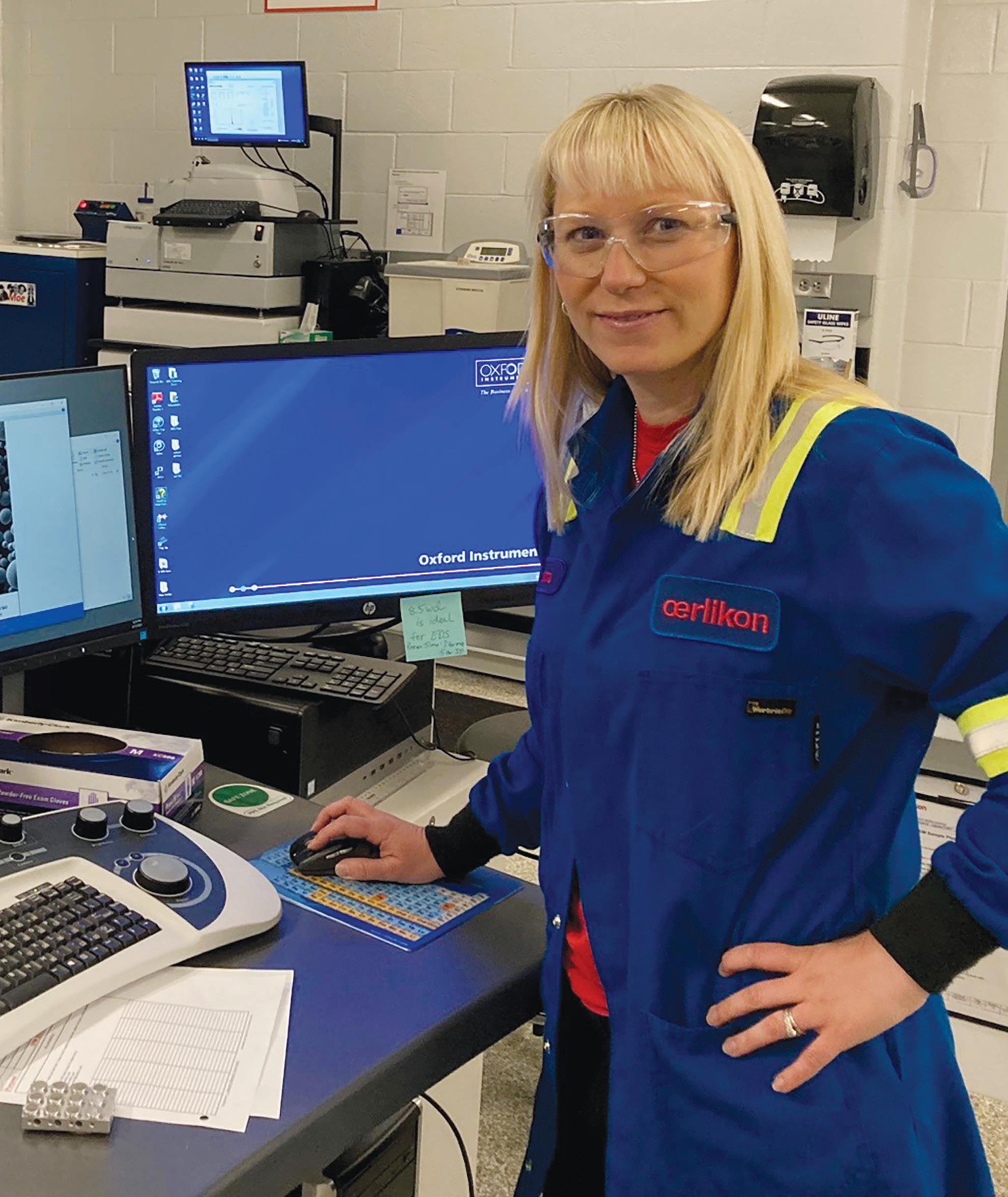
BS, Materials Science and Engineering, University of Michigan MS, Materials Science and Engineering, University of Dayton
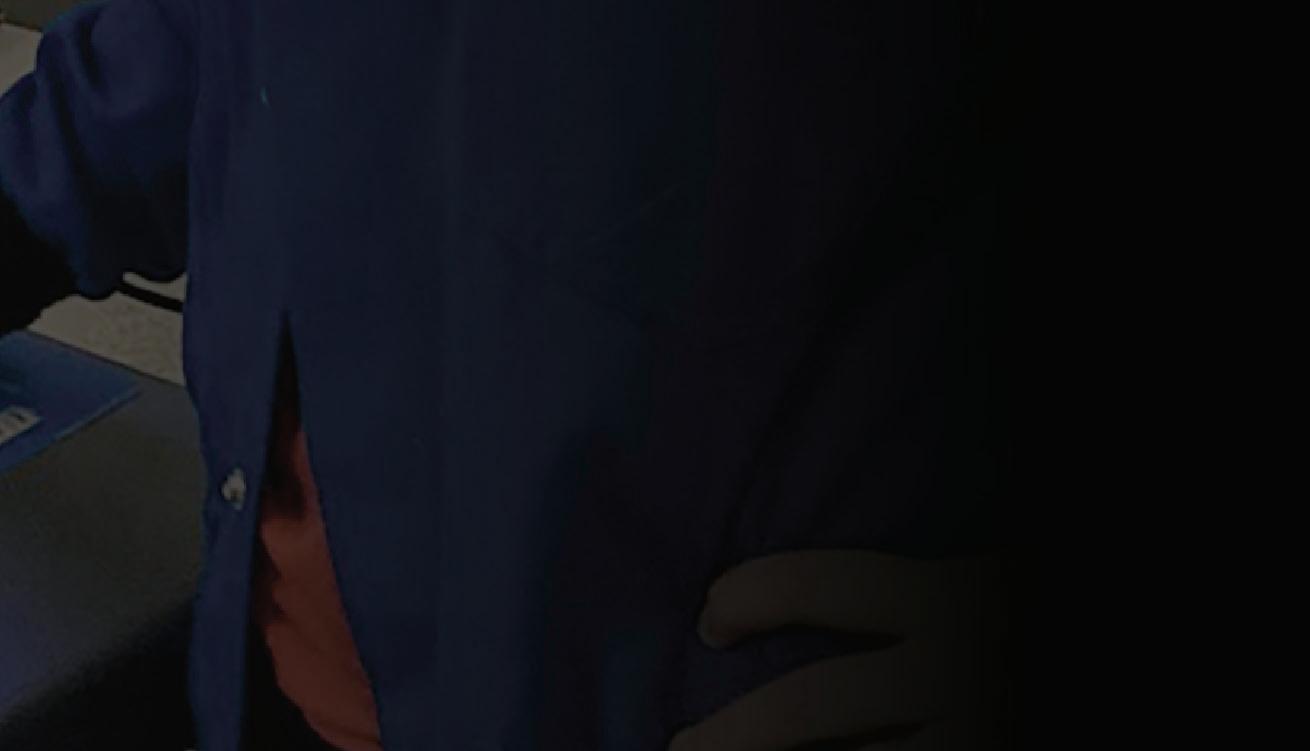
When I went into leadership positions, I realized my favorite part about engineering is uniting a team together to create a solution to a problem. Our teams are filled with many skillsets and perspectives. It is always beautiful to see how a diverse team can solve complicated problems with often simple approaches.
Throughout her schooling, Olds had a number of opportunities to problem solve and build. “I continued to love to build items whether with Legos or other materials for school projects,” she said.
Then in high school, she discovered an area that would become her career.
“I discovered Materials Science & Engineering as a junior at an engineering camp at the University of Michigan. I found that I wanted to dedicate my career to making new materials and learning about the manufacturing processes.”
Mentors continued to play a role in her education. “At the University of Michigan, my classmates inspired me,” she said. “I even married one of my classmates from my Materials Science & Engineering undergraduate program.”
Going professional
After college, Olds moved into her business career. Many leaders and colleagues at GE and Oerlikon helped push her forward to the next level. “Having a supportive team and network makes all the difference to having a fulfilling and successful career in engineering,” she added.
While some people think most engineers work individually, Olds finds her engineering efforts are highly collaborative.
“When I went into leadership positions, I realized my favorite part about engineering is uniting a team together to create a solution to a problem. Our teams are filled with many skillsets and perspectives.
It is always beautiful to see how a diverse team can solve complicated problems with often simple approaches.”
Most engineers enjoy a few aspects of their jobs more than others. However, Olds finds aspects to appreciate in all engineering areas that impact her field.
“There are so many engineering disciplines that there is not a part I
don’t appreciate or like,” she said. “I may enjoy the process engineering side, but 100% appreciate the value of programming and controls engineering. When we have an issue on a piece of equipment, we get the right expertise to resolve it.
“Plus, I love introducing new products and processes. I enjoy the design of experiments and structuring specifications so they are both profitable and manufacturable.”
Bragging rights
When it comes to accomplishments in her engineering career, Olds is most proud of helping start up a new facility in Plymouth, Mich. She became part of the start-up team when she joined Oerlikon in 2017. This facility was built to make metal powders for additive manufacturing and advanced coating applications.
“When I hired into Oerlikon, the foundation was just poured,” she said. “I was the Quality Manager and worked to start up the lab and get the site AS9100/ISO9001 certified. In just under one year of our opening date, we passed our AS9100 audit with no findings. The entire team worked hard to build production processes that were compliant with an aerospace quality management system. As we continued our journey, I added engineers to my team and then was promoted to the Director of Operations in 2020.”
The last two years have not been easy on any business and have brought unique challenges to everyone. Olds received her promotion just as many states and businesses were shifting to a workfrom-home model to prevent the spread of the Coronavirus, which brought a new set of challenges, but which also led to additional accomplishments.
“We had to balance the uncertainty our customers were facing and strategically think about how we navigate forward for the
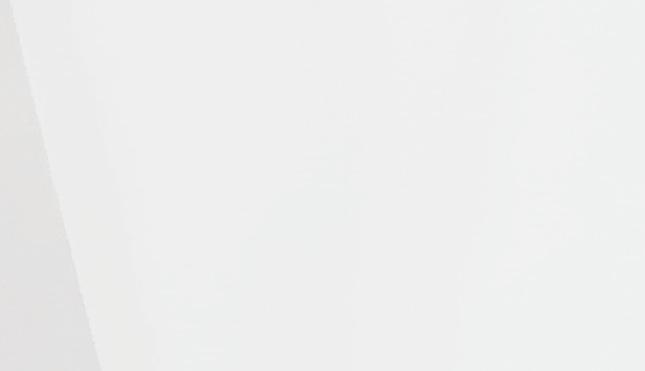
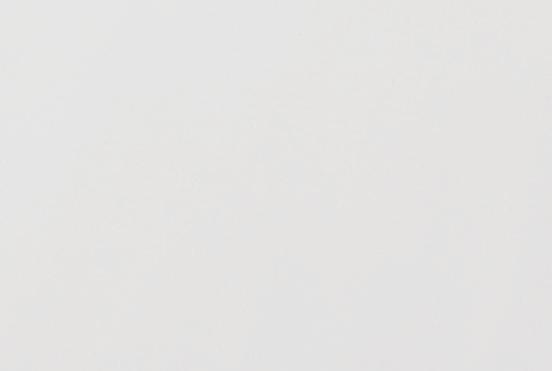
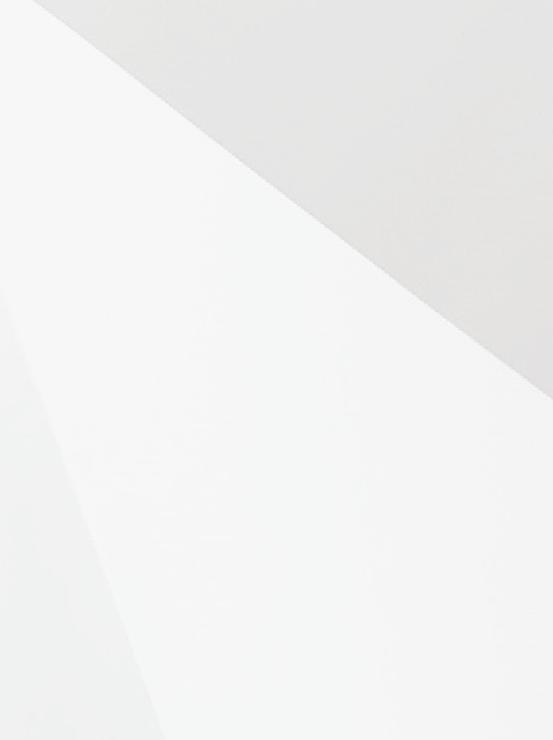
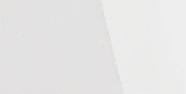
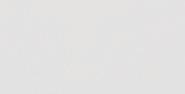


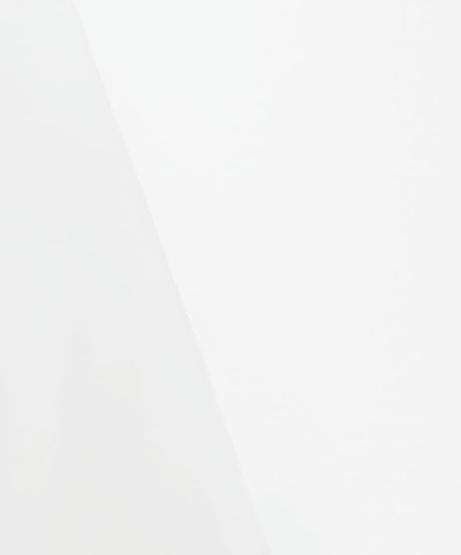
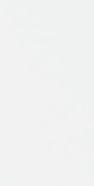
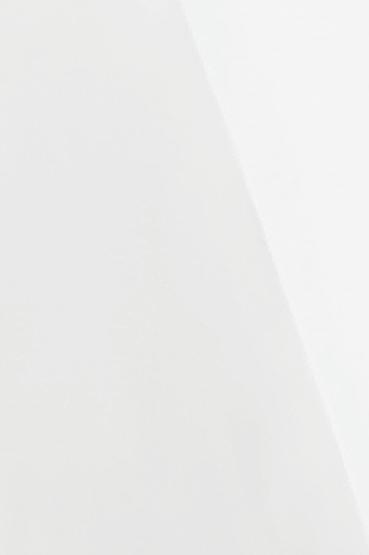
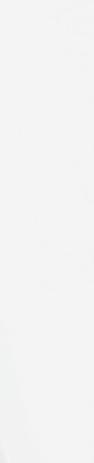
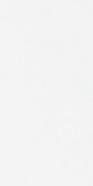

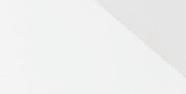
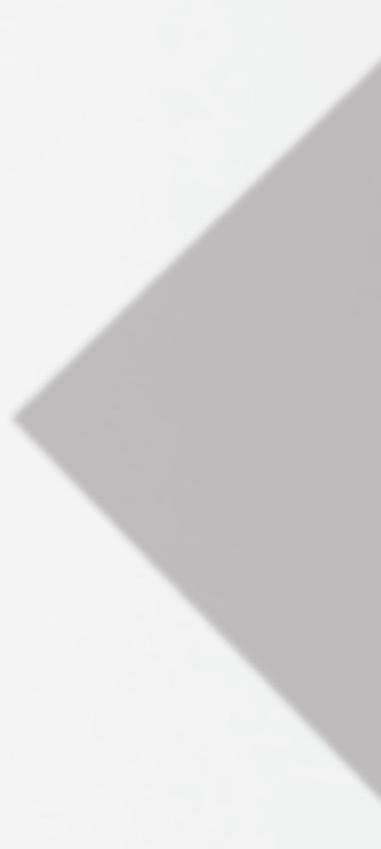

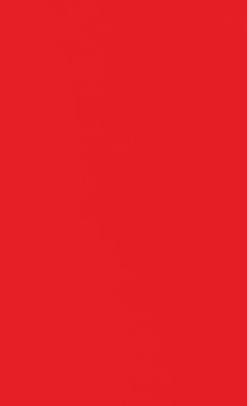
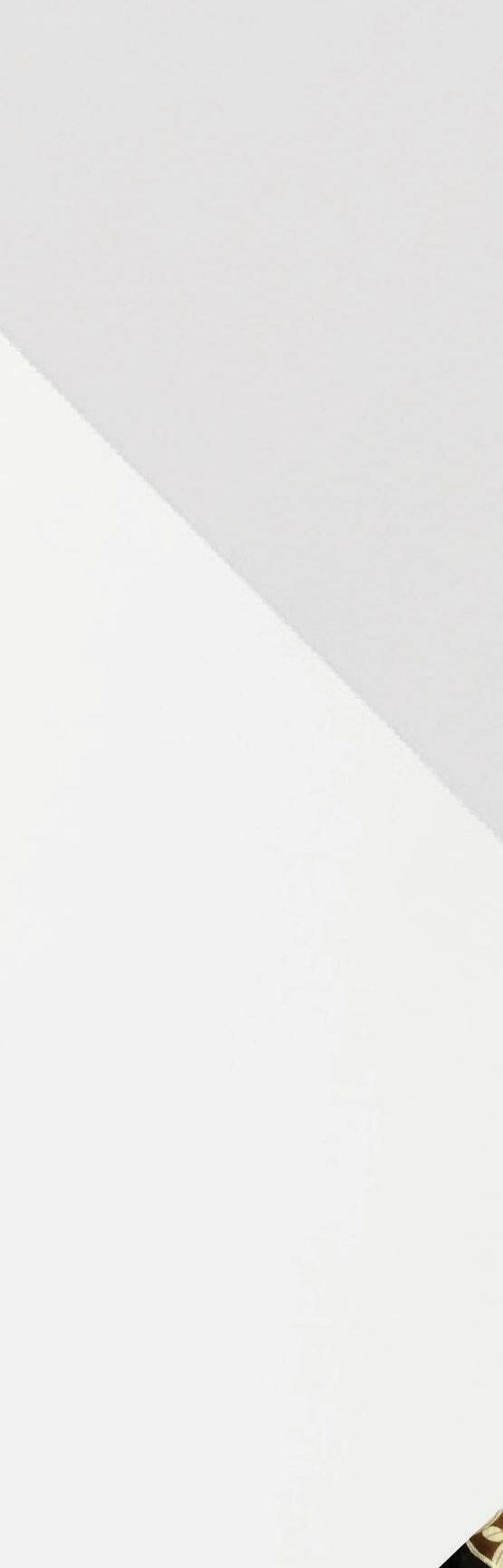


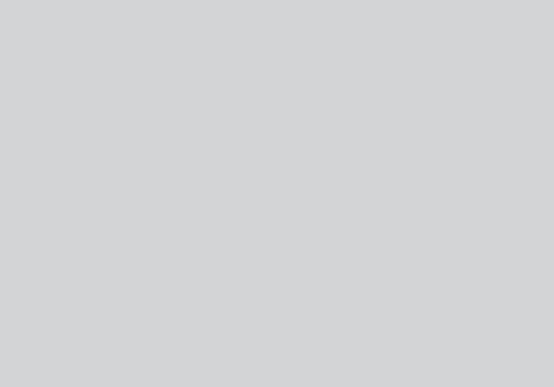


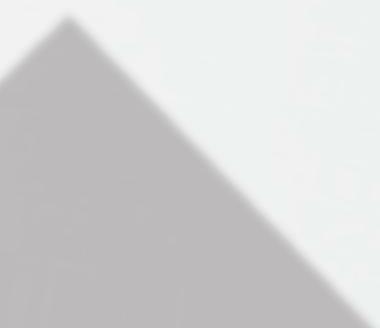
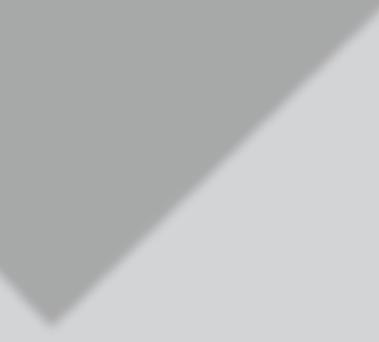

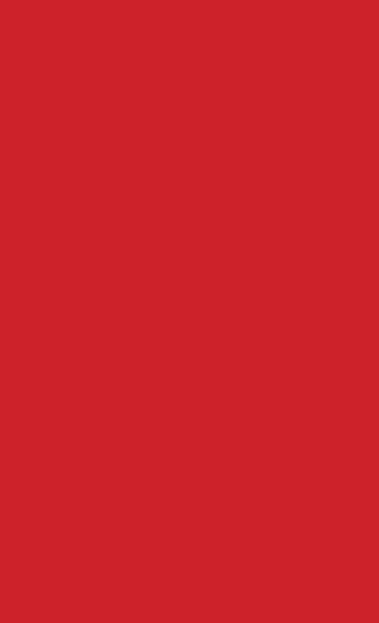
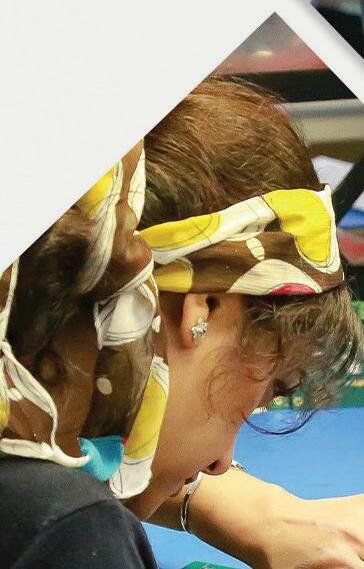





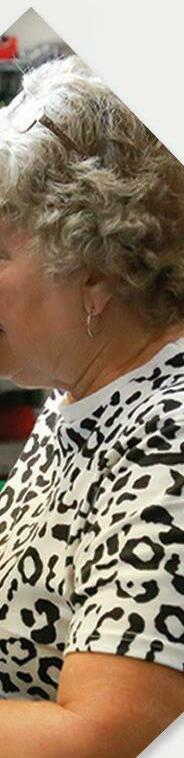
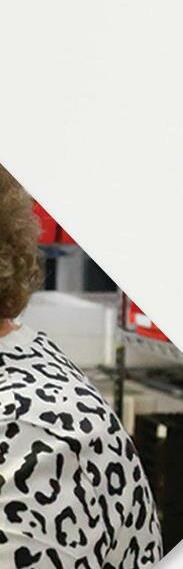
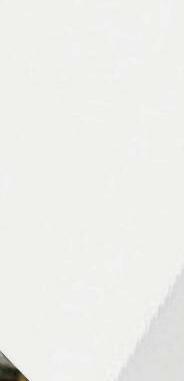

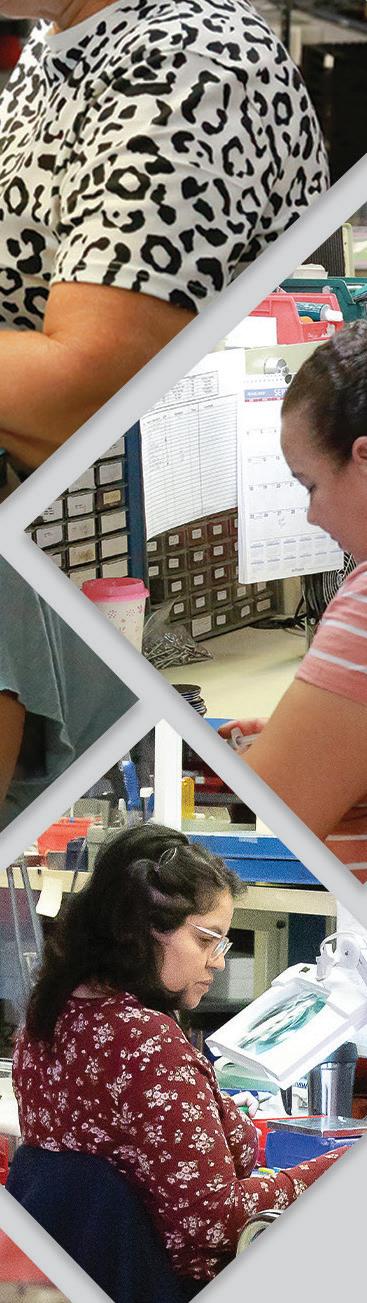


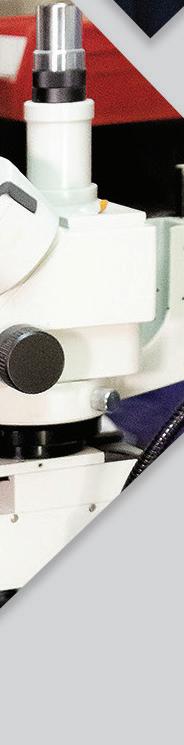
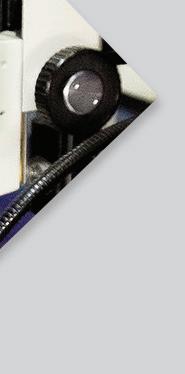
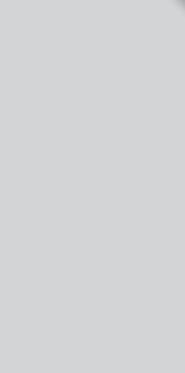


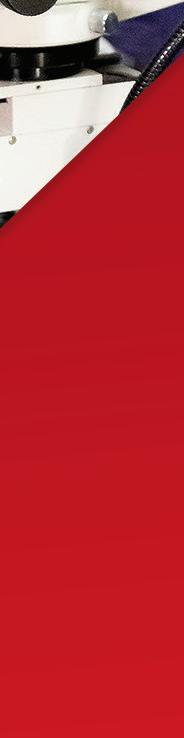
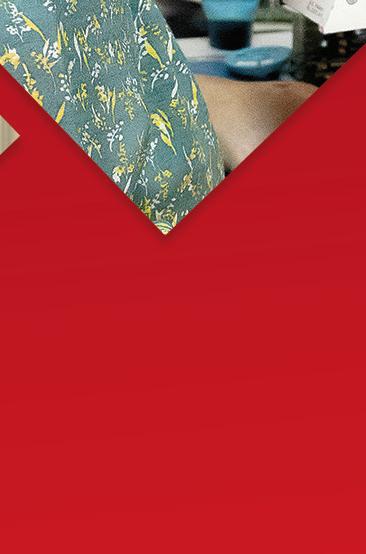
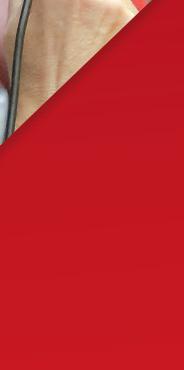
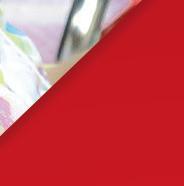
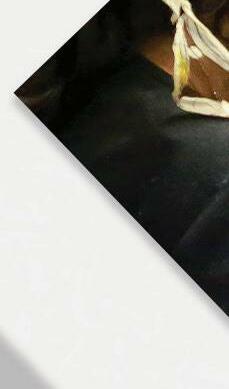
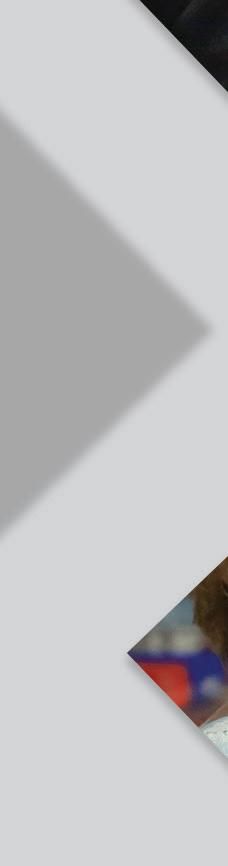
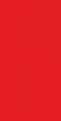
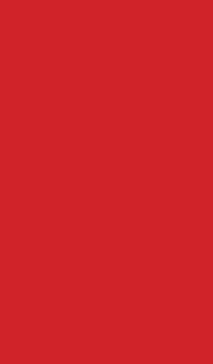
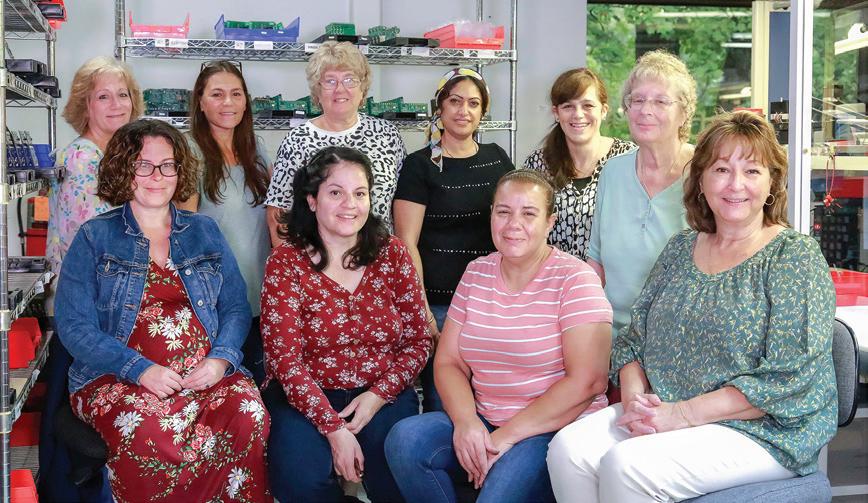
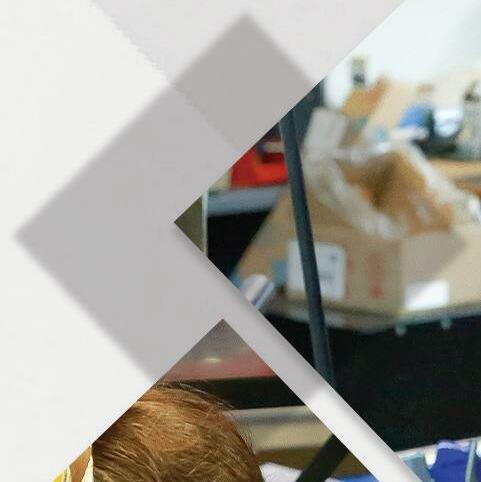

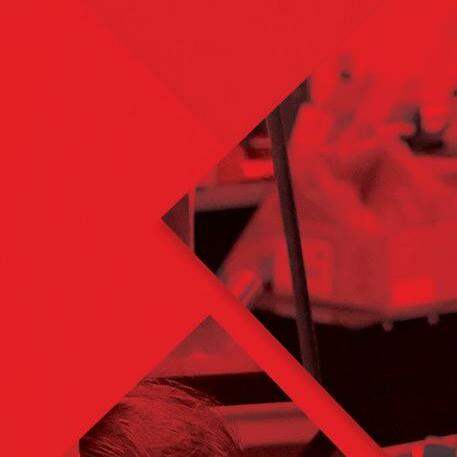
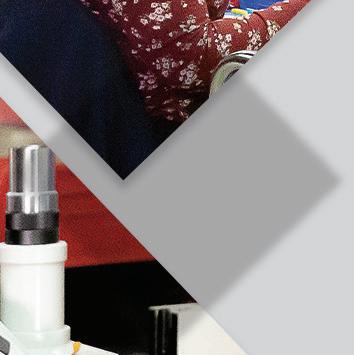
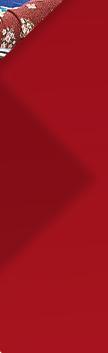
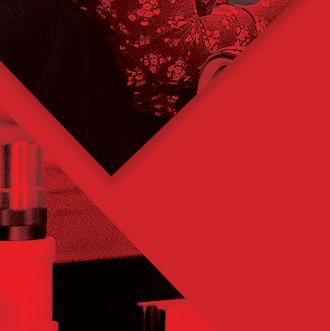
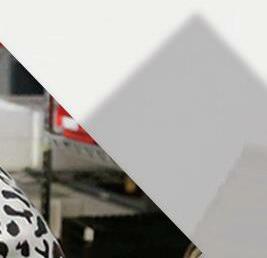
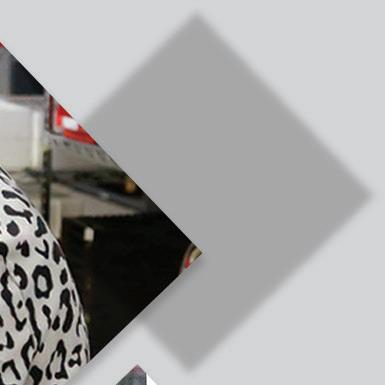
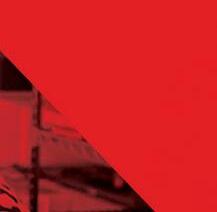
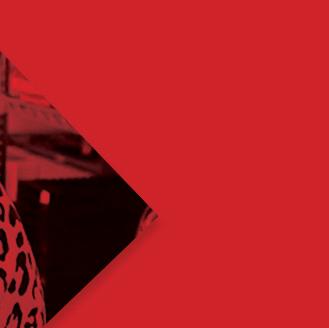
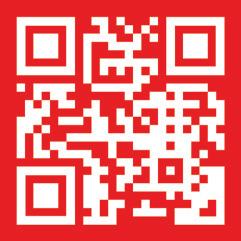
future of the site during that time,” she said. “We were able to qualify a handful of new product introductions that helped strengthen our product portfolio. And by the end of 2020, we were stronger than ever as a team, but also stronger from a cost standpoint. We ended up winning the Metco Team award with our Troy site based on our collaboration and savings for Oerlikon.”
Leading by example
A common skill among women engineers is the ability to work in or lead a team of fellow professionals. For Olds, having an engineering foundation has helped her think logically about a problem, even nontechnical problems.
“I use these same fundamentals to create actions to work towards a solution,” she said. “For example, in teams, many times the root cause of issues can be because of communication. The next step is to break it into actions to improve communication. Over the course of my career, I have learned many valuable lessons, such as patience to understand the whole problem, how to build a team with the right skillsets, and to take advantage of each day.
“My first big professional project when I graduated college was my six-sigma project on inertia welding,” she added. “At that time, I was learning statistical analysis and the DMAIC/DFSS approaches. We were optimizing the inertia welding parameters for welding tubes onto case structures. I learned a lot from the engineer and technician about the welding processes. One of my favorite parts was performing the metallography on the cross-sections of the welds and organizing the mechanical testing results into a regression equation. This helped us predict parameters for joining two different or two similar materials.
“I also have a patent with a team of colleagues for designing
equipment for cleaning gas turbine blade tips in a novel way. The idea was conceived by an engineering manager, and we worked with a company to help turn this idea into a unique piece of equipment. There were many designs of experiment trials to optimize the cleaning process. By the end of the experiments, we showed feasibility of the process and presented the results to our stakeholders.”
One of the more important lessons Olds has learned is to embrace her style of management and leadership. While women engineers bring a range of talents and abilities to their leadership styles, a part of their success involves embracing their unique styles.
“I see that my style of leadership may be different than others in similar roles,” said Olds. “I have learned to embrace my style and be authentic. There are many paths to reach a goal. This is a key point regardless of gender. One factor in leadership is to create a safe working environment so you and your team can perform at your best abilities.”
Encouraging future generations of women engineers
To inspire more young women to enter engineering fields, Olds thinks it’s important to start as early as possible.
“I have a nine-year-old daughter and think about this question often,” she added. “First, I make sure my daughter knows she is capable of pursuing all her desires. Last year we enjoyed doing Science Olympiad with her school. Together we did experiments and collected data and then analyzed them. Also, at home she sees my husband and I do many home-improvement projects. I think we have to be good examples for young women around us and show them what it looks like to be an engineer. Also,
they should be encouraged to tour through manufacturing sites so they can visualize themselves in these environments at a young age.”
For Olds, there are no wrong choices. She believes it’s possible to make any choice the right choice.
“Throughout life there are many choices,” she said. “Where should I go to college? Where should I work? What city should I live in? When should I have kids? I have learned with questions like these, we make the best choice with the information we have at the time. Then once we commit and put our energy into the decision, we make it the best choice.”
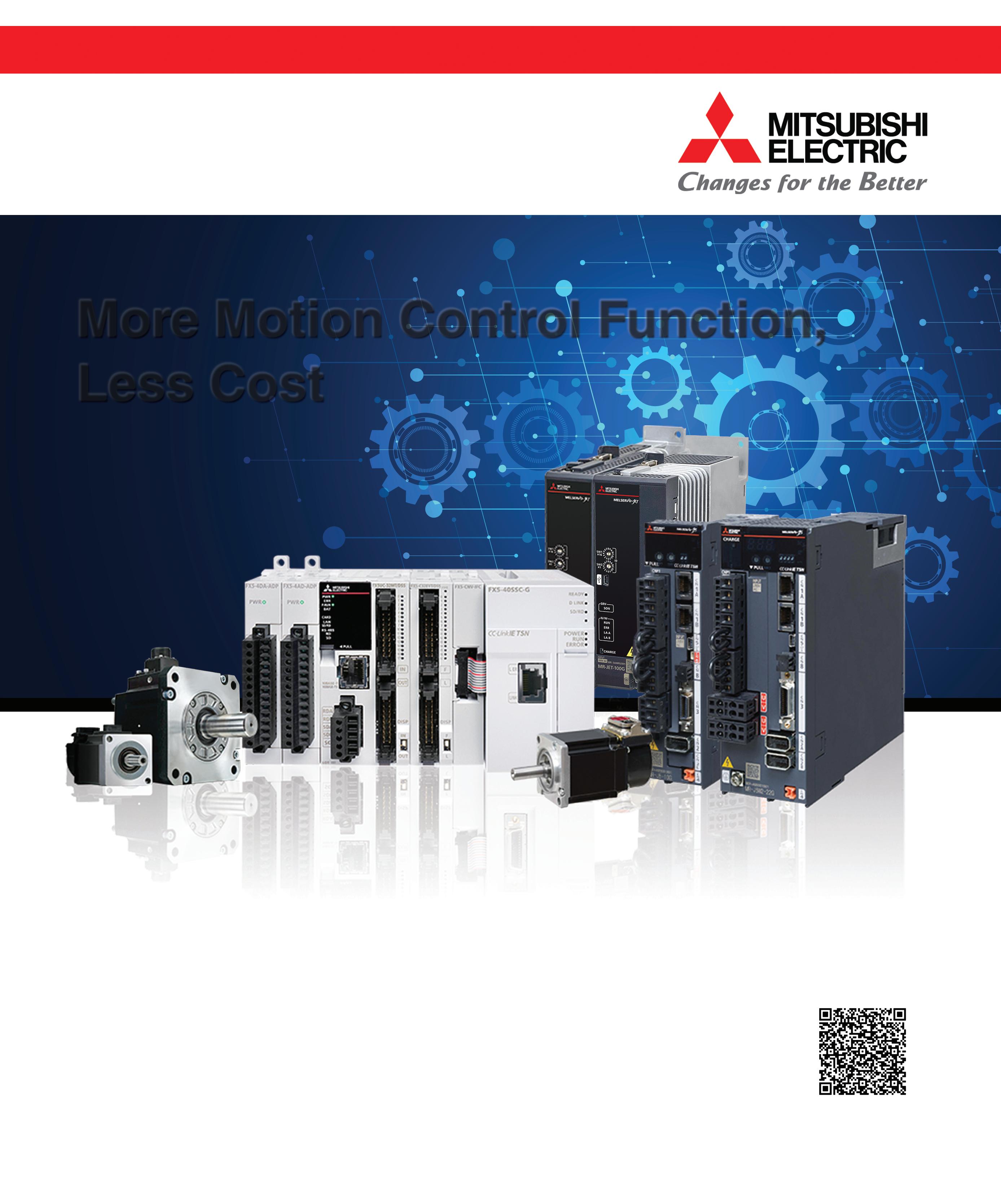
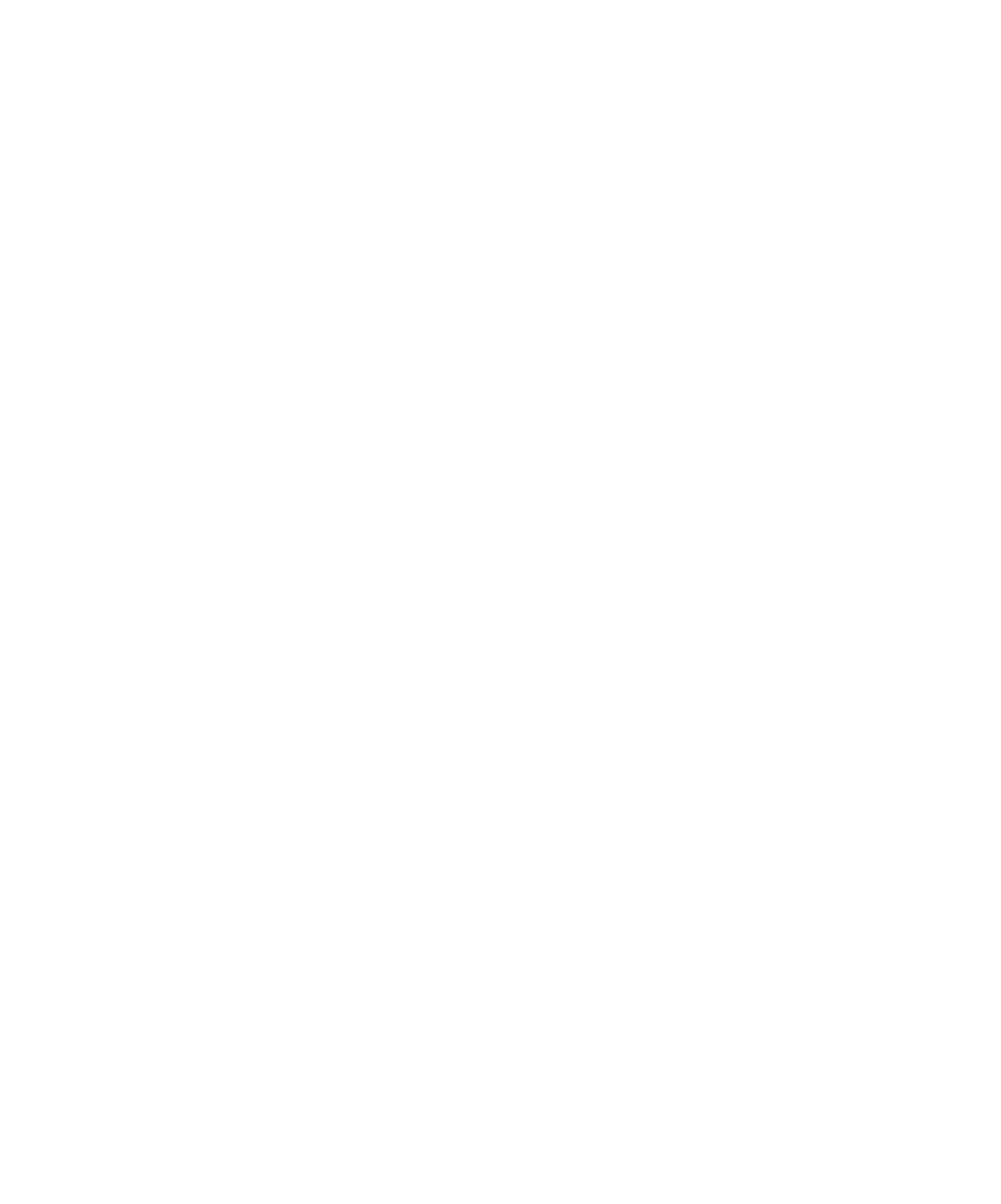
springboard to a range of careers.
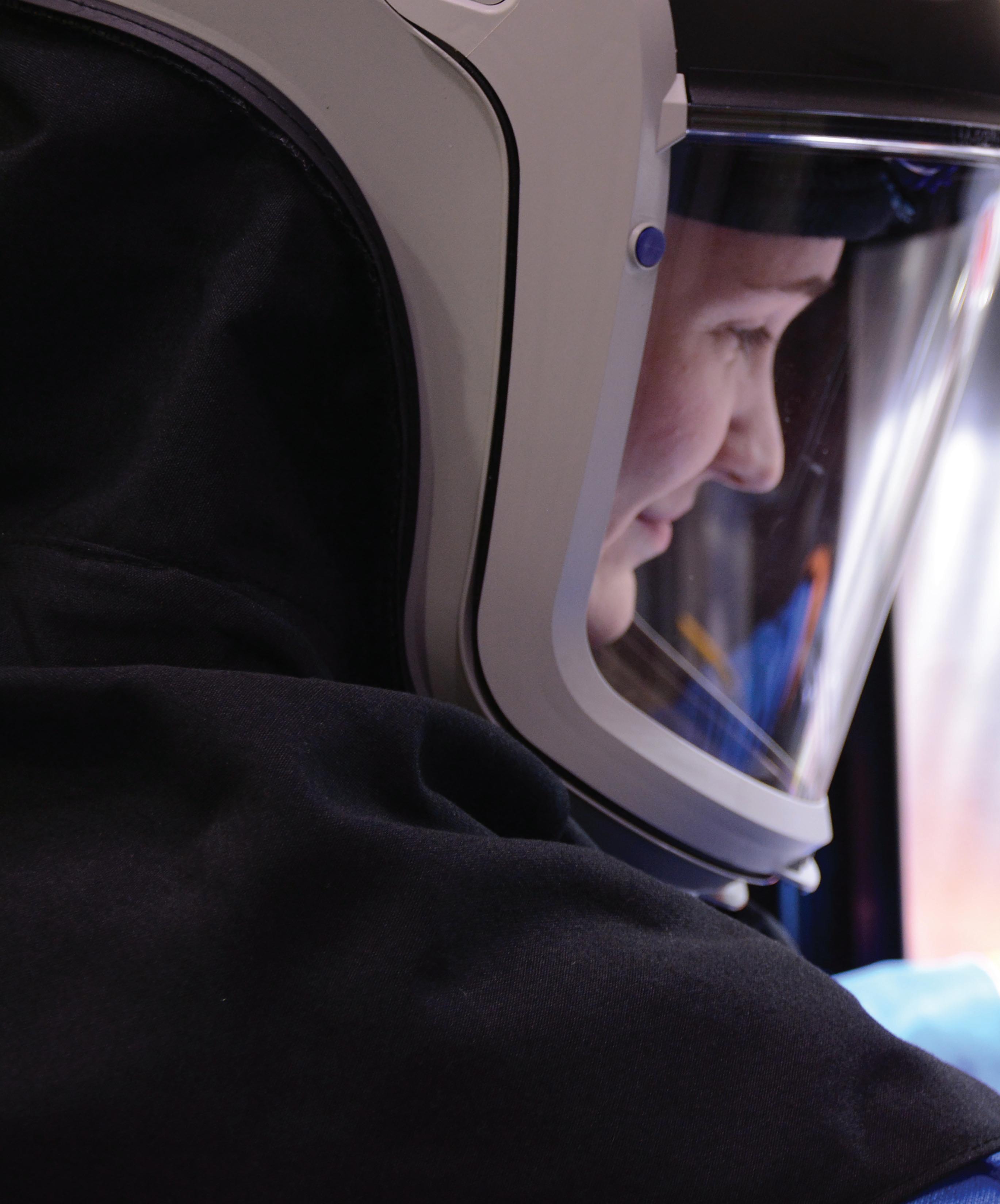
Kate Schneidau
Inspired by engineering
For Kate Schneidau, the idea of becoming an engineer began early, “right after my princess and racecar driver stages as a child,” she says. “I always wanted a field that would allow me to be creative and problem solve.”
Schneidau comes from a family of engineers, as her older sister, father, and grandfather are also engineers. Her mom is a teacher. Her early exposure to engineering began with helping her dad and grandfather work on cars, which built a foundation of understanding tools and how to build your way to a final product.
In middle school, she could always picture herself as an engineer. “I’ve gone through phases of wanting to work on cars like my dad, who is an engineer at Ford Motor Co., build rollercoasters, be an Imagineer at Disney, and be a nuclear engineer. My dad was and still is one of my heroes.”
Stepping up
An opportunity to build her problem-solving skills came while she was finishing her graduate degree at the University of Louisville. The COVID pandemic hit, forcing a number of educational institutions to close down.
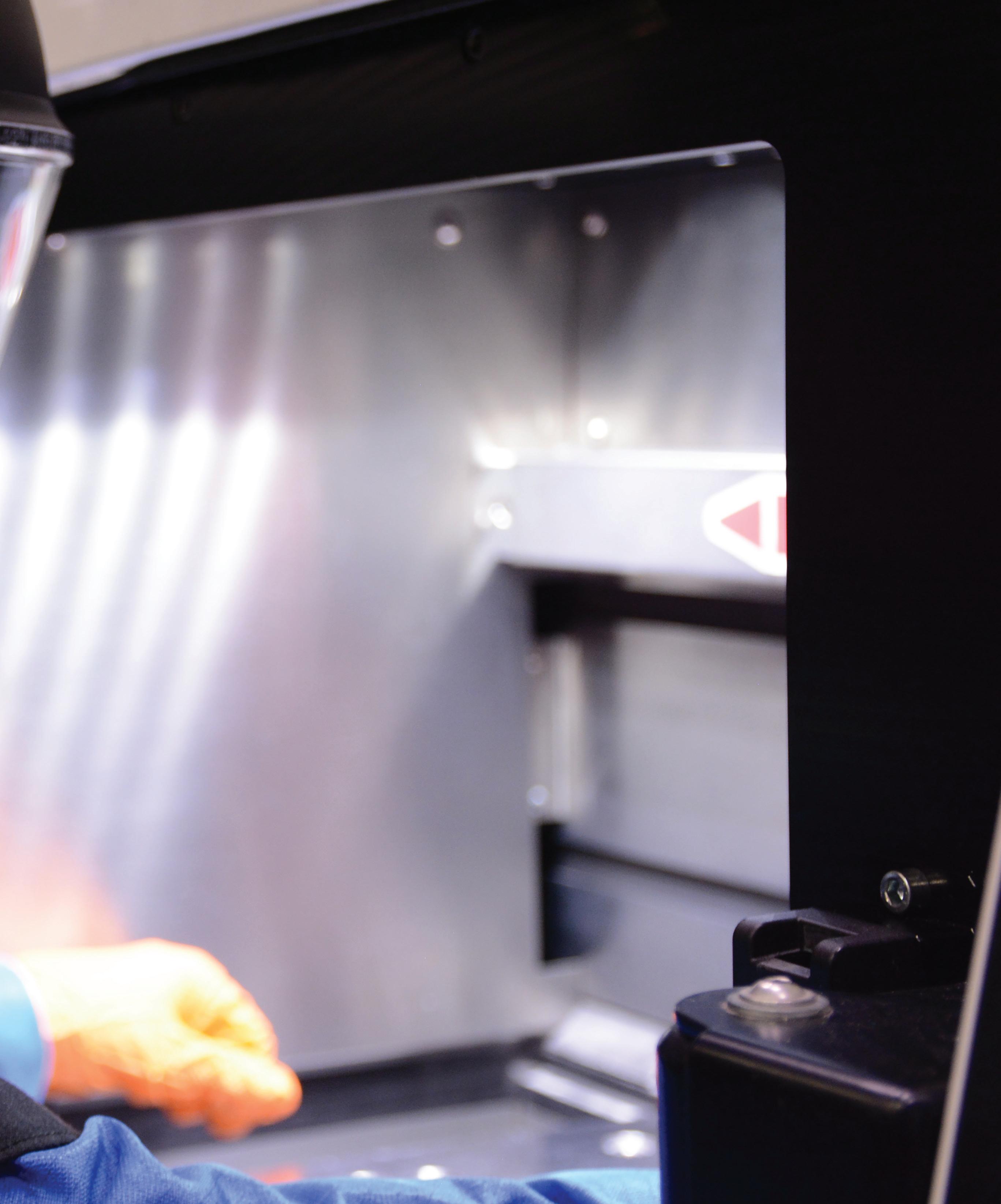
“When I was at U of L, school stopped. I had to put my thesis on hold, like other students.”

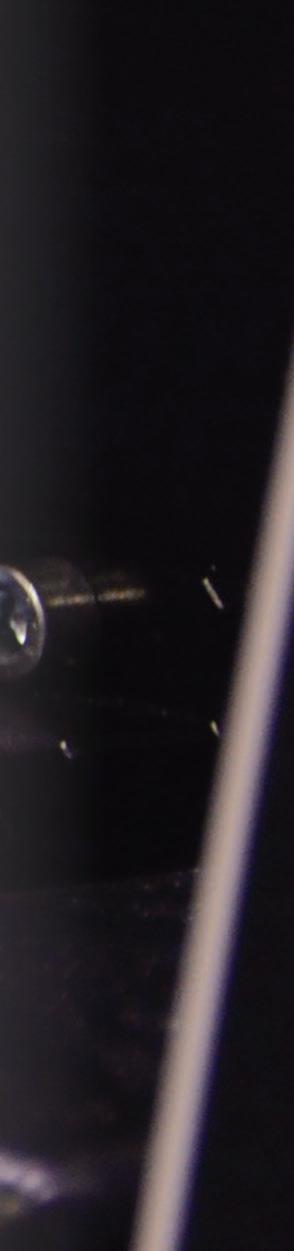
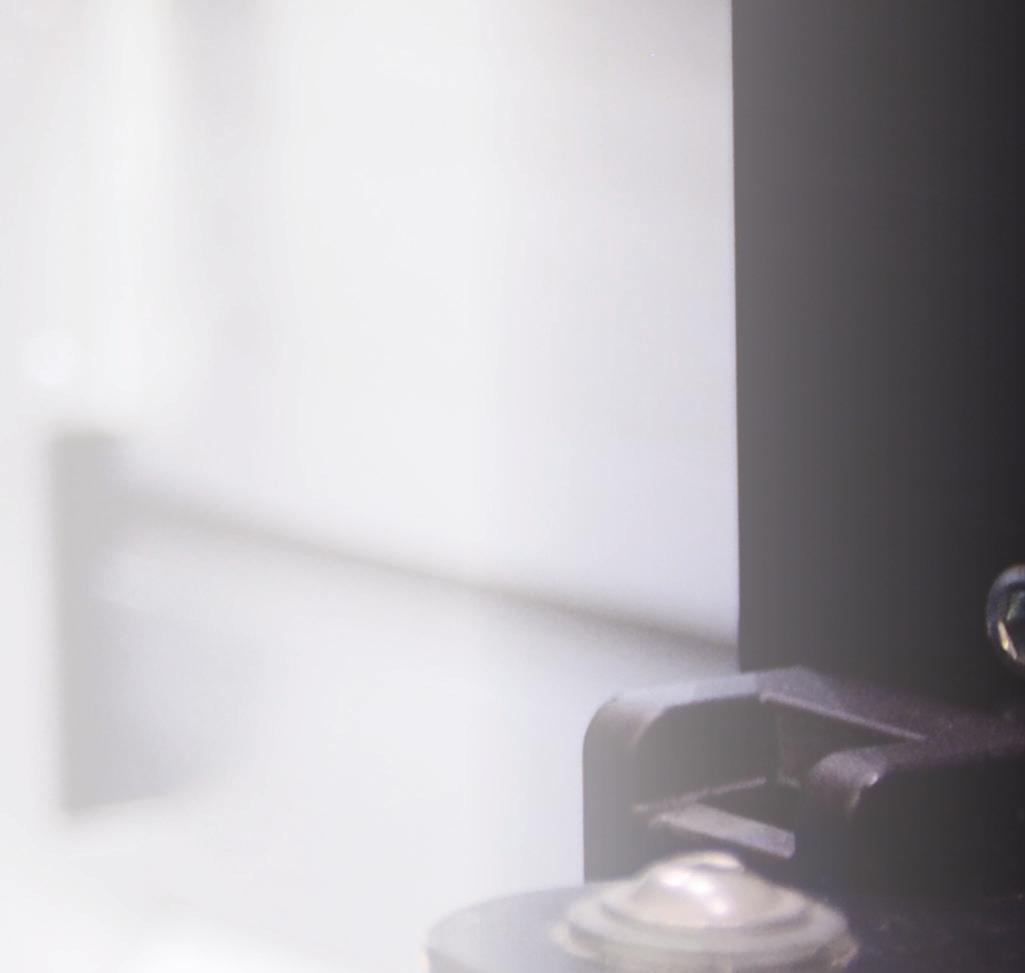
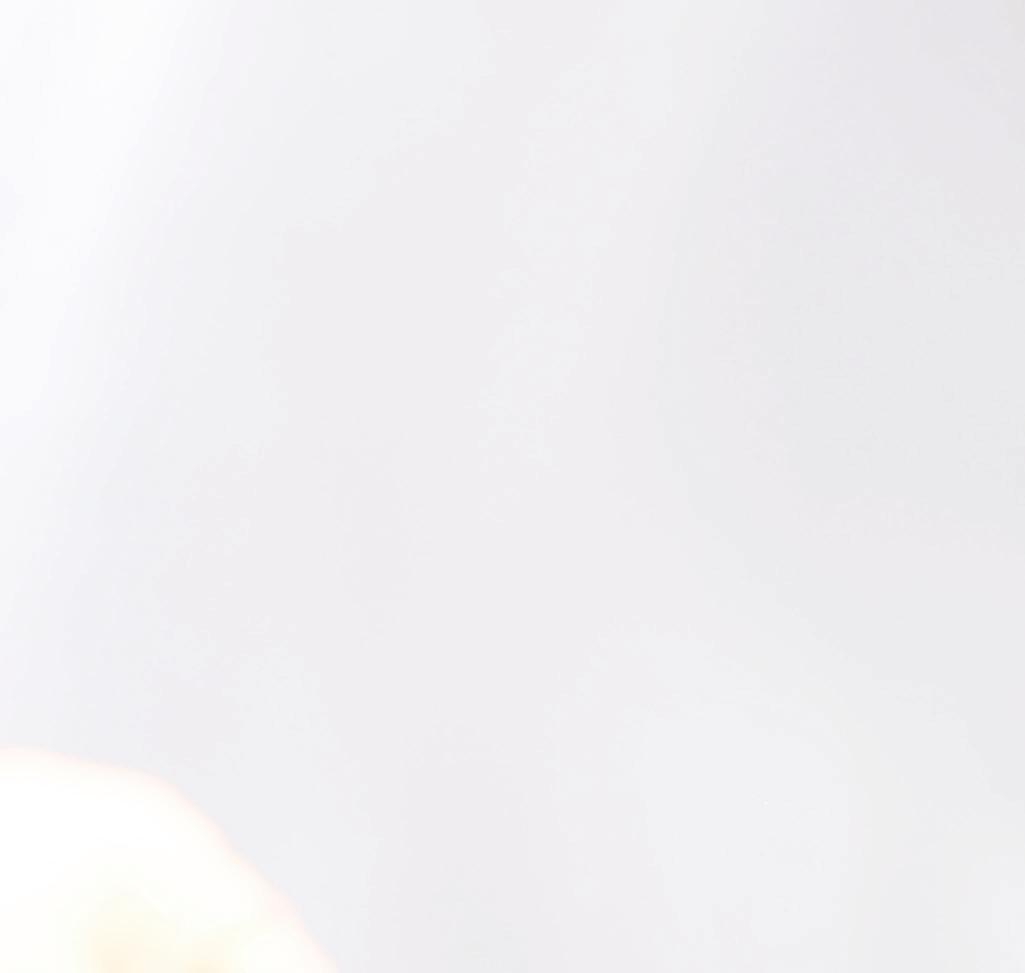
Today’s young women engineers find this field can inspire entrepreneurial ambitions.
Women in Engineering
Most of the students were frustrated and felt a bit helpless given the situation. Students were texting each other about what they could do, if anything, as they all wanted to be involved in something.
When news came out that hospitals were running out of Personal Protection Equipment (PPE), many professional engineers, also side-lined and forced to work at home, began developing PPE face shields and masks. Schneidau and many of her fellow U of L engineering students saw a way to get involved.
“Because I was working in 3D printing, we looked into how we could help,” she says. “It started with us using our at-home 3D printers printing face shield adapters which then turned into a partnership with a local injection molding house. We printed 80,000 injection molded face shields through this community. We would print and then go to the drop off sites that we set up, and drop off the shields. Then we put in place a socially distanced production line. I learned a lot about manufacturing from this because I was basically the person in charge of managing it.”
Schneidau feels she gained a lot of understanding in leadership and communication through this experience. In one example, some members on her team wanted to change how the face shields were fastened to the head band. They learned that they could not simply make a change, as operators at their service bureau taught them how such a change would affect the production process.
“This experience taught us to understand the whole production process,” she says. “To this day, it’s one of the most rewarding things I’ve ever done. And it’s also one of the most challenging things I’ve ever done. Not only did the project distract me from what was going on, it made me feel like I actually was impacting something greater than myself, and I got to meet so many
different people from all across the university. I learned a lot about being a leader and communicating with other engineers.”
As a fairly recent graduate, Schneidau is one of the young additive manufacturing engineers coming into the business world. Asked about what she likes best about this field, she finds in difficult to pick out one aspect, but she narrowed it down to innovation and community.
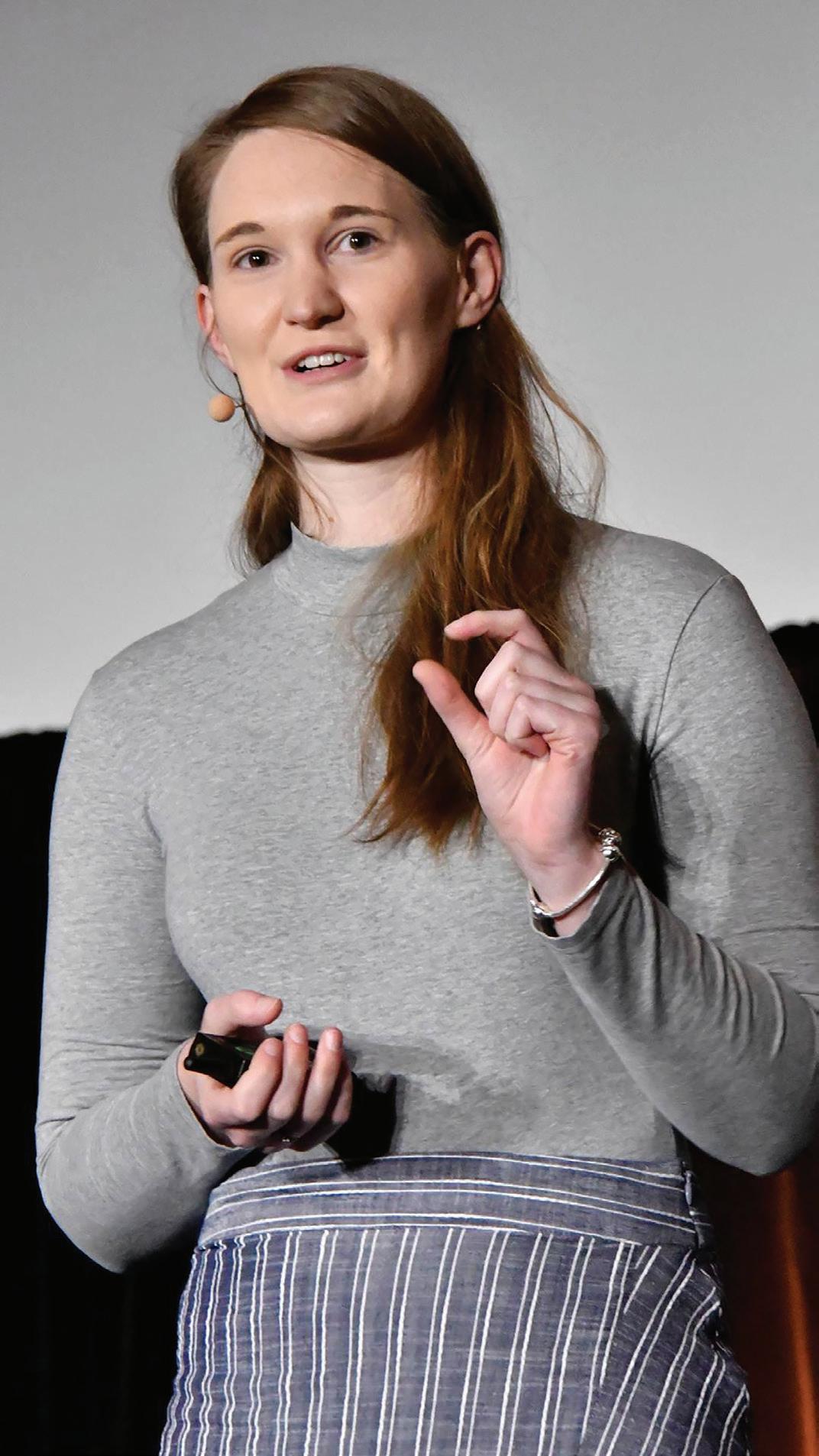
“With additive, we’re really able to express what’s going on in our brain and push the boundaries, push the limitations of what is actually possible, blending engineering and artistic approaches when you’re developing a product. That’s one of the cool things about additive is the innovative capabilities that you have.”
Schneidau was awarded the Guy E. Bourdeau Scholarship during the 2020 AMUG conference. She was able to attend the 2021 conference once the major wave of the COVID virus passed. At the conference, she found a community of like-minded engineers and used this opportunity to create a network of friends with many of the attendees.
“It’s like a family in itself. I have to say, three of my best friends within additive I’ve met at AMUG,” she said.
Building relationships
Schneidau now works at a company where collaboration efforts between coworkers are highly valued. But she’s witnessed how a lack of collaborative relationships affect men and women in the work place.
“I don’t want to put any company on the spot, but if you join a very large corporation, you’re basically working to meet specific needs. So, you’ll put your head down and just work towards the company’s goals. But what do you get out of it? How are you bettering yourself to build your own career? I have worked in a large corporation and realized it wasn’t for me. It didn’t
“The nature of design engineering has changed, to where it’s much more collaborative, thus needing strong communication skills.”
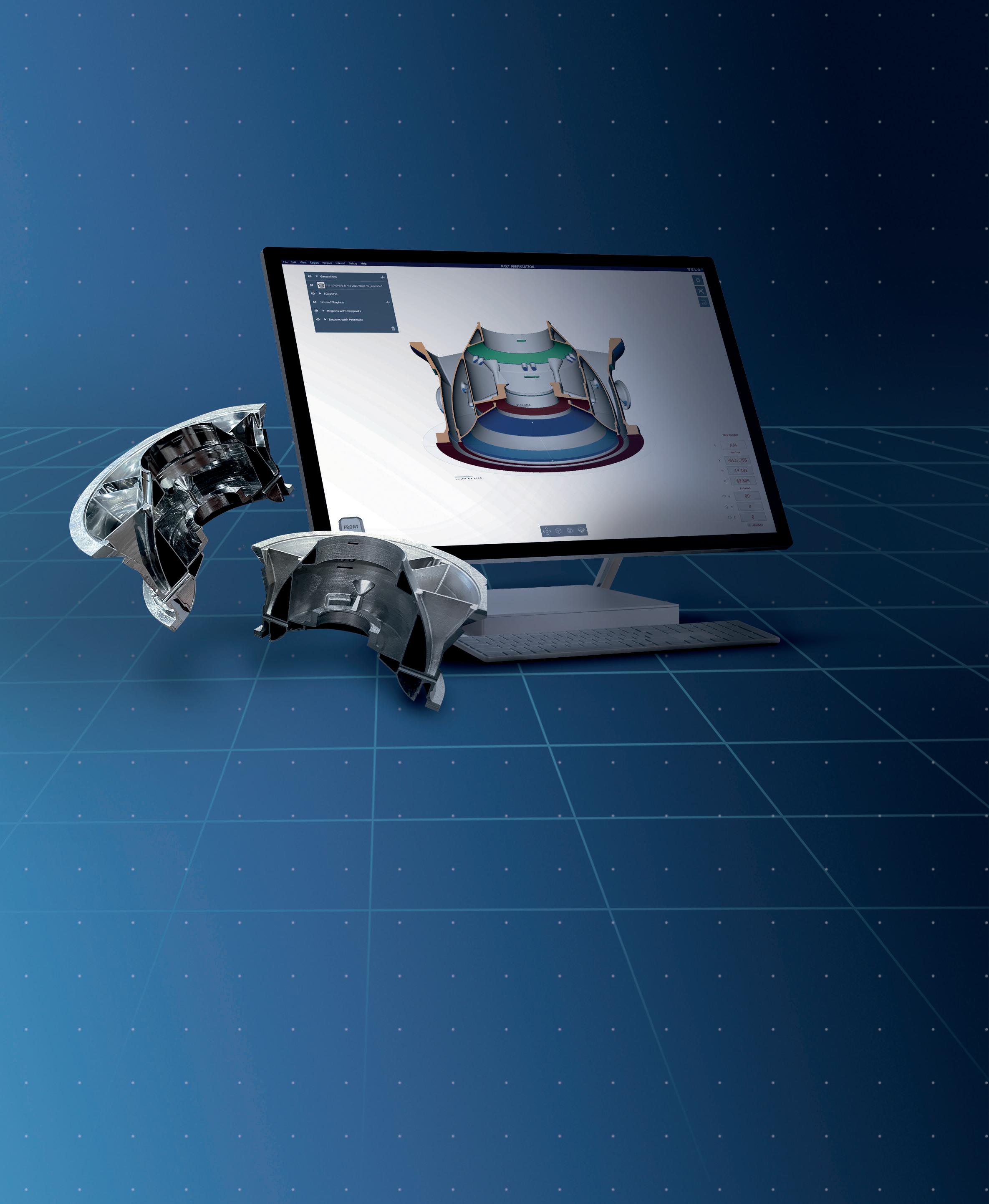

offer much room for collaboration with my coworkers to meet specific company goals,” she said.
Relationships have helped Schneidau become more open. She says she would have been considered shy as recently as five years ago. But through her journey with additive technology and the various roles she’s taken in her career, she’s learned to be more communicative.
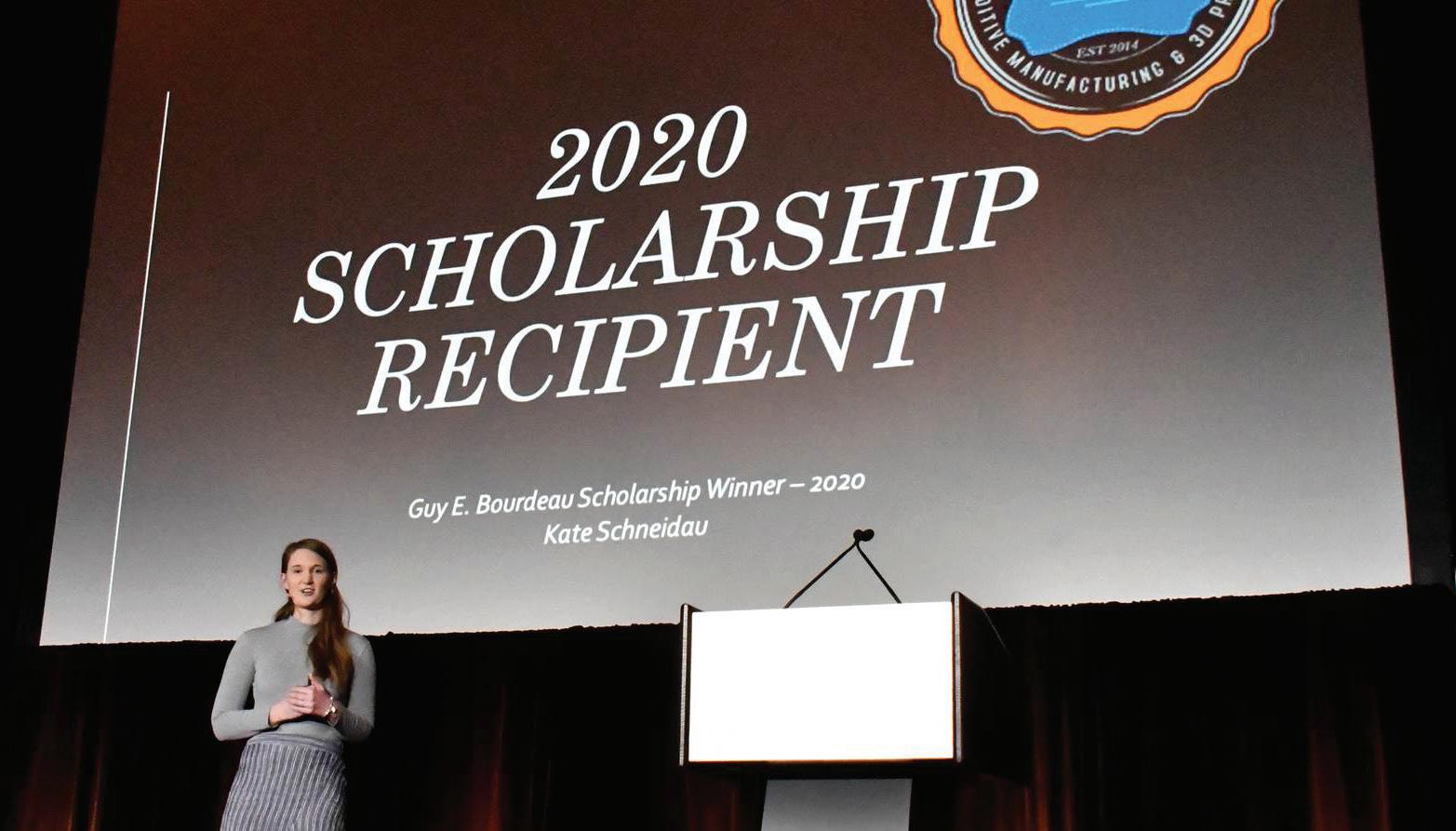
“I build relationships because I like to understand all the different scenarios. I talk to as many people as possible now. When I got into school, I realized that a lot of the other female engineers thought similarly. Communication is 100% one of the most important skills to have to work well with somebody.”
Her perspective now is that while communication issues still arise, it has less to do with the different perspectives male and female engineers bring to a design challenge and instead is “more of a managerial problem.”
“The nature of design engineering has changed,” she adds, “to where it’s much more collaborative, thus needing strong communication skills.”
Getting comfortable
Many women engineers report a number of challenges that they face in the corporate world including being taken seriously, finding growth opportunities, dealing with imposter syndrome, and trusting that they know what they know.
For Schneidau, a challenge she is currently facing, one many women engineers relate to—is trusting your gut.
“There was one issue among several recent ones that showed a common theme,” she says. “Confidence and trusting my gut. I sometimes still struggle with trusting my judgement on some projects but that’s the great thing about an engineering challenge, the constant iteration and testing of new approaches to refine and improve my own thought process. The opportunities I’ve had to collaborate with others and their different perspectives has helped, because the best engineering solutions are from a collection of experiences applied to one possible scenario.”
In Schneidau’s present position, she is one of two women in the department. However, her colleague is not an engineer — she has an artist background.
I build relationships because I like to understand all the different scenarios. I talk to as many people as possible now. When I got into school, I realized that a lot of the other female engineers thought similarly.
Communication is 100% one of the most important skills to have to work well with somebody.
TOPJOB® S MINI TERMINAL BLOCK
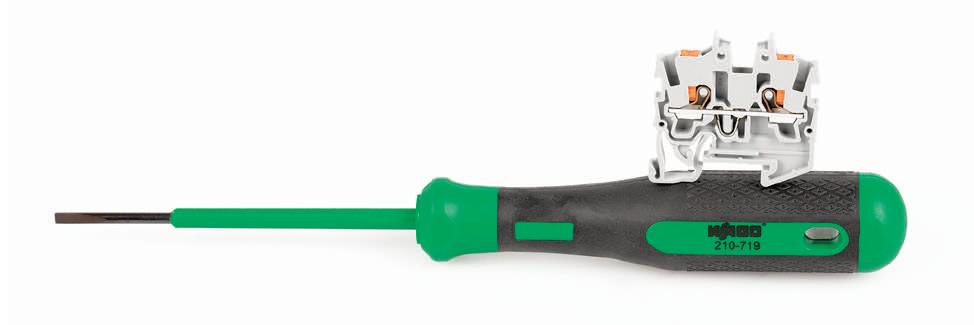
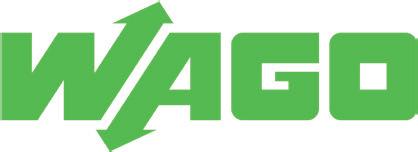
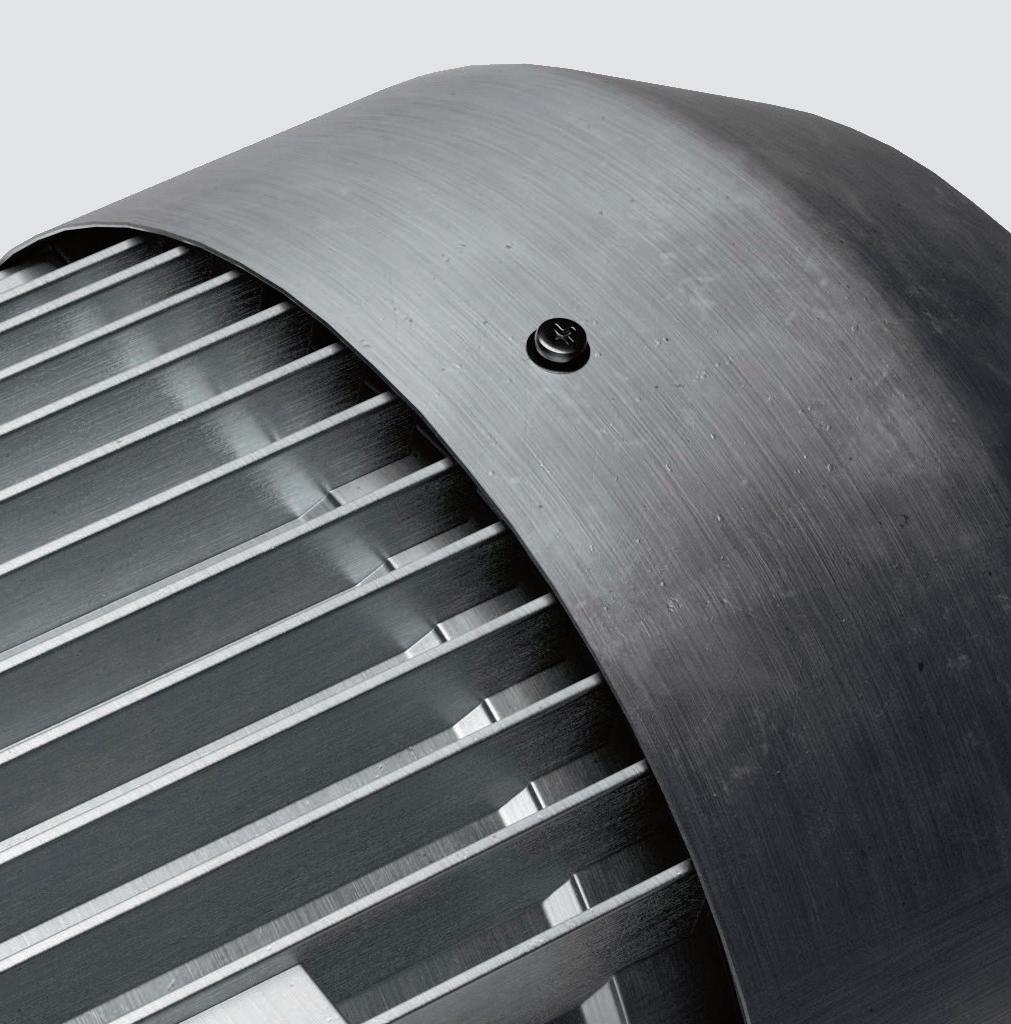
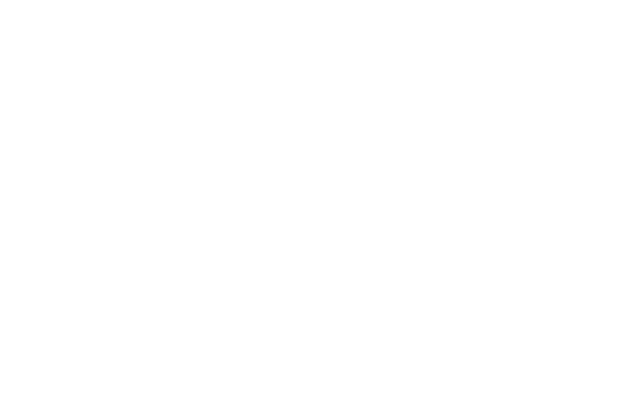

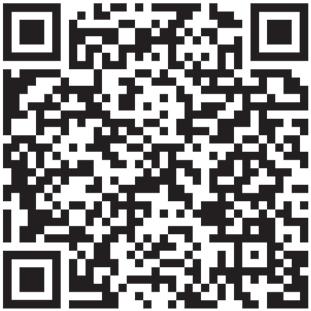
A REAL SPACE GENIUS

The compact design of WAGO’s TopJob® S Mini Rail-Mount Terminal Blocks makes them ideal for work in tight spaces. Various mounting and actuation variants are also available for maximum flexibility; allowing you to choose your Mini terminal blocks based on use and convenience. Thanks to spring pressure connection technology, they can be used in junction boxes and are also suitable for vibration-proof connections.
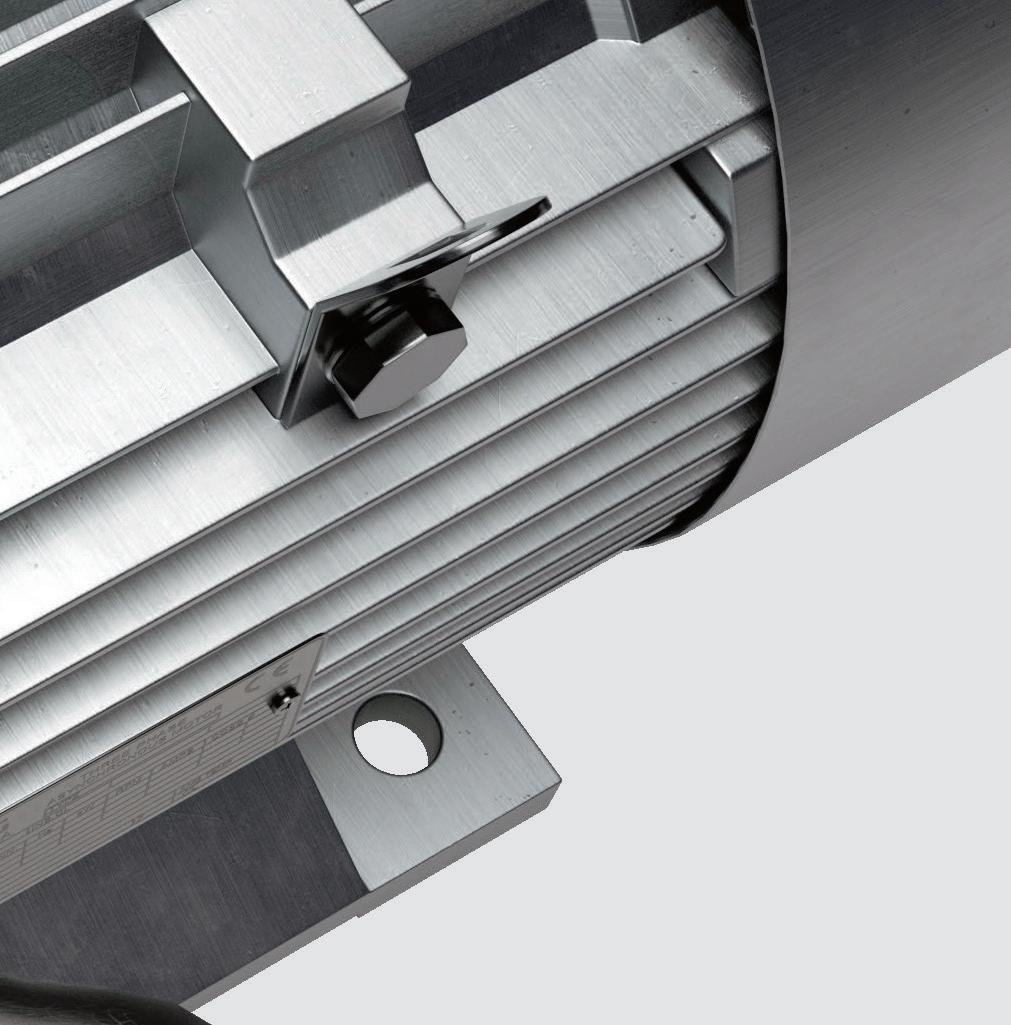
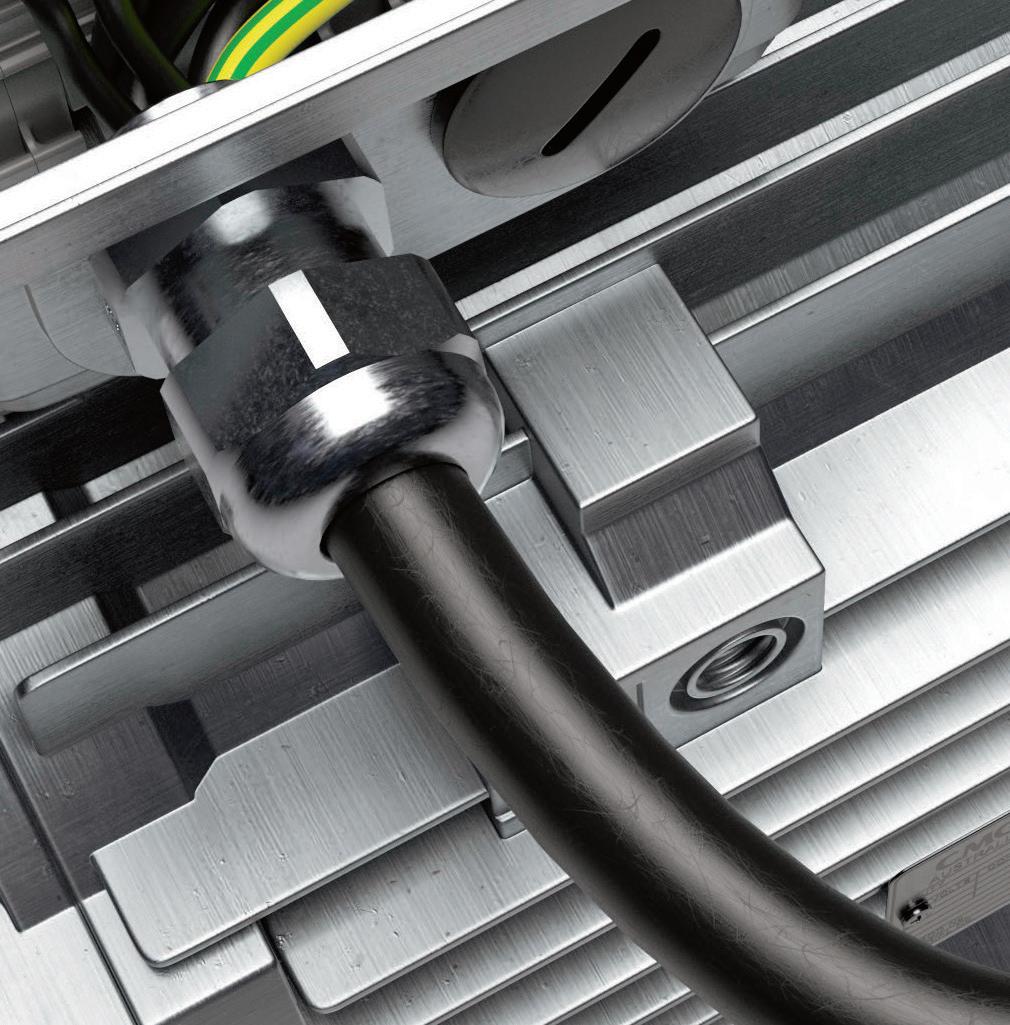

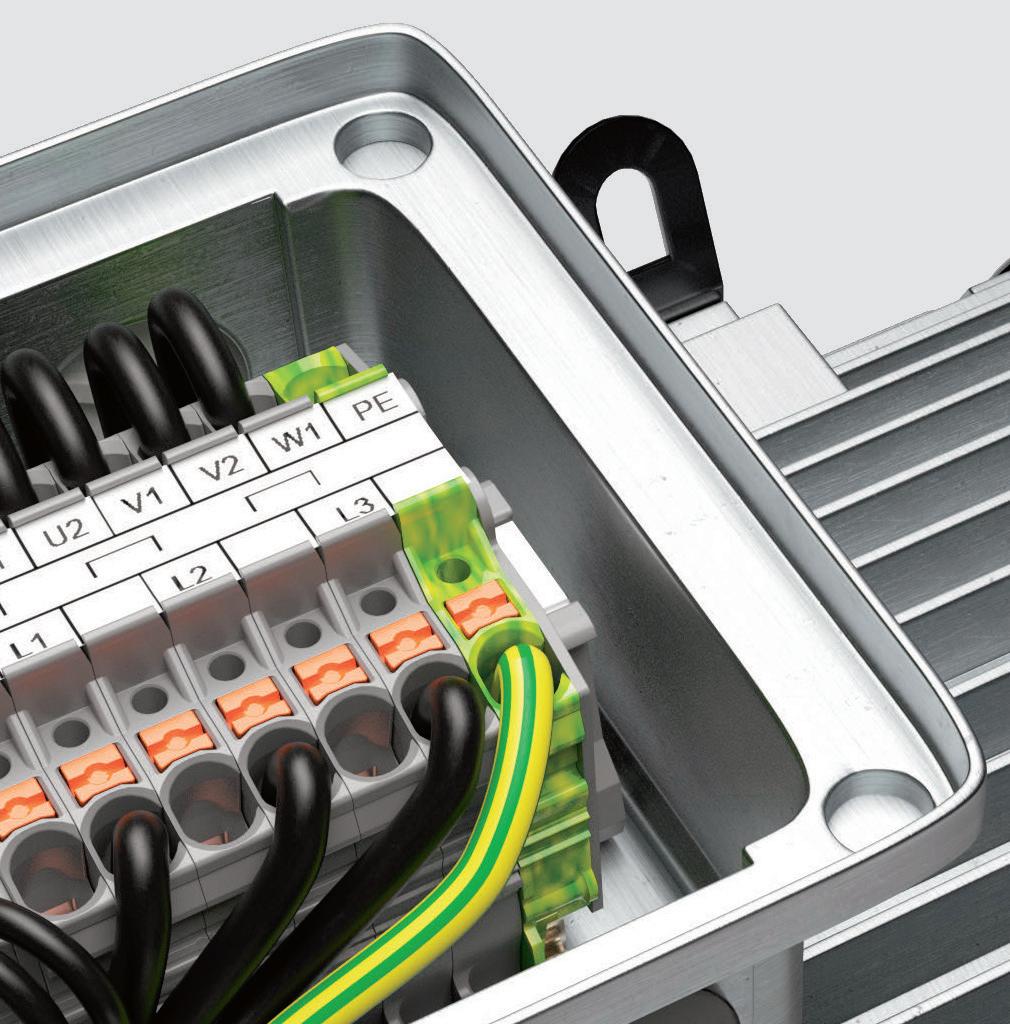
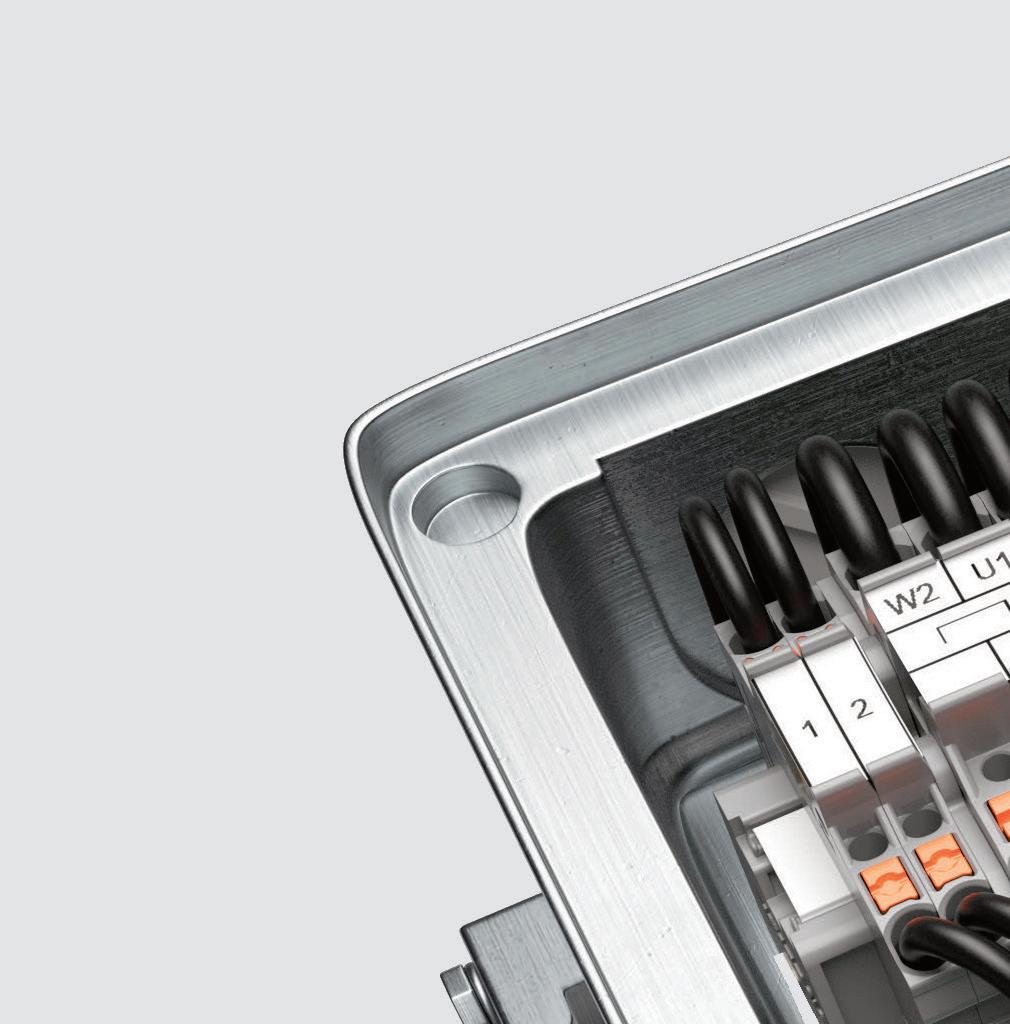
“We each bring something different to the table that breaks up the traditional engineering mindset,” Schneidau said. “While I have an engineering mindset, she has the exact same knowledge on a situation, but she brings a new perspective. It’s been really interesting. In my past jobs, whether engineering or not, it’s always been difficult to have people accept a different perspective.”
Schneidau seeks out different perspectives, even though there are challenges here. “When I’m in a new situation, the hardest thing has been getting people to understand the way I think. But it’s helped me evolve because my mind is constantly moving in a million directions. I do see that it’s a challenge for people to accept the different perspectives
that women bring to the table.” Like many women engineers report, she has had her share of being assigned to take notes for a team of mostly men.
Building her businesses
But she refuses to be defined by others’ limited views of her role. Even before she obtained her master’s, Schneidau had ambitious plans. She sees a problem, and she uses her problem-solving skills to address it, even to the point of creating new businesses.
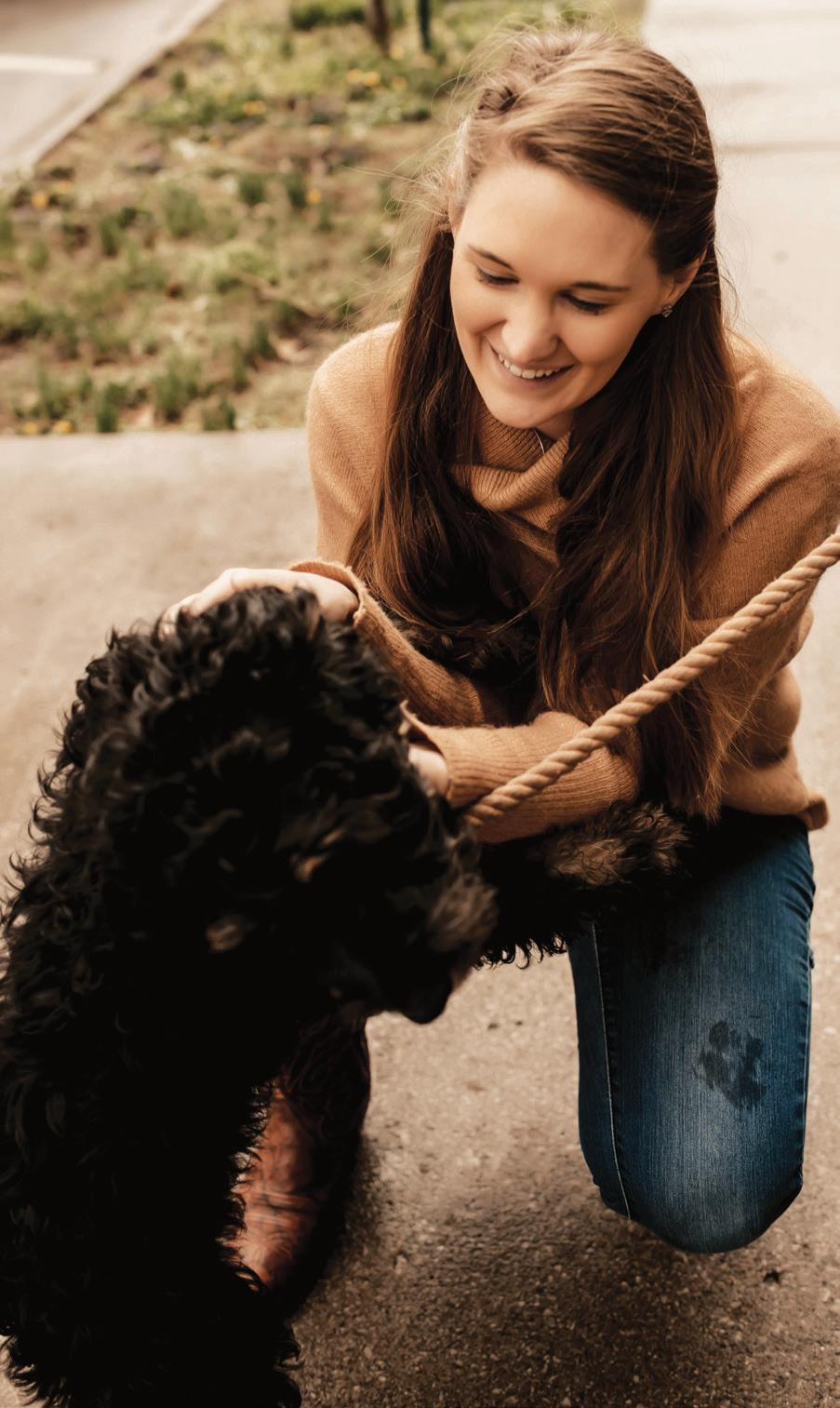
She is CEO and founder of two companies and is involved in a third. The first company is Mod Man Technologies, which she started as an undergrad with two of her friends. They designed a prototype machine that is a modular desktop manufacturing machine with interchangeable 3D printing, milling, laser engraving, slash cutting, and injection molding features.
“We noticed in our engineering classes that we had to use a separate machine for each function,” she said. “And those machines are expensive and there’s not a lot of money available through grants or funds for many education institutions to purchase them. Our goal was to have a desktop machine that was small but built for education use that we could sell for less than a thousand dollars. And have everything integrated into it, including all the software in one package.”
“We convinced our department chair to let us do this as our senior design project. In five months, we went from idea to functioning prototype. Then we recruited some computer science students to help us with the software.”
They continue to iterate the prototype while working on a number of other projects.
Another company for Schneidau focuses on solving the workforce development need in the additive
manufacturing industry. Her company will help educate students about this industry.
“One of my passions in additive is workforce development,” she says. “I’ve trained and taught many students while I was at university. I knew that with this rapid growth of 3D printing, especially during COVID, that many businesses would struggle to hire technicians and process engineers for additive projects. To me, there needs to be a curriculum that can be shared with K through 12 students, especially young girls. The initial approach was for general education in engineering, but why stop there? There are so many other capabilities for 3D printing. So instead of focusing solely on engineering, why not design it for the entire STEAM area?”
“So, now it’s turned into a curriculum for STEAM application for K through 12 with the intent on having modern man-machines integrated so that students can learn and modify the machine. I am working on my first few sets of curricula and building relationships with teachers within my mom’s school district and also within some of my friend’s school districts. The company is called Kettle because a kettle generates steam.”
Schneidau’s third company is a service center for small businesses, high school students, and entrepreneurs who want to try out 3D printing technology. She works with customers on designing concepts. This company is modeled a bit after Etsy, to print small production lots and help customers begin to sell their product and establish their own businesses.
A love of learning
Schneidau has long been active to helping younger students develop a love a learning.
“When I was at U of L, we had a type of ‘summer camp’ for students

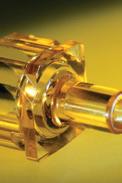

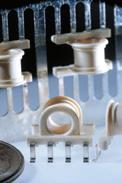
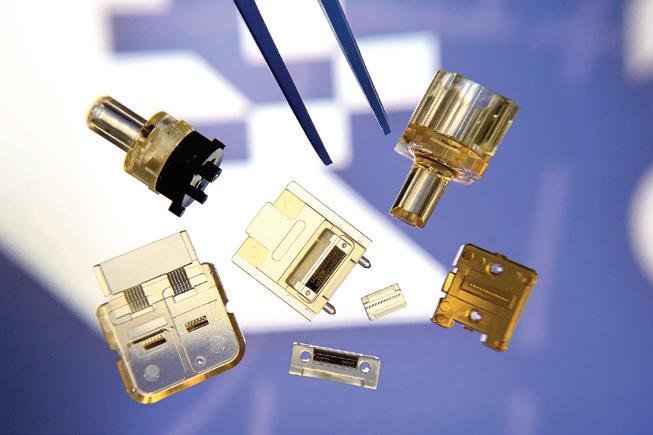
in underdeveloped counties in Kentucky. For a week, high-school students came to campus and experienced the city. They got to see what college life was like, and we gave them a Shark Tank type of learning opportunity,” she said.
“We put them into groups, assigned them roles and had them pick an item or an idea that they would turn into a product. They had a week to design it in CAD, print out their components, assemble and then pitch the product to a panel of experts. All of the students who had limited access to these tools took it and ran. I remember one group struggled with the product assembly part for their idea. They wanted to use 3D printing so I suggested they print it as one part. They didn’t realize they could do that. I showed them how to design a gap in the part so that when it prints, it’s nearly fully assembled. They were so amazed at what 3D printing could do, and I thought, ‘that’s why I do this.’ 3D printing can be such an aid to entice people into engineering because they can see immediate results. By the way, the winning group made cupholders for cars that wouldn’t spill during driving.”
Schneidau can relate to young highschool girls getting teased for liking math and science. It’s one of the reasons she enjoys teaching younger students about engineering.
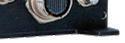

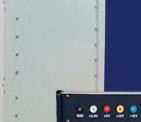
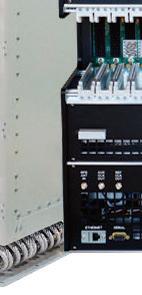
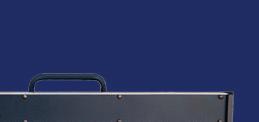
“I was picked on for liking those subjects. And it does something to you. But I was fortunate, a lot of my friends were also good at math and enjoyed science. For those that weren’t good with math, I was able to help. And that taught me about collaboration. Sometimes people forget that for a 14or 15-year-old girl who likes math and science, it can be a little lonely,” she said. “I know so many other people who wanted to help their dads with cars and get grease under their nails, but who weren’t necessarily allowed to. They could have gone into engineering too.”
Schneidau has found a place for all her creativity, problem-solving skills, and her drive and ambition.
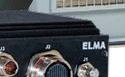
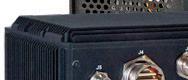
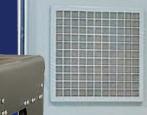
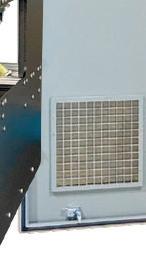
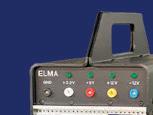

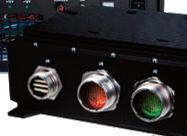
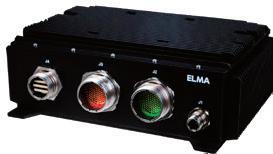
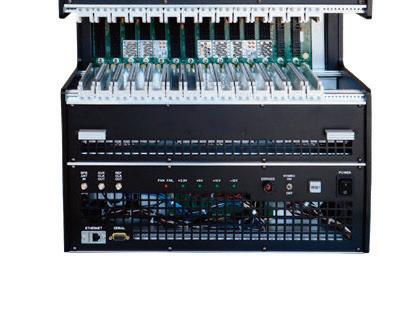
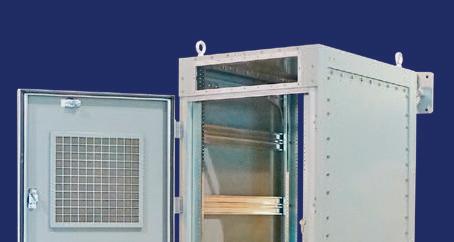
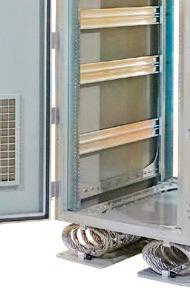


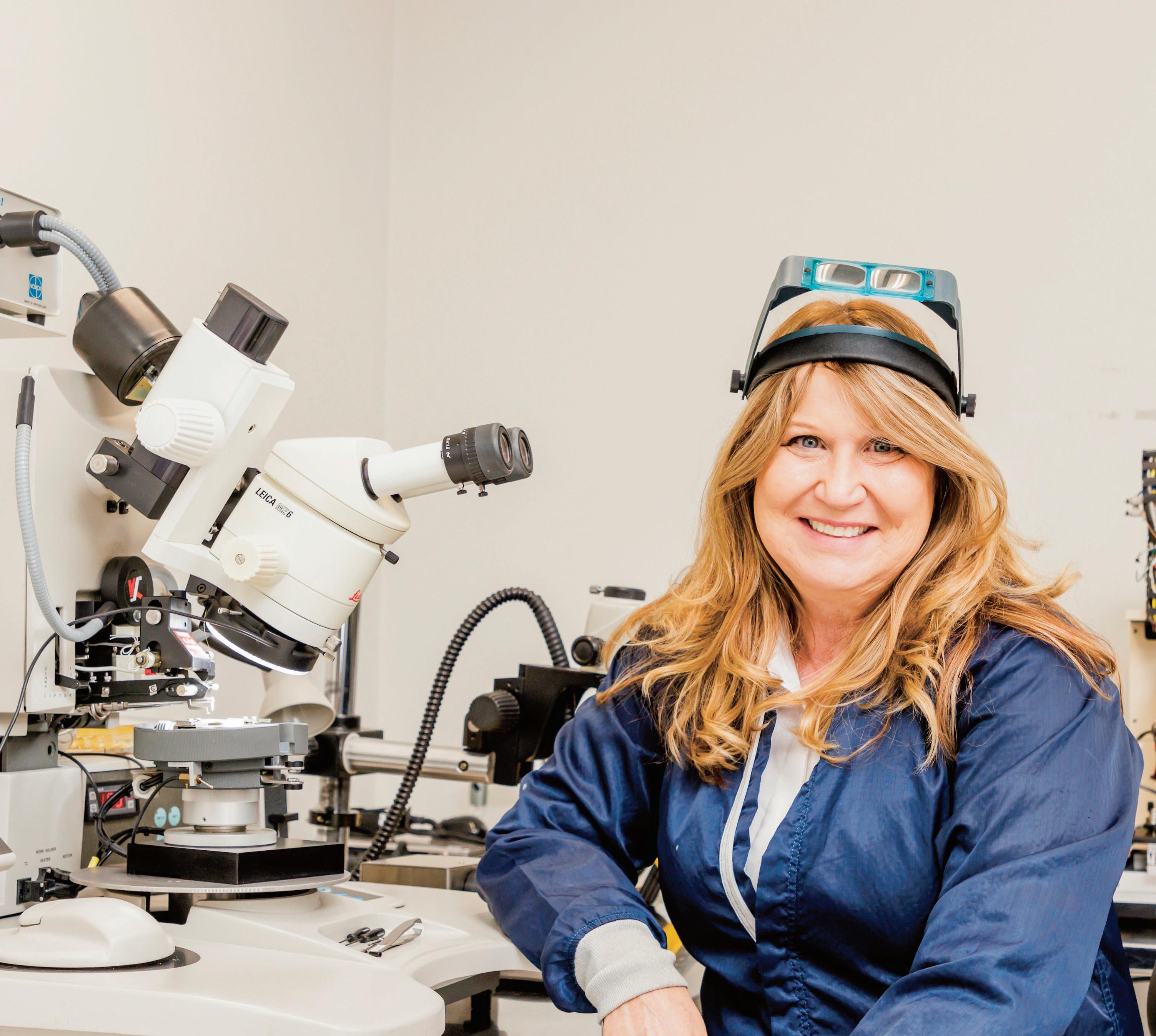
Women in Engineering

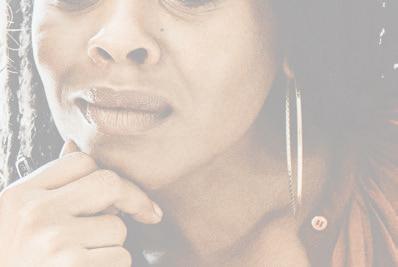
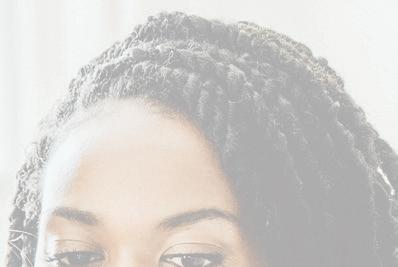
Yejee Choi

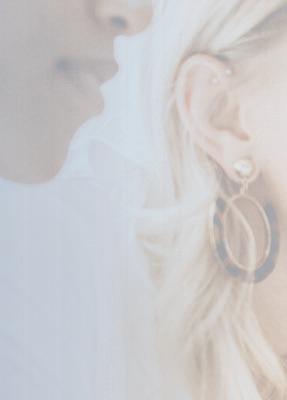
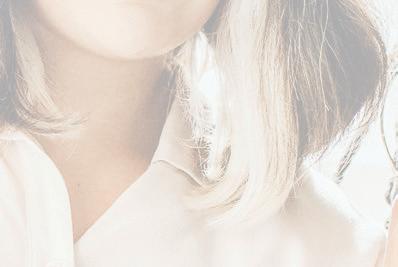
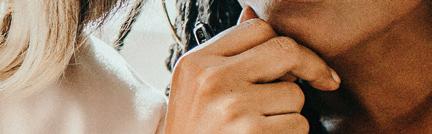

Test Engineer Allegro MicroSystems
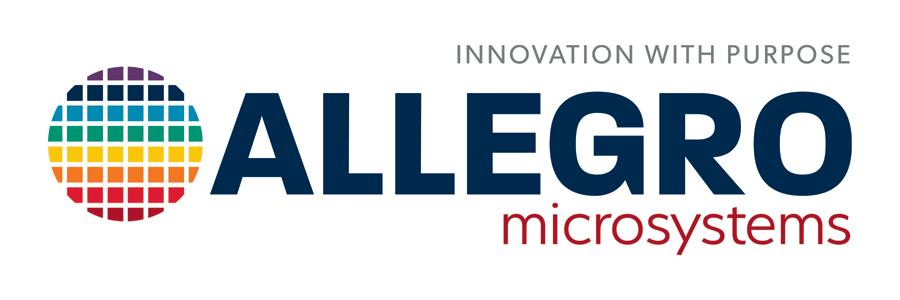


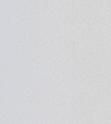





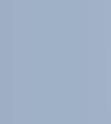
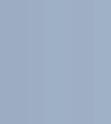
























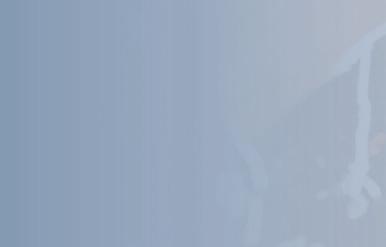
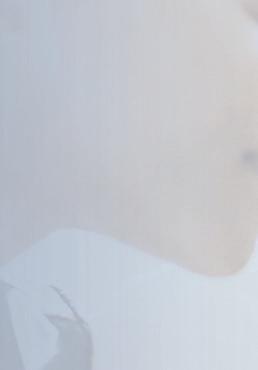
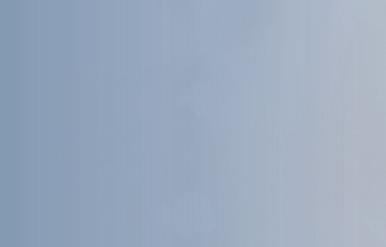
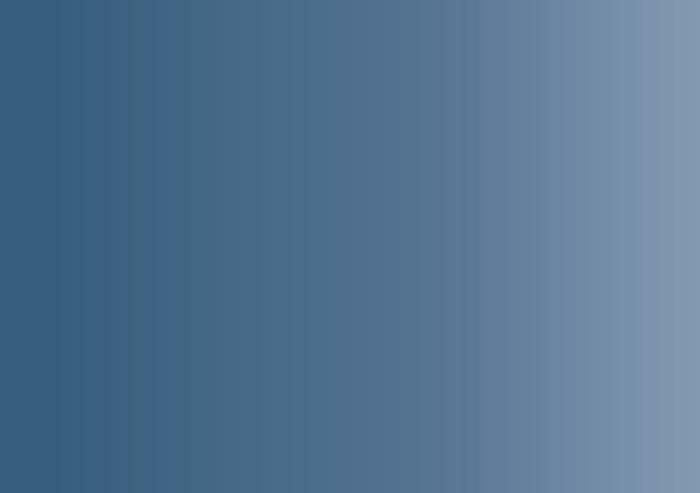








Electrical and Computer Engineering, Worcester Polytechnic Institute (WPI), Worcester, MA
Talk about the culture at your company. What makes it inclusive or supportive of women in engineering and automation?
Working as a female engineer can seem intimidating from the outside as it’s a generally male dominant field. I’ve worked at Allegro for 5 years and never felt I was being treated differently than my male peers. I’m always treated as an equal engineer, not a female engineer.
It’s a great feeling to work for a company that values inclusivity. Everyone is valued equally as an individual, regardless of gender, age, or ethnicity. We’re all given the tools and support we need to succeed in each project and continue advancing in our careers. Last year, Allegro helped sponsor my green card which made me feel valued as an employee and respected as an individual.
Over the past few years, the organization has taken steps to better acknowledge the work of our women engineers, which is so exciting to see.
Describe a recent company project (in which you were involved) that went particularly well. How did you and your team go about ensuring success?
Yejee Choi is currently a test engineer at Allegro MicroSystems. She was raised in Korea until the age of 14, when her family relocated to Ghana.
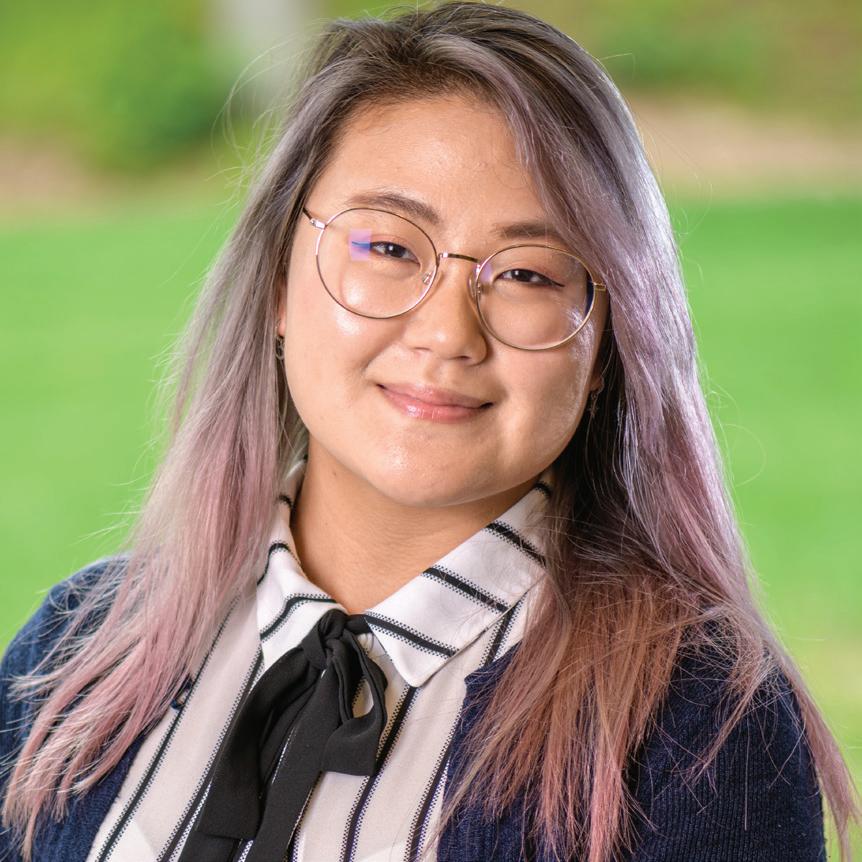

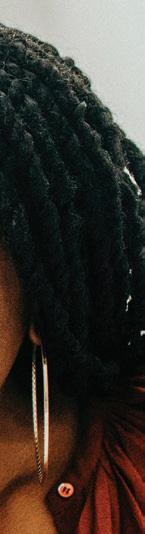
Upon high school graduation, Yejee decided to come to the United States where she studied electrical and computer engineering at Worcester Polytechnic Institute (WPI) in Worcester, MA.
She began her career at Allegro MicroSystems right out of school, quickly taking on new projects and responsibilities, providing significant contributions to the success of Allegro. Her passion for learning and understanding new and evolving technologies is inspiring to everyone around her. She is always going out of her way looking for a new problem to solve.
As a test engineer, my job is to test, develop, and debug newly designed products to ensure product capability and performance. We recently launched the world’s first three-phase BLDC driver IC with integrated power loss brake features. This project was exciting to be a part of, and the challenges it presented were fun to overcome together as a team. It had new features that needed to be finalized, but the COVID-19 pandemic began in the middle of the development cycle, which threw the whole team for a loop. With constant teamwork and ongoing support, we were able to pull it through and successfully launch this product.
What first drew you to engineering and this industry?

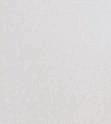
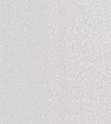

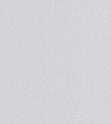

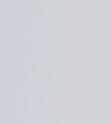
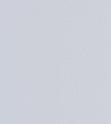
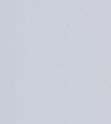
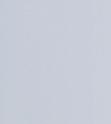
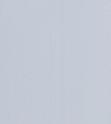
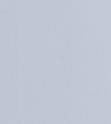
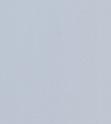
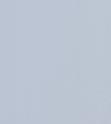
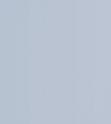

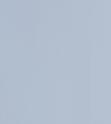
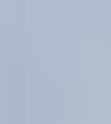

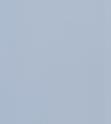
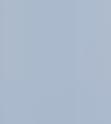
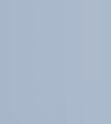
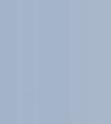
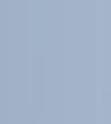




During my junior year of high school, I attended a science research camp taught by brilliant math Ph.D. students from the United States. The whole camp experience opened my eyes to envisioning and viewing the world from a different perspective, and my interest in science and technology peaked.
Living in a country with frequent power outages and slow internet connections as the norm contributed to my choice of electrical engineering when I entered college. I took my first introductory electronic course with all the circuitry lab work during my first year. From the start, the course brought me so much joy. It was clear this was the correct career path for me.

For the rest of Yejee Choi’s insights, visit www.designworldonline.com/WiE.

Women in Engineering
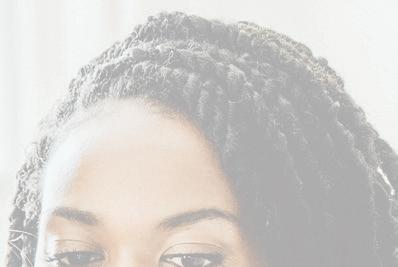

Or Yacobi

Product Portfolio Manager


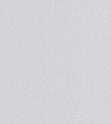







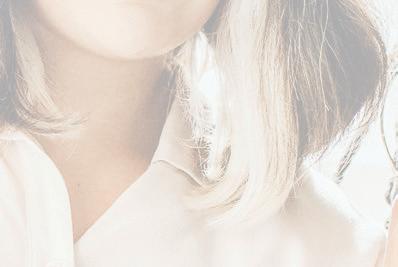
Allied Electronics and Automation











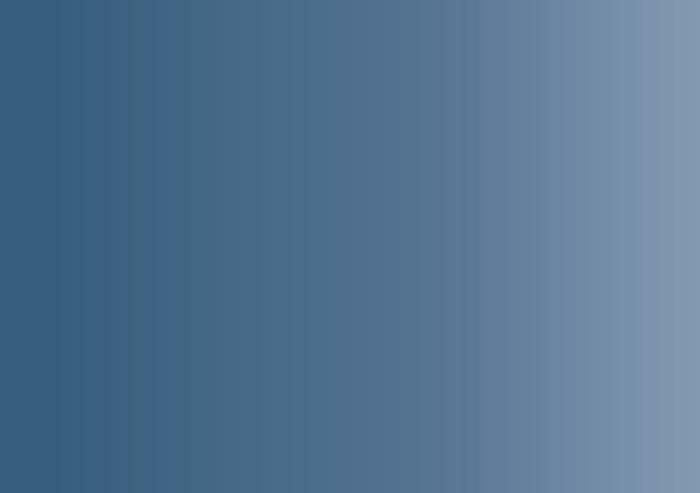
MS in Quality and Engineering Management

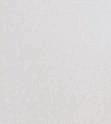
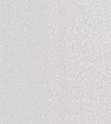

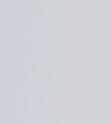

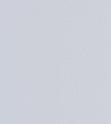
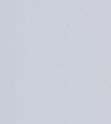

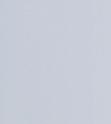
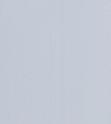
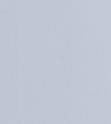
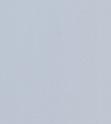
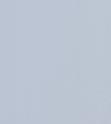
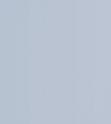

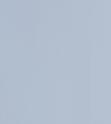

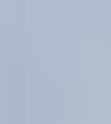

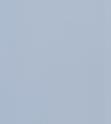
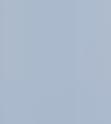

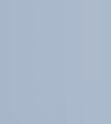
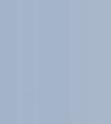

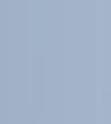
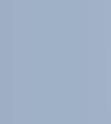
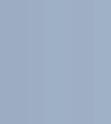














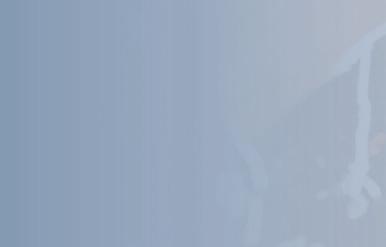
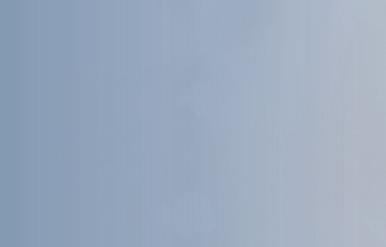






Tarleton State University, Stephenville,Texas
Talk about the culture at your company. What makes it inclusive and supportive of women in engineering and automation?
The culture at Allied is diverse and transparent. The leadership team prioritizes diversity and inclusion, and that’s reflected by the diversity of employees throughout our business; whether by gender, race, or age. Women at Allied are highly-valued and supported through multiple programs and initiatives.
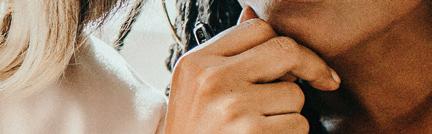
What first drew you into engineering and this industry?
I always wanted to extend my experience to the more technical side of the business. Once I started working in the automation industry it confirmed that I enjoy exploring how things get done and how they can be improved, whether the process involved goods or services.
Describe your biggest career challenge?
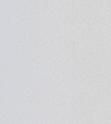

I would say I faced the common challenges most people experience in the field. The main challenge for me was defining my career path and finding an employer that values work-life balance, as well as a team that is collaborative and committed. Luckily, I’ve found all of the above at Allied!

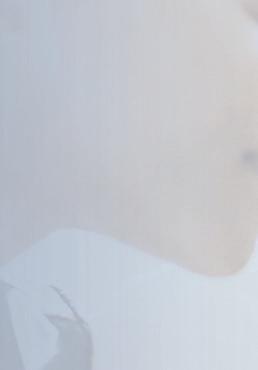
Career advice to your younger self?


One piece of career advice to my younger self would be to ask more questions. It’s okay to not know everything right away or for the first time when doing something new. Asking thoughtful questions leads to better outcomes and more opportunities for growth.
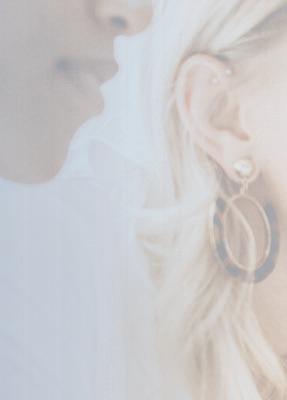
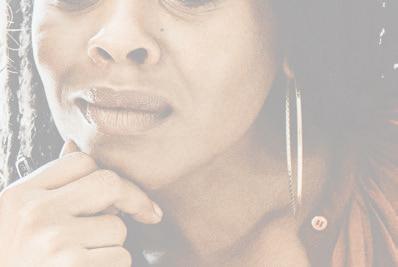
For the rest of Or Yacobi’s insights, visit www.designworldonline.com/WiE.
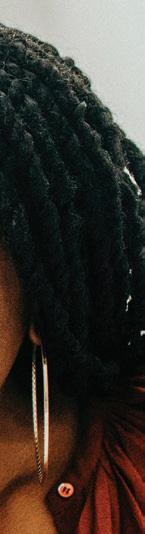
Women in Engineering

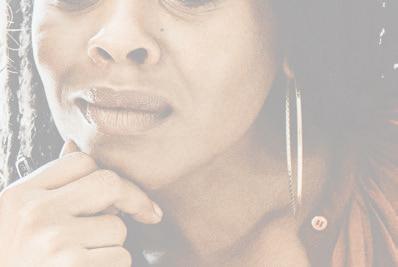
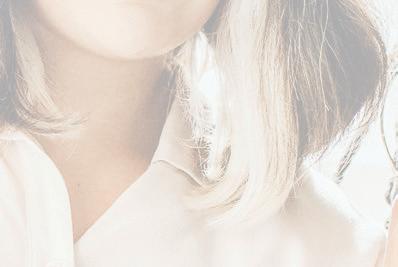
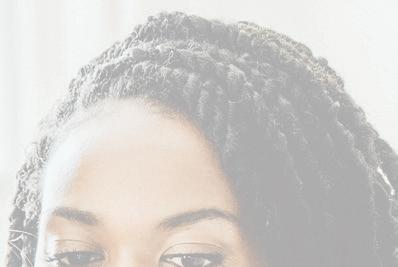
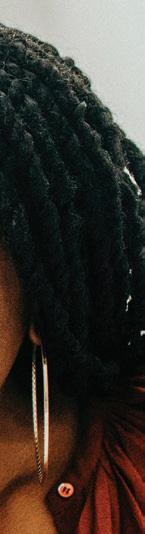
Apurva Deota
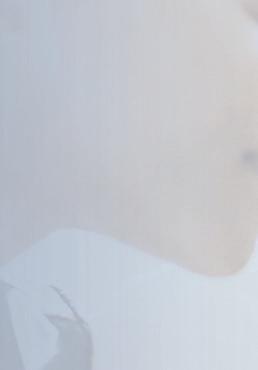

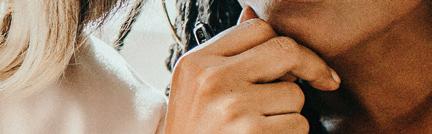

Technical Sales Representative B&R Industrial Automation


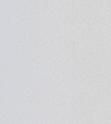
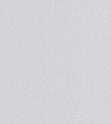




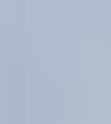
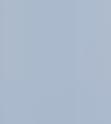


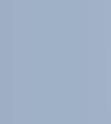
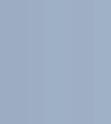


























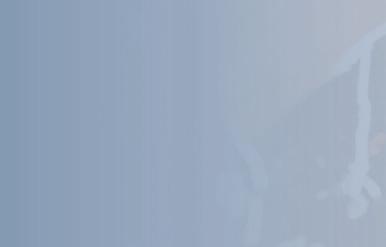
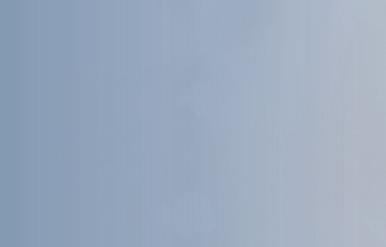
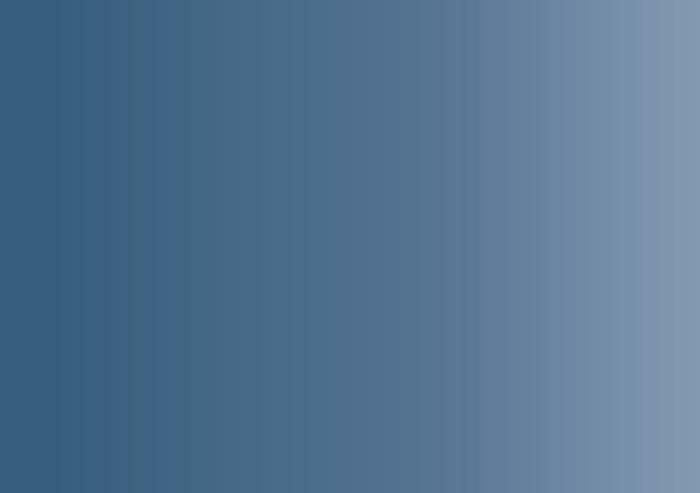





Master of Science Electrical and Computer Engineering Dalhousie University, Nova Scotia, Canada
Apurva Deota’s journey in engineering started 10 years ago after being introduced to the concepts of current and electrical circuits during her high school physics lectures in India. She pursued her Master of Science in the field of Electrical and Computer Engineering from Dalhousie University, Canada, and started working as Electrical Design Engineer at a machine builder in the plastics industry. This is when she first used B&R Industrial Automation products and was impressed by the quality of technology B&R provides.
Talk about the culture at your company. Women in Engineering and Sciences are still a minority, however, due to the inclusive culture at B&R I have never felt any different than any of my colleagues. In fact, team Canada proudly introduces me as an Engineer and allows me to talk about the technicalities of products, help suggest better-engineered solutions, and present our programming software. I don’t ever feel that my gender is considered when challenges and opportunities are distributed. I have been given many opportunities with designing, traveling to meet clients, and represent the company’s complex technical portfolio. Although I am the only woman in the Technical Sales team in Canada, B&R as a company has many women in engineering to look up to. Ultimately, B&R employs many women in high-level management positions who are entrusted with great responsibilities.
Apurva Deota is an Electrical Engineer working in the Technical Sales Team at B&R. In this position, she works with OEMs in various industries, such as plastics, packaging, automotive, and food and beverage. She helps manufacturers design dynamic, innovative, and efficient machine solutions.
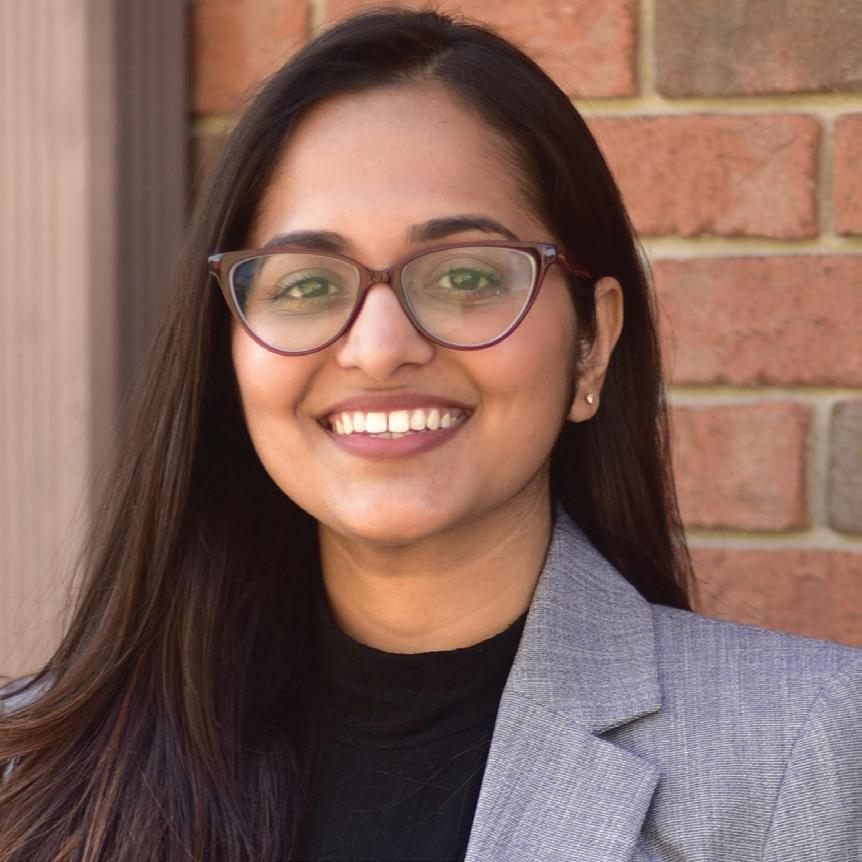

Describe a recent company project you were involved in. How did you and your team go about ensuring success?
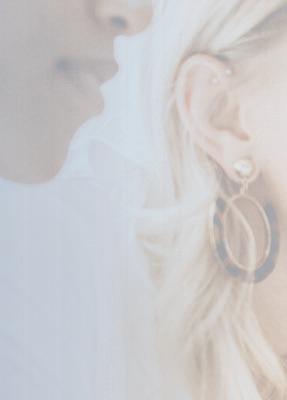
One involved showcasing our capabilities and understanding the demands of a machine manufacturer in the EV (electrical vehicle) market. At B&R we work as a team, and we had several discussions with the territory manager and our country manager to ensure success. Also, B&R is unique in the way that we provide applications support and for this customer, we made sure we had our experienced applications engineer present to help them with any roadblocks.
What first drew you to engineering and this industry?

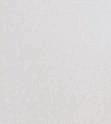
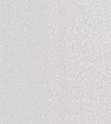

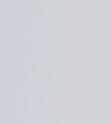
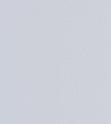
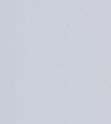
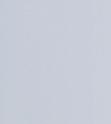
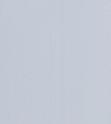
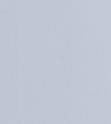
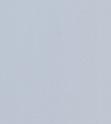
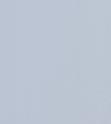
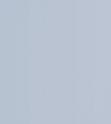

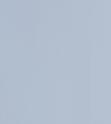

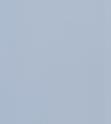
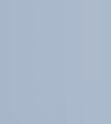
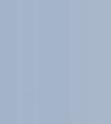
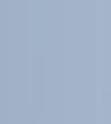







Electrical circuits and concepts of electricity/current got my attention during high school along with C programming. That is when I discovered I can learn more about it in Engineering and I started looking up different fields of engineering and the application of physics. The ability to craft machines that would make complex tasks easier was a powerful feeling which led me to pursue a bachelor’s in electrical engineering.
For the rest of Apurva Deota’s insights, visit www.designworldonline.com/WiE.
Women in Engineering
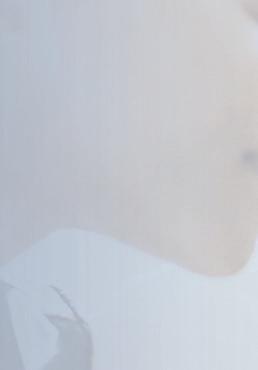

Brittany Langston
Product Manager - North America B&R Industrial Automation





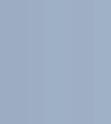

















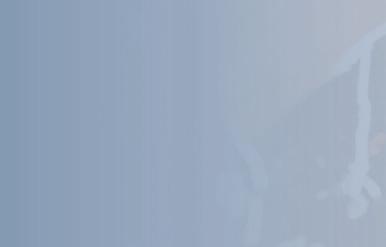
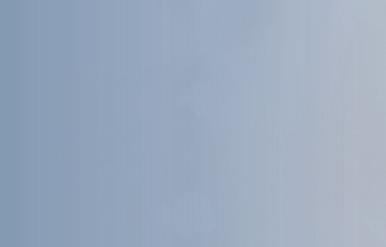
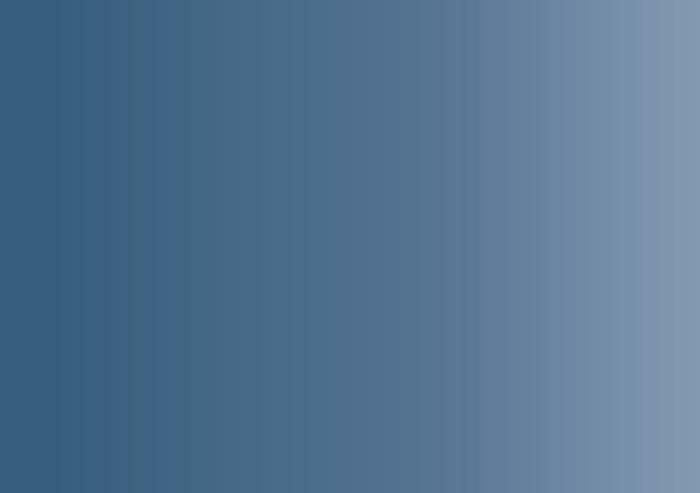








B.S. Electrical Engineering University of Florida










Brittany Langston is a North America

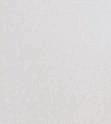
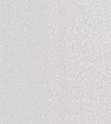
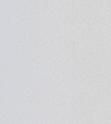
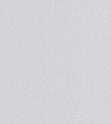
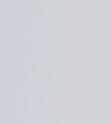
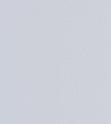
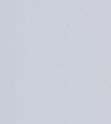
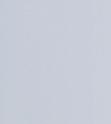
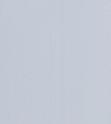
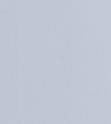
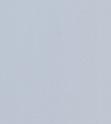
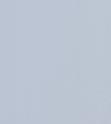
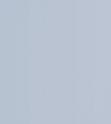

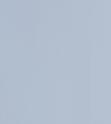
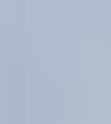
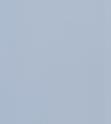
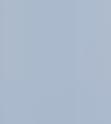
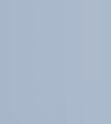
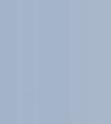

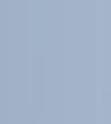
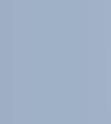

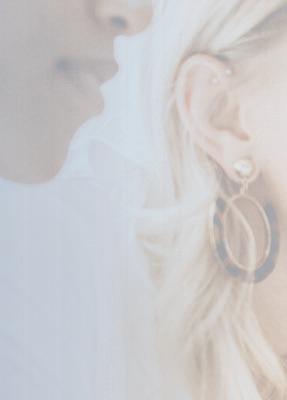

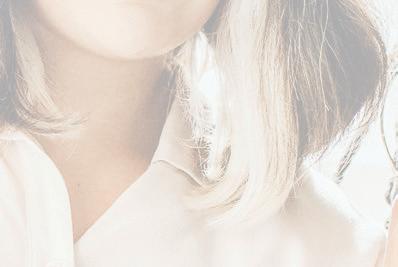
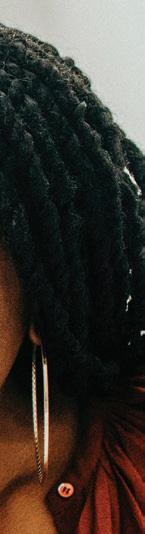
Product Manager at B&R for a handful of technologies, primarily related to software. Her purpose in this role is to improve the success and acceptance of these products within North America, and interface regularly with global product management. Prior to this role she was a senior member of the Product Support team, where she provided engineering support to colleagues / partners / OEMs / end users. She earned her Bachelor of Science degree in Electrical Engineering from the University of Florida in 2013 and joined B&R shortly thereafter.
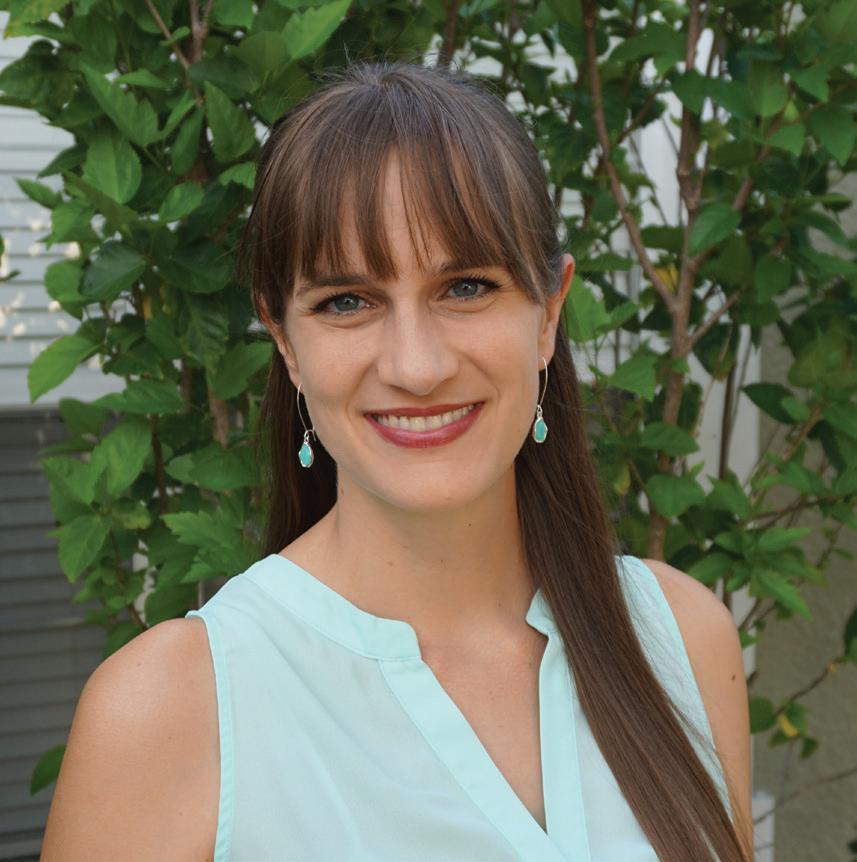
Talk about the culture at your company.
The company culture at B&R has always been quite open and informal. Ideas and thoughts are shared regularly without a fear of backlash or having to go through significant red tape, and everyone here is generally down to earth and approachable. I think this environment of casual approachability has enabled a sense of humanity in our workplace. It therefore naturally follows that women are valued for our contributions to the team rather than being treated as outliers.
Describe a recent company project you were involved in. How did you and your team go about ensuring success?
There were several factors that ultimately led to success in a project that I recently led. First and foremost, there was mutual respect within our team which enabled a productive and positive work environment. The big picture deadlines were clearly set, along with the intermediate deadlines in between which helped keep us on track. We had sync meetings every week to discuss progress and roadblocks. Ultimately, we were proud of the product we were making, which easily motivated us to improve and complete it.
What first drew you to engineering and this industry?






I’ve always been very detail oriented and enjoyed math classes, so engineering was a natural career target. It wasn’t until I was introduced to circuits in my Physics course that I became interested specifically in electrical engineering. Circuits questions were real-life, practical puzzles to me that I got a lot of enjoyment out of solving.
Ultimately the best part of undergrad for me was being a teaching assistant for the microprocessor lab course. I loved the course material and the process of helping guide students to understand it better. This is what ultimately drew me to the support role at B&R Industrial Automation because I got to do a similar function in industry.
Describe your biggest career challenge. How did you solve it, or what was the outcome or lesson learned?
The biggest challenge for me has been learning how to respond in moments when I’m underestimated. This can happen often when you’re a woman in a male dominated field. It took a long time to learn how to use those moments as fuel rather than triggering self-doubt. I was lucky that I always had the support of my teammates, which helped me to gain the confidence to traverse those situations with more boldness.

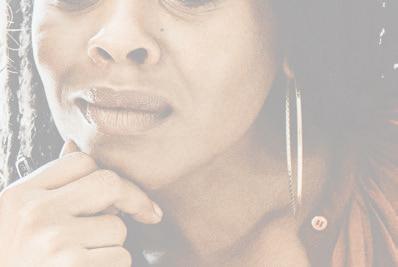
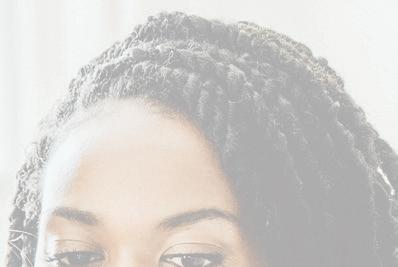
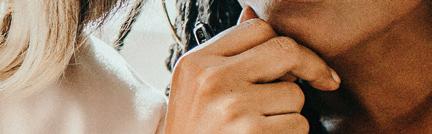
For the rest of Brittany Langston’s insights, visit www.designworldonline.com/WiE.

Women in Engineering

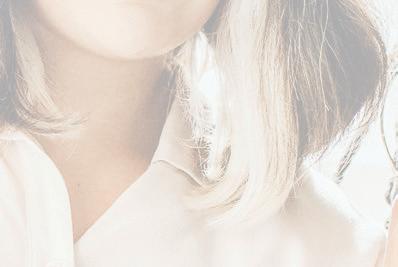
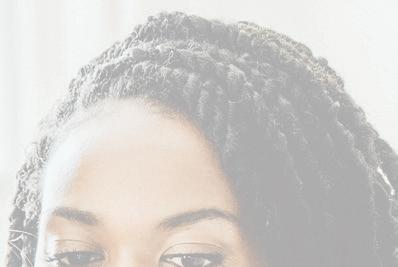

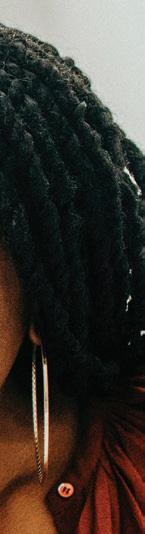
Alyssa Hiedeman


Application Development Engineer


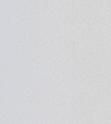
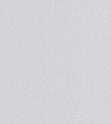



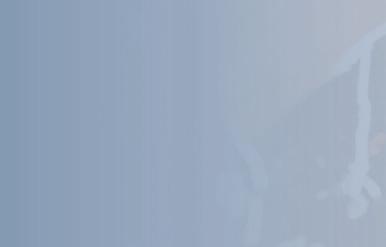
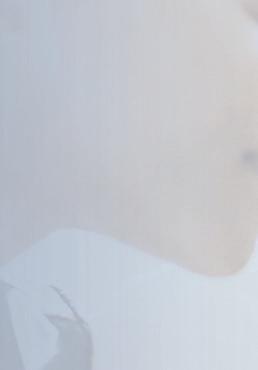
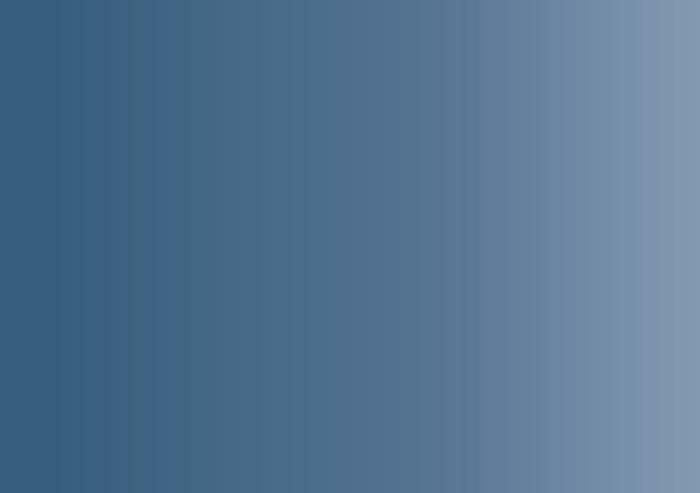








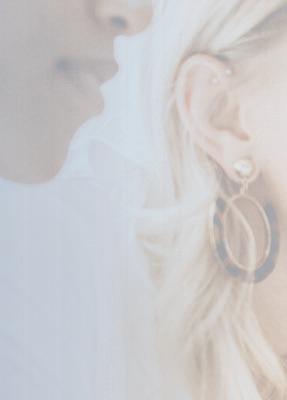
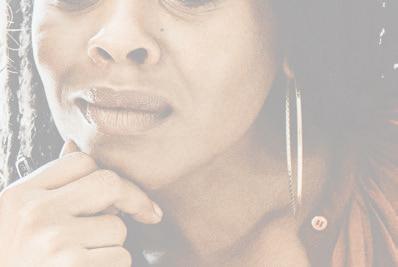
Beckhoff Automation
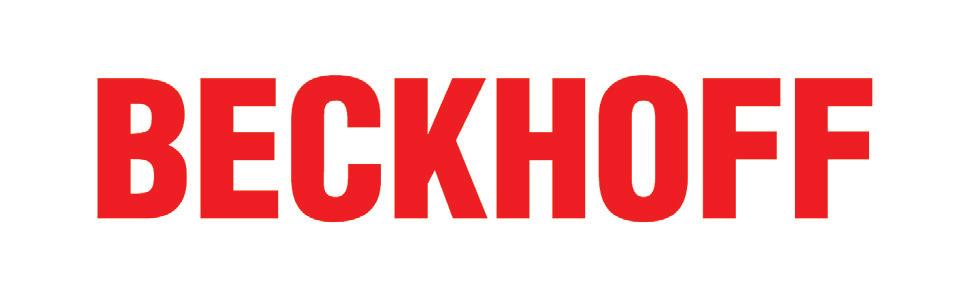
B.S. Electrical Engineering

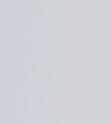

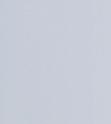
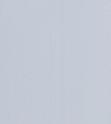
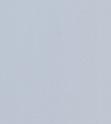
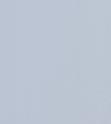
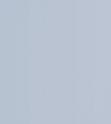

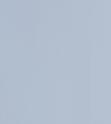

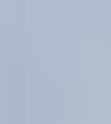

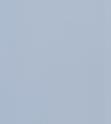
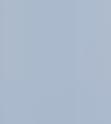

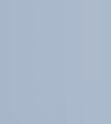
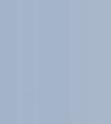

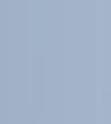
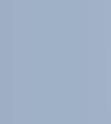
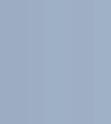

























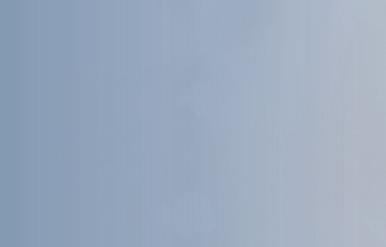

University of St. Thomas, St. Paul, Minnesota
Talk about the culture at your company. What makes it inclusive or supportive of women in engineering and automation?
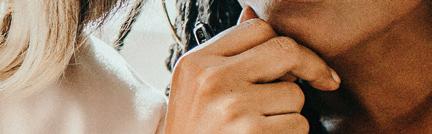
The culture at Beckhoff is very welcoming, inclusive and has a close family feeling. I have had the chance to work in several different roles during my time at Beckhoff and grow my career with the support of some very knowledgeable mentors. The work that we do is often collaborative, and I always feel my opinion is considered equally whenever I give it. I have never been made to feel any differently due to being a woman. Beckhoff USA is currently launching a women’s leadership group, which is an exciting resource for employees from any department working to grow their career in the automation industry.
Describe a recent company project (in which you were involved) that went particularly well. How did you and your team go about ensuring success? The biggest success I’ve experienced has been in helping develop this new Advanced Applications Group at Beckhoff USA. At first, the challenge was defining what it would do and where the team fit within the existing support structure for customers. In the past, the sorts of questions we address would often be handled by the Technical Support Department, applications engineers in the field or the product management team. It took time and internal communication, but we were able to carve out a specific, beneficial niche that fit well within the organization.
Alyssa Hiedeman started working in Technical Support at Beckhoff Automation’s U.S. headquarters in Savage, Minnesota, in 2016. In 2019, she relocated to Denver to take a position as an Application Development Engineer on the recently created Advanced Applications Group. Working on this select team of New Automation Technology experts, she helps Beckhoff sales and applications engineers test and validate complex applications and novel uses of TwinCAT automation software to ensure the success of customer applications before they even start.
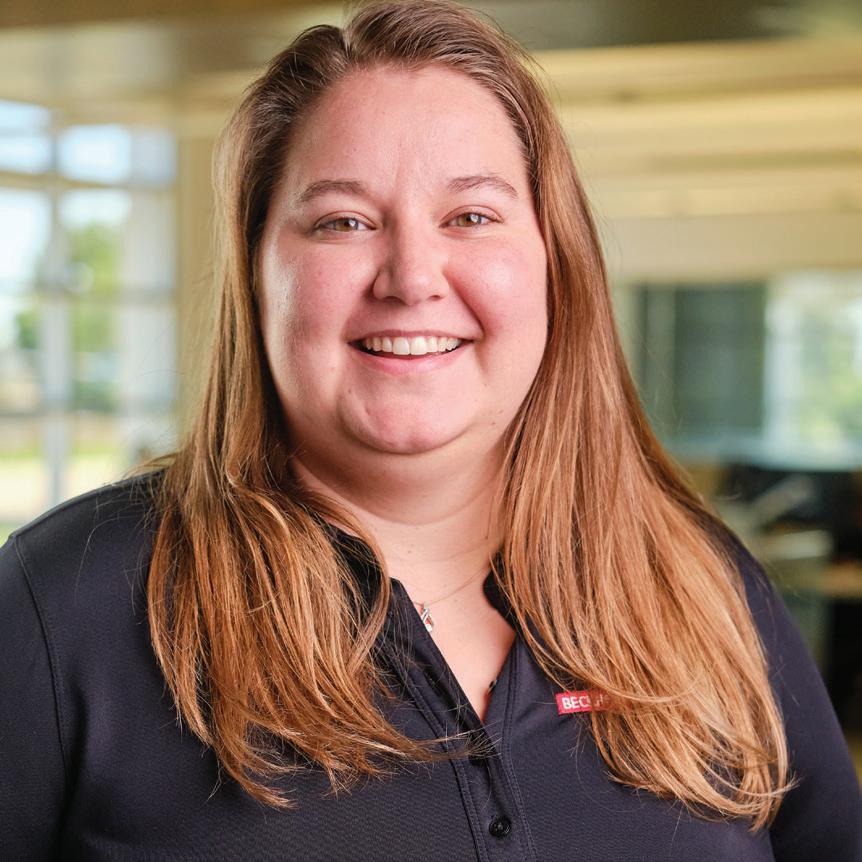
Now, when we are brought in to assist, we sit down with the customers and listen to their goals and concerns. Typically, we end up building a small demo, delivering some sample code and/or provide 3D simulations to validate that an application will work the way they want. Other times, we simply provide a definitive response that a concept will not work and offer alternative options that will do the job. Either way, customers are often very appreciative. I was able to help grow the Advanced Applications Group as well as grow with it, and that has been extremely rewarding.
What first drew you to engineering and this industry?

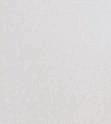
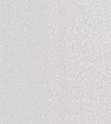
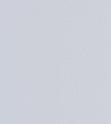
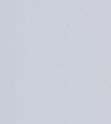
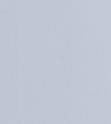



Growing up, I was always very interested in math and science. When I was in middle school, I had the opportunity to attend an engineering camp for girls, STEPS Camp hosted by the School of Engineering at the University of St. Thomas. During the camp, we had the chance to learn and explore everything engineering. We built HAM radios and model airplanes that we got a chance to fly at the end of the week, and I was hooked on engineering from that moment on.
For the rest of Alyssa Hiedeman’s insights, visit www.designworldonline.com/WiE.
Women in Engineering

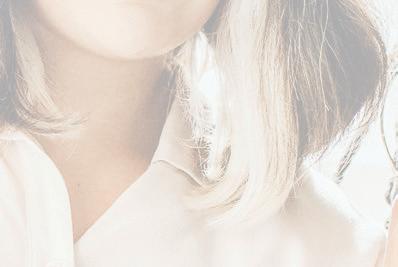
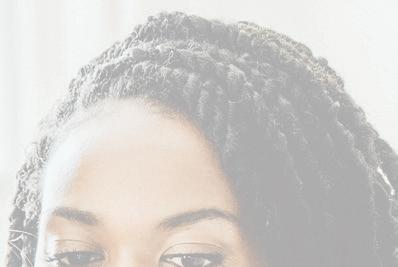

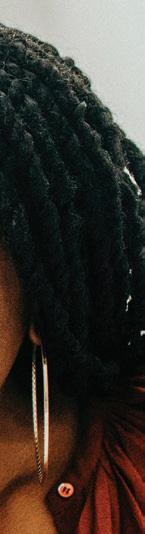
Karen Vintroux

Staff Scientist
Cinch Connectivity Solutions | a bel group
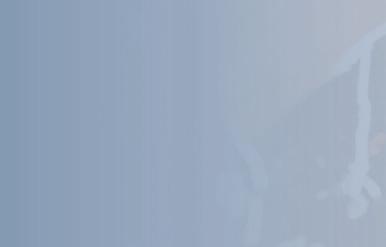
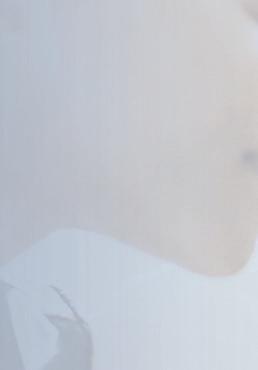




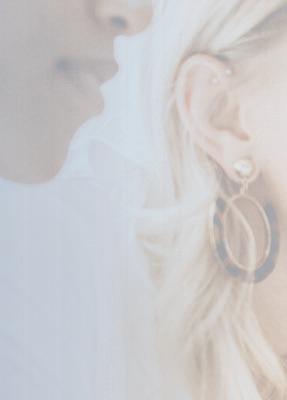
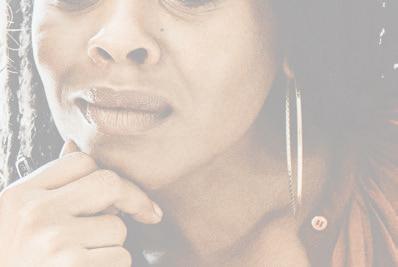
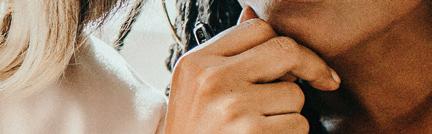
B.S.ChE Chemical Engineer Florida Institute of Technology


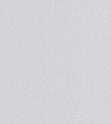


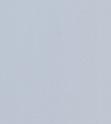
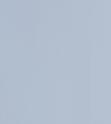

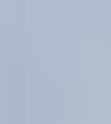

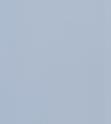
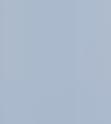

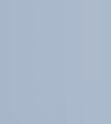
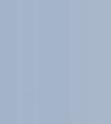

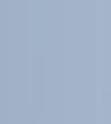
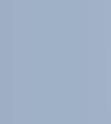
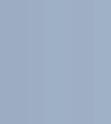


























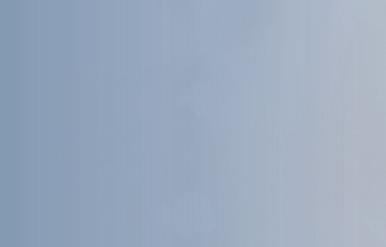
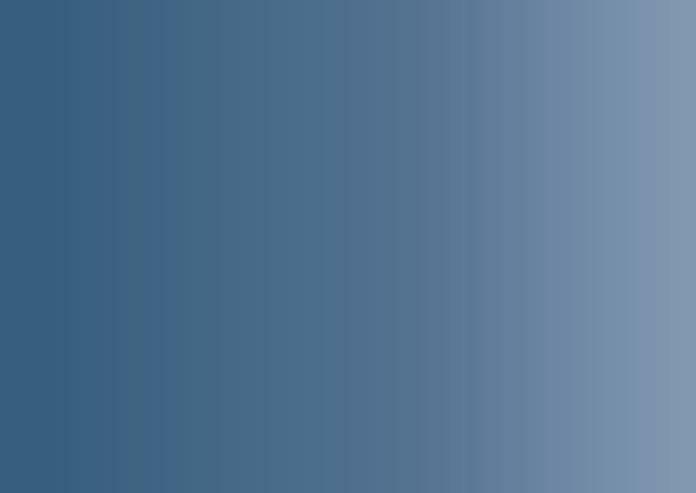
Karen Vintroux is a Staff Scientist working for Cinch Connectivity Solutions, a bel group in Melbourne, Florida. She began working in RF and microwave electronics in 1983 and received her bachelor’s degree in chemical engineering from the Florida Institute of Technology. Solving problems with avionics and automotive hardware led her to create novel alumina powder compaction materials and to develop low-temperature processes for gallium arsenide semiconductors. During the past decade, her work focused on developing hybrid technology for fiber optical transceivers. In that capacity, she defined best practices for the design team to assure robust performance in harsh environments. Her recent work can be summarized as designing and evaluating mechanical, electrical, and optical components, developing materials and processes to assure rugged performance, testing for reliability advancement, and implementing risk mitigation.
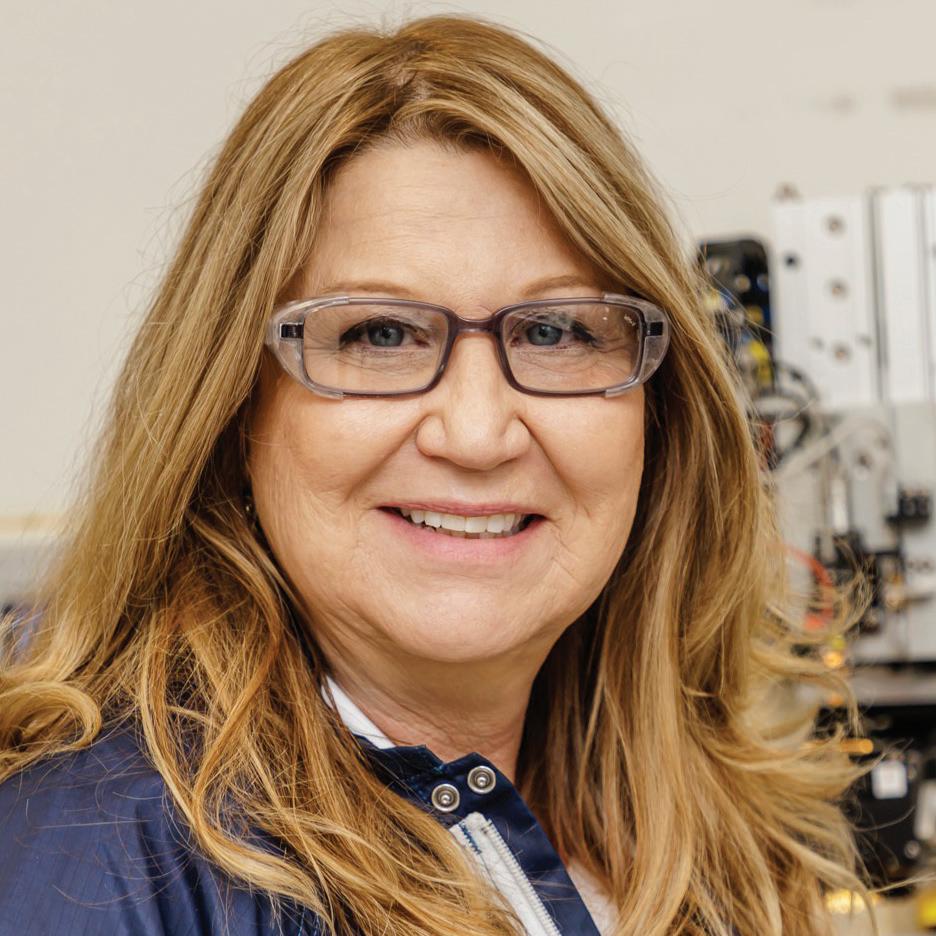
Talk about the culture at your company What makes it inclusive or supportive of women in engineering and automation?
Cinch retains a family-oriented spirit while operating at an internationally high level in advanced interconnects for over 70 years. We make it possible for our customer’s equipment to “talk” to each other, whether on the ground, in the air, or in space. The work is significant for end-user success on some of the biggest missions and has captured my focus for over 20 years. Our team embraces problems or new tasks. Our short design cycle continuously resulting in working prototypes is rare in these industries. With the resources at Cinch, the manufacturing and production steps are handled professionally and with respect to the original design. As a woman in the maledominated engineering field, I’ve never experienced any team hesitation.
Describe a recent company project (in which you were involved) that went particularly well. How did you and your team go about ensuring success?
The pandemic shattered supply chains on a global scale. Here at Cinch, our core multidiscipline team of essential workers came in daily to source replacements and get them qualified for customer approval. While meticulously following CDC guidelines, we laid out new schematics, made mechanical fit adjustments, performed in-house machining, built working parts, completed performance testing, and documented the qualification results for end-user review and feedback. Many of these program changes will move forward permanently since some suppliers did not make it back after the shutdown. The effort took everyone’s full participation, and we added to Cinch’s overall fiscal success during this trying time in history. The results were satisfying for our customers and us.
What first drew you to engineering and this industry?

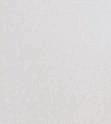
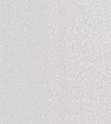
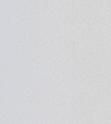


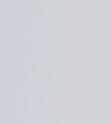
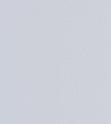
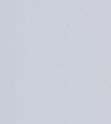
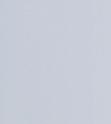
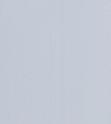
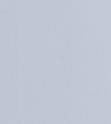
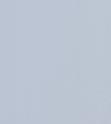
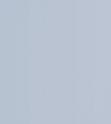









In 1963, during the Great Space Race, my mom moved from West Virginia to Melbourne and started working at Radiation Inc. As a Florida native, long hot summers and crowded winter beaches epitomized my home. We watched the rockets go up into space from our front yard. At my first job, I worked with ceramic circuit cards, semiconductors, and a needle-guided gold wire to create interconnects from point to point. It was natural to me. Little did I know that my mom did hybrid semiconductor technology work at her job. She supported the development of antenna, integrated circuit, and modem technology used in the NASA missions. After 30 years, she retired as a Field Quality Engineer from Harris Corporation. I learned best practices for integrating family and work from mom. Embracing the lifestyle results in a meaningful natural gift to pass down to future generations.
For the rest of Karen Vintroux’s insights, visit www.designworldonline.com/WiE.

Women in Engineering
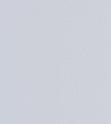
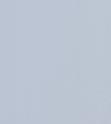
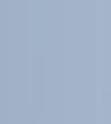

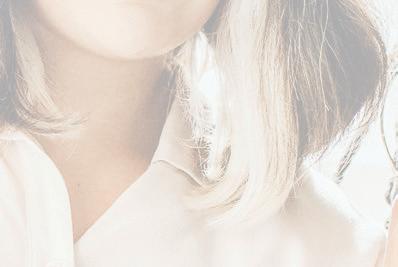
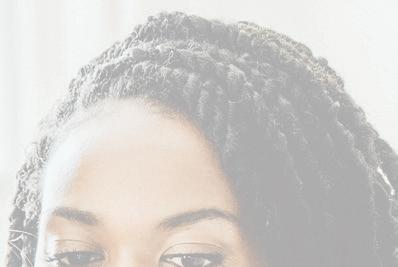
Kristin McKenzie

Senior Director of Information Technology Digi-Key Electronics



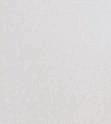
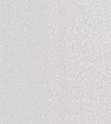
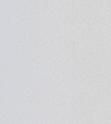

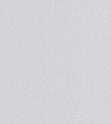

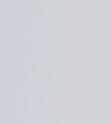

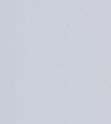

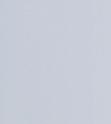
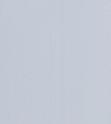
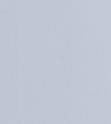
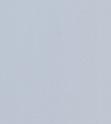
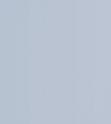

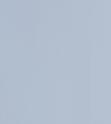

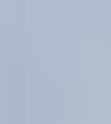

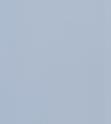
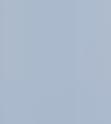

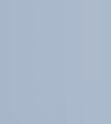
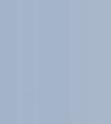

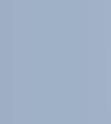
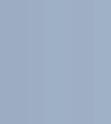


























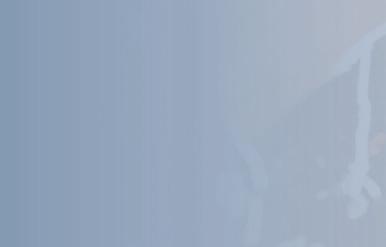
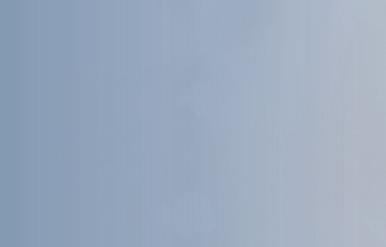
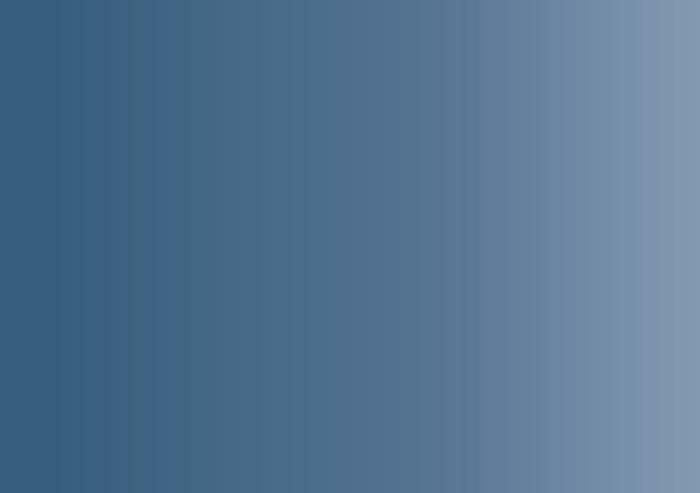











B.S. Computer Science, SCL University of North Dakota
Kristin McKenzie thrives on leading technical teams and solving complex global business and IT challenges to drive business value. She leads an organization of agile development teams who support critical business applications for Digi-Key’s sales and operations capabilities. Presently, her primary focus is leading a large technology transformation program for Digi-Key targeting digital first, enabling rapid growth and driving an exceptional customer experience.
She has worn many hats in her technology career spanning almost three decades, spending her first 12 years writing code as a software engineer and eventually moving into various leadership roles over software development, business analysis, program management, agile practices and international expansion initiatives.
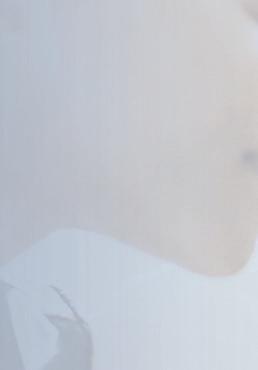

Talk about the culture at your company. What makes it inclusive or supportive of women in engineering and automation?
I’ve been fortunate with my experience at Digi-Key, which is why I’ve been with the organization over 27 years. It’s just a good company. One of our core values is “People Make the Difference,” which has held true throughout my career. Our people are Digi-Key’s secret sauce. I get to work with a lot of smart, creative and dedicated team members who inspire me to do better in my own role. Technology has always been viewed as a differentiator at Digi-Key. Even early in my career, I felt like I was making an impact and contributing to the success of the company.
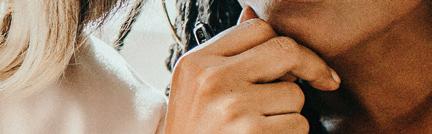
Digi-Key respects women in engineering. I was the first female software engineer hired by the company and was involved in recruitment and mentoring engineers for about 10 years before moving into various leadership roles. It’s been wonderful to see how many bright and capable women in tech have joined Digi-Key over the years.
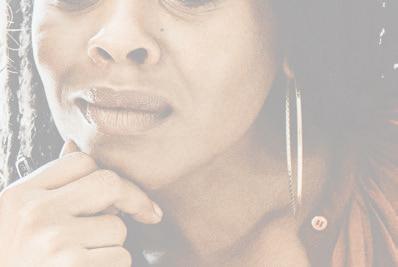

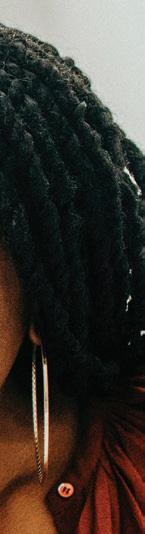
Overall, we have a great group of women leaders in the company. Digi-Key is an active sponsor of Women in Electronics, which is a community of progressive women leaders dedicated to expanding the opportunities for women in the electronics industry.
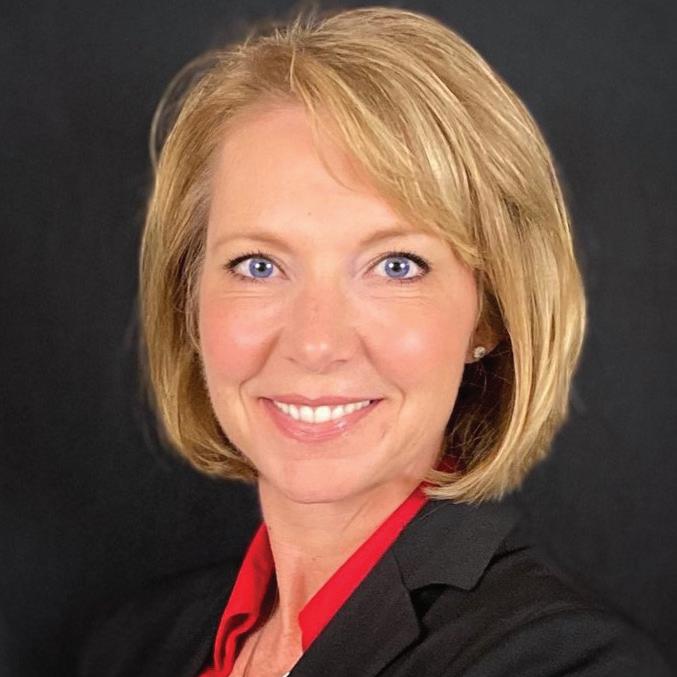

Describe a recent company project (in which you were involved) that went particularly well. How did you and your team go about ensuring success?

Digi-Key launched a marketplace in 2020, which was an exciting initiative to provide a one-stop shop for all aspects of technology innovation. We expanded our breadth of products and suppliers available to design engineers through this program. Our team focused on the customer experience and seamlessly supporting Digi-Key and Marketplace product in the same shopping cart, which was more challenging than it sounds. We’ve been improving the supplier and customer channels over the past couple years and offering new capabilities like a PCB Builder tool and the DKRed program, which allows makers, hobbyists and students to order custom circuit boards.
Describe your biggest career challenge. How did you solve it — or what was the outcome or lesson learned?
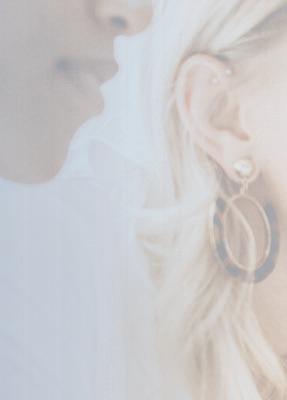
A recent international growth initiative pulled me further away from my technology roots and focused more on business operations in new markets, primarily China. Having no experience with business in China, the learning curve was significant. Building trust and rapport between our U.S. and China team members and partners was essential. I’m not involved in the business side today, but my team still supports the technology for our China operations, and I continue to have a strong affinity for our business team in Shanghai.
For the rest of Kristine McKenzie’s insights, visit www.designworldonline.com/WiE.
Women in Engineering

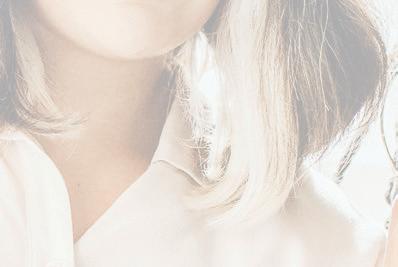

Melissa Heckman
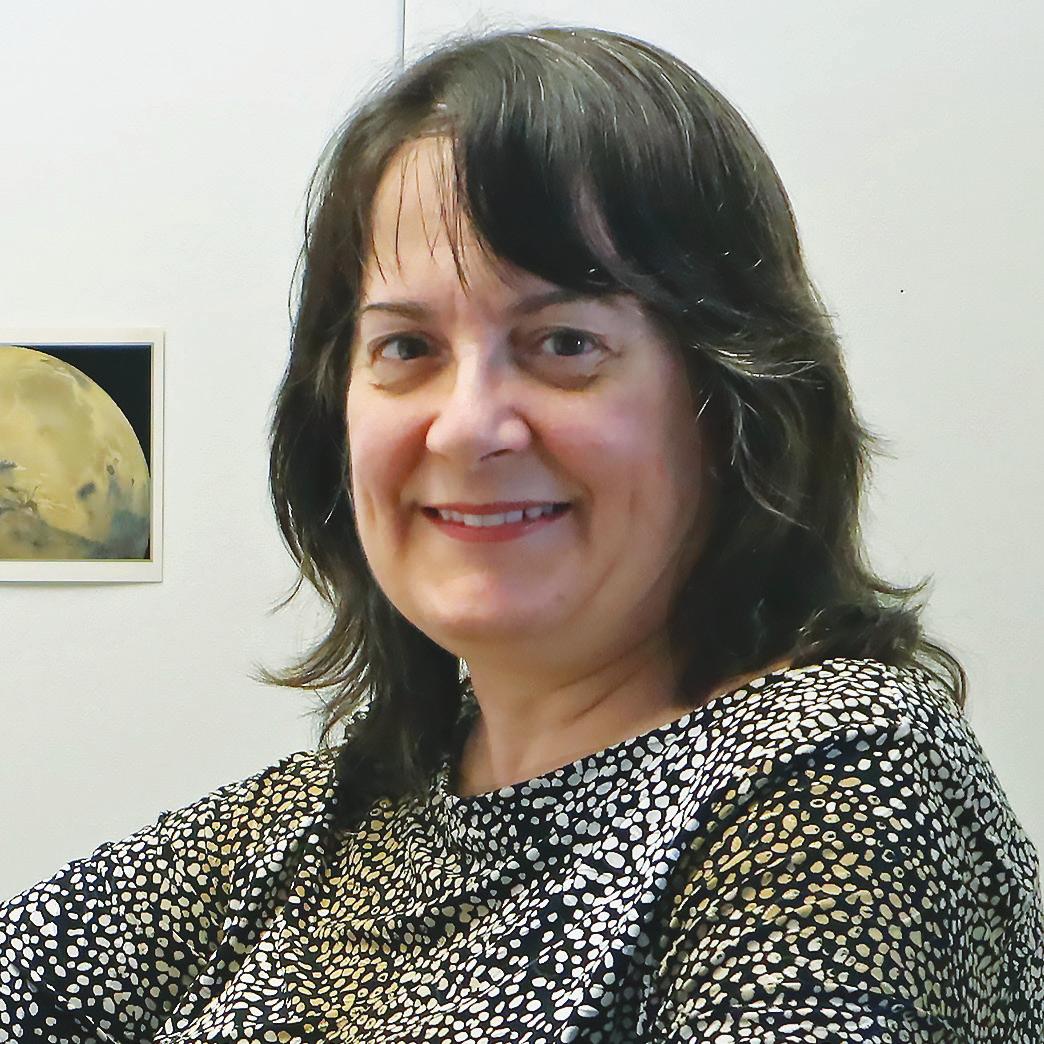

Senior Backplane Engineer


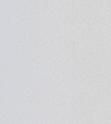
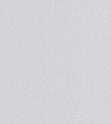

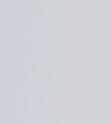


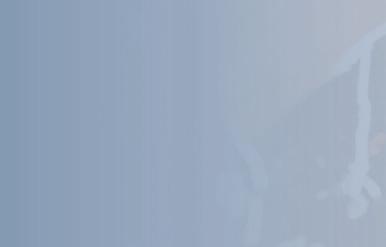
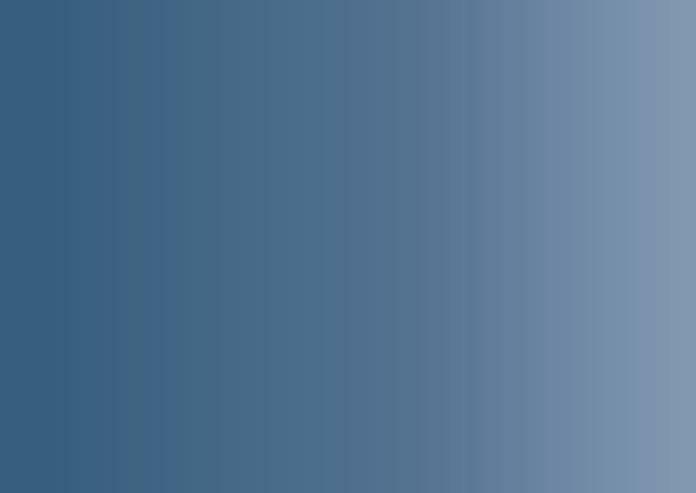






Elma Electronic Inc.
B.S. Electrical Engineering


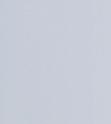
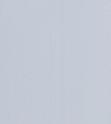
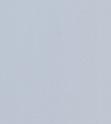
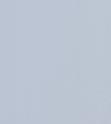
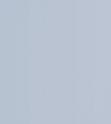

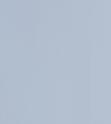

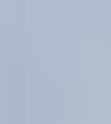

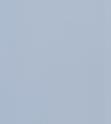
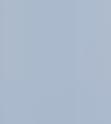

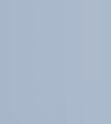
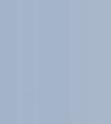

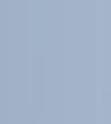
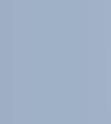
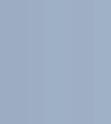

























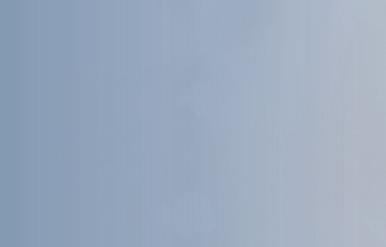

California Polytechnic State UniversitySan Luis Obispo
Talk about the culture at your company. What makes it inclusive or supportive of women in engineering and automation?
Elmanians, as we call ourselves, are a truly multi-cultural group! We pride ourselves on the diversity of our teams, who represent people from all over the globe and walks of life. The culture at Elma welcomes women and people from all types of different cultures. Women are listened to, and our opinions have weight. Most engineers are accepting of women in our industry, and due to that, I feel very fortunate to be in this field.
Describe a recent company project (in which you were involved) that went particularly well. How did you and your team go about ensuring success?
Melissa is a Senior Backplane Engineer and has been with Elma Electronic for almost 25 years. She holds a BS in Electrical Engineering from California Polytechnic State University –San Luis Obispo. Melissa is an indispensable leader in the design of high-speed backplanes used for implementing embedded computers based on high performance open architectures like OpenVPX, SOSA and others. She works through the entire backplane design process, starting with supporting sales on the technical aspect of customer quotes; working with the PCB designers for the schematics and layouts; verifying designs while helping to ensure a quality finished product with the manufacturing team. She is an integral part of a team of mechanical engineers and cable designers that design and deliver the full embedded computing chassis and backplane integration built to customer specifications.
A recent project came to us from a long-time customer, whose newest computing platform was quite small. They wanted us to fit the backplane and two computer boards. It required organizing internal meetings with a special team of backplane designers, a mechanical designer, signal integrity engineer and cabling designers. Due to the severe space limitations, we had to work out a way to fit all the electronic circuits. The solution we proposed came out of a different approach than our usual methods. The team had to be flexible to accommodate changes from the customer, and with frequent internal meetings, we could keep everyone informed and included in the process. It ended up a very rewarding experience for everyone involved, a process that we have continued with new projects.
What first drew you to engineering and this industry?

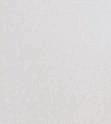
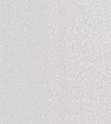
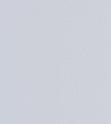
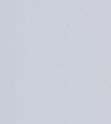
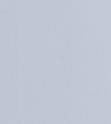





My father was an engineer. He enthusiastically encouraged my fascination with and love of NASA’s Apollo space program. He also brought home one of the early programmable calculators and taught me how to play a submarine game on it. When it was time to choose a university program, I chose electrical engineering, originally because I wanted to get into solar energy. Now I support customers who help enable innovations in the energy sector as well as other industries.
Describe your biggest career challenge. How did you solve it — or what was the outcome or lesson learned?
In the early to mid-90s, I experienced multiple layoffs. It was frustrating and demoralizing, but I stuck with it because I enjoyed what I was doing and wanted to continue to grow in my chosen field. While interviewing, I learned to read red flags, and how to find the positives. The experiences also taught me to understand what I liked and disliked about working in certain industries. One important thing I learned is that I enjoy working for companies that aren’t too large.
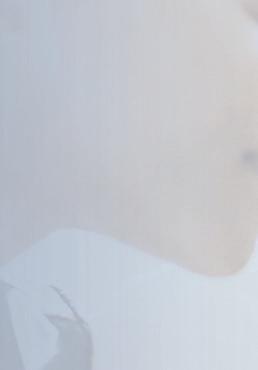

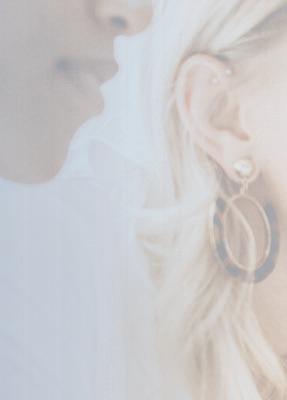
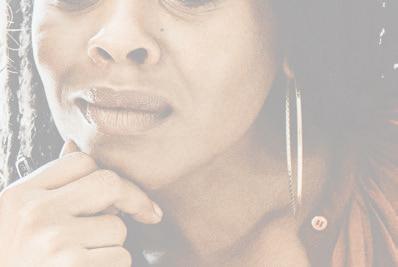
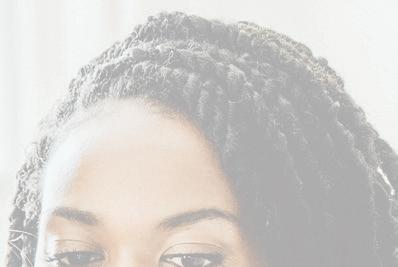
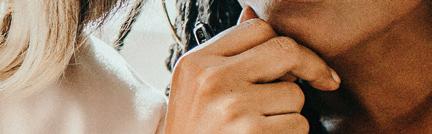
For the rest of Melissa Heckman’s insights, visit www.designworldonline.com/WiE.
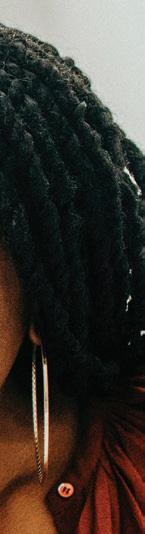
Women in Engineering

Melissa Wallin
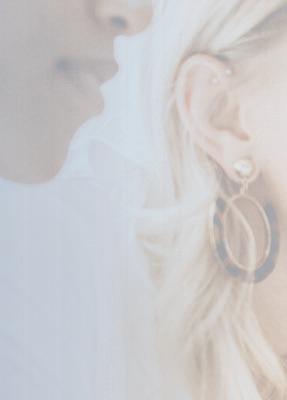

Sustaining Engineer Encoder Products Company






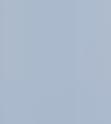

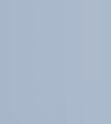
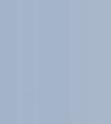
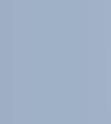
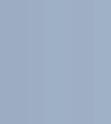


















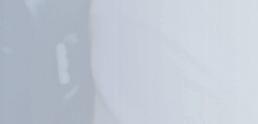
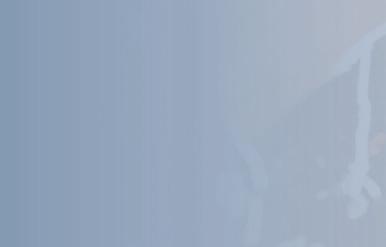
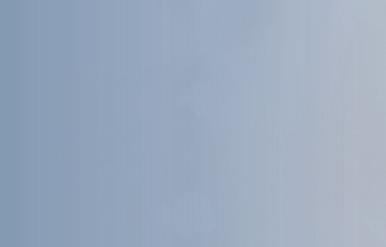






B.S. Mechanical Engineering
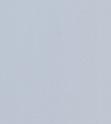
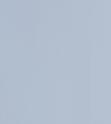
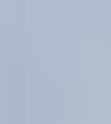
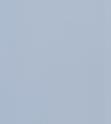

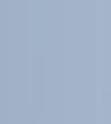








University of Wisconsin-Platteville
Talk about the culture at your company. What makes it inclusive or supportive of women in engineering and automation?
I have always appreciated Encoder Products Company’s desire to see its employees thrive in the work they do. I’ve been asked on multiple occasions, “Are you enjoying your work? Is there any career path you’d like to explore?”

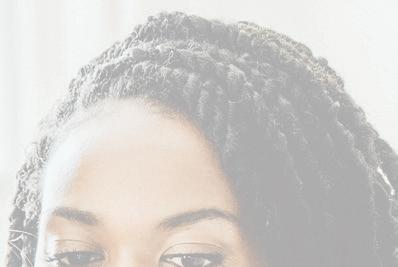
If I find myself wanting a new challenge or a different path in my career, the company has always been open to considering it.
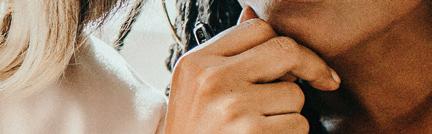
Describe a recent company project (in which you were involved) that went particularly well. How did you and your team go about ensuring success?
Our sustaining team was met with an unplanned part shortage, and we needed new parts as soon as possible so an order could ship ontime. The sustaining engineering team needed to work with our in-house manufacturing process to make the part, the Quality department to review and approve the new part, and production to install the new part and get the order complete before the deadline. Every department worked together and understood the urgency of the situation, and with great team effort, the order shipped on-time.
What first drew you to engineering and this industry?

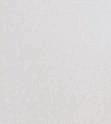
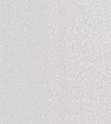
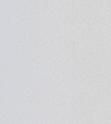

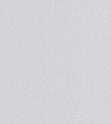

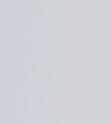
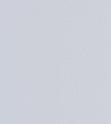
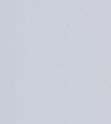
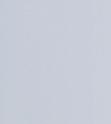
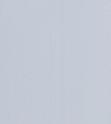
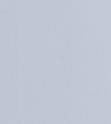
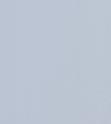
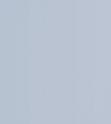






Engineering was something my dad (also a mechanical engineer) put on my radar. In high school I had a Rube Goldberg project in which my team and I opened a can of soda using a chain reaction of simple machines. It required lots of time in my dad’s shop designing and assembling the device. After the project was complete, my dad remarked that the project seemed to come very naturally to me and asked if I’d ever considered engineering as a career. I enjoyed working with my hands and using the scientific method to solve problems, so mechanical engineering seemed like a good fit.
Describe your biggest career challenge. How did you solve it, or what was the outcome or lesson learned?
Melissa Wallin is a Sustaining Engineer at Encoder Products Company, where she develops solutions to product and production problems through fixturing, improved processes, and design changes. She holds a B.S. in Mechanical Engineering from University of WisconsinPlatteville. In her free time, she enjoys hiking, fishing, and baking.
My biggest career challenge is knowing when to act on a problem. For example, production may be seeing issues with installing a screw. Now the question is, what is the root cause of this issue? Is it the screw? Is it the method of installing the screw? Who was involved? Et cetera. Collecting this information is time consuming and sometimes challenging, so you must discern when you have enough information to act. The challenge is knowing when that time is.
What career advice would you give to your younger self?
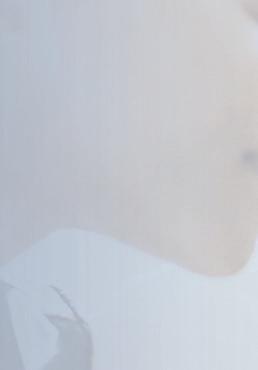


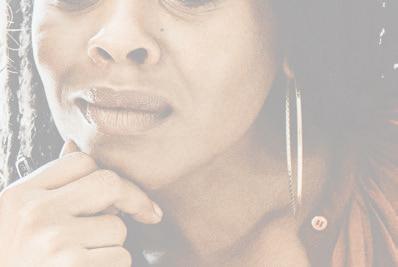
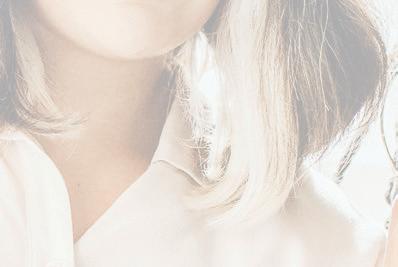
Don’t be afraid to be wrong. There are plenty of times when you will mess up or assume something incorrectly. That’s ok, and it doesn’t necessarily mean you’re a bad engineer. I think it is very easy, especially as a woman engineer, to doubt your skills and think yourself unqualified for the task at hand. While there are always things to learn, the worst thing you can do for yourself is avoid new challenges. There is little growth when you do that.
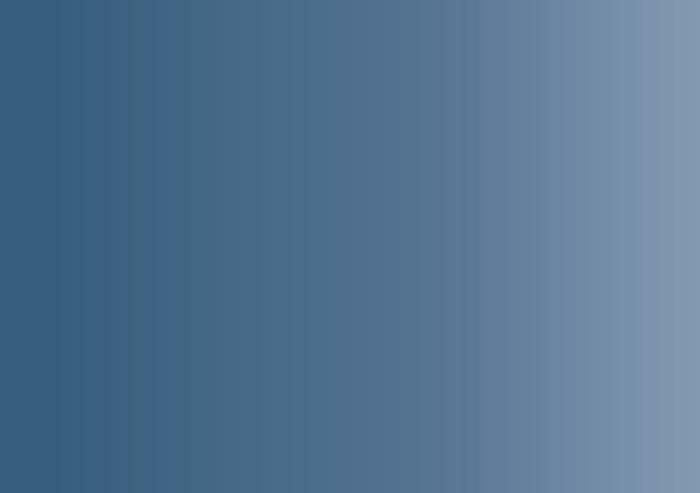
For the rest of Melissa Wallin’s insights, visit www.designworldonline.com/WiE.
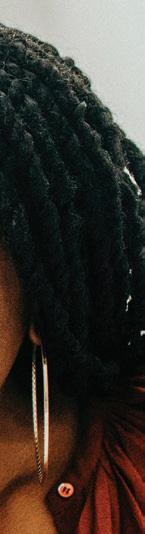
Women in Engineering
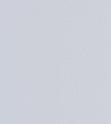
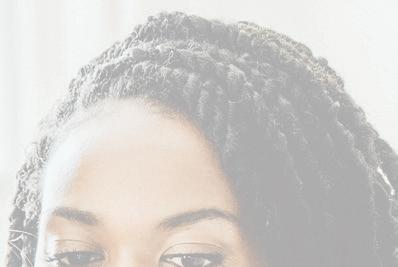

Kristen Copeland Moore

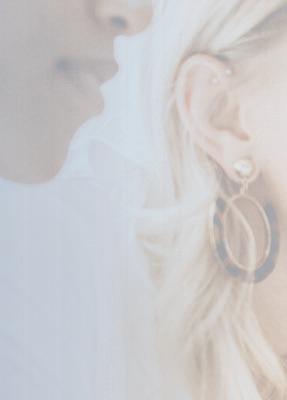
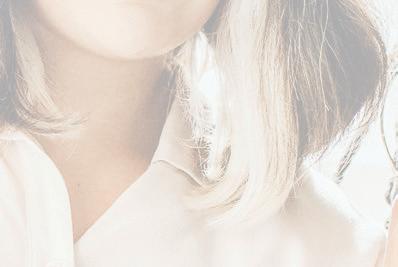



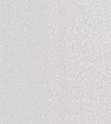
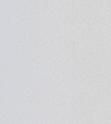

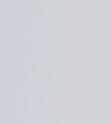


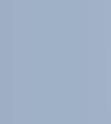
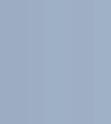

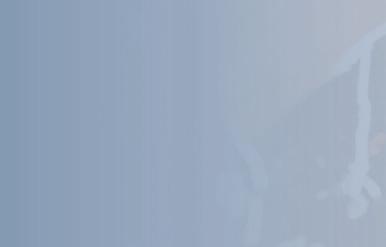
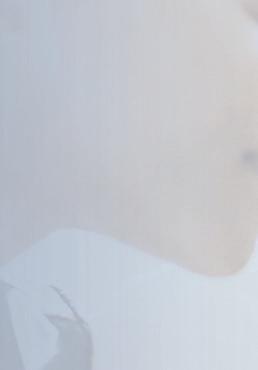
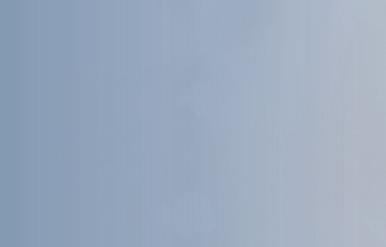
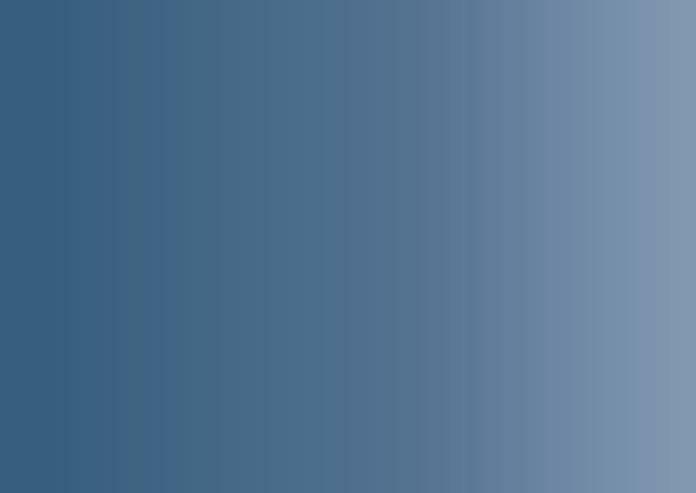










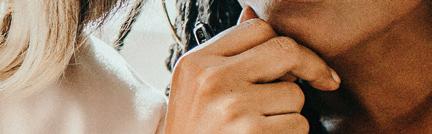
Bachelor’s in mechanical engineering with a minor in mathematics, University of Alabama

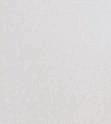

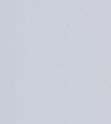
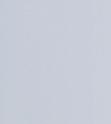
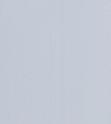
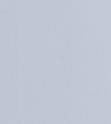
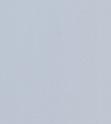
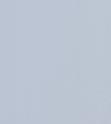
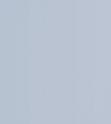

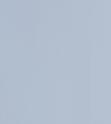

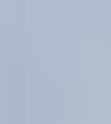

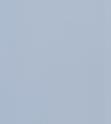
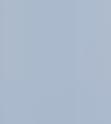

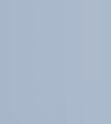
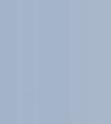

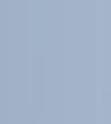












Master’s in business administration with a specialization in sales, University of Alabama















Talk about the culture at your company. What makes it inclusive or supportive of women in engineering and automation?
igus has a very welcoming culture and they are not afraid to take a risk on atypical employees. At the time I was hired, I was the first female outside technical sales representative for our energy chain and cable management division. When I interviewed for the role, our upper management made me aware that I would be the first female in this position, but they informed me that if I was up for the job, they thought I would be a great fit. In a male dominated field, I am grateful that igus was prepared to step outside of the box when offering me the job and they have continued to support me every step of the way.
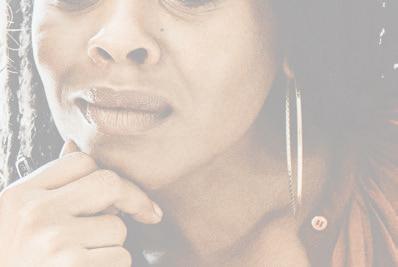
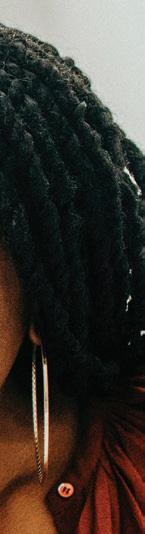
Describe a recent company project (in which you were involved) that went particularly well. How did you and your team go about ensuring success?

Moore participated in the STEM program when she worked on both her bachelor and master’s degrees. She had various mechanical engineering internships with companies such as Project Design Group, Austal USA and Airbus Americas Engineering. These experiences helped her realize her passion for helping people solve problems on a day-to-day basis. Since graduating college, she has worked as an outside technical sales representative and a territory sales manager for igus for the last four years. This position has allowed her to combine her love of engineering with her passion of helping customers find solutions and design innovative equipment using igus products.
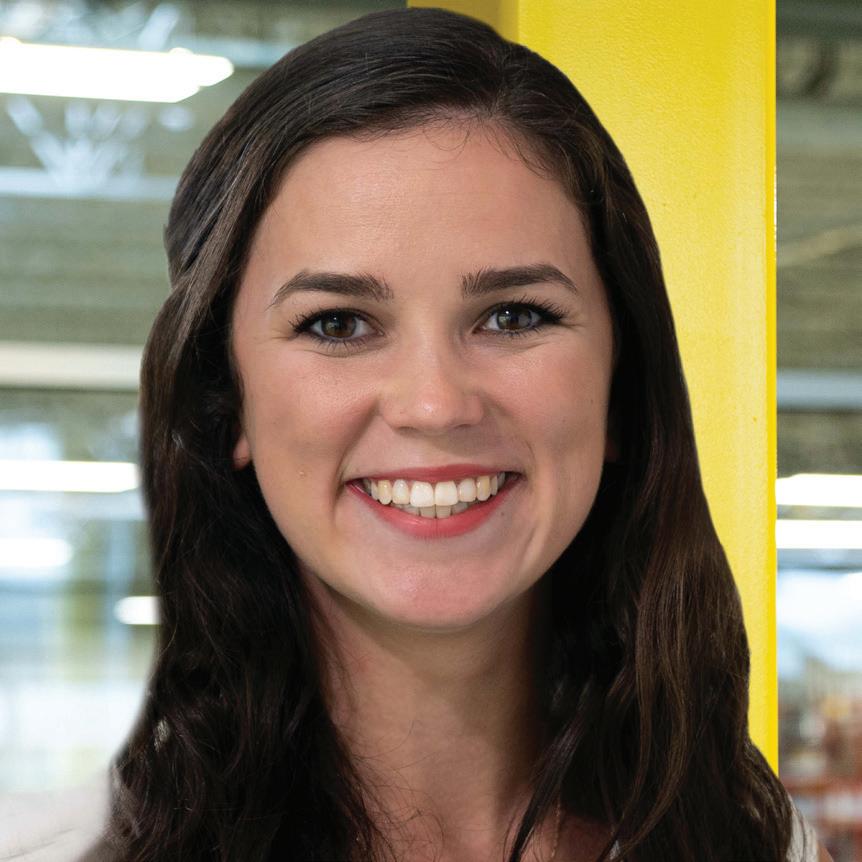
I recently had a customer that was using our cable management system for a plasma table. Our product was originally designed in many years ago by a third-party engineering company and it was not designed per our specifications. This led to frequent failures of our product that was causing the customer expensive downtime. Through various meetings with myself, my regional manager, and our industry manager, we were able to demonstrate to the customer how our newly proposed solution would differ from their current cable management system. It took several different meetings and proposals to ultimately regain the customer’s trust in not only our products but our capabilities as well. We were even able to take things one step above from just offering them products and provided the customer with a turnkey installed system. Since we installed our system two years ago, the customer has seen no downtime which has also restored their confidence in our products and our company as a whole.
Describe your biggest career challenge. How did you solve it — or what was the outcome or lesson learned?
My overall biggest career challenge has been gaining the respect of maintenance managers and engineers who have been doing their jobs longer than I have been alive. Some customers are sometimes reluctant to take constructive criticism from me and would sometimes push back on my recommendations. Ultimately this taught me to enter meetings with even more confidence than I normally would and not to back down from my recommendations. I must trust that I am the product expert in my field and that I have something positive to offer my customers. What originally began as a challenge in my career now has transformed me into a more confident sales engineer.
For the rest of Kristen Copeland Moore’s insights, visit www.designworldonline.com/WiE.
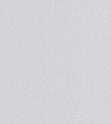
Women in Engineering

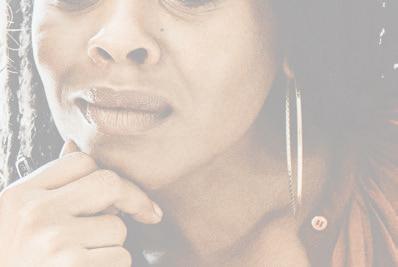
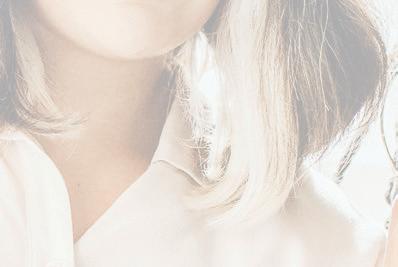
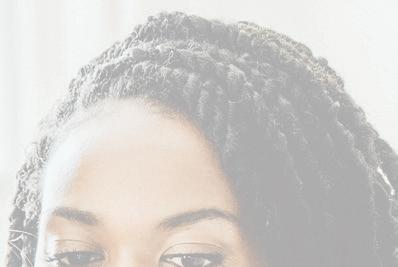
Jaya Bindra
Director of Applications Engineering, IoT, Compute and Wireless Division Infineon Technologies


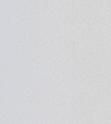





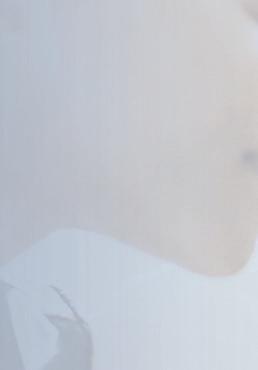
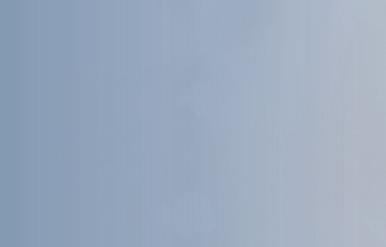
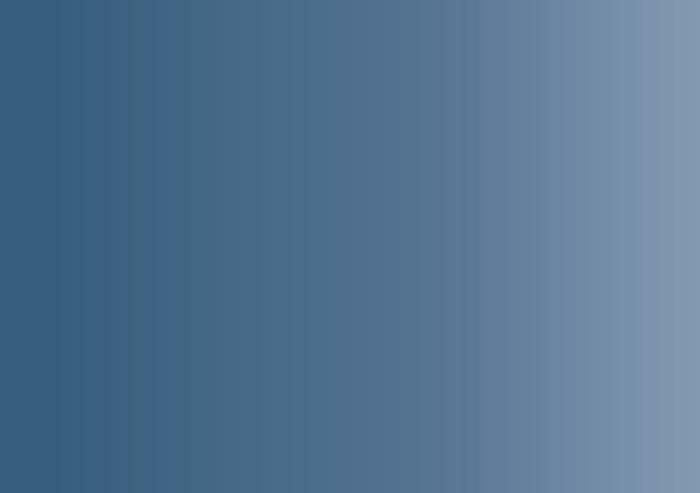




Executive General Management (MBA) Indian Institute of Management - Bangalore, India
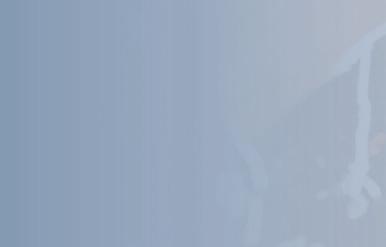


Bachelor of Technology in Electronics and Communication - Kurukshetra University, India

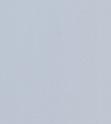
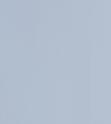
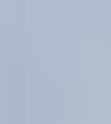
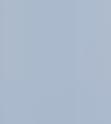
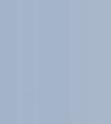

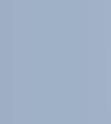
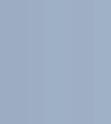






























Talk about the culture at your company. What makes it inclusive or supportive of women in engineering and automation?
Infineon is a unique company that provides ownership of impactful and challenging projects to employees at all levels The company also guides them to the finish line, which is something I appreciate. Infineon inspires me to embrace innovation and continue to work towards creating a new, better version of myself.
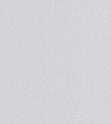
Describe a recent company project (in which you were involved) that went particularly well. How did you and your team go about ensuring success?
In October 2021, our fairly new team of two were approached to deliver a proof-ofconcept for a demo that runs a completely new, state-of-the-art technology called ‘Matter’ using Infineon products. Our deadline was only two months to architect, design, build hardware, firmware and a mobile App to present the demo. The complex project included integrating different Infineon products such as PSoC™ 6 MCU, PSoC™4 MCU, AIROC™ WiFi/Bluetooth devices, OPTIGA™ Trust M, to make a full-fledged smart lock design.
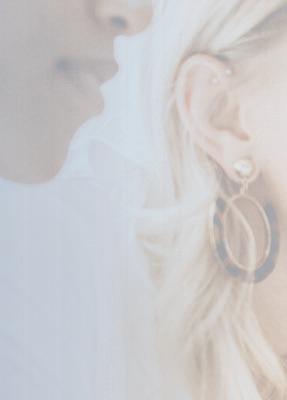
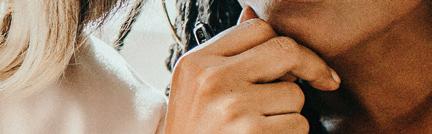

Jaya loves to mentor teams and enable their creativity to build innovative solutions that make life easier, safer and greener. She takes great pride in leading the Applications and Solutions Development group at Infineon in India.
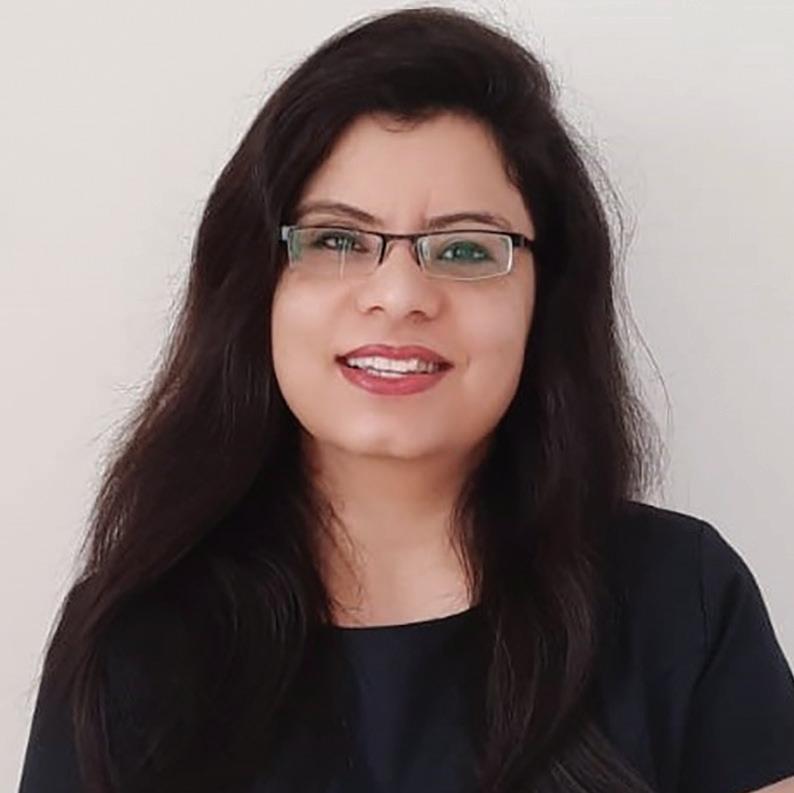
“My team encourages me to be a better version of myself by putting their trust in me as a leader, and I ensure I live up to their expectation by introducing learning opportunities and working hard towards developing their career.”
During her school years, Jaya was a national level gymnast and even today indulges in casual somersaults. She believes in simple and innovative solutions to problems. She is passionate about technology and has authored more than 45 technical write-ups in international magazines related to IoT and embedded systems.

While our team was architecting and learning the new technology, we also collaborated with design partners to support the development. We were able to secure a partner, and our two-month journey began. We trained our partner while working on the design. Eventually, this partner acted like our extended team for Hardware, Firmware and App development and we were able to deliver the solution one week before our deadline.
The notable achievement is the final demo looked more like a reference platform than a proof-of-concept, and the same demo became Infineon’s flagship demo for ‘Matter’ at various events thereafter including CSA (who define the Matter spec) and Embedded world events.
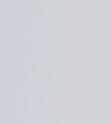

What first drew you to engineering and this industry?

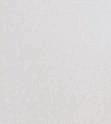
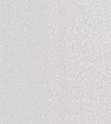
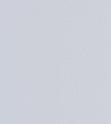
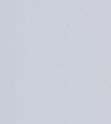
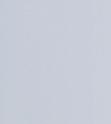
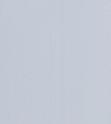
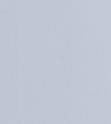
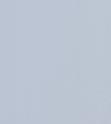
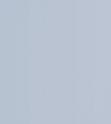

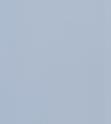
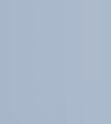
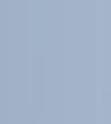



Interest and curiosity initially drew me into engineering. Things like resistors, capacitors, and lights fascinated me. When it came to studying engineering, I knew from the get-go it would be Electronics Engineering. A good engineer requires one to be a creative problem-solver.
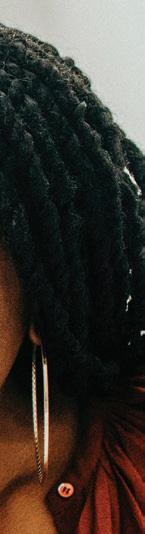
As engineers, we make things work. And I have always enjoyed design and building things, resulting in greater job satisfaction, and keeping me engaged and interested. What I enjoy most is helping customers solve their interesting and complex issues using the right technology, products and software.
For the rest of Jaya Bindra’s insights, visit www.designworldonline.com/WiE.
Women in Engineering
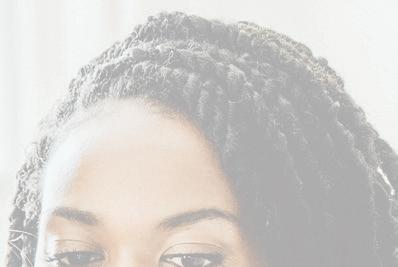
Nicole Mathieu

Inside Sales Engineer maxon



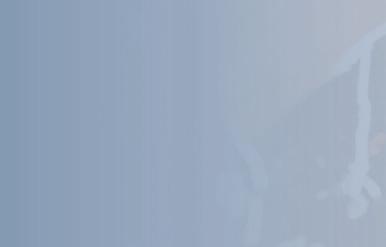
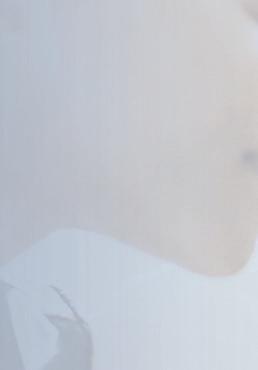
B.S. Mechanical Engineering University of Massachusetts, Dartmouth




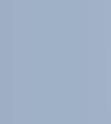
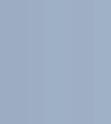


























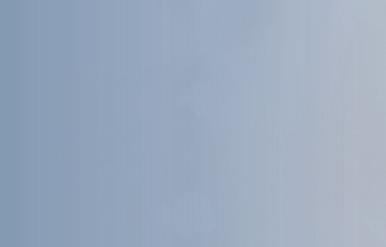
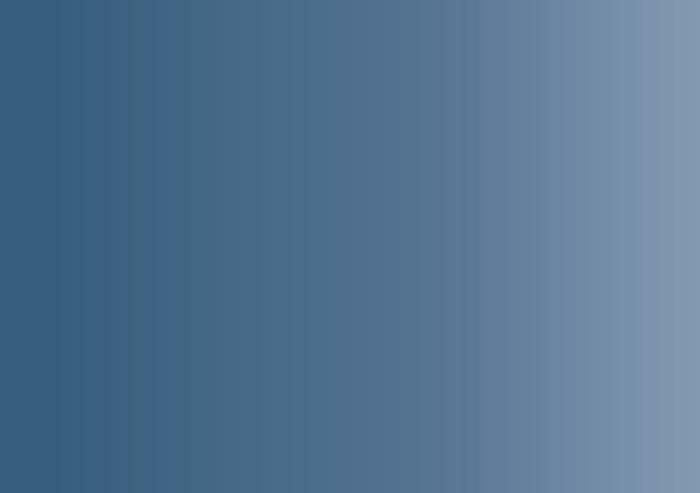
Talk about the culture at your company. What makes it inclusive or supportive of women in engineering and automation?
A main thing I would say about maxon is that they do not hold you back, they want you to succeed and provide you with the tools and support to do so. Anytime you need help or clarification there is always someone there to jump in. I was able to be mentored by various people at my company where they took the time out of their day to help me grow as an employee as well as a person. We have an amazing Women in Engineering program where we do quarterly meetings with the women globally at our company. This group allows us all to connect, lean on each other for support and share our experiences.
What first drew you to engineering and this industry?

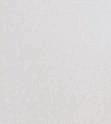
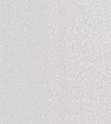
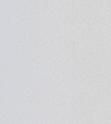

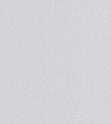

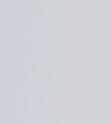

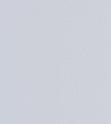
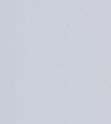
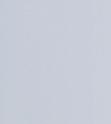
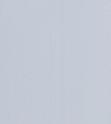
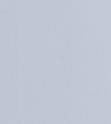
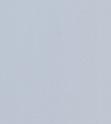
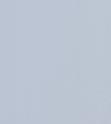
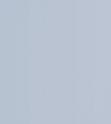

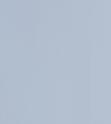
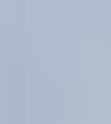

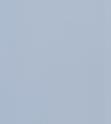
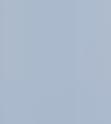
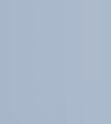
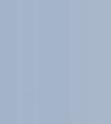
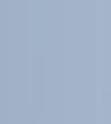












Nicole Mathieu graduated from Umass Dartmouth with a B.S. in Mechanical Engineering in 2020. During her time as a student, she completed an internship at Night Vision Technology Solutions in Jamestown, RI where she created 3D rendered images of night vision cameras used in combat. She began her professional career March of 2021 at Maxon Group Inc. in Taunton, MA. At maxon she works as an Inside Sales Engineer where she acts as a technical and sales support to the outside sales team and small accounts for four territories (Midwest, Upper East, Central and Mexico). Outside of the office, she participated as a panel member for a Society of Women in Engineering event this past May where she was able to be the person she once needed.

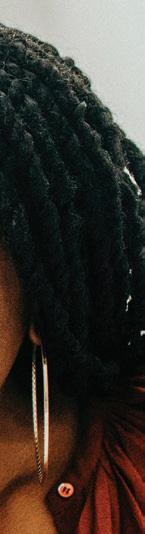
I have loved math and problem solving since my first algebra class. To me, math problems felt like a puzzle where it was fun to do and only had one answer. I am also a very high energy person so when I was able to zone out while doing math and just focus on one thing, it felt nice. I later took physics in high school and one project was to design and build a roller coaster. I instantly loved it because I was able to use math to create something. With my love of math and coming from a family of engineers it felt natural to go down the engineering path. I loved the concept of ideas becoming reality and being able to be a part of that process. I chose mechanical engineering because it was the broadest, it came with a lot of opportunities and options when selecting a job focus. I was drawn to sales engineering because I was able to use problem solving as well as channel my extroverted personality when it came to the sales end. Working in the motion control industry, I can communicate with customers to find out their application needs, help find them a solution and see their ideas come to life. I find it to be rewarding both personally and professionally.

What career advice would you give to your younger self?

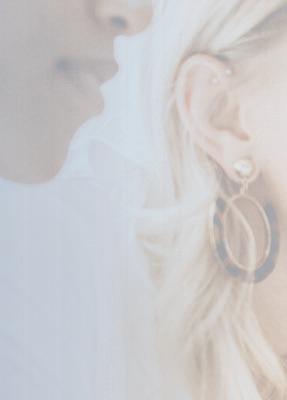

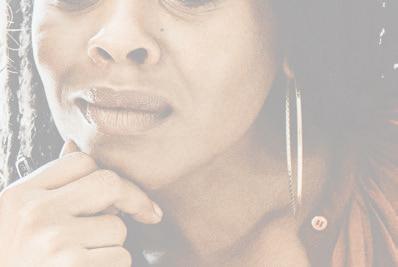
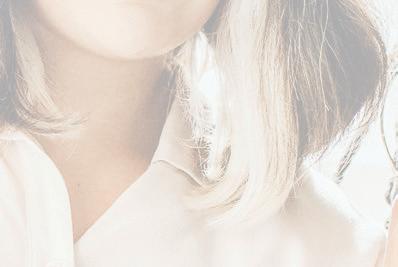
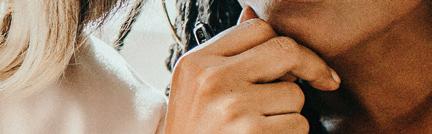
If I could tell the younger version of myself anything it is to simply see it through. No matter how hard something gets or how many times you stumble, never forget why you started. Always believe in yourself even when it seems impossible. Success is on the other side you must keep going to be able to achieve it.
For the rest of Nicole Mathieu’s insights, visit www.designworldonline.com/WiE.
Women in Engineering

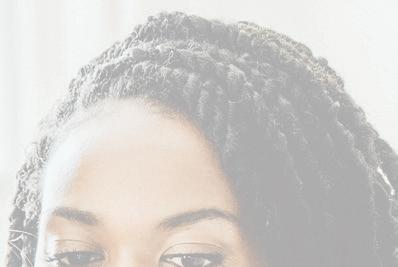
Annalisa Regalado

STEM outreach representative
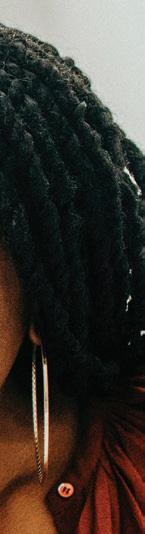
Microchip Technology Incorporated
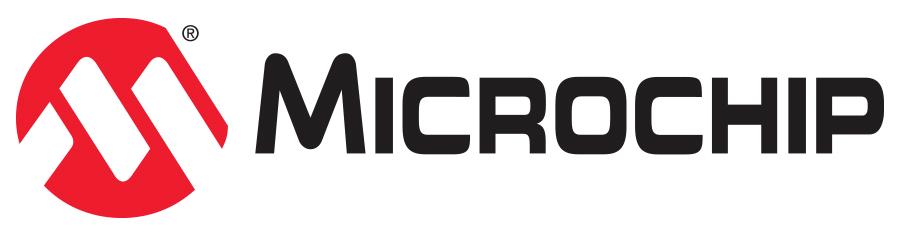
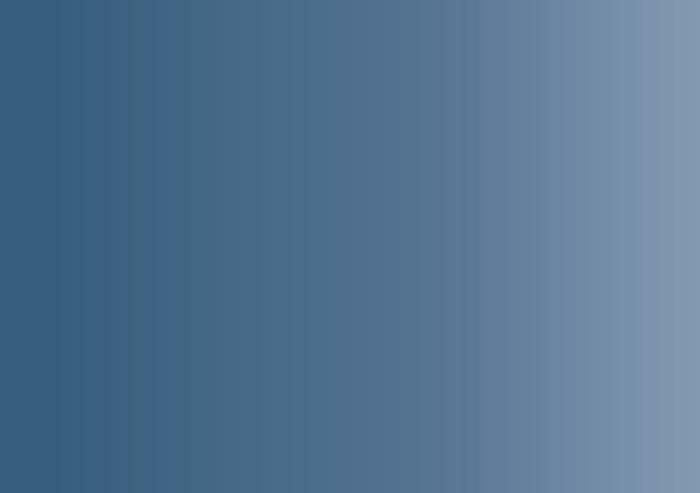
Bachelor of Science in Engineering Arizona State University



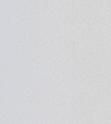


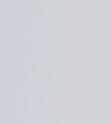

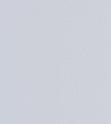
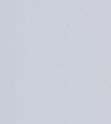

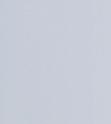
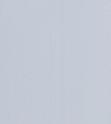
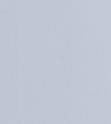
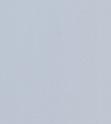
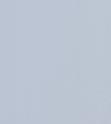
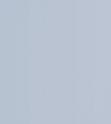

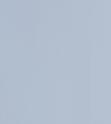

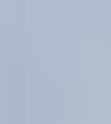

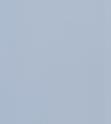
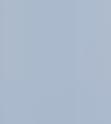

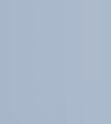
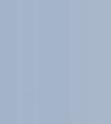

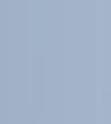
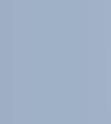
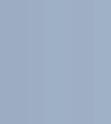


























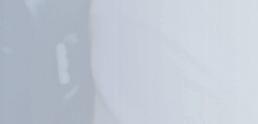
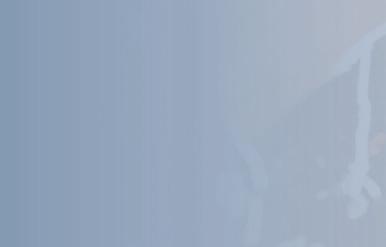
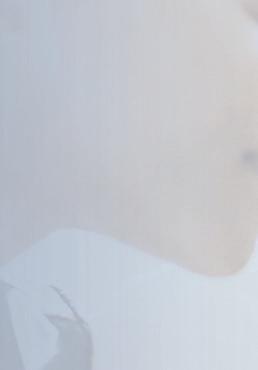
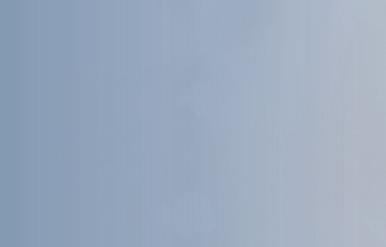










Talk about the culture at your company. What makes it inclusive or supportive of women in engineering and automation?
One of Microchip’s Guiding Values is “employees are our greatest strength,” where inclusion and diversity are emphasized. We have programs that promote and encourage outreach in our communities, from offering mentorship and volunteer opportunities, to helping those in need. I co-chair AZFirst, the charitable foundation founded by Microchip, whose mission is to initiate and support the study of science, technology, and engineering. I am a direct result of one of the programs Microchip supports and wouldn’t have earned my degree had they not provided access to mentors and programs that promote and encourage women to go into STEM careers.
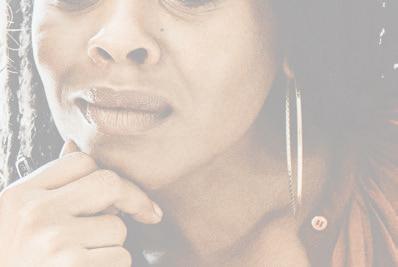
What first drew you to engineering and this industry?
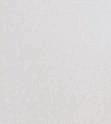
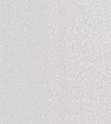


Annalisa Regalado is the STEM outreach representative for Microchip Technology, headquartered in Chandler, Ariz. She manages both internal and external STEM programs, including For Inspiration and Recognition of Science and Technology (FIRST) and Robotics Education & Competition Foundation program offerings. She serves as the statewide regional director for the FIRST Robotics Competition and is an event partner for the Robotics Education Competition Foundation. Her main objective is to engage and support students through science, technology, engineering and math (STEM) programs, grants and scholarships.
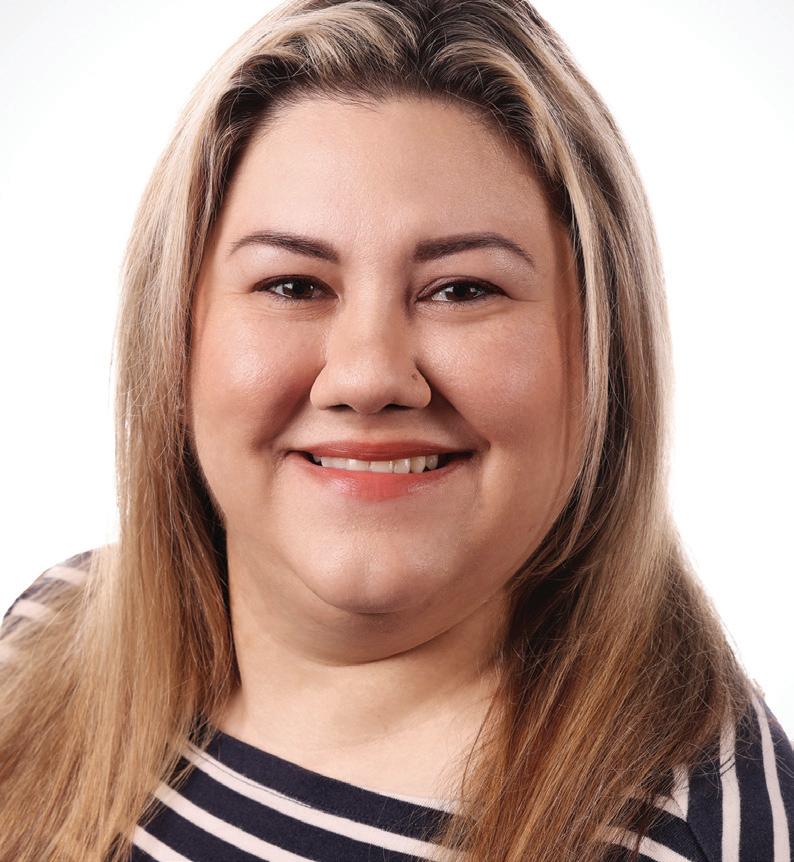
Annalisa is an ASU alum, earning her B.S.E. in Engineering. Her previous positions include several years at Arizona State University as a community and student engagement coordinator, assisting three executive directors, planning and executing K-12 summer camps, recruitment and retention, student advising and front desk administration.
I went through a marine biology program in high school and I initially wanted to be a whale trainer but knew I would need to look outside of Arizona for college and a career. Next to the marine biology room was a smaller room that housed the afterschool Robotics Club. Being the oldest of four girls, fixing things wasn’t completely unfamiliar, but this was more than just helping fix a kitchen sink. One day, they asked for help painting wood for a crate that would be used to ship a robot to California for a competition. Soon after that I was attending meetings and helping to write technical reports. I started spending a lot of time with the other club students and I started to see myself doing engineering as a career. Electric cars, trebuchets, land and underwater robots became my favorite projects. I was elected the club’s president my junior and senior years of high school. Having been on the robotics team for four years, I knew this was the field I wanted to pursue. Now at Microchip, I get to help those same teams and know first-hand the difference these STEM programs can make in a young person’s life.
Describe your biggest career challenge. How did you solve it — or what was the outcome or lesson learned?
My biggest hurdle started in college. As one of only three women from my graduating class, trying to be accepted by my professional peers was tough. By overcoming similar challenges on my high school robotics team, it better prepared me for the uphill battle to prove myself on project teams based on knowledge and not my gender.

In my current role, I have a similar challenge as I am younger than most of my team. I find having open communication and asking my co-workers for their input demonstrates my ability to complete the vision we set forth as a team.
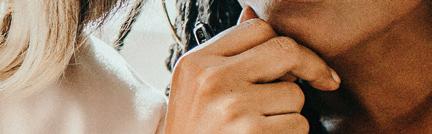
For the rest of Annalisa Regalado’s insights, visit www.designworldonline.com/WiE.
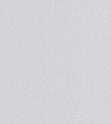
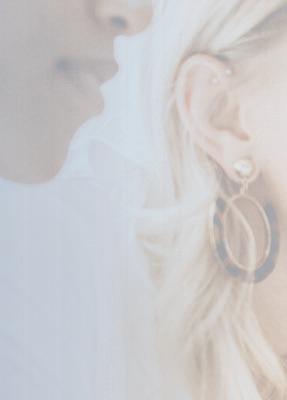
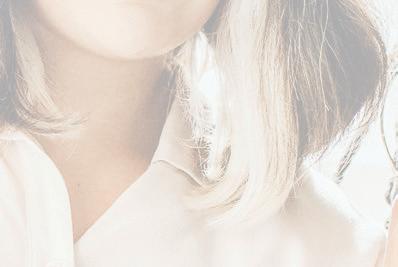

Women in Engineering


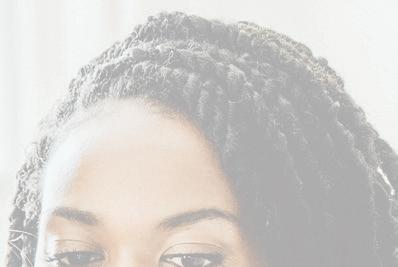

Deana Fu
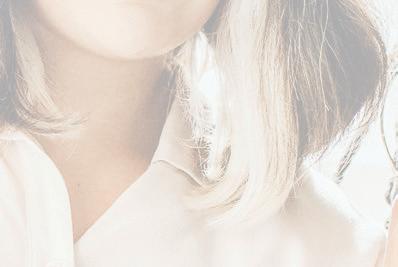
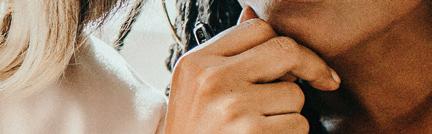

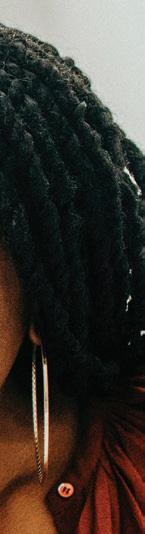
Director of Product Management


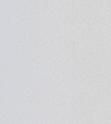
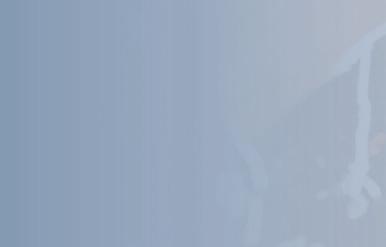
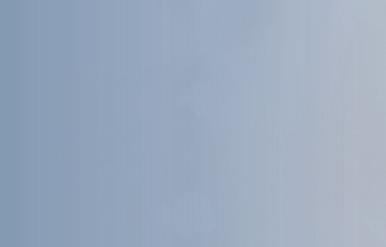







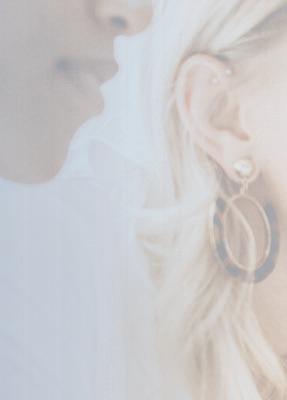
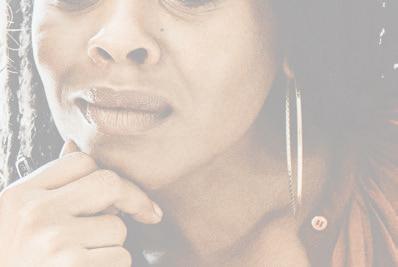
Mitsubishi Electric
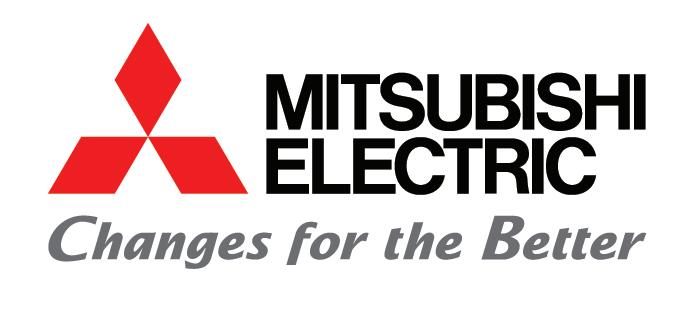
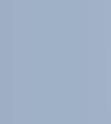



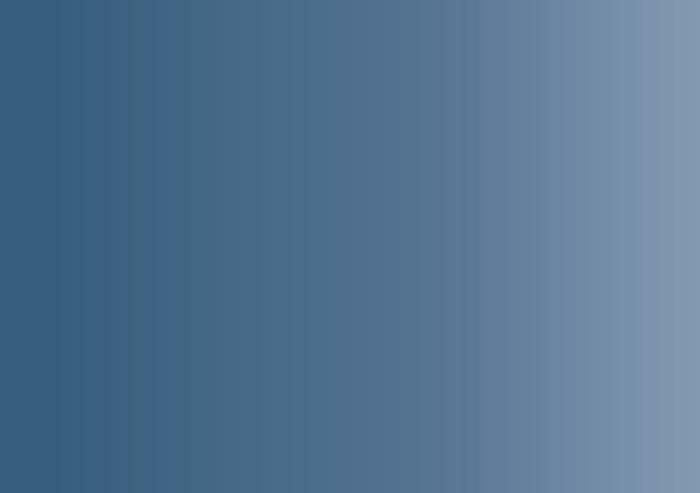
Electrical and Computer Engineering

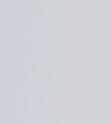



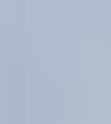



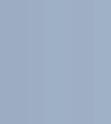























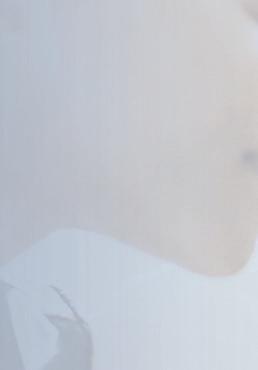
Cornell University
Deana Fu has served as a product manager for various industrial automation products throughout her career. Her passion is in the intricate weave of engineering, business, and relationshipbuilding. As the director of Product Management of Mitsubishi Electric Automation, Inc., she is responsible for the company’s product management team as they master their roles as innovators, problem solvers, and advocates for their product lines.
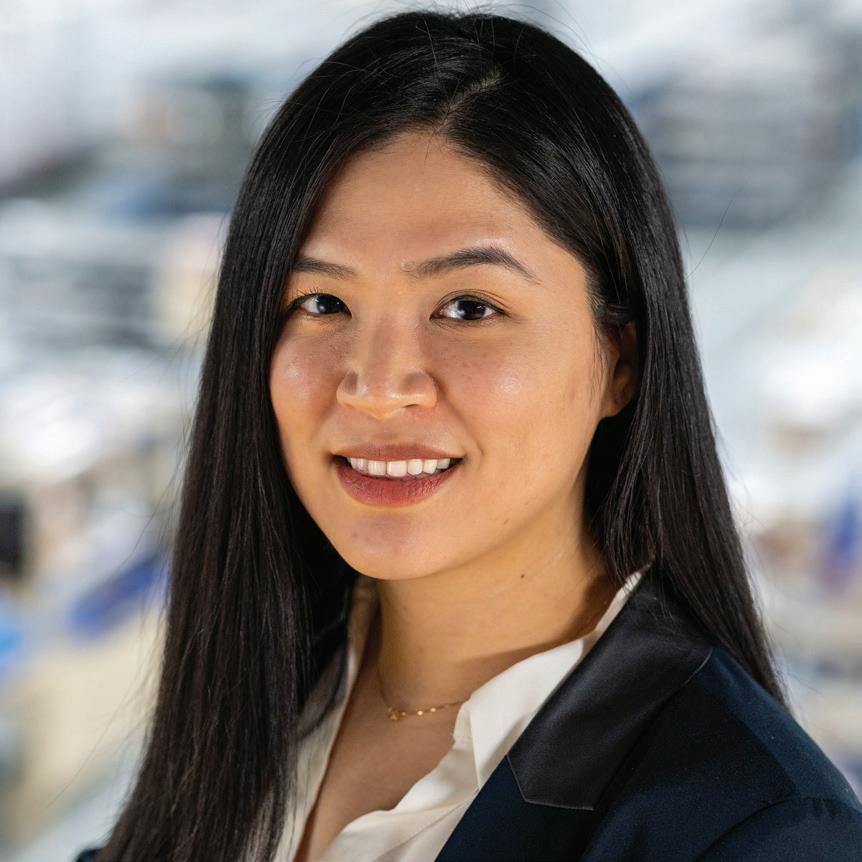
What first drew you to engineering?

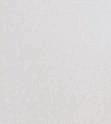
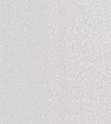

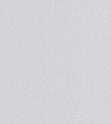
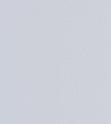
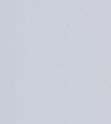
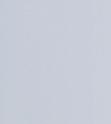
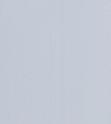
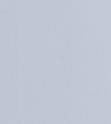
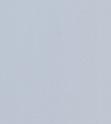
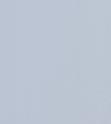
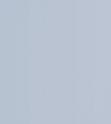

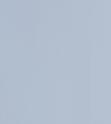
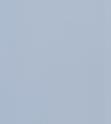
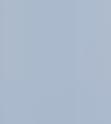
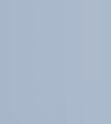
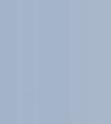
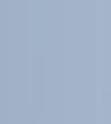





Sending their children to college was everything that my parents had hoped for. When it came time for college applications, I drew a blank at the field labeled intended major. I felt the conflicting emotions of almost living up to my parent’s expectations yet falling short for not having thought out what I was going to spend the next four years studying. I was raised to seek out new experiences, to step into discomfort, and to take calculated risks. So, I did exactly that, and off to Cornell University I went to pursue a degree in Electrical and Computer Engineering.
How has engineering helped you develop leadership skills?
I started in the world of manufacturing, first at Mitsubishi Electric’s factory in Japan and then at the American headquarters near Chicago. Transitioning to life and work in a different country helped me develop leadership skills that were foundational to my career in product management. When you are the least tenured of the team, you must persuade people to help you with your projects, listen and adjust to the team you are working with, and influence without authority over them. I learned to give myself grace when I made mistakes and to be humble in accepting advice and mentorship. When I first joined the team at our American headquarters, my assignment was to launch a campaign to accelerate adoption of a new programmable controller product. I called the stakeholders to get their buy-in, and time and again I heard, “I get that this is the latest and greatest technology, but my customers do not care.” I planned a road trip around the country visiting customers to understand the challenges they were trying to resolve, advocated for enhanced features and functions with the development team, and crafted a new campaign to motivate our sales team to achieve the results I sought after.
Give us an example of your involvement in: a design project, a product launch, the development of a new technology, or the adoption of a new technology or process. Recently, I was asked to lead the effort to implement a business operating system based on the 80/20 principle, which consists of driving a conscious decision to treat things with the appropriate amount of effort, based on the overall value they bring or could bring. Several cross-functional initiatives were implemented, and it became my role to coach each business group to define impactful strategies, be intentional at making data driven decisions (especially when it comes to resource allocations), and establish clear performance indicators to quantify progress. I had doubts about taking on this additional role of driving a cultural change within our organization. It seemed to be a distraction from my focus on building the best product management team I could. But after seeking out advice from my mentors, I realized nothing is in conflict at all. As a product leader, I not only have to understand the technical aspects of my product, but I also drive the growth strategy and own the business outcome.
For the rest of Deana Fu’s insights, visit www.designworldonline.com/WiE.
Women in Engineering

Dana Myers

Global Product Manager nVent
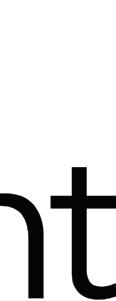
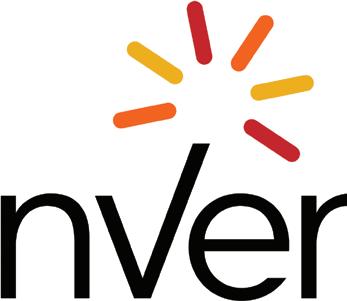


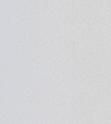
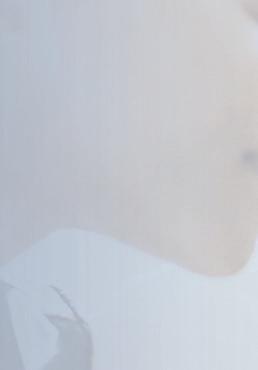
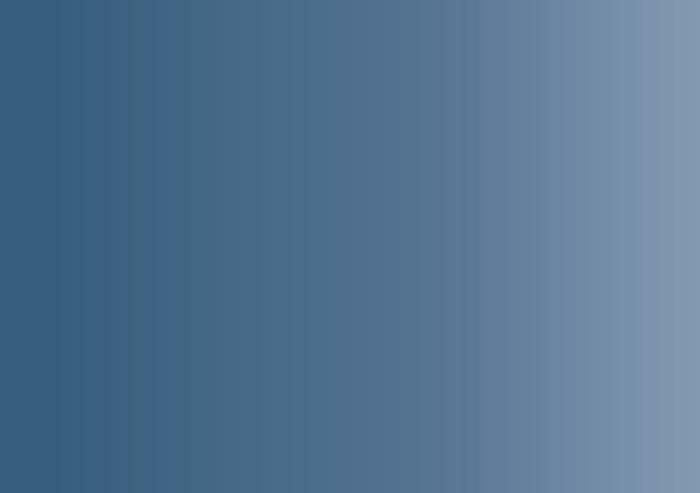





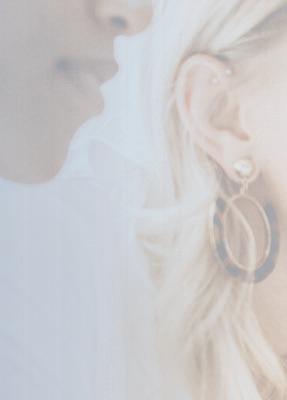

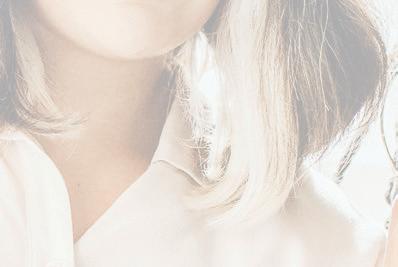
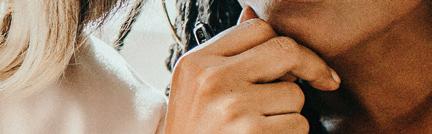
MBA - Carlson School of Management University of Minnesota

Bachelors in Mechanical Engineering Michigan Technological University

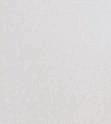
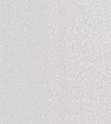

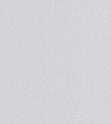

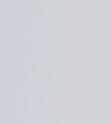

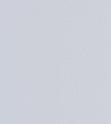
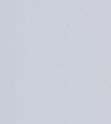

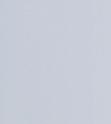
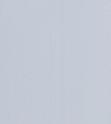
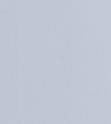
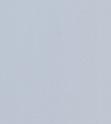
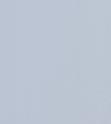
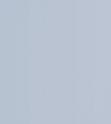

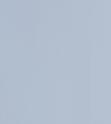

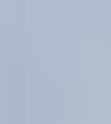

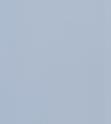
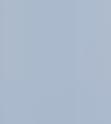

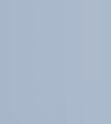
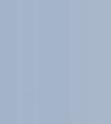

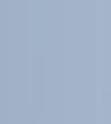
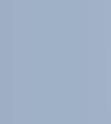
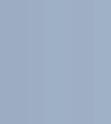


























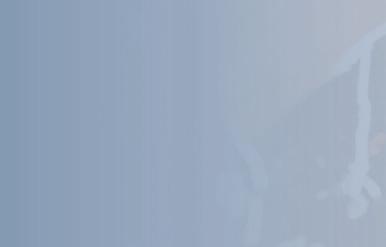
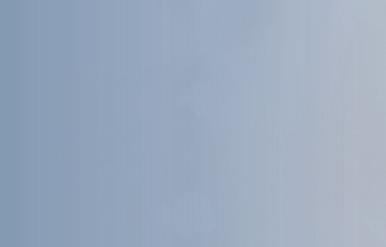






Talk about the culture of your company? What makes it inclusive or supportive of women in engineering and automation?
As a female engineer, I have worked in some very challenging environments. Learning to navigate tough environments in a male-dominated industry is something everyone struggles with. When you find somewhere that truly supports women and shows that by tapping them for leadership opportunities, having them in the board room, having diversity at all levels—that’s the real report card to me. nVent is far and away ahead of many other companies in our industry. My management chain all the way up to the top includes people I genuinely believe want to empower me to succeed. When the president of your company knows your name and asks how your son is doing, that should tell you something about how nVent values people.
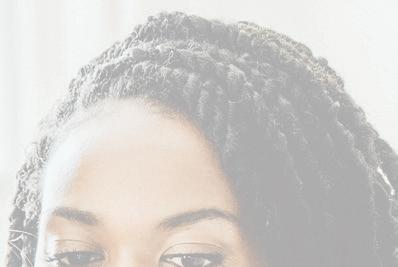
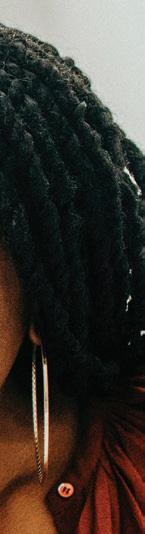
Describe a recent company project that went particularly well. How did you and your team go about ensuring success?
Dana Myers has worked at nVent for nearly 8 years. She entered as an industry specialist following a six year career in the functional and process chemistry consulting industry. During her time at nVent she has moved into several different roles and earned her MBA. She now works as a global product manager.

Dana specializes in building product portfolio strategies to solve unique customer application challenges. She makes an impact by developing and deploying new products and educating sales teams on how to best communicate and deliver the value-add to customers for the products she supports. Her favorite part of her job is the variety. No day is ever the same and she has welcomed the opportunity to work on projects that have pushed her and helped her grow her career at nVent.
I am fortunate to be surrounded by incredibly talented people. In the last few years we’ve had to challenge ourselves to get really creative troubleshooting supply chain and pricing challenges and not letting those things stand in the way of meeting customer commitments. We have been working for years on an innovative electrical enclosure for extreme environments. Knowing the customer problem and figuring out how to create a platform of products that clearly addresses those challenges in a technically advanced way is something I’m very proud of. From start to finish, our team was able to hold the paintbrush, innovate, develop the solution and bring it to life.
Describe your biggest career challenge. How did you solve it—or what was the outcome and lesson learned?
My biggest career challenge was figuring out what I wanted my career to look like in the first place! As I’ve navigated through different roles and responsibilities, I’ve gained a better understanding of myself and where my natural curiosities are, and I’ve learned how to leverage those things to bring value to a business. That growth has led me to a career that plays to my strengths, but I didn’t always know how to get there. I learned that for me, someone with a very mechanical mind, I like to create, I like strategy, I love working with people. I was fortunate to be able to find a workplace that values those things and puts me in a position to do them every day.

For the rest of Dana Myers’s insights, visit www.designworldonline.com/WiE.
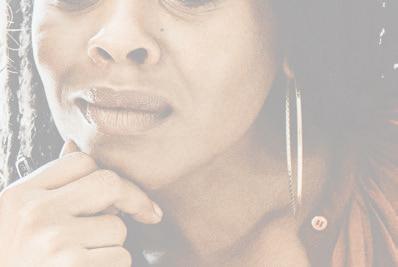
Women in Engineering

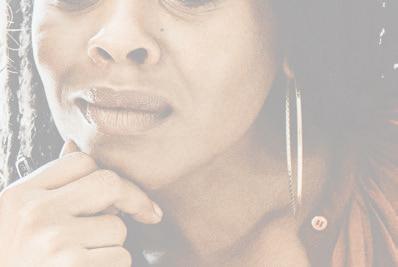
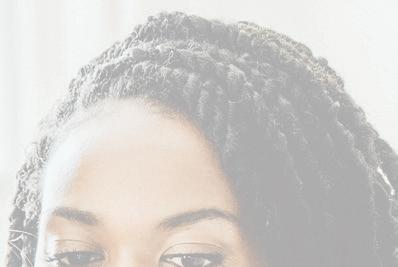

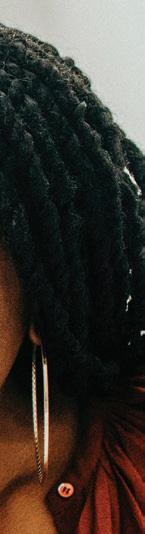
Ana Montes

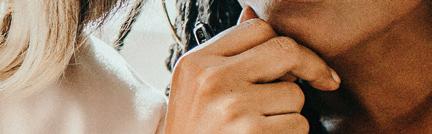

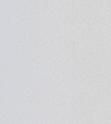
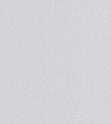

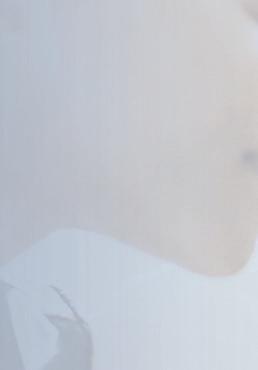
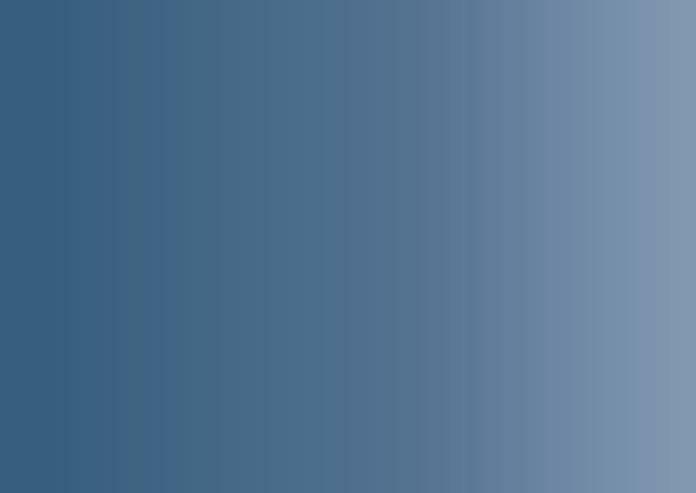


B.S. and M.S. Mechanical Engineering Universidad de los Andes (Bogotá, Colombia)
PhD Mechanical Engineering Northeastern University (Boston, MA)



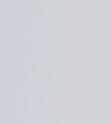


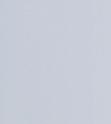
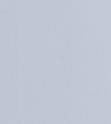
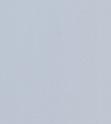
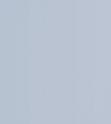
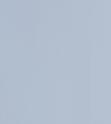

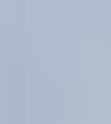

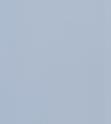
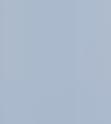

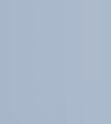
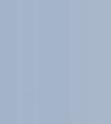

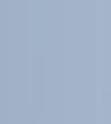
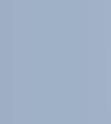
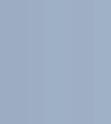


























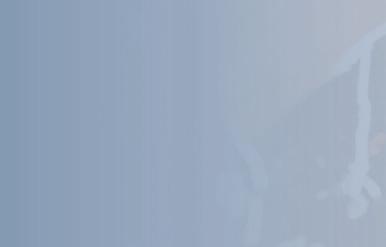
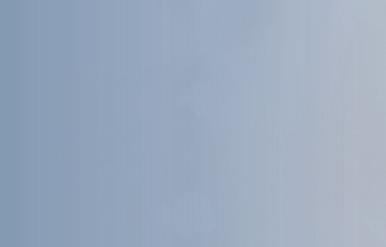





Talk about the culture at your company. What makes it inclusive or supportive of women in engineering and automation?
I’ve always liked that at Velo3D there is a strong sense of collaboration and respect. There are a lot of opportunities to interact with different teams, and everyone is always open to help and work together to achieve our common goals. I have always felt respected and included, and while many times I have found myself to be the only woman in a room or meeting, I’ve always felt my input has been valued and considered.
Describe a recent company project (in which you were involved) that went particularly well. How did you and your team go about ensuring success?
Originally from Colombia, Ana moved to the USA to pursue a PhD in Mechanical Engineering with an emphasis in Material Science. After graduation, she started as a Junior Process Engineer at Velo3D, where she now holds a position as a Senior Technologist. In this role, she works on developing laser powder bed 3D printing processes for a variety of metallic materials. One of her favorite parts about her job is getting to see how the processes she develops on small-scale test structures turn out when used in the 3D printing of large-scale components, and knowing that the technology she is helping develop enables the printing of complex and ambitious designs that allow fast innovation in the aerospace, transportation and energy industries.

I was recently working in qualifying a new material for the Velo3D printers. This material, called GRCop-42, is a copper alloy of particular interest to the aerospace industry. Due to its high reflectivity, conductivity and melting temperature, this alloy proved to be very challenging to print. The typical processes we use for other materials didn’t work very well for this one, and we identified new failure modes that we hadn’t seen before. We had a tight schedule, a small team, and a lot of work to complete. We also had a lot of pressure from other teams that depended on us completing our work to be able to start theirs. I started by clearly laying out what the main requirements would be for this project, while also keeping track of lower priority goals that could be tackled later. We set up regular internal check-ins to track progress, and kept the customer informed along the way on how the project was moving forward. While there were a lot of challenges related to maintaining good communication and synchronization across teams, I consider the project was overall very successful in that we were able to deliver a product that met and exceeded the customer expectations. It required a lot of hard work, a great team of people, good organization, many iterations, and open collaboration both internally as well as with the customer.
What first drew you to engineering and this industry?

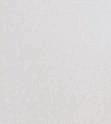
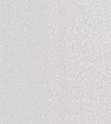
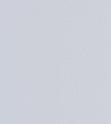
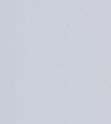
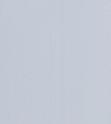
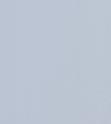






I loved math and science classes during high school. I found it very exciting to learn about basic concepts and principles that allowed me to derive exact solutions to problems. For that reason, engineering felt like a natural choice for me when selecting a career, even though I come from a family of artists. I started my undergrad in a General Engineering program, and after getting more exposure to the different path options available, I opted for Material Science and Engineering under the Mechanical Engineering Department.
In my senior year, I had the opportunity to join a research lab focused on powder metallurgy, and that experience sparked my interest in research and experimentation in manufacturing.
For the rest of Ana Montes’ insights, visit www.designworldonline.com/WiE.
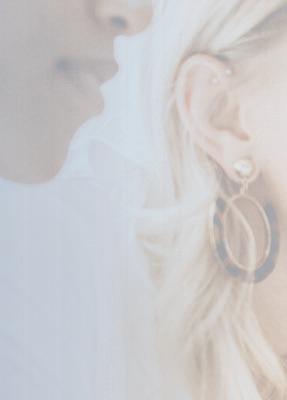
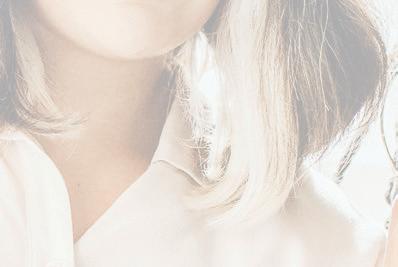
Women in Engineering
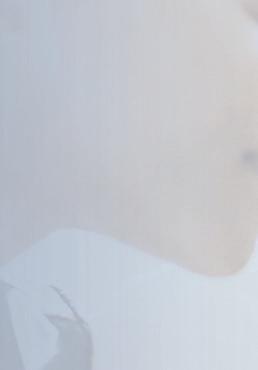


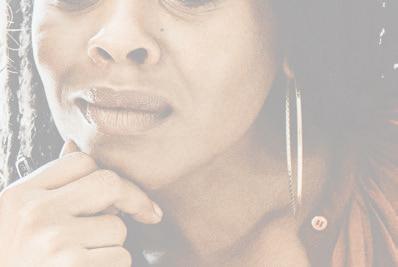
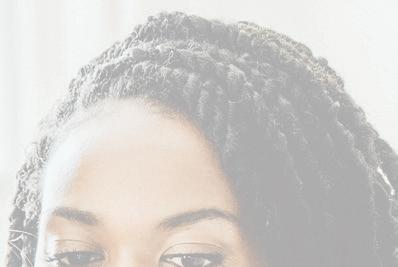

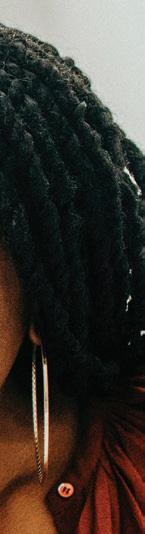
Maritza Ruiz
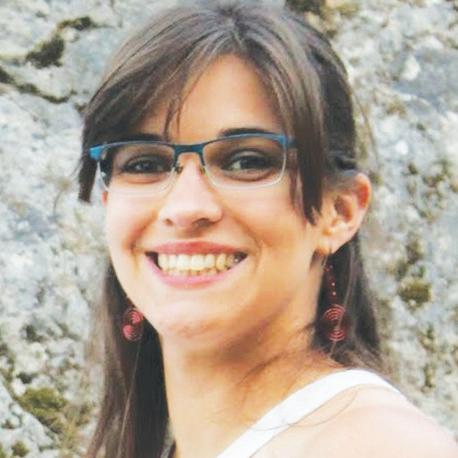
Talk about the culture at your company. What makes it inclusive or supportive of women in engineering and automation?
of Process Engineering Velo3D

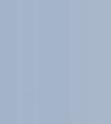

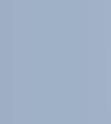
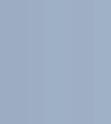























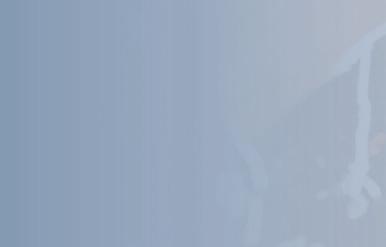
Director
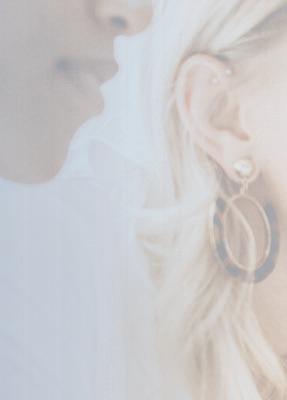
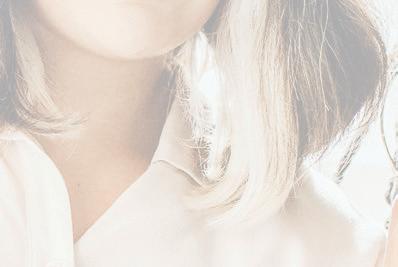
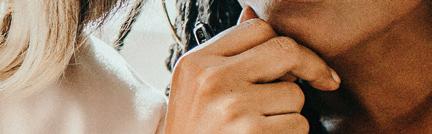
Maritza is the director of process engineering at Velo3D and has been with the 3D printing company for nearly 5 years. As the director of process engineering, Maritza oversees the qualification of new metal alloys in the company’s Sapphire family of printers. She also develops new processes and techniques to improve the material properties of parts printed using Velo3D technology and maximize the capabilities of the lasers used in Sapphire printers. Prior to joining Velo3D, Maritza was a Mechanical Design Engineer at the solar energy company SunPower. When not working with Velo3D’s world-class technology, Maritza enjoys mountain biking in the Santa Cruz mountains, gardening, and spending time with her husband and 6-month-old son.
At Velo3D, we have a very innovative environment which means we must be inclusive of diverse mindsets. We try and encourage innovation across all levels and we regularly see junior engineers and members of other non-technical teams provide possible solutions to various problems.
We also encourage internal mobility within the company, due to our collaborative environment. We regularly have people on adjacent teams—manufacturing, support technicians, and others—change teams to progress in their careers.
Describe a recent company project (in which you were involved) that went particularly well. How did you and your team go about ensuring success?
Early on, we had an issue where one of our printers was generating a safety hazard, stopping production on the printer. We created an action team to work on the issue and come up with solutions that would ensure safe operation of the system. We had to approach it from a fundamental science perspective to mitigate the inherent risk in our system. Team members from various groups came together to resolve the issue, including operations, hardware, software, and process engineering teams. Together, we came up with a system that would test our theory of what was happening on our machine, and validate the plan to ensure its safe operation. Through these experiments, we came up with a novel solution.
What first drew you to engineering and this industry?



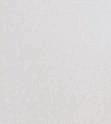
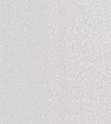
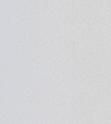


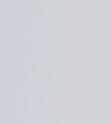

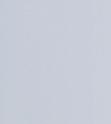
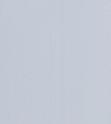
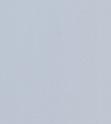
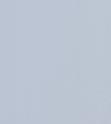
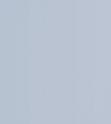

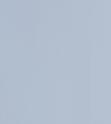
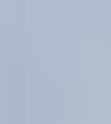

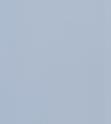
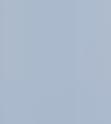
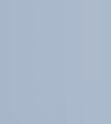
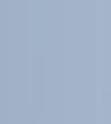
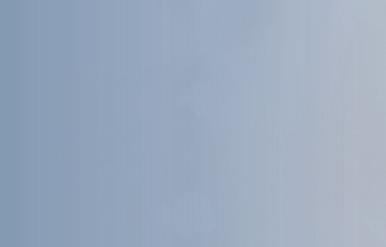












I’ve always been quite interested in physics and I love solving new problems. The field of additive manufacturing has a lot of growth potential. There are endless amounts of unresearched areas in the industry.
When I joined Velo3D, we were extremely focused on how to build parts with low, unsupported overhangs. This was nearly impossible to do in conventional metal additive manufacturing solutions. The physics behind building these surfaces was very interesting. We had to consider how the laser meltpools develop in the powder bed, and how the part reacts to various conditions throughout the build.
Through extensive trials and learnings we developed a technique that would make large unsupported overhangs possible to print. This created many new opportunities for our company and is one of the reasons our customers purchase our technology—especially those in aerospace who are using our technology to produce a variety of components in rocket engines
I really enjoy solving these types of new problems that have a huge possible impact.
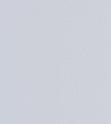
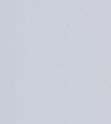

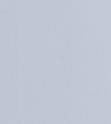



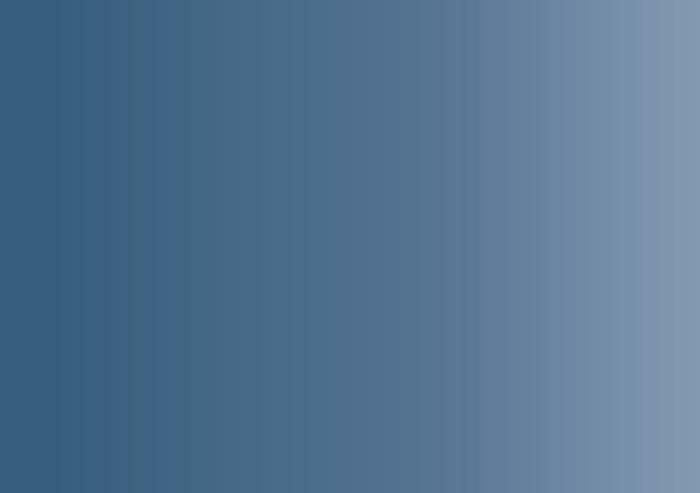

For the rest of Maritza Ruiz’s insights, visit www.designworldonline.com/WiE.
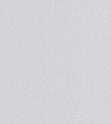
Women in Engineering

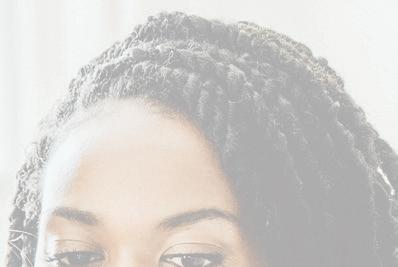

Michelle Goeman


Regional Sales Manager
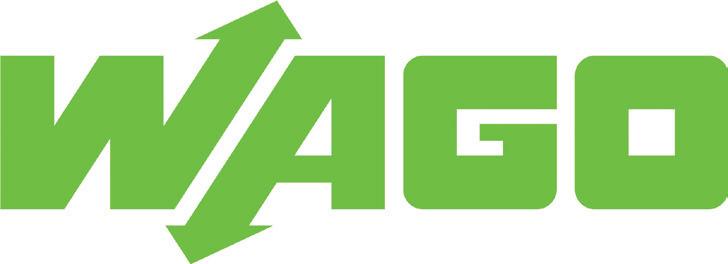


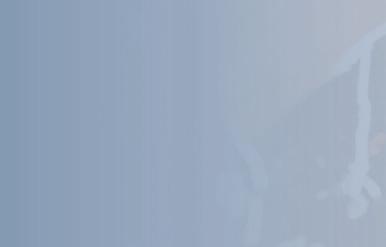
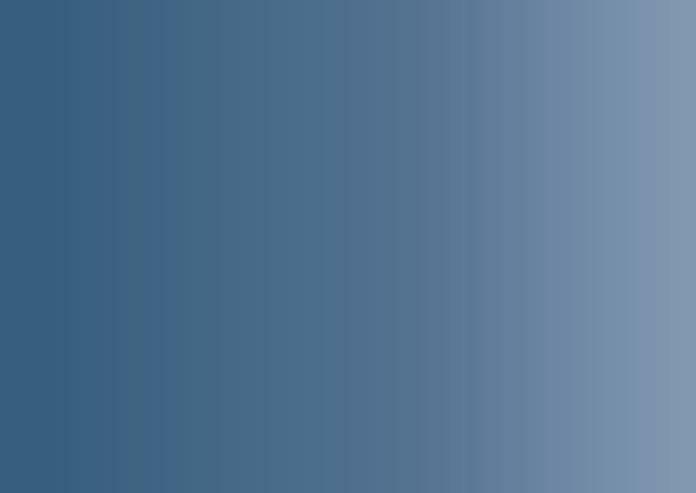


WAGO Corporation
Bachelors of Science Industrial Engineering
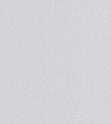
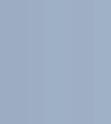
























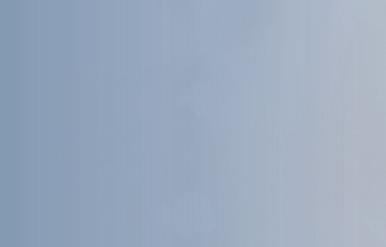

Minor in Business Management

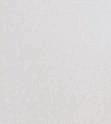
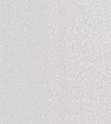
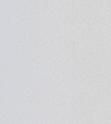

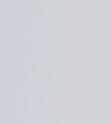

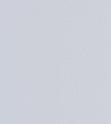
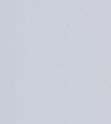

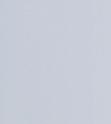
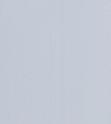
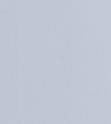
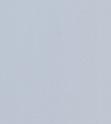
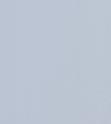
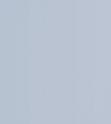

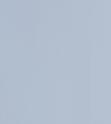

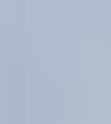

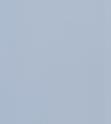
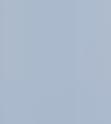

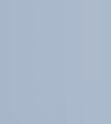
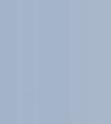

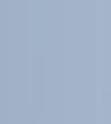
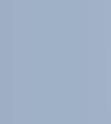





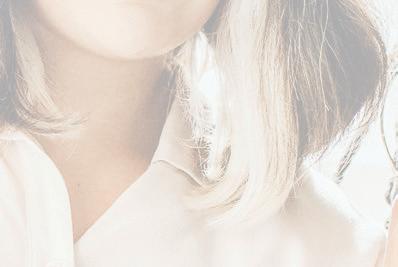
Milwaukee School of Engineering
Talk about the culture at your company. What makes it inclusive or supportive of women in engineering and automation?
WAGO offers opportunity for growth in so many areas for our employees. We’ve had customer service move to product management, product support move to training manager, and my personal story of moving to an outside sales manager position. It is definitely an inclusive atmosphere with low turn-over. We also offer a flexible work environment so that you can have a family and a career.
Describe a recent company project (in which you were involved) that went particularly well. How did you and your team go about ensuring success?
A recent project I worked on was with our Custom Engineering team to save my customer wiring time, and create a harness terminal block assembly to remote I/O connector. They were having trouble getting help in the plant, so this solution saved them so much valuable assembly time. One of our in-house engineers, assisted with the project, and after a Teams meeting with our customer she was able to make some significant time-saving suggestions.
What first drew you to engineering and this industry?







Michelle realized early on that the time studies and ergonomics of Industrial Engineering were not going to be fulfilling enough for her. So she entered the work force from college as an applications engineer for drives / motor control products, where she held various positions. Then she moved to WAGO , where she was a product manager for over 10 years, and is now in outside sales for coming up on 5 years.
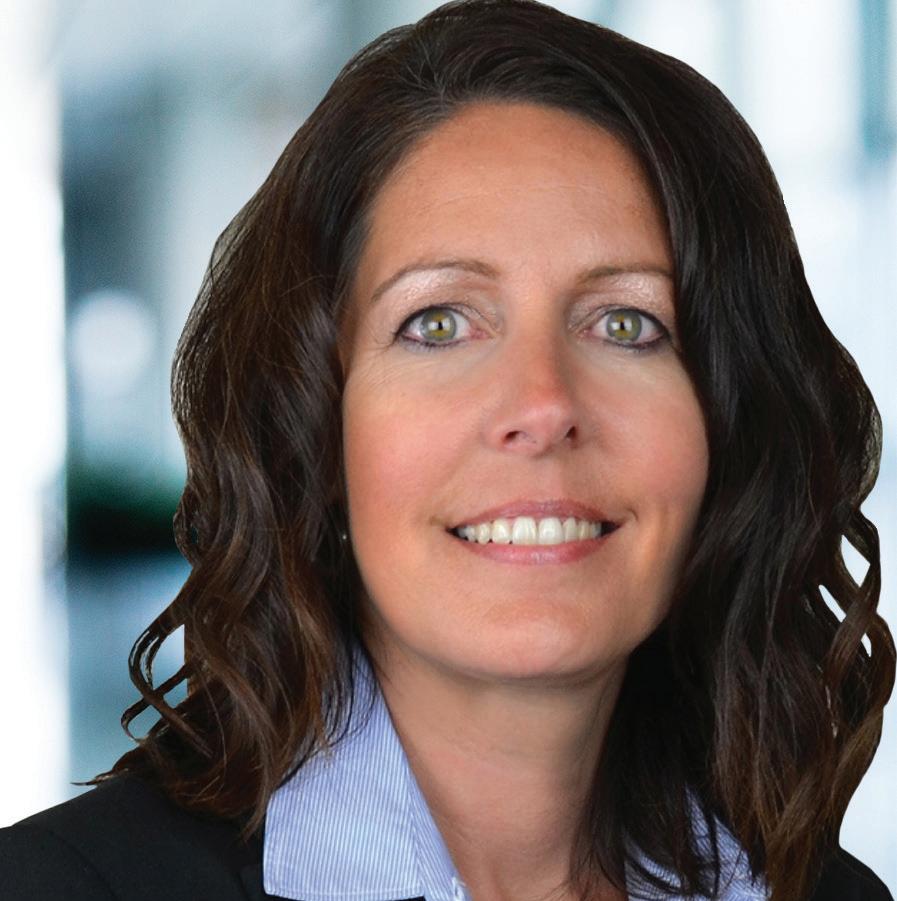
I actually selected engineering as college major from a high-school career assessment test. Although, I discovered early that the Industrial Engineering field was not for me, one of my college professors convinced me to continue on. She informed me that many employers want a 4-yr technical degree, so they know the employee is technically minded and trainable. I quickly transitioned into more of an electrical field, but have enjoyed it ever since.
Describe your biggest career challenge. How did you solve it — or what was the outcome or lesson learned?
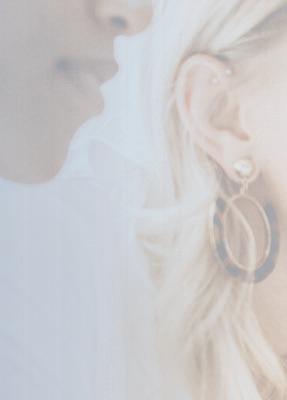
About 5 years ago, I felt like I was becoming complacent in my job. I could handle the responsibilities in less than 40 hours/week, as I had been in the role for over 10 years. I was making good money and good at my job, but wanted more. Initially, I didn’t see a clear path for advancement within the company, and struggled with what was next for me. I discussed a sales position with our VP of Sales as I honestly wasn’t sure I’d be a good fit. He helped me overcome my concerns, and really convinced me to go for it. I am loving the new challenges and experiences of this sales role.
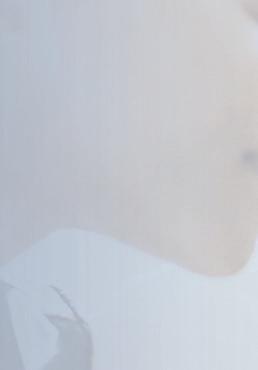
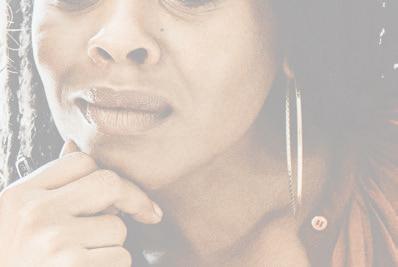
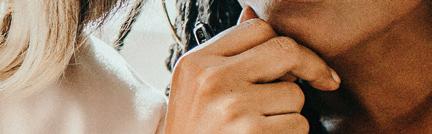
For the rest of Michelle Goeman’s insights, visit www.designworldonline.com/WiE.
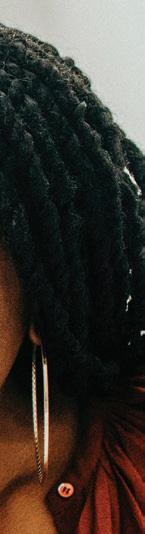
Women in Engineering
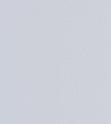

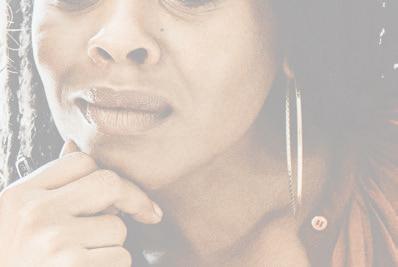
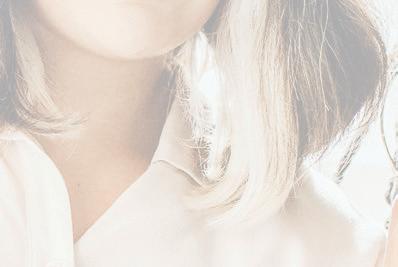
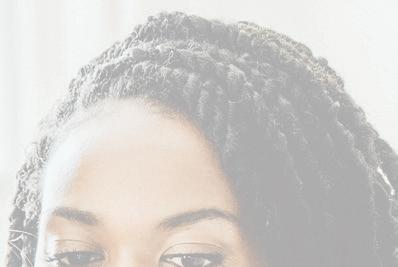

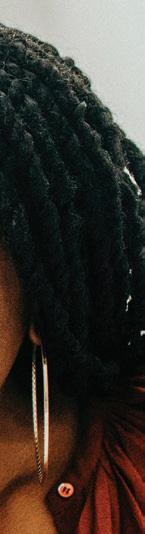
Kitty Kong
Engineering Director Wind River


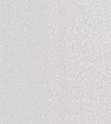

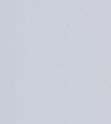
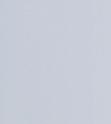
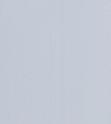
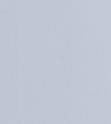
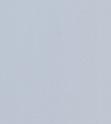
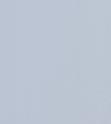
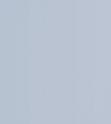

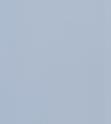
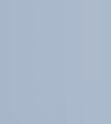
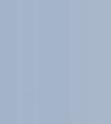
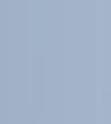
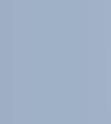
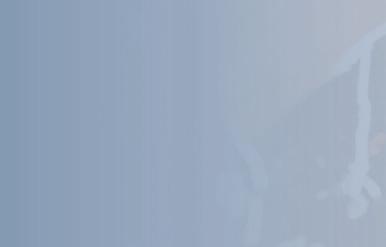
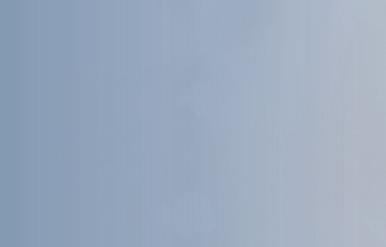











B.A. Computer Software Engineering
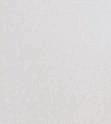
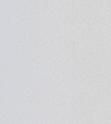

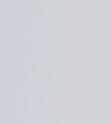


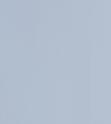

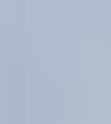

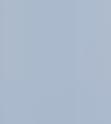


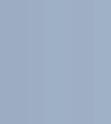


























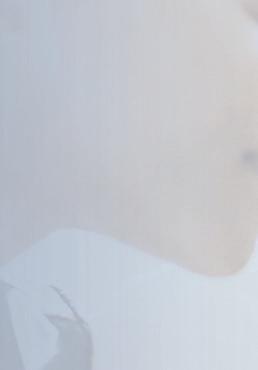


UC – Berkeley
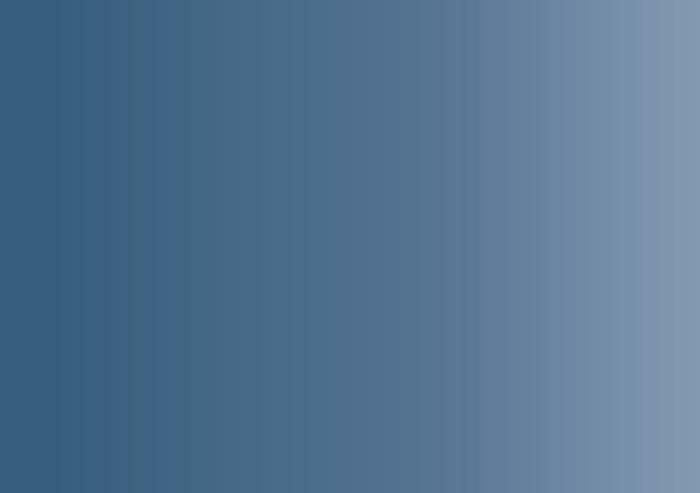
Kitty Kong oversees teams that work on the company’s flagship real-time embedded operating system, full-system simulation of target hardware, and cloud-native platform. She earned her bachelor’s in computer science from University of Berkeley and started her career at Wind River Systems after graduation. She joined Wind River as a kernel engineer, working on device drivers, BSPs, and OS kernel features. She has worked through many engineering levels and technical leadership and project management roles, and is now a director of engineering, leading the teams that she used to work in.
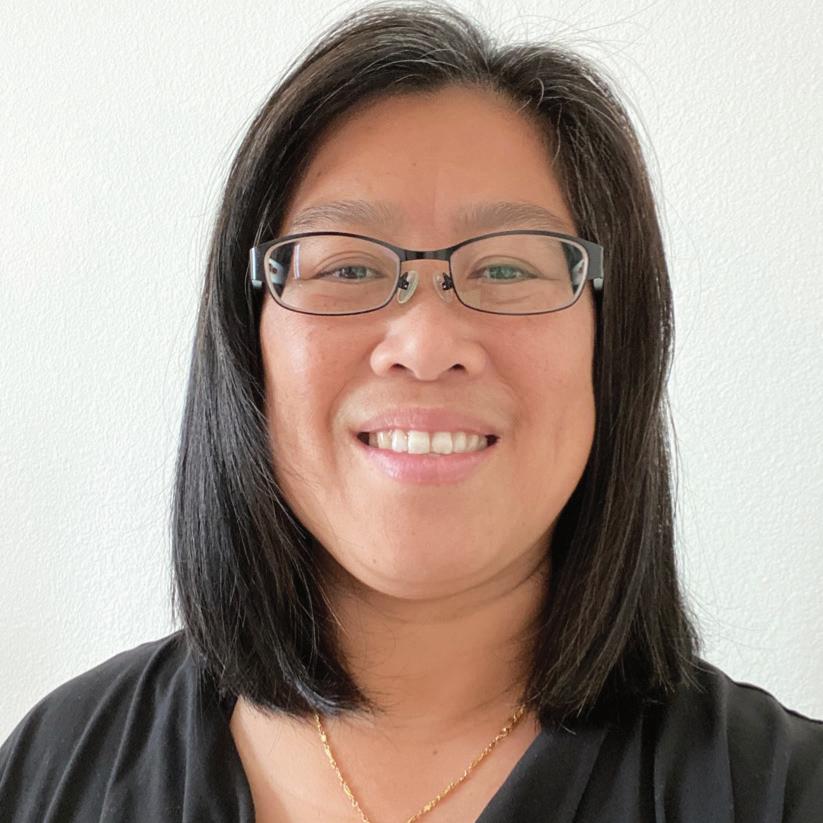
Talk about the culture at your company. What makes it inclusive or supportive of women in engineering and automation?
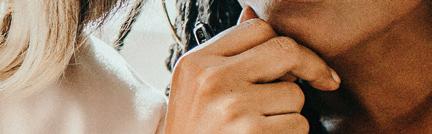
I have worked at Wind River for more than 25 years, starting out as an intern and working my way to my current role as a director. For some, this may seem too long to work at one company. But for me, Wind River has provided an environment of personal and professional growth. One of the reasons I started and stayed there is its culture and diversity. Wind River fosters a culture of collaboration, innovation, knowledge sharing, and teamwork. On every project and every team I have worked with, everyone has been supportive of each other and shared a common goal for success. Even as a woman in a male-dominant profession, I have felt respected and valued for what I can contribute.
Describe a recent company project in which you were involved that went particularly well. How did you and your team go about ensuring success?
Three years ago, Wind River had a vision to transform from a traditional embedded RTOS company to an intelligent systems software company by introducing a cloud-native platform for our customers. This new product encompasses all the existing products within Wind River plus many new technologies. It is a very large-scale project with many teams involved! About a year ago was our official first release of this product. There were lots of challenges along the way to deliver this first release: infrastructure setups, coordination between teams, new processes, new technologies, integration challenges, resource challenges, etc. Even with these challenges, my team and all the teams contributing to the product came together, collaborated as a single team to integrate all the technologies, addressed issues as they came, worked closely with QA testing, and delivered the release on time. It was a proud moment for Wind River and all the teams involved. Such success is due to the collaborative and positive culture we have at Wind River.
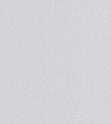
Describe your biggest career challenge. How did you solve it — or what was the outcome or lesson learned?
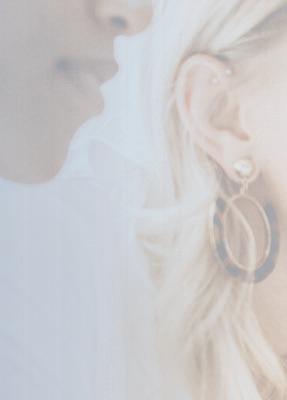
I was a senior member of the technical staff and a technical lead. However, I realized then that I might not have the technical creativity to get to the next level of becoming an architect. I had to figure out where my career path would lead. While I was doubting my readiness, my director approached me and offered me a manager role. I hesitated but decided to take the offer with the condition that I could remain technical and close to the engineers. Becoming a great manager could make a difference for an engineer’s career. I have never looked back as I love managing a team — although I do itch to code occasionally.
For the rest of Kitty Kong’s insights, visit www.designworldonline.com/WiE.

Women in Engineering

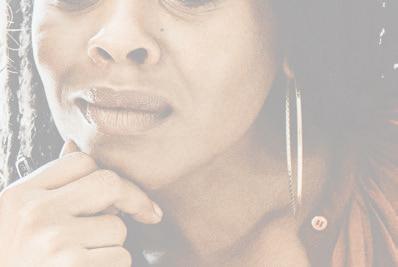
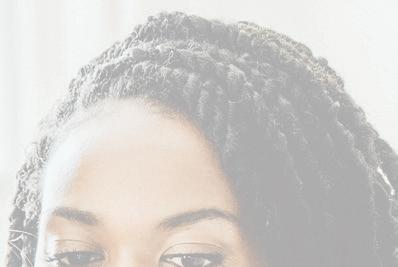

Stephanie Moscrip

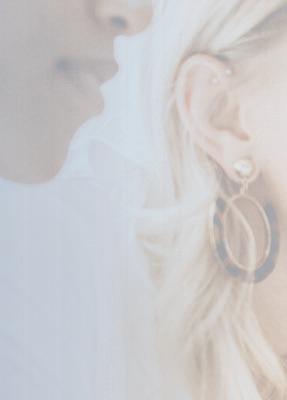
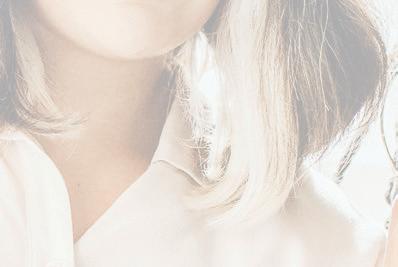

VP of Engineering Excellence and Linux



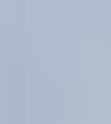




























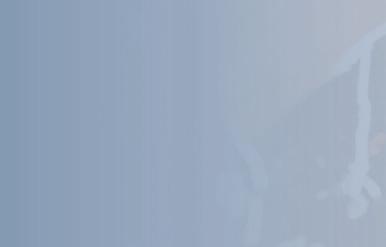
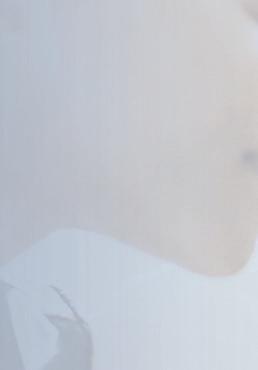
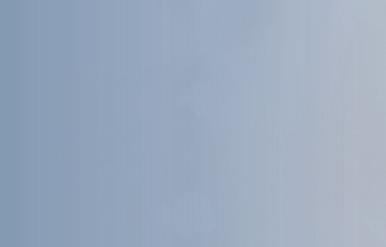
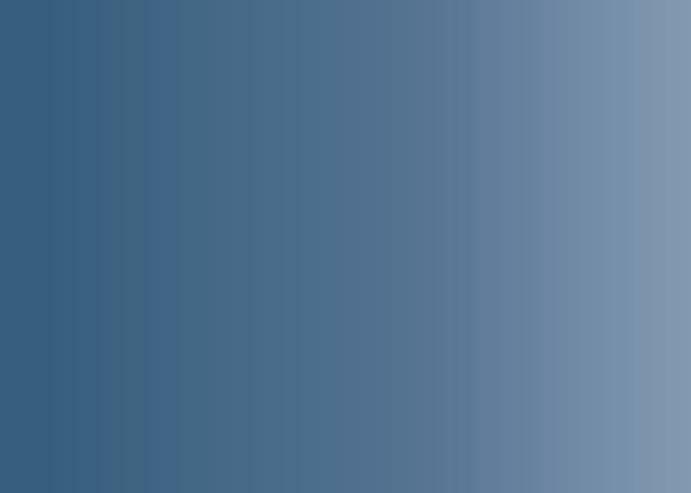







BSc Electrical Engineering Queen’s University
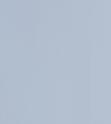
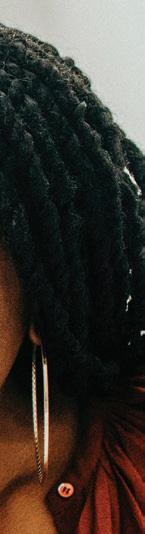
Stephanie Moscrip graduated from Queen’s University in Canada with a degree in electrical engineering with a computer option. Her career started at an optical devices and module company called JDS, which then became JDS Uniphase. For the first few years she worked in embedded software development, and then moved into project management and general leadership roles. After more than 13 years, though, it was time for a change. She moved to Wind River, where she has happily worked for more than 14 years. She started as a project manager for the Wind River Linux project, working her way up to project director and working on most Wind River products in some capacity over the years. She became director of Linux Engineering in 2018, adding responsibilities for Engineering Excellence in 2020 and being promoted to VP of Engineering Excellence and Linux in 2021. She recently took on an additional role as VP of Strategic Initiatives.
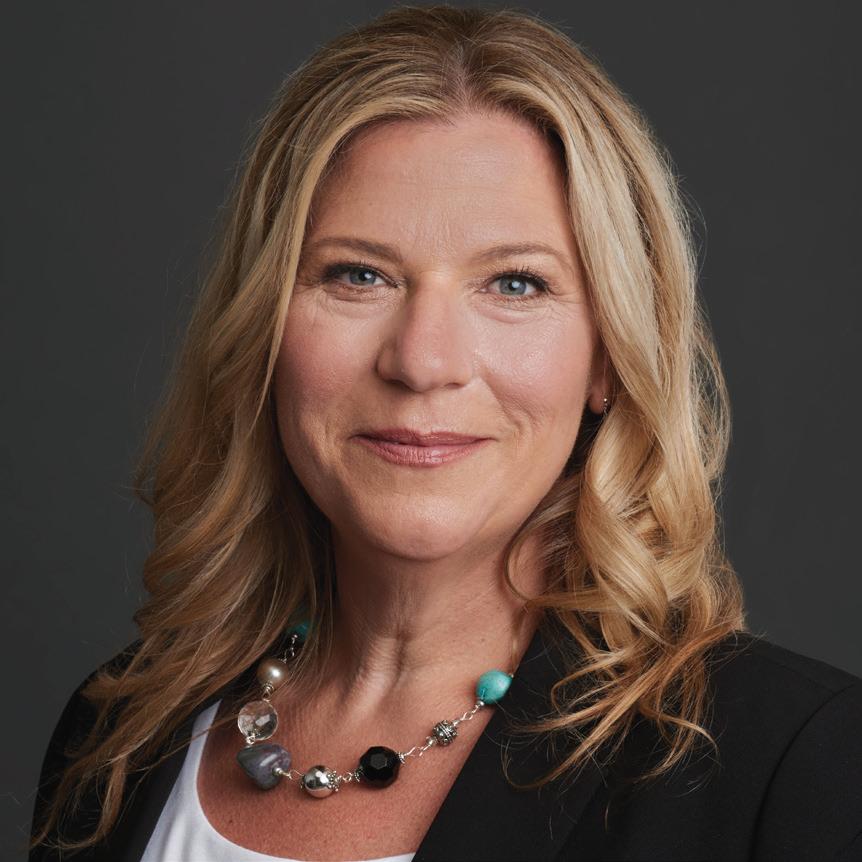
Talk about the culture at your company. What makes it inclusive or supportive of women in engineering and automation?
The word that first comes to mind to describe the culture at Wind River is family. Wind River is a place where people work for decades because we are passionate about our products, we support each other, we pull together to make things happen, and we have fun.
The second word that comes to mind is diverse. People at Wind River strongly believe that the best workforce is a diverse workforce, where different perspectives combine to bring out the best in everyone and everything we do. Wind River hosts a series of diversity and inclusion panels, one of which is geared toward women.
The last word that comes to mind is balance. Wind River encourages and supports a balanced life — something I have appreciated, having raised now-16-year-old twins during the time I have been at Wind River.
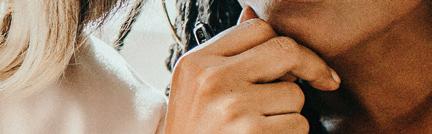
Describe a recent company project in which you were involved that went particularly well.

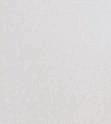
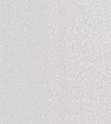
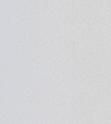

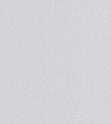

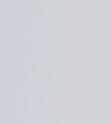

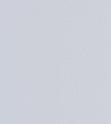
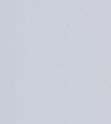

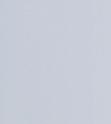
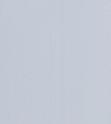
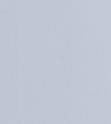
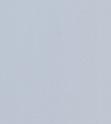
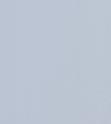
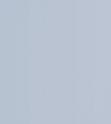

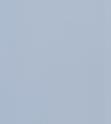
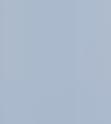
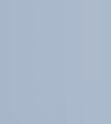
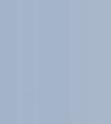
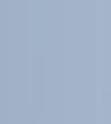
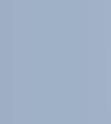
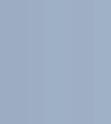






What began as an inkling in someone’s mind is now a product that is going to enable a software-defined, AI-driven world. Bringing it to fruition in less than three years has been an incredible ride. As VP of Engineering Excellence, I was actively involved in working across the department to manage and enable our engineers to deliver as they grew from a team of ten to a team of hundreds. As VP of Strategic Programs, I am working with our partners and customers to further enable the vision. To see this product and vision gain traction across the industry and know that I was part of making it happen is incredibly satisfying.
Describe your biggest career challenge. How did you solve it — or what was the outcome or lesson learned?
My biggest career challenge was being asked to take over our Wind River Linux product engineering team. In my mind, taking on the Director of Linux Engineering role was a big leap over a huge chasm, and I am afraid of heights! However, it ended up being one of the best decisions of my life. I realized a lot about my strengths and how they can be applied in different areas, and I was able to drive several strategic initiatives within the team. I am most proud of transforming the team into a Continuous Integration/Continuous Development (CI/CD) organization. I had to first get buy-in from the extended team and management, then work through the unique hurdles of doing CI/CD with an open source–based product. We were able to complete the transformation within a year, becoming one of the first CI/CD organizations within the company and having the first Linux CI/CD offering in the industry. Lesson learned: Take the leap.
For the rest of Stephanie Moscrip’s insights, visit www.designworldonline.com/WiE.
Women in Engineering

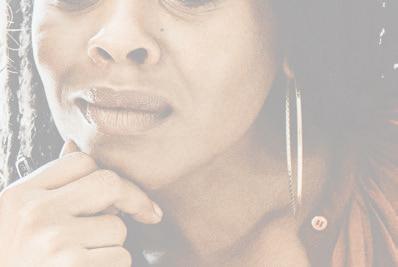
Anna Wint
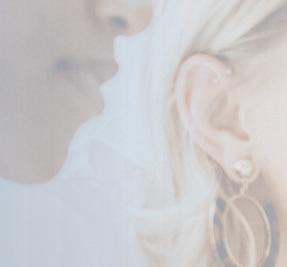
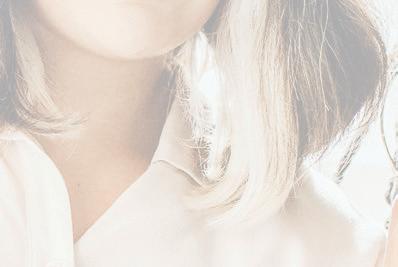

Quality Engineer Wurth Industry North America

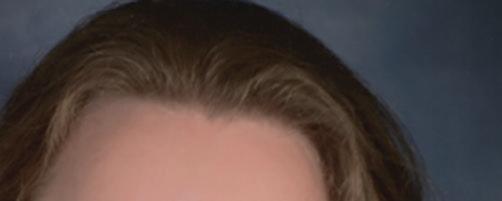
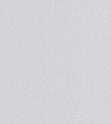
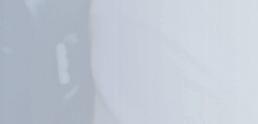
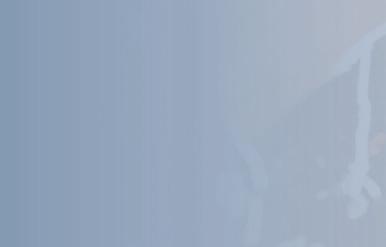
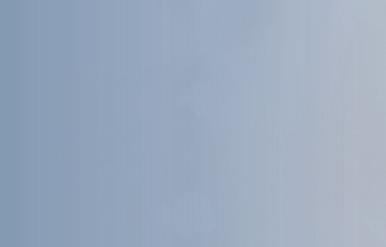
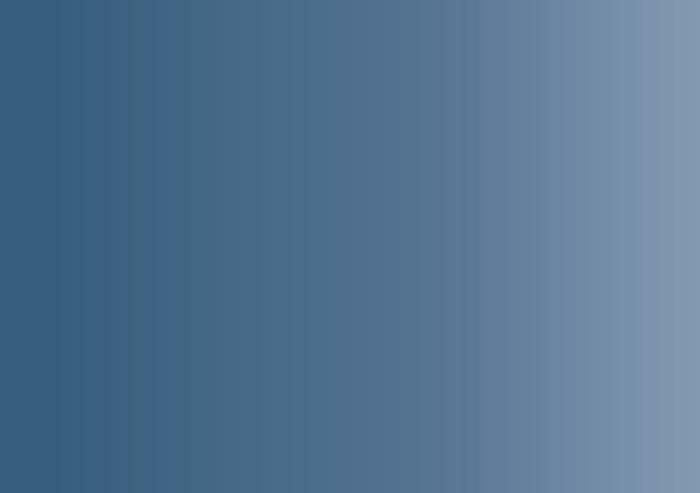

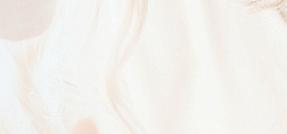
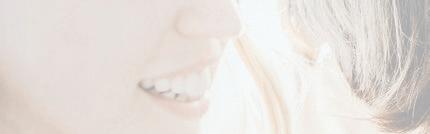

Bachelor of Science in Mechanical Engineering



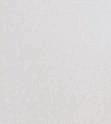
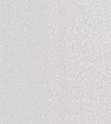
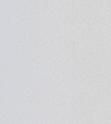


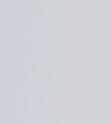

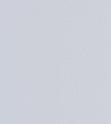
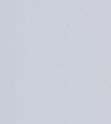

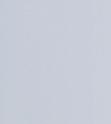
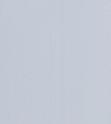
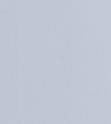
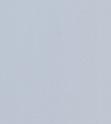
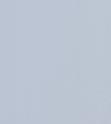
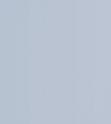

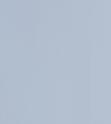

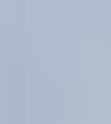

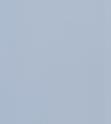
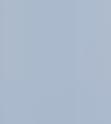

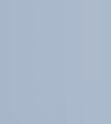
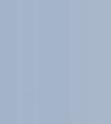

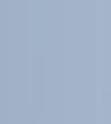
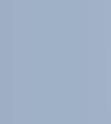
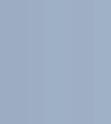


































Valparaiso University
Anna started in the automotive industry as a manufacturing engineer for an engine manufacturer in 2014 and worked as part of a team that helped to begin producing a new diesel engine. In 2017, she transferred to another engine line and began work as a production line quality engineer as well as the shift A3 problem solving coach. In 2020, she moved to the fastener industry and began working at Würth. She currently supports one large customer account and several smaller customer accounts located across the U.S. in regards to quality and production part approvals (PPAPs).
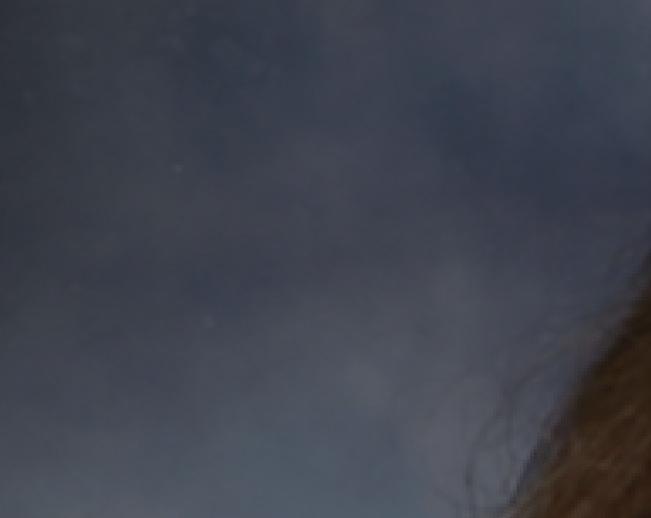
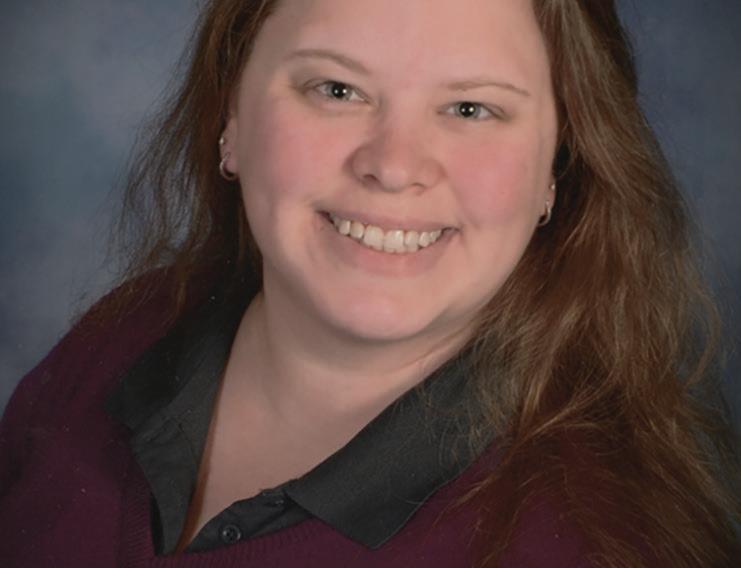
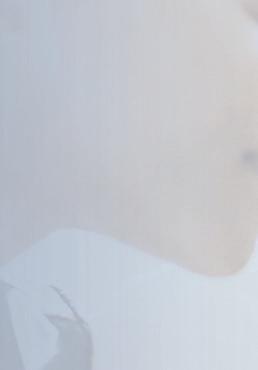

Talk about the culture at your company. What makes it inclusive or supportive of women in engineering and automation?
When I started at Würth, I was warmly welcomed and made a part of the Würth family. The culture here is one that builds people up. From the top down, the mindset has been “We’re a team, we’re a family.” We’re encouraged to learn more about topics we are interested in, with Würth offering various trainings to all employees (effective communication, problem resolution, in depth fastener knowledge, etc.) and supporting continuing education outside the business as well. I’ve never been denied the opportunity to learn and develop my skills. Each time I’ve gone to my manager about something I wanted to learn, I’ve always received the support and help to get that training.
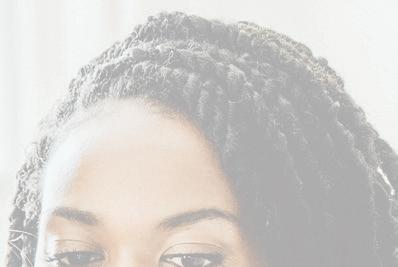
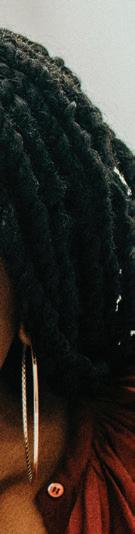
Describe a recent company project (in which you were involved) that went particularly well. How did you and your team go about ensuring success?
One major win has been the growth of the large customer account that I support. In mid-2020 the account was a small one, but now they are one of the larger accounts with the potential for even more growth. There were multiple things we did that ensured our success. One was to have in-depth team trainings with everyone associated with the account about our customer and their requirements and culture. Another major help was that we had, and still have, daily communications with the customer. Those daily communications made sure we avoided any issues with the parts and helped to build their trust in Würth.
What first drew you to engineering and this industry?


Growing up I always wanted to know how things worked: sewing machines, lights, cars, etc. Several members of my extended family are farmers and I remember wanting to know how the tractors and combines worked. I was able to take pre-engineering courses in high school and quickly found that I enjoyed coming up with solutions and working to solve problems. I also took mechanical drafting courses and was able to coop as a drafting student supporting design engineers at a local company. After working as a manufacturing engineer I became more and more interested in quality and quality management. When an opening came in the quality team, I transferred there.
For the rest of Anna Wint’s insights, visit www.designworldonline.com/WiE.
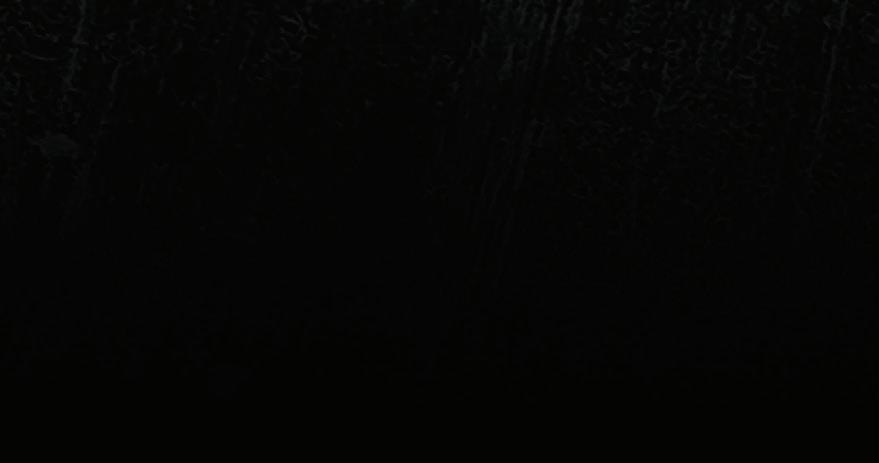

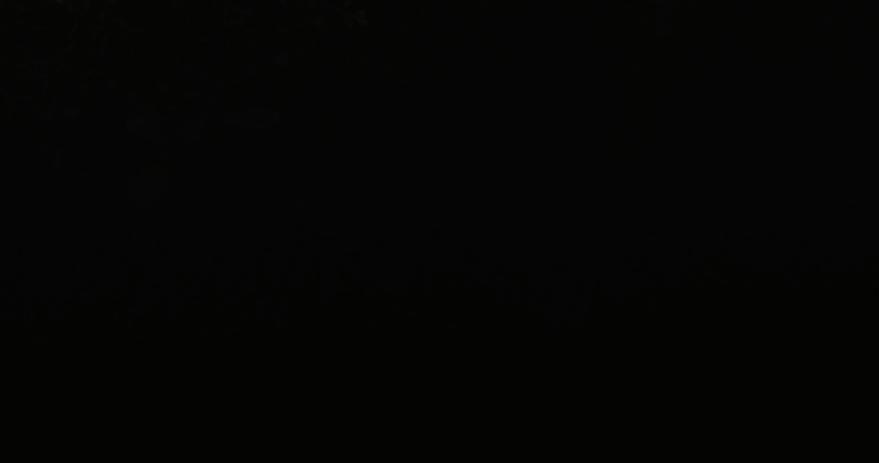
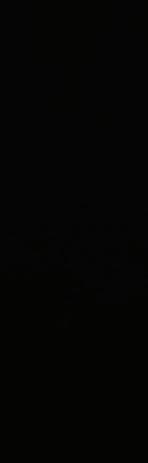
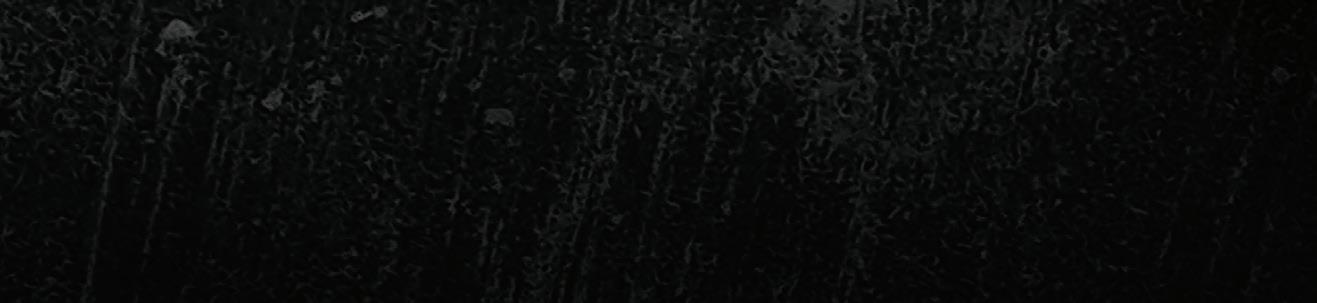
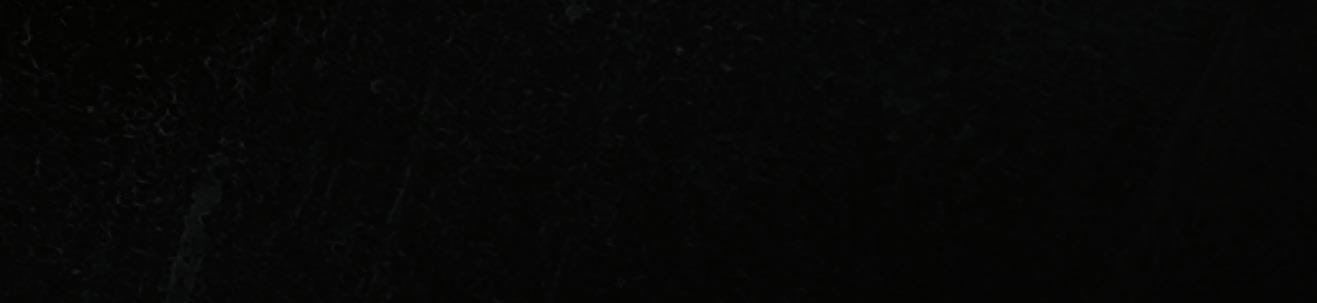
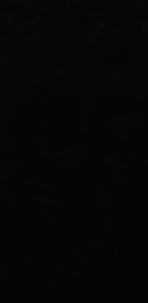





















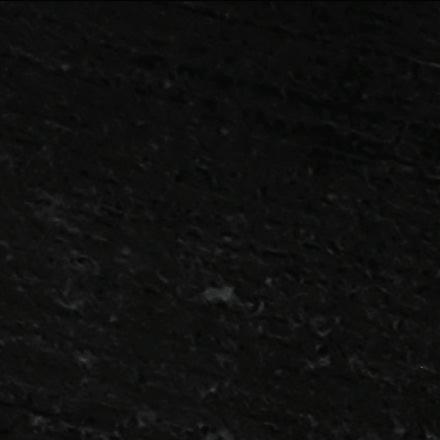
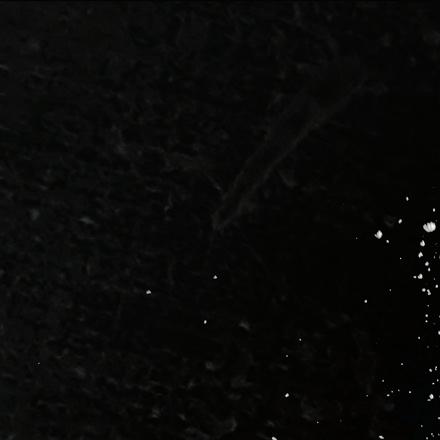
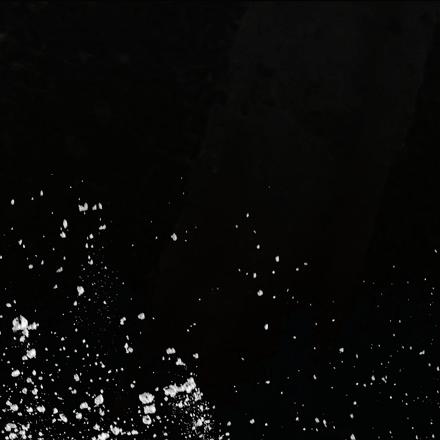
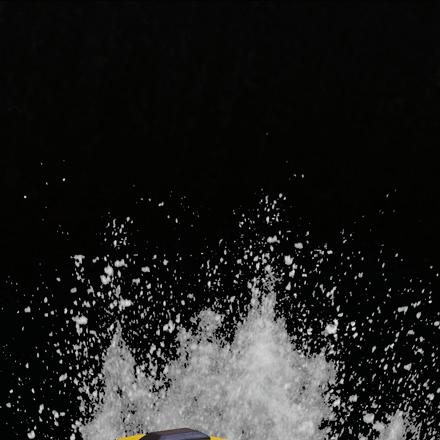


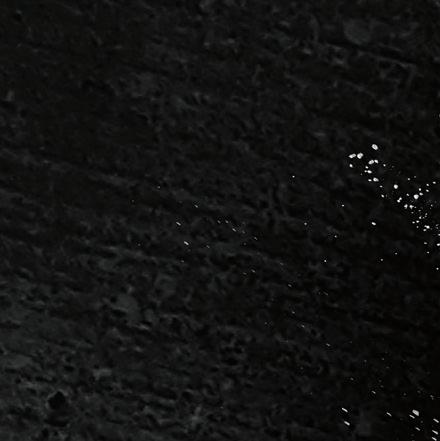
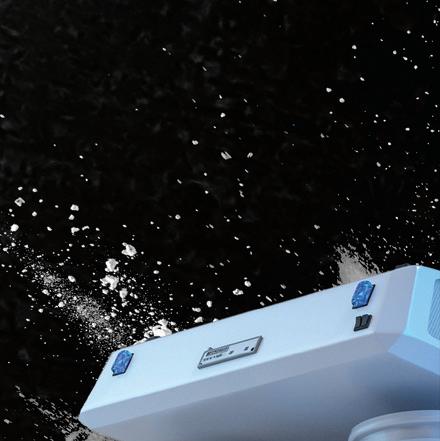
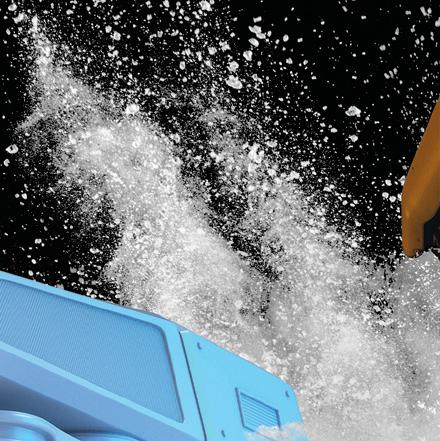
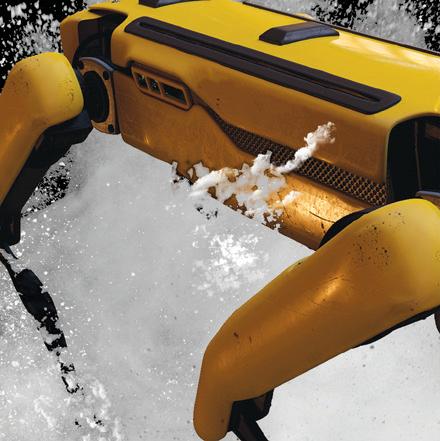



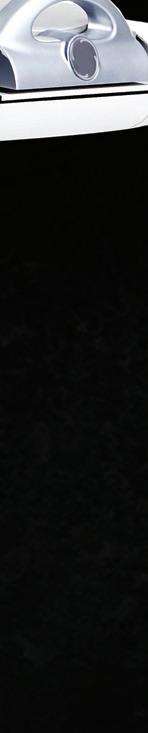

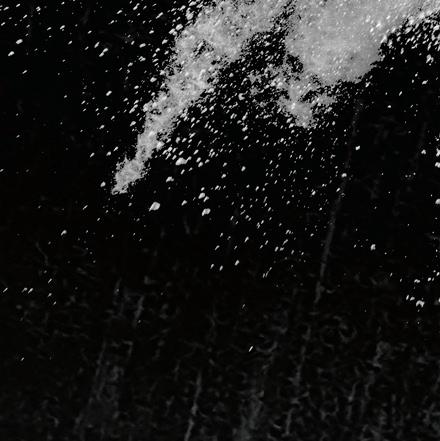
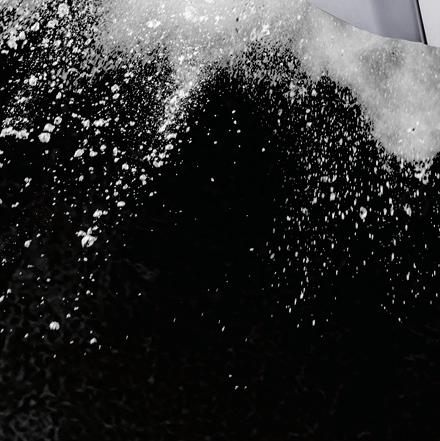
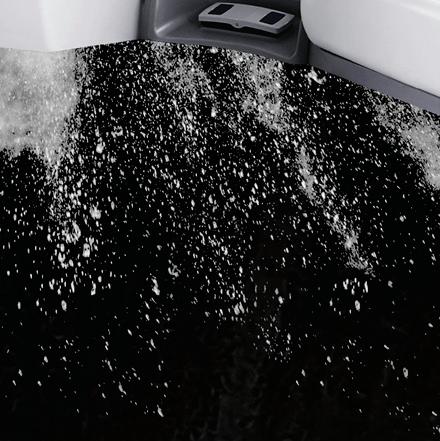
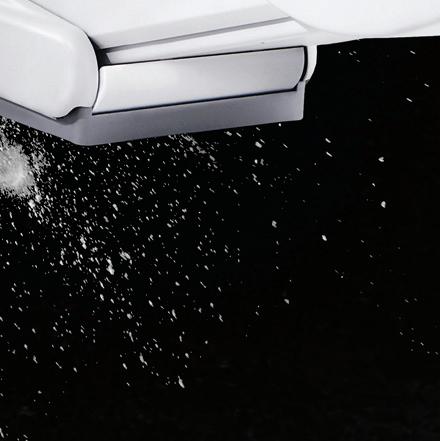
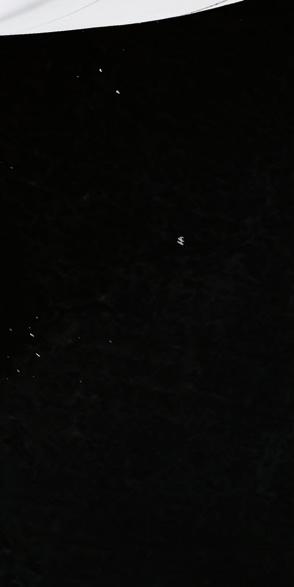
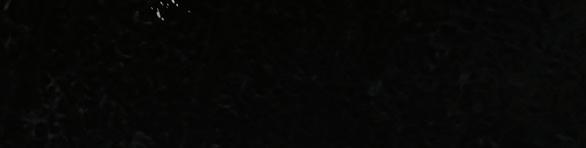
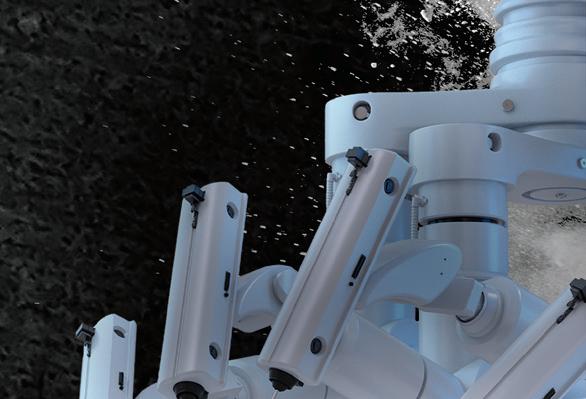
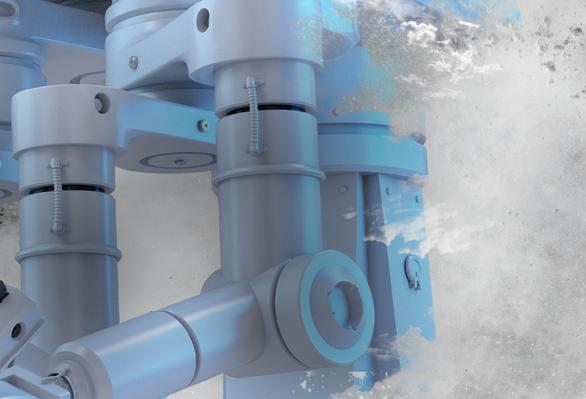
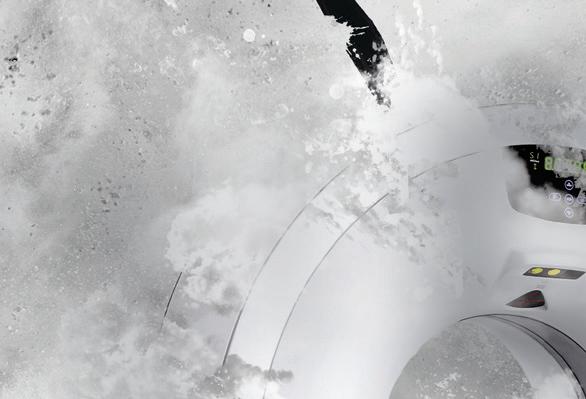

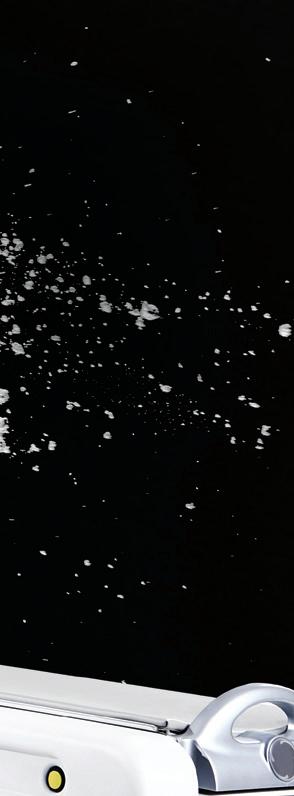
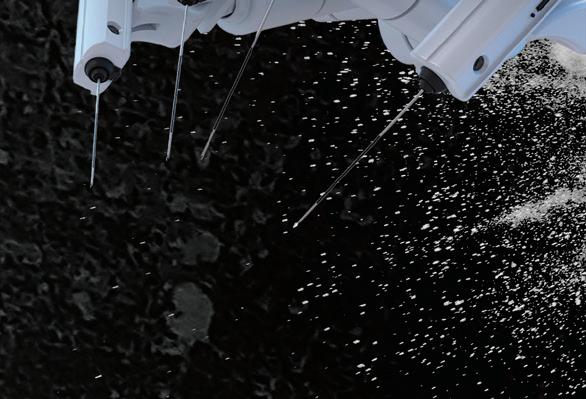


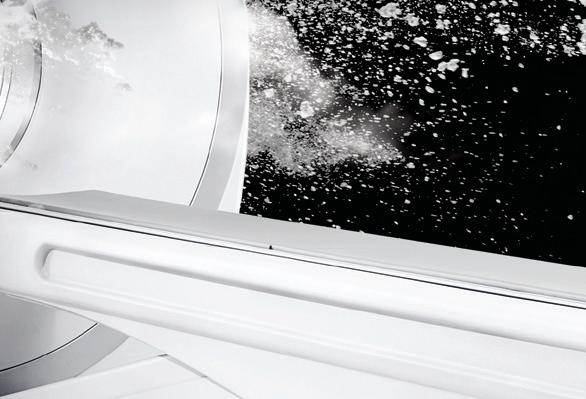

Accumold 143
Advanced Micro Controls Inc 133
Advanced Powder Products 17 Allegro Microsystems 119 Allied Electronics & Automation 129 AllMotion ....................................................................... 126 Altech Corporation 10, 11 B. Braun BC
Bay Associates Wire Technologies, Inc. 18 Beckhoff Automation 117 Biocoat 25
Bishop Wisecarver 127
Carl Stahl Sava Industries ................................................ 14 CGI Inc. 121
Cinch Connectivity Solutions 145 Clinical Research Strategies 5 Clippard 7 Components Corporation 47 COMSOL 56 Confluent Medical Technologies 16 Cretex Medical 13 Digi-Key Electronics 93 Donatelle 8
Eagle Stainless Tube 19 Elma Electronic, Inc. ..................................................... 144 Elsner Engineering 31 Eurofins 2 Filmecc USA, Inc, subsidiary of Asahi Intecc USA. 38 Flexan 3
FLEXcon 35 Hobson & Motzer 63 igus 101 Infineon 95 Integer 69 Interpower 61
Isometric Micro Molding 49 John Evans’ Sons, Inc. ..................................................... 53 Johnson Matthey 29 maxon 97 MedBio 65 MedTech Women 70 MICRO 58 Microchip 125 MicroLumen 42, 43 Mitsubishi Electric Automation 135 New England Wire & Tubing Technologies 1 nVent 103 Phillips Medisize 28 PSN Labs .......................................................................... 23 RECOM Power GmbH 113 Resonectics IFC
SENKO Advanced Components 46 Tegra Medical IBC Velo3D 139 WAGO Corporation 141 Wind River ...................................................................... 109 Würth Industry North America 105
SALES
Ryan Ashdown rashdown@wtwhmedia.com 216.316.6691
Jami Brownlee jbrownlee@wtwhmedia.com 224.760.1055
Ashley N. Burk
737.615.8452 aburk@wtwhmedia.com
Mary Ann Cooke mcooke@wtwhmedia.com 781.710.4659
Jim Dempsey jdempsey@wtwhmedia.com 216.387.1916
Mike Francesconi mfrancesconi@wtwhmedia.com 630.488.9029
Courtney Nagle cnagle@wtwhmedia.com 440.523.1685 @wtwh_CSeel
Jim Powers jpowers@wtwhmedia.com 312.925.7793 @jpowers_media
Brian Toole btoole@wtwhmedia.com 267.290.2386
LEADERSHIP TEAM
Managing Director
Scott McCafferty smccafferty@wtwhmedia.com 310.279.3844 @SMMcCafferty
VP of Sales | Publisher Mike Emich memich@wtwhmedia.com 508.446.1823 @wtwh_memich
EVP Marshall Matheson mmatheson@wtwhmedia.com 805.895.3609 @mmatheson




















It starts with decades of product development expertise. Our vast catalog of standard components can be customized to generate endless possibilities for sets and kits. We put in place processes for ensuring stringent quality levels, managing volumes of documentation and tracking all project details. Add in a full suite of capabilities, and you have a turnkey solution that’s more like a partnership for creating confidence.
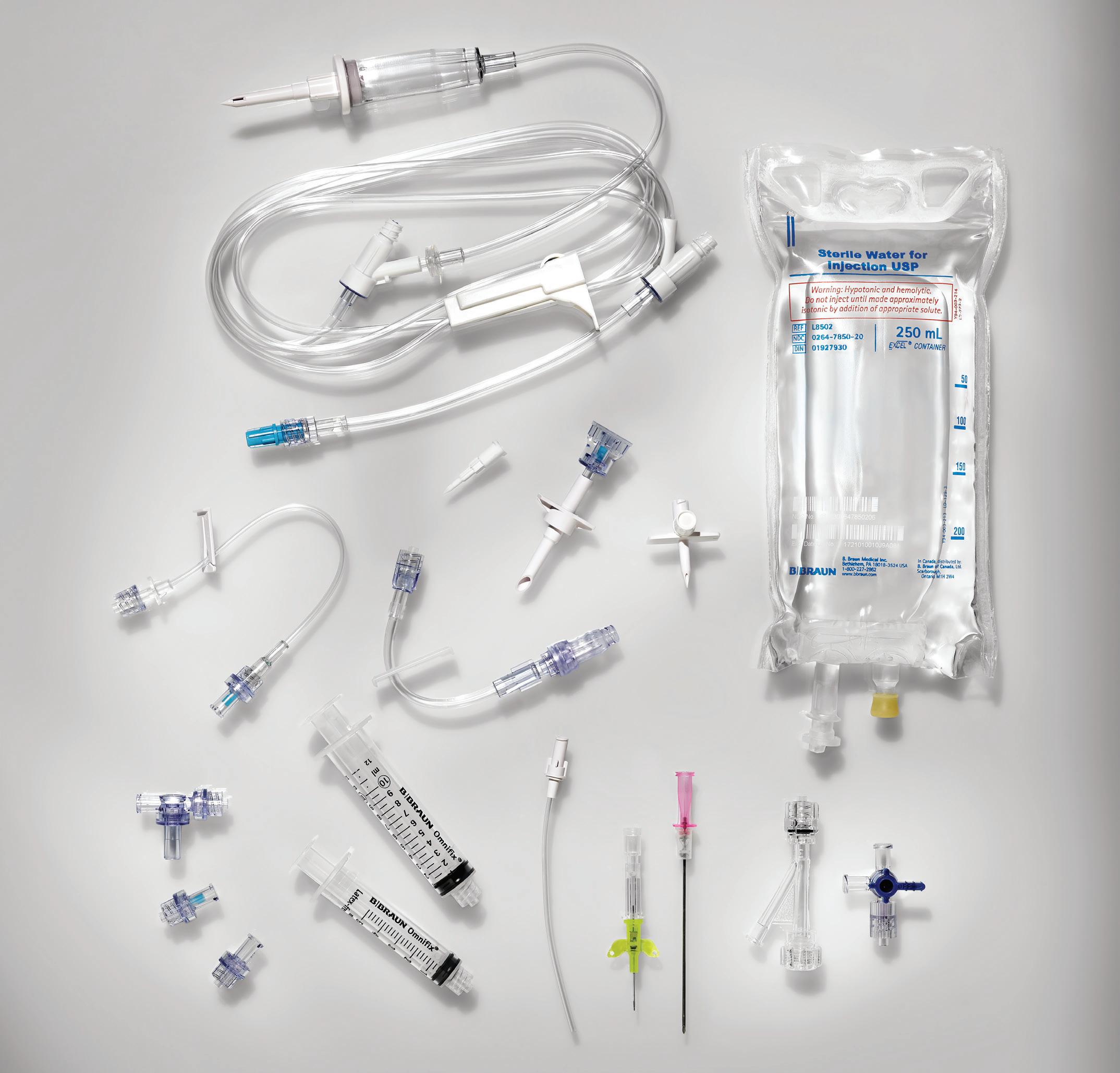