
10 minute read
MAKERBOT


Working with stainless steel


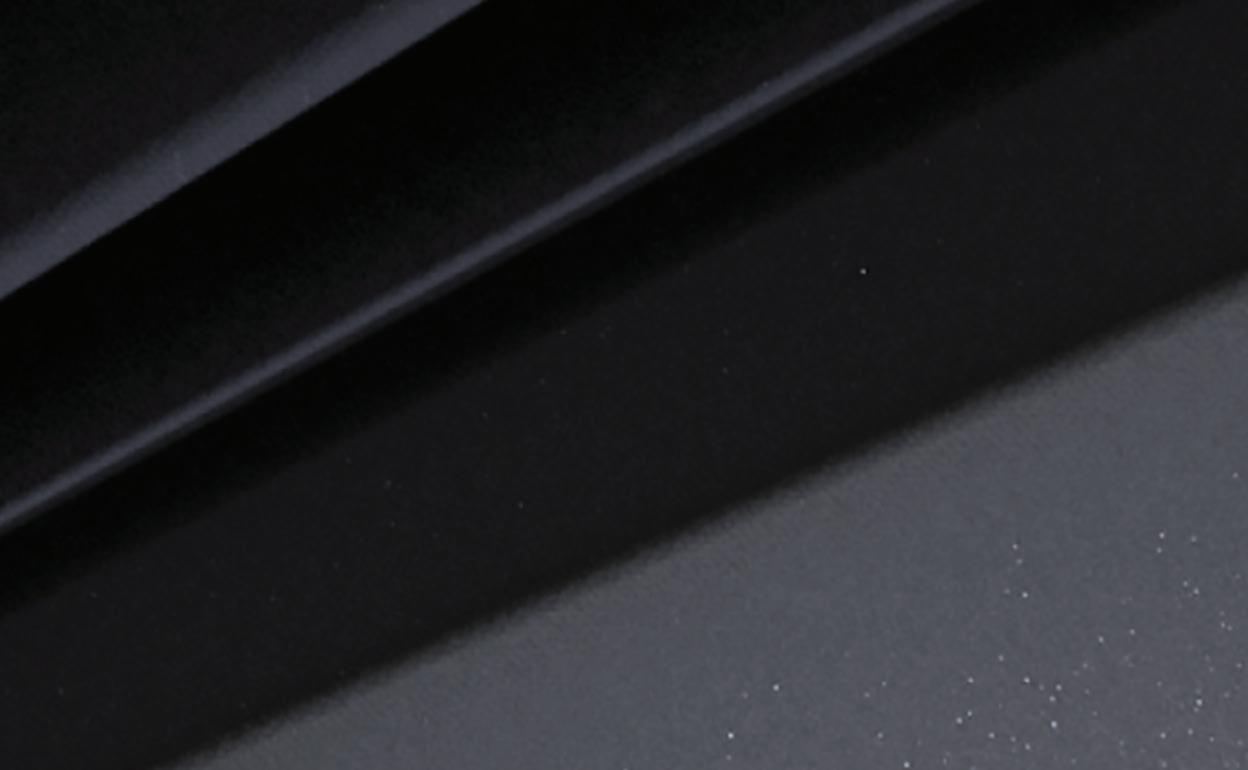
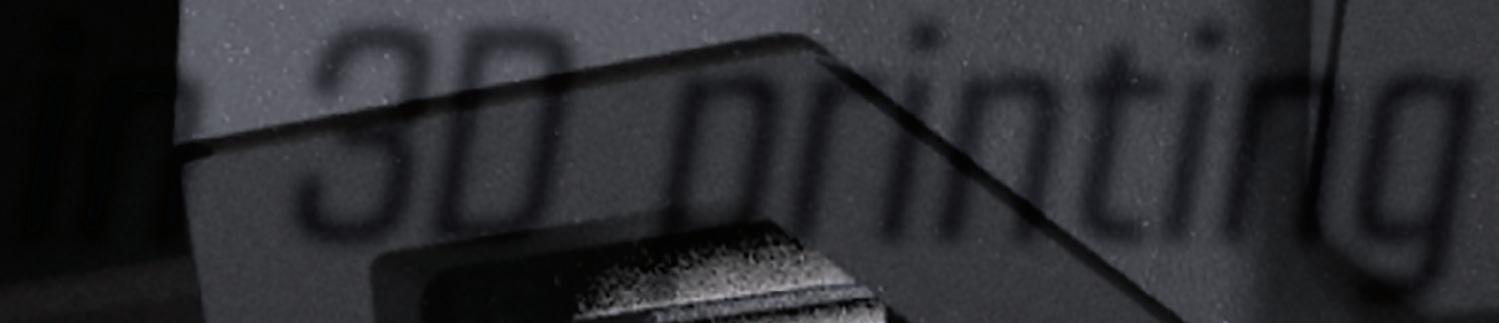
in 3D printing
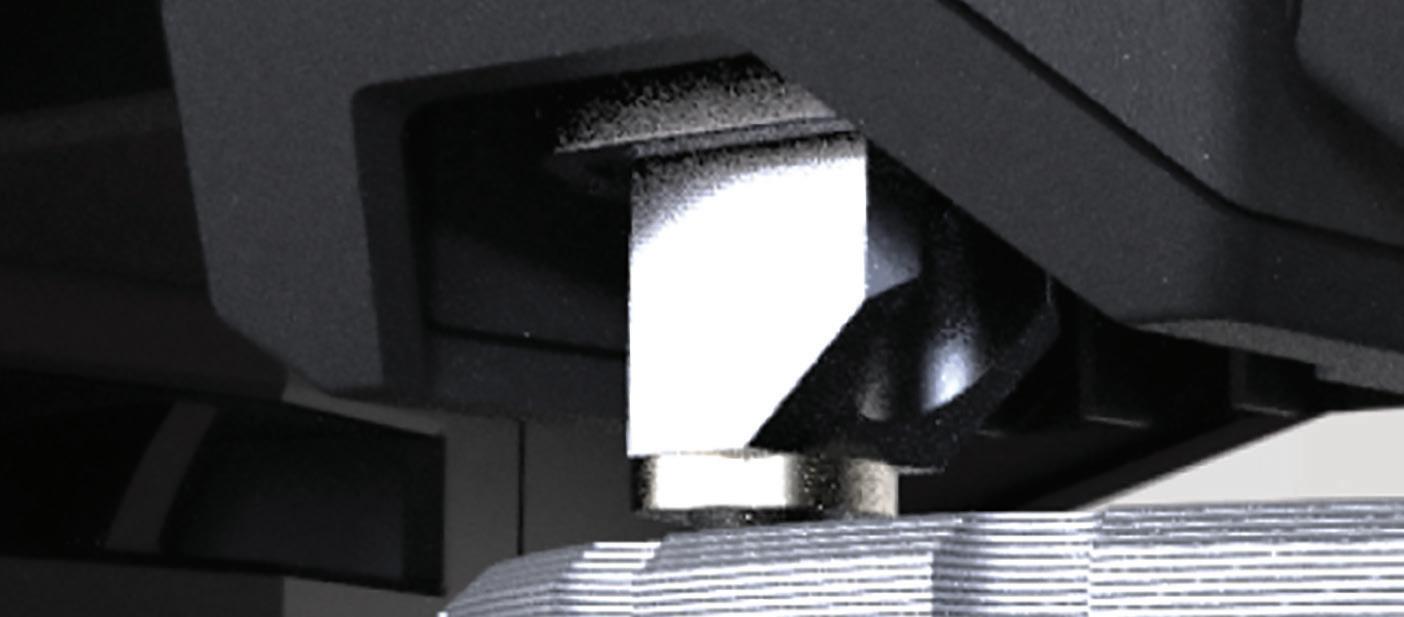
COMPANY MACHINE NAME BUILD SIZE BUILD MATERIALS
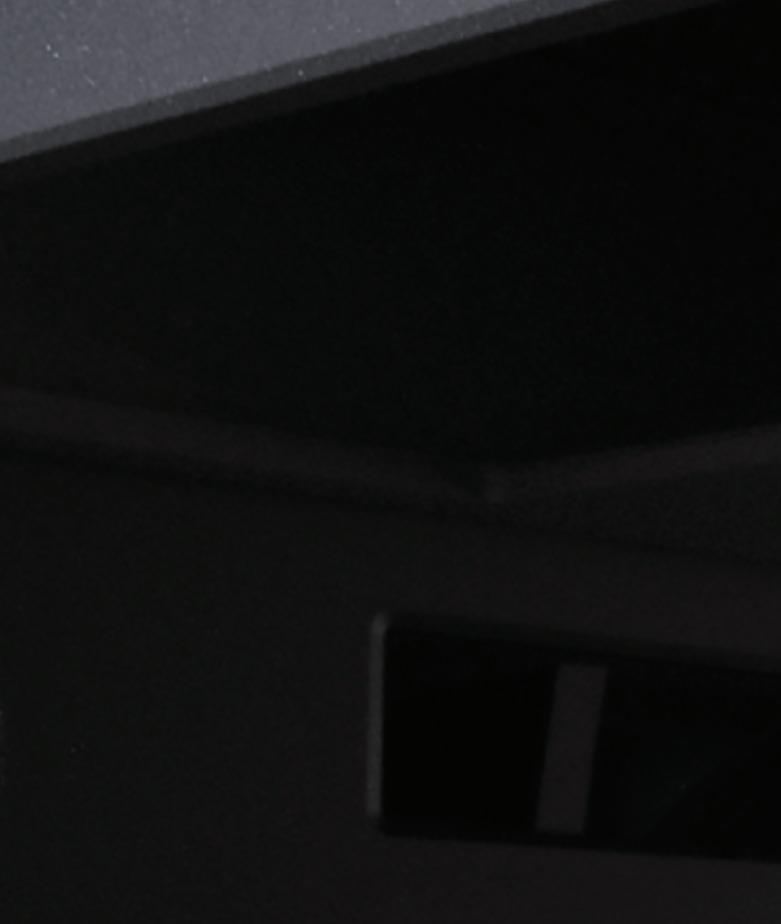
MakerBot
METHOD X
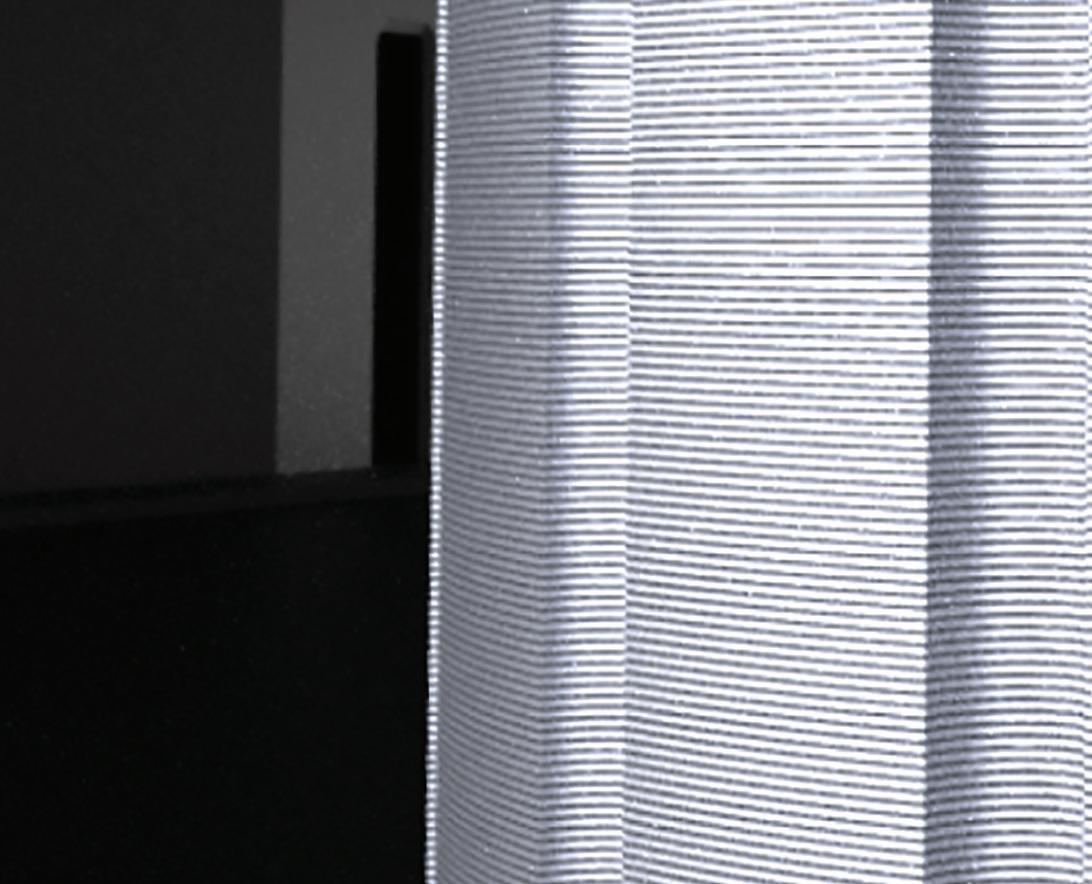
METHOD
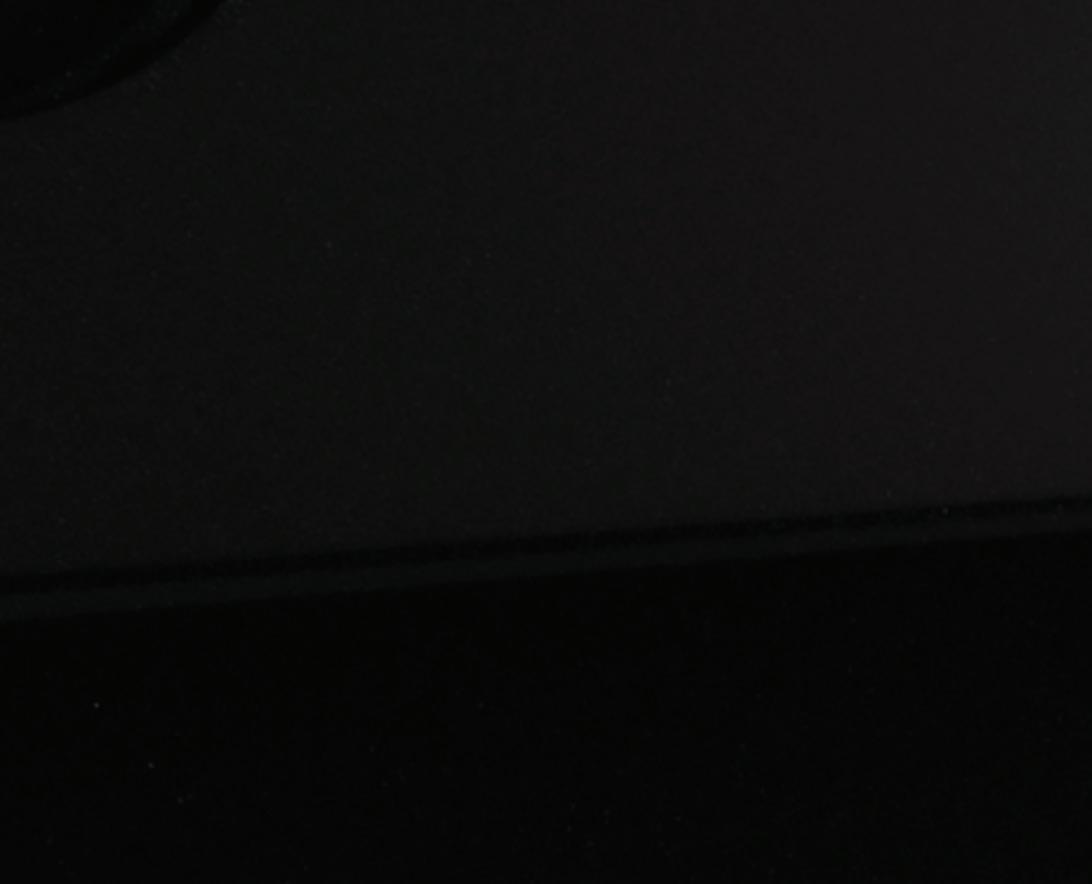
METHOD Carbon Fiber Edition 6 x 7.5 x 7.75 in (dual extrusion)
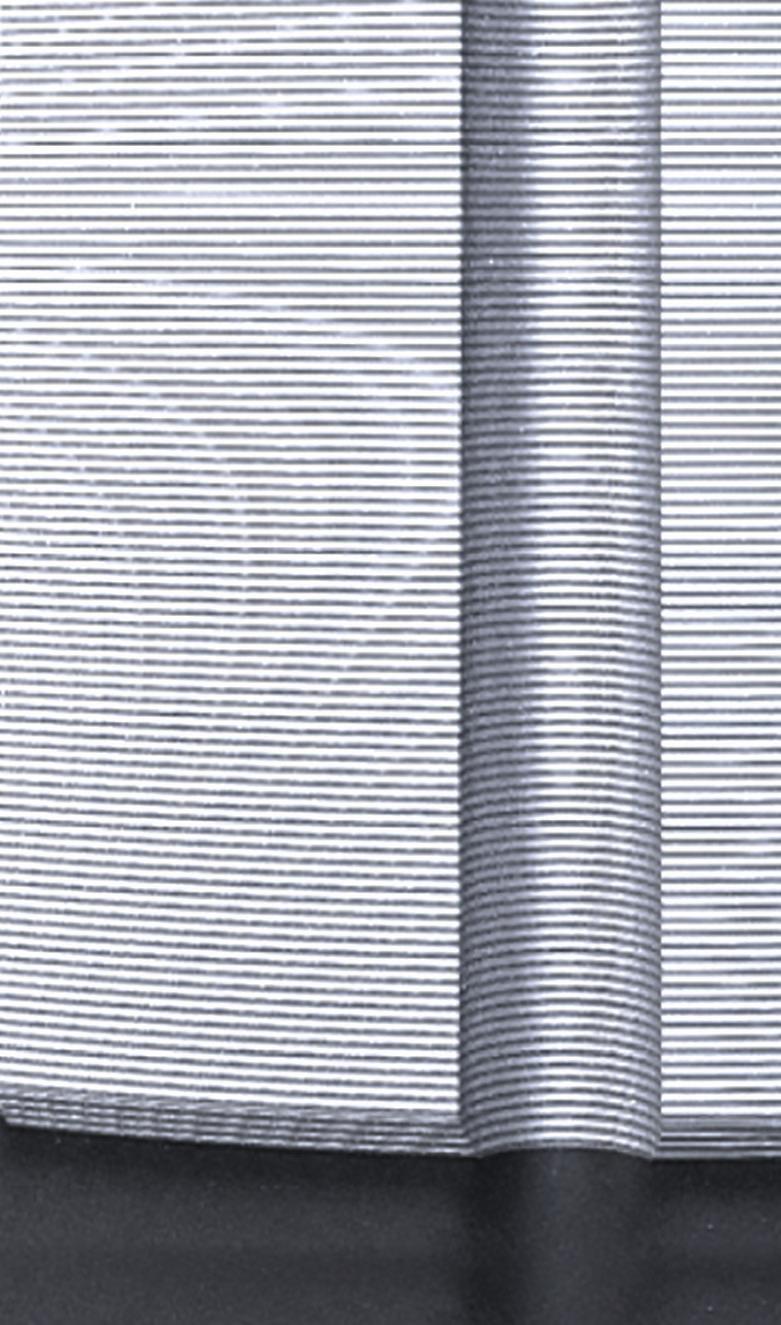
7.5 x 7.5 x 7.75 in (single extrusion)
For METHOD and METHOD Carbon Fiber Edition:
Model Materials: PLA, Nylon,Tough, PETG, PETG ESD, SEBS 95A, Nylon Carbon Fiber, Nylon 12 Carbon Fiber, 316L stainless steel Support Material: PVA
For METHOD X and METHOD X Carbon Fiber Edition:
Model Materials: PLA, Nylon, Tough, PETG, PETG ESD, SEBS 95A, ABS, ABS ESD, ABS EC, ASA, PC-ABS, PC-ABS FR, PC-PBT, PolyLite, PolyMax PC, PolyMax FR, Durabio, Nylon Carbon Fiber, Nylon 12 Carbon Fiber, PETG Carbon Fiber, ABS Carbon, ABS Kevlar, 316L stainless steel Support Materials: PVA, SR-30
LAYER THICKNESS BUILD SPEED
20 - 400 microns 0.2 mm or ± 0.002 mm per mm of travel
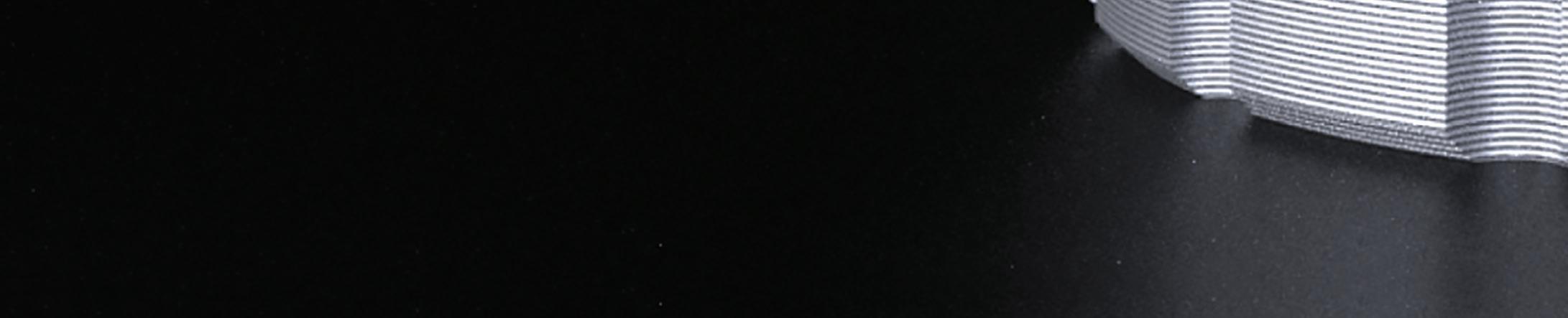
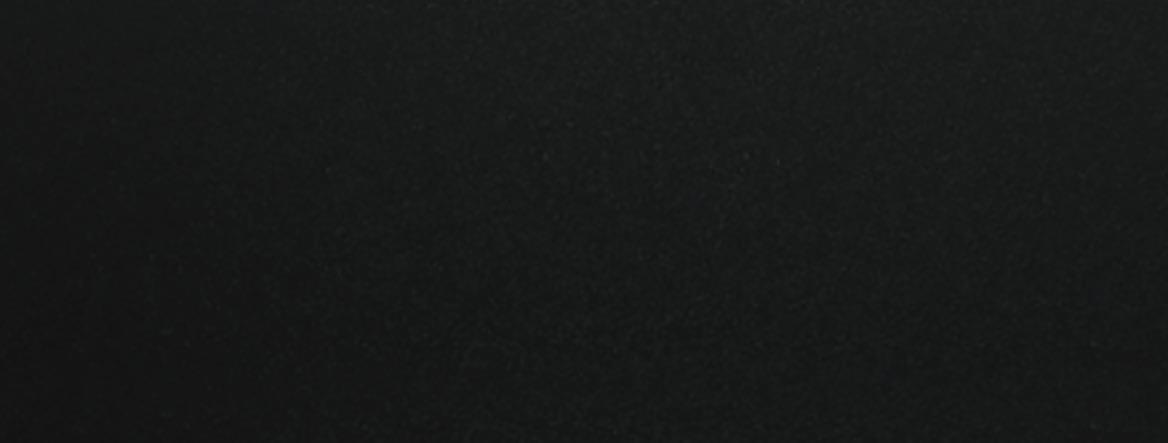
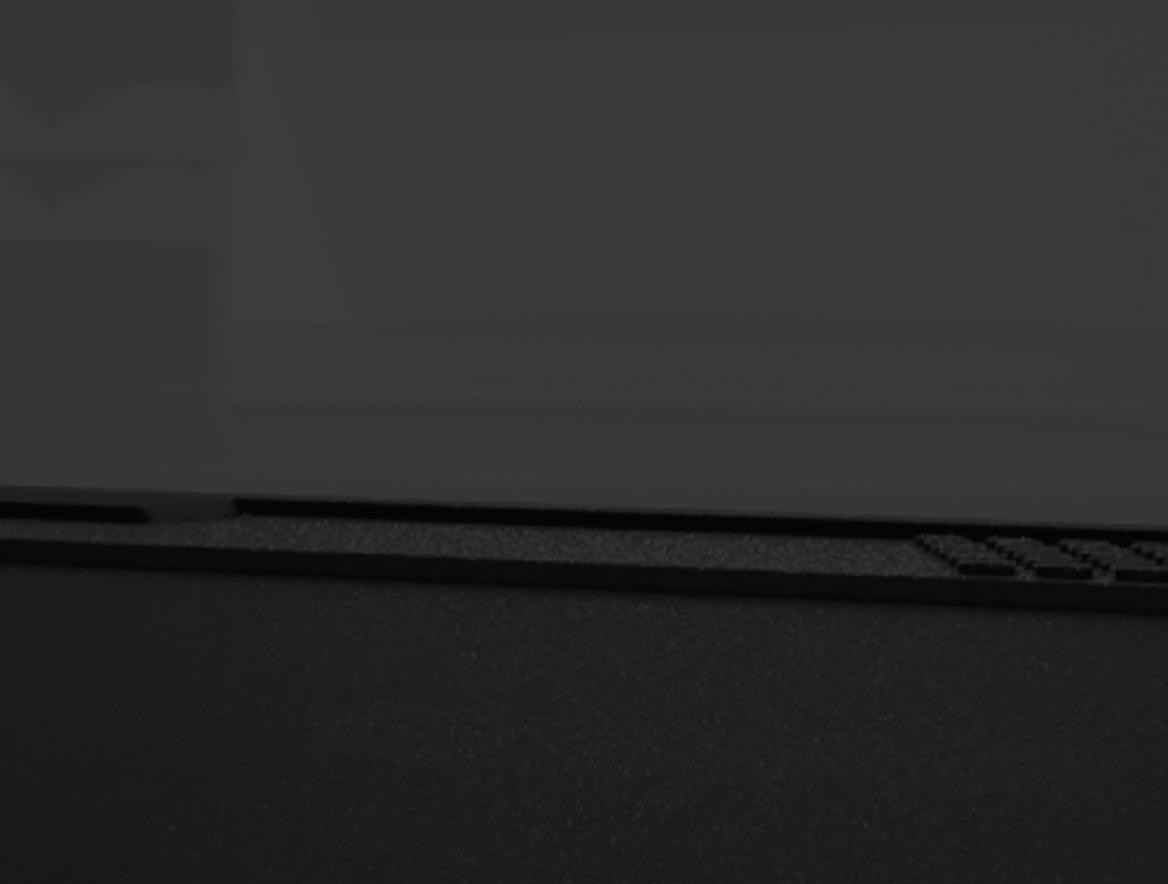
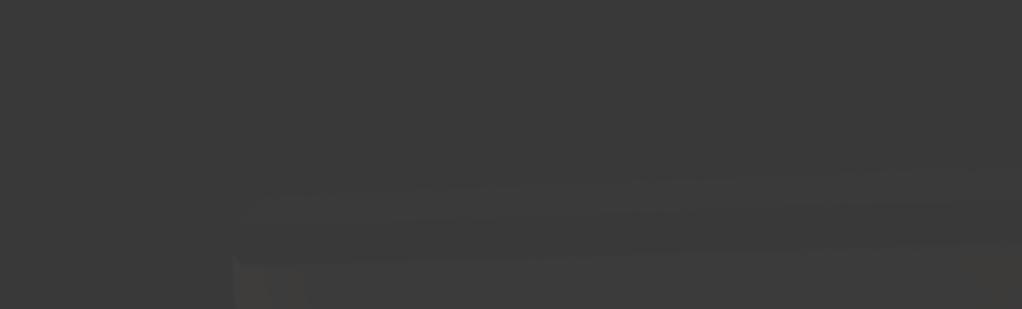
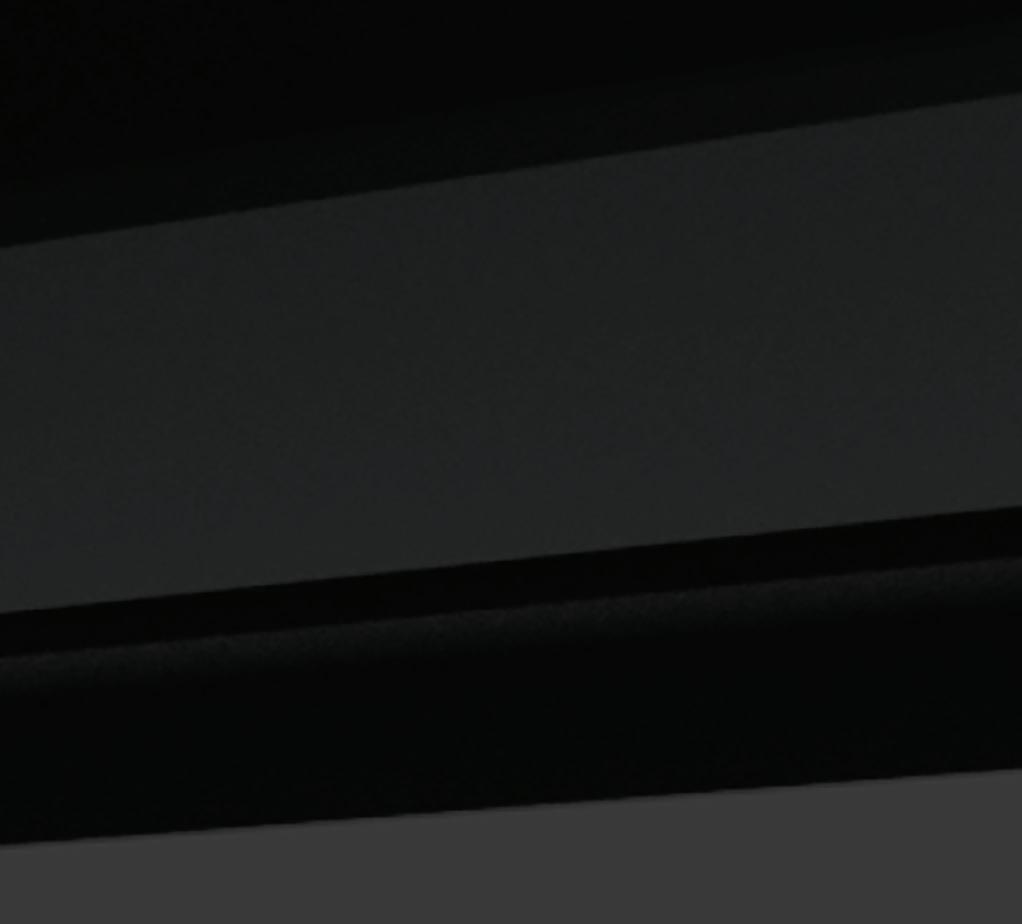
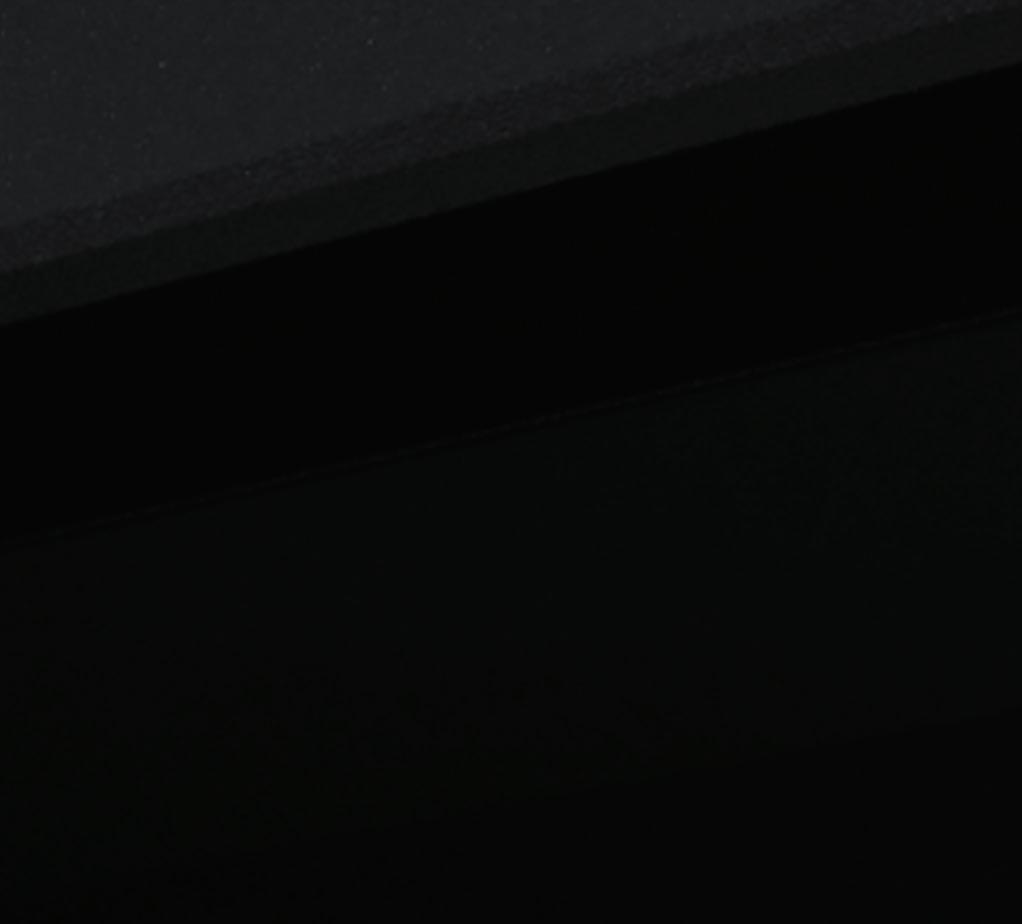
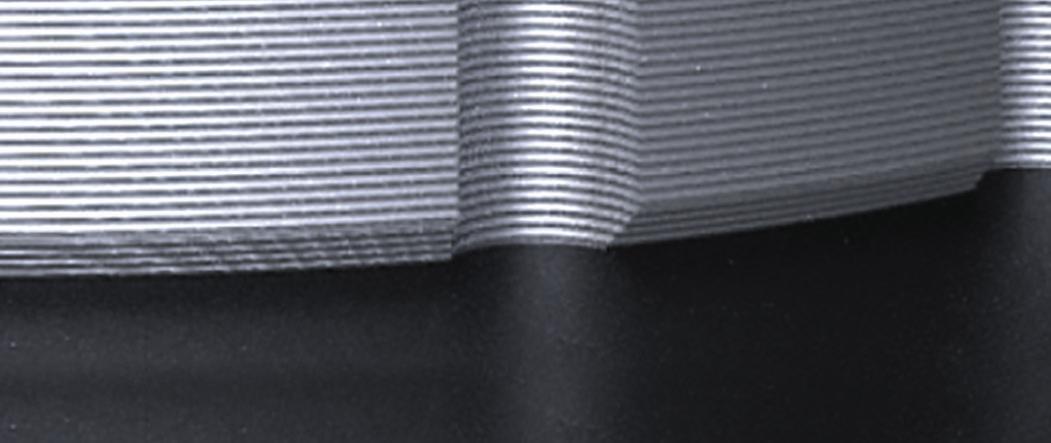
More 3D printing vendors are introducing metal materials for their systems. One popular metal in particular is stainless steel. This material offers a number of benefits to designers. We interviewed Felipe Castaneda, Creative Director at MakerBot, on ways to make the most of it in your designs for 3D printing. Here are key points of the interview.
Software tools
Generative design software will be an important tool in designing with many materials, including stainless steel. When working with this software, it is important to understand the problem you’re working on thoroughly. The goal of generative design is to get as many answers from the computer as possible, to expand the possibilities of what your design will look like. But to do that, you first need a really good grasp of what the problem is in order to form the right questions for the computer to answer. Fortunately, computers are still not as smart as engineers. So, computers are not able to create the questions themselves. You will get answers from computers, but if you don’t phrase the problem appropriately, the answers might not even be relevant. With the nearly infinite processing compute power of computers, it’s a good challenge to first frame the problem of any design. What aspect of the design are you looking for the computer to improve on? Are you trying to enhance a part’s structural properties? Are you trying to enhance the way that it will be made, and so on? Different problems will come up with different solutions, and in that lies the value of the designer to translate that problem into something that the algorithm can react to. “There are multiple approaches to what we would call generative design,” notes Castaneda. “Traditionally it’s been more about the geometries, … but there are places where the generative design will be focused not on creating something complex, but rather on giving you a lot of options. Let’s say, if I have a wrench printed using a mix of carbon fiber and 316L, I could be asking the program to generate, say multiple lengths of the wrench, or multiple sizes for the interfacing bolt in the wrench, different patterns here to be followed and to be created, so that it has a different grip against the user’s hand. So, it varies a lot.”
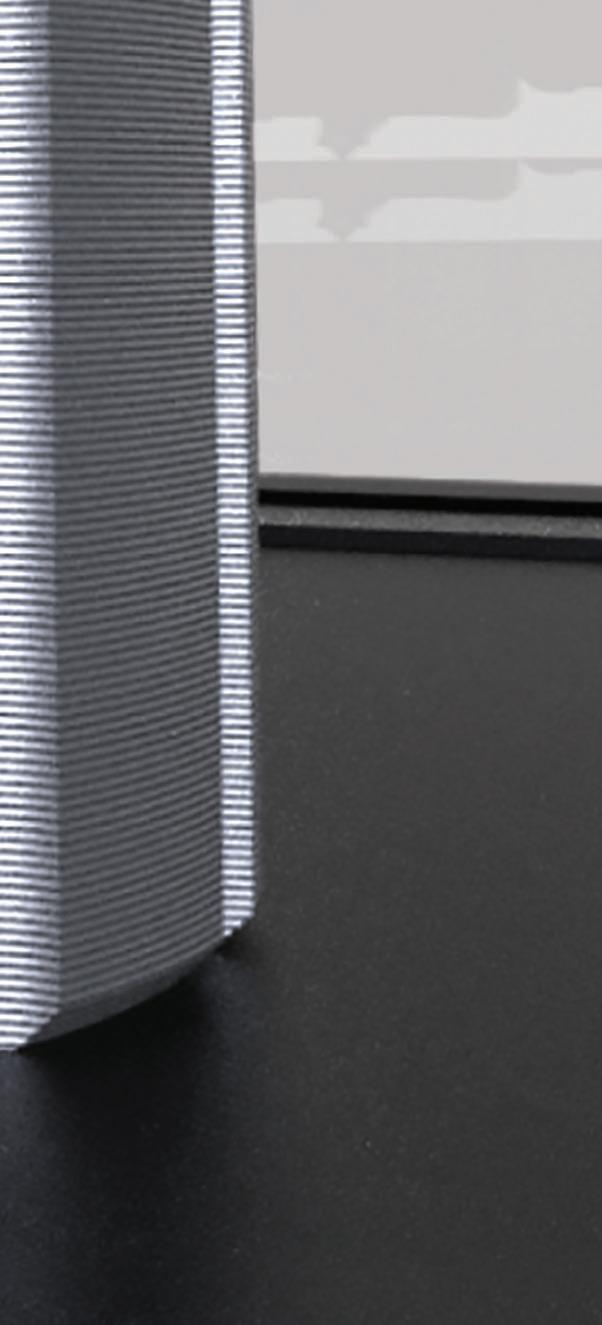
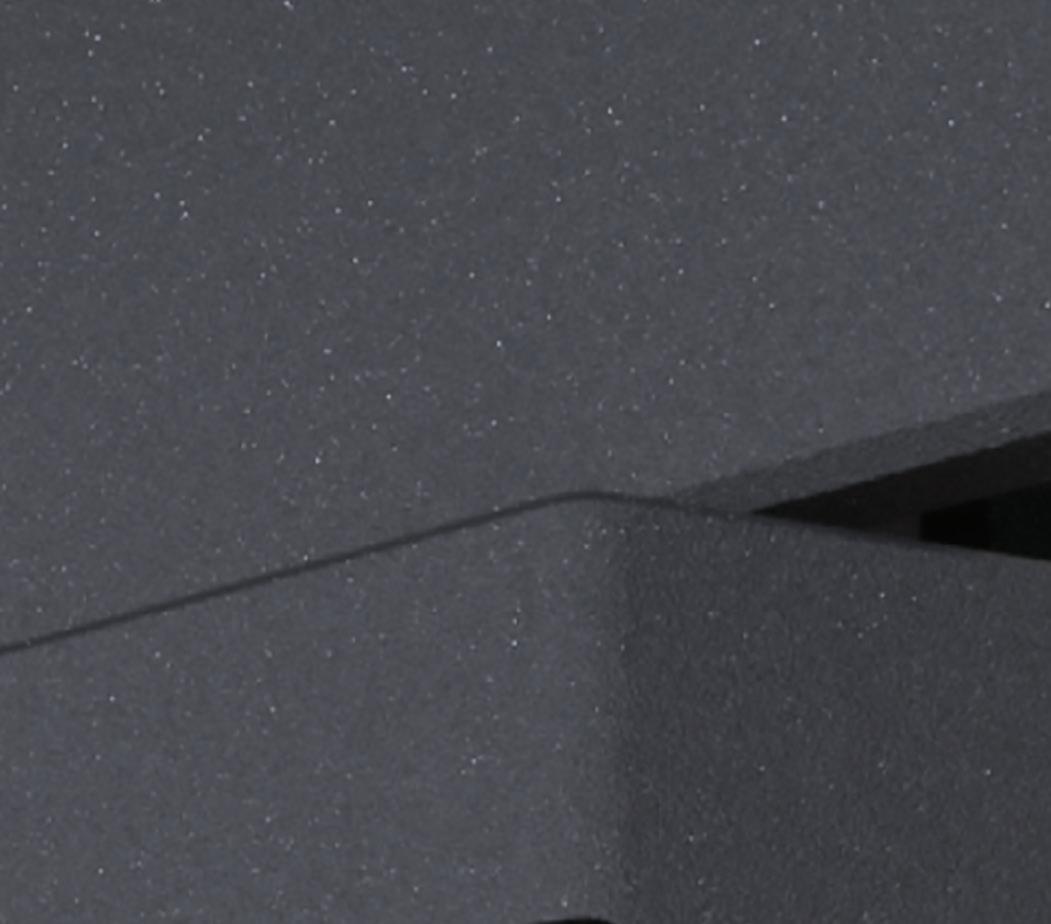
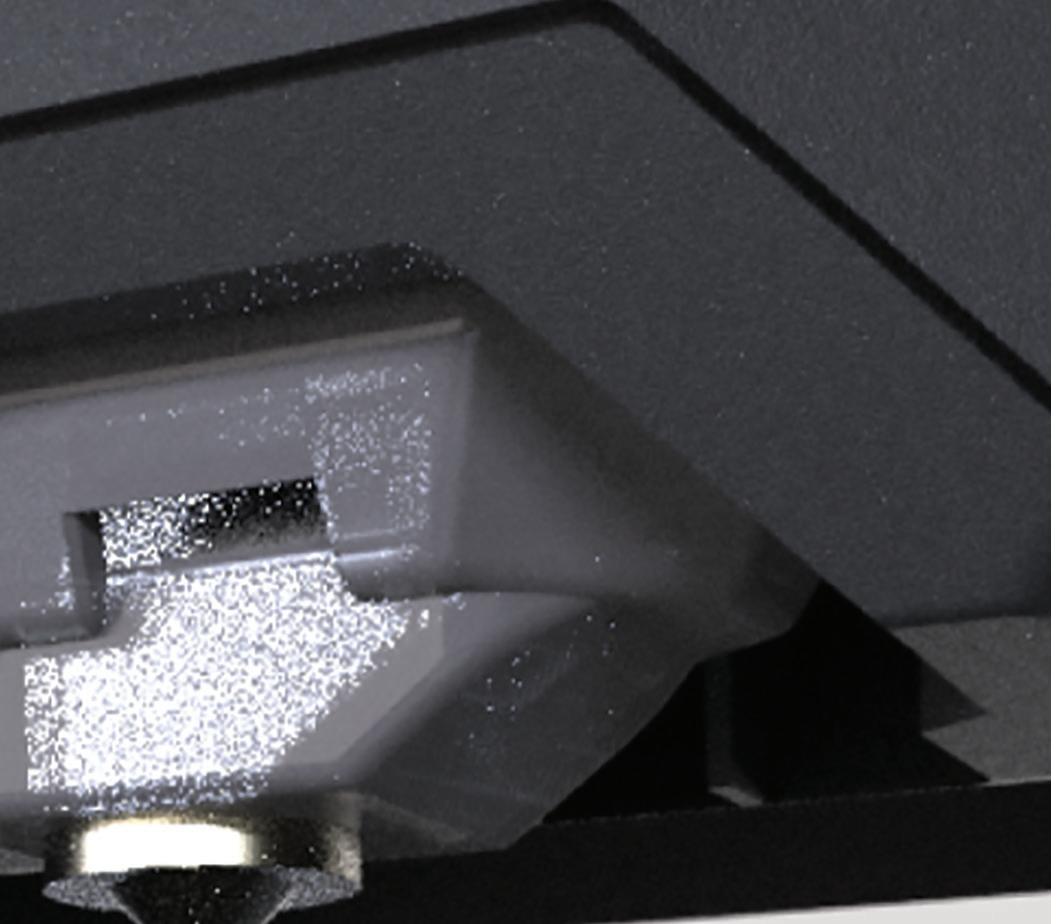
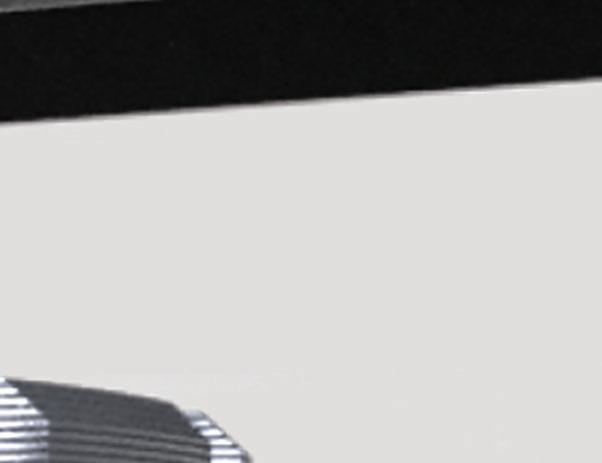




The tips of the gripper claw are made out of the 316L material because the claw is subject to the most wear and
tear as it holds items. Notice the pattern on the inside of the gripper claw. This pattern was created using generative design programs, but it takes the ability of additive manufacturing to make the pattern.
Materials
More vendors are offering a stainless-steel material for use with their 3D printers. What are the benefits of this material?
According to Castaneda, this material gives you the ability to create robust, sturdy parts that are challenging to make using other manufacturing methods. There are certain geometries that you would not be able to generate in any other way with stainless steel than by using 3D printing. Being able to create these complex geometries enables you to ultimately achieve the shape and form that you want. “Specifically,” says Castaneda, “this material is, in some cases, 20 to 50 times as strong as our next strongest composite or polymer. So, its physical properties are rather remarkable.”
“I’ve been using it for quite a range of applications,” says Castaneda, “starting from creating grippers. In this case, we are working on developing what essentially is a robotic gripper. It’s going to be actuated by a NEMA 17 motor, so a pretty standard stepper motor. The tips of the gripper claw are made out of the 316L material. Those tips are going to be the element of the assembly that will be subject to the most wear and tear as it holds items. That’s why we chose to use metal in this case.
“And the reason we used 3D printing as opposed to any other machining method, is that we have some complicated geometries that would not be able to be manufactured in any other way, such as machining or grinding. There’s a little pattern inside of the tips of the claw, in the concave elements. We created that pattern using generative design.
“The 316L material allows us to have a much stronger part only in the section that will be subject to the most wear. The rest of the assembly is made out of nylon and carbon fiber. It’s also 3D printed, but we are focused on lightweighting that part of the design. So, we are applying the material where it’s most valuable. In this case, the part, the section of the part that has the most wear and tear, will be having the stronger material applied to it.
“If we were to print this whole assembly out of stainless steel, which is definitely possible, these would probably end up weighing a good three, five pounds, for a gripper that’s about the size of my hand, right? So that might be just too much for any robot to carry around. However, if I can reduce the weight on the less structural parts of the gripper
and use, in this case, the carbon fiber composite, and just get those tips out of metal, then I’m getting the best of both worlds. I’m getting the sturdy, the rigidity of the metal on the tapers themselves, and the lightweight component, and the stiffness of the carbon fiber on the rest of it.”
You can achieve greater detail, both created from a generative design program and into the geometric shape, than you could have with traditional machining methods.
“We’ve seen stainless steel in medical applications and some other devices,” notes Castaneda. “I have another good example here, it’s basically just a lattice. This is more of a proof of concept of what could be done and pushing the requirements of the process itself, the 3D printing plus sintering process later on. But yeah, these types of geometries are not something that you would be able to create following any other traditional manufacturing method. And that’s where the mix of 3D printing with 316L makes it a rather handy tool to have it at your disposal.
Of course, there are limitations when working with any material. For the Method 3D printer, limitations include the size of the parts that you can create. Specifically, you will be bound by a 100 x 100 x 100 mm box; about 4 in.3. However, the limitation comes not from the printer, but rather from the sintering process itself.
When you send your part out, there are specific additional steps to be taken after the part has been printed from your machine. Once you get the part out of the printer, you’ll get what we call a green part. The green part has this kind of clay like feel to it. It’s rather dense, but that’s not the final shape of the part, or the final expression of the part. You will have to de-bind and then sinter this part. Those steps create the stainless-steel part that you will be using later on.
“What MakerBot does,” notes Castaneda, “is allow users to print the part themselves, which already saves time and money. And then, once they have the green part, they just send it out to a processing facility. The facility heats up the part, and returns a fully, solid stainless-steel part to the user.”
For Method printers, the stainless-steel material comes as a filament in a spool. This filament is a richer metal. Other filaments usually have a mix of 30% of the metal and 70% of the plastic-- the binding agent that keeps it all together during printing. MakerBot’s material is closer to an 80/20 mix. That’s why the parts are rather dense. The filament is not brittle, but it has a clay-like quality to it. It will not bend. If you flex it enough, it snaps. A spool of an average filament would weigh about one kilogram. The MakerBot stainless steel spool weighs about three kilograms, or about six pounds.
The spool is convenient for working with metal, plus it makes it easy to switch out materials quickly and cleanly.
Once you have sent out the part for de-binding, removing that excess 20% binding agent tends to shrink the part size. “It’ll shrink a little bit and it’s going to shrink unevenly,” says Castaneda. “It’s going to shrink about 20% on the X and Y axis, and 26% on the Z axis.” The height skrinkage is due to the weight of the part itself. The weight of the part on itself will shrink a bit more vertically than horizontally.
Whether in powder for filament form, stainless steel will help people to come up with better solutions, more interesting solutions and ultimately expand the size of the market.
MakerBot | www.makerbot.com
make metal parts through additive extrusion
Early in the history of additive manufacturing, working with metal was a challenge. The metal material was usually converted to a powder, which, depending on the metal chosen, tended to be easily explosive. Additive systems used special equipment to move metal powder in and out of the machine, and special atmospheres to eliminate the possibility of the powder igniting.
Since those early days, additive vendors have found ways to combine metal powder with a binder (often a carbon fiber, plastic binder, fiberglass, or Kevlar) and form a safer to handle material composite. The amount of binder combined with the metal varies from 30 to 70%, depending on the metal and the application for the composite material. This composite material can then be shaped into rods, and more recently filament, that can be used in less expensive additive machines that use extrusion to build parts a layer at a time. The filament is not brittle, but it has a clay-like quality to it. It will not bend. If you flex it enough, however, it snaps.
The rods or filament are fed into the printer’s extruder nozzle, which melts the composite material to a point where it can be easily deposited in a layer-bylayer build process.
Once the part is built, it is removed from the build plate and usually must undergo a second operation, known as sintering. Sintering uses high heat, a temperature less than the melting temperature of the composite, to remove the binding material used to make the composite. The end result is a fully dense (99.7%) metal part.