
17 minute read
CARBON
Taking advantage of
lattice designs
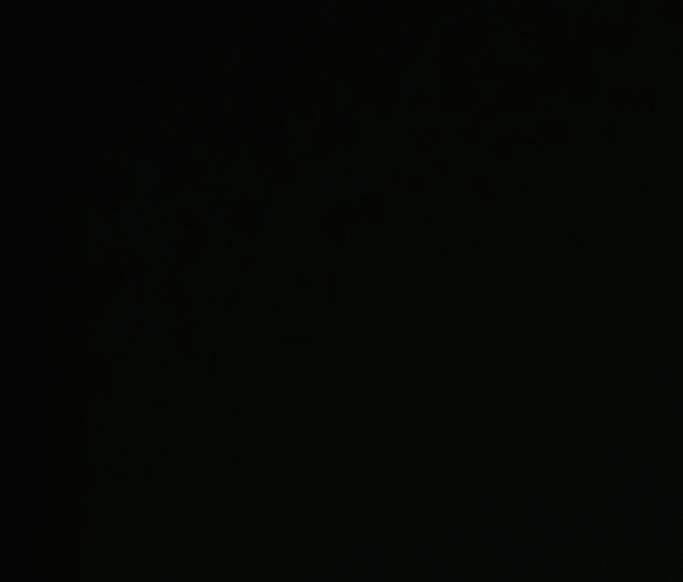
in 3D printing
Leslie Langnau • Senior Contributing Editor
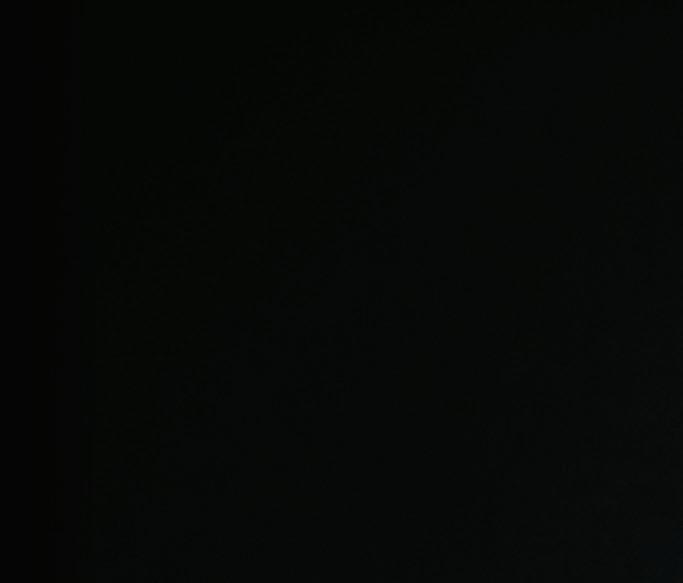
Lattice structures are those geometric shapes grouped together to create repeatable patterns for engineering purposes. The idea of lattices has been around for quite some time. You see these repeating patterns on buildings and bridges. For design engineers, lattices can deliver specific mechanical properties to an object, often in the form of a stiffness-to-mass ratio.
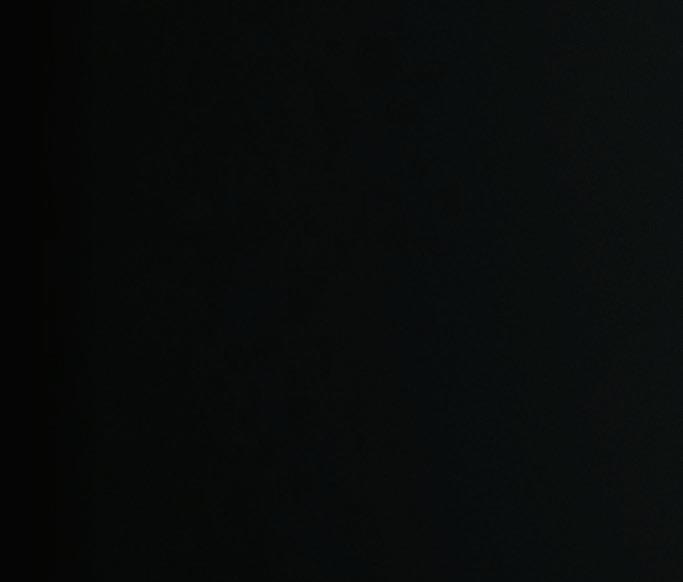
Lattice structures have not been used as often as they could be because manufacturing methods that could produce them easily did not exist until the development of 3D printing / Additive Manufacturing. Injection molding and machining are often cost prohibitive when it comes to producing these shapes.
Today, though, 3D printing easily creates lattice structures in helmets, saddles, shoes, nasal swabs, and in other designs. For example, lattices are being studied for use in soft robotics and in understanding how pulmonary airways work.
The additive company Carbon offers a lattice design generator called Design Engine that automates the process of creating conformal, single-zone lattices.
Using lattices in your design can “basically explode your design freedom significantly,” notes Hardik Kabaria, Director of Engineering at Carbon.
Lattices can be made from metal or polymer materials. If you use the Carbon Design Engine, you’ll work with stereolithography and polymer materials.
According to Kabaria, the Carbon Digital Light Synthesis system opened the door to more easily work with lattice structures. “The initial application we found and have had success with is in the area where, traditionally, you were using foam. So, if you're using foam for shoes, or helmets, or saddles, those are the places where you can replace the foam with polymeric lattice parts.
“And the basic advantage there is you can achieve mechanical properties not easily achievable with foams. But we have also found some areas that are significantly different than foam replacements. And the example I would give is COVID-19 nasal swabs.
“I've been working on a lattice-design computational-geometry algorithm that is dedicated towards these types of applications for quite some time. I would not have imagined that COVID-19 swabs are something that we would be able to make using lattice design ideas.
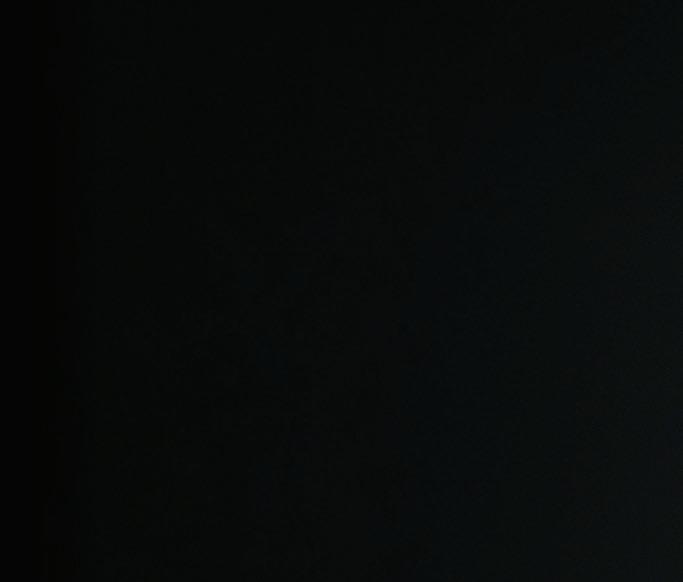
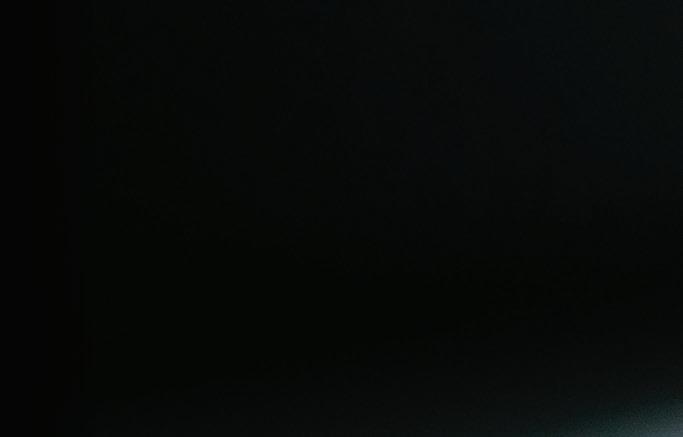
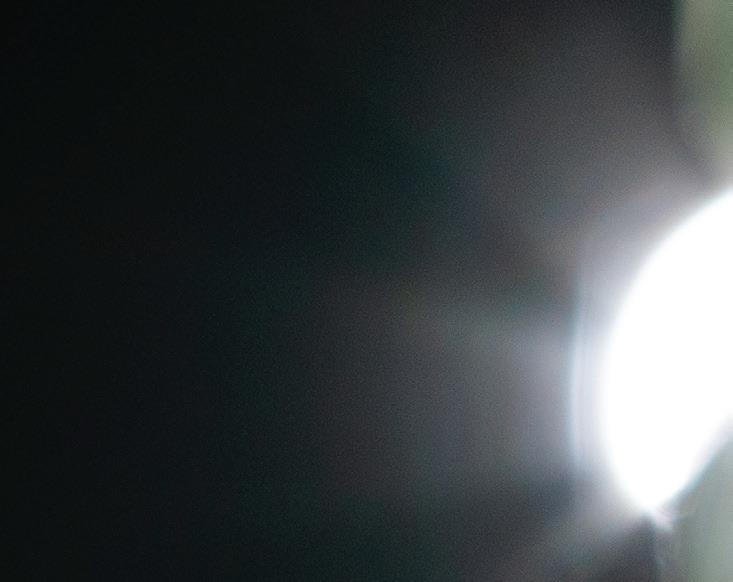


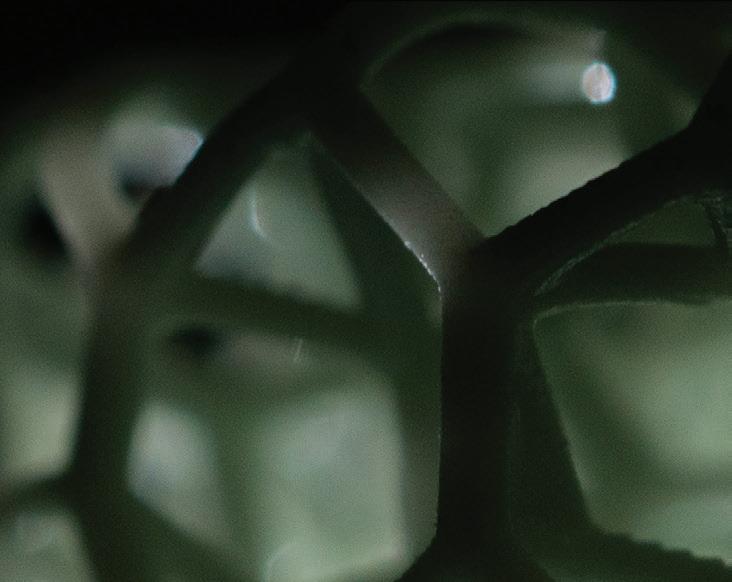
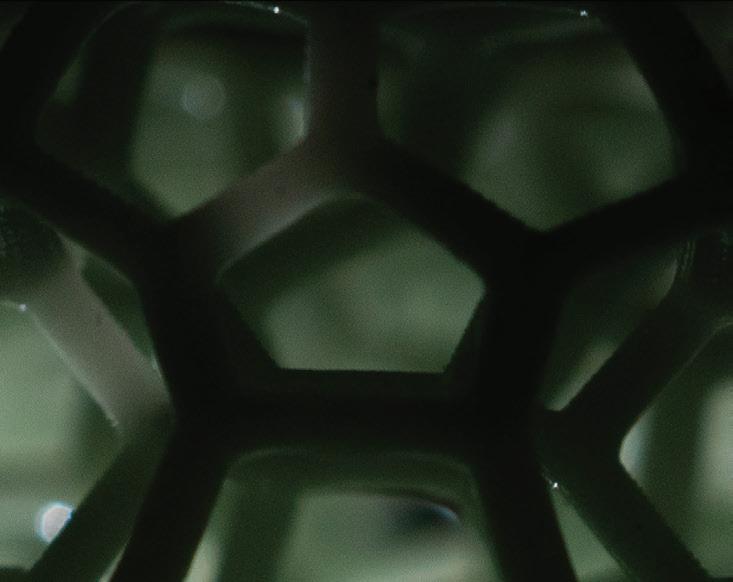
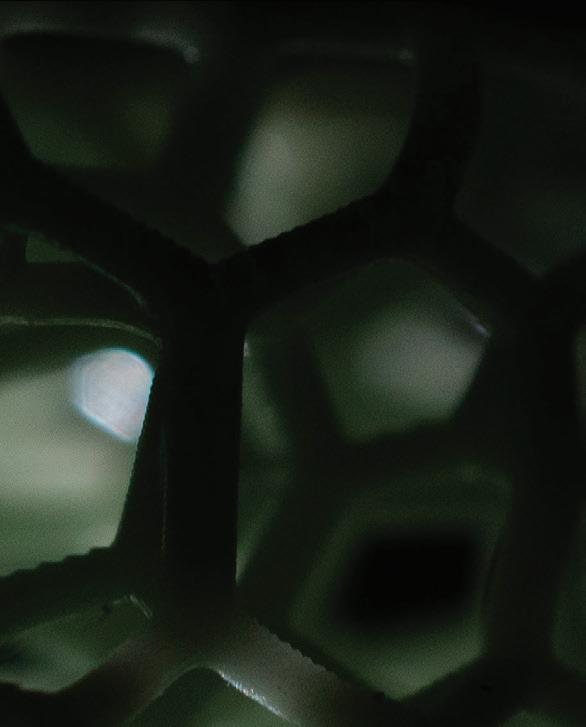
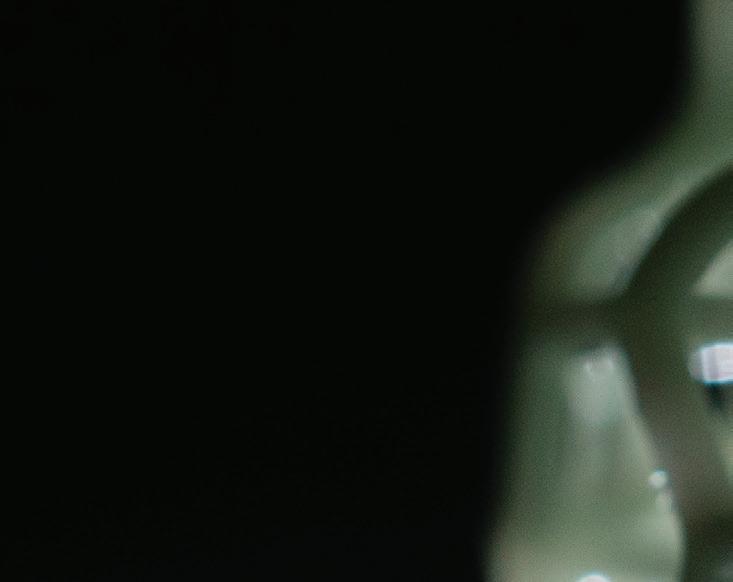
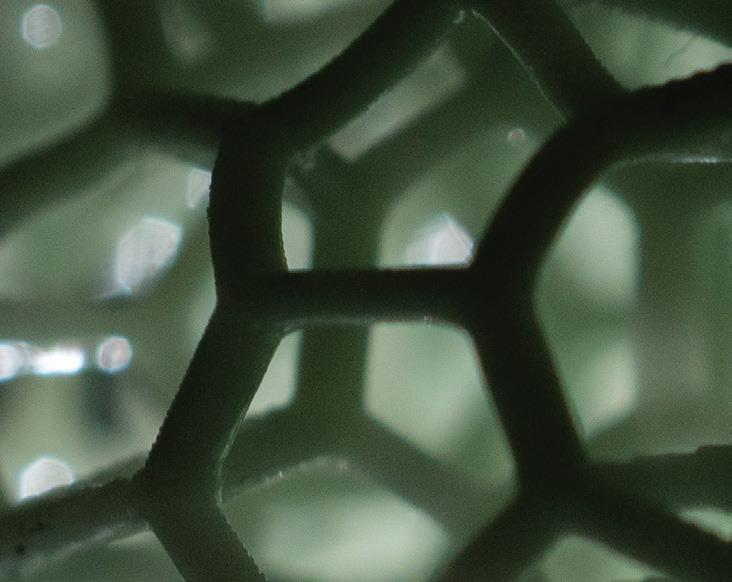
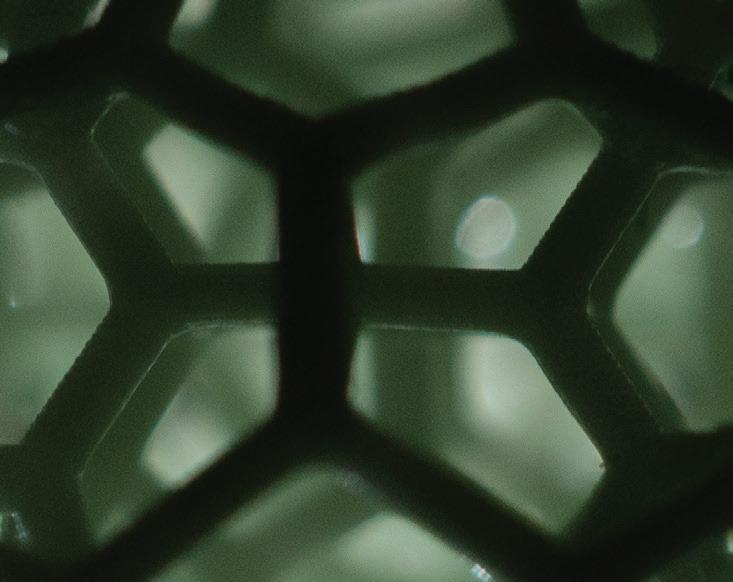
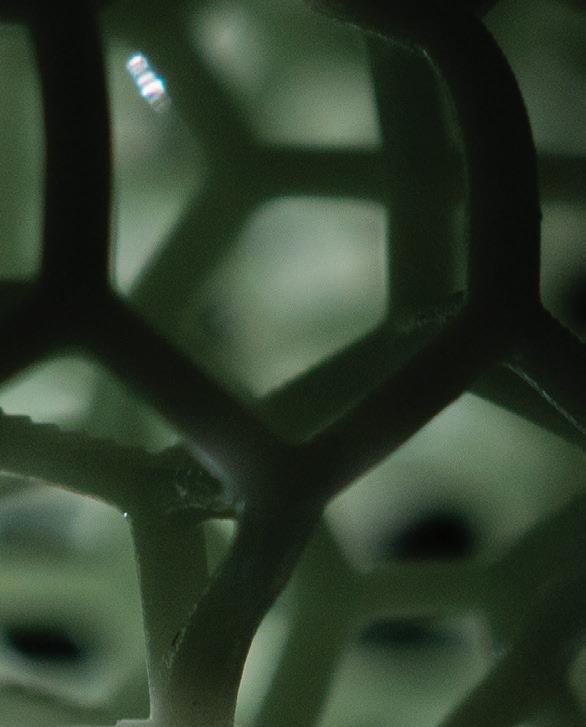

Lattice structures
let you place a range of mechanical properties precisely where you want them in your design.
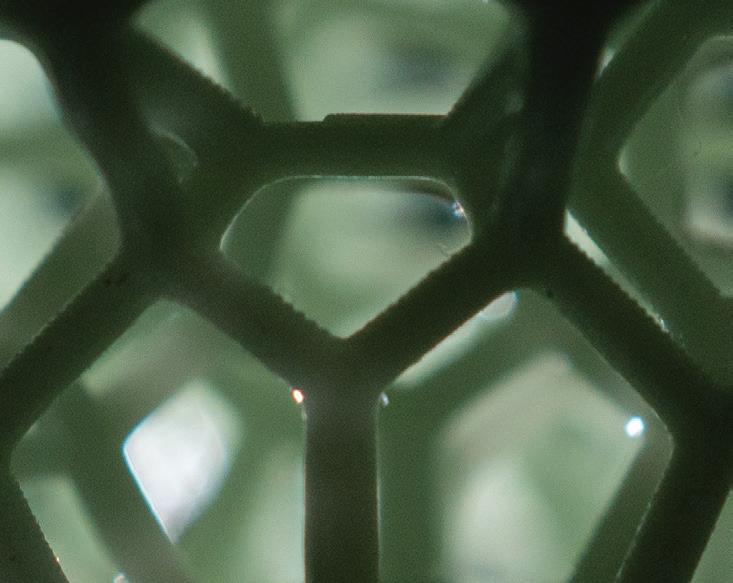

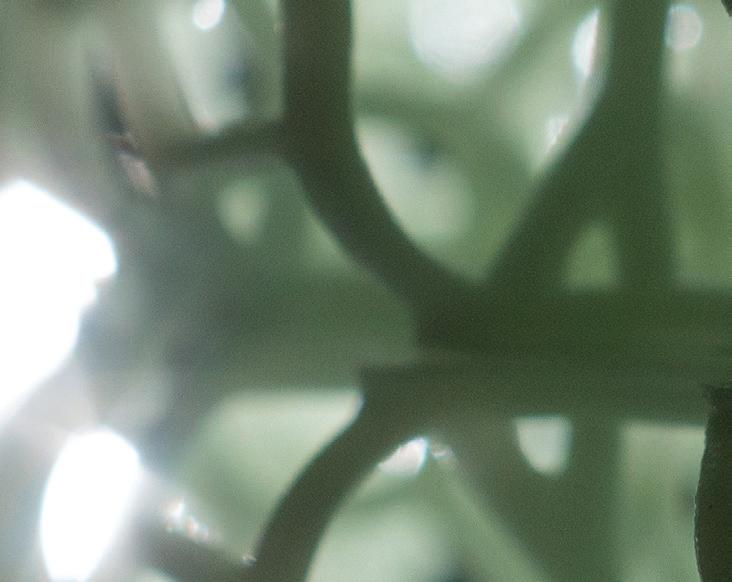
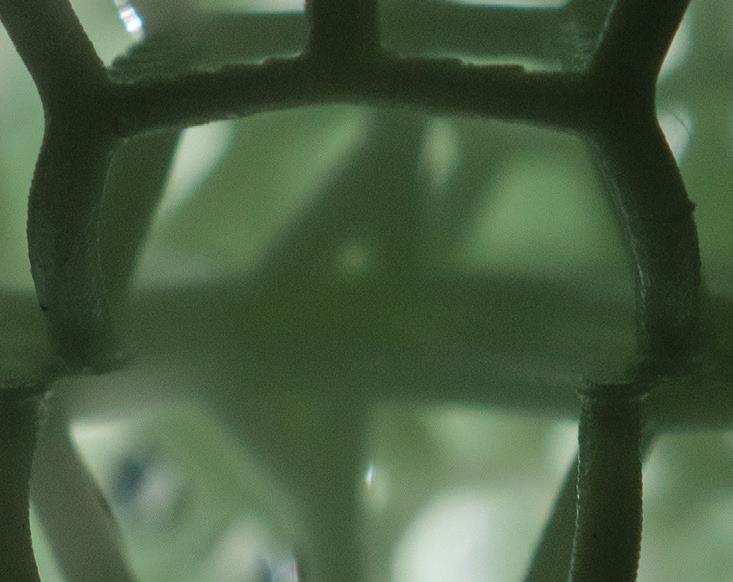
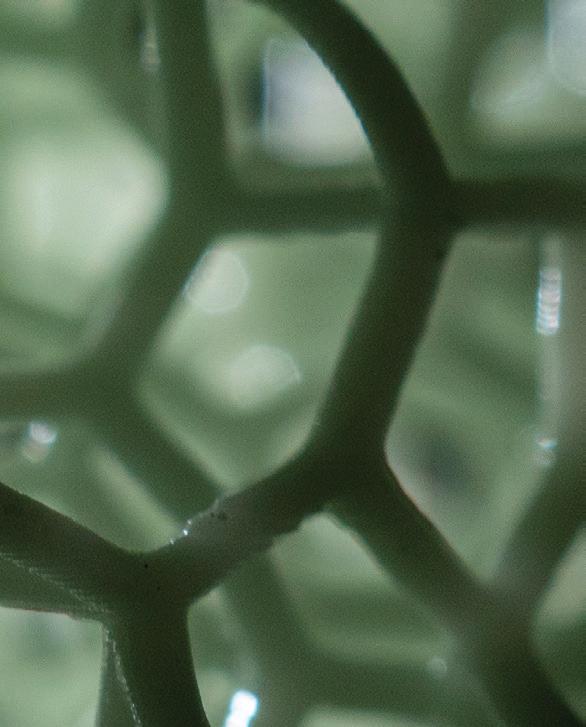
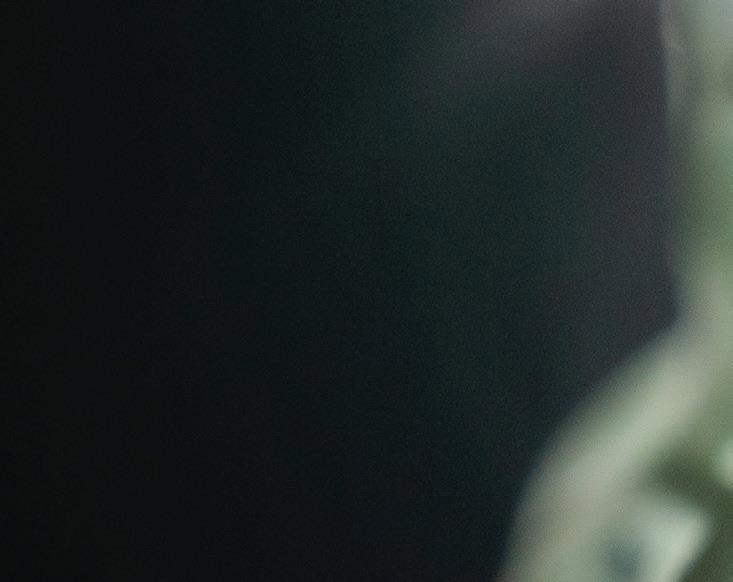
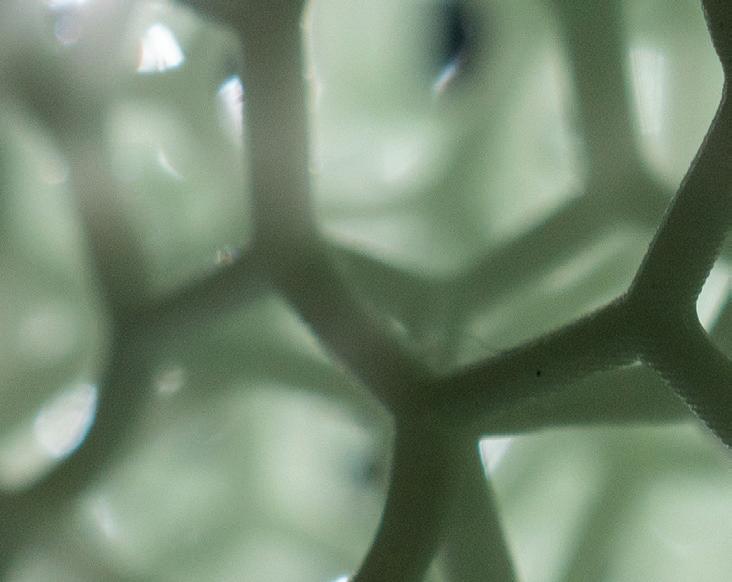
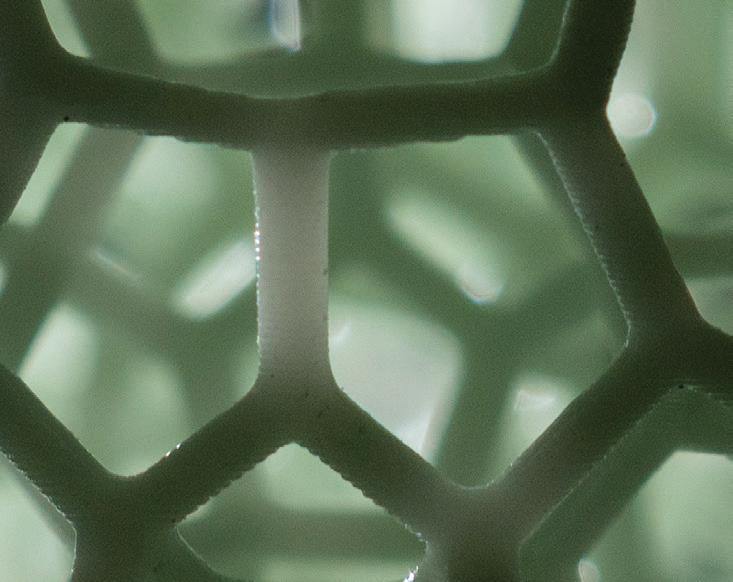
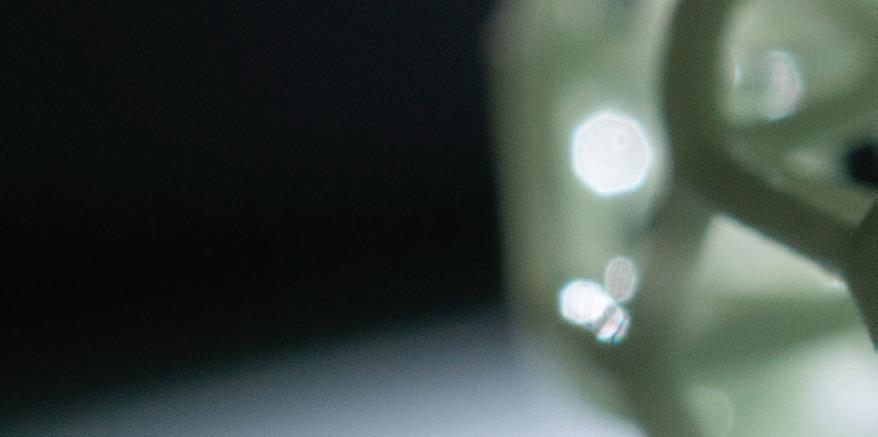
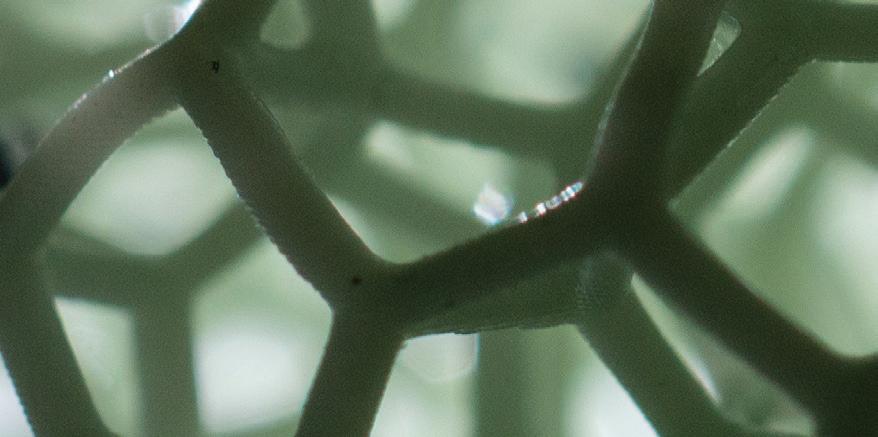


“There are more applications out there than what we, who live and breathe lattices, have ever imagined. And that is one of the reasons why we realized that we needed to create a software program that would give access to more mechanical engineers in our ecosystem.”
Doing more with lattices
Lattices are generally complex designs. You can have hundreds of thousands of these geometric structures in a design. There are generally two problems designers face with lattices. Traditional CAD tools do not make it easy to draw hundreds or thousands of these structures in a design. Second, traditional manufacturing methods, such as injection molding or machining are too costly to use to mold or cut that number of geometric shapes.
“So, you have a problem both on the design software side, as well as the manufacturing side,” says Kabaria. “We at least solved the manufacturing side with additive manufacturing and polymer materials. So, you can print and create an end quality part. But we also realized that's only part of solution. We developed a manufacturing method, but we didn't give you a way to make amazing parts on that manufacturing method. So, that's why we started working on the design engine to enable our customers to create really kickass products. The most beautiful part of this is that we have enabled customers to put parts in production.”
The software can be used by mechanical and industrial design engineers, as well as the manufacturing technician on the floor that may not have access to the high compute power needed for CAD produced lattices.
Design tips
Design for additive manufacturing principles are also needed when working with lattices for a design.
Be sure you can make the structure on the chosen 3D printer or additive system. One question to consider is will you have a good yield on the printer? “Because in the end, some manufacturing projects, almost all of them really, are about unit economics. You can only have so many failed parts, right?”
Be sure the lattice structures are not too small, clustered, or densely packed together. Such designs will inhibit resin flow, which will slow down the printing process. And slow printing effects unit economics.
Lattices can require a lot of memory to render, represent, and transfer to the printer, …. “there are challenges in every one of those stages. Like, our design software works on AWS. We can use the
Lattices suit a range of objects,
from shoe insoles to helmets, and even nasal swabs.
COMPANY MACHINE NAME BUILD SIZE BUILD MATERIALS LAYER THICKNESS BUILD SPEED
Carbon L1 Printer 15.7" x 9.8" x 20" (400mm x 250mm x 508mm)
M1 Printer 5.6 in x 3.1 in x 12.8 in., (141 mm x 79 mm x 326 mm)
M2 Printer 7.4 x 4.6 x 12.8 in. (189 x 118 x 326 mm) Carbon EPX 82 Carbon RPU 70 Carbon RPU 130 Carbon EPU 40 Carbon EPU 41 Carbon MPU 100 Carbon CE 221 Carbon FPU 50 Carbon SIL 30 Carbon UMA 90 Carbon DPR 10 100 μm (Standard), 50 μm (Fine), 25 μm (Super Fine)
Carbon EPX 82 Layerless, isotropic parts
Carbon RPU 70 Carbon RPU 130 Carbon EPU 40 Carbon EPU 41 Carbon MPU 100 Carbon CE 221 Carbon FPU 50 Carbon SIL 30 Carbon UMA 90 Carbon DPR 10 100 μm (Standard), 50 μm (Fine), 25 μm (Super Fine) 40mm/hour (unscripted)
40mm/hour (unscripted)
40mm/hour (unscripted)
cloud infrastructure and highperformance computing to generate the designs, but that's sort of the first step. Then, we have to successfully transfer the design to the printer, make sure we don't run into any problems during that process, ensure it’s sliceable so, … we slice the part and convert it into like images or voxels, and that process has to be foolproof because initially, you had kind of a simple parts, but now you have a very complex geometry.”
In terms of computational geometry algorithms, there are challenges on the design front to make sure that the part is not just a nicely rendered geometry, but that it is something you can print and have it in your hand.
Keep in mind that every printer has a resolution, so don’t design a lattice structure smaller than the resolution, or the pixel size, of the printer.
For some 3D printing systems, materials can be a limitation. Each material has a viscosity. If the viscosity is high and you have little space between the lattice struts, the resin will not flow through. You will only print a few lattice struts, and after that, there'll be nothing there, or it will be a full blob of resin.
Then, there are a few process limitations to consider. For example, how fast will the printer move? Will heat be an issue?
“Generally, we worry about three things, hardware limitation, material-specific limitation, and the limitation of the process. And we try to account for that in the design.”
Lattice shapes
There are thousands of useful geometric shapes suitable for lattices. One of the challenges is determining which structure is right for the project. “We wanted to make that part easy. You are a mechanical engineer, the most important knowledge that you have is figuring out if a mechanical response you’re looking for, let's say for a saddle, has the right stress distribution, so you don't have a peak pressure at your sit bones. So, that's the most important part that you as a mechanical engineer for saddle industry know. The customer cares about the mechanical response, our software will help you find the lattice structures.
“While we know there are hundreds of thousands of different lattice structures, we initially launched with just five different structures. If you're looking for a polymeric foam-like response, which is what we call non-linear response, we'll give you a lattice structure.
“If you're looking for a memory foam-like response, it's a different lattice structure.... Often, you're looking for something very linear, which is actually not achievable with foam easily, but those are the kinds of things you really get in shoes, we have different lattice structure.
“Our goal was to enable custom manufacturing. As in the example of helmets, each head shape is different person to person.
“You have a part that you want to populate with lattice structures that you decided on based on the mechanical response you wanted. We want that process to be flawless, ….so users do not have to worry about broken structures that could lead to part failure. We don’t want users to deploy mechanical engineers to even inspect that there are no broken structures or open structures, it's just not going to work. It's just not going to scale.”
Benefits
Making it easier to include lattice structures in a design opens the door for new applications. If customers know that a design choice achieves a non-linear foamlike response, but they would like a very plateau-like stress versus strain response, which is almost like a flat curve, “we have a mechanical response wave structure for them. We call it the tetrahedral unit cell. They can choose that, and they can start populating it with the geometry and start testing it.
We at least solved the manufacturing
Our idea has been that anything that you want
The engineering team of one of our customers, CCM, has been using this tool and has been able to find a new application on their own.
Customers can work with Carbon engineers to design parts. However, the Design Engine enables customers to design without any aid.
“This is possible because of two things. We don't have to teach everybody which structures are the best, which model to use it with. And the second is, you have a part, you choose the structure, we'll be able to populate it so that they can quickly throw it on a printer, print it, iterate it, and the cycle continues.
Currently, the Design Engine program is not directly connected to CAD programs. “It's not as smooth of a link as we want in the future. Today, you use your SolidWorks, or CATIA, or whichever is your CAD design tool that is your favorite, and you can export it from there, the part you want a lattice in a triangle mesh.
Then you bring it to our tool, which is browser-based, so you can access it through your browser on your computer. You upload it. All the real computation happens on our AWS cloud infrastructure, so you are not really utilizing the computer power you have and more important, we are not limited by it. So if we want to do some heavy computation, we can run it on the cloud, and then we send it back to your browser for you.
“So, our idea has been that anything that you want to do with the lattice design, we'll allow you to do it in our tool base, in our software.”
Examples include creating different zones, creating a “skin” on a surface, creating a texture that is more comforting. Anything that is related to the 3D printing specific design, we'll build it in our tool base, but you can still export it back into the SolidWorks for revision or for version control purposes.
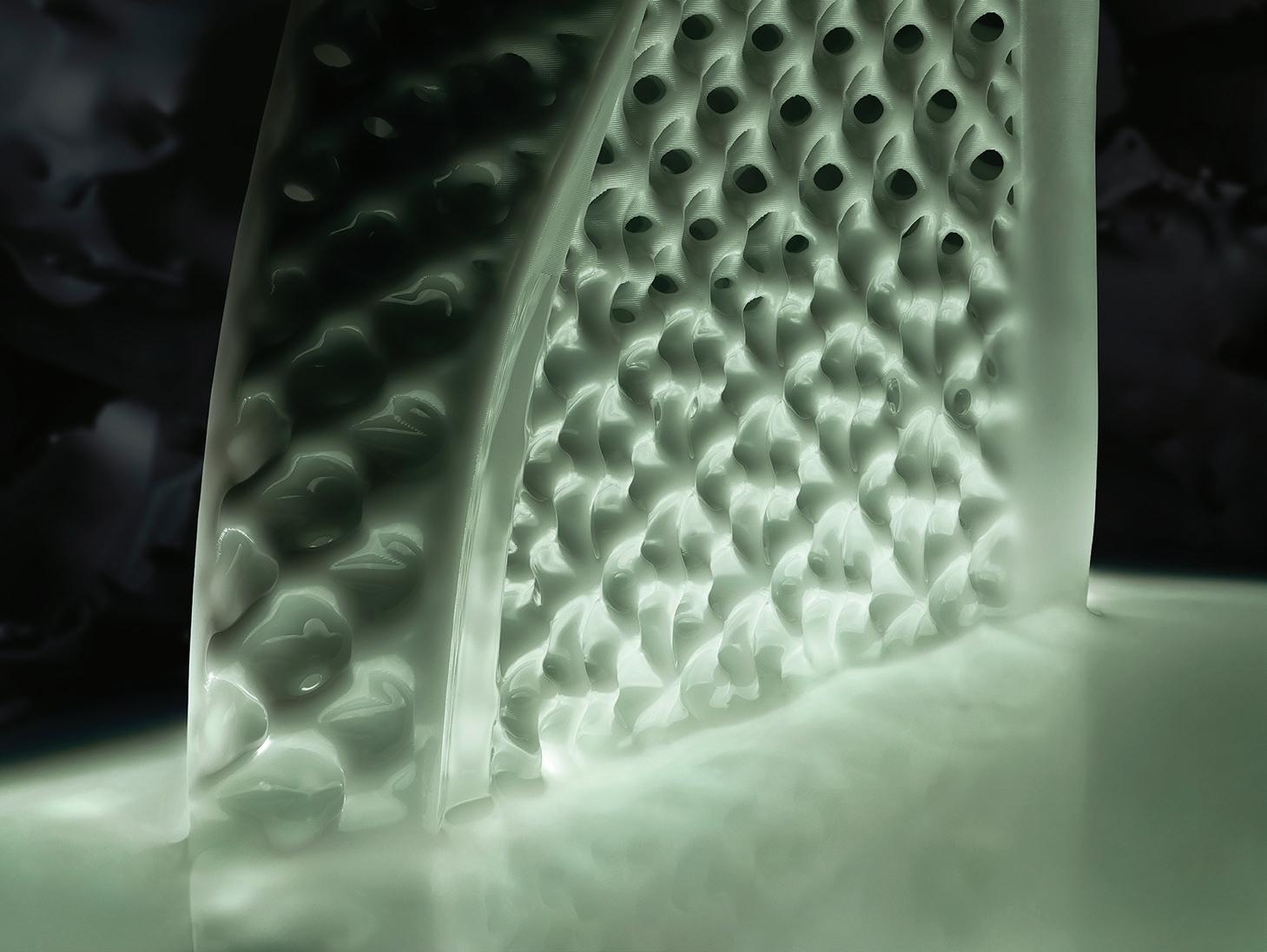
Carbon | www.carbon3d.com
The Carbon Digital Light
Synthesis system opened the door to more easily work with lattice structures. Carbon3D offers a lattice design generator called Design Engine that automates the process of creating conformal, single-zone lattices.
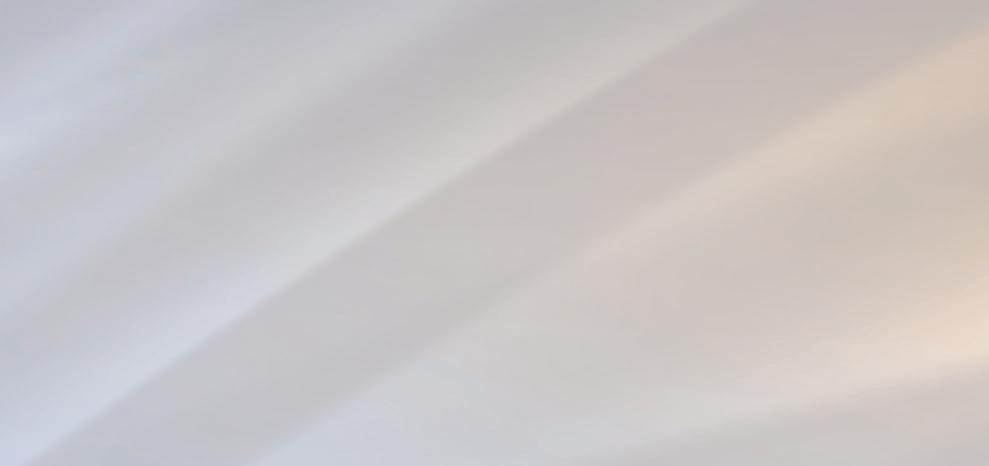
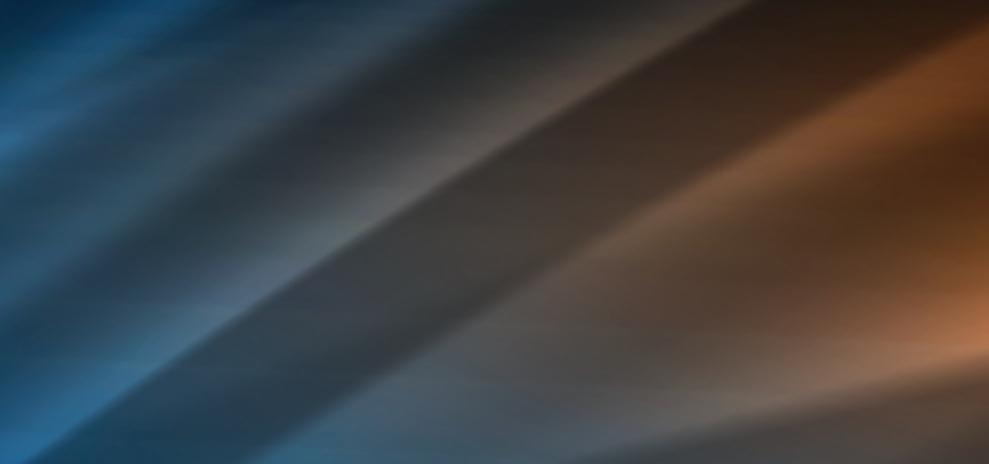
2021 Vendors in the additive industry
3D Platform
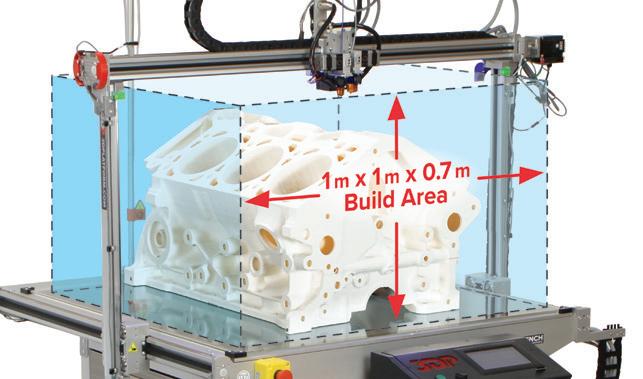
3D Platform is the trusted source for industrial-strength, large-format 3D printers. Based in Roscoe, Illinois, USA, the 3D Platform team is focused on driving advancements in technology to innovate, design, and build next-generation equipment for additive manufacturing. Our approach to 3D printing focuses on four clear industry demands:
Scalability and increased throughput from high-flow extruders allows smart manufacturers to shed legacy product development cycles and small-scale models for full-size prototypes and production.
Open market-enabled solutions allow users to go bigger with 16 times the speed of competitors’ extruders for faster printing and exceptionally strong parts.
• Quick-Swap dual extruder heads deliver high quality 3D prints. • Modular design accommodates variable nozzle and filament sizes • Nozzle flexibility for fine layer resolutions or faster printing and strength.
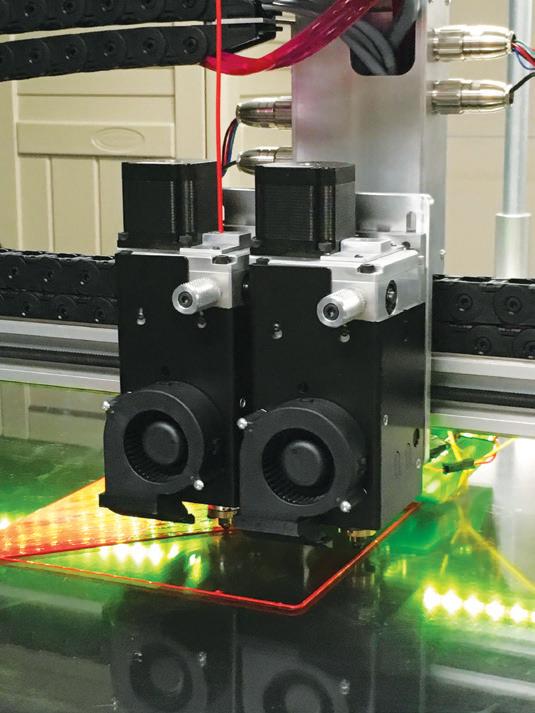
• Nozzle flexibility for fine layer resolutions or faster printing and strength. Affordability of equipment and materials allows SMB’s and Fortune 100 companies to tailor 3D printing to their needs, and quickly develop new products and bring them to the market.
Robust industrial technology stands up to harsh environments and the excessive demands of rapid manufacturing using the world’s leading linear motion mechatronics, reliable motors, and sophisticated control systems.
To learn more about 3D Platform, visit www.3dplatform.com.
3D Platform
6402 E. Rockton Road Roscoe, Illinois 61073 USA
+1.779.771.0000 3dplatform.com marketing@3dplatform.com sales@3dplatform.com
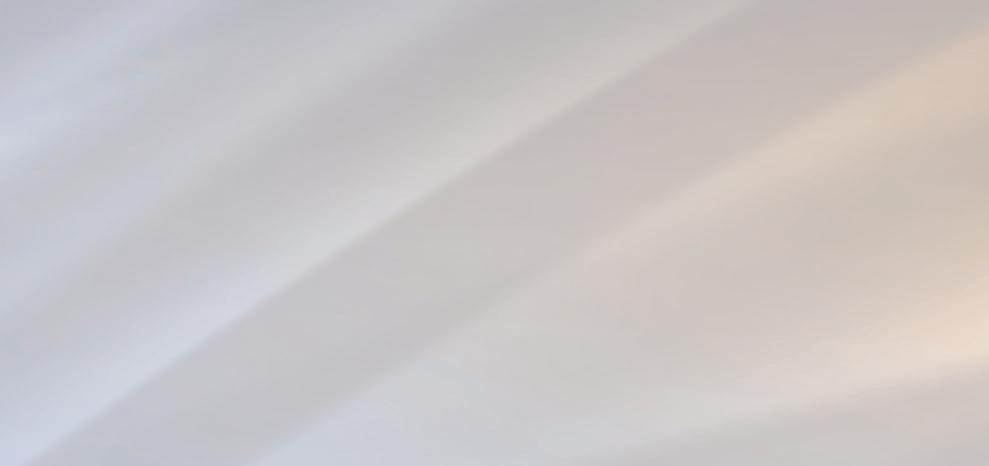
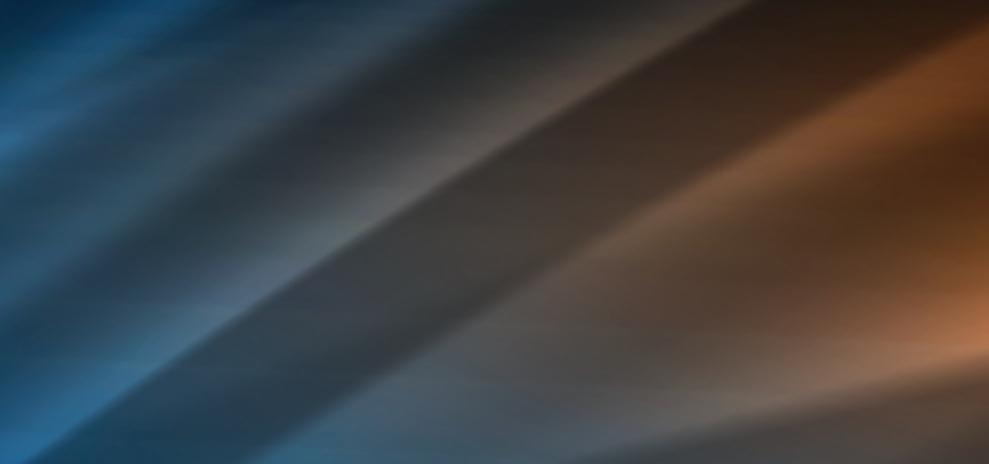
2021 Vendors in the additive industry
BuildParts by CIDEAS Inc.
Additive Manufacturing Since 1998

Established in 1998, BuildParts by CIDEAS Inc. is a full service 3D Printing and Additive Manufacturing provider.
Utilizing over 30 in-house machines, BuildParts offers all major technologies under one roof, including; SLA, SLS, FDM, DLP, DLS, Full Color PolyJet and a variety of part finishing options, urethane castings, as well as, engineering services.
BuildParts sets the benchmark for price, quality, experience and lead-times. Our experienced and dedicated staff of project managers act as a free consulting company for your unique project needs.
Available same day printing and secure interactive online quoting. Receive your 3D Printing and Additive Manufacturing quote at: BuildParts.com or contact us today at 847.639.1000
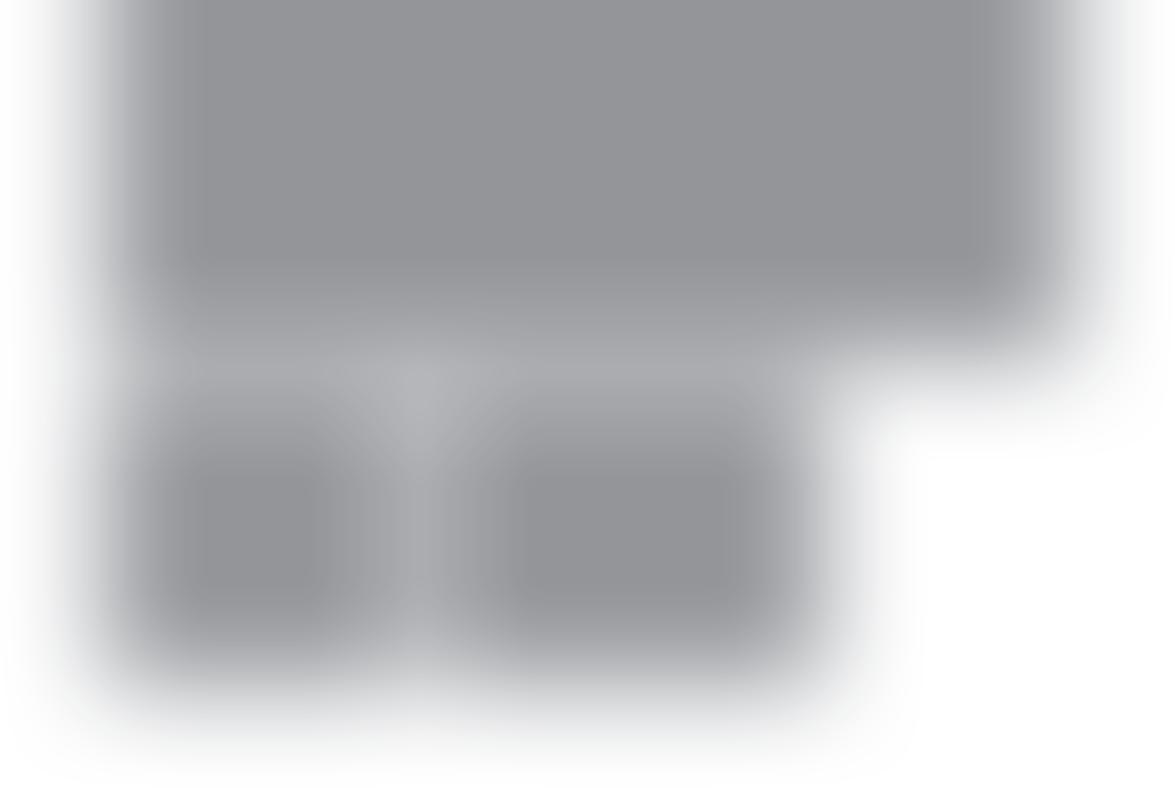
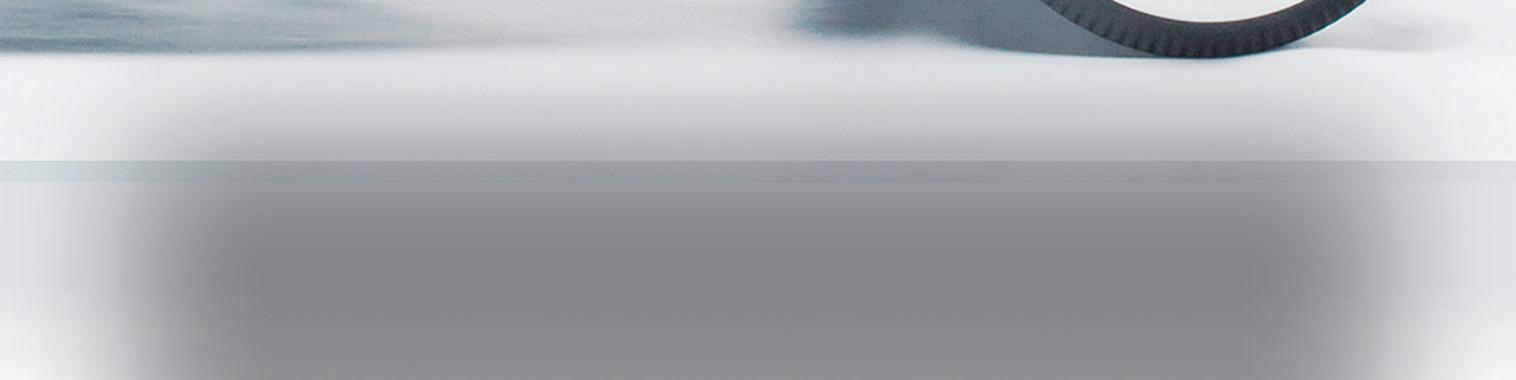

CIDEAS Inc.
125 Erick Street Unit #A115, Crystal Lake IL 60014 USA
Email: info@buildparts.com Web: www.buildparts.com Offi ce: +1 847-639-1000 | Facsimile: +1 847-639-1983
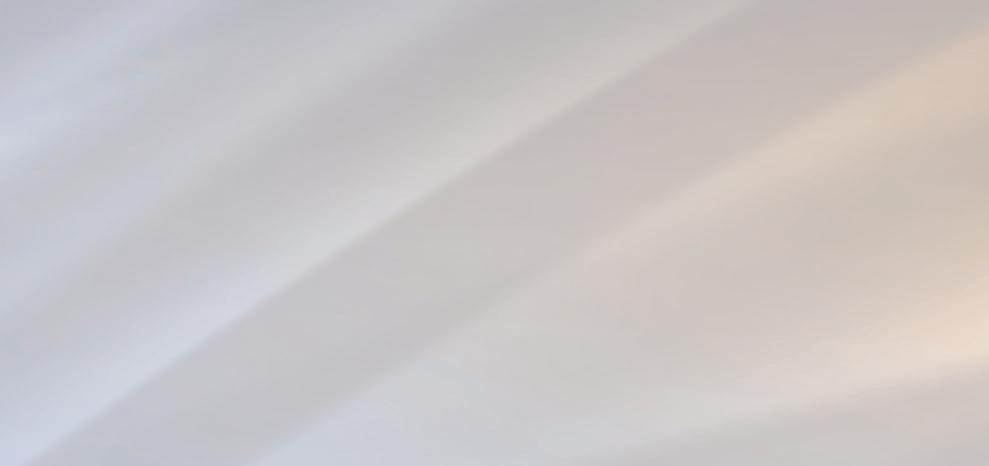
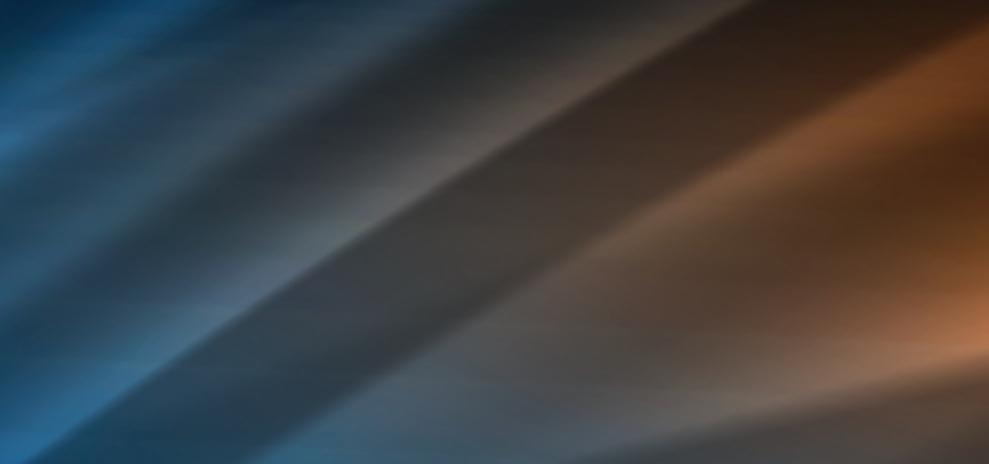
2021 Vendors in the additive industry
CS Hyde Company

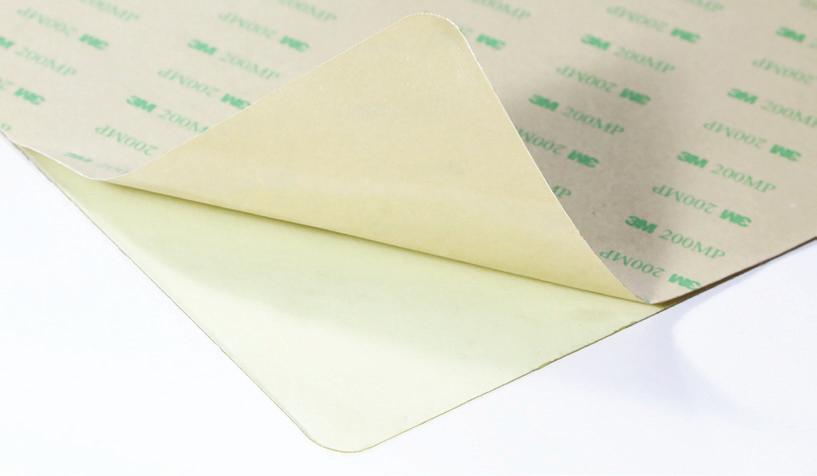

CS Hyde Company is your source high performance tapes, polymer films, fabrics, and silicone. For over 20 years we have been supplying almost every industry with performance materials for all types of applications. Our product line is composed of a variety of materials with properties associated with additive manufacturing/3D printing including low friction, nonstick release, and high temperature resistance. As a polymer film supplier of engineering grade thermoplastics and PTFE Fluoropolymers, we have grown to be a premiere source for custom printing surfaces. Common materials include ULTEM® PEI, and Optically Clear FEP tape or film. FDM printers using PEI benefit from a surface with durability and a surface that will hold filament in place and remove cleanly when cooled. Our PEI sheets are also pre-laminated with high temperature 3M™ adhesive that adhere to spring steel or glass build plates. FEP film is a great release material for resin vats found on DLP, Laser, LCD or as a release layer for tensioned “drum” style resin vats. Our custom cutting capabilities allow us to cut these materials to exact dimensions of any build plate or resin tray. Common sizes are available on our online catalog for click and ship availability.
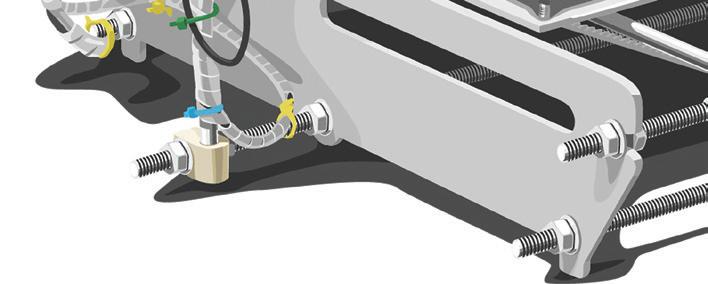
CS Hyde Company
800-461-4161 resources@cshyde.com
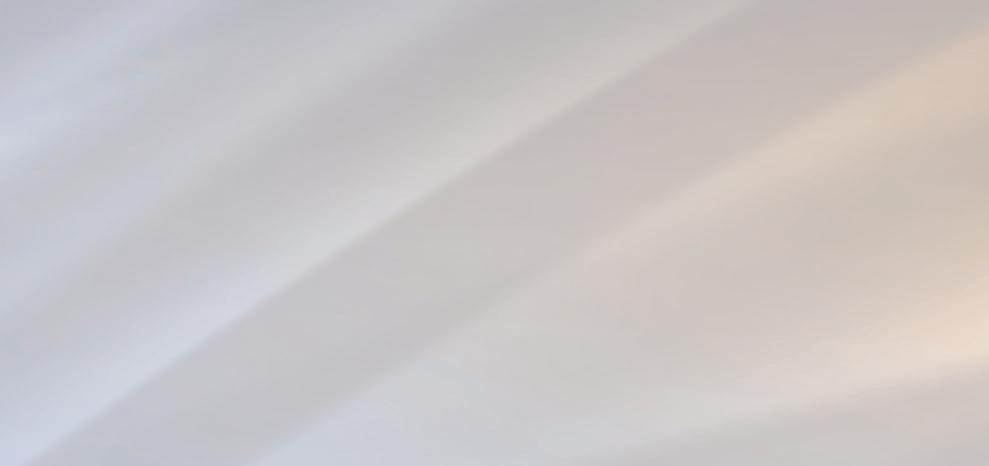
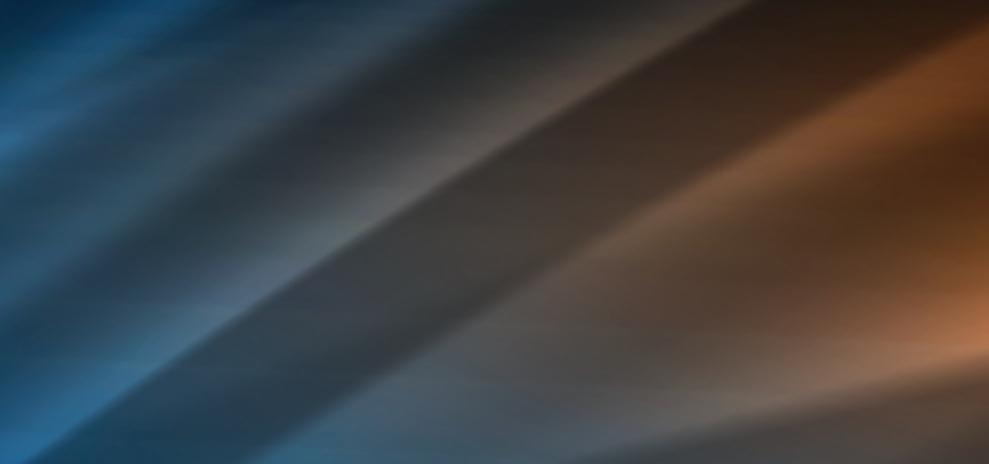
2021 Vendors in the additive industry

HP Multi Jet Fusion 3D Printing Technology

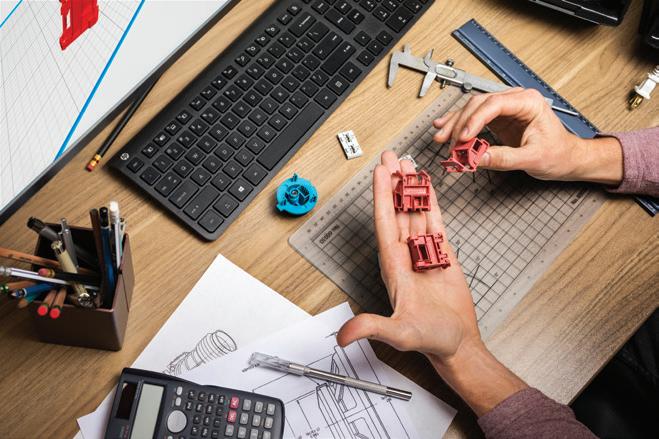
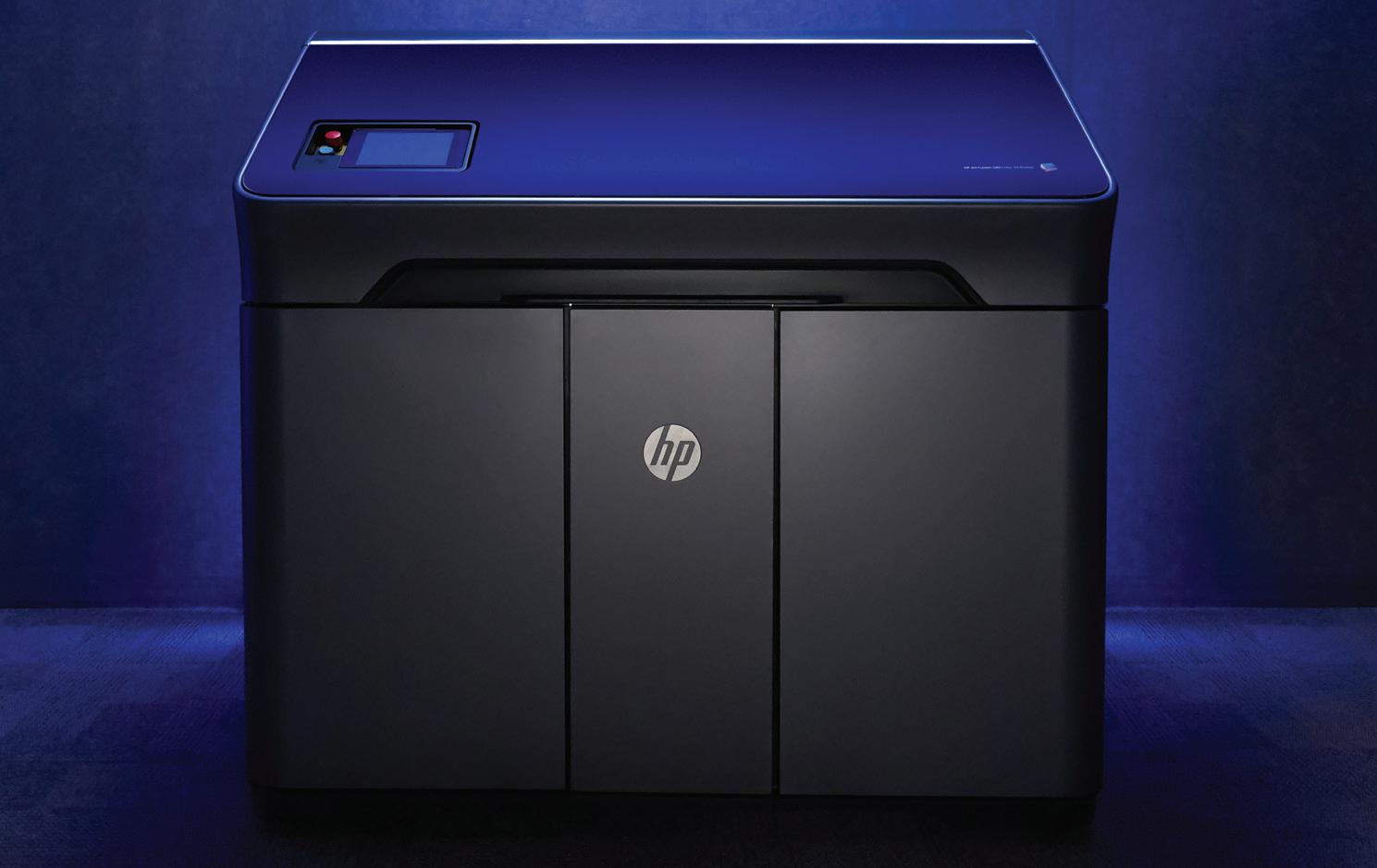
HP Inc. creates technology that makes life better for everyone, everywhere. Through our portfolio of personal systems, printers, and 3D printing solutions, we engineer experiences that amaze. More information about HP Inc. is available at www.hp.com/go/3DPrint.
Products:
• HP Jet Fusion 5200 Series 3D Printer • HP Jet Fusion 4200 Series 3D Printer • HP Jet Fusion 500/300 Series 3D Printers • HP Metal Jet
https://www8.hp.com/us/en/printers/3d-printers.html
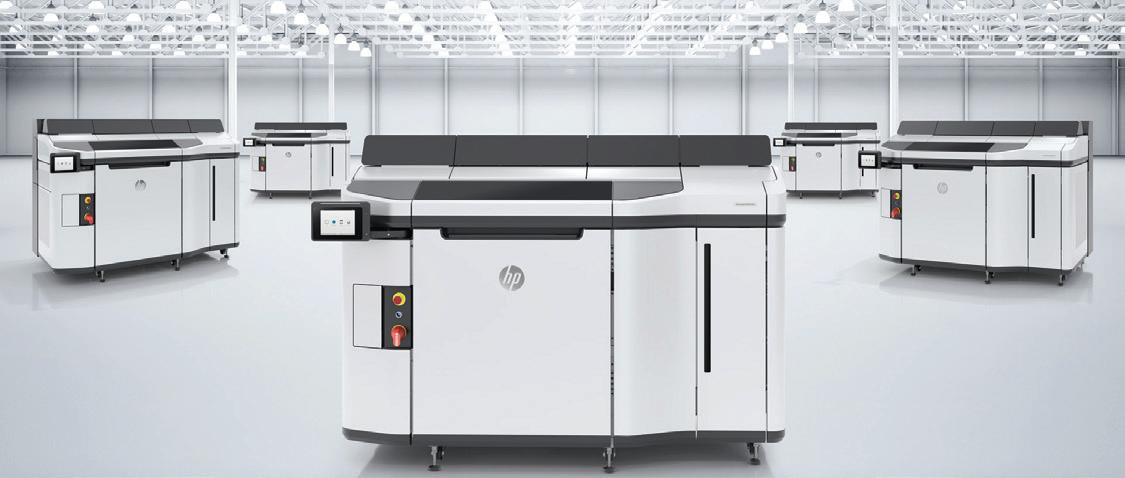
HP 3D Printing
1501 Page Mill Road Palo Alto, California 94304-1100
Phone: 877.468.8369
hp.com/go/3DPrint
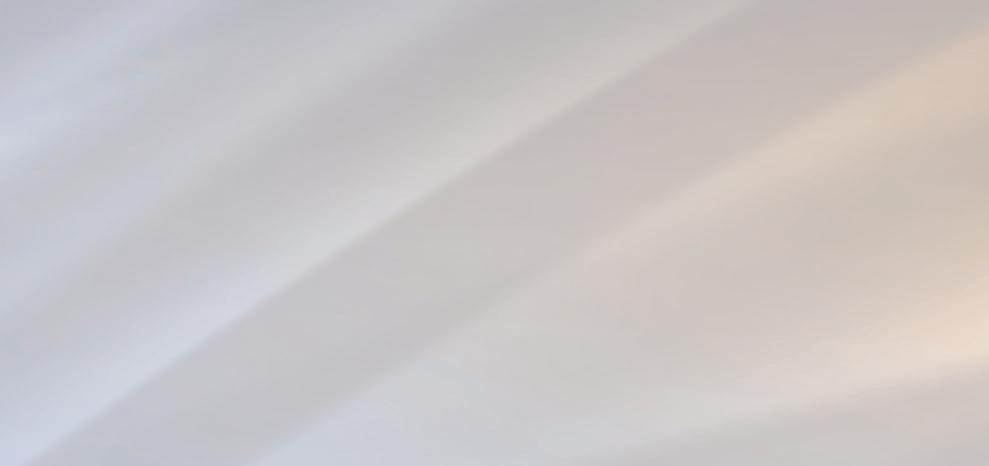
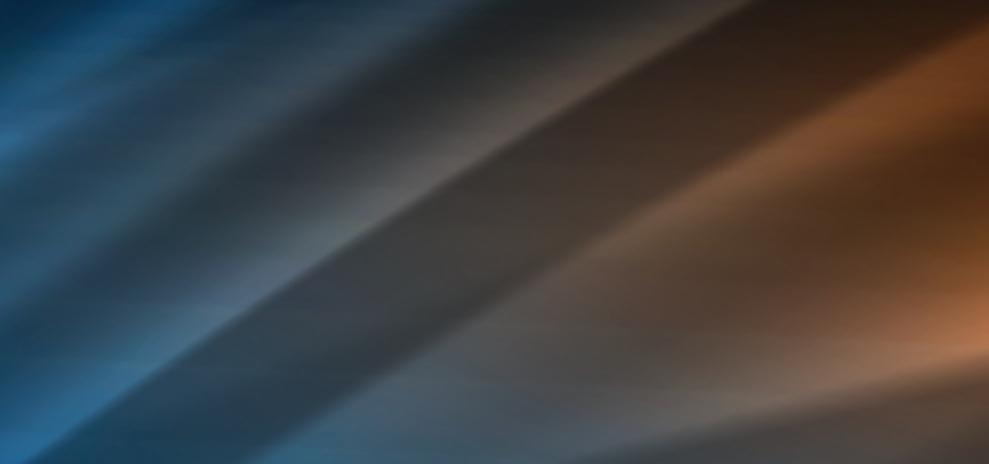
2021 Vendors in the additive industry
Yaskawa America, Inc.
Bring new precision and performance to every stage in your additive machine development with Yaskawa motion control
Rise above the desktop: Shaky, imprecise desktop machines become robust industrial performers with motion control that overcomes vibration, boosts speed and gets you ready for tomorrow's hybrid technologies.
Advance the industry standard: Industrial quality printers benefit from Yaskawa's smooth and precise motion, plus worldwide support that distinguishes your machine in a crowded marketplace.
Restate the state of the art: Top tier manufacturers need new ideas, plus the engineering support to make them work. Yaskawa supplies both, using the latest linear and robotic motion systems and Singular Control to create a seamless, supportable development environment. Our motion control technology also prepares you for new frontiers in additive manufacturing:
• Robotic systems that produce curvilinear motion for true 3D deposition • Additive/Subtractive technology which combines the benefits of 3D printing and traditional routing/machining
Yaskawa servos provide smooth, precise motion for additive manufacturing, while the G-code compatible MP3300iec controller can operate any motion device to implement the latest advances in hybrid manufacturing. Couple these with Yaskawa Compass™, our customizable user interface software package, to bring new precision, performance, and creativity to your additive machines.

Yaskawa America, Inc.
2121 Norman Drive South Waukegan, IL 60085