
Parental
Personal
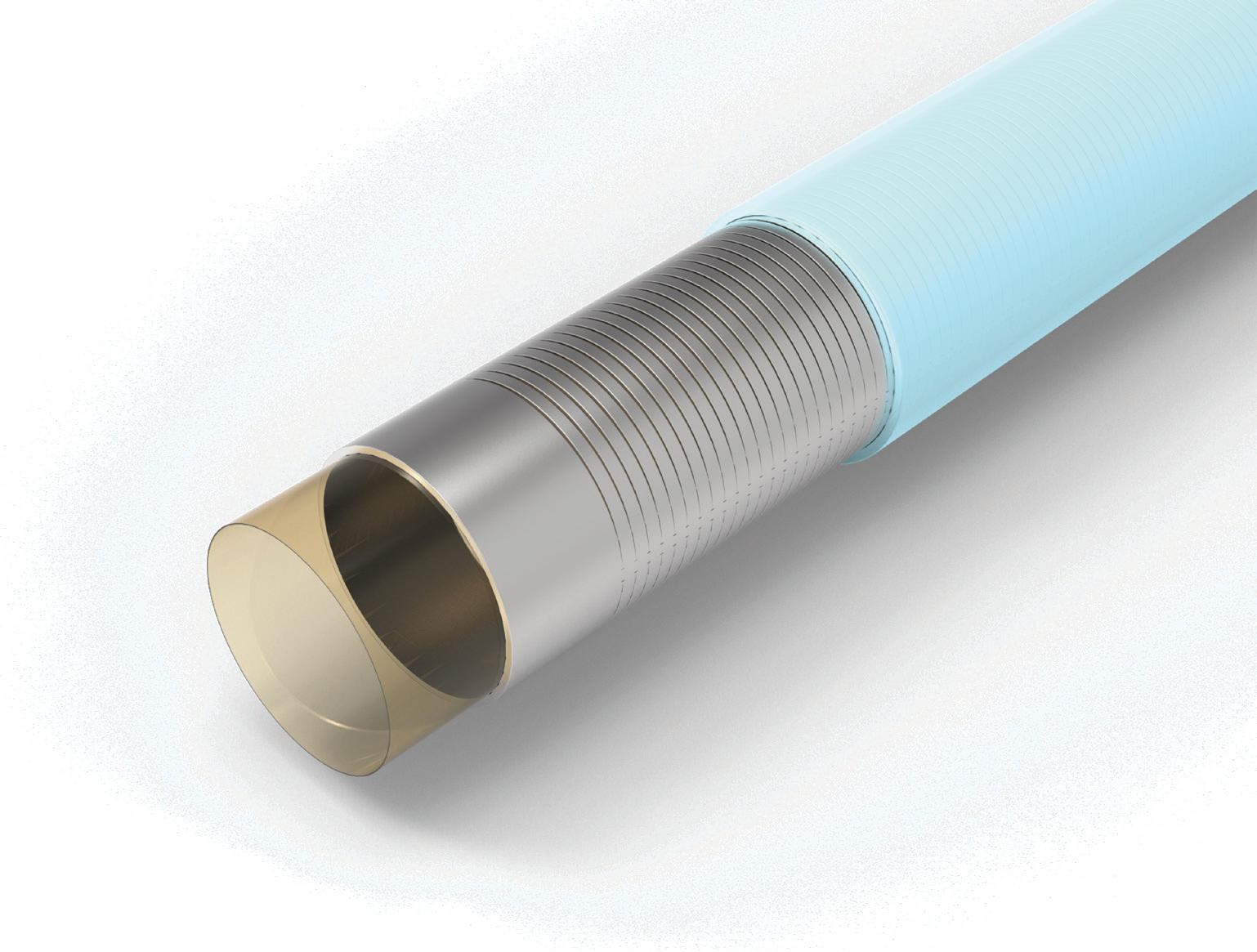
Parental
Personal
With off-the-shelf materials in the most common sizes, our Quick Turn Catheter Shafts put functional parts in your hands faster.
Our LCT reinforced Quick Turn Catheter Shaft offering streamlines your prototyping process, enabling you to bring your innovations to market faster. With a focus on precision and efficiency, we help compress your lead times by delivering superior catheter shafts in as little as two weeks. Simply provide us with your size specifications and application details, and we’ll handle the rest.
Scan to learn more about the Quick Turn Catheter Shaft.
Designed to your specifications.
• Available in 1, 2 and 3 pedal designs
• Robust and slip resistant
• High quality materials, such as Aluminum cast alloy and reinforced polyamide
• Environmental protection level up to IP X8 per IEC/EN 60529
• IEC 60601-1 certi cation
• Easily cleaned and hygienic
• Ergonomic design with intuitive actuation
• Custom colors, markings, circuits, cable types and lengths available
Compact, one pedal foot switch Standard Features
• Housing and Pedal Cover: Polyamide protection upto IP X8
• Protection Level: IP 43 and IP 65
• Switch Insert: Snap action microswitch, cCSAus approved
• Electrical Rating: 5A/125-250V AC
• Contact Types: Momentary, maintained, or two stage momentary
• Circuit: SPDT-SB, DPDT-SB, 2x SPDT-SB
• Strain Relief: PP Cable Gland
• With or Without Cable
• Cable: Multi conductor, PVC, SJT, 2 m (6 ft. - 6 in.)
• Temperature Range: -20°C up to +80°C (-4°F up to +176°F)
• Protection Level: up to IP68
• Switch Insert:
- Gold plated contacts for low current applications
Electrical Rating: 0.1A/125V AC
- Silver-Nickel plated contacts
Electrical Rating: 10.1A, (1/4HP)/125-250V AC
• Metal Top Guard or Heavy Metal Base
• Strain Relief: Per customer speci cations
• Cable: Per customer speci cations
• Connectors: Per customer speci cations
Certification to the latest medical standards:
• 60601-1 General requirements for safety
• 60601-1-6 Usability
• 60601-2-2 HF surgical equipment
• 60601-2-22 Laser equipment: Surgical / Cosmetic / Therapeutic / Diagnostic
• 60601-2-43 X-ray equipment
FOLLOW THE WHOLE TEAM @DESIGNWORLD
EDITORIAL
VP, Editorial Director Paul J. Heney pheney@wtwhmedia.com @wtwh_paulheney
Editor-in-Chief Rachael Pasini rpasini@wtwhmedia.com @WTWH_Rachael
Managing Editor Mike Santora msantora@wtwhmedia.com @dw_mikesantora
Executive Editor Lisa Eitel leitel@wtwhmedia.com @dw_lisaeitel
Senior Editor Miles Budimir mbudimir@wtwhmedia.com @dw_motion
Senior Editor Mary Gannon mgannon@wtwhmedia.com @dw_marygannon
CREATIVE SERVICES
VP, Creative Director Matthew Claney mclaney@wtwhmedia.com
Art Director Allison Washko awashko@wtwhmedia.com
Director, Audience Development Bruce Sprague bsprague@wtwhmedia.com
WEB DEV / DIGITAL OPERATIONS
Web Development Manager B. David Miyares dmiyares@wtwhmedia.com
Senior Digital Media Manager Patrick Curran pcurran@wtwhmedia.com
Front End Developer Melissa Annand mannand@wtwhmedia.com
FINANCE
Controller Brian Korsberg bkorsberg@wtwhmedia.com
Accounts Receivable Specialist Jamila Milton jmilton@wtwhmedia.com
VIDEO SERVICES
Videographer Cole Kistler cole@wtwhmedia.com
PRODUCTION SERVICES
Customer Service Manager Stephanie Hulett shulett@wtwhmedia.com
Customer Service Representative Tracy Powers tpowers@wtwhmedia.com
Customer Service Representative JoAnn Martin jmartin@wtwhmedia.com
Associate Editor Heather Hall hhall@wtwhmedia.com @wtwh_heathhall
Contributing Editor Aimee Kalnoskas akalnoskas@wtwhmedia.com
Contributing Editor Emma Lutjen elutjen@wtwhmedia.com
Contributing Editor Martin Rowe mrowe@wtwhmedia.com
Contributing Editor Stephanie Neil sneil@wtwhmedia.com
WTWH
Ph: 888.543.2447
Software Engineer David Bozentka dbozentka@wtwhmedia.com
DIGITAL MARKETING
VP, Digital Marketing Virginia Goulding vgoulding@wtwhmedia.com
Digital Marketing Manager Taylor Meade tmeade@wtwhmedia.com
Digital Marketing Coordinator Meagan Konvalin mkonvalin@wtwhmedia.com
Webinar Coordinator Emira Wininger ewininger@wtwhmedia.com
Webinar Coordinator Dan Santarelli dsantarelli@wtwhmedia.com
Customer Service Representative Renee Massey-Linston renee@wtwhmedia.com
Customer Service Representative Trinidy Longgood tlonggood@wtwhmedia.com
Digital Production Manager Reggie Hall rhall@wtwhmedia.com
Digital Production Specialist Nicole Johnson njohnson@wtwhmedia.com
Digital Design Manager Samantha King sking@wtwhmedia.com
Marketing Graphic Designer Hannah Bragg hbragg@wtwhmedia.com
Digital Production Specialist Elise Ondak eondak@wtwhmedia.com
HUMAN RESOURCES
Vice President of Human Resources Edith Tarter etarter@wtwhmedia.com
Design for Access, Says Abbott’s Lisa Earnhardt, Medtech’s Most Powerful Woman ........................................... 24
“Innovation is core to who we are,” Abbott Medical Devices Group President Lisa Earnhardt says in an interview covering device design, customer needs and diversity in medtech.
Gender Parity in Medtech Leadership Remains Elusive
The medical device industry’s efforts to achieve gender parity in top leadership have stalled.
As Cardiovascular Deaths Soar for Women,
Nina Goodheart and the
Structural Heart and Aortic President Nina Goodheart shares how Medtronic seeks to save more lives through its SMART trial and development of gender-sensitive medical devices..
Designing efficient systems involves much more than simply understanding a few basic principles. There is a true art to balancing the specific requirements of an application in order to achieve the desired goals in the best possible way. Help us understand the unique needs of your application and together, we’ll develop something that surpasses what any of us could have done alone.
Contact your distributor to learn more, or visit clippard.com to request a free catalog and capabilities brochure.
Succeeding in the rapidly evolving medical device manufacturing industry requires deep expertise to deliver absolute quality, precision and speed, while reducing overall costs. It also requires investing in new and next-gen technologies.
For nearly 60 years, we’ve met – and continue to meet – virtually every contract manufacturing challenge accepted from design through delivery.
You also can rely on our impeccable track record for regulatory compliance, meeting deadlines and on-time delivery.
Bring your medical devices to market with confidence.
Visit donatellemedical.com to learn more.
Being an ally to disadvantaged and minority communities is a truly powerful act. Among other things, it helps whole social circles evolve past reflexive assumptions that “they’re only thinking of themselves” and remain more open-minded.
When I was young, a certain celebrity was afflicted with a medical condition. After their diagnosis, the celebrity suddenly became an outspoken advocate for pouring money into research to treat that condition. People kept calling this person brave, which struck me as odd and inaccurate. At the time, all of it felt a little disingenuous to me. Why was this celebrity only championing for this research once they were affected by the disease?
But today, having lived a few more decades, evolved, and worked though some of my own issues, I can see it a bit differently. As I’ve comprehended more about life’s nuances and the endless struggles individuals must battle, I’ve come to develop more sympathy and understanding.
Sometimes we’re so inundated with the demands of careers, families, and everyday life that we’re unable to comprehend the realities others face. It’s then that personal connections can force us to slow down and face our own prejudices with a new perspective. Some change their viewpoint on racial discrimination once they have biracial grandchildren. Others come to see gender discrimination when their daughter faces harassment. Still others come to view LGBTQ people more kindly after their child comes out. Many more who assume caretaking roles for aging parents or wheelchair-bound kin never look at stairs, narrow doorways, or tight bathrooms the same.
Being an ally to disadvantaged and minority communities is a truly powerful act. Among other things, it helps whole social circles evolve past reflexive assumptions that “they’re only thinking of themselves” and remain more open-minded.
Allies can also help cut through the news and echo chambers of opinion in which many of us find ourselves today.
Paul J. Heney • VP, Editorial Director pheney@wtwhmedia.com
On X (formerly Twitter) @wtwh_paulheney
I have an outspoken brother who is politically conservative and lives in an especially conservative part of the country. I came out later in life, and he’s been an ardent supporter of me and my husband over the years. When someone starts on a politically charged discussion that mentions queer people in a pejorative way, he’ll interject: “Let me give you a different perspective.” Then he tells them about my family and how we’re nothing like the offensive stereotypes (and outright lies) some media outlets push. Conservative folks hearing about the gay experience from my conservative brother — instead of someone like me — are those whose hearts and minds are key to reach.
Bottom line: Don’t be afraid to be an ally to those whose experiences diverge from the typical. Allyship is a critically important role to fill at work and in society today. And for those of you who have been allies, thank you for helping to open minds to new perspectives. DW
Welcome to Mitsubishi Electric’s vision for the future enabled by factory automation.
A bridge of digital automation lies between you and tomorrow’s manufacturing.
All your wants and needs will be translated into data, to be made reality through manufacturing.
It’s a world where digital technology and data utilization sets manufacturing free from traditional constraints.
A world where productivity and quality increase while eliminating waste and errors.
A world of speed, precision, and experiences we can only dream of today.
The digital acceleration of manufacturing will lead us to a tomorrow beyond our wildest dreams. Learn more about Automating the World us.mitsubishielectric.com/fa/en/automatingtheworld/
Aimee Kalnoskas • Editor-in-Chief • EEWorld
In an increasingly complex and fast-paced world, engineers and manufacturers are beginning to recognize the value of neurodiversity in the workplace. This shift comes at a critical time, as many organizations are experiencing fatigue and even backlash after years of expanding diversity, equity, and inclusion (DEI) programs. However, a new perspective is emerging: one that moves beyond simple accommodation to truly embracing cognitive diversity as a key to unlocking team performance and innovation.
Neurodiversity encompasses individuals — roughly 15% of the world’s population — with neurological differences such as autism, ADHD, dyslexia, dyspraxia, and other cognitive variations. These differences are not deficits but unique ways of thinking and processing information that can bring valuable perspectives to a team. As neurodiversity expert Dr. Nicole Radziwill, Co-founder and Chief Data/AI Officer at Qzuku Data and AI Quality Institute explained, “Even a neurodivergent majority company is not diverse enough to achieve the true levels of success that we all can achieve together.”
Neurodiversity creates “spiky profiles” of strengths and weaknesses, in
contrast to the assumed “flat profiles” of neurotypical individuals. This variation can lead to misunderstandings and challenges in the workplace, but it also offers significant potential for innovation and problem-solving.
Radziwill’s own journey of self-discovery illustrates the complex nature of neurodiversity. Despite her academic and professional success, including earning a college scholarship at 16 and later becoming a university professor, she didn’t recognize her neurodivergence until in her late 30s.
“After multiple counselors suggested I might be on the autism spectrum, I initially rejected the idea,” Radziwill recalled. “I stood up and said, ‘You know what’s wrong with me? You think it’s that I’m autistic? Well, clearly, you haven’t learned all you need to learn in your profession…and I walked out.”
Years later, she came to embrace her neurodivergent identity. “I went through that for about a year,” she explained, “And then gradually realized, my God, this explains absolutely everything.”
This experience informs Radziwill’s perspective on workplace inclusion. Rather than focusing narrowly on accommodating specific conditions, she advocates for creating environments
where all employees can understand and leverage their unique cognitive profiles.
In his blog on Foothold (The Institution of Engineering and Technology Benevolent Fund), Principal Geotechnical Engineers and Neurodiversity Advocate Martin Griffin writes about his experience living with multiple neurodivergent conditions: “As someone with dyslexia, dyspraxia, autism, and visual impairment, I’ve learned that my neurodiversity varies from day to day. Some days, I’m hyper-focused and can accomplish tasks with incredible efficiency. Other days, I struggle with basic organization. This ‘spiky profile’ is a reality for many neurodivergent individuals.”
The conversation around diversity in the workplace has expanded beyond traditional categories to include neurodiversity. Shirley Knowles, Chief Inclusion and Diversity Officer at Progress, an AI-powered infrastructure
At Regal Rexnord, we are making the power of one, work for you.
With decades of combined experience and industry expertise, we provide our customers with multiple solutions and products from one source to help create a better tomorrow. This also extends to working in partnership with our customers to solve your problems. We are ready to show you what we can achieve together.
software provider, said, “We’re at a time where people are more and more willing to be open and talk about it.”
Neurodivergent individuals may:
• Develop skills at a different pace or order than expected. Example: Excel in some areas while struggling in others.
• Communicate in unique ways. Example: Prefer direct communication or struggle with small talk.
• Find eye contact uncomfortable or unnecessary Example: Look away while listening to focus better on words.
• Have difficulty modulating voice or speech patterns. Example: Speak with consistent volume regardless of setting.
• Use less conventional body language or facial expressions. Example: Not smile when happy or use fewer gestures while speaking.
• Experience empathy differently. Example: Feel deeply for others but struggle to express it conventionally.
• Find it challenging to interpret others' nonverbal cues. Example: Miss subtle hints or social cues in conversations.
• Interpret language literally. Example: Struggle with figures of speech or sarcasm.
• Prefer to focus deeply on one task at a time. Example: Find it difficult to switch between activities quickly.
• Work best independently or in specific collaborative settings. Example: Prefer structured interactions in group work.
• Experience sensory input intensely. Example: Feel overwhelmed by sounds, lights, or textures others might not notice.
Remember: These traits vary widely among neurodivergent individuals. Many people may experience some of these traits without being neurodivergent, and not all neurodivergent people will experience all of these traits. (Adapted from Verywellhealth.com.)
This openness is crucial for creating an environment where neurodiverse individuals feel comfortable disclosing their needs and leveraging their strengths.
Knowles shared an anecdote about a former colleague who made mistakes on documents that became a frequent occurrence. Finally, after a significant error to an item her former CEO needed, the co-worker confided in Knowles that they had dyslexia.
“It was as though a new door had opened — all of that time where I was feeling upset at the mistakes finally made sense and we were able to come up with solutions from there. It wasn’t that they weren’t focusing on the details, there was a real issue, something they’d been navigating through since childhood that was the root cause.” Although the disclosure was likely tough for Knowles’ colleague to share, it was what was needed to strengthen the working relationship.
However, as Radziwill discovered while at Ultranauts, a company with more than 75% of employees identifying as autistic, even a neurodiverse majority workforce faces challenges. “You cannot expect a whole organization to function perfectly well for everybody.”
The key to successfully integrating neurodiversity in engineering is to move beyond simple accommodation. Instead of asking, “How do we accommodate this different group of people?” the question becomes, “How can neuroinclusion help any group of diverse individuals relate to each other more effectively?”
This approach recognizes that diversity extends far beyond visible demographics or diagnostic labels. Even within seemingly homogenous groups, individuals bring varied thinking styles, communication preferences, and work approaches.
“We want to steer it towards using neurodiversity and neuroinclusion as the basis that we use to understand each other better — whether we are
neurodivergent or not. And then, with that new information, let’s see how we can amplify the performance of our team,” Radziwill said.
Radziwill advocates for giving work groups tools to create positive team dynamics themselves rather than imposing one-size-fits-all solutions from above. One such tool is Ultranaut’s “Biodex” — a guide employees create to explain their work preferences and interaction styles. By sharing these insights, team members can better collaborate and support each other’s success.
“The Biodex has been a game-changer for our teams,” said Radziwill. “It allows individuals to communicate their needs and preferences in a structured way, reducing misunderstandings and fostering a more inclusive environment.”
Beyond the moral imperative for inclusion, there’s a strong business case for embracing neurodiversity in engineering. Neurodiverse individuals often possess unique skills and perspectives that can drive innovation and problem-solving. And in the talent-shortage field of STEM, employing neurodiverse technical staff can not only improve fill rates for hard-tofill positions for companies but also offer a competitive advantage.
“You have that insider knowledge through experience of someone that is dyslexic, ADHD, bipolar, dyspraxia, whatever it is... And so now we can use that thinking and create products and offer services that target these people. They exist,” said Knowles.
She cited an example of a Google Pixel phone camera designed to capture a range of skin tones better, likely due to having a diverse team involved in product development. This kind of inclusive design serves a broader customer base and can lead to increased market share and customer loyalty.
“Neurodivergent individuals often excel in pattern recognition, attention to detail, and out-of-the-box thinking. These are precisely the skills needed to
drive innovation in engineering and technology,” added Radziwill.
In the talent-shortage field of STEM, it doesn’t take a math genius to make the connection between the 15-20% of the world’s population who exhibit some form of neurodivergence — many of whom are underemployed or unemployed — and the potential.
Once hired, integrating neurodiverse individuals into the workplace is not without challenges. Managers may need to adapt their communication styles and expectations. However, the benefits far outweigh the initial adjustments.
Knowles underscored the importance of empathetic leadership in this process. Managers who recognize and appreciate different ways of thinking are better equipped to harness the unique talents of their team members.
Radziwill emphasized that the goal isn’t eliminating all friction or creating perfectly harmonious teams. In fact, she argued that some creative tension is essential for innovation.
“You don’t want teamwork to be effortless,” she said. “You want that creative tension. You want somebody to say, ‘Having a pizza with M&Ms and an entire rotisserie chicken on it is stupid, and here’s why no one will eat it.’ And then you want somebody else to say, ‘Let’s go do a survey and show them pictures of pizza and see who would eat it.’ And then you get data, and then you’re done. But you need that creative tension.”
Employee lifecycle support
To truly embrace neurodiversity, organizations need to consider it at every stage of the employee lifecycle:
1. Attraction: Create inclusive job descriptions and highlight neurodiversity-friendly policies.
2. Selection: Adapt interview processes to accommodate different communication styles.
3. Initialization: Provide clear onboarding processes and
consider mentorship programs.
4. Retention: Offer flexible work arrangements and create a supportive environment.
5. Promotion: Ensure fair evaluation processes that recognize diverse strengths.
6. Cessation: Provide support during transitions and maintain positive relationships.
Griffin writes, “In my experience, the selection and initialization phases are particularly crucial. Many neurodivergent individuals struggle with traditional interview formats, which often don’t accurately reflect their abilities. And starting a new job can be overwhelming due to sensory issues or difficulties with change. Companies that provide clear, structured onboarding processes and allow for gradual adjustment periods can make a world of difference.”
One of the ongoing challenges in creating a neurodiverse-friendly workplace is the issue of disclosure. Many individuals may hesitate to disclose their neurodiversity due to fear of stigma or discrimination. Knowles stresses the importance of creating a supportive environment where people feel safe to be their authentic selves.
She also highlights the role of Employee Resource Groups (ERGs) in providing support not just for neurodiverse individuals but also for their families and colleagues. These groups can serve as valuable resources for education, advocacy, and communitybuilding within organizations.
Radziwill added, “Disclosure should always be a personal choice. What’s important is creating an environment where people feel they can disclose if they want to, without fear of negative consequences. It’s about fostering a culture of understanding and support.”
As engineering evolves, embracing neurodiversity will likely become increasingly important for companies looking to innovate and stay competitive. Radziwill envisions a future where
diverse minds collaborate to create products and services that cater to a wide range of human experiences and needs.
“If there’s going to be a sea change, it’s going to be manager by manager,” she says, emphasizing the importance of individual leaders in driving this transformation.
“The future of engineering lies in our ability to harness the full spectrum of human cognition. By embracing neurodiversity, we’re not just creating more inclusive workplaces — we’re unlocking new realms of innovation and problem-solving,” added Knowles.
The journey towards the true inclusion of neurodiverse individuals in engineering is ongoing, but the potential benefits are clear. By fostering an environment that values different ways of thinking and working, companies can tap into a wealth of talent and creativity that has long been overlooked.
“The problems that we have to work through today in our jobs in society are so complex and moving so quickly that we can no longer assume that any one of us has the answer,” Radziwill said. “Literally, the answer is going to be in between the space of those of us who come to solve it.”
As we move forward, it’s clear that neurodiversity isn’t just about accommodation or compliance — it’s about recognizing and leveraging the unique strengths that come from diverse ways of thinking. In the world of engineering, where innovation is paramount, embracing neurodiversity may well be the key to unlocking the next generation of groundbreaking solutions. DW
By Nicole Imeson
Engineering employers are increasingly challenged to attract and retain talent. Here’s a compelling (and counterintuitive) case for helping new moms and dads stay off work longer.
Adiverse workforce generates fresh ideas, sparks creativity, and drives innovation. Individuals with different experiences and thinking patterns view problems from unique angles, leading to innovative solutions. However, despite these benefits, a 2022 McKinsey & Company study revealed a decline in women’s representation in technical roles like engineering, dropping from 18% in 2018 to 16% in 2022. Additionally, 32% of women in these roles often find
themselves as “the only woman in the room — a situation known as being “onlies.”
Generational shifts in the workforce are driving engineering employers to focus on motivations beyond paychecks and essential benefits. Robust parental leave policies have emerged as a powerful tool for enhancing workplace diversification, retention, and recruitment. Not only do these policies provide parents with valuable
family time and economic stability, but they also cultivate a more loyal and committed workforce. A 2022 Unum consumer research study identified paid family leave as U.S. workers’ third-most important non-insurance benefit. Furthermore, a 2023 Pew Research Center survey showed that 91% of workers deem it essential for their employers to offer paid parental, family, or medical leave in addition to vacation or paid time off (PTO).
The Great Resignation amplified the importance of parental leave, as more than 47 million Americans left their jobs. In response, countless HR leaders prioritized retention. Understanding what drives employees — whether family needs, personal achievements, financial goals, or cultural factors — aligns leadership with team priorities. As more engineers who are planning families seek accommodating employers, parental leave should become a key part of competitive compensation alongside salary, paid time off, and promotions.
In male-dominated fields like engineering, retention and recruitment have always posed challenges. Poor retention undermines recruitment since prospective talent struggles to see themselves in organizations with limited diversity. Weak recruitment stifles diversity across all levels, perpetuating the problem. Offering paid parental leave to birth parents, mainly cisgender women, boosts their return rates, enhances loyalty, and strengthens diversity. Extending parental leave to non-birth parents increases men’s participation, reduces stigma, and promotes gender equality by normalizing the act of sharing parental responsibilities.
“When people are looking for purpose in their lives, to know that a parental leave benefit exists — even if they’ll never use it — says something about the organization,” said HR consultant Michelle Berg, founder and Chief Visionary Officer of Elevated HR Solutions in Calgary, Alberta. “It’s very similar to bereavement leave policies, where you know it’s there if you need it. Most people want to be in a company that has these types of benefits.”
In the U.S., the 1993 Family and Medical Leave Act (FMLA) provides new parents, whether by birth, adoption, or foster care, with 12 weeks of unpaid annual leave while maintaining group health benefits. However, many parents struggle with unpaid leave, often relying
on PTO or skipping leave entirely. Some states have supplemented FMLA by lowering eligibility barriers, extending leave, or offering state-funded benefits, but most provide no additional support. Private companies have stepped up in response to federal funding gaps and state inaction. Netflix offers up to 52 weeks of paid leave for new parents, though most parents take between 16 and 32 weeks. KPMG provides up to 52 weeks for birth parents and two weeks for non-birth parents. In 2022, Google extended its paid leave to 24 weeks for birth parents and 18 weeks for non-birth parents.
McKinstry, a 3,000-employee construction and engineering firm headquartered in Seattle, offers all parents eight weeks of paid parental leave and eight more weeks to birth parents. McKinstry aligns with federal and state benefits by topping up salaries or extending leave when benefits are available. If no such benefits exist, McKinstry covers the cost. The company offers leave with no waiting period nor repayment obligation if an employee resigns rather than returning from their break. It also allows employees to split their leave into two periods over one year and doesn’t require PTO depletion before qualifying.
Around 50 McKinstry employees take parental leave in any given year, with 81% using their full allotment. “We encourage people to take that time away,” sais Karla Sperber, Senior Director of Employee Experience and Operations at McKinstry. “We back that with support for coverage while people are gone.”
In technical fields like engineering, the complexity of knowledge transfer can complicate parental leave. Clear documentation, structured handovers, and open communication ease the burden of this transfer. Comprehensive guides on
projects, workflows, and key contacts, along with knowledge-sharing sessions and mentoring, ensure continuity and minimize disruptions.
Leaders should model the use of parental leave and time off, demonstrating the importance and feasibility of these benefits. “Parental leave is one of those policies that are great to talk about and to say you have, but it’s one of those sneaky policies that some of these organizations have knowing full well that very few employees will actually take it,” said Berg.
The benefits of parental leave extend beyond employee satisfaction. A 2019 American Sustainable Business Council report found that technology companies experienced increases, on average, of 14% in revenue, 25% in profit, and 6.5% in return on human-capital investment after adopting paid parental leave. These gains stem from reduced turnover, increased productivity, and improved morale. Depending on an employee’s position, replacing them costs between 30% and 400% of their annual salary. Experienced employees bring valuable institutional knowledge, which takes replacements months or even years to acquire.
Small businesses, however, face unique challenges with paid parental
leave due to limited resources and tight profit margins. One option is to leverage state benefits programs to help cover costs. Short-term disability coverage can also provide financial relief for birth parents in states with paid leave programs, allowing for a combination of disability and state benefits to extend parental leave.
McKinstry recognizes that supporting employees outweighs the costs of parental leave. “We gain from having strong benefits that keep people here and engaged and make them feel like this is the place for them to be versus having to go and buy that talent,” said Sperber. “It’s good for business and aligns with the value of always putting people first.”
One problem for parents is that time taken for parental leave is often perceived as time not taken to gain
professional experience, including the continuing education hours required to maintain engineering accreditation. Such perceived gaps in career progression can create competitive pressures, particularly for women. “The fight that I still have with many of the employers that I work with is, just because parents take parental leave doesn’t mean that they’re that much less experienced,” Berg explained, citing competencies developed through parenting such as task prioritization, time management, resource allocation, and problem-solving. “Life still plays a role. I would argue that when you go on parental leave, the skills that you learn are incomparable to what you have at work.”
If more men took parental leave in male-dominated fields like engineering, it would normalize the policy and reduce competitive pressures for women. Comprehensive parental leave policies also reduce gender disparities
by fostering a more inclusive culture around parenthood. Observing women and non-binary individuals in senior roles provides hope, but unequal opportunities often make employees believe that only a few can reach top positions.
“If you’re that person who is having a baby or wanting to have a baby, our parental leave policy is fantastic,” said McKinstry’s Sperber. But McKinstry knows it’s only part of a competitive compensation package. “We work hard to provide benefit options that appeal to our entire workforce, whether they’re a new parent, an empty nester, or never plan to have children at all,” said Sperber.
It’s a sound strategy for engineering organizations competing for uncommon talent in today’s business environment — especially for those recognizing the power of workplace diversity. DW
One control platform for all machine functions
TwinSAFE
System-integrated with logic in all safety components
In machine safety, going for “good enough” is never the right choice. Ensuring the safety of your people, equipment and products is simply not optional. TwinSAFE from Beckhoff is the universal safety solution for everything from basic monitoring to complex motion in a fully integrated automation ecosystem. Directly meshing with your PLC, motion control, measurement, IoT and vision technologies, TwinSAFE helps you implement more safety functionality in more places. This comprehensive platform streamlines machine design with programmable safety functionality to safeguard what you value most.
Integrated in all TwinSAFE components: the Safety Logic
Programmable logic controllers (PLCs) are ruggedized microprocessor-based electronics essential to all modern automation, including:
The process-heavy industries of oil and gas, nuclear, steelmaking, and wastewater treatment
Industries with an emphasis on control of discrete tasks — including general factory automation, automated warehousing, packaging, food and beverage, and medicaldevice manufacture
In these installations, PLCs are traditionally found on DINrail mounted or control-cabinet rack systems with slots to accept PLC modules (having CPUs to run logic and
dispatch commands) and complementary power supply modules, application-specific function modules, and digital as well as analog I/O modules.
Of course, PLCs aren’t the only option for automation control. Relay-based systems maintain their indispensability in a vast array of applications, and programmable automation controllers (PACs) or industrial PCs (IPCs), as well as panel PCs (HMIs with control electronics), are other alternatives for many machine designs and systems needing varying degrees of distributed control. PACs and IPCs running industrialgrade Microsoft Windows OSs especially offer top design flexibility.
Each of these control systems is configured and programmed with software of diverse sophistication to render all types of control design more advanced and user-friendly than ever. This in turn allows OEM machine builders and plant engineers to quickly institute system builds, upgrades, and migrations with maximal efficiency, productivity, and IIoT connectivity.
The tools to program controls — including PLCs
Nearly all PLCs today are configured and programmed through PC-based software. Large vendors with broad programmable motion control, sensing, actuation, and machineinterface component offerings (in addition to general automation and PLC products) typically allow programming of all these components in their own proprietary unified programming environments — PC-based Windows-compatible software with design, configuration, programming, and even operating and management modules. That’s especially true where vendor lineups include pre-integrated offerings — such as smart motors or HMIs having PLC functionality, for example.
While potentially daunting to learn, unified programming environments (once mastered) dramatically speed machine design.
One benefit of such software environments is how they provide error-free, editable, and universally applicable databases of symbol, variable, or tag names. These are human-readable alphanumeric names assigned to the addresses of components (including PLCs) and
improving upon the direct use of complicated register addresses — which was once standard practice. Complementing these sortable and searchable device tags are informative machine and workcell tags as well as those for common machine functions such as Auto, Manual, MotorOn, Fault, or Reset.
Consider Siemens STEP 7 Totally Integrated Automation (TIA Portal) software, which includes various usespecific packages and is accessible through the Siemens SIMATIC (Siemens Automatic) softwaremanagement environment. STEP 7 software is convenient for illustrating the most common approaches to PLC programming, as it’s the most widely used software in the world for industrial automation — with copious verification of functionality and reliability. By most estimates, Siemens PLCs are employed in nearly
one-third of all PLC installations worldwide.
With this software, engineers can create process control, discrete automation, energy management, HMI visualization, or simulation and digital-twin programming related to the functions of PLCs and other industrial controllers. For PLCs, Siemens’ STEP 7 (TIA Portal) engineering software evolved from legacy SIMATIC STEP 7 software to support the programming of S7-1200, S7-1500, and S7-1500 controllers — as well as ET 200SP I/O CPUs and legacy S7-300 CPUs (an enduring industry staple) along with S7-400 and SIMATIC WinAC controllers. Professional-grade and specially licensed copies of STEP 7 include additional functions, logic editors, and integration of traditional engineering software.
Figure 1: PLCs offer all the strengths of purpose-built hardware — including reliability. In contrast, PACs offer top flexibility. Some suppliers allow engineers to program both control types in the same unified software environment. Such environments can also impart unrestricted access to digitalized automation, engineering, and operational monitoring tools. (Image source: Siemens)
Though beyond the scope of this article, it’s worth noting that industrial control alternatives to multi-function PLCs are configurable and programmable through complementary software. The vast ecosystem of Siemens controls provides copious examples.
1. LOGO! logic modules satisfy small and modest automation applications to bridge the gap between relays and microprocessor-based industrial controllers. They’re programmed via Siemens LOGO! software with Soft Comfort engineering software, a LOGO! Access Tool, and a LOGO! Web Editor for simple configuration and design operation.
2. Process control systems employ Siemens SIMATIC PCS 7 controller products programmable through SIMATIC PCS 7 system software.
3. Rack (rail), panel, and box industrial PC (IPC) products for distributed controls and machines needing IIoT connectivity rely on Siemens SIMATIC IPC software modules, including an IPC Image and Partition Creator;
IPC DiagMonitor; IPC Remote Manager; IPC FirmwareManager; and the SIMATIC Industrial OS.
4. HMIs serving as panel PCs for on-machine controls employ SIMATIC WinCC Unified (TIA Portal) software as well as SIMATIC WinCC (TIA Portal), WinCC flexible, WinCC V7, WinCC OA, ProAgent process diagnostics software, notification software for mobile devices, and more.
Choosing between SIMATIC PLCs and other machine controls is simplified with still more software — in the form of an online cloud-based Selection Tool (or the offline variation) that asks engineers about a given design’s physical arrangement (whether necessitating a control cabinet or distributed control) and:
• The number of anticipated I/Os including sensors, switches, and actuators.
• The programming language to be used, whether ladder diagram (LD), structured control language (SCL), or Function Block Diagram (FBD); more advanced structured text (ST), graph-based sequential function chart (SFC), and
continuous function chart (CFC); or more advanced languages.
• The level of motion control required (where applicable) — from simple speed and position control to electronic camming and advanced kinematic controls.
• The hardware preference and whether a software PLC program running on an IPC might be most suitable.
PLC programming written in PLC supplier software is often contained in projects. These are associated with focused application-specific operations such as:
• Heating, mixing, filling, metering, and irrigating
• Moving, steering, cycling, positioning, and braking
• Gripping, cutting, punching, and slicing
• Welding, gluing, marking, and dispensing
• Sensing, tracking, sequencing, and indicating
The most advanced options support digital planning and integrated engineering as well as transparent operation that’s easily accessible through HMIs with user-specific screens one in operation. In other
Figure 2: Siemens SIMATIC PLC and automation systems were first introduced in the 1950s. Today, SIMATIC S7 products (including the SIMATIC S7-1500 PLC components shown here) have evolved to support various industrial automation applications. (Image source: Siemens)
words, such PLC software can allow for the presentation of pertinent PLC information on different displays to serve the divergent informational needs of machine operators, technicians, plant managers, or even business managers.
Simulation tools within PLC supplier software environments also can speed time to market for a given product — and boost throughput of finished product. Completing the suite of software-based improvements are energy-management functions and diagnostics.
Verifying and loading PLCs with programs written in software
Core to optimal PLC functionality is the quality of its programming. All code should satisfy softwaredevelopment industry standards and best practices. Beyond that, verification processes (both manual and automated) can reveal everything from critical errors to code inefficiencies. Reconsider the programming of SIMATIC S7 products. Within the Siemens ecosystem, a TIA Portal Project Check application can automatically compare certain code against rules defined by a programming style
PROGRAMMING ASPECT GOAL
guide for these specific PLCs. Then engineers can export comparison results to an XML or Excel file. Userdefined rule sets (even complex types) can also be added via a Project Check software development kit (or SDK) in C# or Visual Basic (.NET). This SDK primarily proofs a program’s style.
After a project destined for a PLC is fully written and verified, it must be loaded onto that PLC. In many cases, a PC (often a laptop) is temporarily connected to the PLC via an Ethernet cable or a specialty PC USB to PLC COMM adapter — to load that programming onto PLC microelectronics. The PLC then connects to controlled components via I/O modules. After additional verification upon startup, the PLC executes its programs by commanding networked actuators (via various signal types) and making real-time adjustments in response to returned feedback from field devices.
Occasionally, a machine or automated workcell will require adjustment, troubleshooting, or repair — and (through some type of programming PC connection to the PLC) the overriding of PLC default responses to feedback with forcing. This “tricks” the PLC into operating as if certain feedback is at some value
Style Comprehensibility
Technique Conformity
Technique Efficiency
Test cases Functionality
Mathematical model Correctness • completeness
when it isn’t — a tactic employed when the stations downstream of a malfunctioning actuator must be cleared, for example. Other times, a machine or workcell might require in-field adjustment of an installed PLC’s parameters via modifying. Such adjustments must reference suitable triggers, variable values or tables, counters, and timers.
Working with the vast array of Siemens automation and industrialcontrols offerings can provide design engineers with a deeper understanding of today’s control options — including PLCs and other hardware types. That’s true no matter the brand or hardware subtype ultimately chosen for an automated installation.
www.digikey.com
Empirical Code review • Style check
Pragmatic Static code analysis • Lint
Pragmatic Dynamic code analysis • Profiling
Syntactic Function test • Unit/integration test
Syntactic Formal verification • Model check
Table 1: Verification of PLC programming can leverage manual and automated approaches — with the latter especially useful for verifying style and technique. (Image source: Siemens)
Growingup near the seashore of Pondicherry, India, Ahamed Azigar Ali was the first in his family to graduate from high school, not to mention go to college. But the seeds of an engineering education came early when he started school at age five. Ali’s father worked to grow a passion for engineering by teaching him foundational skills, such as building toys and tools and repairing household electronic equipment.
“My father told me, ‘Study well and become an engineer,’” Ali recalled. “He believed that becoming an engineer would lift our family out of poverty. This early motivation shaped my educational journey, driving me to excel academically with the primary goal of economic stability for my family.”
However, his perspective on engineering evolved significantly during college at Pondicherry University. Ali said that he was fortunate to have inspiring professors who encouraged him to see beyond the immediate financial benefits
of an engineering career.
Ahamed Azigar Ali sees beyond the business benefits of engineering and aims to make a positive impact on humanity.
Paul J. Heney VP, Editorial Director
“My professors further shaped my path by introducing complex real-world problems in the field of engineering and teaching me how to solve them using scientific methods and research techniques. A particularly memorable learning experience was a research project in which I conducted comprehensive practical experimentation and MATLAB-based software simulation to study the performance of a highvoltage 3-phase induction drive when abnormally switched to a single phase. This project exemplified the application of theoretical knowledge to practical challenges and solidified my commitment to research and innovation in engineering,” he said.
Another pivotal influence during this period was Dr. APJ Abdul Kalam, President of India at the time. Learning about Kalam’s life, from his modest beginnings to his achievements as a top scientist and eventually President, profoundly impacted Ali.
“I realized that engineering could be more than a means to improve my family’s economic status; it could also be a way to make a meaningful impact on society,” he said. “This shift in perspective transformed my approach to my studies and career. After uplifting my family out of poverty and supporting my siblings to pursue engineering, today, as a Senior Director of Technology at Advantage Solutions, I aim to make a positive impact on humanity through innovation and engineering.”
Challenges and opportunities
Ali has been involved in numerous product launches and technology development projects across diverse business domains.
“One particularly exciting and impactful project was when a leading multinational, publicly traded company developing system used car dealership approached me to license my innovation, a ‘Blockchain-based Provenance System,’ for solving the most pressing used car
vehicle history verification problem. The used car dealership market in India is highly unorganized, posing significant challenges in verifying vehicle history, including accidents, insurance claims, ownership, and maintenance records,” he said.
Originally developed to verify user profile information on an online matrimony platform through a blockchain-based verification network, this system needed to be adapted for a completely different application — verifying the history of used cars. This required integrating insurance companies, car dealerships, major car maintenance workshops, and vehicle registration entities into the verification process.
According to Ali, adapting the solution necessitated extensive research to understand the requirements and constraints of India’s used car sector.
“Collaboration with the diverse stakeholders was essential to ensure the system’s comprehensiveness and accuracy. Additionally, pushing the boundaries to accommodate new parameters required significant innovation and problem-solving. With relentless effort and effective collaboration with stakeholders, I successfully extended my innovative solution to verify used car histories... This transformation not only improved the credibility and trust in the used car market but also significantly altered the business dynamics of used car dealerships.”
Future thoughts
Ali said that increasing the participation of young people from underrepresented communities in engineering is essential for fostering diversity and innovation.
“I recommend incorporating innovation and entrepreneurship education into school curricula,” he said. “By teaching students STEM concepts, problem-solving skills, and the process of innovation at an early age, we can nurture their potential as young innovators.”
I realized that engineering could be more than a means to improve my family’s economic status; it could also be a way to make a meaningful impact on society.
He also feels strongly that accomplished engineers should reach out to young people in their communities and share their stories. Ali volunteers through a foundation to share his career experiences for mentorship.
“Similarly, schools should invite and encourage accomplished engineers of different ethnicities to collaborate with the youngsters in building community projects,” Ali explained. “Bringing the sense of diversity, equity, and inclusiveness in schools at the early grades will make the young individuals from underrepresented communities feel valued and motivated to pursue careers in engineering.”
That diversity is important and can drive exceptional outcomes.
“An engineering and design problem can be approached in multiple ways to achieve an optimal solution. Engineers from diversified cultures bring a wealth of different perspectives, ideas, and approaches, fostering innovation and creativity. It allows for more comprehensive problem-solving and leads to solutions that are more inclusive and effective,” he said.
For someone new to engineering, Ali said that it comes back to finding the right mentor. That can provide invaluable guidance and constructive feedback to accelerate a junior engineer’s learning curve and enhance their confidence in the workplace.
“The mentor can be your immediate supervisor or someone from your cross-functional peer network,” Ali explained. “Also, engaging actively in team meetings, expressing your ideas, and contributing to conversations helps you gain confidence in your abilities and establishes your presence within the team. You should also adopt a few safeguard skills, like staying organized
with productivity tools, reviewing your deliverables from your peers to get a fresh perspective, and catching mistakes. As you commit mistakes, don’t stress about it, rather perform root cause analysis and identify remediation actions that can prevent those mistakes from happening in the future. I have learned that sharing my mistakes and the lessons learned with my teammates have enabled me in creating a culture of openness and continuous improvement within the team.”
Ali has never felt disadvantaged in his organization because of his membership in a minority group and feels fortunate to be part of the company. He noted that Advantage Solutions was named one of “America's greatest workplaces for diversity” in 2023, and he was nominated and accepted for the Advantage Ambassador program, which recognizes emerging leaders.
Allies are a part of Ali’s journey, too.
“I feel well-supported by allies who actively promote an inclusive and collaborative culture. In Advantage Solutions, there are multiple ERGs (Employee Resource Groups) like Inspire Asian, Disabilities in Action, Hola, Band, Women's Interactive network, and so on. These ERGs offer associates the opportunity to build community, feel valued, and grow personally and professionally. As a member of Inspire Asian ERG, I was accepted for the McKinsey’s executive leadership program to accelerate my professional growth within my organization,” he said. Looking toward the future, Ali mused about what global challenge would most intrigue him. DW
When Ahmad Muslim was about nine years old, he went to his grandmother’s house and disassembled her VCR — a perfectly fine, operational VCR — just to see what was inside. He took it apart, put it back together, and then explored other household items.
Muslim’s mother recognized his inquisitive nature and innate math skills, which she and his brother admit do not run in the family. As a single mother raising two boys in Washington, D.C., she later told Muslim’s high school guidance counselor about his childhood tinkering and desire to know how things work. When college applications rolled around, engineering seemed like the right fit.
“I definitely credit my mom, and I’ve always been very fortunate to have people who fanned my flame and didn’t try to put it out,” said Muslim.
Muslim studied electrical engineering at Florida A&M University in Tallahassee and joined Proctor & Gamble (P&G) in Cincinnati in 2008. Like many recent graduates, he didn’t fully understand
Ahmad Muslim encourages engineers to be their full selves at work and tackle challenges head-on.
Rachael Pasini • Editor-in-Chief
what being an engineer at the company meant but was grateful to receive a job offer in an uncertain economy.
“I’ll be honest, when I thought of P&G, the first thing that came to mind was the products, but as I navigated my career, it’s been extremely fulfilling,” said Muslim. “I’ve been fortunate to work on many different platforms and have many different experiences where I truly get to exercise that engineering muscle, whether it’s interfacing with our manufacturing sites and helping them troubleshoot or solve a problem or more upstream things like integrating new technologies, machine learning, or AI into our business and processes.”
For the past 15 years, Muslim has worked in P&G’s beauty sector as an intelligent controls and automation engineer. He and his team provide the brains — the electrical hardware and software — of the sector’s manufacturing systems, including data and integration. Early on, he led the installation of a new packing system for Old Spice products, coordinating with numerous suppliers, designing software
and hardware, and integrating multiple systems into the facility. He also helped start up two manufacturing plants by installing new systems, designing new processes, and integrating the facilities. Such projects exposed him to technical challenges and other engineers outside his expertise.
“You need the technical foundation to be an effective engineer, but you can’t get the work done by yourself — that’s just impossible. So, you also need to be able to convey a message, influence people, and articulate a problem statement,” he said.
But engineering problems aren’t the only challenges Muslim has encountered. Day-to-day social expectations and assumptions impacted his initial career and continue fueling his passion for developing inclusive cultures.
“I always like to push the line in terms of style and appearance, so a thought played in the back of my mind: I have to be a certain way to be successful here,” said Muslim. “I spent so much time worried about the perception that
I wasn’t fully unleashing all of what I had to offer. All that focus could have been put towards innovation or solving the next problem.”
Muslim attributes P&G and its employees for cultivating a culture that encourages everyone to be themselves at work.
“You don’t owe it to anyone to try to be somebody that you’re not — to try to fit a mold that isn’t who you are,” he said. “Once I really started to embrace my individuality and bring that into the workplace, it initially shocked me because everyone was so receptive. I was worried for so long, and it was liberating to have that breakthrough. It also really opened me up to start doing the equality, inclusion, and diversity side of things in my career. I felt empowered to encourage everybody to show up in the ways they want and to be their full selves.”
Muslim became actively involved in affinity networks and gender equality programs and started mentoring to increase diversity awareness.
“It’s personal to me. I want to see environments and spaces where women are treated equally because I come from a place where the majority of the people who raised me and got me to the point that I am were women,” he said.
He also started exploring other forms of diversity that often go unseen. “I started researching neurodiversity more because it wasn’t something I was very aware of myself. It’s important that everybody feels like they can be their best selves, and those characteristics can be more challenging because you have to deal with them in silence, and no one can see them. No one would ever know to ask you if you don’t disclose them in some kind of way.”
When it comes to the inclusion of African Americans in the workplace, Muslim feels like society has advanced yet regressed in certain respects.
“Many younger people are a lot more unapologetic than I was, and I’m encouraged by that,” he said. “They’re empowered to use their voice because of the culture they’ve grown up in. In
the last 15 years, they’ve seen things happen in society that I didn’t see as a child — not that they weren’t happening, but it wasn’t as visible and prevalent. I think that has created a certain level of rebelliousness or self-awareness and pride that has allowed younger people coming into the workforce to be a little more aggressive, and I appreciate that about them, but I do think there’s still a ton more work to do.”
Muslim is optimistic, though, mainly because more information is readily available to educate all of us to be more accepting, adaptable, and accountable for our words and actions.
“You can’t be secretive about your hate for any particular group anymore. It’ll get discovered, it’ll get called out, and it will affect your business,” he said.
Muslim remains excited about engineering, especially as technology evolves, and looks forward to new opportunities to learn, reinvent, and add to his toolbox. He aims to continue building his technical and non-technical skills to solve challenging engineering problems that benefit P&G’s business while being a diversity and inclusion leader in the workplace and elsewhere.
“I love the technical work, but my legacy will definitely be in what I’ve poured into other people and the culture that I’ve created here and will leave behind,” he said. “And I tell everyone in our organization, as much as you may view me in a certain light as it relates to diversity, equality, and inclusion, I’m still on the journey just like everybody else — there’s no endpoint.” DW
Fiona Miller is a legend in the world of electronics engineering. After selling her last company a few years ago, she pivoted to run a venture fund that invests in biotech companies focused on age reversal.
Miller’s first introduction to engineering was in high school in 1978. Computers existed but were uncommon, and nobody knew what they were. “One nice teacher brought a very primitive little computer into our math class; the computer read paper tape and had a single-line LCD that could display seven characters. This teacher let us earn class credit by playing with this fascinating computer instead of doing math, and it pulled me right in,” she says.
Miller went to Columbia University’s Barnard College to major in philosophy yet took one computer-science course as a standalone elective. The passion for computers came back, and she found she could play for hours programming the primitive computers.
“In fact, programming is a lot of fun and relatively captivating,” she says. “But I began wanting to know more about the electronics behind these magical capabilities — commands and programmed responses to make people laugh and so on. So, I transferred to
the engineering school at Columbia to study electrical engineering. Coming from a liberal arts school, I wasn’t really prepared for engineering coursework … but curiosity drove me.”
Recently, Design World caught up with Fiona Miller about her experiences at college, her work at automated test-equipment supplier Teradyne after school, and what drove her to her various successes after that. Here’s what she had to say.
Was your university a supportive environment?
At school, there were only two of us women in our graduating engineering class of about 300 engineers. So, we felt a little odd … but the other woman became valedictorian of our class. So, it was clear we could engineer. We just got used to being in classes full of guys, and nobody was particularly encouraging or discouraging — we were simply treated as adults. However, in my last year, I wanted a hands-on project to fully grasp the abstract things that weren’t quite sinking in for me. So, one of my professors let me pursue that as my coursework for the last semester. Well, the guy who ran the electronics lab was a nice old guy and very supportive.
Because everything was very primitive at that time, I had to etch my own circuit board and expose it in a darkroom. He got me all the supplies and showed me how to do it all. We ended up building a little autonomous vehicle and had a ton of fun.
In fact, while in school, I also worked on programming to be used on Wall Street. At the time, no computerized systems were used to run the stock market. It’s very strange to think about now. A Columbia graduate working on a brokerage project bought a PDP 11 computer and put up a help-wanted advertisement looking for programmers. So, I applied and got a part-time job working for him for two or three years. I vividly remember the first project was to write a program to analyze option yields for options trading. My boss ran around with this printout that I’d produced saying, “Now we can do this report every night instead of intermittently doing it by hand.” We were part of the stock market’s initial early use of automation and computers.
But software was too easy for me, and I really wanted to do hardware. In 1983, when I got recruited by Teradyne, I moved to Boston … and that’s where I still am.
After a year and a half at Teradyne, I joined a startup called Chipcom (now 3com) as the seventh employee. Working late nights with founders, I was there to see the initial company setup and laboratory buildout with new equipment.
Of which of your businesses or technologies are you most proud?
I’m most proud of octoScope because it was all mine and therefore the most challenging … and yet I was already a mature professional. I’d worked at startups. I’d managed engineering groups. I’d raised venture capital and knew I didn’t want to go that route with this business. I had to build a team, and we were a good team; octoScope was a tremendous experience. At first, it helped that I was already well known in the computer-networking space. Soon, I had more business than I could handle. So, I got two super-smart engineers to join me as cofounders.
Together, the three of us got the consulting business to a million dollars. Then in a move away from the consulting work, we developed a product. Of course, then we had to figure out how to put this product into production and sell it. We also had to build our team because sales were quickly growing. So, I pretty much went to business school right there — a hands-on school that forced me to read a lot of business books and figure out ways to scale the business up to $20M. Then we sold to Spirent … and then I didn’t have to work anymore.
What is most challenging — actual engineering, managing a team, or raising capital?
Everything about raising capital for my second startup, Azimuth, was challenging. I worked with a couple of venture funds here in Boston. We had to gather information for them and learn to size up the market, competition, and customer base — all that. Even creating a business plan was a new challenge because, as an engineer, I’d never done this before. So, it was an exciting
learning experience. After I raised the money, a CEO was put in place, and I lost a lot of control. Even so, I stuck it out for five years. When I left, I formed a consulting business because I felt like I needed my own space and to determine my own course. Such freedom just went away after venture funding.
In contrast, early on at octoScope, we faced a serious technical challenge. We created a small test system in which we emulated real-life environments for residential and other wireless communications. People used to run around their houses and test their WiFi at different points. Well, our job was to test WiFi setups in a small enclosure … and get that enclosure to behave like a big house. The multi-factor physics of a house involves places where there are walls and other reflection points (such as those from furniture) and varied travel distances based on how big the house is. We couldn’t just test WiFi devices in clean test-enclosure environments and expect to catch all potential issues. No, we had to recreate real environments with multipath motion interference, traffic loads, and other challenges while monitoring how a given device responds to all these impairments.
To put a finer point on it: Wireless devices and their related software are complex and must be adaptive to various phenomena in open air, such as interference and sudden traffic. Testing these technologies required a control system to replicate real-world challenges and record device responses. This was a multi-dimensional challenge involving very serious RF multipath issues — issues having PhD-level complexity due to the physics from multipath as well as motion emulation and software automation to create different scenarios for testing and recording device behavior.
We ultimately succeeded, and our system became the de facto standard for the whole industry — used by wireless operators, including AT&T, Verizon, France Telecom, and others worldwide. In the process of this massive adoption and serving customers around the
globe, I flew enough to get AAdvantage 3-Million Miler status with American Airlines. It was a powerful system, and I wasn’t alone; my cofounders brought in some very smart people. I had to learn how to sell and market it, and that was a new challenge. Then, every year, there seemed to be a different challenge; we became so big that we had to learn how to best grow the team and manage production to maintain the highest quality … things like that. Many very different things must be confronted as a company grows, and we needed to learn something new every year.
If you had unlimited time, what global challenges would you be interested in tackling?
I think right now we’re in the age of AI, biotech, and synthetic biology. Networking is done; we did it. Networking technologies are going to keep evolving and getting faster, but their main era of innovation is done. My son just finished college a year ago, and he wasn’t interested in computing. Unlike when I was young (and computers were just coming online and cool), computers now are old news. I tried to get him to do some programming, and he wanted to play with genes and create engineered organisms. So, he went into synthetic biology. This is the age, right?
But there’s a lot of technology in biotech — including computing, automation, AI, and machine learning. We’re kind of still doing engineering and programming, but now we’re working with genomes. People who used to be in engineering, a lot of them are going into biology, and now they’re flipping genes and creating different organisms or trying to fix imperfections in the design of humans because God knows we’ve got a lot of issues we could fix so we could be healthy. On the longer ride, that’s kind of the next wave. DW
read the rest of this interview at engineering.com/category/edi
Michelle Parker leads Boeing’s Space Mission Systems team, which designs and delivers next-generation spacecraft and associated ground systems.
Growing up, did you bring math workbooks with you on vacation?
Michelle Parker did.
Parker’s love for math and science led her to earn a PhD in mechanical engineering from the University of Pennsylvania. Her high school physics class showed her how to connect math and science with her interest in space.
“I always had an interest in space and would watch Space Shuttle launches,” said Parker, the daughter of a mechanical engineer father. “I drew solar systems and knew the planets’ names. I wanted to be an astronaut and wrote essays about space exploration.” Surprisingly, Parker didn’t join any space-related clubs while a college student. Her interest in space took off in graduate school, where she wrote a proposal for a Space Shuttle experiment.
After earning her PhD, Parker landed a job as a thermal-analysis engineer at Hughes Space and Communications Co. (acquired by Boeing in 2000)
through a newspaper advertisement. At first, the native of Kansas City, Mo., thought she’d stay in California for a year or two. That was nearly 30 years ago.
Over the years, Parker moved up from thermal engineer to her current role: VP of Space Mission Systems for Boeing Space, Defense & Security. Along the way, she’s contributed to and led engineering teams on numerous satellite designs. “I’ve been fortunate to work on the advancement of space exploration and communications,” she said. Some of her thermal designs, which include thermal coatings, blanket design, and heat pipes, are still used today. Her work went into satellites for Sirius XM Radio, which she often listens to in her car. Other spacecraft incorporating Parker’s work include the Boeing Starliner and the Artemis core-stage rocket. She also served as Boeing Space Launch’s chief engineer
during the development of the SES O3b mPOWER satellites — the first two of which launched in December 2022. It was at that launch that I met Parker and, hence, wanted to interview her.
From a heat dissipation perspective, the O3b mPOWER satellite design was one of Parker’s memorable projects. “O3b mPOWER is really a game changer,” she said. “That’s because it’s a software-defined communications satellite. The electrical engineering and the manufacturing were different than anything we’d previously done. The satellites take all the communications payload — waveguides and RF cables that were previously assembled by hand — and put it into a flat pack. That’s analogous to going from a tube TV to a flatscreen TV. All electronic components and interconnects are on PCBs instead of being hand-wired. That let Boeing automate the manufacturing of the satellite’s electronics.”
The problem, however, is dissipating heat. The electronics are now
compressed into a smaller volume but at the same power levels as in previous satellites, making heat transfer much more difficult. “Space is a difficult environment because there’s no convection to dissipate heat. We had to invent new thermal-rejection methods, which included additive manufacturing of a cold plate. Conduits have fluid pumped through them to capture heat and reject heat to space. Developing that 3D-printed plate with its conduits presented a new challenge.”
Driving ingenuity through diversity
Designing and building complex systems such as communications satellites requires a multidisciplinary team of engineers and technicians. Parker understands that such teams need various technical skills; people must think creatively to solve problems.
“It’s important to have diverse teams, especially when you’re solving problems that have never been solved before,” said Parker. “People approach problems differently based on their backgrounds. Difference of opinion is important.” Parker recalled a study of two teams — one diverse, one homogenous — that were asked to solve the same problem. The homogenous team reached a resolution faster, and team members all agreed that it was the best solution. In contrast, the heterogeneous team took much longer to solve the problem. There was some debate about whether they had the best solution, but ultimately, it was decided to be better than the one from the homogeneous team. Thus, Parker stresses the importance of having differing opinions, and she tries to implement those opinions in her engineering teams.
Bringing diversity to engineering starts before people attend a university. Unfortunately, convincing young people to study engineering can be a challenge. “We should support and
It’s important to see how engineering contributes to society. We need to show people that developing new technologies makes a difference in people’s lives.
encourage children to pursue their passions, especially if those passions are in math and science,” said Parker. “We’ve often heard that if girls get off the math track in middle school, then it’s over.”
Patching the women-in-engineering pipeline
Parker related a personal experience. Her daughter was in fourth and fifth grade during COVID-19. Prior to the pandemic, she did very well at math — but not so well after returning to the classroom. As a result, Parker’s daughter was pushed to the lower math group. Unconvinced, Parker used her engineering background to advocate for her daughter. That advocacy resulted in her daughter returning to the advanced math class, where she earned straight A’s.
While Parker’s daughter may yet become a third-generation engineer in the footsteps of her mother and grandfather, Parker noted that the engineering community still struggles for diversity more than other STEMbased careers, such as medicine. “When I was in school, about 10% of the class were women.” While that percentage is higher today, Parker noted that it’s still low for electrical and mechanical engineering. She noted that environmental engineering, computer science and industrial engineering fare better. Why?
“I think that with studies such as medical and environmental, you’re
more directly helping people,” responded Parker.
“You can’t develop complex systems without a team of people with different talents,” Parker continued. “The human aspect is there in that you’re developing systems that help people every day. It’s important to see how engineering contributes to society. We need to show people that developing new technologies makes a difference in people’s lives.”
Building an engineering team means hiring the right people, which means you need more than technical talent. “The ability to communicate and articulate your ideas is very important. I didn’t realize that early in my career,” said Parker. “You need to communicate your ideas and work on a team. You need to listen to others.”
When building a team, Parker looks for excitement and passion. “If you come in with that, you’ll want to learn everything that you can. Curiosity in knowing how things work is also important. I look for a natural curiosity.”
Parker was drawn to math, science and engineering at a young age. “I studied hard but enjoyed it. Contributing to society through technology is greatly rewarding. In my case, it’s developing systems for space that improves people’s lives. I’m really proud of that.” DW
Tsu-Jae Liu, recipient of the 2024 IEEE Founders Medal, has left an indelible mark on the engineering field with her leadership in advancing and commercializing nanometer semiconductor technologies and her pursuit of microelectronics workforce development. Also known for coinventing the revolutionary FinFET transistor design, Liu’s contributions extend far within the engineering community. Combined with her continuing academic career at the University of California, Berkeley, we can be sure her colleagues and students deeply feel her dedication and influence.
A career path defined by passion Liu’s first knowledge of engineering came from her father. His degree in electrical engineering connected him to a community of electrical engineers
who, upon emigrating to the U.S., gave the younger Liu the impression that engineers lived comfortable lives and enjoyed their work. It wasn’t until her own college experience, however, that she turned to engineering.
Initially interested in medicine, Liu learned she lacked the stomach for it after touring the anatomy lab at Stanford University’s medical school. However, she knew that engineers designed and built the instruments and technologies that doctors use to diagnose and treat patients. So, making that her inspiration, she earned a B.S., M.S., and Ph.D. in electrical engineering from Stanford University. Afterward, she worked in industry before returning to academia. Presently, she is an IEEE Fellow and both Dean and Roy W. Carlson Professor of Engineering at UC Berkeley’s college of engineering.
Liu’s path to becoming UC Berkeley faculty began with her first job after graduation. Driven by her love of research, she joined the Xerox Palo Alto Research Center, where she was exposed to the emerging industry of flat panel displays. As she’ll tell you, multiple American companies were interested in thought panel display technology, so research and interest in it were growing. They believed that these displays would eventually usurp the use of paper documents. Liu’s place in this research and UC Berkeley’s sustained interest in new and exciting areas of study created the opportunity for her to join the faculty of UC Berkeley’s Department of Electrical Engineering and Computer Sciences (EECS) in 1986. Perfect timing, as the U.S. government decided after that not to continue investing in the research, instead relying on suppliers of flat panel displays from other countries.
Championing diversity and inclusion in engineering
Today, Liu is not only a professor and dean working to create a welcoming environment for her and potential students at her university but also works with the American Semiconductor Academy (ASA) Initiative. The initiative’s purpose is to increase funding and unity among universities and community colleges so they retain more engineering students who, in their careers, will support the needs of a growing semiconductor infrastructure. The idea is for universities to share best practices and curricula, partnering with the semiconductor industry and the U.S. government to develop career pathways at the speed and scale necessary to meet the industry’s growing workforce needs (a need more than double the current output of graduates).
This is a natural extension of Liu’s work at Berkeley, as both stem from her belief that “As we increase the diversity of students and faculty, we don’t see the full benefit of that unless we change the culture to make it more inclusive and make everybody feel like they belong and are valued and respected as part of the community.” In her capacity as Dean and working with the ASA, her priority is to transform the engineering culture to support diversity and growth better. Even within the ASA, she wants any student from any major to feel like they have a path to the semiconductor industry if that’s what they want to do.
Bottom line: Liu wants every one of her students to feel “… like they are welcome and that they would be supported to thrive in [UC Berkeley’s] engineering programs. That’s the most important thing.” She also believes that this feeling shouldn’t end with her students. It should extend to all engineers, even if they don’t want to be engineers.
She explained, “Society is becoming ever more dependent on devices that engineers design and build. It’s good for doctors, lawyers, politicians, or just general citizens to understand and
appreciate technology and engineering.” If nothing else, this line of thinking could greatly benefit the medical field — Liu has witnessed people who majored in engineering but ended up in medicine and have excelled, mainly because of their technical training. But beyond the technical, it is learning analytical thinking, problem-solving, and the ability to work with others that benefit engineers in other fields and leadership roles.
If widely accepted, this attitude would inevitably generate intersectional diversity in the engineering student body and, eventually, many major industries.
Liu’s students want to save the world no matter what field they seek to do it in. Their institution’s job is to make them feel like they can, or at least like they have the resources to. Many of her students are interested in bioengineering/biomedical engineering, environmental engineering, and aerospace engineering because they care about health, ensuring a sustainable planet, space exploration, and occupying the Moon and then Mars, to extend their own lives and those of all humans. The younger generation cares about ensuring the future of humankind, but
Groundbreaking ceremony for the new Engineering Center at UC Berkeley in Berkeley, Calif. on Friday, April 21, 2023. Adam Lau/ Berkeley Engineering
they have to feel what is possible and believe they can do it.
“What motivates students is knowing that what they do is really making a positive difference on people, society, or the planet,” said Liu. This type of motivation and confidence comes from feeling valued, welcomed, and respected — the exact kind of culture Liu seeks to imbue into the engineering community, starting with her own and universities across the country.
In addition to the accolades already mentioned, Liu’s leadership has been recognized by educators and industry with awards such as the Chang-Lin Tien Leadership in Education Award, the SRC Aristotle Award, and the IEEE EDS Education Award for outstanding contributions to education and achievements in diversity and inclusion. So, maybe her opinion is the expert one. With that in mind, here is some last expert advice from her.
“The old way of doing things wasn’t the best way. Just because you’re successful doesn’t mean that continuing to do things the same way will ensure continued success. One thing we as engineering researchers and professionals should realize is that the world is changing.” DW
If you can’t go through, go around
Unwavering effort and dedication to the work at hand helped Christine King defy the odds.
By Lisa Eitel
www.engineering.com/if-you-cant-go-through-go-around
Controls engineer Alicia Lomas discusses tough challenges and lessons learned throughout her extensive career.
By Stephanie Neil
www.engineering.com/engineering-is-reachable-relatable-and-rewarding/
Maurice Stallard’s career shows how embracing technology and diversity can foster engineering success.
By Mary Gannon
www.engineering.com/empower-change-in-production-and-people/
Veteran 3M innovator Hang Loi reflects on her engineering journey and her mission to elevate women in STEM and Asian-American talent.
By Rachael Pasini
Pragmatism combines with passion for the automation industry when Alicia Gilpin is on the scene.
By Lisa Eitel
www.engineering.com/where-fate-talent-and-responsibility-meet/ www.engineering.com/many-irons-in-the-fire-for-engineering/
Bachelor of Science in Electronics Engineering • Xavier University –Ateneo de Cagayan
In 2009, my career in the semiconductor industry began. I was trained in product engineering, circuit design, and applications. I grew from a line-sustaining engineer of highprecision amplifiers and converters to highspeed RF products and eventually transitioned to a pioneering team of product applications engineers developing turn-key applications from ideation to circuit design, PCB layout, and hardware and software evaluation.
I then spent eight years in another company as an automotive product engineer. My key contributions were record-breaking safe launch releases as well as cycle time. Joining Allegro Microsystems in 2023, the newest challenge in my career is my current position as a section manager, with 32 highly competent, talented and enthusiastic engineers in the Manufacturing Product Engineering team where I strive to develop not only the technical competence of my team but also to mentor and foster personal development, sharing my advocacies on project management, lean manufacturing, 5S and financial education.
Talk about the culture at your company.
Being a new mom and a woman in a male-dominated industry, I had concerns that my current situation might be perceived negatively. But during my interviews with Allegro, my apprehensions subsided when I realized the value they place on family and how supportive they were of me in my plan to have a second child. Even having been at Allegro for a little over a year, I’ve observed numerous women and leaders in engineering who have risen through the ranks, having started as operators or technicians. I believe this is a true testament to the inclusive culture at Allegro, not only in regard to gender but also to Allegro's diverse backgrounds as well.
From programs celebrating Women in Allegro to events recognizing diversity as a whole, it feels great to be a part of a company that not only supports but also nurtures DEI.
Describe a recent company project that went particularly well.
One of the KPIs of the manufacturing product engineering team is on-hold lots performance — the team needs to review and provide timely and quality disposition for any lot that goes on hold. When I joined the team, the holds KPI was crimson red. The team dissected the root causes – from the responsible group to the underlying nature of the reasons it went on hold and streamlined the process by identifying hold codes, reasonable cycle times for each and corresponding delegations for the actions needed.
The support of all the teams involved as well as regular reviews and follow-ups to the compliance of the improved business process led to the success of the project. The holds KPI is now neon green and sustained. But on top of achieving the performance metric, is being able to synergize with multifunctional teams to a common goal and serve as a catalyst of positive change.
What first drew you to engineering?
My earliest influence in engineering was my father. He is a civil engineer and as early as I can remember, I would always be amazed at how he fixed and built things. He also introduced me to technology at an early age via a home computer as well as inkjet printers. I remember enjoying the typing test application and eventually, loving Excel and how it makes data and computing so elegant.
My friends and relatives would always go to me whenever they needed to create documents, spreadsheets, or even print stuff and I would happily oblige. It was a joy to be able to help "engineer" things that would make life easier or better. Even now in my current role, whatever work I need to do, I engineer ways to make life (for my internal and external customers) easier and better.
Describe your biggest career challenge.
My biggest career challenge would be the one that I have today — how to be a good manager of engineers.
With 14 years as an engineer, I’ve managed or helped manage many issues, but not other people ... especially not engineers. I know how to improve KPIs, but it’s a different ballgame to improve a team. I’d never say this challenge is solved. However, one of the most important approaches I have learned so far is to be the leader I always wanted to have — and emphasize the importance of not just working as a manager but also serving as a mentor and life coach.
What career advice would you give to your younger self?
Excellent metrics are good for a year, but kind words or gestures can last a lifetime. It’s always better to be kind than right. If you insist on giving your two cents, the right tone makes all the difference.
VISIT EDI ONLINE AND READ THE FULL
Regional Support Engineer
Beckhoff Automation LLC
My journey in engineering was rooted in my childhood in Palestine, inspired by my father’s hands-on approach to problemsolving. He was a self-taught engineer and often involved me in fixing household electronics as well as crafting batterypowered toy cars for our family races.
In school, when my peers had storebought robotic cars, my family couldn’t afford one. Instead, my father crafted a wooden car body, equipped it with batteries, and we built our own remotecontrolled car from scratch. This early experience ignited my passion for engineering. I continued to learn by watching my brothers repair laptops and explore experimental physics through my dad’s library.
My fascination with mathematics was nurtured by my mother, a mathematics competition winner, who would create equations for me to solve – for fun. This early love for problem-solving and technology led me to become the president of my college’s physics club and much more.
Have you benefitted from mentoring or mentorship?
What I love about working at Beckhoff is the collaborative spirit; everyone is eager to help each other out. It’s a culture where mentorship and support are woven into the fabric of our daily work.
How does company culture make it inclusive or supportive of diversity?
At Beckhoff, we really focus on creating an inclusive and supportive environment for everyone. The company is committed to encouraging diversity, especially in engineering fields, through programs such as the Talent Development Program, career fairs, and internships. We’re always looking to bring in fresh perspectives and support individuals from all kinds of backgrounds, including women. It’s great to be part of a company that genuinely values diversity and works to make engineering and automation more accessible to everyone.
Describe your involvement in a project that went well.
One of the standout technologies I was involved in was the support of TwinCAT 3.1 Build 4026. As a core team member, I played a key role in helping both internal teams and customers with the transition to this new version. My work focused on troubleshooting and guiding the migration process, ensuring a smooth shift to TwinCAT 4026. It was incredibly rewarding to see the successful adoption of this technology, knowing that my contributions helped streamline the transition and improve overall user experience.
What strengths do diverse teams bring to engineering or design projects? When people from different experiences come together, we’re able to tackle problems from multiple angles and uncover solutions that might not be immediately obvious. This diversity also helps us better understand and meet the needs of a wide range of users.
What are some of the most impactful ways diverse educational backgrounds advance the field of engineering?
Diverse educational backgrounds significantly advance the field of engineering by bringing a range of perspectives and problem-solving approaches. For instance, someone with a background in arts and humanities might offer unique insights into user experience and design, while those from a more traditional engineering background provide technical expertise. This blend of skills and viewpoints can lead to innovative solutions and more holistic approaches to complex problems. By integrating diverse knowledge and methodologies, we can tackle engineering challenges in new and more effective ways.
I particularly admire robotics specialists. Their ability to integrate complex technologies and create cutting-edge solutions is truly inspiring. Their work pushes the boundaries of what’s possible and drives significant advancements in the field.
If you had unlimited time to apply your engineering background, what global challenges would you tackle?
Every day, I am profoundly inspired by the extraordinary resourcefulness of children living in conflict zones. Despite the harsh realities of war, young innovators demonstrate a remarkable ability to turn basic materials into life-improving solutions. They ingeniously generate electricity, filter water, charge their phones, create cooking stoves, and even build games from seemingly nothing. Their creativity and resilience reveal the transformative power of engineering, especially in the face of adversity. If I had unlimited time to dedicate to my engineering background, I would focus on improving the lives of children affected by conflict. My vision would be to develop innovative and sustainable solutions that provide safe living conditions and essential support in these dire situations.
scan the qr code for more from dareen awwad on being an engineer
In 2018, DigiKey founded the Northwest Minnesota chapter of Women in Electronics (WE), a community of women in the electronics industry committed to working collaboratively with their male counterparts to advance opportunities for women in electronics and related industries. Since then, membership and participation have continued to grow within DigiKey, bringing increased networking and learning opportunities.
Team members at DigiKey’s headquarters face the unique hurdle of being tucked away in the northwest corner of Minnesota. Being far removed from other tech hubs makes it harder for the team to attend industry networking events and speaker sessions and participate in crossbusiness mentorship programs, which is why the WE chapter has been such an important initiative.
The Thief River Falls chapter of WE is a dynamic group that supports its members in various ways. The chapter offers monthly training, which has helped many feel more confident in their communications and empowered to express their ideas.
The mentorship program has also been an invaluable resource for many. It connects women in different roles and stages in their careers and promotes collaboration, support, and career development opportunities. It’s become a place for many to feel safe and discuss challenges with someone with an outside perspective. Furthermore, it has opened doors previously unavailable to many. Some employees, once mentees, are now looking to become mentors and help encourage the next generation of women in tech.
Talk about the culture at your company. What makes it inclusive or supportive of diversity in engineering and automation?
The responsibility of being a major local employer is not lost on leadership, and this WE investment is an initiative paying dividends for the broader community. Women in Electronics provides access to learning and development resources that we can utilize on-site and share with anyone in our local community who desires access to experts, tools and support to empower and develop women leaders in the workplace.
The DigiKey culture wholeheartedly believes that diverse teams are critical to a business’s success because they broaden perspectives on any initiative or idea. There are many research-proven reasons why diverse teams lead to better business results.
Beyond stronger financial returns, diverse teams increase access to better talent, more effective problem-solving, superior innovation, stronger retention and more relevant solutions for end customers.
Our industry is very forward-looking and thinking, but it’s also a very mature industry, especially at the leadership level. In the next decade, there will be a high turnover rate in the industry due to aging leadership. We need to build that bench for the future of the industry so that we can continue to grow and transform.
With the ongoing competition for talent, addressing this talent reservoir is critical for our ongoing sustainability. Our partnership with Women in Electronics provides a platform to talk about those challenges and promote the need for change within the industry.
Bachelor of Science - Electrical Engineering • University of Wisconsin - Milwaukee
Most of my career has been dedicated to technical sales, where I’ve specialized in navigating customer applications to deeply understand their challenges and goals. My focus has always been on providing tailored solutions that effectively address these challenges and help customers achieve their objectives. Additionally, I spent a period in product marketing, bringing my sales-driven perspective to the marketing team, which enriched my understanding of the product lifecycle and enhanced crossfunctional collaboration.
Talk about the culture at your company.
There is an unwavering commitment to diversity and inclusion. Our CEO consistently emphasizes the importance of fostering a more inclusive environment and actively encourages each of us to contribute to this goal. We have a variety of internal initiatives dedicated to this cause, including efforts to increase the representation of women in our industry, create opportunities for individuals with disabilities, and engage meaningfully with our communities. Our recruiting team is exceptional in their commitment to broadening our talent pool by actively seeking out and engaging with underrepresented groups. Thus we are able to attract top talent from a wide range of backgrounds.
Describe a recent company project that went particularly well. This past year, I was part of an exciting annual project within our organization. We bring together individuals from marketing, sales, manufacturing, and more — and from different regions across North America — to collaborate. We form teams to brainstorm, then go through a selection process to refine our ideas. A final vote determines which ideas will be brought to market. The key to our success is a shared commitment to making things better and easier for our customers.
Describe a pivotal career challenge.
During my college engineering co-op at a local manufacturing facility, I found myself unexpectedly in charge when my manager went on vacation. That day, he received a call from a sister plant where the glue line was down, and he instructed me to go fix the problem. I was just a college student studying electrical engineering, with limited experience in programming and manufacturing lines. I arrived at the plant where boxes were passing through the glue station without any glue being dispensed. I plugged in my laptop, took a deep breath, and began analyzing the code, grateful for the comments left by the programmer. As I reviewed the logic rung by rung, I found an issue — the rung that was supposed to activate the glue dispenser wouldn’t trigger due to a logical error. I fixed the code, redownloaded the program, and handed control back to the operator. In what felt like slow motion, I watched as the first box passed through the gluing station and emerged perfectly glued. I couldn’t believe it — I had just fixed my first manufacturing line.
Leaving the plant that day, I had a huge smile on my face and my head held high. That moment marked a turning point for me, as I realized that with determination and problem-solving skills, I could overcome any challenge thrown my way.
Have you benefitted from mentoring or mentorship?
My father has always been my greatest inspiration. Despite facing significant challenges, including having to drop out of college to work full-time and support himself, he never gave up on his dreams. He began working at a young age yet as an adult found his job opportunities limited without a degree. So, when my siblings and I were young, he made the courageous decision to return to college while still working full-time. This determination and sacrifice left a lasting impact on me.
From a young age, I remember him telling me to find something I love so it would become more than just a job — it would be a fulfilling career. His relentless perseverance and the sacrifices he made for our family have shaped my values and drive. While I haven’t had the official title of mentor, I’ve been fortunate to assist high school students with their Project Lead The Way tasks and coach sports through our local park district. Through these experiences, I hope to inspire the next generation, just as my father inspired me.