
8 minute read
DESKTOP METAL
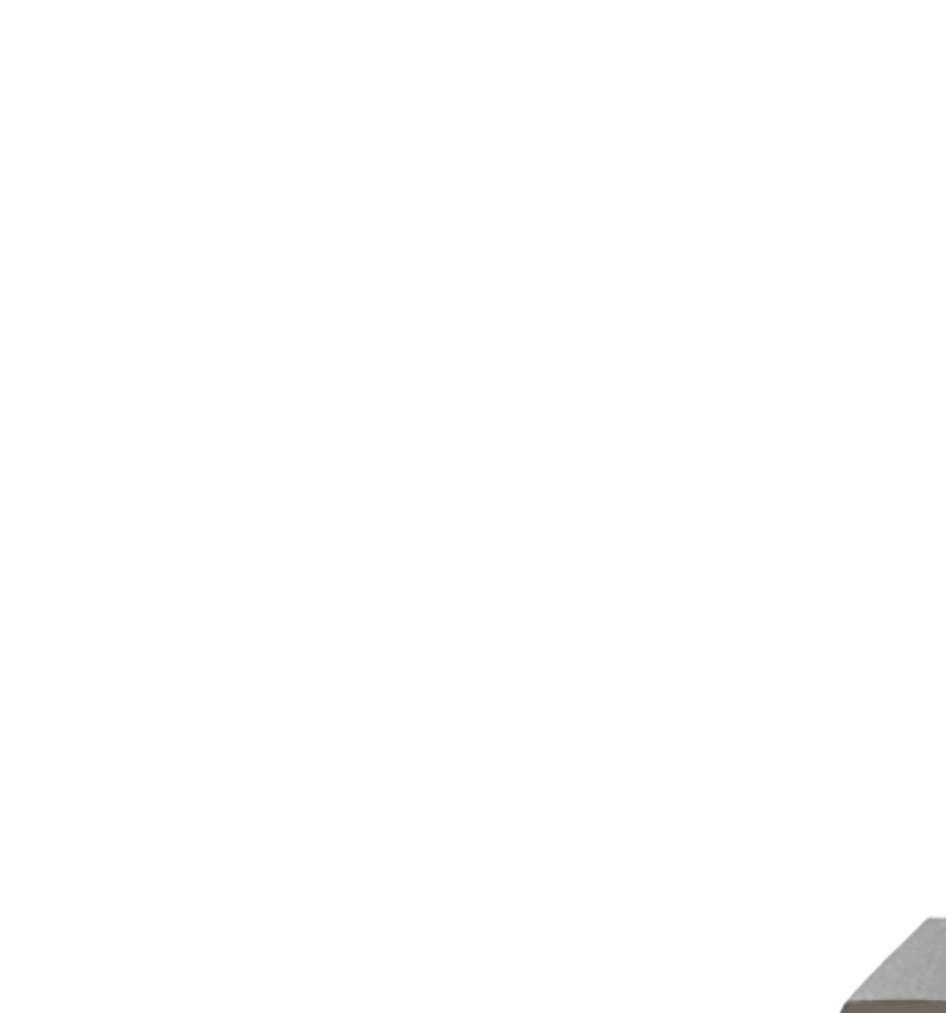
Signs of a maturing technology
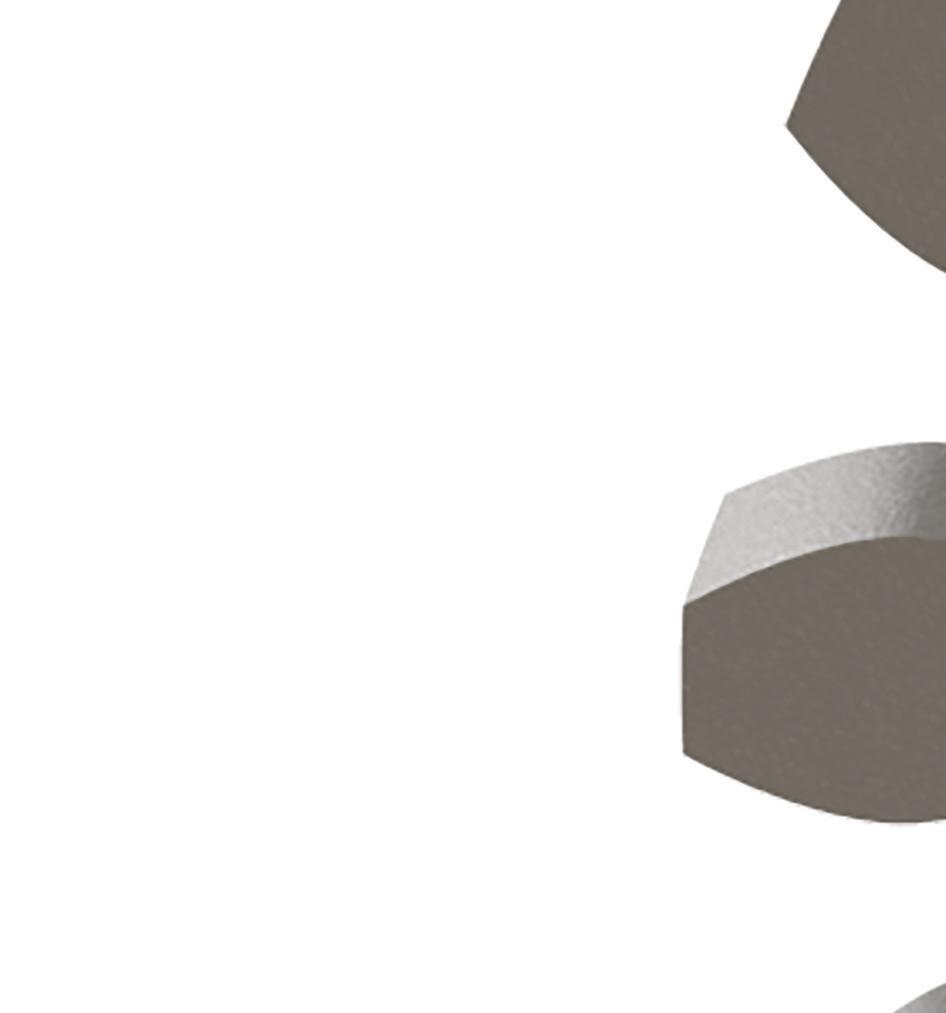
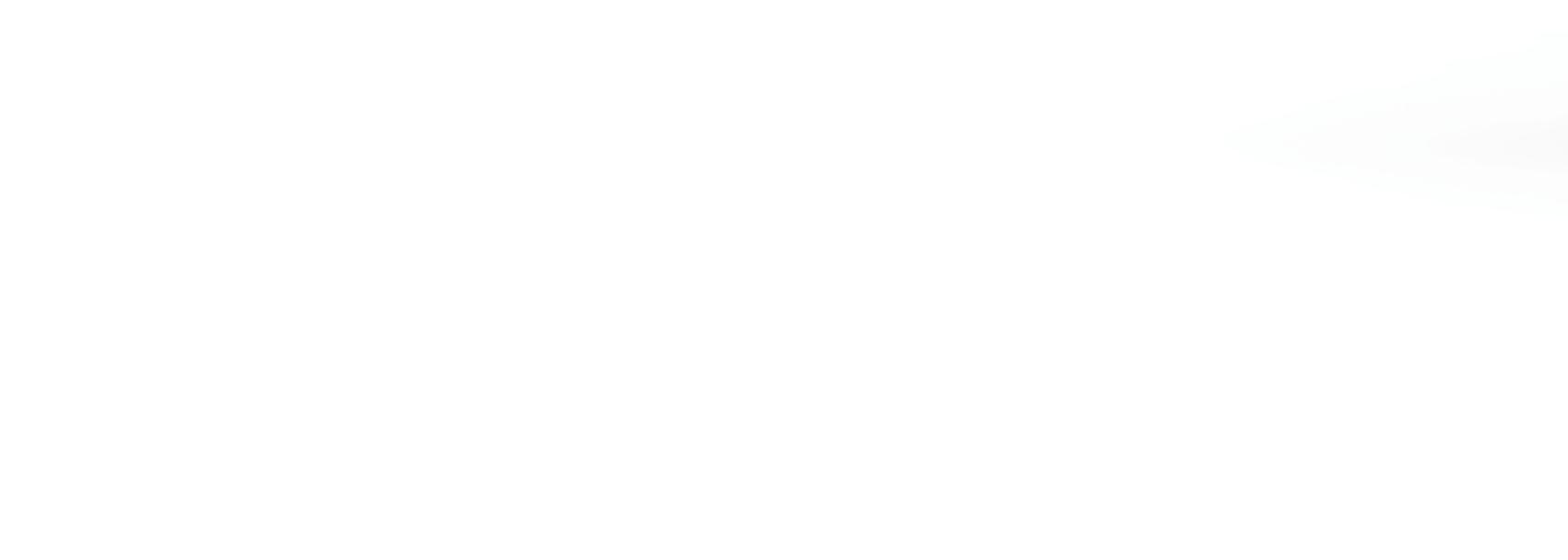

The end of the year 2020 saw Desktop
Metal go public. Using a Special Purpose Acquisition Company (SPAC), the company is now listed on the New York Stock Exchange. That was just the beginning of roughly twelve months of product and materials introductions and acquisitions. The company announced the P-1 printer began global shipments and joins the Production System lineup alongside the flagship P-50 printer. Designed to serve as a bridge from process development to full-scale mass production of end-use metal parts, the P-1 leverages the Single Pass Jetting (SPJ) technology and core additive manufacturing benefits for companies and research institutions alike at the size and scale of serial production. The P-1 offers a form factor to bridge the gap between benchtop process development and mass production, leveraging the same SPJ technology and print carriage design as on the P-50 but with enhanced process flexibility. Also similar to the P-50, the P-1 features a state-of-the-art print bar with native 1200 dpi, printhead technology that supports a variety of binders, and an inert processing environment to support both non-reactive and reactive materials. As a result, materials research and new application development conducted on the P-1 can be transferred directly onto the P-50 to scale. SPJ technology on the P-1 prints a layer in less than three seconds, including powder deposition, powder compaction, anti-ballistics, binder deposition, and printhead cleaning. At this maximum build rate, the P-1 can achieve production throughputs 10 times higher than those of legacy powder bed fusion systems and fast enough to complete a full build in less than one hour. The P-1’s open material platform and inert process environment allow customers to use low-cost, third-party metal injection molding powders across
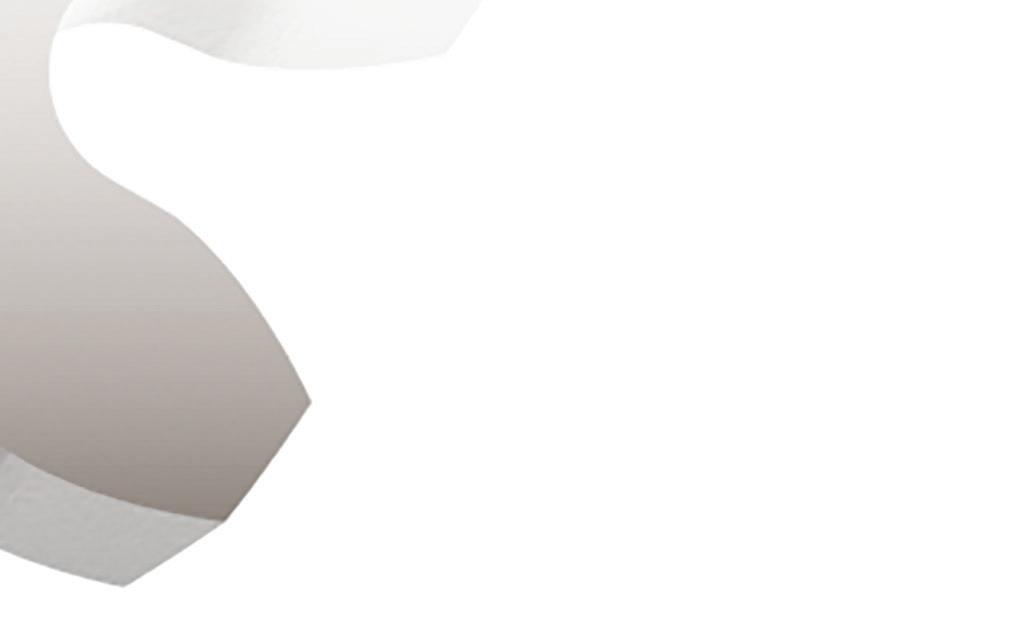
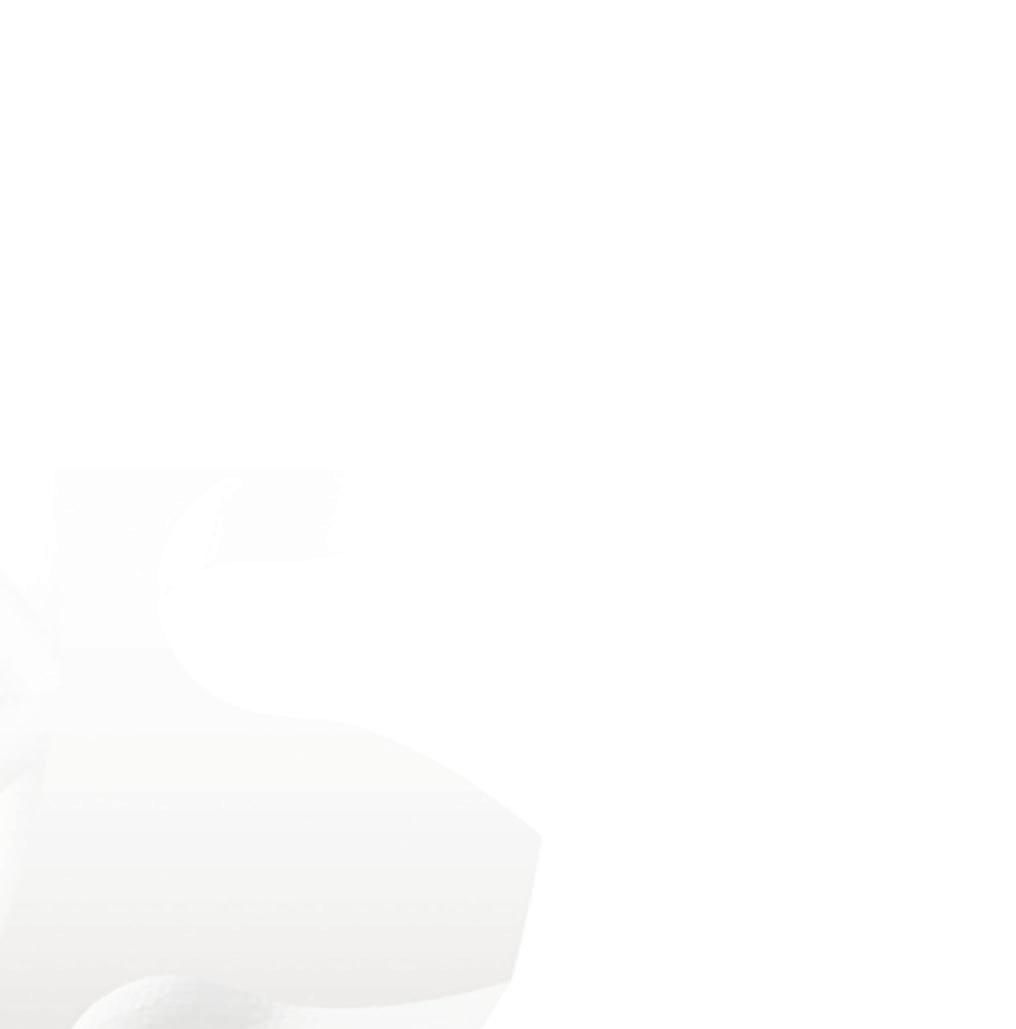
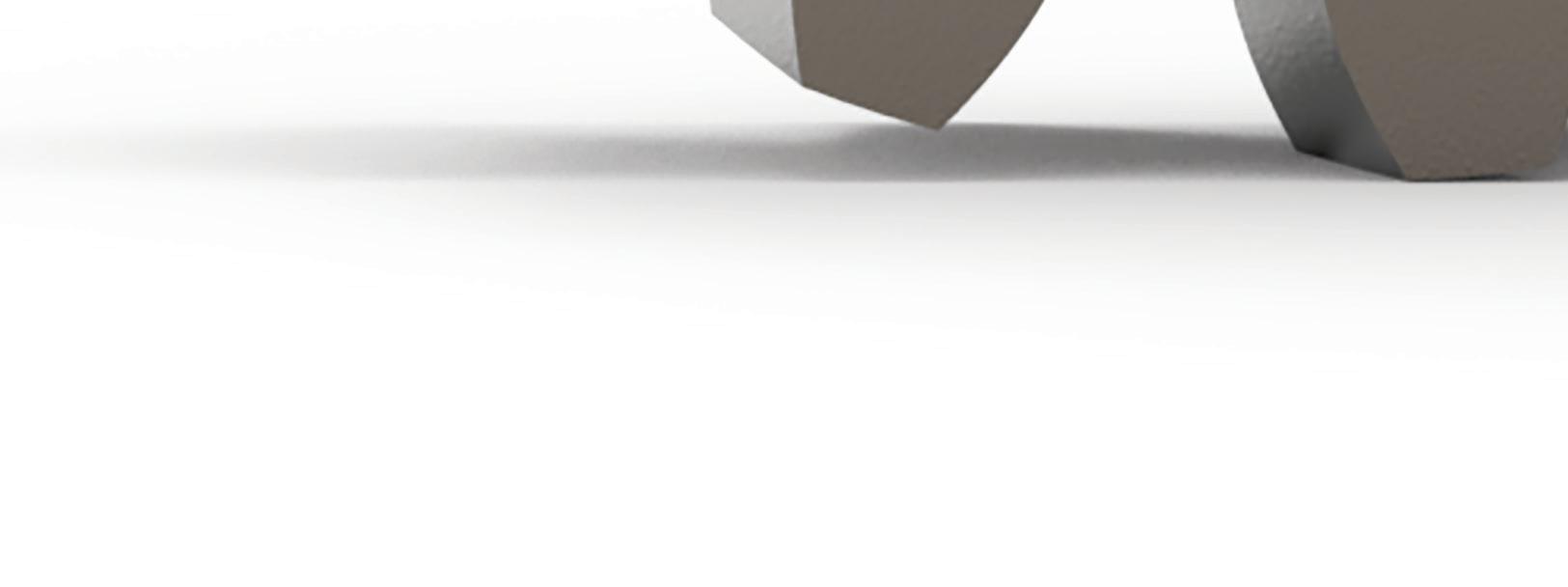

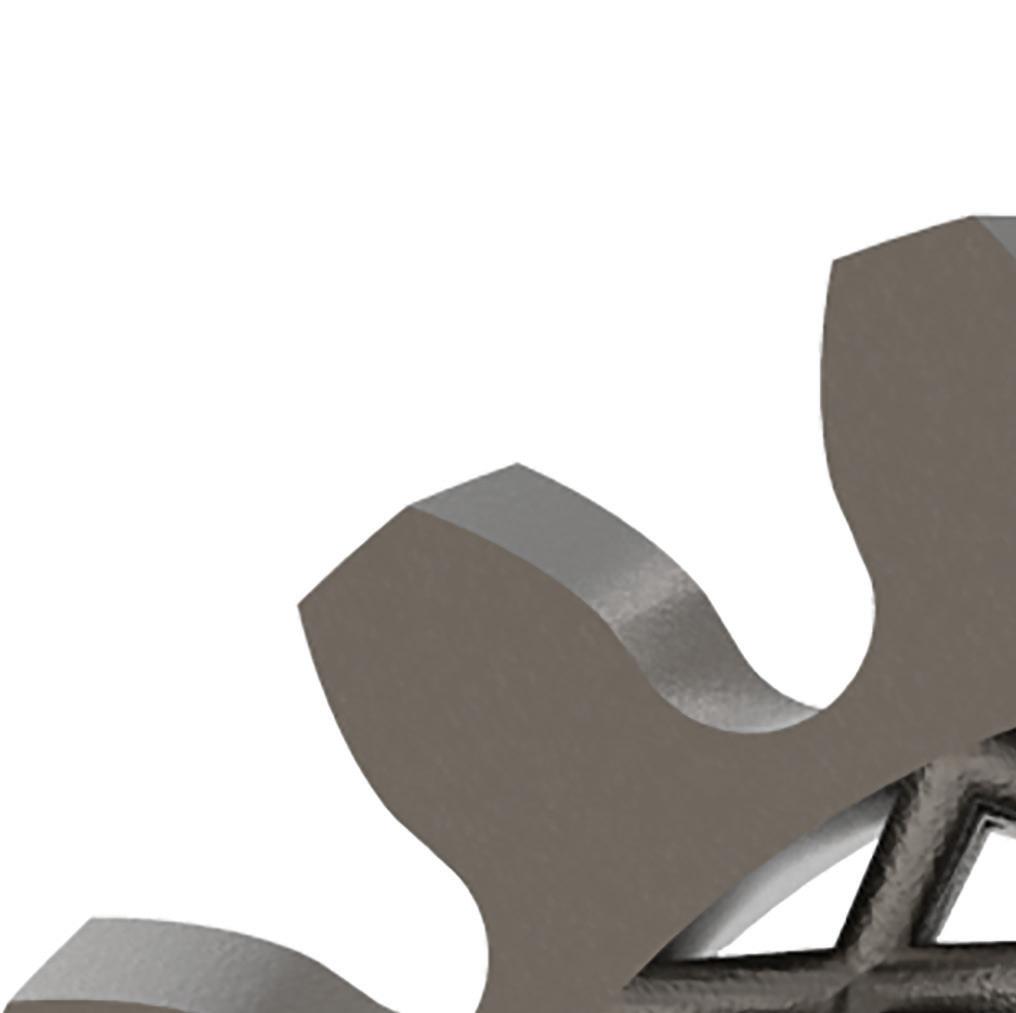
The P-1’s open material platform and inert process environment allow customers to use low-cost, third party metal injection molding powders across a variety of materials,
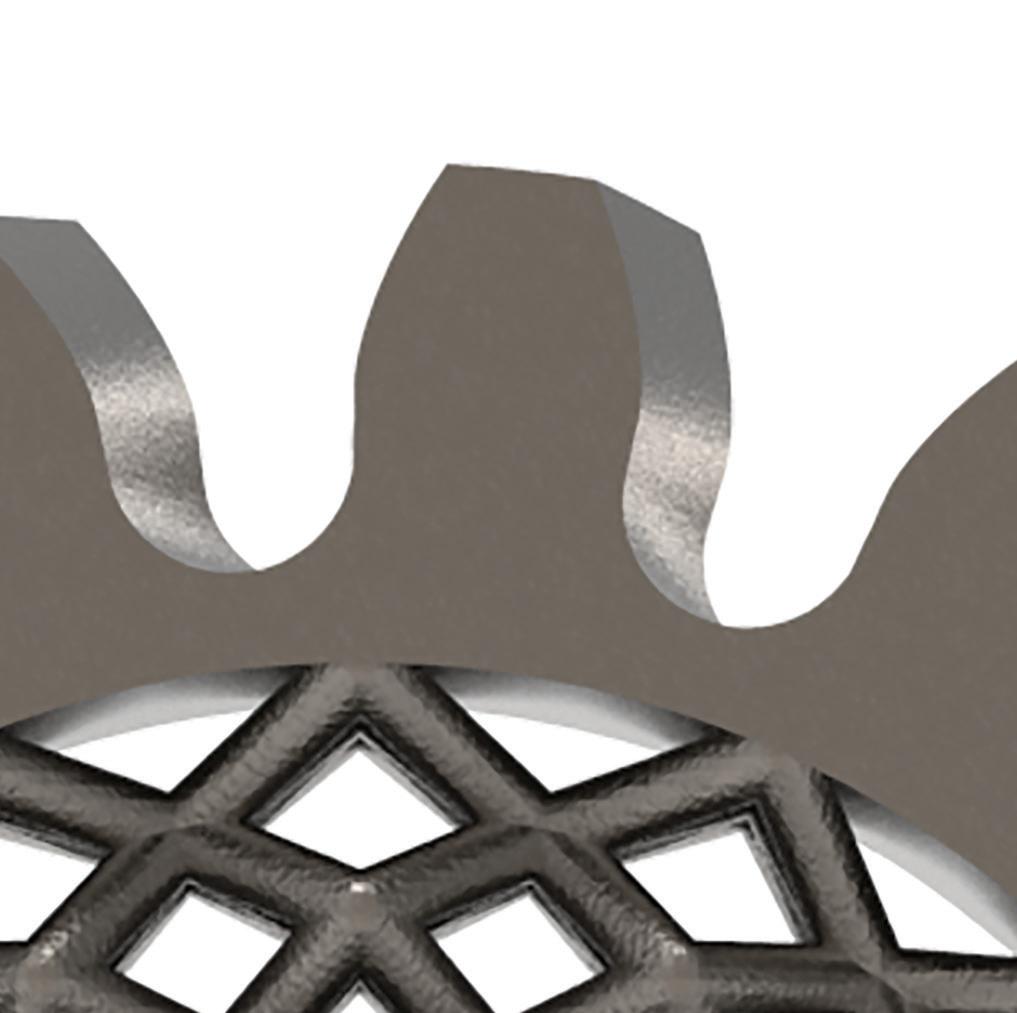

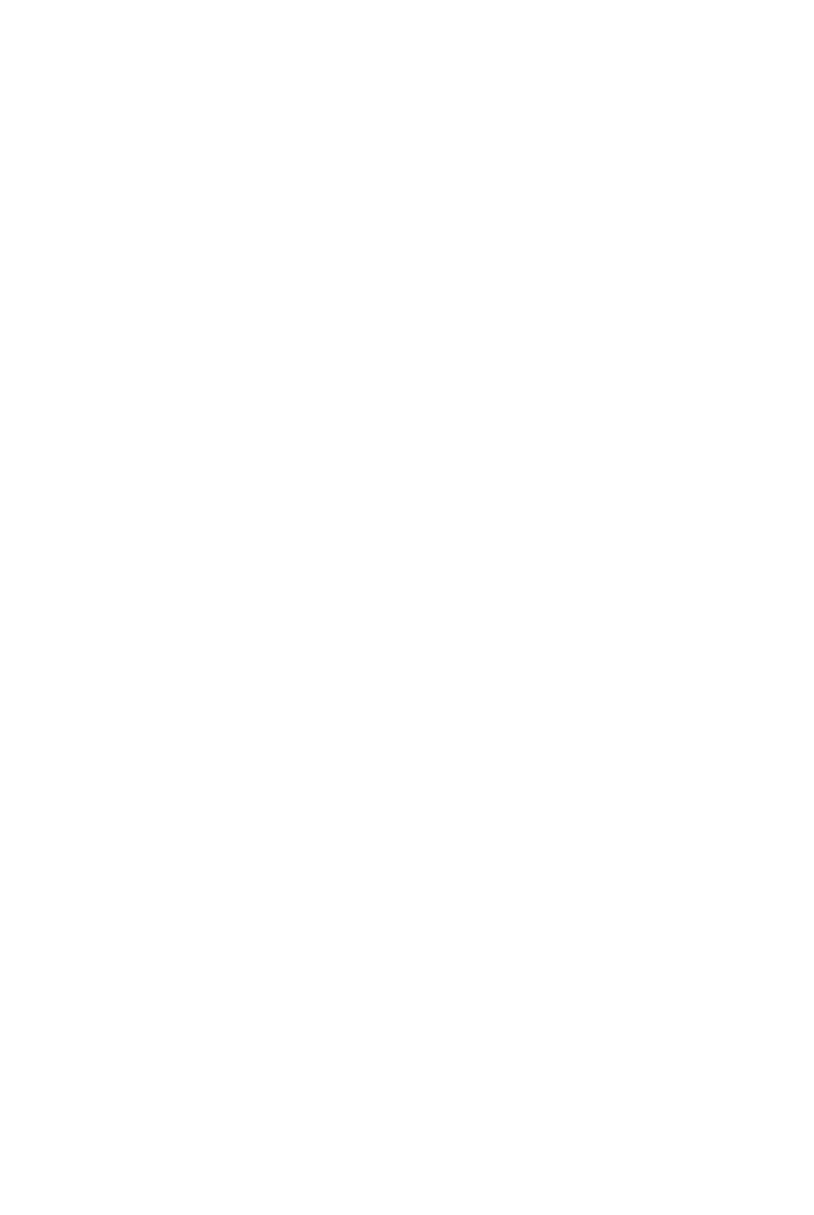
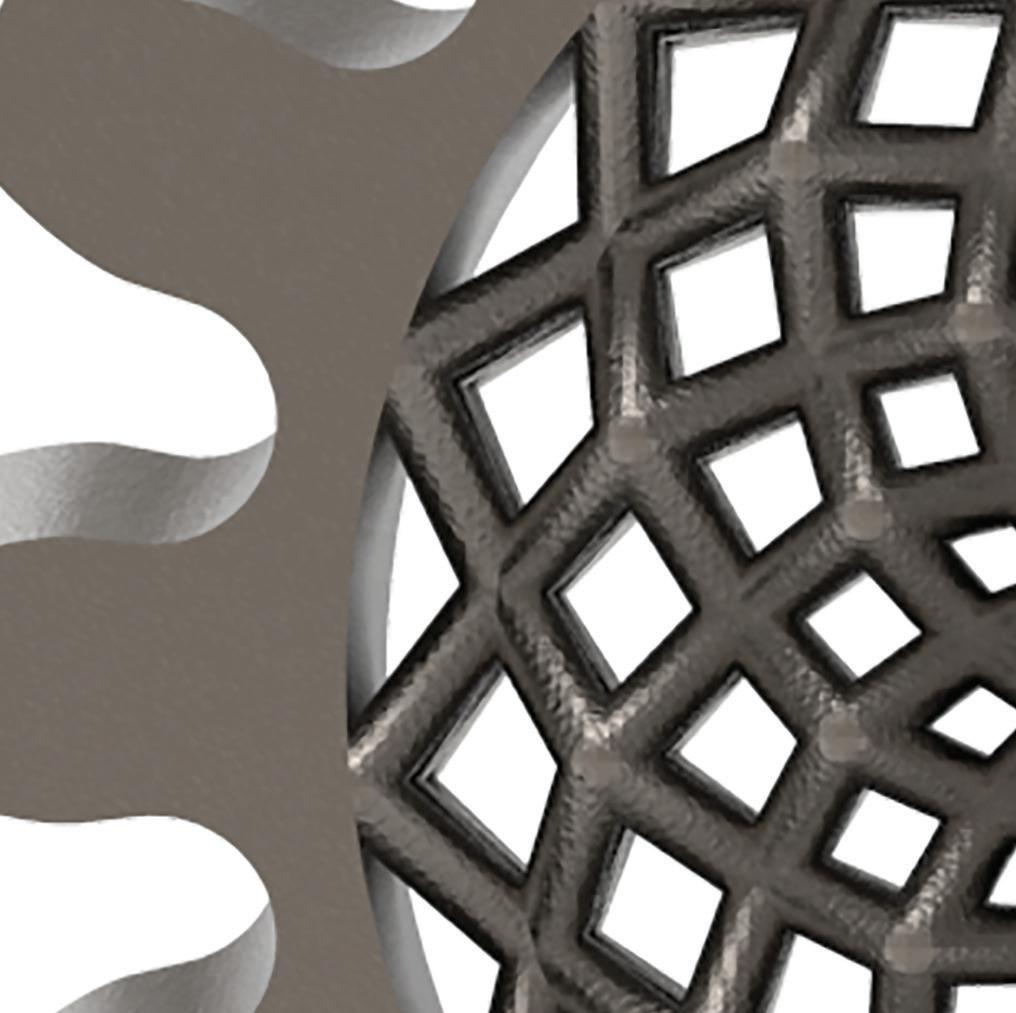
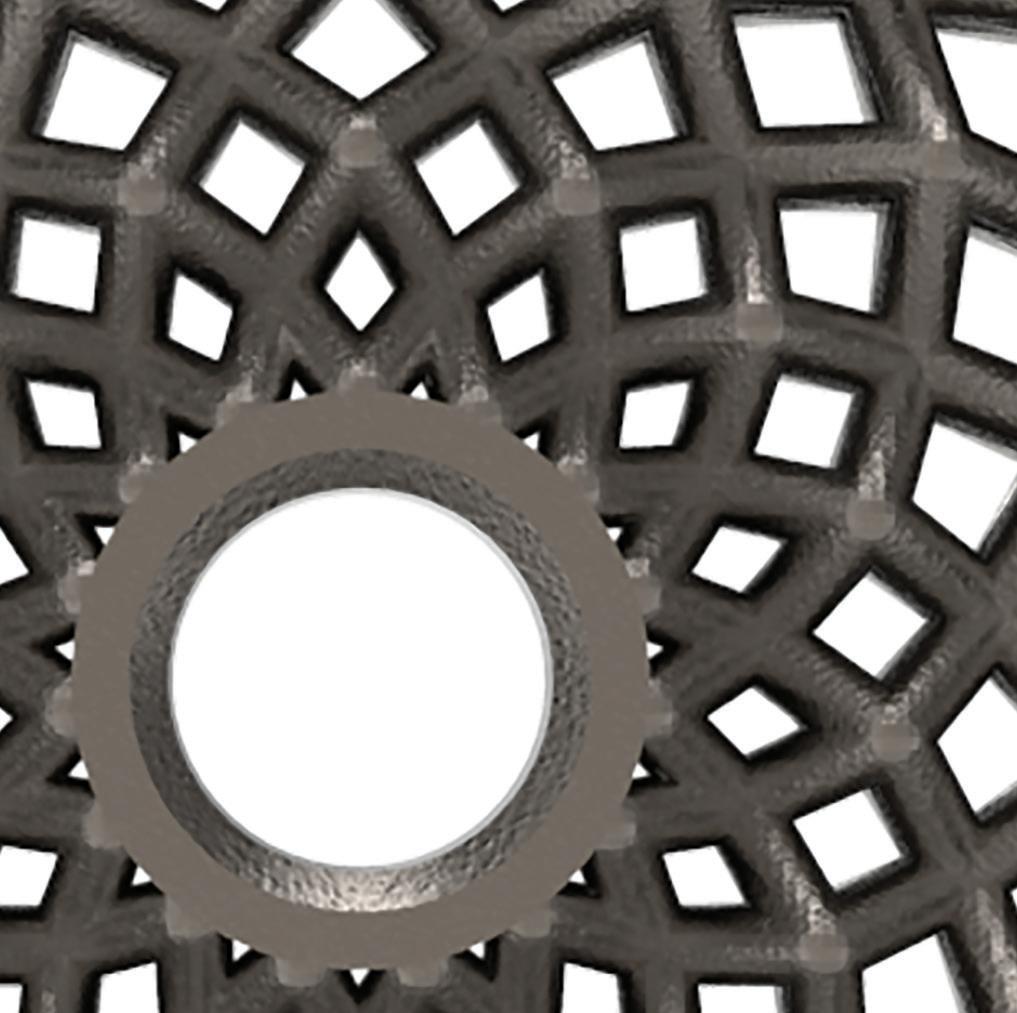
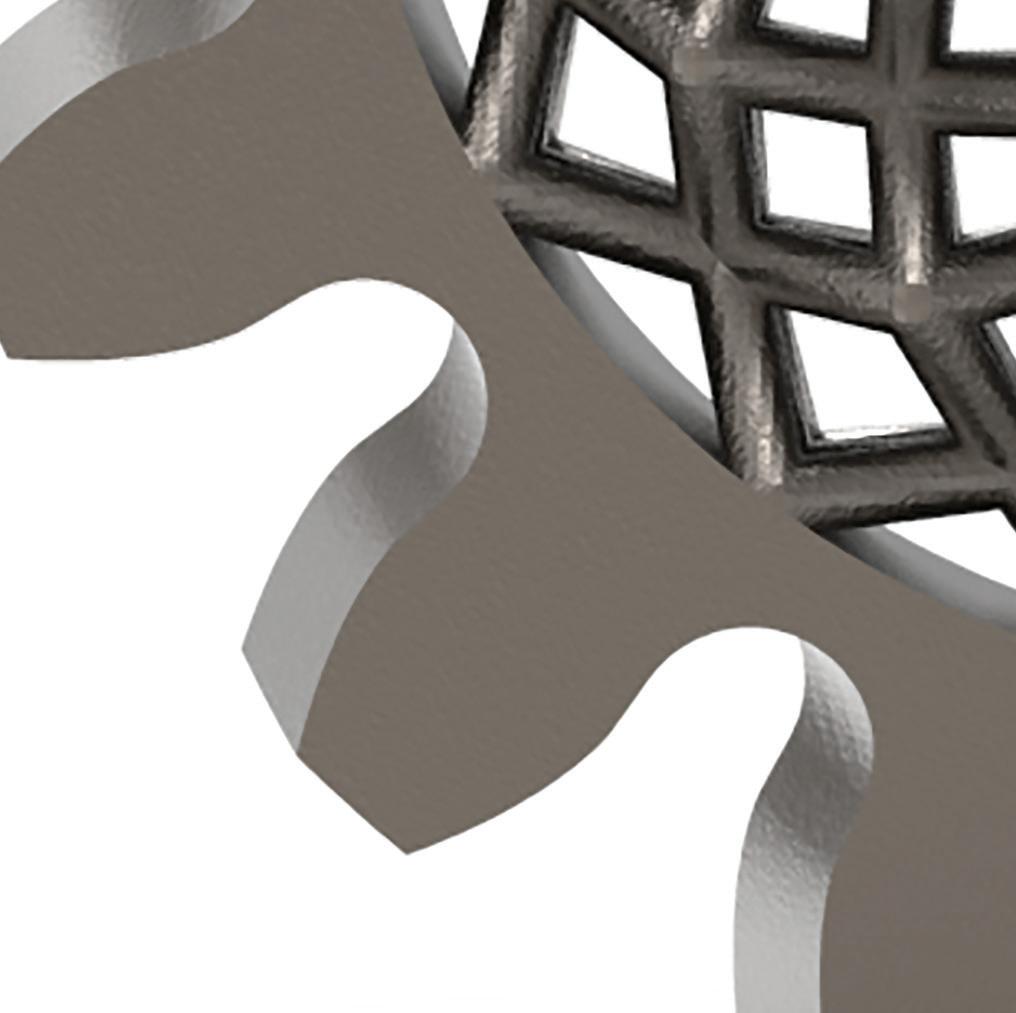
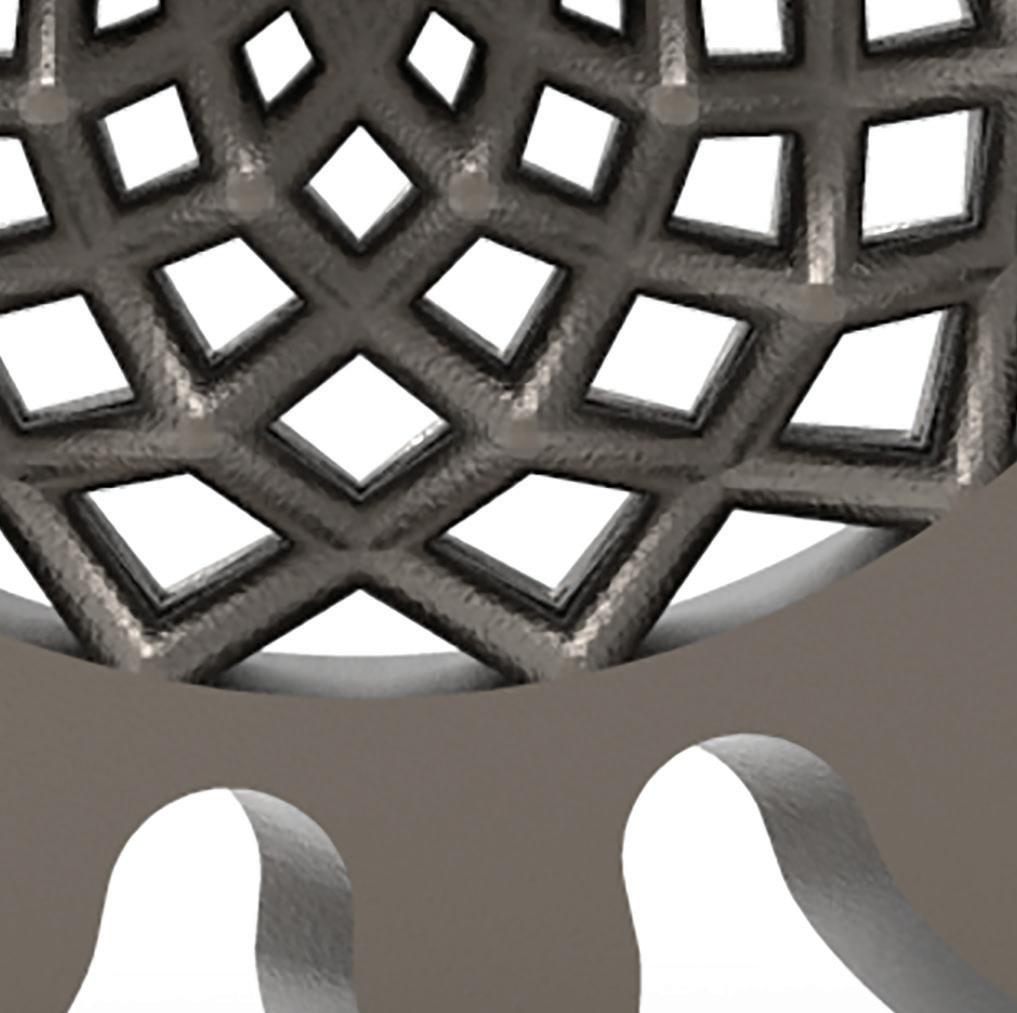
a variety of materials, making the P-1 suitable for serial production of small and complex parts in addition to smaller scale process development activities. Powder reclaimed during the printing and de-powdering process can be recycled for future use, for more cost efficiencies and a more environmentally friendly manufacturing process. In addition, the tooling-free manufacturing process on the P-1 facilitates quick turnovers to new jobs along with the ability to print many complex geometries simultaneously with no print supports required. P-1 customers will also gain access to Desktop Metal’s Fabricate manufacturing build preparation software, as well as to the Live Sinter application, which dynamically simulates the sintering process and automatically generates print-ready geometries that compensate for the shrinkage and distortion that take place during sintering, minimizing process trial and error while improving accuracy. Soon after that, Desktop Metal, Inc., announced the acquisition of EnvisionTEC, a leading global provider of volume production photopolymer 3D printing systems.
One of the newer materials
certified for printing on its systems is 4140 low-alloy steel.
EnvisionTEC will operate as a wholly owned subsidiary of Desktop Metal with its founder, Al Siblani, continuing to serve as Chief Executive Officer of the EnvisionTEC business. The acquisition of EnvisionTEC brings the digital light processing (DLP) 3D printing technology to the overall portfolio of Desktop Metal. EnvisionTEC systems are used in a range of industries, including medical devices, jewelry, automotive, aerospace, and biofabrication. Then, the company’s marketing team announced a powder that enables aluminum sintering for binder jetting AM technology. This powder is the result of a multi-year collaboration between Desktop Metal and Uniformity Labs. The 6061 aluminum powder yields fully dense parts, is sinterable with more than 10% elongation and improved yield strength and ultimate tensile strength versus wrought 6061 aluminum with comparable heat treatment. Said Ric Fulop, CEO and cofounder of Desktop Metal, “The global aluminum castings market is more than $50 billion per year, and it is ripe for disruption with binder jetting AM solutions. These are the best reported properties we are aware of for a sintered 6061 aluminum powder.” Agreed Adam Hopkins, founder and CEO of Uniformity Labs, “This development is a step towards the adoption of mass-produced printed aluminum parts.” The aluminum powder also enables compatibility with water-based binders and has a higher minimum ignition energy (MIE) relative to other commercially available 6061 aluminum powders, for a better safety profile. Desktop Metal also launched a new business line, Desktop Health, that will focus on additive manufacturing solutions for dental, orthodontic and otolaryngology applications. “Today the world manufactures more than $85 billion in medical and dental implants each year,” said Fulop. “We think a large percentage of these parts could be printed and made patient-specific before the end of the decade.” Michael Mazen Jafar will be the President and CEO of Desktop Health. Most recently, Desktop Metal announced it has qualified the use of 316L stainless steel for the Production System platform, which leverages patent-pending Single Pass Jetting (SPJ) technology for fast build speeds. Known for its corrosion resistance and excellent mechanical properties at extreme temperatures, 316L stainless steel is suited for applications in demanding conditions, such as parts exposed to marine or pharmaceutical processing environments, food preparation equipment, medical devices and surgical tooling. It also exhibits excellent weldability by standard fusion and resistance methods. The material meets MPIF 35 standards for structural powder metallurgy parts set by the Metal Powder Industries Federation. Parts printed with 316L have demonstrated excellent mechanical properties and corrosion resistance, while significantly decreasing production time and part cost.
Here are a few example applications.
Rocker arm for saltwater marine environments.Rocker arms open and close intake and exhaust valves on outboard marine engines. The use of 316L extends the part’s life and provides corrosion resistance against harsh saltwater environments. The Production System P-50 can
MACHINE NAME BUILD SIZE BUILD MATERIALS
Fiber 310 x 240 x 270 mm PA6 + CF, PA6 + GF, PEKK + CF, PEEK + CF (Both chopped and continous fiber)
Production System (P50)
Production System (P1) 490 x 380 x 260 mm (48L) Alloys, including stainless steel, copper, and tool steels, 17-4PH, 316L, Inconel 625, H13, AISI 4140, AL 6061
200 x 100 x 40 mm (0.8L) Alloys, including stainless steel, copper, and tool steels, 17-4PH, 316L, Inconel 625, H13, AISI 4140, AL 6061
Studio System+ Printer 300 x 200 x 200 mm 17-4 PH, 316L, AISI 4140, H13, Copper
Shop System 350 x 220 x 50,100,150,200 mm (4L,8L,12L,16L) 17-4 PH
Studio System 2 300 x 200 x 200 mm 316L
LAYER THICKNESS BUILD SPEED
50 μm NA
30 - 200 um 12,000 cc/hr
30 - 200 um 1,350 cc/hr
std resolution =100-220 um, High resolution = 50 um 50 - 100 um
std resolution =100-220 um, High resolution = 50 um NA
800 cc/hr
Max build rate = 16 cm3/hr
produce more than a thousand parts per day with ribbing features and cutouts to deliver adequate strength and stiffness while maintaining low weight and a small footprint versus the standard cast alternatives, which require up to 8 to 14 weeks lead time.
Fluid connector for chemical processing plants. Heavy industry fluid connectors used in many chemical processing plants need to be manufactured in 316L for corrosion resistance against the chemicals moving through the part. The connector’s complex internal channels make it impossible to manufacture as a single component via conventional manufacturing methods. The Production System P-50 prints the fluid connector in 316L as a single, consolidated component and can support a throughput of nearly 5,500 parts per week, at a fully burdened cost of approximately $6.85 per part.
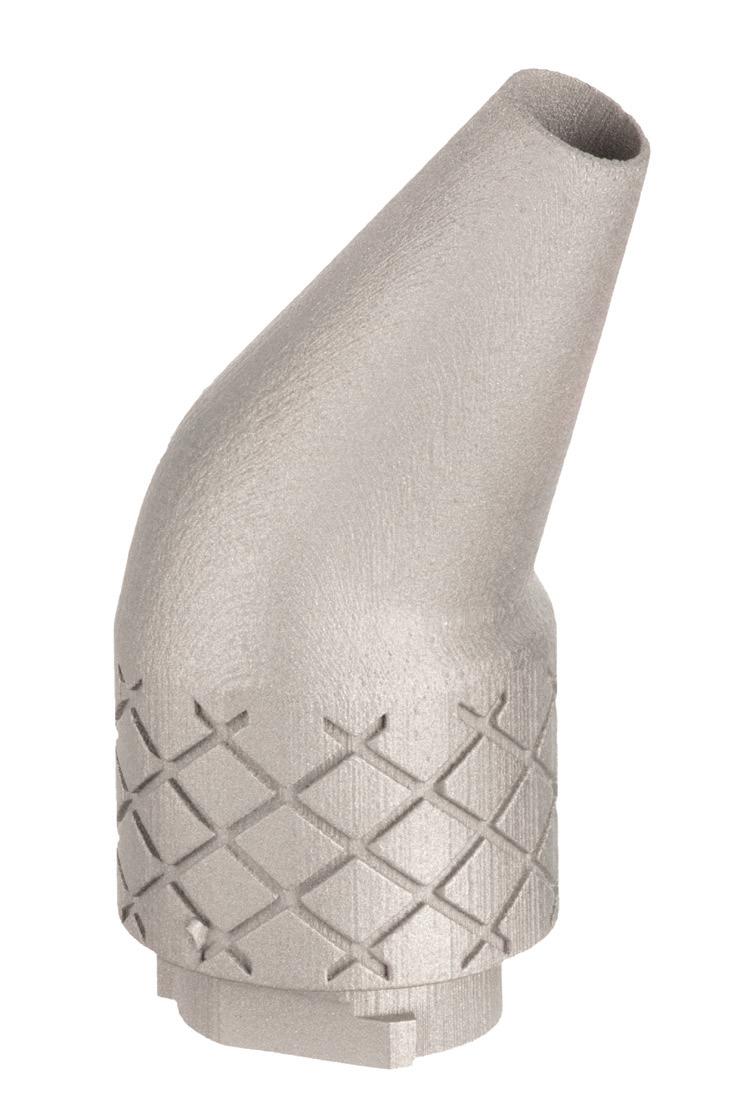
Custom surgical tool for medical applications. Because 316L is a surgical-grade steel, it is an ideal material for medical applications like surgical nozzles. By eliminating tooling, additive manufacturing enables mass production runs of different sized nozzles with no lead time, featuring internal channels that are optimized for individual patient needs.
Printing on the Production System P-50 eliminates multiple fixturing steps otherwise required for machining, and results in a throughput of more than 24,000 parts per week at approximately $2.50 per part. By comparison, machining the same part would cost $20.00 -$40.00 per part, and require up to two months to create the same number of parts the P-50 can produce in just one week.
Continuing its expansion, Desktop Metal acquired Adaptive3D, a leading provider of elastomeric solutions for additive manufacturing. Adaptive3D offers photopolymer elastomers. Its products enable volume enduse parts production with additive manufacturing of odorless, tough, strain-tolerant, tear-resistant, and biocompatible rubbers and rubberlike materials. The flagship resin is Elastic ToughRubber 90, a tough, printable elastomer for all seasons. Adaptive3D printable materials fit high-throughput manufacturing of functional, complex 3D plastic and rubber parts in consumer, healthcare, industrial, transportation, and oil and gas markets. Adaptive3D’s core technology was developed through Defense Advanced Research Projects Agency (DARPA) funding, and the Company has received strategic capital from leading materials companies including Covestro, Arkema Group, West Pharmaceuticals, Applied Ventures, and Royal DSM. And, as of this writing date, Desktop Metal qualified a number of materials for its printing systems, including 4140 low-alloy steel.